Способ производства титановой сварочной проволоки
Формула / Реферат
1. Способ производства пригодной для сварки проволоки или пригодной для сварки ленты из титана, состоящий из следующих этапов:
помещают одну или более частиц титановой губки в камеру одноосного пресса,
проводят холодное уплотнение помещенного в камеру материала, состоящего из частиц, в атмосфере наружного воздуха, чтобы сформировать заготовку,
нагревают заготовку до температуры 400-1000°C,
помещают нагретую заготовку в камеру предварительно нагретого пресса для горячей экструзии и при температуре 400-1000°C экструдируют из заготовки пруток или профиль,
удаляют поверхностные загрязнения с указанного прутка или профиля и
помещают указанный пруток или профиль на прокатный стан, имеющий одну или более прокатных клетей, расположенных последовательно, чтобы сформировать пригодную для сварки ленту или проволоку с требуемым диаметром
2. Способ по п.1, отличающийся тем, что частицы титановой губки представляют собой измельченную и разрезанную титановую губку с пониженным содержанием магния, которая удовлетворяет требованиям стандарта ASTM B299-07.
3. Способ по п.2, отличающийся тем, что измельченная и разрезанная титановая губка содержит фракцию с размером частиц 1-100 мм, предпочтительно 2-50 мм, более предпочтительно 3-25 мм.
4. Способ по любому из пп.1-3, отличающийся тем, что холодное уплотнение образца материала, состоящего из частиц, проводят при комнатной температуре с приложением к образцу уплотняющего давления 200-600 МПа.
5. Способ по п.4, отличающийся тем, что уплотнение осуществляют до тех пор, пока частицы образца не объединятся до состояния твердой компактной заготовки с плотностью более 80% и, по существу, свободной от взаимосвязанных пор, разрушающих поверхность, причем внутренние поры заготовки заполнены воздухом.
6. Способ по п.4, отличающийся тем, что спрессованную заготовку покрывают смазочным материалом.
7. Способ по п.6, отличающийся тем, что смазочный материал представляет собой стекло, а нагрев заготовки проводят в инертной атмосфере.
8. Способ по п.7, отличающийся тем, что нагрев заготовки регулируют так, чтобы ее температура отличалась от точки бета-перехода титана не более чем на 100°С.
9. Способ по п.4, отличающийся тем, что при каждом проходе через валки прокатной клети уменьшают диаметр прокатанной пригодной для сварки ленты или проволоки на 5-35%.
10. Способ по п.9, отличающийся тем, что для снятия остаточных напряжений он включает также нагрев прокатанной проволоки в инертной атмосфере при температуре, при которой титан или легированный титан становится размягченным.
11. Способ по п.4, отличающийся тем, что исходную температуру заготовки во время экструзии выбирают не выше 1000°C.
12. Способ по п.4, отличающийся тем, что выходную температуру экструдата выбирают не выше 1000°C.
13. Способ по п.11 или 12, отличающийся тем, что экструдированный пруток имеет плотность более 98%.
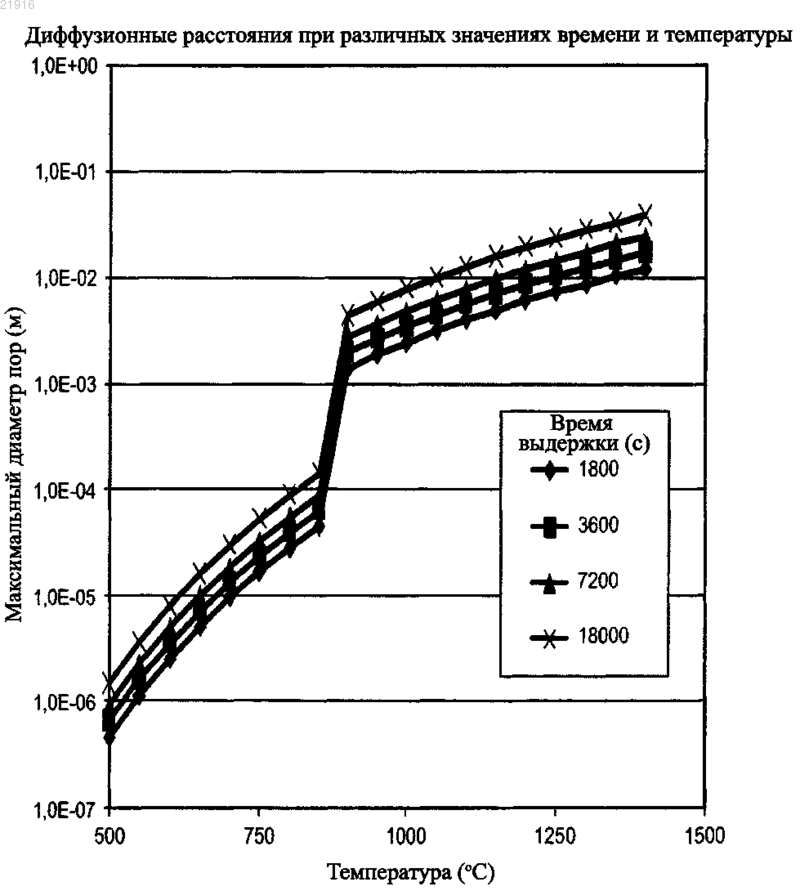
Текст
СПОСОБ ПРОИЗВОДСТВА ТИТАНОВОЙ СВАРОЧНОЙ ПРОВОЛОКИ Предложен способ производства пригодной для сварки проволоки из чистого или легированного титана. Способ характеризуется тем, что формирование проволоки производится посредством обработки твердофазного материала, включающей уплотнение, экструзию и прокатку, т.е. расплавления частиц, составляющих титановую губку, не происходит.(71)(73) Заявитель и патентовладелец: НОРСК ТИТАНИУМ КОМПОНЕНТС АС (NO) Область техники, к которой относится изобретение Изобретение относится к способу производства титановой проволоки, пригодной для сварки(далее - свариваемая проволока), реализуемому посредством холодного прессования, экструзии и прокатки титановой губки. Способ характеризуется тем, что уплотнение и формовку полностью проводят в твердом состоянии, не прибегая к расплавлению или инкапсулированию частиц титановой губки. Предшествующий уровень техники Титан и его сплавы проявляют отличные механические свойства и непревзойденную стойкость к коррозии. В настоящее время металлический титан получают, используя процесс Кролла (см. патентUS 2205854), согласно которому тетрахлорид титана (TiCl4) внутри большого стального реактора подвергают воздействию расплавленного металлического магния. В результате последующей вакуумной дистилляции при 1000C происходит удаление побочного продукта в виде избытков магния и хлорида магния, а в реакторе остается губчатая масса, представляющая собой пористый титан (так называемая"титановая губка"). Ее приходится извлекать принудительным образом, поскольку титан прилипает к стенкам реактора. Затем губку разрезают и измельчают с последующим просеиванием, чтобы получить фракцию с желаемым размером частиц (обычно 3-25 мм). Эти частицы губки смешивают с легирующими добавками, такими как Al, V, Fe, TiO2, Mo, Cr и другие подобные вещества, получая соответствующую легированную композицию. Полученные смеси расплавляют электронным пучком, плазменным факелом или подвергая воздействию вакуумной дуги с получением больших слитков, диаметр и вес которых достигают соответственно 1,5 м и 25 т. Данный производственный этап, с одной стороны, является капиталоемким. С другой стороны, из-за сегрегации во время отверждения содержание многих элементов приходится удерживать в строго контролируемых границах. Слитки нагревают до высоких температур, при которых их в типичном случае обрабатывают посредством ковки и прокатки в ходе нескольких производственных операций, чтобы сделать микроструктуру более тонкой и уменьшить площадь поперечного сечения. В результате получают промежуточный продукт в виде заготовок, прутков или плит. Анализ затрат, связанных с изготовлением титановой плиты толщиной 25,4 мм (1 дюйм), показал, что примерно 40% ее стоимости составляет цена сырьевого губчатого материала, а 60% приходится на последующие операции расплавления и прокатки. Высокая стоимость изготовления (включая отделочные операции) титановых деталей часто вытекает из практикуемой тщательной машинной обработки этих прокатанных продуктов для придания им конечной конфигурации. Дополнительными техническими приемами изготовления сводят к минимуму производственные потери, используя для этого последовательное формирование сложной детали из простого исходного материала, такого как титан в виде порошка или сварочной проволоки. Для всех приложений, за исключением наиболее экзотических вариантов, стоимость заготовки в виде порошка чрезмерно высока из-за проблем, возникающих при обращении с тонкоизмельченным термопластичным материалом с последующим загрязнением кислородом. Поэтому при выборе наиболее перспективного типа заготовки особое внимание было обращено на титановую проволоку. Для изготовления обычной титановой проволоки прутковую заготовку, полученную описанным методом, как правило, прокатывают до диаметра менее 10 мм и посредством волочения придают ей конечный размер, который для вариантов автоматической сварки обычно составляет 1-3 мм. С учетом потерь в выходе продукции, имеющих место во время последующих операций, повышение стоимости за счет трансформации титановой губки в пруток и далее - в свариваемую проволоку составляет главную часть суммарных затрат на производство проволоки. Альтернативные способы получения конечного свариваемого титанового материала, производимого посредством обработки твердой титановой губки (без промежуточного расплавления), столкнулись с проблемами подачи в процесс частиц пористой губки, имеющих неправильную форму. Как следствие,для обработки, не применяющей расплавление, потребовалось заменить легкодоступную титановую губку Кролла другими титановыми частицами.US 7311873 описывает способ изготовления плиты из мелкого порошка или из частиц, полученных посредством процесса Хантера (восстановление TiCl4 натрием), однако по стоимости титановых порошков и затратам данный процесс уступает аналогичным параметрам процесса Кролла, причем для процесса Хантера только 4% титановой губки представляют собой порошкообразные частицы с требуемыми размерами и формой. Титан, производимый электролитическим образом, поставлялся фирмой DuPont [1] и предназначался для последующей прокатки с получением плиты. Дендритная структура продукта, полученного электрическим методом, приводила к значительному захвату солей, что делало материал непригодным к свариванию и ухудшало его механические свойства. Позднее в качестве простого средства получения титановых порошков исследовалась гидрогенизация титановой губки. Хотя в данном случае исходным материалом является пластичная губка Кролла,конечный гидрид титана представляет собой хрупкое вещество, которое можно легко измельчить до частиц требуемого размера. Гидрид титана хорошо уплотнялся и после высокотемпературного вакуумного спекания для повышения плотности и удаления водорода из титана получалась заготовка, которую в дальнейшем можно было использовать таким же образом, как и обычный титан [2]. Однако процесс ва-1 021916 куумного спекания чрезмерно затратен, а остаточное загрязнение водородом, увеличение зерен при нагреве и захват кислорода ограничивают более широкое применение данного способа. Было показано [3], что прямая экструзия гидрированного/дегидрированного титана позволяет получить продукт с высокой плотностью (составляющей почти 100%), благодаря чему отпадает необходимость в горячем изостатическом прессовании, обычно необходимом для продуктов титановой порошковой металлургии. Однако в данном случае приходится проводить два процесса предварительного уплотнения, одним из которых является холодное изостатическое прессование, что создает проблемы, связанные с возможностью расширения масштабов такого процесса (в добавление к высоким концентрациям кислорода в исходном материале). Таким образом, попытки использовать альтернативные заготовки наталкиваются на ограниченную доступность и повышенную стоимость этих материалов и приводят к неприемлемым свойствам конечных продуктов. В результате естественные преимущества альтернативных процессов изготовления сводятся к нулю из-за отсутствия дешевого исходного материала. Сущность изобретения Главная задача, на решение которой направлено изобретение, состоит в разработке способа, предназначенного для производства заготовки для проволоки из чистого или легированного титана и требующего существенно меньшего количества этапов обработки, а также обеспечивающего повышенную ковкость конечного материала (проволоки). Другой задачей является разработка способа производства пригодной для сварки (свариваемой) проволоки из чистого или легированного титана, у которой при расплавлении и превращении в компонент, предназначенный для дополнительной обработки, химический состав и механические свойства сопоставимы с аналогичными параметрами обычной сварочной проволоки. Идея, заложенная в основу изобретения, заключается в том, что перечисленные проблемы, можно по меньшей мере частично, разрешить путем формирования свариваемой титановой проволоки, изготавливая ее из титановой губки и обрабатывая только в твердом состоянии, т.е. не прибегая к расплавлению любого из составляющих компонентов в какой-либо момент обработки. Таким образом, в своем первом аспекте изобретение относится к способу производства пригодной для сварки проволоки или ленты, полученной из чистого или легированного титана, причем способ по изобретению включает следующие этапы: помещают одну или более частиц титановой губки в камеру одноосного пресса; проводят холодное уплотнение образца материала, состоящего из частиц, в атмосфере наружного воздуха с формированием заготовки; нагревают заготовку до температуры 400-1000C; помещают нагретую заготовку в камеру предварительно нагретого пресса для горячей экструзии и экструдируют из заготовки пруток или профиль при температуре 400-1000C; удаляют поверхностные загрязнения с экструдированного прутка или профиля и помещают экструдированный пруток или профиль на прокатный стан, имеющий одну или более прокатных клетей, расположенных последовательно, чтобы сформировать свариваемую ленту или свариваемую проволоку с требуемым диаметром Настоящее изобретение предлагает способ и продукт, использующие при своей реализации имеющуюся в продаже титановую губку (титановую губку Кролла) без предварительного видоизменения ее частиц. Целью такой реализации является получение заготовки для титановой проволоки при условии существенно меньшего количества этапов обработки, а также повышения гибкости в отношении конечного состава проволоки. Кроме того, изобретение обеспечивает получение свариваемой проволоки, у которой при расплавлении и превращении, посредством дополнительной обработки, в требуемый компонент химический состав и механические свойства сопоставимы с аналогичными параметрами обычной сварочной проволоки. Предусмотрена возможность использования в рамках изобретения любой известной титановой губки, причем для получения ее частиц куски увеличенного размера в желательном варианте можно измельчить или разрезать. Размер частиц может лежать в любом интервале, ограниченном размером, выбранным из ряда 1, 2, 3, 4 и 5 мм, и размером, выбранным из ряда 10, 15, 20, 25, 30, 35, 40, 45, 50, 55, 60, 65,70, 75, 80, 85, 90, 95 и 100 мм. Предпочтительны интервалы 1-100 мм, 2-50 мм и 3-25 мм. В данном описании для конкретного интервала термин "размер частиц фракции" соотносится с размером отверстий сита, используемого для классификации частиц, т.е. размер частиц фракции, лежащий в интервале, например, 1-100 мм, следует трактовать в том смысле, что частицы достаточно велики, чтобы задерживаться на сите с размером отверстий 1 мм, но достаточно малы, чтобы проходить через сито с размером отверстий 100 мм. Одним из примеров губки, пригодной для данного случая, является дистиллированная в вакууме титановая губка с уменьшенным содержанием магния, удовлетворяющая требованиям стандартаASTM B299-07 [4]. Преимущество такой губки заключается в высокой рыночной доступности и в низких уровнях остаточных примесей. При использовании доступной титановой губки такого качества способ по изобретению позволяет получить титановые проволоки, содержащие менее 0,25% кислорода, менее 0,03% азота, менее 0,08% углерода и менее 0,015% водорода. Предпочтительным можно признать вариант с проведением холодного уплотнения титановой губки следующим образом. Частицы титановой губки при комнатной температуре, не прибегая к каким-либо дополнительным обработкам или воздействиям типа просеивания, вторичного дробления, перевода в сферическую форму или очистки, загружают в камеру одноосного пресса, у которого дно контейнера герметизировано, чтобы предотвратить проваливание частиц через пресс. Заполнение камеры проводят в атмосфере окружающей среды, поскольку применение очищенного от кислорода инертного газа (или нескольких таких газов) во время холодного уплотнения приводит к удерживанию газа/газов в уплотненной заготовке между частицами губки. Инкапсулирующий инертный газ придает конечному продукту пористость, так как инертные газы проявляют нулевую растворимость в титане. В инкапсулировании заготовки, состоящей из титановой губки, нет необходимости, поскольку уровни содержания исходных составляющих компонентов в виде магния, хлорида магния и кислорода невелики, а уплотнение происходит при низких температурах порядка комнатной температуры. Поэтому из процесса обработки исключаются дорогостоящие операции консервации и обезгаживания, а уплотненной заготовкой можно манипулировать таким же образом, как и обычным титаном, полученным путем механической обработки отливок. Пресс-шток пресса опускают медленно, чтобы дать возможность воздуху выйти из пористой заготовки во время ее медленного сжимания и уплотнения. Так, из титановой губки можно получить заготовку, обладающую высокой плотностью, причем открытая пористость данной заготовки, разрушающая поверхность, пренебрежимо мала. Повышенные плотности желательны, поскольку они позволяют уменьшить дефекты поверхности и внутренние пустоты (хотя полное уплотнение не позволяет получить ограниченные возможности пресса). Затем уплотненную заготовку (далее именуемую просто "заготовкой") извлекают из пресса. Конкретным примером холодного уплотнения изобретение не ограничено, и для холодного уплотнения титановой губки с превращением ее в заготовку с высокой плотностью и пренебрежимо малой открытой пористостью, разрушающей поверхность, можно использовать любой известный или возможный процесс такого назначения. Желательно предусмотреть возможность покрытия заготовки после прессования смазочным материалом, способствующим процессу экструзии. Для экструдирования титановых заготовок пригоден любой реально существующий смазочный материал, известный специалистам в этой области, или еще не реализованный материал. Одним из возможных примеров является стеклянный смазочный материал (далее - стекло). Возможна ситуация, в которой желательно провести нагрев заготовки в инертной атмосфере, причем это может относиться к каждому этапу обработки, на котором заготовка находится при температуре выше 400C. Хотя нагрев заготовки может быть ограничен любой температурой в интервале 400-1000C,желательно использовать температуру, отличающуюся от точки бета-перехода титана не более чем на 100 С. Горячую экструзию уплотненной титановой заготовки можно провести следующим образом. Чтобы свести к минимуму износ экструзионной головки и поглотить загрязнения, поступающие из атмосферы,желательно предусмотреть возможность покрытия заготовки стеклянным смазочным материалом. Заготовку нагревают (предпочтительно в инертной атмосфере или в вакууме) таким образом, чтобы захваченные кислород и азот, образовавшиеся в ходе процесса холодного уплотнения, поглотились, как в матрице, в объеме титана. Такое поглощение приводит к рассасыванию внутренней пористости, а также,возможно, к закрыванию и слиянию внутренних пор. Исходя из максимально допустимого содержания примесей, внедренных в конечный продукт в виде проволоки, и из химического анализа титановой губки, можно приблизительно вычислить максимальный размер пор, используя для этого диффузные свойства уловленных газовых фракций (азот, кислород) воздуха при различных температурах и различных значениях времени выдержки. Если задать время выдержки при 900C, например, равным 1 ч, во время последующего нагрева до момента экструзии титановой заготовкой поглотится заполненная воздухом полость диаметром примерно 2 мм. Результаты вычислений для набора температур и различных значений времени выдержки собраны в табл. 1, а на фиг. 1 представлены в виде графиков. Таблица 1 Вычисленные значения максимальных размеров (в метрах) пор,заполненных воздухом и поглощенных во время нагрева при различных температурах и различных значениях времени нагрева Размеры пор в табл. 1 вычислены согласно формуле где Р - размер пор, в м;t - время, в с. При температурах ниже и выше уровня бета-перехода (882C) коэффициент массовой диффузии определяется соответственно, как Коэффициент массовой диффузии получен из публикации R.J. Wasilewsky, G.L. Kehl (1954), "DIFFUSION OF NITROGEN AND OXIGEN IN TITANIUM", J. Inst. Metals, vol. 83 и выбран равным коэффициенту массовой диффузии для азота, поскольку этот элемент наиболее распространен в воздухе и, как известно, диффундирует в титане медленнее кислорода. Для сведения загрязнений, поступающих из атмосферы, к минимуму желательно проводить нагрев уплотненной заготовки в инертной среде, однако в случае использования стеклянных покрытий в этом нет необходимости. Предпочтительно выбрать температуру предварительного нагрева заготовки вблизи точки бета-перехода титана, так как в более высокотемпературной бета-фазе диффузия кислорода и азота увеличивается примерно на порядок своей величины по сравнению с низкотемпературной аллотропической альфа-фазой. В дополнение к сказанному, плотность уплотненной заготовки, превышающая плотность исходных частиц губки, обеспечивает существенный диффузионный барьер на пути массопередачи газообразных примесей. На практике это означает, что во время экструзии как исходная температура заготовки, так и ее температура на выходе не должны превышать 1000C. После экструзии плотность прутка может увеличиться до 98%. В предварительно нагретую камеру экструзионного пресса заготовку следует переносить без задержки. Для предотвращения быстрого охлаждения титановой заготовки камеру и головку экструдера необходимо нагреть, поскольку такое охлаждение может привести к неоправданно высоким давлениям при экструзии. Пресс-шток экструзионного пресса прикладывает повышенное усилие к тыльной стороне заготовки, производя почти полное уплотнение. По мере увеличения давления материал заготовки начинает просачиваться через экструзионную головку, образуя экструдированное изделие типа прутка или профиля. Скорость вытеснения экструдируемого материала (известная также под названиями "скорость экструзии" и "скорость экструзионного пресса") пропорциональна соотношению площадей поперечного сечения заготовки и прутка. Кроме того, чтобы гарантировать отсутствие дефектов чистоты поверхности экструдированного титана, экструзионная головка должна иметь правильно выбранные конфигурации входа и выхода. Может оказаться желательным очистить поверхность экструдированного титана от загрязнений и навить изделие в форме спирали, пока оно не остыло. Это облегчит последующие операции и хранение. Затем, чтобы уменьшить диаметр экструдата, экструдированный материал переносят на прокатный стан. Желательно, чтобы каждый проход через валки обеспечивал уменьшение диаметра на 5-35%. Процесс прокатки продолжают до тех пор, пока проволока не приобретет окончательные размер и форму. Предпочтительно иметь возможность проводить этот процесс на прокатном стане непрерывного действия, который оборудован несколькими последовательно установленными прокатными клетями. В таком варианте уменьшение диаметра подаваемого материала происходит непрерывно и существенным образом. Профиль поперечного сечения проволоки задается размером и формой проточек (ручьев), выполненных в валках прокатной клети, и во время цикла прокатки может изменяться. Например, предусмотрена возможность, пропуская через валки с полукруглой проточкой четырех-, шести или восьмигранные прутки, получать круглую проволоку, причем возможен и процесс обратного характера. Промежуточное снятие остаточных напряжений проводят, выдерживая проволоку в нагретой печи, предпочтительно заполненной инертным газом, в условиях, содействующих достаточной рекристаллизации с последующим размягчением. После такой термической обработки, но до сматывания проволоки желательно осуществить по меньшей мере один проход через валки, чтобы придать готовой проволоке жесткость, достаточную для пропускания ее через серийные механизмы автоматической подачи сварочной проволоки. Перечень чертежей На фиг. 1 представлены расчетные максимальные размеры пор, заполненных воздухом и поглощаемых во время нагрева, для различных температур и различных времен нагрева. На фиг. 2 представлены фотографии макроструктуры заготовки соответственно до предварительного нагрева (а) и после него (b). Сведения, подтверждающие возможность осуществления изобретения Далее изобретение будет описано более подробно на примерах вариантов его осуществления. Пример 3,5 кг частиц титановой губки перенесли на воздухе в камеру одноосного гидравлического пресса,размерный параметр которой составляет 100 мм. Прикладывая давление примерно 1000 МПа, провели уплотнение частиц титановой губки, превратив их в заготовку высотой примерно 10 мм, что отвечает уплотнению до уровня 95%. Затем данную заготовку покрыли стеклянным смазочным материалом, поместили на 60 мин в печь, заполненную аргоном, и выдержали в ней при 900C. Макроструктура заготовки до и после такой термической обработки показана соответственно на фиг. 2 а и 2b. Нагретую заготовку перенесли в одноосный экструзионный пресс и экструдировали через экструдер с размерным параметром 18 мм при постоянной скорости сдавливания 12 мм/с, выбрав степень вытяжки, равную 22. Затем экструдированный пруток пропустили через несколько расположенных последовательно прокатных клетей. В результате исходный диаметр (диаметр прутка, поступающего в первую клеть) последовательно уменьшили перед вторым проходом до промежуточных значений 7, 6,5, 5,7, 5,1,4,5, 4,1, 3,7, 3,4, 3,0 мм, а затем через значения 2,83, 2,71, 2,52, 2,35, 2,15, 2,00, 1,83, 1,70, 1,61 и 1,5 мм довели до окончательного значения 1,6 мм. Снятие остаточных напряжений проводили при 540C в течение 30 мин между получением диаметров 4,1 и 3,7 мм. Провели анализ химического состава произведенной таким образом проволоки. Полученные результаты в виде содержаний примесей представлены в табл. 2. Затем, чтобы оценить способность данной проволоки к свариванию, ее расплавили в сварочной горелке типа TIG, использующей экранирующую завесу из инертного газа, конкретно, поток аргона (22 л/мин). Сформировали несколько наплавных валиков, образующих монолитную структуру, которую затем разделили на секции для химического анализа и механических испытаний. Таким образом, путем объединения частиц титановой губки без использования плавления получили свариваемую нелегированную титановую проволоку с приемлемым химическим составом, сопоставленную в табл. 2 со стандартной проволокой Grade 2 Commercial Purity (СР) Titanium. В данной таблице представлены данные по проволоке как в ее исходном состоянии, так и после применения в качестве материала-наполнителя сварного шва. Таблица 2 Химический состав и механические свойства уплотненной нелегированной проволоки и соответствующего сварного шваWest Conshohocken, PA 2007, DOI: 10.1520/B0299-07. ФОРМУЛА ИЗОБРЕТЕНИЯ 1. Способ производства пригодной для сварки проволоки или пригодной для сварки ленты из титана, состоящий из следующих этапов: помещают одну или более частиц титановой губки в камеру одноосного пресса,проводят холодное уплотнение помещенного в камеру материала, состоящего из частиц, в атмосфере наружного воздуха, чтобы сформировать заготовку,нагревают заготовку до температуры 400-1000C,помещают нагретую заготовку в камеру предварительно нагретого пресса для горячей экструзии и при температуре 400-1000C экструдируют из заготовки пруток или профиль,удаляют поверхностные загрязнения с указанного прутка или профиля и помещают указанный пруток или профиль на прокатный стан, имеющий одну или более прокатных клетей, расположенных последовательно, чтобы сформировать пригодную для сварки ленту или проволоку с требуемым диаметром 2. Способ по п.1, отличающийся тем, что частицы титановой губки представляют собой измельченную и разрезанную титановую губку с пониженным содержанием магния, которая удовлетворяет требованиям стандарта ASTM B299-07. 3. Способ по п.2, отличающийся тем, что измельченная и разрезанная титановая губка содержит фракцию с размером частиц 1-100 мм, предпочтительно 2-50 мм, более предпочтительно 3-25 мм. 4. Способ по любому из пп.1-3, отличающийся тем, что холодное уплотнение образца материала,состоящего из частиц, проводят при комнатной температуре с приложением к образцу уплотняющего давления 200-600 МПа. 5. Способ по п.4, отличающийся тем, что уплотнение осуществляют до тех пор, пока частицы образца не объединятся до состояния твердой компактной заготовки с плотностью более 80% и, по сущест-6 021916 ву, свободной от взаимосвязанных пор, разрушающих поверхность, причем внутренние поры заготовки заполнены воздухом. 6. Способ по п.4, отличающийся тем, что спрессованную заготовку покрывают смазочным материалом. 7. Способ по п.6, отличающийся тем, что смазочный материал представляет собой стекло, а нагрев заготовки проводят в инертной атмосфере. 8. Способ по п.7, отличающийся тем, что нагрев заготовки регулируют так, чтобы ее температура отличалась от точки бета-перехода титана не более чем на 100 С. 9. Способ по п.4, отличающийся тем, что при каждом проходе через валки прокатной клети уменьшают диаметр прокатанной пригодной для сварки ленты или проволоки на 5-35%. 10. Способ по п.9, отличающийся тем, что для снятия остаточных напряжений он включает также нагрев прокатанной проволоки в инертной атмосфере при температуре, при которой титан или легированный титан становится размягченным. 11. Способ по п.4, отличающийся тем, что исходную температуру заготовки во время экструзии выбирают не выше 1000C. 12. Способ по п.4, отличающийся тем, что выходную температуру экструдата выбирают не выше 1000C. 13. Способ по п.11 или 12, отличающийся тем, что экструдированный пруток имеет плотность более 98%.
МПК / Метки
МПК: B23K 35/32, B22F 3/02, C22F 1/18, C22C 14/00, B21B 1/16
Метки: способ, титановой, производства, сварочной, проволоки
Код ссылки
<a href="https://eas.patents.su/9-21916-sposob-proizvodstva-titanovojj-svarochnojj-provoloki.html" rel="bookmark" title="База патентов Евразийского Союза">Способ производства титановой сварочной проволоки</a>