Способ и устройство для изготовления труб из стали
Формула / Реферат
1. Способ изготовления труб из стали, прочность и вязкость материала которых повышена за счет быстрого охлаждения непосредственно после горячего формообразования, в частности после деформации посредством редуцирования с растяжением, причем в течение отрезка времени не более 20 с после последней деформации при температуре выше 700°C, однако ниже 1050°C, в проход на наружную поверхность трубы по периферии на длину, превышающую толщину стенки трубы более чем в 400 раз, наносят охлаждающее средство под повышенным давлением в количестве, которое обеспечивает при быстром охлаждении одинаковую скорость остывания стенки трубы по ее длине более 1°C/с с 500 до 250°C, после чего осуществляют дальнейшее охлаждение трубы на воздухе до температуры окружающей среды, причем для изготовления труб используют сталь со следующим процентным содержанием в массе легирующих и сопутствующих компонентов или примесей:
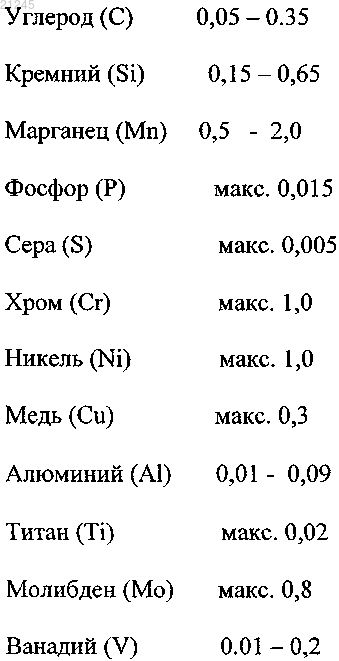
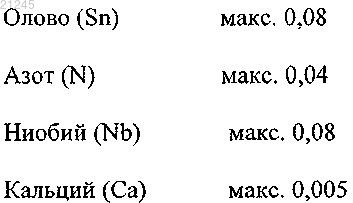
2. Способ по п.1, при котором сталь для изготовления труб содержит по меньшей мере один компонент со следующим процентным содержанием в массе:
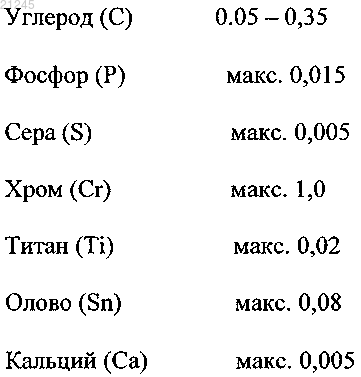
3. Способ по п.1 или 2, при котором быстрое охлаждение наружной поверхности трубы начинают при температуре ниже 950°C.
4. Способ по одному из пп.1-3, при котором после быстрого охлаждения во время последующего охлаждения трубы на воздухе осуществляют целенаправленный обратный нагрев стенки трубы.
5. Способ по одному из пп.1-4, при котором изготавливают трубы нефтяного сортамента длиной более 7 м, в частности до 200 м, наружного диаметра более 20 мм, однако менее 200 мм, и толщиной стенки от 2,0 мм, однако менее 25 мм.
6. Устройство для изготовления труб из стали с химическим составом по п.1 или 2, прочность и вязкость материала которых повышена за счет быстрого охлаждения после деформации, в частности посредством редуцирования с растяжением, состоящее из устройства для нанесения охлаждающего средства на поверхность трубы, отличающееся тем, что в направлении прокатки после последней деформирующей клети расположен переключаемый проходной участок охлаждения с кольцами распределения охлаждающего средства, расположенными друг за другом концентрично вокруг прокатываемого продукта и установленными в продольном направлении с различными интервалами по меньшей мере с тремя направленными к оси соплами, причем каждое кольцо распределения охлаждающего средства или каждая их группа выполнена с возможностью питания охлаждающим средством с регулированием расхода.
7. Устройство по п.6, отличающееся тем, что каждое сопло выполнено с возможностью создания расширяющегося в форме пирамиды в направлении распыления потока охлаждающего средства.
8. Устройство по п.7, отличающееся тем, что поток охлаждающего средства имеет прямоугольную форму сечения, а более длинная ось прямоугольника направлена под углом к оси трубы.
9. Устройство по п.8, отличающееся тем, что система подача охлаждающего средства к проходному участку охлаждения выполнена с возможностью включения в зависимости от положения концов трубы на нем.
Текст
СПОСОБ И УСТРОЙСТВО ДЛЯ ИЗГОТОВЛЕНИЯ ТРУБ ИЗ СТАЛИ Изобретение относится к способу и устройству для изготовления труб из стали. Согласно изобретению предусмотрено, что в течение отрезка времени самое большее 20 с после последней деформации при температуре выше 700C, однако ниже 1050C в проход на наружную поверхность трубы по периферии на длине, более чем в 400 раз превышающей толщину стенки трубы,наносится охлаждающее средство под повышенным давлением в количестве, которое при быстром охлаждении дает одинаковую скорость охлаждения стенки трубы по длине трубы более 1C/с до температуры в диапазоне 500-250C, после чего осуществляется дальнейшее охлаждение трубы на воздухе до комнатной температуры.(71)(73) Заявитель и патентовладелец: ФСТАЛЬПИНЕ ТУБУЛАРС ГМБХ УНД КО КГ (AT) Область техники, к которой относится изобретение Изобретение относится к способу изготовления труб из стали с повышенными прочностью и вязкостью материала. Изобретение относится также к устройству для изготовления труб с особым профилем свойств, состоящему из устройства для нанесения охлаждающего средства на поверхность трубы. Уровень техники При изготовлении бесшовных труб свойства материала их стенок локально и в зависимости от партии могут иметь значительные отличия. Эти отличия свойств являются следствием большей частью неодинакового строения структуры и неблагоприятного состава стали или повышенного содержания сопутствующих и примесных элементов. Подвергаемые большим нагрузкам трубы должны иметь по названным причинам отвечающее требованиям строение структуры с лежащей в узких пределах равномерностью по длине трубы и коаксиально в ее стенке, а также свободный от вредных элементов состав материала. Трубы длиной 7 м и более и наружным диаметром менее 200 мм при толщине стенки менее 25 мм подвергаются лишь с большими затратами термообработке, которая дает равномерно тонкую структуру с нужным строением по всему объему трубы и минимизирует сгибание перпендикулярно продольному направлению. Известны способы, в которых труба вращается вокруг своей оси и охлаждается на наружной и/или внутренней поверхностях. Такие способы термообработки предполагают, однако, приблизительно одинаково высокую температуру материала по длине трубы для достижения однородной структуры в стенке. Раскрытие изобретения Целью изобретения является создание способа, с помощью которого при изготовлении трубы посредством горячего формообразования, в частности посредством редуцирования с растяжением, можно было бы затем осуществлять обработку, которая вызвала бы повышение прочности и вязкости материала трубы. Далее задачей изобретения является создание устройства для изготовления труб, с помощью которого после горячего формообразования можно было бы изготавливать трубы с нужным профилем свойств по всей длине трубы. Эта задача решается родовым способом, при котором за счет непосредственного быстрого охлаждения после горячего формообразования, в частности после деформации посредством редуцирования с растяжением, причем в течение отрезка времени самое большее 20 с после последней деформации при температуре выше 700C, однако ниже 1050C, в проход на наружную поверхность трубы по периферии на длине, более чем в 400 раз превышающей толщину стенки трубы, наносится охлаждающее средство под повышенным давлением в количестве, которое при быстром охлаждении дает одинаковую скорость охлаждения стенки трубы по длине трубы более 1C/с до температуры в диапазоне 500-250C, после чего происходит дальнейшее охлаждение трубы на воздухе до комнатной температуры. Предложенным способом особенно высокие и равномерные механические значения материала, в частности значения вязкости, достигаются в том случае, если начало быстрого охлаждения наружной поверхности трубы происходит при температуре ниже 950C. Для интегрированного отпуска может быть далее предпочтительным, если после быстрого охлаждения трубы при ее дальнейшем охлаждении на воздухе происходит целенаправленный обратный нагрев участка поверхности стенки трубы. Для оптимизации качества труб или повышения качества их материала в одном варианте способа может быть существенным для изобретения, если для изготовления труб применяется сталь с концентрацией легирующих и сопутствующих или примесных элементов в мас.%: Если способ применяется для изготовления бесшовных труб длиной более 7 м, в частности до 200 м, наружным диаметром более 20 мм, однако менее 200 мм, толщиной стенки более 2 мм, однако менее 25 мм, то повышенное качество трубы может со значительным преимуществом уменьшить содержание запасов и минимизировать случаи повреждений за счет разрушения, что влечет за собой значительные расходы на ремонт. При ограниченном содержании углерода оптимальным образом в отношении однородного высокого качества трубы по меньшей мере один элемент стали может иметь содержание в мас.%: Другая задача изобретения, заключающаяся в создании устройства для изготовления труб из стали с повышенными прочностью и вязкостью материала за счет быстрого охлаждения после деформации, состоящего из устройства для нанесения охлаждающего средства на поверхность трубы, решается за счет того, что в направлении прокатки после последней деформирующей клети расположен включаемый проходной участок охлаждения с большим числом расположенных концентрично вокруг прокатываемого продукта, по-разному позиционируемых в продольном направлении распределительных колец для охлаждающего средства соответственно по меньшей мере с тремя направленными соответственно, в основном, к оси соплами, причем каждое распределительное кольцо или каждая их группа питается охлаждающим средством с регулированием расхода. Предпочтительно в предложенном изобретении можно подвергать трубы разной продольной протяженности, а также разных диаметров и толщин стенок целенаправленной термообработке с прокатного нагрева, причем таким образом можно получить нужное строение структуры, равномерное по всей длине труб. Особенно оптимальным в отношении равномерности улучшенной структуры как по периферии, так и в продольном направлении стенки трубы оказалось, если каждое сопло создает расширяющийся в направлении распыления поток охлаждающего средства в форме пирамиды. При этом поток охлаждающего средства может быть выполнен соответственно в виде распыляемого потока охлаждающего средства, большей частью воды, и/или в виде потока распыляемого тумана из охлаждающего средства и воздуха и/или в виде потока газа. Предпочтительные результаты в отношении равномерно высокого качества трубы могут быть достигнуты тогда, когда поток охлаждающего средства имеет прямоугольную форму сечения, а более длинная ось прямоугольника направлена наискось к оси трубы. Существенными для изобретения являются возможность включения и возможность регулирования потоков охлаждающего средства на проходном участке охлаждения. Если подача охлаждающего средства к проходному участку охлаждения включается в зависимости от положения концов трубы на нем, то можно оптимальным образом предотвратить проникновение охлаждающего средства внутрь трубы, что позволяет избежать, в основном, одностороннего в сечении внутреннего охлаждения и задержать образование неодинакового строения структуры. Предпочтительно регулирование охлаждения трубы осуществляется с помощью датчиков положения и температуры для управления потоками охлаждающего средства. Ниже изобретение более подробно поясняется с помощью примеров, представляющих только один путь его реализации. Пример 1. Из трубной заготовки одинакового маточного расплава с химическим составом в мас.% в соответствии с приведенной ниже таблицей посредством редуцирования с растяжением изготавливались трубы следующих размеров: После последнего прохода или после последней деформации в выходной клети установки для редуцирования с растяжением труба через 12 с помещалась при температуре 880C на проходной участок охлаждения. На основе установленного характера превращения стали в рамках исследований отдельных партий при изготовлении труб осуществлялось целенаправленное охлаждение только наружной поверхности трубы, причем на ней за счет регулирования потока охлаждающей среды измерялась скорость охлаждения около 6C/с до следующих температур: температура обозначение образца После достижения этих заданных конечных температур охлаждения подача охлаждающего средства прекращалась, и осуществлялось, таким образом, дальнейшее охлаждение трубы с меньшей интенсивностью, в частности, на спокойном воздухе до комнатной температуры. От термообработанных по-разному труб отбирались образцы с обозначениями Р 1-Р 4, которые направлялись для исследований материала. Определение строения структуры показало, что в любом случае имела место предпочтительно равнонаправленная структура, в основном, без текстуры, однако с зависимыми от конечной температуры охлаждения размером зерен и распределением. Краткое описание чертежей Фиг. 1 изображает структуру пробы Р 1, причем зерна имели размер 20-30 мкм при высокой доле железа. Другим компонентом структуры был, в основном, перлит. На фиг. 2 можно констатировать существенно меньший средний размер зерен образца Р 2 5-8 мкм,что связано с низкой конечной температурой охлаждения Т 2 = 480C. Кроме того, перлитная доля в феррите мельче и чуть выше. Из фиг. 3 видно, что материал образца Р 3 содержит мелкое зерно за счет большого числа зародышей при превращении и рекристаллизации структуры при конечной температуре охлаждения Т 3 = 380C и повышающие прочность, в значительной степени однородно распределенные ферритовые области. Перлит и структура верхней промежуточной ступени или верхнего бейнита были другими компонентами улучшенной структуры. На фиг. 4 изображена структура стенки трубы Р 4, образовавшаяся при быстром охлаждении после деформации до конечной температуры охлаждения Т 4 = 300C. Крайне мелкозернистые и узко ограниченные глобулярные ферритные фазы с мелкопластинчатым перлитом и долями промежуточной ступени в нижней бейнитной области придают высокие прочностные значения при улучшенном растяжении материала. При охлаждении стенки трубы со скоростью более 1C/с непосредственно после горячей деформации материала на основе железа такая аустенитная структура, как было обнаружено, может быть в значительной степени переохлаждена относительно равновесия, причем вследствие этого в зависимости от степени переохлаждения и числа зародышей происходит превращение структуры. Предпочтительно посредством предложенного способа по всей длине трубы и неожиданным образом также по сечению можно регулировать нужное равномерное строение структуры, которое определяет также свойства материала. Другими словами, если от трубы требуются принципиальные свойства материала, указывается выбор сплава. Предусмотренный предпочтительный и оптимальный профиль свойств материала может быть достигнут предложенным способом в предложенном устройстве. На фиг. 5 на гистограмме изображены измеренные значения условного предела текучести (Rp)[МПа], предела прочности при растяжении (Rm) [МПа], сужения (Ас) [%] и вязкости (KV 450) [Дж] образцов Р 1-Р 4, т.е. в зависимости от механических свойств материала, достигнутых за счет разных параметров охлаждения при использовании технологии улучшения. При таком же составе стали после редуцирования с растяжением можно предложенным способом повысить предел текучести материала стенки трубы с 424 до 819 МПа и одновременно минимизировать уменьшение значений растяжения с 26 до 10%, причем вязкость материала снизилась со 170 до 160 Дж. При высоких конечных температурах охлаждения, как это справедливо, например, для материала пробы Р 1, наблюдается высокая степень рекристаллизации и образования крупных зерен, что, правда,придает материалу высокую вязкость и сужение, однако обуславливает сравнительно небольшие прочностные значения. Охлаждение до более низких температур превращения повышает прочностные значения стенки трубы и при этом, разумеется, незначительно уменьшает также сужение и вязкость материала, как это показано с помощью образцов Р 2-Р 4. Предложенным способом можно также целенаправленно регулировать строение структур в материале, из чего следует профиль свойств стенки трубы. Например, в трубе-пробе Р 4 за счет низкой температуры превращения удалось достичь высокой степени превращения в нижнюю бейнитную структуру, в результате чего достигается повышение вязкости материала. На фиг. 6 показаны измеренные значения твердости по длине труб-образцов P1, P4. С повышением твердости HRB и прочностных значений материала за счет интенсификации нанесения охлаждающего средства уменьшается также, как было обнаружено, рассеяние S твердости материала по длине трубы. На фиг. 7 изображена характеристика твердости материала в квадрантах по толщине стенки трубыобразца Р 2. Результаты измерений четырех квадрантов Q1-Q4 являются средними значениями соответственно от четырех измерений на квадрант во внешней, средней и внутренней зоне стенки трубы. Как видно из сравнения соответствующих значений твердости по сечению стенки трубы в квадрантах, имеются лишь минимальные отличия в прочности материала, благодаря чему достигаемое качество изделия обеспечивается за счет применения предложенных способа и устройства. ФОРМУЛА ИЗОБРЕТЕНИЯ 1. Способ изготовления труб из стали, прочность и вязкость материала которых повышена за счет быстрого охлаждения непосредственно после горячего формообразования, в частности после деформации посредством редуцирования с растяжением, причем в течение отрезка времени не более 20 с после последней деформации при температуре выше 700C, однако ниже 1050C, в проход на наружную поверхность трубы по периферии на длину, превышающую толщину стенки трубы более чем в 400 раз,наносят охлаждающее средство под повышенным давлением в количестве, которое обеспечивает при быстром охлаждении одинаковую скорость остывания стенки трубы по ее длине более 1C/с с 500 до 250C, после чего осуществляют дальнейшее охлаждение трубы на воздухе до температуры окружающей среды, причем для изготовления труб используют сталь со следующим процентным содержанием в массе легирующих и сопутствующих компонентов или примесей: 2. Способ по п.1, при котором сталь для изготовления труб содержит по меньшей мере один компонент со следующим процентным содержанием в массе: 3. Способ по п.1 или 2, при котором быстрое охлаждение наружной поверхности трубы начинают при температуре ниже 950C. 4. Способ по одному из пп.1-3, при котором после быстрого охлаждения во время последующего охлаждения трубы на воздухе осуществляют целенаправленный обратный нагрев стенки трубы. 5. Способ по одному из пп.1-4, при котором изготавливают трубы нефтяного сортамента длиной более 7 м, в частности до 200 м, наружного диаметра более 20 мм, однако менее 200 мм, и толщиной стенки от 2,0 мм, однако менее 25 мм. 6. Устройство для изготовления труб из стали с химическим составом по п.1 или 2, прочность и вязкость материала которых повышена за счет быстрого охлаждения после деформации, в частности посредством редуцирования с растяжением, состоящее из устройства для нанесения охлаждающего средства на поверхность трубы, отличающееся тем, что в направлении прокатки после последней деформирующей клети расположен переключаемый проходной участок охлаждения с кольцами распределения охлаждающего средства, расположенными друг за другом концентрично вокруг прокатываемого продукта и установленными в продольном направлении с различными интервалами по меньшей мере с тремя направленными к оси соплами, причем каждое кольцо распределения охлаждающего средства или каждая их группа выполнена с возможностью питания охлаждающим средством с регулированием расхода. 7. Устройство по п.6, отличающееся тем, что каждое сопло выполнено с возможностью создания расширяющегося в форме пирамиды в направлении распыления потока охлаждающего средства. 8. Устройство по п.7, отличающееся тем, что поток охлаждающего средства имеет прямоугольную форму сечения, а более длинная ось прямоугольника направлена под углом к оси трубы. 9. Устройство по п.8, отличающееся тем, что система подача охлаждающего средства к проходному участку охлаждения выполнена с возможностью включения в зависимости от положения концов трубы на нем.
МПК / Метки
МПК: C21D 8/10, C21D 9/08, C22C 38/02, C22C 38/04
Метки: устройство, труб, способ, изготовления, стали
Код ссылки
<a href="https://eas.patents.su/8-21245-sposob-i-ustrojjstvo-dlya-izgotovleniya-trub-iz-stali.html" rel="bookmark" title="База патентов Евразийского Союза">Способ и устройство для изготовления труб из стали</a>