Способ и установка для получения оксида металла из гидроксида металла
Номер патента: 19025
Опубликовано: 30.12.2013
Авторы: Шмидбауер Эрвин, Ярцембовски Ян, Миссалла Михаель, Шнайдер Гюнтер
Формула / Реферат
1. Способ получения оксида металла из гидроксида металла, в частности из гидроксида алюминия, где гидроксид металла сушат в сушилке, подогревают по меньшей мере в одной ступени предварительного нагрева и обжигают до оксида металла в реакторе с псевдоожиженным слоем, причем затем полученный оксид металла охлаждают, отличающийся тем, что перед сушкой гидроксид металла очищают по меньшей мере в одном фильтре, а пар, полученный в сушилке, направляют в фильтр.
2. Способ по п.1, отличающийся тем, что гидроксид металла, подлежащий сушке, псевдоожижают в сушилке.
3. Способ по п.2, отличающийся тем, что гидроксид металла, подлежащий сушке, псевдоожижают в сушилке посредством подачи псевдоожижающего газа.
4. Способ по п.2 или 3, отличающийся тем, что гидроксид металла, подлежащий сушке, псевдоожижают в сушилке с помощью пара, полученного во время сушки.
5. Способ по любому из пп.1-4, отличающийся тем, что в сушилку подают предпочтительно жидкую теплопередающую среду, с помощью которой гидроксид металла нагревают косвенным путем, а жидкую теплопередающую среду нагревают в косвенном охладителе, предусмотренном после реактора с псевдоожиженным слоем.
6. Способ по п.5, отличающийся тем, что осуществляют циркуляцию теплопередающей среды между сушилкой и косвенным охладителем.
7. Способ по п.5 или 6, отличающийся тем, что в сушилку подают теплопередающую среду с температурой от 130 до 220°С.
8. Способ по любому из пп.1-7, отличающийся тем, что часть потока гидроксида металла направляют мимо сушилки.
9. Установка для осуществления способа по любому из пп.1-8, включающая сушилку (60) для сушки гидроксида металла, по меньшей мере один подогреватель (4) для предварительного нагрева гидроксида металла, реактор (20) для обжига гидроксида металла до оксида металла и по меньшей мере одно охлаждающее приспособление (28, 29, 30, 31, 32, 33) для охлаждения полученного оксида металла, отличающаяся тем, что перед сушилкой (60) предусмотрен фильтр (50) для фильтрования гидроксида металла, и тем, что трубопровод (53) для отходящего газа из сушилки (60) соединен с фильтром (50).
10. Установка по п.9, отличающаяся тем, что фильтр (50) включает кожух (52) для подвода пара, и тем, что трубопровод (53) для отходящего газа из сушилки (60) открывается в кожух (52) для подвода пара.
11. Установка по п.9 или 10, отличающаяся тем, что в сушилке (60) предусмотрены теплообменные трубы (61) для теплопередающей среды.
12. Установка по п.11, отличающаяся тем, что теплообменные трубы (61) объединены во множество пучков труб теплообменника, которые можно по отдельности извлекать из корпуса (63) сушилки (60) через выдвижные блоки (62а-с).
13. Установка по п.11 или 12, отличающаяся тем, что охлаждающее приспособление для оксида металла включает многоступенчатый охладитель (36) для косвенного охлаждения оксида металла, и тем, что теплообменные трубы (61) сушилки (60) соединены с первой ступенью (36а) косвенного охладителя (36) через циркуляционный трубопровод (37) для теплопередающей среды.
14. Установка по любому из пп.9-13, отличающаяся наличием обводного трубопровода (5) вокруг сушилки (60), который соединен с первой ступенью предварительного нагрева.
15. Установка по п.14, отличающаяся наличием регулирующего клапана (6) для разделения потока гидрата между сушилкой (60) и обводным трубопроводом (5).
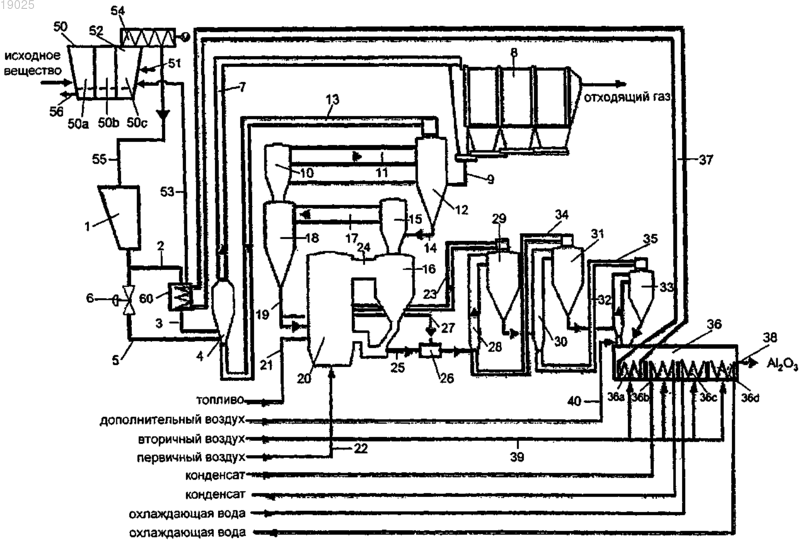
Текст
СПОСОБ И УСТАНОВКА ДЛЯ ПОЛУЧЕНИЯ ОКСИДА МЕТАЛЛА ИЗ ГИДРОКСИДА МЕТАЛЛА Изобретение относится к получению оксида металла из гидроксида металла, в частности из гидроксида алюминия, где гидроксид металла сушат в сушилке, подогревают по меньшей мере в одной ступени предварительного нагрева и обжигают до оксида металла в реакторе с псевдоожиженным слоем, причем затем полученный оксид металла охлаждают. Для снижения потребления энергии обжиговой установкой гидроксид металла перед сушкой очищают по меньшей мере в одном фильтре, а пар, образовавшийся в сушилке, направляют в фильтр. Настоящее изобретение относится к получению оксида металла из гидроксида металла или из других солей металла, в частности из гидроксида алюминия, где гидроксид металла сушат в сушилке, подогревают по меньшей мере в одной ступени предварительного нагрева и обжигают до оксида металла в реакторе с псевдоожиженным слоем, причем затем полученный оксид металла охлаждают. Гидроксиды металлов являются сырьем для получения оксидов металлов, которые представляют собой важное исходное вещество в неорганической химии. В природных месторождениях гидроксиды металлов в основном присутствуют в смешанной форме, так что сырье необходимо очищать. В случае получения гидроксида алюминия очистку осуществляют с помощью так называемого способа Байера, в котором добытые минералы, главным образом боксит, измельчают и пропитывают раствором гидроксида натрия. Нерастворимые остатки, такие как красный шлам, который содержит в основном оксид железа, таким образом, можно отделить от растворенного гидрата алюминия с помощью фильтрования. С помощью кристаллизации и дальнейшего фильтрования из данного раствора получают чистый гидроксид алюминия (Al(OH)3). Способ получения оксида алюминия (Al2O3) из гидроксида алюминия известен, например, из патентов ЕР 0861208 В 1 или DE 102007014435 А 1. Влажный гидроксид алюминия сначала сушат в первом циклонном теплообменнике и подогревают до температуры приблизительно 160 С. После отделения в циклонном сепараторе твердые частицы подают во второй циклонный подогреватель, в котором их дополнительно сушат отходящим газом из рециркуляционного циклона для циркулирующего псевдоожиженного слоя, а затем загружают в циркулирующий псевдоожиженный слой реактора с псевдоожиженным слоем. В реакторе с псевдоожиженным слоем гидроксид алюминия обжигают до оксида алюминия при температуре приблизительно 1000 С. Часть потока подогретого гидроксида алюминия отделяют после первого циклонного подогревателя (ЕР 0861208 В 1) или после второго циклонного подогревателя(DE 102007014435 А 1) и смешивают с горячим оксидом алюминия, извлеченным из рециркуляционного циклона для циркулирующего псевдоожиженного слоя. Затем горячую смесь продуктов охлаждают в многоступенчатом циклонном охладителе при прямом контакте с воздухом, а затем подают в охладитель с псевдоожиженным слоем для окончательного охлаждения. Из патента ЕР 0245751 В 1 известен способ осуществления эндотермических процессов в тонкоизмельченных твердых веществах, с помощью которого тепло, получаемое в процессе в целом, используют лучшим образом. Во время обжига гидроксида алюминия часть потока исходного материала подают в нагретый косвенным путем подогреватель для сушки, а затем вводят в электростатический осадитель вместе с подаваемым напрямую исходным сырьем. Затем твердые частицы подают из электростатического осадителя через две последовательно соединенные подогревающие системы в циркулирующий псевдоожиженный слой, в котором твердые частицы псевдоожижают с помощью псевдоожижающего газа (первичного воздуха) и обжигают при температурах приблизительно 1000 С. Поток твердых частиц,которые извлекают из циркулирующего псевдоожиженного слоя, охлаждают в косвенном охладителе с псевдоожиженным слоем, образующим первую ступень охлаждения, а затем подают во вторую и третью ступени охлаждения, каждая из которых также представляет собой охладитель с псевдоожиженным слоем, чтобы дополнительно охладить твердый продукт. Первичный воздух, нагретый в первом охладителе с псевдоожиженным слоем, вводят в реактор с псевдоожиженным слоем в качестве псевдоожижающего воздуха с температурой 520 С, тогда как псевдоожижающий воздух из охладителей с псевдоожиженным слоем подают в реактор с псевдоожиженным слоем в качестве вторичного воздуха с температурой 670 С. Теплопередающую среду из второго охладителя с псевдоожиженным слоем подают в косвенный подогреватель для исходного материала в качестве нагревающей среды с температурой 200 С, а затем направляют обратно во впускное отверстие второго охладителя с псевдоожиженным слоем после охлаждения до 160 С. После очистки в электростатическом осадителе отходящий газ из подогревателя, служащего сушилкой для подаваемого гидрата, выпускают в окружающую среду. Обжиг гидроксида алюминия требует очень много энергии. Традиционные способы требуют потребления энергии приблизительно 3000 кДж на 1 кг полученного оксида алюминия. Задачей данного изобретения является снижение потребления энергии обжиговой установкой и уменьшение разрушения зерен, в частности, при сушке гидрата. Согласно настоящему изобретению данную задачу, по существу, решают с помощью способа, отличительные признаки которого изложены в п.1 формулы изобретения, в котором перед сушкой гидроксид металла очищают в фильтре, а пар, образовавшийся в сушилке, направляют в фильтр. Посредством направления пара в фильтр увеличивают температуру в нем, чтобы достичь более интенсивной сушки гидроксида металла (гидрата). Таким образом, можно увеличить поток массы гидрата в сушилку, так что можно снизить удельное потребление энергии установкой. Согласно предпочтительному воплощению данного изобретения гидроксид металла, подлежащий сушке, псевдоожижают в сушилке, чтобы увеличить теплопередачу и, таким образом, по возможности минимизировать поверхность теплообмена. Согласно данному изобретению псевдоожижение осуществляют путем подачи псевдоожижающего газа, например воздуха. Однако согласно воплощению данного изобретения, чтобы снизить содержание воздуха в отходящем газе из сушилки, подачу псевдоожижающего газа можно также уменьшить или даже полностью перекрыть. Гидрат псевдоожижается сам в результате испарения поверхностной воды. Согласно данному изобретению в сушилку подают предпочтительно жидкую теплопередающую среду, например теплопередающее масло или предпочтительно воду, с помощью которой гидроксид металла нагревают косвенным путем, а данную жидкую теплопередающую среду нагревают в ступени косвенного охлаждения, например в охладителе с псевдоожиженным слоем или во вращающемся охладителе, предусмотренном после реактора с псевдоожиженным слоем. Согласно воплощению данного изобретения осуществляют циркуляцию теплопередающей среды между ступенью косвенного охлаждения и сушилкой, так что дополнительную теплопередающую среду подавать не нужно. На стадии охлаждения имеется в наличии достаточное количество энергии, чтобы нагреть теплопередающую среду и достичь эффективной сушки. В то же время, перенос энергии между стадиями охлаждения и сушки регулируют в зависимости от количества и влажности гидроксида алюминия, чтобы достичь большей гибкости в управлении установкой и снизить потребление энергии. Согласно данному изобретению в сушилку подают теплопередающую среду с температурой от 130 до 220 С, предпочтительно от 150 до 200 С, в частности от 170 до 190 С. Посредством медленной сушки гидрата при низкой температуре уменьшают нагрузку на частицы гидрата и, следовательно, снижают вероятность их разрушения. Согласно особенно предпочтительному воплощению данного изобретения часть потока гидрата направляют мимо сушилки. Таким образом, можно реагировать на различное содержание влаги в гидрате. В то же время, можно регулировать температуру отходящего газа. Согласно данному изобретению температуру отходящего газа можно снизить до 110-170 С, предпочтительно до 120-140 С, чтобы понизить потери энергии, связанные с выпуском отходящего газа через дымовую трубу после прохождения через фильтр. Данное изобретение также относится к установке для получения оксида металла из гидроксида металла, которая пригодна для осуществления описанного выше способа. Установка включает сушилку для сушки гидроксида металла, по меньшей мере один подогреватель для предварительного нагрева гидроксида металла, реактор для обжига гидроксида металла до оксида металла и по меньшей мере одно охлаждающее приспособление для охлаждения полученного оксида металла. Согласно данному изобретению перед сушилкой предусмотрен по меньшей мере один фильтр для фильтрования гидроксида металла, причем трубопровод для отходящего газа из сушилки соединен с данным фильтром. Предпочтительно фильтр включает кожух для подвода пара, в который открывается трубопровод для отходящего газа из сушилки. Отходящий газ, главным образом пар, который подают из сушилки,может увеличить температуру в фильтре и, таким образом, достичь более интенсивной сушки гидрата. Согласно данному изобретению теплопередающая среда проходит через сушилку по циркуляционным трубопроводам, причем циркуляционные трубопроводы предпочтительно соединены с первой ступенью косвенного охладителя после реактора с псевдоожиженным слоем. Таким образом, тепло, регенерированное в процессе, можно эффективно использовать для сушки гидрата, а потребление энергии установкой можно дополнительно снизить. Простого технического обслуживания и соответствия установки предъявляемым требованиям можно достичь согласно воплощению данного изобретения, в котором циркуляционные трубопроводы объединены во множество пучков труб теплообменника, которые можно по отдельности извлекать из корпуса сушилки. Согласно одному из воплощений данного изобретения вокруг сушилки для гидрата предусмотрен обводной трубопровод, который соединен с первой ступенью предварительного нагрева, чтобы можно было подавать часть потока гидрата прямо в первую ступень предварительного нагрева. Согласно данному изобретению разделение потока гидрата между сушилкой для гидрата и обводным трубопроводом осуществляют с помощью регулирующего клапана, который предпочтительно приводят в действие в зависимости от температуры отходящего газа. Дополнительные воплощения, преимущества и возможные применения данного изобретения также можно узнать из последующего описания воплощения и чертежа. Все описанные и/или проиллюстрированные характерные особенности, сами по себе или в любом сочетании, образуют предмет настоящего изобретения, независимо от их включения в формулу изобретения или от обратной ссылки на них. На чертежах: фиг. 1 представляет собой схематическое изображение установки для осуществления способа по данному изобретению; фиг. 2 представляет собой схематическое изображение сушилки для гидроксида металла; а фиг. 3 представляет собой вид в перспективе сушилки для гидроксида металла. Согласно технологической схеме способа по данному изобретению, которая изображена на чертеже, исходное вещество, в частности осадок гидроксида алюминия, загружают в многоступенчатое фильтровальное приспособление 50 (фильтр для гидрата), в котором гидроксид алюминия (Al(OH)3) промывают промывочной водой или промывочной жидкостью, которую подают через трубопровод 51 и направляют в противотоке по отношению к осадку гидрата, чтобы достичь требуемой чистоты продукта. Промывочную жидкость сливают из камеры 50 а фильтра 50 для гидрата через трубопровод 56. В кожух 52 для подвода пара последней ступени 50 с фильтра 50 для гидрата вводят пар через трубопровод 53,чтобы увеличить температуру и тем самым обеспечить дополнительную сушку гидрата. Таким образом,влажность гидрата, который выпускают через разгрузочный шнек 54, можно снизить с обычных 7% до 36%. Затем отфильтрованный влажный гидроксид алюминия через трубопровод 55 подают в загрузочную станцию 1 и через трубопровод 2 вводят в сушилку 60 (сушилку для гидрата), в которой гидрат нагревают до температуры приблизительно 100-110 С путем косвенного теплообмена с жидкой теплопередающей средой, в частности водой, и сушат почти полностью. Затем высушенный гидрат через трубопровод 3 подают в циклонный теплообменник 4 первой ступени предварительного нагрева и подогревают до температуры 100-200 С. Регулирование температуры в сушилке 60 для гидрата осуществляют в зависимости от влажности подаваемого гидрата, так что можно быстро реагировать на отклонения свойств исходного вещества без снижения энергоэффективности установки. Часть потока гидрата можно подавать через обводной трубопровод 5 мимо сушилки 60 для гидрата прямо в циклонный теплообменник 4. Величину данной части потока регулируют с помощью регулирующего клапана 6, который может располагаться в трубопроводе 2 или в обводном трубопроводе 5. Регулирование обходного потока осуществляют в зависимости от температуры отходящего газа, чтобы по возможности минимизировать потери энергии. Если большее количество гидрата проходит через сушилку 60 для гидрата, то температура отходящего газа из циклонного теплообменника 4 увеличивается,поскольку в сушилке 60 для гидрата удаляют больше влаги (воды) и она не испаряется в последующем циклонном теплообменнике 4. Когда в сушилку 60 для гидрата подают малое количество гидрата, большее количество влажного гидрата подают в циклонный теплообменник 4 и температура отходящего газа соответственно уменьшается. Поток отходящего газа, поступающий из второй ступени предварительного нагрева, увлекает твердые частицы, введенные в циклонный теплообменник 4, нагревает их и пневматически вводит их через трубопровод 7 во впускную область электростатического газоочистителя (электростатического осадителя) 8, который представляет собой предварительный сепаратор. В электростатическом осадителе 8 газ очищают и выпускают в дымовую трубу, которая не показана, с температурой от 110 до 170 С, предпочтительно от 120 до 140 С. В результате уменьшения количества воды из влажного гидрата в отходящем газе благодаря вышерасположенной сушилке 60 для гидрата, отсутствует опасность конденсации воды на частях установки, несмотря на такую низкую температуру. Благодаря отсутствию конденсации избегают коррозии в установке. Через трубопровод 9 твердые частицы, выходящие из электростатического газоочистителя 8, подают во второй циклонный теплообменник 10 второй ступени предварительного нагрева, в котором поток газа, выходящий из третьей ступени предварительного нагрева, увлекает твердые частицы, нагревает их до температуры 150-300 С и подает их в разделительный циклон 12 через трубопровод 11. Через трубопровод 13 поток отходящего газа из разделительного циклона 12 подают в циклонный теплообменник 4,чтобы нагреть гидрат и доставить его в электростатический осадитель 8. Через трубопровод 14 твердые частицы из разделительного циклона 12 подают в третий циклонный теплообменник 15 (третью ступень предварительного нагрева), где их увлекает поток газа, выходящий из рециркуляционного циклона 16 для циркулирующего псевдоожиженного слоя, и дополнительно обезвоживают при температурах от 200 до 450 С, в частности от 250 до 370 С, и, по меньшей мере, частично дегидратируют (предварительно обжигают) до моногидрата алюминия (AlOOH). Через трубопровод 17 поток газа и твердых частиц подают в разделительный циклон 18, в котором,в свою очередь, осуществляют разделение потока газа и твердых частиц, причем твердые частицы выпускают вниз через трубопровод 19, а отходящий газ вводят во второй циклонный теплообменник 10 второй ступени предварительного нагрева. Таким образом, во второй и особенно в третьей ступени предварительного нагрева осуществляют предварительный обжиг гидроксида металла. Предварительный обжиг в смысле настоящего изобретения подразумевает частичную дегидратацию или удаление таких соединений, как HCl и NOx. С другой стороны, обжиг относится к полной дегидратации или к удалению таких соединений, как SO2. Гидроксиды металла в смысле данного изобретения предпочтительно представляют собой гидроксиды металла или карбонаты металла, в частности гидроксид алюминия. Однако данное изобретение не ограничено данными гидроксидами металла и его можно применять для всех соединений, в частности соединений металлов, которые перед термообработкой подвергают отделению жидкости, например, также для силикатов. После разделительного циклона 18, примыкающего к третьему циклонному теплообменнику 15,поток твердых частиц разделяют с помощью устройства, описанного, например, в патенте DE 102007014435 А 1. Через трубопровод 19 основной поток, содержащий приблизительно 80-90% потока твердых частиц, подают в реактор 20 с псевдоожиженным слоем, в котором моногидрат алюминия обжигают при температурах от 850 до 1100 С, в частности приблизительно 950 С, и дегидратируют до оксида алюминия (Al2O3). Подачу топлива, требующегося для обжига, осуществляют через топливный трубопровод 21, который расположен на малой высоте над колосниковой решеткой реактора 20 с псевдоожиженным слоем. Потоки кислородсодержащего газа, требующегося для горения, подают в качестве псевдоожижающего газа (первичного воздуха) через подающий трубопровод 22 и в качестве вторичного воздуха через подающий трубопровод 23. Благодаря подаче газа достигают относительно высокой плотности суспензии в нижней области реактора между колосниковой решеткой и местом подачи 23 вторичного газа и относительно низкой плотности суспензии над местом подачи 23 вторичного газа. После обычного сжатия первичный воздух с температурой приблизительно 90 С без дополнительного нагрева подают в реактор 20 с псевдоожиженным слоем. Температура вторичного воздуха составляет приблизительно 550 С. Через соединительный трубопровод 24 суспензия газа и твердых частиц поступает в рециркуляционный циклон 16 для циркулирующего псевдоожиженного слоя, в котором осуществляют дальнейшее разделение твердых частиц и газа. Выходящие из рециркуляционного циклона 16 твердые частицы, температура которых составляет приблизительно 950 С, через трубопровод 25 подают в смесительный бак 26. Через обводной трубопровод 27 в смесительный бак 26 также вводят отделенную под разделительным циклоном 18 часть потока моногидрата алюминия, температура которого составляет приблизительно от 320 до 370 С. В смесительном баке 26 поддерживают температуру, составляющую приблизительно 700 С, путем смешивания в соответствующем соотношении потока горячего оксида алюминия, который подают через трубопровод 25, и потока моногидрата алюминия, который подают через обводной трубопровод 27. Потоки двух продуктов тщательно смешивают в смесительном баке 26, который включает псевдоожиженный слой, чтобы моногидрат алюминия, который подают через обводной трубопровод 27,также полностью обжечь до оксида алюминия. Очень длительное время пребывания, составляющее до 30 или до 60 мин, приводит к превосходному обжигу в смесительном баке. Однако время пребывания, составляющее менее 2 мин, в частности приблизительно 1 мин или даже менее 30 с, также может быть достаточным. Из смесительного бака 26 полученный продукт вводят в первый циклонный охладитель, образованный из подъемного трубопровода 28 и циклонного сепаратора 29. Через трубопровод 23 отходящий газ из циклонного сепаратора 29 подают в реактор 20 с псевдоожиженным слоем в качестве вторичного воздуха, а твердые частицы подают во второй циклонный охладитель, образованный из подъемного трубопровода 30 и циклонного сепаратора 31, и, наконец, в третий циклонный охладитель, образованный из подъемного трубопровода 32 и циклонного сепаратора 33. Поток газа через отдельные циклонные охладители осуществляют в противотоке по отношению к твердым частицам через трубопроводы 35 и 34. После выхода из последнего циклонного охладителя полученный оксид алюминия подвергают окончательному охлаждению в охладителе 36 с псевдоожиженным слоем, оборудованном тремячетырьмя камерами охлаждения. Оксид алюминия с температурой приблизительно 300 С поступает в его первую камеру 36 а и нагревает жидкую теплопередающую среду, в частности воду, до температуры 140-195 С, предпочтительно 150-190 С, в частности 160-180 С. Нагретую теплопередающую среду подают в сушилку 60 для гидрата через циркуляционный трубопровод 37, чтобы сушить гидроксид металла(гидрат) путем косвенного теплообмена. Давление в теплопередающем контуре предпочтительно регулируют так, чтобы избежать конденсации теплопередающей среды в сушилке 60 для гидрата, и поддерживают его равным приблизительно от 0,1 до 5 МПа (от 1 до 50 бар), в частности от 0,2 до 4 МПа (от 2 до 40 бар). После прохождения через сушилку 60 для гидрата теплопередающую среду с температурой приблизительно 100-190 С, предпочтительно 120-180 С, в частности 140-170 С, направляют обратно в первую ступень 36 а охладителя с псевдоожиженным слоем через циркуляционный трубопровод 37. В камерах 36b-36d, расположенных ниже по потоку, оксид алюминия дополнительно охлаждают до температуры, составляющей приблизительно 80 С, с помощью теплопередающей среды, предпочтительно воды, которую направляют в противотоке, а затем выпускают его в качестве продукта через трубопровод 38. В камерах 36a-36d твердые частицы псевдоожижают с помощью вторичного воздуха с температурой от 80 до 100 С, который подают через трубопровод 39. Затем вторичный воздух отводят из охладителя 36 с псевдоожиженным слоем и применяют в качестве транспортирующего воздуха для третьего циклонного охладителя. Через трубопровод 40 можно подавать дополнительный воздух. Вместо воздуха через трубопроводы 39 и/или 40 также можно подавать чистый кислород или обогащенный кислородом воздух с содержанием кислорода от 20 до 100 об.%. На фиг. 2 и 3 сушилка 60 для гидрата изображена более подробно. Теплопередающую среду через циркуляционный трубопровод 37 подают в теплообменные трубы 61 и пропускают через сушилку 60 для гидрата, перед тем как направить ее обратно в охладитель 36 с псевдоожиженным слоем через циркуля-4 019025 ционный трубопровод 37. Теплообменные трубы 61 объединены, например, в три пучка труб теплообменника, которые можно извлекать из корпуса 63 сушилки 60 для гидрата через отдельные выдвижные блоки 62 а-62 с (см. фиг. 3). Таким образом, существенно упрощают техническое обслуживание сушилки 60 для гидрата. Гидрат, введенный в сушилку 60 для гидрата из загрузочной станции 1 с помощью транспортирующего шнека 64, поддерживают в псевдоожиженном состоянии путем подачи псевдоожижающего газа, в частности воздуха, чтобы увеличить теплопередачу и, таким образом, по возможности минимизировать размеры поверхности теплообмена. Гидрат медленно сушат при низкой температуре и с относительно малыми градиентами температуры или скоростями нагрева. Благодаря такой осторожной обработке уменьшают нагрузку на частицы гидрата и снижают вероятность разрушения частиц. Таким образом, количество мелкой пыли в твердых частицах уменьшается, что приводит к меньшей потере давления в установке. Поскольку пар, полученный при сушке гидрата, осуществляет псевдоожижение твердых частиц, подачу псевдоожижающего газа можно уменьшить или даже полностью прервать. Таким образом, достигают более осторожной обработки гидрата. Объемный расход подаваемого псевдоожижающего газа предпочтительно регулируют и устанавливают в зависимости от влажности гидроксида металла на таком уровне, чтобы обеспечить достаточное псевдоожижение. Также можно полностью или частично использовать отходящий газ из установки в качестве псевдоожижающего газа. Для этой цели можно использовать весь поток отходящего газа или его часть после отделения пыли, например, после электростатического осадителя, и, возможно, после дополнительной очистки газа, например, с помощью фильтра для пыли, который представляет собой мешочный фильтр. Кроме того, можно примешивать атмосферный воздух и/или отходящий газ из установки для обогащения кислородом (т.е. газ с пониженным содержанием кислорода). Высушенный гидрат выходит из сушилки 60 для гидрата через отводную трубу 65. В нижней части 66 отводной трубы 65 от нее отходит подъемная труба 67, которая идет, по существу, вертикально вверх. Твердые частицы в нижней части отводной трубы 65 псевдоожижают с помощью сопла. Сопло можно направлять вверх или вниз, чтобы иметь возможность более надежно предотвращать засоры. Специалисты в данной области могут применять известные им способы псевдоожижения твердых частиц в нижней части отводной трубы 65. Например, можно применять сопло с колпачком или сопло с пористым корпусом на его конце, которые должны предотвращать засорение сопла. Также можно подавать транспортирующий газ через псевдоожижающую ткань или через какую-либо другую пористую среду, которая расположена в нижней части отводной трубы над распределителем газа, который не показан. Твердые частицы поднимаются через подъемную трубу 67 врасширительный бак 68, а из него их подают через трубопровод 3 в циклонный теплообменник 4 первой ступени предварительного нагрева. Вместо расширительного бака 68 также можно применять простой коленчатый патрубок в конце подъемной трубы 67. Через трубопровод 53 пар, полученный при сушке гидрата, направляют в фильтр 50 для гидрата и применяют в нем, как описано выше, для снижения влажности гидрата. Поскольку количество тепла,переходящего к теплопередающей среде в охладителе 36 с псевдоожиженным слоем, зависит только от количества полученного оксида алюминия, поток массы гидрата в сушилку 60 для гидрата можно увеличить вследствие более низкой влажности гидрата. В результате, можно дополнительно снизить удельное потребление энергии установкой. Поток газа из сушилки 60 можно смешать полностью, но предпочтительно только частично, с отходящим газом из установки, например, после электростатического осадителя 8, возможно, после дополнительной очистки газа, например, с помощью фильтра для пыли. Также можно применять смесь с атмосферным воздухом и/или с отходящим газом из установки для обогащения кислородом (т.е. с газом с пониженным содержанием кислорода). Следовательно, температуру, объемный расход и/или содержание воды в газе, который подают в кожух 52 для подвода пара, можно регулировать и устанавливать на уровне, соответствующем предъявляемым требованиям. С помощью данного изобретения можно точно регулировать температуру на отдельных стадиях процесса, посредством чего можно оптимизировать процесс и уменьшить потребление энергии. Можно быстро реагировать на отклонения качества, в частности влажности исходного продукта. По сравнению с уровнем техники можно заметно уменьшить температуру отходящего газа в дымовой трубе и, следовательно, потери энергии. При постоянном качестве продукта модельные расчеты показывают снижение требуемой энергии до 10% на 1 кг продукта. Кроме того, достигают осторожной обработки твердых частиц, так что можно снизить разрушение частиц. Список номеров позиций на чертеже: 1 - загрузочная станция,2 - трубопровод,3 - сушилка для гидрата,4 - циклонный теплообменник,5 - обводной трубопровод,6 - регулирующий клапан,7 - трубопровод,-5 019025 8 - электростатический осадитель,9 - трубопровод,10 - циклонный теплообменник,11 - трубопровод,12 - разделительный циклон,13 - трубопровод,14 - трубопровод,15 - циклонный теплообменник,16 - рециркуляционный циклон,17 - трубопровод,18 - разделительный циклон,19 - трубопровод,20 - реактор с псевдоожиженным слоем,21 - топливный трубопровод,22 - подающий трубопровод,23 - подающий трубопровод,24 - соединительный трубопровод,25 - трубопровод,26 - смесительный бак,27 - обводной трубопровод,28 - подъемный трубопровод,29 - циклонный сепаратор,30 - подъемный трубопровод,31 - циклонный сепаратор,32 - подъемный трубопровод,33 - циклонный сепаратор,34 - трубопровод,35 - трубопровод,36 - охладитель с псевдоожиженным слоем,37 - циркуляционный трубопровод,38 - трубопровод,39 - трубопровод,40 - трубопровод,50 - фильтр для гидрата,51 - трубопровод,52 - кожух для подвода пара,53 - трубопровод,54 - разгрузочный шнек,55 - трубопровод,56 - трубопровод,60 - сушилка (сушилка для гидрата),61 - теплообменные трубы,62 а-с - выдвижные блоки,63 - корпус,64 - транспортирующий шнек,65 - отводная труба,66 - нижняя часть,67 - подъемная труба,68 - расширительный бак. ФОРМУЛА ИЗОБРЕТЕНИЯ 1. Способ получения оксида металла из гидроксида металла, в частности из гидроксида алюминия,где гидроксид металла сушат в сушилке, подогревают по меньшей мере в одной ступени предварительного нагрева и обжигают до оксида металла в реакторе с псевдоожиженным слоем, причем затем полученный оксид металла охлаждают, отличающийся тем, что перед сушкой гидроксид металла очищают по меньшей мере в одном фильтре, а пар, полученный в сушилке, направляют в фильтр. 2. Способ по п.1, отличающийся тем, что гидроксид металла, подлежащий сушке, псевдоожижают в сушилке. 3. Способ по п.2, отличающийся тем, что гидроксид металла, подлежащий сушке, псевдоожижают в сушилке посредством подачи псевдоожижающего газа. 4. Способ по п.2 или 3, отличающийся тем, что гидроксид металла, подлежащий сушке, псевдо-6 019025 ожижают в сушилке с помощью пара, полученного во время сушки. 5. Способ по любому из пп.1-4, отличающийся тем, что в сушилку подают предпочтительно жидкую теплопередающую среду, с помощью которой гидроксид металла нагревают косвенным путем, а жидкую теплопередающую среду нагревают в косвенном охладителе, предусмотренном после реактора с псевдоожиженным слоем. 6. Способ по п.5, отличающийся тем, что осуществляют циркуляцию теплопередающей среды между сушилкой и косвенным охладителем. 7. Способ по п.5 или 6, отличающийся тем, что в сушилку подают теплопередающую среду с температурой от 130 до 220 С. 8. Способ по любому из пп.1-7, отличающийся тем, что часть потока гидроксида металла направляют мимо сушилки. 9. Установка для осуществления способа по любому из пп.1-8, включающая сушилку (60) для сушки гидроксида металла, по меньшей мере один подогреватель (4) для предварительного нагрева гидроксида металла, реактор (20) для обжига гидроксида металла до оксида металла и по меньшей мере одно охлаждающее приспособление (28, 29, 30, 31, 32, 33) для охлаждения полученного оксида металла, отличающаяся тем, что перед сушилкой (60) предусмотрен фильтр (50) для фильтрования гидроксида металла, и тем, что трубопровод (53) для отходящего газа из сушилки (60) соединен с фильтром (50). 10. Установка по п.9, отличающаяся тем, что фильтр (50) включает кожух (52) для подвода пара, и тем, что трубопровод (53) для отходящего газа из сушилки (60) открывается в кожух (52) для подвода пара. 11. Установка по п.9 или 10, отличающаяся тем, что в сушилке (60) предусмотрены теплообменные трубы (61) для теплопередающей среды. 12. Установка по п.11, отличающаяся тем, что теплообменные трубы (61) объединены во множество пучков труб теплообменника, которые можно по отдельности извлекать из корпуса (63) сушилки (60) через выдвижные блоки (62 а-с). 13. Установка по п.11 или 12, отличающаяся тем, что охлаждающее приспособление для оксида металла включает многоступенчатый охладитель (36) для косвенного охлаждения оксида металла, и тем,что теплообменные трубы (61) сушилки (60) соединены с первой ступенью (36 а) косвенного охладителя(36) через циркуляционный трубопровод (37) для теплопередающей среды. 14. Установка по любому из пп.9-13, отличающаяся наличием обводного трубопровода (5) вокруг сушилки (60), который соединен с первой ступенью предварительного нагрева. 15. Установка по п.14, отличающаяся наличием регулирующего клапана (6) для разделения потока гидрата между сушилкой (60) и обводным трубопроводом (5).
МПК / Метки
МПК: B01J 8/24, C01F 7/44, B01J 6/00
Метки: получения, гидроксида, установка, оксида, способ, металла
Код ссылки
<a href="https://eas.patents.su/9-19025-sposob-i-ustanovka-dlya-polucheniya-oksida-metalla-iz-gidroksida-metalla.html" rel="bookmark" title="База патентов Евразийского Союза">Способ и установка для получения оксида металла из гидроксида металла</a>
Предыдущий патент: Соль пиперазина и способ ее получения
Следующий патент: Стиральная машина
Случайный патент: Фенил- и пиридил-тетрагидропиридины, обладающие ингибирующей активностью в отношении фактора некроза опухоли (фно)