Способ и устройство нанесения покрытия на трубы
Формула / Реферат
1. Способ нанесения покрытия на трубу (2; 30) или участок трубы в виде слоя по меньшей мере одного полимера, согласно которому
наносят на наружную поверхность трубы (2; 30) или участка трубы, имеющей или имеющего наружную поверхность, определяющую периферию трубы или участка трубы, слой по меньшей мере одного полимерного материала в виде расплава с помощью экструзионной головки, установленной на каретке (1, 15а, 15b; 36), выполненной с возможностью перемещения вдоль периферии трубы (2) или участка трубы; и
перемещают каретку (1, 15а, 15b; 36) вдоль по меньшей мере части периферии в процессе нанесения полимерного материала с целью формирования слоя на поверхности трубы (2; 30) или участка трубы,
отличающийся тем, что согласно способу дополнительно выравнивают полимерный материал, наносимый с помощью экструзионной головки (3), посредством выравнивающего средства (5; 38), установленного на каретке (1, 15а, 15b; 36).
2. Способ по п.1, в соответствии с которым указанная экструзионная головка представляет собой щелевую экструзионную головку (3), которая установлена на каретке (1, 15а, 15b) и соединена с источником (4) расплавленного полимерного материала.
3. Способ по п.1 или 2, в котором щелевая экструзионная головка (3) имеет ширину, по существу, соответствующую заранее определенной ширине указанного слоя.
4. Способ по п.1 или 2, отличающийся тем, что каретку (1, 15а, 15b; 36) перемещают по меньшей мере на 180°, предпочтительно на 360° или более вдоль периферии трубы (2; 30) или участка трубы для нанесения полимерного слоя, покрывающего наружную поверхность вдоль периферии.
5. Способ по п.4, отличающийся тем, что каретку (1, 15а, 15b; 36) перемещают по спиралеобразной траектории вдоль периферии трубы (2; 30) или участка трубы для нанесения полимерного слоя, когда каждый последующий слой частично накладывается на предыдущий слой.
6. Способ по пп.1, 2, 5, отличающийся тем, что на поверхность наносится полимерный слой, содержащий по меньшей мере две наложенные друг на друга пленки, при этом каждая из полимерных пленок имеет толщину в пределах от 0,01 до 10 мм, предпочтительно от 0,5 до 5 мм и, в частности, от 0,1 до 3 мм.
7. Способ по пп.1, 2, 5, отличающийся тем, что полимерный материал выравнивают с помощью выравнивающего средства (5; 38), прилагающего силу, по существу, перпендикулярно полимерному материалу для разглаживания полимерного слоя по наружной поверхности трубы (2; 30) или участка трубы.
8. Способ по пп.1, 2, 5, отличающийся тем, что полимерный материал выравнивается роликом (5; 38) или ножом.
9. Способ по п.7, отличающийся тем, что полимерный материал выравнивается роликом (5; 38), имеющим эластичную поверхность, имеющим твердость от 10 до 30 по Шору А.
10. Способ по п.7, отличающийся тем, что полимерная пленка извлекается из щелевой экструзионной головки (3) на выравнивающее средство (5) и переносится с выравнивающего средства (5) на наружную поверхность трубы (2) или участка трубы, при этом выравнивающее средство (5) разглаживает и выравнивает пленку и одновременно переносит ее на поверхность.
11. Способ по любому из пп.1, 2, 5, 9, 10, отличающийся тем, что каретку (1, 15а, 15b; 36) перемещают с регулируемой скоростью, при этом полимерный материал экструдируется из вышеуказанной щелевой экструзионной головки (3), по существу, при постоянной скорости экструзии, и толщина пленки контролируется путем регулирования скорости движущейся каретки (1, 15а, 15b).
12. Способ по любому из пп.1, 2, 5, 9, 10, отличающийся тем, что полимерный материал наносят на поверхность стальной трубы (2; 30) с полимерным покрытием, содержащей, по меньшей мере, частично непокрытый участок трубы.
13. Способ по п.12, отличающийся тем, что кольцевой сварной шов и примыкающие части непокрытой стальной трубы, включая примыкающие концы полимерного покрытия, покрывают с целью герметизации кольцевого сварного шва от воздействия воздуха, влажности и воды.
14. Способ по любому из пп.1, 2, 5, 7, 9, 10, отличающийся тем, что трубу (2; 30) или участок трубы покрывают по меньшей мере одним термопластичным полимером, выбираемым из группы, включающей полиолефины, в частности полиэтилен и полипропилен, включая автономные полиолефины и замещенные полиолефины.
15. Способ по п.14, отличающийся тем, что автономный полиолефин содержит адгезионно-поддерживающие группы, выбранные из группы акрилатов, карбоновых кислот и аминов.
16. Способ по любому из пп.1, 2, 5, 7, 9, 10, 15, отличающийся тем, что наружную поверхность трубы (2; 30) или участка трубы перед покрытием нагревают до температуры в пределах от 80 до 300°С.
17. Способ по п.16, отличающийся тем, что поверхность нагревают с помощью нагревательного устройства, установленного на каретке.
18. Способ по любому из пп.1, 2, 5, 7, 9, 10, 15, 17, в котором наружную поверхность трубы (2; 30) или участка трубы покрывают грунтующим агентом до достижения модифицированной поверхности с целью улучшения прилипания полимерного слоя к поверхности.
19. Способ по п.18, отличающийся тем, что грунтующий агент выбирают из группы, включающей композиции с однокомпонентной жидкой эпоксидной смолой, композиции с двухкомпонентной жидкой эпоксидной смолой, порошковых эпоксидных распылителей и кремнийорганики.
20. Способ соединения труб, в частности стальных труб с полиолефиновым покрытием, отличающийся тем, что
концы двух стальных труб с покрытием подгоняют друг к другу;
стальные трубы приваривают друг к другу с образованием соединения и
соединение покрывают по меньшей мере одним слоем материала, способного герметизировать соединение от воздействия воздуха и влажности,
характеризующийся нанесением на соединение покрытия с использованием способа по любому из пп.1-19.
21. Устройство для нанесения покрытия на трубу (2; 30) или участок трубы, имеющую или имеющий наружную поверхность, определяющую периферию трубы или участка трубы, содержащее
подвижную каретку (1, 15а, 15b; 36), выполненную с возможностью перемещения вокруг периферии трубы (2; 30) или участка трубы;
экструзионную головку (3), соединенную с источником (4; 32) полимерного расплава для образования полимерной пленки и установленную на подвижной каретке (1, 15а, 15b; 36); и
выравнивающие средства (5; 38), выполненные с возможностью выравнивания и разглаживания полимерной пленки по наружной поверхности трубы (2; 30) или участка трубы и установленные на подвижной каретке (1, 15а, 15b; 36).
22. Устройство по п.21, отличающееся тем, что каретка (1, 15а, 15b; 36) способна перемещаться по меньшей мере на 360° вдоль периферии трубы (2; 30) или участка трубы для нанесения полимерного слоя, покрывающего наружную поверхность вдоль периферии.
23. Устройство по п.21 или 22, отличающееся тем, что экструзионная головка (3; 36) соединена с источником расплавленного полимерного материала (4; 32), выбранного из группы экструдеров, нагревательных шнековых смесителей или контейнеров для промежуточного хранения.
24. Устройство по п.23, отличающееся тем, что контейнеры для промежуточного хранения (4) выполнены с возможностью опорожнения с помощью прочищающих устройств, приводимых в действие гидравлическим, пневматическим или электрическим способами.
25. Устройство по любому из пп.21, 22, 24, отличающееся тем, что выравнивающее средство (5; 38) выбирают из группы роликов и ножей, прилагающих силу, по существу, перпендикулярно полимерному материалу для разглаживания полимерного слоя по наружной поверхности трубы (2; 30) или участка трубы.
26. Устройство по п.25, отличающееся тем, что поверхность ролика (5; 38) имеет твердость от 10 до 30 по Шору А.
27. Устройство по любому из пп.21, 22, 24, 26, отличающееся тем, что экструзионную головку (3; 36) приспосабливают для образования полимерной пленки на выравнивающем средстве (5; 38), и выравнивающее средство способно переносить полимерную пленку на наружную поверхность трубы (2; 30) или участок трубы.
28. Устройство по любому из пп.21, 22, 24, 26, отличающееся тем, что каретка (1, 15а, 15b; 36) содержит нагревательное устройство, расположенное перед выравнивающим средством в направлении поступательного движения каретки.
29. Устройство по любому из пп.21, 22, 24, 26, отличающееся тем, что каретку (1, 15а, 15b) закрепляют на трубе или участке трубы с помощью по меньшей мере одной тяговой цепи (14), которую обматывают вокруг трубы (2) или участка трубы.
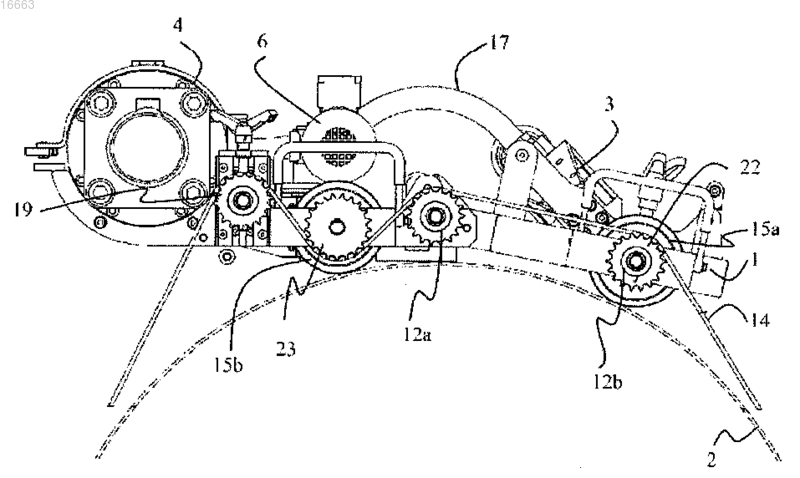
Текст
СПОСОБ И УСТРОЙСТВО НАНЕСЕНИЯ ПОКРЫТИЯ НА ТРУБЫ Способ и устройство для покрытия трубы (2) или участка трубы слоем по меньшей мере одного полимера. Способ состоит из подготовки наружной поверхности трубы (2) или участка трубы,определяющей периферию трубы или участка трубы; нанесения на наружную поверхность трубы или участка трубы слоя по меньшей мере одного полимерного материала в стадии расплава с помощью форсунки (3), которая установлена на каретке, способной перемещаться вдоль периферии трубы (2) или участка трубы; и перемещения каретки вдоль по меньшей мере части периферии в процессе нанесения полимерного материала с целью образования слоя на поверхности трубы(2) или участка трубы. Настоящее изобретение особенно полезно для покрытия монтажных соединений трубопроводов.(71)(73) Заявитель и патентовладелец: ОИ КВХ ПАЙП АБ; БОРЕАЛИС ТЕКНОЛОДЖИ ОЙ (FI) 016663 Изобретение относится к способу нанесения покрытия на трубу или участок трубы в соответствии с преамбулой п.1 формулы изобретения. В соответствии с этим способом слой по меньшей мере одного полимерного материала наносят на поверхность трубы или участка трубы по меньшей мере вдоль части внешней поверхности трубы или участка трубы. Кроме того, настоящее изобретение относится к устройству в соответствии с п.33 формулы изобретения для нанесения полимерного покрытия на поверхность трубы. Стальные трубы, покрытые слоями полимеров, таких как полиэтилен или полипропилен, в течение длительного времени используют в нефте- и газопроводах. Трубы этих типов являются механически прочными и имеют хорошую коррозионную стойкость вдоль участков с нанесенным покрытием. При формировании трубопровода трубы как правило соединяют способом дуговой сварки под флюсом. На заводе-изготовителе, где на поверхность трубы наносят полимерное покрытие, участки с обоих концов трубы обычно оставляют без покрытия с целью облегчения соединения труб сваркой в полевых условиях. Сварные соединения, выполненые в полевых условиях, являются уязвимыми для коррозии, поэтому на кольцевой сварной шов и на околошовные непокрытые участки необходимо наносить покрытие, чтобы полностью покрыть сварное соединение и защитить его от воздействия окружающей среды (влажности и воды). Из уровня техники известно несколько способов нанесения защитного покрытия на сварные соединения, выполняемые в полевых условиях. Традиционно, сварные соединения покрывают полиэтиленовой пленкой (усадочная оболочка), которая может быть обернута с усадкой вокруг соединения для покрытия сварного шва. Этот способ применяют примерно в 65% случаев нанесения защитного покрытия сварных соединений в полевых условиях, когда используются стальные трубы с полиэтиленовым покрытием. Еще один вариант предусматривает нанесение на кольцевой сварной шов покрытия из уретана или эпоксидных смол. Такие покрытия наносят на трубу распылением с использованием распылителя. К другим вариантам относятся машинная обмотка, лента, расплавляемая на поверхности, ручная обмотка и инжекционное прессование. Некоторые из перечисленных способов нанесения покрытий дают хорошие результаты, но их трудно, а иногда и невозможно применять в полевых условиях, а некоторые не обеспечивают надежной защиты от коррозии. Задачей настоящего изобретения является устранение по крайней мере части проблем, относящихся к известному уровню техники, а также обеспечение нового способа покрытия труб. Другая задача настоящего изобретения состоит в обеспечении устройства нового типа нанесенияпокрытия на трубы. Настоящее изобретение основывается на идее нанесения по меньшей мере одного полимерного материала в форме расплавленной пленки или листа на поверхность трубы или участка трубы из движущейся экструзионной головки или форсунки. В частности, расплав полимерной пленки или листа наносят на трубу из экструзионной головки, установленной на каретке, которая может перемещаться вдоль периферии трубы или участка трубы. В соответствии с настоящим изобретением устройство содержит подвижную каретку, способную перемещаться вдоль периферии трубы или участка трубы; и щелевую экструзионную головку, соединенную с источником полимерного расплава и установленную на подвижной каретке для нанесения слоя полимера в форме расплава на поверхность трубы или участка трубы. Кроме того, устройство содержит, в комбинации с вышеуказанными характеристиками, выравнивающее средство для выравнивания слоя полимера в форме расплава на поверхности трубы или участка трубы. Точнее, настоящий способ главным образом характеризуется тем, что сформулировано в описательной части п.1 формулы изобретения. Устройство в соответствии с настоящим изобретением характеризуется тем, что сформулировано в описательной части п.33 формулы изобретения. Благодаря использованию настоящего изобретения можно добиться значительных преимуществ. В частности, настоящий способ и устройство в соответствии с настоящим изобретением могут применяться для покрытия монтажных соединений трубопроводов, а также для других случаев применения покрытий,когда слой полимерного материала необходимо наносить на поверхность трубы или подобного субстрата. Следовательно, настоящее изобретение может также применяться для восстановления различных полимерных покрытий. Устройство является легким по весу и удобным для использования в полевых условиях. Оборудование, описанное ниже, может перевозиться на тягаче с прицепом и перемещаться с помощью вертикального погрузчика, при этом все оборудование размещается в прицепе. С помощью вертикального погрузчика можно также перемещать от одного соединения к другому тент для защиты зоны выполнения покрытия, экструзионной головки и каретки. Охлаждение, по существу, не требуется, но может осуществляться посредством нагнетания воздуха или с помощью влажной ткани. Участок с покрытием при необходимости может быть легко восстановлен с помощью портативного сварочного аппа-1 016663 рата. Важно знать, что с применением настоящего способа и устройства покрытие сварного соединения в полевых условиях получается таким же, что и в заводских условиях, и это с учетом любой погоды. Настоящее изобретение может применяться для покрытия участков труб или целых труб. Кроме того, оно может применяться для покрытия участка, окружающего сварное или иным способом выполненное соединение между двумя трубами, как будет рассмотрено ниже. Далее изобретение будет рассмотрено более подробно с помощью детального описания и со ссылкой на прилагаемые чертежи. Фиг. 1 демонстрирует вид сбоку конструкции устройства для нанесения покрытия в соответствии с одним вариантом осуществления изобретения, где движущаяся экструзионная головка расположена на каретке, имеющей промежуточную емкость для полимерного расплава; фиг. 2 демонстрирует вид в перспективе того же варианта осуществления изобретения; и фиг. 3 а - 3 с демонстрируют процесс экструдирования полимерной пленки на поверхность с помощью одного варианта осуществления настоящего изобретения, где расплав полимерной пленки экструдируется на поверхность трубы с использованием движущейся головки, подсоединенной непосредственно к экструдеру. В соответствии с настоящим изобретением способ покрытия трубы или участка трубы полимерным слоем, по существу, содержит комбинацию следующих стадий: подготовка наружной поверхности трубы или участка трубы, определяющей периферию трубы или участка трубы; нанесение на поверхность трубы или участка трубы слоя по меньшей мере одного полимерного материала в расплавленном состоянии с помощью форсунки или экструзионной головки, установленной на каретке, способной перемещаться вдоль периферии трубы или участка трубы; и перемещение каретки вдоль по меньшей мере части периферии для нанесения материала на по меньшей мере часть трубы или участка трубы. В соответствии с вариантом осуществления настоящего изобретения предусматривается способ нанесения полимерного слоя, имеющего заранее определенную ширину, когда материал наносится на поверхность трубы или участка трубы с помощью щелевой экструзионной головки, имеющей ширину зазора щели, по существу соответствующую заранее определенной ширине слоя. На практике расплав полимерной пленки, нанесенной на поверхность трубы или участка трубы,требует выравнивания после нанесения. Путем выравнивания полимерного материала можно в некоторой степени регулировать толщину слоя, чтобы она соответствовала заранее выбранной толщине покрытия. Важно знать, что путем выравнивания удаляются любые воздушные полости между полимерным слоем и покрываемой поверхностью, и покрытие получается плотным и герметичным. Выравнивание может выполняться вручную или с использованием отдельного инструмента. Однако в соответствии с предпочтительным вариантом осуществления изобретения подвижная каретка снабжена выравнивающим средством, которое будет подробно рассмотрено ниже. В соответствии с предпочтительным вариантом осуществления изобретения каретка перемещается вдоль периферии трубы или участка трубы на расстояние, по существу соответствующее заранее выбранной длине полимерного покрытия. Предпочтительно иметь ход каретки по меньшей мере 180 и в частности 360 вдоль периферии трубы или участка трубы, чтобы обеспечить покрытие полимерным слоем половины или всей наружной поверхности вдоль периферии. Один из вариантов осуществления изобретения предусматривает нанесение нескольких последовательных оберточных полимерных слоев,например, путем перемещения каретки по спиралеобразной траектории вдоль периферии трубы или участка трубы. В этом случае достигается особое преимущество засчет того, что каждый последующий слой частично накладывается на предыдущий, тем самым усиливая герметизирующие свойства покрытия. Для обеспечения спиралеобразной траектории трубу можно перемещать по оси в процессе покрытия. Полимерная пленка может быть любых желаемых размеров, но обычно она имеет толщину в пределах от 0,01 до 10 мм, предпочтительно от 0,1 до 7 мм и, в частности, от 0,5 до 5 мм. Ширина пленки может быть от 1 до 1500 мм, предпочтительно от 5 до 1250 мм и, в частности, от 10 до 1000 мм. Длина предпочтительно должна составлять от % периферии до 20-кратного значения периферии, хотя ограничений нет. Например, для покрытия монтажного соединения/сварного шва обычно бывает достаточно от 1 до 10 последовательных слоев полимерной пленки, частично наложенных друг на друга. Покрытие может содержать пленку только из одного полимерного материала, а может иметь многослойную структуру, то есть состоять из пленок из двух или более полимерных материалов. По меньшей мере одна из пленок может быть вспененным полимером. Обычно поверхностный слой (скин-слой) покрытия является слоем из твердого полимера. Как уже указывалось выше, полимерный материал наносится в форме расплава пленки. Пленка предпочтительно образуется с помощью "экструзионной форсунки" или "экструзионной головки", которая может преобразовывать расплав полимерного материала в полимерную пленку, имеющую ширину,по существу, соответствующую заранее выбранной ширине слоя покрытия. Может использоваться любая-2 016663 экструзионная головка, например щелевая экструзионная головка, способная образовывать расплав пленки или листа из применяемого полимерного материала; при этом она может называться "экструзионной форсункой" или "экструзионной головкой". Иными словами, вышеуказанные термины применимы для обозначения любой головки или форсунки, способной образовывать пленку из подаваемого полимерного расплава. Разумеется, могут также использоваться экструзионные головки или форсунки для многослойной пленки. Согласно известному уровню техники в поперечном разрезе канал потока на входе щелевой экструзионной головки обычно является кругом или прямоугольником с маленьким коэффициентом пропорциональности. В экструзионной головке это исходное поперечное сечение постепенно преобразуется в прямоугольник с большим коэффициентом пропорциональности, требуемый для листовой экструзии. Геометрия канала в щелевой экструзионной головке спроектирована так, чтобы обеспечивать равномерную скорость на выходе экструзионной головки. Экструзионная головка подсоединена по меньшей мере к одному источнику расплава полимерного материала. Этот источник обычно выбирается из группы экструдеров, нагревательных шнековых смесителей и контейнеров для хранения. Для производства многослойной пленки можно подсоединить экструзионную головку к двум или более источникам полимерного материала. Одним из типичных источников полимерного расплава является традиционный экструдер, в котором исходный материал, содержащий полимерные гранулы, нагревается, а затем подается в экструзионное устройство с помощью подающего шнека. Можно соединить головку с экструдером, чтобы обеспечить прямую подачу полимерного расплава в экструзионную головку. Экструдер может быть заменен на нагревательный шнековый смеситель, который можно наполнять полимерными гранулами и в котором полимер может расплавляться. Такой шнековый смеситель может устанавливаться на каретке. Вместо прямой подачи нагретый полимерный расплав может храниться в промежуточной стадии на каретке. Это промежуточное хранение может осуществляться посредством, например, цилиндра, наполненного расплавленной полимерной массой, из которого она может выпрессовываться через экструзионную головку на трубу. Цилиндр нагревается и/или имеет хорошую изоляцию, и он может быть установленным на той же раме, что и экструзионная головка. Цилиндр может нагреваться с помощью нагревателей электрического сопротивления, расположенных рядом с цилиндром. Для опорожнения контейнера промежуточного хранения он предпочтительно должен быть снабжен поршнем, приводимым в действие гидравликой, пневматикой (т.е. любым устройством давления) или электричеством. Вместо поршня может применяться шнек винтового транспортера. В соответствии с одним предпочтительным вариантом осуществления изобретения контейнер промежуточного хранения может быть заменяемым, как картридж, что облегчает замену полимера в процессе работы. Толщина полимерного покрытия может контролироваться путем регулирования толщины полимерной пленки, экструдированной из экструзионной головки. Расстояние между кромками (толщина зазора) обычно составляет от 0,1 до 50 мм, предпочтительно от 1 до 10 мм и, в частности, от 1,5 до 5 мм. Кроме того, возможно, путем использования каретки, способной перемещаться с регулируемой скоростью, контролировать толщину пленки, экструдированной из форсунки, посредством скорости каретки. В этом случае полимерный материал обычно экструдируется из щелевой экструзионной головки при, по существу, постоянной скорости экструзии. Разумеется, может использоваться комбинация двух вышеуказанных альтернатив. Скорость каретки может свободно регулироваться. Обычно в зависимости от толщины пленки и потребления полимерного материала скорость находится в пределах от 0,01 до 20 м/мин, например от 0,1 до 5 м/мин и, в частности, от 0,3 до 2 м/мин. Кроме того, на толщину полимерного слоя и прилипание слоя к трубе или участку трубы влияет выравнивающее средство, используемое для разглаживания и выравнивания полимерного слоя, нанесенного на поверхность. Обычно выравнивающее средство прилагает силу перпендикулярно полимерному материалу. Этим выравнивающим средством может быть, например, ролик или нож. В одном из вариантов осуществления изобретения ролик имеет центральную ось и эластичную поверхность. Эта поверхность регулируется по направлению к центральной оси, чтобы соответствовать профилю поверхности трубы или участка трубы в той части, которая подлежит покрытию. С этой целью ролик может содержать цельный ролик/цилиндр или несколько цилиндрических частей одинаковых или даже различных диаметров. Эластичная поверхность может быть обеспечена использованием силиконовых или каучукоподобных материалов. Обычно твердость эластичной поверхности составляет от 10 до 30 по Шору А. Выравнивающее устройство в форме ножа может быть неэластичным или эластичным, предпочтительно эластичным. Обычно предпочтительно, чтобы поверхность выравнивающего устройства могла следовать по верхней поверхности трубы или участка трубы так, чтобы она плотно разглаживала полимерный слой по поверхности. Кроме того, поверхность выравнивающего устройства должна быть адаптированной к адгезионным свойствам полимерного расплава, чтобы с легкостью происходило отделение материала. В соответствии с одним особенно предпочтительным вариантом осуществления изобретения, уже-3 016663 указанным выше, выравнивающее устройство устанавливается на той же подвижной каретке, что и экструзионная форсунка/щелевая экструзионная головка. Этот вариант осуществления изобретения предусматривает экструдирование пленки из щелевой экструзионной головки на выравнивающее средство и перенос с выравнивающего средства на наружную поверхность трубы или участка трубы. В этом случае выравнивающее средство действует как аппликатор, который разглаживает и выравнивает пленку и одновременно переносит ее на поверхность трубы или участка трубы. Кроме того, возможно нанесение полимерной пленки на наружную поверхность трубы непосредственно из щелевой экструзионной головки, например, путем бесконтактного покрытия (покрытия наливом), когда плоское выравнивающее средство используется для разглаживания полимерного слоя, нанесенного на поверхность. В предпочтительном варианте осуществления изобретения полимерный материал наносят на поверхность стальной трубы с полимерным покрытием, содержащей участок без покрытия. Участок трубы может содержать кольцевой сварной шов между двумя примыкающими трубами, которые приварены друг к другу. Кольцевой сварной шов и примыкающие участки непокрытой стальной трубы, включая примыкающие концы полимерного покрытия, покрываются с целью герметизации кольцевого сварного шва от воздействия воздуха, влажности и воды. К другим случаям применения настоящего способа относятся восстановление полимерных покрытий, покрытие, по существу, любых полимерных труб, а также труб из материалов, отличных от полимеров и металлов. В соответствии с предпочтительным вариантом осуществления изобретения подвижная каретка может направляться для движения вокруг периферии трубы или участка трубы с помощью закрепляющих и направляющих приспособлений. Ниже приведены примеры таких приспособлений; это могут быть цепи для фрикционной передачи, а также различные ремни и провода. Разумеется, каретку можно и вручную прижимать к трубе и перемещать вдоль периферии. Во всех вышеуказанных случаях применения труба или участок трубы покрывается по меньшей мере одним термопластичным полимером, например, выбранным из группы полиолефинов (в частности,полиэтиленом и полипропиленом) и модифицированных полиолефинов. К классу особенно интересных полимеров относятся автономные полиолефины, раскрытые более подробно в нашей родственной заявке на патент ЕР 06010822, под названием "Структура, содержащая слой полиолефинов, или профиль с улучшенной адгезией", внесенной в реестр 26.05.2006, содержание которой прилагается к настоящей заявке по ссылке. Такие полиолефины содержат усиливающие адгезию группы; в частности, полярные группы, например, выбранные из группы акрилатов, к которым относятся метилакрилаты, метилметакрилаты, пропилакрилаты, бутилакрилаты, а также карбоновые кислоты, такие как малеиновая кислота, и амины. Полиолефины с усиливающими адгезию группами, предпочтительно полярными группами, могут приготавливаться путем сополимеризации олефиновых мономеров с сомономерными соединениями,содержащими такие группы, или путем прививки, т.е. пересадки соответствующих соединений на полиолефиновую основную цепь после синтеза полиолефина. Если сополимеризация применяется для производства полиолефинов с усливающими адгезию группами, то предпочтительно, чтобы производился полярный сополимер, содержащий сополимер этилена с одним или более сомономеров, выбранных из С 1- по С 6-алкилакрилатов С 1- по С 6-алкилметакрилатов, гидроксифункциональных мономеров, ангидридфункциональных мономеров, например, 2-гидроксиэтил(мет)акрилат, акриловые кислоты, метакриловые кислоты, винилацетаты и винилсиланы. Например, полярный сополимер может также быть тройным сополимером этилена, одним из вышеуказанных мономеров и винилсиланом. Сополимер может также содержать иономерные структуры (как, например, в типах Surlyn DuPont). Если прививка применяется для получения полиолефина с усиливающими адгезию группами, то в качестве прививающего агента может использоваться любой такой агент, о котором известно, что он пригоден для этой цели специалисту в данной области техники. Предпочтительно, кислотопрививающим агентом может быть ненасыщенная карбоновая кислота или ее производные, такие как ангидриды, эфиры и соли (как металлические, так и неметаллические). Предпочтительно, чтобы ненасыщенная группа была в соединении с карбоновой группой. Среди примеров таких прививающих агентов виниловые силаны, акриловая кислота, метакриловая кислота,фумаровая кислота, малеиновая кислота, надиновая кислота, цитраконовая кислота, итаконовая кислота,кротоновая кислота и их ангидриды, соли металлов, 5 эфиров, амиды или имиды. Предпочтительными прививающими агентами являются малеиновая кислота и ее производные, такие как ангидрид малеиновой кислоты; особенно предпочтителен ангидрид малеиновой кислоты. Прививка может выполняться путем любого процесса в соответствии с известным уровнем техники, например, прививка в расплаве без растворителя, или в растворе, или в дисперсии, или в псевдоожиженном слое. Предпочтительно, чтобы прививка выполнялась в нагретом экструдере или миксере, как описано в US 3236917, US 4639495, US 4950541 или US 5194509. Содержание этих документов прилагается к настоящей заявке по ссылке. Предпочтительно, чтобы прививка выполнялась в двухшнековом экструдере, описанном в US 15 4950541.-4 016663 Прививка может выполняться в присутствии или отсутствии радикального катализатора, но предпочтительно, чтобы она выполнялась в присутствии радикального катализатора, такого как органическая перекись, органический перэфир или органический гидропероксид. Как указано выше, предпочтительно, чтобы полярные группы в полиолефине выбирались из акрилатов, например, метилакрилатов, метилметакрилатов, пропилакрилатов, бутилакрилатов, карбоновых кислот, таких как малеиновая кислота, и аминов. Базовая смола состоит либо из полиолефина одного типа, либо из смеси полиолефинов двух или более типов. Предпочтительно, чтобы полиолефин базовой смолы состоял из этилен гомо- или сополимера и/или пропилен гомо- или сополимера, или из их смеси. Концентрация адгезионно-поддерживающих групп в полиолефине обычно составляет от 0,01 до 5,0 мол.%, предпочтительно от 0,02 до 1,0 мол.%, с расчетом из общего количества олефиновых мономеров в полиолефиной композиции. Способы, рассмотренные выше, предпочтительно должны выполняться с предварительным нагревом наружной поверхности трубы или участка трубы. Путем нагрева поверхности может достигаться лучшее прилипание пленки к наружной поверхности. Температура выбирается в зависимости от свойств полимера и времени нагрева. По существу, нет необходимости нагревать поверхность до температуры плавления полимера. Предпочтительно, чтобы перед покрытием поверхность трубы нагревалась до температуры в пределах от 80 до 300 С. Нагрев может выполняться вручную. В соответствии с предпочтительным вариантом осуществления изобретения нагрев поверхности происходит с помощью нагревательного устройства, установленного на каретке. Это нагревательное устройство предпочтительно устанавливается перед выравнивающим средством и экструзионной головкой в направлении поступательного движения каретки. Перед покрытием можно модифицировать поверхность трубы или участка трубы путем нанесения на нее грунтующего агента с целью улучшения прилипания полимерного слоя к поверхности. Разумеется, поверхность предпочтительно должна очищаться перед любой обработкой. Очистка может выполняться путем дробе- или пескоструйной обработки. Некоторые варианты осуществления настоящего изобретения будут более подробно описаны ниже с помощью прилагаемых чертежей, иллюстрирующих применение настоящего изобретения для покрытия соединений, сваренных в полевых условиях. На фиг. 1 и 2 используются следующие числовые обозначения: 1 - рама; 2 - труба; 3 - форсунка в сборе; 4 - подающий цилиндр; 5 - выравнивающий ролик; 6 - электродвигатель; 12 а, 12b - стопорное кольцо для вала; 14 - цепь; 15 а, 15b - колесики; 16 - натяжитель цепи; 22, 23 - звездочки цепной передачи; 27 - нагнетательный шланг. Как показано на фиг. 1 и 2, настоящее подвижное устройство для нанесения покрытия содержит раму 1, установленную на двух комплектах колесиков 15 для перемещения по поверхности трубы 2. Каретка 1, 15 а, 15b закреплена на трубе 2 с помощью по меньшей мере одной цепи 14. В варианте осуществления изобретения в соответствии с чертежом представлены две цепи, обмотанные вокруг трубы и имеющие длину большую, чем окружность трубы 2. Тяговая цепь 14 входит в зацепление со звездочками цепной передачи 22, 23 на раме, по меньшей мере некоторые из которых жестко установлены на той же оси (валу), что и колесики 15, и удерживаются на месте с помощью стопорных колец 12 а, 12b. Натяжитель цепи 19 предназначен для поддержания натяжения цепи, необходимого для того, чтобы удерживать каретку 1, 15 а, 15b прижатой к поверхности. В направлении движения каретка 1, 15 а, 15b содержит нагревательное устройство (не показано) в виде радиационного нагревателя, такого как инфракрасный радиатор. Рядом с нагревательным устройством находится щелевая экструзионная головка 3, в которую поступает полимерный расплав из цилиндра 4, который может наполняться расчетным объемом полимерного расплава, необходимым для покрытия заранее определенной поверхности трубы. Цилиндр 4 и экструзионная головка 3 соединены нагнетательным шлангом 27. Цилиндр снабжен опорожняющим устройством, например поршнем, который выталкивает полимерный расплав из цилиндра 4 и далее через шланг 27 в экструзионную головку 3. Как указано выше,также возможно подавать полимерный расплав прямо из экструдера в экструзионную головку, как показано на фиг. 3 а-3 с. Рядом с передними колесиками 15 а находится аппликатор/выравнивающий ролик 5, который переносит полимерную пленку, экструдированную из экструзионной головки 3, на поверхность трубы 2.-5 016663 Пружина (не показана) нажимает на ролик 5 так, чтобы он был прижат к поверхности трубы. Каретка приводится в движение электродвигателем 6, соединенным с ведущими колесиками 15 а,15b. Обычно экструзионная головка при перемещении совершает один оборот вокруг трубы, однако в особых случаях она может совершать несколько оборотов в зависимости от желаемой толщины слоя или комбинации материалов. В ходе этого процесса на монтажное соединение экструдируется расплав полимеров. На фиг. 1 и 2 показана экструзионная головка, в которую подается материал из промежуточного контейнера, установленного на подвижной каретке. В одном из вариантов осуществления изобретения стальная труба с покрытием была покрыта полиолефиновой пленкой 3-мм толщины, имеющей ширину 500 мм, при скорости 0,7 м/мин с общим расходованием полимера 60 кг/ч. Фиг. 3 а-3 с демонстрируют работу движущейся экструзионной головки 36, в которую материал поступает прямо из экструдера 32 через нагнетательный шланг 34. Труба, подлежащая покрытию, имеет числовое обозначение 30, а аппликаторный ролик - обозначение 38. На фиг. показан процесс покрытия трубы путем перемещения каретки вокруг трубы. Способ нанесения покрытий в соответствии с настоящим изобретением может выполняться следующим образом. Сначала очищается поверхность трубы или участка трубы, например, монтажное соединение между двумя стальными трубами с полиолефиновым покрытием. Это может выполняться с помощью абразивного инструмента, например, путем дробе- или пескоструйной обработки. После стадии очистки поверхность предварительно нагревается. Можно использовать жар, вырабатываемый в процессе сваривания труб (предварительный и последующий нагрев зоны сварного шва). Однако, как указано выше, каретка может также иметь отдельное нагревательное устройство, такое как инфракрасный нагревательный элемент, или может применяться отдельное инфракрасное нагревательное устройство с ручным управлением. В случаях стационарного применения покрытий на заводах и баржах может применяться индукционный нагрев. Кроме того, возможен нагрев газовой горелкой. Предпочтительно нагрев должен выполняться так, чтобы нагревалась только поверхность трубы. Очищенная и нагретая поверхность затем обрабатывается подходящими материалами. Материалы выбираются в соответствии со спецификациями по проекту; можно пассивировать стальную поверхность путем, например, хроматной или сульфатной обработки. На поверхность могут альтернативно или дополнительно наноситься различные грунтовочные покрытия. Их можно выбрать из композиций, содержащих однокомпонентную жидкую эпоксидную смолу; двухкомпонентную жидкую эпоксидную смолу (основание + отвердитель); порошковый эпоксидный распылитель; автономные кремнеорганические материалы; и кремнеорганические материалы + пассивирование. После стадии предварительной обработки/грунтования наносятся адгезивы и верхние покрытия(например, слой полимерного покрытия). Типичные полимерные покрытия основаны на полиолефинах или иных термопластичных полимерах. Различные варианты осуществления изобретения содержат полиэтилен, полипропилен, адгезивы в виде порошка или расплава, автономные полиолефины (т.е. материалы, которые могут использоваться без отдельных адгезивов). Кроме того, возможны многослойные покрытия, когда на поверхность одновременно или последовательно наносятся два или более слоев. В полевых условиях операторам, управляющим машинами по нанесению покрытий, обычно требуется следующее устройство: маленький экструдер, предпочтительно как можно более простой и легкий, для производства полимерного расплава; предпочтительно два цилиндра для расплавленных полимеров (один для эксплуатации, другой для наполнения); устройство для струйной очистки секций монтажных соединений; устройство для предварительного нагрева, радиаторы (инфракрасные), индуктивный нагрев или газовая горелка; воздушный компрессор для струйной очистки или хода пневматического поршня; описанное выше устройство для нанесения покрытия, прикрепленное к трубе предпочтительно двумя цепями или равнозначным креплением; источник электропитания для нагрева трубы и участка соединения внахлестку, предпочтительно установленные на экструзионной головке; генератор для вырабатывания электричества и гидравлическая система для хода поршня цилиндра. В процессе работы участок нанесения покрытия на гладкопроходное соединение может быть помещен под тент. Как указано выше, настоящее изобретение может быть использовано для покрытия различных труб.-6 016663 Диаметры труб могут различаться в пределах от 200 до 3500 мм. Обычно в особенно предпочтительном варианте осуществления изобретения, применяемом для покрытия монтажных соединений между трубами с полиолефиновым покрытием, диаметры труб находятся в пределах от 250 до 1500 мм. Следует подчеркнуть, что в соответствии с одним из вариантов осуществления изобретения относительное движение между кареткой и трубой может достигаться путем вращения трубы при удержании каретки в неподвижном положении. Такой вариант осуществления изобретения может применяться внутри помещений, например на заводах. ФОРМУЛА ИЗОБРЕТЕНИЯ 1. Способ нанесения покрытия на трубу (2; 30) или участок трубы в виде слоя по меньшей мере одного полимера, согласно которому наносят на наружную поверхность трубы (2; 30) или участка трубы, имеющей или имеющего наружную поверхность, определяющую периферию трубы или участка трубы, слой по меньшей мере одного полимерного материала в виде расплава с помощью экструзионной головки, установленной на каретке(1, 15 а, 15b; 36), выполненной с возможностью перемещения вдоль периферии трубы (2) или участка трубы; и перемещают каретку (1, 15 а, 15b; 36) вдоль по меньшей мере части периферии в процессе нанесения полимерного материала с целью формирования слоя на поверхности трубы (2; 30) или участка трубы,отличающийся тем, что согласно способу дополнительно выравнивают полимерный материал, наносимый с помощью экструзионной головки (3), посредством выравнивающего средства (5; 38), установленного на каретке (1, 15 а, 15b; 36). 2. Способ по п.1, в соответствии с которым указанная экструзионная головка представляет собой щелевую экструзионную головку (3), которая установлена на каретке (1, 15 а, 15b) и соединена с источником (4) расплавленного полимерного материала. 3. Способ по п.1 или 2, в котором щелевая экструзионная головка (3) имеет ширину, по существу,соответствующую заранее определенной ширине указанного слоя. 4. Способ по п.1 или 2, отличающийся тем, что каретку (1, 15 а, 15b; 36) перемещают по меньшей мере на 180, предпочтительно на 360 или более вдоль периферии трубы (2; 30) или участка трубы для нанесения полимерного слоя, покрывающего наружную поверхность вдоль периферии. 5. Способ по п.4, отличающийся тем, что каретку (1, 15 а, 15b; 36) перемещают по спиралеобразной траектории вдоль периферии трубы (2; 30) или участка трубы для нанесения полимерного слоя, когда каждый последующий слой частично накладывается на предыдущий слой. 6. Способ по пп.1, 2, 5, отличающийся тем, что на поверхность наносится полимерный слой, содержащий по меньшей мере две наложенные друг на друга пленки, при этом каждая из полимерных пленок имеет толщину в пределах от 0,01 до 10 мм, предпочтительно от 0,5 до 5 мм и, в частности, от 0,1 до 3 мм. 7. Способ по пп.1, 2, 5, отличающийся тем, что полимерный материал выравнивают с помощью выравнивающего средства (5; 38), прилагающего силу, по существу, перпендикулярно полимерному материалу для разглаживания полимерного слоя по наружной поверхности трубы (2; 30) или участка трубы. 8. Способ по пп.1, 2, 5, отличающийся тем, что полимерный материал выравнивается роликом (5; 38) или ножом. 9. Способ по п.7, отличающийся тем, что полимерный материал выравнивается роликом (5; 38),имеющим эластичную поверхность, имеющим твердость от 10 до 30 по Шору А. 10. Способ по п.7, отличающийся тем, что полимерная пленка извлекается из щелевой экструзионной головки (3) на выравнивающее средство (5) и переносится с выравнивающего средства (5) на наружную поверхность трубы (2) или участка трубы, при этом выравнивающее средство (5) разглаживает и выравнивает пленку и одновременно переносит ее на поверхность. 11. Способ по любому из пп.1, 2, 5, 9, 10, отличающийся тем, что каретку (1, 15 а, 15b; 36) перемещают с регулируемой скоростью, при этом полимерный материал экструдируется из вышеуказанной щелевой экструзионной головки (3), по существу, при постоянной скорости экструзии, и толщина пленки контролируется путем регулирования скорости движущейся каретки (1, 15 а, 15b). 12. Способ по любому из пп.1, 2, 5, 9, 10, отличающийся тем, что полимерный материал наносят на поверхность стальной трубы (2; 30) с полимерным покрытием, содержащей, по меньшей мере, частично непокрытый участок трубы. 13. Способ по п.12, отличающийся тем, что кольцевой сварной шов и примыкающие части непокрытой стальной трубы, включая примыкающие концы полимерного покрытия, покрывают с целью герметизации кольцевого сварного шва от воздействия воздуха, влажности и воды. 14. Способ по любому из пп.1, 2, 5, 7, 9, 10, отличающийся тем, что трубу (2; 30) или участок трубы покрывают по меньшей мере одним термопластичным полимером, выбираемым из группы, включающей полиолефины, в частности полиэтилен и полипропилен, включая автономные полиолефины и замещен-7 016663 ные полиолефины. 15. Способ по п.14, отличающийся тем, что автономный полиолефин содержит адгезионноподдерживающие группы, выбранные из группы акрилатов, карбоновых кислот и аминов. 16. Способ по любому из пп.1, 2, 5, 7, 9, 10, 15, отличающийся тем, что наружную поверхность трубы (2; 30) или участка трубы перед покрытием нагревают до температуры в пределах от 80 до 300 С. 17. Способ по п.16, отличающийся тем, что поверхность нагревают с помощью нагревательного устройства, установленного на каретке. 18. Способ по любому из пп.1, 2, 5, 7, 9, 10, 15, 17, в котором наружную поверхность трубы (2; 30) или участка трубы покрывают грунтующим агентом до достижения модифицированной поверхности с целью улучшения прилипания полимерного слоя к поверхности. 19. Способ по п.18, отличающийся тем, что грунтующий агент выбирают из группы, включающей композиции с однокомпонентной жидкой эпоксидной смолой, композиции с двухкомпонентной жидкой эпоксидной смолой, порошковых эпоксидных распылителей и кремнийорганики. 20. Способ соединения труб, в частности стальных труб с полиолефиновым покрытием, отличающийся тем, что концы двух стальных труб с покрытием подгоняют друг к другу; стальные трубы приваривают друг к другу с образованием соединения и соединение покрывают по меньшей мере одним слоем материала, способного герметизировать соединение от воздействия воздуха и влажности,характеризующийся нанесением на соединение покрытия с использованием способа по любому из пп.1-19. 21. Устройство для нанесения покрытия на трубу (2; 30) или участок трубы, имеющую или имеющий наружную поверхность, определяющую периферию трубы или участка трубы, содержащее подвижную каретку (1, 15 а, 15b; 36), выполненную с возможностью перемещения вокруг периферии трубы (2; 30) или участка трубы; экструзионную головку (3), соединенную с источником (4; 32) полимерного расплава для образования полимерной пленки и установленную на подвижной каретке (1, 15 а, 15b; 36); и выравнивающие средства (5; 38), выполненные с возможностью выравнивания и разглаживания полимерной пленки по наружной поверхности трубы (2; 30) или участка трубы и установленные на подвижной каретке (1, 15 а, 15b; 36). 22. Устройство по п.21, отличающееся тем, что каретка (1, 15 а, 15b; 36) способна перемещаться по меньшей мере на 360 вдоль периферии трубы (2; 30) или участка трубы для нанесения полимерного слоя, покрывающего наружную поверхность вдоль периферии. 23. Устройство по п.21 или 22, отличающееся тем, что экструзионная головка (3; 36) соединена с источником расплавленного полимерного материала (4; 32), выбранного из группы экструдеров, нагревательных шнековых смесителей или контейнеров для промежуточного хранения. 24. Устройство по п.23, отличающееся тем, что контейнеры для промежуточного хранения (4) выполнены с возможностью опорожнения с помощью прочищающих устройств, приводимых в действие гидравлическим, пневматическим или электрическим способами. 25. Устройство по любому из пп.21, 22, 24, отличающееся тем, что выравнивающее средство (5; 38) выбирают из группы роликов и ножей, прилагающих силу, по существу, перпендикулярно полимерному материалу для разглаживания полимерного слоя по наружной поверхности трубы (2; 30) или участка трубы. 26. Устройство по п.25, отличающееся тем, что поверхность ролика (5; 38) имеет твердость от 10 до 30 по Шору А. 27. Устройство по любому из пп.21, 22, 24, 26, отличающееся тем, что экструзионную головку (3; 36) приспосабливают для образования полимерной пленки на выравнивающем средстве (5; 38), и выравнивающее средство способно переносить полимерную пленку на наружную поверхность трубы (2; 30) или участок трубы. 28. Устройство по любому из пп.21, 22, 24, 26, отличающееся тем, что каретка (1, 15 а, 15b; 36) содержит нагревательное устройство, расположенное перед выравнивающим средством в направлении поступательного движения каретки. 29. Устройство по любому из пп.21, 22, 24, 26, отличающееся тем, что каретку (1, 15 а, 15b) закрепляют на трубе или участке трубы с помощью по меньшей мере одной тяговой цепи (14), которую обматывают вокруг трубы (2) или участка трубы.
МПК / Метки
МПК: F16L 58/10, B29C 63/06, F16L 13/02, F16L 58/18
Метки: устройство, трубы, способ, покрытия, нанесения
Код ссылки
<a href="https://eas.patents.su/10-16663-sposob-i-ustrojjstvo-naneseniya-pokrytiya-na-truby.html" rel="bookmark" title="База патентов Евразийского Союза">Способ и устройство нанесения покрытия на трубы</a>
Предыдущий патент: Система демпфирования скручивания приемной камеры молотилки
Следующий патент: Обернутая емкость с наклейкой
Случайный патент: Циклонный сепаратор и способ дегазации смеси текучей среды