Система для гидрирования тетрагалогенида кремния и кремния в тригалогенсилан
Формула / Реферат
1. Система для гидрирования тетрагалогенида кремния и кремния в тригалогенсилан, включающая в себя емкость высокого давления без внутренних распределителей потока для вмещения множества частиц металлургического кремния, имеющую одно или более отверстий для входа газа, одно или более отверстий для входа твердых веществ, одно или более спускных отверстий для твердых веществ и один или более выходов для смесей газ/твердые вещества, причем система содержит
первый теплообменник для нагрева подаваемого потока жидкого тетрагалогенида кремния, причем указанный нагретый жидкий тетрагалогенид кремния смешивают с водородом, чтобы понизить температуру испарения тетрагалогенида кремния;
второй теплообменник для испарения смеси тетрагалогенида кремния и водорода, причем источником тепла являются горячие газы, выходящие из других компонентов системы;
третий теплообменник для повышения температуры испаренной смеси до 500-600°C, где нагрев обеспечен выходящим потоком из емкости высокого давления, причем поток, покидающий третий теплообменник, поступает в емкость высокого давления, причем тепло, обеспеченное потоком из емкости высокого давления, служит источником тепла для подаваемого потока тетрагалогенида кремния, поступающего в первый теплообменник.
2. Система для гидрирования смеси тетрагалогенида кремния и кремния в тригалогенсилан, включающая
реакционную емкость, имеющую заключенный в ней пористый слой частиц металлургического кремния, причем указанная реакционная емкость имеет одно или более отверстий для входа смеси испаренного тетрагалогенида кремния и водорода в своей нижней части, одно или более отверстий для входа твердых веществ в своей верхней части для подачи в указанный реактор дополнительных гранулированных частиц металлургического кремния, одно или более спускных отверстий в нижней части для удаления отработанных твердых веществ и одно или более выходных отверстий в точке над упомянутым слоем частиц металлургического кремния для удаления выходящего тригалогенсиланового газа, который может также включать унесенные твердые частицы;
первый теплообменник для нагрева подаваемого потока жидкого тетрагалогенида кремния, указанный нагретый жидкий тетрагалогенид кремния, выходящий из первого теплообменника, смешивается с водородом, чтобы понизить температуру испарения жидкого тетрагалогенида кремния;
испаритель для испарения смеси тетрагалогенида кремния и водорода;
второй теплообменник для повышения температуры испаренной смеси тетрагалогенида кремния и водорода до 450-550°C, причем нагрев обеспечивается выходящим из указанной реакционной емкости газовым потоком, причем указанный газовый поток, выходящий из указанной реакционной емкости и затем покидающий второй теплообменник, служит источником тепла для подаваемого потока тетрагалогенида кремния, поступающего в первый теплообменник.
3. Система по п.2, в которой источником тепла для испарителя является пар.
4. Система по п.2, дополнительно включающая сепаратор для удаления унесенных твердых веществ из выходящего тригалогенсиланового газа, покидающего реактор.
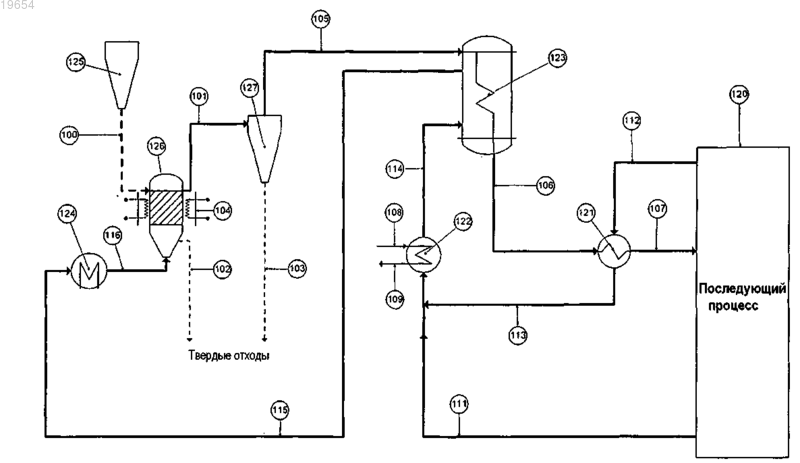
Текст
СИСТЕМА ДЛЯ ГИДРИРОВАНИЯ ТЕТРАГАЛОГЕНИДА КРЕМНИЯ И КРЕМНИЯ В ТРИГАЛОГЕНСИЛАН Реактор для гидрирования тетрагалогенида кремния и металлургического кремния до тригалогенсилана включает слой частиц металлургического кремния, одно или более отверстий для входа газа, одно или более отверстий для входа твердых веществ, одно или несколько спускных отверстий для твердых веществ и одно или более отверстий для удаления тригалогенсилана из реактора. Свежие поверхности образуются на частицах слоя путем внутреннего измельчения и истирания в результате уноса поданных с питанием частиц кремния в поток питания тетрагалогенид кремния/водород, входящий в реактор, и столкновения этого потока со слоем частиц кремния. Это обладает преимуществом наивысшего выхода тригалогенсилана, более высокой степени выгорания MGS, удаления использованного MGS в виде уноса мелкой пыли в выходящем тригалогенсилане, покидающем реактор, и более длительного времени между остановками для удаления слоя. Предпосылки создания изобретения Данное изобретение, в общем, относится к области получения высокочистого кремния и, более конкретно, к устройству и способу гидрирования тетрагалогенида кремния и кремния в тригалогенсилан. Тригалогенсиланы, такие как SiHCl3 и SiHBr3, были впервые получены реакцией кремния с соответствующим галогенидом водорода HCl или HBr при температуре приблизительно 350C и приблизительно атмосферном давлении. Выходы при этой реакции обычно очень высоки, в литературе указываются выходы, превышающие 90%, причем остальное представляет собой тетрагалогенид кремния. Наиболее широко используемым тригалогенсиланом является трихлорсилан, который очищают и разлагают,чтобы получить очень чистый кремний. Эта реакция разложения образует также тетрагалогенид кремния, который таким образом накапливается в процессе. Для того чтобы минимизировать образование тетрагалогенида кремния, предпринимались различные меры, такие как возврат тетрагалогенида в цикл и использование очень большого избытка водорода в реакторе разложения. Избыточный тетрагалогенид также окисляли до аморфного диоксида кремния, причем образующиеся в результате газообразные галогены отделяют промывкой. Более недавний новый способ, основанный на исследованиях DOE/JPL и описанный Breneman в USP 4676967, превращает избыточный тетрагалогенид кремния в тригалогенсилан путем его реакции с водородом и кремнием при высоких температуре и давлении в присутствии медного катализатора. По предшествующей технологии, описанной Breneman в USP 4676967, проводят реакцию между кремнием, тетрагалогенидом кремния и водородом при примерно 400-600C и давлением между 300 и 600 psi в реакторе псевдоожиженного слоя, содержащем распределительные устройства выше камеры смешения. В промышленных осуществлениях вышеуказанного патента входные газовые потоки тетрахлорида кремния и водорода предпочтительно нагревают по отдельности до разных температур и давлений и затем смешивают в камере смешения перед пропусканием через распределительное устройство для образования пузырей, которые контактируют с тонко измельченным кремнием и флюидизируют его. Водород нагревают до 500C при 325 psig, в то время как тетрахлорид кремния нагревают до 500C при 575 psig, что выше 530 psig - критического давления тетрахлорида кремния, и затем снижают давление до 325 psig при смешении с водородом. Промышленные реакторы, спроектированные согласно Breneman, имеют меньший выход, чем в лабораторных испытаниях более малого масштаба, таких как проведенные Ingle и обсужденные в "Kineticsof the Hydrogenation of Silicon Tetrachloride", W. Ingle and M. Peffley, J, Electrochem. Soc., May 1985,pp.1236-1240, и выход понижается со временем с крайней необходимостью выгрузить весь слой кремния и перезапуститься со свежим материалом. Замедление смешения в камере смешения повышает капитальные затраты и эксплуатационные расходы, так как оно делает более трудной утилизацию тепла горячих выходящих газов и вызывает затруднения при работе. Тетрагалогенид кремния часто содержит значительные следы тригалогенсилана и дигалогенсилана, которые могут разлагаться до кремния в подогревателях тетрагалогенида, вызывая закупорку. Использование двух отдельных подогревателей увеличивает капитальные затраты по сравнению с одинарной технологической цепочкой и делает более трудным утилизацию тепла отработанного газа, которая улучшает использование энергоресурсов. Изготовление распределительных устройств увеличивает капитальные затраты. Более низкий выход у промышленных реакторов может быть отнесен на счет конструкции распределительного устройства и выбора типичных условий работы псевдоожиженного слоя, которые вызывают байпассирование кремния крупными пузырями реагирующего газа, что означает, что часть реагирующего газа имеет очень короткое время пребывания. Из работы Ingle можно видеть, что выход зависит от времени пребывания, но со временем достигает плато; таким образом смесь газа с низким и высоким временем пребывания будет давать более низкий выход, чем при таком же среднем времени пребывания,когда весь газ имеет одинаковое время пребывания. Уменьшение выхода со временем вызывается накоплением примесей на поверхности материалов слоя кремния, как обсуждалось в работе Bade, S. "Mechanochemical reaction of metallurgical grade silicon with gaseous hydrogenchloride in a vibration mill", S. Bade etal., Int. J. Mineral Processing, 44-45 (1996), 167-179. Конструкция камеры согласно стандартной практике псевдоожиженного слоя минимизирует степень истирания, что таким образом не отвечает требованию обеспечения достаточной новой реакционной поверхности. Для того чтобы улучшить выход, важно определ Umb параметры процесса более конкретным образом, чем очень общее определение температуры между 400 и 600C и давления от 300 до 600 psig. Ключевым критерием является отношение (U/Umb) приведенной скорости U к минимальной скорости образования пузырей Umb. Приведенная скорость представляет собой фактический объемный поток, приведенный к рабочим температуре и давлению, деленный на площадь поперечного сечения аппарата. Минимальная скорость образования пузырей Umb представляет собой минимальную приведенную скорость, при которой образуются пузыри, и является важной, так как пузыри движутся быстрее, чем газ в пустотах между частицами, и таким образом имеют меньшее время пребывания. Эта скорость зависит от свойств газа и от размера, формы и плотности гранулированных частиц. Имеется много путей рассчитать это свойство, включая компьютерные программы. Для крупных частиц, больших, чем 200 мкм, величина Umb является практически такой же, как приведенная скорость при минимальной флюидизации, Umf. Известно, что обеспечение большего измельче-1 019654 ния явилось ценным в похожем процессе реакции металлургического кремния с хлористым водородом,как обсуждалось в работе Bade. Измельчение повышает скорость реакции и выход, но способ Bade использования шаровой мельницы является затруднительным и дорогим в осуществлении при высоком давлении 500 psig и высокой температуре, 500C, требующихся для этой реакции. Таким образом, имеется потребность в реакторе и совокупности рабочих параметров, которые обеспечат более равномерный контакт газ/твердые вещества, большее измельчение, лучшую утилизацию энергии и более низкие капитальные и эксплуатационные затраты. Сущность изобретения Системы, включающие изобретение, обеспечивают более высокий выход тригалогенсилана, более низкую стоимость производства, более низкие эксплуатационные расходы, высокое потребление подаваемого кремния, гибкие требования к распределению размеров частиц подаваемого металлургического кремния и легко поддающуюся регулированию работу. Другие цели и преимущества изобретения станут очевидны из последующего описания, сделанного в связи с прилагаемыми чертежами, в котором путем иллюстрации и примера раскрыто осуществление настоящего изобретения. В соответствии с предпочтительным осуществлением изобретения устройство для гидрирования тетрагалогенида кремния и кремния в тригалогенсилан включает емкость, не имеющую внутренних распределителей потока, одно или более отверстий для входа газа, одно или более отверстий для входа твердых веществ, одно или более спускных отверстий для твердых веществ, один или более выходов для смеси газ/твердые вещества и образование свежих поверхностей струйным размолом. Способ также охватывает дополнительно выбор набора рабочих параметров для того, чтобы использовать все преимущества устройства и примера улучшенного интегрирования тепла. Это устройство обладает преимуществом более высоких скоростей реакции, более высоких выходов тригалогенсилана и более низких капитальных и эксплуатационных затрат благодаря лучшему интегрированию тепла с остальной частью процесса. Краткое описание чертежей Чертежи составляют часть данного описания изобретения и включают примеры вариантов осуществления изобретения, которое может быть осуществлено в разнообразных формах. Должно быть понятно, что в некоторых случаях различные аспекты изобретения могут быть показаны излишне подчеркнуто или подробно, чтобы облегчить понимание изобретения. Фиг. 1 является принципиальной схемой, иллюстрирующей в целом работу системы, включающей изобретение. Фиг. 2 является поперечным сечением реакторной части фиг. 1. Фиг. 3 является поперечным сечением генерирующего истирание канала ввода газа реакторной части фиг. 2. Фиг. 4 является модифицированной версией фиг. 3, показывающей два входных канала. Подробное описание изобретения Здесь представлено подробное описание варианта осуществления изобретения, включающего характерные признаки изобретения. Однако должно быть понятно, что настоящее изобретение может быть осуществлено в разнообразных формах. Поэтому конкретные подробности, раскрытые здесь, должны интерпретироваться не как ограничительные, а скорее, как основание для формулы изобретения и как представительная основа для указаний специалисту, как применить настоящее изобретение в практически любой подходящей детализированной системе, структуре и любым подходящим образом. Обратимся вначале к фиг. 1, где показана общая принципиальная схема, иллюстрирующая осуществление изобретения, использованного для экономии энергозатрат при интеграции в общий процесс получения тригалогенсилана. Рецикловый поток 112 жидкого тетрагалогенида кремния под высоким давлением уходит из расположенного ниже по потоку процесса 120 и подогревается в первом теплообменнике 121 путем теплообмена с потоком выходящего газа 106, чтобы образовать нагретый поток 113,который затем смешивают с рецикловым потоком сжатого водорода 111 также из расположенного ниже по потоку процесса 120, чтобы понизить температуру испарения потока 112 жидкого тетрагалогенида кремния. Смесь затем испаряют в испарителе 122. Тепло может быть обеспечено любым энергоресурсом,но особо выгодно использовать пар 108 и извлекать конденсат 109. Полученный смешанный паровой поток 114 затем подогревают во втором теплообменнике 123, который одновременно охлаждает циклонный выходной поток 105 из реакторного циклона 127. Очень горячий поток 115 с температурой 450-550C, покидающий второй теплообменник 123, дополнительно нагревают в электрическом подогревателе 124, чтобы довести температуру до 500-600C во входном канале газового потока 116 перед его входом в реактор 126 гидрирования со своим собственным электроподогревателем 104. Этот подогреватель может быть внешним, как показано, или может быть внутренним с проникновением через стенку реактора. Гранулированный металлургический кремний, MGS (metallurgical grade silicon) обычно от примерно 440 до примерно 700 микрон в диаметре периодически добавляется из воронки-затвора 125 потоком 100 MGS и реагирует с нагретым до 500-600C входным газовым потоком 116, чтобы образовать продуктовый поток 101 желаемого трихлорсилана. Этот продуктовый поток 101 затем поступает в циклон 127, где удаляют основной поток 103 твердых отходов из отра-2 019654 ботанного металлургического кремния. Выходной поток 105 циклона затем охлаждают во втором теплообменнике 123, чтобы образовать охлажденный поток выходящего газа 106, который затем дополнительно охлаждают в первом теплообменнике 121, чтобы образовать охлажденный поток 107, который затем проходит на расположенный ниже по потоку процесс 120. В прототипе выход понижался со временем, поэтому основной поток 102 отходов также удаляли из процесса на периодической основе, обычно раз в год путем опорожнения всего реактора. Это является нежелательным из-за потери выхода во время работы и времени и последующей потери продукции, связанной с остановкой. В настоящем способе измельчение (истирание) предложено для того, чтобы удалить нереакционноспособный поверхностный слой, который нарастает со временем в реакторе 126 и чтобы таким образом вывести его в виде пыли в поток 103 отходов циклона. Специфическая конструкция механизма истирания рассмотрена ниже касательно фиг. 2 и 3. Фиг. 2 является видом в разрезе реакторной части 200, соответствующей реактору гидрирования 126 на фиг. 1. Поток 201 газа, который соответствует 500-600C потоку 116 входного газа фиг. 1, поступает через керамическую вставку 206 во входную форсунку 204, расположенную в днище реактора 126,увлекая за собой часть твердых частиц кремния, когда он образует внутреннюю струю 203. Газ в струе 203 затем разгоняет унесенные частицы 202, пока они не ударяют слой частиц 211, расположенный внутри реактора, во время чего происходит измельчение вследствие соударения быстро движущихся унесенных частиц 202 с относительно неподвижными частицами 211 основной массы слоя. Реактор не содержит никаких внутренних распределителей потока для направления потоков входного газа. Газ 205 рассеивается из струи 203 и течет вверх через слой неподвижных частиц 211. Часть газа может образовывать пузыри 212, как показано, но это не требуется для работы. В действительности предпочтительно,чтобы по меньшей мере 90% объема слоя не содержало пузырей. Выходящий газ 208 покидает верх 213 слоя частиц 211 и уносит с собой некоторые небольшие частицы пыли 209, часть из которых выпадает 210 в сепарационном пространстве 214 над слоем, а часть уносится с выходящим газом 208 через выход 215. Выходящий газ 208, который является смесью газа и пыли в потоке 216, поступает затем в циклон 217, который соответствует циклону 127 фиг. 1, где большая часть пыли 218 удаляется в поток 103 отходов циклона, и очищенный газ уходит с верха циклона в поток 219, который соответствует выходящему из циклона потоку 105 фиг. 1. Дополнительный металлургический кремний 220 добавляют через канал 207 ввода кремния, который показан как входящий через боковую стенку вблизи от верха реактора 200. Хотя реактор описан как имеющий керамическую вставку 206 во входной форсунке 204, один или несколько других входов и выходов могут быть также футерованы устойчивой к истиранию керамической композицией. Подходящие материалы включают, но не ограничиваются этим, нитрид кремния, оксид кремния, оксинитрид кремния, оксид алюминия, муллит или карбид кремния. Фиг. 3 является дополнительно увеличенным видом в разрезе впуска 300 в реактор, заполненный слоем частиц 310 MGS (соответствующим слою частиц 211 фиг. 2). Единичный впуск 305 сконструирован так, чтобы создавать интенсивное истирание частиц 310 металлургического кремния путем использования входного газового потока 304 (соответствующего 500-600C входному газовому потоку 116 фиг. 1) для уноса частиц 310 и разгона их в струе 301 (соответствующей внутренней струе 203 фиг. 2) до тех пор, пока они не столкнутся с медленно движущимися частицами основной массы слоя 211. Пути движения частиц 302, 303 показывают общее направление частиц 202, когда они опускаются по коническим стенкам в струю 301. Впуск 305 футерован удаляемой керамической вставкой 306 (соответствующей керамической вставке 206 фиг. 2), чтобы уменьшить износ, вызываемый истиранием, которой также придана такая форма, чтобы повышать скорость входного газа 304. Форма керамической вставки 306 и отверстия в слой 211 могут быть изменены, чтобы модифицировать перепад давления и истирание, как требуется для наладки реактора 200. Вставка удерживается стопорным кольцом 308, закрепленным внутри реактора, и проложена эластичным высокотемпературным уплотнением 307 вверху и внизу. Низ вставки поддерживается переходным фланцем 309 меньшего диаметра, который предпочтительно имеет такой же внутренний диаметр, как керамическая вставка 306. Фиг. 4 показывает вариацию фиг. 3. Двойные впуски 402, 403 подобны по конструкции впуску на фиг. 3, причем каждый из впусков 402, 403 имеет керамическую вставку 406 для уменьшения износа,вызываемого истиранием. Входные газовые потоки 404, 405 поступают через впуски 402 и 403 и затем сталкиваются в центре реактора, чтобы образовать единую вертикальную струю 401. Боковой вектор скорости каждой струи превращается в истирание при более высокой скорости, чем вертикальный вектор, потому что боковые векторы направлены противоположно друг другу, тогда как вертикальный вектор ударяет в слой частиц, которые могут свободно двигаться. Таким образом, две взаимодействующих струи порождают большее истирание, чем можно было бы ожидать при таких же условиях для двух невзаимодействующих струй. Повышение истирания связано с углом 409 между пересекающимися газовыми потоками 404, 405 и достигает максимума, когда угол равен 180 градусам. Созданное истирание служит для того, чтобы удалить уже прореагировавшую поверхность частиц 211 и подвергнуть свежую поверхность кремния атаке с повышением скорости реакции и, следовательно, производительности и выхода тригалогенсилана. Твердый остаток, который иначе оставался бы в реакторе, транспортируется наружу в виде частиц пыли с небольшой поверхностью. Показан также центральный спуск 407 для уда-3 019654 ления слоя. Табл. 1, включенная в данное описание как приложение, представляет потоки и температуры примера способа. Основываясь на условиях, показанных в табл. 1, могут быть выбраны рабочие условия для того, чтобы минимизировать образование пузырей и максимизировать выход и пропускную способность и в результате максимизировать выработку целевого тригалогенсилана для данного реактора. Максимальной скоростью, которая может иметь место без образования пузырей, является по определению минимальная скорость образования газовых пузырей, Umb. Работа при U/Umb = 1 дает максимальный поток без образования газовых пузырей. Как отмечено выше, это может быть рассчитано разными путями, но особенно полезным уравнением является уравнение David and Harrison:f - вязкость среды. Значение пористости зависит от формы частицы и может быть измерено для любого данного образца металлургического кремния. Диаметр частицы является средним спроектированным диаметром и может быть измерен стандартными методами просеивания и откорректирован, как требуется для сферичности. Вязкость газа возрастает с температурой и зависит от состава. Имеется несколько стандартных способов ее точного предсказания. Самым легким путем повысить Umb является повысить средний диаметр частицы, Dp. Пример 1. Состав газа на входе представлен в табл. 1.представляет пористость при Umb - 0, 4;g представляет ускорение силы тяжести - 980 м/с 2;Dp представляет диаметр частицы - должен быть рассчитан; р представляет плотность частицы - 2,33 г/см 3;f представляет плотность среды - 0,0218 г/см 3;f представляет вязкость среды - 0,00024 П;U представляет максимальную приведенную скорость - 0,11 м/с = Umb. Поэтому желаемый минимальный средний размер частиц = 444 мкм. Поскольку MGS является почти угловым, этот размер частицы должен быть скорректирован делением на коэффициент сферичности,который обычно составляет примерно 0,86. Это дает средний размер частицы 516 мкм, как определено ситовым анализом. Дальнейшие стандартные расчеты баланса совокупности могут быть сделаны, чтобы учесть сокращение частиц вследствие реакции и уменьшение размера вследствие истирания, чтобы прийти к требуемому минимальному среднему размеру частиц для подачи в реактор. После того как получена разумная оценка точного размера частиц для подачи, может быть проведено испытание. Пример 2. Реактор длиной 10 м заполняли слоем высотой 7 м, используя MGS с номинальным размером 750 микрон. Реактор работал в течение 120 ч при условиях табл. 1, порции металлургического кремния добавляли раз в 1 ч, чтобы поддерживать уровень. В конце цикла из слоя отбирали образец MGS в слое и анализировали; результаты показаны ниже. Таблица 2. Массовый процент частиц в интервале размера сита Средний размер частиц был рассчитан как 538 мкм. Хотя изобретение было описано в связи с предпочтительным осуществлением, не предполагается ограничить объем изобретения представленной частной формой, но, напротив, предполагается охватить такие альтернативы, модификации и эквиваленты, которые могут быть включены в пределах сущности и объема изобретения, как они определены прилагаемой формулой изобретения. Приложение. Таблица 1. Материальный баланс процесса ФОРМУЛА ИЗОБРЕТЕНИЯ 1. Система для гидрирования тетрагалогенида кремния и кремния в тригалогенсилан, включающая в себя емкость высокого давления без внутренних распределителей потока для вмещения множества частиц металлургического кремния, имеющую одно или более отверстий для входа газа, одно или более отверстий для входа твердых веществ, одно или более спускных отверстий для твердых веществ и один или более выходов для смесей газ/твердые вещества, причем система содержит первый теплообменник для нагрева подаваемого потока жидкого тетрагалогенида кремния, причем указанный нагретый жидкий тетрагалогенид кремния смешивают с водородом, чтобы понизить температуру испарения тетрагалогенида кремния; второй теплообменник для испарения смеси тетрагалогенида кремния и водорода, причем источником тепла являются горячие газы, выходящие из других компонентов системы; третий теплообменник для повышения температуры испаренной смеси до 500-600C, где нагрев обеспечен выходящим потоком из емкости высокого давления, причем поток, покидающий третий теплообменник, поступает в емкость высокого давления, причем тепло, обеспеченное потоком из емкости высокого давления, служит источником тепла для подаваемого потока тетрагалогенида кремния, поступающего в первый теплообменник. 2. Система для гидрирования смеси тетрагалогенида кремния и кремния в тригалогенсилан, включающая реакционную емкость, имеющую заключенный в ней пористый слой частиц металлургического кремния, причем указанная реакционная емкость имеет одно или более отверстий для входа смеси испаренного тетрагалогенида кремния и водорода в своей нижней части, одно или более отверстий для входа твердых веществ в своей верхней части для подачи в указанный реактор дополнительных гранулированных частиц металлургического кремния, одно или более спускных отверстий в нижней части для удаления отработанных твердых веществ и одно или более выходных отверстий в точке над упомянутым слоем частиц металлургического кремния для удаления выходящего тригалогенсиланового газа, который может также включать унесенные твердые частицы; первый теплообменник для нагрева подаваемого потока жидкого тетрагалогенида кремния, указанный нагретый жидкий тетрагалогенид кремния, выходящий из первого теплообменника, смешивается с водородом, чтобы понизить температуру испарения жидкого тетрагалогенида кремния; испаритель для испарения смеси тетрагалогенида кремния и водорода; второй теплообменник для повышения температуры испаренной смеси тетрагалогенида кремния и водорода до 450-550C, причем нагрев обеспечивается выходящим из указанной реакционной емкости газовым потоком, причем указанный газовый поток, выходящий из указанной реакционной емкости и затем покидающий второй теплообменник, служит источником тепла для подаваемого потока тетрагалогенида кремния, поступающего в первый теплообменник. 3. Система по п.2, в которой источником тепла для испарителя является пар. 4. Система по п.2, дополнительно включающая сепаратор для удаления унесенных твердых веществ из выходящего тригалогенсиланового газа, покидающего реактор.
МПК / Метки
МПК: C01B 33/107, C01B 33/04
Метки: система, тригалогенсилан, гидрирования, кремния, тетрагалогенида
Код ссылки
<a href="https://eas.patents.su/8-19654-sistema-dlya-gidrirovaniya-tetragalogenida-kremniya-i-kremniya-v-trigalogensilan.html" rel="bookmark" title="База патентов Евразийского Союза">Система для гидрирования тетрагалогенида кремния и кремния в тригалогенсилан</a>