Флюс и флюсующая ванна для горячего погружного цинкования, способ горячего погружного цинкования изделий из железа или стали
Формула / Реферат
1. Способ горячего погружного цинкования железного или стального изделия, включающий стадии, на которых:
а) обезжиривают изделие в обезжиривающей ванне;
б) промывают изделие;
в) протравливают изделие;
г) промывают изделие;
д) осуществляют обработку изделия во флюсующей ванне, содержащей от 200 до 700 г/л флюса, причем флюс включает от 36 до 60 мас.% хлорида цинка (ZnCl2) (процент от общего веса соли), от по меньшей мере 30 до 62 мас.% хлорида аммония (NH4Cl), от 2,0 до 10 мас.% NiCl2, MnCl2 или их смесь, сумма вышеуказанных солей составляет 100% за исключением обычных загрязнений;
е) высушивают изделие или выдерживают до высыхания в окружающей атмосфере;
ж) погружают изделие в горячую погружную ванну цинковых сплавов, содержащих 200-500 част./млн алюминия или обычно чистый цинк, для цинкования с образованием на нем металлического покрытия и
з) охлаждают изделие в водном растворе или воздухом.
2. Способ по п.1, отличающийся тем, что на стадии (д) изделие погружают во флюсующую ванну на время до 10 мин, предпочтительно не более чем на 5 мин.
3. Способ по п.1 или 2, отличающийся тем, что на стадии (е) изделие сушат посредством воздуха при температуре от 100 до 200°С, предпочтительно от 120 до 150°С.
4. Способ по любому из предыдущих пунктов, отличающийся тем, что флюс включает от 40 до 62 мас.% NH4Cl.
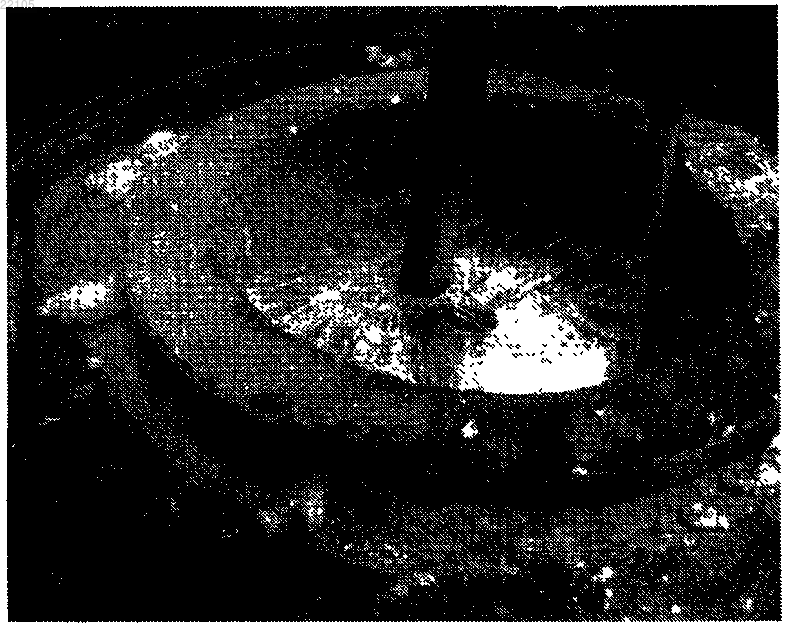
Текст
ФЛЮС И ФЛЮСУЮЩАЯ ВАННА ДЛЯ ГОРЯЧЕГО ПОГРУЖНОГО ЦИНКОВАНИЯ,СПОСОБ ГОРЯЧЕГО ПОГРУЖНОГО ЦИНКОВАНИЯ ИЗДЕЛИЙ ИЗ ЖЕЛЕЗА ИЛИ СТАЛИ Описано изобретение, относящееся, главным образом, к флюсу для горячего погружного цинкования, включающему от 36 до 80 мас.% хлорида цинка (ZnCl2), от 8 до 62 мас.% хлорида аммония (NH4Cl), от 2,0 до 10 мас.% по меньшей мере одного из следующих соединений: NiCl2,MnCl2 или их смесь. Предложенный в изобретении способ дополнительно относится к флюсующей ванне, способу горячего погружного цинкования железного или стального изделия, а также к использованию указанного флюса.(71)(73) Заявитель и патентовладелец: ГАЛВА ПАУЭР ГРУП Н.В. (BE) Область техники, к которой относится изобретение Настоящее изобретение, главным образом, относится к флюсу и флюсующей ванне для горячего погружного цинкования и способу горячего погружного цинкования железных или стальных изделий. Уровень техники Стандартное горячее погружное цинкование, состоящее из погружения железных или стальных изделий в расплавленную цинковую ванну, требует тщательной подготовки поверхности для обеспечения адгезии, непрерывности и однородности цинкового покрытия. Стандартный способ подготовки поверхности железного или стального изделия, подлежащего цинкованию, заключается в сухом флюсовании,при котором пленку флюса осаждают на поверхности изделия перед погружением его в цинковую ванну. Соответственно, изделие, как правило, подвергают обезжириванию с последующей промывкой, очистке кислотой, также с последующей промывкой, и конечному сухому флюсованию, т.е. изделие погружают во флюсующую ванну с последующей сушкой. Основными агентами, используемыми при стандартном флюсовании, обычно являются цинк и хлориды аммония. При периодическом процессе горячего погружного цинкования или при общем промышленном цинковании в настоящее время сталкиваются с несколькими серьезными проблемами. Проблема 1. Было доказано, что добавка от 250 до 500 част./млн алюминия в классическую цинковую ванну благоприятно влияет на несколько факторов, обеспечивая более тонкий слой цинка на стали, обогащеннойSi (Si0,28%), a также лучшую осушаемость расплавленного цинкового сплава. Однако также хорошо известно, что оцинковщики, которые пытались оцинковывать материал с помощью стандартного флюса в цинковой ванне, содержащей от 200 до 500 част./млн Al, сталкивались с проблемой. В частности, некоторые участки поверхности могли быть не покрыты или покрыты в недостаточной степени, или на покрытии могли появиться черные пятна или даже каверны, из-за которых изделие имело неприемлемую отделку поверхности и/или неудовлетворительную коррозионную стойкость. Таким образом, было проведено исследование с целью разработки способа предварительной обработки, и/или флюсов, и/или добавок к расплавленному цинку, которые в большей степени приспособлены для цинкования цинковым сплавом, содержащим 200-500 част./млн Al. Несмотря на эти усилия, когда дело доходит до цинкования железных или стальных изделий в цинк-алюминиевых ваннах в ходе периодических операцияй, т.е. цинкования отдельных изделий, известные флюсы все еще являются неудовлетворительными. Проблема 2. Для цинкования стальных деталей надлежащим и безопасным способом необходимы отверстия разных типов в стальных конструкциях или изделиях. а) отверстия для обеспечения доступа расплавленному цинку во все зоны конструкции/изделия,б) отверстия, необходимые для выпуска воздуха и газов, образующихся при плавлении флюса(NH4Cl, AlCl3, вода). Имеется множество документов, предлагающих наилучшие методики размещения отверстий и определения их размеров. Однако при повседневном производстве, к сожалению, часто случается, что в некоторых изделиях отверстия слишком малы и/или неудачно размещены (см. фиг. 1). В этих условиях в конструкции удерживается значительное количество жидкости (флюсующая ванна), и как только она вступает в контакт с ванной расплавленного цинка, образуется большое количество газа, что приводит к взрыву с выбросом в воздух до нескольких килограмм расплавленного цинка над поверхностью цинковой ванны. Выброс расплавленного цинка достигает частей изделия, которые еще не были погружены в расплавленный цинк, и прилипает к ним. В зависимости от толщины изделия, объема выбросов цинка (количества грамм Zn/см 2) и состава цинковой ванны слой флюса может быть разрушен, что приведет к плохому смачиванию расплавленного цинка и появлению неоцинкованных зон. Если цинковая ванна содержит от около 200 до около 500 част./млн алюминия, это явление, несомненно, будет иметь худшие последствия, чем при более низких содержаниях алюминия. Присутствие алюминия катализирует быстрое выгорание слоя флюса, и так как этих взрывов нельзя полностью избежать, это является главной проблемой цинкования при содержании 200-500 част./млн Al. Проблема 3. Хорошая сушка слоя флюса необходима для того, чтобы избежать взрывов, обеспечить как можно более высокую скорость погружения. Высокая скорость погружения уменьшает риск охрупчивания жидкого металла (также называемое растрескивание под действием жидкого металла), минимизировать образование золы и расход цинка (кг цинка/тонну материала). Наилучшим вариантом было бы доставить материал, подлежащий цинкованию при 100 С, как можно быстрее, чтобы убедиться в том, что вся вода испарилась и флюс еще не выгорел (поврежден). В повседневной практике осуществления периодического процесса горячего погружного цинкования(ПГПЦ), также называемого общее цинкование, сталкиваются с тремя факторами. а) Цинкование конструкций, изготовленных из стальных деталей разной толщины. Например, водя-1 022105 ной бак для фермера, изготовленный из стальных листов и профилей толщиной 5, 8 и 12 мм. После сушки детали имеют разные температуры в зависимости от их толщины: более тонкие детали горячее, а имеющие большую толщину холоднее. б) Число позиций в сушильном аппарате обычно ограничено двумя, таким образом, чтобы соблюсти производственный ритм, требуются более высокие температура воздуха и турбулентность для обеспечения сушки за достаточно короткое время. в) Иногда производство приходится остановить на 30 мин (например, на время перерыва на обед),некоторые погружения могут занять 40 мин при цинковании и поэтому некоторый материал, уже находящийся в сушильном аппарате, может оставаться там 3 ч в случае более продолжительных остановов и при более коротких лишь 10 мин. Следствиями этих факторов является то, что некоторые детали (тонкие детали) иногда могут достичь температуры воздуха, используемого для сушки, и начинают интенсивнее корродировать в сушильном аппарате, а детали с большей толщиной иногда могут быть слишком холодными и еще влажными,что может инициировать взрыв, как упоминалось выше, при вводе в ванну расплавленного цинка. Проблема 4. Некоторые изделия надо погружать в расплав цинка очень медленно, так как они являются полыми и размер отверстий в них ограничен, как в случае примера с автоклавами для сжатого воздуха и воды,находящимися под давлением. Из-за требований, обусловленных давлением, которые предъявляют подобные изделия, необходимы меньшие размеры отверстий, и иногда, чтобы полностью погрузить автоклав в расплавленный цинк, надо затратить до 30 мин. За это время расплавленный цинк нагревает сталь,что приводит к выгоранию (плавление и исчезновение) слоя флюса до того, как он войдет в контакт с расплавленным цинком. Сущность изобретения В основу предложенного изобретения положена задача предложить флюс, обеспечивающий получение непрерывных, однородных, гладких и без пустот покрытий на железных или стальных изделиях с помощью горячего погружного цинкования расплавленным цинком, содержащим от 5 до 500 част./млн алюминия и другие обычные легирующие компоненты (Ni, Sn, Pb, Bi, Mn, V). Флюс для горячего погружного цинкования в соответствии с предлагаемым изобретением включает от 36 до 82 мас.% (массовых процентов) хлорида цинка (ZnCl2); от 8 до 62% мас.% хлорида аммония (NH4Cl); от 2,0 до 10 мас.% по меньшей мере одного из следующих компонентов: NiCl2, MnCl2 или их смесь. Сумма вышеуказанных компонентов составляет 100% за исключением обычных загрязнений. Термин "горячее погружное цинкование" означает цинкование железного или стального изделия погружением его в ванну расплавленного цинка или сплава цинка при непрерывном или периодическом процессе. Вышеуказанный флюс должен демонстрировать более высокую стойкость к разрушению (деструкции) при контакте с горячим турбулентным воздухом в сушильном аппарате или во время процесса погружения в ванну расплавленного цинка и, главным образом, при очень медленном процессе погружения или прерываемом на какое-то время. Кроме того, этот флюс должен быть более стойким при разбрызгивании расплавленного цинка на офлюсованные части. Такой флюс, в котором разные процентные содержания относятся к массовой доле каждого компонента или класса соединения относительно общей массы флюса, позволяет получить непрерывные, однородные, гладкие и не содержащих пустоты покрытия на железных или стальных изделиях с помощью горячего погружного цинкования, в частности, цинкового сплава, содержащего от 200 до 500 част./млн алюминия, главным образом при периодическом процессе. Определенный процент ZnCl2 обеспечивает хорошее покрытие изделия, подлежащего цинкованию, и эффективно препятствует окислению изделия в процессе его сушки перед цинкованием. Процент NH4Cl определяют таким образом, чтобы достичь достаточного эффекта травления при горячем погружении, удаления остаточной ржавчины или плохо протравленных пятен, однако наряду с этим, чтобы избежать образования черных пятен, т.е. непокрытых поверхностей изделия. Следующие соединения: NiCl2, MnCl2 улучшают стойкость флюса к разрушению в сушильном аппарате и/или при погружении деталей в расплавленный цинк и/или при попадании брызг цинка на офлюсованные детали и, главным образом, при использовании цинковального сплава, содержащего 200-500 част./млн Al. Как упоминалось, предлагаемый флюс в особенности пригоден для периодических процессов горячего погружного цинкования с использованием ванны цинковых сплавов, содержащих 200-500 част./млн алюминия, но также ванны чистого цинка. Кроме того, предлагаемый флюс можно использовать в процессах непрерывного цинкования, использующих цинк-алюминиевые или обычные ванны чистого цинка для оцинковывания, например, проволоки, труб или обмоточных материалов (листовые материалы). Термин "ванна чистого цинка" используется в этой заявке в противоположность цинк-алюминиевым сплавам, очевидно, что ванны чистого цинка для цинкования могут содержать некоторые обычные добавки, такие как, например, Pb, V, Bi, Ni, Sn, Mn Что касается хлорида цинка, предпочтительно процентное содержание от 36 до 62 мас.%, более предпочтительно от 45 до 60 мас.% и наиболее предпочтительно от 54 до 58 мас.%. В качестве альтерна-2 022105 тивы, процентное содержание хлорида цинка составляет от 38 до 42%. Предпочтительное процентное содержание хлорида цинка во флюсе составляет по меньшей мере 38%, более предпочтительно по меньшей мере 42%, еще более предпочтительно по меньшей мере 45% и наиболее предпочтительно по меньшей мере 52%. Предпочтительное максимальное процентное содержание хлорида цинка во флюсе составляет до 62%, более предпочтительно до 60%, еще более предпочтительно до 58% и наиболее предпочтительно до 54%. Что касается хлорида аммония (NH4Cl) предпочтительно процентное содержание от 12 до 6 мас.%,более предпочтительно от 40 до 62%, наиболее предпочтительно от 40 до 46%. В качестве альтернативы,процентное содержание хлорида аммония (NH4Cl) составляет от 58 до 62%. Предпочтительное процентное содержание хлорида аммония (NH4Cl) во флюсе составляет по меньшей мере 12%, более предпочтительно по меньшей мере 20%, еще более предпочтительно по меньшей мере 30% и наиболее предпочтительно по меньшей мере 40%. Предпочтительное максимальное процентное содержание хлорида цинка во флюсе составляет до 62%, более предпочтительно до 50%, еще более предпочтительно до 45% и наиболее предпочтительно до 40%. Содержание NiCl2 и/или MnCl2 или их смесей во флюсе составляет предпочтительно до 8%, более предпочтительно до 6%, еще более предпочтительно до 5% и наиболее предпочтительно до 4 мас.%. Содержание NiCl2 и/или MnCl2 или их смесей во флюсе предпочтительно составляет по меньшей мере 2,5%, более предпочтительно по меньшей мере 3%, еще более предпочтительно по меньшей мере 3% и наиболее предпочтительно по меньшей мере 4,5 мас.%. Содержание NiCl2 и/или MnCl2 или их смесей во флюсе составляет 2,7 мас.% NiCl2 или 2,7 мас.%MnCl2 или смеси от 0,9 до 2,7 мас.% MnCl2 с от 0,9 до 2,7 мас.% NiCl2 при условии, что содержание NiCl2+ MnCl2 составляет по меньшей мере 2 мас.%. Согласно другому варианту осуществления изобретения предлагается флюсующая ванна для горячего погружного цинкования, в которой некоторое количество вышеуказанного флюса растворено в воде. Концентрация флюса во флюсующей ванне составляет от 200 до 700 г/л, предпочтительно от 280 до 600 г/л, наиболее предпочтительно от 350 до 550 г/л. Эта флюсующая ванна, в частности, приспособлена к процессам горячего погружного цинкования, в которых используют цинк-алюминиевые ванны, но также могут использоваться оцинковочные ванны чистого цинка в периодических или непрерывных процессах. Флюсующую ванну следует преимущественно поддерживать при температуре от 35 до 90 С, предпочтительно от 40 до 60 С. Флюсующая ванна может также содержать от 0,01 до 2 об.% (по объему) неионного поверхностноактивного вещества, такого, например, как Merpol HCS от Du Pont de Nemours, FX от Henkel, Netzer 4 отLutter Galvanotechnik GmbH (DE) и тому подобное. Согласно другому предпочтительному варианту осуществления изобретения флюс содержит менее 1,5% солей щелочного металла и/или солей щелочно-земельного металла. Предпочтительно флюс содержит менее 1,0% и еще более предпочтительно менее 0,5% солей щелочного металла и/или солей щелочно-земельного металла. В соответствии с другим вариантом осуществления изобретения предлагается способ горячего погружного цинкования железного или стального изделия. На первой стадии способа (а) изделие подвергают обезжириванию в обезжиривающей ванне. Последняя может преимущественно представлять собой ультразвуковую, щелочную обезжиривающую ванну. Затем, на второй стадии (б) изделие промывают. На других стадиях (в) и (г) изделие подвергают протравливающей обработке и затем промывают. Очевидно, что эти стадии предварительной обработки могут повторяться по отдельности или циклами в случае необходимости. Весь цикл предварительной обработки (стадии от а до г) можно проводить дважды. Стадию протравливания и последующую стадию промывки можно также заменить стадией дробеструйной очистки. В обоих случаях следует отметить, что на следующей стадии (д) изделие обрабатывают во флюсующей ванне в соответствии с предлагаемым изобретением для того, чтобы образовалась пленка флюса на поверхности изделия. Изделие можно погрузить во флюсующую ванну на время до 10 мин,однако предпочтительно не более чем на 5 мин. Офлюсованное изделие затем сушат (стадия е). На следующей стадии (ж) изделие погружают в горячую цинковальную ванну для образования на нем металлического покрытия. Время погружения является функцией размера и формы изделия, требуемой толщины покрытия и содержания алюминия (если в качестве цинковальной ванны используют сплав Zn-Al). Наконец, изделие удаляют из цинковальной ванны и охлаждают (стадия з). Охлаждение можно провести погружением изделия в воду или просто охлаждая его на воздухе. Показано, что предложенный в изобретении способ обеспечивает осаждение непрерывных, однородных, гладких и не содержащих пустоты покрытий на отдельных железных или стальных изделиях,главным образом при использовании цинковальной ванны сплава цинка с алюминием в количестве 200500 част./млн. Этот способ в особенности пригоден для периодического горячего погружного цинкова-3 022105 ния отдельных изделий из железа или стали, но также позволяет получить подобные улучшенные покрытия на проволоке, трубах или обмоточных материалах, при непрерывном управлении на разных стадиях процесса. Предлагаемый в изобретении способ применим для разнообразных стальных изделий, например,стальных элементов конструкций, таких как вышки, мосты, промышленные или сельскохозяйственные сооружения, трубы разной формы, ограды вдоль железнодорожных путей, стальные элементы низа кузова транспортного средства (рычаги подвески, узел двигателя), отливки, болты и мелкие детали. Предварительную обработку изделия вначале выполняют погружением изделия, подлежащего цинкованию, на время от 15 до 60 мин в щелочную обезжиривающую ванну, содержащую смесь солей,включая, главным образом, гидроокись натрия, карбонат натрия, полифосфат натрия, а также смесь поверхностно-активных веществ (тензидов), таких как, например, Solvopol SOP и Emulgator SEP от Galvanotechnik GmbH. Концентрация смеси солей предпочтительно составляет от 2 до 8 мас.% и смеси тензидов предпочтительно от 0,1 до 5 мас.%. Температуру в обезжиривающей ванне поддерживают на уровне от 60 до 80 С. В ванне предусмотрен ультразвуковой генератор, способствующий обезжириванию. После этой стадии следуют две промывки водой. Затем предварительная обработка продолжается на стадии протравливания, при которой изделие погружают на время от 60 до 180 мин в водный раствор соляной кислоты с концентрацией от 10 до 22%,содержащий ингибитор (гексаметилентетрамин,), и выдерживают при температуре от 30 до 40 С для удаления окалины и ржавчины с изделия. За этим снова следуют две стадии промывки. Промывку после протравливания предпочтительно выполняют погружением изделия в резервуар с водой при рН ниже 1 на время менее 3 мин, более предпочтительно около 30 с. Очевидно, что эти стадии обезжиривания и протравливания можно при необходимости повторить. Также эти стадии можно частично или полностью заменить стадией продувки стали. Затем детали погружают во флюс, сушат в сушильном аппарате или,если флюс имеет высокую температуру, их можно сушить при температуре окружающего воздуха. Затем детали погружают в расплавленный цинковый сплав. Наконец, выполняют охлаждение покрытого изделия погружением его в воду с температурой от 30 до 50 С или, в качестве альтернативы, выдерживая его в воздухе. В результате на поверхности изделия образуется непрерывное, однородное и гладкое покрытие без каких-либо пустот, пятен, шероховатости или комковатости. Для дополнительной иллюстрации настоящего изобретения ниже приводятся и обсуждаются три примера в соответствии с прилагаемыми к описанию чертежами, на которых показано: на фиг. 1 - фото погружения, прерванного на 45 с, для форсирования разрушения пленки флюса на части трубы как раз над уровнем ванны расплавленного цинка; на фиг. 2 а - вертикальная проекция позиции изделий в сушильном аппарате в соответствии с примером 1; на фиг. 2 б - вертикальная проекция позиции изделия в сушильном аппарате в соответствии с примерами 2 и 3; на фиг. 3 - фото, иллюстрирующее влияние концентрации MnCl2 во флюсе; на фиг. 4 - фото, иллюстрирующее влияние концентрации NiCl2 во флюсе. Пример 1. Оценка стойкости флюса при очень медленном погружении детали или при прерывании процедуры погружения. Для наблюдения за этим явлением провели испытания на трубах от компании Baltimore Aircoil длиной 200 мм (диаметр = 25 мм, толщина = 1,5 мм). Эти трубы были оцинкованы при каждом условии испытания с целью получения статистически совместимого результата. Все эти трубы были подготовлены для цинкования в соответствии со следующими стадиями предварительной обработки: обезжиривание щелочью в течение 10 мин при 60 С, промывка, протравливание в течение 30 мин в ванне, содержащей 95 г/л HCl и 125 г/л FeCl2, промывка (в двух ваннах с последовательным расположением), флюсование(см. табл. 1) в течение 2 мин во флюсующей ванне при 50 С. К флюсу добавили смачивающий агент(Netzer 4 от Lutter Galvanotechnik GmbH) для лучшего смачивания стали и обеспечения на ней более гомогенного слоя флюса, сушка в течение 14 ч воздухом при 120 С при естественной конвекции воздуха(без вентиляции: частотный регулятор на 0 Гц), цинковый сплав в мас.%: 0,33 Sn - 0,03 Ni - 0,86 Bi - 0,05Al - 0,022 Fe - 0 Pb при 440C. Процедура погружения Трубы погрузили с постоянной скоростью (0,5 м/мин) на глубину до 100 мм ниже уровня поверхности цинковой ванны (см фиг. 1), затем движение прекратили и оставили их в этом положении на 45 с. После этого трубу полностью погрузили (т.е. на остальные 100 мм) в расплавленную цинковую ванну(скорость погружения = 0,5 м/мин). Трубы находились в подвешенном состоянии в цинковой ванне в течение 2 мин до начала стадии извлечения, которую проводили с постоянной скоростью (0,5 м/мин). Во время периода прерывания процедуры погружения (см фиг. 1) часть трубы, которая была вне расплавленной цинковой ванны, но вблизи е поверхности, и таким образом все еще была покрыта сухим слоем флюса, находилась под влиянием очень сложных условий (очень высокой температуры), и слой флюса разрушился, что привело к появлению неоцинкованных зон после цинкования. Поэтому это испытание было вполне наглядным. Таблица 1. Состав разных испытанных флюсов (пример 1) Трубы, обработанные флюсом 1 (классический флюс без каких-либо добавок, за исключением смачивающего агента Netzer 4), показали 1 небольшое неоцинкованное пятно; трубы (флюс 10) без Netzer 4 показали небольшие неоцинкованные зоны. Трубы, обработанные флюсом 8 со SnCl2 (5,5 г/л), одна из двух безупречна, другая имела много черных пятен. Обе трубы, обработанные флюсом 3, содержащим NiCl2 (16,5 г/л), были безупречны. Обе трубы, обработанные флюсом 2, содержащим NiCl2 (5,5 г/л), были неудовлетворительны. Трубы, обработанные флюсом 9 со SnCl2 (2,75 г/л), одна из двух имела небольшие дефекты и другая была очень плохо оцинкована. Пример 2. Эти испытания были также проведены на трубах от Baltimore Aircoil длиной 200 мм (диаметр = 25 мм, толщина =1,5 мм). Три трубы были оцинкованы при каждом из условий испытания с целью получения статистически совместимого результата. Все эти трубы были подготовлены для цинкования в соответствии со следующими стадиями предварительной обработки: обезжиривание щелочью в течение 10 мин при 60 С, промывка, протравливание в течение 30 мин при 30 С в ванне, содержащей 95 г/л HCl и 125 г/л FeCl2, промывка (в двух последовательно расположенных ваннах), флюсование (см.табл. 3) в течение 2 мин во флюсующей ванне при 50 С. К флюсу добавили смачивающий агент (Netzer 4 от LutterGalvanotechnik GmbH) для лучшего смачивания стали и обеспечения на ней более гомогенного слоя флюса, сушка в течение 14 ч в сушильном аппарате воздухом при 120 С с естественной конвекцией воздуха (без вентиляции: частотный регулятор на 0 Гц), цинковый сплав в мас.%: 0,33 Sn - 0,03, Ni - 0,086,Bi - 0,05, Al - 0,022, Fe - 0 Pb, остальное цинк с обычными загрязнениями при 440 С. Процедура погружения точно соответствовала таковой в примере 1, однако она была прервана на 120 с вместо 45 с. Таким образом, условия испытания были более сложными, чем в примере 1. Таблица 3. Условия испытания в примере 2 Результаты и заключения из проведенных испытаний Все трубы имели полностью серый цвет после стадии сушки. Это отличается от испытания в примере 1 и может быть обусловлено показателями влажности (относительной влажностью воздуха) в день проведения испытания. Трубы, обработанные флюсом на основе классической двойной соли (10, 12, 13), показали дефекты цинкования от небольших до весьма обширных. Трубы, которые показали безупречное качество после цинкования, являются таковыми, обработанными флюсом, содержащим 15 г/л NiCl2. Присутствие 5 г/л Fe2+ во флюсе привело к плохому качеству оцинковывания труб Baltimore. Это качество немного лучше, чем труб, полученных с флюсом без Fe (флюсы 15 и 16 дали лучшие результаты, чем флюсы 12, 13 и 10). Лучшее сопротивление выгоранию флюса, возможно, обусловлено более толстым слоем флюса на трубах, содержащего добавку FeCl2, что представляет собой явление, уже описанное в литературе. Пример 3. В этом испытании было изучено влияние присутствия во флюсе MnCl2, NiCl2 и комбинации обоих соединений MnCl2 + NiCl2. Были использованы такие же трубы от Baltimore, как в предыдущих примерах, для оценки стойкости этих флюсов. Процедура предварительной обработки, время удержания во флюсе, сушильный аппарат и цинковая ванна были точно такими же, как в примере 2. Состав цинковой ванны также идентичен таковому в примере 2. Таблица 5. Состав флюса, испытанного в примере 3 (двойная соль в этом контексте означает Результаты и заключения из испытаний в примере 3 Трубы, предварительно обработанные флюсом на основе двойной соли, содержащим 2,7 мас.% (15 г/л) MnCl2 (29 и 29bis), показали наилучшее качество после цинкования (3 из 3 получили оценку "очень хорошо"), или в комбинациях 0,9 мас.% (5 г/л) MnCl2 + 2,7 мас.% (15 г/л) NiCl2 (39), или 2,7 мас.% (15 г/л) MnCl2 + 0,9 мас.% (5 г/л) NiCl2 (37). Флюс на основе двойной соли с 2,7 мас.% (15 г/л) NiCl2 (18) или в комбинациях 1,82 мас.% (10 г/л) MnCl2 + 1,82 мас.% (10 г/л) NiCl2 (38) или 1,82 мас.% (10 г/л) MnCl2 + 0,9 мас.% (5 г/л) NiCl2 (36) также показал хорошие результаты. Трубы, предварительно обработанные флюсом на основе двойной соли с (28) или без (28bis) Netzer 4, не получили хорошую оценку, так как слой флюса над поверхностью цинка был разрушен. Трубы,предварительно обработанные другим флюсом, находились в промежуточном положении между флюсом на основе двойной соли без добавки и вышеуказанными наилучшими флюсами. Сравнение труб, предварительно обработанных во флюсе, содержащем 5 (0,9 мас.%), 10 (1,82 мас.%) или 15 (2,7 мас.%) г/л MnCl2, показало, что флюс с 15 г/л MnCl2 дает наилучшие результаты (см. фиг. 3). Этот результат на 100% является воспроизводимым. Точно такое же заключение можно сделать для флюса, содержащего 5-10-15 г/л NiCl2, как показано на фиг. 4. ФОРМУЛА ИЗОБРЕТЕНИЯ 1. Способ горячего погружного цинкования железного или стального изделия, включающий стадии,на которых: а) обезжиривают изделие в обезжиривающей ванне; б) промывают изделие; в) протравливают изделие; г) промывают изделие; д) осуществляют обработку изделия во флюсующей ванне, содержащей от 200 до 700 г/л флюса,причем флюс включает от 36 до 60 мас.% хлорида цинка (ZnCl2) (процент от общего веса соли), от по меньшей мере 30 до 62 мас.% хлорида аммония (NH4Cl), от 2,0 до 10 мас.% NiCl2, MnCl2 или их смесь,сумма вышеуказанных солей составляет 100% за исключением обычных загрязнений; е) высушивают изделие или выдерживают до высыхания в окружающей атмосфере; ж) погружают изделие в горячую погружную ванну цинковых сплавов, содержащих 200-500 част./млн алюминия или обычно чистый цинк, для цинкования с образованием на нем металлического покрытия и з) охлаждают изделие в водном растворе или воздухом. 2. Способ по п.1, отличающийся тем, что на стадии (д) изделие погружают во флюсующую ванну на время до 10 мин, предпочтительно не более чем на 5 мин. 3. Способ по п.1 или 2, отличающийся тем, что на стадии (е) изделие сушат посредством воздуха при температуре от 100 до 200 С, предпочтительно от 120 до 150 С. 4. Способ по любому из предыдущих пунктов, отличающийся тем, что флюс включает от 40 до 62 мас.% NH4Cl.
МПК / Метки
Метки: флюсующая, горячего, железа, способ, изделий, цинкования, погружного, стали, флюс, ванна
Код ссылки
<a href="https://eas.patents.su/11-22105-flyus-i-flyusuyushhaya-vanna-dlya-goryachego-pogruzhnogo-cinkovaniya-sposob-goryachego-pogruzhnogo-cinkovaniya-izdelijj-iz-zheleza-ili-stali.html" rel="bookmark" title="База патентов Евразийского Союза">Флюс и флюсующая ванна для горячего погружного цинкования, способ горячего погружного цинкования изделий из железа или стали</a>
Предыдущий патент: Гербицидно активные циклические дионы и их производные, способы их получения, композиции, содержащие эти соединения
Следующий патент: Износостойкая трубная соединительная деталь пульпопровода
Случайный патент: Способ извлечения золота