Способ получения медных порошков и нанопорошков из промышленных электролитов, в том числе отработанных промышленных электролитов
Формула / Реферат
1. Способ получения медных порошков и нанопорошков из растворов промышленных электролитов с концентрацией ионов меди выше 0,01 г×м-3, в том числе отработанных промышленных электролитов, путем электрохимического осаждения меди на катоде, в котором раствор подвергают потенциостатическому импульсному электролизу, используя диапазон катодного потенциала от -0,2 до -1 В по отношению к медному аноду; катодный ультрамикроэлектрод, содержащий золото, платину или нержавеющую сталь, или набор ультрамикроэлектродов, содержащих золото, платину или нержавеющую сталь; анод, содержащий металлическую медь, причем процесс осуществляют при температуре 18-60°C, а импульс электролиза длится в течение периода от 0,005 до 60 с.
2. Способ по п.1, отличающийся тем, что раствор электролита подвергают потенциостатическому электролизу в соответствии с одним или более из процессов, в которых:
а) имеется импульс катодного потенциала Ек в диапазоне от -0,2 до -1,0 В по отношению к медному аноду длительностью tк от 0,005 до 60 с,
b) имеется импульс катодного потенциала Ек в диапазоне от -0,2 до -1,0 В по отношению к медному аноду длительностью tк от 0,005 до 60 с, а затем импульс анодного потенциала Еа1 в диапазоне от 0,0 до +1,0 В по отношению к медному аноду длительностью ta1, более короткой на по меньшей мере 10%, чем длительность tk,
с) имеется импульс анодного потенциала Еа0 в диапазоне от 0,0 до +1,0 В по отношению к медному аноду длительностью ta0≤tк, а затем импульс катодного потенциала Ек в диапазоне от -0,2 до -1,0 В по отношению к медному аноду длительностью tк от 0,005 до 60 с,
d) имеется импульс анодного потенциала Еа0 в диапазоне от 0,0 до +1,0 В по отношению к медному аноду длительностью ta0≤tк, а затем импульс катодного потенциала Ек в диапазоне от -0,2 до -1,0 В по отношению к медному аноду длительностью tк от 0,005 до 60 с и последующий импульс анодного потенциала Ea1 длительностью ta1, более короткой на по меньшей мере 10%, чем tк.
3. Способ по п.1, при этом потенциостатический импульсный электролиз осуществляют с изменением направления тока.
4. Способ по п.1, при этом потенциостатический импульсный электролиз осуществляют без изменения направления тока.
5. Способ по п.1, при этом потенциостатический импульсный электролиз осуществляют, используя величину катодного потенциала, близкую к плато или на плато вольт-амперной характеристики, показанной на фиг. 1.
6. Способ по п.1, при этом ультрамикроэлектрод является подвижным ультрамикроэлектродом.
7. Способ по п.1, при этом ультрамикроэлектрод является неподвижным ультрамикроэлектродом.
8. Способ по п.1, при этом ультрамикроэлектрод имеет площадь набора от 1´10-6 до 10000 см2.
9. Способ по п.3, при этом анодный потенциал Еа0 составляет примерно 0,6 В.
10. Способ по п.9, при этом катодный потенциал Ек составляет примерно -0,4, -0,45 или -0,5 В.
11. Способ по п.9, при этом импульс анодного потенциала имеет место в течение периода (ta0) примерно 0,1 с.
12. Способ по п.10, при этом катодный потенциал Ек составляет примерно -0,4 В, а импульс катодного потенциала имеет место в течение периода (tк) примерно 0,1 с.
13. Способ по п.1, при этом ультрамикроэлектрод имеет диаметр 1-100 мкм.
14. Устройство для получения медных порошков и нанопорошков из растворов промышленных электролитов с концентрацией ионов меди выше 0,01 г×м-3, в том числе отработанных промышленных электролитов, путем электрохимического осаждения меди на катоде, содержащее средство для обеспечения потенциостатического импульсного электролиза; катодный ультрамикроэлектрод, содержащий золото, платину или нержавеющую сталь, или набор ультрамикроэлектродов, содержащих золото, платину или нержавеющую сталь; анод, содержащий металлическую медь; и средство для обеспечения температуры процесса 18-60°C, а также средство для поддержания импульсов электролиза от 0,005 до 60 с.
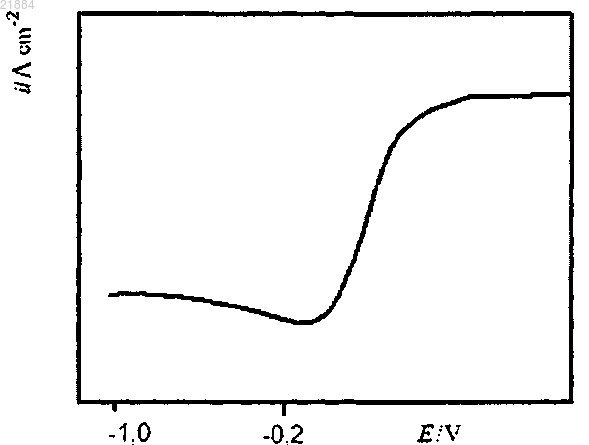
Текст
СПОСОБ ПОЛУЧЕНИЯ МЕДНЫХ ПОРОШКОВ И НАНОПОРОШКОВ ИЗ ПРОМЫШЛЕННЫХ ЭЛЕКТРОЛИТОВ, В ТОМ ЧИСЛЕ ОТРАБОТАННЫХ ПРОМЫШЛЕННЫХ ЭЛЕКТРОЛИТОВ Способ получения медных порошков и нанопорошков из промышленных электролитов, в том числе отработанных промышленных электролитов, путем электрохимического осаждения металлической меди на катоде заключается в использовании потенциостатического импульсного электролиза без изменения направления тока или с изменением направления тока, использовании величины катодного потенциала, близкой к плато или на плато вольт-амперной характеристики, на которой плато диапазона напряжения-тока составляет от -0,2 до -1 В, и в качестве катода используют подвижный или неподвижный ультрамикроэлектрод или набор ультрамикроэлектродов,изготовленных из проволоки или фольги из золота, платины или нержавеющей стали, тогда как в качестве анода используют металлическую медь, а процесс осуществляют при температуре 18-60C, и электролиз длится от 0,005 до 60 с. Указанный способ может быть использован для получения нанопорошков и порошков, характеризующихся воспроизводимостью структуры и размера частиц и чистотой от 99%+ до 99,999%, из отработанных промышленных электролитов и сточных вод медной промышленности и гальванических предприятий без дополнительной обработки. Объектом настоящего изобретения является способ получения медных порошков из промышленных электролитов, в том числе электролитов, которые являются отходами процесса нанесения гальванических покрытий, химической, горнодобывающей и металлургической промышленности. Сточные воды из процессов электрорафинирования и нанесения гальванических покрытий могут быть использованы в очень широком диапазоне назначений. Нанопорошки представляют собой очень ценные продукты, и их производство и применение является важной и развивающейся отраслью. Медные порошки и нанопорошки используют в качестве добавок к полимерам, смазкам, краскам,бактерицидным веществам и соединениям микропроцессоров. Нанопорошки из меди или ее сплавов могут быть применены в микроэлектронике и в качестве сорбентов при очистке радиоактивных отходов, а также как катализаторы в топливных элементах. Нанопорошки могут представлять собой частицы металла, оксида металла или органического комплекса меньше микрометра (по меньшей мере один линейный размер). Из-за необходимости соответствия требованиям к материалам, используемым в различных областях технологии материалов, существенно производство нанопорошков с четкой заданной структурой и регулируемым размером частиц. Одним из используемых в настоящее время способов получения медных нанопорошков является способ электрохимического восстановления (электроосаждения). Электролитическое производство наноструктурированной фольги и отложений представлено в других патентах. Например, в патенте CN 1710737/2005 была получена медная фольга, выполненная из нанокристаллов меди размером примерно 150 нм в процессе электролиза постоянным током при следующих условиях: металлический катод, температура 25-65C, скорость течения электролита 0,5-5,0 м/с, плотность катодного тока 0,5-5,0 А/см 2. Электролит содержал следующие добавки: 1-15 мг/л тиомочевины, 1-15 мг/л животного клея, 0,1-5,0 мг/л хлорид-ионов и другие. Электролитический способ был представлен в патенте US 2006/0021878. Данный способ получения меди с высокой твердостью и хорошей электропроводностью заключается в импульсном электролизе. Способ осуществляли в следующих условиях: рН от 0,5 до 0,1; электролит - сульфат меди полупроводниковой чистоты; металлический катод, анод - медь с чистотой 99,99%, температура от 15 до 30C; длительность катодного импульса от 10 до 50 мс; длительность выключения тока от 1 до 3 с; плотность катодного тока от 40 до 100 мА/см 2. Раствор перемешивался при помощи магнитной мешалки и содержал следующие добавки: от 0,02 до 0,2 мл/л животного клея и от 0,2 до 1 мл/л NaCl. Из рассмотрения вышеуказанных известных из уровня техники электрохимических способов получения медных нанопорошков ясно, что они требуют дорогостоящей подготовки подложки (растворов,реагентов надлежащей чистоты, восстановителей и других реагентов). Эти процессы настолько сложны и дороги, что рыночные цены нанопорошков очень высоки. Одним из фундаментальных условий, гарантирующих технологическую осуществимость и рентабельность извлечения металла из промышленных электролитов с низкой концентрацией осаждаемых элементов, является обеспечение достаточных скоростей массопереноса электроосаждаемых ионов к электроду. Таким образом, увеличиваются производительность и эффективность процесса производства нанопорошка. Настоящее изобретение решает проблему необходимости использования электролита надлежащей чистоты и концентрации и использования дополнительных электролитов и других веществ. Неожиданно было обнаружено, что медные порошки и нанопорошки могут быть получены из растворов промышленных электролитов, в том числе сточных вод, если они подвергаются потенциостатическому импульсному электролизу без изменения направления тока и с изменением направления тока при использовании ультрамикроэлектродов. Способ получения медных порошков и нанопорошков из промышленных электролитов и сточных вод путем электроосаждения металлической меди на катоде в соответствии с указанным изобретением заключается в том, что раствор электролита с концентрацией ионов меди выше 0,01 гдм-3 подвергают потенциостатическому импульсному электролизу без изменения направления тока или с изменением направления тока, используя величину катодного потенциала, близкую к плато или на плато вольтамперной характеристики, показанной на фиг. 1, на которой плато диапазона напряжения-тока составляет от -0,2 до -1 В, в качестве катода используют подвижный или неподвижный ультрамикроэлектрод или набор ультрамикроэлектродов, изготовленных из проволоки или фольги из золота, платины или нержавеющей стали, тогда как в качестве анода используют металлическую медь, а процесс осуществляют при температуре от 18-60C, и электролиз длится от 0,005 до 60 с. Преимущество способа по изобретению заключается в том, что раствор электролита подвергают потенциостатическому электролизу, как показано на фиг. 2 от а) до d), на которых фиг. 2 а) показывает импульс катодного потенциала Ек в диапазоне от -0,2 до -1,0 В по отношению к медному электроду длительностью tк от 0,005 до 60 с,фиг. 2b) показывает импульс катодного потенциала Ек в диапазоне от -0,2 до -1,0 В по отношению к медному электроду длительностью tк от 0,005 до 60 с, а затем импульс анодного потенциала Ea1 в диапазоне от 0,0 до +1,0 В по отношению к медному электроду длительностью ta1, более короткой на по мень-1 021884 шей мере 10%, чем длительность tk,фиг. 2 с) показывает импульс анодного потенциала Еа 0 в диапазоне от 0,0 до +1,0 В по отношению к медному электроду длительностью ta0tк, а затем импульс катодного потенциала Eк в диапазоне от -0,2 до -1,0 В по отношению к медному электроду длительностью tк от 0,005 до 60 с,фиг. 2d) показывает импульс анодного потенциала Еа 0 в диапазоне от 0,0 до +1,0 В по отношению к медному электроду длительностью ta0tк, а затем импульс катодного потенциала Ек в диапазоне от -0,2 до-1,0 В по отношению к медному электроду длительностью tк от 0,005 до 60 с и последующий импульс анодного потенциала Ea1 длительностью ta1, более короткой на по меньшей мере 10%, чем tк. Процесс катодного восстановления меди регулируют посредством диффузии ионов к электроду, что в указанном способе достигается за счет использования ультрамикроэлектродов или набора ультрамикроэлектродов и осуществления потенциостатического электролиза при катодном потенциале, близком к плато или на плато вольт-амперной характеристики (фиг. 1). Указанный процесс электролиза можно исследовать при помощи хроноамперометрии, состоящей в измерении тока как функции времени при постоянном потенциале, прикладываемом к электроду. Диаметр проволочных ультрамикроэлектродов, используемых в указанном способе, может составлять от 1 до 100 мкм. Площадь набора ультрамикроэлектродов может составлять от 110-6 до 10000 см 2. Площадь набора ультрамикроэлектродов в форме пластин может составлять от 1 до 10000 см 2. При использовании подвижных электродов то время, в течение которого они остаются в электролите, равно длительности одного цикла электролиза. При использовании неподвижных электродов то время, в течение которого они остаются в электролите, равно длительности одного цикла электролиза. После каждого цикла электрод извлекают из раствора и погружают в раствор электролита новый электрод. Продукт электролиза, т.е. порошки или нанопорошки, может быть удален с поверхности электрода с использованием струйного потока либо инертного газа, либо жидкости, или же он может быть удален с поверхности электрода механически с использованием собирающего устройства с острым краем, изготовленного, например, из тефлона. Используя указанный электрохимический способ, медные порошки и нанопорошки, характеризующиеся воспроизводимостью структуры и размера частиц, получают из растворов промышленных электролитов, в том числе отработанных промышленных электролитов и сточных вод медной промышленности и гальванических предприятий. Используя указанный способ, можно получить медные нанопорошки с чистотой от 99%+ до 99,999% из отработанных промышленных электролитов и сточных вод без дополнительной обработки. Он позволяет в промышленном масштабе получать нанопорошки с существенно уменьшенными затратами. Используя указанный способ, получают порошки или нанопорошки с различными формами, структурой и размерами в зависимости от размера электрода, металла, из которого изготовлен электрод, условий, при которых осуществляют электролиз, и, особенно, типа электролиза (фиг. 2,подпункты a-d), температуры и концентрации меди в электролите. Получение медных нанопорошков и порошков с использованием указанного способа показано на следующих примерах. Пример I. Рабочий ультрамикроэлектрод из платиновой проволоки, диаметр которой составляет 10 мкм, служащий катодом, и электрод сравнения (анод) в виде медной пластины, площадь которой составляет 0,3 см 2, а ее толщина составляет 0,1 см, поместили в электрохимическую ячейку, термостатированную до 25C. Ячейку заполнили использованным при электрорафинировании меди промышленным электролитом, состоящим из 46 гдм-3 Cu, 170-200 гдм-3 H2SO4, Ni, As, Fe (1000 мгдм-3), Cd, Co, Bi, Ca, Mg, Pb, Sb (от 1 до 1000 мгдм-3) иAg, Li, Mn, Pd, Rh (1 мгдм-3), а также животного клея и тиомочевины (1 мгдм-3). Электроды соединили с измерительным устройством - потенциостатом Autolab GSTST30, работающим под управлением персонального компьютера (ПК) с программным обеспечением GPES от Eco Chemie, при помощи миниатюрного байонетного соединителя (BNC). Параметры процесса были следующими: Еа 0=0,6 В ta0=0,1 c. Ек=-0,4 В tк=0,1 c. После электрохимического осаждения меди на электроде исследовали структуру и размеры осажденного порошка, используя сканирующий электронный микроскоп, и установили, что полученное отложение имеет форму трубок длиной примерно 250 нм и шириной примерно 50-70 нм. На основании анализа спектра рассеяния энергии (EDS) было установлено, что имеются только линии, характерные для меди, что говорит о чистоте полученного продукта. Пример II. Рабочий ультрамикроэлектрод из платиновой проволоки, диаметр которой составляет 10 мкм, служащий катодом, и электрод сравнения (анод) в виде медной пластины, площадь которой составляет 0,3 см 2, а ее толщина составляет 0,1 см, поместили в электрохимическую ячейку, термостатированную до 25C. Ячейку заполнили использованным при электрорафинировании меди промышленным электролитом, состав которого приведен в примере I. Электроды соединили с измерительным устройством - по-2 021884 тенциостатом, работающим под управлением персонального компьютера (ПК) со специальным программным обеспечением. Параметры процесса были следующими: Еа 0=0,6 В ta0=0,1 с. Ек=-0,4 В tк=0,125 с. После электрохимического осаждения меди на электроде исследовали структуру и размеры осажденного порошка, используя сканирующий электронный микроскоп, и установили, что полученное отложение имеет форму трубок длиной примерно 600 нм и шириной примерно 60-120 нм. На основании анализа спектра рассеяния энергии (EDS) было установлено, что имеются только линии, характерные для меди. Пример III. Рабочий ультрамикроэлектрод из платиновой проволоки, диаметр которой составляет 100 мкм, служащий катодом, и электрод сравнения (анод) в виде медной пластины, площадь которой составляет 0,3 см 2, а ее толщина составляет 0,1 см, поместили в электрохимическую ячейку, термостатированную до 25C. Ячейку заполнили использованным при электрорафинировании меди промышленным электролитом, состав которого приведен в примере I. Электроды соединили с измерительным устройством - потенциостатом, работающим под управлением персонального компьютера (ПК) со специальным программным обеспечением. Параметры процесса были следующими: Еа 0=0,6 В ta0=0,1 с. Ек=-0,4 В tк=0,1 с. После электрохимического осаждения меди на электроде исследовали структуру и размеры осажденного порошка, используя сканирующий электронный микроскоп, и установили, что полученное отложение имеет форму крупных кристаллитов с диаметром зерна примерно 200-600 нм. На основании анализа спектра рассеяния энергии (EDS) было установлено, что имеются только линии, характерные для меди. Пример IV. Рабочий ультрамикроэлектрод из золотой проволоки, диаметр которой составляет 10 мкм, служащий катодом, и электрод сравнения (анод) в виде медной пластины, площадь которой составляет 0,3 см 2, а ее толщина составляет 0,1 см, поместили в электрохимическую ячейку, термостатированную до 25C. Ячейку заполнили использованным при электрорафинировании меди промышленным электролитом, состав которого приведен в примере I. Электроды соединили с измерительным устройством потенциостатом, работающим под управлением персонального компьютера (ПК) со специальным программным обеспечением. Параметры процесса были следующими: Еа 0=0,6 В ta0=0,1 с. Ек=-0,4 В tк=0,125 с. После электрохимического осаждения меди на электроде исследовали структуру и размеры осажденного порошка, используя сканирующий электронный микроскоп, и установили, что полученное отложение имеет форму крупных кристаллитов с диаметром зерна примерно 150 нм. На основании анализа спектра рассеяния энергии (EDS) было установлено, что имеются только линии, характерные для меди. Пример V. Рабочий ультрамикроэлектрод из золотой проволоки, диаметр которой составляет 40 мкм, служащий катодом, и электрод сравнения (анод) в виде медной пластины, площадь которой составляет 0,3 см 2, а ее толщина составляет 0,1 см, поместили в электрохимическую ячейку, термостатированную до 25C. Ячейку заполнили использованным при электрорафинировании меди промышленным электролитом, состав которого приведен в примере I. Электроды соединили с измерительным устройством потенциостатом, работающим под управлением персонального компьютера (ПК) со специальным программным обеспечением. Параметры процесса были следующими: Еа 0=0,6 В ta0=0,1 c. Ек=-0,4 В tк=0,5 с. После электрохимического осаждения меди на электроде исследовали структуру и размеры осажденного порошка, используя сканирующий электронный микроскоп, и установили, что полученное отложение имеет сферическую форму с диаметром примерно 250-300 нм. На основании анализа спектра рассеяния энергии(EDS) было установлено, что имеются только линии, характерные для меди. Пример VI. Рабочий ультрамикроэлектрод из золотой проволоки, диаметр которой составляет 40 мкм, служащий катодом, и электрод сравнения (анод) в виде медной пластины, площадь которой составляет 0,3 см 2, а ее толщина составляет 0,1 см, поместили в электрохимическую ячейку, термостатированную до 25C. Ячейку заполнили использованным при электрорафинировании меди промышленным электролитом, состав которого приведен в примере I. Электроды соединили с измерительным устройством потенциостатом, работающим под управлением персонального компьютера со (ПК) специальным программным обеспечением. Параметры процесса были следующими: После электрохимического осаждения меди на электроде исследовали структуру и размеры осажденного порошка, используя сканирующий электронный микроскоп, и установили, что полученное отложение имеет сферическую форму с диаметром примерно 250-300 нм. На основании анализа спектра рассеяния энергии(EDS) было установлено, что имеются только линии, характерные для меди. Пример VII. Рабочий ультрамикроэлектрод в виде проволоки из нержавеющей стали, диаметр которой составляет 25 мкм, служащий катодом, и электрод сравнения (анод) в виде медной пластины, площадь которой составляет 0,3 см 2, а ее толщина составляет 0,1 см, поместили в электрохимическую ячейку, термостатированную до 25C. Ячейку заполнили использованным при электрорафинировании меди промышленным электролитом,состав которого приведен в примере I. Электроды соединили с измерительным устройством - потенциостатом, работающим под управлением персонального компьютера (ПК) со специальным программным обеспечением. Параметры процесса были следующими:Ea=0,6 В ta0=0,1 с. Ек=-0,4 В tк=0,05 с и t=0,075 с. После электрохимического осаждения меди на электроде исследовали структуру и размеры осажденного порошка, используя сканирующий электронный микроскоп, и установили, что полученное отложение имеет сферическую форму. Диаметр зерна составил примерно 300 нм для t=0,05 с и примерно 400 нм для t=0,075 с. На основании анализа спектра рассеяния энергии (EDS) было установлено, что имеются только линии, характерные для меди. Пример VIII. Рабочий ультрамикроэлектрод в виде проволоки из нержавеющей стали, диаметр которой составляет 25 мкм, служащий катодом, и электрод сравнения (анод) в виде медной пластины, площадь которой составляет 0,3 см 2, а ее толщина составляет 0,1 см, поместили в электрохимическую ячейку, термостатированную до 25C. Ячейку заполнили использованным при электрорафинировании меди промышленным электролитом,состав которого приведен в примере I. Электроды соединили с измерительным устройством - потенциостатом, работающим под управлением персонального компьютера (ПК) со специальным программным обеспечением. Параметры процесса были следующими: Еа=0,6 В ta0=0,1 с.Ek=-0,45 В tk=0,05 с и t=0,075 с. После электрохимического осаждения меди на электроде исследовали структуру и размеры осажденного порошка, используя сканирующий электронный микроскоп, и установили, что полученное отложение имеет сферическую форму. Диаметр зерна составил примерно 200 нм для t=0,05 с и примерно 550 нм для t=0,075 с. На основании анализа спектра рассеяния энергии (EDS) было установлено, что имеются только линии, характерные для меди. Пример IX. Рабочий ультрамикроэлектрод в виде проволоки из нержавеющей стали, диаметр которой составляет 25 мкм, служащий катодом, и электрод сравнения (анод) в виде медной пластины, площадь которой составляет 0,3 см 2, а ее толщина составляет 0,1 см, погрузили в такой же промышленный электролит, как в примере I, с содержанием Cu 46 гдм-3, помещенный в электрохимическую ячейку, термостатированную до 25C. Электроды соединили с измерительным устройством - потенциостатом, работающим под управлением персонального компьютера (ПК) со специальным программным обеспечением. Параметры процесса были следующими: Еа=0,6 В ta0=0,1 с. Ек=-0,5 В tк=0,05 с и t=0,075 с. После электрохимического осаждения меди на электроде исследовали структуру и размеры осажденного порошка, используя сканирующий электронный микроскоп, и установили, что полученное отложение имеет сферическую форму. Диаметр зерна составил примерно 600-700 нм для t=0,05 с и примерно 700-800 нм дляt=0,075 с. На основании анализа спектра рассеяния энергии (EDS) было установлено, что имеются только линии, характерные для меди. Пример X. Рабочий ультрамикроэлектрод в виде проволоки из нержавеющей стали, диаметр которой составляет 25 мкм, служащий катодом, и электрод сравнения (анод) в виде медной пластины, площадь которой составляет 0,3 см 2, а ее толщина составляет 0,1 см, поместили в электрохимическую ячейку, термостатированную до 25C. Ячейку заполнили использованным при электрорафинировании меди промышленным электролитом,состав которого приведен в примере I. Электроды соединили с измерительным устройством - потенциостатом, работающим под управлением персонального компьютера (ПК) со специальным программным обеспечением. Параметры процесса были следующими: После электрохимического осаждения меди на электроде исследовали структуру и размеры осажденного порошка, используя сканирующий электронный микроскоп, и установили, что полученное отложение имеет сферическую форму с разной структурой. Диаметр зерна составил в диапазоне 200-1200 нм. На основании анализа спектра рассеяния энергии (EDS) было установлено, что имеются только линии, характерные для меди. Пример XI. Катод - пластину из нержавеющей стали площадью примерно 1 см 2 и анод в виде медной пластины площадью 0,3 см 2 и толщиной 0,1 см погрузили в промышленный электролит, состав которого приведен в примере I. Электроды соединили с измерительным устройством - потенциостатом, работающим под управлением персонального компьютера (ПК) со специальным программным обеспечением. Параметры процесса были следующими: Ек=-0,4 В tк=1 с, tк=15 с, tк=30 с, tк=60 с. После электрохимического осаждения меди на электроде исследовали структуру и размеры осажденного порошка, используя сканирующий электронный микроскоп, и установили, что полученное отложение имеет сферическую форму с разной структурой. Размеры полученных агломератов составили соответственно: примерно 5-10 мкм, 2,5-3 мкм, 1-2 мкм, 0,2-0,5 мкм для следующих длительностей 60, 30, 15, 1 с соответственно. На основании анализа спектра рассеяния энергии (EDS) было установлено, что имеются только линии,характерные для меди. Пример XII. Рабочий ультрамикроэлектрод в виде проволоки из нержавеющей стали, диаметр которой составляет 25 мкм, служащий катодом, и электрод сравнения (анод) в виде медной пластины, площадь которой составляет 0,3 см 2, а ее толщина составляет 0,1 см, поместили в электрохимическую ячейку, термостатированную до 25C. Ячейку заполнили использованным при электрорафинировании меди промышленным электролитом,состоящим из 0,189 гдм-3 Cu, 170-200 гдм-3 H2SO4, Ni, As, Fe (1000 мгдм-3), Cd, Co, Bi, Ca, Mg, Pb, Sb (от 1 до 1000 мгдм-3) и Ag, Li, Mn, Pd, Rh (1 мгдм-3), а также животного клея и тиомочевины. Электроды соединили с измерительным устройством - потенциостатом, работающим под управлением персонального компьютера (ПК) со специальным программным обеспечением. Параметры процесса были следующими: Ек=-0,40 В tк=0,5 с. После электрохимического осаждения меди на электроде исследовали структуру и размеры осажденного порошка, используя сканирующий электронный микроскоп, и установили, что полученное отложение имеет сферическую форму с разной структурой. Диаметр зерна составлял в диапазоне от 350 нм до 2,5 мкм. На основании анализа спектра рассеяния энергии (EDS) было установлено, что имеются только линии, характерные для меди. ФОРМУЛА ИЗОБРЕТЕНИЯ 1. Способ получения медных порошков и нанопорошков из растворов промышленных электролитов с концентрацией ионов меди выше 0,01 гм-3, в том числе отработанных промышленных электролитов,путем электрохимического осаждения меди на катоде, в котором раствор подвергают потенциостатическому импульсному электролизу, используя диапазон катодного потенциала от -0,2 до -1 В по отношению к медному аноду; катодный ультрамикроэлектрод, содержащий золото, платину или нержавеющую сталь, или набор ультрамикроэлектродов, содержащих золото, платину или нержавеющую сталь; анод,содержащий металлическую медь, причем процесс осуществляют при температуре 18-60C, а импульс электролиза длится в течение периода от 0,005 до 60 с. 2. Способ по п.1, отличающийся тем, что раствор электролита подвергают потенциостатическому электролизу в соответствии с одним или более из процессов, в которых: а) имеется импульс катодного потенциала Ек в диапазоне от -0,2 до -1,0 В по отношению к медному аноду длительностью tк от 0,005 до 60 с,b) имеется импульс катодного потенциала Ек в диапазоне от -0,2 до -1,0 В по отношению к медному аноду длительностью tк от 0,005 до 60 с, а затем импульс анодного потенциала Еа 1 в диапазоне от 0,0 до+1,0 В по отношению к медному аноду длительностью ta1, более короткой на по меньшей мере 10%, чем длительность tk,с) имеется импульс анодного потенциала Еа 0 в диапазоне от 0,0 до +1,0 В по отношению к медному аноду длительностью ta0tк, а затем импульс катодного потенциала Ек в диапазоне от -0,2 до -1,0 В по отношению к медному аноду длительностью tк от 0,005 до 60 с,d) имеется импульс анодного потенциала Еа 0 в диапазоне от 0,0 до +1,0 В по отношению к медному аноду длительностью ta0tк, а затем импульс катодного потенциала Ек в диапазоне от -0,2 до -1,0 В по отношению к медному аноду длительностью tк от 0,005 до 60 с и последующий импульс анодного потенциала Ea1 длительностью ta1, более короткой на по меньшей мере 10%, чем tк. 3. Способ по п.1, при этом потенциостатический импульсный электролиз осуществляют с изменением направления тока. 4. Способ по п.1, при этом потенциостатический импульсный электролиз осуществляют без изменения направления тока. 5. Способ по п.1, при этом потенциостатический импульсный электролиз осуществляют, используя величину катодного потенциала, близкую к плато или на плато вольт-амперной характеристики, показанной на фиг. 1. 6. Способ по п.1, при этом ультрамикроэлектрод является подвижным ультрамикроэлектродом. 7. Способ по п.1, при этом ультрамикроэлектрод является неподвижным ультрамикроэлектродом. 8. Способ по п.1, при этом ультрамикроэлектрод имеет площадь набора от 110-6 до 10000 см 2. 9. Способ по п.3, при этом анодный потенциал Еа 0 составляет примерно 0,6 В. 10. Способ по п.9, при этом катодный потенциал Ек составляет примерно -0,4, -0,45 или -0,5 В. 11. Способ по п.9, при этом импульс анодного потенциала имеет место в течение периода (ta0) примерно 0,1 с. 12. Способ по п.10, при этом катодный потенциал Ек составляет примерно -0,4 В, а импульс катодного потенциала имеет место в течение периода (tк) примерно 0,1 с. 13. Способ по п.1, при этом ультрамикроэлектрод имеет диаметр 1-100 мкм. 14. Устройство для получения медных порошков и нанопорошков из растворов промышленных электролитов с концентрацией ионов меди выше 0,01 гм-3, в том числе отработанных промышленных электролитов, путем электрохимического осаждения меди на катоде, содержащее средство для обеспечения потенциостатического импульсного электролиза; катодный ультрамикроэлектрод, содержащий золото, платину или нержавеющую сталь, или набор ультрамикроэлектродов, содержащих золото, платину или нержавеющую сталь; анод, содержащий металлическую медь; и средство для обеспечения температуры процесса 18-60C, а также средство для поддержания импульсов электролиза от 0,005 до 60 с. Фиг. 1. Диаграмма восстановления ионов меди на ультрамикроэлектроде. Е - потенциал, измеренный в Вольтах по отношению к медному электроду, i - плотность катодного тока, измеренная в амперах/см 2 Фиг. 2. Типы импульсов потенциала, используемые в указанном способе получения медных порошков и нанопорошков, Ек - потенциал катодного импульса, Еа - потенциал анодного импульса, tк - длительность катодного импульса, ta - длительность анодного импульса Евразийская патентная организация, ЕАПВ Россия, 109012, Москва, Малый Черкасский пер., 2
МПК / Метки
МПК: C25C 5/02
Метки: способ, медных, нанопорошков, промышленных, электролитов, получения, числе, порошков, том, отработанных
Код ссылки
<a href="https://eas.patents.su/7-21884-sposob-polucheniya-mednyh-poroshkov-i-nanoporoshkov-iz-promyshlennyh-elektrolitov-v-tom-chisle-otrabotannyh-promyshlennyh-elektrolitov.html" rel="bookmark" title="База патентов Евразийского Союза">Способ получения медных порошков и нанопорошков из промышленных электролитов, в том числе отработанных промышленных электролитов</a>
Предыдущий патент: Производные индола в качестве противораковых агентов
Следующий патент: Цементная композиция, которая содержит допа-меланин в качестве добавки, со значительно улучшенными физико-химическими и бактериологическими свойствами
Случайный патент: Волочильный блок стана петлевого типа для волочения и атермической обработки проволоки