Способ получения металлических порошков
Формула / Реферат
1. Способ получения металлического порошка или губки для применения в производстве конденсатора, включающий следующие этапы:
восстановление неметаллического соединения (35) до металла в контакте с расплавленной солью (20), при этом указанное неметаллическое соединение представляет собой твердое соединение в форме частиц порошка или агломератов или в форме пористой заготовки или гранулы, полученной из порошка или агломератов, и при этом содержит кислород, а указанное восстановление до металла осуществляют путем электровосстановления,
причем к указанной соли добавлена легирующая примесь, действующая в металле как замедлитель спекания.
2. Способ по п.1, в котором указанная соль содержит от 50 до 10000 ppm легирующей примеси.
3. Способ по п.1 или 2, в котором металлический порошок или губка представляет собой Та или Nb.
4. Способ по пп.1, 2 или 3, в котором катод (30) и анод (40) находятся в контакте с расплавленной солью, а соединение (35) находится в контакте с катодом, при этом указанный способ включает дополнительный этап приложения достаточного напряжения между катодом и анодом для восстановления указанного соединения до металла.
5. Способ по любому из предыдущих пунктов, в котором легирующая примесь представляет собой элемент, выбранный из группы, включающей бор, азот и фосфор.
6. Способ по любому из предыдущих пунктов, в котором легирующая примесь присутствует в соли на протяжении всего процесса.
7. Способ по любому из пп.1-5, в котором легирующую примесь добавляют в соль на конечных этапах процесса.
8. Способ по любому из пп.1-5, в котором легирующую примесь смешивают с соединением для введения в расплавленную соль и затем растворяют в соли.
9. Система для получения порошка тантала или ниобия путем восстановления соединения тантала или ниобия, включающая электролитическую ячейку, имеющую анод и катод и расплав соли щелочного металла или щелочно-земельного металла, при этом указанная соль содержит долю бора, и/или фосфора, и/или азота.
10. Система по п.9, в которой указанная соль содержит от 50 до 10000 ppm бора, фосфора или азота.
11. Способ получения металлического порошка или губки для применения в производстве конденсатора, включающий этапы, на которых восстанавливают неметаллическое соединение, способное восстанавливаться до металлического порошка или губки, до металла в контакте с расплавленной солью, при этом указанное неметаллическое соединение представляет собой твердое соединение в форме частиц порошка или агломератов или в форме пористой заготовки или гранулы, полученной из порошка или агломератов, и при этом содержит кислород, а указанное восстановление до металла осуществляют путем электровосстановления, причем до восстановления неметаллическое соединение содержит от 50 до 10000 ppm легирующей примеси, действующей в металле как замедлитель спекания.
12. Способ по п.11, в котором выбранное неметаллическое соединение перед восстановлением до металлического порошка или губки легируют от 50 до 5000 ppm легирующей примеси, замедляющей спекание.
13. Способ по п.12, в котором неметаллическое соединение легируют путем реакции с твердым веществом, жидкостью или газом, включающим указанную легирующую примесь, так что легирующая примесь диффундирует в указанное соединение.
14. Способ по пп.11, 12 или 13, в котором легирующая примесь представляет собой бор, фосфор или азот.
15. Способ по любому из пп.11-14, в котором указанное неметаллическое соединение находится в контакте с катодом в электролитической ячейке, дополнительно включающей анод и расплавленную соль, при этом между анодом и катодом прилагают напряжение, достаточное для восстановления соединения до металла.
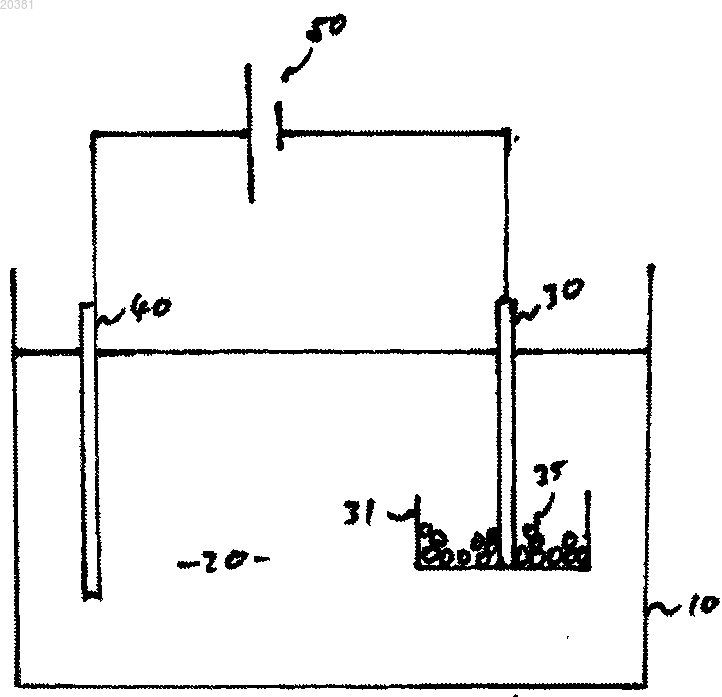
Текст
СПОСОБ ПОЛУЧЕНИЯ МЕТАЛЛИЧЕСКИХ ПОРОШКОВ Способ получения металлического порошка для применения в производстве конденсаторов,включающий этап восстановления неметаллического соединения до металла в контакте с расплавленной солью. Соль содержит по меньшей мере в части процесса легирующий элемент,действующий в металле как замедлитель спекания. В предпочтительных примерах реализации металлическим порошком является порошок Та или Nb, полученный восстановлением оксида Та или Nb, и легирующей примесью является бор, азот или фосфор. Область техники Настоящее изобретение относится к способу получения металлических порошков или губок для применения в производстве конденсаторов, включая производство тантала, ниобия и других металлов 3,4, 5 или 6 Групп или их сплавов. Уровень техники Танталовые или ниобиевые конденсаторы обычно имеют небольшой размер и высокую емкость и стали важными компонентами в сотовых телефонах и персональных компьютерах. При постоянно растущих требованиях к улучшению качества, увеличению надежности и снижению стоимости электронных деталей существует закономерная потребность в танталовых и/или ниобиевых порошках улучшенного качества и более экономичных способах их производства. Существующие способы производства включают много этапов и поэтому являются дорогостоящими и их качество трудно контролировать. Например, танталовые металлические аноды конденсатора, как правило, выпускаются путем прессования агрегированного порошка тантала до значения плотности менее половины реальной плотности металла (обычно от 5 до 7,5 г/см 3 по сравнению с реальной плотностью Та, составляющей 16,6 г/см 3) со встроенным анодным токоподводящим проводником, в результате чего получается пористая гранула. Затем гранулу спекают с получением пористого тела (т.е. анода или тела анода) и анодируют пористое тело путем пропитки соответствующим электролитом с образованием непрерывной диэлектрической оксидной пленки на поверхности тантала. Анодированное пористое тело затем пропитывают катодным материалом с получением равномерного катодного покрытия, соединенного с катодным токоподводящим проводником и заключенного в корпус, изготовленный из смолы. Поэтому пористое тело должно содержать открытые, предпочтительно однородные поры, чтобы обеспечить возможность пропитки на этапах анодирования и пропитки для образования диэлектрической пленки и катода. Увеличение площади поверхности (при сохранении открытой, пористой структуры) агрегированного танталового порошка, используемого для получения анода, может предпочтительно увеличить емкость танталового конденсатора. Поэтому желательно получать анодное тело из порошка или агломерата порошков с большой площадью поверхности. Однако на этапах производства, таких как спекание, площадь поверхности порошка может уменьшиться и снизиться пористость порошка или агломерата. Одним из решений проблемы сокращения пористости и площади поверхности порошка конденсатора при производстве является включение технологической операции введения агента, замедляющего спекание. Такой агент ингибирует рост зерен во время спекания и способствует сохранению площади поверхности и пористости промежуточного порошка/агломерата в готовом конденсаторе. В документе US 6193779 представлен способ получения танталовых порошков путем прокаливания смеси пентахлорида тантала и гидридов щелочно-земельных металлов, где смесь возможно включает легирующие примеси, содержащие фосфор и/или азот (фосфор или азот являются замедлителями спекания тантала). Сущность изобретения В настоящем изобретении в его различных аспектах предложены способ получения металлического порошка или губки, в частности танталового (Та) или ниобиевого (Nb) порошка или губки, металлический порошок или губка, система для получения металлического порошка или губки и конденсатор, как указано в прилагаемых независимых пунктах формулы изобретения, на которые делается ссылка. Предпочтительные или преимущественные признаки настоящего изобретения определены в зависимых подпунктах. Соответственно, согласно первому аспекту предложен способ получения металлического порошка или губки для применения в производстве конденсатора, включающий этапы восстановления промежуточного неметаллического соединения до металла в контакте с расплавленной солью, при этом соль содержит, по меньшей мере, в некоторой части процесса легирующие примеси, действующие в металле как замедлитель спекания. Предпочтительно соль содержит от 50 до 10000 частей на миллион (ppm) легирующей примеси, наиболее предпочтительно от 50 до 5000 ppm легирующей примеси. Полученный металл представляет собой металлический порошок или губку, содержащую определенную концентрацию легирующей примеси. Если не указано иное, ppm в настоящем патенте имеет стандартное значение весовых частей на миллион. Различные легирующие примеси имеют различную эффективность в качестве замедлителей спекания. Так, содержание легирующей примеси в соли может быть низким для легирующей примеси, имеющей высокую эффективность, например между 60 и 400 ppm, предпочтительно между 70 и 200 ppm. Если соединение восстанавливается в ходе непрерывного процесса, то содержание легирующей примеси в соли может обновляться непрерывно, или общая масса соли в системе может превышать массу восстанавливаемого соединения настолько, чтобы содержание легирующей примеси оставалось фактически постоянным во время реакции. То же может быть справедливым для периодического процесса, но масса соли, используемой в реакции, значительно превышает массу восстанавливаемого соединения. Если восстановление осуществляется периодическим способом и отношение массы соли в системе к массе восстанавливаемого соединения низкое, то концентрация легирующей примеси в соли может снижаться по мере протекания реакции и расходования легирующей примеси соединени-1 020381 ем/восстановленным металлом. В таких обстоятельствах исходная концентрация легирующей примеси должна быть высокой для обеспечения желаемого содержания легирующей примеси в восстановленном металле. В качестве альтернативы, дополнительное количество легирующей примеси может быть добавлено во время реакции, если это необходимо. Однако если содержание легирующей примеси в соли является контролируемым, то содержание легирующей примеси в восстановленном металле должно быть достаточным для работы в качестве замедлителя спекания в металле. Предпочтительными металлами для производства по данному способу являются порошки или губки Та или Nb, и предпочтительно, чтобы неметаллическое соединение представляло собой неметаллическое соединение, состоящее в значительной степени из Та или Nb или соединение, которое может быть восстановлено до Та или Nb в расплавленной соли. В качестве альтернативы, таким способом можно получить любой металл, пригодный для использования в качестве конденсатора, например, металл 3, 4, 5 или 6 Группы периодической таблицы. Предшествующее неметаллическое соединение предпочтительно является твердым соединением и может существовать в форме частиц порошка или агломератов или может, в качестве альтернативы, существовать в форме пористой заготовки или гранулы, полученной из порошка или агломератов. Такие заготовки могут быть получены любым известным способом, например прессованием порошка или экструзией. Если используется заготовка, ее можно спечь, чтобы придать ей достаточную прочность для последующей обработки. Присутствие легирующей примеси в расплавленной соли, по меньшей мере, в некоторой части процесса, может преимущественно привести к тому, что в восстановленном металле, содержащем легирующую примесь в достаточных количествах, легирующая примесь будет действовать как агент, замедляющий спекание. Это является преимуществом, если металл выпускается в порошковой форме, поскольку в дальнейшем можно замедлить рост зерен при последующей обработке. Если металл выпускается в форме губки, то присутствие агентов, замедляющих спекание, может способствовать поддержанию высокой площади поверхности во время последующих операций, таких как восстановление массы металла или анодирование для получения диэлектрического оксидного покрытия на поверхности губки. Восстановление соединения может быть выполнено химическим или электрическим способом, например, как описано в публикации WO 99/64638 или WO 03/076690. Предпочтительно, катод и анод контактируют с расплавленной солью, а соединение размещается так, чтобы контактировать с катодом, при этом способ включает дополнительный этап создания достаточного напряжения между катодом и анодом для восстановления соединения до металла. Предпочтительно неметаллическое соединение может содержать кислород, тогда восстановление до металла может осуществляться электровосстановлением. Процесс электровосстановления описан в публикации WO 99/64638. Во время процесса электровосстановления, потенциал ячейки предпочтительно поддерживается на уровне потенциала, достаточного для удаления кислорода с катода или с соединения, контактирующего с катодом, но недостаточного для того, чтобы катионы электролита осаждались на катоде в виде металла. Предпочтительно расплавленная соль состоит из одного или более элементов, выбранных из группы, включающей барий, кальций, цезий, литий, натрий, калий, магний, стронций и иттрий. Особенно предпочтительно, чтобы расплавленная соль содержала галогенид металла и предпочтительно содержала хлорид кальция. Легирующая примесь может быть любым элементом, замедляющим спекание, или может быть композицией элементов, замедляющих спекание или композицией элементов, имеющих комбинированный эффект замедления спекания в восстановленном металле. Предпочтительно соль производится добавлением определенного количества легирующего элемента или легирующих элементов, к соли, предпочтительно соли высокой степени чистоты. Легирующая примесь может присутствовать в соли во время всего процесса, что может предпочтительно упростить переработку. Легирующая примесь не должна присутствовать в расплавленной соли в количестве, достаточном для влияния на восстановление соединения до металла, но должна присутствовать в достаточном количестве для того, чтобы вступать в реакцию с восстановленным металлом или диффундировать в него. Может быть предпочтительным, однако, добавить легирующую примесь к соли на конечных этапах процесса, например, при завершении восстановления или после того, как произошло восстановление до металла. Легирующая примесь может добавляться к расплавленной соли в подходящей форме (т.е. в элементарной форме или в составе соединения, которое растворяется или разлагается в расплавленной соли) или расплавленная соль может быть заменена новой солью, содержащей необходимое количество легирующей примеси. Если легирующая примесь присутствует только на конечных этапах процесса, она может быть добавлена к соли в более высоких количествах, чем было бы желательно в том случае, когда легирующая примесь присутствует на всем протяжении процесса. Контроль момента введения легирующей примеси в расплавленную соль может облегчить контроль содержания легирующей примеси в восстановленном металле. Возможно легирующая примесь, в элементарной форме или в составе соединения, содержащего ле-2 020381 гирующий элемент, может быть смешана с соединением для введения в расплавленную соль. Желательно, чтобы легирующая примесь в этом случае впоследствии растворилась в соли. Например, заготовка или гранула может быть приготовлена из смеси оксида металла и соединения, содержащего бор, азот или фосфор, и эта заготовка затем может быть введена в расплавленную соль. Соединение, содержащие бор,азот или фосфор, может затем раствориться в расплавленной соли для получения легирующей концентрации бора или фосфора в соли. Легирующая примесь должна представлять собой элемент, который действует на металл для ингибирования спекания в металле. Для Та и Nb подходящими легирующими примесями являются бор, азот и фосфор. Азот имеет дополнительное преимущество, поскольку он увеличивает температуру воспламенения слоя в Та. Способ особенно предпочтителен для легирования металла бором и/или фосфором. Согласно второму аспекту предложена система для получения металлического порошка или губки восстановлением неметаллического соединения, включающая электролитическую ячейку, имеющую анод и катод, и соль щелочного металла или соль щелочно-земельного металла, соль, содержащую от 10 до 10000 ppm элемента, действующего в качестве легирующей примеси, замедляющей спекание в металлическом порошке. Особенно предпочтительно, чтобы соль содержала от 50 до 5000 ppm легирующей примеси. Предпочтительно легирующей примесью является бор, фосфор или азот. Предпочтительным является применение установки в производстве порошка или губки Та или Nb,наиболее предпочтительным для восстановления оксида Та или Nb с получением порошка Та или Nb, с замедленным спеканием. Содержание легирующей примеси в соли должно быть достаточным для получения эффекта замедления спекания в порошке. Предпочтительно отношение соли к неметаллическому соединению является достаточно высоким,чтобы расход легирующей примеси в соли во время процесса был минимальным, например, когда отношение (массовое) больше чем 15:1 или 20:1, предпочтительно больше чем 25:1 или 40:1. Предпочтительно система может использоваться в любом описанном выше способе или для производства любого порошка, описанного ниже. Согласно третьему аспекту предложена соль для применения со способом или системе, описанным выше, или для производства порошка, как описано выше. Такая соль содержит от 10 до 10000 ppm легирующего элемента, предпочтительно от 50 до 5000 ppm, например от 60 и 500 ppm или от 70 и 200 ppm легирующего элемента, в зависимости от соотношения расплавленной соли к массе реагента. Предпочтительно легирующей примесью является легирующий элемент из группы, включающей бор, фосфор или азот. Соль может быть солью щелочного металла или солью щелочно-земельного металла, предпочтительно галогенидной солью. Предпочтительно легирующее содержание соли контролируется добавлением к соли легирующей композиции или легирующего сплава для увеличения доли легирующего элемента до желаемого уровня. Предпочтительной солью является CaCl2, содержащая легирующую примесь, выбранную из группы, включающей бор, фосфор и азот. Возможно, такая CaCl2 соль может включать СаО, например, от 0,1 до 0,8 вес.% СаО. Согласно четвертому аспекту предложен альтернативный способ получения металлического порошка или губки для применения в производстве конденсатора, включающий этапы выбора неметаллического соединения, способного восстанавливаться до металлического порошка или губки, и восстановления неметаллического соединения до металла в контакте с расплавленной солью. Перед восстановлением неметаллическое соединение содержит от 50 до 10000 ppm легирующей примеси, действующей как замедлитель спекания в металле, например до 7000 или 8000 ppm легирующей примеси. Предпочтительно соединение содержит легирующую добавку в количестве от 50 до 5000 ppm, например от 100 до 300 ppm или от 200 до 500 ppm или от 250 до 1000 ppm. Содержание легирующей примеси в соединении может варьироваться в зависимости от концентрации легирующей примеси, необходимой в восстановленном металле. Например, предпочтительное содержание фосфора в соединении может составлять от 50 до 500 ppm, тогда как предпочтительное содержание азота и бора может находиться в интервале от 50 до 10000 ppm. Некоторые легирующие элементы могут быть удалены из соединения при его восстановлении до металла. Так, может быть предпочтительным, чтобы концентрация легирующей примеси в соединении до его восстановления была больше, чем концентрация легирующей примеси, необходимая металлу для обеспечения эффекта замедления спекания. Предпочтительно легирующей примесью является один или более элементов из группы, включающей бор, фосфор или азот. Если легирующей примесью является азот, может быть предпочтительным выбрать соединение, содержащее от 100 до 10000 ppm азота, или легировать соединение для получения содержания азота от 100 до 10000 ppm, чтобы в восстановленном металлическом продукте содержание азота составило от 50 до 5000 ppm, например около 250 ppm. Соединение может быть восстановлено в форме порошка или агломерированного порошка. В качестве альтернативы, перед восстановлением соединения ему можно придать форму заготовки или гранулы согласно известному способу. Может быть предпочтительным определить концентрацию легирующей примеси в неметалличе-3 020381 ском соединении, а затем провести процесс или реакцию для увеличения концентрации легирующей примеси в соединении до желаемого уровня. Когда неметаллическому соединению перед его восстановлением придается форма заготовки или гранулы, то процесс легирования для увеличения концентрации легирующей примеси в соединении может быть выполнен до или после производства заготовки. Предопределенное содержание легирующей примеси может быть достигнуто в соединении за счет контроля стадий производства при формовании неметаллического соединения, например содержание азота в Ta2O5 можно контролировать в заранее установленных пределах путем контроля стадий производства при формовании Та 2 О 5. В качестве альтернативы, процесс легирования может осуществляться за счет реакции неметаллического соединения с твердым, жидким или газообразным веществом, состоящим из легирующей примеси или включающим его. Например, соединение может быть обработано при повышенной температуре в атмосфере азота для осуществления диффузии азота в это соединение в качестве легирующей примеси. В качестве другого примера, соединение может быть обработано фосфорной кислотой для получения фосфорного легирования. Предпочтительно, чтобы неметаллическое соединение включало кислород, например соединение может быть оксидом металла. Предпочтительный способ восстановления соединения может заключаться в применении процесса электровосстановления FFC Cambridge. Согласно пятому аспекту предложен металлический порошок, в частности порошок тантала или ниобия, для производства конденсатора, включающего пористые частицы или агломерат, имеющий средний размер частиц между 5 и 500 мкм, удельную площадь поверхности от 0,1 до 10 м 2/г, измеренную по методу БЭТ, отличающийся тем, что частицы включают легирующую примесь, замедляющую спекание, в концентрации от 5 до 5000 ppm, например от 10 до 2000 ppm или от 20 до 1000 ppm. Предпочтительно порошок содержит от 15 до 500 ppm или от 20 до 250 ppm легирующей примеси,замедляющей спекание. Предпочтительно порошок содержит от 45 до 200 ppm легирующей примеси,замедляющей спекание, особенно предпочтительно от 50 до 100 ppm легирующей примеси, замедляющей спекание. Предпочтительно, чтобы легирующая примесь, замедляющая спекание, представляла собой один или более элементов, выбранных из группы, включающей бор, азот и фосфор. Порошок в соответствии с этим вторым аспектом может быть использован на любой стадии производства, необходимой для получения порошка такого качества, которое необходимо при производстве конденсаторов, такой стадии, как восстановление, без значительного увеличения размера зерен порошка или значительного снижения удельной площади поверхности. Порошок может также препятствовать снижению площади поверхности на дальнейших этапах спекания, необходимых для производства конденсатора. Согласно шестому аспекту предложен анод конденсатора или анодное тело, анод, имеющий удельную площадь поверхности, измеренную по методу БЭТ (прибор Micromeritics Tristar) от 0,1 до 10 м 2/г,предпочтительно от 0,1 до 5 м 2/г, и содержащий от 10 и 2000 ppm легирующей примеси, где легирующей примесью является элемент, выбранный из группы, включающей азот, фосфор и бор. Предпочтительно анод формируется из Та или Nb, и предпочтительно анод формируется спеканием порошка или агломератов Та или Nb. Производство анода может включать получение порошка по любому из способов, описанных выше, или использовать любой из порошков, описанных выше. Описание конкретных вариантов реализации настоящего изобретения Здесь на примерах будут описаны конкретные варианты реализации настоящего изобретения со ссылкой на сопроводительный чертеж, который демонстрирует электровосстановительное устройство для осуществления способа согласно аспекту настоящего изобретения. Пример 1. Первый пример описывает производство легированного бором порошка Та путем прямого электровосстановления Та 2 О 5. Схема устройства, используемого в этом способе, представлена на фиг. 1. Использованное устройство состоит из контейнера или тигля 10, наполненного солью 20. Солью являлся хлорид кальция. Соль дополнительно содержала около 50 ppm бора. Нагревательные элементы (не показаны) использовались для повышения температуры соли до значений выше ее температуры плавления. Катод 30 и угольный анод 40 погрузили в расплавленную соль и подключили через источник питания 50. Порошок Та 2 О 5 сформовали в предварительные агломераты путем прессования и спекания. В качестве альтернативы, эти предварительные агломераты могут быть описаны как заготовки, частицы или гранулы. Агломераты Та 2 О 5 (промежуточный материал) 35 привели в контакт с катодом 3. Этот контакт был достигнут за счет помещения агломератов в корзину 31, являющейся частью катода 30. Контакт между агломератами и катодом может быть достигнут за счет любого другого подходящего способа, включая,например, помещение агломератов на поверхность пластины, являющейся частью катода или находящейся в контакте с ним, или за счет навинчивания агломератов на стержень или проволоку, электрически подключенную к катоду. Как часть предварительной обработки, температура соли была сначала увеличена до 400 С в течение 16 ч для высушивания соли, а затем увеличена до 920 С. Понятно, однако, что для подготовки соли к использованию можно использовать любой подходящий способ предварительной подготовки для использования согласно способу настоящего изобретения. Электровосстановление выполнили на агломератах Та 2 О 5 35, так что они были восстановлены до металлического Та. Электровосстановление осуществили в соответствии с процессом Cambridge FFC(описанному в публикации WO 99/64638). На клеммы ячейки (30, 40) наложили напряжение 2,8 В на 56 ч для полного восстановления оксида до металлического Та. Затем катод 30 с прикрепленной к нему корзиной 31, содержащей восстановленный металл, извлекли из расплавленной соли под слоем аргона и остудили. Катод и восстановленный металл промыли водой для удаления избытка соли, а затем металл тщательно промыли сначала горячей деионизированной водой (80 С), а затем 1 М раствором HCl для удаления соли и оксида кальция. После высушивания получили порошок Та такого качества, которое необходимо при производстве конденсаторов. Полученный порошок содержал бор в концентрации 250 ppm,удельная площадь его поверхности составила около 1 м 2/г и удельный заряд около 50103 мкФВ/г(КВ/г). Полученный порошок может быть далее переработан известными способами для получения конденсатора. Типичный пример способа производства конденсатора описан выше в разделе уровень техники. Пример 2. Второй пример описывает производство легированного фосфором порошка Та путем прямого электровосстановления Та 2 О 5. Гранулы Ta2O5 получили прессованием порошка Та 2 О 5 с последующим спеканием, так что гранулы обладали достаточной для работы прочностью и пористостью около 60-65%. Температура спекания и время, необходимое для достижения таких параметров, варьируются в зависимости от конкретных характеристик спекания используемой партии порошка Та 2 О 5. Для восстановления гранул использовали, в сущности, такое же устройство, как описано выше в примере 1 (и представленное на фиг. 1). Однако реакцию электровосстановления проводили в расплавленной соли, легированной фосфором, в отличие от соли, легированной бором, использованной для примера 1. Легированный фосфором хлорид кальция получили добавлением 1000 ppm по весу фосфата кальция (Са 3(РО 4)2) к CaCl2 марки LP. Содержание оксида кальция (СаО) в соли довели до уровня около 4000ppm по весу. Отношение массы соли в ячейке к массе восстанавливаемого оксида составило около 36:1. Перед применением легированный хлорид кальция прошел предварительный этап обработки для того, чтобы высушить соль, как описано выше в примере 1. Для подготовки соли к использованию может использоваться любой подходящий способ предварительной обработки. Электровосстановление гранул Та 2 О 5 осуществляли созданием напряжения около 3 В между анодом и катодом в течение 24 ч таким образом, что гранулы Та 2 О 5 были восстановлены до металлического Та. Температуру соли поддерживали на уровне около 830 С на протяжении реакции электровосстановления. Ячейку охладили, а затем извлекли восстановленный металл и промыли для удаления избытка соли. Полученный металлический Та проанализировали и установили содержание фосфора на уровне 484 ppm(данные масс-спектрометра с индуктивно связанной плазмой, ICP-MS). Пример 3. Третий пример описывает производство легированного фосфором порошка Та путем прямого электровосстановления Ta2O5. Устройство и способ электровосстановления, используемый в примере 3, были, в сущности, такими же, как описано в примере 2, с единственным отличием, что соль легировали более высокой дозировкой фосфора. Соль, использованную в этом третьем примере, получили добавлением около 3000 ppm по весу фосфата кальция к хлориду кальция мари LP. Общее содержание оксида кальция (СаО) в соли установили на уровне около 4000 ppm по весу. Отношение массы соли в ячейке к массе восстанавливаемого оксида составило около 36:1. Гранулы Та 2 О 5 восстанавливали под напряжением около 3 В в течение 24 ч. Полученный металлический Та проанализировали и установили содержание фосфора на уровне 1400 ppm. Пример 4. Четвертый пример описывает производство легированного азотом порошка Та путем прямого электровосстановления легированного азотом Та 2 О 5. Использованное устройство было, в сущности, таким же, как описано выше в примере 1. Использовали расплавленную соль CaCl2, содержащую 0,4 вес.% СаО. Порошок Та 2 О 5 с содержанием азота 783 ppm (измеренным по азотному анализатору Eltra ON900) спрессовали в гранулы и спекали. Гранулы поместили в устройство и выполнили электровосстановление гранул созданием напряжения около 3 В между анодом и катодом в течение 24 ч, таким образом, что гранулы были восстановлены до металлического Та. Температуру соли поддерживали на уровне около 830 С на протяжении реакции электровосстановления. Полученный металлический порошок проанализировали и установили содержание азота на уровне 252 ppm. ФОРМУЛА ИЗОБРЕТЕНИЯ 1. Способ получения металлического порошка или губки для применения в производстве конденсатора, включающий следующие этапы: восстановление неметаллического соединения (35) до металла в контакте с расплавленной солью(20), при этом указанное неметаллическое соединение представляет собой твердое соединение в форме частиц порошка или агломератов или в форме пористой заготовки или гранулы, полученной из порошка или агломератов, и при этом содержит кислород, а указанное восстановление до металла осуществляют путем электровосстановления,причем к указанной соли добавлена легирующая примесь, действующая в металле как замедлитель спекания. 2. Способ по п.1, в котором указанная соль содержит от 50 до 10000 ppm легирующей примеси. 3. Способ по п.1 или 2, в котором металлический порошок или губка представляет собой Та или Nb. 4. Способ по пп.1, 2 или 3, в котором катод (30) и анод (40) находятся в контакте с расплавленной солью, а соединение (35) находится в контакте с катодом, при этом указанный способ включает дополнительный этап приложения достаточного напряжения между катодом и анодом для восстановления указанного соединения до металла. 5. Способ по любому из предыдущих пунктов, в котором легирующая примесь представляет собой элемент, выбранный из группы, включающей бор, азот и фосфор. 6. Способ по любому из предыдущих пунктов, в котором легирующая примесь присутствует в соли на протяжении всего процесса. 7. Способ по любому из пп.1-5, в котором легирующую примесь добавляют в соль на конечных этапах процесса. 8. Способ по любому из пп.1-5, в котором легирующую примесь смешивают с соединением для введения в расплавленную соль и затем растворяют в соли. 9. Система для получения порошка тантала или ниобия путем восстановления соединения тантала или ниобия, включающая электролитическую ячейку, имеющую анод и катод и расплав соли щелочного металла или щелочно-земельного металла, при этом указанная соль содержит долю бора, и/или фосфора,и/или азота. 10. Система по п.9, в которой указанная соль содержит от 50 до 10000 ppm бора, фосфора или азота. 11. Способ получения металлического порошка или губки для применения в производстве конденсатора, включающий этапы, на которых восстанавливают неметаллическое соединение, способное восстанавливаться до металлического порошка или губки, до металла в контакте с расплавленной солью,при этом указанное неметаллическое соединение представляет собой твердое соединение в форме частиц порошка или агломератов или в форме пористой заготовки или гранулы, полученной из порошка или агломератов, и при этом содержит кислород, а указанное восстановление до металла осуществляют путем электровосстановления, причем до восстановления неметаллическое соединение содержит от 50 до 10000 ppm легирующей примеси, действующей в металле как замедлитель спекания. 12. Способ по п.11, в котором выбранное неметаллическое соединение перед восстановлением до металлического порошка или губки легируют от 50 до 5000 ppm легирующей примеси, замедляющей спекание. 13. Способ по п.12, в котором неметаллическое соединение легируют путем реакции с твердым веществом, жидкостью или газом, включающим указанную легирующую примесь, так что легирующая примесь диффундирует в указанное соединение. 14. Способ по пп.11, 12 или 13, в котором легирующая примесь представляет собой бор, фосфор или азот. 15. Способ по любому из пп.11-14, в котором указанное неметаллическое соединение находится в контакте с катодом в электролитической ячейке, дополнительно включающей анод и расплавленную соль, при этом между анодом и катодом прилагают напряжение, достаточное для восстановления соединения до металла.
МПК / Метки
МПК: C25C 3/26, C25C 5/04, C22B 34/24, B22F 9/20, H01G 9/052
Метки: получения, металлических, способ, порошков
Код ссылки
<a href="https://eas.patents.su/8-20381-sposob-polucheniya-metallicheskih-poroshkov.html" rel="bookmark" title="База патентов Евразийского Союза">Способ получения металлических порошков</a>
Предыдущий патент: Светлая магнитная типографская краска для глубокой печати
Следующий патент: Способ удаления мышьяка в виде скородита
Случайный патент: Беговой протектор пневматической шины для сельскохозяйственного трактора