Способ и устройство для переработки угля
Формула / Реферат
1. Способ обработки угля для удаления загрязнений, согласно которому
в реакционном резервуаре из водного аммиака, имеющего концентрацию, не превышающую 19% аммиака, готовят раствор водного аммиака с концентрацией, не превышающей 10% аммиака;
добавляют уголь в реакционный резервуар;
перемешивают уголь в реакционном резервуаре для смешения угля и указанного раствора для обеспечения контакта раствора с поверхностями и порами угля;
осуществляют мониторинг процесса, чтобы определить, когда концентрация водного аммиака в реакционном резервуаре упадет ниже указанного диапазона;
подают в реакционный резервуар раствор водного аммиака с концентрацией аммиака, находящейся в указанном диапазоне или превышающей его, для возвращения концентрации раствора в пределы указанного диапазона;
выгружают обработанный уголь из резервуара.
2. Способ по п.1, согласно которому в реакционном резервуаре готовят раствор водного аммиака с концентрацией от около 3 до около 5% аммиака.
3. Способ по п.1, согласно которому дополнительно
выпускают загрязненный раствор, содержащий угольную мелочь, из реакционного резервуара;
извлекают угольную мелочь из загрязненного раствора;
осуществляют рециркуляцию раствора в реакционный резервуар,
при этом указанный мониторинг выполняют посредством определения концентрации аммиака в выпускаемом растворе либо до, либо после извлечения угольной мелочи.
4. Способ по п.3, согласно которому извлеченную угольную мелочь примешивают обратно к обработанному углю.
5. Способ по п.4, согласно которому дополнительно промывают обработанный уголь и извлеченную мелочь деионизированной водой и обезвоживают промытый уголь.
6. Способ по п.5, согласно которому дополнительно собирают выходящий поток от обезвоживания и обрабатывают выходящий поток для отделения из него угольной мелочи.
7. Способ по п.1, согласно которому дополнительно отделяют от угля пиритную серу и другие более тяжелые, чем уголь, частицы с помощью гравитационного или центробежного ситового разделительного устройства.
8. Способ по п.7, согласно которому гравитационное или центробежное ситовое разделительное устройство размещают в реакционном резервуаре (18, 120).
9. Способ по п.1, согласно которому при удалении обработанного угля из реакционного резервуара удаляют уголь в суспензии угля в водном растворе аммиака, направляют суспензию в гравитационное или центробежное ситовое разделительное устройство снаружи реакционного резервуара для отделения пиритной серы и других более тяжелых, чем уголь, частиц от суспензии и выпускают суспензию для отделения угля от раствора.
10. Способ по п.9, согласно которому дополнительно осуществляют рециркуляцию раствора, выпущенного из суспензии, обратно в реакционный резервуар, при этом осуществляют мониторинг концентрации аммиака в растворе, выпущенном из суспензии, чтобы определить, когда концентрация аммиака уменьшается до уровня ниже установленного диапазона.
11. Способ по п.1, согласно которому дополнительно осуществляют сушку обработанного угля, не промывая его.
12. Устройство для переработки угля для удаления загрязнений, содержащее
резервуар для хранения водного аммиака, имеющего концентрацию аммиака, не превышающую 19%;
реакционный резервуар, приспособленный для размещения водного раствора аммиака с концентрацией, не превышающей 10% аммиака, приготовленного из водного аммиака из резервуара для хранения, и подлежащего обработке угля и имеющий элементы для механического перемешивания, смешивающие уголь и раствор для приведения раствора в контакт с поверхностями и порами угля и выпускной патрубок для обработанного угля;
систему мониторинга для определения концентрации водного аммиака в реакционном резервуаре и
контроллер для подачи водного раствора аммиака из резервуара для хранения в реакционный резервуар для поддержания концентрации раствора в пределах, необходимых для удаления загрязнений.
13. Устройство по п.12, в котором указанная концентрация аммиака в растворе в реакционном резервуаре составляет 3-5%.
14. Устройство по п.12, в котором дополнительно реакционный резервуар имеет второй выпускной патрубок для выпуска загрязненного раствора, содержащего угольную мелочь, из реакционного резервуара и имеет разделительное устройство для извлечения угольной мелочи из загрязненного раствора и выпуска раствора после извлечения угля в возвратную систему для рециркуляции раствора в реакционный резервуар.
15. Устройство по п.12, в котором дополнительно реакционный резервуар и разделительное устройство смонтированы на передвижной платформе.
16. Устройство по п.12, которое содержит гравитационное или центробежное ситовое разделительное устройство для отделения от угля пиритной серы и других более тяжелых, чем уголь, частиц.
17. Устройство по п.12, которое содержит сушильное устройство (42) для сушки обработанного угля с покрытыми аммиаком поверхностями угля, не промывая его.
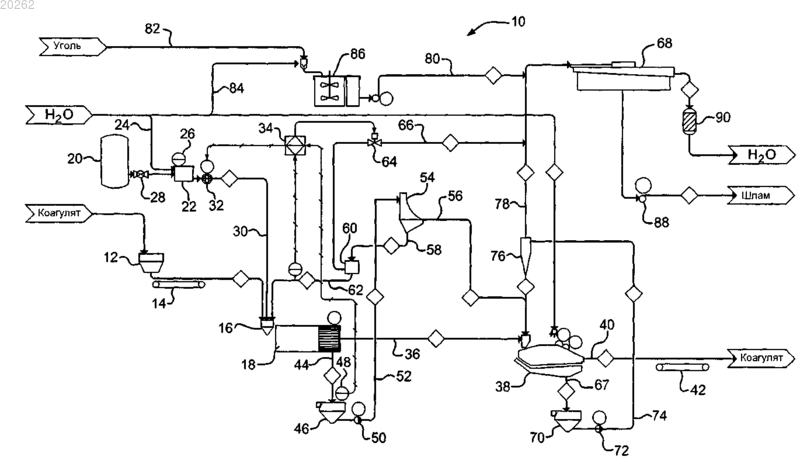
Текст
СПОСОБ И УСТРОЙСТВО ДЛЯ ПЕРЕРАБОТКИ УГЛЯ Способ обработки угля для удаления серы и других загрязнений смешением в реакционном резервуаре угля с раствором водного аммиака, имеющим выбранный диапазон концентрации,предпочтительно составляющий от 3-5%, аммиака в воде. Смешение обеспечивает контакт раствора с поверхностями и порами угля. Способ включает мониторинг обработки для определения, когда концентрация водного аммиака в реакционном резервуаре уменьшилась до уровня ниже выбранного диапазона, и водный аммиак с концентрацией аммиака в выбранном диапазоне или выше данного диапазона подают в реакционный резервуар для возвращения раствора в пределы выбранного диапазона. Очищенный уголь может быть промыт и высушен или высушен без промывания с образованием аммиачного покрытия на поверхностях угля и в порах. Предложены некоторые компоновки установки для реализации способа. Область техники, к которой относится изобретение Настоящее изобретение относится к области переработки угля и, в частности, к области обработки угля для удаления загрязнений, которые могут создавать загрязнения окружающей среды в продуктах сгорания угля. Уровень техники Настоящее изобретение применимо для очистки разнообразных типов угля: антрацита, битуминозного угля и бурого угля. Главным образом оно применимо к углям, которые сжигают для промышленных целей. В зависимости от источника эти угли содержат различные загрязнения, которые могут создавать загрязнения окружающей среды в дымовых газах или зольных остатках. Для сокращения этих загрязнений до сжигания угля использовали и применяют в настоящее время различные способы промывания,механического разделения и химического реагирования. Сера представляет собой существенный загрязнитель, создающий особенную проблему в отношении промышленных установок для сжигания угля. Угли, содержащие большое количество серы, могут выделять значительное количество оксидов серы в отходящих газах. Наиболее распространенной формой оксида серы в дымовом газе является диоксид серы (SO2), и он обусловливает особенно острую экологическую проблему. Диоксид серы реагирует с кислородом, обычно в присутствии катализатора, такого как диоксид азота (NO2), с образованием триоксида серы (SO3), который затем реагирует с молекулами воды в атмосфере, образуя серную кислоту (H2SO4), которая возвращается на Землю в виде кислотного дождя. Таким образом, экологические проблемы в отношении этих загрязнителей в газообразных продуктах горения угля привели к правительственным постановлениям, ограничивающим выбросы оксидов серы (SOx) и оксидов азота (NOx). Выбросы оксидов азота при сжигании угля могут быть сокращены с помощью технологий сжигания, таких как сжигание в псевдоожиженном слое. Для сокращения количеств оксидов серы существуют системы обессеривания топочных газов на основе вымывания оксидов серы из газообразных продуктов горения угля в дымовых трубах современных электростанций, работающих на угле, но все-таки более эффективным является снижение содержания серы в любом высокосернистом угле до его сгорания. Химические анализы угля в основном регистрируют уровень содержания серы в трех категориях: сульфатной серы, пиритной серы и органической серы, которые объединяют для определения общего содержания серы в образце угля. В большинстве методов анализа измеряют уровень пиритной серы и органической серы вместе с общим содержанием серы. Затем разность между долей пиритной и органической серы и общим содержанием серы относят на счет сульфатов. Этот тип сульфата может представлять собой сульфат кальция, такой как гипс, или сульфаты двухвалентного железа, образованные в угле под воздействием атмосферных условий. Независимо от типа, выделение сульфатов из угля является относительно простым, поскольку сульфаты можно растворить в разбавленных растворах кислот или других растворителях. Пиритный сульфат главным образом представляет собой дисульфид железа (FeS2), кристаллический минерал, известный как пирит. Пирит часто находится в жильных интрузиях и слоях, близких к угольным пластам или пересекающихся с ними. Пирит не растворяется в воде или растворе слабых кислот. Однако пиритные сульфаты имеют удельный вес, который в 3-4 раза превышает плотность угля. Таким образом, значительную часть пиритной серы можно отделить от угля традиционными методами гравитационного обогащения, такими как сепараторы для обогащения крупного угля в тяжелой среде или центрифуги, чаще всего применяемые в процессах мокрого обогащения угля. Органическая сера составляет часть самого угля, будучи связанной химическими связями. Органическая сера традиционно трудно поддается удалению, поскольку ее нельзя отделить от угля без разрыва химических связей. Для разрушения связей и высвобождения серы в других формах с целью удаления из матрицы угля могут быть использованы реакции окисления. Таким образом, принимая во внимание эти различные формы содержания серы, известное решение переработки угля для снижения уровня серы включает широкий круг способов: от простого промывания в растворе растворителя или промывания в комбинации с разделением для обогащения угля в тяжелой среде и/или пенной флотацией для растворения большей части сульфатов и отделения большей части пиритной серы от угля до применения химических окислителей, оксидативных ферментов и микробиальных методов обессеривания. Для более интенсивного снижения содержания пиритной серы также были предложены химические реагенты. Например, способ Мейерса, описанный в статье "Chemical Removal of Pyritic Sulfur from Coal"("Химическое удаление пиритной серы из угля") и в патентах США 3926575 и 3917465 на имя Мейерса,направлен на удаление пиритной серы с помощью химической реакции с использованием хлорида трехвалентного железа или сульфата трехвалентного железа в качестве окислителя. Пирит нерастворим в воде и кислоты, обычно используемые для растворения большинства неорганических солей (и сульфатов), не будут растворять пирит. Поэтому окислитель используют в способе Мейерса для преобразования пирита в сульфаты или элементарную серу, которые растворимы в разбавленных растворах кислот. Способ Мейерса основан на постулате, что хлорид трехвалентного железа или сульфат трехвалентного железа являются более селективными в окислении пирита, чем в окислении угля, причем предпочтительным реагентом является сульфат трехвалентного железа. При применении реакционных температур около 100 С Мейерс сообщает об удалении от 40 до 70% пиритной серы из битуминозного угля с использованием сульфата трехвалентного железа в качестве окислителя, с последующей нейтрализацией промыванием в толуоле. Также существуют химические способы удаления органической серы вместе с пиритом. В способе обессеривания угля, описанном в патенте США 4081250, используют газообразный хлор, который барботируют через суспензию влажного угля в хлорированном растворителе для вымывания пиритной серы и для преобразования органической серы в растворимые сульфаты. Затем обработанный хлором уголь отделяют, подвергают гидролизу и дехлорированию нагреванием при температуре 500 С. Другие способы устраняют необходимость в подведении теплоты извне для инициирования экзотермической реакции окисления в угле в течение кратковременного периода. Патент США 4328002 на имя Бендера описывает способ этого типа, в котором уголь предварительно нагревают с разбавленной водной суспензией окислителя, промывают водой и затем набрызгивают на него или погружают его в концентрированный раствор окислителя на время от 1 до 2 мин, в течение которого развивается экзотермическая реакция. Однако более поздний патент Бендера 4560390 раскрывает, что продолжительность воздействия раствора окислителя может быть сокращена до столь короткого, как 22-30 с длительности обработки, когда реакция протекает в гидроциклоне или сепараторе для обогащения в тяжелой среде. В свете этих разнообразных известных способов обработки цель настоящего изобретения состоит в создании эффективного и экономичного способа переработки угля, который может быть реализован в промышленном масштабе для значительного снижения общего содержания серы в угле, включая органическую серу. Желательными дополнительными результатами являются сопутствующее окисление других загрязняющих примесей в угле и повышение теплотворной способности в BTU (британских тепловых единицах). Сущность изобретения Базовый способ. В способе переработки угля согласно настоящему изобретению используют гидроксид аммония(NH4OH), более известный как водный аммиак, в качестве растворителя и в качестве окислителя для сокращения серного загрязнителя в угле. В то время как аммиак был предложен в качестве компонента окислительного реагента, как описано выше в патентах Бендера, способ согласно настоящему изобретению проводят с использованием более разбавленного водного аммиака с пониженными концентрациями для исключения реакций с высокой экзотермичностью, которые описаны в патентах Бендера. Экономическая эффективность и защита окружающей среды в этом способе достигаются поддержанием выбранной концентрации NH4OH в ходе рециркуляции и повторного использования обрабатывающего раствора. В дополнение, для автоматизации рециркуляции и поддержания выбранной концентрации могут быть применены регуляторы технологического процесса. С технической точки зрения гидроксид аммония не является соединением, которое можно выделить, но представление в виде NH4OH дает правильное описание того, как ведет себя раствор аммиака в воде, и обычно так и применяется. Будучи добавленным к воде, аммиак отнимает протоны у некоторой малой части воды с образованием ионов аммония (NH4+) и гидроксид-анионов (OH-). Поэтому датчики,измеряющие концентрацию водного аммиака в описываемом здесь способе, могут измерять концентрацию ионов NH4+ в растворе. В своих общих принципах изобретение включает способ обработки угля для удаления загрязнителей, включающий следующие стадии: (а) приготовление раствора водного аммиака в выбранном диапазоне концентраций аммиака в реакционном резервуаре; (б) добавление угля в реакционный резервуар; (в) перемешивание угля внутри реакционного резервуара для смешения угля и раствора для обеспечения контакта раствора с поверхностями и порами угля; (г) выгрузка обработанного угля из резервуара; (д) мониторинг обработки для определения, когда концентрация водного аммиака в реакционном резервуаре уменьшилась до уровня ниже выбранного диапазона; и (е) подача в реакционный резервуар водного аммиака с концентрацией аммиака в выбранном диапазоне или на уровне выше последнего для возвращения раствора в пределы выбранного диапазона. Водный аммиак, используемый для этого способа, может быть приготовлен смешением безводного аммиака (NH3) с водой. Чтобы избежать необходимости уведомления Управления по охране окружающей среды США, Управления охраны труда США и других распорядительных организаций и для соблюдения требований к обращению с продуктом, диапазон концентраций должен быть в пределах 19 вес.%NH3 или меньше. На практике способ является эффективным, когда диапазон концентраций поддерживается в выбранном диапазоне ниже 10%, в предпочтительном варианте исполнения способа концентрацию поддерживают от около 3 до 5 вес.% безводного аммиака в воде. Водный аммиак наносят на уголь внутри реакционного резервуара или в серии реакционных резервуаров в процессе последовательного течения. В одном описываемом здесь варианте исполнения реакционный резервуар представляет собой реактор типа "смеситель-сепаратор", такой как вращающийся барабанный скруббер, имеющий лопатки для поднятия угля из раствора и погружения его обратно в раствор по мере вращения барабана. Это физическое перемешивающее действие способствует разрушению сцепления пиритной серы с частицами угля так, что более плотный пирит может быть отсеян из раствора на дне барабана. Перемешивание вращением также приводит аммиачный раствор в контакт со всем углем, в том числе с порами на открытых поверхностях, и обеспечивает возможность воздействия воздуха,когда уголь поднимается вверх и падает, так что аммиак способен окислять органическую серу в сульфаты, которые растворяются в растворе. В качестве альтернативных вариантов исполнения оборудования перемешивание и смешение могут быть выполнены в реакционном резервуаре без сопутствующего отделения пиритов. Реакционный резервуар не обязательно должен очищать более легкий уголь от более тяжелого пирита и другой тяжелой среды, если суспензию, выходящую из резервуара, направляют в отстойное устройство для разделения по удельному весу. В качестве еще одного альтернативного оборудования шнековое моечное устройство для крупнозернистого материала или шнековые мойки в последовательном соединении могут быть использованы для требуемых перемешивания, аэрации и выдерживания длительности воздействия в растворе аммиака,в то же время обеспечивая флотационное отделение мелкодисперсных частиц угля от более грубозернистого угля и более тяжелого пирита. Затем, после шнековых моечных устройств может быть применен способ отделения с использованием сепаратора для обогащения в тяжелой среде для удаления чешуек пирита из более грубозернистого угля. Это и другие альтернативные устройства и производственные компоновки показаны на чертежах и описаны в подробном описании. Извлечение и повторное использование аммиака. Еще один аспект изобретения включает извлечение и рециркуляцию аммиачного раствора. Загрязненный раствор аммиака выпускают из реакционного резервуара в виде периодической выгрузки или в виде непрерывного контролируемого по расходу потока. Полезная фракция угольной мелочи может быть извлечена из загрязненного раствора с помощью известных сепараторов частиц, таких как очиститель в виде дугового сита или центрифуга корзиночного типа. Раствор опробуют с помощью датчика или другого устройства для мониторинга, чтобы определить концентрацию аммиака перед сепаратором для угольной мелочи или ниже по потоку относительно него. После извлечения угольной мелочи раствор вовлекают в рециркуляцию в реакционный(ые) резервуар(ы) и, если концентрация аммиака упала до уровня ниже выбранного диапазона, водный аммиак с концентрацией аммиака в выбранном диапазоне или выше такового может быть добавлен в реакционный резервуар для возвращения раствора в пределы выбранного диапазона. Извлечение воды. Обработанный уголь, включающий извлекаемые мелкие частицы, существует в форме плотной суспензии до его обезвоживания и сушки. Перед обезвоживанием и высушиванием суспензия также может быть промыта деионизированной водой. Воду, выжатую из суспензии, в том числе любую промывочную воду, направляют через еще один сепаратор для удаления нерастворимых частиц, таких как остаточный уголь, пирит или другие минералы. Вода может рециркулировать в реакционный резервуар или в накопительный бак с раствором для повторного использования. Воду, выносящую отделенные нерастворимые частицы, направляют в бак для флокуляционной очистки. В способе также можно выводить аммиачный раствор из основного отстойника для выноса пиритной фракции. Фракцию также направляют в бак для флокуляционной очистки, где пирит и другой тяжелый дисперсный материал флокулирует из фракции. Вода, извлеченная из бака для флокуляционной очистки, может быть подвергнута деионизации и повторно использована в процессе. Этот способ является экологически благоприятным в том, что аммиак по большей части извлекают и используют повторно без выброса в атмосферу или выведения в виде загрязненных сточных вод. При предпочтительной автоматизации установки программируемые контрольные устройства управляют утилизацией и повторным смешиванием технологического раствора и сырьевых материалов, в то же время поддерживая концентрацию ионов NH4 в реакционном резервуаре в желательном диапазоне. Компоновки технологической установки. Для реализации вышеописанного способа могут быть применены разнообразные компоновки технологической установки. Большинство крупномасштабных установок будет стационарными, но описаны варианты исполнения, где установку по большей части размещают на передвижной платформе, которая может быть соединена с внешними питающими трубопроводами для подведения аммиака и воды, с баками для флокуляционной очистки и тому подобными для перемещения вокруг штабелей или отстойников с отходами угледобывающего предприятия. Установки также можно эксплуатировать в автоматическом режиме под управлением технологических логических контроллеров или программируемого центрального компьютера для мониторинга и регулирования уровня аммиака в пределах выбранного концентрационного диапазона и добавления нового раствора, чтобы вернуть в этот диапазон. Автоматизация также может включать устройство тестирования дымовых газов для опробирования партий или в периодическом режиме, чтобы подтверждать соответствие стандартам сокращения выбросов. Повышение потенциала теплотворной способности. Для угля, очищенного вышеописанными способами, обнаруживаются определенные дополнитель-3 020262 ные благоприятные изменения. Как описано выше, обработанный уголь может быть промыт и затем обезвожен и высушен или, альтернативно, высушен без промывания, чтобы сохранить покрытие из аммиачного раствора на поверхности угля. Оба способа приводят к повышению потенциальной теплотворной способности угля сравнительно с углем, не подвергнутым мокрому обогащению. Хотя точный механизм повышения теплотворной способности не был исследован, вероятно, он обусловлен отчасти тем,что раствор аммиака удаляет негорючие материалы или материалы с низкой теплотворной способностью из пор угля, приводя к увеличению площади поверхности, на которой может происходить горение, и отчасти остаточным аммиачным покрытием на поверхности угля и в порах, сокращающим склонность угля к повторному поглощению влаги. Если этот механизм повышения теплотворной способности включает две части, этим можно было бы объяснить то наблюдение, что сохранение покрытия из аммиака на поверхности угля обеспечивает большее повышение теплотворной способности, иногда в диапазоне от 20 до 40% прироста теплотворной способности. Механизм очистки пор также объясняет то наблюдение, что коксовые брикеты, изготовленные из паровичного угля, который был обработан этим способом, характеризуются увеличением показателя свободного вспучивания, достаточного для соответствия техническим условиям для металлургического угля. Сокращение содержания основных оксидов. Второе преимущество сохранения покрытия из аммиака на поверхности угля состоит в сокращении содержания основных оксидов, образующихся во время сгорания. Анализ золы от угля с остаточным аммиачным покрытием из процесса очистки показывает снижение уровня триоксида серы, диоксида кремния и других основных оксидов по сравнению с обработанным углем, который был очищен промыванием. Повышение эффективности скрубберов для дымовых газов. Остаточное аммиачное покрытие из процесса очистки также может создавать источник аммиака в дымовом газе, способствующего работе воздухоочистительных установок для удаления NO2. Аммиак иногда добавляют в топочные газы для снижения содержания оксидов азота в газах преобразованием в азот и воду (процесс денитрификации отходящих газов). Присутствуя в образцах газа, аммиак будет легко реагировать с другими компонентами, такими как диоксид серы, в образце с образованием солей аммония. Эта соль является относительно низкокипящей, так что она присутствует в газообразном состоянии при более высоких температурах в дымовой трубе. Остаточный аммиак на высушенном угле, полученном этим способом, может способствовать работе воздухоочистительных установок благодаря наличию дополнительного аммиака в дымовом газе. Сокращение содержания других загрязнений. В дополнение к сокращению содержания серы водный раствор аммиака также растворяет и/или ионизирует другие загрязнения для удаления из угля. Из этих других загрязненийнаиболее значительными являются хлор, ртуть и мышьяк. Многие угольные пласты имеют сильное загрязнение хлором вследствие испарения рассола из старых солончаковых болот, в которых произрастали растения, впоследствии образовавшие уголь. Хлор растворяется в аммиачном промывном растворе. Другие сокращаемые загрязнения включают селен, загрязнения на основе углерода и окисленные соединения. Эти и другие аспекты способа переработки, компоновки установок и улучшение качества угля будут очевидными из нижеследующего описания предпочтительных вариантов исполнения. Краткое описание чертежей Фиг. 1 представляет блок-схему установки для переработки угля с использованием настоящего изобретения. Фиг. 2 представляет вид сбоку вертикальной проекции передвижной установки для переработки угля. Фиг. 3 представляет вид спереди передвижной установки для переработки угля с питающим шнековым транспортером. Подробное описание способа и установки, показанной на чертежах На фиг. 1 показана установка 10 для переработки угля, которая может быть использована для исполнения способа переработки угля согласно настоящему изобретению. Как показано на фиг. 1, путь партии угля начинается слева по стрелке, обозначенной "Уголь", показывающей, что уголь загружают в питающий бункер 12. Перед помещением в питающий бункер уголь может быть подвергнут предварительному промыванию. Если перерабатываемый уголь представляет собой угольные отходы, такие как материал из штабеля отработанной породы или отстойника, он может содержать чрезмерно большое количество пустой породы и растительного материала, и значительное сульфатное покрытие вследствие длительного воздействия погодных условий. Этот древесный и растительный материал может быть отделен флотацией и просеиванием в стадии предварительного промывания перед тем, как угольные отходы будут помещены в питающий бункер. Если используют предварительное промывание, вода для предварительного промывания предпочтительно является деионизированной с использованием имеющегося в продаже на рынке умягчителя воды. К деионизированной воде может быть добавлена каустическая сода для растворения сульфатного покрытия и другого растворимого материала в стадии предварительного промывания. Затем влажный уголь перед загрузкой в питающий бункер подвергают дренированию для стока воды. Уголь транспортируют из бункера 12 по желобчатому конвейеру 14 или ленточному транспортеру во впускной патрубок 16 реакционного резервуара 18. Реакционный резервуар 18 в этом варианте исполнения представляет собой комбинированную реакционную и разделительную камеру, такую как вращающаяся барабанная промывочная камера, описанная в патенте США 4159242, или усовершенствованную конструкцию такого вращающегося барабанного скруббера. Во вращающемся барабанном скруббере используют смесь угля с водным раствором аммиака для удаления растворимых загрязняющих примесей в раствор, окисления органической серы с образованием растворимой формы и отделения пирита и других частиц с более высоким удельным весом от угольной матрицы. Устройство этого типа представляет собой барабанный скруббер, производимый фирмой McLanahan Corporation, с регулируемыми подъемными лопатками для обеспечения интенсивного переворачивания угольной матрицы и тщательного смешивания аммиачного раствора со всей массой угля. Должно быть понятно, что в крупногабаритной установке многочисленные реакционные резервуары могут быть размещены параллельно, с подведением водного аммиака и конструкционными элементами рециркуляции, обсуживающими все резервуары. Реагент представляет собой раствор гидроксида аммония (NH4OH), также называемый здесь как водный аммиак, который используют в качестве растворителя и в качестве окислителя в растворе для очистки угля. В раствор реагента могут быть включены другой растворитель и окислители; однако эффективный раствор получают в выбранном диапазоне концентраций ниже 10% водного аммиака, Предпочтительный концентрационный диапазон для водного аммиака составляет от 3 до 5% аммиака в воде. Для получения раствора в этом диапазоне водный аммиак первоначально готовят дозированием безводного аммиака (NH3) из резервуара-хранилища 20 в барботажный бак 22, в который также поступает деионизированная вода по водопроводу 24, достаточная для создания водного раствора аммиака с коэффициентом разбавления на верхнем конце предпочтительного диапазона концентраций (т.е. при 5% или близко к таковой в барботажном резервуаре для поддержания концентрации в диапазоне от 3 до 5% в реакционном резервуаре). Могут быть использованы датчик 26 для измерения концентрации водного аммиака зондированием концентрации в барботажном баке и клапанные управляющие устройства 28,применяемые для регулирования дозировки воды и NH3 в барботажный бак соответственно. Альтернативно, для смешения с деионизированной водой и создания предпочтительной концентрации могла бы быть использована подача из бака, содержащего водный раствор аммиака с более высокой концентрацией (т.е. 19% во избежание необходимости уведомления и для соблюдения условий обращения). Свежий водный раствор аммиака из барботажного бака 22 направляют в реакционный резервуар по трубопроводу 30 с помощью дозировочного насоса 32, управляемого контроллером 34 технологического процесса. Как будет дополнительно описано ниже, контроллер технологического процесса получает от одного или более датчиков показание объема рециркулирующего раствора, имеющегося для повторного использования в реакционном резервуаре, и показание концентрации NH4 в имеющемся возвращаемом растворе. Контроллер может добавлять свежий раствор из барботажного бака для пополнения потери объема жидкости в угольной суспензии и фракции нерастворимого пирита. Более того, когда концентрация водного аммиака падает ниже целевого диапазона, т.е. ниже 3%, контроллер может отводить часть рециркулирующего раствора в бак для флокуляционной очистки сточных вод и пополнять реакционный резервуар дозированным объемом свежего раствора из барботажного бака для доведения концентрации в реакционном резервуаре обратно до желательного диапазона. Реакционный резервуар 18 в форме вращающегося барабанного скруббера смешивает водный раствор аммиака с углем. Частицы угля многократно поднимаются из раствора подъемными лопатками и падают обратно в него внутри барабана. Это интенсивное механическое перемешивание разбивает крупные куски и агломераты угля и обеспечивает раствору возможность вступать в тесный и повторяющийся контакт с поверхностями и порами угля. В дополнение к окислению органической серы в угле, водный аммиак имеет свойства растворителя, вымывающего и растворяющего грязь и другой малогорючий материал из пор. Поднимающее действие лопаток также подвергает уголь воздействию воздуха в барабане для рассеяния теплоты и для обеспечения доступа кислорода для процесса окисления. Когда реакция в периодическом режиме завершается, загрязненному раствору дают возможность стечь из барабана и вовлекают его в рециркуляцию для повторного использования, как описано далее. Продолжительность пребывания в реакционном резервуаре может быть установлена на основе оценок, сделанных с использованием предварительного химического анализа образца угля. NH4OH действует как растворитель для остаточного сульфата и как поверхностно-активное вещество для свободных частиц пирита, прилипших к углю, таким образом, что более тяжелый пирит может быть отделен от более легкого угля под действием силы тяжести и просеиванием. Он также действует как окислитель для органической серы. Концентрация NH4OH на уровне 3-5% недостаточна для того, чтобы вызывать резкое повышение температуры в результате экзотермического окисления, и небольшое количество теплоты реакции рассеивается так, что не требуется никакого дополнительного охлаждения или сокращения времени пребывания угля в растворе в реакционном резервуаре. Продолжительность пребывания в резервуаре типично может составлять 3-5 мин для обеспечения полного окисления органической серы и отде-5 020262 ления пиритной серы. Более высокий диапазон концентраций NH4OH мог бы сокращать продолжительность пребывания при перемешивании в барабане, но 3-5%-ная концентрация в настоящее время является предпочтительной как хорошая оптимизация. Когда время пребывания истекает, резервуар дренируют и уголь выгружают из резервуара в виде суспензии через трубопровод 36 на установку для промывания и обезвоживания, которая может представлять собой широко используемое ситовое устройство для обезвоживания, которое имеет сопла для проведения очистительного промывания деионизированной водой, если желательно смывать остаточный водный раствор аммиака. Однако промывание чистой водой может быть преднамеренно пропущено так,что уголь проходит с сита для обезвоживания по трубопроводу 40 на конвейерную сушилку для испарения воды и оставления аммиачного покрытия на поверхностях угля. Как описано выше, остаточный аммиак в покрытии может, как представляется, повышать теплотворную способность угля и в то же время сокращать содержание основных оксидов, образующихся во время сгорания угля. Покрытие из аммиака,оставшегося после процесса очистки, также может создавать источник полезного аммиака в топочном газе для способствования работе воздухоочистительных установок для удаления NO2. Аммиак иногда добавляют в дымовые газы для снижения содержания оксидов азота в газах преобразованием в азот и воду (процесс денитрификации отходящих газов). Присутствуя в образцах газа, аммиак будет легко реагировать с другими компонентами, такими как диоксид серы, в образце с образованием солей аммония. Эта соль является относительно низкокипящей, так что она присутствует в газообразном состоянии при более высоких температурах в дымовой трубе. Остаточный аммиак на высушенном угле, полученном этим способом, также может добавлять аммиак к дымовым газам и способствовать работе воздухоочистительных установок подобным образом. Загрязненный раствор реагента, который был слит из реакционного резервуара 18, пропускают по трубопроводу 44 в отстойник 46. Концентрация NH4+ в растворе в отстойнике может быть измерена датчиком 48, который посылает сигнал, показывающий концентрацию, на контроллер 34 технологического процесса, который может представлять собой программируемый логический контроллер или компьютер общего назначения, исполняющий программу технологического управления. Загрязненный раствор в отстойнике 46 будет содержать извлекаемую фракцию угольной мелочи. Насос 50 направляет поток загрязненного раствора из отстойника по трубопроводу 52 в сепаратор для мелких частиц, такой как дуговой ситовой очиститель 54 для извлечения пригодной для использования угольной мелочи. Затем мелочь направляют по трубопроводу 56 из сепаратора 54 на сито 38 для промывания и обезвоживания угля и смешивают с общей массой обезвоживаемого угля. Водный раствор аммиака из дугового ситового очистителя через трубопровод 58 собирают в рециркуляционный бак 60. Когда следующая партия угля готова для подачи в реакционный резервуар, контроллер технологического процесса определяет, достаточно ли количество имеющегося раствора в рециркуляционном баке, если оно недостаточно в рециркуляционном баке, контроллер приводит в действие насос 32 для подведения порции свежего водного раствора аммиака из барботажного бака 22, необходимого для смешения с рециркулирующим раствором в реакционном резервуаре. Раствор из рециркуляцонного бака 60 вовлекают в рециркуляцию по трубопроводу 62 в реакционный резервуар для использования со следующей партией угля. Если уровень содержания NH4+ в рециркулирующем растворе становится слишком низким, как это может произойти после многократно повторенных циклов, контроллер 34 технологического процесса может открыть выпускной клапан 64 для направления некоторого количества или всего использованного раствора через трубопровод 66 из рециркуляционного бака 60 в резервуар-уплотнитель 68 для сточных вод. В резервуар 68 также направляют жидкость, стекающую из сита 38 для промывания и обезвоживания, которую собирают через трубопровод 67 в еще один отстойник 70. Эта жидкость является очень разбавленной (с низкой концентрацией NH4+), если уголь промывают деионизированной промывочной водой. Насос 72 перемещает жидкость по трубопроводу 74 в циклонный сепаратор 76 для удаления частиц угля. Затем жидкость направляют по трубопроводу 78 в резервуар-уплотнитель 68 для сточных вод. Резервуар-уплотнитель 68 может принимать раствор коагулята через трубопровод 80 для агломерирования любого дисперсного материала в сточных водах. Коагулят смешивают через трубопровод 82 с чистой технологической водой через трубопровод 84 в смесительном баке 86, из которого он при необходимости может быть подведен по трубопроводу 80 в резервуар-уплотнитель 68. Тонкодисперсные частицы слипаются в более крупные агломераты и оседают на дно, где они могут быть удалены в виде шлама насосом 88 в контейнер для мусора. Шлам будет содержать концентрированный сульфат, который может быть подвергнут переработке в удобрение. Чистую воду, выведенную из резервуара-уплотнителя 68, пропускают через скруббер 90 для жидкого аммиака, для осаждения аммиака, остающегося в растворе. Вода может быть подвергнута фильтрованию, деионизации и повторно использована в качестве технологической воды. Жидкий аммиак может быть смешан с сульфатным шламом в качестве ингредиента удобрения. Высокотемпературная трубчатая печь и прибор для эмиссионного мониторинга (не показаны) могут быть использованы для исследования образца обработанного угля для определения и регистрации хими-6 020262 ческого анализа продукта сгорания угля. В качестве примера трубчатая печь с температурой 1200 С будет сжигать образец угля при температуре немного выше верхнего предела диапазона горелки с псевдоожиженным слоем, используемой для выработки электрической энергии, но значительно ниже порогового значения, при котором образуются оксиды азота (приблизительно 1400 С). Трубчатая печь этого типа может быть приобретена в фирме SentroTech в Бери, Огайо. Газообразный продукт горения из угля, сожженного в трубчатой печи, может быть автоматически проанализирован с помощью прибора для эмиссионного мониторинга, такого как продаваемый фирмой VARIOplus Industrial. Прибор для мониторинга может обнаруживать следовые количества SO2, NOx, CO2 и других потенциальных загрязнителей атмосферы. Прибор может быть соединен кабелем для передачи данных через последовательный порт RS-232 с компьютером для регистрации данных. Данные могут быть использованы для удостоверения улучшения угля для налоговых льгот или контроля качества и могут иметь определенные пороговые значения,запрограммированные для изъятия партии угля, которая превышает пороговые величины выбросов. Альтернативные компоновки установки. Функции смешения в реакционном резервуаре и гравитационного отделения тяжелых частиц, которые исполняет вращающийся барабанный скруббер, могут быть организованы в последовательном режиме таким образом, что реакционный резервуар только тщательно смешивает водный раствор аммиака с углем для окисления органической серы и высвобождения пиритной серы, прилипшей к углю, без сопутствующего отделения пирита от угольной суспензии внутри барабана. В этой альтернативной компоновке угольная суспензия проходила бы из реакционного резервуара в гравитационный сепаратор для удаления пирита и других тяжелых материалов. В качестве альтернативы вращающемуся барабанному смесителю, реакционный резервуар мог бы представлять собой шнек или смеситель с лопастной мешалкой. Например, шнековая мойка с двойным шнеком типа, который используют для вымывания грязи из дробленого камня или песка, может быть модифицирована для цели использования в качестве реакционного резервуара в непрерывном процессе. Угол наклона и глубина промывного лотка могут быть отрегулированы для обеспечения достаточной глубины слоя водного раствора аммиака, и число и конфигурация перемешивающих лопастей могут быть выбраны для достижения надлежащего перемешивания и продолжительности пребывания. Лопасти будут переносить крупнозернистый уголь, тогда как угольная мелочь и загрязненная вода будут вытекать через задний водослив. Могут быть использованы два или более шнека в последовательном порядке, с выгрузкой на верхнем конце одного промывного устройства и подачей непосредственно в ванну следующего смесителя. Загрязненный раствор, который стекает из задних водосливов промывных устройств, может быть направлен по дренажной трубе в отстойник и очищен для извлечения угольной мелочи и повторно используемого раствора, как описано для компоновки вращающегося барабана. Контроллер технологического процесса может регулировать величину расхода потока в шнековые мойки,обеспечивая непрерывное обратное течение через водосток, и может направлять свежий раствор в рециркуляционную подачу, как потребуется для поддержания концентрационного диапазона. Во всех потенциальных компоновках патрубки реакционных резервуаров, а также некоторые компоненты оборудования ниже по потоку могут быть накрыты вакуумированными кожухами для улавливания паров, выделяющихся в процессе. Компоновка передвижной установки. Фиг. 2 и 3 иллюстрируют передвижную установку 100, в которой смесительный/реакционный резервуар 120 и сепаратор 130 для тяжелых частиц смонтированы на колесном трейлере 140. Баки для аммиака и воды и подводящие и выпускные трубопроводы могут быть установлены на других транспортных средствах и соединены с реакционным резервуаром и сепаратором. В этом варианте исполнения смесительный/реакционный резервуар 120 представляет собой модифицированный смеситель и очиститель, продаваемый фирмой DEL Tank and Filtration Systems под торговым наименованием TOTAL CLEAN. Он имеет V-образный смесительный бак 122 с безвальным шнеком 124 на днище для перемещения оседающих твердых веществ. Этот процесс представляет собой непрерывный процесс, в котором бак остается заполненным раствором аммиачной воды, пока уголь подвергают обработке в нем. Уголь вводят в V-образный бак через питающий шнековый транспортер 150, как показано на фиг. 3. Загрузочный бункер 152 шнекового транспортера может быть использован в качестве устройства для предварительного промывания. Как и в других компоновках, если используют предварительное промывание, вода в предварительном промывании предпочтительно является деионизированной с помощью имеющегося в продаже на рынке умягчителя воды. К деионизированной воде может быть дополнительно добавлена каустическая сода для растворения сульфатного покрытия и другого растворимого материала с поверхности угля. Питающий шнековый транспортер 150 сбрасывает уголь в заполненный аммиачной водой Vобразный бак. Вдоль бака выстроены перемешивающие лопатки 156 с приводом от смесительных двигателей 158. Лопатки перемешивают, поднимают и сбрасывают уголь в раствор. Когда более тяжелые частицы оседают на дно, они перемещаются шнеком в сторону противоположного конца бака, где имеется насос и приемный патрубок к трубопроводу 160, ведущему к сепаратору 130. Уголь захватывается в виде суспензии, которая может быть перекачана в сепаратор. Как в других вариантах исполнения, коэффициент разбавления раствора в V-образном баке поддерживают в предпочтительном диапазоне содержания от 3 до 5% аммиака в воде. Водный аммиак из внешних подсоединений, таких как барботажный бак, направляют в V-образный бак для замещения раствора, выведенного с суспензией и не полностью компенсированного обратным потоком рециркулирующего и частично истощенного водного аммиака из сепаратора. Как в первом варианте исполнения,для контроля выгрузки использованного раствора и добавления свежего аммиака для поддержания концентрационного диапазона могут быть применены датчики, дозировочный насос и клапаны, управляемые контроллером технологического процесса. Когда концентрация NH4 падает ниже целевого диапазона(т.е. ниже 3%) или объем раствора становится малым, контроллер подает дозированный объем свежего раствора для приведения всего раствора в желательный диапазон. Сепаратор 130 в этом варианте исполнения представляет собой сетчатую центрифугу корзиночного типа, такую как продаваемая фирмой Decanter Machine Inc. Первые стадии центрифугирования извлекают основную часть аммиачного раствора в качестве сбросного потока. Этот сбросный поток направляют обратно в V-образный бак, предпочтительно через отстойник, где концентрация NH4+ в растворе может быть измерена и передана в виде сигнала в контроллер технологического процесса, который контролирует течение как возвращаемого сбросного потока, так и свежего раствора в V-образный бак. Последние стадии в сетчатой центрифуге корзиночного типа имеют промывочные сопла и сетчатый сепаратор. На этой стадии может быть подведена и дренирована свежая промывочная вода. Уголь, выходящий из центрифуги, представляет собой влажные, главным образом уплотненные твердые вещества. При желании, для дополнительного извлечения влаги может быть использован пресс или другое сушильное устройство. ФОРМУЛА ИЗОБРЕТЕНИЯ 1. Способ обработки угля для удаления загрязнений, согласно которому в реакционном резервуаре из водного аммиака, имеющего концентрацию, не превышающую 19% аммиака, готовят раствор водного аммиака с концентрацией, не превышающей 10% аммиака; добавляют уголь в реакционный резервуар; перемешивают уголь в реакционном резервуаре для смешения угля и указанного раствора для обеспечения контакта раствора с поверхностями и порами угля; осуществляют мониторинг процесса, чтобы определить, когда концентрация водного аммиака в реакционном резервуаре упадет ниже указанного диапазона; подают в реакционный резервуар раствор водного аммиака с концентрацией аммиака, находящейся в указанном диапазоне или превышающей его, для возвращения концентрации раствора в пределы указанного диапазона; выгружают обработанный уголь из резервуара. 2. Способ по п.1, согласно которому в реакционном резервуаре готовят раствор водного аммиака с концентрацией от около 3 до около 5% аммиака. 3. Способ по п.1, согласно которому дополнительно выпускают загрязненный раствор, содержащий угольную мелочь, из реакционного резервуара; извлекают угольную мелочь из загрязненного раствора; осуществляют рециркуляцию раствора в реакционный резервуар,при этом указанный мониторинг выполняют посредством определения концентрации аммиака в выпускаемом растворе либо до, либо после извлечения угольной мелочи. 4. Способ по п.3, согласно которому извлеченную угольную мелочь примешивают обратно к обработанному углю. 5. Способ по п.4, согласно которому дополнительно промывают обработанный уголь и извлеченную мелочь деионизированной водой и обезвоживают промытый уголь. 6. Способ по п.5, согласно которому дополнительно собирают выходящий поток от обезвоживания и обрабатывают выходящий поток для отделения из него угольной мелочи. 7. Способ по п.1, согласно которому дополнительно отделяют от угля пиритную серу и другие более тяжелые, чем уголь, частицы с помощью гравитационного или центробежного ситового разделительного устройства. 8. Способ по п.7, согласно которому гравитационное или центробежное ситовое разделительное устройство размещают в реакционном резервуаре (18, 120). 9. Способ по п.1, согласно которому при удалении обработанного угля из реакционного резервуара удаляют уголь в суспензии угля в водном растворе аммиака, направляют суспензию в гравитационное или центробежное ситовое разделительное устройство снаружи реакционного резервуара для отделения пиритной серы и других более тяжелых, чем уголь, частиц от суспензии и выпускают суспензию для отделения угля от раствора. 10. Способ по п.9, согласно которому дополнительно осуществляют рециркуляцию раствора, вы-8 020262 пущенного из суспензии, обратно в реакционный резервуар, при этом осуществляют мониторинг концентрации аммиака в растворе, выпущенном из суспензии, чтобы определить, когда концентрация аммиака уменьшается до уровня ниже установленного диапазона. 11. Способ по п.1, согласно которому дополнительно осуществляют сушку обработанного угля, не промывая его. 12. Устройство для переработки угля для удаления загрязнений, содержащее резервуар для хранения водного аммиака, имеющего концентрацию аммиака, не превышающую 19%; реакционный резервуар, приспособленный для размещения водного раствора аммиака с концентрацией, не превышающей 10% аммиака, приготовленного из водного аммиака из резервуара для хранения,и подлежащего обработке угля и имеющий элементы для механического перемешивания, смешивающие уголь и раствор для приведения раствора в контакт с поверхностями и порами угля и выпускной патрубок для обработанного угля; систему мониторинга для определения концентрации водного аммиака в реакционном резервуаре и контроллер для подачи водного раствора аммиака из резервуара для хранения в реакционный резервуар для поддержания концентрации раствора в пределах, необходимых для удаления загрязнений. 13. Устройство по п.12, в котором указанная концентрация аммиака в растворе в реакционном резервуаре составляет 3-5%. 14. Устройство по п.12, в котором дополнительно реакционный резервуар имеет второй выпускной патрубок для выпуска загрязненного раствора, содержащего угольную мелочь, из реакционного резервуара и имеет разделительное устройство для извлечения угольной мелочи из загрязненного раствора и выпуска раствора после извлечения угля в возвратную систему для рециркуляции раствора в реакционный резервуар. 15. Устройство по п.12, в котором дополнительно реакционный резервуар и разделительное устройство смонтированы на передвижной платформе. 16. Устройство по п.12, которое содержит гравитационное или центробежное ситовое разделительное устройство для отделения от угля пиритной серы и других более тяжелых, чем уголь, частиц. 17. Устройство по п.12, которое содержит сушильное устройство (42) для сушки обработанного угля с покрытыми аммиаком поверхностями угля, не промывая его.
МПК / Метки
МПК: C10L 5/00
Метки: устройство, способ, переработки, угля
Код ссылки
<a href="https://eas.patents.su/11-20262-sposob-i-ustrojjstvo-dlya-pererabotki-uglya.html" rel="bookmark" title="База патентов Евразийского Союза">Способ и устройство для переработки угля</a>
Предыдущий патент: Игрушка (варианты)
Следующий патент: Изогнутый металлический элемент и способ его изготовления
Случайный патент: Соединения 2-алкилиндазола для лечения некоторых расстройств цнс