Неразрушающий контроль, в частности, для труб во время изготовления и в готовом состоянии
Номер патента: 21646
Опубликовано: 31.08.2015
Авторы: Лёзаж Фредерик, Бизиё Бернард, Сегура Родригез Нидиа Алехандра
Формула / Реферат
1. Устройство неразрушающего контроля металлических изделий, содержащее ультразвуковые принимающие датчики, образующие схему выбранной геометрии, находящиеся в ультразвуковой связи с изделием посредством жидкой среды, с относительным вращательно-поступательным движением между трубой и схемой расположения датчиков, причем указанное устройство отличается тем, что дополнительно включает
преобразователь (891; 892), выполненный с возможностью выделения цифрового представления возможных эхо-сигналов в установленных временных окнах в зависимости от относительного вращательно-поступательного движения, причем указанное представление включает амплитуду и время прохождения по меньшей мере одного эхо-сигнала, и выполненный с возможностью генерирования параллелепипедного трехмерного графика, построенного по данным, полученным от группы датчиков;
блок трансформации (930), выполненный с возможностью генерирования трехмерного изображения (901; 902) возможных дефектов в трубе на основании трехмерного графика и базы данных, причем блок трансформации (930) присоединен к преобразователю (891; 892);
фильтр (921; 922), выполненный с возможностью определения на изображениях (901; 902) зон предполагаемого дефекта (Zcur), а также свойств каждого предполагаемого дефекта, причем фильтр (921; 922) присоединен к блоку трансформации (930);
выходной каскад, сконфигурированный для генерирования сигнала соответствия или несоответствия изделия.
2. Устройство по п.1, отличающееся тем, что преобразователь (891; 892) включает по меньшей мере один селектор, каждый селектор включает соответственно два выхода: выход максимальной амплитуды и выход времени прохождения.
3. Устройство по п.1 или 2, отличающееся тем, что блок трансформации включает элемент удаления ненужных данных, элемент фильтрации определенных зон, имитатор и элемент интерпретации.
4. Устройство по п.3, отличающееся тем, что имитатор включает элемент теоретической имитации, устройство расчета допуска и блок обратного алгоритма.
5. Устройство по одному из предыдущих пунктов, отличающееся тем, что выходной каскад включает
контроллер (960), приспособленный для подготовки цифровых входных сигналов для нейронного контура из части (951; 952) изображений, соответствующих зоне предполагаемого дефекта (Zcur) и свойствам предполагаемого дефекта в той же зоне, полученных из фильтра (921; 922);
по меньшей мере одну схему типа нейронного контура (970), которая получает входные сигналы от контроллера (960);
цифровой каскад принятия решения и тревоги (992), работающий на базе выходного сигнала от схемы типа нейронного контура (970);
автоматическое устройство отбора и маркировки (994), приспособленное для отбраковки и маркировки изделий, признанных негодными цифровым каскадом принятия решения и тревоги (992).
6. Устройство по одному из предыдущих пунктов, отличающееся тем, что указанное устройство включает два преобразователя (891; 892), соответственно предназначенных для двух схем размещения ультразвуковых датчиков выбранной геометрии (Р11, Р12; Р21, Р22), установленных в ультразвуковой связи с трубой через жидкую среду в соответствии с зеркальной симметрией направления их соответствующих ультразвуковых пучков, и тем, что контроллер (960) приспособлен для работы с эхо-сигналами внутреннего слоя или с эхо-сигналами внешнего слоя либо с эхо-сигналами, возникающими в теле трубы, и в то же время для работы с данными, относящимися к одной и другой из двух схем расположения датчиков.
7. Устройство по одному из предыдущих пунктов, отличающееся тем, что преобразователь (891; 892) приспособлен для изолирования цифрового представления возможных максимумов эхо-сигналов в установленных временных окнах, которые соответствуют эхо-сигналам внутреннего слоя, эхо-сигналам внешнего слоя, а также эхо-сигналам в теле трубы соответственно, и тем, что контроллер (960) предусмотрен для работы с эхо-сигналами внутреннего слоя или с эхо-сигналами внешнего слоя либо с эхо-сигналами, возникающими в теле трубы.
8. Устройство по одному из предыдущих пунктов, отличающееся тем, что контроллер (960) выполнен с возможностью получения по меньшей мере одного входного сигнала (9511; 9521), относящегося к экстремуму амплитуды изображения зоны предполагаемого дефекта.
9. Устройство по одному из предыдущих пунктов, отличающееся тем, что фильтр (921; 922) выполнен с возможностью получения в качестве характеристик каждого предполагаемого дефекта его наклона и длины, при этом контроллер (960) выполнен с возможностью получения соответствующих входных сигналов наклона дефекта (931) и длины дефекта (932).
10. Устройство по одному из предыдущих пунктов, отличающееся тем, что фильтр (921; 922), контроллер (960), нейронный контур (970) и цифровой каскад принятия решения и тревоги (992) приспособлены для многократного функционирования в последовательности зон предполагаемых дефектов (Zcur), определенных указанным фильтром (921; 922).
11. Устройство по п.10, отличающееся тем, что фильтр (921; 922), контроллер (960), нейронный контур (970) и цифровой каскад принятия решения и тревоги (992) приспособлены для альтернативного функционирования на внутреннем слое и на внешнем слое трубы.
12. Устройство по одному из предыдущих пунктов, отличающееся тем, что указанная схема типа нейронного контура включает
первый нейронный контур (NC121-NC123), пригодный для определения природы дефекта среди множества предопределенных классов;
второй нейронный контур (NC141-NC143), пригодный для определения серьезности дефекта.
13. Устройство по п.8, отличающееся тем, что два нейронных контура указанной схемы типа нейронного контура выполнены с возможностью получения следующих входных сигналов, которые отличаются
входным сигналом (9512; 9522) количества максимальных соседних значений для первого нейронного контура;
входным сигналом (9513; 9523) ширины эхо-сигналов для второго нейронного контура.
14. Устройство по одному из пп.12 и 13, отличающееся тем, что два нейронных контура выполнены с возможностью объединения выходных сигналов для уточнения прогноза.
15. Устройство по одному из предыдущих пунктов, отличающееся тем, что один и тот же датчик выполнен с возможностью осуществления передачи и приема ультразвуковых сигналов по меньшей мере для одной части схемы расположения датчиков.
16. Устройство неразрушающего контроля труб во время изготовления и в готовом состоянии, отличающееся тем, что включает
схему расположения ультразвуковых датчиков выбранной геометрии, установленных в ультразвуковой связи с трубой посредством жидкой среды с относительным вращательно-поступательным движением между трубой и схемой расположения датчиков;
контуры для возбуждения (70) этих элементов датчиков в соответствии с выбранным временным законом и для сбора (73) учитываемых обратных сигналов;
устройство по одному из предыдущих пунктов.
17. Способ неразрушающего контроля железных или стальных изделий, таких как трубы или другие продолговатые изделия, во время изготовления и в готовом состоянии, включающий следующие этапы, на которых:
a) обеспечивают схему расположения ультразвуковых датчиков выбранной геометрии, установленных в ультразвуковой связи с трубой посредством жидкой среды с относительным вращательно-поступательным движением между трубой и схемой датчиков;
b) возбуждают (70) указанные ультразвуковые датчики по выбранному временному закону;
c) анализируют принятые обратные сигналы (760-766) для получения из них информации о возможных дефектах в трубе, при этом данная информация включает амплитуду и время прохождения по меньшей мере одного эхо-сигнала, и для генерирования параллелепипедного трехмерного графика;
d) выделяют цифровое представление возможных эхо-сигналов в указанных временных окнах в зависимости от относительного вращательно-поступательного движения (891; 892) и получают оттуда трехмерное изображение (901; 902) возможных дефектов в трубе, основываясь на трехмерном графике и на базе данных;
e) генерируют сигнал соответствия или несоответствия изделия.
18. Способ по п.17, отличающийся тем, что этап е) включает этапы, на которых:
e1) фильтруют (921; 922) изображения (901; 902) по критериям отбора с целью определения там зон предполагаемых дефектов (Zcur), а также свойств каждого предполагаемого дефекта;
е2) формируют (960) цифровые рабочие входные сигналы из части (951; 952) изображений, соответствующих зоне предполагаемого дефекта (Zcur), свойств предполагаемого дефекта в той же зоне после фильтра (921; 922) и данных контекста (740);
е3) применяют сформированные таким образом (960) входные сигналы по меньшей мере к одной схеме типа нейронного контура (970);
е4) производят цифровую обработку выходного сигнала схемы типа нейронного контура (970) по критериям принятия решения с целью выбора решения и/или сигнала тревоги (992);
е5) отбраковывают и маркируют (994) трубы, признанные неудовлетворительными на этапе е4).
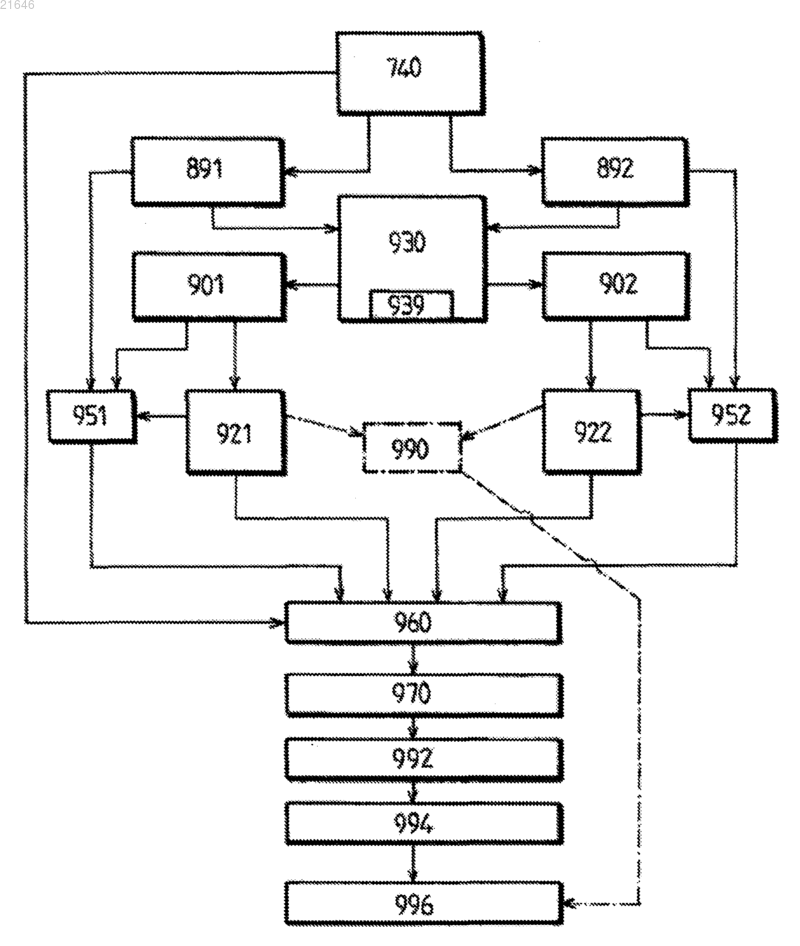
Текст
НЕРАЗРУШАЮЩИЙ КОНТРОЛЬ, В ЧАСТНОСТИ, ДЛЯ ТРУБ ВО ВРЕМЯ ИЗГОТОВЛЕНИЯ И В ГОТОВОМ СОСТОЯНИИ В изобретении устройство, образующее установку подготовки к эксплуатации для неразрушающего контроля металлургических изделий, предназначено для сбора информации о возможных дефектах изделия из обратных сигналов, получаемых посредством ультразвуковых излучающих датчиков, при этом ультразвуковые принимающие датчики образуют схему выбранной геометрии и находятся в связи посредством ультразвука с изделием через жидкую среду с относительным вращательно-поступательным движением между трубой и схемой расположения датчиков, причем указанная установка подготовки к эксплуатации отличается тем, что включает преобразователь (891; 892), способный выборочно выделять цифровое представление возможных эхо-сигналов в указанных временных окнах в зависимости от относительного вращательнопоступательного движения и получать оттуда изображения возможных дефектов изделия, при этом указанное представление включает амплитуду и время прохождения одного эхо-сигнала,и способный генерировать параллелепипедный трехмерный график; блок трансформации (930),способный генерировать трехмерное изображение (901; 902) возможных дефектов в трубе на основании трехмерного графика и базы данных; фильтр (921; 922), способный определить на изображениях (901; 902) зоны предполагаемого дефекта (Zcur), a также свойства каждого предполагаемого дефекта; и выходной каскад, настроенный на генерирование сигнала соответствия или несоответствия изделия. Лзаж Фредерик, Сегура Родригез Нидиа Алехандра, Бизи Бернард (FR) Носырева Е.Л. (RU)(71)(73) Заявитель и патентовладелец: ВАЛЛУРЕК ТЬЮБС ФРАНС (FR) Изобретение относится к неразрушающему контролю материалов, включая трубы в процессе изготовления. В настоящее время известны различные предложения, описанные далее, использующие нейронные сети для неразрушающего контроля материалов. Но данные предложения не предназначены для использования в промышленной среде и из-за этого не могут быть применены для диагностирования работающего оборудования в реальном времени и не позволяют оперативно классифицировать дефекты по их характеристикам так, чтобы было возможно быстро исправить выявленную проблему в процессе производства. В неопубликованной заявке на патент Франции 0605923 раскрывается неразрушающий контроль. Целью данного изобретения является улучшение ситуации до уровня системы, способной использоваться в промышленной среде и легко применяться на уже существующем оборудовании данной среды; использоваться в реальном времени, то есть позволять осуществлять быструю диагностику, а именно диагностику со скоростью, достаточной для поддержания общей скорости производства на прежнем уровне; позволять осуществлять классификацию дефектов в зависимости от их природы, основываясь на небольшом количестве информации, определять их важность, а также позволять определять техническую причину по природе дефекта и быстро устранять проблему на фазе изготовления. Согласно первому аспекту предложена установка подготовки к эксплуатации для неразрушающего контроля труб (или других металлургических изделий) во время и по окончании изготовления. Подобное устройство предназначено для сбора информации о возможных дефектах изделия. Ультразвуковые передающие датчики выборочно возбуждаются согласно выбранному временному закону. Обратные сигналы принимаются ультразвуковыми принимающими датчиками, установленными согласно выбранной геометрической схемы и находящиеся в ультразвуковой связи с трубой через жидкую среду. Кроме того,обычно существует относительное вращательно-поступательное движение между изделием и схемой расположения датчиков. Предложенная установка подготовки к эксплуатации включает преобразователь, способный выборочно выделять цифровое представление возможных эхосигналов в указанных временных окнах в зависимости от относительного вращательно-поступательного движения и получать оттуда изображения возможных дефектов изделия, при этом указанное представление включает амплитуду и время прохождения одного эхо-сигнала, и способный генерировать параллелепипедный трехмерный график; блок трансформации, способный генерировать трехмерное изображение возможных дефектов в трубе, основываясь на трехмерном графике и базе данных; фильтр, способный определить на изображениях зоны предполагаемого дефекта, а также свойства каждого предполагаемого дефекта; выходной каскад, настроенный на генерирование сигнала соответствия или несоответствия изделия. Изобретение может также быть применено в устройстве неразрушающего контроля труб (или других металлургических изделий) во время или по окончании изготовления, при этом устройство включает схему расположения ультразвуковых датчиков выбранной геометрии, установленных в ультразвуковой связи с трубой через связующую среду и с относительным вращательно-поступательным движением между трубой и схемой расположения датчиков; контуры для выборочного возбуждения элементов датчиков согласно выбранному временному закону, предназначенные для приема и регистрации обратных сигналов; установка подготовки к эксплуатации, подобная установке, описанной выше. Другой аспект изобретения представляет собой способ неразрушающего контроля труб (или других металлургических изделий) во время или по окончании изготовления, при этом способ включает этапы,на которых:a) выполняют схему расположения ультразвуковых датчиков выбранной геометрии, установленных в ультразвуковой связи с трубой через связующую среду и с относительным вращательнопоступательным движением между трубой и схемой датчиков;b) выборочно возбуждают данные датчики согласно выбранному временному закону;c) собирают принятые обратные сигналы с целью выборочного анализа обратных сигналов для получения из них информации о возможных дефектах трубы, при этом данная информация включает амплитуду и время прохождения по меньшей мере одного эхо-сигнала, и с целью генерирования параллелепипедного трехмерного графика;d) выборочно выделяют цифровые представления возможных эхо-сигналов в указанных временных окнах посредством относительного вращательно-поступательного движения и получают оттуда трехмерное изображение возможных дефектов в трубе, основываясь на параллелепипедном трехмерном графике и на базе данных; е) генерируют сигнал соответствия или несоответствия изделия.e1) фильтруют изображения по выбранным критериям отбора с целью определения зон предполагаемых дефектов Zраб и свойств каждого предполагаемого дефекта; е 2) формируют цифровые рабочие входные данные из части изображений, соответствующих зоне предполагаемого дефекта Zраб свойств предполагаемого дефекта той же зоны после фильтра; и данных контекста; е 3) применяют сформированные входные данные по меньшей мере к одной схеме типа нейронного контура; е 4) производят цифровую обработку выходных данных схемы типа нейронного контура по критериям принятия решения с целью выбора решения и/или сигнала тревоги; е 5) отбраковывают и маркируют трубы, признанные неудовлетворительными на этапе е 4). Другие аспекты, признаки и преимущества изобретения будут очевидны из следующего ниже подробного описания нескольких не ограничивающих вариантов осуществления и приложенных графических материалов, на которых: на фиг. 1 представлен общий схематический вид трубы, имеющей дефекты или недостатки, названные эталонными дефектами; на фиг. 2 представлен схематический вид сбоку, показывающий пример размещения установки типа"контроль с вращающейся головкой" на готовой трубе; на фиг. 3A-3 С представлены подробности различных типов измерения толщины и контроля продольных и поперечных дефектов; на фиг. 4 представлена принципиальная электронная схема, связанная с ультразвуковым датчиком неразрушающего контроля в обычной установке; на фиг. 5 А и 5 В представлен вид с конца и вид сбоку конкретного типа ячейки для неразрушающего контроля, обычно называемой "вращающейся головкой" и представленной схематически; на фиг. 6 представлен пример совокупности маршрутов ультразвуковых волн в трубе; на фиг. 6 А и 6 В схематично представлены временные диаграммы ультразвуковых сигналов для датчика с наклонным падением сигнала и для датчика с падением сигнала под прямым углом (перпендикулярно) соответственно; на фиг. 7 представлен график, показывающий классическое представление избирательности установки контроля; на фиг. 8 представлена принципиальная электронная схема, связанная с ультразвуковым датчиком неразрушающего контроля в примере установки по данному изобретению; на фиг. 8 А представлена подробная функциональная схема части фиг. 8; на фиг. 8 В представлена другая подробная функциональная схема части фиг. 8; на фиг. 9 схематически представлен снимок экрана, показывающий оцифрованные ультразвуковые изображения потенциальных дефектов в трубе; на фиг. 9 А представлен снимок экрана для другого направления; на фиг. 10A-10D схематически представлены различные типы дефектов по классификации APT на основе выходных данных нейронной сети, предназначенной для определения типа дефекта; на фиг. 11 представлена более подробная функциональная схема другой части фиг. 8; на фиг. 11 А детально представлен вид блока трансформации, изображенный на фиг. 11; на фиг. 12 представлена диаграмма, показывающая обработку потенциальных последовательных дефектов в изображении; на фиг. 13 представлена функциональная схема системы фильтров; на фиг. 14 представлена функциональная схема сборки нейронной сети, предназначенной для определения типа дефекта в трубе; на фиг. 15 представлена функциональная схема сборки нейронной сети, предназначенной для определения серьезности дефекта трубы; на фиг. 16 представлена функциональная схема нейронной модели; на фиг. 17 представлен пример функции передачи элементарного нейрона; на фиг. 18 представлена общая схема установки для определения дефектов различными типами датчиков. Графические материалы содержат элементы определенного характера. Они могут не только помочь лучше понять данное изобретение, а и поспособствовать его определению в случае необходимости. В продолжение к вышесказанному отметим, что ультразвуковой датчик может быть обозначен такими понятными специалисту терминами, как датчик, сенсор, детектор. Нейронные сети. Использование нейронных сетей для неразрушающего контроля материалов являлось темой многих публикаций, большинство из которых были в целом теоретические. Некоторые из них мы рассмотрим ниже. В статье "Localization and Shape Classification of Defects using the Finite Element Method and the Neural Networks" ZAOUI MARCHAND и RAZEK (NDT.NET-AOUT 1999, vol. IV,8) изложены некоторые предложения в данной области техники. Тем не менее, предложения были выполнены в лаборатории и описанное применение не может быть использовано на конвейере в промышленности. Кроме того, рассматривалось только определение токов Фуко, что не всегда является достаточным. Статья "Automatic Detection of Defect in Industrial ultrasound images using a neural Network" Lawson иParker (Proc. of Int. Symposium on Lasers, Optics, and Vision for Productivity in Manufacturing I (Vision Systems: Applications), June 1996, Proc. of SPIE vol. 2786, p. 37-47, 1996) описывает применение обработки изображений и нейронных сетей, называемое "сканирование TOFD". Метод TOFD (времяпролетная дифракция) состоит в определении положений ультразвукового датчика, с помощью которого можно наблюдать за дифракцией пучка на стенках дефекта и определять размеры дефектов. Данный способ трудно применять в уже существующих устройствах неразрушающего контроля, особенно в промышленной среде. В статье "Shape Classification of Flaw Indications in 3-Dimensional ultrasonic Images" Dunlop и McNab(IEE Proceedings - Science, Measurement and Technology - July 1995, Volume 142, Issue 4, p. 307-312) описывается диагностика коррозии трубопровода. Система позволяет осуществлять неразрушающий контроль на глубине и позволяет осуществлять диагностику в трех измерениях и в реальном времени. Тем не менее, данная система работает очень медленно. Поэтому использовать данную систему в промышленной среде довольно сложно. В статье "Application of neuro-fuzzy techniques in oBC pipelines ultrasonic nondestructive testing" Ravanbod (NDTE International, 38 (2005) p.643-653) предполагается, что алгоритмы определения дефектов могут быть улучшены с помощью использования элементов логического потока, добавленных в нейронную сеть. Тем не менее, изложенные способы касаются также проверки дефектов трубопровода и диагностики дефектов коррозии. В документе DE 4201502 С 2 описывается способ создания сигнала, предназначенного для нейронной сети, но почти не описывается или не описывается вообще применение результатов для диагностики. Кроме этого, снова рассматривается только определение токов Фуко. В публикации патента Японии 11-002626 описывается только определение продольных дефектов и только с помощью токов Фуко. В публикации патента 08-110323 описывается изучение частоты сигналов, полученных ультразвуком. В публикации патента 2003-279550 описывается программа, показывающая разницу между целой зоной и зоной с дефектом изделия посредством нейронной сети. Данная программа ограничивается вышесказанным и не позволяет ни классифицировать, ни определить местоположение дефектов. Следовательно, применение данной программы может часто приводить к отбраковке деталей, которые можно было бы классифицировать как годные при проверке человеком. Неразрушающий контроль труб. Приведенное ниже подробное описание главным образом представлено в контексте неразрушающего контроля готовых труб, однако не исключает другие варианты применения. Согласно фиг. 1, дефекты трубы Т могут быть определены согласно их расположению. Таким образом, поверхностные, внутренние и внешние дефекты включают продольные дефекты LD и дефекты по окружности (или поперечные или сквозные) CD и косые или наклонные дефекты ID; при этом посредством различных схем расположения датчиков пытаются определить дефекты, которые превышают определенную длину и определенную глубину согласно нормам или спецификациям или техническим условиям клиентов (например, длина дефекта оговоренного нормами соответствует 1/2 дюйма или приблизительно 12,7 мм на глубине, составляющей примерно 5% от толщины проверяемого изделия). Нас также интересуют дефекты "в стенках", то есть в массе MD (не представленные на фиг. 1), которые часто соответствуют вкраплениям или растрескиваниям и которые должны быть определены одновременно с измерением толщины. Расходящиеся ультразвуковые пучки представлены на фиг. 1 для объяснения принципа определения дефектов. На практике пучки будут больше сходиться, как будет описано ниже. Обычно при неразрушающем контроле ультразвуком используют один из трех типов установок,хорошо известных специалисту в данной области техники, а именно установки типа "с вращающейся головкой", установки типа "с вращающейся трубой" и установки с многоэлементным датчиком. В случае использования датчиков, работающих по способу электронной развертки, относительное вращение трубы/датчиков виртуально. В данном случае выражение "относительное вращательно-поступательное движение между трубой и схемой расположения датчиков" относится к случаю, когда относительное вращение виртуально. На фиг. 2 устройство неразрушающего контроля с вращающейся головкой включает ультразвуковое устройство, установленное на водяной рубашке или на "водяной камере" 100, при этом головка проходит вдоль трубы Т, например, со скоростью v=0,5 м/с. Датчики или ультразвуковые сенсоры излучают продольные волны в воде. Данный датчик, например, работает на частоте 1 МГц или несколько МГц. Датчик периодически возбуждается выбранными волновыми импульсами с интервалом (или с частотой) повторения Fr порядка нескольких кГц или нескольких десятков кГц, например 10 кГц. Ультразвуковой датчик дополнительно включает излучение ближайшего, практически параллельного, поля в зону Френеля с множественными помехами, в которой длина оси пучка равна где D является диаметром активной пластины датчика-преобразователя иявляется длиной рабочей волны, и излучение отдаленного поля в зону Фраунгофера согласно расходящемуся пучку с углом 2 , где На фиг. 3 А-3 С показаны датчики, сходящиеся посредством вогнутой линзы (ультразвуковой), подобные датчикам, используемым при контроле труб. Предпочтительно используют менее перегруженную помехами зону Фраунгофера. Также для таких датчиков как Р 11 и Р 12 обычно сфокусированный ультразвуковой пучок проходит рядом с перпендикуляром к оси трубы Т. Определение осуществляется практически в перпендикулярном направлении. Назначение данных датчиков: если пучок перпендикулярен к оси трубы Т в поперечном сечении, то датчики служат для измерения толщины (например, Р 1, фиг. 3 А); в данном случае речь идет о "поперечном сканировании"; если пучок проходит под наклоном к оси трубы Т в поперечном сечении, то датчики служат для определения продольных дефектов (например, Р 11, фиг. 3 В). В данном случае угол падения в поперечном сечении предпочтительно выбирается так, чтобы вызывать в трубе только поперечные ультразвуковые волны или ультразвуковые волны сдвига, учитывая характеристики границы вода/металл трубы (обычно вода/сталь). Также предусматривают два датчика Р 11 и Р 12, которые имеют противоположный наклон относительно оси трубы (фиг. 2). Устройство включает также такие датчики, как Р 21 и Р 22, ультразвуковой пучок которых, как правило, равномерно сфокусирован и проходит вблизи плоскости, проходящей через ось трубы, и под наклоном к плоскости, которая перпендикулярна оси трубы Т (см. датчик 21, фиг. 3 С). В данном случае угол падения относительно плоскости, перпендикулярной к оси трубы, будет, как правило, выбираться так, чтобы вызывать в трубе только поперечные ультразвуковые волны или ультразвуковые волны сдвига, учитывая характеристики границы вода/металл трубы (обычно вода/сталь). Данные сенсоры используются для определения поперечных дефектов. Также обычно предусматривают два датчика Р 21 и Р 22,которые имеют противоположный наклон относительно плоскости, перпендикулярной оси трубы (фиг. 2). Контроль дефектов, как правило, осуществляется при фокусировке пучка. Фокус измеряется по отношению к "скачку", соответствующему первому прохождению ультразвуков туда-обратно в толще трубы. Также датчик фиг. 3 А сфокусирован на половине скачка, тогда как датчики фиг. 3 В и 3 С сфокусированы на трех четвертях скачка. К тому же, контроль внешних дефектов обычно осуществляется на скачке, а контроль внутренних дефектов осуществляется на половине скачка. Та - время присутствия, необходимое для того, чтобы сенсор смог правильно принять возвращение пучка ультразвуков, характерных для возможных дефектов. Данное время Та зависит от суммы двух следующих временных значений: первое представляет собой отрезок времени, за который продольные ультразвуковые волны проходят в обоих направлениях через "толщу воды", присутствующую между сенсором и трубой на пути ультразвука; второе представляет собой отрезок времени, за который поперечные ультразвуковые волны проходят через трубу непосредственно для неразрушающего контроля. Данное время главным образом зависит от выбора желаемого количества отражений поперечных волн внутри стенки трубы. Обычно сенсоры вращаются вокруг оси трубы не описанным здесь способом со скоростью Т, равной около нескольких тысяч оборотов в минуту (например, 6000 об/мин). В случае, когда вращаются не сенсоры, а труба, которая также известна специалисту в данной области техники (установка типа "вращающаяся труба"), скорость вращения трубы может быть от нескольких десятков до нескольких тысяч оборотов в минуту. Каждый узел датчик - среда передачи (вода) - труба можно назвать "ячейкой". Для ячейки следует рассмотреть открытие пучка Od ультразвуковых сенсоров при определении. Открытие может быть определено с помощью двух составляющих (фиг. 1), а именно расположенной в поперечном сечении трубы,составляющей Od1 и расположенной в плоскости, проходящей через ось трубы и сенсор, составляющейOd2. Настройка установки (скорость вращения, скорость перемещения, размеры Od1 и Od2 и число датчиков) должна гарантировать полное сканирование ультразвуковыми пучками поверхностей и объема контролируемой трубы. Также следует отметить, что некоторые нормы, технические условия или спецификации клиентов накладывают определенные требования на сканируемые зоны. Время анализа Та определяется с помощью компромисса между интенсивностью (частотой) повторяемости Fr; скоростью вращенияс учетом составляющей Od1 открытия ультразвуковых сенсоров в поперечном сечении трубы (иными словами учитывая вращение датчиков, составляющая Od1 открытия пучка должна позволить получить необходимое время присутствия дефекта напротив датчиков, которое, по меньшей мере, будет равно Та); скоростью перемещения v с учетом составляющей Od2 открытия ультразвукового сенсора вдоль трубы и количеством Nfi сенсоров, предназначенных для той же функции Fi (составляющие группу сенсоров) на поверхности трубы (иными словами учитывая продвижение трубы вперед, составляющая Od2 открытия пучка должна позволить получить необходимое время присутствия дефекта напротив датчика(или группы датчиков), которое, по меньшей мере, будет равно Та); количеством датчиков, имеющих одинаковое предназначение (т.е. для выполнения той же функции); время распространения волн, подобных описанным ранее. Обычно устройство включает два датчика, таких как Р 11, Р 12 для контроля дефектов типа LD и возможных дефектов ID, два датчика типа Р 21, Р 22 для контроля дефектов типа CD, к которым добавляют, как правило, датчик типа Р 1 для измерения толщины изделия и контроля дефектов типа MD. Каждый датчик, как будет показано ниже, может являться группой датчиков, работающих вместе. Установка включает интегрированную или присоединяемую электронную схему возбуждения и определения, связанную с каждым датчиком. Она включает (фиг. 4) излучатель (70) импульсов, например,при напряжении 250 В для возбуждения сенсора Р 0, установленного на водной камере 100. Как интегрированная часть системы неразрушающего контроля, ультразвуковой сенсор Р 0, в данном случае приемник/излучатель, получает эхо-сигналы, вызываемые возбуждением. Линии 700 и 710 соответственно передают импульсы возбуждения и сигнал на клеммы сенсора усилителя 73. Выходной сигнал усилителя 73 служит для визуализации отображения, предназначенного для оператора и/или для автоматической установки для отбора, способной отбраковать (на выходе) некондиционные трубы. Визуализация, например, осуществляется осциллоскопом 750, принимающим в качестве сигнала выходной сигнал усилителя 73 и в качестве развертки 752 сигнал каскада синхронизации 753 из излучателя 70. Пороговый каскад 754 предотвращает ослепление осциллоскопа во время излучения импульса. Другой выходной сигнал усилителя 73 поступает на каскад обработки сигнала 760. Данная обработка включает главным образом выпрямление, сглаживание и фильтрование. За ним следует каскад определения или селектор 762, который может выделять значимые эхо-сигналы известным образом. При определении дефекта, именно наличие эхо-сигнала с известными параметрами амплитуды и длительности (а значит и энергии) является важным в некоторых временных интервалах, особенно в интервалах половины скачка и скачка. При определении толщины проверяют, чтобы эквивалентная величина временного промежутка между соответствующими эхо-сигналами из глубины соответствовала желаемой толщине трубы. Отклонения, определенные по этим критериям, используются для генерирования сигнала тревоги 764 и/или включения автоматического устройства 766 отбора, отбраковывающего некондиционные трубы и маркирующего их согласно одному или нескольким обнаруженным дефектам. Фактически, в случае использования установки с вращающейся головкой (фиг. 5 А и 5 В) ячейка включает также водяную камеру 100, установленную на механическом основании 80 и включающую узел датчика Р 0 с соединением 701, соединяющим линии 700 и 710, изображенные на фиг. 4. Также предусматривают, например, три ролика 81-83 для центровки трубы Т. Из уровня техники (к примеру, устройство, продаваемое немецкой компанией GE NUTRONIK, ранее называемое NUKEM) известен узел датчика Р 0, включающий датчики, вращающиеся вокруг трубы со скоростью нескольких тысяч об/мин. Также можно использовать множество датчиков, установленных в форме кольца вокруг трубы. Например, кольцо включает 6 секторов, включающих 128 ультразвуковых датчиков, установленных по окружности. Альтернативно, секторы с датчиками немного смещены по направлению к оси трубы. Это позволяет получить перекрытие между двумя последовательными продольными секторами с датчиками и также уменьшает проблемы с помехами. Помехи образуются при получении датчиком эхо-сигналов, излучаемых другим датчиком. Также для направления трубы выше и ниже устройства неразрушающего контроля данная система содержит направляющую раму (не показана), которая обеспечивает правильное непрерывное расположение трубы по отношению к ультразвуковым датчикам. Неразрушающий контроль должен осуществляться по всей наружной поверхности трубы. Но также необходимо чтобы контроль соответствовал выходной линейной скорости v производства трубы. Необходимо найти компромисс между линейной скоростью v трубы, интенсивностью (или частотой) повторений Fr, временем анализа Та, составляющими Od открытия на определение ультразвукового сенсора,скоростью вращенияи количеством датчиков, выполняющих одинаковую функцию, и скоростью распространения ультразвуковых волн. Также предпочтительно, чтобы данная установка могла быть применена для всех возможных диаметров труб (а также для труб любой толщины), охватывая весь ассортимент изделий. В связи с чем необходимо учитывать различные величины скорости вращенияи частоты повторяемости Fr, то есть величины, выбранные в зависимости от диаметра проверяемой трубы. Наконец отметим, что любые изменения в настройках изготовления требуют изменений настройки углов падения ультразвука каждого датчика на поверхности трубы. Данная операция является очень трудоемкой и выполняется вручную в течение приблизительно 30 мин. Во время регулировки производство труб останавливается. Именно таким образом в настоящее время посредством ультразвука осуществляется неразрушающий контроль труб, профилей или других изделий и/или толщины стенок по окончании изготовления. В области неразрушающего контроля посредством ультразвука часто используется следующая терминология:"сканирование" (или "scan") представляет собой последовательность относительных положений трубы/датчика;"приращение" обозначает шаг сканирования (обратно пропорциональное частоте повторяемости или частоте ультразвуковых излучений);"АСкан" обозначает график электрического напряжения на клеммах ультразвукового датчика, на оси абсцисс которого представлено время прохождения, а на оси ординат представлено электрическое напряжение, также называемое ультразвуковой амплитудой;"ВСкан" обозначает изображение, относящееся к данной величине приращения, на оси абсцисс которой представлено сканирующее ультразвуковое излучение, при необходимости выраженное в градусах угла датчика относительно контролируемой детали, а на оси ординат представлено время прохождения и каждая точка ультразвуковой амплитуды становится серой или цветной;"эходинамика" обозначает график, на абсциссе которого указано ультразвуковое излучение, а на ординате представлена максимальная амплитуда временного селектора АСкан для соответствующего излучения;"ССкан" обозначает изображение, на абсциссе и на ординате которого указаны эквивалентные положения в плоскости точки излучения ультразвуковой волны, представленные серым цветом, а также максимальная амплитуда ультразвука для излучения во временном селекторе АСкан ("амплитуда изображения"). В случае рассмотрения трубы точка абсциссы ССкан соответствует длине трубы, а точка ординат соответствует окружности трубы. В случае рассмотрения плоского изделия точка абсциссы ССкан будет соответствовать длине плоского изделия, а точка на оси ординат будет соответствовать ширине плоского изделия. Кроме того, заявитель в дальнейшем описании использует следующие термины:"параллелепипедный ВСкан 3D" обозначает трехмерное изображение, включающее, кроме прочего,положение датчика относительно оси трубы, при этом изображение рассматривается в простом виде,форма трубы не показана;"уменьшенный ВСкан 3D" обозначает изображение параллелепипедного ВСкан 3D, ограниченное зоной с указанием посредством ультразвука возможных дефектов по окончании фильтрации;"ВСкан 3D трубы" имеет такие же размеры, что и параллелепипедный ВСкан 3D, при этом данные представлены в проверяемой трубе, а амплитуда может при необходимости являться дополнительным измерением. На фиг. 6 схематически представлено продольное сечение системы, образованной датчиком, его водной рубашкой и трубой, а также приведена иллюстрация различных путей ультразвуковых сигналов,образующих эхо-сигналы. Также данный чертеж демонстрирует сложность путей и трудность анализа. На фиг. 6 А схематически представлена диаграмма амплитуды/времени ультразвукового сигнала датчика, работающего под наклонном к оси трубы. Начиная от момента Твозб возбуждения датчика мы получаем эхо-сигнал с границы вода-труба в момент Твзаим (который также можем назвать ТВнешн 0). Также отмечены (вертикальная пунктирная линия) момент ТВнутр, в котором пучок ультразвуков достигает внутреннего слоя трубы, где он преломляется и отражается, а также момент ТВнешн 1, в котором пучок ультразвука достигает внешнего слоя трубы. В результате наклонного падения сигнала при отсутствии дефекта в данном месте не образуется значительного отраженного эхо-сигнала, возвращающегося на датчик в виде ТВнутр. Данный факт также справедлив и для ТВнешн 1. На фиг. 6 В схематически представлена диаграмма амплитуды/времени ультразвукового сигнала датчика, работающего под прямым углом к оси трубы. Общая хронология сигналов такая же, как и хронология фиг. 6 А (с приблизительным фактором,связанным с углом падения). И, напротив, при угле падения, перпендикулярном к оси, существуют значительные эхо-сигналы в ТВнутр и ТВнешн 1, даже при отсутствии дефектов в соответствующих местах трубы. В настоящее время системы неразрушающего контроля, используемые в производстве труб, работают с учетом отношения K между амплитудой As сигнала из проверяемой трубы; амплитудой А 0 сигнала эталонного контрольного дефекта для типа рассматриваемого контроля. Данный "эталонный контрольный дефект" обычно определяется в эталонной трубе с искусственным дефектом (например, прорезь в форме U или V) с выбранными размерами, например, в соответствии со стандартами неразрушающего контроля и/или техническими требованиями клиента. Подразумевается, что данная амплитуда сигнала пропорциональна тяжести дефекта, то есть пропорциональна глубине (DD). График, изображенный на фиг. 7, (хорошо известен специалистам в данной области техники, см. Nondestructive Testing Handbook - глава Статистика, т. 7, опубликован ASNT American Society for Nondestructive Testing) представляет фактическое распределение K=f (DD). График демонстрирует, что в действительности корреляция очень плохая (порядка 0,3-0,4 для контроля ультразвуком). Рассмотрим более детально: на графике, изображенном на фиг. 7, при выборе контрольной амплитуды А 0 (K=1) при величине XL (глубина максимально допустимого дефекта) в центре распределения(по наклонной прямой Траспр) мы видим, что можно найти еще дефекты при K=0,5 глубины DD превышающей XL. Следовательно, из предосторожности мы приняли А 0 меньшей величины, чем XL. Таким образом, мы исключаем из производства трубы, которые, тем не менее, могли бы соответствовать требованиям. Это даже более экономически невыгодно, чем способы производства достаточно тяжелых труб,как по сложности, так и по затратам энергии. Таким образом, целью заявителя является улучшение данной ситуации. На фиг. 8 представлено улучшенное устройство по сравнению с устройством, изображенным на фиг. 4. Выходной сигнал усилителя 73 приходит на каскад 761, преобразующий в цифровую форму сигнал усилителя 73 и работающий на данном цифровом сигнале. Эта обработка будет описана ниже в соответствии с фиг. 11. Каскады 764 и 766 функционально подобны каскадам, изображенным на фиг. 4. Необработанный сигнал датчика, такой как сигнал на осциллоскопе 750, именуется специалистами как А-Скан. Он включает эхо-сигналы, подобные сигналам, изображенным на фиг. 6. Перейдем к изображениям дефектов в трубе с помощью ультразвуковых сигналов. Далее будет описан процесс получения изображения. Фактически изображение получают из нескольких последовательных сканирований трубы датчиком Рх под последовательными углами, покрывающими в целом правую секцию трубы. Возможно получить данные сканирования посредством последовательных излучений ультразвука одним датчиком с использованием относительного вращения трубы/датчика. Рассмотрим в качестве неограничивающего примера установку типа с вращающейся головкой. На фиг. 8 А изображен датчик Рх, который может быть типа Р 1, Р 11, Р 12, Р 21 и Р 22. В изображенном примере датчик Рх включает n элементарных датчиков Рх-1,Px-i, Px-n, которые расположены вдоль продольной оси трубы и являются одновременно объектом ультразвукового излучения. На фиг. 8 А то, что находится между элементарными датчиками и трехмерным графиком выходного сигнала 769 может быть рассмотрено как преобразователь. Сигнал АСкан первого элементарного датчика Рх-1 приходит на усилитель 73-1 с двумя параллельными каналами: канал селектора 763-1 А и канал селектора 763-1 В. Каждый селектор 763-1 А включает соответственно два выхода, выход максимальной амплитуды и выход времени прохождения. Выход максимальной амплитуды связан с линейным цифровым преобразователем 765-1-At. Выход линейного цифрового преобразователя 765-1 Аа максимальной амплитуды связан с хранилищем буферных данных 768-Аа, собирающим данные от линейных цифровых преобразователей максимальной амплитуды 765-iAa, при этом i находится в диапазоне от 1 до n. Выход линейного цифрового преобразователя 765-1 At времени прохождения связан с хранилищем буферных данных 768-At, собирающим данные от линейных цифровых преобразователей времени прохождения 765-iAt, при этом i находится в диапазоне от 1 до n. Выход линейного цифрового преобразователя 765-1 Ва максимальной амплитуды связан с буферным хранилищем данных 768-Ва, собирающим данные от линейных цифровых преобразователей максимальной амплитуды 765-iBa, при этом i находится в диапазоне от 1 до n. Выход линейного цифрового преобразователя 765-1Bt времени прохождения связан с буферным хранилищем данных 768-Bt, собирающим данные от линейных цифровых преобразователей времени прохождения 765-iBt, при этом i находится в диапазоне от 1 до n. Основываясь на полученной информации от прохождения эталонной трубы, оператор может получить в буферных хранилищах 768-Аа и 768-At информацию Т 1 А о положении и временной ширине,обозначающей посредством известной геометрии трубы моменты, при которых можно получить "эхосигнал внутреннего слоя" относительно внутренней части трубы, например первый эхо-сигнал Внутр.1,изображенный на фиг. 6. На фиг. 6 А изображено соответствующее временное окно "Внутр." вокругTphilnter. Также на основе информации, полученной во время прохождения эталонной трубы, оператор может получить в буферных хранилищах 768-Ва и 768-Bt информацию Т 1 В о положении и временной ширине, обозначающей посредством известной геометрии трубы, моменты при которых можно получить "эхосигнал внутреннего слоя" относительно внешней части трубы, например первый эхо-сигнал Внешн. 1,изображенный на фиг. 6. На фиг. 6 А изображено соответствующее временное окно "Внешн." вокруг ТВнешн. Схема повторяется для других датчиков Рх-2, Px-i, Рх-n. Также каждый временной селектор 763 определяет временные окна с учетом момента излучения ультразвука и заранее определенных временных интервалов, в которых можно получить эхо-сигналы,касающиеся данного селектора. На фиг. 6 изображено, как можно определить интересующие временные интервалы, из расчета угла падения пучка ультразвуков на трубу, а также диаметра (внутреннего или внешнего) и толщины трубы. Указанный временной интервал соответствует данному эхо-сигналу данной точки трубы при относительном положении между трубой и датчиком. Для упрощения принято считать, что моменты излучений синхронизированы с относительным вращением трубы/датчиков таким образом, чтобы элементарный датчик всегда работал на одной и той же продольной образующей трубы. Выходной сигнал ее селектора предоставляет пространственную последовательность аналогичных образцов сигналов, каждый из которых соответствует амплитуде ожидаемого эхо-сигнала на стенке трубы. Эти образцы датчика Рх-1, например, оцифрованы в 765. Синхронизация с излучением может быть осуществлена посредством связи (не представленной) с излучателем 70 или с его пусковым устройством, с контуром синхронизации 753 или с генератором развертки 752 (фиг. 8). Отображение 750 может быть выполнено по желанию. Система может функционировать на трубе, вращающейся с практически постоянной скоростью. В данном случае угловая скорость и продвижение трубы вперед могут быть измерены с посредством определенного углового кодера, например, модели RS0550168, производимой компанией Hengstler, и лазерного измерителя скорости, например, модели LSV 065, производимой компанией Polytec. При выполнении системы датчиков с возможностью вращения труба может не вращаться. В этом случае для измерения скорости перемещения трубы будет достаточно лазерного измерителя, а для измерения скорости вращения датчиков может быть использован угловой кодер. Для данного излучения узел датчиков PX-1-PX-n предоставляет линию изображений, соответствующих перпендикулярному сечению трубы. В другом измерении изображения данный элементарный датчик предоставляет линию, соответствующую образующей трубы. Цифровые преобразователи 765-1 Аа, 765-2 Аа, , 765-iAa, , 765-nАа и 765-1At, 765-2At, , 765iAt, , 765-nAt позволяют выполнить "внутреннее" изображение, относящееся к внутреннему слою трубы. Цифровые преобразователи 765-1Ba, 765-2Ba 765-iBa, ,765-nBa и 765-1Bt, 765-2Bt, ,765-nBt позволяют выполнить "внешнее" изображение относительно внешнего слоя трубы со временем прохождения Tvol max эхо-сигнала максимальной амплитуды. Параллелепипедный трехмерный график, сохраненный в блоке 769, касается датчика или рассматриваемой группы датчиков Рх. Каждая точка данного изображения, представленная серым цветом, соответствует величине амплитуды эхо-сигнала, соответствующего отражению ультразвукового сигнала на возможном дефекте рассматриваемой зоны трубы. Данная величина может также представлять отношение между максимальной амплитудой ультразвукового сигнала, полученного от трубы во время испытаний, и между максимальной амплитудой ультразвукового сигнала, полученного от искусственного "эталонного контрольного дефекта", как определено выше. Параллелепипедный трехмерный график является отображением подготовительного трехмерного ВСкан, оцифрованного в блоке 769. Термин подготовительный обозначает то, что он служит основанием для генерации ВСкан трехмерной трубы. Как правило,форма трехмерного графика отличается от формы исследуемого изделия, особенно для труб. Информация параллелепипедного трехмерного графика может включать систему пар (время прохождения, амплитуда) кривой АСкан для длительности определенной оцифровки. Параллелепипедные трехмерные графики, оцифрованные в блоке 769, включают параллелепипедные трехмерные графики 891, построенные по данным, полученным от группы датчиков Р 11, и параллелепипедные графики 892, построенные по данным, полученным от группы датчиков Р 12 и соответственно Р 21 и Р 22 согласно фиг. 11. Данное изображение соответствует зоне трубы, полученной с помощью объединения практически кольцевых зон трубы, соответствующих каждой оцифрованной линии. В действительности, речь идет о кольцевых или геликоидальных зонах в случае, если пучок ультразвука направлен практически перпендикулярно оси трубы. Известно, что есть отличия в зависимости от относительного движения трубы/датчика. Зоны являются скорее эллиптическими и в действительности они являются искривленными или "скрученными" в пространстве. В данном описании выражение "кольцеобразные зоны" включает указанные выше варианты. Также следует отметить, что для полного воссоздания трехмерного графика необходима дополнительная информация о положении датчика по отношению к трубе. Ее можно получить на отдельном входе 740. Эта информация приходит от кодировщика или от системы лазеров и позволяет определить пространственное положение. Так как труба может быть приравнена к полому цилиндру, информация о по-8 021646 ложении может быть сведена к системе с двумя измерениями. Применение изобретения на существующем стенде ультразвукового контроля ("UT bench") включает доступ к необработанным данным ультразвукового контроля ("UT Raw Data"), осуществляемого,например, с помощью платы получения, такой как модель N1 6024 серии Е или N1 6251 серии М компании National Instrument или с помощью прямого доступа к цифровым данным электронной панели управления стендом; доступность текущей информации о скорости вращения (трубы или датчика) или относительном угловом положении трубы по отношению к датчику; доступность текущей информации о скорости перемещения трубы вперед или относительном линейном положении датчика, установленного на оси. Схема, изображенная на фиг. 8 А, может быть применена параллельно датчику типа Р 11 и датчику типа Р 12, исследующим ту же зону трубы по двум различным направлениям. Каждый датчик позволит получить внутреннее и внешнее изображения. Затем одно из изображений сможет быть выбрано с помощью команды "Внутр./Внешн."; параллельно датчику типа Р 21 и датчику типа Р 22, каждый из которых позволит получить внутреннее и внешнее изображения. Схема фиг. 8 А может также быть применена к датчику типа Р 1 и в этом случае предусматриваются три параллельных канала за каждым усилителем (по меньшей мере, виртуально). Один из каналов работает по временному повторяющемуся строб-импульсу, позиционированному, как указано в "Volum." на фиг. 6 В. Данный канал позволяет контролировать глубинные дефекты, т.е. находящиеся в толще трубы. Два других канала могут работать соответственно на временных повторяющихся строб-импульсах,позиционированных, как показано в "WphiExterO" и "Wphilnterl" на фиг. 6 В. Эти два других канала позволяют осуществлять измерения толщи трубы. Между тремя каналами существуют функциональные различия (виртуальные). В действительности,два других указанных канала могут являться физически одинаковыми, при этом различаются моменты или строб-импульсы "WphiExterO" и "Wphilnterl". Также можно использовать одиночный физический канал, в котором различают моменты или строб-импульсы "WphiExterO", "Volum." и "Wphilnterl". Постараемся наглядно и детально описать случай применения датчика типа Р 11 и датчика типа Р 12. Описание приведено ниже. Известно, что две группы датчиков Р 11 и Р 12 служат для определения продольных дефектов труб. Ультразвуковой контроль осуществляется с помощью излучения ультразвука (US) в двух предпочтительных направлениях ("по часовой стрелке" - "против часовой стрелки"): первый датчик или группа датчиков Р 11 предоставляет ультразвуковое изображение трубы в направлении работы ("по часовой стрелке"). второй датчик или группа датчиков Р 12 предоставляет ультразвуковое изображение трубы в противоположном направлении работы ("против часовой стрелки"). Также продольные дефекты хорошо определяются с помощью двух датчиков или групп датчиков,оси пучков которых наклонены симметрично по отношению к перпендикулярной плоскости оси трубы. Наклон, например, составляет приблизительно +/-17. Это является примером применения системы двух датчиков или двух групп датчиков, как указано выше. В варианте осуществления фиг. 8 В каждое окно оцифровывания 782 после усилителя 781 может отличаться началом, длительностью и частотой оцифровки, определяющими количество n точек рассмотренного сигнала АСкан. Каждое окно оцифровывания 782 предоставляет количество n пар информации(амплитуда, время прохождения) для каждого ультразвукового излучения. Буфер/мультиплексор 788 переносит совокупность всех собранных данных в параллелепипедный трехмерный график 769, учитывая соответствующие положения датчиков в момент получения сигнала, что осуществляется благодаря знанию геометрического расположения одних датчиков по отношению к другим датчикам и благодаря информации позиционирования трубы/датчика в момент ультразвукового излучения 740. Рассмотрим теперь фиг. 9. Для первого значения контроля (выбрана строка "sens1") на изображениях 903 и 904 представлено сечение (соответственно поперечное и продольное) ВСкан 3D трубы, трехмерная геометрия трубы, описанной ниже, от датчиков Р 11. Позиционирование этих сечений зафиксировано благодаря параметрам "поперечное сечение в (мм)" и "продольное сечение в (градусах)". Изображения 905 (внутреннее) и 906 (внешнее) являются ССкан, как определено выше, изображение 905 (соответственно 906) сконцентрировано на временной зоне АСкан, в которой дефекты внутреннего слоя (соответственно и внешнего) должны быть определены. Необходимую информацию по воссозданию изображений 905 и 906 получаем из параллелепипедного ВСкан 3D 891, изображенного на фиг. 11. Изображение 901 является прозрачным трехмерным изображением ВСкан 3D трубы части проверяемого изделия для определения в данной части потенциально опасных зон, например описанных ниже зон. Такие же изображения 903 бис, 904 бис, 905 бис, 906 бис и 902 воссозданы для второго значения контроля (строка "sens2" включена), см. фиг. 9 А. Напомним, что предыдущее описание относится к определению дефектов в продольном направле-9 021646 нии. Подобным образом можно исследовать и поперечные дефекты (с группами датчиков Р 21 и Р 22). Рассмотрим фиг. 11. Блоки изображений 901 и 902 получены из параллелепипедных трехмерных графиков 891 и 892 посредством блока трансформации 930, как изображено на фиг. 11 А. Блок преобразователя 891, изображенный на фиг. 11, соответствует сборке, изображенной на фиг. 8 А, для датчика Р 11. Блок преобразователя 892 также соответствует сборке, изображенной на фиг. 8 А, но он применяется к датчику Р 12. Блоки преобразователей 891 и 892 используют данные в контексте труба/датчик блока 740. Эти данные относятся к характеристикам трубы во время исследования и к характеристикам датчиков во время их использования. Блок трансформации 930 расположен ниже параллелепипедных трехмерных графиков 891 и 892 и имеет структуру, показанную на фиг. 11 А. Блок трансформации 930 осуществляет временной подсчет протяженности распространения волн в трубе с учетом преобразования режимов в момент контакта ультразвуковой волны и дефекта. При столкновении поперечная волна может трансформироваться в продольную волну и наоборот. Блок трансформации 930 может определять распространение энергии акустического пучка, основываясь на расчетах коэффициентов передачи и отражения. Может быть выполнен анализ частотного спектра АСкан. Блок трансформации 930 может включать базу данных 939 реальных или смоделированных образцов, позволяющих производить сравнение с полученными трехмерными графиками. Блок трансформации 930 может воссоздавать изображение ВСкан 3D с геометрией трубы. Как показано на фиг. 11 А, блок трансформации 930 включает два блока 931 и 932 устранения зон,не используемых в построении ВСкан 3D из трехмерного графика, блок 931, обрабатывающий данные трехмерных изображений 891, и блок 932, обрабатывающий данные трехмерных изображений 892, два блока 933 и 934 фильтрации посредством применения временного смоделированного окна соответственно ниже блоков 931 и 932, блок теоретической имитации 935, блок расчета допусков 937, который снабжает блок обратного алгоритма 936, блок 936 предоставляет указанные ранее изображения 901 и 902. Фильтрация блоками 931 и 932 позволит снизить количество обрабатываемой информации при сохранении потенциально интересных зон для трехмерного отображения. Фильтрация может быть осуществлена в продольном направлении, начиная от ССкан. Выбранная длина может превышать длину зоны верхней амплитуды с одним порогом. Также можно обрабатывать параллелепипедные ВСкан 3D, включающие зону потенциального дефекта. Фильтрация блоками 933 и 934 может быть осуществлена при ограничении временного окна эхосигналами поверхности и глубины. Данные блоки фильтрации могут также ограничивать потенциально интересную угловую зону трубы и в случае необходимости смещать эти зоны для их идентификации и для полного восстановления потенциально интересной зоны. Изображения из блоков 933 и 934 являются уменьшенными изображениями ВСкан. Блок теоретической имитации 935 может включать базу данных имитаций, например АСкан или ВСкан 3D в соответствии с типами дефектов и их положением. База данных может включать смоделированные результаты и/или результаты показаний естественных и/или искусственных дефектов. Блок обратного алгоритма 936 может сравнивать теоретические АCкан и ВСкан 3D, идущие от блока теоретической имитации 935, и АСкан и ВСкан 3D, полученные во время проверки, с целью определения ближайших теоретических АСкан или ВСкан 3D и, следовательно, наиболее возможного дефекта или дефектов. В качестве примера блок обратного алгоритма 936 сравнивает отобранное экспериментальное АСкан,соответствующее продольному положению и угловому положению, с теоретическими АСкан на том же продольном положении. В качестве примера блок обратного алгоритма 936 сравнивает изображение ВСкан 3D, полученное от уменьшенного ВСкан 3D, соответствующего продольному положению теоретических изображений ВСкан 3D в том же продольном положении. Оба сравнения могут быть выполнены. Лучшая система теоретических представлений эхо-сигналов представляет собой систему с наименьшим отклонением относительно экспериментальных данных. После блока трансформации 930 изображены фильтры 921 и 922 (фиг. 11), позволяющие также представить части изображений и их подготовительных данных в качестве их входных данных, собранных блоком контроллера 960 для нейронной обработки или экспертной обработки 970. В описанном варианте осуществления фильтр 921 включает выходные данные Zраб, обозначающие рабочую зону изображения. Выходные данные используются функцией извлечения 951, которая соответственно извлекает часть изображения (ССкан) для зоны Zраб и предоставляет доступ к подготовке изображения 891 для получения из него запомненной информации (АСкан) относительно зоны Zраб. Совокупность данных передается функцией извлечения 951 на контроллер 960, как входные сигналы нейронной или экспертной обработки 970,выходные данные, предоставляющие информацию, полученную при фильтрации, при этом, по меньшей мере, некоторая информация связана с зоной Zраб. Данная информация передается в качестве входных сигналов к нейронной или экспертной обработке; факультативный вывод (прерывистая линия) дополнительных фильтрованных данных к памяти 990. Так же это используется и для фильтра 922 с функцией извлечения 952 для той же текущей зоныZраб. Нейронная система 970 питает логическую систему принятия решения и тревоги 992, управляю- 10021646 щую автоматизмом сортировки и маркировки 994. Можно предусмотреть интерфейс интерпретации 996 оператором, который может предоставлять все данные или часть непрерывных данных, хранящихся в памяти 990 и соответствующих части трубы во время контроля. Непрерывные данные поступают в память 990 от фильтров 921 и 922. В добавление к прогнозу (происхождение, тип и важность показания) нейронная система 970 предоставляет оценку доверия к данному прогнозу. Эта информация доступна операторам, располагающим в равной степени более подробными дополнительными данными, такими как история выполняемых команд или как проблемы, возникающие во время разработки изделия. Поэтому оператор или специалист может также участвовать в обработке прогноза. На фиг. 11 показана обработка информации, полученной по меньшей мере от двух групп датчиков,осуществляющих одну функцию или предназначенных для одного типа контроля (две группы Р 11 и Р 12 или 2 группы Р 21 и Р 22). Та же схема может быть использована для обработки информации, полученной от большего количества групп датчиков, предназначенных для разного типа контроля. При этом также возрастет количество обрабатываемых одновременно изображений. Первая функция фильтров 921 и 922 основывается на определении зон дефектов изображений 901 и 902. В общем, фильтрация осуществляется для установления анализируемых зон, а также для того, чтобы в данных зонах отличить дефекты от других показаний. Фильтрация осуществляется на двух подобных участках двух изображений. Оба фильтра могут работать одновременно. С помощью сканирования цифрового изображения мы, в первую очередь, определяем местоположение зон изображения с потенциальными дефектами. Поэтому возможно применить фиксированный порог с помощью калибровки. Можно использовать порог, адаптируемый к уровню текущего шума на изображении. Способ основан на теории определения сигнала в белом шуме, который может основываться на двух гипотезах: Гипотеза Н 0: измерение=белый шум средней mb и стандартное отклонение stdb. Гипотеза H1: измерение=сигнал+белый шум. Приступим к статистическим тестам, позволяющим определить, о какой гипотезе Н 0 или H1 идет речь. Эти статистические расчеты осуществляются в реальном времени на n скользящих точках изображения, соответствующих последовательным излучениям. Число n может быть определено опытным путем. Согласно этому способу (случай, именуемый "аддитивный белый гауссовский шум") мы можем привести в качестве примера критерий Неймана-Пирсона для распознания порога определения по возможности данной ложной тревоги (pfa). Это выражается приведенной формулой [21]. Для получения порога инвертируют кумулятивную гауссовскую функцию, называемую также Q (или функция ошибкиerf) согласно приведенной формуле [22]. На практике часто констатируют присутствие фонового шума. Этот шум может быть вызван многими причинами (например, присутствие воды внутри трубы, фон переменного тока, акустические явления, связанные со структурой материала проверяемого изделия). Использование переменного порога позволяет избежать ложных тревог, появляющихся при использовании фиксированного порога. Среди прочих возможных ложных показаний помехи характеризуются очень короткими пиками ультразвуковых сигналов. Этих помех можно избежать с помощью простых алгоритмов, именуемых также алгоритмами кумулятивного расчета или интеграторами (пример: "n импульсов перед тревогой" или "двойной порог"). Заявитель также рассмотрел "виток", являющийся маршрутом, по которому следует датчик вдоль цилиндрической поверхности, с которой мы сравниваем трубу. Фильтрация может быть осуществлена вдоль каждого витка для уменьшения процента ложных тревог. Также мы используем фильтр Баттерворта и/или дискретное преобразование Фурье, такое как, например, быстрое преобразование Фурье. Этот способ применяется в каждом цифровом ряду. Алгоритм такого же рода может быть применен вдоль трубы. Таким образом, положения потенциальных дефектов определены. При определении местонахождения дефекта его положение соответствует анализированному положению изображений фиг. 9, например,с трехмерным изображением, поперечным сечением и осевым сечением. Указания радиального положения/толщины (или просто внутреннего, внешнего состояния или состояния дефекта в толще) могут быть представлены как атрибуты точек изображений. Таким образом, мы получаем два двумерных изображения, представляющих возможные дефекты внешнего слоя трубы; два двумерных изображения, представляющих возможные дефекты внутреннего слоя трубы; двумерное изображение, представляющее возможные дефекты в толщине трубы. Теперь рассмотрим "подтвержденные" дефекты после удаления помех и ложных тревог. Далее заявитель предпочел работать с зоной изображения ограниченного размера. Следует ограничить данную зону согласно данным существования полученного дефекта. Иначе говоря, следует расположить определенные точки как точки, превышающие порог, для определения полной зоны вокруг дефекта. Это необходимо, например, для определения наклонного положе- 11021646 ния дефекта. Алгоритм связан с различными этапами: определение контура (например, градиент Робертса); дилатация (объединение близких контуров); эрозия, а затем закрытие помогут определить защитный слой вокруг дефекта; последний этап окружения позволяет полностью локализовать дефект. Для каждого дефекта получаем координаты зоны соответствующего изображения, которые можно будет использовать для анализа нейронной сети, примененной далее. На фиг. 12 представлена обработка зон изображений в виде диаграммы потока. В начале изображений (801) имеем для обработки зоны изображения от нуля до р с подтвержденным дефектом. Операция 803 предполагает наличие по меньшей мере одной первой зоны, являющейся текущей зоной обработки Zраб в 805. Для данной зоны Zраб операция 807 выборочно извлекает данные изображений 901 и 902, соответствующие данной зоне(определяется ее координатами на изображении); операция 809 выборочно извлекает данные, используемые в подготовке изображений 901 и 902 и соответствующие зоне Zраб. Примеры этих данных соответствуют зоне Zраб. Примеры этих данных будут приведены ниже; операция 811 осуществляет нейронную или, собственно говоря, экспертную обработку, которую мы рассмотрим ниже; полученные результаты для зоны Zраб выборочно запоминаются в 813 в соответствии с обозначением зоны Zраб; тест 820 проверяет наличие другой предназначенной для обработки зоны изображения, и если таковая имеется, то обработка в 805 начинается с этой другой зоны, как и указано в 821; если такой зоны нет,обработка изображения или изображений прекращается (822). В случае обработки датчика Р 1 существует только одно изображение, и это изменяет количество входных параметров. С этого момента обработка практически такая же. После определения каждой интересуемой зоны Zраб фильтрация может включать и другие функции. Для этих других функций на фиг. 13 схематически представлено взаимодействие между фильтрацией и продолжением операций, представленных на фиг. 11. Фиг. 13 похожа на фиг. 11, но только для изображения 901. На чертеже представлены элементы системы труба/датчики блока 740; экстрактор 951, который находит данные для зоны Zраб на изображении 901 и на его приготовлении 891; блок внутренний/внешний 7410, указывающий, находится ли во внешнем или во внутреннем слое рассматриваемый дефект зоны Zраб. То, что фильтрация добавляет базам данных, определено более детально для каждой зоны Zраб (блок 805), как это указывает содержимое кадра прерывистой линией: исследование угла наклона в блоке 941; указание длины дефекта в блоке 942. Также сюда можно добавить указание выравнивания в C-Scan в блоке 945; в блоке 946 указание существования других дефектов в том же поперечном сечении трубы. В описанном варианте применения такие данные как 945 и 946 направляются в память 990. Другие данные идут к нейронным сетям или экспертным системам 970. Эти данные разделены на две функции и это представлено ниже. Дефект в трубе может быть определен положением, типом и важностью, часто сравниваемой с глубиной. В описанном варианте применения тип и степень глубины дефекта трубы определены отдельно с помощью двух нейронных процессов той же общей структуры, что и приведенная в следующем примере структура. Типичный пример дефекта обработан согласно фиг. 14, тогда как особый тип дефекта обработан согласно фиг. 15. Типы дефектов могут быть определены, например, способом, представленным на фиг. 10A-10D. Данные чертежи показывают четыре типа, составляющих упрощающий выбор по отношению к списку дефектов, представленных API, которые могут образоваться вследствие процессов выработки трубы. Ниже мы представили обозначения, которые могут описать природу дефектов и которые будут понятны специалистам. Также мы видим, что дефекты типов 1 и 3 имеют прямую форму, а дефекты, представленные на изображениях 2 и 4, имеют изогнутую форму (хорда). Соответствие между реальными дефектами и четырьмя описанными выше типами может быть определено следующим образом: В данном описании фиг. 14 и 15 используют два нейронных контура с тремя промежуточными нейронами (или "спрятанными нейронами"), отмеченными NC121-NC123 для фиг. 14 и NC 141-NC 143 для фиг. 15. Фиг. 14 и 15 имеют определенное количество входов. Для облегчения понимания входы представлены различными линиями. Двойные линии указывают, что используются множественные входы, то есть они повторяются для каждой зоны Zраб. Прежде всего, в блоке 7410 согласно рассмотренному состоянию селекторов 763 образуется информация, указывающая на то, внутренний или внешний слой стенки трубы анализируется. Данную информацию можно также получить с помощью ВСкан 3D. Вторая категория общих входных данных включает указанные величины из блока 740 (фиг. 13): в блоке 7401, ТС/ДТ, представляет собой отношение толщины стенки к диаметру трубы,в блоке 7402, Част. представляет собой частоту работы ультразвуковых зондов,в блоке 7403, Возм. Диам. представляет собой полезный диаметр ультразвуковых зондов. Третья категория общих величин включает количества, полученные от фильтрации, которые можно рассматривать в качестве общих величин двух датчиков 921 и 922 (или более). Например, возьмем среднее значение результатов двух датчиков или самый значимый результат (максимум/минимум согласно случаю). Эти количества являются величинами в блоке 9201, наклоном дефекта и его длиной в 9202. Эти две величины легко уловимы на двух изображениях, изображенных на фиг. 9, и имеют зеркальную симметрию. Теперь рассмотрим только фиг. 14. Следующая категория величин включает величины различных измерений для каждого из двух датчиков (или группы датчиков) и для каждой из зон Zраб, что и представлено на чертеже двойной линией. Для первого датчика имеем в блоке 9511 К 1, являющийся отношением между максимальной амплитудой ультразвукового сигнала зоны Zраб и изображением 901 по отношению к максимальной амплитуде указанного "эталонного контрольного дефекта". В действительности, в примере амплитуда каждого пикселя изображения 901 определяется этим отношением; К 1 в таком случае является просто максимумом амплитуды зоны Zраб изображения 901; обозначим точку максимума зоны Zраб как Pmax1; в блоке 9512 КСЭ 1 является величиной ССкан, названной QuantBumpsEchodyn, представляющей максимальное число встреченных мест в зоне Zраб изображения 901 вблизи точки Pmax1 максимальной амплитуды. Данное число КСЭ 1 ограничено максимумом полученных мест рядом с Pmax1 с одной и с другой стороны, но уменьшение сигнала ниже соответствующего уровня фонового шума не допускается. КСЭ 1 будет принимать или значение 1, или значение 2. Эти две величины получают из изображения 901 посредством экстрактора 951, как и представлено в примечаниях 951 (901). Добавляют в блоке 9518 RT1, которая является величиной, представляющей время подъема эхо-сигнала в естественный ультразвуковой сигнал, называемый АСкан (речь идет о промежутке времени между моментом, в котором сигнал достигает максимума, и последним моментом,предшествующем моменту, в котором сигнал находится на уровне фонового шума; время измеряется в микросекундах). Данная величина RT1 была ранее измерена на выходе соответствующего усилителя 73(фиг. 8 А); она хранилась, например, в 891 в соответствии с определенной точкой трубы. Также можно получить эту величину выборочно из экстрактора 951. Величина RT1 теперь может быть напрямую измерена оператором по изображению 903, изображенному на фиг. 9, или же по параллелепипедному изображению ВСкан 3D. Для второго датчика имеем в блоке 9521 К 2, определенное как К 1 для изображения 902 вместо изображения 901. В примере К 2 является максимумом амплитуды зоны Zраб изображения 902; обозначим точку максимума Zраб какPmax2; в блоке 9522 КСЭ 2 определяется как КСЭ 1, но на изображении 902 вместо изображения 901 и рядом с Pmax2. Здесь также обычно КСЭ 2 будет принимать или значение 1, или значение 2. Эти две величины получают из изображения 902 посредством экстрактора 952. Добавляют в блоке 9528 RT2, которая является величиной, представляющей время подъема эхо-сигнала в естественный сигнал, называемый АСкан. Как и ранее данная величина RT2 измерялась на выходе соответствующего усилителя 73 (фиг. 8 А); она хранилась, например, в блоке 892 в соответствии с определенной точкой трубы. Также можно получить эту величину выборочно с помощью экстрактора 952. Величина RT2 теперь может быть напрямую измерена оператором по изображению 903 А, изображенному на фиг. 9, или же по параллелепипедному изображению ВСкан 3D. Последний вход 958 нейронной сети является постоянной величиной, названной ПостояннаяА, являющейся константой, определенной во время регулировки модели и на основе опыта. Выход 998, изображенный на фиг. 14, показывает тип дефекта и его средний наклон (определенный согласно типу). Если степень глубины (или важности) дефекта обрабатывается согласно фиг. 15, используются те же входные данные, что и для фиг. 14, кроме: для первого датчика блок 9512 заменяется блоком 9513, который обрабатывает величину ЭШ 1 илиEchodynWidth, являющейся шириной с половинной высотой (50%) формы эходинамической волны для первого датчика. Данную величину ЭШ 1 получаем из ССкан; кроме того, для второго датчика, блок 9522 заменяется блоком 9523, который обрабатывает величину ЭШ 2 или EchodynWidth, являющейся шириной с половинной высотой (50%) формы эходинамической волны для этого второго датчика; константа, называемая ПостояннаяВ, для 959 отличается; выход 999 указывает значимость дефекта и именуется DD. Также отметим, что в двух случаях (фиг. 14 и 15) данный нейронный контур 970 обрабатывает часть изображения 951, полученного одной группой ультразвуковых датчиков, а также часть изображения 952, соответствующую той же зоне, полученной от другой группы датчиков. Заявитель отмечает, что существует возможность получить удовлетворительные результаты при условии подходящей регулировки параметров экспертной системы, например нейронных контуров и,при необходимости, их количества для оптимизации прогноза. К тому же, заявитель утверждает, что с помощью сочетания информации, собранной из различных нейронных сетей, возможно получить более точный прогноз. В целом, параметры входа нейронной сети или экспертной системы являются характеристиками двух трехмерных изображений (отношение максимальной амплитуды к эталонной амплитуде, ширине эхо-сигнала, направлению эхо-сигнала, характерного для наклона дефекта) и контроля (датчик, размеры трубы). Выходные параметры представляют собой характеристики дефектов (глубина, наклон/тип). Принятия решение и/или тревога 992 могут быть инициированы автоматически с помощью выбранных критериев решений, на основе порогов, подобранных по коэффициенту безопасности в случае необходимости. Для определения порогов можно использовать результаты опыта. Теперь рассмотрим фиг. 16, на которой представлена модель элементарного нейронного контура,изображенного на фиг. 14 и 15, для двух датчиков. Данная модель включает уровень или входной слой ВС ("Input Layer"), который перегруппирует все входные параметры (часто именуемые "входные нейроны"). Чтобы не перегружать чертеж, представим на ней только три нейрона Е 1-Е 3 и константу, которую можно рассмотреть как нейрон Е 0. Данная константа чаще всего называется "смещением". На практике входные нейроны более многочисленны в соответствии с фиг. 14 или 15 в зависимости от случая. Затем следует предусмотреть по меньшей мере один уровень или слой СС ("Hidden Layer" или"скрытый слой") включает k нейронов (из которых представлено всего 2 нейрона для упрощения изображения). Затем следует выходной нейрон S1, предоставляющий решение в виде характерной величины важности дефекта трубы, например продольного дефекта. Данный выход соответствует блоку 998, изображенному на фиг. 14, и 999, изображенному фиг. 15. Отметим, что "нейрон" - константа Е 0 применяется не только для уравновешивания одного или нескольких скрытых слоев СС, а также и для выходного нейрона (выходной слой ВыхС или "OutputLayer"). Общие характеристики нейронного контура, подобного используемому здесь, представлены в формуле [11] приложения 1, где wij является принятым весом сигнала Xi на входе нейрона j. В предусмотренном контуре элементарный нейрон действует по формуле [12], как показано схема- 14021646 тически на фиг. 17. Выход S1, изображенный на фиг. 16, предоставляет собой рассчитываемую величину, соответствующую формуле [13] приложения 1. Опытным путем заявитель отрегулировал скрытые нейроны и их веса так, чтобы функция f стала непрерывной, нелинейной, дифференцируемой и ограниченной функцией. Функция арктангенса является предпочтительным примером в данном случае. Известно, что нейронная сеть определяет свои коэффициенты wij, называемые, обычно, синапсами,полученными с помощью опыта. Данный опыт должен привести от 3 до 10 раз больше примеров, чем существует, покрывая тем самым область желаемых условий работы. С помощью примеров Ер (р=от 1 до М) определим для каждого примера промежуток Dp между величиной Sp, полученной из нейронного контура, и действительной величиной Rp, измеренной или определенной экспериментально. Это все относится к формуле [14]. Эффективность работы нейронного контура определяется общей величиной промежутка Cg, называемой "стоимость". Качество может выражаться, например, по формуле [15] как общая величина взвешенного квадратичного отклонения. Из опыта известны различные проблемы в таких случаях, как контроль дефектов в трубах, а именно в случаях, когда речь идет о тяжелой технике, как уже говорилось выше. Прежде всего, заявитель выполнил первый опыт по имитации. Для этого можно использовать программу CIVA, разработанную и представленную на рынок Комиссариатом Атомной Энергии Франции. Первый опыт позволил обозначить влияющие параметры и сформировать первую версию нейронной сети на основе виртуальных дефектов. При этом функция "стоимости" была оптимизирована. Затем заявитель выполнил второй опыт, включающий результаты, полученные на имитации и на искусственных дефектах, то есть специально созданных дефектах в реальных трубах. Второй опыт позволяет сформировать вторую версию нейронной сети, в которой функция "стоимости" была равномерно оптимизирована. Заявитель также совместил результаты, полученные из искусственных дефектов и из совокупности дефектов, встречаемых на реальных трубах. Данные дефекты были точно определены с помощью измерений, выполненных после процесса изготовления. Третья фаза позволила утвердить третью версию нейронной сети. Данная версия использовалась для контроля при изготовлении. В любом случае во время ее применения на новой или измененной установке необходимо будет выполнить ее "настройку" с помощью двенадцати искусственных образцов, включающих всю гамму обрабатываемых дефектов. В результате чего происходит оптимизация. Фиг. 11, 12, 14 и 15 описаны в контексте датчиков Р 11 и Р 12. Тот же принцип может быть применен к группе датчиков Р 1. В этом случае уже не будет изображения 2 и сеть будет иметь меньше входных параметров, как было указано выше. Описанные контуры для двух датчиков могут быть использованы для одного датчика, но без входных параметров для части "Изображение 2". Тот же принцип может быть применен и для двух групп датчиков Р 21 и Р 22, определяющих поперечные дефекты с учетом того факта, что датчики наклонены для этого типа определения (например +/17) к плоскости, перпендикулярной оси трубы. Очевидно, что в каждом случае происходит цифровая обработка типа, изображенного на фиг. 11, за исключением элементов 992-996. Эта обработка полностью обозначена с помощью 763 и в соответствии с фиг. 8, где она следует за блоками 764 и 766. Также мы получаем узел, подобный узлу, представленному на фиг. 18, включающий для датчика P1 фазу обработки 763-1 с последующей фазой принятия решения и тревоги 764-1; для датчика Р 11 и Р 12 фазу обработки 763-10 с последующей фазой принятия решения и тревоги 764-10; для датчиков Р 21 и Р 22 фазу обработки 763-20 с последующей фазой принятия решения и тревоги 764-20; три фазы 764-1, 764-10 и 764-20 были совместно представлены с помощью автоматической установки отбора и тревоги 767. Вариант осуществления, изображенный на фиг. 18, заключается в том, что предусматривается одна фаза "Принятия решения и тревога" с непосредственным использованием выходных данных трех фаз обработки 763-1, 763-10 и 763-20. Проще говоря, неразрушающий контроль осуществляется "на лету", то есть по мере того, как труба проходит по установке контроля. Решение, вызванное обработкой информации, описано выше и может быть принято также по мере того, как трубапроходит через установку контроля (с параметром решениетревога и отметкой "на лету"); в данном варианте осуществления принятие данного решения происходит после того, как вся длина трубы будет проверена или даже еще позже (после контроля совокупности группы труб, например); каждая труба будет определена и идентифицирована (например, порядковый номер). В этом случае необходимо, чтобы полученная информация была записана (сохранена в памяти). Сохранение может быть выполнено с целью последующего анализа квалифицированным специалистом,- 15021646 который может принять решение после анализа записанных и обработанных результатов одной или несколькими нейронными сетями. Естественно, с учетом свойств нейронных контуров можно перегруппировать, по меньшей мере частично, совокупность нейронных контуров (из обработок 763-1, 763-10 и 763-20) в один нейронный контур со всеми желаемыми входными данными. Описанный вариант осуществления непосредственно использует нейронные сети в качестве примера экспертных систем. Изобретение не ограничивается представленным вариантом осуществления. Здесь выражение "устройство типа нейронного контура" может охватывать другие способы анализа нелинейных данных как с нейронными контурами, так и без них. В общем, преобразователь может включать входные данные максимальной амплитуды в селекторе и входные данные соответствующего времени прохождения. Указанные входные данные могут предоставлять достаточно данных для решения соответствия или несоответствия изделия. Блок трансформации может включать элемент удаления ненужных данных, элемент фильтрации помеченных зон, имитатор и элемент интерпретации. Снижение количества информации позволяет получить более высокую скорость обработки. Имитатор может включать элемент теоретической имитации, устройство расчета допуска и обратный алгоритм. Выходной каскад включает контроллер, предназначенный для подготовки цифровых входных данных для нейронного контура из части изображений, соответствующих зоне предполагаемого дефекта и свойствам предполагаемого дефекта в данной зоне, полученных из фильтра и данных контекста; по меньшей мере одну схему типа нейронного контура, получающую рабочие входные данные от контроллера; цифровой каскад принятия решения и тревоги, работающий на базе выходных данных схемы типа нейронного контура; автоматическое устройство отбора и маркировки, предназначенное для отбраковки и маркировки изделий, признанных негодными цифровым каскадом принятия решения и тревоги. Здесь описан предпочтительный вариант предложенной системы для случая неразрушающего контроля во время изготовления труб без сварки. Те же способы, в частности, могут применяться к длинным металлургическим изделиям, не обязательно представленным в форме труб. В случае сварных труб или других сварных изделий (например, листовое железо или пластины), система также способна определить границы сварных швов и, следовательно, определить возможные дефекты сварных швов. С другой стороны, дефекты, расположенные за пределами сварных швов, которые могут соответствовать уже имеющимся вкраплениям на базовой заготовке (или изделии), могут быть определены другими способами. Приложение. Сечение 1 ФОРМУЛА ИЗОБРЕТЕНИЯ 1. Устройство неразрушающего контроля металлических изделий, содержащее ультразвуковые принимающие датчики, образующие схему выбранной геометрии, находящиеся в ультразвуковой связи с изделием посредством жидкой среды, с относительным вращательно-поступательным движением между трубой и схемой расположения датчиков, причем указанное устройство отличается тем, что дополнительно включает преобразователь (891; 892), выполненный с возможностью выделения цифрового представления возможных эхо-сигналов в установленных временных окнах в зависимости от относительного вращательно-поступательного движения, причем указанное представление включает амплитуду и время прохождения по меньшей мере одного эхо-сигнала, и выполненный с возможностью генерирования параллелепипедного трехмерного графика, построенного по данным, полученным от группы датчиков; блок трансформации (930), выполненный с возможностью генерирования трехмерного изображения(901; 902) возможных дефектов в трубе на основании трехмерного графика и базы данных, причем блок трансформации (930) присоединен к преобразователю (891; 892); фильтр (921; 922), выполненный с возможностью определения на изображениях (901; 902) зон предполагаемого дефекта (Zcur), а также свойств каждого предполагаемого дефекта, причем фильтр(921; 922) присоединен к блоку трансформации (930); выходной каскад, сконфигурированный для генерирования сигнала соответствия или несоответствия изделия. 2. Устройство по п.1, отличающееся тем, что преобразователь (891; 892) включает по меньшей мере один селектор, каждый селектор включает соответственно два выхода: выход максимальной амплитуды и выход времени прохождения. 3. Устройство по п.1 или 2, отличающееся тем, что блок трансформации включает элемент удаления ненужных данных, элемент фильтрации определенных зон, имитатор и элемент интерпретации. 4. Устройство по п.3, отличающееся тем, что имитатор включает элемент теоретической имитации,устройство расчета допуска и блок обратного алгоритма. 5. Устройство по одному из предыдущих пунктов, отличающееся тем, что выходной каскад включает контроллер (960), приспособленный для подготовки цифровых входных сигналов для нейронного контура из части (951; 952) изображений, соответствующих зоне предполагаемого дефекта (Zcur) и свойствам предполагаемого дефекта в той же зоне, полученных из фильтра (921; 922); по меньшей мере одну схему типа нейронного контура (970), которая получает входные сигналы от контроллера (960); цифровой каскад принятия решения и тревоги (992), работающий на базе выходного сигнала от схемы типа нейронного контура (970); автоматическое устройство отбора и маркировки (994), приспособленное для отбраковки и маркировки изделий, признанных негодными цифровым каскадом принятия решения и тревоги (992). 6. Устройство по одному из предыдущих пунктов, отличающееся тем, что указанное устройство включает два преобразователя (891; 892), соответственно предназначенных для двух схем размещения ультразвуковых датчиков выбранной геометрии (Р 11, Р 12; Р 21, Р 22), установленных в ультразвуковой связи с трубой через жидкую среду в соответствии с зеркальной симметрией направления их соответствующих ультразвуковых пучков, и тем, что контроллер (960) приспособлен для работы с эхо-сигналами внутреннего слоя или с эхо-сигналами внешнего слоя либо с эхо-сигналами, возникающими в теле трубы, и в то же время для работы с данными, относящимися к одной и другой из двух схем расположения датчиков. 7. Устройство по одному из предыдущих пунктов, отличающееся тем, что преобразователь (891; 892) приспособлен для изолирования цифрового представления возможных максимумов эхо-сигналов в установленных временных окнах, которые соответствуют эхо-сигналам внутреннего слоя, эхо-сигналам внешнего слоя, а также эхо-сигналам в теле трубы соответственно, и тем, что контроллер (960) предусмотрен для работы с эхо-сигналами внутреннего слоя или с эхо-сигналами внешнего слоя либо с эхосигналами, возникающими в теле трубы. 8. Устройство по одному из предыдущих пунктов, отличающееся тем, что контроллер (960) выполнен с возможностью получения по меньшей мере одного входного сигнала (9511; 9521), относящегося к экстремуму амплитуды изображения зоны предполагаемого дефекта. 9. Устройство по одному из предыдущих пунктов, отличающееся тем, что фильтр (921; 922) выполнен с возможностью получения в качестве характеристик каждого предполагаемого дефекта его наклона и длины, при этом контроллер (960) выполнен с возможностью получения соответствующих входных сигналов наклона дефекта (931) и длины дефекта (932). 10. Устройство по одному из предыдущих пунктов, отличающееся тем, что фильтр (921; 922), контроллер (960), нейронный контур (970) и цифровой каскад принятия решения и тревоги (992) приспособ- 17021646 лены для многократного функционирования в последовательности зон предполагаемых дефектов (Zcur),определенных указанным фильтром (921; 922). 11. Устройство по п.10, отличающееся тем, что фильтр (921; 922), контроллер (960), нейронный контур (970) и цифровой каскад принятия решения и тревоги (992) приспособлены для альтернативного функционирования на внутреннем слое и на внешнем слое трубы. 12. Устройство по одному из предыдущих пунктов, отличающееся тем, что указанная схема типа нейронного контура включает первый нейронный контур (NC121-NC123), пригодный для определения природы дефекта среди множества предопределенных классов; второй нейронный контур (NC141-NC143), пригодный для определения серьезности дефекта. 13. Устройство по п.8, отличающееся тем, что два нейронных контура указанной схемы типа нейронного контура выполнены с возможностью получения следующих входных сигналов, которые отличаются входным сигналом (9512; 9522) количества максимальных соседних значений для первого нейронного контура; входным сигналом (9513; 9523) ширины эхо-сигналов для второго нейронного контура. 14. Устройство по одному из пп.12 и 13, отличающееся тем, что два нейронных контура выполнены с возможностью объединения выходных сигналов для уточнения прогноза. 15. Устройство по одному из предыдущих пунктов, отличающееся тем, что один и тот же датчик выполнен с возможностью осуществления передачи и приема ультразвуковых сигналов по меньшей мере для одной части схемы расположения датчиков. 16. Устройство неразрушающего контроля труб во время изготовления и в готовом состоянии, отличающееся тем, что включает схему расположения ультразвуковых датчиков выбранной геометрии, установленных в ультразвуковой связи с трубой посредством жидкой среды с относительным вращательно-поступательным движением между трубой и схемой расположения датчиков; контуры для возбуждения (70) этих элементов датчиков в соответствии с выбранным временным законом и для сбора (73) учитываемых обратных сигналов; устройство по одному из предыдущих пунктов. 17. Способ неразрушающего контроля железных или стальных изделий, таких как трубы или другие продолговатые изделия, во время изготовления и в готовом состоянии, включающий следующие этапы,на которых:a) обеспечивают схему расположения ультразвуковых датчиков выбранной геометрии, установленных в ультразвуковой связи с трубой посредством жидкой среды с относительным вращательнопоступательным движением между трубой и схемой датчиков;b) возбуждают (70) указанные ультразвуковые датчики по выбранному временному закону;c) анализируют принятые обратные сигналы (760-766) для получения из них информации о возможных дефектах в трубе, при этом данная информация включает амплитуду и время прохождения по меньшей мере одного эхо-сигнала, и для генерирования параллелепипедного трехмерного графика;d) выделяют цифровое представление возможных эхо-сигналов в указанных временных окнах в зависимости от относительного вращательно-поступательного движения (891; 892) и получают оттуда трехмерное изображение (901; 902) возможных дефектов в трубе, основываясь на трехмерном графике и на базе данных;e) генерируют сигнал соответствия или несоответствия изделия. 18. Способ по п.17, отличающийся тем, что этап е) включает этапы, на которых:e1) фильтруют (921; 922) изображения (901; 902) по критериям отбора с целью определения там зон предполагаемых дефектов (Zcur), а также свойств каждого предполагаемого дефекта; е 2) формируют (960) цифровые рабочие входные сигналы из части (951; 952) изображений, соответствующих зоне предполагаемого дефекта (Zcur), свойств предполагаемого дефекта в той же зоне после фильтра (921; 922) и данных контекста (740); е 3) применяют сформированные таким образом (960) входные сигналы по меньшей мере к одной схеме типа нейронного контура (970); е 4) производят цифровую обработку выходного сигнала схемы типа нейронного контура (970) по критериям принятия решения с целью выбора решения и/или сигнала тревоги (992); е 5) отбраковывают и маркируют (994) трубы, признанные неудовлетворительными на этапе е 4).
МПК / Метки
МПК: G01N 29/38, G01N 29/28, G01N 29/44, G01N 29/06, G01N 29/04
Метки: готовом, неразрушающий, изготовления, состоянии, время, труб, контроль, частности
Код ссылки
<a href="https://eas.patents.su/27-21646-nerazrushayushhijj-kontrol-v-chastnosti-dlya-trub-vo-vremya-izgotovleniya-i-v-gotovom-sostoyanii.html" rel="bookmark" title="База патентов Евразийского Союза">Неразрушающий контроль, в частности, для труб во время изготовления и в готовом состоянии</a>
Предыдущий патент: Твердая дозированная форма в виде таблетки и способ ее приготовления
Следующий патент: Подложка органического светоизлучающего устройства, а также органическое светоизлучающее устройство, содержащее ее
Случайный патент: Способ защиты животных от хронических заболеваний, вызванных инфекционными простейшими, в чатности защиты домашней птицы от заболевания кокцидиозом