Способ формования алюминиевых торцевых резервуаров теплообменников
Формула / Реферат
1. Способ получения торцевого резервуара теплообменника, включающий следующие стадии, на которых:
a) вставляют трубу, имеющую сердцевину из алюминиевого сплава AA3XXX, в устройство для формования, форма формующей полости которого соответствует форме готового торцевого резервуара;
b) закупоривают концы трубы;
c) нагнетают давление внутри трубы с помощью газа таким образом, чтобы она приняла форму указанной полости устройства, получая в результате готовый торцевой резервуар, причем трубу предварительно нагревают перед вставкой в устройство для формования и/или после вставки в устройство для формования до температуры формования;
d) удаляют торцевой резервуар из устройства;
e) охлаждают торцевой резервуар.
2. Способ получения торцевого резервуара теплообменника по п.1, в котором используемый для трубы материал не был подвергнут гомогенизации.
3. Способ получения торцевого резервуара теплообменника по п.1 или 2, в котором труба не была подвергнута отжигу.
4. Способ получения торцевого резервуара теплообменника по п.2, в котором сердцевина трубы имеет по меньшей мере одну плакировку из алюминиевого сплава.
5. Способ получения торцевого резервуара теплообменника по любому из предыдущих пунктов, в котором пазы для труб или соединений сделаны в фасонном торцевом резервуаре во время или после формования.
6. Способ получения торцевого резервуара теплообменника по любому из предыдущих пунктов, в котором используемое давление газа составляет более 85 бар.
7. Способ получения торцевого резервуара теплообменника по любому из предыдущих пунктов, в котором аксиальное давление прикладывают к концам трубы во время ее формования.
8. Способ получения торцевого резервуара теплообменника по любому из предыдущих пунктов, в котором на конце трубы во время ее формирования формуют резьбу или анкеры.
9. Способ получения торцевого резервуара теплообменника по любому из предыдущих пунктов, в котором на стадии а) обеспечивают трубу, изготовленную из сварной заготовки.
10. Торцевой резервуар теплообменника, выполненный из трубчатой заготовки из негомогенизированного алюминиевого сплава AA3XXX с улучшенными коррозионными и механическими свойствами, имеющий трубчатую форму варьируемой геометрии вдоль всей длины и сформованный способом по пп.1-9.
11. Торцевой резервуар теплообменника по п.10, имеющий по меньшей мере одну плакировку из алюминиевого сплава.
12. Торцевой резервуар теплообменника по пп.10-11, в котором трубчатая заготовка вытянута более чем на 20%.
13. Торцевой резервуар теплообменника по пп.10-12, подходящий для управляемого атмосферного припаивания или вакуумного припаивания.
14. Торцевой резервуар теплообменника по любому из пп.10-13, имеющий любую желательную форму в трех измерениях, такую как одна из кольцеобразной формы, S-образной формы, L-образной формы, C-образной формы, трапецеидальной формы и неправильной формы.
15. Торцевой резервуар теплообменника по любому из пп.10-13, который является одним из специально спроектированного, изогнутого или согнутого вдоль его продольной оси и/или поперек его продольной оси.
16. Торцевой резервуар теплообменника по пп.10-15, имеющий пазы для труб или соединений, выполненные после формования по пп.1-9.
17. Теплообменник, включающий торцевой резервуар теплообменника по пп.10-16.
18. Теплообменник по п.17, имеющий непрямоугольную форму.
19. Теплообменник по п.18, имеющий одну из форм: круглую, изогнутую, ступенчатую или неправильную.
20. Способ получения теплообменника, включающий следующие стадии, на которых
получают торцевой резервуар способом по пп.1-9;
обеспечивают отверстия для проточных труб в торцевом резервуаре;
соединяют множество проточных труб с торцевым резервуаром с помощью отверстий;
вставляют ребра между проточными трубами;
припаивают ребра к проточным трубам.
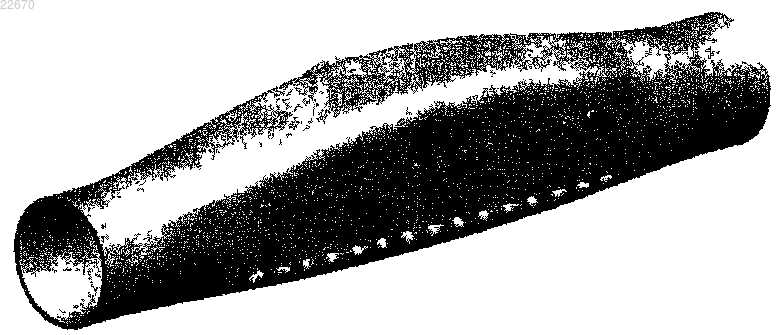
Текст
СПОСОБ ФОРМОВАНИЯ АЛЮМИНИЕВЫХ ТОРЦЕВЫХ РЕЗЕРВУАРОВ ТЕПЛООБМЕННИКОВ Изобретение относится к способу получения торцевого резервуара теплообменника, включающему следующие стадии: получение трубы, имеющей сердцевину, состоящую из алюминиевого сплаваAA3XXX; необязательное предварительное нагревание трубы; размещение трубы в устройстве для формования, форма полости которого соответствует форме готового торцевого резервуара; закупоривание концов трубы; нагнетание давления внутри трубы с помощью газа таким образом,чтобы она приняла форму полости устройства, получая в результате готовый торцевой резервуар; удаление торцевого резервуара из устройства; и охлаждение торцевого резервуара. Данный способ позволяет эффективно изготавливать торцевые резервуары неправильной формы из алюминиевого сплава AA3XXX. Настоящее изобретение также относится к способу получения теплообменника,согласно которому торцевой резервуар соединен с множеством труб и гофрированных ребер,вставленных между трубами, с последующим припаиванием ребер к трубам.(71)(73) Заявитель и патентовладелец: ГРЕНГЕС СВИДЕН АБ (SE) Область техники, к которой относится изобретение Изобретение относится к торцевым резервуарам и способам получения торцевых резервуаров, также называемых манифольдными емкостями, для паянных алюминиевым припоем автомобильных или стационарных теплообменников с почти произвольными формами резервуаров. Настоящее изобретение также относится к теплообменнику, включающему сформованные коллекторы, и способам его получения. Уровень техники Современные проектировщики автомобилей сталкиваются с все нарастающими трудностями по рациональной подгонке и сборке всех деталей под капотом. Двигатели становятся более мощными, и для поддержки двигателя приходится устанавливать все большее количество различных деталей, а также обеспечивать пассажиров постоянно повышающимся уровнем впечатления от вождения, безопасности и комфорта. Это приводит к еще большему дефициту доступного пространства под капотом. Теплообменники имеют, почти по умолчанию, прямоугольную форму, ограничивающую проектировщиков автомобилей относительно подходящего размещения собранного теплообменника в автомобиле. Множество ограничений геометрии теплообменника определяется экономической осуществимостью производства пластин и торцевых резервуаров для изготовления таких теплообменников, имеющих подобную неправильную или обычную форму; такие коллекторы и резервуары при существующих способах производства делают теплообменники слишком дорогостоящими. Также растущие требования к безопасности, комфорту и работе деталей под капотом делают переднюю часть транспортного средства более тяжелой, чем задняя часть, что является нежелательным. В обычных пассажирских транспортных средствах теплообменники, подобные CAC, конденсаторы, радиаторы и EGR охладители должны быть расположены в максимально передней части транспортного средства для того, чтобы обеспечить удовлетворительную работу теплообменников. Настоящее изобретение облегчает снижение веса таких деталей, одновременно уменьшая стоимость и повышая геометрическую гибкость уплотнения без ухудшения рабочих характеристик. Наиболее часто используемый способ получения торцевых резервуаров теплообменников включает подготовку плоского прокатанного листа для твердого припоя и формование его таким образом, чтобы получить коллектор с петлями для обжима пластмассового резервуара, пазами для вставки проточных труб, используемыми для циркуляции охлаждающей жидкости, и окончательную форму готового коллектора. Такой способ обычно осуществляют, обрезая плоский прокатанный лист до нужного размера,пробивая стороны для получения края листа прямоугольной формы (для петель), подвергая отрезок листа глубокой вытяжке для получения плиты для коллектора и, наконец, пробивая пазы, в которые вставляют проточную трубу/реберный блок. Затем начинается обычная процедура пайки твердым припоем. После пайки плакировка на поверхностях коллектора плавится и затекает в соединение трубы коллектора, образуя соединение с боковым швом правильного размера и формы. Затем резервуар обжимают по ее месту. Резервуар, как правило, изготавливают из полимерных материалов при наличии радиаторов и обогревателей, а для CAC ее обычно изготавливают из алюминия. Другим способом, использовавшимся ранее для формирования торцевых резервуаров, является гидроформинг. Вышеописанные способы производства являются дорогостоящими и требуют очень строгого контроля геометрии инструментальных средств и смазки контакта инструментального средства/листа. Они также требуют контролируемого слива и очистки остатков смазки и выбрасывания металлического скрапа, оставшегося, например, после пробивания, на производственной площадке, а также ручного управления, площади и вложений в контролируемое механическое оборудование, увеличивающих стоимость. Кроме того, поскольку глубокую вытяжку осуществляют при комнатной температуре, способ ограничивается использованием подвергнутых холодной обработке инструментальных сталей, механическая обработка которых до жесткого допуска обычно является весьма затруднительной и дорогостоящей. Изготовление пластмассовых резервуаров литьевым формованием является сравнительно медленной и дорогостоящей процедурой, требующей больших вложений в механическое оборудование, инструментальные средства и управление. Резервуар представляет собой многофункциональную часть теплообменника, также изготавливаемую с фиксирующими приспособлениями и удобными для доступа местами расположения собранных узлов, например, размещенных в резервуаре масляных охладителей и сенсорного оборудования. Также поскольку пластмассы существенно менее жестки по сравнению с алюминием, резервуар имеет толстые стенки и снабжена интегрированными наружными каркасами жесткости для получения достаточно высокой жесткости при кручении. Поэтому резервуар оказывается тяжелой, несмотря на то, что она изготовлена из материала низкой плотности. Однако жесткость может быть существенно повышена благодаря использованию нитевидного кристалла или армированию волокнами, однако это влечет за собой существенное повышение стоимости. При использовании CAC рабочая температура может превышать температуры, при которых пластмассы теряют слишком большую часть прочности для того, чтобы быть использованными на практике. Поэтому в настоящее время резервуары обычно изготавливают из алюминия. Наиболее часто такие резервуары изготавливают с использованием технологии литья под давлением, обычно ограничивающей толщину стенок резервуары в диапазоне более 1,5 мм, что увеличивает вес теплообменника. Литой алюминий также нелегко обжимать до коллектора, поэтому обычным способом соединения является MIG(дуговая сварка металлическим электродом в среде инертного газа) или TIG (дуговая сварка вольфрамовым электродом в среде инертного газа). Такой вид резервуары и способ соединения обычно позволяют собрать прочный узел. Однако сварка является дорогостоящей, отнимает много времени и существенно утяжеляет теплообменник, особенно при использовании резервуары с очень толстыми стенками, подвергаемыми сварке, при этом плита коллектора также должна быть толстой для того, чтобы выдержать качественное сварное соединение. Раскрытие изобретения Существует потребность в разработке эффективного и гибкого способа получения торцевых резервуаров. Настоящее изобретение относится к торцевым резервуарам, изготовленным из алюминиевых сплавов AA3XXX. Получение желаемых форм из группы сплавов, обычно используемых для торцевых резервуаров теплообменников, AA3XXX, способами, как правило, использовавшимися до настоящего времени для изготовления торцевых резервуаров, является затруднительным. Такие сплавы в литом и прокатанном состоянии не обладают формуемостью, необходимой для улучшенного формования торцевых резервуаров при комнатной температуре. Использовавшиеся ранее способы не в состоянии удовлетворить существующую в течение длительного времени потребность в торцевых резервуарах, которые могут быть подвергнуты пайке твердым припоем и иметь сложные формы. Согласно настоящему изобретению разработан способ изготовления таких торцевых резервуаров в результате осуществления стадий, раскрытых в прилагаемой формуле изобретения. Для осуществления успешного высококачественного формования материал обязательно должен иметь удлинение до разрыва, превышающее 20%. Согласно известным способам для получения очень хорошей формуемости слиток с сердцевиной из плакированного листового материала для пайки твердым припоем подвергают высокотемпературной гомогенизирующей обработке. Гомогенизирующая обработка позволяет получить микроструктуру, которая после горячей и холодной прокатки и отжига, при их правильном осуществлении, повышает формуемость полосы из сплава. Во время гомогенизации большая часть марганца, присутствующая в сплаве, осаждается, формируя большие дисперсоидные частицы, при этом некоторая часть потенциала прочности, обеспечиваемая марганцем в твердом растворе, теряется. Гомогенизирующая обработка может также отрицательно повлиять на коррозионную стойкость сплавовAA3XXX. Гомогенизация и отжиг также повышают стоимость материала по сравнению со всего лишь предварительным нагреванием перед горячей прокаткой. Поэтому желательно избегать гомогенизации и отжига сплавов, предназначенных для изготовления торцевых резервуаров в теплообменниках. Для того чтобы обеспечить высокую степень удлинения в условиях доставки материала, его подают в полностью размягченном О-состоянии или, иногда, в состоянии Н 112, т.е. отожженном состоянии. Такая операция также повышает стоимость материала для теплообменника. При изготовлении торцевых резервуаров для теплообменника способом согласно настоящему изобретению отсутствует необходимость гомогенизации сплава для трубы, что позволяет эффективно формовать трубы из негомогенизированного алюминиевого сплава. Кроме того, отсутствует необходимость отжига заготовки для трубы перед формованием, что делает данный способ еще более экономически выгодным. Настоящее изобретение относится к способу получения торцевого резервуара теплообменника,включающему следующие стадии: подготовку трубы, имеющей сердцевину, состоящую из алюминиевого сплава AA3XXX; необязательное предварительное нагревание трубы; вставку трубы в устройстве для формования, форма формующей полости которого соответствует форме готового торцевого резервуара; закупоривание концов трубы; нагревание трубы до температуры формования в том случае, если труба не была достаточно предварительно нагрета, и нагнетание давления внутри трубы с помощью газа таким образом, чтобы она приняла форму полости устройства, получая, таким образом, готовый торцевой резервуар; удаление торцевого резервуара из устройства; и охлаждение торцевого резервуара. Использование негомогенизированного материала для трубы позволяет получить улучшенные коррозионные и механические свойства. Стоимость не подвергнутой отжигу трубы ниже, при этом снижается наносимый окружающей среде вред. Таким образом, торцевой резервуар из негомогенизированного сплава AA3XXX, полученный в соответствии со способом согласно настоящему изобретению, обладает более высокой прочностью и улучшенной коррозионной стойкостью по сравнению с полученной в результате глубокой вытяжки торцевого резервуара, изготовленного из соответствующего, но гомогенизированного сплава AA3XXX. Сердцевина трубы может иметь по меньшей мере одну плакировку, состоящую из алюминиевого сплав, для улучшения способности к пайке твердым припоем. После формования в фасонного торцевого резервуара могут быть сделаны пазы для труб или соединений с целью облегчения производства теплообменника. Давление газа, используемого во время формования, может предпочтительно составлять более 85 бар, что обеспечивает эффективное формование трубы в формирующей полости устройства. При желании, к концам трубы во время ее формования может быть приложено аксиальное давление для подачи материала в формирующую полость во время формования. Кроме того, во время формирования трубы на ее концах формуют соединители, резьбу или анкеры с целью облегчения сборки теплообменника. В зависимости от формы резервуары и толщины алюминиевой заготовки может потребоваться давление более 200 бар. Труба, из которой формируют торцевой резервуар, может быть изготовлена из прокатанной заготовки из алюминиевого сплава, сваренной для получения трубы. Получение трубы таким способом является эффективным. Особенно предпочтительным является получение трубы из прокатанной, плакированной твердым припоем алюминиевой заготовки, поскольку такой способ является эффективным для получения плакированной твердым припоем трубы. Экструдирование плакированных твердым припоем труб является весьма дорогостоящим и чрезвычайно затруднительным. В качестве альтернативы, труба может быть изготовлена из экструдированного алюминиевого сплава, что является предпочтительным в некоторых ситуациях, в частности, когда труба не плакирована твердым припоем. Настоящее изобретение также относится к торцевому резервуару теплообменника, полученному вышеописанным способом газового формования горячего металла. Настоящее изобретение также относится к теплообменнику, включающему описываемый торцевой резервуар, в тех случаях, когда теплообменник имеет непрямоугольную форму. Настоящее изобретение также относится к способу получения теплообменника, согласно которому торцевой резервуар соединен с множеством труб и гофрированными ребрами, вставленными между трубами, с последующим припаиванием ребер к трубам. Газовое формование горячего металла позволяет получить конструкцию из алюминиевых торцевых резервуаров для теплообменников, изготовленных из сплавов AA3XXX, имеющих почти произвольную форму. Торцевые резервуары согласно настоящему изобретению для таких теплообменников имеют небольшой вес и могут быть оптимизированы с небольшими затратами по сравнению с конкурирующей технологией. Исключение пластмассовых резервуаров способствует более легкому извлечению материала. Геометрия поперечного сечения резервуаров может варьироваться в более широких пределах, чем при использовании конкурирующих способов формования алюминия, т.е. гидроформинга или глубокой вытяжки. Проведенные испытания на растяжение показали, что формуемость материала торцевых резервуаров существенно улучшается при повышении температуры формования, что означает, что удлинение до разрыва может повыситься до более 100% при повышении температуры до 400C по сравнению с 20-30% при комнатной температуре. Геометрия торцевого резервуара, изготовленного согласно настоящему изобретению, не ограничивается прямоугольными теплообменниками - возможны также неправильные формы. В частности, что касается формы, могут быть получены непрямоугольные теплообменники с большой гибкостью. Торцевые резервуары, изготовленные согласно настоящему изобретению, имеют очень высокий выход материала, более высокий, чем при используемой в настоящее время глубокой вытяжке или гидроформинге. Торцевые резервуары согласно настоящему изобретению облегчают экономическое производство теплообменников, что позволяет конструкторам автомобилей более эффективно размещать детали под капотом и одновременно открывает возможности для оптимизации теплообмена. Торцевые резервуары, изготовленные согласно настоящему изобретению, могут быть изготовлены с использованием материалов, имеющих более высокую прочность и более высокую коррозионную стойкость, при этом такие материалы могут быть получены более экологически безопасным способом в результате осуществления меньшего количества термомеханических операций по сравнению с конкурирующей технологией. Чертежи Варианты осуществления настоящего изобретения станут более понятны из следующего подробного описания в сочетании с прилагаемыми чертежами. Варианты осуществления настоящего изобретения проиллюстрированы примером и не ограничены фигурами, представленными на прилагаемых чертежах. Фиг. 1 представляет собой вид торцевого резервуара теплообменника в соответствии с одним вариантом осуществления настоящего изобретения. Фиг. 2 представляет собой вид торцевого резервуара теплообменника, показанной на фиг. 1, повернутой на 90. На фиг. 3 показан ряд конфигураций поперечных сечений труб для торцевых резервуаров согласно настоящему изобретению. На фиг. 4 показан схематический рисунок непрямоугольного теплообменника, включающего тор-3 022670 цевые резервуары, полученные согласно настоящему изобретению. На фиг. 5 показан боковой вид теплообменника согласно настоящему изобретению, в котором торцевой резервуар изогнут вдоль своей продольной оси. Подробное описание изобретения Торцевые резервуары согласно настоящему изобретению получают, осуществляя следующие технологические операции: i) пайка листового материала согласно стандартным промышленным способам;ii) сварка и возможное сгибание труб, изготовленных из паяных листов; iii) газовое формование горячего металла трубы в устройстве, внутренняя часть которого соответствует форме готового торцевого резервуара; iv) пробивание отверстий в проточных трубах и снабжение их соединительными деталями для присоединения к остальной части теплообменной системы. Лист для припоя состоит из материала сердцевины, который может быть плакирован по одной или обеим сторонам поверхности листа. Материал сердцевины выбирают из сплавов серии AA3XXX, имеющих температуры плавления более 610C, например АА 3003 или АА 3005. Плакировку для припоя обычно выбирают из низкоплавких доэвтектических сплавов АА 4XXX, например, АА 4343 и АА 4045. Кроме того, одна или обе стороны могут быть плакированы более чем одним материалом, т.е. может быть использовано так называемое мультиплакирование. Более того, в частности, на штрипсе труб для радиаторов и нагревателей, а также для других теплообменников плакировка может быть выполнена из электрохимически сбалансированного материала таким образом, чтобы он защищал сердцевину в коррозионных окружающих средах. Таким образом, могут быть плакированы одна или обе стороны, либо вовсе ни одна сторона материала сердцевины. Плакировка может включать один слой или два слоя на одной или обеих сторонах; плакировка может состоять из низкоплавкой пайки либо представлять собой защитную плакировку или плакировку, расположенную между пайкой и сердцевиной с целью снижения уровня взаимодействия между пайкой и сердцевиной, например, в результате диффузии. Плакировки наносят на сердцевину посредством горячей прокатки с последующей холодной прокаткой и необходимой термической обработкой для достижения нужных промежуточных и конечных состояний до продольной резки на отрезки нужной ширины. Изделия, изготовленные из листа для припоя, затем могут быть припаяны в результате управляемого атмосферного припаивания (CAB) или вакуумного припаивания. Сплавы 6XXX или 5XXX обычно используют для изделий, не предназначенных для припоя (с использованием CAB). Такие сплавы используют для изделий, которые должны обладать высокой прочностью, например строительные детали. Сплавы 6XXX или 5XXX приобретают высокую прочность благодаря высокому содержанию Mg. Припой с использованием CAB таких сплавов является затруднительным из-за реакции между магнием и флюсом. У производителей радиаторов, использующих управляемое атмосферное припаивание (CAB), при использовании доступных ранее материалов для сердцевин коллекторов возникают две основные проблемы, а именно, слишком низкая механическая прочность и слишком низкая коррозионная стойкость. АА 6063, поддающийся термической обработке сплав, содержание Mn в котором составляет около 0,7 вес.%, не считается пригодным для пайки в CAB процессе. АА 6060, содержащий около 0,4-0,5 вес.% Mg,пригоден для пайки, несмотря на то, что он требует использования большего количества флюса, специального флюса и специальной методики применения флюса, при этом прочность пайки в некоторых случаях является недостаточной. В AlMgSi сплавах во время старения формируются небольшие осадки Mg2Si, обеспечивающие повышение прочности. Таким образом, тривиальным решением для повышения прочности кажется увеличение содержания Mg и Si, обеспечивающее формирование большего количества Mg2Si. Однако поскольку Mg взаимодействует с флюсом во время пайки, что ограничивает содержание Mg, сплавы, имеющие содержание Mg более 0,4%, с трудом поддаются эффективной пайке в CAB. К тому же, упомянутые выше АА 6060 и АА 6063 обычно обладают низкой перфорационной коррозионной стойкостью из-за,например, межкристаллизационной коррозии. Сплавы 3XXX, максимальное содержание Mg в которых составляет 0,4%, могут быть подвергнуты пайке в CAB. Применение способа согласно настоящему изобретению устраняет трудности по приданию сплавам 3XXX желаемой формы. Таким образом, способ согласно настоящему изобретению позволяет выбирать сплавы 3XXX для торцевых резервуаров, что обеспечивает возможность пайки торцевого резервуара в CAB на более поздней стадии. Согласно настоящему изобретению одной из промежуточных деталей при изготовлении торцевого резервуара является труба. Для того чтобы получить возможность изготовления трубы из плакированного или неплакированного листа для припоя, необходимо изготовить из него сварную трубу. Фактический способ сварки может представлять собой индукционную сварку, MIG, TIG, сварку трением с перемешиванием или любой иной соответствующий способ сварки. Труба может иметь круглую, эллиптическую, квадратную, треугольную или любую другую соответствующую симметричную или асимметричную геометрию поперечного сечения. Труба может иметь постоянную или варьируемую геометрию поперечного сечения и размеры длины в зависимости от требований покупателя. Целесообразно, хотя и не всегда необходимо, выбирать поперечное сечение таким образом, чтобы избежать чрезмерных требований к деформации при последующей обработке. Также при сварке трубы таким образом, что геометрия поперечного сечения является постоянной на протяжении ее длины, выход материала теоретически составляет 100% во время операции сварки, за которой следует операция поперечной резки. Теплообменники, используемые в автомобильной промышленности, обычно имеют прямоугольную форму. Это приводит к ограничению относительно соответствующих позиций для комплекта теплообменника в автомобиле. В некоторых случаях идеальным для размещения такого комплекта в имеющемся под капотом пространстве является теплообменник круглой, изогнутой или ступенчатой формы, или даже неправильной формы для использования имеющегося под капотом пространства наилучшим образом с целью оптимизации эксплуатационных качеств теплообменника. В таких случаях желательным может оказаться использование теплообменника, имеющего форму,подходящую к имеющемуся в автомобиле пространству либо подходящую к желаемому режиму течения. Для такого теплообменника нужна специально спроектированный торцевой резервуар. Способ согласно настоящему изобретению позволяет формировать торцевые резервуары любой желательной формы в трех измерениях. Возможные формы включают, например, кольцеобразную форму, S-образную форму,L-образную форму или C-образную форму. Торцевой резервуар может быть изогнут или согнут вдоль его продольной оси и/или поперек его продольной оси. Проточные трубы прикрепляют в ряд вдоль длины торцевого резервуара, что означает, что весь теплообменник приобретает форму поперечного сечения, соответствующую форме торцевого резервуара. Таким образом, может возникнуть необходимость в непрямоугольном, например круговом, торцевом резервуаре, обусловленная компоновкой под капотом, производительностью теплообменника или просто требованиями заказчика. Такая необходимость может быть удовлетворена посредством сгибания сварной трубы, изготовленной из плакированного листа для припоя, до формы, имеющей соответствующий радиус или изгиб. В качестве альтернативы, может потребоваться S-образная, трапецеидальная или неправильная форма торцевого резервуара. При изготовлении согнутой или изогнутой резервуары труба может быть согнута до соответствующей предварительной формы до формирования горячим газом. Сгибание трубы может быть осуществлено любым способом, соответствующим конкретной получаемой форме. Сгибание может быть осуществлено при температуре окружающей среды или повышенной температуре для получения конкретной формы, необходимой для готового торцевого резервуара. Трубу, сваренную и согнутую в соответствии с требованиями заказчика, необязательно, нагревают любым подходящим способом, например в печи, пламенем или индукцией либо с помощью нагретого инструментального средства. Преимущество индукционного и пламенного нагрева заключается в том,что подвод тепла может быть локализован до выбранных участков трубы. Такой подвод может быть использован в качестве средства для варьирования механических свойств выбранных участков, поскольку известно, что температура материала является решающим фактором, влияющим на такие свойства как предел текучести, предел прочности на растяжение, удлинение до разрыва и формуемость. В зависимости от вида сплава состояния отпуска, толщины листа и деформации, необходимых для изготовления торцевого резервуара, желаемая температура формования может варьироваться от 250 до 550C. Трубу помещают в устройство для формования, изготовленное таким образом, что внутренние поверхности устройства соответствуют наружной геометрии готового торцевого резервуара. Устройство может быть холодным (например, иметь комнатную температуру), при этом труба должна быть подвергнута предварительному нагреванию, однако устройство предпочтительно нагревают до соответствующей повышенной температуры до формования или во время формования. Выбор устройства и температуры трубы определяются механическими свойствами и характеристиками формуемости материала трубы, а также конечной геометрией торцевого резервуара. Затем концы трубы закупоривают и трубу соединяют с газовой системой высокого давления. Во время формования труба имеет температуру от 250 до 550C. Такая температура формования может быть обеспечена посредством предварительного нагревания трубы до такой температуры до ее вставления в полость для формования либо предварительного нагревания устройства перед размещением в нем трубы,либо нагревания устройства, например, индукцией, во время формования. Давление газа внутри трубы повышают, что влияет на повышающееся давление в результате деформирования. Давление повышают до тех пор, пока труба не примет очертания поверхностей устройства. Фактическое конечное давление и скорость повышения давления газа определяются, среди прочего, механическими свойствами сплава трубы при данной температуре, толщиной стенок трубы, конечной формой торцевого резервуара и объемом деформации, необходимым для того, чтобы труба приняла желаемую форму. После формования находящийся под высоким давлением газ может быть выпущен, а сформованное изделие изъято из устройства. Газ может представлять собой воздух, азот, инертные газы либо любое иное соответствующее газообразное вещество. Давление во время формования является достаточно низким, намного ниже давления, используемого, например, при гидроформинге. Приблизительный верхний предел, составляющий 250 бар, является достаточным для придания материалу из алюминиевого сплава желаемой формы, необходимой для теплообменника. Благодаря ограниченному давлению во время фор-5 022670 мования резервуары, устройство для формования, используемое для получения торцевых резервуаров согласно настоящему изобретению, может быть изготовлено из иных материалов, чем материалы, используемые в устройствах согласно известным способам формования. После окончания формования сформованный продукт может быть охлажден на открытом воздухе или подвергнут резкому охлаждению в воде. Материал может быть также подан в устройство в результате приложения аксиального давления к концам трубы во время формования. Это может оказаться выгодным при получении труб с меньшей толщиной стенок после формования или для предотвращения повреждения труб при получении очень сложных профилей труб, требующих сильных локальных деформаций, например, острого радиуса или угла. Для того чтобы избежать прилипания трубы к поверхностям устройства, может понадобиться применение смазки для форм или высокотемпературного смазочного материала. Такая смазка может быть нанесена на трубу или на поверхности устройств перед формованием каждой новой трубы или в виде покрытия, требующего обновления только в редких случаях. Существует несколько способов получения пазов, необходимых для вставки, соединения и прикрепления труб. Один из способов включает пробивание пазов по отдельности, либо нескольких или всех пазов за один раз. Отверстия и пазы могут быть также профрезерованы или просверлены, или сформованы в результате обработки сформованного горячим газом изделия любым другим соответствующим способом. В качестве альтернативы отверстия могут быть пробиты во время осуществления более поздних стадий процесса формования горячим газом, после получения конечной формы трубы, когда давление горячего газа может обеспечить поддержку изнутри трубы для предотвращения разрушения в результате пробивания. Соединительные детали могут быть прикреплены к сформованному горячим газом изделию любым соответствующим способом, например, клепкой, пайкой, сваркой или приклеиванием. Выбор способа прикрепления зависит от потребностей покупателя, затрачиваемых средств, эксплуатационных качеств и от того, осуществляют ли прикрепление до или после пайки. Как проиллюстрировано на фиг. 2, торцевой резервуар может быть выполнен с углублениями для облегчения пробивания пазов в торцевом резервуаре. Для того чтобы обеспечить поступление газа в трубу во время формования горячим газом по меньшей мере одна из заглушек на конце трубы имеет отверстие, соединенное с находящейся под давлением газовой системой. До использования резервуара с целью теплообмена отверстие должно быть закрыто. Это может быть достигнуто несколькими способами. Во-первых, открытый конец трубы может быть закупорен благодаря прикреплению впускного и выпускного соединений для теплообменной среды, независимо от того, является ли она жидкой или газообразной. Во-вторых, он может быть закрыт герметиком, который может быть припаян, приварен или приклеен в данной позиции либо прикреплен любыми иными подходящими способами. В качестве альтернативы конец может быть закрыт в результате сжатия, а оставшиеся зазоры и щели могут быть заполнены соответствующим металлическим или полимерным наполнителем, обеспечивая не имеющее протечек закупоривание. Такие герметики могут быть нанесены любым соответствующим способом. Для облегчения соединения труб или шлангов может быть предусмотрено нарезание резьбы на конце трубы, на которую может быть накручен трубопровод. В качестве альтернативы могут быть сформированы анкеры для прикрепления шлангов с помощью зажимов. Описание предпочтительного варианта осуществления Более глубокому пониманию настоящего изобретения служит пример, иллюстрирующий его осуществление. Алюминиевый лист толщиной 3 мм из сплава АА 3003, плакированного АА 4343, сваривают, формируя трубу диаметром 40 мм. Трубу предварительно сгибают в виде угла и помещают в устройство,предварительно нагретое до 500C, имеющее такую же форму. Устройство заранее смазывают твердым смазывающим веществом, способным выдержать температуру формования без разложения. Концы трубы закупоривают и с помощью гидравлических цилиндров прилагают силу для того, чтобы предотвратить разъединение двух частей устройства. Давление газа, подаваемого внутрь трубы через одну из заглушек, повышают от 0 до 200 бар. Давление снижают после нескольких секунд выдерживания при максимальном давлении, после чего сформованную трубу удаляют из устройства и охлаждают, разбрызгивая на нее воду. Пазы пробивают в тех местах, где требуется соединение. Теперь труба приобретает окончательную форму торцевого резервуара с заранее сформированными пазами и утолщениями. После этого ребра теплообменника и проточные трубы могут быть соединены с резервуаром и спаяны для получения теплообменника. ФОРМУЛА ИЗОБРЕТЕНИЯ 1. Способ получения торцевого резервуара теплообменника, включающий следующие стадии, на которых:a) вставляют трубу, имеющую сердцевину из алюминиевого сплава AA3XXX, в устройство для формования, форма формующей полости которого соответствует форме готового торцевого резервуара;c) нагнетают давление внутри трубы с помощью газа таким образом, чтобы она приняла форму указанной полости устройства, получая в результате готовый торцевой резервуар, причем трубу предварительно нагревают перед вставкой в устройство для формования и/или после вставки в устройство для формования до температуры формования;d) удаляют торцевой резервуар из устройства;e) охлаждают торцевой резервуар. 2. Способ получения торцевого резервуара теплообменника по п.1, в котором используемый для трубы материал не был подвергнут гомогенизации. 3. Способ получения торцевого резервуара теплообменника по п.1 или 2, в котором труба не была подвергнута отжигу. 4. Способ получения торцевого резервуара теплообменника по п.2, в котором сердцевина трубы имеет по меньшей мере одну плакировку из алюминиевого сплава. 5. Способ получения торцевого резервуара теплообменника по любому из предыдущих пунктов, в котором пазы для труб или соединений сделаны в фасонном торцевом резервуаре во время или после формования. 6. Способ получения торцевого резервуара теплообменника по любому из предыдущих пунктов, в котором используемое давление газа составляет более 85 бар. 7. Способ получения торцевого резервуара теплообменника по любому из предыдущих пунктов, в котором аксиальное давление прикладывают к концам трубы во время ее формования. 8. Способ получения торцевого резервуара теплообменника по любому из предыдущих пунктов, в котором на конце трубы во время ее формирования формуют резьбу или анкеры. 9. Способ получения торцевого резервуара теплообменника по любому из предыдущих пунктов, в котором на стадии а) обеспечивают трубу, изготовленную из сварной заготовки. 10. Торцевой резервуар теплообменника, выполненный из трубчатой заготовки из негомогенизированного алюминиевого сплава AA3XXX с улучшенными коррозионными и механическими свойствами,имеющий трубчатую форму варьируемой геометрии вдоль всей длины и сформованный способом по пп.1-9. 11. Торцевой резервуар теплообменника по п.10, имеющий по меньшей мере одну плакировку из алюминиевого сплава. 12. Торцевой резервуар теплообменника по пп.10-11, в котором трубчатая заготовка вытянута более чем на 20%. 13. Торцевой резервуар теплообменника по пп.10-12, подходящий для управляемого атмосферного припаивания или вакуумного припаивания. 14. Торцевой резервуар теплообменника по любому из пп.10-13, имеющий любую желательную форму в трех измерениях, такую как одна из кольцеобразной формы, S-образной формы, L-образной формы, C-образной формы, трапецеидальной формы и неправильной формы. 15. Торцевой резервуар теплообменника по любому из пп.10-13, который является одним из специально спроектированного, изогнутого или согнутого вдоль его продольной оси и/или поперек его продольной оси. 16. Торцевой резервуар теплообменника по пп.10-15, имеющий пазы для труб или соединений, выполненные после формования по пп.1-9. 17. Теплообменник, включающий торцевой резервуар теплообменника по пп.10-16. 18. Теплообменник по п.17, имеющий непрямоугольную форму. 19. Теплообменник по п.18, имеющий одну из форм: круглую, изогнутую, ступенчатую или неправильную. 20. Способ получения теплообменника, включающий следующие стадии, на которых получают торцевой резервуар способом по пп.1-9; обеспечивают отверстия для проточных труб в торцевом резервуаре; соединяют множество проточных труб с торцевым резервуаром с помощью отверстий; вставляют ребра между проточными трубами; припаивают ребра к проточным трубам.
МПК / Метки
МПК: F28F 9/02, B21D 53/02, B21D 26/02
Метки: торцевых, способ, теплообменников, алюминиевых, формования, резервуаров
Код ссылки
<a href="https://eas.patents.su/9-22670-sposob-formovaniya-alyuminievyh-torcevyh-rezervuarov-teploobmennikov.html" rel="bookmark" title="База патентов Евразийского Союза">Способ формования алюминиевых торцевых резервуаров теплообменников</a>
Предыдущий патент: 1,2,5-оксадиазолы в качестве ингибиторов индоламин-2,3-диоксигеназы
Следующий патент: Композиция
Случайный патент: Способ лазерной резки хрупких прозрачных неметаллических материалов