Частицы фосфата, полифосфата и метафосфата алюминия, их использование в качестве пигментов в красках и способ их получения
Формула / Реферат
1. Композиция фосфата алюминия для покрытий, содержащая фосфат алюминия, полифосфат алюминия, метафосфат алюминия или их смесь, и компонент, выбранный из солей натрия, калия и аммония, где композиция включает частицы, которые имеют среднее значение радиуса частицы от 10 до 40 нм, и, по меньшей мере, некоторые из частиц имеют в среднем одну или более закрытых полостей на частицу, и композиция дополнительно характеризуется тем, что
(a) обладает диспергируемостью в воде по меньшей мере 0,025 г на 1,0 г воды,
(b) соотношение Р/Аl составляет от 1,1 до 1,5, соотношение P/Na составляет от 0,93 до 4,53 и соотношение Al/Na составляет 0,75 до 3,62.
2. Композиция по п.1, где композиция выбрана из группы композиций, характеризующихся следующими параметрами:
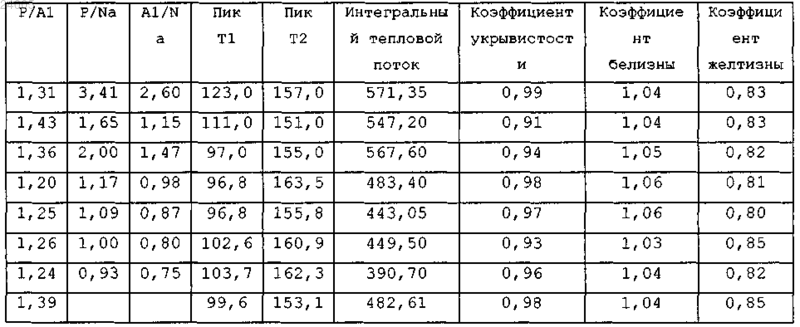
3. Композиция по п.1, где дифференциальная сканирующая калориметрия не показывает пика между 335 и 345°С.
4. Композиция по п.1, где композиция, будучи в виде суспензии, имеет рН в диапазоне примерно от 3,0 до 7,5.
5. Композиция по п.1, где композицию получают контактом комбинации веществ, включающих фосфорную кислоту, сульфат алюминия и щелочной раствор.
6. Композиция по п.1, где средний радиус отдельной частицы составляет от 10 до 40 нм.
7. Краска, лак, масляный лак, печатная краска или пластмасса, включающие композицию по любому из пп.1-6 в качестве ингредиента.
8. Краска, содержащая композицию фосфата алюминия по любому из пп.1-6, растворитель, связующий полимер.
9. Краска по п.8, где указанная краска также содержит диоксид титана и необязательные добавки, включающие загуститель, пластификатор, противопенная добавка, наполнитель, регулятор рН, тонирующий цвет и биоцид.
10. Краска по п.8, где указанный растворитель содержит воду.
11. Краска по п.8, где указанный растворитель содержит полярный растворитель.
12. Краска по п.8, где указанный растворитель содержит неполярный растворитель.
13. Краска по п.8, где указанный растворитель содержит органический растворитель.
14. Способ получения краски, включающий следующие стадии: объединение растворителя и композиции по любому из пп.1-6.
15. Способ получения краски по п.14, где способ дополнительно включает следующие стадии:
одновременное смешивание фосфорной кислоты, сульфата алюминия и гидроксида натрия и обеспечение взаимодействия смешанных материалов друг с другом в течение приблизительно 30 мин с образованием осадка;
высушивание осадка при температуре в диапазоне от комнатной температуры до 135°С, предпочтительно между 40 и 130°С с образованием композиции аморфного фосфата алюминия по пп.1-6, содержащей частицы, имеющие одну или более закрытых полостей на частицу, обладающие диспергируемостью в воде по меньшей мере 0,025 г на 1,0 г воды, и соотношением Р/Аl от 1,1 до 1,5, соотношением P/Na от 0,93 до 4,53 и соотношением Al/Na от 0,75 до 3,62, и добавление связующего полимера.
Текст
interface science. 1996, vol. 178, 1, стр. 93-103,реферат [он-лайн] [Найдено 27.07.2007]. Найдено из Интернет URL: http://www.cheric.org/research/ Композиция фосфата алюминия, включающая фосфат алюминия, полифосфат алюминия,метафосфат алюминия или их смесь. Композиция может характеризоваться тем, что, когда она имеет порошкообразную форму, содержит частицы, где некоторые из частиц имеют по меньшей мере одну или более полостей на частицу. Кроме того, композиция характеризуется тем, что показывает два эндотермических пика в дифференциальной сканирующей калориметрии между примерно 90 и примерно 250 С. Композиция также характеризуется тем, что, когда имеет порошкообразную форму, обладает диспергируемостью по меньшей мере 0,025 г на 1,0 г воды. Композицию получают способом, включающим контакт фосфорной кислоты с сульфатом алюминия и щелочным раствором с получением основного продукта, представляющего собой фосфат алюминия; и необязательно кальцинирование основного продукта, представляющего собой фосфат, полифосфат или метафосфат алюминия, при повышенной температуре. Композиция применима в красках и в качестве заместителя диоксида титана.(71)(73) Заявитель и патентовладелец: БУНГЕ ЭЙМОРФИК СОЛЮШИНЗ ЭлЭлСи (US); УНИВЕРСИДАДИ ЭСТАДУАЛ ДИ КАМПИНАС (BR) Предшествующие родственные заявки Данная заявка является частичным продолжением заявки 11/215 312, поданной в США 30 августа 2005 года, которая заявляет приоритет заявкиPI0403713-8, поданной в Бразилии 30 августа 2004 года. Описание как заявки США 11/215 312, так и заявки БразилииPI0403713-8, включено сюда посредством ссылки во всей полноте. Государственно финансируемый научный отчет - отсутствует. Ссылка на микрофишное приложение - отсутствует. Область техники, к которой относится изобретение Изобретение относится к способам получения частиц фосфата алюминия, метафосфата алюминия,ортофосфата алюминия и полифосфата алюминия. Данное изобретение в дальнейшем относится к использованию таких частиц в качестве пигментов в красках и других областях использования. Уровень техники настоящего изобретения Диоксид титана является наиболее распространенным белым пигментом из-за своей сильной способности рассеивать в обратном направлении видимый свет, которая, в свою очередь, зависит от его коэффициента преломления. Был проведен поиск заменителей диоксида титана, однако, коэффициенты преломления анатаза и рутила - обоих форм данного оксида, намного выше, чем коэффициенты преломления любого другого белого порошка, по структурным причинам. Пигменты диоксида титана являются нерастворимыми в растворителях покрытий, в которых они диспергированы. Характерные свойства таких пигментов диоксида титана, включая его физические и химические свойства, определяются размером частиц пигмента и химическим составом его поверхности. Диоксид титана является коммерчески доступным в двух кристаллических структурах: анатаза и рутила. Пигменты диоксида титана, представляющие собой рутил, являются предпочтительными, поскольку они рассеивают свет более эффективно и являются более стабильными и долговечными, чем пигменты анатаза. Диоксид титана рассеивает свет очень эффективно благодаря своему большому коэффициенту преломления. Декоративные и функциональные свойства диоксида титана из-за его способностей рассеивать свет делают его весьма желанным пигментом. Однако известно, что диоксид титана является дорогим пигментом для производства. Таким образом, существует потребность в более доступном заменителе диоксида титана в качестве пигмента. Как отмечалось, желанным свойством диоксида титана является его большая способность к рассеиванию видимого света. Данное свойство является результатом его высокого коэффициента преломления,вместе с отсутствием электронных переходов в видимой части спектра. Было предпринято много попыток замены диоксида титана, частично или полностью, при его использовании в качестве пигмента. Однако, коэффициенты преломления двух его форм, анатаза и рутила, трудно получить с другими белыми твердыми веществами (Handbook of Chemistry and Physics, CRC Press, 57th ed., 1983). Таким образом, поиск новых белых пигментов ведет к поиску систем с другим механизмом рассеяния света. Многофазная среда, обладающая различными коэффициентами преломления, может действовать как рассеиватель света. Имеющиеся в настоящее время варианты способов производства пигментов или красок, которые приводят к пленке, содержащей "поры" во внутренней части частиц или между частицами и смолой,также достаточно ограничены. Некоторые методы получения полых частиц были описаны в литературе,однако большинство методов включают производство шаровидных полых и полимерных частиц полимеризацией в эмульсии. Примером является работа N. Kawahashi and E. Matijevic (Preparation of HollowSpherical Particle of Itrium Compounds, J. Colloid and Interface Science 143(1), 103, 1991) по нанесению покрытия полистирольного латекса с основным карбонатом иттрия и последующей прокалкой на воздухе при высоких температурах, с получением полых частиц соединений иттрия. Получение полых частиц метафосфатов алюминия химической реакцией между метафосфатом натрия и сульфатом алюминия, вслед за которой следует термическая обработка, было описано Galembecket al. в патенте Бразилии BR 9104581. Данная работа ссылается на образование полых частиц фосфата алюминия, синтезированных из фосфата натрия и нитрата алюминия. Как отмечалось, данные два пигмента, фосфат и метафосфат алюминия, могут быть использованы для замены большой части TiO2 в красках на основе ПВА латекса или акриловых эмульсий. Патент Бразилии BR 9500522-6 Galembeck et al. описывает способ получения белого пигмента из двойного метафосфата алюминия и кальция, полученного непосредственно химической реакцией между частицами метафосфата алюминия и карбоната кальция в полимерной латексной эмульсионного типа водной среде. Данный патент расширяет предыдущие результаты до солей кальция, которые, с точки зрения окружающей среды, являются преимущественными вследствие их полной нетоксичности. Несколько публикаций обсуждают синтез алюминий-фосфатных материалов преимущественно для использования в качестве носителя катализаторов, включая кристаллические и аморфные формы. Многие из данных способов дают высокопористые и кристаллические формы и несколько - термически стабильные аморфные композиции. Примеры таких материалов описаны в патентах США номера: 3 943 231; 4 289 863; 5 030 431; 5 292 701; 5 496 529; 5 552 361; 5 698 758; 5 707 442; 6 022 513 и 6 461 415. Однако существует потребность в фосфате алюминия с полыми частицами, особенно в порошке, который может быть относительно легко произведен. Сущность изобретения Предметом настоящего изобретения является композиция фосфата алюминия, включающая фосфат алюминия, полифосфат алюминия, метафосфат алюминия или их смесь. Композиция, в порошкообразной форме, может характеризоваться тем, что имеет частицы, некоторые из которых имеют по меньшей мере одну или более полостей на частицу. Кроме того, композиция характеризуется тем, что показывает два эндотермических пика по данным дифференциальной сканирующей калориметрии примерно между 90 и 250 С. Композиция также характеризуется тем, что, когда она имеет порошкообразную форму, обладает дисперсностью по меньшей мере 0,025 г на 1,0 г воды. Краткое описание чертежей Фиг. 1 а представляет собой изображение вещества по изобретению, полученное просвечивающим электронным микроскопом с использованием энергетического фильтра. Фиг. 1b представляет собой изображение вещества по изобретению, полученное просвечивающим электронным микроскопом в режиме светлого поля. Фиг. 2 а представляет собой изображение вещества по изобретению, полученное просвечивающим электронным микроскопом с использованием энергетического фильтра. Фиг. 2b представляет собой изображение вещества по изобретению, полученное просвечивающим электронным микроскопом в режиме светлого поля. Фиг. 3 а представляет собой изображение, полученное просвечивающим электронным микроскопом в режиме светлого поля, демонстрирующее продукт на основе фосфата алюминия, в котором отсутствуют полости. Фиг. 3b представляет собой изображение, полученное просвечивающим электронным микроскопом в режиме светлого поля, демонстрирующее продукт на основе фосфата алюминия, в котором отсутствуют полости. Фиг. 4 представляет собой термограмму вещества по изобретению, полученную с помощью дифференциального сканирующего калориметра. Фиг. 5 представляет собой термограмму вещества по изобретению, полученную с помощью дифференциального сканирующего калориметра. Фиг. 6 представляет собой термограмму вещества по изобретению, полученную с помощью дифференциального сканирующего калориметра. Фиг. 7 представляет собой термограмму вещества по изобретению, полученную с помощью дифференциального сканирующего калориметра. Описание вариантов осуществления настоящего изобретения В следующем ниже описании все описанные числа являются приблизительными величинами, независимо от того, используется ли в связи с этим слово "примерно" или "приблизительно". Они могут отличаться на 1, 2, 5% или иногда от 10 до 20%. Всякий раз, когда описан числовой диапазон с нижним пределом RL и верхним пределом RU, любое число, попадающее в диапазон, является конкретно описанным. В частности, следующие числа в диапазоне являются конкретно описанными: R= RL+k (RU- RL),где к является переменной, находящейся в диапазоне от 1 до 100% с 1% возрастания, т.е. k равно 1, 2, 3,4, 5, , 50, 51, 52, , 95, 96, 97, 98, 99 или 100%. Более того, любой числовой ряд, определенный двумя числами R, как указано выше, также является конкретно описанным. Изобретение, описанное в данном патенте, относится к композиции фосфата алюминия, включающей фосфат алюминия, полифосфат алюминия, метафосфат алюминия или их смесь. Используемые здесь термины "фосфат алюминия" и "композиция фосфата алюминия" предназначены для включения как фосфата алюминия, так и полифосфата алюминия, метафосфата алюминия и их смесей. Композиция фосфата алюминия характеризуется тем, что, когда она в порошкообразной форме, имеет дисперсность по меньшей мере 0,025 г на 1,0 г воды. Предпочтительно композиция характеризуется тем, что, когда она в порошкообразной форме, имеет дисперсность по меньшей мере 0,035 г на 1,0 г воды. Еще более предпочтительно композиция характеризуется тем, что, когда она в порошкообразной форме, имеет дисперсность по меньшей мере 0,05 г на 1,0 г воды. Новые полые частицы фосфата алюминия, как правило, могут характеризоваться несколькими различными характеристиками. Например, фосфат алюминия, когда он приготовлен в порошкообразной форме, включает частицы, часть из которых имеет по меньшей мере одну полость на частицу в среднем. Кроме того, когда фосфат, полифосфат и/или метафосфат алюминия имеет порошкообразную форму,образцы, подвергнутые тесту дифференциальной сканирующей калориметрии, будут демонстрировать два отчетливых эндотермических пика. Причем указанные пики находятся, как правило, между 90 С и 250 С. Предпочтительно первый пик находится примерно между температурами 90 и 120 С, более предпочтительно между примерно 96 и 116 С, а второй пик находится примерно между температурами 149 и 189 С, более предпочтительно между температурами 149 и 164 С. Еще более предпочтительно два пика находятся примерно при 106 С и примерно 164 С. Кроме того, фосфат алюминия типично показывает превосходные характеристики диспергируемости, описанные здесь. Композиция по изобретению состоит из некристаллического твердого вещества, в противоположность огромному большинству неорганических промышленных химикатов, включая продукты, продаваемые в настоящее время как кристаллические фосфаты и полифосфаты алюминия. CAS номер, наиболее часто даваемый для продуктов фосфата алюминия, представляет собой 7784-30-7, но он относится к стехиометрическому, кристаллическому веществу. Изобретение, описанное в данном патенте, далее относится к новому фосфату алюминия, полифосфату алюминия, метафосфату алюминия или их смеси. Аморфные (т.е., некристаллические) твердые вещества демонстрируют отличия от своих кристаллических двойников одинакового состава, и такие отличия могут давать выгодные свойства. Например,такие отличия могут включать: (i) некристаллические твердые вещества не рассеивают рентгеновские лучи при четко определенных углах, но могут давать взамен широкое рассеяние гало; (ii) некристаллические твердые вещества не имеют хорошо определенной стехиометрии, таким образом, они охватывают широкий диапазон химических составов; (iii) разнообразие химической композиции включает возможность внедрения ионных компонентов, отличных от ионов алюминия и фосфата; (iv) поскольку аморфные твердые вещества являются термодинамически метастабильными, они могут демонстрировать тенденцию подвергаться спонтанным морфологическим, химическим и структурным изменениям; и (v) химический состав поверхности и объема кристаллической частицы является высоко однородным, в то время как химический состав поверхности и объема аморфной частицы может показывать большие или малые отличия, как резкие, так и постепенные. Кроме того, в то время как частицы кристаллических веществ имеют тенденцию расти по хорошо известному механизму созревания Оствальда, некристаллические частицы могут расширяться или разбухать и сжиматься (сокращаться) при адсорбции или десорбции воды, образуя геле-подобный или пластичный материал, который легко деформируется под воздействием сдвига, сжатия или капиллярных сил. Как было указано, один аспект описанного здесь изобретения представляет собой синтетический способ, который производит некристаллические частицы фосфата алюминия наноразмера с уникальными свойствами. Когда дисперсию таких частиц сушат на воздухе при комнатной температуре или до 120 С, образуются наночастицы, которые имеют структуру ядра и оболочки. Такие частицы можно наблюдать аналитическим электронным микроскопом. Более того, данные частицы содержат много полостей, распределенных в виде закрытых пор внутри частиц. Ядра частиц являются более пластичными, чем соответствующие оболочки данных частиц. Данное явление подтверждается ростом полостей при нагревании, в то время как периметр оболочек остается, по существу, неизменным. Другой аспект данного изобретения состоит в разработке нового продукта и способа получения полых частиц фосфата алюминия, полифосфата алюминия и метафосфата алюминия (и их смесей) для использования в качестве пигмента. Более конкретно, данный аспект изобретения относится к новому пигменту, полученному реакцией фосфорной кислоты, в частности, фосфорной кислоты промышленной чистоты, с сульфатом алюминия в условиях контролируемых рН и температуры. Реагент может быть фильтрован, диспергирован, высушен, прокален и измельчен для использования в качестве пигмента в красках, включая акриловые краски для внутренних работ. Данные пигменты могут быть использованы в других продуктах и областях применения, таких как краски, пластики, лаки, печатные краски и т.д. Как описано здесь, многие исследователи стремились образовать полости внутри частиц, но это трудно достижимо, поскольку большинство твердых веществ образуют открытые поры при сушке, и такие открытые поры не вносят вклад в укрывистость краски или кроющую способность. Полые частицы,образованные фосфатом, полифосфатом или метафосфатом алюминия, дают полезные свойства, как физические, так и химические, которые можно использовать во многих различных областях использования. Один аспект описанного здесь изобретения заключается в получении фосфата, полифосфата или метафосфата алюминия (или их комбинаций) с такими полыми частицами, чтобы воспользоваться преимуществами таких полезных свойств. Термин "полость", на который здесь ссылаются, как правило, является синонимом термина "полая частица", а также описывается здесь как "закрытая полость". Полость (или закрытая полость или полая частица) является частью структуры ядра и оболочки смеси фосфата алюминия. Образец композиции по изобретению, исследованный просвечивающим электронным микроскопом с использованием энергетического фильтра, показан на фиг. 1 а и 2 а. Образец композиции по изобретению, исследованный просвечивающим электронным микроскопом в режиме светлого поля, показан на фиг. 1b и 2b. Образец демонстрирует полости, содержащиеся в композиции по изобретению. По контрасту фиг. 3 а и 3b представляют собой изображение в режиме светлого поля, полученное просвечивающим электронным микроскопом,образца фосфата алюминия, не содержащего пустоты. Светорассеивающая способность образцов на фиг. 1a, 1b, 2 а и 2b превосходит светорассеивающую способность образца на фиг. 3 а и 3b. Полости можно наблюдать и/или характеризовать, используя либо просвечивающие, либо сканирующие электронные микроскопы ("ПЭМ" или "СЭМ"). Использование ПЭМ и СЭМ хорошо известно специалистам в данной области. Как правило, оптическая микроскопия ограничивается длиной волной света к разрешению в диапазоне сотни и обычно сотен нанометров. ПЭМ и СЭМ не имеют данного ограничения и способны достигать значительно более высокого разрешения в диапазоне нескольких нанометров. Оптический микроскоп использует оптические линзы для фокусировки волн света, изгибая их, в то время как электронный микроскоп использует электромагнитные линзы для фокусировки пучка электронов, изгибая их. Пучок электронов дает большие преимущества по сравнению с пучками света, как в контроле уровней увеличения, так и в четкости изображения, которое можно получить. Сканирующие электронные микроскопы дополняют просвечивающие электронные микроскопы тем, что они предлагают инструмент для получения трехмерного изображения поверхности образца. Как правило, пучок электронов получают в электронном микроскопе, нагревая нить накала. Нить накала можно изготовить из различных металлических материалов, включая, но не ограничиваясь этим,вольфрам или гексаборид лантана. Данная металлическая нить накала работает как катод, и когда прикладывают напряжение, температура нити возрастает. Анод, который является положительным относительно нити накала, формирует мощную силу притяжения для электронов. Электроны притягиваются от катода к аноду, причем некоторая часть пролетает мимо анода, формируя пучок электронов, который используется при формировании изображения образца. Данный пучок электронов затем концентрируют и фокусируют на образце, используя электромагнитные линзы. В СЭМ катушки сканирования создают магнитное поле, которое можно изменять, чтобы направлять пучок назад и вперед через образец контролируемым образом. Такое же изменяющееся напряжение, которое создает образ на образце, прикладывают к электронно лучевой трубке. Это создает световой образ на поверхности электронно-лучевой трубки, который аналогичен рельефу на образце. Как указано, материал по изобретению имеет новые характеристики, которые отражены в тестах,проведенных на дифференциальном сканирующем калориметре. Кратко, дифференциальная сканирующая калориметрия ("ДСК") представляет собой аналитический метод, в котором тепловой поток, связанный с химическими, физическими или кристаллографическими превращениями в веществе измеряют в виде функции температуры и времени (и, возможно, давления). Дифференциальные сканирующие калориметры ("ДСК") измеряют тепловой поток к образцу, по мере того как температуру меняют контролируемым образом. Существуют два основных типа ДСК - теплового потока и компенсации мощности. ДСК теплового потока включают сенсор для измерения теплового потока к образцу, который необходимо анализировать. Сенсор имеет положение образца и положение эталона. Сенсор установлен в печи,температуру которой меняют динамически в соответствии с желаемой температурной программой. По мере того, как печь нагревают или охлаждают, измеряют разницу температур между образцовым и эталонным положениями сенсора. Предполагается, что данная разница температур пропорциональна тепловому потоку к образцу. ДСК с компенсацией мощности включают держатель образца и эталона, установленные в камере постоянной температуры. Каждый держатель имеет нагреватель и сенсор температуры. Среднее значение температур держателя образца и эталона используют для контроля температуры, которая следует желаемой температурной программе. Кроме того, дифференциальную мощность, пропорциональную разнице температур между держателями, добавляют к средней мощности для держателя образца и вычитают из средней мощности для держателя эталона, снижая температурную разницу между держателями образца и эталона до нуля. Предполагается, что дифференциальная мощность пропорциональна тепловому потоку для образца и получается измерением разницы температуры между держателями образца и эталона. В коммерческих ДСК с компенсацией мощности разница между температурой образца и эталона, как правило, не равна нуля, так как пропорциональный контроллер используют для контроля дифференциальной мощности. Образец, который надо анализировать, загружают в чашку и помещают в положение образца ДСК. Инертное эталонное вещество можно загрузить в чашку и поместить в положение эталона ДСК, хотя обычно чашка эталона является пустой. Программа температуры для обычной ДСК типично включает комбинации линейно-возрастающих температурных участков и участков постоянной температуры. Экспериментальный результат представляет собой зависимость теплового потока образца от температуры или времени. Сигнал теплового потока представляет собой результат теплового потока к образцу или от образца вследствие его удельной теплоемкости и в результате превращений, происходящих в образце. В течение динамической части эксперимента ДСК создают разницу температур между положениями образца и эталона ДСК. В тепловом потоке ДСК разница температур возникает из комбинации трех различных тепловых потоков: разницы между тепловыми потоками образца и эталона, разницы между тепловыми потоками сенсора образца и эталона и разницей между тепловыми потоками чашки образца и эталона. В ДСК с компенсацией мощности разница температур возникает из комбинации трех различных тепловых потоков плюс дифференциальной мощности, подаваемой к держателям образца: разницы между тепловыми потоками образца и эталона, разницы между тепловыми потоками держателя образца и эталона и разницы между тепловыми потоками чашки образца и эталона. Разница тепловых потоков между образцом и эталоном состоит из теплового потока вследствие разницы теплоемкости между образцом и эталоном или теплового потока превращения. Разница теплового потока между секциями образца и эталона ДСК является результатом термического сопротивления и разбаланса емкостей в сенсоре или между держателями и разницы в скорости нагрева, которая имеет место между секциями образца и эталона ДСК в течение превращения. Аналогичным образом, разница тепловых потоков между чашками образца и эталона является результатом разницы масс между чашками и разницы в скорости нагрева,-4 024005 которая имеет место в течение превращения образца. В традиционной ДСК теплового потока разбаланс сенсоров и разбаланс чашек, как предполагают,является незначительным, и различия в скоростях нагревания не учитываются. В традиционной ДСК с компенсацией мощности разбаланс держателей и разбаланс чашек, как предполагают, является незначительным, и различия в скоростях нагревания не учитываются. Когда предположения баланса удовлетворяются, и скорость нагревания образца является такой же, как и скорость запрограммированного нагрева,разница температур пропорциональна тепловому потоку образца и дифференциальная температура дает точную меру теплового потока образца. Температурный поток образца пропорционален только измеренной разнице температур между образцом и эталоном, когда скорости нагрева образца и эталона являются идентичными, сенсор, предпочтительно, является симметричным, и массы чашек являются идентичными. Пропорциональность теплового потока образца разнице температур для сбалансированных сенсора и чашек имеется только в течение частей эксперимента, когда прибор работает при постоянной скорости нагрева, образец меняет температуру с той же скоростью, что и прибор, и нет превращений, происходящих в образце. В течение превращения тепловой поток к образцу увеличивается или снижается от допереходного значения, в зависимости от того, является ли переход эндотермическим или экзотермическим, и является ли ДСК нагреваемой или охлаждаемой. Изменение теплового потока образца вызывает то, что скорость нагревания образца отличается от скорости ДСК и, как следствие, скорости нагрева чашки с образцом и сенсора образца становятся отличными от программируемой скорости нагрева. Различные образцы продукта, представляющего собой фосфат, полифосфат и/или метафосфат алюминия, тестировали на ДСК. Приведенные в настоящем описании результаты ДСК получены с использованием приборов ТА модели Q Series 600 DSC, оборудованных охлаждающим устройством RCS и автоматическим устройством подачи проб. Для продувки используют поток 50 мл/мин газообразного азота. Образцы осадка или суспензии фосфата алюминия сушили, нагревая при 110 С до постоянной массы. Альтернативно, можно было следовать стандарту, изложенному в ASTM D-280, чтобы достичь аналогичных результатов. Полученный в результате образец высушенного порошка взвешивают (примерно 4 мг) в открытой алюминиевой чашке (модель DSC Q10). Затем чашку устанавливают в приборе ДСК и нагревают от комнатной температуры до 420 С при скорости нагрева 10 С/мин. Исследуют кривую ДСК и записывают температуры максимумов скоростей тепловых потоков (W/g) относительно сигмоидальной базисной линии, проведенной от комнатной температуры до 420 С. Измеряют тепло, поглощенное образцом, в виде площади под кривой в использованном температурном диапазоне. Для упрощения вычислений в ДСК используют сигмоидальную базисную линию. Хотя может быть достаточной прямая линия, когда теплоемкости твердой и жидкой фазы сильно не различаются, типично создают сигмоидальную базисную линию, чтобы определить нижний предел площади под кривой ДСК. Это необходимо вследствие факта, что наклон базисной линии, представляющей теплоемкость, изменяется с фазовыми превращениями и, следовательно, использование линейной базовой линии может вести к значительным ошибкам. Сигмоидальная базисная линия представляет собой S-образную кривую, уровень и/или наклон которой подвергается изменению до, либо после пика. Это используется в качестве компенсации любого изменения базисной линии, которое может происходить в течение фазового перехода. Базисная линия претерпевает корректировку на прореагировавшую долю в сравнении со временем. Сигмоидальную базисную линию вначале рассчитывают в виде прямой линии от начала пика до конца пика. Затем ее пересчитывают для каждой точки ввода данных между пределами пика в виде средневзвешенной величины между намеченными горизонтальными или касательными базисными линиями в начале пика и в конце пика. Табл. 1 отражает результаты различных тестов, проведенных на образцах фосфата алюминия,включая данные, полученные на образцах, протестированных на ДСК. Первая колонка табл. 1 представляет собой номер образца. Вторая колонка табл. 1 отражает мольное отношение фосфора к алюминию полученной в результате смеси. Третья колонка табл. 1 отражает мольное отношение фосфора к натрию данных смесей. Четвертая колонка табл. 1 отражает мольное отношение алюминия к натрию данных смесей. Отношения фосфора, алюминия и натрия определяли оптической эмиссионной спектрометрией с индуктивно связанной плазмой ("ICP-OES"), модель Optima 3000 DV, Perkin Elmer. Примерно 100 мг суспензии по изобретению растворяли в 1,5 г (НС 1) (3 М) и добавляли 100 г воды. Конечные растворы отфильтровывали и проводили измерения ICP. ICP представляет собой аргоновую плазму, поддерживаемую взаимодействием поля радиочастоты (RF) и ионизированного газообразного аргона. В ICP-OES плазму используют в качестве источника энергии, создавая тепло 5500-8000 К и до 10000 К в некоторых областях, достаточное для ионизации и возбуждения большинства атомов анализируемого вещества. При возвращении электрона в свое основное состояние, свет испускается и детектируется. Поскольку возбужденный ион испускает свет только определенных длин волн, получаются спектральные линии, зависящие от элемента. Данные линии затем можно использовать для качественного определения компонентов образца. Можно использовать калибровочную кривую зависимости интенсивности спектра от концентрации для количественного определения концентрации анализируемого вещества в образце. Пятая и шестая колонки табл. 1 отражают температуры, при которых располагаются пики, относительно тестов, проведенных на ДСК, как описано здесь. Седьмая колонка отражает интегрирование кривых, созданных измерением теплового потока ДСК. Остающиеся три колонки отражают отношение между индексами непрозрачности, белизны и желтизны краски, изготовленной с заменой 50% оксида титана фосфатом алюминия в стандартной краске. Индекс укрывистости измеряют согласно стандарту ASTM D 2805-96 а, в то время как индексы белизны и желтизны измеряют согласно стандарту ASTM Е 313-00. Оптические измерения (укрывистость,белизна и желтизна) проводили Колориметром BYK-Gardner модели color-guide sphere d/8 spin. КартыLeneta с мазками приготовлены по ASTM D2805 с использованием красок, составленных с описанной здесь композицией по изобретению и TiO2. Шкала цветового охвата представляет собой портативный спектрофотометр, который можно использовать для обеспечения постоянного качества при входящем и выходящем контроле качества в технологическом контроле на местах. Он работает на батарейках, чтобы отвечать требованиям измерений в полевых условиях. Принцип измерения основан на измерении спектральной отражательной способности в видимом спектре при длинах волн 400-700 нм. Предлагаются две геометрии измерений: 45/0 и d/8 (с наличием или без отражающего глянца). При 45/0 освещение происходит в круглом образце при угле 45, в то время как угол наблюдения составляет 0. При d/8 свет падает на образец диффузным образом, в то время как угол наблюдения составляет 8 "от вертикали". Инструмент шкалы светового охвата с глянцем измеряет (d/8) и 60 одновременно. Образец освещается светоизлучающими диодами (СИДами) с ожиданием высокой продолжительности срока службы. СИДы не нагревают образец, поэтому нет риска термохромных эффектов, вызванных освещением. Таблица 1. Результаты различных тестов, проведенных на образцах фосфата алюминия Образцы 1-12 были, как правило, приготовлены процедурой, изложенной в примере 1 настоящего описания. Образцы 1-4 изготовлены из "осадка" фосфата алюминия, собранного с фильтра. Образец 3 представляет собой смесь первого и второго осадков образцов. Образцы 5-12 изготовлены из суспензий смеси фосфата алюминия. Образцы 13-26, представляют собой суспензии, приготовленные согласно примеру 1, описанному в настоящем описании, но в уменьшенном масштабе, используя 1/20 количества фосфорной кислоты, указанного в примере 1. Использованные технологические переменные представляли собой: массовое отношение Р/А 1 в сырье; рН в течение добавления; используемые щелочи, либо гидроксид натрия, гидроксид калия, либо гидроксид аммония; количество щелочи, добавленной в конце приготовления для регулирования рН. Образец 25 не содержит запись в таблице для отношений Al/Na или P/Na, поскольку в данной композиции в качестве катиона использовали калий. Специалисту в данной области очевидно, что некоторые катионы можно использовать в композиции взаимозаменяемо в зависимости от обстоятельств и имеющихся веществ. Аналогично, в образце 26 использовали гидроксид аммония в качестве вещества основания и, следовательно, он также не имеет величин для отношенийAl/Na или P/Na. Образцы, полученные из тестов ДСК, показаны на фиг. 4-7. Как можно видеть из фиг. 4-7, полный профиль показывает, что он эндотермический (т.е. тепло втекает в образец). Кроме того, могут наблюдаться два широких отрицательных пика примерно при 106 С и приблизительно при 164 С. Конечно, два данных пика могут сдвигаться вверх или вниз по температуре, в зависимости от состава и структуры порошка. Вычисляют, что интеграл эндотермы, или энтальпия дегидратации, составляет примерно 490 Дж/г. Такая энтальпия дегидратации также может меняться в зависимости от ряда факторов. Пики,на которые здесь сделана ссылка, иногда перекрываются, так что только верхушка одного из пиков оптически видна в виде "свободно стоящего" пика на результатах ДСК. В некоторых вариантах осуществле-6 024005 ния пик при более высокой температуре ("второй пик") является интенсивнее пика при более низкой температуре ("первого пика"). В других вариантах осуществления первый пик может не являться хорошо определенным пиком и наложен на второй пик, который может быть широким и хорошо определенным. В данных случаях первый пик подтверждается маленьким плечом или изменением кривизны второго пика. Более того, результаты ДСК могут включать дополнительные пики вне указанных здесь температурных диапазонов. Однако, предпочтительно, нет пика между примерно 300 и 400 С. Более предпочтительно, нет пика между примерно 310 и 380 С. Еще более предпочтительно, нет пика между примерно 320 и 360 С. И еще более предпочтительно, нет пика между примерно 335 и 345 С. Фиг. 4 показывает два отчетливых пика на термограмме ДСК, один пик примерно при 110 С и один пик примерно при 172 С. Композицию образца, для которого показаны результаты фиг. 4, как правило,готовили по процедуре примера 1, указанного в настоящем описании. Фиг. 5 показывает два пика, которые перекрываются друг с другом, так что второй пик более заметен по сравнению с первым пиком. Композицию образца, для которого показаны результаты из фиг. 5, как правило, готовили процедурой примера 1, указанного в настоящем описании, но в уменьшенном масштабе, используя 1/20 от количества фосфорной кислоты, указанного в примере 1. Фиг. 6 также показывает два пика, которые слегка перекрываются. Фиг. 6 включает образец, в котором в качестве щелочного сырья используют калий. Фиг. 7 также показывает два пика, которые слегка перекрываются. Образец, соответствующий фиг. 7, получали,используя гидроксид аммония в качестве сырья. Кроме характеристик ДСК композиция фосфата алюминия также диспергируется в воде, что характеризуется ее диспергируемостью в воде. Тесты диспергируемости также проводили на различных образцах композиции фосфата алюминия. "Диспергируемость" в воде относится к количеству фосфата алюминия, диспергирующегося или растворяющегося в воде. Подразумевается, что сюда включаются условия, в которых фосфат алюминия растворяется с образованием молекулярного раствора или диспергируется в водной среде с получением стабильного продукта. Часто является возможным получить растворимые и диспергируемые фракции, когда композицию фосфата алюминия смешивают с водой. Более того, также можно увеличить или уменьшить диспергируемость, добавляя добавки к воде или изменяя рН раствора. Следовательно, диспергируемость, указанная в формуле изобретения, относится к количеству диспергированной композиции фосфата алюминия в воде без добавления других добавок или реагентов. Тесты для определения характеристик дисперсии композиции по изобретению были следующие: во-первых, измеренное количество фосфата, полифосфата или метафосфата алюминия (или их смесей),типично примерно один грамм, добавляли к измеренному количеству диспергатора. Фосфат алюминия находился в форме "осадка". В качестве диспергатора использовали воду (необязательно с некоторыми добавками). Полученную в результате смесь энергично встряхивали в вихревой мешалке в течение двух минут. Суспензию фильтровали самотеком через фильтр из нержавеющей стали 400 меш. Остаток промывали 2 миллилитрами деионизированной воды. Затем фильтр и влажный осадок на фильтре сушили в сушильном шкафу при 110 С в течение двадцати минут. Затем смесь взвешивали. Результаты дисперсии тестовых образцов изложены в табл. 2. Таблица 2. Данные диспергируемости для частиц фосфата алюминия Как показано в табл. 2, смесь фосфата алюминия, когда она подвергнута вышеуказанному тесту диспергируемости, показывает диспергируемость до 96,3% (которая является очень диспергируемой) и 65,7% (которая является менее диспергируемой). Как поймет специалист в данной области, диспергируемость любой данной композиции можно регулировать в зависимости от конечной области использования, в которой фосфат алюминия будет использован. Например, фосфат алюминия с более высокой диспергируемостью может быть желателен для использования при изготовлении красок. В зависимости от способа, использованного для изготовления красок, может быть желательным иметь более высокую диспергируемость или более низкую диспергируемость. Тип диспергатора также имеет некоторое влияние на диспергируемость. Как показано в табл. 2, когда диспергатором является Н 2 О, наименее диспергируемый образец имеет диспергируемость примерно 81,2%, в то время как наиболее диспергируемый образец имеет диспергируемость 95,0%. В табл. 2 образец А соответствует образцу 12 из табл. 1. Образец С соответствует образцу 13 из табл. 1. Образец D соответствует образцу 18 из табл. 1. Образец Е соответствует образцу 21 из табл. 1, в то время как образец F соответствует образцу 25 из табл. 1. Описанные здесь частицы фосфата алюминия демонстрируют уникальные свойства. Например, частицы фосфата алюминия дают полости, даже когда частицы сушат при комнатной температуре или при температуре до 130 С. Предпочтительно частицы сушат при температуре от 40 до 130 С. Более предпочтительно частицы сушат при температуре от 60 до 130 С. Еще более предпочтительно частицы сушат при температуре от 80 до 120 С. Кроме того, частицы фосфата алюминия имеют структуру ядро-иоболочка. Другими словами, данные частицы имеют оболочки, химически отличные от их ядер. Данное свойство подтверждается несколькими различными наблюдениями. Во-первых, неупругие электронные изображения частиц с использованием энергетического фильтра в области плазмонов (10-40 эВ), измеренные просвечивающим электронным микроскопом, показывают яркие линии, окружающие большую часть частиц. Контрастность изображения, видимая на плазмонных микрографиях, зависит от локального химического состава и, в свою очередь, структура частиц ядро-и-оболочка может наблюдаться при исследовании микрографии на фиг. 1. Затем, присутствие полостей внутри частиц, продемонстрированное на фиг. 1, высушенных при довольно низких температурах, имеется вследствие факта, что частицы теряют массу посредством сжатия,в то время как их наружный слой не подвергается сокращению. Такие полости, или полые частицы, становятся возможными, если пластичность ядра частицы выше, чем оболочки. Дополнительные указания образования полых частиц наблюдаются при нагревании частиц посредством концентрирования электронного пучка на частицах. Тогда внутри частиц создаются большие полости, в то время как их периметр подвергается небольшому изменению. Другим дополнительным указанием присутствия закрытых полостей, или полых частиц, является скелетная плотность фосфата алюминия, полученного описанным здесь способом, которая находится в диапазоне 1,73-2,40 г/см 3 при измерении после сушки при 110 С до постоянной массы, и содержание воды, составляющее примерно 15-20%, по сравнению с величинами 2,5-2,8 г/см 3, зарегистрированными для плотных частиц фосфата алюминия. Предпочтительно, скелетная плотность составляет менее 2,40 г/см 3. Более предпочтительно, скелетная плотность составляет менее 2,30 г/см 3. Более предпочтительно, скелетная плотность составляет менее 2,10 г/см 3. Еще более предпочтительно, скелетная плотность составляет менее 1,99 г/см 3. Частицы фосфата алюминия, приготовленные согласно описанному здесь способу, могут диспергироваться в латексе в присутствии кристаллического порошкообразного твердого вещества. Если отливают пленку, используя данную дисперсию, то получают весьма непрозрачные пленки. Весьма непрозрачные пленки получают даже в случае тонких одиночных слоев частиц. Экспериментальное доказательство непрозрачности пленки получают, используя аморфный фосфат, полифосфат или метафосфат алюминия(или их смеси) в качестве замены диоксида титана (т.е. TiO2). Диоксид титана представляет собой современный стандартный белый пигмент, используемый практически всеми производителями, связанными с рецептурами латексных красок. Стандартные акриловые или стирольные латексные краски получали с использованием обычной загрузки диоксида титана, и сравнивали с краской, где пятьдесят процентов загрузки диоксида титана заменяли аморфным фосфатом алюминия. Данное сравнение проводили в двух различных тестирующих краски лабораториях. Оптические измерения, проведенные на вытянутых пленках с использованием двух красок, демонстрируют, что фосфат алюминия может заменять диоксид тита-8 024005 на, давая пленки с сохранением оптических свойств пленки. Результаты и высокая эффективность нового фосфата алюминия, обсужденного в настоящем описании, частично связаны с относительно маленьким размером его частиц. Такие маленькие размеры частиц позволяют частицам широко распределяться в пленке и однородно ассоциироваться со смолой и неорганическими наполнителями краски, таким образом, создавая кластеры, которые являются центрами экстенсивного образования полостей при высыхании краски. Фосфат алюминия по настоящему изобретению показывает данную тенденцию образовывать закрытые полости, или полые частицы, до такой степени, которую ранее не наблюдали для фосфатов, полифосфатов алюминия или любых других частиц. В некоторых вариантах осуществления частицы фосфата, полифосфата или метафосфата алюминия по существу не содержат открытые поры, в то же время содержат ряд закрытых пор. В результате в таких вариантах осуществления объем макропор значительно меньше 0,1 см 3/г. Укрывистость пленок водорастворимой краски, использующей фосфат алюминия, в некоторых вариантах осуществления данного изобретения включает в себя уникальные черты. Влажная покрывающая пленка представляет собой вязкую дисперсию частиц полимера, фосфата алюминия, диоксида титана и наполнителя. Когда данную дисперсию отливают в виде пленки и сушат, она ведет себя отлично от стандартной краски (ниже критической объемной концентрации пигмента, КОКП). В стандартной краске смола с низкой температурой стеклования (Тстекл.) является пластичной при комнатной температуре и коалесцированной, так что пленка смолы заполняет поры и полости. Однако краска, составленная с использованием фосфата алюминия, может показывать отличающееся поведение. Образуются закрытые поры, как описано здесь, и вносят вклад с кроющую способность пленки. Фосфат или полифосфат алюминия в пигментах можно приготовить и использовать, по меньшей мере, в одной из следующих форм: в виде суспензии (дисперсии с высоким содержанием сухого остатка,которая течет под действием силы тяжести или насосов низкого давления) с содержанием сухого остатка 18% или более; в виде высушенного и тонкоизмельченного фосфата алюминия с влажностью 15-20%; а также в полимерной форме в виде кальцинированного и тонкоизмельченного полифосфата алюминия. Фосфат алюминия, полифосфат алюминия или метафосфат алюминия (или их смеси), используемые в виде белого пигмента, могут заменить диоксид титана в дисперсиях в водной среде, таких как эмульсии полимерного латекса. Мольное отношение фосфор:алюминий в фосфате алюминия, предпочтительно,составляет от 0,6 до 2,5. Более предпочтительно мольное отношение фосфор:алюминий в фосфате алюминия находится в диапазоне от 0,8 до 2,3. Еще более предпочтительно мольное отношение фосфор : алюминий в фосфате алюминия находится в диапазоне от 1,1 до 1,5. Как обсуждалось, одним аспектом данного изобретения является новый способ получения полых частиц фосфата алюминия, полифосфата алюминия, метафосфата алюминия (или их комбинации), которые можно использовать в различных областях использования, включая белый пигмент в рецептурах красок на основе водного полимерного латекса. Способ описан в виде следующих общих стадий. Специалист в данной области поймет, что некоторые стадии можно изменить или пропустить в целом. Данные стадии включают: приготовление основных реагентов, используемых в способе, таких как разбавленный раствор фосфорной кислоты, разбавленный раствор сульфата алюминия и разбавленный раствор гидроксида натрия, карбоната натрия, гидроксида калия или гидроксида аммония; одновременное и контролируемое добавление реагентов в реактор, оборудованный взбалтывающей системой для поддержания гомогенности смеси в течение данного способа; контроль, в течение добавления реагентов в реактор,температуры и рН (кислотности) смеси и, преимущественно, времени реакции; фильтрование суспензии,содержащей примерно 8,0% сухого остатка, и разделение жидкой и твердой фазы на соответствующем оборудовании; вымывание примесей, присутствующих в осадке на фильтре слегка щелочным водным раствором; диспергирование промытого осадка, содержащего примерно 20-30% сухого остатка в подходящем диспергирующем устройстве; сушку диспергированной пульпы в турбосушилке; тонкое измельчение высушенного продукта до средней гранулометрии от 5,0 до 10 мкм и полимеризацию высушенного продукта термической обработкой фосфата алюминия в кальцинаторе. Существует несколько путей приготовления основных ингредиентов в данном способе. Как было указано, одним источником фосфора для изготовления фосфата алюминия и полифосфата алюминия является фосфорная кислота сорта, используемого в качестве удобрения, из любого источника, поскольку она осветлена и обесцвечена. Например, коммерческую фосфорную кислоту, содержащую примерно 54% Р 2 О 5, можно химически обработать и/или разбавить химически обработанной водой, в результате получая 20% концентрацию Р 2 О 5. Кроме того, в качестве альтернативы данному способу (вместо фосфорной кислоты сорта, используемого в качестве удобрения, или очищенной фосфорной кислоты), можно использовать соли фосфора, такие как ортофосфаты, полифосфаты или метафосфаты. Другим реагентом для способа является коммерческий сульфат алюминия. Сульфат алюминия можно получить реакцией между оксидом алюминия (гидратированным оксидом алюминия) и концентрированной серной кислотой (98% H2SO4), затем осветлить и хранить при концентрации Al2O3 28%. Чтобы реакция имела подходящую кинетику, сульфат алюминия разбавляют очищенной водой до 5,0% А 12 О 3. В качестве альтернативы данному способу, источником алюминия может являться любая другая соль алюминия, а также гидроксид алюминия или алюминий в металлической форме. Реакцию нейтрализации осуществляют раствором гидроксида натрия, который можно купить в различных концентрациях. Можно купить раствор NaOH с концентрацией 50% и разбавить. Например, в первой фазе реакции, при смешивании исходных реагентов, гидроксид натрия можно использовать с концентрацией 20% NaOH. Во второй фазе реакции, вследствие необходимости тонкой настройки кислотности продукта, можно использовать раствор гидроксида натрия, содержащий 5% NaOH. В качестве альтернативного нейтрализатора можно использовать гидроксид аммония или карбонат натрия (кальцинированную соду). В одном варианте осуществления изобретения химическая реакция приводит к образованию ортофосфатов гидроксоалюминия, чистых или смешанных (например, Al(OH)2 (H2PO4) или Al(OH) (HPO4). Описанную реакцию осуществляют посредством смеси трех реагентов, т.е. раствора фосфорной кислоты,раствора сульфата алюминия и раствора гидроксида натрия. Реагенты дозировано подают в реактор,обычно содержащий взбалтывающую систему, в течение 30-минутного периода. В течение добавления реагентов в реактор рН смеси контролируют внутри диапазона от 1,4 до 4,5, а температуру реакции от 35 до 40 С. Реакцию завершают через 15 мин после смешивания реагентов. В данный период рН смеси можно регулировать в диапазоне от 3,0 до 5,0, добавляя более разбавленный гидроксид натрия. В данном варианте осуществления температура, преимущественно, составляет примерно менее 40 С. В конце взаимодействия полученная суспензия должна содержать мольное отношение элементов фосфор:алюминий в диапазоне от 1,1 до 1,5. После образования ортофосфата алюминия суспензию, содержащую примерно от 6,0 до 10,0% сухого остатка, с приблизительной максимальной температурой 45 С и плотностью в диапазоне от 1,15 до 1,25 г/см 3, перекачивают в обычный фильтр-пресс. В фильтр-прессе жидкую фазу (иногда называемую"жидкость") отделяют от твердой фазы (часто называемую "осадок на фильтре"). Влажный осадок, содержащий примерно от 18 до 45% сухого вещества, и все еще возможно загрязненный раствором сульфата натрия, сохраняют на фильтре для цикла промывки. Отфильтрованный концентрат, который в основном представляет собой концентрированный раствор сульфата натрия, удаляют из фильтра и хранят для дальнейшего использования. В одном варианте осуществления изобретения промывку влажного осадка проводят в самом фильтре и в трех технологических стадиях. В первой промывке ("замещающая промывка") удаляют наибольшую часть фильтрующегося вещества, которое загрязняет осадок. Стадию промывки осуществляют, используя химически обработанную воду поверх осадка при скорости потока 6,0 м 3 воды/тонну сухого осадка. Вторую промывочную стадию, также химически обработанной водой и с потоком 8 м 3 воды/тонну сухого осадка, можно осуществить, чтобы далее снизить, если не исключить, примеси. И, наконец, можно осуществить третью промывочную стадию, используя слегка щелочной раствор. Такую третью стадию промывки можно исполнить для нейтрализации осадка и поддержки его рН в диапазоне 7,0. Наконец, осадок можно продуть сжатым воздухом в течение определенного периода времени. Предпочтительно, влажный продукт должен содержать от 35 до 45% сухого вещества. Далее, в данном конкретном варианте осуществления изобретения дисперсию осадка можно обработать таким образом, что осадок на фильтре, влажный и промытый, и содержащий примерно 35% сухого вещества, извлекают из фильтр-пресса лентой конвейера и перемещают в реактор/диспергирующее устройство. Диспергированию осадка содействуют, добавляя разбавленный раствор тетранатрий пирофосфата. После стадии диспергирования продукт затем сушат, когда "ил" фосфата алюминия, с процентным содержанием сухого вещества в диапазоне от 18 до 50%, перекачивают в сушильное устройство. В одном варианте осуществления удаление воды из вещества можно осуществить осушающим оборудованием,таким как устройство типа "турбосушилки" посредством прокачивания потока горячего воздуха при температуре от 135 до 140 С через образец. Конечную влажность продукта предпочтительно следует поддерживать в диапазоне от 10 до 20% воды. В некоторых вариантах осуществления следующая стадия способа включает кальцинирование продукта. В данной стадии сухой ортофосфат алюминия, в виде Al(H2PO4)3, конденсируют термической обработкой с получением полого полифосфата алюминия, то есть (Al(n+2/3(PnO(3n+1, где n может представлять собой любое целое число больше 1, предпочтительно n больше или равно 4. Более предпочтительноn больше или равно 10. Еще более предпочтительно n больше или равно 20. Предпочтительно n меньше 100. Еще более предпочтительно n меньше 50. Данную технологическую операцию осуществляют, нагревая фосфат алюминия в обжиговой печи типа распылительной сушилки в температурном диапазоне от 500 до 600 С. После полимеризации продукт можно быстро охладить и направить в устройство тонкого измельчения. В данный момент можно осуществить стадию тонкого измельчения продукта. Наконец,полученный в результате продукт, который покидает сушилку (или обжиговую печь) перемещают в устройство измельчения и окончательной обработки, измельчают в мельнице тончайшего помола/сортирующем устройстве и его гранулометрию поддерживают в диапазоне 99,5% ниже 400 меш. Фосфат алюминия или полифосфат алюминия после термической обработки можно использовать в качестве белого пигмента в рецептурах краски для внутренних работ, на основе воды, благодаря своему свойству присущей непрозрачности в латексных, ПВА или акриловых пленках, вследствие образования частиц с пористой структурой с высокой способностью распространения света в течение процесса сушки краски. Различные краски можно составить, используя в качестве пигмента фосфат или полифосфат алюминия, изготовленный согласно различным вариантам осуществления изобретения, в одиночку или в комбинации с другим пигментом, таким как диоксид титана. Краска включает один или несколько пигментов и один или несколько полимеров в качестве связующего (иногда называемый "связующим полимером") и необязательно различные добавки. Существуют водоразбавляемые краски и неводоразбавлемые краски. Как правило, композиция водоразбавляемой краски состоит из четырех основных компонентов: связующего, водного носителя, пигмента(ов) и добавки(ок). Связующее представляет собой нелетучее смолистое вещество, которое диспергируется в водном носителе с образованием латекса. Когда водный носитель испаряется, связующее образует пленку краски, которая связывает вместе частицы пигмента и другие нелетучие компоненты композиции водоразбавляемой краски. Композиции водоразбавляемых красок можно составить в соответствии со способами и компонентами, описанными в патенте США 6646058 с модификациями или без них. Описание данного патента включено сюда посредством ссылки во всей его полноте. Фосфат или полифосфат алюминия, изготовленный согласно различным вариантам осуществления изобретения, можно использовать для составления рецептур водоразбавляемых красок в качестве пигмента, в одиночку или в комбинации с диоксидом титана. Обычная краска представляет собой латексную краску, которая включает связующий полимер,кроющий пигмент и необязательно загуститель и другие добавки. Снова, фосфат или полифосфат алюминия, изготовленные по различным вариантам осуществления изобретения, можно использовать для составления рецептуры латексной краски в качестве пигмента, в одиночку или в сочетании с диоксидом титана. Другие компоненты для изготовления латексной краски описываются в патентах США 6 881 782 и 4 782 109, которые включаются ссылкой во всей своей полноте. С целью иллюстрации подходящие компоненты и методы изготовления латексных красок кратко объяснены ниже. В некоторых вариантах осуществления подходящие связующие полимеры включают сополимеризованные в эмульсии ненасыщенные этиленовые мономеры, включающие от 0,8 до 6% акрилата или метакрилата жирной кислоты, такие как лаурилметакрилат и/или стеарилметакрилат. Исходя из массы сополимеризованных этиленовых мономеров, полимерное связующее включает от 0,8 до 6% метакрилата или акрилата жирной кислоты, где предпочтительные композиции содержат от 1 до 5% сополимеризованного акрилата или метакрилата жирной кислоты, имеющей цепь алифатической жирной кислоты,включающую от 10 до 22 атомов углерода. Предпочтительные сополимерные композиции основаны на сополимеризованном метакрилате жирной кислоты. Предпочтительным является лаурилметакрилат и/или стеарилметакрилат, и лаурилметакрилат является наиболее предпочтительным мономером. Другие применимые метакрилаты жирной кислоты включают миристилметакрилат, децилметакрилат, пальмитилметакрилат, олеилметакрилат, гексадецилметакрилат, цетилметакрилат и эйкозилметакрилат и аналогичные алифатические метакрилаты с неразветвленной цепью. Метакрилаты или акрилаты жирной кислоты типично включают коммерческие масла жирных кислот, прореагировавшие с метакриловой кислотой или акриловой кислотой, чтобы обеспечить, прежде всего, метакрилат с фрагментом преобладающей жирной кислоты с незначительным количеством акрилатов или метакрилатов другой жирной кислоты. полимеризоваться ненасыщенные этиленовые мономеры содержат ненасыщенность угСпособные лерод-углерод и включают виниловые мономеры, акриловые мономеры, аллиловые мономеры, акриламидные мономеры, а также моно- и дикарбоновые ненасыщенные кислоты. Сложные виниловые эфиры включают винилацетат, винилпропионат, винилбутираты, винилбензоаты, винилизопропилацетаты и аналогичные виниловые сложные эфиры; винилгалогениды включают винилхлорид, винилфторид и винилиденфторид; виниловые ароматические углеводороды включают стирол, метилстиролы и аналогичные содержащие низшие алкилы стиролы, хлорстирол, винилтолуол, винилнафталин и дивинилбензол; виниловые алифатические углеводородные мономеры включают альфа-олефины, такие как этилен, пропилен, изобутилен и циклогексен, а также сопряженные диены, такие как 1,3-бутадиен, метил-2 бутадиен, 1,3-пиперилен, 2,3-диметилбутадиен, изопрен, циклогексан, циклопентадиен и дициклопентадиен. Винилалкиловые эфиры включают метилвиниловый эфир, изопропилвиниловый эфир, нбутилвиниловый эфир и изобутилвиниловый эфир. Акриловые мономеры включают мономеры, такие как низшие алкиловые эфиры акриловой или метакриловой кислоты, часть алкилового сложного эфира,содержащую от 1 до 12 атомов углерода, а также ароматические производные акриловой и метакриловой кислоты. Применимые акриловые мономеры включают, например, акриловую и метакриловую кислоту,метилакрилат и метилметакрилат, этилакрилат и этилметакрилат, бутилакрилат и бутилметакрилат, пропилакрилат и пропилметакрилат, 2-этилгексилакрилат и 2-этилгексилметакрилат, циклогексилакрилат и циклогексилметакрилат, децилакрилат и децилметакрилат, изодецилакрилат и изодецилметакрилат, бензилакрилат и бензилметакрилат и различные реакционные продукты, такие как бутилфенил- и крезилглицидиловые эфиры, прореагировавшие с акриловой и метакриловой кислотами, гидроксиалкилакрилаты и гидроксиалкилметакрилаты, такие как гидроксиэтил- и гидроксипропилакрилаты и -метакрилаты, а также аминоакрилаты и аминометакрилаты. Акриловые мономеры могут включать очень незначитель- 11024005 ные количества акриловых кислот, включая акриловую и метакриловую кислоту, этакриловую кислоту,альфа-хлоракриловую кислоту, альфа-цианакриловую кислоту, кротоновую кислоту, бэта-акрилоксипропионовую кислоту и бэта-стиролакриловую кислоту. В других вариантах осуществления полимеры применимые в качестве компонента (а), "связующий полимер", латексных красок представляют собой продукты сополимеризации смесей со-мономеров, которые включают мономеры, выбранные из стирола, метилстирола, винила или их комбинаций. Предпочтительно сомономеры включают (более предпочтительно, состоят, по существу, из) по меньшей мере 40 моль.% мономеров, выбранных из стирола, метилстирола или их комбинаций, и по меньшей мере 10 мол.% одного или нескольких мономеров, выбранных из акрилатов, метакрилатов и акрилонитрила. Предпочтительно, акрилаты и метакрилаты содержат от 4 до 16 атомов углерода, например, 2 этилгексилакрилат и метилметакрилаты. Также предпочтительно, чтобы мономеры использовали в такой пропорции, что конечный полимер имел температуру стеклования (Тстекл.) больше чем 21 С и меньше чем 95 С. Полимеры предпочтительно имеют средневесовую молекулярную массу по меньшей мере 100000. Предпочтительно связующий полимер включает звенья интерполимера, полученные из 2 этилгексилакрилата. Более предпочтительно, связующий полимер включает полимерные звенья, включающие от 50 до 70 мол.% звеньев, полученных из стирола, метилстирола или их комбинаций; от 10 до 30 мол.% звеньев, полученных из 2-этилгексилакрилата; и от 10 до 30 мол.% звеньев, полученных из метилакрилата, акрилонитрила или их комбинаций. Иллюстративные примеры подходящих связующих полимеров включают сополимер, интерполимерные звенья которого получены из примерно 49 мол.% стирола, 11 мол.% альфа-метилстирола, 22 мол.% 2-этилгексилакрилата и 18 мол.% метилметакрилата с Тстекл. примерно 45 С (продаваемый в виде полимерной эмульсии Neocryl XA-6037 компанией ICI Americas, Inc., Бриджвотер, Нью Джерси); сополимер, интерполимерные звенья которого получены из примерно 51 мол.% стирола, 12 мол.% альфаметилстирола, 17 мол.% 2-этилгексилакрилата и 19 мол.% метилметакрилата с Тстекл. примерно 44 С(продаваемый в виде полимерной эмульсии Joncryl 537 компанией S.C. JohnsonSons, Расин, Висконсин); и тройной сополимер, интерполимерные звенья которого получены из примерно 54 мол.% стирола,23 мол.% 2-этилгексилакрилата и 23 мол.% акрилонитрила с Тстекл. примерно 44 С (продаваемый в виде полимерной эмульсии Carboset.TM. XPD-1468 компанией B.F. Goodrich Co.). Предпочтительно связующий полимер представляет собой Joncryl.TM.537. Как описано выше, фосфат, полифосфат или метафосфат алюминия, изготовленный согласно различным вариантам осуществления изобретения, можно использовать для составления рецептур латексных красок в качестве пигмента, в одиночку или в комбинации с другим пигментом. Подходящие дополнительные кроющие пигменты включают белые, непрозрачные, кроющие пигменты и окрашенные органические и неорганические пигменты. Типичные примеры подходящих белых непрозрачных кроющих пигментов включают рутиловые и анатазные диоксиды титана, литопон, сульфид цинка, титанат свинца, оксид сурьмы, оксид циркония, сульфид бария, свинцовые белила, оксид цинка, содержащие свинец цинковые белила и аналогичные, а также их смеси. Предпочтительный белый непрозрачный кроющий пигмент представляет собой рутиловый диоксид титана. Более предпочтительным является рутиловый диоксид титана, имеющий средний размер частиц примерно от 0,2 до 0,4 мкм. Примерами окрашенных органических пигментов являются фталовый синий и ганза желтый. Примерами окрашенных неорганических пигментов являются красный железооксидный пигмент, коричневый железооксидный пигмент, охра и умбра. Наиболее известные латексные краски содержат загустители для модифицирования реологических свойств краски, чтобы обеспечить хорошее распределение, обращение и характеристики нанесения. Подходящие загустители включают нецеллюлозный загуститель (предпочтительно, ассоциированный загуститель, более предпочтительно, уретановый ассоциированный загуститель). Ассоциированные загустители, такие как, например, гидрофобно модифицированные щелочные набухающие акриловые сополимеры и гидрофобно модифицированные уретановые сополимеры, как правило, придают более ньютоновскую реологию эмульсионным краскам по сравнению с обычными загустителями, такими как, например, целлюлозные загустители. Типичные примеры подходящих ассоциированных загустителей включают полиакриловые кислоты (продаваемые, например, RohmHaas Co., Филадельфия, Ра., в виде Acrysol RM-825 и модификатора реологии QR-708) и активированный аттапульгит(продаваемый Engelhard, Изелин, Нью Джерси в виде Attagel 40). Пленки латексной краски образуются коалесценцией связующего полимера с образованием связующей матрицы при нанесении краски при температуре окружающей среды с получением твердой, нелипкой пленки. Коалесцирующие растворители помогают коалесценции пленкообразующего связующего, понижая температуру пленкообразования. Латексные краски, предпочтительно, содержат коалесцирующий растворитель. Типичные примеры подходящих коалесцирующих растворителей включают 2 феноксиэтанол, бутиловый эфир диэтиленгликоля, дибутилфталат, диэтиленгликоль, 2,2,4-триметил 1,1,3-пентандиолмоноизобутират и их комбинации. Предпочтительно коалесцирующий растворитель представляет собой бутиловый эфир диэтиленгликоля (бутилкарбитол) (продаваемый Sigma-Aldrich,Милуоки, Висконсин) или 2,2, 4-триметил-1,1,3-пентандиолмоноизобутират (продаваемый EastmanChemical Co., Кингспорт, Теннеси, в виде тексанола) или их комбинации. Коалесцирующий растворитель предпочтительно используют на уровне, примерно, от 12 до 60 г(предпочтительно, примерно 40 г) коалесцирующего растворителя на литр латексной краски, или примерно от 20 до 30%, исходя из массы полимерного сухого остатка в краске. Краски, составляемые в соответствии с различными вариантами осуществления настоящего изобретения, могут дополнительно включать обычные вещества, используемые в красках, такие как, например,пластификатор, противопенную добавку, наполнитель, регулятор рН, тонирующий цвет и биоцид. Такие типичные ингредиенты перечисляются, например, в TECHNOLOGY OF PAINTS, VARNISHES ANDLACQUERS, изданной C.R. Martens, R.E. Kreiger Publishing Co., p.515 (1974). Краски обычно составляют с "функциональными наполнителями" для увеличения кроющей способности, снижения стоимости, достижения долговечности, изменения внешнего вида, контроля реологии и влияния на другие желательные свойства. Примеры функциональных наполнителей включают,например, сульфат бария, карбонат кальция, глину, гипс, кремнезем и тальк. Большинство обычных функциональных наполнителей для красок для внутренних работ представляют собой глины. Глины имеют ряд свойств, которые делают их желательными. Недорогие кальцинированные глины, например, применимы при контролировании вязкости при низком усилии сдвига и имеют огромную внутреннюю удельную поверхность, что вносит вклад в "сухую укрывистость". Но данная площадь поверхности также доступна для поглощения красящего вещества. Из-за тенденции кальцинированных глин поглощать красящее вещество, предпочтительно, их используют в красках по изобретению только в незначительных количествах, требующихся для контроля реологии, например, типично менее примерно половины от общего наполнителя, либо не используют вовсе. Предпочтительные наполнители для использования в красках по изобретению представляют собой карбонаты кальция; наиболее предпочтительными являются ультратонко измельченные карбонаты кальция, такие как, например, опацимит (продаваемый ЕСС International, Силакауга, Алабама), супермит(продаваемый Imerys, Розуэлл, Ga.) или другие, имеющие размер частиц примерно от 1,0 до 1,2 мкм. Ультратонкий карбонат кальция помогает распределить диоксид титана оптимально для укрывистостиlatex flat paint," American PaintCoatings Journal, Apr. 4, 1988, pp. 89-94). Латексные краски, составленные в соответствии с различными вариантами осуществления изобретения, можно получить, используя традиционные методики. Например, некоторые ингредиенты краски обычно смешивают вместе при высоком усилии сдвига с получением смеси, обычно называемой "помолом" разработчиками краски. Консистенция данной смеси сравнима с консистенцией ила, что является желательным для того, чтобы эффективно диспергировать ингредиенты в мешалке с высоким усилием сдвига. В течение получения помола энергию высокого усилия сдвига используют для отделения друг от друга агломерированных частиц пигмента. Ингредиенты, не включенные в помол, обычно называют "разбавителями". Разбавитель обычно является намного менее вязким по сравнению с помолом, и обычно его используют для разбавления помола, чтобы получить конечную краску с соответствующей консистенцией. Конечное перемешивание помола с разбавителем типично осуществляют перемешиванием с низким усилием сдвига. Большинство полимерных латексов на стабильны к сдвигу и, следовательно, не используются в качестве компонента помола. Включение нестабильных к сдвигу латексов в помол может привести к коагуляции латекса, давая комковатую краску с отсутствующей, или незначительной, пленкообразующей способностью. Следовательно, краски обычно готовят, добавляя латексный полимер к разбавителю. Однако, некоторые краски, составленные в соответствии с различными вариантами изобретения, содержат латексные полимеры, которые, как правило, стабильны к сдвигу. Следовательно, латексные краски можно получить введением некоторого количества или всего латексного полимера в помол. Предпочтительно, по меньшей мере, часть латексного полимера добавляют в помол. Два примера возможных форм способа описываются ниже. И вновь, специалист в данной области признает варианты, которые можно использовать при осуществлении описанного здесь нового способа. Следующие ниже примеры представлены для иллюстрации вариантов осуществления изобретения. Все численные величины являются приблизительными. Когда даются численные диапазоны, необходимо понимать, что варианты осуществления вне указанных диапазонов все еще могут попадать в объем защиты изобретения. Конкретные детали, описанные в каждом примере, не следует истолковывать как необходимые черты изобретения. Пример 1. В данном примере получали 535,0 кг фосфата алюминия. Влажный продукт сушили в "турбосушилке", и он представлял характеристики полых частиц с 15% влажностью и отношением Р:Al (фосфор:алюминий) 1:1,50. Приготовляли 940,0 кг фосфорной кислоты для удобрений, содержащей 55,0% Р 2 О 5. В начальной фазе приготовления осуществляли обесцвечивание кислоты, которое продолжалось примерно 30 мин при температуре 85 С. Для данной фазы к кислоте добавляли 8,70 кг раствора пероксида водорода, содержащего примерно 50% Н 2 О 2. Затем кислоту разбавляли 975,0 кг технологической воды, охлаждали до температуры 40 С и затем хранили при концентрации 27,0% Р 2 О 5. Источник алюминия, используемый в данной заявке, представлял собой раствор коммерческого сульфата алюминия, содержащий 28% Al2O3. Раствор фильтровали и разбавляли технологической водой. Конкретно, объединяли 884,30 кг раствора сульфата алюминия и 1776,31 кг технологической воды для получения раствора, содержащего примерно 9,30% Al2O3. В данном конкретном эксперименте в качестве нейтрализующего агента использовали разбавленный раствор коммерческого гидроксида натрия, содержащий 20,0% NaOH. Конкретно, смешивали 974,0 кг раствора гидроксида натрия, содержащего 50% NaOH и 1461,0 кг технологической воды. Конечную смесь охлаждали до 40 С. Одновременно смешивали три реагента в течение примерно 30 мин в реакторе объемом 7500 л. В течение добавления реагентов в реактор температуру смеси поддерживали в диапазоне 40 С-45 С, рН контролировали, чтобы оставаться в диапазоне от 4,0 до 4,5. В конце добавления реагентов смесь взбалтывали в течение примерно 15 мин. Величину рН в данный момент контролировали примерно при 5,0,добавляя раствор гидроксида натрия, содержащий 5,0% NaOH. Полученная в результате суспензия имела массу 7000 кг с плотностью 1,15 г/см 3, представляющей 6,5% сухого остатка, что представляет примерно 455,0 кг осадка. Затем суспензию фильтровали в пресс-фильтре, получая в результате 1300 кг влажного осадка на фильтре и 5700 кг фильтрата. Фильтрат преимущественно состоял из раствора сульфата натрия (Na2SO4). Осадок на фильтре содержал примерно 35% сухого остатка. Осадок промывали непосредственно в прессфильтре 3860 л технологической воды при комнатной температуре, поддерживая при промывочном отношении примерно 8,5 см 3 промывочного раствора на тонну сухого осадка. Образующийся при промывке осадка фильтрат хранили для необязательного будущего использования или для очистки сточных вод. Затем извлеченный из фильтра осадок, примерно 1300 кг, переносили в диспергирующее устройство(объемом примерно 1000 л) посредством конвейерной ленты. Дисперсия, содержащая примерно 35% сухого остатка, имела плотность 1,33 г/см 3 и вязкость 17400 сП, и ее можно было использовать в качестве суспензии для изготовления краски. Затем дисперсную суспензию фосфата алюминия, с содержанием сухого остатка примерно 35%,перекачивали в турбосушилку. Продукт нагревали потоком горячего воздуха при температуре 135 С. Получали примерно 535,0 кг ортофосфата алюминия с влажностью примерно 15%. Конечный продукт подвергали тонкому измельчению и его гранулометрию поддерживали ниже 400 меш. Конечный анализ сухого продукта представил следующие результаты: содержание фосфора в продукте составляло примерно 20,2%; содержание алюминия составляло примерно 13,9%; содержание натрия составляло примерно 6,9% и величина рН водной дисперсии составляла примерно 7,0; содержание воды составляло примерно 15%; скелетная плотность 2,20 г/см 3 и средний диаметр частиц порошка составлял от 5 до 10 мкм. Пример 2. Из результатов примера 1 использовали примерно 200 кг осушенного и тонкоизмельченного фосфата алюминия. Образец использовали для изготовления образца краски для внутренних работ. Вначале готовили 900 литров непрозрачной белой акриловой краски. Такую краску наносили и эксплуатационные характеристики оценивали в сравнении с одной из коммерчески имеющихся красок. Основная композиция краски на основе оригинальной рецептуры, содержащей примерно 18% диоксида титана,была следующей: фосфата алюминия содержалось примерно 14,20%; оксида титана содержалось примерно 8,34%; каолина содержалось примерно 7,10%; алгаматолита содержалось примерно 10,36%; диатомита содержалось примерно 0,84%; акриловой смолы содержалось примерно 12,25% и ПВХ содержалось примерно 47,45%. Характеристики краски, приготовленной с фосфатом алюминия, после ее нанесения при окраске представляли собой следующее: а) влажная кроющая способность аналогична кроющей способности эталонной краски; b) сухая кроющая способность лучше, чем кроющая способность эталонной краски и с) тесты стойкости после шести месяцев внутреннего окрашивания дали превосходные результаты. Наконец, было видно, что непрозрачная белая акриловая краска, растворимая в воде, с фосфатом алюминия, приготовленная в примере 2, сохранила все характеристики коммерчески доступных красок с выходом 50 м 2/3,6 л на поверхности, подготовленной со шпаклевкой. Изображения рентгеновской дифракции вместе с ПЭМ демонстрируют, что описываемое здесь изобретение представляет собой водный, некристаллический и нейтральный фосфат алюминия, полученный из слабо агрегированных частиц наноразмера. Кроме того, средний размер агрегата набухших частиц (в суспензии) находится в диапазоне 200-1500 нм, что определено динамическим светорассеянием. Более предпочтительно, средний размер агрегата набухших частиц (в суспензии) находится в диапазоне 400700 нм. Однако размер индивидуальных частиц может иметь радиус только от 5 до 80 нм, определенный электронной микроскопией. Более предпочтительно, размер индивидуальных частиц может иметь радиус только от 10 до 40 нм. Как указано, основную диоксид титановую водоэмульсионную краску составляют из подходящей латексной дисперсии и частиц пигмента. Частицы латекса отвечают за создание коалесцированной пленки, наполненной частицами пигмента, и отвечают за кроющую способность пленки. Также используют многие добавки, такие как: неорганические наполнители, которые уменьшают требования по смоле и пигменту; коалесцирующие агенты, которые улучшают пленкообразование смолы; диспергаторы и модификаторы реологии, которые предотвращают комкование пигмента и наполнителя и, таким образом,улучшают срок годности вместе с реологическими свойствами краски. В типичной сухой пленке краски частицы пигмента и наполнителя диспергированы в пленке смолы. Кроющая способность в значительной степени зависит от коэффициента преломления и размера частиц. Как указано, диоксид титана в настоящее время является стандартным белым пигментом благодаря своему огромному коэффициенту преломления и отсутствию поглощения света в видимой области. Сухая пленка краски, составленной с новым фосфатом алюминия, в некоторых вариантах осуществления имеет несколько отличий от сухой пленки типичной краски. Во-первых, пленка с фосфатом алюминия не является просто пленкой смолы. Скорее она образована смолой, переплетенной с фосфатом алюминия. Таким образом, она представляет собой нанокомпозитную пленку, которая объединяет две взаимопроникающие фазы с различнымисвойствами для достижения синергетических преимуществ касательно механических свойств пленки и сопротивления воде и другим агрессивным агентам. Во-вторых, хорошую кроющую способность пленки получают при более низком содержании диоксида титана, поскольку пленка содержит значительное количество закрытых пор, которые рассеивают свет. Более того, если частица диоксида титана находится поблизости от одной из данных полостей, она будет рассеивать намного сильнее,чем, если она полностью окружена смолой, вследствие более высокого градиента коэффициента преломления. Это создает синергизм между новым фосфатом алюминия и диоксидом титана при рассмотрении кроющей способности. В тестах, сравнивающих сухую пленку стандартной краски и пленку с фосфатом алюминия, выбирали стандартную рыночную рецептуру полуматовой акриловой краски и диоксид титана постепенно заменяли описанным здесь новым продуктом фосфата алюминия. Содержание воды и другие компоненты краски регулировали, как требуется. Некоторые из модификаций в рецептуре в данном варианте осуществления имеют отношение к сниженному использованию загустителя/модификатора реологии, диспергатора, акриловой смолы и коалесцирующего агента. Табл. 4 описывает пример одной из рецептур,используемой в данном эксперименте, вместе с соответствующей рецептурой для нового фосфата алюминия. Таблица 3. Стандартная рецептура краски, используемая в настоящее время на рынке, и соответствующая рецептура, использующая фосфат алюминия. Количества даются в граммах В приведенной выше рецептуре была достигнута замена 50% TiO2 (по массе), сохраняя условия кроющей способности и белизны сухой пленки. Кроме того, исследовали другие свойства нового продукта, как модификатора реологии и пленкоструктурирующего агента. Сравнение между двумя приведенными выше рецептурами показывает, что пигменты, изготовленные согласно вариантам осуществления изобретения будут приводить к дополнительному снижению стоимости помимо снижения, получен- 15024005 ного вследствие замены пигмента, представляющего собой диоксид титана. Более того, такие доходы можно получить, в то же время, получая лучшие характеристики в нанесенной пленке краски. Описанное здесь изобретение также можно использовать для замены до 100% TiO2, и включая данное количество,фосфатом алюминия, полифосфатом алюминия, метафосфатом алюминия (или их смесями). Из предшествующего описания различных вариантов осуществления изобретения можно наблюдать, что новые продукт и способ отличаются от существующих фосфатов, полифосфатов и метафосфатов алюминия в нескольких аспектах. Например, поскольку его стехиометрия не является определенной,можно приготовить различные рецептуры изобретения, изменяя способ изготовления и, таким образом,композицию конечного продукта. Поскольку изобретение осуществляют при контролируемых уровнях рН, композиция является почти нейтральной, таким образом, избегая загрязнения окружающей среды и токсикологических проблем. Кроме того, изобретение может также быть свободно от проблем коррозии, связанных с некоторыми фосфатами алюминия, встречающимися на рынке и используемыми при превращении оксидов железа в фосфаты железа. Кроме того, нестехиометрия вместе с относительной некристалличностью (как в суспензии, так и порошкообразной форме) и тщательно контролируемое водосодержание сухого порошка позволяет легко контролировать набухание, что является полезным для его эксплуатационных характеристик. Частицы наноразмера легко диспергируются, и они стабильны относительно осаждения, что позволяет получать однородные дисперсии краски. Кроме того, наночастицы могут быть весьма совместимы с частицами латекса посредством механизмов капиллярной адгезии (в стадии сушки дисперсии), после чего следует опосредованная ион-кластерами электростатическая адгезия (в сухой пленке) - во многих случаях могут быть получены взаимно непрерывные сетки. Наконец, новый продукт также весьма совместим со многими другими порошкообразными твердыми веществами, обычно используемыми в качестве наполнителей краски, такими как различные силикаты, карбонаты и оксиды, встречающиеся в рецептированных дисперсиях на водной основе, что может внести вклад в когезию и прочность сухой пленки краски. Таким образом, описанное здесь изобретение использует различное сырье, что предлагает дополнительные преимущества, делая способ более экономичным и давая удивительные результаты. Здесь описываются очистка, обесцвечивание и очистка фосфорной кислоты, широко распространенной в промышленности по производству удобрений. Фосфорная кислота, как правило, доступна по цене, которая является частью цены используемых ранее фосфатов или метафосфатов. Поскольку фосфорная кислота является исходным веществом, которое типично имеет наиболее высокую стоимость, используемую при производстве пигмента, представляющего собой фосфаты алюминия, использование сорта кислоты дает важное снижение стоимости изготовления фосфатов алюминия. Такой способ делает реальным широкое принятие данных пигментов. Кроме того, определенные особенности описанного здесь изобретения представляют новые пути использования фосфатов алюминия, например, в дисперсии или во влажном порошке. Данные новые методы предоставляют важные технологические выигрыши. Например, новые способы и продукты предотвращают проблемы агрегации частиц, которые ухудшают эксплуатационные характеристики пигмента и снижают его кроющую способность. Кроме того, новый способ и продукт исключает проблемы дисперсии частиц в частицах латекса, используемых при изготовлении красок на водной основе, облегчая способы использования фосфата алюминия в красках для внутренних работ. Далее, новые способы и продукты не требуют стадий исчерпывающей сушки фосфата, которые увеличивают сложность и стоимость изготовления. Другой положительный аспект описанного здесь нового способа состоит в том, что его можно рассматривать продуктом "зеленой химии" с нулевыми промышленными отходами, поскольку его изготавливают при умеренных условиях температуры и давления, что не создает проблем для окружающей среды в течение процесса изготовления. Вследствие своей химической природы остатки, создаваемые описанным новым способом, можно безопасно сбрасывать в окружающую среду в виде компонента удобрений. Его производят в виде суспензии, а также в виде сухого порошка. В обоих случаях он легко диспергируется в воде, образуя стабильные дисперсии, которые обладают стабильными реологическими свойствами. Как продемонстрировано выше, варианты осуществления изобретения предлагают новый способ получения аморфного фосфата алюминия. В то время как изобретение было описано относительно ограниченного ряда вариантов осуществления, конкретные черты одного варианта осуществления не следует приписывать другим вариантам осуществления изобретения. Никакой один вариант не является типичным представителем всех аспектов изобретения. В некоторых вариантах осуществления композиции или способы могут включать многочисленные соединения или стадии, не указанные в настоящем описании. В других вариантах осуществления композиции и способы не включают, или по существу не содержат,какие-либо соединения или стадии, не перечисленные в настоящем описании. Существуют разновидности и модификации, отличающиеся от описанных вариантов осуществления. Описан способ изготовления смолы, включающий ряд действий или стадий. Данные стадии или действия могут быть осуществлены на практике в любой последовательности или порядке, если не указано иным образом. Наконец, любое число, описанное здесь, следует истолковывать как среднее приближение, независимо от того, ис- 16024005 пользуется ли слово "примерно" или "приблизительно" при описании данного числа. Прилагаемая формула изобретения имеет намерение охватить все данные модификации и изменения, как попадающие в объем защиты изобретения. ФОРМУЛА ИЗОБРЕТЕНИЯ 1. Композиция фосфата алюминия для покрытий, содержащая фосфат алюминия, полифосфат алюминия, метафосфат алюминия или их смесь, и компонент, выбранный из солей натрия, калия и аммония,где композиция включает частицы, которые имеют среднее значение радиуса частицы от 10 до 40 нм, и,по меньшей мере, некоторые из частиц имеют в среднем одну или более закрытых полостей на частицу,и композиция дополнительно характеризуется тем, что(a) обладает диспергируемостью в воде по меньшей мере 0,025 г на 1,0 г воды,(b) соотношение Р/Аl составляет от 1,1 до 1,5, соотношение P/Na составляет от 0,93 до 4,53 и соотношение Al/Na составляет 0,75 до 3,62. 2. Композиция по п.1, где композиция выбрана из группы композиций, характеризующихся следующими параметрами: 3. Композиция по п.1, где дифференциальная сканирующая калориметрия не показывает пика между 335 и 345 С. 4. Композиция по п.1, где композиция, будучи в виде суспензии, имеет рН в диапазоне примерно от 3,0 до 7,5. 5. Композиция по п.1, где композицию получают контактом комбинации веществ, включающих фосфорную кислоту, сульфат алюминия и щелочной раствор. 6. Композиция по п.1, где средний радиус отдельной частицы составляет от 10 до 40 нм. 7. Краска, лак, масляный лак, печатная краска или пластмасса, включающие композицию по любому из пп.1-6 в качестве ингредиента. 8. Краска, содержащая композицию фосфата алюминия по любому из пп.1-6, растворитель, связующий полимер. 9. Краска по п.8, где указанная краска также содержит диоксид титана и необязательные добавки,включающие загуститель, пластификатор, противопенная добавка, наполнитель, регулятор рН, тонирующий цвет и биоцид. 10. Краска по п.8, где указанный растворитель содержит воду. 11. Краска по п.8, где указанный растворитель содержит полярный растворитель. 12. Краска по п.8, где указанный растворитель содержит неполярный растворитель. 13. Краска по п.8, где указанный растворитель содержит органический растворитель. 14. Способ получения краски, включающий следующие стадии: объединение растворителя и композиции по любому из пп.1-6. 15. Способ получения краски по п.14, где способ дополнительно включает следующие стадии: одновременное смешивание фосфорной кислоты, сульфата алюминия и гидроксида натрия и обеспечение взаимодействия смешанных материалов друг с другом в течение приблизительно 30 мин с образованием осадка; высушивание осадка при температуре в диапазоне от комнатной температуры до 135 С, предпочтительно между 40 и 130 С с образованием композиции аморфного фосфата алюминия по пп.1-6, содержащей частицы, имеющие одну или более закрытых полостей на частицу, обладающие диспергируемостью в воде по меньшей мере 0,025 г на 1,0 г воды, и соотношением Р/Аl от 1,1 до 1,5, соотношением
МПК / Метки
МПК: C09D 1/00, C01B 25/36
Метки: частицы, красках, пигментов, метафосфата, полифосфата, способ, использование, качестве, фосфата, получения, алюминия
Код ссылки
<a href="https://eas.patents.su/21-24005-chasticy-fosfata-polifosfata-i-metafosfata-alyuminiya-ih-ispolzovanie-v-kachestve-pigmentov-v-kraskah-i-sposob-ih-polucheniya.html" rel="bookmark" title="База патентов Евразийского Союза">Частицы фосфата, полифосфата и метафосфата алюминия, их использование в качестве пигментов в красках и способ их получения</a>
Предыдущий патент: Способ получения (1-циклопропил-6-фтор-1,4-дигидро-8-метокси-7-[(4as,7as)-октагидро-6h-пирроло[3,4-b]пиридин-6-ил]-4-оксо-3-хинолинкарбоновой кислоты
Следующий патент: Ингибиторы е1 активирующих ферментов
Случайный патент: Способ получения 5-(2-{[6-(2,2-дифтор-2-фенилэтокси)гексил]амино}-1-гидроксиэтил)-8-гидроксихинолин-2(1h)-oha