Способ получения батареи топливных элементов
Номер патента: 24612
Опубликовано: 31.10.2016
Авторы: Клитхольм Зёрен Кливер, Кристианзен Нильс, Ларсен Гутцон Ёрген
Формула / Реферат
1. Способ получения батареи топливных элементов, в которой соединительные пластины отдельных элементов сделаны кондиционированием поверхности пластины или листа из нержавеющей стали толщиной от 0,2 до 8 мм и последующим нанесением слоя на указанную кондиционированную поверхность, причем указанный способ включает следующие стадии:
a) отжиг стальной пластины или листа в течение вплоть до 100 ч в атмосфере защитного газа, выбираемого из инертных газов, N2 и H2, и при температуре 600-1000°C, для того чтобы удалить Si, Al, Ti и другие окисляемые элементы с поверхности,
b) контролируемое протравливание поверхности пластины или листа для получения шероховатой поверхности с несквозными углублениями, то есть закрытыми или несквозными отверстиями, приводящее к поверхности с шероховатостью Rz между 3 и 50 мкм, и
c) нанесение защитного и проводящего электричество слоя на шероховатую металлическую поверхность.
2. Способ согласно п.1, в котором наносимый слой представляет собой металлический или керамический слой.
3. Способ согласно п.1, при котором защитный и проводящий электричество слой наносят на шероховатую металлическую поверхность путем термического напыления, нанесения тонкого покрытия мокрым способом, печатания через сетчатый трафарет, влажного распыления порошка, газопламенного напыления или плазменного напыления, вакуумного напыления (PVD), химического осаждения из газовой фазы (CVD) или применения гальванических процессов.
4. Способ согласно любому из пп.1-3, при котором слой, нанесенный на стадии c), состоит из лантаново-стронциевых манганитов (LSM), La-Sr-Cr-O, La-Ni-Fe-O, La-Sr-Co-O, Co-Mn-Ni-O или La-Sr-Fe-Co-O, или состоит из материала перовскита, имеющего общую формулу ABO3, или из шпинельного материала, имеющего общую формулу ABO4, в которой элементы A и B, как правило, имеют состояния окисления +2 и +3.
5. Способ согласно любому из пп.1-3, при котором покрытие, нанесенное на стадии c), состоит из Co или комбинации Co и Ni и сформировано вакуумным напылением (PVD), химическим осаждением из газовой фазы (CVD) или гальваническим процессом.
6. Способ согласно любому из пп.1-3, при котором металлический слой выбирают из сплавов, устойчивых к окислению при высоких температурах.
7. Способ согласно любому из пп.1-6, при котором контролируемое протравливание на стадии b) проводят с применением влажного химического или других способов протравливания.
8. Способ согласно любому из пп.1-6, при котором термическое напыление представляет собой способ плазменного напыления, выполняемый при температуре, при которой напыляемый порошок полностью или преимущественно расплавлен.
9. Способ согласно п.7, при котором протравливание осуществляют путем применения влажного химического способа, включающего FeCl3 и HCl.
10. Способ согласно п.7 или 9, при котором контролируемое протравливание осуществляют путем применения влажного химического способа, включающего FeCl3, HCl, HNO3, NH4F или их комбинацию.
11. Способ согласно любому из пп.1-10, при котором за протравливанием следует оксидирование на воздухе при температуре 800-950°C в течение 1-10 ч перед нанесением покрытия.
12. Способ согласно любому из пп.1-11, при котором нержавеющая сталь листа представляет собой высокотемпературную ферритовую нержавеющую сталь.
13. Способ согласно п.12, при котором нержавеющую сталь выбирают из сортов Crofer® 22 Н, Crofer® 22 APU, Sandvik SanergyÔ HT, ZMG 232L, ZMG J3 и ZMG G10.
14. Способ согласно любому из пп.1-13, при котором металлические листы перед протравливанием термически обрабатывают в содержащей низкое количество O2 атмосфере H2, Ar или подобных при температуре 600-1200°C в течение вплоть до 100 ч, для того чтобы сконцентрировать Si, Ti и Al близко к поверхности или на поверхности.
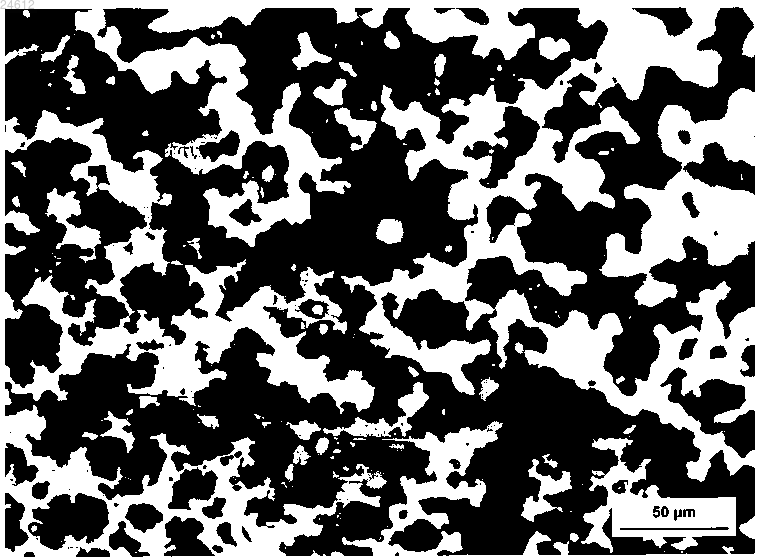
Текст
СПОСОБ ПОЛУЧЕНИЯ БАТАРЕИ ТОПЛИВНЫХ ЭЛЕМЕНТОВ Способ получения батареи топливных элементов, в которой соединительные пластины отдельных элементов сделаны кондиционированием поверхности пластины или листа из нержавеющей стали толщиной от 0,2 до 8 мм и последующим нанесением слоя на указанную кондиционированную поверхность, причем указанный способ включает следующие стадии: а) отжига стальной пластины или листа в течение вплоть до 100 ч в атмосфере защитного газа, выбираемого из инертных газов,N2 и Н 2, и при температуре 600-1000C, для того чтобы удалить Si, Al, Ti и другие окисляемые элементы с поверхности, b) контролируемого протравливания поверхности пластины или листа для получения шероховатой поверхности с несквозными углублениями, то есть закрытыми или несквозными отверстиями, приводящего к поверхности с шероховатостью Rz между 3 и 50 мкм,и c) нанесения защитного и проводящего электричество слоя на шероховатую металлическую поверхность. Область техники Данное изобретение относится к способу кондиционирования поверхности пластины или листа из нержавеющей стали и последующего нанесения слоя на поверхность. Изобретение далее относится к соединительной пластине, изготовленной способом, и к использованию указанной соединительной пластины в батареях топливных элементов. Более предпочтительно способ данного изобретения предназначен для применения произведенной соединительной пластины в высокотемпературных топливных элементах, в частности в твердом оксидном топливном элементе (ТОТЭ) или в твердой оксидной электролитической ячейке (ТОЭЯ), а также в других высокотемпературных топливных элементах, таких как топливные элементы с расплавленным карбонатом (ТЭРК). Основа изобретения В дальнейшем изобретение будет описано относительно твердого оксидного топливного элемента(ТОТЭ) или твердой оксидной электролитической ячейки (ТОЭЯ), которая является твердым оксидным топливным элементом, действующим в регенеративной моде, для электролиза воды с помощью твердого оксидного электролита с получение газообразного кислорода и водорода. Твердый оксидный топливный элемент содержит твердый электролит, в котором возможна проводимость ионов кислорода, катод, где кислород восстанавливается до иона кислорода, и анод, где водород окисляется. Вся реакция в ТОТЭ состоит в том, что водород и кислород реагируют электрохимически с выработкой электричества, тепла и воды. Для того чтобы получить необходимый водород, анод нормально обладает каталитической активностью для реформинга углеводородов с водяным паром, в частности природного газа, при котором генерируются водород, моноокись углерода и двуокись углерода. Реформинг метана, главного компонента природного газа, с водяным паром может быть описан следующими уравнениями:CH4 + H2OCO + 3H2,CH4 + CO22CO + 2H2,CO + Н 2 ОCO2 + H2. Во время работы окислитель, такой как воздух, подают в твердый оксидный топливный элемент, в катодную область. Топливо, такое как водород подают в анодную область топливного элемента. Альтернативно, углеводородное топливо, такое как метан, подают в анодную область, где оно превращается в водород и окислы углерода в результате приведенных выше реакций. Водород проходит через пористый анод и реагирует на поверхности раздела анод/электролит с ионами кислорода, генерированными на катодной стороне, которые диффундируют через электролит. Ионы кислорода создаются на катодной стороне при подаче электронов из внешней электрической цепи элемента. Для того чтобы увеличить напряжение, несколько индивидуальных элементов (единиц элементов) объединяют с образованием батареи элементов, и их связывают между собой с помощью соединительных пластин. Соединительная пластина служит в качестве барьера для газа для разделения анодной (топливо) и катодной (воздух/кислород) сторон соседних единиц элементов, и в то же самое время она способствуют проводимости тока между соседними элементами, то есть между анодом одной единицы элемента с избытком электронов и катодом соседней единицы элемента, который нуждается в электронах для процесса восстановления. Соединительные пластины нормально обеспечены несколькими путями пролета топливного газа с одной стороны соединительной пластины и окислительного газа с противоположной стороны. Для оптимизации исполнения батареи ТОТЭ должен быть максимизирован ряд положительных факторов, в то время как неприемлемые последствия другого ряда связанных отрицательных факторов должны быть минимизированы. К факторам, которые должны быть максимизированы, относятся использование топлива, электрическая эффективность и срок службы, тогда как к факторам, которые должны быть минимизированы, относятся стоимость продукции, размеры, время производства, частота отказов и число компонентов. Соединительная пластина оказывает прямое влияние на большую часть упомянутых факторов. В связи с этим как конфигурация, так и характеристики соединительной пластины очень важны для функции батареи элементов. Часто является желательным, чтобы соединительная пластина была оснащена защитным покрытием, для того чтобы улучшить характеристики соединительной пластины. Такие покрытия могут быть нанесены такими способами, как нанесение тонкого покрытия мокрым способом, печатание через сетчатый трафарет, влажное распыление порошка, газопламенное напыление или плазменное напыление. В случае, когда защитное покрытие наносится на поверхность металлической соединительной пластины,эта поверхность должна иметь шероховатость Rz как минимум 3-5 мкм, чтобы происходило сильное сцепление между покрытием и соединительной пластиной, таким путем связывают покрытие должным образом. Однако прессованные тонкие листы или полосы из нержавеющей стали, которые можно использовать в качестве соединительных пластин, как правило, имеют малую шероховатость поверхностиRz, равную 3 мкм или менее, что затрудняет обеспечение соединительных пластин необходимым защитным покрытием. Обработка песком представляет собой эффективный путь решения этой проблемы, од-1 024612 нако тонкие стальные полосы, то есть полосы толщиной около 1 мм или менее, будут деформироваться,что делает невозможным применение соединительной пластины. Действительно, стальные полосы могут быть получены для предполагаемого применения, то есть они могут быть получены с определенной специфической шероховатостью, однако последующее придание формы стальной полосе может испортить эту шероховатость, как минимум, в некоторой степени. Неожиданно было обнаружено, что кондиционирование поверхности, включающее контролируемое травление (флэш травление) соединительных пластин или листов, которым придана форма, с использованием влажного химического способа, такого как влажный химический способ, включающий растворFeCl3 и HCl плюс при необходимости фторид, может приводить к образованию поверхности с нерегулярными, с крутыми сторонами скрытыми отверстиями, то есть закрытыми или не сквозными отверстиями, связанными с селективным протравливанием зерен с определенной ориентацией кристаллической решетки, давая поверхность желательной шероховатости Rz между 3 и 50 мкм. Эта шероховатая поверхность будет обеспечивать сильное связывание с покрытием, когда это покрытие располагается на поверхности. Кроме того, протравливание понижает концентрацию элементов которые могут быть сконцентрированы на поверхности или вблизи нее, то есть таких элементов, как Mn, Si, Ti и Al. Такие элементы, как правило, концентрируются на поверхности во время тепловой обработки сплава. Известно, что существует возможность оказания влияния на характеристики поверхности или на изменение характеристик поверхности металлических предметов, таких как пластины или листы из нержавеющей стали, путем протравливания поверхности. Например, в US 2010/0132842 A1 раскрыт способ улучшения свойств поверхности специфической нержавеющей стали для биполярных пластин полимерной электролитной мембраны топливных элементов, обеспечивающих низкое пограничное контактное сопротивление и в то же время хорошее сопротивление коррозии. Этот способ включает травление нержавеющей стали водным раствором серной кислоты, промывание нержавеющей стали водой, погружение ее в смесь растворов азотной кислоты и фтористоводородной кислоты, для того чтобы образовался пассивационный слой и плазменное нитридирование погруженной под воду нержавеющей стали с образованием нитридного слоя на поверхности нержавеющей стали. Этот известный способ распространяется на специфические типы стали и специфичное протравливание кислотой H2SO4, за которым следует равноспецифичный способ нитридирования, с образованием нитридного слоя, включающего CrN и/или Cr2N на поверхности стали. В связи с тем, что этот подход может быть использован для специфических целей, его не расширяют для более широкой области применения, и цитированная патентная заявка не должна предусматривать возможность применения различных видов покрытий стальной поверхности путем варьирования условий протравливания и условий покрывания покрытием. Кроме того, описание указанной ссылки не содержит данных о важности получения специально выбранных конфигураций ямок на поверхности стали. В JP 4491363 B2 описан аппарат для протравливания плазмой и для других плазменных процессов,причем, аппарат среди прочего может быть применен для образования тонкой пленки на тонкой металлической пластине при изготовлении сепараторов для топливных элементов. Протравливание в связи с изготовлением соединительных пластин для топливных элементов также описано в US 2003/0064269 A1, где не плоская соединительная пластина может быть образована из плоской чистой пластины путем механической обработки или химического протравливания. Здесь цель состоит в том, чтобы создать штырьки на пластинке, эти штырьки простираются в сторону и контактируют как с анодом, так и с катодом, поскольку цель согласно данному изобретению состоит в создании контролируемой степени шероховатости на поверхности металлической пластины, таким образом, создавая возможность плотно прилегающее покрытие на поверхности. В JP 4093321 B2 раскрыта пористая трубчатая структура смешанного типа, то есть печная внутренняя трубка использована для изготовления твердого оксидного топливного элемента, который способен выдерживать высокую температуру 900C или более без риска повреждения, такого как растрескивание,связанного с температурным циклом. Пористая керамическая пленка, образованная газопламенным напылением, формируется на пористой пленке сплава способом плазменного напыления. Кроме того, материал основы протравливают влажным методом протравливания. Однако цели и средства их достижения полностью отличаются от таковых данного изобретения. Наконец, в US 2007/0248867 описана протравленная соединительная пластина топливных элементов, содержащих твердый оксидный электролит, анод и катод, причем, соединительная пластина содержит проводящий основной лист, имеющий первую и вторую стороны с проходами для анодного и катодного газового потока, соответственно. В предпочтительном варианте проходы для газового потока изготавливают способом фотохимического протравливания, однако в патенте отсутствуют ссылки в отношении применения покрытий на поверхности соединительной пластины. Краткое описание изобретения Как указано выше, изобретение относится к способу нанесения слоя, например, керамического или металлического слоя на пластину или лист из нержавеющей стали, при котором поверхность стальной пластины или листа, до того, как нанести на нее слой, делают шероховатой путем протравливания для улучшения связывания слоя со стальной поверхностью. Изобретение далее относится к соединительной пластине, изготовленной этим способом, и к применению указанной соединительной пластины в батареях топливных элементов. Подробное описание изобретения Более специфично изобретение относится к способу кондиционирования поверхности пластины или листа из нержавеющей стали с толщиной от 0,2 до 8 мм и последующего нанесения слоя, такого как керамический или металлический слой, на указанную кондиционированную поверхность путем нанесения тонкого покрытия мокрым способом, печатания через сетчатый трафарет, влажного распыления порошка, газопламенного напыления или плазменного напыления, причем указанный процесс включает следующие стадии:a) проводимого при необходимости отжига стальной пластины или листа в течении вплоть до 100 часов в атмосфере защитного газа при температуре 600-1000C, для того чтобы удалить Si, Al, Ti и другие окисляемые (электроположительные) элементы с поверхности,b) контролируемого протравливания поверхности пластины или листа для получения шероховатой поверхности с несквозными углублениями, то есть закрытыми или несквозными отверстиями, приводящего к поверхности с шероховатостью Rz между 3 и 50 мкм, иc) нанесения защитного и проводящего электричество слоя на шероховатую металлическую поверхность, тем самым формируя слой на поверхности. Защитный и проводящий электричество слой может быть нанесен на шероховатую металлическую поверхность путем термического напыления, нанесения тонкого покрытия мокрым способом, печатания через сетчатый трафарет, влажного распыления порошка, газопламенного напыления или плазменного напыления или любыми другими подходящими способами. К другим подходящим способам относятся физическое напыление паров (PVD), химическое напыление паров (CVD) и применение гальванических процессов. Таким образом, идея, лежащая в основе данного изобретения, состоит в том, что улучшенное исполнение может быть достигнуто при применении батареи топливных элементов, в которой соединительные пластины отдельных элементов сделаны способом данного изобретения, причем, этот способ включает кондиционирующую предварительную обработку стальной поверхности, после которой следует термическое напыление керамического слоя на кондиционированную поверхность. Кондиционирующая предварительная обработка состоит из проводимого при необходимости отжига поверхности стальной пластины или листа в течение вплоть до 100 ч в атмосфере защитного газа при температуре 600-1000C, за которым следует контролируемое протравливание этой при необходимости отожженной поверхности, для получения шероховатой поверхности, которая оптимально подходит для керамического слоя, подлежащего нанесению. Причина, из-за которой предпочтительно проведение предварительной термической обработки стальной пластины или листа, связана с тем фактом, что сталь почти неизбежно содержит такие элементы, как Si, Ti и Al, которые концентрируются на поверхности стали или вблизи нее во время работы при высоких температурах батареи ТОТЭ или при соответствующей термической обработке. В обоих случаях электропроводность поверхности будет уменьшаться. В предпочтительном варианте изобретения защитный и проводящий электричество керамический порошковый слой, нанесенный на стадии c) способа, состоит из лантаново-стронциевых манганитов(ЛСМ), La-Sr-Cr-O, La-Ni-Fe-O, La-Sr-Co-O, Co-Mn-Ni-O или La-Sr-Fe-Co-O. Способ напыления предпочтительно выбирают из термических плазменных способов напыления покрытий. Особенно предпочтительным является то, что термическое плазменное напыление покрытий проводят при температуре плавления или выше температуры плавления применяемого порошка. Контролируемое протравливание может быть проведено с применением влажного химического или других способов протравливания. Среди влажных химических способов предпочтение отдается способам, включающим FeCl3 + HCl. Еще более предпочтительно выполнение контролируемого протравливания путем применения влажного химического способа, включающего раствор FeCl3 и HCl, при необходимости содержащий фторид. Протравливание можно проводить оксидированием в воздухе при температуре 800-950C в течение 1-10 ч перед нанесением слоя. Нержавеющая сталь может быть выбрана из типов стали с подходящей высокотемпературной устойчивостью к коррозии, выбираемой из ферритных, аустенитовых, дуплексных сталей или сплавов на основе хрома или никеля. Предпочтительной сталью является ферритовая нержавеющая сталь. Подходящими ферритовыми нержавеющими сталями являются крофер 22 H и крофер 22 APU фирмыThyssen Krupp, санерги HT фирмы Sandvik AB и ZMG 232 типы фирмы Hitachi Metals Ltd. Такие стали особенно хорошо подходят для целей данного изобретения, которое, однако, не ограничено этими специфическими сталями. При применении протравливания вместо других способов обработки поверхности возможно получение металлической поверхности с уменьшенной концентрацией Si, Ti, Al, Mn и возможно других ки-3 024612 слородофильных элементов, которые (исключая Mn) имеют тенденцию понижать электропроводность поверхности, приводя к понижению контактного сопротивления. Когда протравленные и затем покрытые слоем соединительные пластины используют в батареях топливных элементов, наблюдается заметно улучшенное исполнение батареи, как видно из фиг. 3. Кроме того, коррозия батареи топливных элементов проявляется более слабо. Далее изобретение поясняется следующими примерами. Пример 1 В этом примере показано протравливание тонких стальных полос способом согласно данному изобретению, в особенности обращается внимание на важное значение концентрации кислоты. Протравливание является желательным приближением для получения необходимой шероховатости поверхности тонких пластин или полос из стали, так как протирание песком тонких стальных полос, то есть полос с толщиной менее 1 мм, имеет тенденции к изменению формы полос, тем самым делая невозможным применение их в соединительных пластинах. Ряд экспериментов протравливания был проведен на стальных пластинах крофер 22 APU для исследования того, как на глубину протравливания влияет время протравливания и концентрация кислоты. Стремились проводить протравливание внимательно, чтобы полученное протравливание было не слишком глубоким. Полученные результаты приведены ниже в табл. 1. Таблица 1 удаленной стали с обеих сторон, опираясь на потерю веса Протравливание проводят, применяя влажный химический способ, включающий раствор FeCl3 с 01,5 вес. процентами HCl. Приведенные выше результаты показывает, что протравливание проникает глубоко (Rz = 27,7-36,2 мкм) в пластину, тогда как только 5-7 мкм поверхности было удалено. В этом примере причина состоит в том, что приблизительно 40% исходной поверхности еще сохранена (см. фиг. 1; глубина протравливания 5-7 мкм). Это может быть связано с селективным протравливанием зерен с определенной ориентацией кристаллической решетки и/или в связи с присутствием устойчивого слоя защитного оксида хрома на поверхности, позволяя более глубокое проникновение протравливания в незащищенных местах для того же количества удаляемого материала. Видно, что шероховатость поверхности меньше у образцов, которые были протравлены более глубоко (фиг. 2; глубина протравливания 11-20 мкм). Очевидно, что плазменное покрытие способно связываться с этими поверхностями. На фиг. 3 приведена микрофотография соединительной пластины, которая была вначале протравлена FeCl3 + HCl и затем покрыта лантаново-стронциевым манганитом (LSM). Ограниченный участок той же самой микрофотографии показан на фиг. 4. Другая фотография, полученная на сканирующем электронном микроскопе (СЭМ), показана на фиг. 5. Картина показывает шероховатую поверхность, образованную флэш-протравливанием ферритовой нержавеющей стали сорта крофер 22 APU. Пример 2 Исполнение батарей топливных элементов, изготовленных из топливных элементов с соединительными пластинами, которые были изготовлены способом согласно данному изобретению, измерено и сравнено с исполнением похожих батарей топливных элементов изготовленных из топливных элементов с соединительными пластинами, приготовленными предшествующим способом предварительной обработки соединительных пластин фирмы Topsoe Fuel Cell A/S. При обработке протравливанием, проводимой согласно данному изобретению, количество Si уменьшается на поверхности. Количество Ti и количество Al уменьшается в 5-10 раз в результате обработки. Результаты наблюдаемого исполнения двух типов батарей топливных элементов представлены в табл. 2 (предшествующий способ предварительной обработки соединительных пластин) и в табл. 3 (способ согласно данному изобретению). Таблица 2. Среднее электрическое напряжение на элементе(предшествующий способ обработки соединительных пластин) Таблица 3. Среднее электрическое напряжение на элементе(способ обработки согласно данному изобретению) На фиг. 6 проиллюстрировано наблюдаемое поведение двух типов батарей топливных элементов,которые описаны выше. На левой части фигуры показано поведение батареи, изготовленной из топливных элементов с соединительными пластинами, изготовленными предшествующим способом предварительной обработки соединительных пластин, тогда на правой части фигуры показано поведение батареи,изготовленной из топливных элементов с соединительными пластинами, изготовленными способом согласно данному изобретению. На фигуре приведены средние напряжения на элементе, измеренные в течение периода около двух месяцев, и отчетливо видно, что напряжение элемента при силе тока 35 А остается почти постоянным (около 0,9 В) в элементах с соединительными пластинами, приготовленными способом согласно данному изобретению, тогда как напряжение на элементах при силе тока 35 А у элементов с соединительными пластинами, изготовленными предшествующим способом предварительной обработки соединительных пластин, измеренное при идентичных условиях, обнаруживает устойчивое уменьшение от около 0,88 В до около 0,78 В за период измерения. ФОРМУЛА ИЗОБРЕТЕНИЯ 1. Способ получения батареи топливных элементов, в которой соединительные пластины отдельных элементов сделаны кондиционированием поверхности пластины или листа из нержавеющей стали толщиной от 0,2 до 8 мм и последующим нанесением слоя на указанную кондиционированную поверхность, причем указанный способ включает следующие стадии:a) отжиг стальной пластины или листа в течение вплоть до 100 ч в атмосфере защитного газа, выбираемого из инертных газов, N2 и H2, и при температуре 600-1000C, для того чтобы удалить Si, Al, Ti и другие окисляемые элементы с поверхности,b) контролируемое протравливание поверхности пластины или листа для получения шероховатой поверхности с несквозными углублениями, то есть закрытыми или несквозными отверстиями, приводящее к поверхности с шероховатостью Rz между 3 и 50 мкм, иc) нанесение защитного и проводящего электричество слоя на шероховатую металлическую поверхность. 2. Способ согласно п.1, в котором наносимый слой представляет собой металлический или керамический слой. 3. Способ согласно п.1, при котором защитный и проводящий электричество слой наносят на шероховатую металлическую поверхность путем термического напыления, нанесения тонкого покрытия мокрым способом, печатания через сетчатый трафарет, влажного распыления порошка, газопламенного напыления или плазменного напыления, вакуумного напыления (PVD), химического осаждения из газовой фазы (CVD) или применения гальванических процессов. 4. Способ согласно любому из пп.1-3, при котором слой, нанесенный на стадии (c), состоит из лантаново-стронциевых манганитов (LSM), La-Sr-Cr-O, La-Ni-Fe-O, La-Sr-Co-O, Co-Mn-Ni-O или La-Sr-FeCo-O, или состоит из материала перовскита, имеющего общую формулу ABO3, или из шпинельного материала, имеющего общую формулу ABO4, в которой элементы A и B, как правило, имеют состояния окисления +2 и +3. 5. Способ согласно любому из пп.1-3, при котором покрытие, нанесенное на стадии c), состоит изCo или комбинации Co и Ni и сформировано вакуумным напылением (PVD), химическим осаждением из газовой фазы (CVD) или гальваническим процессом. 6. Способ согласно любому из пп.1-3, при котором металлический слой выбирают из сплавов, устойчивых к окислению при высоких температурах. 7. Способ согласно любому из пп.1-6, при котором контролируемое протравливание на стадии b) проводят с применением влажного химического или других способов протравливания. 8. Способ согласно любому из пп.1-6, при котором термическое напыление представляет собой способ плазменного напыления, выполняемый при температуре, при которой напыляемый порошок полностью или преимущественно расплавлен. 9. Способ согласно п.7, при котором протравливание осуществляют путем применения влажного химического способа, включающего FeCl3 и HCl. 10. Способ согласно п.7 или 9, при котором контролируемое протравливание осуществляют путем применения влажного химического способа, включающего FeCl3, HCl, HNO3, NH4F или их комбинацию. 11. Способ согласно любому из пп.1-10, при котором за протравливанием следует оксидирование на воздухе при температуре 800-950C в течение 1-10 ч перед нанесением покрытия. 12. Способ согласно любому из пп.1-11, при котором нержавеющая сталь листа представляет собой высокотемпературную ферритовую нержавеющую сталь. 13. Способ согласно п.12, при котором нержавеющую сталь выбирают из сортов Crofer 22 Н, Crofer 22 APU, Sandvik Sanergy HT, ZMG 232L, ZMG J3 и ZMG G10. 14. Способ согласно любому из пп.1-13, при котором металлические листы перед протравливанием термически обрабатывают в содержащей низкое количество O2 атмосфере H2, Ar или подобных при температуре 600-1200C в течение вплоть до 100 ч, для того чтобы сконцентрировать Si, Ti и Al близко к поверхности или на поверхности.
МПК / Метки
МПК: H01M 8/02
Метки: способ, топливных, получения, батареи, элементов
Код ссылки
<a href="https://eas.patents.su/9-24612-sposob-polucheniya-batarei-toplivnyh-elementov.html" rel="bookmark" title="База патентов Евразийского Союза">Способ получения батареи топливных элементов</a>
Предыдущий патент: Установка для извлечения серы и способ извлечения серы
Следующий патент: Машина для удаления щебеночного балласта рельсового пути
Случайный патент: Низкотемпературный катализатор конверсии водяного газа