Способ удаления кислотных газов из потока углеводородного газа
Номер патента: 21006
Опубликовано: 31.03.2015
Авторы: Нортроп Пол Скотт, Март Чарльз Дж., Келли Брюс Т.
Формула / Реферат
1. Способ удаления кислотных газов из исходного газового потока, в котором
подают исходный газовый поток в криогенную дистилляционную колонну, которая имеет нижнюю зону дистилляции и промежуточную зону контролируемого замерзания, в которую подают распылением холодную жидкость, образованную, главным образом, из метана;
разделяют исходный газовый поток в криогенной дистилляционной колонне на верхний метановый поток и нижний поток кислотного газа;
пропускают верхний метановый поток через охлаждающую систему ниже по ходу от криогенной дистилляционной колонны, причем охлаждающая система охлаждает верхний метановый поток;
возвращают первую часть охлажденного верхнего метанового потока в криогенную дистилляционную колонну в виде жидкости орошения, служащей в качестве распыляемой холодной жидкости;
пропускают вторую часть охлажденного верхнего метанового потока через слой твердого адсорбента ниже по ходу от криогенной дистилляционной колонны для удаления дополнительных кислотных газов и образования очищенного газового потока;
конструируют охлаждающую систему таким образом, чтобы производить жидкость орошения в достаточном количестве для удаления кислотных газов из исходного газового потока в криогенной дистилляционной колонне до первой выбранной композиции и подавать верхний метановый поток на слой твердого адсорбента ниже по ходу от криогенной дистилляционной колонны для удаления дополнительных кислотных газов до второй выбранной композиции;
по меньшей мере, частично дегидратируют исходный газовый поток путем пропускания исходного газового потока через слой твердого адсорбента выше по ходу от криогенной дистилляционной колонны, где слой твердого адсорбента ниже по ходу от криогенной дистилляционной колонны и слой твердого адсорбента выше по ходу от криогенной дистилляционной колонны представляют собой слои молекулярного сита;
насыщают слой выше по ходу от криогенной дистилляционной колонны адсорбированной водой и заменяют его слоем молекулярного сита, который насытился кислотным газом при использовании в качестве слоя твердого адсорбента ниже по ходу от криогенной дистилляционной колонны.
2. Способ по п.1, где
кислотные газы содержат диоксид углерода;
количество генерируемого жидкого орошения является достаточным для удаления диоксида углерода из исходного газового потока до первой композиции приблизительно от 1 до 4 мол.%;
слой твердого адсорбента ниже по ходу от криогенной дистилляционной колонны удаляет дополнительный диоксид углерода из верхнего метанового потока до второй композиции приблизительно от 0,2 до 3 мол.%.
3. Способ по п.1, где
количество генерируемого жидкого орошения является достаточным для удаления диоксида углерода из исходного газового потока до первой композиции, которая соответствует спецификациям трубопровода;
слой твердого адсорбента ниже по ходу от криогенной дистилляционной колонны удаляет диоксид углерода из верхнего метанового потока до второй выбранной композиции кислотного газа, которая удовлетворяет спецификациям СПГ.
4. Способ по п.3, где спецификации трубопровода требуют содержания диоксида углерода меньше чем приблизительно 3 мол.%.
5. Способ по п.3, где спецификации СПГ требуют содержания диоксида углерода меньше чем приблизительно 50 ч./млн.
6. Способ по п.3, где слой твердого адсорбента ниже по ходу от криогенной дистилляционной колонны удаляет диоксид углерода из верхнего метанового потока до содержания меньше чем приблизительно 100 ч./млн.
7. Способ по п.2, где кислотные газы дополнительно содержат сероводород и слой твердого адсорбента ниже по ходу от криогенной дистилляционной колонны удаляет сероводород из верхнего метанового потока до содержания менее чем приблизительно 10 ч./млн.
8. Способ по п.7, где слой молекулярного сита удаляет сероводород из верхнего метанового потока до содержания менее чем приблизительно 4 ч./млн.
9. Способ по п.2, где дополнительно отделяют диоксид углерода от метана, используя (i) ионные жидкости, (ii) физические растворители или (iii) химические растворители, в одном или нескольких резервуарах ниже по ходу от криогенной дистилляционной колонны.
10. Способ по п.1, где дополнительно заменяют слой твердого адсорбента выше по ходу от криогенной дистилляционной колонны, когда слой молекулярного сита выше по ходу от криогенной дистилляционной колонны становится, по существу, насыщенным водой.
11. Способ по п.1, где дополнительно регенерируют слой молекулярного сита выше по ходу от криогенной дистилляционной колонны после того, как данный слой молекулярного сита выше по ходу от криогенной дистилляционной колонны становится, по существу, насыщенным водой.
12. Способ по п.11, где регенерируют слой молекулярного сита выше по ходу от криогенной дистилляционной колонны, используя адсорбцию с термическими колебаниями или адсорбцию с колебаниями давления.
13. Способ по п.11, где дополнительно заменяют слой молекулярного сита ниже по ходу от криогенной дистилляционной колонны, когда слой молекулярного сита ниже по ходу от криогенной дистилляционной колонны становится, по существу, насыщенным диоксидом углерода, регенерированным слоем молекулярного сита, ранее находившимся в обслуживании дегидратации выше по ходу от криогенной дистилляционной колонны.
14. Способ по п.2, где дополнительно вводят по меньшей мере часть нижнего потока кислотного газа в подземную формацию по меньшей мере через одну скважину ввода кислотного газа.
15. Способ удаления кислотных газов из исходного газового потока, где
пропускают исходный газовый поток через первый слой молекулярного сита, при этом получают входящий газовый поток, который является, по меньшей мере, частично дегидратированным;
направляют входящий газовый поток в криогенную дистилляционную колонну, где данная колонна имеет нижнюю дистилляционную зону и промежуточную зону контролируемого замерзания, в которую подают распылением холодную жидкость, образованную, главным образом, из метана;
выводят верхний метановый поток из криогенной дистилляционной колонны;
пропускают верхний метановый поток через второй слой молекулярного сита ниже по ходу от криогенной дистилляционной колонны, удаляя дополнительные кислотные газы и получая очищенный газовый поток;
удаляют первый слой молекулярного сита выше по ходу от криогенной дистилляционной колонны, когда данный слой молекулярного сита выше по ходу от криогенной дистилляционной колонны становится, по существу, насыщенным водой;
заменяют слой молекулярного сита выше по ходу от криогенной дистилляционной колонны слоем молекулярного сита, который ранее, по существу, насытился диоксидом углерода в результате использования в качестве второго слоя молекулярного сита ниже по ходу от криогенной дистилляционной колонны;
регенерируют слой молекулярного сита выше по ходу от криогенной дистилляционной колонны после того, как данный слой молекулярного сита выше по ходу от криогенной дистилляционной колонны становится, по существу, насыщенным водой.
16. Способ по п.15, где дополнительно пропускают верхний метановый поток через охлаждающую систему ниже по ходу от криогенной дистилляционной колонны, чтобы охладить верхний метановый поток перед тем, как верхний метановый поток пропускают через второй слой молекулярного сита.
17. Способ по п.15, где дополнительно возвращают часть охлажденного верхнего метанового потока в криогенную дистилляционную колонну в виде жидкости орошения.
18. Способ по п.15, где охлаждающая система организована так, чтобы производить жидкое орошение в достаточном количестве для удаления кислотных газов из входящего газового потока в криогенной дистилляционной колонне до первой выбранной композиции и подавать верхний метановый поток в слой молекулярного сита ниже по ходу от криогенной дистилляционной колонны для удаления дополнительных кислотных газов до второй выбранной композиции.
19. Способ по п.18, где
кислотные газы содержат диоксид углерода;
количество генерируемого жидкого орошения является достаточным для удаления диоксида углерода из входящего газового потока до первой композиции приблизительно от 1 до 4 мол.%;
слой молекулярного сита ниже по ходу от криогенной дистилляционной колонны удаляет дополнительный диоксид углерода из верхнего метанового потока до второй композиции приблизительно от 0,2 до 3 мол.%.
20. Способ по п.18, где
количество генерируемого жидкого орошения является достаточным для удаления диоксида углерода из входящего газового потока до первой композиции, которая удовлетворяет спецификациям трубопровода;
слой молекулярного сита ниже по ходу от криогенной дистилляционной колонны удаляет диоксид углерода из верхнего метанового потока до второй выбранной композиции кислотного газа, которая удовлетворяет спецификациям СПГ.
21. Способ по п.20, где трубопроводные спецификации требуют содержания диоксида углерода меньше чем приблизительно 3 мол.%.
22. Способ по п.21, где СПГ спецификации требуют содержания диоксида углерода меньше чем приблизительно 100 ч./млн.
23. Способ по п.17, где слой молекулярного сита ниже по ходу от криогенной дистилляционной колонны удаляет диоксид углерода из верхнего метанового потока до содержания меньше чем приблизительно 50 ч./млн.
24. Способ по п.15, где кислотные газы дополнительно содержат сероводород и слой молекулярного сита ниже по ходу от криогенной дистилляционной колонны удаляет сероводород из верхнего метанового потока до композиции менее чем приблизительно 10 ч./млн.
25. Способ по п.15, где дополнительно заменяют слой молекулярного сита ниже по ходу от криогенной дистилляционной колонны, когда данный слой молекулярного сита ниже по ходу от криогенной дистилляционной колонны становится, по существу, насыщенным диоксидом углерода, регенерированным слоем молекулярного сита, который ранее находился в работе выше по ходу от криогенной дистилляционной колонны.
26. Способ по п.22, где
кислотные газы содержат диоксид углерода;
исходный газовый поток содержит азот,
в данном способе дополнительно пропускают верхний метановый поток через третий слой молекулярного сита ниже по ходу от криогенной дистилляционной колонны, удаляя азот из верхнего метанового потока ниже содержания приблизительно 3 мол.%.
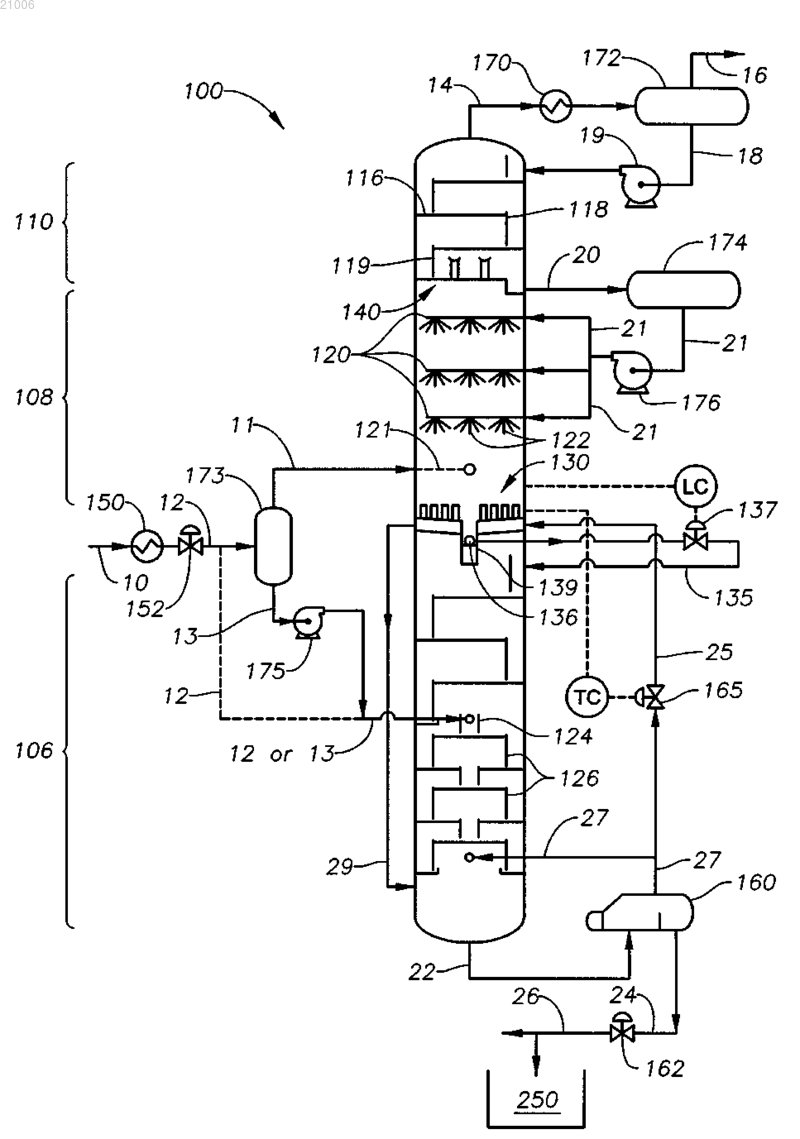
Текст
СПОСОБ УДАЛЕНИЯ КИСЛОТНЫХ ГАЗОВ ИЗ ПОТОКА УГЛЕВОДОРОДНОГО ГАЗА В изобретении представлена система для удаления кислотных газов из исходного газового потока,которая включает в себя криогенную дистилляционную колонну. Данная колонна принимает и разделяет исходный газовый поток на верхний метановый поток и нижний поток сжиженного кислотного газа. Охлаждающее оборудование ниже по ходу от криогенной дистилляционной колонны охлаждает верхний метановый поток и возвращает часть верхнего метанового потока в криогенную дистилляционную колонну в виде жидкого орошения. Данная система также может включать в себя первый слой молекулярного сита выше по ходу от дистилляционной колонны и второй слой молекулярного сита ниже по ходу от дистилляционной колонны. Первый слой молекулярного сита адсорбирует воду, тогда как второй слой молекулярного сита адсорбирует дополнительные кислотные газы из охлажденного верхнего метанового потока.(71)(73) Заявитель и патентовладелец: ЭКСОНМОБИЛ АПСТРИМ РИСЕРЧ КОМПАНИ (US) Перекрестная ссылка на родственные заявки Данная заявка устанавливает приоритет предварительной патентной заявки США 61/170919, зарегистрированной 20 апреля 2009 г. Уровень техники изобретения Данный раздел предназначен для введения различных аспектов техники, которые могут быть связаны с типичными вариантами осуществления настоящего описания. Считается, что это обсуждение способствует обеспечению структуры, облегчающей понимание конкретных аспектов настоящего описания. Соответственно следует понимать, что данный раздел необходимо читать в данном освещении, а не обязательно как признание предшествующего уровня техники. Область техники, к которой относится изобретение Настоящее изобретение относится к области разделения текучих сред. Более конкретно, настоящее изобретение относится к области отделения диоксида углерода и других кислотных газов от потока углеводородной текучей среды. Обсуждение технологии. Добыча углеводородов из месторождений часто происходит вместе с побочной добычей не углеводородных газов. Такие газы включают в себя примеси, такие как сероводород (H2S) и диоксид углерода(CO2). Когда H2S и CO2 получаются в виде части потока углеводородного газа (такого как метан или этан), данный газовый поток иногда называют "кислый газ". Кислый газ обычно обрабатывают, удаляя CO2, H2S и другие примеси до того, как его направляют далее для дополнительной обработки или продажи. Процесс отделения вызывает проблему удаления отделенных примесей. В некоторых случаях концентрированный кислотный газ (состоящий, главным образом, из H2S и CO2) направляют в установку извлечения серы ("УИС"). УИС превращает H2S в полезную элементарную серу. Однако в некоторых областях (таких как область Каспийского моря) дополнительное получение элементарной серы нежелательно, так как существует ограниченный рынок. Следовательно, миллионы тонн серы необходимо хранить в больших наземных блоках в некоторых областях мира, больше всего в Канаде и Казахстане. Тогда как сера хранится на земле, газообразный диоксид углерода часто выбрасывается в атмосферу. Однако практика выброса CO2 иногда нежелательна. Одной возможностью минимизации выбросовCO2 является способ, называемый впрыскивание кислотного газа ("ВКГ"). ВКГ означает, что нежелательные кислые газы повторно впрыскивают в подземную формацию под давлением и изолируют для потенциального позднейшего использования. Альтернативно, кислые газы используют, чтобы создавать искусственное давление месторождения для усиленных операций нефтедобычи. Для ВКГ необходимо иметь газоперерабатывающую установку, которая выделяет кислотные газовые компоненты из углеводородных газов. Однако для "сильнокислых" потоков, то есть производственных потоков, содержащих больше чем приблизительно 15% CO2 и H2S, может быть особой проблемой сконструировать, построить и привести в действие установку, которая может экономично отделять примеси от желаемых углеводородов. Многие месторождения природного газа содержат относительно низкий процент углеводородов (меньше чем 40%, например) и высокий процент кислотных газов, главным образом диоксида углерода, а также сероводород, сульфид карбонила, дисульфид углерода и различные меркаптаны. В этих случаях криогенная обработка газа может применяться выгодным образом. Криогенная обработка газа представляет собой процесс дистилляции, иногда используемый для разделения газов. Криогенная обработка газа генерирует поток охлажденного и сжиженного газа при средних давлениях (например, 350-600 фунтов на квадратный дюйм по датчику (psig) (2,45-4,19 МПа. В случае криогенной дистилляции кислого газа сжиженный кислотный газ образуется в виде "донного" продукта. Так как сжиженный кислотный газ имеет относительно высокую плотность, гидростатический напор может преимущественно использоваться в ВКГ скважине, способствуя процессу впрыскивания. Это означает, что энергия, требуемая для закачивания сжиженного кислотного газа в формацию, ниже,чем энергия, требуемая для сжатия кислотных газов низкого давления до давления месторождения. Таким образом, криогенная обработка газа особенно подходит для ВКГ. Проблемы также существуют в отношении криогенной дистилляции кислых газов. Когда CO2 присутствует в концентрации, большей чем приблизительно 5 мол.% в обрабатываемом газе, он будет замерзать в виде твердого вещества в стандартной установке криогенной дистилляции. Образование CO2 в виде твердого вещества нарушает процесс криогенной дистилляции. Чтобы обойти эту проблему, ранее разработали различные способы "контролируемой зоны охлаждения" (CFZ). CFZ способ имеет преимуществом склонность диоксида углерода образовывать твердые частицы, позволяя замерзшим частицам CO2 образовываться в открытой части дистилляционной колонны, и затем захватывая данные частицы на тарелке плавления. В результате поток чистого метана (вместе с любым азотом или гелием, присутствующими в исходном газе) образуется у вершины колонны, тогда как поток жидкого CO2/H2S образуется на дне колонны. Определенные аспекты CFZ способа и соответствующее оборудование описаны в патентах США 4533372, 4923493, 5062270, 5120338 и 6053007. Как, в общем, описано в указанных патентах США, дистилляционная башня или колонна, используемая для криогенной обработки газа, включает в себя нижнюю зону дистилляции и промежуточную зону контролируемого замерзания. Предпочтительно также включается верхняя зона ректификации. Колонна функционирует, образуя частицы твердого CO2, обеспечивая часть колонны, имеющей диапазон температур ниже точки замерзания диоксида углерода, но выше температуры кипения метана при данном давлении. Более предпочтительно зона контролируемого замерзания работает при температуре и давлении, которые позволяют метану и другим легким углеводородным газам испаряться, в то же время заставляя CO2 образовывать замерзшие (твердые) частицы. Когда поток газового сырья движется вверх колонны, замерзшие частицы CO2 вырываются из потока сырья и опускаются под действием гравитации из зоны контролируемого замерзания на тарелку плавления. Здесь частицы сжижаются. Богатый диоксидом углерода жидкий поток затем течет из тарелки плавления вниз в нижнюю зону дистилляции на дне колонны. Нижняя зона дистилляции поддерживается при температуре и давлении, при которых, по существу, не образуется твердый диоксид углерода, а растворенный метан выкипает. В одном аспекте донный поток кислотного газа образуется при от 30 до 40F(от -1,1 до 4,4C). Зона контролируемого замерзания включает в себя распыление холодной жидкости. Этот обогащенный метаном жидкий поток известен как "орошение". Когда газовый поток легких углеводородных газов и увлеченных кислых газов движется вверх по колонне, газовый поток сталкивается с распылением жидкости. Распыление холодной жидкости помогает выбрасывать частицы твердого CO2, позволяя метановому газу испаряться и течь вверх в колонне. В верхней зоне ректификации метан (или верхний газ) захватывается и направляется по трубам на продажу или делается доступным для топлива. В одном аспекте верхний метановый поток освобождается при приблизительно -130F (-90C). Верхний газ может частично сжижаться путем дополнительного охлаждения, и жидкость возвращается в колонну в виде "орошения". Жидкость орошения впрыскивается в виде холодного распыления в секцию распыления зоны контролируемого замерзания. Метан, получаемый в верхней зоне дистилляции, удовлетворяет большинству спецификаций для трубопроводной доставки. Например, данный метан может удовлетворять трубопроводной спецификации по CO2 менее чем 2 мол.%, а также спецификации H2S 4 ч./млн, если генерируется достаточное орошение. Однако более строгие спецификации по CO2 для природного газа существуют для таких приложений, как извлечение гелия, криогенное извлечение жидкого природного газа, конверсия в жидкий природный газ (СПГ) и удаление азота. Более строгие спецификации по CO2 можно удовлетворить путем увеличения количества орошения жидким метаном. Это, в свою очередь, требует больше и/или большего холодильного оборудования. В связи с этим, процесс генерации холодного жидкого метана для секции распыления требует оборудования, добавочного к CFZ башне. Это оборудование включает в себя трубы, сопла, компрессоры, сепараторы, насосы и расширительные клапаны. Чем больше пожелания оператора к удалению CO2, тем больше становятся требования охлаждения. Существует необходимость снизить требования охлаждения CFZ способа, все еще снижая содержание CO2 до очень низких уровней. Существует также необходимость в системе криогенного разделения газа и сопровождающих процессах, которые прибавляются с помощью других технологий удаления CO2. Кроме того, существует необходимость в способе криогенного разделения газа, который способен снижать содержание CO2 и H2S в газе до уровней, допустимых для дальнейших процессов сжижения, без увеличения мощности охлаждающего оборудования. Сущность изобретения Предлагается система для удаления кислотных газов из потока сырого газа. В одном варианте осуществления данная система включает в себя криогенную дистилляционную колонну. Дистилляционная колонна может иметь нижнюю зону дистилляции и промежуточную зону контролируемого замерзания. Промежуточная зона контролируемого замерзания, или секция распыления, принимает распыление холодной жидкости, образованной, главным образом, из метана. Холодное распыление представляет собой орошение жидкостью, образованной из верхней петли ниже по ходу от дистилляционной колонны. Дистилляционная колонна функционирует, удаляя кислотные газы. В этой связи, дистилляционная колонна принимает и затем разделяет исходный газовый поток на верхний метановый поток и нижний поток кислотного газа. Данная система также включает в себя охлаждающее оборудование. Некоторое из этого охлаждающего оборудования может использоваться для предварительного охлаждения сырого газа, тогда как остальное охлаждающее оборудование находится ниже по ходу от криогенной дистилляционной колонны для охлаждения верхнего метанового потока. Часть верхнего метанового потока возвращается в криогенную дистилляционную колонну в виде жидкости орошения. Дистилляционная колонна также включает в себя слой твердого адсорбента ниже по ходу от криогенной дистилляционной колонны. Слой твердого адсорбента функционирует, адсорбируя по меньшей мере часть оставшихся кислотных газов из охлажденного верхнего метанового потока. В настоящей системе охлаждающее оборудование разработано так, чтобы генерировать орошение жидкостью в достаточном количестве для удаления кислотных газов из потока исходного газа в криоген-2 021006 ной дистилляционной колонне до первой выбранной композиции. Это значит, что некоторый процент или количество кислотной газовой композиции намеренно выходит с верхним метановым потоком. Верхний метановый поток подается на слой твердого адсорбента ниже по ходу от криогенной дистилляционной колонны для удаления оставшихся кислотных газов до второй выбранной меньшей композиции. Таким образом, слой твердого адсорбента ниже по ходу от криогенной дистилляционной колонны обеспечивает доочистку метанового потока. Он дополнительно позволяет уменьшать охлаждающее оборудование или мощность, которые, в ином случае, нужно было бы обеспечивать для генерации жидкости орошения. В одном аспекте кислотные газы содержат диоксид углерода. Количество генерируемого жидкого орошения является достаточным для удаления диоксида углерода из исходного газового потока до первой композиции приблизительно от 1 до 4 мол.%. Одновременно слой твердого адсорбента ниже по ходу от криогенной дистилляционной колонны удаляет дополнительный диоксид углерода из верхнего метанового потока до второй композиции. Например, вторая композиция может быть приблизительно от 0,2 до 3,0 мол.%. В другом аспекте количество генерируемого жидкого орошения является достаточным для удаления диоксида углерода из исходного газового потока до первой композиции, которая удовлетворяет трубопроводным спецификациям. Одновременно слой твердого адсорбента ниже по ходу от криогенной дистилляционной колонны удаляет диоксид углерода из верхнего метанового потока до второй композиции, которая удовлетворяет СПГ спецификациям. Например, слой твердого адсорбента ниже по ходу от криогенной дистилляционной колонны может удалять диоксид углерода из верхнего метанового потока до композиции менее чем приблизительно 100 ч./млн или более предпочтительно до композиции менее чем приблизительно 50 ч./млн. В еще одном аспекте кислотные газы дополнительно содержат сероводород. В этом случае слой твердого адсорбента ниже по ходу от криогенной дистилляционной колонны может удалять сероводород до композиции менее чем приблизительно 10 ч./млн или более предпочтительно до композиции менее чем приблизительно 4 ч./млн. В одной компоновке по меньшей мере один слой твердого адсорбента ниже по ходу от криогенной дистилляционной колонны расположен так, чтобы заменять по меньшей мере один слой твердого адсорбента выше по ходу от криогенной дистилляционной колонны в цикле регенерации. Способ удаления кислотных газов из исходного газового потока также предлагается здесь. В одном аспекте данный способ включает в себя обеспечение криогенной дистилляционной колонны. Данная колонна имеет нижнюю зону дистилляции и промежуточную зону контролируемого замерзания, которая принимает распыление холодной жидкости, образованной, главным образом, из метана. Данный способ также включает в себя прием исходного газового потока в криогенную дистилляционную колонну. После приема исходного газового потока данный способ включает в себя разделение исходного газового потока в криогенной дистилляционной колонне на верхний метановый поток и нижний поток кислотного газа. Данный способ затем включает в себя прохождение верхнего метанового потока через систему охлаждения ниже по ходу от криогенной дистилляционной колонны. Система охлаждения охлаждает верхний метановый поток. Данный способ дополнительно включает в себя возврат первой части охлажденного верхнего метанового потока в криогенную дистилляционную колонну в виде жидкости орошения. Жидкое орошение служит в качестве распыления холодной жидкости в колонне. Данный способ также включает в себя прохождение второй части охлажденного верхнего метанового потока через слой твердого адсорбента ниже по ходу от криогенной дистилляционной колонны. Это служит для удаления дополнительных кислотных газов и образования очищенного газового потока. Предпочтительно слой твердого адсорбента представляет собой слой молекулярного сита. Данный способ также включает в себя конструирование системы охлаждения таким образом, чтобы производить жидкость орошения в достаточном количестве для удаления кислотных газов из исходного газового потока в криогенной дистилляционной колонне до первой выбранной композиции и подавать верхний метановый поток на слой твердого адсорбента ниже по ходу от криогенной дистилляционной колонны для удаления дополнительных кислотных газов до второй, меньшей композиции. В одном аспекте кислотные газы содержат диоксид углерода. В этом случае, количество генерируемого жидкого орошения является достаточным для удаления диоксида углерода из исходного газового потока до первой композиции приблизительно от 1 до 4 мол.%. Кроме того, слой твердого адсорбента ниже по ходу от криогенной дистилляционной колонны удаляет дополнительный диоксид углерода из верхнего метанового потока до второй композиции приблизительно от 0,2 до 3,0 мол.%. В одной компоновке количество генерируемого жидкого орошения является достаточным для удаления диоксида углерода из исходного газового потока до первой композиции, которая удовлетворяет трубопроводным спецификациям. Например, трубопроводные спецификации могут требовать содержания диоксида углерода менее чем приблизительно 3,0 мол.%. Слой твердого адсорбента ниже по ходу от криогенной дистилляционной колонны затем удаляет диоксид углерода из верхнего метанового потока до второй композиции, которая удовлетворяет СПГ спецификациям. Например, СПГ спецификации мо-3 021006 гут требовать содержания диоксида углерода менее чем приблизительно 100 ч./млн или даже приблизительно 50 ч./млн. В другом варианте осуществления данного способа кислотные газы дополнительно содержат сероводород. В этом случае слой твердого адсорбента ниже по ходу от криогенной дистилляционной колонны может удалять сероводород из верхнего метанового потока до композиции менее чем приблизительно 10 ч./млн. Предпочтительно слой твердого адсорбента ниже по ходу от криогенной дистилляционной колонны представляет собой слой молекулярного сита, и данный слой молекулярного сита удаляет сероводород из верхнего метанового потока до композиции менее чем приблизительно 4 ч./млн. В одном аспекте данный способ дополнительно включает в себя этап, по меньшей мере, частичной дегидратации исходного газового потока путем прохождения исходного газового потока через слой твердого адсорбента выше по ходу от криогенной дистилляционной колонны. Предпочтительно слой твердого адсорбента выше по ходу от криогенной дистилляционной колонны также представляет собой слой молекулярного сита. Данный способ может затем дополнительно включать в себя замену слоя молекулярного сита выше по ходу от криогенной дистилляционной колонны, когда слой молекулярного сита выше по ходу от криогенной дистилляционной колонны становится, по существу, насыщенным водой. Когда слой молекулярного сита выше по ходу от криогенной дистилляционной колонны становится,по существу, насыщенным водой, слой молекулярного сита выше по ходу от криогенной дистилляционной колонны заменяют слоем молекулярного сита, который ранее использовали для адсорбции диоксида углерода ниже по ходу от криогенной дистилляционной колонны. Данный способ может дополнительно включать в себя регенерацию слоя молекулярного сита выше по ходу от криогенной дистилляционной колонны после того, как слой молекулярного сита выше по ходу от криогенной дистилляционной колонны становится, по существу, насыщенным водой. Регенерация слоя молекулярного сита выше по ходу от криогенной дистилляционной колонны может включать в себя адсорбцию с термическими колебаниями или адсорбцию с колебаниями давления. Когда слой молекулярного сита ниже по ходу от криогенной дистилляционной колонны становится, по существу, насыщенным диоксидом углерода, данный слой молекулярного сита может быть заменен слоем, регенерированным ранее при работе по дегидратации выше по ходу от криогенной дистилляционной колонны. Краткое описание чертежей Чтобы настоящее изобретение было более понятным, к нему прилагаются определенные иллюстрации, графики и/или блок-схемы. Следует заметить, однако, что данные чертежи изображают только выбранные варианты осуществления изобретения и, следовательно, не должны рассматриваться как ограничение его объема, так как данное изобретение может допускать другие, равно эффективные варианты осуществления и приложения. На чертежах: фиг. 1 представляет собой вид сбоку CFZ дистилляционной колонны в одном варианте осуществления; видно, что исходный газовый поток вводится в промежуточную зону контролируемого замерзания данной колонны; фиг. 2 А представляет собой вид сверху тарелки плавления в одном варианте осуществления; эта тарелка плавления находится внутри колонны ниже зоны контролируемого замерзания; фиг. 2 В представляет собой вид в разрезе тарелки плавления с фиг. 2 А, сделанном по линии В-В; фиг. 2 С представляет собой вид в разрезе тарелки плавления с фиг. 2 А, сделанном по линии С-С; фиг. 3 представляет собой увеличенный вид сбоку отпарных тарелок в нижней дистилляционной секции дистилляционной колонны в одном варианте осуществления; фиг. 4 А представляет собой вид в перспективе форсуночной тарелки, которая может быть использована в нижней дистилляционной секции или в верхней ректификационной секции дистилляционной колонны в одном варианте осуществления; фиг. 4 В представляет собой вид сбоку отверстий в форсуночной тарелке с фиг. 4 А; фиг. 5 представляет собой вид сбоку промежуточной зоны контролируемого замерзания дистилляционной колонны на фиг. 1; на этом виде две иллюстративных отбойных перегородки добавлены к промежуточной зоне контролируемого замерзания; фиг. 6 представляет собой схематичное изображение, показывающее газоперерабатывающую установку для удаления кислотных газов из газового потока согласно настоящему изобретению в одном варианте осуществления; фиг. 7 А-7 С вместе представляют блок-схему способа удаления кислотных газов из газового потока согласно настоящему изобретению в одном варианте осуществления; фиг. 8 А представляет собой схематичное изображение контрольной системы, которая применяет контроль с прямой связью; иллюстративная контрольная система используется для контроля временных циклов для твердого адсорбента выше по ходу от криогенной газоперерабатывающей системы; фиг. 8 В представляет схематичное изображение контрольной системы, которая применяет прямой контроль с обратной связью; иллюстративная контрольная система используется для контроля временных циклов для твердого адсорбента выше по ходу от криогенной газоперерабатывающей системы. Подробное описание определенных вариантов осуществления Определения Применяемый здесь термин "углеводород" относится к органическому соединению, которое включает в себя, главным образом, элементы водород и углерод. Углеводороды обычно попадают в два класса: алифатические, или углеводороды с прямой цепью, и циклические, или замкнутые кольцом углеводороды, включая циклические терпены. Примеры углеводородсодержащих материалов включают в себя любую форму природного газа, нефти, угля и битума, которая может быть использована в качестве топлива или превращаться в топливо. Применяемый здесь термин "углеводородные текучие среды" относится к углеводороду или смесям углеводородов, которые являются газами или жидкостями. Например, углеводородные текучие среды могут включать в себя углеводород или смеси углеводородов, которые являются газами или жидкостями в условиях месторождения, в условиях переработки или в окружающих условиях (15C и давление 1 атм). Углеводородные текучие среды могут включать в себя, например, нефть, природный газ, метан угольного слоя, горючий сланец, нефтепродукт пиролиза, газ пиролиза, продукт пиролиза угля и другие углеводороды, которые находятся в газообразном или жидком состоянии. Термин "устройство массопереноса" относится к любому объекту, который принимает текучие среды для контакта и пропускает эти текучие среды в другие объекты, например, путем гравитационного точения. Одним неограничивающим примером является тарелка для отгонки определенных текучих сред. Решетчатая насадка является другим примером. Применяемый здесь термин "текучая среда" относится к газам, жидкостям и комбинациям газов и жидкостей, а также к комбинациям газов и твердых веществ и комбинациям жидкостей и твердых веществ. Применяемый здесь термин "конденсируемые углеводороды" обозначает те углеводороды, которые конденсируются при приблизительно 15C и давлении одна абсолютная атмосфера. Конденсируемые углеводороды могут включать в себя, например, смеси углеводородов, имеющих число атомов углерода больше чем 4. Применяемый здесь термин "система охлаждения с замкнутым контуром" означает любую систему охлаждения, в которой внешняя рабочая текучая среда, такая как пропан или этилен, используется в качестве охладителя, чтобы охлаждать верхний метановый поток. Этот термин противоположен "системе охлаждения с открытым контуром", в которой часть верхнего метанового потока сама используется в качестве рабочей текучей среды. Применяемый здесь термин "подземный" относится к геологическим слоям, находящимся ниже поверхности земли. Описание конкретных вариантов осуществления Фиг. 1 представляет схематичный вид криогенной дистилляционной колонны 100, которая может использоваться в связи с настоящим изобретением в одном варианте осуществления. Криогенная дистилляционная колонна 100 может взаимозаменяемо называться здесь "криогенной дистилляционной башней", "колонной", "CFZ колонной" или "расщепляющей башней". Криогенная дистилляционная колонна 100 на фиг. 1 принимает исходный поток 10 текучей среды. Поток 10 текучей среды образован, главным образом, из добытых газов. Обычно поток текучей среды представляет собой поток высушенного газа из скважины (не показана) и содержит от приблизительно 65 до приблизительно 95% метана. Однако поток 10 текучей среды может содержать меньший процент метана, например приблизительно от 30 до 65% или даже от 20 до 30%. Метан может присутствовать вместе со следовыми элементами других легких углеводородных газов, таких как этан. Кроме того, могут присутствовать следовые количества гелия и азота. В настоящей заявке поток 10 текучей среды будет также включать в себя определенные примеси. Это кислотные газы,такие как СО 2 и H2S. Исходный поток 10 текучей среды может быть под давлением после добычи приблизительно 600 фунтов на квадратный дюйм (psi) (4,19 МПа). В некоторых случаях давление исходного потока 10 текучей среды может быть приблизительно до 750 psi (5,24 МПа) или даже 1000 psi (6,99 МПа). Поток 10 текучей среды обычно охлаждают до подачи в дистилляционную колонну 100. Теплообменник 150, такой как кожухотрубный обменник, обеспечивают для потока 10 исходной текучей среды. Охлаждающий блок (не показан) обеспечивает охлаждающую текучую среду (такую как жидкий пропан) в теплообменник 150, доводя температуру потока 10 исходной текучей среды до приблизительно от -30 до -40F (от -34,4 до -40C). Охлажденный поток текучей среды может затем двигаться через расширительное устройство 152. Расширительное устройство 152 может быть, например, клапаном ДжоуляТомпсона ("J-T). Расширительное устройство 152 служит в качестве расширителя, чтобы получать дополнительное охлаждение потока 10 текучей среды. Предпочтительно также возникает частичное сжижение потока 10 текучей среды. Клапан Джоуля-Томпсона (или "J-T) является предпочтительным для потоков газового сырья, которые склонны к образованию твердых веществ. Расширительное устройство 152 предпочтительно устанавливают близко к криогенной дистилляционной колонне 100, чтобы минимизировать поте-5 021006 рю тепла в трубе подачи. В качестве альтернативы J-T клапану расширительное устройство 152 может быть турбодетандером. Турбодетандер обеспечивает большее охлаждение и создает источник работы вала для процессов,подобных блоку охлаждения, указанному выше. Блок охлаждения является частью теплообменника 150. Таким образом, оператор может минимизировать общие энергетические требования для процесса дистилляции. Однако турбодетандер не может обращаться с замерзшими частицами также хорошо, как J-T клапан. В любом случае, теплообменник 150 и расширительное устройство 152 превращают исходный газ в потоке 10 исходной текучей среды в охлажденный поток 12 текучей среды. Предпочтительно температура охлажденного потока 12 текучей среды составляет приблизительно от -40 до -70F (от -40 до-56,7C). В одном аспекте криогенная дистилляционная колонна 100 работает при давлении приблизительно 550 psi (3,84 МПа) и охлажденный поток 12 текучей среды находится при приблизительно -62F(-52,2C). При этих условиях охлажденный поток 12 текучей среды представляет собой, по существу,жидкую фазу, хотя некоторая газовая фаза может неизбежно увлекаться в охлажденный поток 12 текучей среды. Наиболее вероятно, никакого образования твердых веществ не возникает из-за присутствия CO2. Криогенная дистилляционная колонна 100 делится на три главных секции. Это нижняя зона дистилляции или "отгоночная секция" 106, промежуточная зона контролируемого замерзания или "секция распыления" 108 и верхняя зона дистилляции или "секция ректификации" 110. При компоновке колонны на фиг. 1 охлажденный поток 12 текучей среды вводится в секцию распыления 108 дистилляционной колонны 100. Однако охлажденный поток 12 текучей среды может альтернативно вводиться возле вершины отгоночной секции 106. В компоновке на фиг. 1 заметно, что отгоночная секция 106, промежуточная секция распыления 108, секция ректификации 110 и все компоненты находятся внутри одного резервуара 100. Однако для применения в открытом море, когда может быть необходимо учитывать высоту колонны 100 и движение,или для удаленного расположения, когда транспортные ограничения являются проблемой, колонна 110 может быть разделена на два отдельных герметичных резервуара (не показано). Например, отгоночная секция 106 и секция распыления 108 могут быть расположены в одном резервуаре, тогда как секция ректификации 108 - в другой секции. Внешние трубопроводы будут тогда применяться для взаимного соединения двух резервуаров. В любом варианте осуществления температура отгоночной секции 106 выше, чем температура подачи охлажденного потока 12 текучей среды. Температура отгоночной секции 106 установлена так, чтобы быть гораздо выше точки кипения метана в потоке 12 охлажденной текучей среды при рабочем давлении колонны 100. Таким образом, метан предпочтительно отгоняется от более тяжелых углеводородов и жидкого кислотного газа. Конечно, специалисты в данной области техники поймут, что жидкость внутри дистилляционной колонны 100 представляет собой смесь, что означает, что данная жидкость будет "кипеть" при некоторой промежуточной температуре между чистым метаном и чистым CO2. Кроме того, если более тяжелые углеводороды присутствуют в данной смеси, это будет увеличивать температуру кипения смеси. Эти факторы станут предметом рассмотрения для установления рабочих температур в дистилляционной колонне 100. В отгоночной секции 106 CO2 и любые другие жидкофазные текучие среды под действием гравитации падают ко дну криогенной дистилляционной колонны 100. Одновременно метан и другие газофазные текучие среды выпадают и поднимаются вверх к вершине колонны 100. Это разделение происходит,главным образом, из-за разницы плотности между газовой и жидкой фазами. Однако процессу разделения, возможно, помогают внутренние компоненты в дистилляционной колонне 100. Как описано ниже,они включают в себя тарелку плавления 130, множество выгодно сконструированных устройств массопереноса 126 и возможную линию обогревателя 25. Боковые ребойлеры (не показаны) также могут быть добавлены к отгоночной секции 106, чтобы облегчать удаление СО 2 и теплоперенос. Согласно фиг. 1 поток 12 охлажденной текучей среды может вводиться в колонну 100 возле вершины отгоночной секции 106. Альтернативно, может быть желательно вводить поток 12 сырья в промежуточную секцию распыления 108 выше тарелки плавления 130. Точка ввода потока 12 охлажденной текучей среды является вопросом конструкции, диктуемым композицией потока 10 исходной текучей среды. Когда температура потока 10 текучей среды достаточно высока (например, больше чем -70C), так что твердые вещества не ожидаются, может быть предпочтительно вводить поток 12 охлажденной текучей среды непосредственно в отгоночную секцию 106 через устройство типа двухфазного расширителя(или распределитель пара) 124 в колонне 100. Применение расширителя 124 служит для разделения двухфазной смеси пар-жидкость в потоке 12 охлажденной текучей среды. Расширитель 124 может быть щелевым, так что двухфазная текучая среда сталкивается с перегородками в расширителе 124. Если твердые вещества ожидаются вследствие низкой входной температуры, поток 12 охлажденной текучей среды может нуждаться в частичном разделении в резервуаре 173 до подачи в колонну 100, как описано выше. В этом случае поток 12 охлажденной текучей среды может разделяться в двухфазном резервуаре 173, минимизируя вероятность закупоривания твердыми веществами входной линии и внутренних компонентов колонны 100. Газовые пары покидают двухфазный резервуар 173 по входной линии 11 резервуара, где они входят в колонну 100 через входной распределитель 121. Газ затем проходит вверх через колонну 100. Суспензия 13 жидкость/твердое выпускается из двухфазного резервуара 173. Суспензия жидкость/твердое направляется в колонну 100 через распределитель пара 124 и на тарелку плавления 130. Суспензия 13 жидкость/твердое может подаваться в колонну 100 под действием гравитации или с помощью насоса 175. В любой компоновке, то есть с двухфазным резервуаром 173 или без него, поток 12 охлажденной текучей среды (или 11) поступает в колонну 100. Жидкий компонент покидает расширитель 124 и проходит вниз через набор отпарных тарелок 126 в отгоночной секции 106. Отпарные тарелки 126 включают в себя последовательность сливов 129 и плотин 128. Они описаны более полно в связи с фиг. 3. Отпарные тарелки 126 в комбинации с большей температурой в отгоночной секции 106 заставляют метан и другие легкие газы выходить из раствора. Полученный пар несет метан и легкие газы вместе с молекулами диоксида углерода, которые выкипели. Пар дополнительно проходит вверх через стояки 131 тарелки плавления 130 в зону замерзания 108. Стояки 131 тарелки плавления действуют как распределитель пара для равномерного распределения по зоне замерзания 108. Пар будет затем контактировать с холодной жидкостью из распылительных головок 120, "вымораживая" CO2. Другими словами, CO2 будет замерзать и затем "падать" обратно на тарелку плавления 130. Твердый CO2 затем плавится и течет под действием гравитации в жидкой форме вниз от тарелки плавления 130 и через отгоночную секцию 106 ниже. Как будет обсуждаться подробнее ниже, секция распыления 108 находится в промежуточной зоне замерзания криогенной дистилляционной колонны 100. При альтернативной конфигурации, в которой поток 12 охлажденной текучей среды разделяется в резервуаре 173 до входа в колонну 100, отделенная суспензия 13 жидкость/твердое вводится в колонну 100 на тарелку плавления 130. Таким образом, смесь жидкость-твердое вещество кислого газа и более тяжелых углеводородных компонентов будет течь из распределителя 121, причем твердые вещества и жидкости будут падать вниз на тарелку плавления 130. Тарелка плавления 130 сконструирована так, чтобы гравитационно принимать жидкие и твердые материалы, главным образом CO2 и H2S, из промежуточной секции распыления 108. Тарелка плавления 130 служит для нагрева жидких и твердых материалов и направления их вниз через отгоночную секцию 106 в жидкой форме для дальнейшей очистки. Тарелка плавления 130 собирает и нагревает смесь жидкость-твердое вещество из промежуточной секции распыления 108 в объеме жидкости. Тарелка плавления 130 сконструирована так, чтобы выделять поток пара обратно в промежуточную секцию распыления 108, обеспечивая надлежащий теплоперенос, расплавляя твердый CO2 и облегчая слив жидкости/суспензии в нижнюю дистилляционную или отгоночную секцию 106 колонны 100 ниже тарелки плавления 130. Фиг. 2 А представляет вид сверху тарелки плавления 130 в одном варианте осуществления. Фиг. 2 В представляет вид в разрезе тарелки плавления 130, сделанном вдоль линии В-В на фиг. 2 А. Фиг. 2 С показывает вид в разрезе тарелки плавления 130, сделанном вдоль линии С-С. Тарелка плавления 130 будет описана со ссылкой на эти три чертежа вместе. Во-первых, тарелка плавления 130 включает в себя основание 134. Основание 134 может быть, по существу, плоским телом. Однако в предпочтительном варианте осуществления, показанном на фиг. 2 А-2 С, основание 134 имеет, по существу, неплоский профиль. Неплоская конфигурация обеспечивает увеличенную площадь поверхности для контакта жидкостей и твердых веществ, приземляющихся на тарелку плавления 130 из промежуточной секции распыления 108. Это служит для увеличения теплопереноса от паров, проходящих вверх из отгоночной секции 106 колонны 100 к жидкостям и тающим твердым веществам. В одном аспекте основание 134 является рифленым. В другом аспекте основание 134 является, по существу, синусоидальным. Этот аспект дизайна тарелки показан на фиг. 2 В. Понятно,что другие неплоские геометрии могут альтернативно применяться для увеличения площади теплопереноса тарелки плавления 130. Основание 134 тарелки плавления предпочтительно является наклонным. Наклон показан на виде сбоку на фиг. 2 С. Хотя большинство твердых веществ должно плавиться, наклон служит для того, чтобы гарантировать, что любые нерасплавившиеся твердые вещества в жидкой смеси стекают с тарелки плавления 130 в отгоночную секцию 106 ниже. На фиг. 2 С колодец или слив 138 виден в центре тарелки плавления 130. Основание 134 тарелки плавления наклонено внутрь к сливу 138, чтобы подавать смесь твердое вещество-жидкость. Основание 134 может быть наклонено любым образом, чтобы облегчить гравитационное вытекание жидкости. Как описано в патенте США 4533372, тарелка плавления называется "вытяжная тарелка". Это изза присутствия единственной отводящей вытяжки. Вытяжка обеспечивает отверстие, через которое пар может двигаться вверх через вытяжную тарелку. Однако наличие единственной вытяжки означает, что все газы, движущиеся вверх через вытяжную тарелку, должны выходить через единственное отверстие. С другой стороны, в тарелке плавления 130 на фиг. 2 А-2 С обеспечено множество вытяжек 131 (или "стояков"). Использование множества вытяжек 131 обеспечивает улучшенное распределение пара. Это содействует лучшему тепло-/массопереносу в промежуточной секции распыления 108. Вытяжки 131 могут быть любого профиля. Например, вытяжки 131 могут быть круглыми, прямо-7 021006 угольными или любой другой формы, которая позволяет пару проходить через тарелку плавления 130. Вытяжки 131 также могут быть узкими или распространяться вверх в промежуточной секции распыления 108. Это делает возможным выгодный перепад давления, чтобы распределять пар равномерно, когда он поднимается в CFZ промежуточную секцию распыления 108. Вытяжки 131 предпочтительно расположены на вершинах рифленого основания 134, обеспечивая дополнительную область теплопереноса. Верхние отверстия вытяжек 131 предпочтительно покрыты шляпками или крышками 132. Это минимизирует вероятность того, что твердые вещества, падающие из секции распыления 108, могут избежать падения на тарелку плавления 130. На фиг. 2 А-2 С крышки 132 видны поверх каждой из вытяжек 131. Тарелка плавления 130 также может быть сконструирована с колпачками. Колпачки задают выпуклые надрезы в основании 134, поднимающиеся от тарелки плавления 130. Колпачки дополнительно увеличивают площадь поверхности в тарелке плавления 130, обеспечивая дополнительный теплоперенос кCO2-богатой жидкости. При этой конструкции подходящий сток жидкости, такой как увеличенный угол наклона, должен быть обеспечен, чтобы гарантировать, что жидкость направляется на отпарные тарелки 126 ниже. Согласно фиг. 1 тарелка плавления 130 также может быть сконструирована с внешней системой переноса жидкости. Данная система переноса служит для того, чтобы гарантировать, что вся жидкость, по существу, свободна от твердых веществ и что обеспечен достаточный теплоперенос. Система переноса,во-первых, включает в себя сливное сопло 136. В одном варианте осуществления сливное сопло 136 находится внутри сливного колодца или слива 138. Текучие среды, собранные в сливе 138, поступают в линию переноса 135. Течение через линию переноса 135 регулируется регулирующим клапаном 137 и контроллером уровня "LC" (см. на фиг. 1). Текучие среды возвращаются в отгоночную секцию 106 по линии переноса 135. Если уровень жидкости слишком высокий, регулирующий клапан 137 открывается; если уровень слишком низкий, регулирующий клапан 137 закрывается. Если оператор выбирает не применять систему переноса в отгоночной секции 106, то регулирующий клапан 137 закрыт и текучие среды направляют непосредственно в устройства массопереноса или "отпарные тарелки" 126 ниже тарелки плавления 130 для отгонки путем наполнения слива 139. Используется или нет внешняя система переноса, твердый CO2 нагревается на тарелке плавления 130 и превращается в богатую CO2 жидкость. Тарелка плавления 130 нагревается снизу парами из отгоночной секции 106. Дополнительное тепло может быть добавлено к тарелке плавления 130 или непосредственно выше основания 134 тарелки плавления с помощью различных средств, таких как нагревающая линия 25. Нагревающая линия 25 использует тепловую энергию, уже доступную от нижнего ребойлера 160, для облегчения таяния твердых веществ. Богатая CO2 жидкость отводится из тарелки плавления 130 под контролем уровня жидкости и под действием гравитации вводится в отгоночную секцию 106. Как указано, множество отпарных тарелок 126 обеспечено в отгоночной секции 106 ниже тарелки плавления 130. Отпарные тарелки 126 предпочтительно расположены, по существу, параллельно одна над другой. Каждая из отпарных тарелок 126 может располагаться при очень слабом наклоне с плотиной, так что некоторый уровень жидкости поддерживается на тарелке. Текучие среды гравитационно текут вдоль каждой тарелки, над плотиной и затем стекают на следующую тарелку через слив. Отпарные тарелки 126 могут быть в различном расположении. Отпарные тарелки 126 могут быть расположены в основном горизонтально, образуя синусоидальное каскадное течение жидкости. Однако предпочтительно, когда отпарные тарелки 126 расположены, образуя каскадное течение жидкости, которое разделено отдельными отпарными тарелками, по существу, вдоль одной горизонтальной плоскости. Это показано в расположении на фиг. 3, где течение жидкости расщепляется по меньшей мере один раз,так что жидкость падает в два противоположных слива 129. Фиг. 3 обеспечивает вид сбоку расположения отпарных тарелок 126 в одном варианте осуществления. Каждая из отпарных тарелок 126 принимает и собирает текучие среды сверху. Каждая отпарная тарелка 126 предпочтительно имеет плотину 128, которая служит в качестве дамбы, позволяя накопление небольшого объема текучей среды на каждой из отпарных тарелок 126. Выступ может быть от 1/2 до 1 дюйма (от 1,27 до 2,54 см), хотя любая высота может применяться. Эффект водопада возникает с помощью сливов 128, когда текучая среда падает от одной тарелки 126 на следующую нижнюю тарелку 126. В одном аспекте отпарным тарелкам 126 не придается никакого наклона, но эффект водопада возникает посредством более высокой конфигурации слива 128. Текучая среда контактирует с восходящим паром,богатым более легкими углеводородами, что отбирает метан из встречно текущей жидкости в этой "области контакта" тарелок 126. Плотины 128 служат для динамической герметизации сливов 129, предотвращая проскок пара сквозь сливы 129 и дополнительно облегчая отрыв углеводородных газов. Процент метана в жидкости уменьшается, когда жидкость движется вниз сквозь отгоночную секцию 106. Степень дистилляции зависит от числа тарелок 126 в отгоночной секции 106. В верхней части отгоночной секции 106 содержание метана в жидкости может быть высоким - до 25 мол.%, тогда как на нижней отпарной тарелке содержание метана может быть низким - до 0,04 мол.%. Содержание метана быстро падает вдоль отпарных тарелок 126 (или других устройств массопереноса). Число устройств мас-8 021006 сопереноса, используемых в отгоночной секции 106, является предметом конструкционного выбора, основанного на композиции исходного газового потока 10. Однако необходимо использовать только немного уровней отпарных тарелок 126, чтобы удалить метан до желаемого уровня 1% или меньше в сжиженном кислотном газе, например. Могут применяться различные конфигурации индивидуальных отпарных тарелок 126, которые облегчают отрыв метана. Отпарные тарелки 126 могут быть просто площадкой с ситовыми отверстиями или колпачками. Однако чтобы обеспечить дополнительный теплоперенос к текучей среде и предотвратить нежелательную блокировку твердыми веществами, так называемые "струевые тарелки" могут применяться ниже тарелки плавления. Вместо тарелок может также применяться неупорядоченная или структурированная насадка. Фиг. 4 А представляет вид сверху примерной струевой тарелки 426 в одном варианте осуществления. Фиг. 4 В представляет вид в разрезе струевой высечки 422 от струевой тарелки 426. Как показано,каждая струевая тарелка 426 имеет тело 424 с множеством струевых высечек 422, образованных в теле 424. Каждая струевая высечка 422 включает в себя наклонный высечной элемент 428, закрывающий отверстие 425. Таким образом, струевая тарелка 426 имеет множество маленьких отверстий 425. При работе одна или несколько струевых тарелок 426 могут быть расположены в отгоночной 106 и/или ректификационной 110 секциях колонны 100. Тарелки 426 могут быть расположены с множеством проходов, как расположение отпарных тарелок 126 на фиг. 3. Однако может применяться любое расположение тарелок или насадки, которое облегчает отрыв метанового газа. Текучая среда падает каскадом вниз на каждую струевую тарелку 426. Текучие среды затем текут вдоль тела 424. Текучая среда затем контактирует с паром, выходящим через отверстия 425. Высечки 422 оптимально ориентированы, чтобы двигать текучую среду быстро и эффективно по тарелке 426. Прилегающий слив (не показан) может быть обеспечен, чтобы перемещать жидкость на соседнюю тарелку 426. Отверстия 425 также позволяют парам выделяться во время процесса движения текучей среды в отгоночной секции 106, перемещаясь вверх более эффективно к тарелке плавления 130 и сквозь вытяжки 131. В одном аспекте тарелки 126 или 426 могут быть изготовлены из стойких к засорению материалов,то есть материалов, которые предотвращают нарастание твердого вещества. Стойкие к засорению материалы применяются в некотором обрабатывающем оборудовании, чтобы предотвращать нарастание металлических частиц, полимеров, солей, гидратов, мелких частиц катализатора или других твердых химических соединений. В случае криогенной дистилляционной колонны 100 стойкие к засорению материалы могут быть использованы в тарелках 126 или 426, чтобы ограничивать прилипание твердого CO2. Например, тефлоновое покрытие может наноситься на поверхность тарелок 126 или 426. Альтернативно, может быть обеспечен физический дизайн, гарантирующий, что CO2 не начинает нарастать в твердой форме вдоль внутреннего диаметра колонны 100. В этой связи, струевые высечки 422 могут быть ориентированы так, чтобы толкать жидкость вдоль стенки колонны 100, предотвращая тем самым накопление твердых веществ вдоль стенки колонны 100 и гарантируя хороший контакт паржидкость. В любом из расположений тарелок, когда текущая вниз жидкость ударяется об отпарные тарелки 126, происходит разделение компонентов. Метановый газ отрывается из раствора и движется вверх в газообразной форме. CO2, однако, является достаточно холодным и в достаточно высокой концентрации,чтобы оставаться в жидкой форме и перемещаться вниз на дно отгоночной секции 106. Жидкость затем движется из криогенной дистилляционной колонны 100 в выходную линию в виде потока 22 выходящей текучей среды. После выхода из колонны 100 поток 22 выходящей текучей среды входит в ребойлер 160. На фиг. 1 ребойлер 160 котельного типа, который обеспечивает испаренный пар на дно отпарных тарелок. Линия пара ребойлера видна под номер 27. Кроме того, пар ребойлера может подаваться через нагревающую линию 25, обеспечивая дополнительное тепло к тарелке плавления 130. Дополнительное тепло регулируется клапаном 165 и контроллером температуры ТС. Альтернативно, теплообменник, такой как термосифонный теплообменник (не показан), может быть использован для потока 10 исходной текучей среды,чтобы экономить энергию. В этой связи, жидкости, входящие в ребойлер 160, остаются при относительно низкой температуре, например приблизительно от 30 до 40F (-1,1 до 4,4C). Суммируя тепло с потоком 10 исходной текучей среды, оператор может нагревать холодный выходящий поток 22 текучей среды из дистилляционной колонны 100, охлаждая поток 10 добытой текучей среды. В этом случае, текучая среда, обеспечивающая дополнительное тепло по линии 25, представляет собой смешанную фазу, возвращающуюся из ребойлера 160. Предполагается, что в некоторых условиях тарелка плавления 130 может работать без нагревающей линии 25. В этих случаях, тарелка плавления 130 может быть сконструирована с признаком внутреннего нагрева, таким как электрический нагреватель. Однако предпочтительно, когда предлагается тепловая система, которая использует тепловую энергию, доступную в потоке 22 выходящей текущей среды. Теплые текучие среды в нагревающей линии 25 после выхода из ребойлера 160 существуют в одном аспекте при от 30 до 40F (от -1,1 до 4,4C), поэтому они содержат соответствующую тепловую энергию. Таким образом, на фиг. 1 поток 25 пара показан направляющимся в тарелку плавления 130 через нагревающую спираль (не показана) на тарелке плавления 130. Поток 25 пара может альтернативно привязываться к линии переноса 135. При работе поток пара ребойлера вводится из кубовой части колонны по линии 27 выше уровня донной жидкости и ниже последней отпарной тарелки 126. Когда пар ребойлера проходит через каждую тарелку 126, остаточный метан испаряется из жидкости. Этот пар охлаждается, когда он путешествует вверх в колонне. Ко времени, когда отгоночный пар потока 27 достигает рифленой тарелки плавления 130, температура может падать приблизительно от -20 до 0F (от -28,9 до -17,8C). Однако он остается достаточно теплым по сравнению с плавящимся твердым веществом на тарелке плавления 130, которое может быть приблизительно от -50 до -80F (от -45,5 до -62,2C). Пар все еще имеет достаточную энтальпию, чтобы плавить твердый CO2, когда он вступает в контакт с тарелкой плавления 130, нагревая тарелку плавления 130. Возвращаясь к ребойлеру 160, текучие среды в нижнем потоке 24, который выходит из ребойлера 160 в жидкой форме, могут проходить через расширительный клапан 162. Расширительный клапан 162 снижает давление нижнего жидкого продукта, эффективно обеспечивая охлаждающий эффект. Таким образом, обеспечивается охлажденный нижний поток 26. Это также создает гидростатический напор. В этой связи, богатая CO2 жидкость, выходящая из ребойлера 160, может закачиваться в скважину через одну или несколько ВКГ скважин (схематично видно под номером 250 на фиг. 1). В некоторых ситуациях жидкий CO2 может закачиваться в частично извлеченное нефтяное месторождение в качестве части процесса усиленной нефтедобычи. Таким образом, CO2 может быть смешивающимся агентом впрыскивания. В качестве альтернативы CO2 может использоваться в качестве смешивающегося затопляющего агента для усиленной нефтедобычи. Возвращаясь снова к отгоночной секции 106 колонны 100, газ движется вверх через отгоночную секцию 106, через вытяжки 131 в тарелке плавления 130 и в промежуточную секцию распыления 108. Секция распыления 108 представляет собой открытую камеру, имеющую множество распыляющих сопел 122. Когда пар движется вверх через секцию распыления 108, температура пара становится гораздо холоднее. Пар контактирует с жидким метаном, приходящим из распыляющих сопел 122. Этот жидкий метан холоднее, чем двигающийся вверх пар, охлажденный внешним охлаждающим блоком 170. В одном расположении жидкий метан выходит из распыляющих сопел 122 при температуре приблизительно от -120 до -130F (от -84,4 до -90C). Однако, когда жидкий метан испаряется, он поглощает тепло из его окружения, тем самым снижая температуру двигающегося вверх пара. Испаренный метан также течет вверх из-за его низкой плотности (относительно жидкого метана) и градиента давления внутри колонны 100. Когда пары метана движутся далее к верху криогенной дистилляционной колонны 100, они покидают промежуточную секцию распыления 108 и входят в ректификационную секцию 110. Пары продолжают двигаться вверх вместе с другими легкими газами, вырванными из потока 12 исходной охлажденной текучей среды. Объединенные углеводородные пары движутся из вершины криогенной дистилляционной колонны 100, становясь верхним метановым потоком 14. Углеводородный газ в верхнем метановом потоке 14 движется во внешний охлаждающий блок 170. В одном аспекте охлаждающий блок 170 использует этиленовый охлаждающий агент или другой охлаждающий агент, способный охлаждать верхний метановый поток 14 от -135 до -45F (от -92,8 до-42,8C). Это служит, по меньшей мере, для частичного сжижения верхнего метанового потока 14. Охлажденный метановый поток 14 затем движется в дефлегматор или разделительную камеру 172. Разделительная камера 172 используется для отделения газа 16 от жидкой флегмы 18. Газ 16 представляет собой более легкие, углеводородные газы, главным образом метан, из исходного сырого газового потока 10. Азот и гелий также могут присутствовать. Метановый газ 16 является, конечно, "продуктом", в конечном счете отбираемым и продаваемым коммерчески вместе с любым этаном. Часть верхнего метанового потока 14, покидающего охлаждающий блок 170, остается конденсированной. Эта часть становится жидкостью орошения 18, которая отделяется в разделительной камере 172 и возвращается в колонну 100. Насос 19 может использоваться, чтобы перемещать жидкость орошения 18 обратно в колонну 100. Альтернативно, разделительная камера 172 устанавливается над колонной 100, обеспечивая гравитационную подачу жидкости орошения 18. Жидкость орошения 18 будет включать в себя любой диоксид углерода, который ускользнул из верхней ректификационной секции 110. Однако большая часть жидкости орошения 18 является метаном, обычно 95% или больше, с азотом (если присутствует в потоке 10 исходной текучей среды) и следами диоксида углерода и сероводорода (также если присутствует в потоке 10 исходной текучей среды 10). В одной конфигурации охлаждения верхний метановый поток 14 отбирается через охлаждающую систему с открытым контуром, такую как охлаждающая система, показанная и обсуждаемая в связи с фиг. 6. В этой компоновке верхний метановый поток 14 отбирается через встречный обменник, охлаждающий возвращающуюся часть верхнего метанового потока, используемую в качестве жидкости орошения 18. Затем верхний метановый поток 14 сжимают до давления приблизительно от 1000 до 1400 psi(от 6,99 до 9,78 МПа) и затем охлаждают, используя окружающий воздух и, возможно, внешний пропановый охладитель. Сжатый и охлажденный газовый поток затем направляется через расширитель для дополнительного охлаждения. Турбодетандер может использоваться, чтобы извлекать еще больше жидкости, а также некоторую работу вала. Патент США 6053007, озаглавленный "Process For Separating aMulti-Component Gas Stream Containing at Least One Freezable Component", описывает охлаждение верхнего метанового потока и включен сюда во всей полноте посредством ссылки. Понятно, что настоящее изобретение не ограничивается данным способом охлаждения верхнего метанового потока 14. Также понятно, что степень охлаждения между охлаждающим блоком 170 и исходным охлаждающим блоком 150 может меняться. В некоторых случаях может быть желательно, чтобы охлаждающий блок 150 работал при более высокой температуре, но затем было более интенсивное охлаждение верхнего метанового потока 14 в охлаждающем блоке 170. Опять настоящее изобретение не ограничивается этими типами выборов конструкции. Возвращаясь к фиг. 1, жидкость орошения 18 возвращается в ректификационную секцию 110. Жидкость орошения 18 затем гравитационно переносится через одно или несколько устройств массопереноса 116 в ректификационной секции 110. В одном варианте осуществления устройства массопереноса 116 представляют собой ректификационные тарелки, которые обеспечивают каскадную серию плотин 118 и сливов 119 подобно тарелкам 126, описанным выше. Когда поток 18 жидкости орошения движется вниз через ректификационные тарелки 116, дополнительный метан испаряется из ректификационной секции 110. Метановые газы повторно присоединяются к верхнему метановому потоку 14, становясь частью потока 16 газового продукта. Однако оставшаяся жидкая фаза жидкости орошения 18 падает на собирающую тарелку 140. Когда это происходит, поток 18 жидкости орошения неизбежно будет подбирать небольшой процент углеводородных и остаточных кислотных газов, движущихся вверх из секции распыления 108. Жидкая смесь метана и диоксида углерода собирается на собирающей тарелке 140. Собирающая тарелка 140 предпочтительно представляет собой, по существу, плоское тело для сбора жидкостей. Однако, как для тарелки плавления 130, собирающая тарелка 140 также имеет один, а предпочтительно множество вытяжек для выпуска газов, поднимающихся из секции распыления 108. Может быть использовано такое же расположение вытяжек и крышек, как представлено компонентами 131 и 132 на фиг. 2 В и 2 С. Вытяжки 141 и крышки 142 собирающей тарелки 140 показаны в увеличенном виде на фиг. 5, дополнительно обсуждаемой ниже. Здесь следует заметить, что в ректификационной секции 110 любой присутствующий H2S имеет предпочтение к растворению в жидкости относительно нахождения в газе при рабочей температуре. В этом отношении H2S имеет сравнительно низкую относительную летучесть. Путем контакта оставшегося пара с большим количеством жидкости криогенная дистилляционная колонна 110 сдвигает концентрацию H2S вниз внутрь желаемого предела частей-на-миллион, такого как 10 или даже 4 ч./млн в спецификации. Когда текучая среда движется через устройства массопереноса 116 в ректификационной секции 110, H2S контактирует с жидким метаном, вытягивается из газовой фазы и становится частью жидкого потока 20. Оттуда H2S движется в жидкой форме вниз через отгоночную секцию 106 и в конечном счете выходит из криогенной дистилляционной колонны 100 как часть потока 22 сжиженного кислотного газа. В криогенной дистилляционной колонне 100 жидкость, захваченная на собирающей тарелке 140,выходит из ректификационной секции 110 в виде потока жидкости 20. Поток жидкости 20 образован,главным образом, из метана. В одном аспекте поток жидкости 20 образован из приблизительно 93 мол.% метана, 3% CO2, 0,5% H2S и 3,5% N2. В этой точке поток жидкости 20 находится при приблизительно от-125 до -130F (от -87,2 до -90C). Это только немного теплее, чем поток 18 отбираемой текучей среды. Поток жидкости 20 направляется в сборник орошения 174. Задачей сборника орошения 174 является обеспечить напорную емкость для насоса 176. После выхода из сборника орошения 174 образуется поток распыления 21. Поток распыления 21 сдавливается в насосе 176 для повторного ввода в криогенную дистилляционную колонну 100. В этом случае поток распыления 21 нагнетается в промежуточную секцию распыления 108 и выпускается через сопла 122. Некоторая часть потока распыления 21, в частности метан, испаряется при выходе из сопел 122. Оттуда метан поднимается через промежуточную секцию распыления 108, через вытяжки в собирающей тарелке 140 и через устройства массопереноса 116 в ректификационной секции 110. Метан покидает дистилляционную колонну 100 в виде верхнего метанового потока 14 и в конечном счете становится коммерческим продуктом в газовом потоке 16. Поток распыления 21 из сопел 122 также заставляет диоксид углерода десублимировать из газовой фазы. При этом часть CO2 мгновенно проникает в газовую фазу и движется вверх с метаном. Однако изза холодной температуры в промежуточной секции распыления 108 газообразный диоксид углерода быстро превращается в твердую фазу и начинает "падать". Это явление называется десублимацией. Таким образом, часть CO2 никогда не попадает повторно в жидкую фазу до того, как он ударяется о тарелку плавления 130. Этот диоксид углерода "оседает" на тарелку плавления 130 и плавится в жидкую фазу. Оттуда богатая СО 2 жидкость проходит каскадом вниз на устройства массопереноса или тарелки 126 в отгоночной секции 106 вместе с жидким CO2 из потока 12 охлажденной текучей среды, как описано выше. В этой точке любой оставшийся метан из потока распыления 21 сопел 122 будет быстро вырываться в пар. Эти пары движутся вверх в криогенной дистилляционной колонне 100 и повторно входят в ректи- 11021006 фикационную секцию 110. Предпочтительно обеспечивать контакт охлажденной жидкости с максимально большим количеством газа, который движется вверх в колонне. Если пар обходит поток распыления 21, испускаемый из сопел 122, более высокие уровни CO2 могут достигать ректификационной секции 110 колонны 100. Чтобы улучшить эффективность контакта газ/жидкость в промежуточной секции распыления 108, может применяться множество сопел 122, имеющих разработанную конфигурацию. Таким образом, несколько распылительных головок 120, возможно, оборудованных многими распылительными соплами 122, могут быть использованы предпочтительнее, чем использовать единственный источник распыления на одном или нескольких уровнях в потоке 21 текучей среды орошения. Таким образом, конфигурация сопел распыления 122 имеет влияние на массоперенос, происходящий внутри промежуточной секции распыления 108. Уполномоченное лицо ранее предложило различные расположения сопел в совместно рассматриваемой патентной публикации WO2008/091316, имеющей дату международной регистрации 20 ноября 2007 г. Эта заявка и фиг. 6 А и 6 В включены сюда посредством ссылки для описания конфигураций сопел. Сопла стремятся гарантировать 360 и полное радиальное покрытие внутри секции распыления 108 и обеспечить хороший контакт пар-жидкость в тепло-/массоперенос. Это, в свою очередь, более эффективно охлаждает любой диоксид углерода, движущийся вверх через криогенную дистилляционную колонну 100. Использование множества головок 120 и соответствующее перекрывающееся расположение сопел 122 для полного покрытия хорошо минимизирует обратное смешение. В этой связи, полное покрытие предотвращает тонкие частицы CO2 в низкой массе от движения обратно вверх в колонне и повторного входа в ректификационную секцию 110. Эти частицы затем повторно смешивались бы с метаном и повторно попадали в верхний метановый поток 14, чтобы опять возвращаться. Можно видеть, что процесс рециркуляции паров через криогенную дистилляционную колонну 100 в конечном счете дает углеводородный продукт, образованный из коммерческого метанового продукта 16. Газовый продукт 16 направляется в трубопровод для продажи. Поток 16 газового продукта предпочтительно удовлетворяет трубопроводной спецификации по CO2 от 1 до 4 мол.%, а также спецификации по H2S 4 ч./млн, если генерируется достаточное орошение. В то же время, кислотные газы удаляются посредством потока 22 выходящей текучей среды. Если азот будет присутствовать в количестве, например, больше чем 3 мол.%, отдельный процесс повторного закачивания азота может применяться. Трубопроводные спецификации обычно требуют содержания всех инертных газов менее чем 3 мол.%. Одной возможностью удаления избыточного азота является использование слоя твердого адсорбента (не показан). Твердый адсорбент может быть цеолитным материалом, который образует молекулярное сито, имеющее выбранный размер пор. Молекулярное сито помещают вдоль верхнего метанового потока для удаления азота из верхнего потока. Предпочтительно это происходит до охлаждения. Как только это молекулярное сито полностью наполняется азотом, его можно регенерировать, используя либо адсорбцию с колебаниями давления, либо адсорбцию с термическими колебаниями. Молекулярное сито обычно не может быть регенерировано, используя адсорбцию воды выше по ходу от криогенной колонны, так как азот останется обратно в колонне и, таким образом, не устраняется из системы. Хотя вышеуказанная система, описанная в связи с фиг. 1, является преимущественной для получения, по существу, свободного от кислот трубопроводного газового продукта 16, допустимо, что в некоторых приложениях может требоваться дополнительное охлаждение. Например, СПГ спецификации могут быть настолько низкими, как 50 ч./млн для CO2. При использовании системы, описанной выше, требуется значительное охлаждение орошения от внешнего охлаждающего блока 170 (или другой охлаждающей системы). Кроме того, дополнительное охлаждение может потребоваться до введения орошения из насоса 19 или насоса 176. Еще дополнительно значительное удаление тепла может быть необходимо из исходного теплообменника 150 для частичного сжижения потока 10 сырья. Эти холодильники требуют емкости для генерации жидкого орошения и энергии для мощности. В качестве альтернативы здесь предлагается способ "доочистки". "Доочистка" применяется к верхнему метановому потоку 14 в качестве пост-CFZ способа. Это означает, что верхний метановый поток 14, выходящий из криогенной дистилляционной колонны 100, дополнительно очищается ниже по ходу от колонны 100, чтобы удовлетворять, например, спецификациям сжиженного природного газа (СПГ) без увеличения жидкого орошения, вводимого через сопла распыления 122. Фиг. 6 представляет собой схематичное изображение, показывающее газоперерабатывающую установку 600 для удаления кислотных газов из газового потока в одном варианте осуществления. Добытый газовый поток показан под номером 612. Газовый поток 612 происходит от деятельности углеводородной добычи, которая имеет место в области разработки месторождения или "поля" 610. Понятно, что поле 610 может представлять любое место, где добывают сжимаемые углеводороды. Поле 610 может быть береговым, возле берега или в открытом море. Поле 610 может работать от исходного давления месторождения или может подвергаться процедурам усиленной добычи. Системы и способы, заявленные здесь, не ограничиваются типом поля, которое находится в разработке, пока оно про- 12021006 изводит сжимаемые углеводороды, загрязненные кислотным газом. Поток 612 добытого газа может направляться сквозь процесс дегидратации, такой как гликольный процесс дегидратации. Резервуар дегидратации схематично показан под номером 620. В результате прохождения потока 612 добытого газа через резервуар дегидратации 620 образуется поток удаленной воды 622. Вода 622 может направляться в установку обработки воды. Альтернативно, вода 622 может повторно вводиться в подземную формацию, обозначенную блоком 630. Альтернативно, вода может обрабатываться и затем повторно вводиться обратно в подземную формацию 630, связанную с полем 610. Также в результате прохождения потока 612 добытого газа через резервуар дегидратации 620 получается, по существу, дегидратированный поток 624 исходного газа. Исходный газовый поток 624 предпочтительно содержит метан и, возможно, следовые количества этана, азота, гелия и других легких газов. Исходный газовый поток 624 может проходить по трубопроводу, например, из обрабатывающей установки в открытом море в обрабатывающую установку на берегу. Газ может затем проходить через слой твердого адсорбента 625 для дополнительной дегидратации газа в газовом потоке 624. Удаление воды из исходного газового потока 624 помогает гарантировать, что ни гидраты, ни лед не образуются в последующих охлаждающих или криогенных установках. Слой твердого адсорбента 625 может быть слоем молекулярного сита. "Молекулярное сито" относится к материалу, содержащему крошечные поры определенного и, по существу, однородного размера. В настоящем контексте такие сита используются в качестве адсорбента для газов и/или жидкостей. Молекулярные сита часто состоят из твердых материалов и неполимерных материалов. Типичные материалы включают алюмосиликатные минералы, глины, пористые стекла, микропористый древесный уголь,цеолиты, активированный уголь или синтетические соединения, которые имеют открытые структуры,через которые маленькие молекулы, такие как азот и вода, могут диффундировать. Полярные молекулы(такие как молекулы воды), которые являются достаточно маленькими, чтобы проходить в данные поры,адсорбируются, тогда как слабо поляризуемые молекулы (такие как метан и азот), а также большие молекулы (например, пропан и бутан) текут вокруг частиц и кристаллитов и, таким образом, проходят ниже по ходу. В данном случае слой молекулярного сита 625 адсорбирует молекулы воды и позволяет легким газам проходить насквозь. Исходный газовый поток 624 затем проходит через охлаждающий блок 626. Охлаждающий блок 626 охлаждает дегидратированный исходный газовый поток 624 до температуры приблизительно от-30 до -40F (от -34,4 до -40C). Охлаждающий блок 626 может быть, например, этиленовым или пропановым охладителем. Исходный газовый поток 624 затем предпочтительно движется через расширительное устройство 628. Расширительное устройство 628 может быть, например, клапаном Джоуля-Томпсона ("J-T"). Расширительное устройство 628 служит в качестве расширителя для получения дополнительного охлаждения исходного газового потока 624. Расширительное устройство 628 дополнительно снижает температуру дегидратированного исходного газового потока 624, например, до приблизительно от -70 до -80F (от-56,7 до -62,2C). Предпочтительно также выполняется, по меньшей мере, частичное сжижение газового потока 624. Охлажденный исходный газовый поток 624 затем поступает в криогенную дистилляционную колонну 640. Криогенная дистилляционная колонна может быть любой колонной, которая функционирует,дистиллируя метан от кислотных газов посредством процесса, который преднамеренно замораживает частицы CO2. Криогенная дистилляционная колонна может быть, например, колонной 100 с фиг. 1. Охлажденный исходный газовый поток 624 поступает в резервуар при давлении приблизительно от 500 до 600 psig (от 3,49 до 4,19 МПа). Дистилляционная колонна 640 включает в себя нижнюю отгоночную секцию (видимую как секцию 106 на фиг. 1). Дистилляционная колонна 640 также включает в себя зону контролируемого замерзания(видимую как секция 108 на фиг. 1), где пар контактирует с холодной жидкость орошения (главным образом, метаном). Она заставляет СО 2 вымерзать из газовой фазы. Оставшийся метан и другие газофазные компоненты испаряются и поднимаются вверх в верхнюю ректификационную секцию (видимую как секция 110 на фиг. 1). Там остаточные H2S и CO2 дополнительно удаляются из газовой фазы. В одном аспекте (не показан) используется "расщепляющая колонна", в которой ректификационная секция 110 находится в отдельном резервуаре от отгоночной секции 106 и зоны контролируемого замерзания 108. Как объясняется в связи с фиг. 1, кислотные газы удаляются из дистилляционной колонны 640 в виде нижнего потока 642 сжиженного кислотного газа. Этот жидкий поток 642 может направляться через ребойлер 643, где газ, содержащий следовые количества метана, повторно направляется обратно в колонну в виде газового потока 644. Остальная жидкость, образованная, главным образом, из кислотных газов, выходит по линии 646 кислотных газов. Сжиженный кислотный газ в линии 646 может испаряться,декомпремироваться и затем направляться в блок извлечения серы (не показан). Альтернативно, сжиженный кислотный газ может вводиться в подземную формацию через одну или несколько скважин ввода кислотного газа (ВКГ), как показано блоком 650. В этом случае, кислотный газ в линии 646 предпочтительно проходит через усилитель давления 648. Метан выходит из дистилляционной колонны 640 в виде верхнего метанового потока 662. Верхний метановый поток 662 будет предпочтительно содержать не больше чем приблизительно 2% диоксида углерода. При этом процентном содержании верхний метановый поток 662 может быть использован в качестве топливного газа или может продаваться на определенных рынках в качестве природного газа. Однако согласно определенным здесь способам, желательно, чтобы верхний метановый поток 662 подвергался дополнительной обработке. Как указано выше, верхний метановый поток 662 проходит через систему охлаждения с открытым контуром. Сначала верхний метановый поток 662 проходит через теплообменник 664. Он служит для предварительного охлаждения потока орошения 680, который повторно вводится в криогенную дистилляционную колонну 640. Верхний метановый поток 662 затем направляют через компрессор 666 для увеличения его давления. Затем сжатый метановый поток 662, нагретый компрессией, охлаждают. Это может быть сделано путем, например, прохождения метанового потока 662 через воздушный охладитель 668. Получается холодный и сжатый метановый поток. Часть холодного и сжатого метанового потока, покидающего охладитель 668, отщепляется в поток орошения 680. Поток орошения 680 дополнительно охлаждается во встречном обменнике 664, затем расширяется посредством устройства 682, образуя поток жидкого орошения 684. Поток жидкого орошения 684 поступает в дистилляционную колонну 640, где он используется в качестве орошения и в конечном счете в распылении для вымораживания частиц CO2 и других кислотных газов из дегидратированного газового потока 624. Генерируется достаточное орошение, так что спецификации по CO2 и H2S частично удовлетворяются вверху колонны 640. Поток жидкого орошения 684 из расширителя 682 может вводиться непосредственно в сопла распыления в зоне контролируемого замерзания. Более предпочтительно поток жидкого орошения 684 сначала направляется в ректификационную секцию дистилляционной колонны 640, чтобы дополнительно снижать концентрацию CO2 в верхнем газе. В любом случае,охлажденный поток орошения 680 предпочтительно проходит через расширительный клапан или турбодетандер 682 для образования жидкости. Возвращаясь к верхнему метановому потоку 662, верхний метановый поток 662 может проходить через один или несколько расширительных клапанов или турбодетандеров. Расширительный клапан показан под номером 670 на фиг. 6. Расширительный клапан или (турбодетандер) 670 снижает давление газового потока 662 и охлаждает его дополнительно при подготовке сжижения с образованием СПГ. Таким образом, образуется охлажденный газовый поток 672. Понятно, что спецификации для сжиженного природного газа или СПГ могут требовать, чтобы концентрация кислотного газа была ниже чем 2 мол.%. СПГ-спецификации обычно позволяют не больше чем 50 ч./млн CO2 и 4 ч./млн H2S. Соответственно согласно настоящим способам предварительный СПГ поток 672 направляют на слой твердого адсорбента 674 в качестве пост-обработки для дополнительного удаления кислотного газа. Предпочтительно слой твердого адсорбента 674 представляет собой слой молекулярного сита. Определенные молекулярные сита, такие как 4-ангстремные и 5-ангстремные слои,могут быть использованы для удаления CO2, a также H2O из метанового газового потока. Меркаптаны также могут удаляться. Верхний метановый поток 672 находится при высоком давлении и является относительно холодным, что облегчает адсорбцию CO2 на слое твердого адсорбента 674. Слой твердого адсорбента 674 может быть слоем молекулярного сита, который использует адсорбцию с колебаниями давления. Адсорбция с колебаниями давления или АКД относится к процессу, в котором примесь адсорбируется на твердом адсорбенте, затем удаляется из адсорбента путем снижения давления. В случае удаления кислотного газа CO2 может удаляться из кислого газа. В одном аспекте слой адсорбции с колебаниями давления является слоем адсорбции с быстрыми циклическими колебаниями давления или АБЦКД. Резервуар АБЦКД является особенно выгодным, так как он является компактным относительно стандартного АКД устройства. АКД используется для различных газовых разделений, например для удаления примесей из водородных потоков в нефтепереработке. Такие системы изготавливаются, например, QuestAir of British Columbia, Канада. Твердый адсорбент, используемый в слое молекулярного сита, может быть сделан из любого из нескольких материалов. Предпочтительно используются цеолиты. Цеолиты представляют собой кристаллические материалы, образованные из кремния и алюминия. Альтернативно, пост-процессор может быть резервуаром, который использует адсорбент, который зависит от скорости, с которой определенные частицы адсорбируются относительно других частиц. Это известно как адсорбционное кинетическое разделение (АКР). После насыщения CO2 цеолит или другой материал слоя может регенерироваться или очищаться. Это может быть сделано, например, путем снижения давления в слое и высвобождения кислотных газов или путем пропускания горячего газа через него. Горячий газ может быть, например, горячим метановым газом или нагретым азотом. Горячий метановый газ может захватываться и затем использоваться в качестве топлива, например, для работы охлаждающего оборудования при условии, что содержание H2S достаточно низкое. Слои молекулярного сита идеальны для последующей обработки, так как верхний метановый поток 662 уже является вполне чистым. Никакой дополнительно предварительной обработки не требуется для достижения газового потока СПГ-спецификации 672. Кроме того, нет необходимости в расходуемом слое материала в упакованном слое. Вместо слоя молекулярного сита другие типы постпроцессоров (не показаны) также могут применяться с газоперерабатывающей системой 600. Например, могут применяться один или несколько резервуаров, которые используют химические растворители для поглощения кислотных газов. Альтернативно,пост-процессор может представлять собой один или несколько резервуаров, которые используют физические растворители или ионные растворители для удаления остаточного CO2. Преимуществом этих растворителей является то, что они не являются водными, поэтому не потребуется никакой дополнительной дегидратации верхнего метанового потока 662. Конечно, добавление системы на основе растворителя в качестве пост-процессора будет существенно добавлять к количеству оборудования и, следовательно, не является предпочтительным. Можно видеть, что пост-процессор позволяет оптимизацию криогенной системы удаления кислотного газа путем использования уменьшенного жидкого орошения (то есть снижения емкости и мощности охлаждения) со слоем молекулярного сита 674 ниже по ходу или другим пост-процессором для захвата дополнительного CO2, а также H2S. Таким образом, верхний метановый поток 662 может превышать СПГ спецификацию 50 ч./млн для CO2 и СПГ спецификацию 4 ч./млн для H2S при условии, что постпроцессор 674 ниже по ходу, например слой молекулярного сита, будет удалять дополнительный кислотный газ, приводя конечный газовый продукт в соответствие со спецификациями. В любой форме пост-процессор генерирует газовый поток 676 для конечной продажи. Окончательный продажный газовый поток подходит для процесса сжижения ниже по ходу, в конечном счете приводя к продаже сжиженного природного газа или СПГ. Фиг. 7 А-7 С вместе представляют блок-схему. Данная блок-схема представляет способ 700 удаления кислотных газов из исходного газового потока с использованием системы удаления кислотных газов согласно настоящему изобретению в одном варианте осуществления. Способ 700, во-первых, включает в себя прием исходного газового потока. Этот этап показан блоком 705. Исходный газовый поток принимается как результат деятельности по добыче углеводородов. Другими словами, исходный газовый поток получается из подземного месторождения и поступает на поверхность для переработки. Согласно способу 700 исходный газовый поток содержит сжимаемые углеводороды. Они, главным образом, представляют собой метан. Однако следовые количества этана, азота, гелия и других жидких газов также могут присутствовать. Исходный газовый поток дополнительно содержит кислотные газы. Кислотные газы могут содержать диоксид углерода, сероводород, меркаптаны или другие примеси. Содержание кислотных газов в исходном газовом потоке может составлять, например, приблизительно от 5 до 60 мол.% от всего газового потока. В его добытой форме исходный газовый поток наиболее вероятно также содержит воду или рассол. Следовательно, как часть способа 700 исходный газовый поток подвергают процессу дегидратации. В одном аспекте исходный газовый поток, возможно, пропускают через первый слой молекулярного сита. Этот этап показан как блок 710. В настоящей заявке слой молекулярного сита адсорбирует молекулы воды из исходного газового потока. Таким образом, слой молекулярного сита в этапе 710 действует как влагопоглотитель. Слои молекулярного сита для адсорбции воды доступны из различных источников, таких как Texas Technologies,Inc. of Cedar Park, Texas и Eurecat U.S. of Houston, Texas. После дегидратации исходный газовый поток может проходить через охлаждающую систему. Этот этап показан как блок 715. Это может быть сделано, например, путем движения газового потока через холодильник, такой как охлаждающий блок 150 на фиг. 1. За этим может следовать прохождение исходного газового потока через расширитель, такой как расширительное устройство 152. Расширитель обеспечивает дополнительное охлаждение исходного газового потока. Согласно способу 700 исходный газовый поток затем очищают от кислотных газов. Это выполняется путем прохождения исходного газового потока через криогенную дистилляционную колонну. Этап прохождения исходного газового потока через криогенную дистилляционную колонну показан в блоке 720. Криогенная дистилляционная колонна может быть любой колонной, которая функционирует, дистиллируя метан или другие легкие углеводородные газы от кислотных газов посредством процесса, который включает в себя намеренное замораживание частиц CO2. Криогенная дистилляционная колонна может быть, например, колонной 100 с фиг. 1. Замерзшие частицы CO2 предпочтительно собираются на тарелке плавления на дне секции распыления дистилляционной колонны. Когда частицы плавятся и превращаются в жидкость, данная жидкость может каскадом стекать вниз через серию тарелок или сливов. Это заставляет добавочный метан вырываться из раствора, двигаясь вверх сквозь колонну в виде пара,как описано выше. Оставшаяся богатая CO2 жидкость затем отводится в виде нижнего потока сжиженного кислотного газа, включающего любой сероводород. В результате обработки исходного газового потока в криогенной дистилляционной колонне получается верхний метановый поток. Верхний метановый поток будет предпочтительно содержать не больше чем 5 мол.% и более предпочтительно не больше чем приблизительно 2 мол.% диоксида углерода. Способ 700 затем включает в себя охлаждение верхнего метанового потока. Этап охлаждения верхнего метанового потока показан в блоке 725 фиг. 7 А. Целью охлаждения верхнего метанового потока является, по меньшей мере, частично сжижать метан в нем. Верхний метановый поток охлаждают, используя охлаждающую систему. Данная система может быть, например, внешним блоком охлаждения с замкнутым контуром, таким как этиленовый или пропановый охлаждающий блок 170 на фиг. 1. Другим примером охлаждающей системы с замкнутым контуром является серия пропановых и этиленовых каскадных охладителей. Альтернативно, охлаждающая система может быть охлаждающей системой с открытым контуром, такой как охлаждающая система с открытым контуром, показанная в патенте США 6053007. В одном аспекте используется охлаждающая система с открытым контуром, в которой верхний метановый поток 14 отбирает тепло от возвращающегося жидкого потока посредством теплообменника и затем сжимается. Сжатый газ затем охлаждается до приблизительно окружающей температуры, используя воздушные охладители или, возможно,охладители морской водой. Газ может дополнительно охлаждаться до суб-окружающих температур, используя пропановый охладитель, например. Охлаждающая система с открытым контуром показана и описана в связи с фиг. 6. Способ 700 затем включает в себя отделение по меньшей мере части верхнего метанового потока для генерации жидкости орошения. Этот этап обеспечивается в блоке 730 на фиг. 7 В. Процесс отделения части верхнего метанового потока предпочтительно выполняют после того, как метановый поток, по меньшей мере, частично сжижают. В другом аспекте частично сжиженный верхний метановый поток(такой как поток 14) проходит через сепаратор (такой как дефлегматор или сепаратор 172). Сепаратор образует газовый поток 16 и жидкий поток 18. Часть или весь жидкий поток 18 повторно вводится в колонну 100 в качестве жидкости орошения. В связи с охлаждением верхнего метанового потока и как подразумевается выше работает охлаждающая система. Этап работы охлаждающей системы показан в блоке 735. Одной целью работы охлаждающей системы является генерировать некоторое количество жидкости орошения, которая будет удалять желаемый процент кислотных газов из исходного газового потока. Специалисты в данной области техники поймут, что существует корреляция между количеством жидкости орошения, вводимой в криогенную дистилляционную колонну, и эффективностью, с которой твердый диоксид углерода выпадает из потока пара внутри криогенной дистилляционной колонны. Чем сильнее охлаждается жидкий метан и чем больше генерируется количество жидкости орошения 18, тем более эффективно криогенная дистилляционная колонна будет высаживать диоксид углерода и другие кислотные газы. Однако охлаждающее оборудование дорого, и чем ниже температура жидкого орошения и чем больше генерируется жидкого орошения, тем больше требуется энергии и оборудования. На этапе 735 оператор или разработчик процесса намеренно не генерирует так много жидкого орошения, чтобы удалять все кислотные газы. Другими словами, количество жидкого орошения установлено так, чтобы удалять большую часть, но не весь диоксид углерода. Например, количество жидкого орошения может быть установлено так, чтобы доводить содержание диоксида углерода до приблизительно от 2 до 5 мол.%. Альтернативно, температура жидкого орошения может быть установлена так, чтобы доводить содержание диоксида углерода до трубопроводных спецификаций. Понятно, что температура будет установлена рабочим давлением. Более конкретно, температура устанавливается на основании оптимизации между рабочим давлением, количеством тарелок в верней дистилляционной секции или "охлаждающей секции" и количеством используемой жидкости орошения. В любом случае, сохраняется энергия, требуемая охлаждающей системой в противном случае для доведения верхнего метанового потока до СПГ спецификаций. В одном варианте осуществления способа 700 достаточное охлаждение обеспечивается на этапе 735, обеспечивая количество жидкости орошения, которое будет удалять диоксид углерода из верхнего метанового потока до процентного содержания приблизительно от 0,5 до 2,0 мол.%. Это составляет первую выбранную композицию. Затем пост-процессор удаляет диоксид углерода из верхнего метанового потока до уровня приблизительно от 50 до 200 ч./млн. Это составляет вторую выбранную композицию. В одном потенциальном варианте осуществления CFZ охлаждение минимизируется путем использования только достаточного жидкого орошения (генерируемого либо внешним охлаждением, либо с помощью процесса с открытым контуром, или от установки СПГ) для вымораживания входной концентрации CO2 до приблизительно 2% CO2 вверху секции распыления. Пост-процессор затем удаляет добавочный CO2 ниже 2%, например, до требований СПГ. Таким образом, этап охлаждения 735 обеспечивает замену охлаждающего оборудования молекулярно-ситовым оборудованием во время нормальной работы. Способ 700 затем включает в себя введение по меньшей мере части жидкого орошения обратно в криогенную дистилляционную колонну. Этот этап показан как блок 740 на фиг. 7 В. Этап 740 введения жидкого орошения в криогенную дистилляционную колонну представлен, например, линией 21 на фиг. 1 и линией 680 на фиг. 6. Целью введения жидкого орошения обратно в криогенную дистилляционную колонну является обеспечение очень холодной текучей среды внутри колонны, что заставляет диоксид углерода высаживаться из метанового пара в виде твердого вещества. В одном аспекте отделенное жидкое орошение 18 падает вниз сквозь тарелки и в конечном счете становится холодным жидким распылением 21. В другом варианте осуществления часть верхнего метанового потока, которая становится жидким орошением, может прямо вводиться в дистилляционную колонну, например, по линии жидкости 680 из газоперерабатывающей системы 600. В любом случае, жидкий поток 21 или 680 предпочтительно подвергается увеличению давления, например, посредством усилителя давления 176 на фиг. 1. В одном расположении жидкий метан повторно вводится в колонну 640 при температуре, например, приблизительно от -120 до -140F (от -84,4 до -95,5C). Однако рабочие условия, при которых кислотный газовый компонент исходного газового потока будет вымерзать, являются функцией ряда переменных. Они включают в себя, например, композицию исходного газового потока, химический характер замерзающего кислотного газового компонента и температуру и давление системы разделения. Преимущественно условия образования твердого вещества для любого замерзающего компонента исходной газовой смеси могут быть определены путем использования коммерчески доступного программного обеспечения для моделирования процесса. Затем часть верхнего метанового потока, которая не отделена в качестве жидкости орошения, проходит через некриогенный пост-процессор. Этот этап показан в блоке 745. Целью прохождения оставшегося верхнего метанового потока через слой молекулярного сита 674 является дополнительное удаление кислотных газов. Результатом является конечный газовый поток, который имеет меньше чем приблизительно 200 ч./млн диоксида углерода. Более предпочтительно содержание CO2 меньше чем приблизительно 50 ч./млн. В одном аспекте содержание диоксида углерода удовлетворяет трубопроводным спецификациям. Альтернативно, содержание диоксида углерода удовлетворяет стандартам сжиженного природного газа(СПГ), то есть меньше чем 50 ч./млн CO2 и меньше чем приблизительно 4 ч./млн H2S. СПГ может импортироваться из другой страны и выгружаться в Соединенных Штатах на импортном терминале. Некриогенный пост-процессор может быть одним из некоторого числа разных типов резервуаров или систем удаления кислотных газов для удаления диоксида углерода из метанового газового потока. Предпочтительно пре-процессор представляет собой слой молекулярного сита. Слой молекулярного сита может быть, например, 4-ангстремным или 5-ангстремным слоем, который способен удалять диоксид углерода из метанового газового потока. Однако пост-процессор может, альтернативно, быть одним или несколькими резервуарами, которые применяют химические растворители для извлечения кислотного газа из метанового потока. Альтернативно, пост-процессор может быть одним или несколькими резервуарами, которые приводят в контакт ионные жидкости или физические растворители с метаном для удаления остаточного диоксида углерода. Когда слой молекулярного сита используется в качестве пост-процессора, его предпочтительно вводят в систему удаления кислотного газа, по существу, в чистом состоянии. В ходе работы слой сита насыщается диоксидом углерода. Интересно, что в настоящем способе 700 слой молекулярного сита,который насытился диоксидом углерода, может служить в качестве второго слоя молекулярного сита,заменяя первый слой молекулярного сита из этапа 710. Это происходит, когда первый слой молекулярного сита насыщается водой. Стадия замены первого слоя молекулярного сита вторым слоем молекулярного сита демонстрируется в блоке 750. Следует заметить, что слой молекулярного сита будет предпочтительно замещать диоксид углерода путем адсорбции водяного пара. Это происходит потому, что вода более прочно адсорбируется, чем CO2. Следовательно, водяной пар будет замещать или десорбировать СО 2, который был ранее адсорбирован на слое молекулярного сита. Это значит, что второй слой молекулярного сита (насыщенный адсорбированным диоксидом углерода) может быть установлен в качестве первого слоя молекулярного сита в целях дегидратации без воздействия предварительного процесса регенерации. Второй слой молекулярного сита будет теперь дегидратировать исходный газовый поток и пропускать замещенный диоксид углерода в криогенную дистилляционную колонну. Так как количество CO2, выделяемого из второго слоя молекулярного сита в колонну, относительно невелико, дистилляционная колонна может перерабатывать его с небольшой потерей мощности или без потери. Таким образом, возникает неотъемлемый синергизм между слоями молекулярного сита выше по ходу и ниже по ходу со способом 700. Понятно, что первый слой молекулярного сита из этапа 710, который теперь насытился водой, необходимо подвергать специальному процессу регенерации. Этап регенерации показан в блоке 755 на фиг. 7 С. Регенерация гидратированного слоя сита обычно включает в себя направление нагретого газа сквозь слой молекулярного сита. Нагретый газ может быть метановым газом, например, из газового потока 676 для продажи или нагретым азотом. Затем слой молекулярного сита охлаждают и оставляют в стороне для позднейшего использования. В настоящем способе 700 позднейшее использование означает удаление CO2 ниже по ходу от дистилляционной колонны, например пост-процессор или слой доочистки. Способ 700 также может включать в себя этап замены второго слоя молекулярного сита (используемого ниже по ходу от криогенной дистилляционной колонны) третьим слоем молекулярного сита. Эта стадия показана блоком 760. Третий слой молекулярного сита может быть новым слоем сита. Альтернативно, третий слой молекулярного сита может быть слоем, который регенерировали после предыдущего использования, таким как регенерированный слой из этапа 755. Понятно, что скорость насыщения слоя молекулярного сита может быть иной, когда адсорбируется вода, чем когда адсорбируются кислотные газы, такие как CO2 и H2S. Скорость насыщения для любого слоя молекулярного сита зависит от таких переменных, как скорости потоков текучих сред, относительные концентрации примесей в текучих средах и емкость поглощения разных примесей. В настоящем контексте это означает, что первый слой молекулярного сита (который адсорбирует, главным образом,воду в связи с этапом 710) и второй слой молекулярного сита (который адсорбирует, главным образом,CO2 в связи с этапом 740) могут не насыщаться одновременно. Обычно емкость слоя молекулярного сита существенно ниже для H2S и CO2, чем для паров воды. Однако может присутствовать большее количество воды, чем СО 2, например. В любом случае, больше чем два слоя молекулярного сита должны быть включены в ротацию для непрерывной работы. В одном режиме работы три слоя молекулярного сита размещают для использования. Один слой будет в обслуживании дегидратации, другой будет в обслуживании доочистки и третий слой будет подвергаться регенерации. Регенерация будет, конечно, включать в себя нагрев с последующим охлаждением с последующим переводом в резервный режим. Этот способ использования трех слоев молекулярного сита преимущественно уподобляется известному применению минимум четырех слоев сита, где службы дегидратации и очистки остаются раздельными. Фиг. 7 С показывает этап 765 расположения регенерированного первого слоя молекулярного сита в ожидании замены третьего слоя молекулярного сита. Замена происходит, когда третий слой молекулярного сита насыщается диоксидом углерода или когда некоторый слой сита после замены насыщается диоксидом углерода. Альтернативно, замена может вызываться насыщением слоя сорбента в службе влагопоглощения. В одном аспекте четыре слоя молекулярного сита используются в ротации. Первый слой сита используется для службы удаления CO2 для верхнего метанового потока. Второй слой сита, который ранее был в службе удаления CO2 для верхнего газа, теперь находится в службе дегидратации для исходного газового потока. Третий слой сита регенерируется. Это обычно делают путем нагрева третьего слоя продувочным газом. Продувочный газ обычно проходит через третий слой в противоточном направлении при меньшем давлении. Четвертый слой находится в режиме охлаждения после регенерации. Охлаждение обычно выполняют путем протекания холодного газа сквозь четвертый слой. Четвертый слой молекулярного сита будет переключаться на службу удаления CO2, когда первый слой сита, по существу, насыщается диоксидом углерода. Таким образом продолжается ротация. В связи со способом 700 удаления кислотных газов из исходной газовой смеси могут быть установлены временные циклы, относящиеся к этапам 750 и 760. Оператор должен понимать, сколько времени требует слой твердого адсорбента выше по ходу от дистилляционной колонны для гидратации, то есть насыщения водой, и сколько времени требует слой твердого адсорбента ниже по ходу от дистилляционной колонны для насыщения CO2. Временные циклы следует устанавливать так, чтобы предотвращать"проскок" воды или кислотных газов из соответствующих слоев, даже в наиболее экстремальных условиях подачи. Это означает, что некоторая часть соответствующих слоев может не полностью использоваться для адсорбции. Также следует заметить, что такой материал, как цеолит, который используется в слоях твердого адсорбента, имеет тенденцию становиться менее активным или менее поглощающим со временем. Поглощающий материал будет более эффективным в начале рабочего периода ("SOR"), чем в конце рабочего периода ("EOR"). Это означает, что слои твердого адсорбента может быть необходимо циклически заменять чаще со временем. Таким образом, в одном аспекте временные циклы, касающиеся этапов 750 и 760, постепенно укорачиваются. Фиксированное регулирование временного цикла применимо независимо от того, является ли слой твердого адсорбента (такой как слой дегидратации 625) слоем молекулярного сита или слоем адсорбции с колебаниями давления. Понятно, что для процессов адсорбции с колебаниями давления временные циклы будут гораздо короче. Например, временные циклы для слоев адсорбции с колебаниями давления имеют тенденцию быть порядка минут или даже секунд, а не часов. Предпочтительно, когда временные циклы регулируются контрольной системой. Таким образом, в одном аспекте газоперерабатывающая система 600 включает в себя контрольную систему. Контрольная система может, например, контролировать регенерацию слоя твердого адсорбента 625, используемого для дегидратации, чтобы гарантировать, что заметный "проскок" воды не происходит во время процесса дегидратации. Контроль может быть сделан на основе фиксированных расписаний. Например, второй слой, описанный выше, может быть в службе дегидратации в течение 12 ч, тогда как третий слой подвергается регенерации в течение 6 ч. Четвертый слой может подвергаться охлаждению в течение 3 ч и затем помещаться в резерв на 3 ч. Регенерированный и охлажденный четвертый слой затем вводят в службу,тогда как первый слой выводят из службы и помещают в службу дегидратации. В одном аспекте контрольная система использует схему контроля "с прямой связью". Фиг. 8 А пред- 18021006 ставляет схематичное изображение контрольной системы 800 А, которая использует контроль с прямой связью. На фиг. 8 А виден слой твердого адсорбента 625 из системы 600, используемый для дегидратации. Кроме того, показан частично дегидратированный исходный газовый поток 624. Исходный газовый поток 624 направляется в слой 625 для дополнительной дегидратации. Исходный газовый поток 624 в конечном счете обрабатывается в системе удаления кислотных газов, имеющей криогенную дистилляционную колонну. Система удаления кислотных газов схематично показана под номером 850 принимающей дополнительно дегидратированный поток кислотного газа 820 из слоя 625. Контрольная система 800 А может, во-первых, включать в себя измеритель потока 805. Измеритель потока 805 располагается вдоль исходного газового потока 624. Измеритель потока 805 измеряет скорость потока исходного газового потока 624 в слой твердого адсорбента 625. Контрольная система 800 А также включает в себя измерительное устройство 810. Измерительное устройство 810 используется для измерения концентрации воды в исходном газовом потоке 624. Измерительное устройство 810 может быть, например, устройством, где изменение диэлектрической постоянной оксида алюминия измеряется как функция адсорбированной на нем влаги. Заметим, что измерительное устройство 810 является необязательным. В этом отношении концентрация водяного пара может быть известна непосредственно. Например, если содержание воды выше по ходу регулируется охлаждением газа, можно считать, что газ является насыщенным водой при температуре охладителя. Используя найденную скорость потока кислотного газа 624 и измеренную или известную концентрацию водяного пара, оператор может перемножить эти величины, получая полное количество примеси,т.е. воды, которое поступает в слой твердого адсорбента 625 за некоторый период времени. Сравнивая это количество с модельным вычислением емкости слоя (возможно принимая во внимание его возраст),можно определить более оптимальный временной цикл. Это можно делать автоматически, используя блок распределенного контроля 811. Альтернативное средство модификации цикла заключается в обеспечении измерительного устройства, способного к непрерывному измерению содержания воды возле стока из слоя твердого адсорбента 625, используемого для дегидратации. Контрольная система 800 В, которая использует такое измерительное устройство, представлена на фиг. 8 В. Контрольная система 800 В использует прямой контроль с обратной связью. Фиг. 8 В представляет схематичное изображение контрольной системы 800 В, которая использует прямой контроль с обратной связью. На фиг. 8 В снова виден слой твердого адсорбента 625 из системы 600, используемый для гидратации. Кроме того, показан частично дегидратированный исходный газовый поток 624. Исходный газовый поток 624 направляется в слой 625 для дополнительной дегидратации. Исходный газовый поток 624 в конечном счете обрабатывается (после дополнительной дегидратации с использованием слоя 625) в системе 850 удаления кислотных газов. В отличие от контрольной системы 800 А контрольная система 800 В не включает в себя измеритель потока. Однако контрольная система 800 В включает в себя измерительное устройство 810'. Вместо измерения концентрации кислотных газов в исходном газовом потоке 624 измерительное устройство 810' измеряет концентрацию воды над выходом слоя твердого адсорбента 625. Измерительное устройство 810' отбирает пробы из выходящего потока сразу внутри слоя 625 или непосредственно над выходом 815. Таким образом, адсорбент может быть переключен до того, как любая примесь, т.е. вода, проходит выход 815. Предпочтительно измерительное устройство 810' расположено примерно в футе (0,305 м) над дном слоя твердого адсорбента 625, чтобы избежать любой утечки водяного пара в обработанный газ. Измерения, выполняемые измерительным устройством 810', посылаются в контрольный блок 811. Контрольный блок 811 содержит центральное процессорное устройство или ЦПУ. ЦПУ может быть выполнено в виде любого типа процессора, включая коммерчески доступные микропроцессоры от таких компаний, как Intel, AMD, Motorola и NEC. Контрольный блок 811 получает измерения воды из измерительного устройства 810' и определяет, если слой 625 близок к проскоку воды. Если слой 625 близок к полной емкости, контрольный блок 811 посылает соответствующий сигнал, чтобы закончить цикл службы дегидратации для этого слоя. Следующий слой твердого адсорбента (то есть слой, который был в службе удаления кислотного газа) помещают затем в службу дегидратации. Контрольные системы 800 А и 800 В показаны в контексте измерения концентраций воды в связи с работой слоя твердого адсорбента, используемого для дегидратации. Такой слой твердого адсорбента используется в настоящем контексте выше по ходу от криогенной дистилляционной колонны. Однако контрольные системы 800 А и 800 В могут аналогично применяться в связи с работой слоя твердого адсорбента, используемого для удаления СО 2 из верхнего метанового потока. Такой слой твердого адсорбента используется в настоящем контексте ниже по ходу от криогенной дистилляционной колонны. Использование молекулярно-ситового оборудования ниже по ходу от криогенной дистилляционной колонны не только выгодно для снижения концентраций кислотных газов, чтобы удовлетворить СПГ спецификациям во время нормальной работы, но также может быть использовано для начального удаления CO2 из исходного газового потока во время "грязного" запуска. Такая система описывается более подробно в связи с патентом США 5062270. Фиг. 1 этого патента и сопровождающее текстовое описание упоминаются здесь и включены сюда посредством ссылки. При работе исходный газовый поток сначала подается в резервуар дегидратации (такой как резервуар дегидратации 620). До входа в дистилляционную колонну газовый поток проходит через охлаждающее оборудование, чтобы образовать охлажденный исходный газовый поток. Данное охлаждающее оборудование может содержать пропановый охладитель, который снижает температуру исходного газового потока до приблизительно -35F (-37,2C). Охлаждающее оборудование может также включать в себя охладитель входа, который дополнительно снижает температуру исходного газового потока приблизительно от -40 до -65F (от -40 до -53,8C). Охлаждающее оборудование может также включать в себя расширительное устройство для обеспечения еще большего охлаждения дегидратированного газа. Расширительное устройство может быть турбодетандером, гидравлической турбиной или клапаном ДжоуляТомпсона. Расширительное устройство дополнительно снижает температуру исходного газового потока приблизительно от -112 до -123F (от -80 до -86,1C). Дегидратированный и охлажденный газовый поток затем подается в дистилляционную колонну. Дистилляционная колонна работает, разделяя исходный газовый поток на верхний метановый поток и нижний поток кислотного газа, как обсуждается выше в связи с колонной 100 или 640. Весь поток орошения плюс продажный поток обрабатываются в слое молекулярного сита ниже по ходу. Дистилляционная колонна (такая как колонна 640), включая ректификационную секцию и встречный обменник (такой как встречный обменник 664), охлаждается путем работы охлаждающей системы выше по ходу от колонны, но не делая их такими холодными, чтобы образовывать твердый СО 2 на поверхностях теплопереноса внутри охладителей. Во время этого очищенный метановый газ выделяется из вершины колонны и затем течет через слой твердого адсорбента ниже по ходу от колонны для удаленияCO2. Данный газ затем возвращается к входу колонны, так что достигается постепенно меньшее содержание CO2. Когда содержание СО 2 становится достаточно низким, чтобы удовлетворять исходным трубопроводным спецификациям, охлаждение может регулироваться к нормальным уровням, так как не будет достаточного CO2 в газе для вымерзания на поверхностях теплопереноса в теплообменниках. Следует заметить, что никакой газ не поступает в трубопровод продажи (или СПГ установку), пока газ рециркулирует сквозь колонну. Доочистка удаляет достаточно CO2, чтобы входные трубы и внутренние компоненты дистилляционной колонны не накапливали твердые вещества во время позднейших стадий запуска. Другими словами, газ, содержащий высокие уровни СО 2, исходно не контактирует с холодными поверхностями внутри дистилляционной колонны или встречного обменника, где СО 2 может замерзать и вызывать закупоривание. Как только соответствующие профили концентрации СО 2 устанавливаются, очищенный газ может обрабатываться охлаждающей системой и слоем молекулярного сита ниже по ходу от колонны, причем существенная часть верхнего метанового продукта идет на продажу или в СПГ процесс. Также следует заметить, что во время запуска часть очищенного газа поставляется в дистилляционную колонну в виде жидкого орошения. Слой молекулярного сита удаляет CO2 до низких уровней, так что дистилляционная колонна не вымораживает существенного CO2, когда жидкое орошение распыляется вниз через секцию распыления. Хотя будет понятно, что описанные здесь изобретения хорошо вычислены, чтобы достигать выгод и преимуществ, установленных выше, будет ясно, что данные изобретения восприимчивы к модификации, вариации или изменению без отклонения от их сущности. Обеспечиваются улучшения в работе способа удаления кислотных газов, использующего зону контролируемого замерзания. Данные улучшения обеспечивают конструкцию для удаления CO2 до очень низких уровней в получаемом газе. Изобретения здесь также снижают требования охлаждения криогенных дистилляционных колонн, в то же время удовлетворяя СПГ спецификациям для максимального допустимого CO2. ФОРМУЛА ИЗОБРЕТЕНИЯ 1. Способ удаления кислотных газов из исходного газового потока, в котором подают исходный газовый поток в криогенную дистилляционную колонну, которая имеет нижнюю зону дистилляции и промежуточную зону контролируемого замерзания, в которую подают распылением холодную жидкость, образованную, главным образом, из метана; разделяют исходный газовый поток в криогенной дистилляционной колонне на верхний метановый поток и нижний поток кислотного газа; пропускают верхний метановый поток через охлаждающую систему ниже по ходу от криогенной дистилляционной колонны, причем охлаждающая система охлаждает верхний метановый поток; возвращают первую часть охлажденного верхнего метанового потока в криогенную дистилляционную колонну в виде жидкости орошения, служащей в качестве распыляемой холодной жидкости; пропускают вторую часть охлажденного верхнего метанового потока через слой твердого адсорбента ниже по ходу от криогенной дистилляционной колонны для удаления дополнительных кислотных газов и образования очищенного газового потока; конструируют охлаждающую систему таким образом, чтобы производить жидкость орошения в достаточном количестве для удаления кислотных газов из исходного газового потока в криогенной дистил- 20021006 ляционной колонне до первой выбранной композиции и подавать верхний метановый поток на слой твердого адсорбента ниже по ходу от криогенной дистилляционной колонны для удаления дополнительных кислотных газов до второй выбранной композиции; по меньшей мере, частично дегидратируют исходный газовый поток путем пропускания исходного газового потока через слой твердого адсорбента выше по ходу от криогенной дистилляционной колонны,где слой твердого адсорбента ниже по ходу от криогенной дистилляционной колонны и слой твердого адсорбента выше по ходу от криогенной дистилляционной колонны представляют собой слои молекулярного сита; насыщают слой выше по ходу от криогенной дистилляционной колонны адсорбированной водой и заменяют его слоем молекулярного сита, который насытился кислотным газом при использовании в качестве слоя твердого адсорбента ниже по ходу от криогенной дистилляционной колонны. 2. Способ по п.1, где кислотные газы содержат диоксид углерода; количество генерируемого жидкого орошения является достаточным для удаления диоксида углерода из исходного газового потока до первой композиции приблизительно от 1 до 4 мол.%; слой твердого адсорбента ниже по ходу от криогенной дистилляционной колонны удаляет дополнительный диоксид углерода из верхнего метанового потока до второй композиции приблизительно от 0,2 до 3 мол.%. 3. Способ по п.1, где количество генерируемого жидкого орошения является достаточным для удаления диоксида углерода из исходного газового потока до первой композиции, которая соответствует спецификациям трубопровода; слой твердого адсорбента ниже по ходу от криогенной дистилляционной колонны удаляет диоксид углерода из верхнего метанового потока до второй выбранной композиции кислотного газа, которая удовлетворяет спецификациям СПГ. 4. Способ по п.3, где спецификации трубопровода требуют содержания диоксида углерода меньше чем приблизительно 3 мол.%. 5. Способ по п.3, где спецификации СПГ требуют содержания диоксида углерода меньше чем приблизительно 50 ч./млн. 6. Способ по п.3, где слой твердого адсорбента ниже по ходу от криогенной дистилляционной колонны удаляет диоксид углерода из верхнего метанового потока до содержания меньше чем приблизительно 100 ч./млн. 7. Способ по п.2, где кислотные газы дополнительно содержат сероводород и слой твердого адсорбента ниже по ходу от криогенной дистилляционной колонны удаляет сероводород из верхнего метанового потока до содержания менее чем приблизительно 10 ч./млн. 8. Способ по п.7, где слой молекулярного сита удаляет сероводород из верхнего метанового потока до содержания менее чем приблизительно 4 ч./млн. 9. Способ по п.2, где дополнительно отделяют диоксид углерода от метана, используя (i) ионные жидкости, (ii) физические растворители или (iii) химические растворители, в одном или нескольких резервуарах ниже по ходу от криогенной дистилляционной колонны. 10. Способ по п.1, где дополнительно заменяют слой твердого адсорбента выше по ходу от криогенной дистилляционной колонны, когда слой молекулярного сита выше по ходу от криогенной дистилляционной колонны становится, по существу, насыщенным водой. 11. Способ по п.1, где дополнительно регенерируют слой молекулярного сита выше по ходу от криогенной дистилляционной колонны после того, как данный слой молекулярного сита выше по ходу от криогенной дистилляционной колонны становится, по существу, насыщенным водой. 12. Способ по п.11, где регенерируют слой молекулярного сита выше по ходу от криогенной дистилляционной колонны, используя адсорбцию с термическими колебаниями или адсорбцию с колебаниями давления. 13. Способ по п.11, где дополнительно заменяют слой молекулярного сита ниже по ходу от криогенной дистилляционной колонны, когда слой молекулярного сита ниже по ходу от криогенной дистилляционной колонны становится, по существу, насыщенным диоксидом углерода, регенерированным слоем молекулярного сита, ранее находившимся в обслуживании дегидратации выше по ходу от криогенной дистилляционной колонны. 14. Способ по п.2, где дополнительно вводят по меньшей мере часть нижнего потока кислотного газа в подземную формацию по меньшей мере через одну скважину ввода кислотного газа. 15. Способ удаления кислотных газов из исходного газового потока, где пропускают исходный газовый поток через первый слой молекулярного сита, при этом получают входящий газовый поток, который является, по меньшей мере, частично дегидратированным; направляют входящий газовый поток в криогенную дистилляционную колонну, где данная колонна имеет нижнюю дистилляционную зону и промежуточную зону контролируемого замерзания, в которую подают распылением холодную жидкость, образованную, главным образом, из метана; выводят верхний метановый поток из криогенной дистилляционной колонны; пропускают верхний метановый поток через второй слой молекулярного сита ниже по ходу от криогенной дистилляционной колонны, удаляя дополнительные кислотные газы и получая очищенный газовый поток; удаляют первый слой молекулярного сита выше по ходу от криогенной дистилляционной колонны,когда данный слой молекулярного сита выше по ходу от криогенной дистилляционной колонны становится, по существу, насыщенным водой; заменяют слой молекулярного сита выше по ходу от криогенной дистилляционной колонны слоем молекулярного сита, который ранее, по существу, насытился диоксидом углерода в результате использования в качестве второго слоя молекулярного сита ниже по ходу от криогенной дистилляционной колонны; регенерируют слой молекулярного сита выше по ходу от криогенной дистилляционной колонны после того, как данный слой молекулярного сита выше по ходу от криогенной дистилляционной колонны становится, по существу, насыщенным водой. 16. Способ по п.15, где дополнительно пропускают верхний метановый поток через охлаждающую систему ниже по ходу от криогенной дистилляционной колонны, чтобы охладить верхний метановый поток перед тем, как верхний метановый поток пропускают через второй слой молекулярного сита. 17. Способ по п.15, где дополнительно возвращают часть охлажденного верхнего метанового потока в криогенную дистилляционную колонну в виде жидкости орошения. 18. Способ по п.15, где охлаждающая система организована так, чтобы производить жидкое орошение в достаточном количестве для удаления кислотных газов из входящего газового потока в криогенной дистилляционной колонне до первой выбранной композиции и подавать верхний метановый поток в слой молекулярного сита ниже по ходу от криогенной дистилляционной колонны для удаления дополнительных кислотных газов до второй выбранной композиции. 19. Способ по п.18, где кислотные газы содержат диоксид углерода; количество генерируемого жидкого орошения является достаточным для удаления диоксида углерода из входящего газового потока до первой композиции приблизительно от 1 до 4 мол.%; слой молекулярного сита ниже по ходу от криогенной дистилляционной колонны удаляет дополнительный диоксид углерода из верхнего метанового потока до второй композиции приблизительно от 0,2 до 3 мол.%. 20. Способ по п.18, где количество генерируемого жидкого орошения является достаточным для удаления диоксида углерода из входящего газового потока до первой композиции, которая удовлетворяет спецификациям трубопровода; слой молекулярного сита ниже по ходу от криогенной дистилляционной колонны удаляет диоксид углерода из верхнего метанового потока до второй выбранной композиции кислотного газа, которая удовлетворяет спецификациям СПГ. 21. Способ по п.20, где трубопроводные спецификации требуют содержания диоксида углерода меньше чем приблизительно 3 мол.%. 22. Способ по п.21, где СПГ спецификации требуют содержания диоксида углерода меньше чем приблизительно 100 ч./млн. 23. Способ по п.17, где слой молекулярного сита ниже по ходу от криогенной дистилляционной колонны удаляет диоксид углерода из верхнего метанового потока до содержания меньше чем приблизительно 50 ч./млн. 24. Способ по п.15, где кислотные газы дополнительно содержат сероводород и слой молекулярного сита ниже по ходу от криогенной дистилляционной колонны удаляет сероводород из верхнего метанового потока до композиции менее чем приблизительно 10 ч./млн. 25. Способ по п.15, где дополнительно заменяют слой молекулярного сита ниже по ходу от криогенной дистилляционной колонны, когда данный слой молекулярного сита ниже по ходу от криогенной дистилляционной колонны становится, по существу, насыщенным диоксидом углерода, регенерированным слоем молекулярного сита, который ранее находился в работе выше по ходу от криогенной дистилляционной колонны. 26. Способ по п.22, где кислотные газы содержат диоксид углерода; исходный газовый поток содержит азот,в данном способе дополнительно пропускают верхний метановый поток через третий слой молекулярного сита ниже по ходу от криогенной дистилляционной колонны, удаляя азот из верхнего метанового потока ниже содержания приблизительно 3 мол.%.
МПК / Метки
Метки: кислотных, потока, удаления, газа, газов, способ, углеводородного
Код ссылки
<a href="https://eas.patents.su/27-21006-sposob-udaleniya-kislotnyh-gazov-iz-potoka-uglevodorodnogo-gaza.html" rel="bookmark" title="База патентов Евразийского Союза">Способ удаления кислотных газов из потока углеводородного газа</a>
Предыдущий патент: Система отделения катализатора
Следующий патент: Способ ферментативного превращения углеродсодержащего сырья
Случайный патент: Вагонные весы