Способ непрерывного выпаривания галогеноводородных кислот и воды из гидролизатов биомассы
Формула / Реферат
1. Способ непрерывного выпаривания галогеноводородных кислот и воды из гидролизатов биомассы, отличающийся тем, что содержащие воду и галогеноводород гидролизаты биомассы дозировано подают в емкость, частично заполненную непрерывно подогреваемым теплоносителем, выпарившиеся воду и галогеноводородные кислоты непрерывно отводят через головную часть емкости, в то время как образованные частицы гидролизата биомассы непрерывно удаляют сбоку или поверх отстойника и отделяют, при этом теплоноситель является химически инертным по отношению к загружаемым веществам, а в качестве теплоносителя применяют насыщенные углеводороды и/или их смеси, обладающие точкой кипения выше 150°С.
2. Способ по п.1, отличающийся тем, что в головной части емкости создают пониженное давление.
3. Способ по пп.1 и 2, отличающийся тем, что давление в головной части емкости составляет менее 0,1 бар.
4. Способ по п.1-3, отличающийся тем, что теплоноситель не смешивается с гидролизатом биомассы, образуя неоднородную жидкость.
5. Способ по пп.1-4, отличающийся тем, что гидролизат биомассы подают в емкость независимо от теплоносителя.
6. Способ по пп.1-5, отличающийся тем, что гидролизат биомассы подают над находящимся в емкости теплоносителем в газовую камеру емкости.
7. Способ по пп.1-5, отличающийся тем, что гидролизат биомассы подают в теплоноситель.
8. Способ по пп.1-7, отличающийся тем, что гидролизат биомассы подают в емкость тонко распределенным, что аппаратурно осуществляется через сопло.
9. Способ по пп.1-7, отличающийся тем, что гидролизат биомассы подают в емкость тонко распределенным, что аппаратурно осуществляется через систему из нескольких сопел.
10. Способ по пп.1-7, отличающийся тем, что гидролизат биомассы подают в емкость тонко распределенным, что аппаратурно осуществляется через расположенную кольцеобразно сопловую пластину.
11. Способ по пп.1-7, отличающийся тем, что гидролизат биомассы подают в емкость тонко распределенным, что аппаратурно осуществляется через пористое тело.
12. Способ по пп.1-7, отличающийся тем, что при применении сопел для подачи гидролизата биомассы осуществляется распыление двух веществ.
13. Способ по пп.1-12, отличающийся тем, что гидролизат биомассы подают в емкость таким образом, что возникает конвективный поток в находящемся в емкости теплоносителе.
14. Способ по пп.1-13, отличающийся тем, что уровень теплоносителя в емкости поддерживают постоянным посредством регулирования.
15. Способ по пп.1-14, отличающийся тем, что теплоноситель, в том числе частицы гидролизата биомассы, отводят через перелив или насос.
16. Способ по пп.1-15, отличающийся тем, что теплоноситель подают в газовую камеру емкости выше ввода гидролизата биомассы.
17. Способ по пп.1-16, отличающийся тем, что теплоноситель подают в емкость таким образом, что образуется конвективный поток в находящемся в емкости теплоносителе.
18. Способ по пп.1-17, отличающийся тем, что теплоноситель, содержащий частицы гидролизата биомассы, после выведения через боковую сторону или дно и после отделения частиц гидролизата биомассы возвращают в емкость.
19. Способ по пп.1-18, отличающийся тем, что потерю тепла в теплоносителе перед возвратом в емкость компенсируют за счет подвода тепла.
20. Способ по пп.1-19, отличающийся тем, что потерю тепла в теплоносителе перед возвратом в емкость частично компенсируют за счет подвода тепла, а полная компенсация осуществляется за счет дополнительного подвода тепла в саму емкость.
21. Способ по пп.1-20, отличающийся тем, что в качестве галогеноводородной кислоты используют соляную кислоту.
22. Способ по пп.1-21, отличающийся тем, что в качестве теплоносителя применяют полиальфаолефины, парафины и/или их смеси.
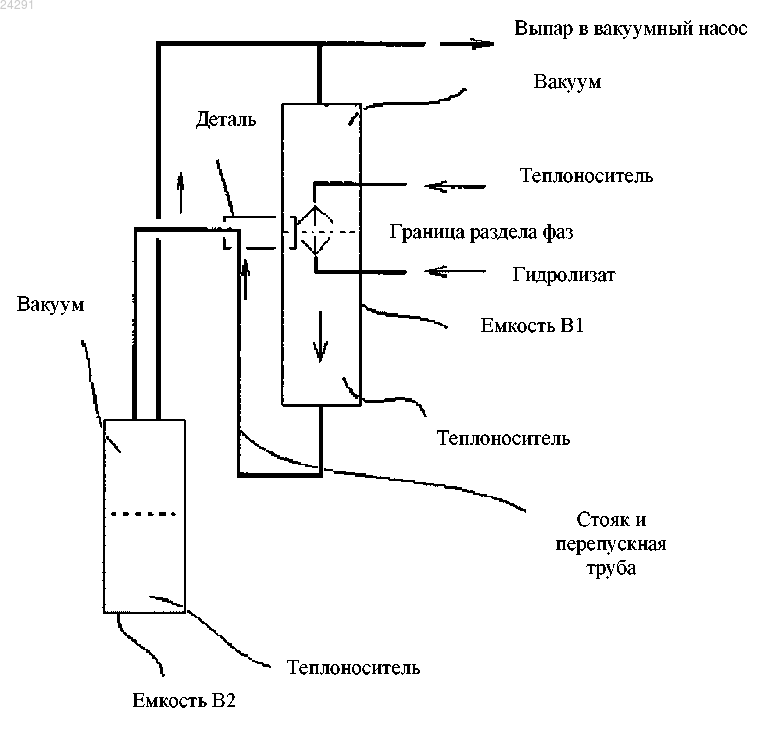
Текст
СПОСОБ НЕПРЕРЫВНОГО ВЫПАРИВАНИЯ ГАЛОГЕНОВОДОРОДНЫХ КИСЛОТ И ВОДЫ ИЗ ГИДРОЛИЗАТОВ БИОМАССЫ Изобретение относится к способу и устройству, с помощью которых галогеноводород и вода отделяются от гидролизатов биомассы, содержащих галогенокислоту. Преимуществами являются компактность устройства, эффективность в выпаривании и множество вариантов осуществления,что дает возможность приспособления к конкретной цели. Основу изобретения представляет вакуумированная емкость, которая постоянно заполняется теплоносителем и которая в одной части полностью заполнена теплоносителем (испарительная камера). В эту испарительную камеру также непрерывно подается гидролизат биомассы. В емкости происходит перенос тепла от теплоносителя на гидролизат, причем галогеноводород и вода постоянно выпариваются. Оставшиеся частицы гидролизата непрерывно выгружаются с охлажденным теплоносителем и непрерывно отделяются от теплоносителя. В отношении аппаратуры изобретение может характеризоваться разными вариантами осуществления. Описанное здесь изобретение может использоваться также для обработки других смесей и, соответственно, растворов с целью выпаривания. Основополагающим в отношении использованного теплоносителя является: он является химически инертным по отношению к загружаемым веществам; он плохо смешивается с загружаемыми веществами,так что обогащение не может продолжаться беспрепятственно (установление равновесия) и их беспрерывное присутствие не приводит к такой химической модификации теплоносителя, так что экономическая эксплуатация не может быть обоснована за счет частичной замены теплоносителя. Уровень техники То, что галогеноводородные кислоты и воду из гидролизатов можно выделять дистилляцией с помощью жидких теплоносителей, которые не смешиваются с гидролизатом, а также являются химически инертными, стало известно не позднее появления немецкого германского патента RP 362230 (опубликован 25-го октября 1922 г.). В этом патенте сказано, что "летучую соляную кислоту" вытесняют "известным образом с помощью подачи в сахарный раствор жидкого теплоносителя". "Для этой цели в раствор подают нагретое до высокой температуры масло, в частности сланцевое масло, которое практически не смешивается с сахарным раствором []. В результате вызванного таким образом повышения температуры сахарного раствора улетучивается соляная кислота, причем для подготовки часового количества 100 л сахарного раствора [] необходимо 1000 л циркулирующего масла". В отношении аппаратуры и технологического процесса этот принцип был усовершенствован с помощью впрыскивания гидролизата и теплоносителя в вакуумированный сосуд (патент DE 102008022242 А 1). Преимущества такого решения заключаются в следующем: соляная кислота попадает в теплоноситель, по существу, в незначительном количестве, так что отсутствует необходимость в предварительной обработке, как это описано в патенте 362230; доля энергии, которая необходима для вытеснения галогеноводородной кислоты из объемной доли теплоносителя, увеличилась. В соответствии с данными, приведенными в описании к патенту RP 362230, используемая для выпаривания полезная энергия составляет примерно 16,4 кДж на каждый литр используемого теплоносителя. В техническом решении в соответствии с усовершенствованным вариантом (патент DE 102008022242 А 1, дата подачи заявки 6-го мая 2008 года), используют, однако, примерно 50,7 кДж на каждый литр используемого для выпаривания теплоносителя. В результате этого можно в значительной мере сократить количество циркулирующего масла. Теперь было обнаружено, что представленную в патенте DE 102008022242 А 1 аппаратуру можно упростить за счет того, что отказались от циклона, который обозначен в патенте в качестве емкости 2. Эта модификация описана в патенте под названием "Modifizierte Apparatur zur Entfernung von Halogenwasserstoffsuren aus Biomassehydrolysaten". Недостаток аппаратного решения, в котором гидролизат и теплоноситель тщательно перемешиваются с помощью распыления, заключается в склонности к образованию эмульсии (так называемые осадки). По этой причине принцип был усовершенствован, причем были внесены следующие новшества: поток теплоносителя подается в камеру в виде замкнутой пленки на поверхность или пластину; применяют сверхгидрофильные материалы на поверхностях для лучшего распределения потоков жидкости; указанные изменения были объединены в виде осуществляющего наружное смешивание сопла для распыления двух веществ. На эти технические новшества была подана заявка на получения патента под названием "Verfahrenund Apparatur zur Entfernung von Halogenwasserstoff und Wasser aus Hydrolysaten" (номер дела 102010009310). Полезная для выпаривания доля энергии на единицу объема используемого теплоносителя в результате этого не была улучшена, но также и не ухудшена. Изобретение Неожиданно было обнаружено, что предыдущие недостатки уже описанного принципа можно устранить, аппаратное конструктивное исполнение упростить и выполнить более компактным и обеспечить,в частности, повышение эффективности в отношении количества энергии на единицу объема используемого теплоносителя. Описание изобретения Принцип изобретения будет пояснен с помощью фиг. 1. Здесь мы видим две емкости В 1 и В 2, которые сообщаются друг с другом с помощью стояка и перепускной трубы таким образом, что внизу труба выступает из В 1, затем сбоку вдоль В 1 поднимается вверх и там на определенной высоте, которая расположена под нижней кромкой верхней крышки емкости В 1, горизонтально изгибается (далее называется"изгиб") и затем сверху заходит в емкость В 2, причем В 2 (предпочтительно полностью) расположена под В 1. В обеих емкостях с помощью расположенных сверху отводов устанавливается вакуум (обычно 50 мбар). При первом пуске аппаратуры в соответствии с предлагаемым здесь способом теплый теплоноситель через направленное вниз сопло распыляется в емкость В 1. Емкость В 1 начинает заполняться и вместе с ней также стояк и перепускная труба. Если В 1 заполнится в такой мере, что будет достигнут изгиб,теплоноситель начинает перетекать в емкость В 2. Поверхность жидкости (далее граница раздела фаз) в В 1 между теплоносителем и вакуумом далее не поднимается. Происходит стабилизация потока теплоносителя, который протекает от сопла через В 1, стояк и перепускную трубу в В 2. При таком исполнении сопло для теплоносителя, хотя и расположено над границей раздела фаз, однако другое расположение в В 1 не было бы отрицательным для измерения уровня границы раздела фаз. При этом очень важно, чтобы горизонтальный участок стояка и перепускной трубы (далее "перелив") полностью не заполнялся. Такое дополнительное условие можно легко обеспечить в том случае, если геометрические параметры В 1(диаметр), стояка и перепускной трубы (также диаметр), а также объемный поток теплоносителя соот-1 024291 ветствующим образом согласованы друг с другом. Емкость В 2 в отношении показанного расположения представляет также только один (находящийся под вакуумом) сборник, так как собственно процесс выпаривания происходит в емкости В 1. Для этого после установки уровня границы раздела фаз подключают сопло, которое расположено под границей раздела фаз (следовательно, в пределах теплоносителя), через которое впрыскивается гидролизат. Сразу же над соплом для гидролизата образуется турбулентная зона, которая перемещается в результате того, что тонко распределенные в теплоносителе капельки гидролизата нагреваются и вытесняют галогеноводородный газ, а также водяной пар при образовании пузырьков. В этой зоне выпаривается примерно от двух третей до трех четвертей содержащегося количества жидкости. Оставшиеся теперь сиропообразные частицы выносятся потоком вниз. По пути вниз оставшееся количество жидкости выпаривается. С помощью такого принципа действия можно практически выпарить все количество галогеноводорода и воды. Таким образом, такой принцип действия обеспечивает, по меньшей мере, одинаковую эффективность выпаривания, как это имеет место в известных разработках. Предпочтительным является то, что в противоположность известным способам не образуется эмульсий. Частицы гидролизата осаждаются на дне в емкости В 2. Такой эффект достигался до настоящего времени только в том случае,если теплоноситель поступает в камеру в виде пленки или пластины. Описанное здесь изобретение проявляет наряду с этим другие существенные, дополнительные преимущества. Во-первых, аппаратурное осуществление способа значительно проще. При распылении в камере требуются емкости очень большого объема. Это соответствует принципу действия, который основан на том, что частицы гидролизата и теплоносителя после смешивания тонко распределяются в камере. Под действием ускорения свободного падения без торможения в вакууме впрыснутые частицы дополнительно ускоряются так быстро, что необходимо выдерживать соответствующую минимальную высоту. Если теплоноситель подводят в виде пленки, можно использовать емкости меньшего размера. Разумеется, что необходимые при этом встроенные элементы для достижения этого являются более сложными по сравнению с простыми соплами. Минимальный объем на расстоянии между всеми тремя альтернативными решениями можно обеспечить с помощью размещения согласно настоящему изобретению. Это связано с тем, что плотность энергии в зависимости от объемного элемента используемой испарительной камеры обусловленной замкнутой фазой теплоносителя является самой высокой. При использовании простых сопел можно использовать также простой и надежный способ загрузки. Во-вторых, полезное количество энергии, которое использовалась на каждую единицу объема теплоносителя для испарения, повышается минимум на 60 кДж/л. По сравнению с данными в патенте RP 362230 возникает уменьшение циркулирующего количества теплоносителя на коэффициент 3,6. Этот показатель был достигнут уже в неоптимизированных опытных установках. Необходимо исходить из дальнейшего снижения. Возможность для достижения этого кроется в простом увеличении времени пребывания частиц гидролизата в текущей среде. Этого можно достигнуть следующим образом. Одна из возможностей заключается в том, чтобы увеличить высоту емкости В 1 и расположить оба сопла на большей высоте. Это в определенных пределах можно легко осуществить, однако невозможно производить бесконечно, так как гидростатическое давление столба жидкости (теплоносителя) воздействует также и на выпаривание. Вторая возможность заключается в расширении стояка и перепускной трубы к емкости, в результате чего увеличивается время обработки. Диаметр расширенного стояка (и, следовательно, скорость потока) необходимо рассчитать таким образом, чтобы частицы переносились вверх и,таким образом, на изгибе снова достигали границы раздела фаз. Этот эффект уже был доказан при проведении опытов на основании метода градиента. При этом объемный поток гидролизата при неизменном потоке теплоносителя был соразмерно увеличен. Протекающий в стояке выпар удаляется из системы через отвод в емкости В 2. Оба принципа действия можно легко преобразовать с точки зрения аппаратуры. В-третьих, в показанном на фиг. 1 исполнении в конструкции предусмотрен зафиксированный режим для саморегулирования при перебросе кипящей жидкости и, соответственно, автоматическое прерывание. Для более четкого пояснения показанная на фиг. 1 деталь увеличена на фиг. 2 в виде эскиза. В случае, если турбулентная зона скачкообразно увеличится (так называемый "переброс кипящей жидкости"), например, в результате задержки кипения, уровень в емкости В 1 повысится также скачкообразно. Это означает, что уровень на переливе также повысится и происходит повышенное стекание теплоносителя. Одновременно подводимый поток теплоносителя в емкости В 1 остается без изменения. В итоге в емкости В 1 уменьшается количество теплоносителя, в результате чего прерывается перевар, так как общее количество тепловой энергии в В 1 снижается. Как только процесс выпаривания снова нормализуется, уровень теплоносителя будет ниже по сравнению с тем, как это имело место до переброса кипящей жидкости. Перелив в стояке и перепускной трубе также прекращается до тех пор, пока в емкости В 1 снова не будет установлен рабочий уровень. Таким образом, как очевидно, представленное расположение имеет разнообразные преимущества. Однако было обнаружено, что представленное расположение при изменении аппаратурных устройств нужно рассматривать значительно шире, чем это показано на фиг. 1. Фиг. 1 представляет, таким образом, "только" один вариант осуществления основополагающего принципа. Так, например, являются возможными и равноценны по эффективности следующие модификации: сопло для подачи гидролизата может быть направлено вниз над соплом для теплоносителя. Выпаривание происходит при совпадении обоих распыляющих конусов и при соприкосновении с границей раздела фаз; сопло для подачи гидролизата может направляться вверх над соплом для теплоносителя и осаждаться вторым, направленным вниз соплом для теплоносителя; в качестве устройства для подачи гидролизата не обязательно использовать только сопла. Здесь представлено несколько альтернативных решений простая трубка с отверстием,перфорированная пластина,трубка с насаженным пористым фильтром,трубка (кольцо) с перфорациями,сопла и, соответственно, устройства с соплами любого типа,вращающийся диск,двустенная трубка (внутри гидролизат, теплоноситель между внутренней и наружной стенкой) для поддержания равномерной температуры гидролизата перед загрузкой; гидролизат в подводящей трубе сопла для гидролизата уже частично выпарился. Это производится при соответствующем конструктивном исполнении и пропускании подводящей трубы через заполненную теплоносителем камеру (например, как это имеет место на фиг. 1). За счет предварительного выпаривания воды и галогеноводорода внутри сопла производится распыление двух веществ. Этот принцип действия известен, например, в баллонах для дезодоранта, при этом бутан выпаривается в пределах подвода к выпускному соплу и обеспечивает тончайшее распыление дезодоранта. Также согласно настоящему изобретению производится в результате этого более тонкое распределение гидролизата; осуществление устройства для подачи гидролизата в виде сопла не является обязательным согласно описанному здесь изобретению. Перед устройством для подачи можно предусмотреть смесительную аппаратуру, в которой гидролизат сразу смешивается с потоком теплоносителя и затем вводится в испарительную камеру по простой трубке. В измерительной камере теперь происходит только перенос тепла,включая выпаривание, но не распределение теплоносителя. Таким образом, согласно изобретению было обнаружено, что выпаривание связано с наличием замкнутой фазы теплоносителя, которая полностью заполняет выпарную емкость и в которой протекает выпаривание (главным образом и в конечном итоге) до полного удаления галогеноводорода и воды. Согласно изобретению теплоноситель не подводится к гидролизату (RP 362230), а гидролизат подводиться в замкнутую фазу и, следовательно, в теплоноситель. Далее часть камеры испарительной емкости, которая полностью заполняется теплоносителем, будет обозначаться как "испарительная камера". При осуществлении изобретения возможны другие варианты осуществления, так как для непрерывного принципа действия принципиальными являются следующие предпосылки: для выпаривания в испарительную камеру необходимо непрерывно подводить тепло; в испарительную камеру необходимо непрерывно подводить гидролизат; необходимо непрерывно отводить выпар в виде галогеноводорода и воды; частицы гидролизата и теплоноситель после выпаривания необходимо непрерывно отделять друг от друга. В качестве примера возникают аппаратные возможности выполнения для подвода тепла, в том случае, если: теплоноситель подводится в теплой форме, а отводится в холодной форме и нагревается за пределами испарительной камеры (косвенный нагрев); теплоноситель в измерительной камере нагревается путем наружного нагрева (например, нагрев стенок) (прямой нагрев); теплоноситель нагревается за счет сочетания прямого и косвенного нагрев. Если теплоноситель при прямом нагреве вводится, а также и выводится, то для осуществления этого возникают различные возможности. Например, теплоноситель может впрыскиваться над испарительной камерой и сливаться на дне (соответствует концепции на фиг. 1). В результате этого образуется направленный вниз вертикальный поток. Теплоноситель может подаваться также снизу с помощью разнообразных устройств для подачи и выгружаться через перелив на верхнем конце. В этом случае емкость В 1 и стояк и перепускная труба объединяются в одной емкости. Возникает направленный вертикально вверх поток теплоносителя. Возможна также боковая загрузка через сопла, которые расположены вдоль боковой стенки, в комбинации с выгрузкой через заходящую в испарительную камеру трубу. То, каким образом будет с аппаратной точки зрения выполнена загрузка и выгрузка, также не является основополагающим для достижения преимуществ согласно настоящему изобретению. Основополагающим является,напротив, полное заполнение испарительной камеры теплоносителем, который переносит тепло для выпаривания на гидролизат, и непрерывный подвод тепла в эту испарительную камеру. Является очевидным, что испарительная камера в зависимости от аппаратного выполнения может иметь различные фор-3 024291 мы. Например, трубчатая испарительная камера может конусообразно расширяться по направлению вверх в месте, в котором гидролизат подается в испарительную камеру. В результате выпаривания возникает сильное выделение газа, в том числе увеличение объема. Этот фактор учитывают, благодаря коническому расширению. Выпаренный газ легче поддается выпариванию. При другом аппаратном выполнении исходят из того, что подвод тепла происходит через нагрев стенок. Теперь внутри трубы, которая представляет собой испарительную камеру, поток теплоносителя образуется за счет того, что в измерительной камере аксиально расположена еще одна труба меньшего диаметра и в нее подается гидролизат. Эта труба полностью погружается в теплоноситель и может на своем верхнем и нижнем конце омываться теплоносителем. В пределах этой трубы теплоноситель охлаждается под действием выпаривания, а снаружи нагревается. Одновременно внутри трубы происходит выделение газа. В общей сложности образуется конвективный поток, который обеспечивает постоянную подачу тепла во внутреннюю трубу, а там - выпаривание. Для предотвращения возможного образования пены на поверхности теплоносителя его можно подавать в предварительно подогретом виде на поверхность. В общей сложности здесь возникает сочетание косвенного и прямого нагрева. Аппаратные возможности отвода гидролизата после его высвобождения из галогеноводорода и воды также являются такими же многогранными, как и проблема вообще. Так, например, допускается, чтобы теплоноситель внутри испарительной камеры вертикально подводился снизу вверх, а именно с такой скоростью потока, что частицы гидролизата, хотя и обладают более высокой плотностью, подавались вверх. В верхней области размещают сита, которые хоть и пропускают газ, но не пропускают частицы гидролизата. Если эти сита расположены под наклоном или формованы, то частицы могут проходить. При использовании трубы будет предпочтительной форма установленного на вершине конуса. Поток переносит частицы. На ситах происходит разделение газа и твердой фазы. Частицы подаются до оси емкости и падают там в аксиально расположенное под ситом приемное устройство, которое одновременно сообщается с трубой для непрерывного отвода частиц. Однако так же частицы гидролизата можно отводить из испарительной камеры также с охлажденным теплоносителем и там в отстойнике, и/или центрифуге, и/или гидроциклоне, и/или комбинации этих возможностей отделять от теплоносителя. Согласно этому аппаратное оформление выгрузки не является сущностью изобретения, а является всего лишь частью изобретения, а именно выражением необходимости подавать теплоноситель и гидролизат вместе для выпаривания в испарительной камере и после этого снова разделять. Если объединить все обязательно необходимые части, возникнет следующее сводное описание изобретения. Вакуумированная емкость составляет одну часть, называемую испарительной камерой, полностью заполняемой горячим, химически инертным теплоносителем, который не смешивается с гидролизатом. Гидролизат подается в испарительную камеру. В измерительной камере происходит выпаривание галогеноводорода и воды с помощью переноса тепла от теплоносителя на гидролизат. Образованный выпар отсасывается из расположенного над испарительной камерой пространства. Тепло непрерывно подводится в испарительную камеру и, соответственно, в находящийся там теплоноситель. Высвобожденные из галогеноводорода и воды частицы гидролизата непрерывно отделяются от теплоносителя и выгружаются. Описанный здесь способ согласно настоящему изобретению для непрерывного выпаривания жидкостей с целью отделения освободившихся составных веществ, свойства которых после выпаривания приводит к затруднениям в отношении используемой аппаратуры, не ограничивается только гидролизатом. Например, предлагаемое изобретение может использоваться также для отделения воды из морской воды с целью обессоливания. Соль часто образует в испарительных емкостях большую корку. С помощью настоящего изобретения соль в виде кристаллов соли удаляется из теплоносителя без возникновения таких затруднений с точки зрения аппаратуры. Однако можно разделять также и смеси. Например,ацетон и воду, так как они выпариваются при различных температурах. Вместо твердых частиц после выпаривания образуются две фазы из теплоносителя и невыпаренной жидкости. По умолчанию для работоспособности всегда предполагается химическая инертность теплоносителя, а также его плохая смешиваемость с остающейся фазой. Для более подробной характеристики этого "смешивания" будет достаточно знать, что обогащение веществ из поданных жидкостей не может продолжаться беспрепятственно(установление равновесия) и их беспрерывное присутствие не приводит к такой химической модификации теплоносителя, так что экономическая эксплуатация способа не может быть обоснована за счет частичной замены теплоносителя. ФОРМУЛА ИЗОБРЕТЕНИЯ 1. Способ непрерывного выпаривания галогеноводородных кислот и воды из гидролизатов биомассы, отличающийся тем, что содержащие воду и галогеноводород гидролизаты биомассы дозировано по-4 024291 дают в емкость, частично заполненную непрерывно подогреваемым теплоносителем, выпарившиеся воду и галогеноводородные кислоты непрерывно отводят через головную часть емкости, в то время как образованные частицы гидролизата биомассы непрерывно удаляют сбоку или поверх отстойника и отделяют,при этом теплоноситель является химически инертным по отношению к загружаемым веществам, а в качестве теплоносителя применяют насыщенные углеводороды и/или их смеси, обладающие точкой кипения выше 150 С. 2. Способ по п.1, отличающийся тем, что в головной части емкости создают пониженное давление. 3. Способ по пп.1 и 2, отличающийся тем, что давление в головной части емкости составляет менее 0,1 бар. 4. Способ по пп.1-3, отличающийся тем, что теплоноситель не смешивается с гидролизатом биомассы, образуя неоднородную жидкость. 5. Способ по пп.1-4, отличающийся тем, что гидролизат биомассы подают в емкость независимо от теплоносителя. 6. Способ по пп.1-5, отличающийся тем, что гидролизат биомассы подают над находящимся в емкости теплоносителем в газовую камеру емкости. 7. Способ по пп.1-5, отличающийся тем, что гидролизат биомассы подают в теплоноситель. 8. Способ по пп.1-7, отличающийся тем, что гидролизат биомассы подают в емкость тонко распределенным, что аппаратурно осуществляется через сопло. 9. Способ по пп.1-7, отличающийся тем, что гидролизат биомассы подают в емкость тонко распределенным, что аппаратурно осуществляется через систему из нескольких сопел. 10. Способ по пп.1-7, отличающийся тем, что гидролизат биомассы подают в емкость тонко распределенным, что аппаратурно осуществляется через расположенную кольцеобразно сопловую пластину. 11. Способ по п.1-7, отличающийся тем, что гидролизат биомассы подают в емкость тонко распределенным, что аппаратурно осуществляется через пористое тело. 12. Способ по пп.1-7, отличающийся тем, что при применении сопел для подачи гидролизата биомассы осуществляется распыление двух веществ. 13. Способ по пп.1-12, отличающийся тем, что гидролизат биомассы подают в емкость таким образом, что возникает конвективный поток в находящемся в емкости теплоносителе. 14. Способ по пп.1-13, отличающийся тем, что уровень теплоносителя в емкости поддерживают постоянным посредством регулирования. 15. Способ по пп.1-14, отличающийся тем, что теплоноситель, в том числе частицы гидролизата биомассы, отводят через перелив или насос. 16. Способ по пп.1-15, отличающийся тем, что теплоноситель подают в газовую камеру емкости выше ввода гидролизата биомассы. 17. Способ по пп.1-16, отличающийся тем, что теплоноситель подают в емкость таким образом, что образуется конвективный поток в находящемся в емкости теплоносителе. 18. Способ по пп.1-17, отличающийся тем, что теплоноситель, содержащий частицы гидролизата биомассы, после выведения через боковую сторону или дно и после отделения частиц гидролизата биомассы возвращают в емкость. 19. Способ по пп.1-18, отличающийся тем, что потерю тепла в теплоносителе перед возвратом в емкость компенсируют за счет подвода тепла. 20. Способ по пп.1-19, отличающийся тем, что потерю тепла в теплоносителе перед возвратом в емкость частично компенсируют за счет подвода тепла, а полная компенсация осуществляется за счет дополнительного подвода тепла в саму емкость. 21. Способ по пп.1-20, отличающийся тем, что в качестве галогеноводородной кислоты используют соляную кислоту. 22. Способ по пп.1-21, отличающийся тем, что в качестве теплоносителя применяют полиальфаолефины, парафины и/или их смеси.
МПК / Метки
МПК: C08H 8/00, B01D 1/16, C10G 3/00, C13K 1/00, B01D 1/14
Метки: галогеноводородных, непрерывного, биомассы, гидролизатов, воды, способ, выпаривания, кислот
Код ссылки
<a href="https://eas.patents.su/7-24291-sposob-nepreryvnogo-vyparivaniya-galogenovodorodnyh-kislot-i-vody-iz-gidrolizatov-biomassy.html" rel="bookmark" title="База патентов Евразийского Союза">Способ непрерывного выпаривания галогеноводородных кислот и воды из гидролизатов биомассы</a>
Предыдущий патент: Способ сепарации жидкости
Следующий патент: Новое антитело против ngf человека
Случайный патент: Полипропиленовая композиция, подходящая для нанесения покрытий экструзией