Элемент отопительного радиатора с полной антикоррозионной защитой и способ антикоррозионной обработки отопительного радиатора
Формула / Реферат
1. Элемент (1) отопительного радиатора, имеющий корпус (2), изготовленный из алюминия и выполненный с внутренней камерой (5) для циркуляции воды, границы которого определены внутренними поверхностями (6) алюминиевого корпуса (2); причем камера (5) полностью покрыта защитным покрытием (51), выполненным из материала антикоррозионного полимерного покрытия, который защищает внутренние поверхности (6) алюминиевого корпуса (2) при работе от контакта с водой, причем защитное покрытие (51) изготовлено из электрофорезной краски или фторированного полимерного состава.
2. Элемент по п.1, в котором корпус (2) содержит трубчатый корпус (7), имеющий концевую часть (25), которая проходит за пару поперечных соединительных рукавов (9), внутренне соединенных с трубчатым корпусом (7) посредством соответствующих отверстий (29), границы которых определены периферийными кромками (30), при этом корпус выполнен с нижним отверстием (27), закрытым крышкой (28), при этом крышка (28) имеет закрывающую поверхность (33), размещенную внутри концевой части (25) в непосредственной близости от упомянутых отверстий (29).
3. Элемент по п.2, в котором закрывающая поверхность (33) размещена в непосредственной близости от соответствующих участков (37) кромок (30), обращенных к нижнему отверстию (27), и ближе всего к нижнему отверстию (27).
4. Элемент по п.2 или 3, в котором закрывающая поверхность (33) является, по существу, касающейся отверстий (29).
5. Элемент по одному из пп.2-4, в котором крышка (28) вставлена в концевую часть (25) и соединена непроницаемым для текучей среды образом с концевой частью (25).
6. Способ антикоррозионной обработки для элементов отопительного радиатора, имеющих корпус (2), изготовленный из алюминия и выполненный с внутренней камерой (5) для циркуляции воды, границы которого определены внутренними поверхностями (6) алюминиевого корпуса (2), включающий этап, на котором наносят защитное покрытие (51), изготовленное из материала антикоррозионного полимерного покрытия, на внутренние поверхности (6) алюминиевого корпуса (2) с тем, чтобы полностью покрыть камеру (5) для зашиты внутренних поверхностей (6) алюминиевого корпуса (2) при использовании от контакта с водой, в котором защитное покрытие (51) выполнено из материала покрытия, который имеет свойства адгезии к алюминиевым поверхностям и защиты от коррозии, при этом материал покрытия представляет собой:
(А) электрофорезную краску, осажденную посредством процесса электрохимического осаждения, в котором внутренние поверхности (6) приводят в контакт с составом для обработки, содержащим материал покрытия, путем погружения элементов (1), по отдельности или в батарее, в ванну для электроосаждения, содержащую состав для обработки, при этом способ включает этап введения удаляемых электродов (60) в единичные элементы (1) или в большее количество элементов (1), соединенных в батареи (55); либо
(В) материал фторированного полимерного покрытия, нанесенный путем циркуляции состава для обработки, содержащего материал покрытия внутри элементов (1), отдельных или соединенных в батарею, посредством системы (70) принудительной циркуляции.
7. Способ по п.6, содержащий этап заполнения камеры (5) составом для обработки, содержащим материал полимерного покрытия, и этап высушивания камеры, как только материал покрытия приклеился к внутренним поверхностям (6) камеры (5).
8. Способ по п.6 или 7, в котором материал покрытия осаждают посредством процесса электрофореза.
9. Способ по п.6, в котором время контакта элементов (1) с составом для обработки и/или другие рабочие параметры, которые влияют на осаждение защитного покрытия (51), такие как напряжение, приложенное для осуществления электрохимического осаждения материала покрытия, выбирают с тем, чтобы получить полное покрытие всех внутренних поверхностей (6) корпуса (2).
10. Способ по п.9, в котором каждый элемент (1) обрабатывают по отдельности в течение времени контакта, которое меньше чем около 150 с, в частности от около 90 до около 150 с, предпочтительно около 120 с, и при приложенном напряжении, которое меньше чем около 360 В, в частности от около 250 до около 350 В.
11. Способ по п.9, в котором батареи (55), состоящие из 2-4 элементов (1), обрабатывают в течение времени контакта, которое больше чем около 150 с и предпочтительно около 180 с, и при напряжении от около 250 до около 400 В.
12. Способ по п.9, в котором батареи (55), состоящие более чем из одного элемента (1), в частности более чем из четырех элементов (1), обрабатывают в течение времени контакта, которое меньше чем около 150 с, в частности от около 90 до около 150 с и предпочтительно около 120 с, и при приложенном напряжении, которое меньше чем около 360 В, в частности от около 250 до около 350 В.
13. Способ по п.6, в котором электроды 60 выполняют в форме вилок и имеют пару прямолинейных параллельных проводящих стержней (62), вставляемых в соответствующие каналы, выполненные внутри элемента (1) или внутри батареи (55) из элементов (1), соединенных друг с другом.
14. Способ по одному из пп.6-13, в котором защитное покрытие (51) наносят по отдельности на каждый элемент (1) или на множество элементов (1), соединенных с тем, чтобы образовать батарею (55).
15. Способ по одному из пп.6-14, содержащий этап обжига в печи после этапа нанесения защитного покрытия (51).
16. Способ по одному из пп.6-15, в котором корпус (2) элемента (1) содержит трубчатый корпус (7), имеющий концевую часть (25), которая проходит за пару поперечных соединительных рукавов (9), внутренне соединенных с трубчатым корпусом (7) посредством соответствующих отверстий (29), границы которых определены периферийными кромками (30), при этом корпус снабжен нижним отверстием (27), закрытым крышкой (28); при этом способ содержит этап закрытия нижнего отверстия (27) крышкой (28), которая имеет закрывающую поверхность (33), размещенную внутри концевой части (25), в непосредственной близости от упомянутых отверстий (29) для предотвращения образования воздушных карманов во время этапа заполнения камеры (5) составом для обработки.
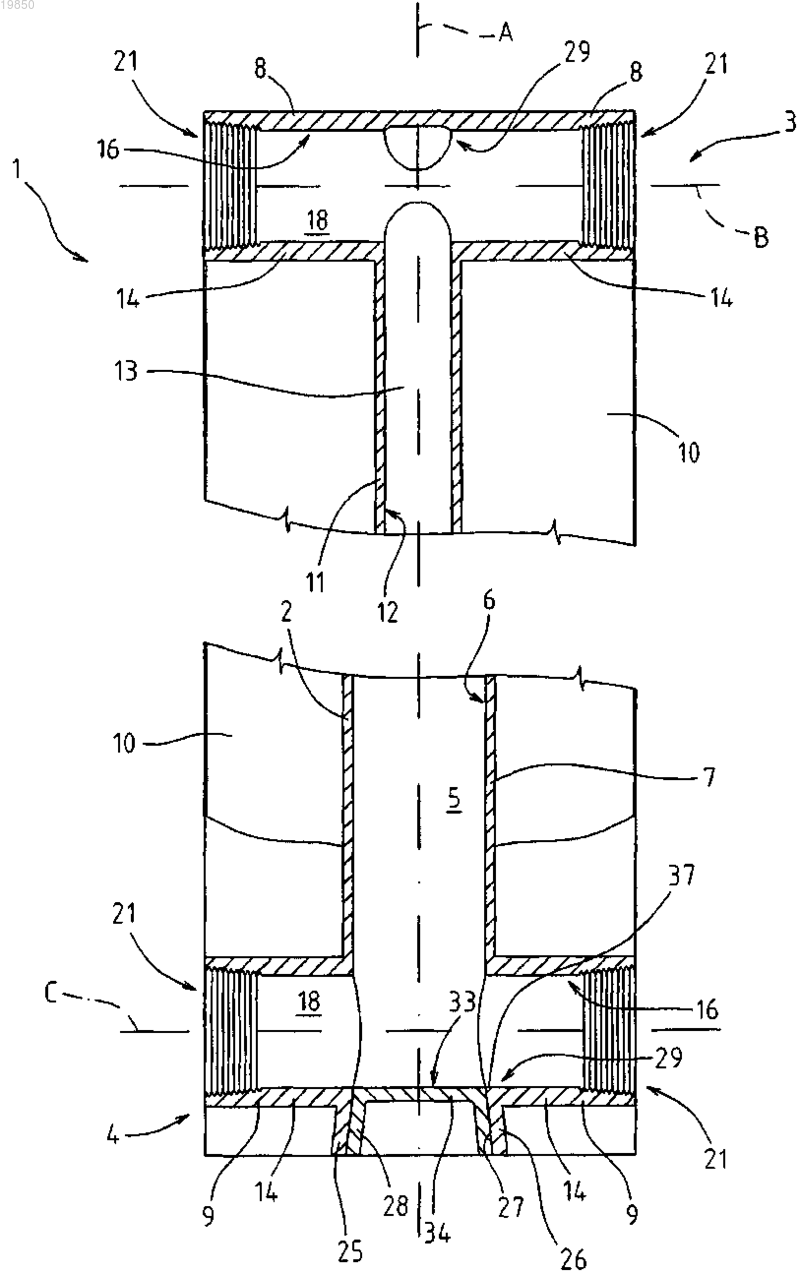
Текст
ЭЛЕМЕНТ ОТОПИТЕЛЬНОГО РАДИАТОРА С ПОЛНОЙ АНТИКОРРОЗИОННОЙ ЗАЩИТОЙ И СПОСОБ АНТИКОРРОЗИОННОЙ ОБРАБОТКИ ОТОПИТЕЛЬНОГО РАДИАТОРА Изобретение относится к элементу (1) отопительного радиатора, имеющему корпус (2),изготовленный из алюминия, полученного литьем под давлением, и выполненный с внутренней камерой (5) для прохождения воды, границы которого определены внутренними поверхностями (6) алюминиевого корпуса (2), который снабжен защитным покрытием (51), выполненным из материла антикоррозионного полимерного покрытия, нанесенного на каждую внутреннюю поверхность(6) алюминиевого корпуса (2) с тем, чтобы полностью покрыть камеру (5) для защиты при работе внутренних поверхностей (6) алюминиевого корпуса (2) от контакта с водой. Нанесение защитного покрытия (51) осуществляют путем заполнения камеры (5) составом для обработки,содержащим материал полимерного покрытия, и затем сушки камеры (5), как только материал покрытия приклеился к внутренним поверхностям (6) камеры (5). Настоящее изобретение относится к элементу отопительного радиатора с полной антикоррозионной защитой и к способу антикоррозионной обработки элементов отопительного радиатора. Как известно, алюминиевый радиатор, полученный литьем под давлением, обычно состоит из батареи элементов, соединенных друг с другом для того, чтобы образовать радиатор соответствующего размера; каждый элемент имеет алюминиевый корпус с внутренней камерой, в которой циркулирует вода отопления. Обычно элемент имеет трубчатый корпус, проходящий продольно, и поперечные соединительные рукава: концевая часть трубчатого корпуса обычно проходит вдоль оси за пару рукавов и образует нижнюю часть элемента, закрытую крышкой. Известные элементы радиатора обычно окрашены снаружи, но не изнутри; таким образом, границы внутренней камеры определены алюминиевыми стенками, поверхности которых при работе находятся непосредственно в контакте с водой и не защищены от коррозии. Действительно, элементы обычно окрашивают с помощью процесса электрофорезного окрашивания, главным образом, анафорезного. Эти способы, в качестве традиционно применяемых, не позволяют полностью покрасить внутреннюю камеру радиаторного элемента, поскольку камера имеет, по существу,трубчатую, очень вытянутую, относительно узкую форму. С другой стороны, электрофорезное окрашивание обычно не применяют к элементам такого типа,потому что проникновение краски может быть неполным, что обусловлено и эффектом клетки Фарадея,который происходит в структуре такого типа, и воздушными карманами в концевых участках элементов,погруженных в ванны для окрашивания. В частности, когда элемент погружен в ванну для окрашивания в обычном положении, обратном по отношению к положению использования (т.е. нижней частью вверх), в дне действительно образуется воздушный карман, который предотвращает доступ и осаждение краски в этой зоне. С другой стороны,та же самая проблема (образование воздушного кармана) возникает также, когда элемент погружен в любой другой резервуар для обработки, например для промывки и для всех предварительных обработок,который обычно осуществляют перед окрашиванием. Следовательно, в настоящее время нет в наличии элементов алюминиевого радиатора, защищенных внутри от коррозии. Вместо этого известны так называемые "биметаллические" радиаторы с центральным трубчатым сердечником, изготовленным из железа или латуни (образующим внутри камеру для циркуляции воды) и покрытым алюминием, и на котором установлены другие наружные алюминиевые части. Этот тип решения приводит к сокращению теплового коэффициента полезного действия (особенно в случае железа, которое является плохим проводником тепла), значительному увеличению веса каждого элемента радиатора и, кроме того, повышает сложность, а также стоимость процесса изготовления и транспортных операций. Задачей настоящего изобретения является создание элемента радиатора, в котором устранены эти недостатки, и, в частности, создание элемента радиатора, который имеет полную противокоррозионную защиту по всем внутренним поверхностям элемента. Таким образом, настоящее изобретение относится к элементу отопительного радиатора и к способу противокоррозионной обработки элементов отопительного радиатора, как определено основными признаками в пп.1 и 9 соответственно приложенной формулы изобретения. Изобретение описано в следующих, не носящих ограничительного характера, вариантах осуществления настоящего изобретения со ссылкой на сопровождающие чертежи, на которых: фиг. 1 представляет собой схематичный вид продольного разреза элемента радиатора согласно настоящему изобретению; фиг. 2 представляет собой вид продольного разреза в соответствии с плоскостью, перпендикулярной плоскости фиг. 1 детали элемента на фиг. 1 с дополнительно увеличенной деталью; на фиг. 3 схематично показан первый вариант осуществления способа противокоррозионной обработки в соответствии с изобретением с деталью в увеличенном масштабе; на фиг. 4 схематично показан второй вариант осуществления способа противокоррозионной обработки в соответствии с изобретением. Как показано на фиг. 1, элемент 1 отопительного радиатора имеет корпус 2, изготовленный из алюминия, например алюминия, литого под давлением, по существу, проходящий вдоль оси A между двумя осевыми концами 3 и 4, которые в соответствии с обычным, по существу, вертикальным положением использования элемента 1 являются верхним и нижним концами соответственно; корпус 2 выполнен с внутренней камерой 5 для прохода воды, границы которой определены внутренними поверхностями 6 алюминиевого корпуса 2. Термин "камера" включает в себя любую зону внутри элемента 1, которая, при работе, смачивается водой, циркулирующей в элементе 1, при этом "внутренними поверхностями" являются все поверхности внутри корпуса 2, которые определяют границы камеры 5 (находясь, таким образом, в контакте с используемой водой). В частности, корпус 2 элемента 1 содержит по меньшей мере один основной трубчатый корпус 7,который проходит продольно вдоль оси A; две пары поперечных соединительных рукавов 8, 9 и множе-1 019850 ство излучающих ребер и/или пластин 10, по-разному соединенных друг с другом и/или с трубчатым корпусом 7. Трубчатый корпус 7 может иметь разнообразную форму и иметь поперечное сечение различной формы, также изменяемое вдоль оси А. Трубчатый корпус 7 имеет боковую стенку 11, размещенную вокруг оси А и выполненную с внутренней поверхностью 12, которая определяет границы основного участка 13 камеры 5. Две пары рукавов 8, 9 размещены на аксиально противоположных концах 3, 4 трубчатого корпуса 7 соответственно; рукава 8, 9 каждой пары проходят от противоположных сторон трубчатого корпуса 7, по существу, перпендикулярно оси А, при этом проходят вдоль соответствующих осей В, С, по существу,параллельными друг другу и перпендикулярными оси А. Каждый из рукавов 8, 9 имеет боковую стенку 14, выполненную с внутренней поверхностью 16, которая определяет границы канала 18. Каждый рукав 8, 9 выполнен с концевым отверстием 21, снабженным внутренней резьбой для соединения нескольких элементов 1 с тем, чтобы образовать радиатор путем вставления определенных соединений (известных и не показанных). Пара рукавов 8, которая при использовании и, таким образом, с элементом 1, который будучи вертикальным находится в верхнем положении, соединена с трубчатым корпусом 7 с тем, чтобы образовать Т-образное соединение; пара рукавов 9, которая при использовании и, таким образом, с элементом 1,который будучи вертикальным находится в нижнем положении, пересекается с трубчатым корпусом 7 на заданном расстоянии от конца 4 трубчатого корпуса 7 и, таким образом, перекрестно соединена с трубчатым корпусом 7. Как видно на фиг. 2, концевая часть 25 трубчатого корпуса 7, которая проходит вдоль оси A за пару нижних рукавов 9 и границы которой определены концевым участком 26 стенки, образует нижнюю часть элемента 1 с нижним отверстием 27, закрытым крышкой 28. Каждый рукав 8, 9 внутренне соединен с трубчатым корпусом 7 посредством отверстия 29, выполненного через боковую стенку 11 трубчатого корпуса 7, и границы которого определены периферийной кромкой 30; рукава 8, 9 каждой пары имеют торцевые отверстия 29, расположенные на одной прямой вдоль осей B, C. Камера 5 содержит основной участок 13, главным образом образованный внутри трубчатого корпуса 7, и каналы 18, образованные внутри рукавов 8, 9; каналы 18 соединены с основным участком 13 посредством отверстий 29. Крышка 28 имеет закрывающую поверхность 33, размешенную внутри концевой части или нижней части 25. Внутренние поверхности 6 корпуса 2 включают в себя поверхность 12, которая определяет границы основного участка 13 камеры 5, поверхности 16, которые определяют границы каналов 18, и закрывающую поверхность 33 крышки 28. Крышка 28 может иметь различные формы: в качестве примера, не носящего ограничительного характера, показанного на фиг. 1 и 2, крышка имеет нижнюю стенку 34 и кольцевой буртик 35, который проходит от периферийной кромки 36 нижней стенки 34. Закрывающая поверхность 33 образована поверхностью нижней стенки 34, обращенной к стороне, противоположной буртику 35. Крышка 28 предпочтительно полностью вставлена в нижнюю часть 25, т.е. в концевую часть трубчатого корпуса 7. Закрывающая поверхность 33 крышки 28 размещена внутри нижней части 25 и в непосредственной близости от кромок 30 отверстий 29 нижних рукавов 9 и, конкретно, в непосредственной близости от участков 37 кромок 30, обращенных к нижнему отверстию 27, и ближе всего к нижнему отверстию 27. В частности, закрывающая поверхность 33 является, по существу, соприкасающейся с отверстиями 29, выполненными в боковой стенке 11 трубчатого корпуса 7 и которые соединяют рукава 9 с камерой 5. Крышка 28 интегрально прикреплена и соединена непроницаемым для текучей среды образом с нижней частью 25 и, конкретно, с концевым участком 26 стенки. Крышка 28 может быть соединена с нижней частью 25 различным образом, например с помощью сварки, пластической деформации, герметичных уплотнений, заклеивания и т.д. Крышка 28 предпочтительно прикреплена к нижней части 25 (т.е. к концевому участку 26 стенки) посредством наружной радиальной сварки, т.е. посредством сварного шва, выполненного на радиальных наружных поверхностях крышки 28 (конкретно, буртика 35); посредством этого устраняют вещества, остающиеся после сварки,или искры внутри камеры, которые могут отделяться и вызвать рабочие проблемы в работе элемента 1. Кроме того, концевая часть 25 трубчатого корпуса 7, которая образует нижнюю часть, предпочтительно имеет развальцовку, расходящуюся наружу (т.е. по направлению к нижнему отверстию 27), при этом крышка 28 (в частности, ее буртик 35) имеет соответствующую расширяющуюся книзу форму. Понятно, что крышка 28 может быть различной формы; например, согласно одному возможному варианту крышка является, по существу, плоской, например состоящей только из нижней стенки 34, и размещается внутри нижней части 25, при этом периферийная кромка 36 вставлена в гнездо, полученное в концевом участке 26 стенки, который также может быть, по существу, параллелен оси А и не расширяться книзу. Камера 5 полностью покрыта защитным покрытием 51, изготовленным из материала антикоррозионного полимерного покрытия, нанесенного на все внутренние поверхности 6 алюминиевого корпуса 2,и которое защищает поверхности 6 при работе от контакта с водой. В частности, покрытие 51 изготовлено из краски, полученной электрофорезом, например эпоксидной или акриловой смолы, или фторированного полимерного покрытия (например, на основе Тефлона) или подобных продуктов. На фиг. 3 схематично показан первый вариант осуществления способа антикоррозионной обработки элемента 1, в котором покрытие 51 наносят на поверхности 6 посредством процесса электрохимического осаждения и, конкретно, посредством процесса электрофореза (катафорезного или анафорезного окрашивания). Как известно, в процессах электрофореза используется электрокинетическое явление, заключающееся в перемещении электрически заряженных частиц, диспергированных в текучей среде, под действием электрического поля, приложенного с помощью пары электродов к самой текучей среде. Частицы перемещаются по направлению к катоду (катафорез), если они заряжены положительно, и по направлению к аноду (анафорез), если они заряжены отрицательно. Элементы 1, по отдельности или в батарее, свешивают с приводной системы 52, которая транспортирует их к резервуару 53 для обработки, который в зависимости от контекста используется для окрашивания наружных частей элементов 1. Для того чтобы получить хорошее окрашивание наружных поверхностей элементов 1, элементы 1 подвешивают вертикально в положении, обратном по отношению к положению обычного использования, и, таким образом, рукава 9 и концевая часть 25, образующие нижнюю часть, обращены вверх, при этом рукава 8 обращены вниз. В примере на фиг. 3 показана батарея 55 из элементов 1, соединенных друг с другом посредством соответствующих рукавов 8, 9 (и образующих, таким образом, радиатор требуемой длины); при этом соответствующие отверстия 21 концевых элементов 1 батареи 55 открыты. Рукава 8, 9 элементов 1 очевидным образом расположены на одной прямой и образуют соответствующие непрерывные трубопроводы 56, образованные каналами 18 единичных рукавов 8, 9. Резервуар 53 содержит ванну для электроосаждения, например, состоящую из воды и жидкого состава для обработки, содержащего материал для электроосаждения, который образует материал антикоррозионного полимерного покрытия; в частности, ванна содержит катафорезную или анафорезную краску(т.е. состоящую из положительно или отрицательно заряженных частиц), содержащую полимерные смолы (например, эпоксидную, акриловую и т.д.), пигменты, наполнители, добавки и растворители. Вынимаемые электроды 60 вставлены в трубопроводы 56. Электроды 60 предпочтительно выполнены в форме вилок и имеют стойку 61, из которой выступают два параллельных прямолинейных проводящих стержня 62, эти стержни могут быть вставлены в рукава 8, 9; каждый стержень 62 покрыт снаружи изолирующей оболочкой 63, имеющей отверстия 64, разнесенные вдоль стержня 62. Электроды 60 дополнительно снабжены изолирующими опорными участками 65, например, образованными дисками,установленными на стержнях 62 близко к стойке 61, и при работе взаимодействующими примыкающим образом с соответствующими фронтальными кромками рукавов 8, 9, через которые вставлены электроды. Электроды 60, как и дополнительные электроды 66, погруженные в резервуар 53, электрическим образом соединены посредством соединения 67 с полюсом выпрямителя (известен и не показан), в то время как элементы 1 соединены с противоположным полюсом посредством соединения 68, объединенного с приводной системой 52. Очевидно, что возможно работать и с катафорезными красками и с анафорезными красками путем соединения электродов 60, 66 и элементов 1 с соответствующими полюсами; элементы 1 будут соединены с полюсом, имеющим противоположный знак по отношению к зарядам частиц краски, с тем, чтобы притягивать эти частицы. Когда батарея 55 погружена в ванну для электроосаждения и в резервуаре 53 приложено электрическое поле (путем приложения заданного напряжения), частицы краски мигрируют по направлению к элементам 1, где краска схватывается и осаждается на поверхностях 6, образуя, таким образом, покрытие 51. После осаждения покрытия 51 элементы 1 вынимают из резервуара 53 и (при этом электроды 60 уже удалены) направляют к так называемому этапу обжига, например, осуществляемому в печи, для сушки и возможной полимеризации материала полимерного покрытия. Понятно, что описанная обработка может быть также применена по отдельности к каждому элементу 1 перед тем, как элементы соединяют с тем, чтобы образовать батарею 55. В этом случае использование электродов 60, вставленных в рукава 8, 9, может быть ненужным, но потребуется соответствующим образом изменить рабочие параметры процесса электроосаждения. В целом, время контакта между элементами 1 и составом для обработки (т.е. время нахождения элементов 1 в ванне, определяемое скоростью, с которой приводная система 52 перемещает элементы через резервуар 53) и/или другие рабочие параметры, которые влияют на осаждение покрытия 51, такие как, в частности, напряжение, приложенное к ванне для того, чтобы способствовать электрохимическому осаждению материала покрытия, выбирают с тем, чтобы получить полное покрытие всех поверхностей 6. В качестве примера полное покрытие поверхностей 6 получают:a) без использования электродов 60, путем обработки каждого элемента 1 по отдельности, в течение времени контакта, которое меньше чем около 150 с, в частности от около 90 до около 150 с и предпочтительно около 120 с, при этом приложенное напряжение меньше чем около 360 В, в частности от около 250 до около 350 В;b) без использования электродов 60, путем обработки батарей 55 из нескольких элементов 1, в частности до четырех элементов 1, в течение времени контакта, которое больше чем около 150 с, предпочтительно около 180 с и с напряжением от около 250 до около 400 В, предпочтительно выше чем около 350 В;c) с электродами 60, путем обработки батарей 55, состоящих из нескольких элементов 1, в частности более чем из четырех элементов 1, в течение времени контакта, которое меньше чем около 150 с, в частности от около 90 до около 150 с, предпочтительно около 120 с и с приложенным напряжением, которое меньше чем около 360 В, в частности от около 250 до около 350 В; Согласно варианту осуществления настоящего изобретения на фиг. 4 покрытие 51 наносят путем введения жидкого состава для обработки, содержащего материал полимерного покрытия, который имеет свойства адгезии к алюминиевым поверхностям и защиты от коррозии, в одиночный элемент 1 или, как показано на фиг. 4, в батарею 55 соединенных элементов 1. Например, используются фторированные полимерные составы (такие как Тефлон) или подобные продукты. Батарея 55 соединена с системой 70 для принудительной циркуляции состава для обработки; два из четырех в сумме отверстий 21 концевых элементов 1 батареи 55 используются для подсоединения к системе 70, будучи, в частности, подсоединенными посредством соответствующих отдельных соединений 72, к питающей трубе 71 и к выводящей трубе 74 соответственно; при этом два других отверстия закрыты снимаемыми эксплуатационными крышками 75. Когда состав для обработки циркулирует через элементы 1, материал полимерного покрытия, содержащийся в составе для обработки, осаждается на внутренних поверхностях 6 и прилипает к ним. Как только элементы 1 были высушены от состава для обработки, который не приклеился к поверхностям 6,батарею 55 направляют в печь для этапа сушки и/или (если требуется) возможной полимеризации. Затем батарею 55 направляют на этап окрашивания для того, чтобы покрасить элементы 1 снаружи посредством традиционного электрофорезного или порошкового окрашивания. Понятно, что окрашивание наружных частей может быть осуществлено до описанной выше обработки внутренних поверхностей 6 (которая могла бы быть применена таким образом к предварительно окрашенным снаружи элементам 1). Преимущества изобретения очевидны из приведенного выше описания. Элемент радиатора по изобретению полностью защищен от коррозии, так же и на всех его внутренних поверхностях, и таким образом может работать в течение длительных периодов времени, даже в условиях особенно агрессивных вод. Защитное антикоррозионное покрытие наносят либо во время этапа окрашивания элемента снаружи, используя, таким образом, одну и ту же операцию и один и тот же процесс электрохимического осаждения, или во время отдельного этапа, который, однако, осуществить более просто и быстро. В обоих случаях способ обработки является простым, выгодным с точки зрения стоимости и полностью эффективным. Если материал покрытия осаждают посредством процесса электрохимического осаждения (в частности, посредством процесса электрофореза), наличие электродов, расположенных внутри элемента, позволяет полностью покрыть поверхности покрытия в каждой точке внутренних поверхностей элемента. Особенная форма закрывающей крышки нижней части позволяет избежать образования воздушных карманов точно внутри нижней части, когда элемент погружен в состав для обработки в обычном положении, обратном по отношению к положению использования (т.е. нижней частью вверх), или во всех случаях во время этапа заполнения внутренней камеры составом для обработки. Таким образом, все внутренние поверхности элемента могут быть полностью обработаны, в частности промыты, предварительно обработаны и/или окрашены. Кроме того, понятно, что дополнительные изменения и перемены могут быть произведены в проиллюстрированном здесь описании, не выходя за объем изобретения, как он определен приложенной формулой изобретения. ФОРМУЛА ИЗОБРЕТЕНИЯ 1. Элемент (1) отопительного радиатора, имеющий корпус (2), изготовленный из алюминия и выполненный с внутренней камерой (5) для циркуляции воды, границы которого определены внутренними поверхностями (6) алюминиевого корпуса (2); причем камера (5) полностью покрыта защитным покрытием (51), выполненным из материала антикоррозионного полимерного покрытия, который защищает внутренние поверхности (6) алюминиевого корпуса (2) при работе от контакта с водой, причем защитное покрытие (51) изготовлено из электрофорезной краски или фторированного полимерного состава. 2. Элемент по п.1, в котором корпус (2) содержит трубчатый корпус (7), имеющий концевую часть(25), которая проходит за пару поперечных соединительных рукавов (9), внутренне соединенных с трубчатым корпусом (7) посредством соответствующих отверстий (29), границы которых определены периферийными кромками (30), при этом корпус выполнен с нижним отверстием (27), закрытым крышкой(28), при этом крышка (28) имеет закрывающую поверхность (33), размещенную внутри концевой части(25) в непосредственной близости от упомянутых отверстий (29). 3. Элемент по п.2, в котором закрывающая поверхность (33) размещена в непосредственной близости от соответствующих участков (37) кромок (30), обращенных к нижнему отверстию (27), и ближе всего к нижнему отверстию (27). 4. Элемент по п.2 или 3, в котором закрывающая поверхность (33) является, по существу, касающейся отверстий (29). 5. Элемент по одному из пп.2-4, в котором крышка (28) вставлена в концевую часть (25) и соединена непроницаемым для текучей среды образом с концевой частью (25). 6. Способ антикоррозионной обработки для элементов отопительного радиатора, имеющих корпус(2), изготовленный из алюминия и выполненный с внутренней камерой (5) для циркуляции воды, границы которого определены внутренними поверхностями (6) алюминиевого корпуса (2), включающий этап,на котором наносят защитное покрытие (51), изготовленное из материала антикоррозионного полимерного покрытия, на внутренние поверхности (6) алюминиевого корпуса (2) с тем, чтобы полностью покрыть камеру (5) для зашиты внутренних поверхностей (6) алюминиевого корпуса (2) при использовании от контакта с водой, в котором защитное покрытие (51) выполнено из материала покрытия, который имеет свойства адгезии к алюминиевым поверхностям и защиты от коррозии, при этом материал покрытия представляет собой:(А) электрофорезную краску, осажденную посредством процесса электрохимического осаждения, в котором внутренние поверхности (6) приводят в контакт с составом для обработки, содержащим материал покрытия, путем погружения элементов (1), по отдельности или в батарее, в ванну для электроосаждения, содержащую состав для обработки, при этом способ включает этап введения удаляемых электродов (60) в единичные элементы (1) или в большее количество элементов (1), соединенных в батареи (55); либо(В) материал фторированного полимерного покрытия, нанесенный путем циркуляции состава для обработки, содержащего материал покрытия внутри элементов (1), отдельных или соединенных в батарею, посредством системы (70) принудительной циркуляции. 7. Способ по п.6, содержащий этап заполнения камеры (5) составом для обработки, содержащим материал полимерного покрытия, и этап высушивания камеры, как только материал покрытия приклеился к внутренним поверхностям (6) камеры (5). 8. Способ по п.6 или 7, в котором материал покрытия осаждают посредством процесса электрофореза. 9. Способ по п.6, в котором время контакта элементов (1) с составом для обработки и/или другие рабочие параметры, которые влияют на осаждение защитного покрытия (51), такие как напряжение, приложенное для осуществления электрохимического осаждения материала покрытия, выбирают с тем, чтобы получить полное покрытие всех внутренних поверхностей (6) корпуса (2). 10. Способ по п.9, в котором каждый элемент (1) обрабатывают по отдельности в течение времени контакта, которое меньше чем около 150 с, в частности от около 90 до около 150 с, предпочтительно около 120 с, и при приложенном напряжении, которое меньше чем около 360 В, в частности от около 250 до около 350 В. 11. Способ по п.9, в котором батареи (55), состоящие из 2-4 элементов (1), обрабатывают в течение времени контакта, которое больше чем около 150 с и предпочтительно около 180 с, и при напряжении от около 250 до около 400 В. 12. Способ по п.9, в котором батареи (55), состоящие более чем из одного элемента (1), в частности более чем из четырех элементов (1), обрабатывают в течение времени контакта, которое меньше чем около 150 с, в частности от около 90 до около 150 с и предпочтительно около 120 с, и при приложенном напряжении, которое меньше чем около 360 В, в частности от около 250 до около 350 В. 13. Способ по п.6, в котором электроды 60 выполняют в форме вилок и имеют пару прямолинейных параллельных проводящих стержней (62), вставляемых в соответствующие каналы, выполненные внутри элемента (1) или внутри батареи (55) из элементов (1), соединенных друг с другом. 14. Способ по одному из пп.6-13, в котором защитное покрытие (51) наносят по отдельности на каждый элемент (1) или на множество элементов (1), соединенных с тем, чтобы образовать батарею (55). 15. Способ по одному из пп.6-14, содержащий этап обжига в печи после этапа нанесения защитного покрытия (51). 16. Способ по одному из пп.6-15, в котором корпус (2) элемента (1) содержит трубчатый корпус (7),имеющий концевую часть (25), которая проходит за пару поперечных соединительных рукавов (9), внутренне соединенных с трубчатым корпусом (7) посредством соответствующих отверстий (29), границы которых определены периферийными кромками (30), при этом корпус снабжен нижним отверстием (27),закрытым крышкой (28); при этом способ содержит этап закрытия нижнего отверстия (27) крышкой (28),которая имеет закрывающую поверхность (33), размещенную внутри концевой части (25), в непосредственной близости от упомянутых отверстий (29) для предотвращения образования воздушных карманов во время этапа заполнения камеры (5) составом для обработки.
МПК / Метки
МПК: F28D 1/053, C09D 5/08, C25D 13/14, C25D 13/22, C25D 13/04, F16L 58/10, F28F 19/04
Метки: отопительного, полной, защитой, обработки, радиатора, элемент, способ, антикоррозионной
Код ссылки
<a href="https://eas.patents.su/8-19850-element-otopitelnogo-radiatora-s-polnojj-antikorrozionnojj-zashhitojj-i-sposob-antikorrozionnojj-obrabotki-otopitelnogo-radiatora.html" rel="bookmark" title="База патентов Евразийского Союза">Элемент отопительного радиатора с полной антикоррозионной защитой и способ антикоррозионной обработки отопительного радиатора</a>
Предыдущий патент: Способ лечения, подавления, ингибирования или уменьшения инцидентов симптомов, ассоциированных с почечным заболеванием: гипогонадизма и непроизвольной потери веса
Следующий патент: Контейнер с ломким герметичным входным отверстием и паропроницаемым вентиляционным отверстием
Случайный патент: Получение механоактивированных аморфной и аморфно-кристаллической кальциевых солей глюконовой кислоты