Тонкопленочное покрытие и способ его изготовления
Формула / Реферат
1. Способ изготовления продукта с покрытием, включающим оптическую пленку, в котором:
а) подготавливают подложку;
б) осаждают первое покрытие оптической пленки по меньшей мере на часть подложки в онлайн режиме из положения в онлайн процессе для первого покрытия, причем это первое покрытие содержит кремний;
в) осаждают второе покрытие, содержащее оксид олова, легированный фтором, по меньшей мере на часть первого покрытия, причем второе покрытие осаждают при температуре в интервале 400-800°С из газового потока, содержащего окисляющее вещество, которое выбирают из группы, состоящей из перекисей, азотной кислоты, нитратов, нитритов, закиси азота, серной кислоты, сульфатов, персульфатов, хлорноватистой кислоты, хлоратов, перхлоратов, броматов, боратов и их комбинаций.
2. Способ по п.1, в котором в качестве подложки используют стеклянную подложку.
3. Способ по п.1, в котором первое покрытие содержит кремний в форме оксида, нитрида или карбида или их комбинаций.
4. Способ по п.1, в котором первое покрытие содержит материал, выбранный из группы, состоящей из оксида кремния, диоксида кремния, нитрида кремния, оксинитрида кремния, карбида кремния или оксикарбида кремния или их комбинаций.
5. Способ по п.1, в котором первое покрытие содержит оксикарбид кремния.
6. Способ по п.1, в котором окисляющее вещество выбирают из группы, состоящей из азотной кислоты, закиси азота, хлорноватистой кислоты и серной кислоты и их комбинаций.
7. Способ по п.1, в котором в качестве окисляющего вещества используют азотную кислоту.
8. Способ по п.1, в котором второе покрытие осаждают при температуре в интервале 550-750°С.
9. Способ по п.1, в котором первое покрытие содержит единичный слой оптический пленки.
10. Способ по п.1, в котором первое покрытие содержит несколько слоев оптической пленки.
11. Способ по п.1, в котором первое покрытие осаждают при температуре в интервале 400-800°С.
12. Способ по п.1, в котором первое покрытие осаждают при температуре в интервале 650-750°С.
13. Способ изготовления продукта с покрытием, в котором:
а) подготавливают подложку;
б) осаждают предварительное покрытие покрытия оптической пленки по меньшей мере на часть подложки в онлайн режиме из положения в онлайн процессе для предварительного покрытия;
в) осаждают первое покрытие покрытия оптической пленки по меньшей мере на часть предварительного покрытия в онлайн режиме из положения в онлайн процессе для первого покрытия, причем это первое покрытие содержит кремний;
г) осаждают второе покрытие покрытия оптической пленки, содержащее оксид олова, легированный фтором, по меньшей мере на часть первого покрытия в онлайн режиме из положения в онлайн процессе для второго покрытия,
причем второе покрытие осаждают из газового потока, содержащего окисляющее вещество, которое выбирают из группы, состоящей из перекисей, азотной кислоты, нитратов, нитритов, закиси азота, серной кислоты, сульфатов, персульфатов, хлорноватистой кислоты, хлоратов, перхлоратов, броматов, боратов и их комбинаций, и при температуре в интервале 400-800°С.
14. Способ по п.13, в котором предварительное покрытие содержит материал, выбранный из группы, состоящей из оксида титана, нитрида титана, карбида или оксикарбида титана или их комбинаций.
15. Способ по п.13, в котором предварительное покрытие содержит диоксид титана.
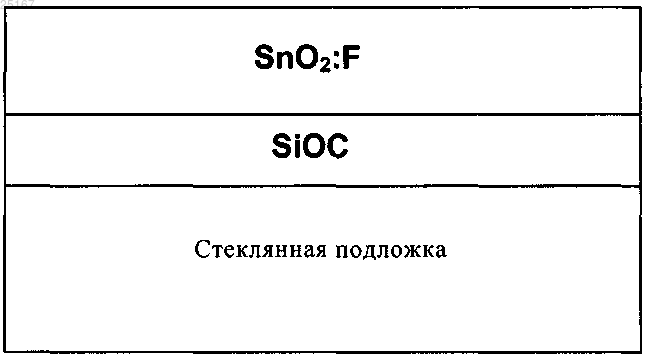
Текст
В изобретении описаны многослойные системы оптических тонких пленок с низкой излучательной способностью, с улучшенными характеристиками отражения оптического и инфракрасного излучения и способы их изготовления. Предложен способ изготовления продукта с покрытием,включающим оптическую пленку, в котором осаждают первое покрытие оптической пленки,содержащее кремний, по меньшей мере на часть подложки и осаждают второе покрытие,содержащее оксид олова, легированный фтором, по меньшей мере на часть первого покрытия,причем второе покрытие осаждают при температуре в интервале 400-800 С из газового потока,содержащего окисляющее вещество, которое выбирают из группы, состоящей из перекисей,азотной кислоты, нитратов, нитритов, закиси азота, серной кислоты, сульфатов, персульфатов,хлорноватистой кислоты, хлоратов, перхлоратов, броматов, боратов и их комбинаций.(71)(73) Заявитель и патентовладелец: ЭЙ-ДЖИ-СИ ФЛЕТ ГЛАСС НОРТ ЭМЕРИКЕ, ИНК. (US); ЭЙ-ДЖИ-СИ ГЛАСС ЮЭРОП (BE) Область техники Настоящее изобретение в целом относится к покрытиям с низкой излучательной способностью и, в частности, к покрытиям с низкой излучательной способностью, включающим по меньшей мере один слой оксида металла в качестве слоя(ев), отражающего инфракрасное (ИК) излучение. Уровень техники Все патенты и патентные документы, которые упоминаются в настоящем описании, полностью включены в настоящую заявку посредством ссылки. В случае разночтений считать правильным настоящее описание, включая определения. Покрытия на стекле с низкой излучательной способностью (low-E) должны пропускать видимый свет, одновременно отражая и задерживая инфракрасное (ИК) излучение. Покрытия с высоким пропусканием видимого света и низкой излучательной способностью, при их использовании в окнах зданий,автомобилях и дверках торговых холодильников и морозильников, могут обеспечить получение значительной экономии в расходах, связанных в управлением параметрами окружающей среды, например,расходами на нагревание и охлаждение. Как правило, покрытия, имеющие высокое пропускание в видимом свете и низкую излучательную способность, выполняются в виде многослойной системы, обычно включающей прозрачную подложку(основу) и оптическое покрытие. Многослойная система может включать один или более тонких металлических слоев, обладающих высоким отражением и низким пропусканием ИК излучения, расположенных между просветляющими (антибликовыми) диэлектрическими слоями. Просветляющие диэлектрические слои представляют собой в целом прозрачные материалы, выбираемые для улучшения пропускания в области видимого света. Эти системы отражают излучаемое тепло и служат изолятором как от холода,так и от солнечного излучения. Большая часть существующих многослойных low-E систем основана на слоях металлов, например серебра, помещенного между тонкими прозрачными слоями оксидов металлов. Обычно, толщина диэлектрических слоев выбирается исходя из снижения внутреннего и внешнего отражения с тем, чтобы пропускание света превышало 60%. В качестве металла слоев, отражающих ИК излучение, может использоваться практически любой отражающий металл, например серебро, медь или золото. Наиболее часто в подобных применениях используется серебро (Ag), благодаря его относительно нейтральному цвету. В то время, однако, как покрытия, включающие нанесенные распылением слои серебра в комбинации с диэлектрическими слоями в многослойных системах, позволяют получить продукт, защищающий от солнечного излучения, с высокими рабочими характеристиками (например, почти нейтральная характеристика, как при отражении, так и при пропускании), они обладают значительными недостатками, связанными с использованием серебра в многослойных системах с низкой излучательной способностью. Во-первых, подходящие слои серебра не допускают их нанесения "онлайн" методами, когда покрытие наносится на ленту горячего стекла в процессе ее изготовления, например перед ее нарезкой и снятия с технологической линии, а вместо этого наносятся в отдельном процессе ("офлайн"), например, нанесением вакуумным магнетронным распылением. Это ограничение, присущее слоям серебра, наносимым распылением, увеличивает общее время изготовления конечного продукта с покрытием. Во-вторых, такие покрытия обладают пониженной химической и механической стойкостью, требуют тщательной защиты и аккуратного обращения при изготовлении и транспортировке. Тонкие, прозрачные слои металлического серебра при наличии влаги или в условиях влажной атмосферы подвержены коррозии в случае контакта с коррозионно-активными веществами, например, находящимися в атмосфере хлоридами,сульфидами, диоксидом серы и т.д. Для защиты таких слоев серебра на их поверхность могут быть нанесены различные защитные слои. Однако защита, обеспечиваемая обычными защитными слоями, зачастую оказывается недостаточной. Тонкие, прозрачные слои металлического серебра также подвержены деградации при тепловой обработке, гибке и(или) закалке. Когда покрытое стекло подвергается закалке или гибке, покрытие нагревается вместе со стеклом до температуры порядка 600 С и более на время до нескольких минут. Такая термическая обработка может привести к необратимому ухудшению оптических свойств Ag покрытия. Это ухудшение может быть результатом окисления серебра кислородом,диффундирующим сквозь слои, расположенные над и под слоем Ag. Ухудшение также может быть следствием реакции серебра с щелочными ионами, например ионами натрия (Na+), мигрирующими из стекла. Диффузия кислорода или щелочных ионов может поддерживаться и усиливаться деградацией или изменением структуры диэлектрических слоев над слоем серебра и под ним. Покрытия на стекле должны быть в состоянии выдержать такие повышенные температуры. Однако известные многослойные покрытия, использующие серебро в качестве пленки, отражающей инфракрасное излучение, зачастую не в состоянии выдерживать такие температуры без некоторой деградации пленки серебра. Таким образом, существует потребность в многослойных системах с низкой излучательной способностью (и способах их изготовления), в которых преодолены упомянутые выше недостатки, известные специалистам. В частности, требуются low-E оптические покрытия, сохраняющие или имеющие улучшенную эстетическую привлекательность и механическую и(или) химическую стойкость, и которые при необходимости могут подвергаться закалке или термическому упрочнению. Требуются покрытия для солнцезащитного остекления с высокими характеристиками, не страдающие упомянутыми недостатками серебряных покрытий, которые в предпочтительном варианте имели бы отражение и пропускание с цветовой характеристикой, близкой к нейтральной. Такой альтернативой являются тонкопленочные low-E отражающие ИК излучение слои покрытия на основе оксида олова или легированного оксида олова, применение которых позволяет обойти упомянутые проблемы, возникающие при использовании отражающих ИК излучение слоев напыленного серебра. Тонкопленочные покрытия на основе оксида олова с низкой излучательной способностью хорошо известны. Такие покрытия из оксида олова обладают рядом преимуществ по сравнению с отражающими ИК излучение слоями Ag, нанесенными напылением. Одно из таких преимуществ состоит в том, что покрытия оксида олова могут быть нанесены пиролитическим осаждением на поверхность нагретой стеклянной ленты. Другими словами, тонкопленочный слой оксида олова может пиролитически наноситься в процессе производства стекла (онлайн), благодаря чему сокращается время изготовления конечного продукта с покрытием. Другим преимуществом является то, что пиролтически нанесенные тонкопленочные слои оксида олова являются твердыми покрытиями. Твердые покрытия обычно обладают более высокой механической и химической стойкостью по сравнению с нестойкими покрытиями, например нанесенными офлайн напылением тонкими пленками серебра. Такие твердые покрытия, введенные в оптическуюlow-E систему, придают ей повышенную устойчивость к деградации при термической обработке, закалке или гибке. Однако тонкопленочные low-E слои на основе оксида олова обычно не обладают свойством отражать ИК излучение, сравнимое с этой способностью low-E тонкопленочных слоев металла, или серебра. Кроме того, такие пиролитические покрытия на стекле обладают термостойкостью и стекло может подвергаться термическому упрочнению или закалке без повреждения покрытия. Таким образом, существует потребность в low-E тонкопленочных слоях на основе оксида металла,которые позволяют преодолеть упомянутые выше проблемы, присущие тонкопленочным слоям металла или Ag, полученным напылением. В частности требуются low-E тонкопленочные слои на основе оксида металла, обладающие отражением ИК излучения, близким к отражению ИК излучения тонкопленочными слоями напыленного металла или серебра. Сущность изобретения В настоящем изобретении предлагаются многослойные тонкопленочные оптические системы, обладающие улучшенными оптическими свойствами, а также способы получения таких улучшенных low-E тонкопленочных многослойных оптических систем. Согласно особенности настоящего изобретения предлагаются способы улучшения оптических характеристик и(или) характеристик отражения ИК излучения low-E тонкопленочных многослойных оптических систем. Согласно другой особенности настоящего изобретения предлагаются способы улучшения оптических характеристик и(или) характеристик отражения ИК излучения low-E тонкопленочных многослойных оптических систем путем введения окисляющих химических присадок в процессе пиролитического осаждения тонкой пленки легированного оксида олова. Согласно другой особенности настоящего изобретения окисляющая химическая присадка, вводимая во время пиролитического осаждения, позволит получить конечный продукт с покрытием, который при введении его в стеклопакет придаст стеклопакету улучшенные оптические характеристики и(или) характеристики отражения ИК излучения. Согласно еще одной особенности настоящего изобретения окисляющая химическая присадка, вводимая в процессе пиролитического осаждения, позволит добиться более 20% увеличения эффективности покрытия. Краткое описание чертежей Ниже изобретение более подробно рассмотрено со ссылкой на прилагаемые чертежи, на которых на фиг. 1 представлена структура оптической многослойной системы в соответствии с особенностью настоящего изобретения; на фиг. 2 - структура оптической многослойной системы в соответствии с другой особенностью настоящего изобретения; на фиг. 3 представлен стеклопакет, включающий структуру оптической многослойной системы, показанную на фиг. 1; на фиг. 4 представлен стеклопакет, включающий структуру оптической многослойной системы, показанную на фиг. 2. Подробное описание осуществления изобретения Хотя настоящее изобретение может быть осуществлено во многих различных формах, в настоящем описании приводится несколько частных вариантов осуществления и подразумевается, что настоящее раскрытие представляет примеры осуществления принципов изобретения, которые не ограничивают изобретение описанными и(или) изображенными здесь предпочтительными вариантами осуществления. Различные варианты осуществления раскрыты достаточно подробно для того, чтобы специалисты могли осуществить изобретение. Должно быть понятно, что возможно использование и других вариантов осуществления, и что изменения в конструкции и последовательности могут быть введены без отступления от существа или области притязаний настоящего изобретения. В настоящем изобретении предложены low-E тонкопленочные многослойные оптические системы с улучшенными оптическими и ИК отражающими свойствами, и способы изготовления таких low-E тонкопленочных многослойных оптических покрытий. Способы в соответствии с настоящим изобретением обеспечивают получение low-E тонкопленочных многослойных оптических систем, представленных на фиг. 1. Такие low-E тонкопленочные оптические системы имеют общую конфигурацию: стеклянная подложка/SiOC/SnO2:F. Способы в соответствии с настоящим изобретением также применимы к low-E слоям, расположенным на нескольких подслоях и(или) зародышевых слоях, например, как показано на фиг. 2. Такие low-E оптические многослойные системы могут иметь общую конфигурацию: стеклянная подложка/TiO2/SiO2/SnO2:F. В такой конфигурации нанесенные подслои SiO2 могут также содержать оксиды кремния с содержанием кислорода ниже стехиометрического (обозначены как "SiOx" или "SiOC"), а также имеющие примесь металла, напримерAl и Sn. Специалистам известно и понятно использование подобных альтернативных многослойных систем. В настоящем описании обозначения "Е 2+" или "Комфорт Е 2+" представляют систему стеклянная подложка (СП)/SiOC/SnO2:F, в которой тонкая пленка оксида олова, легированного фтором, наносится пиролитическим химическим осаждением из паровой фазы известными специалистам способами в присутствии окисляющей химической добавки. В этой системе окисляющей химической добавкой являетсяHNO3. В этих системах толщина пленки оксида олова может составлять от 150 до 800 нм и более желательно примерно 430 нм."Подслой" или ПС может включать слой оксикарбида кремния различной толщины, включая интервал от 400 до 1000 и в предпочтительном варианте примерно 720 . Подслой обеспечивает получение необходимого коэффициента преломления для получения нейтральной цветовой характеристики и,тем самым, способствует улучшению пропускания оптической многослойной системы в целом, и, кроме того, выполняет функцию защитного слоя для подавления миграции ионов натрия из стеклянной подложки в low-E тонкую пленку."Флоат-стекло" или "листовое стекло" означает стекло, изготавливаемое методом "плавающей ленты", когда непрерывный поток расплавленного стекла выпускают в ванну поверх расплавленного олова. Расплавленное стекло расходится по поверхности металла и образует лист стекла высокого качества постоянной толщины. Изготовление стекла, таким способом, является общепринятым в промышленности. Фактически, свыше 95% мирового производства листового стекла использует технологию плавающей ленты. Если не указано иначе, далее подразумевается, что стекло изготовлено по технологии плавающей ленты."Онлайн технология" или "онлайн" является хорошо знакомым и понятным термином для специалистов в области покрытий на стекле, и в настоящем раскрытии относится к покрытию стеклянной ленты в процессе изготовления стекла методом плавающей ленты."Офлайн технология" или "офлайн" является также хорошо знакомым и понятным термином для специалистов в области покрытий на стекле, и в настоящем раскрытии относится к покрытию стекла после того, как оно было изготовлено и извлечено из флоат-ванны. Используемые здесь термины "нанесенный на" или "нанесенный поверх" означают, что вещество нанесено прямо либо опосредованно на соответствующий слой. Если вещество нанесено опосредованно,то могут быть один или более промежуточных слоев. Кроме того, если не указано иначе, при описании покрытий настоящего изобретения с использованием формы "[вещество или слой 1]/[вещество или слой 2]/[вещество или слой 3]/" или формы "первый [вещество 1] слой; первый [вещество 2] слой; второй[вещество 1] слой; второй [вещество 2] слой; " или аналогичной, имеется в виду, что каждое следующее вещество или слой нанесены на предшествующее вещество или слой прямо или опосредованно. Термин "матовость" используется здесь в соответствии со стандартом Американского общества по испытаниям материалов ASTM D 1003, который определяет матовость как процент света, который при прохождении отклоняется от направления падающего луча в среднем более чем на 2,5. "Матовость" может быть измерена методами, известными специалистам. Приводимые здесь данные по матовости были получены измерениями на нефелометре фирмы BYK Gardner (все приведенные здесь значения матовости получены измерением на таком нефелометре и выражены в процентном соотношении рассеянного и падающего света). Термин "коэффициент отражения" хорошо известен и используется здесь в соответствии с его известным значением. Например, используемый здесь термин "коэффициент отражения" означает количество видимого, инфракрасного и ультрафиолетового света, которое отражается поверхностью, по отношению к количеству света, падающего на поверхность. Термин "коэффициент поглощения" хорошо известен и используется здесь в соответствии с его известным значением. Коэффициент поглощения представляет собой отношение части солнечной энергии,падающей на поглотитель, которая поглощается поглотителем, к части солнечной энергии, падающей на черное тело (идеальный поглотитель) и поглощающейся им, при той же температуре. Термины "термическая обработка" и "термически обработанный" в настоящем раскрытии означают нагревание изделия до температуры, достаточной для термического закаливания, гибки и термического упрочнения изделия с покрытым стеклом. Это определение включает, например, нагревание покрытого изделия до температуры по меньшей мере примерно 1100F (т.е. до температуры примерно от 550 до 700 С) в течение времени, достаточного для закалки, термического упрочнения или гибки. Термин "коэффициент солнечного теплопритока" или "SHGC" (от англ. solar heat gain coefficient) или "G" широко известен и характеризует соотношение прошедшего сквозь оконную систему полного солнечного теплопритока и падающего солнечного излучения. Эта величина является мерой того, насколько хорошо окно задерживает тепло от солнечного света и представляет часть тепла от солнца, проходящего сквозь окно. Коэффициент солнечного теплопритока выражается числом от 0 до 1. Чем нижеSHGC окна, тем меньше солнечного тепла оно пропускает. Термин "излучательная способность" (или коэффициент излучения) (Е) представляет собой меру или характеристику отражения света на данной длине волны и выражается формулой Е=1 - коэффициент отраженияпленки для волн инфракрасного диапазона. Излучательная способность представляет собой отношение излучения черного тела или поверхности и излучения, предсказываемого законом Планка. Термином "излучательная способность" пользуются для величин излучательной способности, измеренной в инфракрасном диапазоне по методикам стандарта Американского общества специалистов по испытаниям материалов (ASTM - American Society for Testing and Materials). Излучательная способность определяется радиометрическими измерениями и выражается излучательной способностью в полусферу и излучательной способностью по нормали. Излучательная способность показывает процент длинноволнового ИК излучения, испускаемого покрытием. Более низкая излучательная способность показывает, что сквозь стекло может пройти меньше тепла. Практический сбор данных для измерения величин излучательной способности является обычной процедурой, известной специалистам, и может быть выполнен с использованием, например, спектрофотометра Beckman Model 4260 с приставкой "VW" (компанияBeckman Scientific Inst. Corp.). Этот спектрофотометр измеряет спектральный коэффициент отражения, и на основании полученных результатов может быть рассчитан коэффициент излучения с использованием стандартных уравнений, известных специалистам."Коэффициент теплопередачи" (U value), используемый в настоящем описании, является мерой скорости потери или поступления тепла, не связанного с солнечным излучением, сквозь материал или конструкцию. Коэффициенты теплопередачи показывают, насколько хорошо материал позволяет теплу проходить сквозь него. Значения коэффициента теплопередачи обычно составляют от 0,20 БТЕ/ч кв.футF и 1,2 БТЕ/ч кв.фут F. Чем ниже величина коэффициента теплопередачи, тем сильнее материал сопротивляется потоку тепла и тем лучше его изолирующие свойства. Величина, обратная коэффициенту теплопередачи (единица, деленная на этот коэффициент), представляет собой теплосопротивление. Коэффициент теплопередачи (U value) обычно выражается в Вт/м С или БТЕ/ч кв.фут F. В США эти величины обычно определяются по методике Национального совета по оценке окон/Американского общества отопления, охлаждения и воздушного кондиционирования (National Fenestration Rating Council/AmericanSociety of Heating, Refrigerating, Airconditioning Engineers) для зимних условий при наружной температуре 0F(-18 С), температуре в помещении 70F (21 С), скорости ветра 15 миль/ч и в отсутствие солнечного облучения. Коэффициенты теплопередачи часто приводятся для окон и дверей. В случае окна, например, коэффициент теплопередачи может быть дан для одного стекла или для всего окна с учетом влияния рамы и заполняющих пустоты материалов."Low-E" или "low-E покрытие" в настоящем описании означает микроскопически тонкий, практически невидимый слой(и) металла или оксида металла, нанесенный на стеклянную подложку для снижения излучательной способности путем подавления потока теплового излучения сквозь стекло. Термин "Твердое покрытие", используемый в настоящем описании применительно к low-E тонкопленочным покрытиям, означает пиролитически осажденное покрытие, которое было распылено или нанесено на поверхность стекла при высокой температуре в процессе изготовления флоат-стекла. Термин "Мягкое покрытие", используемый в настоящем описании применительно к low-E тонкопленочным покрытиям, означает покрытие, нанесенное вакуумным напылением в несколько слоев оптически прозрачного металла, заключенного между диэлектрическими слоями (обычно, оксидами металлов)."Коэффициент пропускания" является хорошо известным термином и используется в настоящем описании в своем обычном значении. Коэффициент пропускания в настоящем описании учитывает пропускание энергии в видимом, инфракрасном и ультрафиолетовом диапазонах. Термин "поверхностное сопротивление" (Rs) хорошо известен специалистам и используется здесь в соответствии с его известным значением. Эта величина выражается в омах на квадратную площадку. Вообще, этот термин относится к сопротивлению в омах, которое оказывает любой квадрат слоистой системы на стеклянной подложке электрическому току, проходящему через слоистую систему. Поверхностное сопротивление показывает, насколько хорошо слой или слоистая система отражают энергию инфракрасного излучения, и часто используется, наряду с излучательной способностью, как мера этой характеристики. Поверхностное сопротивление удобно измерить, например, посредством 4-зондового омметра, например 4-зондовым измерителем сопротивлений Model M-800 с одноразовыми электродами,-4 025167 производимым компанией Signatone Corp. из Санта Клары, шт. Калифорния, с использованием измерительной головки Magnetron Instruments Corp. Термин "стеклопакет" хорошо известен специалистам. Стеклопакет состоит из двух или трех листов стекла, загерметизированных по краям в герметизирующем узле, обычно называемом краевым уплотнителем. В стеклопакете, состоящем из трех листов стекла, между тремя листами стекла сформированы две изолирующие камеры. В стеклопакете, состоящем из двух листов стекла, формируется одна изолирующая камера. Число листов стекла, содержащихся в стеклопакете, зависит от его назначения. Например,стеклопакеты, которые должны быть использованы для холодильных камер, обычно выполнены из двух листов стекла, в то время как стеклопакеты для морозильных камер обычно используют три листа стекла. Перед окончательной герметизацией камеры могут быть заполнены воздухом или инертным газом,например аргоном, криптоном или иным подходящим газом, для улучшения тепловых характеристик стеклопакета."Эффективностью покрытия" в настоящем описании называют отношение фактической толщины слоя SnO2:F к теоретической толщине такого же слоя SnO2:F в предположении, что 100% исходных материалов преобразовались в нанесенную конечную тонкую пленку. Теоретическая толщина может быть вычислена на основе исходного количества материала олова, наносимого на поверхность стеклянной подложки, расхода исходного материала олова, площади поверхности стеклянной ленты, на которую наносится покрытие, и скорости движения стеклянной ленты, проходящей под устройством для нанесения покрытия, подающем исходные материалы оксида олова. Подобные способы расчета теоретической толщины знакомы специалистам. Приведенное далее описание представляет общий способ получения подслоя и тонкой пленки оксида металла, например оксида олова, легированного фтором, в соответствии с настоящим изобретением. Приведенное описание не подразумевает ограничения изобретения, и описанный в целом способ может быть модифицирован и изменен специалистами в области нанесения тонких пленок для его адаптации к конечному продукту, при этом изменения остаются в пределах области притязаний настоящего изобретения. Известково-натриевое флоат-стекло или листовое стекло, полученное из стекольной шихты известных составов, может быть расплавлено в стеклоплавильной печи. Температура, необходимая для расплавления такой стекольной шихты, обычно составляет примерно от 1500 до 1600 С. После расплавления для получения расплавленного стекла, расплавленное стекло выливается в флоат-ванну расплавленного олова, из которой стекло выплывает, образуя стеклянную ленту. Стеклянная лента обычно имеет температуру примерно 600-1100 С во флоат-ванне расплавленного олова. Стеклянная лента остывает по мере удаления от стеклоплавильной печи. В зоне нанесения покрытия по технологии "плавающей ленты", где происходит пиролитическое осаждение тонких пленок подслоя и оксида олова, легированного фтором, температура стеклянной ленты обычно составляет примерно 500-800 С. Подслой в соответствии с настоящим изобретением может быть пиролитически осажден первым устройством для нанесения покрытий, расположенным во флоат-ванне. Поток газовой смеси, содержащий силан (SiH4), углекислый газ (СО 2), этилен (С 2 Н 4) и азот (транспортирующий газ), может быть направлен на нагретую поверхность стеклянной ленты для создания и нанесения тонкой пленки подслоя оксикарбида кремния. Газы потока смешанных газов могут быть включены в каждый из вышеупомянутых исходных материалов, подводимых со следующим расходом: 1) силан (SiH4) 2,0-40,0 г/мин; 2) углекислый газ (СО 2) 50,0-500,0 г/мин; 3) этилен (С 2 Н 4) 0,0-150,0 г/мин и 4) азот (транспортирующий газ) 0,0200,0 г/мин. В предпочтительном варианте исходные материалы подводятся со следующим расходом: 1) силан (SiH4) 15,0-25,0 г/мин; 2) углекислый газ (СО 2) 150,0-200,0 г/мин; 3) этилен (С 2 Н 4) 20,0-100,0 г/мин и 4) азот (транспортирующий газ) 30,0-60,0 г/мин. Если должен использоваться двойной подслой TiO2 SiO2, то во флоат-ванну может быть также помещено устройство нанесения предварительного покрытия перед первым устройством нанесения покрытия, которое наносит слой на основе Si. От устройства предварительного нанесения покрытия поток смешанного газа, содержащий тетраизопропилат титана Ti[-OCH-(CH3)2]4 (кратко TTIP - от англ. titanium tetra-isopropoxide) и азот (транспортирующий газ), может быть направлен на поверхность подложки для создания и нанесения тонкопленочного подслоя оксида титана. Специалисты знают и понимают, что расположение устройств для нанесения покрытий может быть изменено. В примерах, не ограничивающих изобретение, оба устройства для нанесения подслоя могут быть установлены во флоат-ванне, как это было описано выше, либо одно устройство для нанесения подслоя может быть установлено во флоат-ванне, а другое устройство для нанесения подслоя может быть установлено ниже по движению ленты относительно первого устройства во флоат-ванне. Кроме того, оба устройства для нанесения подслоя могут быть установлены после флоат-ванны вниз по движению ленты. Из второго устройства для нанесения покрытия, расположенного ниже по движению ленты от первого устройства, может осуществляться пиролитическое осаждение тонкой пленки оксида олова, легированного фтором. Поток смешанных газов, содержащий монобутил олово трихлорид (C4H9SnCl3), трифторуксусную кислоту (CF3CO2H), воздух, водяной пар, кислород и азотную кислоту (HNO3 - окисляющая химическая присадка), может быть направлен на поверхность подслоя для создания и нанесения тонкой пленки оксида олова, легированного фтором. Как должно быть понятно специалистам, иногда требуется использовать растворитель для поддержания в растворе исходного материала, содержащего олово, для снижения летучести исходного материала, содержащего олово, а также для предотвращения реагирования друг с другом исходных материалов в газовой смеси. К хорошо известным растворителям для этой цели относятся низшие (С 1-С 5) диалкилкетоны, например ацетон, диэтилкетон, метилизобутилкетон и метилэтилкетон. Предпочтительным для использования низшим диалкилкетоном в соответствии с настоящим изобретением является метилизобутилкетон. В том случае, когда газы подаются по отдельности, в таких растворителях необходимости нет, но при желании они могут быть использованы. Газы в потоке смешанных газов могут быть включены в каждый из упомянутых выше исходных материалов, подаваемых со следующими расходами: 1) 0,20-2,00 кг/мин смеси, содержащей 70-95% монобутил оловотрихлорида, 5-20% трифторуксусной кислоты и 0-15% метилизобутилкетона; 2) 0,00-5,00 кг/мин водяного пара; 3) 0,00-2,00 кг/мин воздуха и 4) 0,10-2,50 кг/мин водного раствора 10-100% азотной кислоты. Предпочтительными диапазонами расхода для подачи исходных материалов являются: 1) 0,20-2,00 кг/мин смеси, содержащей 80-95% монобутил оловотрихлорида, 5-15% трифторуксусной кислоты и 0-15% метилизобутилкетона; 2) 0,00-2,5 кг/мин водяного пара; 3) 0,00-2,00 кг/мин воздуха и 4) 0,30-2,20 кг/мин водного раствора 20-100% азотной кислоты. В альтернативном варианте тонкая пленка оксида олова, легированного фтором, в соответствии с настоящим изобретением также может быть пиролитически осаждена с использованием следующих исходных веществ. Поток смешанных газов, содержащий монобутил трихлоридолова (C4H9SnCl3 или МВТС - от англ. monobutil tin trichloride), воздух, водяной пар, плавиковую кислоту (HF) и азотную кислоту (HNO3), может быть направлен на поверхность подслоя для создания и нанесения пленки оксида олова, легированного фтором. В этом варианте никакого растворителя не требуется. Газы в газовом потоке альтернативного варианта могут подаваться со следующими расходами: 1) 20-170 кг/ч МВТС; 2) 100-2000 кг/ч воздуха; 3) 0-30 кг/ч Н 2 О; 4) 10-50 кг/ч HF (2,5 мас.% водный раствор) и до 30 кг/ч HNO3(70 мас.% водный раствор). Введение иного, чем вода, воздух или кислород, окисляющего вещества может выполняться известными специалистам способами. В качестве частного примера введения окисляющего химического вещества может служить смешивание паров окисляющего химического вещества с пиролитическим паром до подачи в устройство нанесения оксида олова, легированного фтором. Авторы раскрытого здесь предмета изобретения обнаружили, что использование окисляющих химических добавок, помимо традиционных воды, воздуха или кислорода, в процессе пиролитического осаждения SnO2:F low-E тонкой пленки на стекло может привести к усилению отражения оптического и инфракрасного излучения low-E тонкой пленки. Таким образом, система low-E оптического покрытия с такими свойствами желательна для использования в оконных продуктах с одним или несколькими стеклами. Частным примером оконного продукта с несколькими стеклами может служить стеклопакет, например, показанный на фиг. 3 и 4. На фиг. 3 представлен двухслойный стеклопакет, включающий покрытие, представленное на фиг. 1. Блок 10 стеклопакета включает наружный стеклянный лист 20 и внутренний стеклянный лист 30, разделенные камерой 70, раму 50 и герметизирующий узел 60. Покрытие 40, показанное на фиг. 1, находится на внутренней поверхности наружного стеклянного листа 20. При желании, покрытие 40 также может быть нанесено на внутреннюю поверхность внутреннего стеклянного листа 30 (вместо наружного стеклянного листа 20). Low-E покрытие, предложенное в настоящем изобретении, может быть нанесено на любую обращенную внутрь поверхность наружного стеклянного листа 20 или внутреннего стеклянного листа 30. На фиг. 4 представлен двухслойный блок стеклопакета, включающий покрытие, показанное на фиг. 2. Блок 10 стеклопакета включает наружный стеклянный лист 20 и внутренний стеклянный лист 30, разделенные камерой 70, раму 50 и герметизирующий узел 60. Покрытие 40 в стеклопакете, показанном на фиг. 2, расположено на внутренней поверхности наружного стеклянного листа 20. При желании, покрытие 40 также может быть расположено на внутренней поверхности внутреннего стеклянного листа 30(вместо наружного стеклянного листа 20). Авторы изобретения обнаружили, что добавление окисляющего химического вещества, помимо традиционных воды, воздуха или кислорода, в онлайн процесс пиролитического осаждения пара при получении low-E тонких пленок оксида металла на стекле дает увеличение отражения инфракрасного излучения тонкой пленкой оксида металла. Раскрытые здесь способы онлайн нанесения тонких пленок оксида металла на стекло также применимы для получения тонких пленок оксида металла на стекле в офлайн технологии. Подобная адаптация к офлайн технологии должна быть понятна специалисту. Частными примерами подходящих окисляющих химических добавок могут служить кислород,озон, перекись водорода и другие перекиси, азотная кислота, нитрат аммония и другие нитраты, нитриты, закись азота, серная кислота, сульфаты и персульфаты, хлорноватистая кислота, хлораты, перхлораты, броматы и бораты. Согласно другой особенности настоящего изобретения представлен способ получения тонкой пленки оксида металла, позволяющей улучшить отражающие свойства нанесенной тонкой пленки оксида ме-6 025167 талла в оптическом и инфракрасном диапазонах. Для предложенной в настоящем изобретении тонкой пленки подслой желательно располагать под тонкой пленкой оксида металла так, чтобы подслой находился между подложкой и тонкой пленкой оксида металла. Подслой может служить нескольким целям. Подслой может предотвращать термическую диффузию содержащегося в подложке, т.е. в стекле, щелочного компонента в тонкую пленку, расположенную над подслоем. Кроме того, подслой может способствовать усилению связи подложки с тонкой пленкой настолько, что деградация характеристик тонкой пленки затруднена. Далее подслой также может обеспечивать получение нужного коэффициента преломления, действуя как слой, подавляющий цвета, возникающие при интерференции в тонкой пленке или подложке. Подслой в соответствии с настоящим изобретением может представлять собой одиночный тонкопленочный слой либо может быть многослойной структурой. Материалы, используемые для подслоя,предложенного в настоящем изобретении, хорошо известны специалистам. Частными примерами таких материалов являются оксиды, нитриды, карбиды, оксинитриды и оксикарбиды титана, кремния, олова,цинка, циркония, хрома, алюминия, индия, марганца, ванадия и их комбинации. Для предложенного в настоящем изобретении подслоя желательно использовать одиночный тонкопленочный слой, содержащий кремний. В более предпочтительном варианте в подслое используется тонкопленочный материал, содержащий кремний и кислород. Частным вариантом предпочтительного для использования подслоя может быть оксид кремния, диоксид кремния, нитрид кремния, оксинитрид кремния, карбид кремния, оксикарбид кремния и их комбинации. Представленный в настоящем раскрытии подслой представляет собой тонкую пленку оксикарбида кремния. Осаждение из паровой фазы слоев оксикарбида кремния хорошо известно в технологии тонкопленочных покрытий. Подслой оксикарбида кремния, используемый в настоящем изобретении, может быть получен пиролитическим осаждением из паровой фазы из исходных материалов, например силана (SiH4),углекислого газа (СО 2), этилена (С 2 Н 4) и азота (транспортирующий газ), при повышенных температурах,желательно в интервале 400-800 С. В наиболее предпочтительном варианте стеклянная подложка находится при повышенной температуре в интервале 650-750 С. Толщина подслоя в настоящем изобретении не имеет определенных ограничений. Предпочтительной толщиной является толщина в интервале 400-1000 . Более предпочтительным интервалом толщин тонкой пленки подслоя является 600-900 . Наиболее предпочтительным интервалом толщин тонкой пленки подслоя является 700-800 . Предложенные в настоящем изобретении подслои из оксикарбида кремния, имеющие толщину в указанных выше интервалах, могут обеспечить подавление радужных цветов, возникающих из-за пленки оксида олова. Область притязаний настоящего изобретения включает и другие исходные материалы, содержащие кремний. Другие хорошо известные исходные материалы, содержащие кремний, включают дисилан, трисилан, монохлорсилан, дихлорсилан, 1,2-диметилсилан, 1,1,2-триметилдисилан и 1,1,2,2-тетраметилдисилан, а также и другие. При использовании силанов в качестве исходных материалов обычно включают окисляющие материалы в газовый поток. В качестве окисляющих материалов могут использоваться углекислый газ, моноксид углерода и диоксид азота. При использовании силана в качестве исходного материала в газовый поток может быть добавлен ненасыщенный углеводородный газ, например этилен,ацетилен или толуол, для предотвращения вступления в реакцию исходного материала силана до того,как он достигнет поверхности подложки. При использовании дополнительного подслоя на основе титана в соответствии с настоящим изобретением содержащие титан исходные материалы, которые могут быть использованы, включают галоиды, например TiCl4, алкоксиды, например тетраэтилат титана, тетраизоропилат титана и тетрабутилат титана и -дикетоны, например (диизопропилат) бис-ацетилацетонат титана. Тетраизопропилат титана(Ti[-О-СН-(СН 3)2]4, или TTIP) обладает высокой летучестью и обычно используется. Пленка оксида олова, легированного фтором, в соответствии с настоящим изобретением может быть получена методами пиролитического осаждения, известными специалистам в области тонкопленочных технологий. В этих процессах для получения конечного продукта в виде low-E тонкой пленки оксида металла может быть использовано большое число известных исходных материалов и прекурсоров. Прекурсоры олова для тонкопленочных покрытий, полученных процессами пиролитического осаждения в соответствии с настоящим изобретением, известны и широко употребляются. Особенно пригоден для использования в качестве прекурсора олова монобутил оловотрихлорид. Это вещество хорошо известно и доступно, и обычно используется в качестве прекурсора олова для нанесения тонкопленочных покрытий с оловом на листовое стекло. Другие прекурсоры олова также могут быть использованы в пределах области притязаний настоящего изобретения. Другие хорошо известные прекурсоры олова включают, не ограничивая изобретение, диметил оловодихлорид, дибутил оловодихлорид, тетраметил олово,тетрабутил олово, диоктил олово дихлорид, дибутил оловодиацетат и оловотетрахлорид. Легирование фтором тонких пленок оксида олова также хорошо известно специалистам в области тонкопленочных покрытий. Для легирования содержащий фтор исходный материал может быть добавлен в газовый поток вместе с исходным материалом, содержащим олово. Частные примеры исходных материалов, содержащих фтор, включают газообразный фтор, фтористый водород, трехфтористый азот,трифторуксусную кислоту, бромтрифторметан, дифторэтан и хлордифторметан. Тонкопленочное покрытие оксида олова, легированного фтором, в соответствии с настоящим изобретением может быть получено при высоких температурах пиролитическим осаждением из газовой фазы из таких исходных материалов, как монобутил оловотрихлорид (C4H9SnCl3), трифторуксусная кислота(CF3CO2H), воздух, водяной пар и дополнительная окисляющая химическая добавка, иная, нежели вода,воздух или кислород. В предпочтительном варианте повышенные температуры для пиролитического осаждения из паровой фазы составляют 400-800 С. В более предпочтительном варианте повышенные температуры составляют 550-750 С. Толщина тонкопленочного покрытия оксида олова, легированного фтором, в соответствии с настоящим изобретением желательно составляет от 100 до 1000 нм. В более предпочтительном варианте толщина тонкопленочного покрытия оксида олова, легированного фтором, составляет 200-800 нм. В наиболее предпочтительном варианте толщина тонкопленочного покрытия оксида олова, легированного фтором, составляет 200-600 нм. Пример 1. От первого устройства для нанесения покрытия, размещенного внутри флоат-ванны, поток смеси газов, содержащий силан (SiH4), углекислый газ (СО 2), этилен (С 2 Н 4) и азот (N2 - транспортирующий газ), направлялся на нагретую поверхность стеклянной ленты. Газы потока смеси газов включали исходные материалы, подаваемые со следующими расходами: 1) силан (SiH4) 13,5 г/мин; 2) углекислый газ(СО 2) 100,0 г/мин; 3) этилен (С 2 Н 4) 50,0 г/мин и 4) азот (транспортирующий газ) 40,0 г/мин. От второго устройства для нанесения покрытия, расположенного ниже по движению ленты от первого устройства для нанесения покрытия, поток смеси газов, содержащий монобутил оловотрихлорид(C4H9SnCl3), трифторуксусную кислоту (CF3CO2H), воздух, водяной пар и азотную кислоту (HNO3 окисляющая химическая добавка), направлялся на поверхность подслоя. Газы потока смеси газов включали исходные материалы, подаваемые со следующими расходами: 1) 0,98 кг/мин смеси, содержащей 93% монобутилоловотрихлорида, 5% трифторуксусной кислоты и 2% метилизобутилкетона; 2) 0,85 кг/мин водяного пара; 3) 0,88 кг/мин воздуха; и 4) 0,78 кг/мин водного раствора 67,2% азотной кислоты. Пример 2. От первого устройства для нанесения покрытия, размещенного внутри флоат-ванны, поток смеси газов, содержащий силан (SiH4, углекислый газ (СО 2), этилен (С 2 Н 4) и азот (N2 - транспортирующий газ),направлялся на нагретую поверхность стеклянной ленты. Газы потока смеси газов включали исходные материалы, подаваемые со следующими расходами: 1) силан (SiH4) 13,5 г/мин; 2) углекислый газ (СО 2) 100,0 г/мин; 3) этилен (С 2 Н 4) 50,0 г/мин и 4) азот (транспортирующий газ) 40,0 г/мин. От второго устройства для нанесения покрытия, расположенного ниже по движению ленты от первого устройства для нанесения покрытия, поток смеси газов, содержащий монобутилоловотрихлорид(C4H9SnCl3), трифторуксусную кислоту (CF3CO2H), воздух, водяной пар и азотную кислоту (HNO3 окисляющая химическая добавка), направлялся на поверхность подслоя. Газы потока смеси газов включали исходные материалы, подаваемые со следующими расходами: 1) 0,81 кг/мин смеси, содержащей 81% монобутилоловотрихлорида, 15% трифторуксусной кислоты и 4% метилизобутилкетона; 2) 0,80 кг/мин водяного пара; 3) 1,62 кг/мин воздуха и 4) 0,34 кг/мин водного раствора 67,2% азотной кислоты. Тонкие пленки оксида олова, легированного фтором, полученные способами в соответствии с настоящим изобретением, обладают увеличенным отражением оптического и инфракрасного излучения по сравнению с тонкими пленками оксида олова, легированного фтором, полученными пиролитическим осаждением в отсутствие окисляющей химической добавки, например азотной кислоты. Характеристики отражения видимого и инфракрасного излучения оксидов олова, легированных фтором, полученных способами в соответствии с настоящим изобретением, рассмотрены ниже. Следует заметить, что описанные выше способы, представляющие изобретение, являются частными примерами способов получения описанных ниже образцов, предложенных в изобретении. В табл.1 приведены характеристики отражения оптического и инфракрасного излучения предложенного в изобретении образца Е 2+ в сравнении с контрольным образцом Е 2. Оба образца были нанесены на флоат-стекле толщиной 3,2 мм. Таблица 1 Характеристики отражения оптического и инфракрасного излучения low-E покрытий Е 2+ и Е 2 на одинарном стекле толщиной 3,2 мм Для приведенных в табл. 1 данных можно отметить, что нанесенные тонкопленочные покрытия оксида олова, легированного фтором, как в полученном в соответствии с изобретением образце Е 2+, так и в контрольном образце Е 2, были получены с использованием одних и тех же исходных материалов и усло-8 025167 вий осаждения, и единственное отличие состояло в добавлении окисляющей химической добавки, в данном случае азотной кислоты, к потоку смеси газов исходных материалов для предложенного в изобретении образца Е 2+. В предложенном в изобретении образце Е 2+ получена величина излучательной способности на 0,09 меньше, чем в контрольном образце Е 2. Излучательные способности обоих образцов были измерены измерителем коэффициента излучения, прибором, хорошо известным специалистам. Добавление окисляющей химической добавки, например азотной кислоты, в поток смеси газов исходных материалов для получения тонкой пленки SnO2:F предложенного в изобретении образца Е 2+ может иметь неожиданно сильное влияние на излучательную способность тонкопленочного покрытия. У предложенного в изобретении образца наблюдается более низкое поверхностное сопротивление (Rs), приблизительно на 10,0 по сравнению с контрольным образцом Е 2. Поверхностные удельные сопротивления для обоих образцов были измерены посредством 4-зондового измерителя поверхностных сопротивлений, прибора, хорошо известного специалистам. Для целей архитектуры и эстетики зданий поверхностное сопротивление позволяет оценить, насколько хорошо слой или система слоев отражает инфракрасную энергию и поэтому часто используется, наряду с излучательной способностью как показатель этой характеристики. Таким образом, как излучательная способность, так и поверхностное сопротивление оказались ниже для полученного посредством изобретения образца Е 2+ по сравнению с контрольным образцом Е 2, показывая тем самым, что введение окисляющей химической добавки, например азотной кислоты, в поток смеси газов в процессе осаждения тонких пленок SnO2:F позволяет получить тонкопленочное покрытие с неожиданно улучшенными характеристиками отражения ИК излучения, т.е. тонкопленочное покрытие Е 2+. Также наблюдаются, в целом, одинаковые значения матовости для обоих образцов - полученного с помощью изобретения Е 2+ и контрольного Е 2. Это показывает, что введение окисляющей химической добавки в поток смеси газов исходных материалов для SnO2:F при получении Е 2+ в целом не влияет на способность результирующего покрытия рассеивать свет. Также наблюдается значительное различие в толщине SnO2:F тонких пленок. В полученном посредством изобретения образце Е 2+ толщина тонкой пленки составляет 430 нм. В контрольном образце Е 2 наблюдаемая толщина тонкой пленки составляет 280 нм. Как было показано выше, осаждение тонкопленочного покрытия SnO2:F для полученного в изобретении образца Е 2+ и контрольного образца Е 2 выполнялось, в целом, с использованием одних и тех же исходных материалов, и их количества, а также условий осаждения, и единственным отличием было добавление окисляющей химической добавки, в данном случае азотной кислоты, в поток смеси газов исходных материалов при получении образца Е 2+. Видно, что толщина тонкой пленки SnO2:F для Е 2+(430 нм) значительно выше, чем толщина тонкой пленки SnO2:F для Е 2 (280 нм). Таким образом, оказалось, что использование окисляющей химической добавки, например азотной кислоты, может значительно повысить эффективность покрытия по сравнению с осаждением тонкой пленки SnO2:F. Данные толщин тонких пленок, приведенные в табл. 1, демонстрируют увеличение толщины тонкой пленки приблизительно на 150 нм. Это соответствует повышению эффективности нанесения тонкой пленки более 50% (примерно 55%). Другими словами, способами, предложенными в изобретении для получения образца Е 2+, примерно 55% увеличение толщины тонкой пленки SnO2:F может быть достигнуто добавлением азотной кислоты в поток смеси газов исходных материалов. Это повышение эффективности покрытия достигается без необходимости увеличения количества исходных материалов и обеспечивает снижение производственных затрат при получении тонкопленочных покрытий в соответствии с настоящим изобретением. В табл. 2 приведены характеристики отражения оптического и инфракрасного излучения для стеклопакетов, в которых используются полученные в изобретении образцы Е 2+ и контрольные образцы Е 2. Для сравнения также включены данные стеклопакетов, в которых используются тонкие пленки "EnergyAmerica, Inc. из Альфаретта, шт. Джорджия, и представляет собой стекло с low-E покрытием. В системеAdvantage" (EA) производится компанией Pilkington, Inc. из Мерсейсайд, Англия, и представляет собой стекло с low-E покрытием. В системе ЕА для слоев, отражающих инфракрасное излучение, используется Таблица 2 Характеристики отражения оптического и инфракрасного покрытий Е 2+ и Е 2, ЕА и Ti-PS,использованных в стеклопакетах Содержащиеся в табл. 2 данные представляют предложенное в изобретении, контрольное и использованные для сравнения low-E тонкопленочные покрытия на стекле, использованные в стеклопакетах с двумя стеклами, имеющими толщину 3,2 мм и установленными с промежутком 12 мм. Промежуток заполнен либо воздухом, либо аргоном, как указано в таблице. Кроме того, описанные здесь предложенные в изобретении и контрольные покрытия расположены на третьей поверхности стекла, от которой отражается наружный свет. Более низкие U values (коэффициенты теплопередачи) наблюдаются у тонких пленок Е 2+ по сравнению с контрольными тонкими пленками Е 2 при использовании в стеклопакетах с воздухом или аргоном между двумя листами стекла. Когда между двумя листами стекла находится воздух, разница в U value составляет 0,016 или 4,6% между стеклопакетами с Е 2+ и Е 2. Если промежуток между листами стекла заполнен аргоном, эта разница составляет 0,020 или 6,6%. В предложенных в изобретении тонких пленках Е 2+ также имеют место более низкие значения коэффициента солнечного теплопритока и T-vis (пропускание видимого излучения) по сравнению с контрольными тонкими пленками Е 2 при установке их в стеклопакеты, заполненные либо воздухом, либо аргоном. Из трех продуктов, упомянутых в табл. 2, которые нанесены пиролитическим осаждением тонких пленок SnO2:F, образец Е 2+, полученный способом, предложенном в изобретении, имеет более низкую излучательную способность, более низкий коэффициент теплопередачи, более низкий коэффициент солнечного теплопритока и более низкое пропускание видимого света по сравнению с контрольным образцом Е 2 и образцом ЕА сравнения. Образец Ti-PS,представляющий собой стекло с low-E покрытием на основе серебра, имеет лучшие характеристики отражения инфракрасного излучения (излучательная способность, коэффициент теплопередачи и коэффициент солнечного теплопритока), чем Е 2+. Кроме того, Ti-PS имеет лучшие характеристики отражения ИК излучения, чем Е 2 и ЕА. Таким образом, введение окисляющей химической добавки, например азотной кислоты, в поток смеси газов во время нанесения тонких пленок SnO2:F в соответствии с настоящим изобретением обеспечивает повышение отражения инфракрасного излучения по меньшей мере на 4%, когда такие предложенные в изобретении тонкие пленки SnO2:F вводятся в стеклопакеты, включающие два стекла. Такое увеличение отражения инфракрасного излучения делает low-E покрытия на основе SnO2:F конкурентоспособными с обычными low-E тонкопленочными покрытиями на основе Ag с точки зрения эксплуатационных характеристик. Более того, предложенные в изобретении тонкие пленки и способы получения обеспечивают существенное увеличение эффективности покрытия по сравнению с обычным пиролитическим осаждением SnO2:F. Такое увеличение в эффективности покрытия делает low-E покрытия на основе SnO2:F конкурентоспособными по сравнению с обычными low-E тонкопленочными покрытиями на основе серебра также и с точки зрения стоимости. В технологии нанесения тонкопленочных покрытий хорошо известно, что более высокая эффективность покрытия позволяет нанести тонкие пленки с большей толщиной слоя. Более толстые слои тонких пленок, в свою очередь, приводят к более низкой излучательной способности тонкой пленки. Таким образом, эффективность покрытия, увеличенная за счет введения окисляющей химической добавки, например азотной кислоты, может также обеспечить улучшенные характеристики отражения инфракрасного излучения. Пример 3. От первого устройства для нанесения покрытия, размещенного внутри флоат-ванны, поток смеси газов, содержащий силан (SiH4), углекислый газ (СО 2), этилен (С 2 Н 4) и азот (N2 - транспортирующий газ), направлялся на нагретую поверхность стеклянной ленты. Газы потока смеси газов включали исходные материалы, подаваемые со следующими расходами: 1) силан (SiH4) 1,2 кг/ч; 2) углекислый газ (СО 2) 14 кг/ч; 3) этилен (С 2 Н 4) 2 кг/ч и 4) азот (транспортирующий газ) 1,6 кг/ч. От второго устройства для нанесения покрытия, расположенного ниже по движению ленты от первого устройства для нанесения покрытия, поток смеси газов, содержащий монобутилоловотрихлорид(C4H9SnCl3 или МВТС), фтористо-водородную кислоту (HF), воздух и водяной пар, направлялся на поверхность подслоя. Газы потока смеси газов включали исходные материалы, подаваемые со следующими расходами: 1) 93,5 кг/ч монобутилоловотрихлорида; 2) 1160 кг/ч воздуха; 3) 8,4 кг/ч воды и 4) 22,5 кг/ч водного раствора 2,5 мас.% HF. Пример 3+. От первого устройства для нанесения покрытия, размещенного внутри флоат-ванны, поток смеси газов, содержащий силан (SiH4), углекислый газ (СО 2), этилен (С 2 Н 4) и азот (N2 - транспортирующий газ), направлялся на нагретую поверхность стеклянной ленты. Газы потока смеси газов включали исходные материалы, подаваемые со следующими расходами: 1) силан (SiH4) 1,2 кг/ч; 2) углекислый газ (СО 2) 14 кг/ч; 3) этилен (С 2 Н 4) 2 кг/ч и 4) азот (транспортирующий газ) 1,6 кг/ч. От второго устройства для нанесения покрытия, расположенного ниже по движению ленты от первого устройства для нанесения покрытия, поток смеси газов, содержащий монобутилоловотрихлорид(C4H9SnCl3 или МВТС), фтористо-водородную кислоту (HF), азотную кислоту (HNO3), воздух и водяной пар, направлялся на поверхность подслоя. Газы потока смеси газов включали исходные материалы, подаваемые со следующими расходами: 1) 85,0 кг/ч монобутилоловотрихлорида; 2) 1160 кг/ч воздуха; 3) 4,3 кг/ч воды; 4) 22,5 кг/ч водного раствора 2,5 мас.% HF и 5) 10,5 кг/ч водного раствора 70 мас.% HNO3. Тонкие пленки оксида олова, легированного фтором, полученные способами в соответствии с настоящим изобретением, при сравнимой толщине демонстрируют улучшенные оптические свойства при тех же характеристиках отражения инфракрасного излучения. Некоторые оптические характеристики приведены ниже в табл. 3. Таблица 3 Оптические и ИК характеристики отражения для low-E покрытий из примеров 3+ и 3 на одиночных листах известково-натриевого стекла толщиной 3,85 мм Источник освещения типа D65, в телесном угле 2.В соответствии со стандартом ISO 9050 (2003). Из таблицы видно, что при введении HNO3 (пример 3+) увеличился коэффициент затенения и уменьшилась матовость по сравнению с примером 3, где азотная кислота не использовалась. Кроме того,увеличились пропускание света и коэффициент затенения. Пример 4. От первого устройства для нанесения покрытия, размещенного внутри флоат-ванны, поток смеси газов, содержащий тетраизопропилат титана (Ti[-O-СН-(СН 3)2]4 или TTIP) и азот (N2 - транспортирующий газ), направлялся на нагретую поверхность стеклянной ленты. Газы потока смеси газов включали исходные материалы, подаваемые со следующими расходами: 1) TTIP 1,85 кг/ч и 2) азот (транспортирующий газ) 150 кг/ч. От первого устройства для нанесения покрытия, размещенного внутри флоат-ванны ниже по движению ленты от устройства нанесения предварительного покрытия TiO2, поток смеси газов, содержащий силан (SiH4), воздух, этилен (С 2 Н 4) и азот (N2 - транспортирующий газ), направлялся на нагретую поверхность стеклянной ленты. Газы потока смеси газов включали исходные материалы, подаваемые со следующими расходами: 1) силан (SiH4) 0,75 кг/ч; 2) воздух 96 кг/ч; 3) этилен (С 2 Н 4) 1,0 кг/ч и 4) азот(транспортирующий газ) 101 кг/ч. От второго устройства для нанесения покрытия, расположенного ниже по движению ленты от первого устройства для нанесения покрытия, поток смеси газов, содержащий монобутилоловотрихлорид(C4H9SnCl3 или МВТС), фтористо-водородную кислоту (HF), азотную кислоту (HNO3), воздух и водяной пар, направлялся на поверхность подслоя. Газы потока смеси газов включали исходные материалы, подаваемые со следующими расходами: 1) 98,6 кг/ч МВТС; 2) 970 кг/ч воздуха; 3) 9,1 кг/ч воды и 4) 25,6 кг/ч водного раствора 2,5 мас.% HF. Пример 4+. От устройства для нанесения предварительного покрытия, размещенного внутри флоат-ванны, поток смеси газов, содержащий тетраизопропилат титана (Ti[-О-СН-(СН 3)2]4 или TTIP) и азот (N2 - транспортирующий газ), направлялся на нагретую поверхность стеклянной ленты. Газы потока смеси газов включали исходные материалы, подаваемые со следующими расходами: 1) TTIP 1,85 кг/ч и 2) азот(транспортирующий газ) 150 кг/ч. От первого устройства для нанесения покрытия, размещенного внутри флоат-ванны ниже по движению ленты от устройства для нанесения предварительного покрытия TiO2, поток смеси газов, содержащий силан (SiH4), воздух, этилен (С 2 Н 4) и азот (N2 - транспортирующий газ), направлялся на нагретую поверхность стеклянной ленты. Газы потока смеси газов включали исходные материалы, подаваемые со следующими расходами: 1) силан (SiH4) 0,75 кг/ч; 2) этилен (С 2 Н 4) 1,0 кг/ч и 3) азот (транспортирующий газ) 101 кг/ч. От второго устройства для нанесения покрытия, расположенного ниже по движению ленты от первого устройства для нанесения покрытия, поток смеси газов, содержащий монобутилоловотрихлорид(C4H9SnCl3 или МВТС), фтористо-водородную кислоту (HF), азотную кислоту (HNO3), воздух и водяной пар, направлялся на поверхность подслоя. Газы потока смеси газов включали исходные материалы, подаваемые со следующими расходами: 1) 85,0 кг/ч МВТС; 2) 970 кг/ч воздуха; 3) 4,9 кг/ч воды и 4) 25,6 кг/ч водного раствора 2,5 мас.% HF и 5) 14 кг/ч HNO3. Тонкие пленки оксида олова, легированного фтором, полученные способами в соответствии с настоящим изобретением, при сравнимой толщине демонстрируют улучшенные оптические свойства при тех же характеристиках отражения инфракрасного излучения. Результаты измерений оптических характеристик приведены ниже в табл. 4. Таблица 4 Оптические и ИК характеристики отражения для Low-E покрытий из примеров 4+ и 4 на одиночных листах известково-натриевого стекла толщиной 3,85 мм Источник освещения типа D65, в телесном угле 2.В соответствии со стандартом ISO 9050 (2003). Здесь также видно, что при введении HNO3 (пример 4+) увеличился коэффициент затенения и уменьшилась матовость по сравнению с примером 4, где HNO3 не использовалась. Кроме того, увеличились пропускание света и коэффициент затенения. В то время как настоящее изобретение было описано применительно к частным вариантам осуществления, оно не сводится к приведенным конкретным деталям, но включает различные изменения и модификации, которые могут представить себе специалисты и которые попадают в область притязаний изобретения, определяемую следующей далее формулой. ФОРМУЛА ИЗОБРЕТЕНИЯ 1. Способ изготовления продукта с покрытием, включающим оптическую пленку, в котором: а) подготавливают подложку; б) осаждают первое покрытие оптической пленки по меньшей мере на часть подложки в онлайн режиме из положения в онлайн процессе для первого покрытия, причем это первое покрытие содержит кремний; в) осаждают второе покрытие, содержащее оксид олова, легированный фтором, по меньшей мере на часть первого покрытия, причем второе покрытие осаждают при температуре в интервале 400-800 С из газового потока, содержащего окисляющее вещество, которое выбирают из группы, состоящей из перекисей, азотной кислоты, нитратов, нитритов, закиси азота, серной кислоты, сульфатов, персульфатов,хлорноватистой кислоты, хлоратов, перхлоратов, броматов, боратов и их комбинаций. 2. Способ по п.1, в котором в качестве подложки используют стеклянную подложку. 3. Способ по п.1, в котором первое покрытие содержит кремний в форме оксида, нитрида или карбида или их комбинаций. 4. Способ по п.1, в котором первое покрытие содержит материал, выбранный из группы, состоящей из оксида кремния, диоксида кремния, нитрида кремния, оксинитрида кремния, карбида кремния или оксикарбида кремния или их комбинаций. 5. Способ по п.1, в котором первое покрытие содержит оксикарбид кремния. 6. Способ по п.1, в котором окисляющее вещество выбирают из группы, состоящей из азотной кислоты, закиси азота, хлорноватистой кислоты и серной кислоты и их комбинаций. 7. Способ по п.1, в котором в качестве окисляющего вещества используют азотную кислоту. 8. Способ по п.1, в котором второе покрытие осаждают при температуре в интервале 550-750 С. 9. Способ по п.1, в котором первое покрытие содержит единичный слой оптический пленки. 10. Способ по п.1, в котором первое покрытие содержит несколько слоев оптической пленки. 11. Способ по п.1, в котором первое покрытие осаждают при температуре в интервале 400-800 С. 12. Способ по п.1, в котором первое покрытие осаждают при температуре в интервале 650-750 С. 13. Способ изготовления продукта с покрытием, в котором: а) подготавливают подложку; б) осаждают предварительное покрытие покрытия оптической пленки по меньшей мере на часть подложки в онлайн режиме из положения в онлайн процессе для предварительного покрытия; в) осаждают первое покрытие покрытия оптической пленки по меньшей мере на часть предвари- 12025167 тельного покрытия в онлайн режиме из положения в онлайн процессе для первого покрытия, причем это первое покрытие содержит кремний; г) осаждают второе покрытие покрытия оптической пленки, содержащее оксид олова, легированный фтором, по меньшей мере на часть первого покрытия в онлайн режиме из положения в онлайн процессе для второго покрытия,причем второе покрытие осаждают из газового потока, содержащего окисляющее вещество, которое выбирают из группы, состоящей из перекисей, азотной кислоты, нитратов, нитритов, закиси азота,серной кислоты, сульфатов, персульфатов, хлорноватистой кислоты, хлоратов, перхлоратов, броматов,боратов и их комбинаций, и при температуре в интервале 400-800 С. 14. Способ по п.13, в котором предварительное покрытие содержит материал, выбранный из группы, состоящей из оксида титана, нитрида титана, карбида или оксикарбида титана или их комбинаций. 15. Способ по п.13, в котором предварительное покрытие содержит диоксид титана.
МПК / Метки
МПК: B32B 17/06
Метки: изготовления, покрытие, способ, тонкопленочное
Код ссылки
<a href="https://eas.patents.su/15-25167-tonkoplenochnoe-pokrytie-i-sposob-ego-izgotovleniya.html" rel="bookmark" title="База патентов Евразийского Союза">Тонкопленочное покрытие и способ его изготовления</a>
Предыдущий патент: Производные пиридина
Следующий патент: Самогерметизирующаяся композиция для пневматического изделия
Случайный патент: Препарат 2-метилтиенобензодиазепина