Способ получения жидких углеводородов из природного газа
Формула / Реферат
1. Способ получения жидких углеводородов из природного газа, включающий стадии, на которых
удаляют из природного газа соединения серы путем гидрообессеривания;
получают синтез-газ посредством реакции риформинга природного газа после гидрообессеривания паром и/или диоксидом углерода;
получают нефть Фишера-Тропша из синтез-газа путем осуществления реакции Фишера-Тропша в полученном синтез-газе;
осуществляют обогатительную реакцию гидрогенизации полученной нефти Фишера-Тропша;
проводят обогатительное газожидкостное разделение для разделения полученного гидрогенизированного продукта на газовую и жидкую фазы с целью получения жидких углеводородов;
отделяют водород для частичного отведения синтез-газа, полученного на стадии получения синтез-газа, с образованием отводной линии на этапе, предшествующем подаче на стадию получения нефти Фишера-Тропша, отделяют и получают водород высокой степени чистоты из синтез-газа, поступающего в отводную линию, и отделяют получаемый при этом остаточный газ,
где водород высокой степени чистоты, отделенный и полученный на стадии отделения водорода, полностью подают на стадию обогатительной реакции и используют в качестве водорода в обогатительной реакции вместе с содержащим водород газом, отделенным на стадии обогатительного газожидкостного разделения, с тем, чтобы концентрация водорода, подлежащего использованию в обогатительной реакции, составляла от 96,0 до 97,5 мол.%, причем содержащий водород газ, отделенный на стадии обогатительного газожидкостного разделения, подают на стадию обогатительной реакции, а также на стадию гидрообессеривания.
2. Способ по п.1, дополнительно включающий стадию конверсии, на которой осуществляют реакцию конверсии водяного газа в синтез-газе, поступающем в отводную линию, с целью увеличения концентрации водорода, причем стадию проводят до стадии отделения водорода с тем, чтобы рециркулировать остаточный газ, отделенный на стадии отделения водорода, на стадию получения синтез-газа с целью использования этого остаточного газа в качестве сырья для получения синтез-газа.
3. Способ по п.2, в котором остаточный газ, отделенный на стадии отделения водорода, содержит метан и диоксид углерода, являющиеся его основными компонентами.
4. Способ по любому из пп.1-3, в котором стадию получения синтез-газа организуют таким образом, что пар и/или диоксид углерода добавляют в соотношении H2O/C, равном 0,0-3,0, и/или в соотношении CO2/C, равном 0,0-1,0, где H2O и CO2 отражают количество молекул H2O и количество молекул CO2 соответственно и C отражает количество атомов углерода в углеводородах, источником которых являются углеводороды, подаваемые в качестве сырья.
5. Способ по любому из пп.1-4, в котором стадию получения синтез-газа организуют таким образом, что температура и давление на выходе со слоя катализатора составляют соответственно от 800 до 950°С и от 1,5 до 3,0 МПа изб., а часовая объемная скорость газа составляет от 500 до 5000 ч-1.
6. Способ по любому из пп.1-5, в котором стадию получения синтез-газа организуют таким образом, что природный газ, подаваемый в качестве сырья, содержит углеводороды с длиной цепи от 1 до 6 атомов углерода, его основным компонентом является метан.
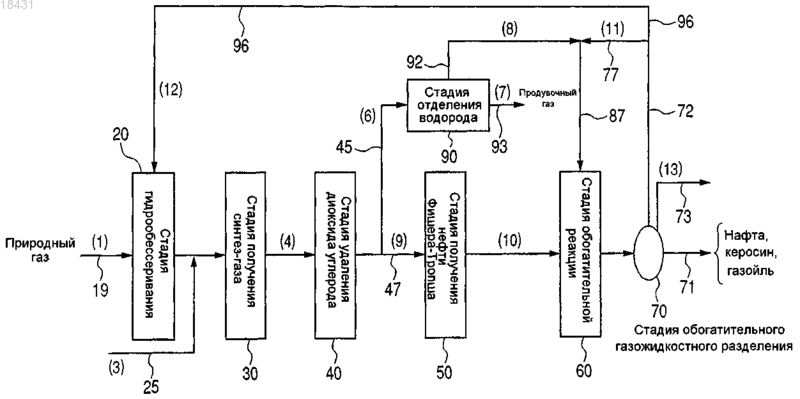
Текст
СПОСОБ ПОЛУЧЕНИЯ ЖИДКИХ УГЛЕВОДОРОДОВ ИЗ ПРИРОДНОГО ГАЗА В так называемом способе GTL для получения жидких углеводородов, которые содержат топливную нефть, путем получения из природного газа синтез-газа, последующего получения из полученного синтез-газа нефти Фишера-Тропша посредством синтеза Фишера-Тропша и обогащения полученной нефти Фишера-Тропша синтез-газ, полученный на стадии получения синтез-газа, частично отводят на этапе, предшествующем подаче на стадию получения нефти Фишера-Тропша, и отделяют от синтез-газа, поступающего в отводную линию, водород высокой степени чистоты. Весь отделенный водород высокой степени чистоты подают на стадию обогатительной реакции, где он расходуется в обогатительной реакции в качестве водорода. Кроме того, в синтез-газе, поступающем в отводную линию, осуществляют реакцию конверсии водяного газа с целью увеличения концентрации водорода перед стадией разделения и получения водорода высокой степени чистоты; остаточный газ, оставшийся после разделения, может быть рециркулирован на стадию получения синтез-газа в качестве сырья для получения синтез-газа.(71)(73) Заявитель и патентовладелец: ДЖЭПЭН ОЙЛ, ГЭЗ ЭНД МЕТАЛЗ НЭШНЛ КОРПОРЕЙШН; ИНПЕКС КОРПОРЕЙШН; ДжейЭкс НИППОН ОЙЛ ЭНД ЭНЕРДЖИ КОРПОРЕЙШН; ДЖАПАН ПЕТРОЛЕУМ ЭКСПЛОРЕЙШН КО., ЛТД.; КОСМО ОЙЛ КО., ЛТД.; НИППОН СТИЛ ИНДЖИНИРИНГ КО., ЛТД.; ТИЙОДА КОРПОРЕЙШН Область техники, к которой относится изобретение Настоящее изобретение относится к так называемому способу GTL (gas to liquids - перевод газовой фазы в жидкости) получения жидких углеводородов, которые содержат топливную нефть, из природного газа. Уровень техники Так называемый способ GTL для получения жидких углеводородов, которые содержат топливную нефть, из природного газа описан, например, в документе WO 2007/114274 A1. Фиг. 3 прилагаемых чертежей представляет собой схематическое пояснение последовательности технологических операций такого известного способа GTL. Показанный на фиг. 3 способ GTL включает стадию 120 гидрообессеривания для удаления соединений серы из природного газа; стадию 130 получения синтез-газа посредством реакции риформинга природного газа паром и/или диоксидом углерода; стадию 140 извлечения диоксида углерода, осуществляемую при необходимости; стадию 150 получения нефти по Фишеру-Тропшу для получения нефти Фишера-Тропша из синтез-газа посредством синтеза Фишера-Тропша (FT); стадию 160 обогатительной реакции гидрогенизации полученной нефти Фишера-Тропша; стадию 170 обогатительного газожидкостного разделения, заключающуюся в осуществлении разделения гидрогенизированного продукта, полученного на стадии обогатительной реакции, на газовую и жидкую фазы с целью получения жидких углеводородов, вышеназванные стадии располагаются последовательно от стороны подачи природного газа(сторона впуска) или левой части фиг. 3. Синтез-газ, полученный на стадии 130 получения синтез-газа, частично отводят на этапе, предшествующем подаче на стадию 150 получения нефти по Фишеру-Тропшу, при этом образуется отводная линия 145; синтез-газ в отводной линии 145 разделяют на водород высокой степени чистоты (линия 192) и продувочный газ (линия 191) на стадии 190 отделения водорода обычно с использованием способа PSA(pressure swing adsorption - короткая безнагревная адсорбция). Отделенный водород высокой степени чистоты частично соединяют, посредством линий 192 и 197, с водородом в линии рециркуляции 177, где водород циркулирует со стадии 170 обогатительного газожидкостного разделения на стадию 160 обогатительной реакции, тогда как оставшуюся часть подают по линии 196 на стадию гидрообессеривания. С другой стороны, продувочный газ, выходящий по линии 191, обычно используют в качестве топлива. В описанном выше известном способе концентрация водорода, подаваемого на стадию 160 обогатительной реакции, составляет примерно 92 мол.%. Если бы удалось увеличить концентрацию водорода,подаваемого на стадию 160 обогатительной реакции, относительно известного уровня техники, можно было бы снизить давление, необходимое для осуществления реакции гидрогенизации на стадии 160 обогатительной реакции, с соответствующим уменьшением эксплуатационных затрат. Кроме того, повышается эффективность реакции, что делает возможным уменьшение размера реактора стадии 160 обогатительной реакции. Кроме того, эта стадия может быть осуществлена при более низкой температуре реакции с целью сдерживания деактивации и повышения срока службы катализатора. Поскольку продувочный газ 191, отводимый со стадии 190 отделения водорода, содержит непрореагировавший метан, можно было бы достичь значительного усовершенствования в отношении потребления сырья на единицу продукта с соответствующим экономическим эффектом, если бы снова вводить его в процесс и повторно использовать в качестве сырья. Однако в настоящее время нет известного способа решения указанной проблемы осуществления реалистичного процесса обработки такого продувочного газа. Сущность изобретения Ввиду указанных выше обстоятельств, целью настоящего изобретения является предоставление способа, позволяющего снизить эксплуатационные затраты на стадии обогатительной реакции, уменьшить размер реакторов стадии 160 обогатительной реакции, а также снова ввести в процесс продувочный газ, отводимый со стадии отделения водорода процесса GTL получения жидких углеводородов из природного газа, чтобы повторно использовать его в качестве сырья и, тем самым, достигнуть преимуществ с точки зрения потребления сырья на единицу продукта. В соответствии с настоящим изобретением указанная цель достигается путем обеспечения способа получения жидких углеводородов из природного газа, включающего стадию гидрообессеривания для удаления из природного газа соединений серы путем гидрообессеривания; стадию получения синтез-газа для получения синтез-газа посредством реакции риформинга природного газа после гидрообессеривания паром и/или диоксидом углерода; стадию получения нефти Фишера-Тропша для получения нефти Фишера-Тропша из синтез-газа путем осуществления реакции Фишера-Тропша в синтез-газе, полученном на стадии получения синтез-газа; стадию обогатительной реакции гидрогенизации нефти ФишераТропша, полученной на стадии получения нефти Фишера-Тропша; стадию обогатительного газожидкостного разделения для разделения гидрогенизированного продукта, полученного на стадии обогатительной реакции, на газовую и жидкую фазы с целью получения жидких углеводородов; стадию отделения водорода для частичного отведения синтез-газа, полученного на стадии получения синтез-газа, с образованием отводной линии на этапе, предшествующем подаче на стадию получения нефти Фишера-Тропша,отделения и получения водорода высокой степени чистоты из синтез-газа, поступающего в отводную линию, и отделения попутно получаемого остаточного газа, где водород высокой степени чистоты, отделенный и полученный на стадии отделения водорода, полностью подается на стадию обогатительной реакции и используется в качестве водорода в обогатительной реакции. В способе получения жидких углеводородов из природного газа, определение которому дано выше,предпочтительно водород высокой степени чистоты, отделенный на стадии отделения водорода, и содержащий водород газ, отделенный на стадии обогатительного газожидкостного разделения, используются в качестве водорода в обогатительной реакции с тем, чтобы концентрация водорода, подлежащего использованию в обогатительной реакции, составляла 96,0-97,5 мол.%. В способе получения жидких углеводородов из природного газа, определение которому дано выше,предпочтительно содержащий водород газ, отделенный на стадии обогатительного газожидкостного разделения, подают на стадию обогатительной реакции, а также на стадию гидрообессеривания. Способ получения жидких углеводородов из природного газа, определение которому дано выше,предпочтительно дополнительно включает стадию конверсии для осуществления реакции конверсии водяного газа в синтез-газе, поступающем в отводную линию, с целью увеличения концентрации водорода, котора предусматривается до стадии отделения водорода с тем, чтобы рециркулировать остаточный газ (продувочный газ), отделенный на стадии отделения водорода, на стадию получения синтез-газа с целью использования этого остаточного газа в качестве сырья для получения синтез-газа. В способе получения жидких углеводородов из природного газа, определение которому дано выше,предпочтительно остаточный газ (продувочный газ), отделенный на стадии отделения водорода, содержит метан и диоксид углерода, являющиеся его основными компонентами. В способе получения жидких углеводородов из природного газа, определение которому дано выше,предпочтительно стадия получения синтез-газа организована таким образом, что пар и/или диоксид углерода добавляют в соотношении H2O/C, равном 0,0-3,0, или в соотношении CO2/C, равном 0,0-1,0, гдеH2O и CO2 отражают количество молекул H2O и количество молекул CO2 соответственно и C отражает количество атомов углерода в углеводородах, источником которых являются углеводороды, подаваемые в качестве сырья. В способе получения жидких углеводородов из природного газа, определение которому дано выше,предпочтительно стадия получения синтез-газа организована таким образом, что температура и давление на выходе слоя катализатора составляют соответственно от 800 до 950C и от 1,5 до 3,0 МПа изб., а часовая объемная скорость газа составляет от 500 до 5000 ч-1. В способе получения жидких углеводородов из природного газа, определение которому дано выше,предпочтительно стадия получения синтез-газа организована таким образом, что природный газ, подаваемый в качестве сырья, содержит углеводороды с длиной цепи от 1 до 6 атомов углерода, его основным компонентом является метан. Таким образом, в соответствии с настоящим изобретением предусматривается стадия отделения водорода, на которой синтез-газ, полученный на стадии получения синтез-газа, частично отводят с образованием отводной линии на этапе, предшествующем подаче на стадию получения нефти Фишера-Тропша,с целью отделения от синтез-газа, поступающего в отводную линию, водорода с высокой степенью чистоты, и весь водород высокой степени чистоты, отделенный на стадии отделения водорода, подают на стадию обогатительной реакции и используют в качестве водорода в обогатительной реакции. Таким образом, можно сократить эксплуатационные затраты на стадии обогатительной реакции и уменьшить размеры реакторов стадии обогатительной реакции. Кроме того, в соответствии с настоящим изобретением предусматривается стадия конверсии, предшествующая стадии отделения водорода и предназначенная для увеличения концентрации водорода путем осуществления в синтез-газе реакции конверсии водяного газа. Затем остаточный газ (продувочный газ), отделенный на стадии отделения водорода, возвращают на стадию получения синтез-газа с целью его использования в качестве сырья для получения синтез-газа. Следовательно, преимущество в отношении потребления сырья на единицу продукта может быть достигнуто благодаря направлению продувочного газа, поступающего со стадии отделения водорода, который обычно используют в качестве топлива,снова в данный процесс и его повторному использованию в качестве сырья. Краткое описание чертежей На фиг. 1 представлена схема способа получения жидких углеводородов из природного газа в соответствии с первым вариантом осуществления настоящего изобретения. На фиг. 2 представлена схема способа получения жидких углеводородов из природного газа в соответствии со вторым вариантом осуществления настоящего изобретения. На фиг. 3 представлена схема способа получения жидких углеводородов из природного газа в соответствии с известным уровнем техники. Описание предпочтительного варианта осуществления изобретения Далее настоящее изобретение описано более подробно в отношении вариантов его осуществления. Первый вариант осуществления изобретения. На фиг. 1 представлена схема способа получения жидких углеводородов из природного газа в соответствии с первым вариантом осуществления настоящего изобретения. Способ получения жидких углеводородов из природного газа в соответствии с первым вариантом осуществления настоящего изобретения в своей основе включает стадию 20 гидрообессеривания для удаления соединений серы из природного газа путем гидрообессеривания, стадию 30 получения синтезгаза для получения синтез-газа посредством реакции риформинга природного газа паром и/или диоксидом углерода, стадию 40 удаления диоксида углерода, которую осуществляют при необходимости, стадию 50 получения нефти Фишера-Тропша для получения нефти Фишера-Тропша из синтез-газа путем осуществления в синтез-газе реакции Фишера-Тропша, стадию 60 обогатительной реакции путем гидрогенизации полученной нефти Фишера-Тропша и стадию 70 обогатительного газожидкостного разделения для разделения полученного гидрогенизированного продукта на газовую и жидкую фазы с целью получения жидких углеводородов, вышеназванные стадии располагаются последовательно от стороны подачи природного газа (сторона линии 19) или левой части фиг. 1. Несмотря на то что стадия 60 обогатительной реакции и стадия 70 обогатительного газожидкостного разделения на фиг. 1 показаны как отдельные стадии, они могут быть объединены в одну стадию, не разделенную на две отдельные стадии. В таком случае эту стадию называют просто "обогатительная стадия". Как показано на фиг. 1, из синтез-газа, полученного на стадии 30 получения синтез-газа, при необходимости удаляют диоксид углерода, затем на этапе до подачи на стадию 50 получения нефти ФишераТропша отводят часть синтез-газа по отводной линии 45, синтез-газ, отведенный по отводной линии 45,подают на стадию 90 отделения водорода. На стадии 90 отделения водорода водород высокой степени чистоты отделяют от образующегося при этом остаточного газа. Весь полученный на стадии 90 отделения водорода водород высокой степени чистоты затем подают на стадию 60 обогатительной реакции по линии 92 и линии 87. С другой стороны,остаточный газ (продувочный газ), отделенный стадии 90 отделения водорода, отводят и используют обычно в качестве топлива. Поясняемый на фиг. 1 способ получения жидких углеводородов из природного газа, соответствующий настоящему изобретению, отличается тем, что синтез-газ, полученный на стадии 30 получения синтез-газа, частично отводят на этапе до подачи на стадию 50 получения нефти Фишера-Тропша с образованием отводной линии 45; синтез-газ, отведенный по отводной линии 45, подают на стадию 90 отделения водорода с целью разделения и получения водорода высокой степени чистоты и остаточного газа; весь полученный водород высокой степени чистоты подают на стадию 60 обогатительной реакции. Содержащий водород газ, отделенный и направленный в линию 72 со стадии 70 обогатительного газожидкостного разделения, частично поступает в линию 77 и соединяется с потоком водорода высокой степени чистоты со стадии 90 отделения водорода до его подачи на стадию 60 обогатительной реакции по линии 87, тогда как оставшаяся часть содержащего водород газа направляется на стадию 20 гидрообессеривания по линии 96. Далее подробно описывается каждая стадия способа получения жидких углеводородов из природного газа в соответствии с настоящим изобретением.A. Стадия 20 гидрообессеривания. Стадия гидрообессеривания, на фиг. 1 обозначенная номером 20, представляет собой стадию гидроочистки природного газа, подаваемого в качестве сырья по линии 19, от соединений серы. Содержащий водород газ, отделенный на стадии 70 обогатительного газожидкостного разделения,частично подают по линиям 72 и 96 на стадию гидрообессеривания в качестве источника водорода для осуществления гидрообессеривания.B. Стадия 30 получения синтез-газа. Стадия 30 получения синтез-газа представляет собой стадию получения синтез-газа (CO и H2) посредством реакции риформинга природного газа, подаваемого в качестве сырья, паром и/или диоксидом углерода. Другими словами, это стадия получения синтез-газа, содержащего в качестве основных компонентов CO и H2, путем риформинга природного газа, являющегося сырьем и содержащего в качестве основного компонента метан, паром (H2O) и/или диоксидом углерода (CO2) в присутствии катализатора получения синтез-газа. Пар (H2O) и/или диоксид углерода (CO2) подают по линии 25. Если природный газ, подаваемый в качестве сырья, уже содержит диоксид углерода (CO2), по линии 25 может подаваться только пар (H2O). Соотношение подаваемых на стадию 30 получения синтез-газа пара и/или диоксида углерода регулируют так, чтобы они поступали в соотношении H2O/C, равном 0,0-3,0, и/или в соотношении CO2/C,равном 0,0-1,0 (в обоих случаях отношение количества молекул/атомов), где H2O и CO2 отражают количество молекул Н 2 О и количество молекул CO2 соответственно и C отражает количество атомов углерода в углеводородах, источником которых являются углеводороды, подаваемые в качестве сырья. Отношение H2O/C предпочтительно составляет от 0,3 до 1,7, более предпочтительно от 0,7 до 1,3. С другой стороны, отношение CO2/C предпочтительно составляет от 0,2 до 0,8, более предпочтительно от 0,4 до 0,6. На стадии 30 получения синтез-газа настоящего изобретения обычно температура на выходе со слоя катализатора составляет предпочтительно от 800 до 950C, более предпочтительно от 850 до 920C,тогда как давление на выходе со слоя катализатора составляет предпочтительно от 1,5 до 3,0 МПа изб. Часовая объемная скорость газа составляет предпочтительно от 500 до 5000 ч-1. Катализатор получения синтез-газа. Катализатор получения синтез-газа снабжен носителем, который играет роль материала-основы,носитель несет на себе каталитически активный металл. В качестве носителя предпочтительно используется формованный массив кальцинированного оксида магния. Такой формованный массив получают путем смешивания порошкообразного оксида магния со смазочным веществом, литья полученной смеси под давлением в форму определенного очертания и последующего кальцинирования формованного массива. Хотя формованный массив может иметь любую форму без ограничений, предпочтительно он имеет очертания, подходящие для промышленного катализатора, например, является кольцеобразным или седлообразным, имеет множество отверстий или представляет собой гранулы. Формованный массив, который играет роль носителя, предпочтительно обладает удельной площадью поверхности от 0,1 до 1,0 м 2/г, более предпочтительно от 0,2 до 0,5 м 2/г при определении методом Брунауэра, Эммета, Теллера (БЭТ). Если удельная площадь поверхности превышает 1,0 м 2/г, имеется тенденция к увеличению скорости образования углерода, следствием чего является такой недостаток, как снижение каталитической активности. Если удельная площадь поверхности менее 0,1 м 2/г, каталитическая активность на единицу катализатора настолько мала, что проявляется такой недостаток, как необходимость использовать большое количество катализатора. Как правило, получение необходимой удельной площади поверхности носителя регулируют, подбирая температуру кальцинирования и время кальцинирования. Оксид магния (MgO), используемый в качестве носителя, может быть получен путем кальцинирования выпускаемого серийно оксида магния (MgO). Необходимо, чтобы степень чистоты оксида магния(MgO) составляла не менее 98 вес.%, предпочтительно не менее 99 вес.%. Загрязнение компонентами,ускоряющими осаждение углерода, или компонентами, разлагающимися при высокой температуре и в атмосфере восстановительного газа, такими как железо, никель и подобные им металлы и диоксид кремния (SiO2), является особенно нежелательным. Рутений (Ru), выступающий в качестве каталитически активного металла, наносят на носитель в количестве, лежащем в диапазоне от 10 до 5000 вес.част./млн, предпочтительно от 100 до 2000 вес.част./млн, выраженном как эквивалентное количество металла (весовое отношение к носителю катализатора). Количество Ru более 5000 вес.част./млн нежелательно, так как это увеличивает стоимость катализатора и из-за того, что в ходе получения проявляется тенденция к осаждению углерода. Слишком малое количество Ru, менее 10 вес.част./млн, не обеспечивает удовлетворительной каталитической активности. В целях настоящего изобретения рутений (Ru) может быть заменен на родий (Rh). Далее в качестве примера описан предпочтительный способ приготовления катализатора синтезгаза.(1) Формование носителя катализатора. Порошкообразный оксид магния (MgO) смешивают со смазочным веществом, которое обычно может представлять собой углерод, и отливают под давлением с целью придания заданных очертаний. Затем отформованный продукт кальцинируют при температуре не ниже 1000C, предпочтительно от 1150 до 1300C, более предпочтительно от 1150 до 1250C в течение от 1 до 4 ч, обычно на воздухе. Хотя активность обычного катализатора риформинга зависит от типа катализатора, она в значительной степени пропорциональна площади его наружной поверхности. Следовательно, каталитическая активность увеличивается, когда размер частиц катализатора уменьшается, однако в то же время увеличивается гидравлическое сопротивление, так как высока массовая скорость газа. По этой причине широко применяется катализатор цилиндрической формы.(2) Нанесение каталитически активного металла (Ru). Рутений (Ru) может быть нанесен на наружную поверхность формованного оксида магния путем пропитки формованного носителя водным раствором, содержащим соль рутения, и его последующей сушки и кальцинирования. Способы, пригодные для осуществления пропитки формованного носителя водным раствором, содержащим соль рутения, включают способ погружения и способ распыления, из которых способ распыления, заключающийся в атомизации водного раствора, содержащего соль рутения, и его распылении на носитель, может быть предпочтительно использован в целях настоящего изобретения. В качестве соли рутения могут быть использованы хлорид рутения или нитрат рутения. Носитель, на который нанесен Ru, затем сушат при температуре от 50 до 150C в течение от 1 до 4 ч, после чего кальцинируют при температуре от 150 до 500C, предпочтительно от 350 до 450C в течение от 1 до 4 ч. Сушка и кальцинирование могут быть осуществлены в воздушной атмосфере. Реакционную активность каталитически активного металла дополнительно увеличивают путем кальцинирования. Получение синтез-газа. Синтез-газ, содержащий в качестве основных компонентов CO и H2, получают в результате риформинга H2O и/или CO2, который проводят в присутствии катализатора получения синтез-газа, подготовленного, как описано выше, используя смесь газов, содержащую природный газ (углеводороды с длиной цепи от 1 до 6 атомов углерода, как правило, основным компонентом является метан), пар и/или диоксид углерода, подаваемые по линии 25, водород и углеводороды с длиной цепи от 1 до 6 атомов углерода, в качестве основного компонента содержащие метан, циркулирующие по линии 96. Допустим, что метан является основным компонентом подаваемого сырья.(а) Когда метан (CH4) вступает в реакцию с диоксидом углерода (CO2) (риформинг CO2), происходящая реакция может быть представлена уравнением (1)(b) Когда метан (СН 4) вступает в реакцию с паром (H2O) (паровой риформинг), происходящая реакция может быть представлена уравнением (2)(с) В условиях реакции риформинга реакция конверсии водяного газа, отображаемая приведенным ниже уравнением (3), происходит одновременно с реакциями по уравнениям (1) и (2), приведенным выше, так как катализатор активен в отношении реакции конверсии В соответствии со стехиометрией приведенных выше уравнений (1) и (2) при риформинге метанаCO2 и паровом риформинге метана образуется синтез-газ с молярным отношением H2/CO=1 и синтез-газ с молярным отношением H2/CO=3 соответственно. Таким образом, теперь возможно непосредственно производить синтез-газ с молярным отношением H2/CO=2, что подходит для синтеза FT, путем объединения этих реакций без необходимости разделения газов с целью отделения водорода от образующегося газа. Однако в условиях реакции, соответствующих непосредственному производству синтез-газа с таким молярным отношением, образующийся газ, как правило, имеет состав, способствующий отложению углерода на поверхности катализатора, из-за отложения углерода происходит деактивация катализатора. Следовательно, в качестве катализатора, позволяющего решить эту проблему, используют описанный выше катализатор получения синтез-газа.C. Стадия 40 удаления диоксида углерода. Это стадия удаления газообразного диоксида углерода из синтез-газа. Например, удаление газообразного диоксида углерода осуществляют посредством жидкого абсорбента, такого как амин, и последующей десорбции газообразного диоксида углерода из жидкого абсорбента, содержащего газообразный диоксид углерода, с целью регенерации жидкого абсорбента. Однако стадия 40 удаления диоксида углерода не является обязательной и может не предусматриваться в обязательном порядке.D. Стадия 50 получения нефти Фишера-Тропша (стадия FT синтеза). В описанном выше синтез-газе проводят реакцию Фишера-Тропша, газообразный продукт отделяют от продукта реакции и получают нефть Фишера-Тропша. Реакция синтеза FT представляет собой реакцию получения смеси углеводородов из CO и H2 синтез-газа в соответствии с уравнением К каталитически активным металлам, которые могут быть использованы для проведения указанной реакции, относятся железо (Fe), кобальт (Co), рутений (Ru) и никель (Ni) в металлическом состоянии. Если нужно, эти каталитически активные металлы могут быть нанесены на носитель, такой как оксид кремния, оксид алюминия, алюмосиликат или оксид титана. Условия реакции, как правило, следующие: температура реакции: от 200 до 350C, давление реакции: от атмосферного давления до примерно 4,0 МПа изб. Если используется железный катализатор, условия реакции предпочтительно следующие: температура реакции: от 250 до 350C, давление реакции: от примерно 2,0 до 4,0 МПа изб. Если используется кобальтовый катализатор, условия реакции предпочтительно следующие: температура реакции: от 220 до 250C, давление реакции: от примерно 0,5 до 4,0 МПа изб. Эта реакция относится к типу реакций полимеризации. В целом, трудно поддерживать степень полимеризации (n) постоянной, и продукты реакции располагаются в широком диапазоне от C1 до C100+. Следовательно, распределение количества атомов углерода в образующихся углеводородах соответствует закону распределения Шульца-Флори и может быть выражено как вероятность роста цепиэтого закона распределения. В случае промышленного катализатора величинасоставляет примерно от 0,85 до 0,95. В ходе реакции FT образуются преимущественно -олефины, которые вступают в следующие вторичные реакции. А именно, к вторичным реакциям относятся гидрогенизация, приводящая к образованию парафинов с прямой углеродной цепью, гидрокрекинг, приводящий к образованию низших парафинов, таких как метан, и реакции вторичного роста цепи, приводящие к образованию высших углеводородов. В качестве побочных продуктов в небольших количествах образуется спирт, такой как этанол, кетоны, такие как ацетон, и карбоновые кислоты, такие как уксусная кислота. К реакторам, которые могут быть использованы для осуществления синтеза FT, относятся реакторы с неподвижным слоем катализатора, реакторы с псевдоожиженным слоем катализатора, реакторы с суспендированным слоем катализатора и надкритические реакторы. Поскольку операции очистки, такие как удаление пыли и обессеривание, для защиты катализатора осуществляют на стадии получения синтез-газа, используемого в синтезе FT в качестве сырья, получаемые углеводороды не содержат ни серы, ни тяжелых металлов и, следовательно, являются очень чистыми. Углеводороды, производимые посредством синтеза FT, состоят, главным образом, из олефинов с прямой цепью (1-олефин) и нормальных парафинов. Средство разделения, которое может быть использовано для отделения газообразного продукта от продуктов реакции Фишера-Тропша с целью получения нефти Фишера-Тропша (жидких нефтепродуктов), не имеет каких-либо определенных ограничений и может быть подобрано среди различных известных средств разделения. В качестве одного из примеров можно привести испаритель мгновенного вскипания.E. Стадия 60 обогатительной реакции. Нефть Фишера-Тропша, полученную на стадии 50 получения нефти Фишера-Тропша, затем подвергают гидрогенизации (каталитической гидрогенизации). Хотя гидрогенизация не имеет каких-либо определенных ограничений, для осуществления гидрогенизации большей частью применяют реактор с неподвижным слоем катализатора. Условия гидрогенизации обычно следующие: температура реакции: примерно от 175 до 400C, парциальное давление водорода: от 1 до 25 МПа изб. (от 10 до 250 атм). Для гидрогенизации используют водород высокой степени чистоты, получаемый на стадии 90 отделения водорода (и подаваемый по линиям 92 и 87), и водород, отделяемый на стадии 70 обогатительного газожидкостного разделения (и подаваемый по линиям 72, 77 и 8), которые будут описаны далее. Отметим, что линия 92 и линия 77, показанные на фиг. 1, соединяются друг с другом и образуют линию 87, по которой водород поступает на стадию 60 обогатительной реакции. Поток водорода, содержащий газ, отделенный на стадии 70 обогатительного газожидкостного разделения и выходящий в линию 72, разветвляется в линии 77 и 96.F. Стадия 70 обогатительного газожидкостного разделения. Являющиеся продуктами углеводороды 71, такие как нафта, керосин и газойль, и газообразные вещества, в качестве основного компонента содержащие водород, отделяют друг от друга на стадии 70 обогатительного газожидкостного разделения. Как описано выше, газообразные вещества, в качестве основного компонента содержащие водород, рециркулируют по линиям 72, 77 и 87 и используют на стадии 60 обогатительной реакции, по линии 73 газообразные вещества частично выбрасываются в виде продувочного газа.G. Стадия 90 отделения водорода. Синтез-газ, полученный на стадии 30 получения синтез-газа и прошедший стадию 40 удаления диоксида углерода, частично отводят из основной линии по отводной линии 45 на этапе, предшествующем подаче на стадию 50 получения нефти по Фишеру-Тропшу. Затем, как показано на фиг. 1, поток отводной линии 45 поступает на стадию 90 отделения водорода. Основная линия после ответвления обозначена номером 47. На стадии 90 отделения водорода получают водород 92 высокой степени чистоты и попутно образующийся остаточный газ 93, отделяемые друг от друга. Остаточный газ 93 содержит в качестве основных компонентов метан и монооксид углерода, а также водород, оставшийся неотделенным. Как правило, остаточный газ 93 используют как топливо. На стадии 90 отделения водорода предпочтительно применяют устройство короткой безнагревной адсорбции (PSA) водорода. В устройстве PSA водорода имеются адсорбенты (адсорбенты на основе цеолитов, активированный уголь, оксид алюминия, силикагель и т.д.), которыми заполнено множество адсорбционных колонн, расположенных параллельно и предназначенных для отделения газообразного водорода высокой степени чистоты (например, не менее 98%) от синтез-газа путем последовательного и многократного осуществления в каждой адсорбционной колонне стадий повышения давления, адсорбции, десорбции (сбрасывания давления) и продувки водорода. Отделенный газообразный водород высокой степени чистоты может быть отведен по линии 92. Однако стадия 90 отделения водорода не ограничивается использованием описанного выше способа PSA водорода, в качестве альтернативы может быть применен способ адсорбции водорода сплавом-аккумулятором, способ мембранного разделения или любое их сочетание. Расход, с которым синтез-газ подают в отводную линию 45, определяют в соответствии с расходом водорода на стадии 60 обогатительной реакции и стадии 20 гидрообессеривания. В первом варианте осуществления изобретения, поясняемом фиг. 1, весь водород высокой степени чистоты, отделенный на стадии 90 отделения водорода, подают на стадию 60 обогатительной реакции,где он расходуется в ходе обогатительной реакции, благодаря чему эксплуатационные затраты на осуществление стадии обогатительной реакции могут быть снижены, а размер реакторов стадии обогатительной реакции уменьшен. Кроме того, срок службы катализатора может быть увеличен в результате уменьшения температуры реакции. Второй вариант осуществления изобретения. На фиг. 2 представлена схема способа получения жидких углеводородов из природного газа в соответствии со вторым вариантом осуществления настоящего изобретения. Второй вариант осуществления изобретения, показанный на фиг. 2, отличается от первого варианта осуществления изобретения, показанного на фиг. 1, по пп. (1) и (2), приведенным ниже.(1) Как показано на фиг. 2, между отводной линией 45 и стадией 90 отделения водорода имеется стадия 80 конверсии, предназначенная для увеличения концентрации водорода посредством стадии конверсии водяного газа, на которой синтез-газ, поступающий по отводной линии, подвергают реакции конверсии водяного газа.(2) Как показано на фиг. 2, остаточный газ, отделенный на стадии 90 отделения водорода, рециркулируют на стадию 30 получения синтез-газа по линии 95, он расходуется как сырье для получения синтез-газа. Далее описывается стадия 80 конверсии, показанная на фиг. 2. Н. Стадия 80 конверсии. Синтез-газ, полученный на стадии 30 получения синтез-газа и прошедший стадию 40 удаления диоксида углерода, частично отводят из основной линии по отводной линии 45 на этапе, предшествующем подаче на стадию 50 получения нефти по Фишеру-Тропшу. Основная линия после ответвления обозначена номером 47. Как показано на фиг. 2, поток отводной линии 45 поступает на стадию 80 конверсии. Концентрация водорода в синтез-газе, поступающем из отводной линии 45, увеличивается в результате реакции конверсии водяного газа на стадии 80 конверсии. Более конкретно, CO, являющийся одним из компонентов синтез-газа, вступает в реакцию с паром, как видно из приведенного ниже уравнения реакции (реакции конверсии водяного газа), с образованием H2 и CO2, в результате чего концентрация водорода увеличивается: Синтез-газ, концентрация водорода в котором увеличена на стадии 80 конверсии, направляют на стадию 90 отделения водорода по линии 81. На стадии 90 отделения водорода в результате отделения водорода и попутного образования остаточного газа получают водород высокой степени чистоты. Весь водород высокой степени чистоты, отделенный и полученный на стадии 90 отделения водорода, подают на стадию 60 обогатительной реакции по линии 92 и линии 87. С другой стороны, остаточный газ, отделенный на стадии 90 отделения водорода, выводят по линии 95 и рециркулируют на стадию 30 получения синтез-газа, где он расходуется в качестве сырья для получения синтез-газа. Остаточный газ в качестве основных компонентов содержит метан и диоксид углерода, а также оставшийся неотделенным водород. Во втором варианте осуществления изобретения, поясняемом фиг. 2, синтез-газ, поступающий в отводную линию 45, подвергают реакции конверсии водяного газа с целью увеличения в нем концентрации водорода перед его подачей на стадию отделения водорода, а остаточный газ (продувочный газ), отделенный на стадии отделения водорода, рециркулируют на стадию получения синтез-газа, где он расходуется в качестве сырья для получения синтез-газа. Таким образом, второй вариант осуществления изобретения обеспечивает преимущество, достигаемое благодаря направлению выходящего со стадии отделения водорода продувочного газа, обычно используемого в качестве топлива, снова в данный процесс и его повторному использованию в качестве сырья, в результате, в дополнение к преимуществам описанного выше первого варианта осуществления изобретения процесс усовершенствуется с точки зрения потребления сырья на единицу продукта. Далее настоящее изобретение более подробно описано на примерах. Пример 1. Синтез-газ с H2/CO=2,0, который пригоден для синтеза FT (Фишера-Тропша) жидких углеводородов, произвели из природного газа посредством осуществления стадий, показанных на фиг. 1. В качестве катализатора получения синтез-газа использовали катализатор, представляющий собойRu, нанесенный на носитель из MgO. Условия реакции на стадии 30 получения синтез-газа были следующими: температура на выходе со слоя катализатора: 900C, давление на выходе со слоя катализатора: 2,0 МПа изб, часовая объемная скорость газа: 2000 ч-1, H2O/С=0,94, CO2/С=0,37 (H2O: количество молекул H2O; CO2: количество молекулCO2; C: количество атомов углерода в углеводородах, источником которых являются углеводороды, подаваемые в качестве сырья). Состав природного газа: C1/C2/C3/C4/C5/C6+/CO2/N2 = 64,0/2,9/1,7/0,9/0,3/0,1/30,0/0,1 (молярное отношение). Определили и зафиксировали материальный баланс между входом на стадию получения синтез-газа и выходом со стадии обогатительной реакции, как показано на фиг. 1, и произвели оценку стадии получения синтез-газа способа получения жидких углеводородов из природного газа на основании материального баланса. Материальный баланс определили путем вычислений на основе составов, наблюдаемых в точках, обозначенных на фиг. 1 номерами (1)-(13). В результате, концентрация водорода в содержащем водород газе, подаваемом на стадию обогатительной реакции, составила 97%, что соответствует улучшению примерно на 4,6% относительно концентрации 92,4%, имеющей место в известном уровне техники. Таким образом, на стадии обогатительной реакции увеличивается активность гидрогенизации, что делает возможным уменьшение количества катализатора примерно на 10% по сравнению с вариантом известного уровня техники, показанным на фиг. 3. Если количество катализатора в известном уровне техники для данного процесса задано, можно уменьшить температуру реакции примерно на 3C, таким образом, срок службы катализатора можно увеличить примерно на 25%. Пример 2. Синтез-газ с H2/CO=2,0, который пригоден для синтеза FT (Фишера-Тропша) жидких углеводородов, произвели из природного газа посредством осуществления стадий, показанных на фиг. 2. В качестве катализатора получения синтез-газа использовали катализатор, представляющий собойRu, нанесенный на носитель из MgO. Условия реакции на стадии 30 получения синтез-газа были следующими: температура на выходе со слоя катализатора: 900C, давление на выходе со слоя катализатора: 2,0 МПа изб, часовая объемная скорость газа: 2000 ч-1, H2O/C=1,03, CO2/C=0,38 (отношение количеств молекул/атомов; C: количество атомов углерода в углеводородах, источником которых являются углеводороды, подаваемые в качестве сырья). Состав природного газа: C1/C2/C3/C4/C5/C6+/CO2/N2 = 64,0/2,9/1,7/0,9/0,3/0,1/30,0/0,1 (молярное отношение). Определили и зафиксировали материальный баланс между входом на стадию получения синтез-газа и выходом со стадии обогатительной реакции, как показано на фиг. 2, и произвели оценку стадии получения синтез-газа способа получения жидких углеводородов из природного газа на основании материального баланса. Материальный баланс определили путем вычислений на основе составов, наблюдаемых в точках, обозначенных на фиг. 2 номерами (1)-(13). В результате, помимо преимущества, заключающегося в увеличении концентрации водорода на стадии обогатительной реакции примера 1, способ настоящего изобретения, включающий стадию рециркуляции остаточного газа, обеспечил получение равной 64,9% степени преобразования атомов углерода,являющегося сырьем природного газа, в жидкие углеводороды, являющиеся продуктами (керосин, газойль, нафта), что является усовершенствованием относительно значения 60,8% варианта известного уровня техники, показанного на фиг. 3. Кроме того, в соответствии с настоящим изобретением расход подаваемого в качестве сырья природного газа был уменьшен на 6,8% относительно расхода в обычном процессе (или способе известного уровня техники, показанном на фиг. 3). Как описано выше, в соответствии с настоящим изобретением весь водород высокой степени чистоты, отделенный и полученный на стадии отделения водорода, подается на стадию обогатительной реакции и расходуется в качестве водорода в этой обогатительной реакции, что делает возможным сокращение эксплуатационных затрат на стадии обогатительной реакции и уменьшение размеров реакторов стадии обогатительной реакции. Кроме того, можно достичь усовершенствования с точки зрения потребления сырья на единицу продукции, если в качестве стадии, предшествующей стадии отделения водорода, предусматривается стадия конверсии с тем, чтобы осуществить в синтез-газе реакцию конверсии водяного газа с целью увеличения концентрации водорода, а остаточный газ (продувочный газ), отделенный на стадии отделения водорода, рециркулируется на стадию получения синтез-газа с целью его использования в качестве сырья для получения синтез-газа, так как продувочный газ, обычно используемый в качестве топлива, может быть снова направлен в процесс и повторно использован в качестве сырья. Промышленная применимость Таким образом, в соответствии с настоящим изобретением природный газ может быть химически преобразован и использован в способе GTL (перевод газовой фазы в жидкости) для получения жидких углеводородов. Заявкой на данное изобретение испрашивается приоритет заявки на патент Японии 2008-089592,поданной 31 марта 2008 г., содержание которой во всей полноте включено в настоящий документ посредством ссылки. ФОРМУЛА ИЗОБРЕТЕНИЯ 1. Способ получения жидких углеводородов из природного газа, включающий стадии, на которых удаляют из природного газа соединения серы путем гидрообессеривания; получают синтез-газ посредством реакции риформинга природного газа после гидрообессеривания паром и/или диоксидом углерода; получают нефть Фишера-Тропша из синтез-газа путем осуществления реакции Фишера-Тропша в полученном синтез-газе; осуществляют обогатительную реакцию гидрогенизации полученной нефти Фишера-Тропша; проводят обогатительное газожидкостное разделение для разделения полученного гидрогенизированного продукта на газовую и жидкую фазы с целью получения жидких углеводородов; отделяют водород для частичного отведения синтез-газа, полученного на стадии получения синтезгаза, с образованием отводной линии на этапе, предшествующем подаче на стадию получения нефти Фишера-Тропша, отделяют и получают водород высокой степени чистоты из синтез-газа, поступающего в отводную линию, и отделяют получаемый при этом остаточный газ,где водород высокой степени чистоты, отделенный и полученный на стадии отделения водорода,полностью подают на стадию обогатительной реакции и используют в качестве водорода в обогатительной реакции вместе с содержащим водород газом, отделенным на стадии обогатительного газожидкостногоразделения, с тем, чтобы концентрация водорода, подлежащего использованию в обогатительной реакции, составляла от 96,0 до 97,5 мол.%, причем содержащий водород газ, отделенный на стадии обогатительного газожидкостного разделения, подают на стадию обогатительной реакции, а также на стадию гидрообессеривания. 2. Способ по п.1, дополнительно включающий стадию конверсии, на которой осуществляют реакцию конверсии водяного газа в синтез-газе, поступающем в отводную линию, с целью увеличения концентрации водорода, причем стадию проводят до стадии отделения водорода с тем, чтобы рециркулировать остаточный газ, отделенный на стадии отделения водорода, на стадию получения синтез-газа с целью использования этого остаточного газа в качестве сырья для получения синтез-газа. 3. Способ по п.2, в котором остаточный газ, отделенный на стадии отделения водорода, содержит метан и диоксид углерода, являющиеся его основными компонентами. 4. Способ по любому из пп.1-3, в котором стадию получения синтез-газа организуют таким образом, что пар и/или диоксид углерода добавляют в соотношении H2O/C, равном 0,0-3,0, и/или в соотношении CO2/C, равном 0,0-1,0, где H2O и CO2 отражают количество молекул H2O и количество молекул CO2 соответственно и C отражает количество атомов углерода в углеводородах, источником которых являются углеводороды, подаваемые в качестве сырья. 5. Способ по любому из пп.1-4, в котором стадию получения синтез-газа организуют таким образом, что температура и давление на выходе со слоя катализатора составляют соответственно от 800 до 950 С и от 1,5 до 3,0 МПа изб., а часовая объемная скорость газа составляет от 500 до 5000 ч-1. 6. Способ по любому из пп.1-5, в котором стадию получения синтез-газа организуют таким образом, что природный газ, подаваемый в качестве сырья, содержит углеводороды с длиной цепи от 1 до 6 атомов углерода, его основным компонентом является метан.
МПК / Метки
МПК: C01B 3/38, C10G 2/00, B01J 23/46, C10L 3/10, C01B 3/48, C01B 3/56, C10G 49/00
Метки: природного, способ, газа, жидких, углеводородов, получения
Код ссылки
<a href="https://eas.patents.su/11-18431-sposob-polucheniya-zhidkih-uglevodorodov-iz-prirodnogo-gaza.html" rel="bookmark" title="База патентов Евразийского Союза">Способ получения жидких углеводородов из природного газа</a>
Предыдущий патент: Трехфазная эмульсия (варианты), способы ее приготовления и нанесения
Следующий патент: Колпачок (варианты) и контейнер (варианты)
Случайный патент: Устройство и способ для заполнения структур с различными полыми пространствами