Способ получения твердой металлоценовой каталитической системы и ее применение при полимеризации олефинов
Формула / Реферат
1. Способ получения твердой каталитической системы для полимеризации олефина, включающей металлоорганическое соединение переходного металла группы 3-10 Периодической таблицы (IUPAC 2007) в форме твердых частиц, включающий стадии
I) получения эмульсии диспергированием жидкого клатрата в растворителе (S), где
(i) растворитель (S) составляет непрерывную фазу эмульсии и включает инертное фторированное синтетическое масло с вязкостью при температуре 20°C согласно ASTM D445 по меньшей мере от 10 сСт вплоть до 2000 сСт;
(ii) жидкий клатрат в форме капель составляет дисперсную фазу эмульсии, и
II) отверждения указанной дисперсной фазы для превращения указанных капель в твердые частицы, где жидкий клатрат включает
(а) кристаллическую решетку, представляющую продукт реакции
a1) соединения переходного металла с формулой (I)

где T представляет переходный металл любой из групп 3-10 Периодической таблицы (IUPAC 2007),
каждый X независимо представляет моновалентный лиганд,
каждый L независимо представляет органический лиганд, который образует координационные связи с переходным металлом (Т) и представляет собой
(α) замещенный или незамещенный циклоалкилдиен, или
(β) ациклический η1-, ациклический η2-, ациклический η3-, ациклический η4- или ациклический η6-лиганд, включающий атомы из групп 13-16 Периодической таблицы (IUPAC 2007), или
(γ) циклический s-, циклический η1-, циклический η2-, циклический η3-, циклический η4- или ациклический η6-, моно-, би- или мультидентатный лиганд, включающий незамещенные или замещенные моно-, би- или мультициклические кольцевые системы, выбранные из ароматических, или неароматических, или частично насыщенных кольцевых систем и содержащие углеродные атомы колец, при этом, когда органические лиганды (L) замещены, по меньшей мере один органический лиганд (L) включает один или более остаток, независимо выбранный из группы, состоящей из галогена, C1-C10 алкила, C2-C20 алкенила, C2-C20 алкинила, C3-C12 циклоалкила, C6-C20 арила, C7-C20 арилалкила, C3-C12 циклоалкила, который содержит 1, 2, 3 или 4 гетероатома в кольцевой функциональной группе, и C1-C20 галоалкила,
R представляет мостиковую группу, соединяющую указанные органические лиганды (L), при этом мостиковая группа имеет формулу (II)

где Y представляет собой С, Si или Ge и
R', R" независимо выбран из группы, состоящей из C1-C20 алкила, C4-C10 циклоалкила, C6-C12 арила, C7-C12 арилалкила или триметилсилила,
m представляет 2 или 3,
n представляет 0, 1 или 2,
q представляет 1, 2 или 3,
m+q равно валентности переходного металла (Т),
a2) сокатализатора, включающего алюмоксан,
a3) соединения, эффективного для образования кристаллической решетки при использовании соединения переходного металла и/или алюмоксана,
при этом указанное соединение, эффективное для образования клатратов с алюмоксаном и/или соединением переходного металла, представляет собой M-X соединение, кремнийорганическое соединение или галосилоксан,
при этом M-X соединение представляет собой органическое, неорганическое или металлоорганическое соединение, которое потенциально может диссоциировать или частично диссоциировать на катионные и анионные компоненты, и выбрано из группы, состоящей из щелочных и щелочно-земельных галидов или псевдогалидов, анионной углеводородной группы, металлогидридов и алкил, арил и алкил-арил аммония, фосфония и сульфония, солей галидов и псевдогалидов,
при этом кремнийорганическое соединение выбрано из группы гидрокарбилоксисиланов с формулой R3Si-O[-SiR2-O]n-SiR3 или Si-[O-R]4, где R независимо представляет группу нециклического углеводородного остатка с вплоть до около 18 атомов углерода и n представляет в пределах от 0 до 3; и
гидрокарбилполисилоксанов с в пределах от 2 до 6 атомами кремния в молекуле, которые отделены друг от друга атомом кислорода таким образом, что представляет линейный, разветвленный или циклический скелет из чередующихся атомов Si и кислорода, где оставшиеся от четырех валентных связей каждого из атомов кремния непосредственно связаны с одновалентным остатком нециклической углеводородной группы R, независимо представляющим группу нециклического углеводородного остатка с вплоть до около 18 атомов углерода, и
b) углеводородный растворитель (HS), выбранный из группы, состоящей из линейного алкана, циклического алкана, линейного алкена, циклического алкена, ароматического углеводорода.
2. Способ по п.1, включающий также стадию удаления указанных твердых частиц для получения указанной каталитической системы.
3. Способ по п.1 или 2, где
(a) лиганды (X) независимо выбраны из группы, состоящей из водорода, галогена, C1-C20 алкила, C1-C20 алкокси, C2-C20 алкенила, С2-С20 алкинила, C3-C12 циклоалкила, C6-C20 арила, C6-C20 арилокси, C7-C20 арилалкила, С7-С20 арилалкенила, -SR", -PR''3, -SiR''3, -OSiR''3 и -NR''2, где каждый R" независимо представляет водород, C1-C20 алкил, C2-C20 алкенил, C2-C20 алкинил, C3-C12 циклоалкил или C6-C20 арил; и/или
(b) по меньшей мере один органический лиганд (L) независимо выбран из группы, состоящей из незамещенного циклопентадиенильного лиганда, замещенного циклопентадиенильного лиганда, незамещенного инденильного лиганда, замещенного инденильного лиганда, незамещенного флуоренильного лиганда и замещенного флуоренильного лиганда.
4. Способ по любому из предшествующих пунктов, где переходный металл (Т) представляет цирконий (Zr), гафний (Hf) или титан (Ti).
5. Способ по любому из предшествующих пунктов, где по меньшей мере один органический лиганд (L) включает один или более остаток, независимо выбранный из группы, состоящей из галогена, C1-C20 алкила, C2-C20 алкенила, C2-C20 алкинила, C3-C12 циклоалкила, C5-C20 циклоалкила, замещенного C1-C20 алкилом, где циклоалкильный остаток замещен C1-C20 алкилом, C6-C20 арилом, C7-C20 арилалкилом, C3-C12 циклоалкилом, который содержит 1, 2, 3 или 4 гетероатома в кольцевой функциональной группе, и C1-C20 галоалкила.
6. Способ по любому из предшествующих пунктов, где указанный алюмоксан а2) представляет метилалюмоксан.
7. Способ по п.1, где M-X соединение выбирают из группы, состоящей из KCl, KF, NaF, KH, LiH, KOSiR3, NaBPh4, Me4NCl, (октил)3NClMe, MePh3PBr, KB(C6F5)4 и K+CH2Ph-.
8. Способ по любому из пп.1-7, где жидкий клатрат получен
(i) получением смеси углеводородного растворителя (HS), алюмоксана и соединения, образующего клатрат (a3),
(ii) добавлением в указанную смесь соединения переходного металла с формулой (I),
(iii) получением двухфазной системы, где верхняя фаза представляет фазу, богатую углеводородным растворителем (HS), а нижняя фаза представляет фазу жидкого клатрата, и
(iv) отделением нижней фазы жидкого клатрата от верхней фазы, богатой углеводородным растворителем (HS).
9. Способ по любому из предшествующих пп.1-7, где жидкий клатрат получен
(i) получением раствора углеводородного растворителя (HS), алюмоксана и соединения переходного металла с формулой (I),
(ii) добавлением в указанный раствор соединения, образующего клатрат (a3),
(iii) получением двухфазной системы, где верхняя фаза представляет фазу, богатую углеводородным растворителем (HS), а нижняя фаза представляет фазу жидкого клатрата,
(iv) отделением нижней фазы жидкого клатрата от верхней фазы, богатой углеводородным растворителем (HS).
10. Способ по любому из предшествующих пп.1-9, где углеводородный растворитель (HS) представляет ароматический углеводород, и/или инертное фторированное синтетическое масло, используемое в качестве растворителя (S), представляет перфторполиэфир, политрихлорфторэтилен, фторсиликон или их комбинации с вязкостью при температуре 20°C согласно ASTM D445 по меньшей мере в пределах от 10 сСт вплоть до 2000 сСт.
11. Способ по любому из предшествующих пунктов, где растворитель (S) представляет перфторполиэфиры с формулой:
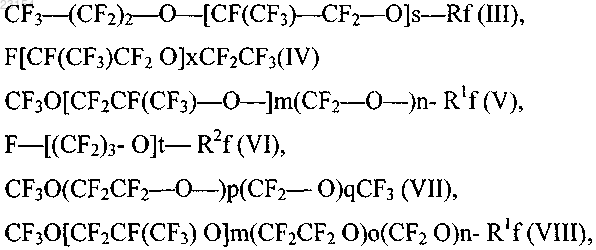
или комбинации двух или более из них;
где s представляет целое число в пределах 2-100; Rf представляет CF2CF3, C3-C6 перфторалкильную группу или их комбинации; х представляет целое число в пределах от 10 до 60; R1f представляет CF3, C2F5, C3F7 или комбинации двух или более из них; (m+n) представляет 8-45 включительно; (m+n+o) представляет 8-45 включительно; m/n представляет 20-1000 включительно; о представляет > 1; R2f представляет CF3, C2F5 или их комбинации; t представляет 2-200 включительно; (p+q) представляет 40-180 включительно; и p/q представляет 0,5-2 включительно, при условии, что перфторполиэфир имеет вязкость при температуре 20°C согласно ASTM D445 в пределах по меньшей мере от 10 сСт вплоть до 2000 сСт.
12. Способ по п.11, где перфторполиэфир имеет формулу (III) или (IV).
13. Способ по п.12, где перфторполиэфир имеет формулу (IV).
14. Способ по любому из предшествующих пунктов, где отверждение происходит за счет испарения углеводородного растворителя (HS) инертным газом.
15. Способ по п.1, где стадию отверждения проводят в той же емкости, что и стадию эмульгирования.
16. Применение перфторполиэфира в качестве растворителя для получения непрерывной фазы эмульсии в комбинации с соединением, эффективным для образования клатратов с алюмоксаном и/или соединением переходного металла с формулой (I), при этом перфторполиэфир имеет формулу:

или комбинации двух или более из них;
где s представляет целое число в пределах 2-100; Rf представляет CF2CF3, C3-C6 перфторалкильную группу или их комбинации; х представляет целое число в пределах от 10 до 60; R1f представляет CF3, C2F5, C3F7 или комбинации двух или более из них; (m+n) представляет 8-45 включительно; (m+n+o) представляет 8-45 включительно; m/n представляет 20-1000 включительно; о представляет >1; R2f представляет CF3, C2F5 или их комбинации; t представляет 2-200 включительно; (p+q) представляет 40-180 включительно; и p/q представляет 0,5-2 включительно, при условии, что перфторполиэфир имеет вязкость при температуре 20°C согласно ASTM D445 в пределах по меньшей мере от 10 сСт вплоть до 2000 сСт.
Текст
СПОСОБ ПОЛУЧЕНИЯ ТВЕРДОЙ МЕТАЛЛОЦЕНОВОЙ КАТАЛИТИЧЕСКОЙ СИСТЕМЫ И ЕЕ ПРИМЕНЕНИЕ ПРИ ПОЛИМЕРИЗАЦИИ ОЛЕФИНОВ Способ получения твердой каталитической системы для полимеризации олефина, включающей металлоорганическое соединение переходного металла группы 3-10 Периодической таблицы(IUPAC 2007) в форме твердых частиц, включающий стадии I) получения эмульсии диспергированием жидкого клатрата в растворителе (S), где (i) растворитель (S) составляет непрерывную фазу эмульсии и включает инертное фторированное синтетическое масло с вязкостью при температуре 20C согласно ASTM D445 по меньшей мере от 10 сСт вплоть до 2000 сСт;(ii) жидкий клатрат в форме капель составляет дисперсную фазу эмульсии, II) отверждения указанной дисперсной фазы для превращения указанных капель в твердые частицы и III) необязательно удаления указанных частиц с получением указанной каталитической системы, где жидкий клатрат включает (а) кристаллическую решетку, представляющую продукт реакции a1) соединения переходного металла с формулой (I) где T представляет переходный металл любой из групп 3-10 Периодической таблицы (IUPAC 2007),предпочтительно переходный металл любой из групп 4-6 Периодической таблицы (IUPAC 2007),более предпочтительно титан (Ti), цирконий (Zr) или гафний (Hf), то есть цирконий (Zr) или гафний (Hf), каждый X независимо представляет моновалентный -лиганд, каждый L независимо представляет органический лиганд, который образует координационные связи с переходным металлом (Т), R представляет мостиковую группу, соединяющую указанные органические лиганды(L), m представляет 2 или 3, предпочтительно 2, n представляет 0, 1 или 2, предпочтительно 1, q представляет 1, 2 или 3, предпочтительно 2, m+q равно валентности переходного металла(Т), a2) сокатализатора, включающего алюмоксан, a3) соединения, эффективного для образования кристаллической решетки при использовании соединения переходного металла и/или алюмоксана и b) углеводородный растворитель (HS). Изобретение относится к улучшенному способу получения твердой металлоценовой каталитической системы при использовании технологии эмульсия/отверждение и применению каталитической системы при полимеризации олефина. В частности, настоящее изобретение относится к получению твердой металлоценовой каталитической системы при использовании технологии эмульсия/отверждение, где жидкий клатрат составляет дисперсную фазу эмульсии, а инертное фторированное синтетическое масло с вязкостью при температуре 20C согласно ASTM D445 по меньшей мере 10 сСт используют в качестве непрерывной фазы. Предшествующий уровень техники Известно множество катализаторов и способов получения олефиновых полимеров. Например, для получения полиолефинов используют композиции катализатора Циглера-Натта - (ZN) и соединения оксида хрома. Дополнительно, использование металлоценовых катализаторов при полимеризации олефинов известно в течение многих лет, и было обнаружено, что при использовании катализаторов ZN не легко придать полимерам заданные свойства. Металлоценовые соединения/прокатализаторы традиционно активируют при использовании сокатализатора, такого как алюмоксан, известного из литературы для активации металлоценовых катализаторов. Первые разработанные катализаторы с единым центром полимеризации на металле представляли гомогенные, то есть их используют в растворе в процессе полимеризации. Из-за множества недостатков гомогенных жидких систем при попытках решения проблем жидких каталитических систем было использовано несколько различных подходов. В настоящее время широко используются каталитические системы, включающие гетерогенные катализаторы, где каталитические компоненты находятся на подложке из наружного носителя. Такие каталитические системы описаны, например, Severn et al., Chem.Polymerisation Catalysts of Severn et al. Используемые носители имеют пористую структуру для облегчения импрегнирования подложкой катализатора. Как правило, материалы-носители представляют полимерные или неорганические подложки, наиболее типичными являются материалы на основе дихлорида кремния, алюминия или магния. Однако использование наружной подложки влечет дополнительные расходы, качество подложки должно тщательно контролироваться, и полимеры, полученные при использовании катализаторов на подложках, могут содержать остатки носителя, что может приводить к возникновению проблем. Например, это очень важный признак при применении в виде пленок, поскольку для полимеров,полученных при использовании катализаторов на подложках, в пленке могут быть видны остатки носителя. За последние годы были разработаны твердые металлоценовые каталитические системы, обладающие преимуществами обоих, и гомогенного, и гетерогенного катализаторов при использовании технологии эмульсия/отверждение для их получения без использования наружного носителя, как например, описано в WO 03/051934. Такие каталитические системы дополнительно характеризуются сферическими частицами с низкой пористостью. Получают каталитические системы такого типа при использовании технологии эмульсия/отверждение на основе эмульсионной системы жидкость/жидкость, включающей по меньшей мере две фазы, при этом частицы катализатора отделяют от дисперсной фазы эмульсии отверждением. Как описано в WO 03/051934. такой способ включает получение эмульсии, где непрерывная фаза, в которой раствор компонентов катализатора образует дисперсную фазу в форме капель, не смешивается с указанным раствором компонентов катализатора и выбрана из галогенированных органических растворителей, и последующее отверждение указанных капель, включающих компоненты катализатора, диспергированные в непрерывной фазе полученной эмульсии. Согласно описанию WO 03/051934 предпочтительно непрерывная фаза включает галогенированные органические растворители, по существу, фторированный органический растворитель и/или их функционализированные производные, еще более предпочтительно растворитель включает полуфторированный углеводород, высокофторированный углеводород или перфторуглерод и/или их функционализированные производные. По существу предпочтительно, чтобы указанный растворитель включал, предпочтительно состоял из перфторуглерода или его функционализированного производного, предпочтительно C3-C30 перфторалканов, -алкенов или -циклоалканов, более предпочтительно C4-C10 перфторалканов, -алкенов или-циклоалканов, по существу, предпочтительно перфторгексана, перфторгептана, перфтороктана или перфтор(диметилциклогексана) или их смеси. Согласно описанному способу такие каталитические системы получают эмульгированием раствора катализатора в холодных фторированных углеводородах, таких как перфтороктан (PFO) или перфтор 1,3-диметилциклогексан (PFC,) и затем отверждают капли смешиванием эмульсии с горячим PFO илиPFC. Затем отвержденные частицы отделяют от PFO или PFC и сушат в потоке инертного газа. Поскольку PFO и PFC очень легко испаряются, то некоторые из растворителей в этом процессе могут быть утрачены, и при транспортировке в процессе технологической обработки требуются дополнительные хими-1 023154 ческие реагенты. Дополнительно, PFO и PFC являются довольно дорогими растворителями, поэтому их потери в процессе технологической обработки не желательны. Дополнительно, для получения такой эмульсии и, в частности, также для сохранения морфологии капель на стадии отверждения, является обязательным применение поверхностно-активного вещества. Согласно описанию WO 03/051934 поверхностно-активное вещество предпочтительно на основе углеводородов (включая полимерные углеводороды с молекулярной массой вплоть до 10 000) необязательно прерывается гетероатом(ами), предпочтительно галогенированными углеводородами, необязательно с функциональной группой, предпочтительно полуфторированными углеводородами, высокофторированными углеводородами или перфторуглеродами, как известно из предшествующего уровня техники. В качестве альтернативы и как видно из цитированных документов предшествующего уровня техники, поверхностно-активное вещество получают in-situ за счет реакции предшественника поверхностноактивного вещества с соединением жидкого катализатора. Указанный предшественник поверхностноактивного вещества может представлять галогенированный углеводород по меньшей мере с одной функциональной группой, например, высокофторированный C1-C30 спирт по меньшей мере с одной функциональной группой, выбранной из -OH, -SH, -NH2, -COOH, -COONH2, оксидов алкенов, оксогрупп и/или любого реакционноспособного производного этих групп, которое вступает в реакцию, например, с компонентом сокатализатора, такого как алюмоксан. Применение поверхностно-активных веществ существенно улучшает процесс получения и имеет явное преимущество для морфологии катализатора. Однако в некоторых случаях поверхностно-активные вещества могут быть недостаточно эффективны для стабилизации эмульсии, и следовательно, морфология не сохраняется на заданном уровне. Дополнительно, из-за многих факторов, оказывающих воздействие на конечный результат, может требоваться контроль процессов образования in-situ поверхностноактивного вещества. Дополнительно, использование таких высоко реакционноспособных фторированных соединений считается проблематичным с точки зрения HSE (здоровья, безопасности и окружающей среды), так что доступность этих соединений в будущем не гарантируется. Многие каталитические системы по предшествующему уровню техники имеют недостатки, состоящие в их склонности до некоторой степени растворяться в среде, в которой происходит полимеризация, необходимой в суспензионных реакторах, и следовательно, морфология каталитических систем ухудшается, что в свою очередь вызывает загрязнение и расслаивание в реакторах. Для решения указанных выше недостатков, связанных с растворимостью каталитических систем, в уровне техники предлагается катализатор предварительной полимеризации, обеспечивающий высокую степень контроля, как часть катализатора. Дополнительно к тому, что она требует контроля, предварительная полимеризация увеличивает расходы при промышленном производстве. Следовательно, продолжает существовать острая потребность в разработке способов получения твердых металлоценовых каталитических систем, однако без какой-либо наружной подложки по технологии эмульсия/отверждение при использовании более экологичных, безопасных и здоровых материалов, что решит проблемы каталитических систем но предшествующему уровню техники. Следовательно, объект настоящего изобретения относится к улучшенному и подходящему способу получения твердых металлоценовых каталитических систем при использовании технологии эмульсия/отверждение без необходимости использования материалов наружной подложки, которые делают возможным получение полимеров эффективным способом, то есть использование твердых каталитических систем, которые менее растворимы в среде, в которой происходит полимеризация, и получены более дружественным для окружающей среды способом, соответственно, могут быть использованы более безопасные материалы. Дополнительно, объект настоящего изобретения каталитическая система позволяет эффективным способом получить полимеры с высокой насыпной плотностью с узким распределением размера частиц. Находка настоящего изобретения состоит в том, что твердая каталитическая система должна быть получена на основе технологии эмульсия/отверждение, в которой жидкий клатрат составляет дисперсную фазу эмульсии, а жидкий растворитель, используемый в качестве непрерывной фазы эмульсии,представляет инертное фторированное синтетическое масло с вязкостью при температуре 20C согласноASTM D445 по меньшей мере 10 сСт. В частности, находка настоящего изобретения состоит в использовании инертного фторированного синтетического масла в качестве непрерывной фазы, что позволяет избежать добавления отдельного поверхностно-активного вещества и позволяет получить твердую каталитическую систему с очень узким распределением размера частиц. Следовательно, объект настоящего изобретения относится к способу получения твердой каталитической системы для полимеризации олефина, включающей металлоорганическое соединение переходного металла группы 3-10 Периодической таблицы (IUPAC 2007) в форме твердых частиц, включающему стадииI) получение эмульсии диспергированием жидкого клатрата в растворителе (S), где(i) растворитель (S) составляет непрерывную фазу эмульсии и включает инертное фторированное синтетическое масло с вязкостью при температуре 20C согласно ASTM D445 по меньшей мере от 10 сСт вплоть до 2000 сСт;(ii) жидкий клатрат в форме капель составляет дисперсную фазу эмульсии,II) отверждение указанной дисперсной фазы для превращения указанных капель в твердые частицы иIII) необязательно удаление указанных частиц с получением указанной каталитической системы,где жидкий клатрат включаетa1) соединения переходного металла с формулой (I) где T представляет переходный металл любой из групп 3-10 Периодической таблицы (IUPAC 2007),предпочтительно переходный металл любой из групп 4-6 Периодической таблицы (IUPAC 2007), более предпочтительно титан (Ti), цирконий (Zr) или гафний (Hf), то есть цирконий (Zr) или гафний (Hf); каждый X независимо представляет моновалентный -лиганд; каждый L независимо представляет органический лиганд, который образует координационные связи с переходным металлом (T);R представляет мостиковую группу, соединяющую указанные органические лиганды (L);m+q равно валентности переходного металла (Т);a2) сокатализатора, включающего алюмоксан,a3) соединения, эффективного для образования кристаллической решетки при использовании соединения переходного металла и/или алюмоксана, иb) углеводородный растворитель (HS). Следовательно, дополнительный объект настоящего изобретения представляет применение растворителя (S), как приведено ниже в описании настоящей патентной заявки, для образования и стабилизации эмульсии, используемой при получении каталитической системы в комбинации с жидкими клатратами. Особенно следует отметить, что специфические выбранные растворители (S), использованные для получения каталитической системы по настоящему изобретению, например, являются более удобными материалами с точки зрения HSE. Дополнительно следует отметить, что специфический растворитель (S), используемый согласно настоящему изобретению, не являются летучим, что делает его значительно проще и безопаснее для транспортировки в процессе технологической обработки. Дополнительной находкой настоящего изобретения является то, что получают очень стабильные эмульсии без необходимости добавления отдельного поверхностно-активного вещества, и что могут быть получены сферические частицы катализатора с узким распределением размера частиц. Как дополнительное преимущество может быть указано то, что способ по настоящему изобретению может быть осуществлен простым способом, например, только в одной емкости и с простой стадией отверждения, как описано более детально ниже. Следовательно, способ получения по настоящему изобретению представляет экономически более привлекательную альтернативу для получения такого типа каталитических систем, описанных в настоящей патентной заявки. Далее существенные признаки настоящего изобретения описаны более детально. Используемый в описании настоящей патентной заявки термин "раствор" относится к двум или более веществам, гомогенно смешанным. По меньшей мере одно из веществ представляет растворитель, в котором растворены другие вещества (растворенные вещества). Используемый в описании настоящей патентной заявки термин "эмульсия" относится к смеси по меньшей мерс двух жидких веществ. Одно вещество (дисперсная фаза) диспергирование в другом (непрерывная фаза) в виде капель. В настоящей патентной заявке непрерывная фаза представляет растворитель (S), а дисперсная фаза (в форме капель) представляет жидкий клатрат, содержащий компоненты катализатора. Используемый в описании настоящей патентной заявки термин "жидкость" относится к соединению (включая жидкость), представляющему жидкость при нормальном давлении (1 атмосфера) при комнатной температуре (то есть температуре в пределах от 20 до 25C). Используемый в описании настоящей патентной заявки термин жидкий клатрат относится к жидкости, включающей, предпочтительно состоящей из кристаллической решетки и углеводородного растворителя (US) в качестве гостя (G), заключенного в ней. Жидкие клатраты хорошо известны и, например, описаны Atwood, Jerry L. Dep. Chem., Univ. Alabama, Tuscaloosa, AL, USA. Editor(s): Robinson, Gregory Heagward.; Coord. Chem. Alum. (1993), p. 197-32. Publisher: VCH, New York. N. Y CODEN: 59ECAIConference; General Review written in English. CAN 119:117290;, John D. Holbrey, "Liquid clathrate formation in ionic liquid-aromatic mixtures", Chem. Commun., 2003, страницы 476 - 477, и Scott К. Spear, Encyclopedia of Supramolecular Chemistry, 2001, страницы 804 - 807. Следовательно, "жидкий клатрат" представляет жидкость, в которой кристаллическая решетка составляет суперструктуру, в которую встроен гость,то есть углеводородный растворитель (HS). Предпочтительно гость стабилизирует указанную суперструктуру. Дополнительным преимуществом клатрированных катализаторов по настоящему изобретению по сравнению со стандартными металлоценовыми катализаторами/катализаторами на основе МАО является низкая растворимость в растворителях, включая растворители, используемые при полимеризации, что может представлять самое большое дополнительное преимущество. Одна из находок настоящего изобретения состоит в том, что жидкий клатрат более стабилен, чем традиционные структуры катализатор/сокатализатор и, следовательно, менее растворим в предпочтительной для отверждения среде. Эта улучшенная стабильность открывает новые пути для превращения каталитических систем в жидкой форме на основе соединений переходного металла в твердые каталитические системы. Следовательно, один из существенных аспектов настоящего изобретения относится к твердому катализатору, полученному при использовании специфического жидкого клатрата. Следовательно, жидкий клатрат по настоящему изобретению включаетa1) соединения переходного металла с формулой (I) где T представляет переходный металл любой из групп 3-10 Периодической таблицы (IUPAC 2007),предпочтительно переходный металл любой из групп 4-6 Периодической таблицы (IUPAC 2007), более предпочтительно титан (Ti), цирконий (Zr) или гафний (Hf), то есть цирконий (Zr) или гафний (Hf); каждый X независимо представляет моновалентный -лиганд; каждый L независимо представляет органический лиганд, который образует координационные связи с переходным металлом (T);R представляет мостиковую группу, соединяющую указанные органические лиганды (L);m+q равно валентности переходного металла (T);a2) сокатализатора, включающего алюмоксан,a3) соединения, эффективного для образования кристаллической решетки при использовании соединения переходного металла и/или алюмоксана, иb) углеводородный растворитель (HS). Предпочтительно кристаллическая решетка образуется при реакции соединения (a3) с алюмоксаном(a2) и/или соединением переходного металла (a1) в углеводородном растворителе(HS). Далее будут более детально описаны отдельные реагенты. Как указанно выше, для образования кристаллической решетки жидкого клатрата необходимо соединение (a3), которое реагирует с алюмоксаном (a2) и/или соединением переходного металла (a1). Предпочтительно соединение (a3) представляет M-X соединение, кремнийорганическое соединение или соединение галосилоксана.M-X соединения, являющиеся эффективными для образования клатратов с алюмоксаном, представляют органические, неорганические или металлоорганические соединения, которые потенциально могут диссоциировать или частично диссоциировать на катионные (M+) и анионные компоненты (X-). Такие соединения представляют, например, описанные в WO 97/14700.M могут представлять щелочной или щелочно-земельный металл, такой как Na, K, Li, Mg или Ca.X могут представлять галид, такой как F, Cl или Br, псевдогалид или анионную группу, такую как аллильная углеводородная группа или бензильная углеводородная группа. Используемый в описании настоящей патентной заявки термин "псевдогалид" относится к функциональным группам, которые не являются галогенами, но, как правило, считаются легко замещаемыми группами в реакции замещения. Псевдогалиды могут включать, например, азиды, цианид, цианат, тиоцианат, изоцианат, изотиоцианат, кремниевые группы, серные группы, азотные группы, кислородные группы, борные группы и фосфорные группы. Не ограничивающие примеры представляют щелочные и щелочно-земельные галиды или псевдогалиды, такие как KCl, KF, LiCl, CaCl2, MgCl2, MgF2, NaF,KOSiR3, NaBO4, R представляет C1-C6-алкильный остаток или KR', где R' представляет аллильную углеводородную группу или бензильную углеводородную группу. Реакция таких M-X соединений с алюмоксаном и/или переходным металлом, предпочтительно в жидком углеводородном растворителе (HS), как детально описано ниже, приводит к образованию кристаллической решетки жидкого клатрата. Другие примеры M-X соединений включают металлогидридные, такие как KH, LiH и алкил, арил и алкил-арил аммония, фосфоний, сульфоний и другие металлоорганические соли галидов и псевдогалидов, таких как R4NCl, MePh3PBr, NaBPh4, KB(C6F5)4, LiR4Al, которые будут образовывать клатрат за счет реакций с алюмоксаном в углеводородных растворителях.R4 представляет C1-C8 алкильный остаток. Предпочтительными примерами используемых M-X соединений являются KCl, KF, NaF, LiCl,CaCl2, MgCl2, MgF2, KH, LiH, KOSiR3, NaBPh4, K+CH2Ph-, Me4NCl,(октил)3NClMe, MePh3PBr и KB(C6F5)4. Более предпочтительно используемые M-X соединения представляют KCl, KF, NaF, Me4NCl, (октил)3NClMe, KH, MePh3PBr, NaBPh4, K+CH2Ph- и KOSiMe3. Молярное соотношение алюминия, обеспеченного алюмоксаном, и М (катионной функциональной группы), обеспеченной M-X соединением, составляет в пределах от 1:1 до 50:1, предпочтительно в пределах от 5:1 до 30:1 и более предпочтительно в пределах от 8:1 до 25:1. Кремнийорганическое соединение, являющееся эффективным для образования кристаллической решетки с алюмоксаном (а 3) и/или соединением переходного металла, может быть выбрано из группы гидрокарбилоксисиланов с формулой R3Si-O[-SiR2-O]n-SiR3 или Si-[O-R], где R независимо представляет группу нециклического углеводородного остатка с вплоть до около 18 атомов (например, линейный или разветвленный алкил, циклоалкил, арил, арилалкил), и n представляет в пределах от 0 до 3; и гидрокарбилполисилоксанов с в пределах от 2 до 6 атомами кремния в молекуле, которые отделены друг от друга атомом кислорода, таким образом, что представляет линейный, разветвленный или циклический скелет из чередующихся атомов Si и кислорода, где оставшиеся от четырех валентных связи каждого из атомов кремния непосредственно связаны с одновалентным остатком нециклической углеводородной группы R,как указано выше. Предпочтительные группы нециклического углеводородного остатка R, представляют метил, этил и пентил. Примеры таких кремнийорганических соединений (OS) включают тетраметоксисиланы, тетра-этоксисиланы, тетрафеноксисилан, метокситриметилсилан, этокситриметилсилан,гексаметилдисилоксан, гексаэтилдисилоксан, гексафенилдисилоксан, тетраметилдифенилдисилоксан,диметилтетрафенилдисилоксан, гексаметилциклотрисилоксан, окстаметилциклотетрасилоксан, окстафенилциклотетрасилоксан, октаметилтрисилоксан, декаметилтетрасилоксан, додекаметилпентасилокеан и тетрадекаметилгексасилоксан. Предпочтительными кремнийорганическими соединениями (OS) являются окстаметилтрисилоксан,декаметилтетрасилоксан, октаметилциклотетрасилоксан, метокситриметилсилан и тетраэтоксисилан. Молярное соотношение алюминия, обеспеченного алюмоксаном, и кремнийорганического соединения составляет в пределах от 1:1 до 200:1, предпочтительно в пределах от 100:1 до 5:1 и более предпочтительно в пределах от 50:1 до 10:1. Подходящие галосилоксановые соединения, которые могут образовывать кристаллическую решетку с алюмоксаном (a3) и/или соединением переходного металла, представляют силоксаны с группами нециклического углеводородного остатка, которые могут содержать в пределах от 1 до 30 атомов углерода и включают линейные и/или разветвленные алкильные группы, которые содержат в пределах от 1 до 24 атомов углерода, циклоалкильные группы, которые содержат в пределах от около 3 до 24 атомов углерода, и алкиларильные или арильные группы, которые содержат в пределах от около 6 до 30 атомов углерода, и по меньшей мере одну группу нециклического углеводородного остатка силоксана, содержащую по меньшей мере один активный атом галогена. Силоксаны выбраны из дисилоксанов и линейных или циклических полисилоксанов. Силоксаны содержат Si-O-Si связь и, по существу, свободны отSi-OH связей. Силоксаны могут содержать смешанные группы нециклических углеводородных остатков. Полисилоксаны имеют линейные или разветвленные или циклические скелеты из чередующихся атомов кремния и кислорода. Такие галосилоксаны описаны, например, в US 2009/0088541. Предпочтительно используемое соединение (a3) представляет указанные выше кремнийорганические соединения. Используемый алюмоксан может представлять любой традиционный алюмоксан, известный из предшествующего уровня техники. Алюмоксаны коммерчески доступны или могут быть получены согласно литературе из предшествующего уровня техники, например, при использовании гидролиза алкилэфиров алюминия при непосредственном добавлении воды или обработке гидратами солей. Существует множество способов получения алюмоксанов и модифицированных алюмоксанов, не ограничивающие примеры которых приведены в US 4665208, US 4952540, US 5091352, US 5206199, US 5204419, US 4874734, US 4924018, US 4908463, US 4968827, US 5308815, US 5329032, US 5248801, US 5235081, US 5157137, US 5103031, US 5391793, US 5391529, US 5693838, US 5731253, US 5731451 US 5744656, EP-A0 561 476, EP-B1-0 279 586. EP-A-0 594-218, и WO 94/10180, каждая из которых введена здесь ссылкой в полном объеме. Также алюмоксаны известны, как алюминоксаны. Предпочтительно используют C1-C10 алкилалюмоксаны, в частности, метилалюмоксан или модифицированный метилалюмоксан, изобутилалюмоксан, например, TIBAO (тетраизобутилалюмоксан) илиHIBAO (гексаизобутилалюмоксан). Более предпочтительно алюмоксан (А) представляет метилалюмоксан (МАО). Наиболее предпочтительно МАО коммерчески доступный в виде в пределах от 5 до 30 мас.% рас-5 023154 твора в толуоле. Третье соединение, используемое для образования кристаллической решетки, представляет соединение переходного металла с формулой (I). В формуле (I) T представляет переходный металл группы 3-10 Периодической таблицы (IUPAC 2007), предпочтительно переходный металл любой из групп 4-6 Периодической таблицы (IUPAC 2007),более предпочтительно титан (Ti), цирконий (Zr) или гафний (Hf), то есть цирконий (Zr) или гафний (Hf),каждый X независимо представляет моновалентный -лигнад,каждый L независимо представляет органический лиганд, который образует координационные связи с переходным металлом (Т),R представляет мостиковую группу, соединяющую указанные органические лиганды (L),m представляет 2 или 3, предпочтительно 2,n представляет 0,1 или 2, предпочтительно 1,q представляет 1, 2 или 3, предпочтительно 2,m+q равно валентности переходного металла (T). Соединение переходного металла с формулой (I) LmRnTXq включает симметричные соединения наряду с ассиметричными соединениями, где по меньшей мере два лиганда L имеют различную химическую структуру. Каждый органический лиганд L предпочтительно независимо представляет(а) замещенный или незамещенный циклоалкилдиен, предпочтительно циклоалкилдиен, выбранный из группы, состоящей из незамещенного циклопентадиена, замещенного циклопентадиена, моноконденсированного производного циклопентадиена, биконденсированного производного циклопентадиена и мультиконденсированного производного циклопентадиена; или(b) ациклический 1-, ациклический 2-, ациклический 3-, ациклический 4- или ациклический 6 лиганд, включающий атомы из групп 13-16 Периодической таблицы (IUPAC 2007), предпочтительно ациклический 1-, ациклический 2-, ациклический 3-, ациклический 4- или ациклический 6-лиганд,включающий атомы из групп 13-16 Периодической таблицы (IUPAC 2007), где открыто-цепочечный лиганд может быть конденсирован с одним или двумя, предпочтительно двумя ароматическими или не ароматическими кольцами и/или несет дополнительные заместители; или(c) циклический -, циклический 1-, циклический 2-, циклический 3-, циклический 4- или ациклический 6-, моно-, би- или мультидентатный лиганд, включающий ненасыщенные или насыщенные моно-, би или мультициклические кольцевые системы, выбранные из ароматических или не ароматических или частично насыщенных кольцевых систем и содержащих углеродные атомы колец. Более предпочтительно по меньшей мере один из органических лигандов (L) выбирают из группы,состоящей из незамещенного циклопентадиенила, незамещенного инденила, незамещенного тетрагидроинденила, незамещенного флуоренила, замещенного циклопентадиенила. замещенного инденила, замещенного тетрагидроинденила и замещенного флуоренила. Дополнительно, в случае, когда органические лиганды (L) замещены, предпочтительно по меньшей мере один органический лиганд (L) включает(a) один или более остаток, независимо выбранный из группы, состоящей из галогена, C1-C10 алкила, C2-C20 алкенила, C2-C20 алкинила, C3-C12 циклоалкила, C6-C20 арила, C7-C20 арилалкила, C3-C12 циклоалкила, который содержит 1, 2, 3 или 4 гетероатома в кольцевой функциональной группе, C6-C20 гетероарила и C1-C20 галоалкила; или более предпочтительно(b) один или более остаток, независимо выбранный из группы, состоящей из галогена, C1-C10 алкила, C3-C12 циклоалкила, C6-C20 арила, C7-C20 арилалкила, C3 -C12 циклоалкила, который содержит 1, 2, 3 или 4 гетероатома в кольцевой функциональной группе, C6-C20 гетероарила и C1-C20 галоалкила. Используемый в описании настоящей патентной заявки термин "-лиганд" относится к группе, связанной с переходным металлом (M) в одном или более месте сигма-связью. Дополнительно, лиганды X предпочтительно независимо выбраны из группы, состоящей из водорода, галогена, C1-C20 алкила, C1-C20 алкокси, C2-C20 алкенила, C2 -C20 алкинила, C3-C12 циклоалкила, C6C20 арила, C6-C20 арилокси, C7-C20 арилалкила, C7-C20 арилалкенила, SR'-PR3, -SiR3, -OSiR3 и -NR2, где каждый R" независимо представляет водород,C1-C20 алкил, C2-C20 алкенил, C2-C20 алкинил, C3-C12 циклоалкил или C6-C20 арил. Дополнительно, мостиковая группа (R) может представлять мостик из в пределах от 1 до 7 атомов длиной, предпочтительно по меньшей мере с одним гетероатомом. По существу понятно, что мостиковая группа(ы) (R) имеет формулу (II) где Y представляет углерод (С), кремний (Si) или германий (Ge), иR', R" независимо выбран из группы, состоящей из C1-C20 алкила, C4-C10 циклоалкила, C6-C12 арила,C7-C12 арилалкила или триметилсилила. Следовательно, в предпочтительном варианте воплощения настоящего изобретения указанное соединение переходного металла с формулой (I) представляет группу соединений, известных как металло-6 023154 цены. Указанные металлоцены несут по меньшей мере один органический лиганд, как правило, 1, 2 или 3, например 1 или 2, который -связан с металлом, например, 2-6-лигандом, таким как 5-лиганд. Предпочтительно металлоцен но настоящему изобретению представляет переходный металл (M) любой из групп 4-6 Периодической таблицы (IUPAC), соответственно, титаноцен, цирконоцен или гафноцен, который содержит по меньшей мере один 5-лиганд, который является необязательно замещенным циклопентадиенилом, необязательно замещенным инденилом, необязательно замещенным тетрагидроинденилом или необязательно замещенным флуоренилом. Следовательно, соединение переходного металла предпочтительно имеет формулу (III) где T представляет цирконий (Zr), гафний (Hf) или титан (Ti), предпочтительно цирконий (Zr) или гафний (Hf), каждый X независимо представляет моновалентный анионный -лиганд, предпочтительно выбранный из группы, состоящей из водорода, галогена, C1-C20 алкила, C1-C20 алкокси, C2-C20 алкенила,C1-C20 алкинила, C3-C12 циклоалкила, C6-C20 арила, C6-C20 арилокси, C7-C20 арилалкила, C7-C20 арилалкенила, -SR", -PR3, -SiR"3, -OSiR"3 и -NR"2, где каждый R" независимо представляет водород, C1-C20 алкил,C2-C20 алкенил, C2-C20 алкинил, C3-C12 циклоалкил или C6-C20 арил, более предпочтительно каждый X представляет Cl,каждый Cp независимо представляет ненасыщенный органический циклический лиганд, который образует координационные связи с переходным металлом (Т),R представляет мостиковую группу, связывающую два органических лиганда (L), предпочтительно мостиковая группа (R) имеет формулу (II),n представляет 0 или 1, предпочтительно 1, и по меньшей мере один Ср-лиганд выбран из группы, состоящей из незамещенного циклопентадиенила, незамещенного инденила, незамещенного тетрагидроинденила, незамещенного флуоренила, замещенного циклопентадиенила, замещенного инденила, замещенного тетрагидроинденила и замещенного флуоренила, предпочтительно замещенного инденила. Соединение переходного металла с формулой (III) (Ср)2RnTX2 включает симметричные соединения наряду с ассиметричными соединениями, где оба Ср-лиганда имеют отличающуюся химическую структуру. Замещенный Ср-лиганд(ы) может иметь один или более заместитель(и) выбранный из группы, состоящей из галогена, нециклического углеводородного остатка (например, линейный C1-C20 алкил, разветвленный C3-C20 алкил, линейный C1-C20 алкенил, разветвленный C4-C20 алкенил, C2-C20 алкинил, C3C12 циклоалкил, C1-C20 алкил, замещенный C5-C20 циклоалкилом, C5-C20 циклоалкил, замещенный C1-C20 алкилом, где циклоалкильный остаток замещен C1-C20 алкилом, C6-C20 арил, C7-C20 арилалкил, C3-C12 циклоалкил, который содержит 1, 2, 3 или 4 гетероатома в кольцевой функциональной группе, C6-C20 гетероарил, C1-C20 галоалкил, -SiR"3, -SR", -PR2 или -NR"2, каждый R" независимо представляет водород или нециклический углеводородный остаток (например, C1-C20 алкил, C1-C20 алкенил, C2-C20 алкил, C3C12 циклоалкил или C6-C20 арил) или, например, в случае -NR"3, два заместителя R" могут образовывать кольцо, например, пяти или шестичленное кольцо вместе с атомом азота, с которым они соединены. Дополнительно R формулы (III) представляет предпочтительно мостик из в пределах от 1 до 7 атомов С, например, мостик из в пределах от 1 до 4 атомов и в пределах от 0 до 4 гетероатомов, где гетероатом(ы) могут, например, представлять атом(ы) кремния (Si), германия (Ge) и/или кислорода (О), при этом каждый из мостиковых атомов независимо может нести заместители, такие как C1-C20 алкил,три(C1-C20-алкил)силил, три(C1-C20-алкил)силокси или C6-C20 арил; или мостик в пределах от 1 до 3, например, один или два, гетероатомы, такие как атом(ы) кремния (Si), германия (Ge) и/или кислорода (О),например, -SiR12-, где каждый R1 независимо представляет C1-C20-алкил, C4-C10 циклоалкил, C6-C20 арил или три(C1-C20 алкил)силил- остаток, такой как триметилсилил-. Ср-лиганд формулы (III) предпочтительно представляет циклопентадиенил, инденил, тетрагидроинденил или флуоренил, необязательно замещенный, как указано выше, и дополнительно может нести конденсированное кольцо с в пределах от 3 до 7 атомов, например 4, 5 или 6, где кольцо может представлять ароматическое или частично насыщенное. В подходящей подгруппе соединений с формулой (III) каждый Ср-лиганд независимо несет один или более, такие как два, заместителя, выбранные из C1-C20 алкила, C5-C20 циклоалкила, замещенного C1C20 алкилом, где циклоалкильный остаток замещен C1-C20 алкилом, C6-C20 арила, C7-C20 арилалкила (где арильное кольцо одно или как часть дополнительной функциональной группы может быть замещено, как указано выше), где R" представляет, как указано выше, предпочтительно C1-C20 алкил, лиганд X представляет водород (Н), галоген, C1-C20 алкил, C1-C20 алкокси, C6-C20 арил, C7-C20 арилалкенил или -NR2,как указано выше, например, -N(C1-C20 алкил)2, и мостиковая группа R представляет метиленовый, этиленовый или силильный мостик, при этом силил может быть замещен, как указано выше, например, диметилсилил=, метилфенилсилил=, метилциклогексилсилил= или триметилсилилметилсилил. Конкретная подгруппа включает хорошо известные металлоцены Zr, Hf и Ti с одним или с двумя,например, двумя органическими лигандами (L), которые могут представлять соединенные мостиком или не соединенные мостиком циклопентадиенильные лиганды, необязательно замещенные, например, силокси, алкилом и/или арилом, как указано выше, или с двумя не соединенными мостиковой связью или соединенными мостиковой связью инденильными лигандами, необязательно замещенными по любой кольцевой функциональной группе 5, например, алкилом и/или арилом, как указано выше, например, по 2-, 3-, 4- и/или 7-иозициям. В качестве конкретных примеров могут быть указаны, например, бис(алкилциклопентадиенил) Zr (или Ti или Hf) дигалогениды, такие как бис-(n-бутилциклопентадиенил)ZrCl2 и бис-(n-бутилциклопентадиенил)HfCl2, смотрите, например, EP 129368. Одна из типичных металлоценовых функциональных групп рац-R2Si(2-Me-4-Phlnd)2ZrCl2, где каждый R независимо представляет линейный или циклический алкил с в пределах от 1-10 атомов С, и где Ph группа может быть необязательно замещена алкильной группой в пределах от 1 до 10 атомов, в качестве одного из примеров таковых может быть указан рац-Me2Si(2-Me-4-Phlnd)2ZrCl2, используемый для полимеризации полипропилена. Примеры соединений, где атом металла несет -NR"2 лиганд, приведены, например, в WO 98/56831 иWO 00/34341. Содержание документов введено ссылкой. Дополнительно, металлоцены описаны, например в EP 260 130. Дополнительные примеры используемых металлоценов также могут быть найдены вWO 97/28170, WO 98/46616, WO 98/49208, WO 99/12981, WO 99/19335, WO 98/56831, WO 00/34341, ЕР 423101 и EP 537130 наряду с V.С. Gibson et al., in Angew. Chem. Int. Ed., engl., vol 38,1999, стр. 428-447,описание каждого из которых введено здесь ссылкой. Указанные соединения переходного металла с формулой (I) и (III) представляют металлоценовый тип, и их получение хорошо известно из предшествующего уровня техники. По существу, предпочтительны металлоцены, указанные в описании настоящей патентной заявки. В качестве альтернативы, в дополнительной подгруппе металлоценовых соединений переходный металл (M) несет Ср-лиганд, как указано выше, и дополнительно 1- или 2-лиганд, где указанные лиганды могут быть или могут не быть соединены друг с другом мостиком. Эта подгруппа включает так называемые "скорпионатные соединения" (с ограниченной геометрией), в которых переходный металл(M) образует комплекс с 5-лигандом, соединенным мостиком с а 1- или 2-лигандом, предпочтительно 1- (например, -связанным) лигандом, например, металлический комплекс Ср-лиганда, как указано выше, например, циклопентадиенильная группы, которая несет через мостиковый элемент ациклическую или циклическую группу, содержащую по меньшей мере один гетероатом, например, -NR2, как указано выше. Такие соединения описаны, например, в WO 96/13529, содержание которой введено здесь ссылкой. Любой алкильный, алкенильный или алкинильный остаток, указанный выше, один или как часть функциональной группы, может быть линейным или разветвленным и содержит предпочтительно вплоть до 9, например, вплоть до 6 атомов углерода. Арил предпочтительно представляет фенил или нафталин. Галоген представляет F, Cl, Br или I, предпочтительно Cl. Другая подгруппа соединений переходных металлов с формулой (I), используемая в настоящем изобретении, известна как неметаллоцены, где переходный металл (M) (предпочтительно переходный металл группы 4-6, соответственно Ti, Zr или Hf) имеет координационный лиганд, иной, чем циклопентадиенильный лиганд. Используемый в описании настоящей патентной заявки термин "неметаллоцен" относится к соединениям, которые несут не циклопентадиенильные лиганды или их конденсированные производные, а один или более нециклопентадиенильных - или -, моно-, би- или мультидентатный лиганд. Такие лиганды могут быть выбраны, например, из(а) ациклических 1 - 4- или 6- лигандов, состоящих из атомов группы 13-16 Периодической таблицы (IUPAC), например ациклического пентадиенильного лиганда, где цепь состоит из атомов углерода и необязательно одного или более гетероатомов из группы 13-16 (IUPAC), и где открыто-цепочечный лиганд может быть конденсирован с одним или двумя, предпочтительно двумя ароматическими или не ароматическими кольцами и/или несет дополнительные заместители и/или несет дополнительные заместители (смотрите, например, WO 01/70395, WO 97/10248 и WO 99/41290); или(b) циклических -, 1- 4- или 6-, моно-, би- или мультидентатных лигандов, состоящих из незамещенных или замещенных моно-, би- или мультициклических кольцевых систем, например, ароматических или неароматических, или частично насыщенных кольцевых систем, содержащих углеродные атомы кольца и необязательно один или более гетероатом, выбранный из группы 15 и 16 Периодической таблицы (IUPAC) (см., например, WO 99/10353). Би- или мультидентатные кольцевые системы включают также мостиковые кольцевые системы, где каждое кольцо связано через мостиковую группу, например через атом групп 15 или 16 Периодической таблицы, например N, О или S, с атомом переходного металла (см., например, WO 02/060963). Примерами таких соединений являются, например, комплексы переходного металла (M) с циклическими или ациклическими алифатическими или ароматическими лигандами на основе азота, например, такие как те,которые описаны в более ранней заявке авторов настоящего изобретения WO 99/10353 или в обзоре V.C.Gibson at al. в Angew. Chem. Int. Ed., англ., vol. 38, 1999, стр. 428-447, или с лигандами на основе кислорода, такими как комплексы металлов группы 4, несущие бидентатные циклические или ациклические алифатические или ароматические алкоксидные лиганды, например, необязательно замещенные мостиковые бисфенольные лиганды (смотрите, например, указанный выше обзор Gibson at al.). Дополнительными специфическими примерами не-5-лигандов являются амиды, амиддифосфан, амидинато, аминопиридинат, бензамидинат, азациклоалкснил, такой как триазадициклоалкенил, аллил, бета-дикетимат и арилоксид. Описания указанных выше документов введены здесь ссылкой. Получение металлоценов и неметаллоценов и их органических лигандов, используемых в настоящем изобретении, хорошо отражено в предшествующем уровне техники и приведена ссылка, например,на процитированные выше документы. Некоторые из указанных выше соединений также коммерчески доступны. Таким образом, указанные соединения переходных металлов могут быть получены при использовании способов, описанных в литературе, например, сначала путем получения органической лигандной функциональной группы, а затем металлирования указанного органического лиганда (лиганда) переходным металлом. В качестве альтернативы ион металла уже присутствующего металлоцена может быть заменен на другой ион металла при использовании реакции переметаллирования. При использовании нескольких различных соединений переходного металла (смешанные двойные или мультикаталитические системы), они могут представлять любую комбинацию из указанных выше соединений переходного металла с формулой (I) или указанных выше соединений переходного металла с формулой (I) с другими каталитическими соединениями (включая, системы Циглера-Натта и системы оксида хрома), например, комбинация по меньшей мере двух или более металлоценов, металлоцена и не металлоцена наряду с металлоценом и/или не металлоценом с каталитической системой Циглера-Натта(который, как правило включает соединение переходного металла и соединение металла из группы 2 Периодической таблицы, такие как соединение Mg). Молярное соотношение алюминия, обеспеченного алюмоксаном (a3), и переходного металла Т составляет в пределах от 1 до 10 000, предпочтительно в пределах от 10 до 7000, например, в пределах от 100 до 4000, таком как от 100 до 2000, например в пределах от 100 до 1000. Как правило, в случае твердого (гетерогенного) катализатора соотношение предпочтительно составляет менее 500, такое как в пределах от 100 до 400. Количество сокатализатора, используемого в катализаторе по настоящему изобретению, варьирует в зависимости от условий и конкретного соединения переходного металла, выбранного способом, хорошо известным из предшествующего уровня техники, специалисту в области техники, к которой относится настоящее изобретение. Углеводородный растворитель (HS) может быть выбран из группы, состоящей из линейного алкана,циклического алкана, линейного алкена, циклического алкена, ароматического углеводорода и предпочтительно представляет ароматический углеводородный растворитель, такой как, например толуол, бензол, ксилены, этилбензол, кумол, мезитилен или цимол. Более предпочтительно углеводородный растворитель (HS) представляет толуол. Жидкий клатрат может быть получен, предпочтительно получен, получением сначала клатрата алюмоксана и реакцией этого предварительно полученного клатрата с соединением переходного металла с формулой (I) (вариант А) или проведением сначала реакции алюмоксана с соединением переходного металла с формулой (I) с последующим образованием клатрата (вараинт В). Следовательно в одном варианте воплощения настоящего изобретения (вариант А) жидкий клатрат может быть получен, предпочтительно получен,(i) получением смеси углеводородного растворителя (HS), алюмоксана и соединения, образующею клатрат (a3),(ii) добавлением в указанную смесь соединения переходного металла с формулой (I),(iii) получением двух фазной системы, где верхняя фаза представляет фазу богатую углеводородным растворителем (HS), а нижняя фаза представляет фазу жидкого клатрата, и(iv) отделением нижней фазы жидкого клатрата от верхней фазы богатой углеводородным растворителем (HS). В другом варианте воплощения настоящего изобретения (вариант В) жидкий клатрат может быть получен, предпочтительно получен,(i) получением раствора углеводородного растворителя (HS), алюмоксана и соединения переходного металла с формулой (I),(ii) добавлением в указанный раствор соединения, образующего клатрат (a3),(iii) получением двух фазной системы, где верхняя фаза представляет фазу богатую углеводородным растворителем (HS), а нижняя фаза представляет фазу жидкого клатрата,(iv) отделением нижней фазы жидкого клатрата от верхней фазы богатой углеводородным растворителем (HS). Вариант А. Согласно варианту А на стадии (i) соединение, образующее клатрат, добавляют в алюмоксан в молярном соотношении, как указанно выше, в углеводородный растворитель. Начальная концентрация алюмоксана в растворителе, по существу, не критична и, как правило, со-9 023154 ставляет в пределах от 5 до 30 мас.% раствора. В качестве растворителя используют углеводородный растворитель, как указанно выше, предпочтительно ароматический углеводородный растворитель, такой как, например, толуол, бензол, ксилены,этилбензол, кумол, мезитилен или цимол. Более предпочтительно используют толуол. Температуру реакции выбирают, таким образом, чтобы получить клатрат. Такая реакция характеризуется образованием двух фазной системы, включающей два стабильных не смешивающихся органических слоя, которые остаются интактными, таким образом, что верхний слой углеводородного растворителя может быть отделен от нижнего слоя, содержащего клатрат алюмоксана. Хотя очень удобно использовать комнатную температуру, то есть температуру в пределах от 0 до 30C, некоторые соединения требуют повышенной температуры, такой как вплоть до 80C или выше для образования клатрата. В других случаях некоторые соединения образуют клатраты при температуре вплоть до -25C. Специалист в области техники, к которой относится настоящее изобретение, может легко экспериментально определить подходящую температуру для любого из соединений, образующих клатрат. Предпочтительно для варианта А используют метилалюмоксан (МАО). Более предпочтительно используют коммерчески доступные растворы МАО в толуоле. Такие растворы доступны в виде от 5 до 30 мас.% растворов в толуоле. Преимущественно МАО клатрат образует нижний слой клатрата, а триметилалюминий (не прореагировавший исходный материал при получении МАО) экстрагируется в верхнюю богатую толуолом фазу, таким образом, что МАО клатрат предпочтительно содержит пониженное количество не прореагировавшего триметилалюминия. Количество алкилалюминия зависит от используемого клатрата, его содержания при синтезе и используемой температуры реакции. Специалист в области техники, к которой относится настоящее изобретение, может оптимизировать условия синтеза для достижения оптимального удаления не прореагировавшего триметилалюминия. Для дальнейшей технологической обработки нижнюю фазу, содержащую клатрат, отделяют от верхнего слоя растворителя при использовании традиционной технологии отделения, например, декантирование или осушение. Необязательно фаза отделенного клатрата алюмоксана может быть промыта перед дальнейшим использованием. Предпочтительно фазу клатрата промывают однократно или вплоть до 5 раз, предпочтительно однократно или вплоть до трех раз растворителем, используемым для ее получения. Предпочтительно для получения клатрата и для стадии промывания используют ароматический углеводородный растворитель, более предпочтительно толуол. Затем предварительно полученный клатрат вступает в реакцию с металлоорганическим соединением переходного металла с формулой (I), как указанно выше, предпочтительно реакцию проводят при перемешивании в инертной атмосфере, например, в атмосфере N2 или аргона при температуре в пределах от 10 до 40C, предпочтительно в пределах от 15 до 35C и более предпочтительно в пределах от 20 до 30C, например, при комнатной температуре. Вариант В. Согласно варианту В алюмоксан сначала вступает в реакцию с соединением переходного металла с формулой (I) в углеводородном растворителе, как указано выше. Затем полученный раствор далее вступает в реакцию с соединением, образующим клатрат, что приводит к образованию двух фазной системы,включающей стабильные не смешивающиеся органические слои, которые остаются интактыми, таким образом, что верхний слой ароматического растворителя может быть отделен от нижнего слоя, содержащего клатрат алюмоксана/переходного металла. Реакцию предпочтительно проводят при перемешивании в инертной атмосфере, например, в атмосфере N2 или аргона при температуре в пределах от 10 до 40C, предпочтительно в пределах от 15 до 35C и более предпочтительно в пределах от 20 до 30C, например, при комнатной температуре. Удаляют верхнюю фазу и нижнюю фазу необязательно промывают перед последующим использованием. Предпочтительно фазу, содержащую клатрат, промывают однократно или вплоть до 5 раз растворителем, используемым для его получения. Предпочтительно ароматическим углеводородом, более предпочтительно толуолом, используемым для получения клатрата и на стадии промывания. Следовательно, реакция по вариантам (А) и (В) характеризуется образованием двух фазной системы, включающей два стабильных не смешивающихся органических слоя, которые остаются интактными,таким образом, что верхний слой (представляющий слой богатый углеводородным растворителем (HS может быть отделен от нижнего слоя жидкого клатрата, то есть жидкого клатрата. Для дальнейшей технологической обработки фазу жидкого клатрата, то есть жидкий клатрат, отделяют от верхнего слоя растворителя при использовании традиционной технологии отделения, например,декантирование или осушение. Дополнительная находка настоящего изобретения состоит в том, что могут быть получены частицы твердого катализатора, которые удобны в процессе транспортировки при технологической обработке. Следовательно, в способе по настоящему изобретению используют специфический растворитель(S), включающий инертное фторированное синтетическое масло с вязкостью при температуре 20C со- 10023154 гласно ASTM D445 по меньшей мере 10 сСт. Дополнительно, использование комбинации жидкого клатрата и специфического растворителя (S) позволяет получить твердые каталитические системы с очень малой площадью поверхности и очень узким распределением размера частиц. Следовательно, дополнительный важный аспект настоящего изобретения относится к специфическому выбранному растворителю (S), который образует с жидким клатратом эмульсию. Следовательно, жидкий клатрат должен быть несмешиваемым или только частично смешиваемым(не более чем 20 мас.%, предпочтительно не более чем 10 мас.%, такое как не более чем 5 мас.% жидкого клатрата) с растворителем (S) при условиях (например, температура), используемых во время стадии (I). Кроме того, растворитель (S) также должен быть инертным в отношении соединений получаемой твердой каталитической системы. Используемый в описании настоящей патентной заявки термин"инертный в отношении соединений" означает, что растворитель (S), составляющий непрерывную фазу,химически инертен, то есть не вступает в химическую реакцию с каким-либо соединением, образующим твердую каталитическую систему, или соединением, образующим предшественник каталитической системы (например, соединение переходного металла и алюмоксана). Таким образом, твердые частицы каталитической системы или любого ее предшественника образуют капли из соединений, которые происходят из дисперсной фазы, то есть обеспеченны эмульсией в жидком клатрате, диспергированном в непрерывной фазе, образуемой растворителем (S). Растворитель (S) по настоящему изобретению представляет инертное фторированное синтетическое масло с вязкостью при температуре 20C согласно ASTM D445 по меньшей мере 10 сСт. Фторированное синтетическое масло предпочтительно имеет вязкость при температуре 20C (согласно ASTM D445) по меньшей мере 30 сСт, более предпочтительно по меньшей мере 100 сСт, еще более предпочтительно по меньшей мере 300 сСт, еще более предпочтительно по меньшей мере 400 сСт и наиболее предпочтительно по меньшей мере 700 сСт. Верхний предел ограничения вязкости при температуре 20C (согласно ASTM D445) используемого фторированного синтетического масла предпочтительно составляет 2000 сСт, более предпочтительно 1600 сСт и еще более предпочтительно 1000 сСт. Примеры таких фторированных синтетических масел без ограничения представляют фторированные полимеры простого эфира, фторированные и хлорированные полиэтилены, фторированные силиконы и их комбинации. Предпочтительно в качестве фторированных синтетических масел используют перфторполиэфиры,политрихлорфторэтилены, фторсиликоны или их комбинации, более предпочтительно используют перфторполиэфиры. В композиции настоящего изобретения может быть использован любой перфторполиэфир с вязкостью при температуре 20C (согласно ASTM D445) по меньшей мере от 10 сСт вплоть до 2000 сСт, известный специалисту в области техники, к которой относится настоящее изобретение. Общей характеристикой перфторполиэфиров, подходящих для настоящего изобретения, является наличие функциональных групп перфторалкильного эфира. Используемый в описании настоящей патентной заявки термин "перфторполиэфир" взаимозаменяем с "PFPE", "PFPE масло", "PFPE жидкость","PFAE" (перфторалкилэфир) или "PFPAE" (перфторполиалкилэфир), как известно специалисту в области техники, к которой относится настоящее изобретение. Подходящие перфторполиэфиры описаны, например, в WO 2007/082046, US 2007/049502, US 6528457, WO 00/18849 и так далее. Предпочтительный указанный перфторполиэфир выбран из группы, состоящей из перфторполиэфиров с формулой: или комбинации двух или более из них; гдеs представляет целое число в пределах 2-100; Rf представляет CF2CF3, C3-C6 перфторалкильную группу или их комбинации; х представляет целое число в пределах от 10 до 60; R1f представляет CF3,C2F5, C3F7 или комбинации двух или более из них; (m+n) представляет 8-45 включительно; (m+n+o) представляет 8-45 включительно; m/n представляет 20-1000 включительно; о представляет 1; R2f представляет CF3, C2F5 или их комбинации; t представляет 2-200 включительно; (p+q) представляет 40-180 включительно; и p/q представляет 0,5-2 включительно, при условии, что перфторполиэфир имеет вязкость при температуре 20C (согласно ASTM D445) в пределах по меньшей мере от 10 сСт вплоть до 2000 сСт, предпочтительно по меньшей мере от 30 сСт вплоть до 1600 сСт и более предпочтительно в пределах по меньшей мере от 100 сСт вплоть до 1000 сСт. Более предпочтительно используемый перфторполиэфир имеет формулу (I)CF3-(CF2)2-O-[CF(CF3)-CF2-O]s-Rf или формулу(II) F[CF(CF3)CF2O] CF2CF3 и вязкость при температуре 20C (согласно ASTM D445) в пределах по меньшей мере от 10 сСт вплоть до 2000 сСт, предпочтительно в пределах по меньшей мере от 30 сСт вплоть до 1600 сСт и более предпочтительно в пределах по меньшей мере от 100 сСт вплоть до 1000 сСт. Наиболее предпочтительно в качестве растворителя (В) используют перфторполиэфир с формулой(II) с вязкостью при температуре 20C (согласно ASTM D445) в пределах по меньшей мере от 10 сСт вплоть до 2000 сСт, предпочтительно в пределах по меньшей мере от 30 сСт вплоть до 1600 сСт и более предпочтительно в пределах по меньшей мере от 100 сСт вплоть до 1000 сСт. Приведенные в качестве примера перфториолиэфиры, которые могут быть использованы в настоящем изобретении и имеют указанные выше формулы (I)-(V), доступны на рынке под торговыми маркамиFOMBLIN и GALDEN (от Ausimont, Milan, Italy), KRYTOX (от Е. I. du Pontde Nemours and Company, Wilmington, Delaware), и DEMNUM (от Daikin, Osaka, Japan). Таким образом, используемые и коммерчески доступные масла представляют перфторполиэфиры,продающиеся под торговой маркой Krytox от E.I. du Pont de Nemours and Company, и в частности, серии масел Krytox GPL или FG (пищевые масла Krytox), которые отвечают требованиям вязкости, как указано выше, то есть имеющие вязкость при температуре 20C (согласно ASTM D445) по меньшей мере 10 сСт, например масла Krytox GPL 102-107. Фторированные масла Krytox представляют серии с низкой молекулярной массой, с концевыми фтор группами, гомополимеры гсксафторпропилен эпоксида. Цепь полимера полностью насыщена и содержит только элементы углерода, кислорода и фтора, водород не присутствует. По массе Krytox содержит 21,6% углерода, 9,4% кислорода и 69,0% фтора. Следует отметить, что в способе получения по настоящему изобретению могут быть использованы все инертные фторированные синтетические масла, отвечающие требованиям по вязкости и другим требованиям для использования в качестве подходящего растворителя (В) для непрерывной фазы. Подходящими способами диспергирования жидкого клатрата в растворителе (S) с получением эмульсии (Е) является использование механического устройства наряду с использованием ультразвука для смешивания, что известно специалисту в области техники, к которой относится настоящее изобретение. Для регулирования размера каталитической системы используют параметры способа, такие как время смешивания, интенсивность смешивания, тип смешивания, сила, прилагаемая для смешивания, такая как скорость миксера или длина ноли используемого ультразвука, вязкость фазы растворителя. В одном варианте воплощения настоящего изобретения жидкий клатрат может быть инжектирован под поверхность растворителя (S) во время смешивания, а в другом варианте воплощения настоящего изобретения жидкий клатрат может быть инжектирован на поверхность растворителя (S) перед или во время смешивания. Независимо от способа, используемого для получения эмульсии, температура перед стадией (II) предпочтительно составляет в пределах от -20 до -1-50C, более предпочтительно в пределах от -10 до+40C, еще более предпочтительно в пределах от -5 до 30C, и еще более предпочтительно в пределах от 0 до 20C. Подходящая температура зависит от используемых растворителей. На стадии (II) способа по настоящему изобретению каталитическая система отверждается из капель дисперсной фазы. Согласно настоящему изобретению отверждение происходит за счет испарения углеводородного растворителя (HS), предпочтительно толуола инертным газом, таким как аргон, с получением твердых сферических частиц катализатора. Выбор параметров, таких как температура, поток инертного газа и тому подобное для проведения испарения лежит в области общих знаний и навыков специалиста в области техники, к которой относится настоящее изобретение. Эффективность испарения может быть усилена повышением скорости потока инертного газа и температуры. Этот упрощенный способ отверждения имеет преимущество, состоящее в том, что эмульгирование и отверждение может быть проведено в одной емкости. Затем каталитическая система, то есть твердые сферические частицы катализатора, могут быть промыты и/или высушены для удаления любых остатков растворителя, присутствующих в частицах. Промывание и/или сушка частиц катализатора может быть проведена любым подходящим способом,известным из предшествующего уровня техники. Более детальное описание, варианты воплощения и примеры способа получения эмульсии введены ссылкой, например, на международную патентную заявку WO 03/051934. Способ по настоящему изобретению позволяет получить твердую каталитическую систему, не включающую какой-либо материал-носитель наружной подложки. Такая твердая каталитическая система характеризуется малой площадью поверхности и/или пористостью. Дополнительно, каталитическая система, полученная способом по настоящему изобретению, имеет преимущество, состоящее в том, что, по существу, не растворима в углеводородах. Дополнительно в случае, когда в качестве соединения, образующего клатртат, используют кремнийорганические соединения, полученные каталитические системы дополнительно демонстрируют улучшенную производительность по сравнению с каталитическими системами, полученными при использовании "классической" технологии эмульсия/отверждение без образования клатрата. И в качестве дополнительного преимущества повышен объемный выход, то есть при использовании реактора того же объема может быть получен больший объем катализатора, что позволяет сократить время производства и, таким образом, повышает экономичность производства. Указанный выше способ также позволяет получить новую каталитическую систему, как детально описано ниже. Следовательно, настоящее изобретение также относится к каталитической системе, которая предпочтительно может быть получена, более предпочтительно получена при использовании указанного выше способа, включая (a2) соединения переходного металла с формулой (I) где T представляет переходный металл любой из групп 3-10 Периодической таблицы (IUPAC 2007),каждый X независимо представляет моновалентный анионный -лиганд,каждый L независимо представляет органический лиганд, который образует координационные связи с переходным металлом (Т),R представляет мостиковую группу, соединяющую указанные органические лиганды (L),m представляет 2 или 3, предпочтительно 2,n представляет 0, 1 или 2, предпочтительно 1,q представляет 1, 2 или 3, предпочтительно 2,m+q равно валентности переходного металла (T),a2) сокатализатор, включающий алюмоксан,a3) соединение, эффективное для образования кристаллической решетки при использовании соединения переходного металла и/или алюмоксана,где твердая каталитическая система имеет средний размер частиц в пределах от 1 до 100 м, более предпочтительно в пределах от 3 до 60 м и наиболее предпочтительно в пределах от 5 до 40 м, измеренные при использовании анализа изображений, полученных при световой микроскопии. Согласно способу по настоящему изобретению можно получить частицы катализатора с очень малым размером, например, средний размер частиц составляет в пределах от 5 до 40 м, и с очень узким распределением размера частиц. Дополнительно полученные частицы имеют очень правильную сферическую форму и очень гладкую поверхность. Предпочтительные соединения переходного металла с формулой (I) и сокатализаторы (Со) приведены выше. Дополнительно, как указано выше, каталитическая система по настоящему изобретению характеризуется тем фактом, что не включает каталитически инертным материал подложки, такой как органические или не органические материалы подложки, такие как кремний, MgCl2 или пористый полимерный материал. В результате каталитическая система представляет самоподдерживающуюся и имеет значительно меньшую площадь поверхности, как более детально указанно ниже. Таким образом, следует ответить, что полимер, полученный при использовании каталитической системы, полученной по настоящему изобретению, не содержит каких-либо остатков кремния. Дополнительно, каталитическая система не содержит каких-либо остатков не желательных поверхностно-активных веществ в виду того, что способ получения по настоящему изобретению позволяет избежать использования поверхностно-активных веществ. Полученные частицы катализатора имеют малую площадь поверхности и низкую пористость. Частицы катализатора по настоящему изобретению имеют плотную структуру с высокой насыпной плотностью, и в результате из-за эффекта повтора позволяют получить полимеры с высокой насыпной плотностью. Дополнительно настоящее изобретение относится к применению указанной выше каталитической системы для полимеризации олефинов с получением полиолефинов и полиолефинам, полученным при использовании такой каталитической системы. Подходящие полиолефины включают гомополимеры полиэтилена и полипропилена, и также сополимеры полиэтилена, полипропилена и полипропилена/полиэтилена, включающие в пределах от 0 до 40 мас.% C2-олефина или C3-C30-альфа-олефина или C4-C30-диеновых единиц и, в частности, сополимер или терполимер этилена и/или пропилена с в пределах от 0 до 10 мас.% алкенов, например, этилен, 1-пропен,1-бутен, 1-пентен, 4-метил-пент-1-ен, 1-гексен, циклогексен, 1-октен и норборнен, или диены, например,бутадиен, гексадиен или октадиен. В предпочтительном варианте воплощения настоящего изобретения полиодефины, полученные при использовании катализатора по настоящему изобретению, представляют полимеры пропилены. В зависимости от конфигурации процесса полимеризации, полученные полимеры могут представлять уни- или мультимодальные, такие как бимодальные. Дополнительно, настоящее изобретение относится к способу получения полиолефинов при использовании каталитической системы, как указано выше. Для полимеризации олефинов в комбинации с каталитической системой по настоящему изобретению может быть использован любой способ, например, газофазный, суспензионный, полимеризации в растворе или любая их комбинация, известный для полимеризации олефинов с получением полиолефинов. Полимеризация может представлять одностадийный, или двухстадийный, или многостадийный процесс полимеризации и проводится по меньшей мере в одном реакторе для полимеризации. Традиционные реакторы для полимеризации включают суспензионные и газофазные реакторы. Следовательно,полимеризация может быть проведена в комбинации по меньшей мере из двух реакторов, в некоторых случаях используют по меньшей мере три реактора, например, газофазный/газофазный, суспензионный/суспензионный, суспензионный/газофазный или суспензионный/газофазный/газофазный; предпочтительно плимеризацию проводят при использовании комбинации суспензионный/газофазный или суспензионный/газофазный/газофазный. Дополнительно к фактической полимеризации процесс может включать любые пре- и постреакторы. Каталитическая система по настоящему изобретению может быть введена в реактор полимеризации при использовании любых подходящих средств, известных из предшествующего уровня техники, независимо от типа используемого реактора для полимеризации. Как правило, количество используемой каталитической системы зависит от природы каталитической системы, типа реактора, условий и заданных свойств полимерного продукта. Могут быть использованы традиционные количества катализаторов, приведенные в публикациях,введенных здесь ссылкой. Установка реактора, по существу, не ограничена и может быть использована любая установка реактора, известная специалисту в области техники, к которой относится настоящее изобретение. 1. Методы. Для приведенного выше описания настоящего изобретения, если ясно не указанно иное, наряду с приведенными ниже примерами применяют следующие определения терминов и методы определения. Активность катализатора/Производительность катализатора. Для полимеризации пропилена используют 5-литровый реактор из нержавеющей стали. В реактор подают 1100 г жидкого пропилена (степень полимеризации Borealis polymerization grade). В качестве акцептора подают 0,2 мл триэтилалюминия (100%, от Crompton) и 15 ммоль водорода в качестве агента передачи цепи. Температуру реактора устанавливают около 30C. В реактор под избыточным давлением азота подают катализатор. Реактор нагревают до температуры 70C в течение 15 мин. Через 30 мин полимеризации оставшийся пропилен промывают и полимер сушат и взвешивают. Определяют выход полимера (на основе 30-минутной полимеризации). Активность катализатора представляет выход полимера[кг] разделенный на количество катализатора [г]. Производительность катализатора представляет активность катализатора, разделенную на время [часы].ICP анализ. Элементный анализ катализатора проводят на образце твердой фазы массой М, которую охлаждают на сухом льду. Образцы разводят до известного объема V, растворяя азотной кислотой (HNO3, 65%, 5%V) и свежей деионизированной водой (DI) (5% V). Затем раствор добавляют в плавиковую кислоту (HF,40%, 3% V), разводят DI водой до конечного объема V и оставляют для стабилизации на два часа. Анализ проводят при комнатной температуре при использовании атомно-эмиссионного спектрометра (Thermo Elemental IRIS Advantage XUV) с индуктивно связанной плазмой (ICP-AES), который колибруют непосредственно перед анализом при использовании контроля (раствор 5% HNO3, 3% HF в DI воде), низкий стандарт (10 ч./мил Al в растворе 5% HNO3, 3% HF в DI воде), высокий стандарт (50 ч./милAl, 50 ч./мил Hf, 20 ч./мил Zr в растворе 5% HNO3)3, 3% HF в DI воде) и образец для контроля качества(20 ч./мил Al, 20 ч./мил Hf, 10 ч./мил Zr в растворе 5% HNO3, 3% HF в DI воде). Содержание переходного металла определяют при использовании 282,022 нм и 339,980 нм линий, и содержание циркония определяют при использовании 339,198 нм линии. Содержание алюминия определяют при использовании 167,081 нм линии, когда концентрация Al в ICP образце составляет в пределах 0-10 ч./мил, и при использовании 396,152 нм линии для концентрации Al в пределах 10-100 ч./мил. Приведенные показатели представляют среднее трех последовательных аликвот, взятых из одного и того же образца, и соотносятся обратнопропорциально к первоначальному катализатору по уравнению 1,и должны быть в пределах от 0 до 100 или требуется провести дополнительное разведение, где С представляет концентрацию в частях на миллион, относящуюся к % содержанию при факторе 10000,R представляет приведенный показатель по ICP-AES,- 14023154V представляет общий объем разведения в мл,М представляет оригинальную массу образца в г. Если требуется разведение, то это также должно быть учтено путем умножения C на фактор разбавления.PSD (Метод 1). Распределение размера частиц (PSD) и средний размер частиц определяют при использовании анализа статического изображения. Для сканирования изображений частиц катализатора, диспергированного в масле на предметных стеклах, используют систему, включающую световой микроскоп Zeiss Axioplan, снабженный камерой Flea 2 Digital от Point Grey Research Inc., предметный столик, моторизованный по осям XY, от Marzhauser с контроллером Corvus и PC. Калибровку системы проводят при использовании многоступенчатого микрометра (2 мм, с делениями 0,01 мм). Для анализа получают суспензию в пределах от 2 до 3 мас.% катализатора в масле. После гомогенизации суспензии три образца наносят на отдельные предметные стекла и закрывают покровным стеклом. Стекла помещают на предметный столик микроскопа и используют 10-кратное увеличение (числовая апертура 0,30) для получения в пределах от 10 до 20 частиц в рамке для измерений. Освещение регулируют таким образом, чтобы светлое поле и микроскоп были сфокусированы на частицах образца. Для каждого предметного стекла сканируют около 500 изображений при двухмерном сканировании и сохраняют. Обработку и анализ изображений проводят при использовании программного обеспечения для анализа изображений. Для каждого изображения проводят подсчет и рассчитывают площадь, эквивалент диаметра и другие параметры выделенных частиц, которые не попадают на края изображений и фиксируют данные. Всего сложности подсчитано минимум 15000 частиц. Для получения конечного результата изображения всех частицы классифицируют по размерам и представляют в виде гистограммы. Классы крупности определяют при использовании где xi представляет верхний предел размера частиц, а xi-1 нижний предел размера частиц. Частицы с заданным интервалом размера имеют диаметр, равный или более чем xi-1 и и менее чем xi. Распределение размера частиц, варьирование распределения размера частиц (x1,0; x2,0; x3,0; x1,2 и x1,3) рассчитывают согласно ISO 9276-1:1998(Е) и ISO 9276-2:2001 (Е).PSD (Метод 2). Распределение размера частиц определяют при использовании сканирующей электронной микроскопии (SEM). Реагенты. МАО от Albermarle и используют, как 30 мас.% раствор в толуоле.PFPE Krytox GPL 106 от Е. I. de Pont de Nemours and Company, Wilmington, Delaware, высушенный под вакуумом в течение нескольких часов при температуре 100C перед использованием.PFPE Krytox GPL 102 от Е. I. du Pont de Nemours and Company, Wilmington, Delaware, высушенный под вакуумом в течение нескольких часов при температуре 100C перед использованием. рац-циклогексил(метил)силанедил-бис(2-метил-4-(4'-трет-бутилфенил)инден-1-ил)дихлорид циркония от Boulder Scientific company (CAS Registry Number 888227 55-2). Октаметилтрисилоксан (OMTS), от Sigma Aldrich Finland Oy (CAS Registry Number 107-51-7). Пропилен от Borealis и соответствующе очищенный перед использованием. Триэтилалюминий отCrompton используют в чистой форме. Водород от AGA очищают перед использованием. Транспортировку в процессе технологической обработки всех реагентов и все химические реакции проводят в атмосфере инертного газа при использовании Schlenk и перчаточной камеры, высушенной в сушилке лабораторной посуды, шприцов и игл. 2. Примеры получения. Пример 1. Получение жидкого клатрата, вариант В. Раствор катализатора получают, проводя реакцию 250 мг рацциклогексил(метил)силанедил-бис(2 метил-4-(4'-трст-бутил-фенил)инден-1-ил) дихлорид циркония и 15 мл 30 мас.% раствора МАО в толуоле, смешивая комплекс и МАО при комнатной температуре в течение 0,5 ч. Al/Zr составляет 370 моль/моль. В раствор добавляют 0,97 мл октаметилтрисилоксана (OMTS) агента для образования клатрата, оставляют полученный раствор в перчаточной камере в течение ночи при перемешивании. После добавления OMTS красная смесь становится оранжевой. На следующий день смешивание останавливают и жидкость разделяют на фазу толуола и фазу катализатора. Используют 5 мл нижней фазы катализатора. Жидкость меняет свой цвет на темно красный и также верхняя фаза имеет красноватый цвет. Пример 2. Получение жидкого клатрата, вариант А. В 0,97 мл раствора октаметилтрисилоксана (OMTS) агента для образования клатрата добавляют 15 мл 30 мас.% раствора МАО в толуоле, полученную в результате суспензию перемешивают в течение ночи. Перемешивание останавливают и проводят разделение на две фазы. Верхнюю фазу удаляют. 5 мл нижней фазы, содержащей клатрированный МАО, добавляют в 179 мг рац-циклогексил(метил) силанедил-бис(2-метил-4-(4'-трет-бутилфенил)инден-1-ил)дихлорид циркония. Полученный в результате раствор перемешивают в течение 1 ч и он приобретает темно красный цвет. Al/Zr составляет 235 моль/моль. Пример 3. 5 мл раствора катализатора по примеру 1 добавляют в 30 мл Krytox GPL 106 в 50 мл стеклянном реакторе для эмульгирования с "открытыми перегородками", снабженном верхнеприводной мешалкой ниже поверхности масла. Затем проводят 15-минутное смешивание при скорости конца лопатки 0,75 м/с (скорость смешивания 250 об/мин). Затем при использовании аргона выпаривают тлуол. Промывание аргоном, проводимое перед смешиванием в течение 120 мин останавливают и оставшуюся суспензию катализатор/масло перекачивают через сифон в емкость с септой. Катализатор: PSD: 5-15 м (на основе изображений SEM). Производительность катализатора составляет 5 кг РР/г катализатора в час. Как видно на фиг. 1 и на фиг. 2 получают очень правильные сферические частицы малого размера. Пример 4. 5 мл раствора катализатора по примеру 2 добавляют в 30 мл Krytox GPL 106 в 50 мл стеклянном реакторе для эмульгирования с "открытыми перегородками", снабженном верхнеприводной мешалкой ниже поверхности масла. Затем проводят 15-минутное смешивание при скорости конца лопатки 0,75 м/с (скорость смешивания 250 об/мин). Затем при использовании аргона выпаривают тлуол. В течение 120 мин перед смешиванием проводят промывание аргоном смешивание останавливают и удаляют суспензию катализатор/масло, суспензию перекачивают через сифон в емкость с септой. Катализатор: PSD: 20-30 м (на основе изображений SEM). Производительность катализатора составляет 5 кг РР/г катализатора в час. Как видно на фиг. 3 и на фиг. 4 получают сферические частицы малого размера. ФОРМУЛА ИЗОБРЕТЕНИЯ 1. Способ получения твердой каталитической системы для полимеризации олефина, включающей металлоорганическое соединение переходного металла группы 3-10 Периодической таблицы (IUPAC 2007) в форме твердых частиц, включающий стадииI) получения эмульсии диспергированием жидкого клатрата в растворителе (S), где(i) растворитель (S) составляет непрерывную фазу эмульсии и включает инертное фторированное синтетическое масло с вязкостью при температуре 20C согласно ASTM D445 по меньшей мере от 10 сСт вплоть до 2000 сСт;(ii) жидкий клатрат в форме капель составляет дисперсную фазу эмульсии, иII) отверждения указанной дисперсной фазы для превращения указанных капель в твердые частицы,где жидкий клатрат включаетa1) соединения переходного металла с формулой (I) где T представляет переходный металл любой из групп 3-10 Периодической таблицы (IUPAC 2007),каждый X независимо представляет моновалентный лиганд,каждый L независимо представляет органический лиганд, который образует координационные связи с переходным металлом (Т) и представляет собой замещенный или незамещенный циклоалкилдиен, или ациклический 1-, ациклический 2-, ациклический 3-, ациклический 4- или ациклический 6 лиганд, включающий атомы из групп 13-16 Периодической таблицы (IUPAC 2007), или циклический -, циклический 1-, циклический 2-, циклический 3-, циклический 4- или ациклический 6-, моно-, би- или мультидентатный лиганд, включающий незамещенные или замещенные моно-, би- или мультициклические кольцевые системы, выбранные из ароматических, или неароматических, или частично насыщенных кольцевых систем и содержащие углеродные атомы колец, при этом,когда органические лиганды (L) замещены, по меньшей мере один органический лиганд (L) включает один или более остаток, независимо выбранный из группы, состоящей из галогена, C1-C10 алкила, C2-C20 алкенила, C2-C20 алкинила, C3-C12 циклоалкила, C6-C20 арила, C7-C20 арилалкила, C3-C12 циклоалкила, который содержит 1, 2, 3 или 4 гетероатома в кольцевой функциональной группе, и C1-C20 галоалкила,R представляет мостиковую группу, соединяющую указанные органические лиганды (L), при этом мостиковая группа имеет формулу (II) где Y представляет собой С, Si или Ge иR', R" независимо выбран из группы, состоящей из C1-C20 алкила, C4-C10 циклоалкила, C6-C12 арила,C7-C12 арилалкила или триметилсилила,m представляет 2 или 3,- 16023154n представляет 0, 1 или 2,q представляет 1, 2 или 3,m+q равно валентности переходного металла (Т),a2) сокатализатора, включающего алюмоксан,a3) соединения, эффективного для образования кристаллической решетки при использовании соединения переходного металла и/или алюмоксана,при этом указанное соединение, эффективное для образования клатратов с алюмоксаном и/или соединением переходного металла, представляет собой M-X соединение, кремнийорганическое соединение или галосилоксан,при этом M-X соединение представляет собой органическое, неорганическое или металлоорганическое соединение, которое потенциально может диссоциировать или частично диссоциировать на катионные и анионные компоненты, и выбрано из группы, состоящей из щелочных и щелочно-земельных галидов или псевдогалидов, анионной углеводородной группы, металлогидридов и алкил, арил и алкил-арил аммония, фосфония и сульфония, солей галидов и псевдогалидов,при этом кремнийорганическое соединение выбрано из группы гидрокарбилоксисиланов с формулой R3Si-O[-SiR2-O]n-SiR3 или Si-[O-R]4, где R независимо представляет группу нециклического углеводородного остатка с вплоть до около 18 атомов углерода и n представляет в пределах от 0 до 3; и гидрокарбилполисилоксанов с в пределах от 2 до 6 атомами кремния в молекуле, которые отделены друг от друга атомом кислорода таким образом, что представляет линейный, разветвленный или циклический скелет из чередующихся атомов Si и кислорода, где оставшиеся от четырех валентных связей каждого из атомов кремния непосредственно связаны с одновалентным остатком нециклической углеводородной группы R, независимо представляющим группу нециклического углеводородного остатка с вплоть до около 18 атомов углерода, иb) углеводородный растворитель (HS), выбранный из группы, состоящей из линейного алкана, циклического алкана, линейного алкена, циклического алкена, ароматического углеводорода. 2. Способ по п.1, включающий также стадию удаления указанных твердых частиц для получения указанной каталитической системы. 3. Способ по п.1 или 2, где(a) лиганды (X) независимо выбраны из группы, состоящей из водорода, галогена, C1-C20 алкила, C1C20 алкокси, C2-C20 алкенила, С 2-С 20 алкинила, C3-C12 циклоалкила, C6-C20 арила, C6-C20 арилокси, C7-C20 арилалкила, С 7-С 20 арилалкенила, -SR", -PR3, -SiR3, -OSiR3 и -NR2, где каждый R" независимо представляет водород, C1-C20 алкил, C2-C20 алкенил, C2-C20 алкинил, C3-C12 циклоалкил или C6-C20 арил; и/или(b) по меньшей мере один органический лиганд (L) независимо выбран из группы, состоящей из незамещенного циклопентадиенильного лиганда, замещенного циклопентадиенильного лиганда, незамещенного инденильного лиганда, замещенного инденильного лиганда, незамещенного флуоренильного лиганда и замещенного флуоренильного лиганда. 4. Способ по любому из предшествующих пунктов, где переходный металл (Т) представляет цирконий (Zr), гафний (Hf) или титан (Ti). 5. Способ по любому из предшествующих пунктов, где по меньшей мере один органический лиганд(L) включает один или более остаток, независимо выбранный из группы, состоящей из галогена, C1-C20 алкила, C2-C20 алкенила, C2-C20 алкинила, C3-C12 циклоалкила, C5-C20 циклоалкила, замещенного C1-C20 алкилом, где циклоалкильный остаток замещен C1-C20 алкилом, C6-C20 арилом, C7-C20 арилалкилом, C3C12 циклоалкилом, который содержит 1, 2, 3 или 4 гетероатома в кольцевой функциональной группе, иC1-C20 галоалкила. 6. Способ по любому из предшествующих пунктов, где указанный алюмоксан а 2) представляет метилалюмоксан. 7. Способ по п.1, где M-X соединение выбирают из группы, состоящей из KCl, KF, NaF, KH, LiH,KOSiR3, NaBPh4, Me4NCl, (октил)3NClMe, MePh3PBr, KB(C6F5)4 и K+CH2Ph-. 8. Способ по любому из пп.1-7, где жидкий клатрат получен(i) получением смеси углеводородного растворителя (HS), алюмоксана и соединения, образующего клатрат (a3),(ii) добавлением в указанную смесь соединения переходного металла с формулой (I),(iii) получением двухфазной системы, где верхняя фаза представляет фазу, богатую углеводородным растворителем (HS), а нижняя фаза представляет фазу жидкого клатрата, и(iv) отделением нижней фазы жидкого клатрата от верхней фазы, богатой углеводородным растворителем (HS). 9. Способ по любому из предшествующих пп.1-7, где жидкий клатрат получен(i) получением раствора углеводородного растворителя (HS), алюмоксана и соединения переходного металла с формулой (I),(ii) добавлением в указанный раствор соединения, образующего клатрат (a3),(iii) получением двухфазной системы, где верхняя фаза представляет фазу, богатую углеводородным растворителем (HS), а нижняя фаза представляет фазу жидкого клатрата,- 17023154(iv) отделением нижней фазы жидкого клатрата от верхней фазы, богатой углеводородным растворителем (HS). 10. Способ по любому из предшествующих пп.1-9, где углеводородный растворитель (HS) представляет ароматический углеводород, и/или инертное фторированное синтетическое масло, используемое в качестве растворителя (S), представляет перфторполиэфир, политрихлорфторэтилен, фторсиликон или их комбинации с вязкостью при температуре 20C согласно ASTM D445 по меньшей мере в пределах от 10 сСт вплоть до 2000 сСт. 11. Способ по любому из предшествующих пунктов, где растворитель (S) представляет перфторполиэфиры с формулой: или комбинации двух или более из них; где s представляет целое число в пределах 2-100; Rf представляет CF2CF3, C3-C6 перфторалкильную группу или их комбинации; х представляет целое число в пределах от 10 до 60; R1f представляет CF3,C2F5, C3F7 или комбинации двух или более из них; (m+n) представляет 8-45 включительно; (m+n+o) представляет 8-45 включительно; m/n представляет 20-1000 включительно; о представляет 1; R2f представляет CF3, C2F5 или их комбинации; t представляет 2-200 включительно; (p+q) представляет 40-180 включительно; и p/q представляет 0,5-2 включительно, при условии, что перфторполиэфир имеет вязкость при температуре 20C согласно ASTM D445 в пределах по меньшей мере от 10 сСт вплоть до 2000 сСт. 12. Способ по п.11, где перфторполиэфир имеет формулу (III) или (IV). 13. Способ по п.12, где перфторполиэфир имеет формулу (IV). 14. Способ по любому из предшествующих пунктов, где отверждение происходит за счет испарения углеводородного растворителя (HS) инертным газом. 15. Способ по п.1, где стадию отверждения проводят в той же емкости, что и стадию эмульгирования. 16. Применение перфторполиэфира в качестве растворителя для получения непрерывной фазы эмульсии в комбинации с соединением, эффективным для образования клатратов с алюмоксаном и/или соединением переходного металла с формулой (I), при этом перфторполиэфир имеет формулу: или комбинации двух или более из них; где s представляет целое число в пределах 2-100; Rf представляет CF2CF3, C3-C6 перфторалкильную группу или их комбинации; х представляет целое число в пределах от 10 до 60; R1f представляет CF3,C2F5, C3F7 или комбинации двух или более из них; (m+n) представляет 8-45 включительно; (m+n+o) представляет 8-45 включительно; m/n представляет 20-1000 включительно; о представляет 1; R2f представляет CF3, C2F5 или их комбинации; t представляет 2-200 включительно; (p+q) представляет 40-180 включительно; и p/q представляет 0,5-2 включительно, при условии, что перфторполиэфир имеет вязкость при температуре 20C согласно ASTM D445 в пределах по меньшей мере от 10 сСт вплоть до 2000 сСт. Фиг. 1. Фотографии катализатора в форме клатрата и масле Krytox, полученные при световой микроскопии (40) Фиг. 3. Фотографии катализатора в форме клатрата в масле Krytox, полученные при световой микроскопии (40)
МПК / Метки
МПК: C08G 65/00, C08F 4/659, C08F 10/00, C07F 5/06
Метки: металлоценовой, каталитической, способ, применение, полимеризации, получения, системы, олефинов, твердой
Код ссылки
<a href="https://eas.patents.su/20-23154-sposob-polucheniya-tverdojj-metallocenovojj-kataliticheskojj-sistemy-i-ee-primenenie-pri-polimerizacii-olefinov.html" rel="bookmark" title="База патентов Евразийского Союза">Способ получения твердой металлоценовой каталитической системы и ее применение при полимеризации олефинов</a>
Предыдущий патент: Способ низкотемпературного пиролиза (отжига) биомассы
Следующий патент: Силовая установка с системой охлаждения и устройством фильтрации охлаждающей жидкости
Случайный патент: Слитый белок bche-альбумин для лечения злоупотребления кокаином