Способ получения частиц сложного полиэфира при высокой производительности линии
Номер патента: 24875
Опубликовано: 31.10.2016
Авторы: Родригес Маурисио, Кристель Андреас, Кулберт Брент Аллан, Гигер Франц
Формула / Реферат
1. Способ получения термопластичного сложного полиэфира, включающий стадии, на которых:
a) получают частицы форполимера сложного эфира с характеристической вязкостью от 0,35 до 0,75 дл/г,
b) подвергают частицы форполимера сложного эфира кристаллизации для получения частично кристаллизованных частиц форполимера сложного эфира,
c) подогревают частично кристаллизованные частицы форполимера сложного эфира до приемлемой температуры реакции для получения нагретых частиц форполимера сложного эфира,
d) осуществляют реакцию поликонденсации нагретых частиц форполимера сложного эфира при температуре, достаточной для получения частиц полимера сложного эфира с характеристической вязкостью от 0,70 до 0,95 дл/г,
при этом реакцию на стадии d) проводят по меньшей мере в одном реакторе, в котором частицы перемещаются под действием силы тяжести, и время выдержки в реакторе составляет от 6 до 30 ч,
отличающийся тем, что частицы, по меньшей мере, на стадию d) подают при массовом расходе от 40 до 100 т/ч, скорость потока частиц в реакторе поддерживают от 2 до 6 м/ч, и стадию d) осуществляют в реакторе объемом от 400 до 3000 м3 с отношением L/D реактора от 5 до 11, где D - диаметр и L - длина.
2. Способ по п.1, отличающийся тем, что реакцию на стадии d) осуществляют в потоке инертного газа, причем продукты повышающих молекулярный вес реакций переносятся в газ, а разность между давлением у отверстия для впуска газа в реактор и давлением у отверстия для выпуска газа из реактора составляет от 450 до 1000 мбар.
3. Способ по п.1 или 2, отличающийся тем, что частицы форполимера сложного эфира между стадией b) кристаллизации и стадией с) подогрева подают с уровня (НА) расположения выходного отверстия на лежащий выше уровень (НЕ) расположения входного отверстия.
4. Способ по любому из пп.1-3, отличающийся тем, что частицы форполимера сложного эфира перед стадией с) пропускают через обеспыливающее устройство.
5. Способ по любому из пп.1-4, отличающийся тем, что частицы форполимера сложного эфира, полученные на стадии а), имеют содержание карбоксильных концевых групп (ХСООН), составляющее от 0,25 до 0,6, и что во время обработки на стадиях b), с) и d) доля реакции этерификации (Е) от реакций поликонденсации (Е+Т) составляет от 0,5 до 1.
6. Способ по любому из пп.1-5, отличающийся тем, что нагретые частицы форполимера сложного эфира, полученные на стадии с), подают с начального уровня (НО) на уровень (HR) расположения входного отверстия в реактор и тем, что уровень (HR) расположения входного отверстия лежит выше уровня (НО) расположения выходного отверстия на 40-80 м.
7. Способ по любому из пп.1-6, отличающийся тем, что подачу нагретых частиц форполимера сложного эфира, полученных на стадии с), осуществляют при температуре подачи (TF), которая ниже точки плавления кристаллов сложного полиэфира предпочтительно на 5-80°С.
8. Способ по любому из пп.1-7, отличающийся тем, что подачу нагретых частиц форполимера сложного эфира, полученных на стадии с), осуществляют с помощью пневматической подачи.
9. Способ по любому из пп.1-8, отличающийся тем, что подачу нагретых частиц форполимера сложного эфира, полученных на стадии с), осуществляют по подающему трубопроводу с внутренним диаметром (DF) от 250 до 500 мм.
10. Способ по любому из пп.1-9, отличающийся тем, что подачу осуществляют при скорости (vF) от 5 до 12 м/с.
11. Способ по любому из пп.1-10, отличающийся тем, что подачу нагретых частиц форполимера сложного эфира, полученных на стадии с), осуществляют по меньшей мере по двум подающим трубопроводам.
12. Способ по любому из пп.1-11, отличающийся тем, что по меньшей мере в одно отдельное устройство на стадиях b), с) или d) частицы подают при массовом расходе от 40 до 100 т/ч.
13. Устройство для осуществления способа получения термопластичного сложного полиэфира по любому из пп.1-12, содержащее:
a) реактор поликонденсации расплава для получения частиц форполимера сложного эфира с характеристической вязкостью от 0,35 до 0,75 дл/г,
b) по меньшей мере один кристаллизатор для кристаллизации частиц форполимера сложного эфира для получения частично кристаллизованных частиц форполимера сложного эфира,
c) по меньшей мере один подогреватель для нагрева частично кристаллизованных частиц форполимера сложного эфира до приемлемой температуры реакции для получения нагретых частиц форполимера сложного эфира,
d) по меньшей мере один реактор, выполненный с возможностью эксплуатации при температуре, достаточной для получения частиц форполимера сложного эфира с характеристической вязкостью от 0,70 до 0,95 дл/г,
отличающееся тем, что уровень (HR) расположения входного отверстия в реактор d) находится на 40-80 м выше уровня (НО) расположения выходного отверстия из подогревателя с), реактор d) имеет объем от 400 до 3000 м3, отношение L/D от 5 до 11, где D - диаметр и L - длина, и содержит средство регулирования скорости потока частиц в реакторе d) от 2 до 6 м/ч, для обеспечения возможности эксплуатации при массовом расходе от 40 до 100 т частиц в час и времени выдержки частиц в реакторе d) от 6 до 30 ч.
14. Устройство по п.13, отличающееся тем, что подогреватель с) и реактор d) соединены между собой посредством по меньшей мере двух подающих трубопроводов.
15. Устройство по любому из пп.13, 14, отличающееся тем, что подающие трубопроводы заведены в реактор d) раздельно, при этом входы ориентированы различно или же значительно отдалены друг от друга.
16. Устройство по любому из пп.13-15, отличающееся тем, что подающие трубопроводы имеют внутренний диаметр (DF) от 250 до 500 мм.
17. Устройство по любому из пп.13-16, отличающееся тем, что кристаллизатор b) и подогреватель с) расположены рядом и соединены между собой подающим трубопроводом.
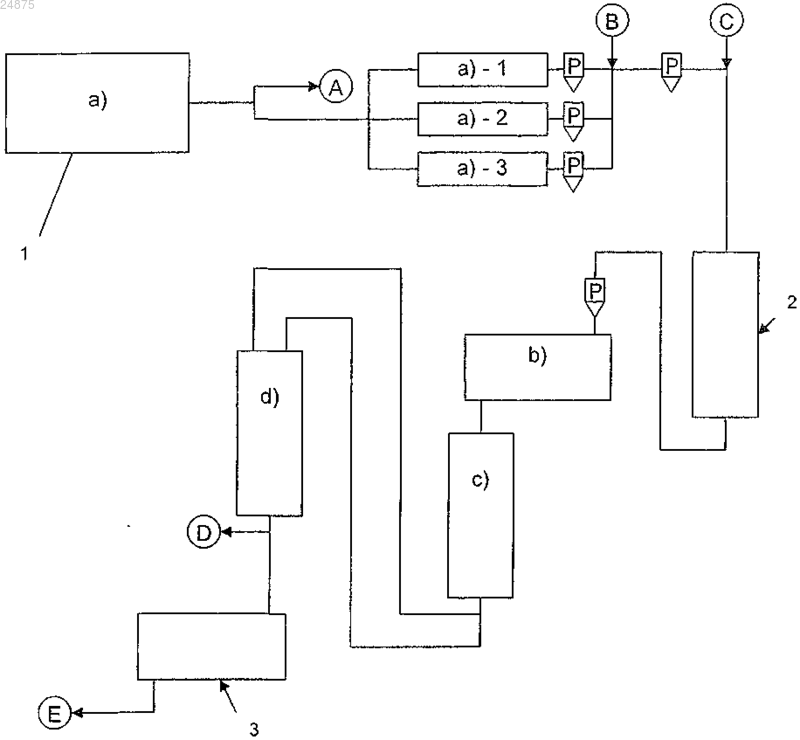
Текст
СПОСОБ ПОЛУЧЕНИЯ ЧАСТИЦ СЛОЖНОГО ПОЛИЭФИРА ПРИ ВЫСОКОЙ ПРОИЗВОДИТЕЛЬНОСТИ ЛИНИИ Настоящее изобретение относится к способу и устройству для получения термопластичного сложного полиэфира, при этом предусмотрены следующие стадии: а) получение частиц форполимера сложного эфира, b) кристаллизация частиц форполимера сложного эфира для получения частично кристаллизованных частиц форполимера сложного эфира, с) нагрев частично кристаллизованных частиц форполимера сложного эфира до приемлемой температуры реакции для получения нагретых частиц форполимера сложного эфира, d) реакция нагретых частиц форполимера сложного эфира для получения частиц форполимера сложного эфира с характеристической вязкостью от 0,70 до 0,95 дл/г. Реакция на стадии d) проводится по меньшей мере в одном реакторе, в котором частицы перемещаются под действием силы тяжести. Время выдержки частиц в реакторе составляет от 6 до 30 ч. По меньшей мере, на стадию d) частицы подаются при массовом потоке от 40 до 100 т/ч. Настоящее изобретение отличается тем, что скорость оседания частиц в реакторе составляет от 2 до 6 м/ч.(71)(73) Заявитель и патентовладелец: БЮЛЕР ТЕРМАЛЬ ПРОЦЕССЕС АГ Область техники, к которой относится изобретение Изобретение относится к способу получения термопластичного сложного полиэфира согласно родовому понятию п.1 формулы изобретения. Уровень техники Способы получения частиц сложного полиэфира посредством полимеризации в фазе расплава и последующей полимеризации в тврдой фазе на практике известны. Для повышения рентабельности таких способов постоянно требуется увеличивать пропускную способность производственной линии. При этом для обработки больших количеств продукта в тврдой фазе требуются крупные реакторы. Однако при использовании реакторов с большим диаметром мкости внутри реактора образуется продукт с высоким давлением, что в свою очередь ограничивает максимально допустимую температуру реакции и таким образом ведт к более продолжительному времени выдержки и применению реакторов ещ большего размера. Если же через реактор пропускается технологический газ, то с увеличением высоты реактора снижается давление в нм, что снова ограничивает допустимое количество технологического газа и, следовательно, также ведт к продолжительным выдержкам и ещ большим реакторам Одновременно вс больше возрастают затраты на эксплуатацию зданий при обработке больших количеств продукта из-за применения больших реакторов в том случае, когда нагрев частиц должен производиться на локальном уровне над реактором. Для того чтобы это исключить, горячие частицы могут подаваться со стадии нагрева к входному отверстию реактора. При большой высоте реактора создатся также большая высота подачи. Однако при большой высоте подачи повреждение продукта во время подачи выступает ограничивающим фактором. Следовательно, для обеспечения экономичного рабочего режима необходимо ограничить размер реактора, падение давления в нм и расходы на эксплуатацию здания. Одновременно с этим необходимо разработать щадящий способ подачи горячих частиц форполимера сложного эфира. Поэтому задачей настоящего изобретения является создание по возможности экономичного способа, обеспечивающего щадящую обработку больших количеств частиц сложного полиэфира в тврдой фазе. В источнике DE 10200502597 А 1 раскрыты реакторы, обрабатывающие до 60 т/ч гранулята сложного полиэфира. Приводятся данные о времени выдержки обрабатываемого материала в реакторе, объме реактора и о соотношении между длиной реактора и его диаметром. Однако не приводятся данные относительно того, как должен быть оптимально организован режим работы отдельного реактора для сведения к минимуму риска склеивания продукта, сопротивления потока газа и повреждения продукта во время подачи. Описано, что применяются несколько расположенных последовательно реакторов с несколькими путями подачи продукта и несколькими потоками технологического газа. По сравнению с уровнем техники настоящее изобретение позволяет задавать технологические условия, конструктивное выполнение реактора и выполнение пути подачи для достижения высокой производительности реактора. Раскрытие изобретения Согласно изобретению указанная задача решается способом получения термопластичного сложного полиэфира, содержащим признаки п.1 формулы изобретения в результате того, что обработка в реакторах ведтся в тврдой фазе, при которой частицы перемещаются с большой скоростью потока для предупреждения склеивания продукта при высокой температуре. Так согласно п.1 формулы изобретения способ получения термопластичного сложного полиэфира включает в себя стадии, на которыхa) получают частицы форполимера сложного эфира с характеристической вязкостью от 0,35 до 0,75 дл/г,b) подвергают частицы форполимера сложного эфира кристаллизации для получения частично кристаллизованных частиц форполимера сложного эфира,c) подогревают частично кристаллизованные частицы форполимера сложного эфира до приемлемой температуры реакции для получения нагретых частиц форполимера сложного эфира,d) осуществляют реакцию нагретых частиц форполимера сложного эфира при температуре, достаточной для получения частиц полимера сложного эфира с характеристической вязкостью от 0,70 до 0,95 дл/г,при этом реакцию на стадии d) проводят по меньшей мере в одном реакторе, в котором частицы перемещаются под действием силы тяжести, и время выдержки в реакторе составляет от 6 до 30 ч, отличающийся тем, что частицы, по меньшей мере, на стадию d) подают при массовом расходе от 40 до 100 т/ч, скорость потока частиц в реакторе поддерживают от 2 до 6 м/ч, и стадию d) осуществляют в реакторе объемом от 400 до 3000 м 3 с отношением L/D реактора от 5 до 11, где D - диаметр и L - длина. Кроме того, нагретые частицы форполимера сложного эфира посредством по меньшей мере одной стадии подачи поднимаются с начального уровня (НО) на уровень (HR) расположения входного отверстия в реактор, при этом уровень (HR) расположения входного отверстия находится выше начального уровня (НО) предпочтительно на 40-80 м. Кроме того, перед стадией подогрева частицы форполимера сложного эфира предпочтительно про-1 024875 пускаются через обеспыливающее устройство. Также настоящее изобретение относится к устройству для получения термопластичного сложного полиэфира, содержащему:a) реактор поликонденсации расплава для получения частиц форполимера сложного эфира с характеристической вязкостью от 0,35 до 0,75 дл/г;b) по меньшей мере один кристаллизатор для кристаллизации частиц форполимера сложного эфира для получения частично кристаллизованных частиц форполимера сложного эфира;c) по меньшей мере один подогреватель для нагрева частично кристаллизованных частиц форполимера сложного эфира до приемлемой температуры реакции для получения нагретых частиц форполимера сложного эфира;d) по меньшей мере один реактор для получения полимерных частиц сложного эфира с характеристической вязкостью от 0,70 до 0,95 дл/г, в котором перед подогревателем с) расположено обеспыливающее устройство, уровень (HR) расположения входного отверстия в реактор находится от 40 до 80 м выше уровня (НО) расположения выходного отверстия в подогревателе с), реактор d) имеет объем от 400 до 3000 м 3, отношение L/D от 5 до 11, где D - диаметр и L - длина, и выполнен с возможностью эксплуатации при массовом расходе от 40 до 100 т частиц в час, времени выдержки частиц в реакторе от 6 до 30 ч и скорости потока частиц в реакторе от 2 до 6 м/ч. Согласно предпочтительному варианту выполнения способ по изобретению необходимо применять в реакторах, через которые пропускается газовый поток, падение давления которого ограничивается для того, чтобы можно было применять реакторы, которые не относятся к классу мкостей, работающих под давлением. Согласно изобретению подача частиц производится на большое вертикальное расстояние в высокие реакторы, при этом предпочтительной является щадящая продукт подача при е низкой скорости, так как в этом случае снижаются истирание продукта и пылеобразование. Согласно другому предпочтительному варианту выполнения в способе согласно изобретению используется пневмотранспорт. Способ согласно изобретению предназначен для получения сложного полиэфира, причм, в частности, предпочтительным является получение полиэтилентерефталата или одного из его сополимеров. Сложными полиэфирами являются кристаллизуемые термопластичные поликонденсаты, как, например, полиэтилентерефталат, полибутилентерефталат, политриметилтерефталат, полиэтиленнафталат или политриметилнафталат, имеющие вид либо гомополимеров, либо сополимеров. Сложный полиэфир представляет собой полимер, получаемый поликонденсацией его мономеров,диолов и карбоновых кислот. Применяются разные, в большинстве случаев линейные или цикличные диолы с 2-10 атомами углерода. Также могут применяться разные, в большинстве свом ароматические дикарбоновые кислоты обычно с 1-3 ароматическими кольцами. Вместо дикарбоновой кислоты может использоваться также сложный диэфир, в частности сложный диметиловый эфир. Обычно сложные полиэфиры получают реакцией поликонденсации при отщеплении низкомолекулярного продукта реакции. При этом поликонденсация может протекать непосредственно между мономерами или через промежуточный продукт с последующей реакцией переэтерификации, при этом переэтерификация может проводиться в свою очередь с отщеплением низкомолекулярного продукта реакции или посредством полимеризации с раскрытием кольца. По существу, полученный при этом сложный полиэфир является линейным, при этом может образоваться незначительное количество ответвлений. Сложный полиэфир может представлять собой новый или же повторно применяемый материал. В сложный полиэфир могут вводиться добавки. В качестве последних пригодны, например, катализаторы, красители и пигменты, ультрафиолетовые блокаторы, вспомогательные средства для переработки, стабилизаторы, модификаторы ударной вязкости, порообразователи химического и физического типа, наполнители, зародышеобразователи, огнезащитные средства, пластификаторы, частицы, повышающие барьерные или механические свойства, армирующие тела, такие как шарики или волокна, а также реакционноспособные вещества, как, например, абсорбент кислорода, абсорбент ацетальдегида или вещества, увеличивающие молекулярный вес, и т.д. В качестве катализаторов применяются металлические элементы, как, например, сурьма, германий,алюминий или титан или также марганец, кобальт, пинк, олово или кальций. Содержание металлических элементов в сложном полиэфире составляет обычно от 5 до 400 ч./млн, при этом предпочтительно содержание сурьмы составляет от 20 до 300 ч./млн, германия от 10 до 150 ч./млн, алюминия, кобальта,цинка, олова или кальция от 10 до 200 ч./млн, титана от 5 до 20 ч./млн. Сложным полиэфиром, часто применяемым, прежде всего, при изготовлении полых изделий, например бутылок, является полиэтилентерефталат. Полиэтилентерефталат получают поликонденсацией при отщеплении низкомолекулярных продуктов реакции из его мономеров, диола и дикарбоновой кислоты. При этом диол состоит большей частью, в частности, более чем на 90 мол.% из этиленгликоля (1,2-этандиола), а компонент дикарбоновая кислота большей частью, в частности, более чем на 90 мол.% из терефталовой кислоты, причм содержание сомономера составляет в целом, как правило, от 1 до 15 мол.%, в частности от 2 до 10 мол.%. Вместо терефталовой кислоты может также применяться е соответствующий сложный диэфир, в частности сложный диметиловый эфир. При этом содержание сомономера соответствует сумме содер-2 024875 жания сомономера диола и содержания сомономера дикарбоновой кислоты. Содержание сомономера диола определяют как количество молей сомономеров диола от общего количества молей диолов. Содержание сомономеров дикарбоновой кислоты определяют как количество молей сомономеров дикарбоновой кислоты от общего количества молей дикарбоновой кислоты. В качестве сомономеров применяются дополнительные линейные, цикличные или ароматические диолы и дикарбоновые кислоты. Типичными сомономерами являются диэтиленгликоль, изофталовая кислота или 1,4-бис-гидроксиметилциклогексан. В качестве низкомолекулярных продуктов реакции образуются, например, вода, этиленгликоль,ацетальдегид, метанол, а также другие возможные диолы. Для получения частиц форполимера сложного эфира необходимо прежде всего приготовить расплав форполимера сложного эфира, который затем охлаждают и из которого формируют частицы. При этом расплав форполимера сложного эфира получают поликонденсацией мономеров в жидкой фазе (поликонденсация в фазе расплава). Обычно приготовление расплава поликонденсата проводится в виде непрерывного процесса. При этом обычно проводятся прежде всего стадия смешения мономеров (приготовление пасты),стадия этерификации и затем стадия преполиконденсации в вакууме. При традиционном способе получения сложного полиэфира стадия поликонденсации в реакторе для придания высокой вязкости (называемом также финишером) также проводится в вакууме. В результате образуется форполимер сложного эфира с собственной вязкостью обычно от 0,35 до 0,8 дл/г, в частности свыше 0,5 дл/г и меньше 0,7 дл/гLtd., 2003; глава 2.4.2). Сложный полиэфир можно также получать с помощью периодического технологического процесса (см., например, Modern Polyesters, Wiley Series in Polymer Science, Edited by JohnScheirs, J. WileySons Ltd., 2003, глава 2.4.1). В качестве альтернативы упомянутая выше стадия поликонденсации в реакторе для получения высокой вязкости может не проводиться. В результате образуется низковязкий форполимер сложного эфира с характеристической вязкостью обычно от 0,2 до 0,5 дл/г, в частности свыше 0,3 дл/г, но меньше 0,45 дл/г. Альтернативно расплав форполимера сложного эфира получают также расплавлением сложных полиэфиров в качестве исходного продукта. Это может производиться, например, в смесителе непрерывного действия или также в реакторе для полимеризации. При этом сложные полиэфиры находятся в тврдом состоянии, например в виде гранул, порошка или стружки. Обычно сложный полиэфир предпочтительно сушат перед его расплавлением. После расплавления может при необходимости проводиться дополнительная стадия поликонденсации. Также расплавлением и деполимеризацией уже полученный высокий уровень вязкости сложного полиэфира может быть сведн к более низкому. Расплав форполимера сложного эфира может быть также получен из смеси свежеполимеризированного сложного полиэфира и расплавленного сложного полиэфира, при этом расплавленный сложный полиэфир добавляется в свежеполимеризированный сложный полиэфир в конце процесса полимеризации или на промежуточной стадии. В частности, при плавлении вторично применяемых сложных лолиэфиров предпочтительно проверить расплав перед его объединением со свежеполимеризированным расплавом путм линейного измерения или измерения в режиме он-лайн на качественные признаки, например на вязкость или цвет с тем,чтобы можно было отвести возможные низкокачественные продукты, например, в отдельный гранулятор и тем самым предупредить загрязнение, нового материала. Линейное измерение проводится в этом случае непосредственно в расплавленном форполимере. Измерение в режиме он-лайн может проводиться в боковом потоке расплава или в изготовленном из него пробном теле, жгуте, ленте, грануляте и пр. Обычно расплав форполимера сложного эфира подвергается фильтрации с целью отделения тврдых примесей, при этом в зависимости от вязкости применяются сита с размером ячейки от 5 до 150 мкм. Согласно изобретению получают расплав форполимера сложного эфира с характеристической вязкостью от 0,35 до 0,75 дл/г, предпочтительно свыше 0,45 дл/г, в частности свыше 0,50 дл/г, предпочтительно менее 0,7 дл/г, в частности менее 0,65 дл/г. Характеристическая вязкость (IV) указывает при этом на вязкость раствора и определяется в соответствии со следующим предписанием. Для измерения вязкости раствора применяют смесь из фенола и дихлорбензола (50:50 вес.%) в качестве растворителя. Пробу из сложного полиэфира растворяют в течение 10 мин при 130 С при концентрации 0,5% (0,5 г/дл). Измерение относительной вязкости (R.V.) проводится при 25 С с помощью вискозиметра Ubbelohde (в соответствии со стандартом DIN53728, ч. 3, от января 1985 г.). Относительная вязкость - это частное от деления вязкости раствора на вязкость чистого растворителя, которое сопоставимо с соотношением соответствующей скорости капиллярного течения. Величина характеристической вязкости определяется уравнением Хаггинса из замеренной относительной вязкости Приведнные выше методы измерения (концентрации полимера С = 0,5 г/дл и постоянной Хаггинса Вязкость сложного полиэфира может указываться либо в виде характеристической вязкости (IV),либо в виде среднего молекулярного веса (среднее число Mn). Для пересчта измеренного в феноле показателя IV дихлорметан = 11 в средний молекулярный вес применяется уравнение где: k = 2.1 Е-4 и а = 0,82. Это уравнение применяется, как правило, применительно к опубликованным данным в том случае,когда не является явной другая смесь растворителей и не приведены соответствующие коэффициенты пересчта. Из среднего молекулярного веса рассчитывается концентрация (EGN) концевых групп по уравнениюEGN = 2E6/Mn,где Mn применяется в г/моль, a EGN получают в моль/т. С помощью концентрации карбоксильных концевых групп (CCOOH) и концентрации концевых групп рассчитывается содержание отдельных концевых групп, при этом для упрощения учитывается только присутствие гидроксильных и карбоксильные концевых групп, в результате чего EGN = CCOOH + COH. Содержание карбоксильных концевых групп XCOOH = CCOOH/EGN; содержание гидроксильных концевых групп XOH = COH/EGN = (1 - XCOOH). При этом CCOOH означает концентрацию карбоксильных концевых групп в моль/т, а COH - концентрацию гидроксильных концевых групп в моль/т. Согласно предпочтительному варианту выполнения настоящего изобретения количество диола и дикарбоновой кислоты, а также режим способа получения форполимера сложного эфира выбираются с таким расчтом, чтобы образовался форполимер сложного эфира с содержанием карбоксильных концевых групп от 0,25 до 0,6, причм содержание карбоксильных концевых групп составляет предпочтительно более 0,30, в частности более 0,35, предпочтительно менее 0,55, в частности менее 0,5. Частицы могут формироваться из расплава форполимера сложного эфира разными способами. Возможно применять измельчение кусков, жгутов или лент, образованных из расплава полимера, или применять прямое формование частиц, например, капанием или распылением. Охлаждение и формование из расплава форполимера сложного эфира проводится обычно грануляцией. При грануляции расплав форполимера сложного эфира выдавливается через головку экструдера с отверстием или множеством отверстий, режется или вытекает в виде капель. Отверстия в головке экструдера являются обычно круглыми, однако они могут иметь и другой профиль, например щелевой. Необходимо обращать внимание на то, чтобы количество вытекающего через отверстие головки экструдера продукта выдерживалось в узком диапазоне в отношении времени и места,причм стандартное отклонение отдельных количеств потока продукта должно выдерживаться от 0,1 до 10%. Для того чтобы этого достигнуть, должен варьироваться диаметр или длина отверстия головки экструдера в зависимости от его положения. Одновременно с этим необходимо следить по возможности за равномерными условиями притекания к отдельным отверстиям головки экструдера (давлением, скоростью, температурой, вязкостью и пр.). Резание может производиться либо непосредственно на выходе из головки экструдера или же после прохождения через участок обработки. Охлаждением обеспечивается отверждение расплава форполимера сложного эфира. Охлаждение может достигаться жидким хладагентом (например, водой, этиленгликолем) или газообразным хладагентом (например, воздухом, азотом, водяным паром) или в результате контакта с холодной поверхностью,причм возможна комбинация хладагентов. Охлаждение может проводиться либо одновременно, либо до или после формования частиц. Известными способами грануляции являются, например, роторное формование, стренговая грануляция, водокольцевая грануляция, подводная грануляция или грануляция на выходе из головки экструдера (также грануляция с горячей поверхностью), а также капание или распыление. Такие способы описаны, например, в источниках WO 00/23497 Matthaei; WO 01/05566 Glockner и др.; WO 05/087838 Christel и др.; WO 03/054063 Culbert и др.; WO 96/22179 Stoufier и др., которые включены в настоящее изобретение. При использовании жидкого хладагента его необходимо отделить, что частично проводится с помощью простых отделителей, таких как сетки или грохоты, и дополнительно посредством центробежной силы, например, в центробежной сушилке, посредством удара, например, в ударной сушилке, и/или посредством газового потока. Средний размер гранул должен составлять от 0,1 до 10 мм, предпочтитгльно от 0,5 до 3 мм, в част-4 024875 ности от 0,85 до 2,5 мм. Средним размером гранулы считается статистическая средняя величина среднего диаметра гранулы, которая выводится из средней величины высоты гранулы, е длины и ширины. Распределение размеров гранул должно поддерживаться в узком диапазоне. Предпочтительным является стандартное отклонение веса 100 замеренных гранул, составляющее от 2 до 20%. Гранулы могут иметь заданную форму, например цилиндрическую, шарообразную, каплеобразную, шаровидную или в виде дизайна, предложенного, например, в ЕР 0541674 В 1. Могут применяться тврдые или пористые гранулы, полученные, например, вспениванием, спеканием и пр. Охлаждение может проводиться до температуры, лежащей ниже температуры стеклования сложного полиэфира, что позволяет производить погрузку и/или транспортировку гранулята в течение продолжительного отрезка времени. Однако среднюю температуру гранул из форполимера сложного эфира можно поддерживать и на более высоком уровне для повышения энергетической эффективности последующих процессов. Для этого можно поднять температуру хладагента и/или выбрать более короткое время выдержки в хладагенте. Несмотря на то, что частичная кристаллизация может происходить при получении частиц форполимера сложного эфира, обычно требуется стадия кристаллизации для получения частично кристаллизованных частиц форполимера сложного эфира. Кристаллизация может проводиться самостоятельно или же одновременно с получением частиц. Несколько устройств для получения частиц могут быть сопряжены с устройством кристаллизации. Кристаллизация может протекать в одну стадию или в несколько стадий и следовательно в одном или нескольких последовательно расположенных устройствах. Кристаллизация может проводиться непрерывно или периодически. При необходимости кристаллизация может проводиться в двух и более одновременно работающих устройствах. Кристаллизация проводится с применением известных из уровня техники способов, например способом термической кристаллизации, способом индуцированной растворителем кристаллизации или способом механической вытяжки. Предпочтительно кристаллизация проводится термическим способом, при котором образуется термически частично кристаллизованный поликонденсат. Кристаллизация должна проводиться при соответствующей температуре и соответствующем времени выдержки. В результате кристаллизации должна быть достигнута по меньшей мере одна степень кристаллизации, обеспечивающая дополнительную термическую обработку, как, например, сушку или твердофазную поликонденсацию с исключением склеивания или комкования. Соответствующий температурный диапазон становится очевидным, если полупериод кристаллизации (t1/2), замеренный способом дифференциальной сканирующей калориметрии (DSC), будет нанесн в виде температурной функции. Этот диапазон ограничивается вверх и вниз температурой, при которой полупериод кристаллизации достигает величины, превышающей приблизительно в 10 раз минимальный полупериод кристаллизации t1/2 мин. Учитывая, что очень короткие полупериоды кристаллизации (t1/2) трудно определять, в качестве минимальной величины принимается t1/2 мин = 1 мин. Приемлемая продолжительность выдержки выводится из времени, необходимого для нагрева продукта до температуры кристаллизации, с которым суммируется по меньшей мере один полупериод кристаллизации при данной температуре, причм к времени нагрева добавляются предпочтительно 2-20 полупериодов для обеспечения достаточной кристаллизации. Для исключения склеивания кристаллизуемых частиц форполимера последние должны совершать движения относительно друг друга. Приемлемыми реакторами для кристаллизации являются вибрирующие реакторы, вращающиеся реакторы, реакторы с мешалками и реакторы, через которые пропускается технологический газ, при этом скорость потока технологического газа должна быть достаточной для перемещения частиц форполимера. Предпочтительны скорости потока от 1 до 6 м/с, в частности свыше 1,5 м/с и меньше 4 м/с. При этом скорость движения газа соответствует скорости движения в пустой трубе,т.е. количеству газа в единицу времени, делнному на сечение пространства, в котором проводится обработка. Особо пригодными реакторами для кристаллизации являются кристаллизаторы с псевдоожиженным или кипящим слоем, поскольку они не вызывают пылеобразования. Для полиэтилентерефталата приемлемый температурный диапазон составляет от 100 до 220 С, при этом через 5-20 мин достигается степень кристаллизации, составляющая не менее 20%, предпочтительно не менее 30%. Кристаллизация может проводиться из стеклообразного состояния, т.е. после временного охлаждения до температуры ниже температуры кристаллизации, в частности ниже температуры стеклования Tg. Пригодными к применению являются способы, в которых кристаллизация протекает, по меньшей мере, частично из расплава, причм кристалличность возрастает на фазе охлаждения и/или выдержки при повышенной температуре. Если температура частиц форполимера сложного эфира при подаче в процесс кристаллизации составляет менее соответствующей температуры кристаллизации, то частицы форполимера сложного эфира необходимо нагревать. Это может производиться, например, посредством нагретой стенки реактора для кристаллизации, нагретых внутренних устройств реактора для кристаллизации, облучения или вдувания горячего технологического газа. Одновременно с повышением степени кристаллизации также выводятся из процесса грануляции возможные остатки жидкости. Если в процессе кристаллизации применяется циркулирующий технологический газ, то в него необходимо добавлять достаточное количество свежего газа или очищенного технологического газа для предупреждения избыточной концентрации жидкости или других обратно диффундирующих веществ. В качестве технологического газа могут применяться, например, воздух, водяной пар или инертные газы,такие как азот, СО 2, или их смеси. Технологические газы могут содержать в себе добавки, которые либо оказывают реакционное действие на обрабатываемый продукт, либо пассивно осаждаются на обрабатываемом продукте. В контур циркуляции технологического газа могут быть встроены дополнительные агрегаты, такие как теплообменники, отделители, такие как фильтры или циклоны, агрегаты для подачи газа, такие как воздуходувки, компрессоры или вентиляторы, газоочистительные системы, такие как скрубберы, системы для сжигания или абсорбционные системы, или арматура, такая как клапаны, вентили или ответвители. При необходимости перед кристаллизацией частицы форполимера сложного эфира могут подвергаться обработке для снижения их склеивающей способности, как это описано в источнике РСТ/СН 2008/000389, который включен в настоящее изобретение. При необходимости частицы форполимера сложного эфира могут подогреваться перед кристаллизацией. Это может проводиться на стадии подогрева, причм подаваемое тепло отводится от стадии охлаждения, как описано в источнике ЕР 01789469 В 1, который включн в настоящее изобретение. В качестве альтернативы тепло может создаваться непосредственно для подогрева или за счт рекуперации тепла из его источника, которым является предшествующий процесс полимеризации из фазы расплава. При получении полиэтилентерефталата используется, например, пар из колонны для отделения воды от этиленгликоля в качестве источника тепла на стадии подогрева. Особо пригодными аппаратами для кристаллизации являются аппараты с псевдоожиженным слоем,как, например, описанные в источнике ЕР-1425146 А 2, соответствующая часть содержания которого включена со ссылкой в настоящую заявку. Нагрев до температуры кристаллизации и последующая кристаллизация могут проводиться в одном или нескольких кристаллизаторах. Размер требуемых аппаратов указывается при этом в виде суммы всех поверхностей ситовых полотен аппаратов, причм для обработки от 40 до 100 т/ч требуется поверхность рабочего полотна сита от 10 до 100 м 2. При кристаллизации холодных гранул из полиэтилентерефталата требуется поверхность ситовых полотен от 20 до 60 м 2. После кристаллизации необходим нагрев частично кристаллизованных частиц форполимера сложного полиэфира до соответствующей температуры реакции для получения нагретых частиц форполимера сложного эфира. Согласно изобретению было установлено, что для работы установки с высокой производительностью очень выгодно подавать частично кристаллизованные частицы форполимера сложного эфира через обеспыливающее устройство, так как в противном случае снижается эффективность при проведении последующих рабочих операций. Нагрев может проводиться самостоятельно или в сочетании с кристаллизацией. Несколько устройств для кристаллизации могут быть сопряжены с нагревательным устройством Нагрев может происходить в один или несколько примов и следовательно в одном или нескольких последовательно расположенных устройствах. Нагрев может быть непрерывным или периодическим. При необходимости нагрев может проводиться в двух или более одновременно работающих устройствах. Пригодными устройствами для нагрева являются вращающиеся реакторы, реакторы с мешалками и реакторы, через которые пропускается технологический газ. Пригодная температура реакции лежит в диапазоне, который ограничен вниз минимальной скоростью реакции сложного полиэфира и вверх температурой, лежащей незначительно ниже температуры плавления сложного полиэфира. Обычно температура реакции ниже температуры кристаллизации расплава сложного полиэфира на 5-80 С. Одновременно с нагревом проводится термообработка, в результате которой кристаллическая структура улучшается настолько, что снижается способность частиц форполимера сложного эфира к склеиванию. При этом термообработка может проводиться при соответствующей температуре реакции или же при температуре, превышающей температуру реакции на 1-30 С. Если термообработка проводится при более высокой температуре, то температуру частиц форполимера сложного эфира необходимо снизить до температуры реакции. Продолжительность нагрева определяется при этом необходимой кристаллизацией и может составлять от нескольких минут до нескольких часов. Если нагрев происходит, по существу, под действием технологического газа, то применяется соотношение количества газа к количеству продукта (mg/mp), равное 1,5-15, в частности 2,5-10, в результате чего температура продукта существенно приближается к температуре газа. При этом mp означает сумму всех подаваемых в процесс потоков продукта, mg - сумму всех подаваемых в процесс газовых потоков. В качестве технологического газа могут служить, например, инертные газы, такие как азот, СО 2, или смеси инертных газов. В технологическом газе могут содержаться добавки, которые либо оказывают реакционное действие на обрабатываемый продукт, либо пассивно осаждаются на обрабатываемый продукт. Если для нагрева используется циркулирующий технологический газ, то в него необходимо добавлять достаточное количество свежего газа или очищенного технологического газа с тем, чтобы исключалась избыточная концентрация обратно диффундируемых веществ. В контур циркуляции технологического газа могут быть встроены дополнительные агрегаты, такие как теплообменники, отделяющие агрегаты, такие как фильтры или циклоны, агрегаты для подачи газа,такие как воздуходувки, компрессоры или вентиляторы, газоочистительные системы, такие как скрубберы, системы сжигания или абсорбционные системы или арматура, такая как клапаны, вентили или ответвители. Для полиэтилентерефталата типичное время нагрева и термообработки составляет от 10 мин до 2 ч,температура термообработки - от 200 до 245 С. Содержание кислорода в инертном газе должно составлять менее 500 ч./млн, в частности менее 100 ч./млн. В виде варианта предусмотрено, чтобы нагрев проводился в течение менее 10 мин. Это описано в источнике WO 02/068498, включнном в состав настоящего изобретения. Особо пригодными для подогрева аппаратами являются крышеобразные аппараты (такие как описанные, например, в DE 4300913 А 1), аппараты с перекрстными потоками (такие как описанные, например, в ЕР-1019663 А 1) и противоточные аппараты (такие как описанные, например, в СН-101579610 А (соответствует находящейся на рассмотрении патентной заявки Швейцарии СН 0735/08). Соответствующие части описания этих заявок на патент включены в настоящую заявку путм ссылки на них. Подогрев может проводиться в одном или нескольких аппаратах. Размер требуемого аппарата указывается при этом в виде суммы всех объмов аппаратов, причм для обработки 40-100 т/ч требуются объмы аппаратов от 50 до 300 м 3, высота аппаратов составляет от 10 до 50 м. После нагрева требуется проведение реакции нагретых частиц форполимера сложного эфира для получения характеристической вязкости этих частиц от 0,70 до 0,95 дл/г, в частности более 0.75 дл/г. При этом повышение характеристической вязкости должно составлять не менее 0.05, в частности не менее 0,1 дл/г. Реакция нагретых частиц форполимера сложного эфира происходит в соответствующем, по существу, вертикальном реакторе. Согласно изобретению нагретые частицы форполимера сложного эфира подаются в верхнюю часть реактора, откуда эти частицы под действием силы тяжести перемещаются в реакторе сверху вниз. Частицы сложного полиэфира перемещаются при этом в реакторе в виде плотного слоя, который может быть также обозначен, как движущийся плотный слой. При этом стремятся по возможности к узкому диапазону времени выдержки отдельных частиц. Завихрения или другого активного перемешивания частиц необходимо избегать. Несколько нагревательных устройств могут быть связаны с реактором. Обычно реакция проводится в реакторе. При необходимости реакция может протекать в двух и более одновременно работающих реакторах, причм каждый отдельный реактор работает в соответствии с признаками изобретения. Согласно изобретению реакция проводится в реакторе при показателе IV 0,7 дл/г. По выбору могут применяться дополнительные реакторы для дополнительной обрабатывающей операции. Реакция проводится при температуре, лежащей ниже точки плавления кристаллов частиц сложного полиэфира на 5-80 С, при этом предпочтительными являются температуры, которые ниже точки плавления кристаллов частиц поликонденсата менее чем на 60 С и/или более чем на 20 С. В результате реакции и продолжающейся кристаллизации во время реакции температура частиц сложного полиэфира может возрасти на 120 С, причм образующаяся при этом максимальная температура также должна находиться в диапазоне приемлемой температуры реакции. Приемлемое время реакции составляет от 6 до 30 ч, причм по экономическим соображениям время выдержки составляет предпочтительно менее 24 ч, в частности менее 20 ч, но более 8 ч. Согласно предпочтительному варианту выполнения настоящего изобретения частицы сложного полиэфира омываются в реакторе технологическим газом. В качестве технологического газа могут применяться инертные газы, такие как азот, CO2 или смеси инертных газов. Технологический газ может содержать добавки, которые либо оказывают реакционное действие на обрабатываемый продукт, либо пассивно осаждаются на нм. Технологический газ движется, по существу, по контуру. В целях исключения отрицательного воздействия на реакцию поликонденсации технологический газ необходимо очищать от нежелательных продуктов, в частности от продуктов расщепления при реакциях поликонденсации. Типичные продукты расщепления, такие как вода, диолы (например, этиленгликоль, пропандиол, бутандиол) или альдегиды (например, ацетальдегид) должны быть при этом сведены до содержания менее 1000 ч./млн. При этом продукты расщепления обратимых реакций поликонденсации должны быть уменьшены до значений менее 100 ч./млн. Данные в ч./млн приведены в качестве весовых долей. Очистка может проводиться с помощью известных из уровня техники систем газовой очистки, таких как, например, системы каталитического сжигания, скрубберы, адсорбционные системы или охлаждаемые ловушки. Системы каталитического сжигания известны, например, из WO 00/07698, ЕР 0660746 В 2 и DE 102004006861 А 1, которые включены в настоящее изобретение. Могут применяться несколько систем очистки. Могут быть предусмотрены дополнительные стадии очистки. Отделение тврдых веществ может производиться, например, с помощью фильтров или циклонов. Для очистки в газоочистительной системе могут применяться разные объединнные или раздельные газовые потоки. Обычно в контур вводится дополнительно некоторое количество свежего технологического газа. В контур технологического газа могут быть также встроены дополнительные агрегаты, такие как теплообменники, агрегаты для подачи газа, такие как воздуходувки, компрессоры или вентиляторы, или арматура, такая как клапаны, вентили или ответвители. Для полиэтилентерефталата соответствующая температура дополиконденсации составляет от 190 до 240 С, причм предпочтительна температура ниже 225 С. В качестве продуктов расщепления при обратимых реакциях поликонденсации образуются, в частности, вода и этиленгликоль. Если реакция протекает, по существу, под действием технологического газа, то применяется соотношение между количеством газа и количеством продукта (mg/mp) от 0,2 до 2, в частности от 0,6 до 1,4,благодаря чему температура газа приближается, по существу, к гемпературе продукта. При этом mp означает сумму всех подведнных к процессу потоков продукта, a mg - сумму всех подведнных к процессу газовых потоков. В один реактор могут подаваться один или несколько газовых потоков, отличающихся, в частности, своей температурой. Подведнный поток технологического газа может иметь температуру, которая выше, располагается внутри или ниже диапазона приемлемой температуры реакции. Если температура частиц сложного полиэфира должна сохраняться постоянной при впуске газа, то технологический газ необходимо нагреть до температуры частиц сложного полиэфира. Если же температуру частиц сложного полиэфира необходимо понизить при впуске газа, то этот газ может подводиться с более низкой температурой. Обычно технологический газ податся в реактор в его нижнем конце и отводится из него на его верхнем конце, благодаря чему поток технологического газа движется встречно потоку частиц сложного полиэфира. Возможно и наоборот, когда поток движется с верхнего конца реактора к его нижнему концу прямотоком. Вследствие сопротивления потока в реакторе, заполненном частицами сложного полиэфира, создатся разность давлений на входе и выходе газа, причм эта разность давлений зависит от высоты реактора, размера и формы частиц сложного полиэфира, а также от скорости газа и следовательно его количества и от диаметра реактора. Согласно предпочтительному варианту выполнения настоящего изобретения разность давлений между местом впуска газа в реактор и местом его выпуска из реактора составляет от 450 до 1000 мбар. Предпочтительной является разница давлений свыше 500 мбар и менее 900 мбар В месте выпуска из реактора присутствует избыточное давление от 20 до 300 мбар, причм вследствие повышенного начального давления, составляющего предпочтительно более 50 мбар, в частности более 100 мбар, снижается скорость движения газа в реакторе и следовательно падение давления в нм. Пригодными реакторами являются шахтные реакторы, называемые также реакторами с неподвижным слоем или реакторами с движущимся слоем. Обычно шахтный реактор имеет цилиндрическую форму, например, круглого или прямоугольного сечения. При этом реактор закрыт сверху крышкой, а снизу выпускным конусом. Реактор диаметром (D) и длиной (L) обычно имеет соотношение L/D от 5 до 11. При этом L относится к цилиндрической части реактора без учта выпускного конуса и D означает средний диаметр по длине цилиндрической части, при этом применяются при круглом сечении непосредственно диаметр, при квадратном сечении длина кромки и при неравномерном сечении корень из площади поверхности поперечного сечения. Размер необходимых реакторов указывается при этом в виде суммы всех объмов реакторов, причм для обработки 40-100 т/ч требуются объмы реакторов от 400 до 3000 м 3, в частности более 500 м 3, а высота аппаратов составляет вместе с выпускным конусом от 30 до 60 м, в частности более 40 м. Реактор может содержать внутренние устройства, предназначенные, например, для выравнивания условий потока, для впуска газа или для снижения давления на продукт. Подобные реакторы раскрыты,например, в источниках ЕР 1337321 B1, US 6010667 и DE 102007031653 А 1, включнных в настоящее изобретение. Для исключения тепловых потерь реактор может быть наружно изолирован и/или снабжн нагревательными элементами. Возможные трубопроводы для подачи частиц сложного полиэфира могут быть при этом встроены в реактор или, по меньшей мере, в изоляцию вокруг реактора, вследствие чего снижаются тепловые потери в подающем трубопроводе. Согласно изобретению частицы форполимера сложного эфира подаются на стадию реакции в виде массового потока от 40 до 100 т/ч, при этом, в частности, частицы форполимера сложного эфира поступают в реактор в виде массового потока в количестве от 40 до 100 т/ч. Согласно изобретению скорость оседания частиц сложного полиэфира в реакторе составляет от 2 до 6 м/ч. Предпочтительно скорость оседания составляет более 2,2, ещ более предпочтительно более 2,6, в частности более 3 м/ч. Скорость оседания рассчитывается по массовому потоку частиц, который делят на насыпной вес частиц и на среднюю площадь сечения реактора. Поток частиц форполимера сложного эфира в качестве продукта регулируется при подаче в реактор и выходе из него блокирующими устройствами, такими как лопастные питатели, задвижки и/или подающие устройства. Вследствие большой скорости осаждения частиц сложного полиэфира в реакторе происходит интенсивное движение отдельных частиц относительно друг друга. В результате снижается способность к склеиванию гранул сложного полиэфира, что обеспечивает обработку при высоких температурах, в результате чего в свою очередь снижается необходимое время выдержки и следовательно необходимый размер реактора. Снижение способности к склеиванию объясняется более коротким временем контакта между двумя граничными поверхностями двух частиц, что сокращает зависящий от температуры, выходящий за пределы граничных поверхностей обмен свободно подвижных концов полимерной цепи. Вследствие также зависящей от температуры скорости реакции снижается время выдержки для определнного повышения характеристической вязкости. Таким образом при заданной ограничивающей способности к склеиванию продукта в результате повышения скорости осаждения возможно уменьшить размеры реактора. Если измеряется концентрация концевых групп в сложном полиэфире, в частности в полиэтилентерефталате, до и после реакции, то можно определить количество реакций этерификации (Е) и реакций переэтерификации (Т) в расчте на одну тонну материала. Е = CCOOH начало - CCOOH окончание,Т = (COH начало - COH окончание - Е)/2. На основании полученных долей становится очевидным, будет ли протекать реакция многократно через реакцию этерификации Е/(Е+Т) 0,5 или многократно через реакцию транс-этерификации Е/(Е+Т)0,5. Согласно предпочтительному варианту выполнения настоящего изобретения реакция должна протекать более чем на 50%, в частности более чем на 65%, предпочтительно более чем на 70% через реакцию этерификации. Для этого применяются также возможные реакции на предшествующих стадиях кристаллизации и нагрева. Благодаря предпочтительному применению реакции этерификации снижается способность продукта к склеиванию, что в свою очередь позволяет применять повышенные температуры реакции и следовательно реакторы меньшего размера. Обычно частицы форполимера сложного эфира поступают после нагрева в верхнюю часть реактора. Согласно варианту выполнения настоящего изобретения частицы форполимера сложного эфира поднимаются с начального уровня (НО) на уровень расположения (HR) входного отверстия в реактор,причм уровень расположения (HR) входного отверстия находится на 40-80 м, предпочтительно более чем на 45 м, в частности более чем на 50 м, выше начального уровня (НО). Этим обеспечивается преимущество, состоящее в том, что нагревательные устройства могут быть установлены в здании на низком уровне и не обязательно над реактором. При необходимости над реактором может располагаться буферная мкость и/или устройство для обеспыливания частиц форполимера сложного эфира, причем в этом случае уровень расположения входного отверстия в буферную мкость и/или обеспыливающее устройство определяет уровень расположения (HR) входного отверстия. Если обеспыливание производится под действием технологического газа, то в результате может повыситься или понизиться температура продукта, причм, в частности, поправки возможны в диапазоне 20 С. В качестве подающих устройств пригодны механические подающие устройства, такие как шнековые, цепные или ковшовые подающие устройства, а также пневматические подающие устройства. Особенно пригодны пневматические подающие устройства для подачи с низкой скоростью, которые приводятся в действие инертным газом. Пневматическое подающее устройство для подачи с низкой скоростью содержит при этом по меньшей мере один сборник, в который поступают продукт и подающий газ, устройство для создания давления подающего газа, дозатор для продукта, подающий трубопровод для отвода смеси из продукта и газа из сборника, а также клапаны для регулирования подвода подающего газа. При этом сборник может состоять из одной или нескольких мкостей или только из загрузочной воронки для подающего трубопровода. При этом устройство для создания напора подающего газа может содержать нагнетатель, такой как компрессор или вентилятор, а также возможные буферные баки. Для создания напора подающего газа может проводиться дополнительный нагрев подающего газа. Дозатор может содержать лопастные питатели, задвижки или шнековые дозаторы Для непрерывного режима работы предпочтительными являются, в частности, лопастные питатели, причм при доставке на большие расстояния и следовательно при больших потерях напора предпочтительно применять два последовательно установленных лопастных дозатора, так как в результате этого снижается падение давления посредством лопастного питателя и таким образом уменьшается количество теряемого при утечках газа. Подающий трубопровод может состоять из нескольких горизонтальных или косо установленных отдельных участков и трубных колен. Трубные колена должны иметь такой радиус, который более чем в три раза, в частности более чем в четыре раза, обычно менее чем в десять раз превышает диаметр трубопровода. Диаметр подающего трубопровода может изменяться на участке транспортного пути, например,для компенсации расширения подающего газа при снижении давления. Отдельные участки транспортного пути с разными диаметрами соединены между собой на переходных участках. С помощью клапанов подача подающего газа может управляться поочердно перед и за сборником для образования групп продуктов, которые затем перемещаются по подающему трубопроводу. Согласно предпочтительному варианту выполнения настоящего изобретения подача нагретых частиц форполимера сложного эфира производится по двум или более подающим трубопроводам. В результате может быть, во-первых, ограничена пропускная способность подающим трубопроводом и, вовторых, может быть предусмотрено наличие параллельного подающего трубопровода в качестве резервного с тем, чтобы исключить возможные производственные сбои, вызванные простоем подающего трубопровода. Каждому подающему трубопроводу могут быть приданы устройства для создания напора и для дозирования, а также клапаны. Однако можно также соединить устройство для создания напора и/или для нагрева подающего газа с двумя и более подающими трубопроводами. Температура подающего газа выбирается с таким расчтом, чтобы температура частиц форполимера сложного эфира при подаче изменялась не существенно, в частности менее чем на 10 С, при этом, в частности, необходимо избегать повышения температуры. Обычно применяется температура подающего газа от 60 до 250 С, предпочтительно свыше 100 С и ниже 230 С, в частности свыше 150 С. Согласно предпочтительному варианту выполнения настоящего изобретения подача нагретых частиц форполимера сложного эфира проводится при температуре подачи (TF), причм TF ниже температуры плавления кристаллов сложного полиэфира на 5-80 С, в частности более чем на 20 С и менее чем на 60 С. При получении полиэтилентерефталата температура подачи (TF) составляет предпочтительно от 190 до 230 С, в частности свыше 200 С и менее 225 С. Под температурой подачи понимается температура частиц форполимера сложного эфира в конце участка подачи. Согласно другому предпочтительному варианту выполнения настоящего изобретения подача нагретых частиц форполимера сложного эфира производится по подающему трубопроводу с внутренним диаметром (DF) от 250 до 500 мм, в частности свыше 290 мм и менее 450 мм. При этом подающий трубопровод имеет обычно круглое сечение. Внутренний диаметр соответствует при круглом сечении свободному диаметру сечения, при другом сечении он равен корню квадратному из свободной площади сечения. Согласно ещ одному предпочтительному варианту выполнения настоящего изобретения подача нагретых частиц форполимера сложного эфира проводится при скорости (vF) от 5 до 12 м/с. Под скоростью подачи здесь понимается скорость подающего газа в пустой трубе при заданных рабочих условиях на участке в конце пути подачи, причм скорость в пустой трубе соответствует количеству газа в единицу времени, делнному на сечение подающего трубопровода. Вследствие низкой скорости подачи по трубопроводу с относительно большим диаметром предупреждается чрезмерное пылеобразование из-за истирания. При этом масса подающего газа составляет предпочтительно от 3 до 15%, в частности менее 10% от транспортируемой массы продукта. Подающий трубопровод может заканчиваться либо непосредственно в реакторе, либо в расположенном над ним отделителе. Вход в реактор может обеспечиваться сверху через крышку или через верхнюю часть корпуса реактора. Если применяются два или более подающих трубопровода, то вход в реактор обеспечивается через общий трубопровод или через раздельные трубопроводы, при этом раздельные входы,которые либо имеют разную ориентацию, либо удалены друг от друга, являются предпочтительными, так как в этом случае частицы распределяются в реакторе, что улучшает использование его объма. В реакторе или отделителе подающий газ отделяют от частиц форполимера сложного эфира и либо отводят назад для использования с целью подачи, либо смешивают с другим инертным газом. Обычно перед последующим применением подающий газ очищают, по меньшей мере, от поликонденсатной пыли. Наряду с подачей на стадии между нагревом и реакцией могут дополнительно проводиться другие виды подачи. В частности, могут проводиться подачи на стадии между изготовлением частиц и кристаллизацией, между отдельными стадиями кристаллизации, между кристаллизацией и нагревом, между реакцией и охлаждением, после охлаждения, а также между технологической операцией и возможным хранилищем. Согласно изобретению особо предпочтительно, чтобы была предусмотрена подача на стадии между кристаллизацией и подогревом (нагревом). При использовании обычной установки для твердофазной поликонденсации кристаллизатор располагается над подогревателем. В крупной установке, являющейся,например, предметом настоящего изобретения, такой очень важный технологический процесс проводился бы в верхней части установки (т.е. очень высоко в здании, в котором расположена установка). Это очень дорого. Поэтому согласно изобретению предпочтительно, чтобы кристаллизатор находился рядом с подогревателем (т.е. в нижней части здания). Это делает необходимой подачу частично кристаллизованных частиц форполимера сложного эфира от выпускного отверстия в нижнем конце кристаллизатора к впускному отверстию на верхнем конце подогревателя. Относительно подробностей такой подачи (высота подачи, подающие трубопроводы и пр.) можно отослать к приведнным выше пояснениям, касающимся подачи в реактор. При подаче на участке между кристаллизатором и подогревателем предпочтительно осуществляются одинаковые меры. Однако при этом неожиданно было установлено, что при расположении кристаллизатора и подог- 10024875 ревателя рядом друг с другом в нижней части установки и при обусловленной этим подаче в подогревателе, в противоположность обычным установкам твердофазной поликонденсации, происходит нежелательная запылнность. Эта запылнность вызывает образование трудно расплавляемых частиц в подогревателе и обусловленную этим очень дорогостоящую очистку подогревателя по истечении некоторого времени работы установки. Неожиданно было найдено, что данная проблема может решаться просто и дшево в том случае, когда в конце участка пути подачи между кристаллизатором и подогревателем расположено предпочтительно выше впускного отверстия подогревателя обеспыливающее устройство. Под пылью подразумеваются частицы, размер которых заметно меньше среднего диаметра гранул. Если средний диаметр гранул составляет более 1 мм, то частицы, прошедшие через сито с размером ячеи 500 мкм, считаются пылью. Пыль может отделяться посредством механической энергии, например, в виброситах, ударных отделителях или зигзагообразных отделителях или посредством газового потока, например, в аппаратах с псевдоожиженным слоем или воздушных сепараторах. Для отделения пылевых частиц, налипающих под действием электростатических сил на гранулы, могут применяться деионизирующие газовые потоки. Предпочтительными обеспыливающими устройствами являются аппараты с кипящим или псевдоожиженным слоем с поверхностью сита, через которое пропускается газ, от 0,5 до 10 м 2, в частности более 1 и меньше 8 м 2, при этом соотношение между количеством газа и количеством продукта составляет от 1:15 до 1:1. Средняя продолжительность пребывания гранулята в обеспыливающем устройстве составляет от нескольких секунд до 5 мин, причм в исключительных случаях возможно также и более длительное время пребывания. Обеспыливание происходит при температуре, соответствующей, по существу,температурному диапазону кристаллизации. Поэтому согласно изобретению заявленный способ включает в себя предпочтительно стадию обработки (частично кристаллизованного) сложного полиэфира в аппарате с псевдоожиженным слоем при температуре от 100 до 250 С, в частности от 130 до 200 С, при удельной пропускной способности от 10 до 100 т/ч на 1 м 2 поверхности сита, в частности более 15 т/ч на 1 м 2 поверхности сита. Благодаря этой операции неожиданно было обеспечено эффективное обеспыливание частично кристаллизованных частиц форполимера и, следовательно, значительно более эффективная эксплуатация всей установки. Аппараты с псевдоожиженным слоем из уровня техники известны и описаны, например, в уже упоминавшемся источнике ЕР-1425146 А 2. Аппараты содержат по меньшей мере одно отверстие для подачи обеспыливаемых частиц и по меньшей мере одно отверстие для выхода обеспыленных частиц. Кроме того они содержат по меньшей мере одно входное отверстие для используемого при обеспыливании технологического газа и по меньшей мере одно выходное отверстие для содержащего пыль технологического газа. Ситовое полотно, через которое может пропускаться технологический газ, но не могут проходить частицы, расположено между но меньшей мере одним входным отверстием для частиц и, по меньшей мере, входным отверстием для газа таким образом, что технологический газ проходит через частицы и псевдоожижает их, в частности приводит в завихрение. Пригодные для обеспыливания скорости движения газа составляют от 2 до 5 м/с (скорость в пустой трубе), при этом при наличии пульсирующих газовых потоков решающее значение имеет максимальная скорость движения газа. После реакции может проводиться охлаждение частиц форполимера сложного эфира. При этом частицы форполимера сложного эфира могут быть охлаждены до температуры, пригодной для хранения или подачи, или до температуры непосредственной дальнейшей обработки. При этом охлаждение проводится известными из уровня техники способами, например, в пластинчатых теплообменниках, холодильниках с псевдоожиженным слоем, в подающих установках с наличием избыточного количества хладагента, непосредственным помещением в охлаждающую жидкость, путм контакта с холодной поверхностью или с применением комбинации разных методов охлаждения. Частично охлаждение может проводиться уже внутри реактора при впуске холодного газового потока. Предпочтительными охлаждающими устройствами являются холодильник с псевдоожиженным слоем и охлаждающие реакторы, через которые в противотоке пропускается газовый поток. Частицы полимера сложного эфира могут перерабатываться с получением разных продуктов, например волокон, лент, плнок, деталей, получаемых литьм под давлением. Полиэтилентерефталат обрабатывают для изготовления, в частности, полых изделий, например бутылок. Настоящее изобретение относится к способу получения частиц сложного полиэфира при высокой пропускной способности линии. Поскольку возможно проведение отдельных технологических операций или частичных технологических операций как в одном устройстве, так и нескольких одновременно работающих устройствах, то производительность линии определяется максимальной производительностью устройства. Согласно предпочтительному варианту выполнения настоящего изобретения, по меньшей мере,кристаллизация, нагрев или реакция проводятся в отдельном устройстве с массовым потоком от 40 до 100 т/ч. Другие предпочтительные варианты выполнения охарактеризованы в зависимых пунктах формулы изобретения. Осуществление изобретения Вариант выполнения способа согласно изобретению представлен на чертеже. В реакторе а) для полимеризации расплава получают расплав 1 форполимера поликонденсата, состоящий из полиэтилентерефталата с показателем IV 0,60 дл/г и сомономера в количестве ок. 6% (мол.% от соответствующего мономера в качестве компонента) при производительности 62,6 т/ч. Температура расплава составляет около 285 С. Расплав распределяют между множеством трубопроводов и подают во множество грануляторов, причм показаны только грануляторы а)-1 - а)-3. Другие грануляторы связаны с точкой (А). Грануляторами служат стандартные подводные грануляторы непрерывного действия, как, например, продаваемые фирмой Automatik Plastics Mashinery и обозначаемые как USG. Грануляторы состоят из головки экструдера с фильерой для получения множества жгутов, омываемого водой примного участка для жгутов, расположенного на расстоянии от 1 до 300 мм от головки, наклонного орошаемого водой жлоба, на котором жгуты охлаждаются и отверждаются, режущего устройства с втягивающими валками и режущими валками, в котором жгуты режутся на отдельные гранулы, устройства водоподготовки, в котором охлаждающая вода выдерживается при температуре 30-50 С и фильтруется, сушильного устройства, в котором от гранул отделяют техническую воду, и сита для классификации, которым удаляются сверхкрупные и/или мелкие частицы. Полученные гранулы обладают цилиндрической формой, имеют длину около 3 мм и диаметр около 2,4 мм, а также вес около 18 мг. Температура гранул составляет около 50 С. При необходимости для каждого гранулятора или нескольких грануляторов может быть предусмотрена буферная мкость (Р). Посредством одного или нескольких пневматических подающих устройств гранулы подаются в одно или несколько хранилищ 2, при этом поток продукта поступает из точки (А) в точку(В) или (С). В свою очередь из хранилища 2 частицы форполимера перемещаются одним или несколькими подающими пневматическими устройствами в необязательную буферную мкость (Р) и затем в кристаллизатор b). В зависимости от наружной температуры и от выполняемой при необходимости предварительной обработки температура на входе в кристаллизатор может составлять от -20 до 90 С. Загрузка частиц в кристаллизатор производится дозировано через лопастный питатель. Обработка в кристаллизаторе происходит в атмосфере воздуха. Внутри кристаллизатора частицы нагреваются в нескольких камерах горячим псевдоожижающим газом за 5-20 мин до температуры около 165 С и кристаллизуются при степени кристаллизации около 35%. Посредством одного или нескольких необязательных подающих устройств кристаллизованные частицы поступают в подогреватель с) с атмосферой азота. Также при необходимости перед подогревателем может быть установлено по меньшей мере одно обеспыливающее устройство. Если в обеспыливающем устройстве используется горячий псевдоожижающий газ, то одновременно температура повышается на 1-20 С. Между кристаллизатором и подогревателем расположен по меньшей мере один лопастный питатель для исключения чрезмерного переноса азота. В подогревателе частицы нагреваются потоком горячего технологического газа приблизительно за 30-120 мин до температуры около 216 С, причм перед выпуском температура снижается на 1-10 С. Степень кристаллизации частиц повышается при этом до около 44%. Показатель IV возрастает до около 0,63 дл/г. При выходе из подогревателя горячие частицы разделяются на два потока продукта по около 31,3 т/ч каждый. Одновременно проводятся две подачи в горячем состоянии с помощью пневматического средства в атмосфере азота, причм применяются при каждой подаче 2,2 т/ч подающего газа с температурой 200 С. При этом подача происходит от максимально низкой точки до максимально высокой точки с преодолением высотной разницы около 55 м. На протяжении участка пути подачи внутренний диаметр трубопровода увеличивается с 180 до 280 мм, причм окончательный внутренний диаметр трубопровода в конце пути подачи составляет 280 мм. В результате скорость подачи сохраняется постоянной и составляет от 7 до 11 м/с, при этом скорость подачи в конце пути составляет 11 м/с. Средняя температура при подаче составляет 212 С. Подача производится непосредственно в реактор d), при этом вследствие расстояния между подающими трубопроводами на входе в реактор образуются два насыпных конуса, что способствует более эффективному использованию объма реактора. Таким образом, в реактор поступают 62,6 т/ч частиц форполимера. Объм реактора составляет 687 м 3, высота его цилиндрической части 35 м. Время выдержки в реакторе составляет около 9 ч. Снизу в реактор поступает чистый азот с температурой около 170 С. Соотношение количество газа/количество продукта составляет 1:3,2. Падение давления над реактором достигает около 700 мбар, скорость оседания частиц в реакторе составляет 3,9 м/ч. В результате обработки в реакторе характеристическая вязкость возрастает до 0,86 дл/г. Частицы полимера в точке (D) могут непосредственно применяться в сухом и горячем состоянии для последующей обработки, например, для придания предварительной формы бутылок из полиэтилентерефталата. Под реактором располагается холодильник 3, в котором частицы полимера охлаждаются воздухом в противотоке. После охлаждения полимерные частицы подаются от точки (Е) в хранилище или в транспортную мкость. Азот из реактора используется сначала в качестве обменного газа в подогревателе, затем очищается скруббером, работающем на этиленгликоле, от летучих компонентов, таких как этиленгликоль, вода,ацетальдегид, в несколько примов и затем охлаждается до температуры ниже 10 С. Остаточное содержание воды составляет около 15 ч./млн, содержание этиленгликоля около 25 ч./млн и содержание ацетальдегида около 75 ч./млн. Кислород, проникающий в установку вместе с полимером или через лопаст- 12024875 ные питатели, удаляется из частичного потока азота каталитическим сжиганием при 200-350 С. В качестве топлива используется при этом содержащийся в газовом потоке ацетальдегид, содержание которого при этом дополнительно снижается. Очищенный азот снова податся в реактор в качестве свежего газа, в качестве охлаждающего газа в конце подогревателя и в качестве газа для подачи от подогревателя к реактору. Горячий отработанный воздух холодильника очищают с помощью циклона от возможных остатков пыли и затем направляют в качестве обменного газа в контур газа для кристаллизации, благодаря чему снижается расход энергии для нагрева обменного газа. ФОРМУЛА ИЗОБРЕТЕНИЯ 1. Способ получения термопластичного сложного полиэфира, включающий стадии, на которых:a) получают частицы форполимера сложного эфира с характеристической вязкостью от 0,35 до 0,75 дл/г,b) подвергают частицы форполимера сложного эфира кристаллизации для получения частично кристаллизованных частиц форполимера сложного эфира,c) подогревают частично кристаллизованные частицы форполимера сложного эфира до приемлемой температуры реакции для получения нагретых частиц форполимера сложного эфира,d) осуществляют реакцию поликонденсации нагретых частиц форполимера сложного эфира при температуре, достаточной для получения частиц полимера сложного эфира с характеристической вязкостью от 0,70 до 0,95 дл/г,при этом реакцию на стадии d) проводят по меньшей мере в одном реакторе, в котором частицы перемещаются под действием силы тяжести, и время выдержки в реакторе составляет от 6 до 30 ч,отличающийся тем, что частицы, по меньшей мере, на стадию d) подают при массовом расходе от 40 до 100 т/ч, скорость потока частиц в реакторе поддерживают от 2 до 6 м/ч, и стадию d) осуществляют в реакторе объемом от 400 до 3000 м 3 с отношением L/D реактора от 5 до 11, где D - диаметр и L - длина. 2. Способ по п.1, отличающийся тем, что реакцию на стадии d) осуществляют в потоке инертного газа, причм продукты повышающих молекулярный вес реакций переносятся в газ, а разность между давлением у отверстия для впуска газа в реактор и давлением у отверстия для выпуска газа из реактора составляет от 450 до 1000 мбар. 3. Способ по п.1 или 2, отличающийся тем, что частицы форполимера сложного эфира между стадией b) кристаллизации и стадией с) подогрева подают с уровня (НА) расположения выходного отверстия на лежащий выше уровень (НЕ) расположения входного отверстия. 4. Способ по любому из пп.1-3, отличающийся тем, что частицы форполимера сложного эфира перед стадией с) пропускают через обеспыливающее устройство. 5. Способ по любому из пп.1-4, отличающийся тем, что частицы форполимера сложного эфира, полученные на стадии а), имеют содержание карбоксильных концевых групп (ХСООН), составляющее от 0,25 до 0,6, и что во время обработки на стадиях b), с) и d) доля реакции этерификации (Е) от реакций поликонденсации (Е+Т) составляет от 0,5 до 1. 6. Способ по любому из пп.1-5, отличающийся тем, что нагретые частицы форполимера сложного эфира, полученные на стадии с), подают с начального уровня (НО) на уровень (HR) расположения входного отверстия в реактор и тем, что уровень (HR) расположения входного отверстия лежит выше уровня(НО) расположения выходного отверстия на 40-80 м. 7. Способ по любому из пп.1-6, отличающийся тем, что подачу нагретых частиц форполимера сложного эфира, полученных на стадии с), осуществляют при температуре подачи (TF), которая ниже точки плавления кристаллов сложного полиэфира предпочтительно на 5-80 С. 8. Способ по любому из пп.1-7, отличающийся тем, что подачу нагретых частиц форполимера сложного эфира, полученных на стадии с), осуществляют с помощью пневматической подачи. 9. Способ по любому из пп.1-8, отличающийся тем, что подачу нагретых частиц форполимера сложного эфира, полученных на стадии с), осуществляют по подающему трубопроводу с внутренним диаметром (DF) от 250 до 500 мм. 10. Способ по любому из пп.1-9, отличающийся тем, что подачу осуществляют при скорости (vF) от 5 до 12 м/с. 11. Способ по любому из пп.1-10, отличающийся тем, что подачу нагретых частиц форполимера сложного эфира, полученных на стадии с), осуществляют по меньшей мере по двум подающим трубопроводам. 12. Способ по любому из пп.1-11, отличающийся тем, что по меньшей мере в одно отдельное устройство на стадиях b), с) или d) частицы подают при массовом расходе от 40 до 100 т/ч. 13. Устройство для осуществления способа получения термопластичного сложного полиэфира по любому из пп.1-12, содержащее:a) реактор поликонденсации расплава для получения частиц форполимера сложного эфира с характеристической вязкостью от 0,35 до 0,75 дл/г,- 13024875b) по меньшей мере один кристаллизатор для кристаллизации частиц форполимера сложного эфира для получения частично кристаллизованных частиц форполимера сложного эфира,c) по меньшей мере один подогреватель для нагрева частично кристаллизованных частиц форполимера сложного эфира до приемлемой температуры реакции для получения нагретых частиц форполимера сложного эфира,d) по меньшей мере один реактор, выполненный с возможностью эксплуатации при температуре,достаточной для получения частиц форполимера сложного эфира с характеристической вязкостью от 0,70 до 0,95 дл/г,отличающееся тем, что уровень (HR) расположения входного отверстия в реактор d) находится на 40-80 м выше уровня (НО) расположения выходного отверстия из подогревателя с), реактор d) имеет объем от 400 до 3000 м 3, отношение L/D от 5 до 11, где D - диаметр и L - длина, и содержит средство регулирования скорости потока частиц в реакторе d) от 2 до 6 м/ч, для обеспечения возможности эксплуатации при массовом расходе от 40 до 100 т частиц в час и времени выдержки частиц в реакторе d) от 6 до 30 ч. 14. Устройство по п.13, отличающееся тем, что подогреватель с) и реактор d) соединены между собой посредством по меньшей мере двух подающих трубопроводов. 15. Устройство по любому из пп.13, 14, отличающееся тем, что подающие трубопроводы заведены в реактор d) раздельно, при этом входы ориентированы различно или же значительно отдалены друг от друга. 16. Устройство по любому из пп.13-15, отличающееся тем, что подающие трубопроводы имеют внутренний диаметр (DF) от 250 до 500 мм. 17. Устройство по любому из пп.13-16, отличающееся тем, что кристаллизатор b) и подогреватель с) расположены рядом и соединены между собой подающим трубопроводом.
МПК / Метки
МПК: C08G 63/78, C08G 63/80, B07B 4/08
Метки: сложного, высокой, полиэфира, частиц, получения, линии, способ, производительности
Код ссылки
<a href="https://eas.patents.su/15-24875-sposob-polucheniya-chastic-slozhnogo-poliefira-pri-vysokojj-proizvoditelnosti-linii.html" rel="bookmark" title="База патентов Евразийского Союза">Способ получения частиц сложного полиэфира при высокой производительности линии</a>