Способ получения производного бензимидазола
Формула / Реферат
1. Способ получения соединения формулы

необязательно в форме его солей присоединения с кислотой,
отличающийся тем, что на первой стадии диамин формулы 2
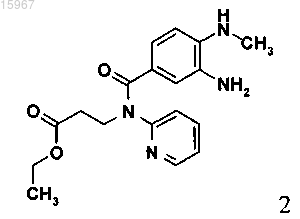
вводят в реакцию с карбоновой кислотой 3
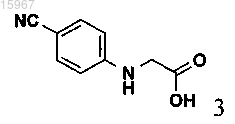
в присутствии подходящего реагента сочетания с образованием соединения формулы 4
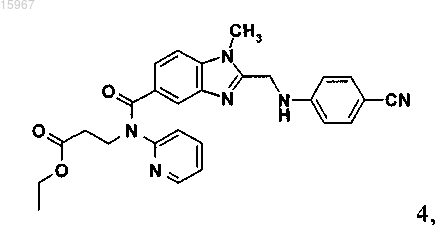
которое без выделения превращают в гидробромид формулы 4-Br
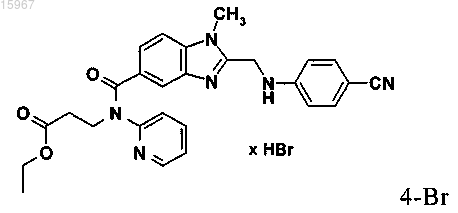
который затем превращают в амидин формулы 1.
2. Способ по п.1, отличающийся тем, что реакцию 2 с 3 проводят в растворителе, который выбран из группы, включающей метиленхлорид, диметилформамид, бензол, толуол, хлорбензол, тетрагидрофуран, диоксан и их смеси.
3. Способ по п.1 или 2, отличающийся тем, что реагент сочетания выбран из группы, включающей N,N'-дициклогексилкарбодиимид, N,N'-карбонилдиимидазол и карбонилди-(1,2,4-триазол).
4. Способ по одному из пп.1-3, отличающийся тем, что для получения соединения формулы 4 прибавляют уксусную кислоту.
5. Способ по одному из пп.1-4, отличающийся тем, что соединение формулы 4-Br получают из соединения формулы 4 путем прибавления водного раствора бромисто-водородной кислоты.
6. Способ по одному из пп.1-5 получения соединения формулы 1 в виде его соли присоединения с п-толуолсульфоновой кислотой, отличающийся тем, что превращение соединения формулы 4-Br в амидин формулы 1 в форме его соли присоединения п-толуолсульфоновой кислотой проводят путем прибавления соединения формулы 4-Br к содержащему кислоту спирту с прибавлением п-толуолсульфоновой кислоты и последующим прибавлением раствора аммиака.
7. Способ по п.6, отличающийся тем, что полное количество п-толуолсульфоновой кислоты прибавляют в начале реакции соединения формулы 4-Br с помощью содержащего кислоту спирта.
8. Способ по одному из пп.6 или 7, отличающийся тем, что содержащий кислоту спирт представляет собой содержащий хлористо-водородную кислоту этанол.
9. Соединение формулы 4-Br
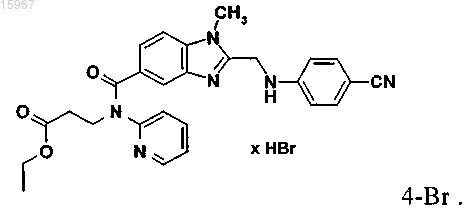
Текст
ОПИСАНИЕ ИЗОБРЕТЕНИЯ К ЕВРАЗИЙСКОМУ ПАТЕНТУ Дата публикации и выдачи патента СПОСОБ ПОЛУЧЕНИЯ ПРОИЗВОДНОГО БЕНЗИМИДАЗОЛА В изобретении описан способ получения соединения формулы 1 ценного промежуточного продукта для синтеза фармацевтически активного вещества дабигатран этексилата.(71)(73) Заявитель и патентовладелец: БРИНГЕР ИНГЕЛЬХАЙМ ИНТЕРНАЦИОНАЛЬ ГМБХ (DE) 015967 Настоящее изобретение относится к способу получения соединения формулы 1 ценного промежуточного продукта для синтеза фармацевтически активного вещества дабигатран этексилата. Уровень техники Дабигатран этексилат известен в предшествующем уровне техники и впервые был раскрыт в заявкеWO 98/37075. Способы получения дабигатран этексилата также описаны в WO 2006/000353 и в публикации Hauel et al. (J. Med. Chem., 2002, 45, 1757 ff). Как показано в WO 2006/000353, соединение формулы 1 является весьма важным промежуточным продуктом для синтеза дабигатран этексилата. В основу настоящего изобретения была положена задача разработки способа, который обеспечивает улучшенный крупномасштабный промышленный синтез соединения формулы 1. Подробное описание изобретения Настоящее изобретение относится к способу крупномасштабного промышленного синтеза соединения формулы необязательно в форме его солей присоединения с кислотой, предпочтительно в форме его соли с паратолуолсульфоновой кислотой,отличающемуся тем, что на первой стадии диамин формулы 2 в присутствии подходящего реагента сочетания с образованием соединения формулы 4 которое без выделения превращают в гидробромид формулы 4-Br который в конечном счете превращают в амидин формулы 1.-1 015967 Для реакции соединения формулы 2 с образованием соединения формулы 4 в контексте настоящего изобретения предпочтительно используют следующую методику. Соединение формулы 2 сначала растворяют в подходящем растворителе. Подходящими растворителями в контексте настоящего изобретения предпочтительно являются растворители, выбранные из группы, включающей метиленхлорид, диметилформамид, бензол, толуол, хлорбензол, тетрагидрофуран,диоксан и их смеси, из которых диметилформамид и тетрагидрофуран являются предпочтительными. В контексте настоящего изобретения на этой стадии в качестве растворителя особенно предпочтительно использовать тетрагидрофуран. Предпочтительно 0,5-1 л, особенно предпочтительно 0,65-0,85 л, более предпочтительно 0,7-0,8 л указанного выше растворителя используют на 1 моль применяющегося соединения формулы 2. Кроме указанного выше раствора также готовят другой раствор, который содержит карбоновую кислоту формулы 3, а также указанный выше реагент сочетания. Для этого в контексте настоящего изобретения реагент сочетания предпочтительно сначала растворяют в растворителе, который предпочтительно выбран из группы растворителей, указанной выше. Предпочтительно используют тот же растворитель,который используют для растворения соединения формулы 2. Реагент сочетания предпочтительно выбран из группы, включающей N,N'-дициклогексилкарбодиимид, N,N'-карбонилдиимидазол и карбонилди-(1,2,4-триазол) и N,N'-карбонилдиимидазол и карбонилди-(1,2,4-триазол), предпочтительно карбонилди-(1,2,4-триазол), являются особенно важными в контексте настоящего изобретения. Предпочтительно 1-2 моль, особенно предпочтительно 1-1,5 моль, более предпочтительно 1,05-1,25 моль указанного выше реагента сочетания используют на 1 моль применяющегося соединения формулы 2. Для растворения реагента сочетания в указанном выше растворителе предпочтительно используют 1-3 л, особенно предпочтительно 1,5-2,5 л, более предпочтительно 1,8-2,2 л указанного выше растворителя на 1 моль применяющегося соединения формулы 2. Приготовленный таким образом раствор реагента сочетания или перемешивают при температуре окружающей среды, или нагревают при перемешивании до температуры, равной примерно 25-50C,предпочтительно 30-40C, особенно предпочтительно 32-38C и затем объединяют с соединением формулы 3. Прибавление соединения формулы 3 предпочтительно проводят порциями в течение от 0,25 до 4 ч, предпочтительно в течение от 0,5 до 3 ч, особенно предпочтительно в течение от 1 до 2 ч. Прибавление соединения 3 предпочтительно проводят с помощью имеющегося раствора при постоянной температуре. Предпочтительно 1-2 моль, особенно предпочтительно 1-1,5 моль, более предпочтительно 1,05-1,15 моль указанного выше соединения формулы 3 используют на 1 моль применяющегося соединения формулы 2. После прибавления соединения формулы 3 полученный таким образом раствор реагента сочетания и 3 необязательно перемешивают в течение еще 0,25 до 4 ч, предпочтительно в течение от 0,5 до 3 ч,особенно предпочтительно в течение от 0,5 до 1 ч. В течение этого времени температуру раствора предпочтительно поддерживают в одном из указанных выше температурных диапазонов и особенно предпочтительно, если температуру поддерживают постоянной. Полученный таким образом раствор затем прибавляют к уже приготовленному раствору соединения формулы 2. Описанный выше раствор соединения 2 предпочтительно предварительно нагревают при перемешивании до температуры в диапазоне примерно 30-65C, предпочтительно 40-60C, особенно предпочтительно 47-53C. Полученный раствор реагента сочетания и соединения 3 предпочтительно прибавляют к раствору соединения 2 в течение 0,5-5 ч, предпочтительно 1-4 ч, особенно предпочтительно 2-3 ч. В течение этого времени температуру имеющегося раствора соединения 2 предпочтительно поддерживают постоянной. После завершения прибавления раствора, приготовленного из соединения 3 и реагента сочетания необязательно может быть полезным дополнительное разбавление реакционного раствора путем прибавления растворителя. Если дополнительно прибавляют растворитель, предпочтительно используют один из указанных выше растворителей, а особенно предпочтительно использовать растворитель, который уже использован для приготовления раствора соединения 2. Если раствор дополнительно разбавляют, то предпочтительно используют 0,1-0,5 л, особенно предпочтительно 0,2-0,3 л указанного выше растворителя на 1 моль применяющегося соединения формулы 2. После завершения прибавления раствора, приготовленного из соединения 3, и завершения прибавления реагента сочетания и любого дополнительного растворителя полученный раствор перемешивают в течение еще не менее от 1 до 8 ч, предпочтительно не менее от 2 до 7 ч, особенно предпочтительно не менее от 3 до 6 ч. Температуру раствора предпочтительно поддерживают в одном из указанных выше температурных диапазонов и особенно предпочтительно, если температуру поддерживают постоянной. Затем большие количества растворителя необязательно отгоняют при пониженном давлении. Особенно предпочтительно, если на 1 моль применяющегося соединения 2 путем отгонки удаляют 1-1,8 л,более предпочтительно 1,2-1,7 л, еще более предпочтительно 1,4-1,5 л указанного выше растворителя. Отгонку растворителя предпочтительно проводят при температуре в диапазоне примерно 40-65C,-2 015967 особенно предпочтительно в диапазоне 50-60C. Если невозможно отогнать растворитель при нормальном давлении в этом температурном диапазоне вследствие выбора растворителя, давление снижают, пока не произойдет эффективная отгонка в указанном температурном диапазоне. Необязательно может быть полезным захват остаточных количеств использующегося в начале растворителя, которые содержатся в остатке после отгонки, путем прибавления другого растворителя. Если,например, в качестве растворителя для описанной выше реакции используют тетрагидрофуран, то установлено, что целесообразно использовать н-бутилацетат. Если на этой стадии используют н-бутилацетат,то его отгоняют вместе с тетрагидрофураном при пониженном давлении при температуре, равной примерно 50-85C. Отгонку проводят так, чтобы использованный ранее тетрагидрофуран удалялся почти полностью и в качестве растворителя оставался только н-бутилацетат. После завершения отгонки оставшийся раствор объединяют с уксусной кислотой. На этой стадии предпочтительно используют концентрированную уксусную кислоту, предпочтительно ледяную уксусную кислоту (примерно 99% уксусную кислоту). Предпочтительно, если на 1 моль применяющегося соединения формулы 2 используют 100-200 г,особенно предпочтительно 120-170 г, более предпочтительно 130-145 г указанной выше концентрированной уксусной кислоты. Затем смесь нагревают при перемешивании до температуры в диапазоне примерно 65-100C, предпочтительно 75-95C, особенно предпочтительно 85-90C и перемешивают в течение не менее 0,5-5 ч,предпочтительно 1-4 ч, особенно предпочтительно 2-3 ч при постоянной температуре. Затем температуру смеси предпочтительно доводят до значения, находящегося в диапазоне примерно 45-85C, предпочтительно 55-80C, особенно предпочтительно 65-75C и ее смешивают с водой для последующей обработки. Особенно предпочтительно, если на 1 моль применяющегося соединения формулы 2 прибавляют 0,5-2 л, особенно предпочтительно 0,75-1,5 л, более предпочтительно 0,9-1,1 л воды. Кроме воды также необязательно прибавляют водный раствор NaCl. Если также прибавляют NaCl,то предпочтительно используют 20-80 г, особенно предпочтительно 30-60 г, более предпочтительно 4050 г NaCl на 1 моль применяющегося соединения формулы 2. Полученную таким образом смесь фаз тщательно перемешивают и водную фазу отделяют по обычным методикам. Отделенную фазу необязательно повторно экстрагируют использующимся ранее органическим растворителем. Растворитель удаляют из органических фаз путем отгонки при пониженном давлении. Отгонку растворителя предпочтительно проводят при температуре в диапазоне ниже 80C, предпочтительно примерно при 60-80C, особенно предпочтительно при 70-80C. Если невозможно отогнать растворитель в этом температурном диапазоне при нормальном давлении вследствие выбора растворителя, давление снижают, пока не произойдет эффективная отгонка в указанном температурном диапазоне. Остаток после отгонки содержит соединение формулы 4, которое в контексте настоящего изобретения без выделения дополнительно вводят в реакцию по методике, описанной ниже, и получают соединение формулы 4-Br. Остаток после отгонки объединяют со спиртом, предпочтительно с этанолом или изопропанолом,особенно предпочтительно изопропанолом, и необязательно немного нагревают. Предпочтительно, если на 1 моль применяющегося соединения формулы 2 используют 0,5-3 л, особенно предпочтительно 1-2,5 л, более предпочтительно 1,5-2 л указанного выше спирта. Если полученную смесь нагревают, то выбирают температуру, предпочтительно равную примерно 25-50C, более предпочтительно 30-40C, особенно предпочтительно 32-38C. Затем прибавляют водный раствор бромисто-водородной кислоты. Особенно предпочтительно использовать концентрированный водный раствор бромисто-водородной кислоты. Например, можно использовать 48% водный раствор бромисто-водородной кислоты. При перемешивании при постоянной температуре прибавляют достаточное количество бромисто-водородной кислоты, пока значение рН полученной смеси не станет равным менее 3, предпочтительно менее 2 и особенно предпочтительно, если оно будет находиться в диапазоне 0,6-1,3. При использовании 48% бромисто-водородной кислоты, указанной выше в качестве примера, на 1 моль применяющегося соединения формулы 2 можно прибавить 0,1-0,3 кг, предпочтительно 0,15-0,25 кг,особенно предпочтительно 0,17-0,21 кг бромисто-водородной кислоты (48%). После завершения прибавления бромисто-водородной кислоты полученную смесь перемешивают в течение еще не менее от 5 до 60 мин, предпочтительно не менее от 10 до 45 мин, особенно предпочтительно не менее от 20 до 30 мин. В течение этого времени температуру раствора предпочтительно поддерживают в одном из указанных выше температурных диапазонов и особенно предпочтительно, если температуру поддерживают постоянной. Затем полученную смесь предпочтительно охлаждают до температуры в диапазоне от 0 до 20C, предпочтительно от 5 до 15C, особенно предпочтительно 7-13C и перемешивают при этой температуре в течение еще не менее от 0,5 до 2 ч, предпочтительно не менее от 0,75 до 1,5 ч, особенно предпочтительно не менее 1 ч.-3 015967 Затем полученную суспензию 4-Br в спирте освобождают от растворителя путем центрифугирования и полученный остаток необязательно промывают одним из указанных выше спиртов. Затем полученный 4-Br сушат в вакууме при температуре не выше 30-65C, предпочтительно не выше 50-60C. Настоящее изобретение также относится к полученному таким образом гидробромиду формулы 4-Br Согласно изобретению неожиданно было установлено, что эту соль соединения формулы 4 особенно легко отделить, что делает особенно простым выделение этого промежуточного продукта при реакциях в промышленном масштабе. Легкость отделения в контексте настоящего изобретения означает возможность отделения полученного кристаллического продукта от растворителя с помощью фильтрования,фильтрования с отсасыванием или сравнимых методик отделения. Улучшение качества отделения оказывает прямое влияние на производительность способа и поэтому является особенно важным, в особенности при проведении реакций в промышленном масштабе. Поскольку продукт лучше отделяется, его можно быстрее выделить, быстрее и лучше промыть и, следовательно, также быстрее высушить. Соединение формулы 1 можно получить из соединения 4-Br по следующей методике. Сначала 4-Br предпочтительно прибавляют к органическому растворителю, смешанному с подходящей кислотой. В контексте настоящего изобретения кислотой предпочтительно является хлористоводородная кислота и растворителем предпочтительно является спирт. Особенно предпочтительно использовать изопропанол или этанол, более предпочтительно этанол. В контексте настоящего изобретения показано, что особенно предпочтительно использовать 5-12 М, более предпочтительно 9-11 М этанольный раствор хлористо-водородной кислоты. Если, что особенно предпочтительно в контексте настоящего изобретения, используют 10 М этанольный раствор хлористо-водородной кислоты, то на 1 моль применяющегося соединения 4-Br предпочтительно используют 0,4-1,5 кг, более предпочтительно 0,6-1,0 кг,особенно предпочтительно 0,75-0,85 кг 10 М этанольного раствора хлористо-водородной кислоты. В контексте настоящего изобретения 4-Br предпочтительно прибавляют к содержащему кислоту спирту при температуре в диапазоне примерно 20-25C, предпочтительно при перемешивании при температуре окружающей среды (23C). В контексте настоящего изобретения соединение формулы 1 предпочтительно готовят в форме соли присоединения с кислотой. Особенно предпочтительно, если соединение формулы 1 готовят в форме его соли с паратолуолсульфоновой кислотой. Показано, что если соединение формулы 1 необходимо получить в форме соли присоединения с паратолуолсульфоновой кислотой, то эффективно прибавлять паратолуолсульфоновую кислоту на этой стадии. В соответствии с этим,после прибавления раствора 4-Br к указанному выше предпочтительно содержащему хлористоводородную кислоту спирту также прибавляют п-толуолсульфоновую кислоту. Паратолуолсульфоновую кислоту предпочтительно прибавляют в виде ее гидрата. В качестве альтернативы к описанной выше методике всю паратолуолсульфоновую кислоту можно прибавит вначале, до прибавления соединения 4-Br к содержащему кислоту спирту. На 1 моль применяющегося соединения формулы 4-Br предпочтительно можно прибавить 180-300 г, особенно предпочтительно 200-300 г, более предпочтительно 245-255 г водного раствора указанной выше п-толуолсульфоновой кислоты. После завершения прибавления температуру смеси при перемешивании предпочтительно доводят до значения в диапазоне примерно 23-40C, предпочтительно 25-35C, особенно предпочтительно 2829C и перемешивают в течение еще не более 12-36 ч, предпочтительно не более 20-28 ч, особенно предпочтительно не более 23-25 ч при постоянной температуре. Затем необязательно может быть целесообразным дополнительное разбавление реакционного раствора путем прибавления растворителя. Если дополнительно прибавляют растворитель, предпочтительно использовать один из указанных выше спиртов и особенно предпочтительно использовать конкретный спирт, который уже использован для приготовления раствора соединения 4-Br. В этом случае также предпочтительно использовать этанол. Если раствор дополнительно разбавляют, то на 1 моль применяющегося соединения формулы 4-Br предпочтительно используют 0,5-1,5 л, особенно предпочтительно 0,8-1,0 л указанного выше растворителя, предпочтительно спирта, особенно предпочтительно этанола. Затем смесь охлаждают при перемешивании до температуры в диапазоне примерно от -10 до 15C,предпочтительно от -5 до +5C, особенно предпочтительно от 1 до 3C и объединяют с водным раствором аммиака. Особенно предпочтительно использовать 20-30%, предпочтительно 20-25% раствор аммиака, и в контексте настоящего изобретения предпочтительно используют 25% водный раствор аммиа-4 015967 ка. Если используют 25% водный раствор аммиака, то на 1 моль применяющегося соединения формулы 4-Br предпочтительно используют 0,5-1,5 кг, особенно предпочтительно 0,6-1,0 кг, более предпочтительно 0,7-0,8 кг указанного выше 25% водного раствора аммиака. Водный раствор аммиака предпочтительно прибавлять так, чтобы температура поддерживалась в диапазоне примерно 0-15C, предпочтительно 0-10C. Особенно предпочтительно регулировать прибавление так, чтобы температура оставалась постоянной. Значение pH раствора предпочтительно повышают до находящегося в диапазоне 9-10,5, предпочтительно до pH 9,3-10. После завершения прибавления смесь предпочтительно нагревают при перемешивании до температуры в диапазоне примерно 20-30C, предпочтительно 22-27C, особенно предпочтительно примерно 25C и перемешивают в течение еще не менее 2-8 ч, предпочтительно не менее 2,4-6 ч, особенно предпочтительно не менее 3-5 ч при постоянной температуре. Затем большие количества растворителя необязательно отгоняют при пониженном давлении. Особенно предпочтительно, если на 1 моль применяющегося соединения 4-Br путем отгонки удаляют 0,2-0,8 л, более предпочтительно 0,3-0,7 л, еще более предпочтительно 0,4-0,5 л указанного выше растворителя. Отгонку растворителя предпочтительно проводят при температуре в диапазоне примерно 40-65C,особенно предпочтительно при 50-60C. Если невозможно отогнать растворитель при нормальном давлении в этом температурном диапазоне вследствие выбора растворителя, давление снижают, пока не произойдет эффективная отгонка в указанном температурном диапазоне. Затем смесь для последующей обработки смешивают с водой при постоянной температуре (примерно 50-60C). Особенно предпочтительно, если на 1 моль применяющегося соединения 4-Br прибавляют 2-8 л, особенно предпочтительно 4-7 л, более предпочтительно 5-6 л воды. Кроме прибавления воды также прибавляют водный раствор NaOH, предпочтительно 30-60%, особенно предпочтительно 4050% раствора NaOH. В контексте настоящего изобретения особенно предпочтительно прибавлять 50% водный раствор NaOH. Если прибавляют 50% раствор NaOH, то на 1 моль применяющегося соединения 4-Br предпочтительно прибавляют 50-200 мл, особенно предпочтительно 70-150 мл, более предпочтительно 90-110 мл 50% раствора NaOH. После завершения прибавления температуру смеси при перемешивании предпочтительно доводят до значения, находящегося в диапазоне примерно 40-70C, предпочтительно 50-60C, особенно предпочтительно примерно 55C и перемешивают в течение еще не менее 0,5-1,5 ч, предпочтительно не менее 0,6-1,25 ч, особенно предпочтительно не менее 0,75-1 ч при постоянной температуре. Затем смесь необязательно охлаждают до температуры в диапазоне примерно 0-30C, предпочтительно 5-20C, особенно предпочтительно 10-15C и перемешивают в течение еще не менее 0,5-2 ч,предпочтительно не менее 0,75-1,5 ч, особенно предпочтительно не менее 1 ч при постоянной температуре. Полученные кристаллы отделяют, промывают водой и необязательно органическим растворителем и затем сушат в вакууме при температуре не выше 50-90C, предпочтительно не выше 60-70C. Приведенные ниже примеры предназначены для иллюстрации способа синтеза, приведенного в качестве примера. Они являются только примерами возможных методик и настоящее изобретение не ограничивается их содержанием. Пример 1. Крупномасштабный промышленный синтез соединения формулы 4-Br. Используют 88 кг карбонилди-(1,2,4-триазола) и его объединяют с 920 л тетрагидрофурана. Содержимое аппарата нагревают до 35C при перемешивании. Затем 3 порциями при 35C в течение от 1 до 2 ч прибавляют 90 кг соединения. 160 кг соединения 2 помещают во второй реактор, затем прибавляют 350 л тетрагидрофурана и смесь при перемешивании нагревают до 50C. Раствор 3 прибавляют к раствору 2 в течение от 2 до 3 ч при 47-53C и полученный раствор разбавляют с помощью 115 л тетрагидрофурана. Затем смесь перемешивают в течение еще 4 ч при 47-53C (предпочтительно 50C). Затем 670-695 л тетрагидрофурана отгоняют в вакууме при 50-60C. Затем к остатку прибавляют 235 л н-бутилацетата. После этого 600-630 л смеси н-бутилацетат/ТГФ отгоняют в вакууме при 50-85C. Во время отгонки вводят 700 л бутилацетата. К остатку прибавляют 65 кг уксусной кислоты, содержимое нагревают до 85-90C и перемешивают в течение не менее еще 2,5 ч при этой температуре. Затем смесь охлаждают до 65-75C. К содержимому прибавляют раствор 165 л воды и 20 кг хлорида натрия и смесь промывают спомощью 300 л воды. Затем температуру доводят до 60-70C и смесь перемешивают при этой температуре в течение не менее 15 мин. Для разделения фаз перемешивание прекращают и смеси дают отстояться в течение не менее 15 мин. Водную фазу сливают в другой реактор, который содержит 120 л н-бутилацетата. Смесь нагревают до 60-70C при перемешивании и перемешивают в течение не менее 10 мин. После разделения фаз водную фазу сливают в систему сбора химических отходов. Содержащие бутилацетат фазы и 20 л бутилацетата,-5 015967 использованного для промывки, объединяют. Из этой смеси в вакууме при максимальной внутренней температуре, равной 80C, отгоняют 590-620 л н-бутилацетата. К остатку после отгонки прибавляют 880 л изопропанола и температуру содержимого доводят до 32-38C. Затем при 32-38C прибавляют примерно 90 кг 48% бромисто-водородной кислоты, пока значение pH не станет равным от 0,6 до 1,3. Смесь перемешивают в течение не менее 20 мин при 32-38C и затем охлаждают до 7-13C и перемешивают при этой температуре в течение не менее 1 ч. Полученную суспензию центрифугируют, промывают с помощью всего 840 л изопропанола и сушат в вакууме при температуре не выше 55C. Выход: 211-250 кг. Температура плавления: 200-215C (с разложением). Соединение 4-HBr можно выделить с помощью стандартной имеющейся в продаже центрифуги. Пример 2. Крупномасштабный промышленный синтез соединения формулы 1 (в форме соли присоединения с паратолуолсульфоновой кислотой). 330 кг соединения 4-Br и 147 кг п-толуолсульфоновой кислоты (водного раствора) при перемешивании при 23C прибавляют к 470 кг 10 М этанольного раствора хлористо-водородной кислоты. Затем смесь нагревают до 28-29C и перемешивают в течение 23 ч при этой температуре. Реакционную смесь разбавляют с помощью 693 л этанола и переносят во второй реактор. Содержимое этого реактора разбавляют с помощью еще 536 л этанола и охлаждают до 2C. Прибавляют 440 кг 25% раствора аммиака, поддерживая температуру равной примерно 10C, пока не установится значение pH, равное от 9,3 до 10, и дополнительно охлаждают и перемешивают. Содержимое аппарата нагревают до 25C и перемешивают в течение 4 ч при этой температуре. Затем содержимое нагревают до температуры, равной от 50 до 60C, и 248-261 л этанола отгоняют в вакууме. Затем 1220 л воды прибавляют при внутренней температуре, равной 50-60C. Содержимое аппарата разделяют на равные количества (примерно 1450 л) между двумя реакторами одинакового объема. Обработку продолжают параллельно (одновременно) в обоих аппаратах. В каждом случае прибавляют раствор 950 л воды и 31 л раствора гидроксида натрия (50%). Температуру содержимого этих двух аппаратов доводят до равной от 50 до 60C (предпочтительно 55C) и перемешивают в течение 45 мин. Затем в течение 3 ч смесь охлаждают до 10-15C и перемешивают при этой температуре в течение еще 60 мин. Суспензию кристаллов разделяют с помощью двух центрифуг. Продукт промывают сначала водой,затем ацетоном и после этого сушат в вакууме при максимальной температуре, равной 70C. Выход: 314371 кг; температура плавления: 209-211C. ФОРМУЛА ИЗОБРЕТЕНИЯ 1. Способ получения соединения формулы необязательно в форме его солей присоединения с кислотой,отличающийся тем, что на первой стадии диамин формулы 2 в присутствии подходящего реагента сочетания с образованием соединения формулы 4 которое без выделения превращают в гидробромид формулы 4-Br который затем превращают в амидин формулы 1. 2. Способ по п.1, отличающийся тем, что реакцию 2 с 3 проводят в растворителе, который выбран из группы, включающей метиленхлорид, диметилформамид, бензол, толуол, хлорбензол, тетрагидрофуран, диоксан и их смеси. 3. Способ по п.1 или 2, отличающийся тем, что реагент сочетания выбран из группы, включающейN,N'-дициклогексилкарбодиимид, N,N'-карбонилдиимидазол и карбонилди-(1,2,4-триазол). 4. Способ по одному из пп.1-3, отличающийся тем, что для получения соединения формулы 4 прибавляют уксусную кислоту. 5. Способ по одному из пп.1-4, отличающийся тем, что соединение формулы 4-Br получают из соединения формулы 4 путем прибавления водного раствора бромисто-водородной кислоты. 6. Способ по одному из пп.1-5 получения соединения формулы 1 в виде его соли присоединения с п-толуолсульфоновой кислотой, отличающийся тем, что превращение соединения формулы 4-Br в амидин формулы 1 в форме его соли присоединения п-толуолсульфоновой кислотой проводят путем прибавления соединения формулы 4-Br к содержащему кислоту спирту с прибавлением птолуолсульфоновой кислоты и последующим прибавлением раствора аммиака. 7. Способ по п.6, отличающийся тем, что полное количество п-толуолсульфоновой кислоты прибавляют в начале реакции соединения формулы 4-Br с помощью содержащего кислоту спирта. 8. Способ по одному из пп.6 или 7, отличающийся тем, что содержащий кислоту спирт представляет собой содержащий хлористо-водородную кислоту этанол. 9. Соединение формулы 4-Br
МПК / Метки
МПК: C07D 401/12
Метки: получения, производного, способ, бензимидазола
Код ссылки
<a href="https://eas.patents.su/8-15967-sposob-polucheniya-proizvodnogo-benzimidazola.html" rel="bookmark" title="База патентов Евразийского Союза">Способ получения производного бензимидазола</a>
Предыдущий патент: Лопасть вентилятора градирни (варианты)
Следующий патент: Лопасть вентилятора градирни