Способ транспортировки рельсов и машина для его осуществления
Формула / Реферат
1. Машина для транспортировки рельса (9), имеющего головку и подошву, содержащая:
множество перемещающих средств (20) для захвата и переворота рельса (9) из наклонного положения на одной боковой стороне в положение, в котором головка рельса повернута вверх;
множество кантователей (10), снабженных зажимными средствами, предназначенных для зажима рельса (9) у подошвы и перемещения его из вышеуказанного положения с головкой рельса, повернутой вверх, в положение с головкой рельса, повернутой вниз, характеризующаяся тем, что
вышеуказанные перемещающие средства (20) включают в себя первые рычаги (26), выполненные с возможностью поворота с помощью первых трансмиссионных средств (11), обеспечивающие перемещение рельса (9) из наклонного положения боковой стороной на первой плоскости в положение с головкой рельса, повернутой вверх, на второй плоскости, находящейся выше упомянутой первой плоскости.
2. Машина по п.1, в которой первые рычаги (26) закреплены одним концом на соответствующем первом конце трансмиссионного вала (11') и имеют на втором конце две выступающие части (26', 26"), образующие пространство для размещения участка рельса во время перемещения первых рычагов (26).
3. Машина по п.1 или 2, в которой перемещающие средства (20) содержат вторые рычаги (25), установленные с возможностью поворота с помощью вторых исполнительных средств (28) и предназначенные для транспортировки рельса (9) по вышеуказанной первой плоскости из первого наклонного положения на одной боковой стороне во второе наклонное положение на той же стороне.
4. Машина по п.3, в которой вторые рычаги (25) установлены с возможностью поворота вокруг соответствующей оси (27) на заданный угол.
5. Машина по любому из предыдущих пунктов, в которой вышеуказанные зажимные средства имеют два захвата (14), установленные с возможностью поворота вокруг соответствующих пальцев (19), так что рельс зажимается посредством контакта только между участками внутренней поверхности захватов (14) и боковыми сторонами подошвы рельса (9).
6. Машина по п.5, в которой все кантователи (10) содержат плечо (12), которое первым концом закреплено к трансмиссионному валу (11), а на втором конце установлены захваты (14) вышеуказанных зажимных средств.
7. Машина по п.6, которая снабжена исполнительными средствами (13) для поворота захватов (14) на каждом плече (12).
8. Машина по п.7, в которой средства поворота захватов (14) содержат шестерни или рычаги, взаимодействующие с вышеуказанными исполнительными средствами (13).
9. Установка для термообработки головки рельсов, выходящих из прокатного стана, имеющего ось (X) прокатки, содержащая
продольный роликовый стол (3), расположенный вдоль оси (X) прокатки;
первый продольный резервуар (5) охлаждения, расположенный рядом и параллельно первому участку роликового стола (3);
и транспортирующую машину по п.1,
причем поперек роликового стола (3), образующего вышеуказанную первую плоскость, расположены первые рычаги (26) для захвата рельсов с вышеуказанного роликового стола (3) и их переворота из наклонного положения на одной боковой стороне на вышеуказанном роликовом столе (3) в положение, в котором головка рельса обращена вверх, на вышеуказанной второй плоскости выше первой плоскости, рядом с множеством кантователей (10);
кантователи (10) снабжены зажимными средствами, предназначенными для зажима первого рельса у подошвы, и выполнены с возможностью перемещения вышеуказанного первого рельса из вышеуказанного положения с головкой, повернутой вверх, в положение над первым резервуаром (5) охлаждения с головкой, повернутой вниз.
10. Установка по п.9, характеризующаяся тем, что снабжена
вторым продольным резервуаром (6) охлаждения для термообработки головки второго рельса, расположенным рядом и параллельно второму участку роликового стола (3), при этом вышеуказанный второй участок расположен после первого участка,
и третьим продольным резервуаром (7) охлаждения для термообработки головки третьего рельса, расположенным рядом и параллельно третьему участку роликового стола (3), при этом вышеуказанный третий участок расположен после второго участка.
11. Установка по п.10, характеризующаяся тем, что первые кантователи (10) расположены между вышеуказанным первым резервуаром (5) охлаждения и вышеуказанным первым участком роликового стола (3), вторые кантователи (10) расположены между вышеуказанным вторым резервуаром (6) охлаждения и вышеуказанным вторым участком роликового стола (3) для транспортировки второго рельса и выполнения его термической обработки во втором резервуаре (6), третьи кантователи (10) расположены между вышеуказанным третьим резервуаром (7) охлаждения и вышеуказанным третьим участком роликового стола (3) для транспортировки третьего рельса и выполнения его термической обработки в третьем резервуаре (7).
12. Установка по п.11, в которой первый, второй и третий резервуары (5, 6, 7) охлаждения и соответствующие кантователи (10) в исходном положении, по существу, расположены на вышеуказанной второй плоскости.
13. Способ транспортировки рельса с помощью установки для термообработки головки рельсов по п.9, содержащий следующие этапы, на которых
перемещают рельс (9) с помощью первых рычагов (26) из наклонного положения на одной боковой стороне, на первой плоскости, в положение с головкой рельса, повернутой вверх, на второй плоскости, находящейся выше указанной первой плоскости;
зажимают рельс (9) с помощью зажимных средств множества кантователей (10) за счет контакта участков внутренней поверхности захватов (14) только с боковыми сторонами подошвы рельса (9);
поворачивают кантователи (10) для перемещения рельса (9) из вышеуказанного положения с головкой, повернутой вверх, в положение с головкой, повернутой вниз, и погружают рельс (9) в резервуар (5) охлаждения,
выгружают рельс (9) из резервуара (5) охлаждения.
14. Способ по п.13, в котором перед этапом зажимания рельса (9) выполняют правку рельса посредством совместного использования кантователей (10) и первых рычагов (26).
15. Способ по п.14, в котором правку выполняют за счет поворота кантователей (10), начиная с исходного положения, рельс (9) поднимают до достижения положения взаимодействия с первыми рычагами (26), в котором головка рельса соответствующим образом отделяется от выступающих частей (26') первых рычагов за исключением точек большего изгибания рельса, в которых существует контакт между головкой рельса и выступающими частями (26').
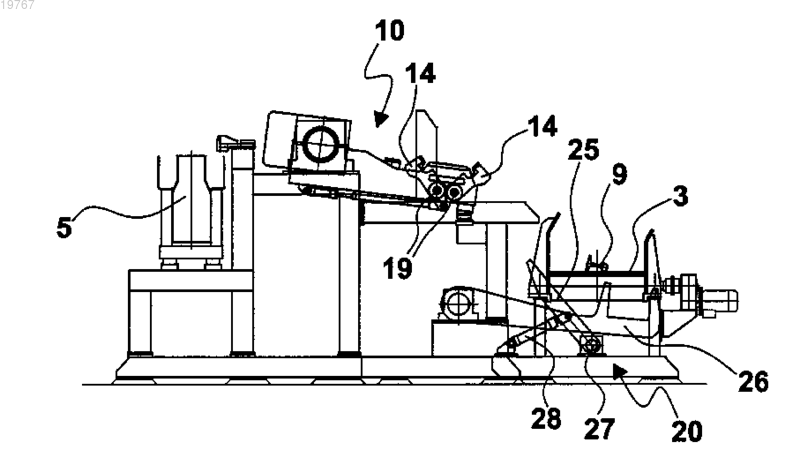
Текст
СПОСОБ ТРАНСПОРТИРОВКИ РЕЛЬСОВ И МАШИНА ДЛЯ ЕГО ОСУЩЕСТВЛЕНИЯ Машина для транспортировки рельсов, установленная в производственной линии непосредственно после прокатной установки, что обеспечивает как легкое манипулирование рельсом для его транспортировки с роликового стола в зону термообработки, так и оптимальное зажимание рельса по продольной длине, эффективно препятствуя изгибанию и отклонению, в то же время, обеспечивая продольное перемещение рельса, вызываемое термической усадкой; тем самым, предотвращается повреждение, как наружной поверхности рельса, так и кантователей. Также описывается способ транспортировки рельсов, оптимизирующий транспортировку,позиционирование вдоль роликового стола и поддержание рельса, по существу, в прямолинейном состоянии во время термообработки, которой он подвергается. Область техники, к которой относится изобретение Изобретение относится к транспортирующей машине для транспортировки рельсов, в частности по меньшей мере одного рельса в установке термообработки головок рельсов, при этом вышеуказанная установка термообработки расположена непосредственно после прокатной установки; настоящее изобретение также относится к соответствующему способу транспортировки рельсов. Уровень техники По существующему уровню техники предлагаются различные установки для термообработки катаных рельсов, в частности для закалки головки. Многие из этих систем не расположены непосредственно у выхода из прокатной клети. Это вызывает необходимость создания запаса катаных рельсов и их последующего нагрева перед закаливанием,что влечет за собой большой расход энергии и низкую эффективность. В других решениях эти системы расположены после прокатного стана: катаный рельс выгружается на роликовый стол; затем рельс захватывается кантователями, содержащими сложные рычаги, которые управляют перемещением рельса во время термообработки; и, наконец, рельс устанавливается на плиту или стеллаж охлаждения с помощью соответствующих установочных механизмов. Первым недостатком этих решений является сложность систем транспортировки рельсов, перемещающих рельс на роликовом столе вдоль установки для термообработки. Рельсы либо нагретые, либо поступающие непосредственно с прокатного стана, подвергаются быстрому охлаждению головки за счет использования распыляющих сопел, которые подают охлаждающую среду (воду, воздух или воду, смешанную с воздухом) на головку рельса или за счет погружения головки в резервуар, содержащий охлаждающую среду. В частности, если используется погружной резервуар, охлаждение по длине будет более равномерным, но во всех случаях различие температур основания горячего рельса и охлаждаемой головки приводит к деформированию или изгибанию рельсов. Фактически, рельс уже изогнут на выходе из прокатной установки. В частности, из-за различия температур подошвы (или пяты) и головки рельс изгибается, образуя вогнутость на более холодной стороне. Перед термообработкой подошва является более холодной, чем головка; следовательно, подошва имеет вогнутый продольный профиль. Во время термообработки головка охлаждается быстрее подошвы, и в конце термообработки головка будет более холодной, чем подошва, и будет иметь вогнутый продольный профиль. Через несколько минут подошва станет более холодной, чем головка рельса; следовательно, боковая сторона подошвы снова будет иметь вогнутый профиль. Таким образом вторым недостатком известных решений является то, что эти изменения продольного профиля рельса, более заметные на концах, являются причиной воздействия вертикальных усилий на зажимы кантователей рельсов; эти усилия могут вынуждать сами зажимы открываться с последующим падением рельса. Зажимы по существующему уровню техники имеют недостаток, состоящий в том, они не пригодны для выдерживания вышеуказанного отклонения и его изменений во время термообработки. Для устранения этого недостатка были спроектированы кантователи с гидроцилиндрами для зажимов рельсов с целью создания высоких усилий зажима рельса. С одной стороны, эти усилия обеспечивают надлежащий зажим рельса, когда он перемещается ближе к резервуару охлаждения, но, с другой стороны, они препятствуют продольному перемещению рельса, вызываемого термической усадкой, которой подвергается сам рельс, когда он охлаждается. Известно, что катаный рельс, например, длиной 100 м,становится примерно на 100-150 см короче, когда он охлаждается. Это укорочение может привести к повреждению как поверхности рельса, так и самих кантователей из-за высоких усилий зажимания. Следовательно, существует необходимость предложить транспортирующую машину для транспортировки рельсов и соответствующий способ транспортировки, способные устранить вышеуказанные недостатки. Сущность изобретения Главная задача настоящего изобретения состоит в том, чтобы предложить машину для транспортировки рельсов, установленную в производственной линии непосредственно после прокатной установки,что обеспечивает как легкое манипулирование рельсом для его транспортировки с роликового стола в зону термообработки, так и оптимальное зажимание рельса по продольной длине, эффективно препятствуя изгибанию и отклонению, в то же время обеспечивая продольное перемещение рельса, вызываемое термической усадкой; тем самым, предотвращается повреждение как наружной поверхности рельса, так и кантователей. Другая задача настоящего изобретения состоит в том, чтобы предложить установку термообработки рельсов, содержащую вышеуказанную транспортирующую машину. Следующая задача изобретения состоит в том, чтобы предложить способ транспортировки рельса,оптимизирующий транспортировку, позиционирование вдоль роликового стола и поддержание рельса,по существу, в прямолинейном состоянии во время термообработки, которой он подвергается. Настоящее изобретение также предлагает решение вышеуказанных задач за счет использования машины для транспортировки рельса, имеющего головку и подошву, в которой содержится: множество перемещающих средств для захвата рельса и его переворота из наклонного положения на боковой стороне в положение с головкой рельса, повернутой вверх; множество кантователей, снабженных зажимными средствами, адаптированными для зажимания рельса у подошвы и адаптированными для перемещения рельса из вышеуказанного положения с головкой рельса, повернутой вверх, в положение с головкой рельса, повернутой вниз; при этом вышеуказанные перемещающие средства содержат первые рычаги, поворачиваемые с помощью первых исполнительных средств так, что они перемещают рельс из наклонного положения на боковой стороне на первой плоскости в положение с головкой рельса, повернутой вверх на второй плоскости, находящейся выше упомянутой первой плоскости. Второй аспект настоящего изобретения включает в себя установку термообработки рельсов для термообработки головки вышеуказанных рельсов в составе линии; рельсы выходят из прокатной установки, образующей ось прокатки, при этом установка термообработки содержит: продольный роликовый стол, размещенный вдоль оси прокатки; первый продольный резервуар охлаждения, расположенный рядом и параллельно вышеуказанному роликовому столу; и транспортирующую машину, в которой первые рычаги расположены вдоль роликового стола, образующего первую плоскость, для захватывания рельсов с вышеуказанного роликового стола и их переворота из наклонного положения на одной боковой стороне на вышеуказанном роликовом столе в положение, в котором головка рельса обращена вверх, на вышеуказанной второй плоскости рядом с множеством кантователей; первые кантователи из вышеуказанного множества кантователей, которые снабжены зажимными средствами и предназначены для зажимания первого рельса у подошвы, перемещают вышеуказанный первый рельс из вышеуказанного положения с головкой, повернутой вверх, в положение над первым резервуаром охлаждения с головкой, повернутой вниз. Следующий аспект настоящего изобретения включает в себя способ транспортировки рельса с помощью вышеуказанной транспортирующей машины, содержащий следующие этапы: перемещение рельса с помощью первых рычагов из наклонного положения на одной боковой стороне на первой плоскости в положение с головкой рельса, повернутой вверх, на второй плоскости, находящейся выше указанной первой плоскости; зажим рельса с помощью зажимных средств множества кантователей за счет контакта участков внутренней поверхности захватов только с боковыми сторонами подошвы рельса; поворот кантователей для перемещения рельса из вышеуказанного положения с головкой, повернутой вверх, в положение с головкой, повернутой вниз. Транспортирующая машина и способ транспортировки рельсов по настоящему изобретению также имеют следующие преимущества: улучшенное зажимание изогнутого рельса при одновременном прикладывании относительно низких зажимных усилий во время термического закаливания в резервуаре благодаря тому, что точка приложения усилий, создаваемых при зажимании зажимов на изогнутой подошве рельса, по существу, выровнена с осями поворота самих зажимов; возможность управления гидравлическими цилиндрами зажимов кантователей с целью перехода от высокого усилия зажимания при перемещении рельса из положения с головкой, повернутой вверх,в положение погружения рельса в резервуар охлаждения с целью сопротивления силе веса и центробежному усилию, возникающему во время поворота кантователей; к достаточно низкому усилию зажимания во время погружения для обеспечения укорочения рельса из-за термической усадки. Транспортирующая машина и способ транспортировки используются в установке термической обработки, которая включает в себя три последовательно расположенных резервуара охлаждения и имеет следующие преимущества: обеспечивает высокую производительность с учетом количества термообработанных рельсов в единицу времени; позволяет оптимизировать занимаемые пространства и уменьшает начальные капиталовложения на фундаменты машины; позволяет усовершенствовать промышленную эксплуатацию линий и систем водопроводных труб,питающих резервуары охлаждения; является гибкой благодаря тому, что она позволяет выгружать катаные рельсы и выполнять их термообработку и изменять производственный цикл для производства крупносортного профиля; является модульной, т.е. позволяет добавлять другие резервуары охлаждения для дополнительного увеличения часовой производительности или термообработки рельсов других размеров. Зависимые пункты формулы изобретения описывают предпочтительные варианты выполнения изобретения. Краткое описание чертежей Дополнительные отличительные характеристики и преимущества изобретения станут более понятными из подробного описания предпочтительных, но неисключительных вариантов выполнения машины для транспортировки рельсов, представленной с помощью не ограничивающего примера со ссылкой на приложенные чертежи, на которых фиг. 1 - компоновка установки термической обработки головки рельса по изобретению; фиг. 2 а - вид сбоку на первую часть машины для транспортировки рельсов по изобретению с кантователем, установленным в положении погружения головки рельса в резервуар; фиг. 2b - вид сбоку на вторую часть машины для транспортировки рельсов по изобретению; фиг. 3 - 14 - этапы транспортировки рельсов с помощью машины по изобретению; фиг. 15 - первое выполнение исполнительного устройства зажимов в двух различных положениях; фиг. 16 - первый вариант второго выполнения исполнительного устройства зажимов в двух различных положениях; фиг. 17 - второй вариант второго выполнения исполнительного устройства зажимов в двух различных положениях; фиг. 18 - третий вариант второго выполнения исполнительного устройства зажимов в двух различных положениях; фиг. 19 - четвертый вариант второго выполнения исполнительного устройства зажимов в двух различных положениях; фиг. 20 - вид установки, на котором показан подвижный контейнер для удаления катаного материала с роликового стола в случае аварийной ситуации. Подробное описание предпочтительных вариантов выполнения изобретения На фиг. 2 а и 2b показан предпочтительный вариант выполнения машины для транспортировки рельсов по настоящему изобретению. Рельсы имеют головку, шейку и подошву или пяту. Подошва, в свою очередь, имеет плоское основание, боковые стороны и верхние стороны, имеющие поверхности,которые наклонены по отношению плоскости основания. Боковые стороны и наклонные поверхности соединены с помощью соединительной секции. По первому варианту такая машина содержит: продольный роликовый стол 3, расположенный вдоль оси X прокатки для приема рельса 9, выходящего из последней прокатной клети; продольный резервуар 5 охлаждения, расположенный параллельно рядом с вышеуказанным роликовым столом 3, для термообработки рельса 9 посредством погружения в охлаждающую среду, содержащуюся в резервуаре; множество перемещающих средств 20, расположенных вдоль роликового стола 3, для перемещения рельса 9 с роликового стола 3 и его поворота из положения, в котором он опирается на боковую сторону на роликовом столе с подошвой, обращенной к резервуару 5 охлаждения (фиг. 3), т.е. положения, в котором он поступает на роликовый стол, в положение с обращенной вверх от роликового стола головкой(фиг. 8); множество кантователей 10, снабженных зажимами, предназначенными для зажима рельса 9 у подошвы и его поворота из положения на роликовом столе с головкой, обращенной вверх (фиг. 8), в положение с головкой, обращенной вниз и погруженной в резервуар 5 охлаждения (фиг. 14). Вышеуказанное положение рельса с головкой, обращенной вверх, имеет место не на роликовом столе 3, а около исходного положения кантователей 10 (фиг. 3-8). Наличие промежуточных перемещающих средств, которые перемещают рельсы с роликового стола 3 к кантователям 10, установленным на участке термообработки, исключает непосредственное воздействие на кантователи повышенной тепловой нагрузки, действующей вблизи роликового стола. Это дополнительно упрощает операции технического обслуживания на участке термообработки, поскольку последний находится на большем расстоянии от роликового стола по сравнению с конструкциями по существующему уровню техники. Резервуар 5 охлаждения имеет длину, позволяющую полностью погружать в него рельс. Сразу же по завершении термообработки головки рельсы выгружаются с роликового стола на охлаждающую плиту или стеллаж 8. Перемещающие средства 20 расположены вдоль роликового стола 3 с шагом, например, равным 1,5 метрам, при этом каждое перемещающее средство содержит: рычаг или толкатель 25, который поворачивается гидроцилиндром 28 или другим соответствующим исполнительным средством вокруг оси 27 на заданный угол, например 30, перемещая рельс 9, наклоненный на боковую сторону, к боковой части роликового стола 3, удаленную от резервуара охлаждения(фиг. 3 и 4); рычаг 26, закрепленный первым концом на трансмиссионном валу 11', расположенном с боковой стороны относительно роликового стола 3, и имеющий на втором конце две выступающие части 26', 26",образующие по существу U-образное пространство для размещения части рельса во время поворота вышеуказанного рычага 26. Преимущественно конфигурация рычага 26 такова, что в исходном положении его второй конец расположен под боковой частью роликового стола 3, удаленной от резервуара охлаждения (фиг. 4). Кантователи 10 расположены вдоль роликового стола 3, например, с шагом 3 метра, при этом каждый из них содержит плечо 12, которое на одном конце крепится на передаточном валу 11, расположенном между резервуаром 5 и роликовым столом 3. Каждое плечо 12 снабжено с одного конца зажимом, захваты 14 которого установлены на пальцах 19. Для привода захватов 14 на каждом плече 12 также установлен гидроцилиндр 13 или другое соответствующее исполнительное средство. Совместно с вышеуказанным гидроцилиндром 13 могут быть использованы другие средства для привода захватов 14. На фиг. 15 показан первый вариант, в котором пара зацепляющихся шестерней 32 установлена на соответствующих пальцах 19 захватов 14, гидроцилиндр 13 предназначен для поворота одной из двух шестерней и раздвигания обоих захватов 14. Это решение имеет то преимущество, что исполнительная система имеет небольшие размеры и всегда перемещает захваты симметричным образом. На фиг. 16-19 показаны четыре других варианта, в которых вместо шестерней используются рычажные механизмы. Эти рычажные механизмы имеют преимущество, состоящее в том, что по сравнению с шестернями система передачи между захватами не предусматривает зубчатого зацепления, подвергающегося высоким тепловым нагрузкам из-за близкого расположения рельса и загрязнения металлическими частицами, попадающими в зацепление с самого рельса. В частности, первый вариант на фиг. 16 содержит систему из трех тяг 33, 34 и 35. Тяга 35 шарнирно соединена у ее первого конца с плечом 12 кантователя и у второго конца - с гидроцилиндром 13. Обе тяги 33 и 34 вместе с тягой 35 шарнирно присоединены у соответствующего первого конца к гидроцилиндру 13, у второго конца они шарнирно соединены с соответствующими точками захватов 14. На фиг. 16b показаны захваты 14 в открытом положении, в то время как на фиг. 16 а показаны захваты 14 в закрытом положении. Этот первый вариант является немного громоздким: он предусматривает закрывание захватов с более высоким усилием путем выдвижения штока гидроцилиндра и несимметричным перемещением захватов. Кроме того, захваты 14 в максимально открытом положении расположены не симметрично, тогда как в закрытом положении они расположены симметрично. Второй вариант выполнения на фиг. 17 содержит систему из двух тяг 36, 37 и балансир 38. Балансир 38 шарнирно соединен у первого конца с гидроцилиндром 13, и в центральной точке он шарнирно соединен с опорой, составляющей одно целое с плечом 12. Тяга 36 вместе с балансиром 38 шарнирно соединена у соответствующего первого конца с гидроцилиндром 13; тяга 37 шарнирно соединена у соответствующего первого конца со вторым концом балансира 38. Тяги 36 и 37 шарнирно соединены у соответствующих вторых концов с соответствующими точками захватов 14. На фиг. 17b показаны захваты 14 в открытом положении, в то время как на фиг. 17 а показаны захваты 14 в закрытом положении. Второй вариант является немного более громоздким, чем первый вариант: он предусматривает закрывание захватов путем выдвижения штока гидроцилиндра. В этом случае захваты 14 расположены симметрично в закрытом положении. Третий вариант на фиг. 18 содержит систему, снабженную рычагом 39 и двумя тягами 40 и 41. Рычаг 39, имеющий в этом примере треугольную форму, шарнирно соединен, соответственно, с гидроцилиндром 13 у первой вершины, с опорой, составляющей одно целое с плечом 12 кантователя у второй вершины и с первыми концами тяг 40, 41 у третьей вершины. Тяги 40 и 41 шарнирно соединены у соответствующих вторых концов с соответствующими точками захватов 14. На фиг. 18b показаны захваты 14 в открытом положении, в то время как на фиг. 18 а показаны захваты 14 в закрытом положении. Третий вариант является более громоздким, чем второй вариант: он предусматривает закрывание захватов путем выдвижения штока гидроцилиндра и несимметричное перемещение захватов. Захваты 14 находятся в симметричном положении при максимальном открывании и в положении зажима. Это решение обеспечивает очень сильный и надежный зажим. И, наконец, четвертый вариант на фиг. 19 содержит систему, снабженную рычагом 39' и двумя тягами 40 и 41. Рычаг 39' имеет в этом примере, по существу, L-образную форму с вогнутой поверхностью,обращенной к плечу 12, и шарнирно соединен у первого конца с гидроцилиндром 13, рычаг 39' шарнирно соединен в центральной части с опорой, составляющей одно целое с плечом 12, и шарнирно соединен у второго конца с первыми концами тяг 40, 41. Тяги 40 и 41 шарнирно соединены у соответствующих вторых концов с соответствующими точками захватов 14. На фиг. 19b показаны захваты 14 в открытом положении, в то время как на фиг. 19 а показаны захваты 14 в закрытом положении. Четвертый вариант является менее громоздким, чем третий и второй варианты: он предусматривает закрывание захватов путем втягивания штока гидроцилиндра, т.е. с меньшим усилием закрывания, предусматривает несимметричное перемещение захватов. Захваты 14 расположены симметрично в максимально открытом положении и закрытом положении. Это решение обеспечивает очень сильное надежное зажимание, несмотря на то что гидроцилиндр создает намного меньшее усилие. Зажимы выполнены таким образом, что захваты 14 имеют внутреннюю поверхность, обычно предусматриваемую на изнашиваемом элементе 30, часто именуемом "планка", которая имеет профиль, по существу, сопрягающийся с профилем рельса относительно половины шейки и предназначенный для опирания на боковые стороны пяты или подошвы рельса, при этом обеспечивается заданный зазор на верхней или наклонной поверхности пяты. Фактически, угол наклона верхней поверхности пяты относительно плоскости основания подошвы меньше угла наклона сопрягающейся внутренней поверхности захвата 14 в положении зажимания (фиг. 2 а). Когда рельс 9 зажат в захватах 14 в положении зажимания (фиг. 2 а), изгиб самого рельса в продольном направлении создает в некоторых точках контакт участка соединительной секции между боковыми сторонами и верхней стороной с соответствующим участком внутренней поверхности захватов; к этим контактным поверхностям прикладываются усилия, параллельные плоскости симметрии рельса и имеющие интенсивность приблизительно одного порядка со значением, превышающим усилие закрывания, создаваемое самими захватами. Результирующее значение вышеуказанных параллельных усилий преимущественно имеет направление, проходящее или через ось соответствующего поворотного пальца 19, или близко от нее. Таким образом, плечо результирующих значений усилий, параллельных плоскости симметрии рельса, создаваемое за счет изгиба рельса при зажимании изогнутого рельса с помощью захватов, относительно поворотных пальцев 19 равно нулю или является небольшим, например, максимум 30 мм, и предпочтительно равно 5 мм. Соответственно, момент, создаваемый вышеуказанными усилиями, параллельными плоскости симметрии рельса, относительно поворотных пальцев 19 закрытых зажимов равен нулю или является незначительным. Таким образом: исключается случайное открывание захватов в результате перемещений, создаваемых при зажимании рельса, который изгибается под действием неравномерных температурных полей между пятой и головкой; могут использоваться относительно низкие усилия закрывания захватов. Транспортирующая машина разделена на модули, каждый из которых содержит трансмиссионный вал 11; модули расположены в ряд один за другим для обеспечения требуемого продольного размера транспортирующей машины. Для каждого модуля предусмотрена система управления, предпочтительно синхронный двигатель. Трансмиссионные валы 11 различных модулей управляются соответствующими двигателями. В случае возникновения проблемы с передачей движения в каком-либо модуле установки валы 11 преимущественно имеют на одном конце соединительный элемент, адаптированный для зацепления с соответствующей выемкой, предусмотренной на ближнем конце следующего вала 11. Способ транспортировки рельсов, осуществляемый с помощью вышеуказанного первого варианта выполнения транспортирующей машины, содержит следующие этапы: 1) выгрузка рельса 9 на роликовый стол 3 в наклонном положении на одной боковой стороне; во время этого этапа приема рельса толкатели 25 и рычаги 26 находятся в соответствующих наружных исходных положениях и под роликовым столом 3 (фиг. 3); 2) поворот толкателей 25 с помощью гидроцилиндров 28 на заданный угол, например, приблизительно 30, в первом направлении поворота относительно соответствующих пальцев 27, перемещая рельс 9, наклоненный на боковую сторону, в сторону относительно продольной средней плоскости самого роликового стола 3, в частности на боковую сторону роликового стола, удаленную от резервуара 5 (фиг. 4); 3) возможное приведение в действие вторых рычагов 26 для их частичного подъема, при этом нижние части пространств, в которых размещается рельс 9, все еще будут находиться под плоскостью, образуемой роликовым столом 3 (фиг. 5); 4) поворот толкателей 25 с помощью гидроцилиндров 28 во втором направлении, противоположном первому направлению, вокруг соответствующих пальцев 27 для возврата в соответствующие исходные положения (фиг. 6); 5) поворот рычагов 26 с помощью трансмиссионного вала 11' в соответствующем первом направлении поворота на заданный угол, по существу, примерно на 90, тем самым, размещая рельс 9 в концевых пространствах, подъем рельса с роликового стола 3 и его переворот в положение с головкой, обращенной вверх; во время поворота рельс 9 скользит по нижней части пространств до контакта с выступающими частями 26" (фиг. 7) и в конце хода рычагов 26 он достигает положения с головкой, обращенной вверх, и основание подошвы опирается на выступающие части 26" (фиг. 8); 6) возможное центрирование рельса на выступающих частях 26" с помощью зажимов кантователей 10 во избежание затягивания рельса, в частности, на передних концах и задних концах во время этапа зажимания с помощью зажимов; 7) правка рельса 9 посредством совместного использования кантователей 10 и выступающих частей 26' рычагов 26; начиная с исходного положения (фиг. 8), кантователи 10 поворачиваются с открытыми захватами 14 для поднимания рельса 9 с помощью опорной поверхности 24 до достижения положения взаимодействия с рычагами 26 (фиг. 9), в котором головка рельса соответствующим образом отделяется от выступающих частей, например, на несколько сантиметров, за исключением точек большего изгибания рельса, в которых существует контакт между головкой рельса и выступающими частями 26' рычагов 26, удерживаемых в поднятом положении; 8) зажим рельса 9 в вышеуказанном положении по фиг. 9 с помощью полного закрывания захватов 14, которые упираются в боковые стороны подошвы, оставляя заданный зазор между захватами и верхней поверхностью подошвы (фиг. 10); 9) незначительный поворот кантователей 10 в нижнем направлении для отделения головки рельса от выступающих частей 26' во избежание затягивания поверхности головки рельса на следующем этапе 10); 10) поворот рычагов 26 с помощью трансмиссионного вала 11' в соответствующем втором направлении (фиг. 12), по меньшей мере, для выхода из зоны действия кантователей; 11) поворот кантователей 10 в первом направлении, примерно на 170, в положение головки рельса 9, обращенной вниз, на заданном расстоянии от резервуара 5 охлаждения (фиг. 13); рельс 9 удерживается в этом положении до тех пор, пока головка не достигнет заданной температуры поверхности, по меньшей мере 720C, за счет охлаждения на воздухе; 12) дальнейший поворот кантователей 10 в первом направлении в положение погружения головки рельса в резервуар (фиг. 14); это охлаждение с помощью охлаждающей жидкости, содержащейся в резервуаре, продолжается до тех пор, пока не будет достигнута температура поверхности головки рельса,превышающая на 50-150C температуру Ar3, чтобы предотвратить фазовое превращение аустенита в перлит; 13) поворот кантователей 10 во втором направлении, противоположном первому направлению, так чтобы головка рельса 9 была обращена вниз на вышеуказанном заданном расстоянии от резервуара 5 охлаждения (такое же положение, как на фиг. 13); рельс 9 удерживается в этом положении до тех пор,пока за счет охлаждения на воздухе температура поверхности головки не станет равной температуре поверхностного слоя головки рельса, при этом вышеуказанный слой имеет глубину 15-25 мм от поверхности головки; 14) поворот кантователей 10 в первом направлении в положение погружения головки рельса в резервуар 5 (фиг. 14); охлаждение с помощью охлаждающей среды продолжается до тех пор, пока не будет достигнута температура поверхности головки рельса ниже 500C, в результате чего происходит фазовое превращение аустенита в перлит; 15) поворот кантователей 10 во второе положение примерно на 170-180 для размещения головки рельса 9 так, чтобы она была обращена вверх и находилась, по существу, в положении, при котором выполняется зажим; 16) поворот рычагов 26 в соответствующем первом направлении, так чтобы выступающие части 26' достигли вышеуказанного положения взаимодействия с головкой рельса (фиг. 10); 17) открывание захватов 14 и дальнейший поворот кантователей 10 во втором направлении до тех пор, пока пята рельса не будет опираться на выступающие части 26" (фиг. 8); 18) поворот рычагов 26 с помощью трансмиссионного вала 11' в соответствующем втором направлении на заданный угол, по существу, примерно, на 90, возвращая рельс 9 на роликовый стол 3 в наклонное положение на одной боковой стороне с подошвой, обращенной к резервуару 5 охлаждения, сбоку от продольной средней плоскости самого роликового стола 3. На данном этапе термообработанный рельс готов к подаче на роликовый стол 3 и последующей выгрузке на охлаждающую плиту. Сразу же по завершении термической закалки рельса, содержащей четыре этапа охлаждения, соответственно, на воздухе, в жидкости, на воздухе и в жидкости, получают поверхностный слой головки рельса глубиной 15-25 мм, начиная от наружной поверхности головки, при этом поверхностный слой имеет однородную тонкозернистую перлитную структуру с размером зерна, предпочтительно составляющим 9-4 баллов по российскому стандарту ГОСТ Р 8233-56. На выходе из последней прокатной клети 2 рельс 9 выгружается на роликовый стол 3 в наклонном положении на боковой стороне с подошвой, обращенной к резервуару 5 охлаждения (случай, показанный на фигурах); как вариант, он может выгружаться на роликовый стол 3 в наклонном положении на боковой стороне с головкой, обращенной к резервуару 5 охлаждения (не показано). Возможное центрирование рельса 9 на выступающих частях 26" (этап 6) выполняется следующим образом: небольшой поворот кантователей 10 из исходного положения с открытыми захватами до тех пор,пока концы захватов, по существу, не достигнут высоты пяты; частичное закрытие захватов 14 зажимов до контакта с обеими боковыми сторонами подошвы и центрировка рельса 9, не зажимая его; открытие захватов 14. Измерение температуры поверхности головки рельса можно выполнять во время этапа 11) и этапа 13) с помощью пирометров. На фиг. 1 показана компоновка части установки для производства рельсов, содержащей второй предпочтительный вариант выполнения транспортировочной машины по настоящему изобретению. Эта примерная компоновка содержит установку для прокатки крупных слитков, пригодных для изготовления рельсов или крупносортного профиля, образующих ось X прокатки (на фиг. 1 показана только последняя прокатная клеть 2); установку 1 термообработки для термообработки головки, содержащую вышеуказанную транспортировочную машину; плиту или стеллаж 8 охлаждения, на которую выгружаются термообработанные рельсы 9. Машина для возможной правки может быть установлена после плиты 8 охлаждения; эта машина используется для выдерживания требуемых допусков на прямолинейность, а также может быть предусмотрен разгрузочный роликовый стол по направлению участка хранения. Установка 1 термообработки содержит продольный роликовый стол 3, расположенный вдоль оси X прокатки сразу же за последней прокатной клетью 2, для приема и перемещения в переднем направлении рельсов перед термической обработкой головки и после термической обработки головки; первый продольный резервуар 5 охлаждения для термообработки головки первого рельса, расположенный рядом и параллельно первому начальному участку роликового стола 3; второй продольный резервуар 6 охлаждения для термообработки головки второго рельса, расположенный рядом и параллельно второму участку роликового стола 3, при этом вышеуказанный второй участок расположен после первого участка; третий продольный резервуар 7 охлаждения для термообработки головки третьего рельса, расположенный рядом и параллельно третьему участку роликового стола 3, при этом вышеуказанный третий участок расположен после второго участка; по желанию заказчика, убираемые упоры, расположенные вдоль роликового стола 3 и автоматически приводимые в действие в направлении снизу вверх для остановки переднего конца рельса в точном положении относительно резервуара, в котором он подвергается термообработке. Резервуары 5, 6, 7 охлаждения имеют длину, достаточную для погружения в них всего рельса. Преимущественно вышеуказанные резервуары 5, 6, 7 являются раздельными, поскольку каждый резервуар обеспечен всем оборудованием и системами, необходимыми для эксплуатации, такими как гидросистема, устройство обработки охлаждающей жидкости, устройство смазки и т.д. Таким образом, любой из трех резервуаров может быть исключен из цикла термообработки для выполнения технического обслуживания, в то время как два оставшихся резервуара могут продолжать работу. Между установкой 1 термообработки и охлаждающей плитой 8 могут быть предусмотрены ножницы. Роликовый стол 3 может использоваться для непосредственной выгрузки на плиту 8 или рельсов,которые не требуютобработки, или крупносортного профиля, которые не требует обработки. В предпочтительном варианте, показанном на фигурах, роликовый стол 3 расположен на стандартной высоте от пола, примерно 800 мм, в то время как резервуары 5, 6, 7 с соответствующими кантователями 10 расположены выше, куда рельс 9 подается с помощью рычагов 26. Эта конструкция позволяет изготавливать менее глубокие фундаменты для участка термообработки при значительном снижении расходов. Вдоль второго и третьего участков роликового стола установлено следующее оборудование: множество перемещающих средств 20 для перемещения рельса 9 с роликового стола и его переворачивания из наклонного положения на одной боковой стороне с подошвой, обращенной к соответствующему резервуару 6, 7 охлаждения, т.е. положения, в котором рельс достигает второго и третьего участка на роликовом столе 3, в положение с головкой, обращенной вверх, близко к исходному положению(фиг. 8) кантователей 10; множество кантователей 10, расположенных между роликовым столом 3 и вторым резервуаром 6 охлаждения, для зажимания рельса и его поворота с целью его погружения в вышеуказанный резервуар 6, и между роликовым столом 3 и третьим резервуаром 7 охлаждения для зажимания рельса и его поворота с целью его погружения в вышеуказанный резервуар 7. Передающие валы 11 соответственно предусмотрены в промежуточном положении между резервуаром 6 и роликовым столом 3 и между резервуаром 7 и самим роликовым столом 3. Вдоль роликового стола 3 предусмотрены отверстия для прохода рычагов или толкателей 25 или рычагов 26. В преимущественном варианте сбоку от роликового стола 3 у соответствующих участков роликового стола 3 расположены подвижные контейнеры для удаления катаного материала, рельса или профиля с самого роликового стола в случае аварийной ситуации ниже по технологическому потоку. Подвижный контейнер 42 показан на фиг. 20 у первого участка роликового стола 3 и резервуара 5 охлаждения. После выгрузки рельса 9 на роликовый стол 3, если первый резервуар 5 охлаждения является пустым, способ перемещения содержит следующие этапы: рельс 9 перемещается и переворачивается из наклонного положения на одной боковой стороне в первом положении роликового стола 3 в положение с головкой, обращенной вверх, близко к исходному положению захватов 14 кантователей 10, как описано выше для этапов 2) и 5); этапы 6)-18) выполняются в зоне установки, содержащей резервуар 5 охлаждения и соответствую-7 019767 щий первый участок роликового стола 3; подача рельса 9 вдоль второго и третьего участков роликового стола 3, рядом с которыми расположены второй 6 и третий 7 резервуары охлаждения, без препятствования кантователям и перемещающим средствам, расположенным вдоль вышеуказанных второго и третьего участков роликового стола 3; выгрузка рельса 9 с термообработанной головкой на охлаждающую плиту 8. Если первый резервуар 5 охлаждения занят предыдущим рельсом, то рельс 9 перемещается на второй участок роликового стола 3; и если второй резервуар 6 охлаждения свободен, рельс переворачивается, зажимается, и головка подвергается термической обработке в вышеуказанном втором резервуаре 6 охлаждения, как описано в этапах со 2) по 18); если второй резервуар 6 охлаждения занят, рельс транспортируется на третий участок роликового стола 3, где он переворачивается и зажимается, и головка подвергается термической обработке в третьем резервуаре 7 охлаждения, как описано в этапах со 2) по 18); Основным преимуществом, обеспечиваемым этим вторым вариантом выполнения транспортировочной машины, является производительность 27-28 рельсов/час и часовая производительность 180-200 тонн/час. ФОРМУЛА ИЗОБРЕТЕНИЯ 1. Машина для транспортировки рельса (9), имеющего головку и подошву, содержащая: множество перемещающих средств (20) для захвата и переворота рельса (9) из наклонного положения на одной боковой стороне в положение, в котором головка рельса повернута вверх; множество кантователей (10), снабженных зажимными средствами, предназначенных для зажима рельса (9) у подошвы и перемещения его из вышеуказанного положения с головкой рельса, повернутой вверх, в положение с головкой рельса, повернутой вниз, характеризующаяся тем, что вышеуказанные перемещающие средства (20) включают в себя первые рычаги (26), выполненные с возможностью поворота с помощью первых трансмиссионных средств (11), обеспечивающие перемещение рельса (9) из наклонного положения боковой стороной на первой плоскости в положение с головкой рельса, повернутой вверх, на второй плоскости, находящейся выше упомянутой первой плоскости. 2. Машина по п.1, в которой первые рычаги (26) закреплены одним концом на соответствующем первом конце трансмиссионного вала (11') и имеют на втором конце две выступающие части (26', 26"),образующие пространство для размещения участка рельса во время перемещения первых рычагов (26). 3. Машина по п.1 или 2, в которой перемещающие средства (20) содержат вторые рычаги (25), установленные с возможностью поворота с помощью вторых исполнительных средств (28) и предназначенные для транспортировки рельса (9) по вышеуказанной первой плоскости из первого наклонного положения на одной боковой стороне во второе наклонное положение на той же стороне. 4. Машина по п.3, в которой вторые рычаги (25) установлены с возможностью поворота вокруг соответствующей оси (27) на заданный угол. 5. Машина по любому из предыдущих пунктов, в которой вышеуказанные зажимные средства имеют два захвата (14), установленные с возможностью поворотавокруг соответствующих пальцев (19), так что рельс зажимается посредством контакта только между участками внутренней поверхности захватов(14) и боковыми сторонами подошвы рельса (9). 6. Машина по п.5, в которой все кантователи (10) содержат плечо (12), которое первым концом закреплено к трансмиссионному валу (11), а на втором конце установлены захваты (14) вышеуказанных зажимных средств. 7. Машина по п.6, которая снабжена исполнительными средствами (13) для поворота захватов (14) на каждом плече (12). 8. Машина по п.7, в которой средства поворота захватов (14) содержат шестерни или рычаги, взаимодействующие с вышеуказанными исполнительными средствами (13). 9. Установка для термообработки головки рельсов, выходящих из прокатного стана, имеющего ось(X) прокатки, содержащая продольный роликовый стол (3), расположенный вдоль оси (X) прокатки; первый продольный резервуар (5) охлаждения, расположенный рядом и параллельно первому участку роликового стола (3); и транспортирующую машину по п.1,причем поперек роликового стола (3), образующего вышеуказанную первую плоскость, расположены первые рычаги (26) для захвата рельсов с вышеуказанного роликового стола (3) и их переворота из наклонного положения на одной боковой стороне на вышеуказанном роликовом столе (3) в положение, в котором головка рельса обращена вверх, на вышеуказанной второй плоскости выше первой плоскости,рядом с множеством кантователей (10); кантователи (10) снабжены зажимными средствами, предназначенными для зажима первого рельса у подошвы, и выполнены с возможностью перемещения вышеуказанного первого рельса из вышеуказан-8 019767 ного положения с головкой, повернутой вверх, в положение над первым резервуаром (5) охлаждения с головкой, повернутой вниз. 10. Установка по п.9, характеризующаяся тем, что снабжена вторым продольным резервуаром (6) охлаждения для термообработки головки второго рельса, расположенным рядом и параллельно второму участку роликового стола (3), при этом вышеуказанный второй участок расположен после первого участка,и третьим продольным резервуаром (7) охлаждения для термообработки головки третьего рельса,расположенным рядом и параллельно третьему участку роликового стола (3), при этом вышеуказанный третий участок расположен после второго участка. 11. Установка по п.10, характеризующаяся тем, что первые кантователи (10) расположены между вышеуказанным первым резервуаром (5) охлаждения и вышеуказанным первым участком роликового стола (3), вторые кантователи (10) расположены между вышеуказанным вторым резервуаром (6) охлаждения и вышеуказанным вторым участком роликового стола (3) для транспортировки второго рельса и выполнения его термической обработки во втором резервуаре (6), третьи кантователи (10) расположены между вышеуказанным третьим резервуаром (7) охлаждения и вышеуказанным третьим участком роликового стола (3) для транспортировки третьего рельса и выполнения его термической обработки в третьем резервуаре (7). 12. Установка по п.11, в которой первый, второй и третий резервуары (5, 6, 7) охлаждения и соответствующие кантователи (10) в исходном положении, по существу, расположены на вышеуказанной второй плоскости. 13. Способ транспортировки рельса с помощью установки для термообработки головки рельсов по п.9, содержащий следующие этапы, на которых перемещают рельс (9) с помощью первых рычагов (26) из наклонного положения на одной боковой стороне, на первой плоскости, в положение с головкой рельса, повернутой вверх, на второй плоскости,находящейся выше указанной первой плоскости; зажимают рельс (9) с помощью зажимных средств множества кантователей (10) за счет контакта участков внутренней поверхности захватов (14) только с боковыми сторонами подошвы рельса (9); поворачивают кантователи (10) для перемещения рельса (9) из вышеуказанного положения с головкой, повернутой вверх, в положение с головкой, повернутой вниз, и погружают рельс (9) в резервуар (5) охлаждения,выгружают рельс (9) из резервуара (5) охлаждения. 14. Способ по п.13, в котором перед этапом зажимания рельса (9) выполняют правку рельса посредством совместного использования кантователей (10) и первых рычагов (26). 15. Способ по п.14, в котором правку выполняют за счет поворота кантователей (10), начиная с исходного положения, рельс (9) поднимают до достижения положения взаимодействия с первыми рычагами (26), в котором головка рельса соответствующим образом отделяется от выступающих частей (26') первых рычагов за исключением точек большего изгибания рельса, в которых существует контакт между головкой рельса и выступающими частями (26').
МПК / Метки
МПК: B21B 39/24, C21D 9/06, B65G 7/08
Метки: машина, способ, осуществления, транспортировки, рельсов
Код ссылки
<a href="https://eas.patents.su/14-19767-sposob-transportirovki-relsov-i-mashina-dlya-ego-osushhestvleniya.html" rel="bookmark" title="База патентов Евразийского Союза">Способ транспортировки рельсов и машина для его осуществления</a>
Предыдущий патент: Низкоэмиссионная газовая горелка трубчатого типа с направленным воздушным потоком
Следующий патент: Соединения, модулирующие активность toll-подобных рецепторов
Случайный патент: Защищенные от растворения желудочным соком микрогранулы, способ получения и фармацевтические препараты