Метод и оборудование для очистки сланцевого масла от твердых частиц
Номер патента: 16667
Опубликовано: 30.06.2012
Авторы: Хилков Андрей, Николаев Игорь, Булдакова Елена
Формула / Реферат
1. Метод очистки сланцевого масла от твердых частиц, согласно которому из фракций сланцевого масла подготавливают очищаемую смесь, а затем производят процесс очистки этой смеси, отличающийся тем, что
процесс очистки состоит из одинаковых следующих друг за другом циклов, где в течение каждого цикла
очищаемую смесь вводят в емкость разделения твердых частиц;
выходящую из емкости разделения твердых частиц чистую смесь фракций сланцевого масла собирают в емкости готовой продукции;
емкость разделения твердых частиц очищают от оставшихся в ней твердых частиц, для чего ее опустошают от очищаемой смеси, а затем из пустой емкости разделения твердых частиц удаляют твердые частицы, при этом
очищаемую смесь готовят путем одновременного смешения 0,5-1,0 об. долей тяжелой фракции сланцевого масла, 1,0-2,0 об. долей легкосредней фракции и 0,7-1,4 об. долей бензина;
перед введением в емкость разделения твердых частиц очищаемую смесь подогревают до температуры 60-70°С;
в качестве емкости разделения твердых частиц используют фильтр, содержащий, как минимум, два фильтрующих элемента;
очищаемую смесь вводят в емкость разделения твердых частиц под давлением 1,5-2,5 бар;
очищенную смесь выводят через выходы фильтрующих элементов, через трубопровод соединенные с емкостью готовой продукции;
для опустошения фильтра от очищаемой смеси в фильтр под давлением вводят инертный газ;
после опорожнения фильтра от очищаемой смеси твердые частицы, оставшиеся на поверхности фильтрующих элементов, сушат инертным газом;
для удаления твердых частиц с поверхности фильтрующих элементов внутри фильтра после просушки фильтрующих элементов производят пневмоудары;
сухие твердые частицы удаляют из нижней части фильтра.
2. Метод очистки сланцевого масла от твердых частиц согласно п.1, отличающийся тем, что после опустошения фильтра от очищаемой смеси и перед осуществлением пневмоударов внутри фильтра для удаления твердых частиц с поверхности фильтрующих элементов
в фильтр направляют бензин и осуществляют циркуляцию бензина через фильтрующие элементы;
по окончании циркуляции оставшийся в фильтре бензин направляют обратно в емкость бензина;
после опорожнения фильтра от бензина оставшиеся на поверхности фильтрующих элементов твердые частицы просушивают инертным газом.
3. Метод очистки сланцевого масла от твердых частиц согласно п.1, отличающийся тем, что для подготовки очищаемой смеси используют полученный из сланца бензин.
4. Метод очистки сланцевого масла от твердых частиц согласно п.1, отличающийся тем, что в качестве инертного газа используют азот.
5. Метод очистки сланцевого масла от твердых частиц согласно п.1, отличающийся тем, что давление направляемого в фильтр инертного газа - как минимум 2,5 бар, а температура - 50-90°С.
6. Метод очистки сланцевого масла от твердых частиц согласно п.2, отличающийся тем, что циркуляцию бензина через фильтрующие элементы осуществляют в течение 9-14 мин.
7. Метод очистки сланцевого масла от твердых частиц согласно п.2, отличающийся тем, что циркуляцию бензина через фильтрующие элементы осуществляют из емкости бензина через фильтрующие элементы обратно в емкость бензина.
8. Метод очистки сланцевого масла от твердых частиц согласно п.1, отличающийся тем, что использованный в фильтрах инертный газ очищают от растворенных в нем смоляных паров и направляют обратно для повторного использования, а смоляные пары конденсируют и направляют обратно к очищаемой смеси.
9. Оборудование для осуществления метода очистки сланцевого масла от твердых частиц согласно п.1, включающее в себе установку подготовки очищаемой смеси фракций сланцевого масла, установку по отделению твердых частиц от очищаемой смеси и емкость готового продукта, отличающееся тем, что
установка подготовки очищаемой смеси включает в себе емкость бензина, емкости тяжелой и легкосредней фракций сланцевого масла и соединенный с ними смеситель, выход которого соединен со входом емкости очищаемой смеси,
емкостью разделения твердых частиц является фильтр, содержащий как минимум два фильтрующих элемента;
выходы фильтрующих элементов являются выходом фильтра, который через клапаны соединен с емкостью очищенного сланцевого масла и с емкостью бензина;
оборудование включает источник инертного газа, предусмотренный для обеспечения процесса очистки инертным газом и включающий в себя емкость инертного газа и конденсатор;
выход емкости инертного газа и вход конденсатора через клапаны соединены с фильтром, один выход конденсатора через насос соединен со входом емкости инертного газа, второй выход конденсатора через клапан соединен с емкостью легкосредней фракции;
выход емкости очищаемой смеси через насос и параллельно с ним подключенный клапан соединен с входом фильтра;
выход емкости бензина через насос соединен с входом фильтра.
10. Оборудование согласно п.9, отличающееся тем, что выходы фильтрующих элементов соединены параллельно по отношению к выходу фильтра.
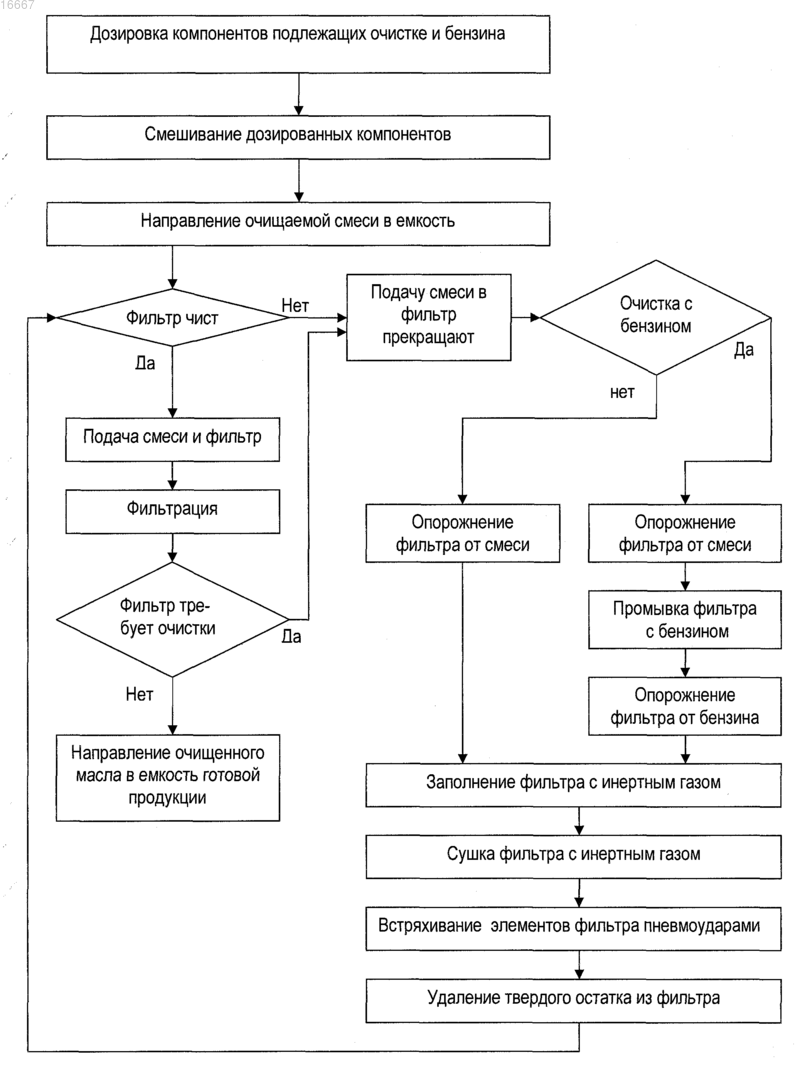
Текст
МЕТОД И ОБОРУДОВАНИЕ ДЛЯ ОЧИСТКИ СЛАНЦЕВОГО МАСЛА ОТ ТВЕРДЫХ ЧАСТИЦ Изобретение предназначено для очистки сланцевого масла от находящихся в нм тврдых частиц,оставшихся в масле после термической переработки сланца. Первым объектом изобретения является метод, согласно которому подготавливают очищаемую смесь из тяжлой и легкосредней фракций сланцевого масла и бензина, а затем производят циклический процесс очистки этой смеси. В течение каждого цикла сначала происходит фильтрация смеси до момента, когда эффективность фильтрации падает ниже требуемого уровня. Затем фильтр опустошают от очищаемой смеси,а фильтрующие элементы очищают. В зависимости от плотности слоя, скопившегося на фильтрующих элементах, их либо только сушат инертным газом высокой температуры, а затем воздействуют на них пневмоударами, либо при более плотном слое сушке предшествует промывка фильтрующих элементов бензином. После очистки фильтрующих элементов следует второй аналогичный цикл. Вторым объектом изобретения является оборудование, которое позволяет реализовать описанный метод.(71)(73) Заявитель и патентовладелец: ВКГ ОЙЛ АС (EE) 016667 Область техники Изобретение относится к области химической промышленности и затрагивает термическую переработку сланцевого масла, а точнее изобретение предназначено для очистки сланцевого масла от присутствующих в нм тврдых частиц. Уровень техники Полученное путм термической переработки сланца сланцевое масло в значительной мере содержит тврдые частицы, которыми являются частицы сланца, золы и полукокса. Их наличие в сланцевом масле затрудняет его дальнейшую переработку, в ходе которой из сланцевого масла выделяются нужные фракции. Вредное воздействие тврдых частиц проявляется в первую очередь в том, что они засоряют используемое оборудование и способствуют эрозии находящихся с ними в контакте поверхностей. Поэтому очень важно очищать сланцевое масло от тврдых частиц перед его дальнейшей переработкой. В уровне техники известны различные методы и оборудование для очистки сланцевого масла от присутствующих в нм тврдых частиц. Например, известен метод очистки сланцевого масла от тврдых частиц, предусматривающий отстаивание сланцевого масла в соответствующих мкостях. Процесс трудомкий и длительный, при этом он способствует удалению тврдых частиц, в первую очередь, из среднелгкой фракции сланцевого масла, но применение метода для удаления тврдых частиц из тяжлой фракции не дат значительного эффекта (см. Н.И. Зеленин, В.С. Файнберг, К.Б. Чернышева. Химия и технология сланцевой смолы. Издательство Химия, Ленинградское отделение, 1968 г., стр. 186). Известен также метод очистки сланцевого масла от тврдых частиц путем центрифугирования, но и этот метод не дат достаточно чистого сланцевого масла, кроме того, процесс очень энергомкий (см. Н.И. Зеленин, В.С. Файнберг, К.Б. Чернышева. Химия и технология сланцевой смолы. Издательство Химия, Ленинградское отделение, 1968 г., стр. 187). Для очистки сланцевого масла от тврдых частиц пробовали и его фильтровать, но удовлетворительных результатов не получили. Сланцевое масло, в первую очередь из-за высокой вязкости его тяжлой фракции, создат на фильтрующей поверхности плотный слой, засоряющий фильтры и препятствующий дальнейшему процессу, по причине чего известные решения по фильтрации вообще не подходят для очистки тяжлой фракции сланцевого масла (см. Н.И. Зеленин, В.С. Файнберг, К.Б. Чернышева. Химия и технология сланцевой смолы. Издательство Химия, Ленинградское отделение, 1968 г., стр. 188). Известен также метод очистки сланцевого масла от тврдых частиц, при котором тяжлую фракцию сланцевого масла смешивают с бензином, полученную смесь в течение необходимого времени отстаивают в декантере, после чего отстоявшуюся смесь направляют дальше в термоотстойник, где также отстаивают в течение необходимого времени. Затем очищенную таким путм тяжлую фракцию смешивают со среднелгкой фракцией, а эту смесь в свою очередь смешивают с фенольной водой в смесителе и направляют в следующий термоотстойник, где после отстаивания в течение предусмотренного времени получают очищенное сланцевое масло и выделяют фенольную воду (описанный метод используется эстонской фирмой ВКГ ОЙЛ АО в Кохтла-Ярве, Эстония). Описанный метод позволяет задействовать в процессе очистки тяжлую фракцию сланцевого масла, но к недостаткам метода можно отнести следующие обстоятельства: во-первых, для реализации метода требуется очень мкое оборудование (декантер, термоотстойники), по причине чего для использования метода требуются большие производственные площади; во-вторых, при очистке сланцевого масла известным методом в ходе работы происходит довольно значительное улетучивание лгкой фракции из смеси (бензин), что значительно увеличивает производственные потери; в-третьих, получаемые в процессе очистки остаточные продукты содержат помимо удалнных тврдых частиц также в больших количествах и очищаемую смесь, например, в остаточном продукте на выходе из второго термоотстойника содержится 85-90% очищаемой смеси и воды. Для обработки подобных остаточных продуктов требуются дополнительные затраты, что также увеличивает стоимость процесса; в-четвртых, процесс очистки требует много времени. В уровне техники известно оборудование для очистки сланцевого масла, в котором выходы мкостей тяжлой фракции и бензина соединены со входом первого диафрагменного смесителя, его выход соединн со входом декантера, а выход последнего с входом первого термоотстойника. Выход первого термоотстойника и выход мкости фенольной воды соединены с входом второго диафрагменного смесителя, с которым соединн также выход мкости легкосредней фракции. Выход второго диафрагменного смесителя соединн с входом второго термоотстойника. Через один из выходов второго термоотстойника выводится очищенное сланцевое масло, а через второй - отделнная фенольная вода. Как на декантере,так и на обоих термоотстойниках имеются дополнительные выходы для вывода остаточного продукта(описанное оборудование используется эстонской фирмой ВКГ ОИЛ АО в Кохтла-Ярве, Эстония). Недостатки, связанные с установкой и использованием описанного оборудования, совпадают с недостатками уже описанного известного метода.-1 016667 Цель и сущность изобретения Первой целью изобретения является усовершенствование метода очистки сланцевого масла от тврдых частиц таким образом, чтобы сделать процесс очистки более эффективным, уменьшить объем используемого оборудования, уменьшить количество остатков, возникающих в процессе очистки, направляя их обратно в процесс, но также и понизить содержание тврдых частиц в очищенном сланцевом масле, которое направляется на дальнейшую дистилляцию, что позволяет путм дальнейшего процесса дистилляции получать более качественные продукты. Поставленная цель изобретения достигается первым альтернативным решением, согласно которому из тяжлой и легкосредней фракций сланцевого масла изготовляют очищаемую смесь, а затем осуществляют процесс циклической очистки этой смеси, где каждый цикл процесса включает в себя следующие этапы: очищаемую смесь под давлением закачивают в мкость для удаления тврдых частиц; очищенную смесь фракций сланцевого масла, выходящую из мкости для удаления тврдых частиц,собирают в мкости готового продукта; мкость для удаления тврдых частиц очищают от оставшихся там частиц, для чего эту мкость опустошают от очищаемой смеси, а затем из пустой мкости удаляют тврдые частицы, причм очищаемую смесь готовят путм одновременного смешения 0,5-1,0 об. долей тяжлой фракции сланцевого масла, 1,0-2,0 об. долей легкосредней фракции и 0,7-1,4 об. долей бензина; очищаемую смесь подогревают перед вводом в разделительную мкость до температуры 60-70 С; разделительной мкостью служит фильтр, содержащий, как минимум, два фильтрующих элемента; очищаемую смесь вводят в разделительную мкость под давлением 1,5-2 бар; очищенную смесь удаляют через выходы фильтрующих элементов в мкость готового продукта; для опорожнения фильтра от очищаемой смеси в него под давлением вводят инертный газ; после опорожнения фильтра оставшиеся на поверхности фильтрующих элементов тврдые частицы сушат инертным газом; после просушки фильтрующих элементов внутри фильтра путм резких изменений давления инертного газа создают пневматические удары, в результате чего сухие тврдые частицы освобождаются с поверхности фильтрующих элементов и падают в нижнюю часть фильтра; сухие тврдые частицы удаляют из нижней части фильтра. Согласно второму альтернативному решению изобретения из тяжлой и легкосредней фракций сланцевого масла готовят очищаемую смесь, а затем осуществляют процесс циклической очистки смеси,где каждый цикл процесса включает следующие этапы: очищаемую смесь под давлением закачивают в мкость отделения тврдых частиц; очищенную смесь фракций сланцевого масла, выходящую из мкости отделения тврдых частиц,собирают в мкости готового продукта; мкость отделения тврдых частиц очищают от оставшихся в ней тврдых частиц, для чего е освобождают от очищаемой смеси, а затем из пустой разделительной мкости удаляют тврдые частицы,причм очищаемую смесь готовят путм одновременного смешения 0,5-1,0 об. долей тяжлой фракции сланцевого масла, 1,0-2,0 об. долей легкосредней фракции и 0,7-1,4 об. долей бензина; очищаемую смесь подогревают перед накачиванием в разделительную мкость до температуры 6070 С; разделительной мкостью служит фильтр, содержащий, как минимум, два фильтрующих элемента; очищаемую смесь вводят в разделительную мкость под давлением 1,5-2,5 бар; очищенную смесь удаляют через выходы фильтрующих элементов в мкость готового продукта; для опорожнения фильтра от очищаемой смеси в него под давлением подают инертный газ; после опорожнения фильтра оттуда выводят инертный газ и в фильтр подают бензин и осуществляют циркуляцию бензина через фильтрующие элементы; по окончании циркуляции оставшийся в фильтре бензин направляют обратно в мкость бензина; после опорожнения фильтра тврдые частицы, оставшиеся на поверхности фильтрующих элементов, сушат инертным газом; после сушки фильтрующих элементов внутри фильтра путм резких изменений давления инертного газа создают пневматические удары, в результате чего сухие тврдые частицы освобождаются с поверхности фильтрующих элементов и падают в нижнюю часть фильтра; сухие тврдые частицы удаляются из нижней части фильтра. Для подготовки очищаемой смеси используют бензин, полученный из сланцевого масла. В качестве инертного газа используют азот. Температура направляемого в фильтр инертного газа 50-90 С. Циркуляция бензина через фильтрующие элементы осуществляется в течение 10-20 мин из бензиновой мкости через фильтрующие элементы и обратно в бензиновую мкость. Использованный в фильтрах инертный газ очищают от растворнных в нм масляных паров и направляют для повторного использования, а масляные пары конденсируют и направляют обратно в очи-2 016667 щаемую смесь. Второй целью изобретения является создание оборудования для осуществления изобретнного метода, которое было бы менее мким, чем в известном решении, и использование которого позволило бы избежать недостатков известного метода. Вторая цель изобретения достигается тем, что оборудование для очистки сланцевого масла от тврдых частиц включает в себя установку подготовки очищаемой смеси фракций сланцевого масла, мкость отделения тврдых частиц от подготовленной смеси и мкость готового продукта, причм установка подготовки очищаемой смеси включает мкости бензина, тяжлой и легкосредней фракций сланцевого масла и соединенный с ними смеситель, выход которого соединен с входом емкости очищаемой смеси; разделительной мкостью служит фильтр, содержащий, как минимум, два фильтрующих элемента; выходы фильтрующих элементов образуют выход фильтра, который через клапаны соединн с мкостью очищенного сланцевого масла и бензиновой мкостью; оборудование дополнительно содержит источник инертного газа, предусмотренный для обеспечения процесса очистки инертным газом, в который входят мкость инертного газа и конденсатор, последний предназначен для удаления из инертного газа растворившихся там фракций сланцевого масла; выход мкости инертного газа и вход конденсатора через клапаны соединены с фильтром, один выход конденсатора через насос соединн с входом мкости инертного газа, а второй выход конденсатора через клапан соединн с мкостью легкосредней фракции; выход мкости очищаемой смеси через насос и соединнный параллельно к насосу клапан соединн с входом в фильтр; выход мкости бензина через насос соединн с входом фильтра; выходы фильтрующих элементов фильтра соединены для параллельного функционирования. Краткое описание чертежей Изобретение поясняется чертежами, где на фиг. 1 изображена блок-схема осуществления метода изобретения; на фиг. 2 - принципиальная схема установки для очистки сланцевого масла от тврдых частиц. У имеющихся на схеме клапанов стрелочками показано направление, в котором движется находящийся в трубопроводе материал, когда соответствующий клапан открыт. Детальное описание изобретения с примерами исполнения Очистка сланцевого масла от тврдых частиц согласно настоящему изобретению происходит следующим образом. Прежде всего подготавливают очищаемую смесь, для чего смешивают обе фракции сланцевого масла и бензин в следующих объмных соотношениях: 0,5-1,0 об. долей тяжлой фракции сланцевого масла, 1,0-2,0 об. долей лгкосредней фракции сланцевого масла и 0,7-1,4 об. долей бензина. Произведнные у заказчика испытания свидетельствуют о том, что подобное соотношение компонентов обеспечивает достижение лучшего эффекта фильтрации. Смешение производится без подогрева компонентов предпочтительно в диафрагмальном смесителе. После смешения смесь подогревают до температуры 6070 С и направляют в промежуточное хранилище, которым служит мкость очищаемой смеси. Дальнейший процесс очистки происходит циклически, в виде последовательности одинаковых циклов. Цикличность процесса обусловлена тем, что эффективность фильтра, используемого для удаления тврдых частиц, падает в ходе работы, по причине чего фильтр нужно чистить. Первым этапом цикла является заполнение фильтра очищаемой смесью, для чего смесь накачивают в фильтр под давлением 1,5-2,5 бар. При заполнении корпуса фильтра смесь начинает профильтровываться через фильтрующие элементы, и очищенную смесь направляют в мкость очищенного сланцевого масла. Подобный процесс фильтрации длится до тех пор, пока фильтрация не перестат быть эффективной. При значительном снижении эффективности фильтрации накачивание смеси в фильтр прерывают и в него направляют инертный газ (азот) под давлением минимум 2,5 бар и при температуре 50-90 С, в результате чего находящаяся в фильтре смесь вытесняется обратно в мкость очищаемой смеси, и корпус фильтра пустеет. После опустошения корпуса фильтра происходит очистка фильтрующих элементов, для чего возможны два альтернативных способа в зависимости от того, насколько велик удельный вес очищаемой смеси в слое скопившихся на фильтрующих элементах очищаемой смеси и отфильтрованных тврдых частиц. В первом случае, если удельный вес очищаемой смеси в слое, скопившемся на фильтрующей поверхности элементов, составляет до 30%, то в течение 10-20 мин осуществляют циркуляцию азота через фильтр, в результате чего тврдые частицы, осевшие на фильтрующих поверхностях элементов внутри фильтра, высыхают. После просушки фильтра внутри фильтра создают пневмоудары путм резкого изменения давления азота, в результате чего осевшие на фильтрующих элементах тврдые частицы падают в нижнюю часть фильтра, откуда их удаляют. Фильтр опустошают от азота, и начинается следующий цикл фильтрации.-3 016667 Во втором случае, если удельный вес очищаемой смеси в слое, собравшемся на фильтрующей поверхности элементов, превышает 30%, только просушка азотом и последующая очистка пневмоударами могут быть недостаточными. В подобном случае, аналогично вышеописанному, опустошают корпус фильтра, но затем производят промывку фильтрующих элементов бензином, для чего бензин подают в фильтр при обычной температуре и под давлением в 2-3 бар и после заполнения фильтра бензином осуществляют циркуляцию бензина через фильтрующие элементы. Длительность подобной циркуляции может быть от 8 до 15 мин. После очистки поверхности фильтрующих элементов от смеси сланцевых масел циркуляцию бензина прекращают и корпус фильтра опустошают от бензина, для чего оставшийся там бензин направляют обратно в мкость бензина. Дальнейшая очистка фильтра аналогична первому альтернативному варианту: в корпус фильтра направляют азот под давлением минимум 2,5 бар и при температуре 50-90 С и в течение 10-20 мин осуществляют циркуляцию азота через фильтр, в результате чего высыхают тврдые частицы, осевшие внутри фильтра на поверхности фильтрующих элементов, а затем внутри фильтра путм резкого изменения давления азота создают пневмоудары, в результате которых осевшие на фильтрующих элементах тврдые частицы падают в нижнюю часть фильтра, откуда их удаляют. Фильтр опустошают от азота, и начинается новый цикл фильтрации. Оборудование для очистки сланцевого масла от тврдых частиц состоит из четырх основных устройств - устройство 1 подготовки очищаемой смеси фракций сланцевого масла, устройство 2 для ввода подготовленной смеси в фильтр, фильтрующее устройство 3 и источник 4 инертного газа. В устройство 1 подготовки смеси фракций сланцевых масел входят мкость 101 бензина, мкость 102 тяжлой фракции сланцевого масла и мкость 103 легкосредней фракции сланцевого масла, а также смеситель 104, с входом которого соединены выходы всех трх вышеназванных мкостей. Указанные соединения выполнены через клапаны 105, 106 и 107, управляя которыми (так как устройство управление клапанами не является объектом изобретения, оно не изображено на чертежах), можно производить дозировку подлежащих смешению компонентов. В устройство 2 ввода подготовленной смеси в фильтр входят мкость 201 очищаемой смеси, вход которой соединн с выходом смесителя 104, выход мкости 201 соединн с входом параллельной цепи,включающей насос 202 и клапан 203. В устройство 2 также входят насос 204, установленный между выходом параллельной цепи и мкости 101 бензина, а также клапан 205, установленный между выходом параллельной цепи и входом мкости 101 бензина. Фильтрующее устройство 3 включает фильтр 301, размещнную под ним мкость 302 отфильтрованных тврдых частиц и мкость 303 очищенного сланцевого масла. Фильтр состоит из вертикального предпочтительно цилиндрического корпуса 304, нижняя часть которого выполнена конусообразной для сбора тврдых частиц и оснащена клапаном сброса 305, который открывается и закрывается исполнительным узлом 306. В цилиндрическом корпусе 304 размещены вертикальные фильтрующие элементы 307, число которых может варьироваться в зависимости от требуемой производительности фильтрующего устройства. Каждый фильтрующий элемент 307 представляет собой перфорированную трубу, покрытую снаружи фильтрующей тканью. Выходы всех фильтрующих элементов 307 соединены вместе (все фильтрующие элементы работают параллельно) и образуют выход 308 фильтра 301, находящийся в верхней части корпуса 304 и через клапаны 309 и 310 соединнный соответственно с мкостью 303 очищенного сланцевого масла и мкостью 101 бензина. Вход 311 фильтра 301, находящийся в нижней части корпуса 304, соединн с выходом параллельной цепи, включающей насос 202 и клапан 203, а через насос 204 - с выходом мкости 101 бензина и через клапан 205 - также со входом мкости 101 бензина. Вывод 312 фильтрующего устройства 3 соединн с источником инертного газа 4. Источник 4 инертного газа включает мкость 401 сжатого инертного газа, конденсатор 402 и насос 403. Насос 403 размещн между одним выходом конденсатора 402 и входом мкости 401 сжатого инертного газа и предусмотрен для откачки отделнного в конденсаторе 402 инертного газа обратно в мкость 401. Выход мкости 401 через клапан 404 соединн с выводом 312 фильтра 301, а вход конденсатора 402 через последовательные клапаны 405 и 407 также соединен с выводом 312 фильтра 301, дополнительно вход конденсатора 402 через клапаны 405 и 408 соединен с выходом 308 фильтра 301. Второй выход конденсатора 402 через клапан 406 соединн с мкостью 103 среднелгкой фракции. Описанное оборудованиеработает следующим образом. Компоненты, находящиеся в мкости 101 бензина, в мкости 102 тяжлой фракции и в мкости 103 среднелгкой фракции, дозируют через открытые клапаны 105, 106 и 107 в смеситель 104 в таком соотношении, как указано выше. В результате смешения в смесителе 104 получают очищаемую смесь, е температуру поднимают до 60-70 С и подготовленную таким образом очищаемую смесь направляют в мкость 201. Процесс подготовки очищаемой смеси не связан однозначно с циклами очистки смеси. Критерием е подготовки является постоянное обеспечение требуемого уровня смеси в мкости 201. В начале цикла очистки смеси насосы 204 и 403 выключены, закрывают клапаны 203, 205, 310, 404,405 и 406, 407 и 408, открывают клапан 309 и запускают насос 202, в результате чего фильтр 301 начинает заполняться очищаемой смесью. При заполнении фильтра 301 давление смеси в фильтре 301 составля-4 016667 ет 1,5-2,5 бар, и очищаемая смесь начинает фильтроваться через фильтрующие элементы 307, а прошедшая их чистая смесь направляют через открытый клапан 309 в мкость 303 очищенного сланцевого масла. Если в процессе фильтрации на фильтрующих элементах 307 возникает слой очищаемой смеси и тврдых частиц такой толщины, что дальнейшая фильтрация нецелесообразна, прекращают подачу очищаемой смеси в фильтр 301 путм остановки насоса 202 и закрывают клапан 309. Затем открывают клапаны 203 и 404, в результате чего находящийся в мкости 401 под давлением минимум 2,5 бар и температуре 50-90 С азот поступает в фильтр 301 через открытый клапан 404 и вытесняет оттуда оставшуюся там очищаемую смесь, которую через открытый клапан 203 направляют назад в мкость 201 очищаемой смеси. Когда фильтр 301 опустошн от очищаемой смеси, клапан 203 закрывают, и следует очистка фильтрующих элементов 307, для чего описываемому оборудованию обеспечивают две возможности. Если удельный вес очищаемой смеси в слое, скопившемся на фильтрующих поверхностях элементов 307 и состоящем из очищаемой смеси и тврдых частиц, составляет до 30%, в течение 10-20 мин производят циркуляцию азота через фильтр 301, для чего клапан 404 оставляют открытым и дополнительно открывают клапаны 405 и 408 (клапан 407 уже предварительно закрыт). Вследствие этого азот под давлением минимально 2,5 бар и температурой 50-90 С начинает циркулировать из мкости 401 азота через клапан 404, фильтр 301 и клапаны 408 и 405 в конденсатор 402, просушивая тврдые частицы,находящиеся на фильтрующей поверхности элементов 307. Подобную циркуляцию осуществляют в течение 10-20 мин. После этого фильтр опорожняют от азота, для чего закрывают клапаны 404 и 408 и открывают клапаны 405 и 407, вследствие чего азот из-за своего высокого давления и низкого давления в трубах входит в конденсатор 402, а в фильтре 301 восстанавливается нормальное давление. В опустошнном фильтре 301 осуществляют путм резких изменений давления азота пневмоудары,для чего закрывают клапаны 405 и 407, а клапан 404 открывают на короткое время полностью, по причине чего давление в фильтре за короткое время возрастает до максимального значения. По достижении максимального значения давления в фильтре 301 клапан 404 закрывают, а на короткое время полностью открывают клапаны 405 и 407, в результате чего азот из-за своего избыточного давления и низкого давления в трубах поступает в конденсатор 402, давление в фильтре 301 скачкообразно падает, а затем в фильтре 301 восстанавливается нормальное давление. Описанные пневмоудары повторяют требуемое число раз, вследствие чего осевшие на поверхность фильтрующих элементов 307 высохшие частицы падают в нижнюю коническую часть корпуса 304 фильтра на клапан сброса 305, который открывают и закрывают посредством исполнительного узла 306. Когда на клапане сброса 305 собирается достаточное количество частиц, его открывают и остатки фильтрации падают в мкость 302, после чего клапан сброса 305 закрывают. После очистки фильтра 301 в нм устанавливается нормальное давление. После очистки фильтрующих элементов закрывают клапаны 404, 405 и 407 (клапан 408 был закрыт ранее), открывают клапан 309, а также запускают насос 202, чем начинается новый цикл фильтрации. Если удельный вес очищаемой смеси в слое, осевшем на фильтрующих поверхностях элементов 307 и состоящем из очищаемой смеси и тврдых частиц, составляет более 30%, то одной сушки фильтрующих элементов 307 азотом для их очистки недостаточно. В этом случае используют альтернативный вариант, согласно которому после опустошения фильтра 301 от очищаемой смеси клапан 404 закрывают,и открывают клапаны 405 и 407 и запускают насос 204. Накачиваемый последним в фильтр 301 бензин обычной температуры вытесняет оттуда азот, который через открытые клапаны 405 и 407 поступает в конденсатор 402. После заполнения фильтра 301 бензином клапаны 405 и 407 закрывают и открывают клапан 310,чем начинается циркуляция бензина через фильтр 301 по кругу: мкость 101 бензина, насос 204, фильтр 301, фильтрующие элементы 307, клапан 310, мкость 101 бензина. Циркуляция бензина длится 8-15 мин, и в ходе циркуляции с поверхности фильтрующих элементов 307 смывается приставшее к ним масло. Для завершения циркуляции останавливают насос 204, открывают клапаны 404 и 205, из-за чего азот, поступающий под давлением в фильтр 301, вытесняет оставшийся в нм бензин обратно в мкость 101. После опустошения фильтра 301 закрывают клапан 205 и в течение 10-20 мин осуществляют циркуляцию азота через фильтр 301, для чего открывают клапаны 405 и 408 (клапан 404 был открыт уже заранее), а клапан 407 закрывают. В результате этого азот под давлением минимально 2,5 бар и температуре 50-90 С начинает циркулировать из мкости 401 азота через фильтр 301, фильтрующие элементы 307 и клапаны 408 и 405 в конденсатор 402, высушивая тврдые частицы, находящиеся на поверхности фильтрующих элементов 307. Такую циркуляцию производят в течение 10-20 мин. После этого фильтр 310 опорожняют от азота, для чего закрывают клапаны 404 и 408 и открывают клапаны 405 и 407, из-за чего азот вследствие своего высокого давления и низкого давления в трубах поступает в конденсатор 402, и давление в фильтре 301 нормализуется. В опустевшем фильтре 301 путм резких изменений давления азота создают пневмоудары, для чего закрывают клапаны 405 и 407, а клапан 404 открывают на короткое время полностью, в результате чего в фильтре давление вырастает моментально до максимального значения. По достижении максимального значения давления клапан 404 закрывают и открывают на короткое время полностью клапаны 405 и 407,-5 016667 в результате чего азот из-за собственного высокого давления и низкого давления в трубах попадает в конденсатор 402, давление в фильтре 301 скачкообразно падает, а затем восстанавливается нормальное давление. Описанные пневмоудары производят необходимое число раз, вследствие чего осевшие на поверхности фильтрующих элементов высохшие частицы падают в нижнюю коническую часть корпуса фильтра 304 на клапан сброса 305, который открывают и закрывают посредством исполнительного узла 306. Когда на клапане сброса 305 собирается достаточное количество частиц, его открывают и остатки фильтрации падают в мкость 302, после чего клапан сброса 305 закрывают. После очистки фильтра 301 в нм устанавливается нормальное давление. После очистки фильтрующих элементов 307 закрывают клапаны 404, 405 и 407 (клапан 408 был закрыт ранее), а также запускают насос 202, чем начинается новый цикл фильтрации. Азот, используемый в фильтре 301 для опустошения и просушки, который через клапаны 405, 407 и 408 направляют в конденсатор 402, включает парообразные сланцевые масла. В конденсаторе 402 происходит выделение сланцевых масел из азота, после чего сконденсированное сланцевое масло направляют обратно в процесс очистки, для чего открывают клапан 406, направляющий сконденсированное сланцевое масло в мкость 103 легкосредней фракции. Очищенный азот насосом 403 закачивают обратно в мкость 401 азота. Изобретение не исчерпывается вышеописанным применением, а охватывает все покрытые формулой изобретения и эквивалентные им применения. Список имеющихся на схеме символов 1 - установка подготовки очищаемой смеси фракций сланцевого масла; 101 - мкость бензина; 102 - мкость тяжлой фракции сланцевого масла; 103 - мкость легкосредней фракции сланцевого масла; 104 - смеситель; 105 - клапан; 106 - клапан; 107 - клапан; 2 - установка ввода в фильтр подготовленной очищаемой смеси; 201 - мкость очищаемой смеси; 202 - насос; 203 - клапан; 204 - насос; 205 - клапан; 3 - установка фильтрации; 301 - фильтр; 302 - мкость отфильтрованных тврдых частиц; 303 - мкость очищенного сланцевого масла; 304 - корпус фильтра; 305 - клапан сброса; 306 - исполнительный узел; 307 - фильтрующий элемент; 308 - выход фильтра; 309 - клапан; 310 - клапан; 311 - вход фильтра; 312 - вывод из фильтра; 4 - источник инертного газа; 401 - мкость сжатого инертного газа (азота); 402 - конденсатор; 403 - насос; 404 - клапан; 405 - клапан; 406 - клапан; 407 - клапан; 408 - клапан. ФОРМУЛА ИЗОБРЕТЕНИЯ 1. Метод очистки сланцевого масла от тврдых частиц, согласно которому из фракций сланцевого масла подготавливают очищаемую смесь, а затем производят процесс очистки этой смеси, отличающийся тем, что-6 016667 процесс очистки состоит из одинаковых следующих друг за другом циклов, где в течение каждого цикла очищаемую смесь вводят в мкость разделения тврдых частиц; выходящую из мкости разделения тврдых частиц чистую смесь фракций сланцевого масла собирают в мкости готовой продукции; мкость разделения тврдых частиц очищают от оставшихся в ней тврдых частиц, для чего е опустошают от очищаемой смеси, а затем из пустой мкости разделения тврдых частиц удаляют тврдые частицы, при этом очищаемую смесь готовят путм одновременного смешения 0,5-1,0 об. долей тяжлой фракции сланцевого масла, 1,0-2,0 об. долей легкосредней фракции и 0,7-1,4 об. долей бензина; перед введением в мкость разделения тврдых частиц очищаемую смесь подогревают до температуры 60-70 С; в качестве мкости разделения тврдых частиц используют фильтр, содержащий, как минимум, два фильтрующих элемента; очищаемую смесь вводят в мкость разделения тврдых частиц под давлением 1,5-2,5 бар; очищенную смесь выводят через выходы фильтрующих элементов, через трубопровод соединнные с мкостью готовой продукции; для опустошения фильтра от очищаемой смеси в фильтр под давлением вводят инертный газ; после опорожнения фильтра от очищаемой смеси тврдые частицы, оставшиеся на поверхности фильтрующих элементов, сушат инертным газом; для удаления тврдых частиц с поверхности фильтрующих элементов внутри фильтра после просушки фильтрующих элементов производят пневмоудары; сухие тврдые частицы удаляют из нижней части фильтра. 2. Метод очистки сланцевого масла от тврдых частиц согласно п.1, отличающийся тем, что после опустошения фильтра от очищаемой смеси и перед осуществлением пневмоударов внутри фильтра для удаления тврдых частиц с поверхности фильтрующих элементов в фильтр направляют бензин и осуществляют циркуляцию бензина через фильтрующие элементы; по окончании циркуляции оставшийся в фильтре бензин направляют обратно в мкость бензина; после опорожнения фильтра от бензина оставшиеся на поверхности фильтрующих элементов тврдые частицы просушивают инертным газом. 3. Метод очистки сланцевого масла от тврдых частиц согласно п.1, отличающийся тем, что для подготовки очищаемой смеси используют полученный из сланца бензин. 4. Метод очистки сланцевого масла от тврдых частиц согласно п.1, отличающийся тем, что в качестве инертного газа используют азот. 5. Метод очистки сланцевого масла от тврдых частиц согласно п.1, отличающийся тем, что давление направляемого в фильтр инертного газа - как минимум 2,5 бар, а температура - 50-90 С. 6. Метод очистки сланцевого масла от тврдых частиц согласно п.2, отличающийся тем, что циркуляцию бензина через фильтрующие элементы осуществляют в течение 9-14 мин. 7. Метод очистки сланцевого масла от тврдых частиц согласно п.2, отличающийся тем, что циркуляцию бензина через фильтрующие элементы осуществляют из мкости бензина через фильтрующие элементы обратно в мкость бензина. 8. Метод очистки сланцевого масла от тврдых частиц согласно п.1, отличающийся тем, что использованный в фильтрах инертный газ очищают от растворнных в нм смоляных паров и направляют обратно для повторного использования, а смоляные пары конденсируют и направляют обратно к очищаемой смеси. 9. Оборудование для осуществления метода очистки сланцевого масла от тврдых частиц согласно п.1, включающее в себе установку подготовки очищаемой смеси фракций сланцевого масла, установку по отделению тврдых частиц от очищаемой смеси и мкость готового продукта, отличающееся тем, что установка подготовки очищаемой смеси включает в себе мкость бензина, мкости тяжлой и легкосредней фракций сланцевого масла и соединенный с ними смеситель, выход которого соединн со входом мкости очищаемой смеси,мкостью разделения тврдых частиц является фильтр, содержащий как минимум два фильтрующих элемента; выходы фильтрующих элементов являются выходом фильтра, который через клапаны соединн с мкостью очищенного сланцевого масла и с мкостью бензина; оборудование включает источник инертного газа, предусмотренный для обеспечения процесса очистки инертным газом и включающий в себя мкость инертного газа и конденсатор; выход мкости инертного газа и вход конденсатора через клапаны соединены с фильтром, один выход конденсатора через насос соединн со входом мкости инертного газа, второй выход конденсатора через клапан соединн с мкостью легкосредней фракции; выход мкости очищаемой смеси через насос и параллельно с ним подключенный клапан соединн с входом фильтра;-7 016667 выход мкости бензина через насос соединн с входом фильтра. 10. Оборудование согласно п.9, отличающееся тем, что выходы фильтрующих элементов соединены параллельно по отношению к выходу фильтра.
МПК / Метки
МПК: C10G 1/00, C10G 31/09, B01D 27/14, B01D 35/16
Метки: оборудование, очистки, твердых, метод, частиц, сланцевого, масла
Код ссылки
<a href="https://eas.patents.su/9-16667-metod-i-oborudovanie-dlya-ochistki-slancevogo-masla-ot-tverdyh-chastic.html" rel="bookmark" title="База патентов Евразийского Союза">Метод и оборудование для очистки сланцевого масла от твердых частиц</a>
Предыдущий патент: Устройство и система для переработки бытовых отходов
Следующий патент: Цифровая следящая система
Случайный патент: Производные гуанидина с антимикробным действием на основе диамина