Титановая плоская заготовка для горячей прокатки, способ ее получения и способ ее прокатки
Номер патента: 20258
Опубликовано: 30.09.2014
Авторы: Такахаси Кадзухиро, Мори Кенити, Танака Хисамунэ, Фудзии Хидеки, Оцука Хироаки, Ода Такаси, Тада Осаму, Фудзии Ёсихиро, Куниэда Томонори, Миядзаки Ёсимаса
Формула / Реферат
1. Титановая плоская заготовка для горячей прокатки, характеризующаяся тем, что она выполнена посредством отливки в условиях, при которых угол между направлением ее литья и направлением затвердевания находится в диапазоне от 45 до 90°.
2. Титановая плоская заготовка по п.1, характеризующаяся тем, что в части ее поверхностного слоя имеется область толщиной 10 мм или больше, образованная в условиях, когда угол между направлением литья заготовки и направлением затвердевания находился в диапазоне от 70 до 90°.
3. Титановая плоская заготовка для горячей прокатки, характеризующаяся тем, что она выполнена посредством отливки в электронно-лучевой плавильной печи и содержит слой толщиной 10 мм или больше из кристаллических зерен, для которых угол наклона С-оси гексагональной плотно упакованной структуры, являющейся альфа-фазой титана, относительно направления нормали к поверхности, подлежащей горячей прокатке, находится в диапазоне от 35 до 90°, где направление нормали определяется как 0°.
4. Титановая плоская заготовка по любому из пп.1-3, характеризующаяся тем, что ее толщина составляет от 225 до 290 мм и отношение W/T ширины W к толщине T составляет от 2,5 до 8,0.
5. Титановая плоская заготовка по любому из пп.1-3, характеризующаяся тем, что отношение L/W ее длины L к ширине W составляет 5 или больше, а длина L равна 5000 мм или больше.
6. Титановая плоская заготовка по любому из пп.1-3, характеризующаяся тем, что она изготовлена из технически чистого титана.
7. Титановая плоская заготовка по любому из пп.1-3, характеризующаяся тем, что она является титановой плоской заготовкой для горячей прокатки, отлитой в электронно-лучевой плавильной печи.
8. Способ получения титановой плоской заготовки для горячей прокатки по п.1 или 2 в электронно-лучевой плавильной печи, характеризующийся тем, что скорость извлечения титановой плоской заготовки составляет не менее 1,0 см/мин, при этом угол между направлением ее литья и направлением затвердевания находится в диапазоне от 45 до 90°.
9. Способ получения титановой плоской заготовки для горячей прокатки по п.3 в электронно-лучевой плавильной печи, характеризующийся тем, что скорость извлечения титановой плоской заготовки составляет на менее 1,0 см/мин, при этом в титановой плоской заготовке образуется слой из кристаллических зерен, для которых угол наклона С-оси гексагональной плотно упакованной структуры, являющейся альфа-фазой титана, относительно направления нормали к поверхности, подлежащей горячей прокатке, находится в диапазоне от 35 до 90°.
10. Способ прокатки титановой плоской заготовки для горячей прокатки, характеризующийся тем, что титановую плоскую заготовку для горячей прокатки по любому из пп.1-3 подают в стан горячей прокатки и подвергают горячей прокатке в рулон полосового материала.
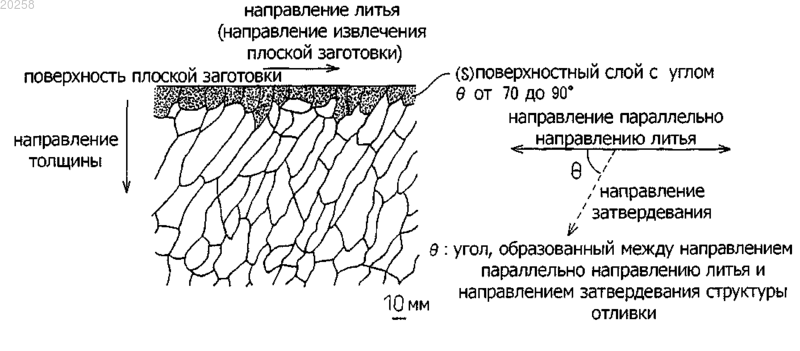
Текст
ТИТАНОВАЯ ПЛОСКАЯ ЗАГОТОВКА ДЛЯ ГОРЯЧЕЙ ПРОКАТКИ, СПОСОБ ЕЕ ПОЛУЧЕНИЯ И СПОСОБ ЕЕ ПРОКАТКИ Предложена титановая плоская заготовка для горячей прокатки, которую можно подавать в стан горячей прокатки общего назначения для получения рулона полосового материала без прохождения через процесс обжима, такой как блюминг или процесс рихтования, за счет подавления появления дефектов поверхности в рулоне полосового или плоского материала. Также предложены способы получения и прокатки материала, согласно которым в отлитой титановой плоской заготовке угол , образованный между направлением роста кристаллов (направление затвердевания) от поверхностного слоя внутрь и направлением, параллельным направлению литья плоской заготовки(в продольном направлении), составляет от 45 до 90. Кроме того, в поверхностном слое толщиной 10 мм или больше этот уголсоставляет от 70 до 90. Способ дополнительно характеризуется тем,что формируется слой размером 10 мм или больше из кристаллических зерен, для которых угол наклона С-оси альфа-фазы титана на виде со стороны боковой поверхности плоской заготовки,подлежащей горячей прокатке, к направлению нормали к поверхности, подлежащей горячей прокатке, находится в диапазоне от 35 до 90. Данная титановая плоская заготовка производится с использованием электронно-лучевой плавильной печи путем литья со скоростью извлечения свыше 1,0 см/мин. Область техники Изобретение относится к титановой заготовке для горячей прокатки, способу получения титановой заготовки и к способу ее прокатки, в частности к способу прямого получения плоской титановой заготовки с использованием электронно-лучевой плавильной печи для последующей горячей прокатки полученной плоской титановой заготовки. Более конкретно, изобретение относится к титановой заготовке для горячей прокатки, полученной непосредственно в электронно-лучевой плавильной печи и обеспечивающей возможность получения путем горячей прокатки полосового материала с необходимыми характеристиками поверхности, даже если исключается горячая обработка болванки, такая как блюминг, проковка,прокатка или т.п., а также к способам получения и прокатки указанной заготовки. Уровень техники Известный способ получения рулона титановой полосы заключается в следующем. Сначала берут большую болванку, полученную при застывании титана, расплавленного методом электродуговой плавки с расходуемым электродом или методом электронно-лучевой плавки. При использовании электродуговой плавки с расходуемым электродом указанная большая болванка имеет форму цилиндра диаметром около 1 м, а при использовании электронно-лучевой плавки получается болванка прямоугольной формы,поперечное сечение которой имеет размеры приблизительно от 0,5 до 1 м для каждой стороны. Поскольку поперечное сечение настолько велико, большая болванка подвергается блюмингу, проковке, горячей прокатке или другой горячей обработке (далее эта обработка иногда будет называться процесс обжима) с целью получения плоской заготовки, которая может быть прокатана с использованием стана горячей прокатки. После разрушения плоскую заготовку для горячей прокатки дополнительного подвергают процессу рихтования для усиления сглаженности и обрабатывают для удаления поверхностной окалины и дефектов. Полученная плоская заготовка для горячей прокатки перерабатывается в рулон полосового материала (лист) путем нагрева до заданной температуры и горячей прокатки с использованием универсального стана горячей прокатки для стали или т.п. После горячей прокатки для получения конечного продукта полученный полосовой материал подвергают отжигу и/или очистке от окалины или дополнительной холодной прокатке или другой холодной обработке и отжигу. В процессе очистки от окалины после горячей прокатки удаляются поверхностная окалина и дефекты, поэтому очистка поверхности должна быть относительно более глубокой, так как поверхностные дефекты находятся глубоко, из-за чего снижается выход продукта. С другой стороны, при использовании, например, электронно-лучевой или плазменно-дуговой плавки плавление исходного материала проводится в регулируемой подине, не зависящей от литейной формы, в связи с чем литейная форма может быть самой разнообразной конструкции, в отличие от применения вакуумной дуговой плавки, в результате чего обеспечивается возможность производства болванки с прямоугольным поперечным сечением. При производстве плоского материала или рулона полосового материала из прямоугольной болванки,полученной посредством электронно-лучевой или плазменно-дуговой плавки, в связи с вышеупомянутой возможностью получения болванки определенной формы можно исключить указанный выше процесс обжима и, следовательно, снизить себестоимость. В связи с этим далее будет рассмотрена технология получения прямоугольных болванок, которые являются достаточно тонкими для непосредственной подачи в стан горячей прокатки (далее такая заготовка иногда будет называться литой плоской заготовкой). Для получения указанной тонкой титановой плоской заготовки требуется более тонкая прямоугольная литейная форма, изготовление которой не вызывает затруднений. На характеристики поверхности и структуру отливки значительно влияют толщина и/или ширина литейной формы и условия литья. Что касается поверхности отлитой плоской заготовки, то, когда на ней имеются впадины/выпуклости, складки или другие глубокие дефекты, даже если поверхность плоской заготовки непосредственно после литья сглаживается путем механической или другой обработки, любые дефекты, оставшиеся в нижних участках, даже в незначительном количестве, могут стать поверхностными дефектами, что становится заметным после горячей прокатки. Для устранения этого необходим способ обработки и удаления поверхностного слоя на значительную глубину литой плоской заготовки. Кроме того, как показано на фиг. 2 и 3, структура литой заготовки состоит из крупнокристаллических зерен размером в несколько десятков миллиметров, и, если такая структура подвергается непосредственной горячей прокатке без предварительного обжима, крупнокристаллические зерна приведут к неравномерной деформации, которая иногда приводит к появлению крупных дефектов поверхности. В результате значительно снижается выход продукта после осуществления процесса очистки от окалины для удаления поверхностных дефектов, обследования продукта и т.п. В связи с этим при исключении процесса обжима поверхностные дефекты, образующиеся в титановом материале после горячей прокатки, должны быть минимизированы, насколько это возможно. Для решения данной проблемы были предложены методы сглаживания поверхности плоской отливки. В качестве способов, улучшающих поверхность отливки, известны способ, заключающийся в извлечении из литейной формы титановой плоской заготовки, полученной с использованием электронно-1 020258 лучевой плавильной печи, и немедленной подаче ее на профилирующий валок с целью сглаживания ее поверхности (заявка JP 63-165054), и способ улучшения поверхности отлитой в электронно-лучевой плавильной печи плоской заготовки путем направления пучка электронов на поверхность извлеченной из литейной формы титановой плоской заготовки с целью плавления участка поверхностного слоя и последующей подачи заготовки на профилирующий валок (заявка JP 63-050047). Даже если поверхность литой титановой плоской заготовки, полученной с использованием электронно-лучевой плавильной печи, сглаживается путем применения вышеописанных способов, обычно на плоском материале, полученном горячей прокаткой, возникают дефекты вследствие литой структуры исходной титановой плоской заготовки. Кроме того, в указанных выше способах для нагревания титановой плоской заготовки после извлечения ее из литейной формы требуется отдельная электронная пушка, устанавливаемая или в зоне профилирующего валка, или в электронно-лучевой плавильной печи на выходе из литейной формы, что требует дополнительных затрат. Кроме электронно-лучевой плавильной печи иногда применяется печь вакуумно-плазменного плавления. В публикациях Keizo Murase, Toshio Suzuki, Shunji Kobayashi, Качество и характеристики титановых болванок, полученных в электронно-плазменной печи, Nippon Stainless Technical Report,15,стр. 105-117, 1980, и Motohiko Nagai, Keizo Murase, Toshio Suzuki, Tadahiko Kishima, Производство титановых болванок в вакуумно-плазменной печи, знакомство с вакуумно-плазменной печью, NipponStainless Technical Report,10, стр. 65-81, 1973, описаны способы непосредственной горячей прокатки титановой плоской заготовки, полученной с использованием печи вакуумно-плазменного плавления, в рулон полосового материала (лист). В способах, раскрытых в указанных публикациях, скорость плавления составляет 5,5 кг/мин, а скорость извлечения плоской заготовки весьма мала, приблизительно 0,38 см/мин. Из-за формы поперечного сечения литейной формы рулон после горячей прокатки пропускают через участок шлифовальных станков (далее этот участок иногда будет называться участок CG). Таким образом, в рулоне после горячей прокатки имеются дефекты поверхности, которые удаляются на участке CG. Таким образом, аналогично случаю с титановой плоской заготовкой, полученной с использованием электронно-лучевой плавильной печи, в этом случае также существует проблема образования дефектов на поверхности плоского материала, полученного горячей прокаткой. Кроме того, в способе вакуумно-плазменной плавки (в дуге плазмы) нет возможности отклонить дугу, в отличие от пучка электронов в способе электронно-лучевой плавки, что делает затруднительным регулирование выбора места облучения в плавильной печи и количества подведенного тепла, поэтому трудно получить поверхность и/или структуру отливки с заданными характеристиками. Таким образом, в результате горячей прокатки титановой плоской заготовки, полученной с использованием электронно-лучевой плавильной печи или т.п., в рулон полосового материала (плоский лист) образуются дефекты поверхности вследствие остаточных дефектов на поверхности отливки, а также структуры отливки, и поэтому необходима технология производства титановой плоской заготовки для последующей горячей прокатки. Раскрытие изобретения Как изложено выше, проблема заключается в появлении дефектов поверхности, когда титановая плоская заготовка, полученная в электронно-лучевой плавильной печи или т.п., подвергается горячей прокатке в рулон полосового материала (плоский материал). Задача настоящего изобретения заключается в разработке титановой плоской заготовки для горячей прокатки и способов получения и прокатки такой заготовки, в частности титановой плоской заготовки, полученной в электронно-лучевой плавильной печи и подаваемой в стан горячей прокатки общего назначения (например, для стали) для получения рулона полосового материала без прохождения через процессы обжима, такие как блюминг или процесс рихтования, и обеспечивающей подавление поверхностных дефектов в рулоне полосового материала (плоский материал) при горячей прокатке; а также способа получения титановой плоской заготовки с использованием указанной выше электронно-лучевой плавильной печи и, кроме того, способа прокатки титановой плоской заготовки для горячей прокатки. Для решения поставленной задачи была подробно исследована взаимосвязь между затвердевшей структурой титановой плоской заготовки, полученной с использованием электронно-лучевой плавильной печи, и направлением прокатки плоской заготовки. При этом было установлено, что в отлитой титановой плоской заготовке направление затвердевания, т.е. направление роста кристаллов от поверхностного слоя внутрь материала, имеет сильную корреляцию с поверхностью отлитой титановой плоской заготовки и степенью распространения дефектов поверхности в ходе горячей прокатки. Кроме того, обнаружено, что поверхность отливки может быть улучшена и сведены к минимуму дефекты поверхности в ходе горячей прокатки путем регулирования направления затвердевания в ходе производства плоской заготовки. В частности, у титановой плоской заготовки для горячей прокатки согласно настоящему изобретению в структуре поперечного сечения, параллельного направлению литья титановой плоской заготовки,-2 020258 угол, образованный направлением литья и направлением затвердевания, находится в диапазоне от 45 до 90. Термин направление литья означает направление извлечения полученной в литейной форме, входящей в состав электронно-лучевой плавильной печи, титановой плоской заготовки, а термин направление затвердевания означает направление роста кристаллов, составляющих затвердевшую структуру, образовавшуюся в микроструктуре титановой плоской заготовки, от поверхностного слоя плоской заготовки в направлении центра слоя. Согласно настоящему изобретению предпочтительно в части поверхностного слоя титановой плоской заготовки имеется структура толщиной 10 мм или больше, в которой угол, образованный направлением литья и направлением затвердевания, находится в диапазоне от 70 до 90. Кроме того, предпочтительно в титановой плоской заготовке, отлитой в электронно-лучевой плавильной печи, сформирован слой толщиной 10 мм или больше из кристаллических зерен, для которых угол наклона С-оси гексагональной плотно упакованной структуры альфа-фазы титана на виде со стороны боковой поверхности заготовки, подлежащей горячей прокатке, относительно нормали к поверхности, подлежащей горячей прокатке, находится в диапазоне от 35 до 90 (где направление нормали определяется как 0). Предпочтительно толщина титановой плоской заготовки для горячей прокатки составляет от 225 до 290 мм, а отношение ширины W заготовки к ее толщине T составляет от 2,5 до 8,0. Предпочтительно отношение длины L титановой плоской заготовки к ее ширине W для горячей прокатки составляет 5 или больше, причем длина L составляет 5000 мм или больше. Предпочтительно титановая плоская заготовка для горячей прокатки изготовлена из технически чистого титана. Предпочтительно титановая плоская заготовка для горячей прокатки отливается в электроннолучевой плавильной печи. В способе получения титановой плоской заготовки для горячей прокатки в электронно-лучевой плавильной печи скорость извлечения титановой плоской заготовки находится в диапазоне от 1,0 см/мин или больше. В способе прокатки титановой плоской заготовки для горячей прокатки заготовку подают в стан горячей прокатки и подвергают горячей прокатке в рулон полосового материала. Следует отметить, что согласно настоящему изобретению титановая плоская заготовка непосредственно после литья подвергается горячей прокатке после удаления впадин, выпуклостей и других дефектов на поверхности отливки посредством механической или другой обработки, или, если поверхность отливки является гладкой и находится в хорошем состоянии, указанная выше обработка до горячей прокатки исключается. Таким образом, титановая плоская заготовка, подвергаемая горячей прокатке, имеет структуру поперечного сечения, полученную при отливке заготовки, или структуру поперечного сечения, полученную после механической обработки или т.п. Изобретение позволяет достигнуть результата, заключающегося в том, что горячую прокатку полученной с помощью электронно-лучевой плавильной печи титановой плоской заготовки на стане горячей прокатки общего назначения (например, для стали) для получения рулона полосового материала осуществляют без прохождения заготовкой предварительного процесса обжима, такого как блюминг или процесс рихтования. Кроме того, достигнут эффект минимизации поверхностных дефектов в рулоне полосового материала (плоский материал), сформованного путем горячей прокатки. Краткое описание фигур На фиг. 1 показаны диаграммы зависимости между углом (далее угол ), образованным направлением роста кристаллических зерен в ходе затвердевания и направлением, параллельным направлению горячей прокатки материала (продольное направление), и степенью распространения дефектов поверхности после горячей прокатки. Уголсоответствует углумежду направлением затвердевания титановой плоской заготовки и направлением, параллельным направлению литья; на фиг. 2 показаны затвердевшая структура заготовки в поперечном сечении, параллельном направлению литья титановой плоской заготовки для горячей прокатки согласно настоящему изобретению, и уголмежду направлением затвердевания заготовки (направлением роста кристаллических зерен) и направлением, параллельным направлению литья; на фиг. 3 - то же, но при меньшем значении угламежду направлением затвердевания заготовки(направление роста кристаллических зерен) и направлением, параллельным направлению литья; на фиг. 4 - поперечное сечение титановой плоской заготовки с затвердевшей структуры, вид в перспективе; на фиг. 5 - схематическое изображение электронно-лучевой плавильной печи. Варианты осуществления изобретения На фиг. 1 показана зависимость между углом , образованным направлением роста кристаллических зерен в ходе затвердевания и направлением, параллельным направлению горячей прокатки материала (продольное направление), и степенью распространения дефектов поверхности после горячей про-3 020258 катки материала. Этот уголсоответствует углу , образованному направлением затвердевания титановой плоской заготовки и направлением, параллельным направлению литья. Отлитая титановая плоская заготовка имеет литую структуру, аналогичную той, что показана на фиг. 2 и 3. Для каждого уровня испытаний из отлитой плоской заготовки из технически чистого титана типа 2 по стандарту JIS (JIS Н 4600) нарезают два материала для прокатки (толщина 50 мм, ширина 130 мм,длина 170 мм) и обрабатывают таким образом, чтобы уголимел различные значения от 0 до 90. Подлежащий прокатке материал нагревают до 800, 850 или 900C и затем подвергают горячей прокатке до толщины 5 мм. После этого полученный горячей прокаткой плоский материал подвергают дробеструйной обработке, маркируют возникшие дефекты поверхности и оценивают степень их распространения. Следует отметить, что дефекты поверхности имеют задиры вследствие дробеструйной обработки, за счет чего их можно легко обнаружить, касаясь поверхности рукой в рабочей перчатке. Поверхность плоского материала, полученного горячей прокаткой, за исключением неровных областей на переднем и заднем концах в направлении прокатки, разбивают на сегменты размером 100 мм, а степень распространения дефектов поверхности определяют как отношение числа сегментов с участками, на которых были обнаружены поверхностные дефекты, к общему числу сегментов (всего 30 сегментов для двух плоских материалов после горячей прокатки). Как показано на фиг. 1, при всех температурах нагревания степень распространения дефектов поверхности является весьма высокой и превышает 60% при малом угле , равном 30 или меньше, однако она снижается до 20% или меньше, когда уголравен 45 или больше, и стабилизируется на уровне 10% или меньше, когда уголравен 70 или больше. Как следует из диаграмм, показанных на фиг. 1, для подавления степени распространения дефектов поверхности в ходе горячей прокатки очень важно контролировать угол, который образуется между направлением роста кристаллических зерен (направлением затвердевания) и продольным направлением титановой плоской заготовки, соответствующим направлению литья. Следует отметить, что поверхность после вышеупомянутой дробеструйной обработки выглядит так, как показано на фиг. 2 (представляет собой поверхность, не подвергнутую травлению смесью азотной и фтористо-водородной кислот), причем возникшие дефекты поверхности можно оценить весьма тщательно. Далее описана затвердевшая структура титановой плоской заготовки для горячей прокатки согласно настоящему изобретению. На фиг. 2 показаны затвердевшая структура в поперечном сечении, параллельном направлению литья титановой плоской заготовки для горячей прокатки согласно настоящему изобретению, и уголмежду направлением затвердевания и направлением, параллельным направлению литья. Указанный уголсоответствует углуна фиг. 1. Макроструктура полученной изложенным ниже способом титановой плоской заготовки, представляющей собой образец из технически чистого титана тип 2 по стандарту JIS (JIS Н 4600), показана на фиг. 2 в поперечном сечении с отмеченными кристаллическими зернами для облегчения распознавания направления затвердевания (направление роста кристаллических зерен). В качестве сравнения на фиг. 3 показаны затвердевшая структура в поперечном сечении, параллельном направлению литья титановой плоской заготовки, и уголмежду направлением затвердевания и направлением, параллельным направлению литья. Макроструктура плоской затвердевшей заготовки в поперечном сечении показана на фиг. 3 в виде отмеченных кристаллических зерен для облегчения распознавания направления затвердевания (направление роста кристаллических зерен). На фиг. 4 показано поперечное сечение затвердевшей структуры в перспективе. Для исследования затвердевшей структуры (литой структуры) и измерения указанного выше углав продольном сечении, параллельном направлению извлечения плоской заготовки, т.е. направлению литья (заштрихованная прямоугольная поверхность на фиг. 4), из титановой плоской заготовки, полученной с использованием электронно-лучевой плавильной печи, отрезают плоскую заготовку и протравливают ее поверхность после полировки. Произвольно выбирают 50 кристаллических зерен из зерен, расположенных в указанном сечении,которое пересекает прямую линию, параллельную направлению литья, на уровне 1/4 от толщины плоской заготовки (приблизительно на глубине 60-70 мм), и с помощью анализа изображений рассчитывают среднее значение углаглавной оси (соответствуетв настоящем изобретении). В частности, для каждого из аппроксимирующих эллипсов, соответствующих отдельным кристаллическим зернам (площадь эллипсов соответствует кристаллическим зернам), определяют следующие величины: длину большой оси a, длину малой оси b и угол главной оси(уголобразован прямой линией на уровне 1/4 толщины плоской заготовки и главной осью, совпадающей с большой осью данного аппроксимирующего эллипса) по методу наименьших квадратов таким образом, чтобы минимизировать сумму квадратов отклонений между данным аппроксимирующим эллипсом и реальным профилем кристаллического зерна. В результате обнаружено, что средние значения углов главной осидля затвердевших структур,-4 020258 показанных на фиг. 2 и 3, составляют 61 и 22, соответственно. Как показано на фиг. 5, титановая плоская заготовка 6 согласно настоящему изобретению имеет затвердевшую структуру, сформировавшуюся в процессе охлаждения в литейной форме 4, причем затвердевание структуры можно регулировать путем изменения количества тепла, подводимого электронной пушкой 1, путем изменения области облучения пушкой, изменением скорости литья (скорости извлечения), изменением охлаждающей способности литейной формы 4 и т.п., таким образом, чтобы образовывался практически постоянный угол между направлением затвердевания титановой плоской заготовки 6 и направлением, параллельным направлению литья. Путем установления значения указанного углав диапазоне от 45 до 90, как показано в затвердевшей структуре на фиг. 2, согласно первому варианту осуществления изобретения достигается эффект подавления впадин/выпуклостей и других дефектов поверхности отливки, а также происходит минимизация дефектов поверхности после горячей прокатки. При малом значении , меньше чем 45, в затвердевшей структуре, как показано на фиг. 3, структура становится более удлиненной в направлении извлечения плоской заготовки, т.е. в продольном ее направлении. Подобная затвердевшая структура легко образуется в условиях относительно малой скорости затвердевания и неглубокой ванны жидкого металла 5. Когда вышеупомянутая плоская заготовка подвергается горячей прокатке, на начальной стадии прокатки возникают впадины, которые становятся исходными точками дефектов поверхности и превращаются в дефекты поверхности по мере осуществления последующей горячей прокатки, что нежелательно. Хотя механизм возникновения указанных впадин изучен не полностью, полагают, что причина их возникновения заключается в том, что, как видно на поверхности плоской заготовки на фиг. 3, видимые кристаллические зерна являются крупными вследствие того, что затвердевшая структура является удлиненной в продольном направлении, в результате чего наблюдается тенденция к образованию больших складок при сжатии в вертикальном направлении (деформация сдвига). Кроме того, возможно, что впадины возникают не только из-за наличия крупнокристаллических зерен, но также и из-за ориентации кристаллов, например из-за волнистости и бороздчатости металла. Напротив, в затвердевшей структуре согласно настоящему изобретению, показанной на фиг. 2, уголсоставляет от 45 до 90, т.е. направление затвердевания почти перпендикулярно поверхности плоской заготовки, в результате чего подавляется возникновение впадин в начале прокатки и достигается эффект минимизации дефектов поверхности после горячей прокатки. Предполагается, что причина заключается в том, что на поверхности плоской заготовки, показанной на фиг. 2, кристаллические зерна мельче, чем в заготовке, показанной на фиг. 3. Предпочтительно, как показано на фиг. 1, уголсоставляет от 70 до 90, и согласно второму варианту осуществления изобретения поверхностный слой плоской заготовки имеет структуру, в которой уголсоставляет от 70 до 90,и толщину 10 мм и более, поскольку это обеспечивает сильную минимизацию дефектов поверхности после горячей прокатки. Как показано на фиг. 2, вышеупомянутый поверхностный слой со структурой, имеющей уголот 70 до 90, представляет собой слой, образованный кристаллическими зернами, обозначенными точками(S), и расположенный непосредственно под поверхностью плоской заготовки. Когда средняя толщина поверхностного слоя из 50 условных кристаллических зерен указанной структуры поверхностного слоя составляет меньше 10 мм, то иногда не может быть достигнут соответствующий эффект подавления дефектов поверхности в связи с малой толщиной поверхностного слоя. С целью предельной минимизации дефектов поверхности, возникающих при горячей прокатке титановых плоских заготовок, полученных с использованием электронно-лучевой плавильной печи, было проведено исследование влияния ориентации кристаллов на образование впадин, в ходе которого была определена ориентация кристаллов -фазы титана, имеющей гексагональную плотноупакованную структуру, с помощью рентгеновского метода Лауэ части поверхностного слоя плоской заготовки с угломот 70 до 90 и части поверхностного слоя плоской заготовки, для которой значениеотклоняется от указанного, и были сопоставлены распределения ориентации кристаллов. В результате было обнаружено, что в части поверхностного слоя с угломот 70 до 90 угол наклона С-оси альфа-фазы (сокращенно ) титана (с гексагональной плотно упакованной структурой) на виде со стороны боковой поверхности заготовки, подлежащей горячей прокатке (направление нормали определяется как 0), не меньше 35 и достигает значения около 90, причем отсутствуют углысо значениями в диапазоне от 0 до менее 35. С другой стороны, когда уголменьше 70,также может иметь значение в диапазоне от 0 до 35. Таким образом, уголможет иметь значение во всем диапазоне от 0 до 90. Более того, установлено, что при значениименьше чем 45 значениеможет быть статистически распределено во всем диапазоне от 0 до 90 с меньшим систематическим отклонением, и также значениешироко распределено в области менее 35. Другими словами, это означает, что ориентация С-оси кристаллов -фазы при значениименьше чем 35 является почти перпендикулярной к поверхности пло-5 020258 ской заготовки, которая будет прокатана, и такая ориентация кристаллов подавляется при задании углаот 70 до 90. Наоборот, когдаменьше чем 70, т.е. фактически значениераспределено в диапазоне меньше 35, полагают, что это приведет к возникновению дефектов поверхности после горячей прокатки. Следует отметить, что образец, используемый при макроструктурном исследовании для определения вышеупомянутого угла(плоская заготовка нарезана, отполирована и протравлена в продольном сечении, параллельном направлению извлечения плоской заготовки, т.е. направлению литья), применяется при записи лауэграммы. На уровне 10 мм вглубь от поверхности плоской заготовки, которая подвергается горячей прокатке, целевой W-пучок рентгеновских лучей (диаметр пучка 0,5 мм) направляют на кристаллические зерна в каждой из 40-50 точек образца, регистрируют дифракционные пятна Лауэ от альфа-фазы титана (гексагональная плотноупакованная структура) с помощью метода рентгеноструктурного анализа обратных лауэграмм и определяют ориентацию кристаллов -фазы титана (гексагональная плотноупакованная структура) по дифракционным пятнам Лауэ с использованием программы анализа лауэграмм (Laue Analysis System Ver. 5.1.1, продукт фирмы Norm Engineering Co., Ltd.). Значениев каждой точке измерения получают определением ориентации кристаллов -фазы. Поскольку уголпредставляет собой угол наклона С-оси относительно направления нормали к поверхности плоской заготовки, подлежащей горячей прокатке (направление нормали определяется как 0), его минимальное значение составляет 0 и максимальное 90. Также было установлено, что на глубине 5 мм от поверхности плоской заготовки, которая подвергается горячей прокатке согласно настоящему изобретению, наблюдается такое же распределение значения , как и на глубине 10 мм, и, поскольку вплоть до глубины 10 мм распределение находится на первой стадии кристаллических зерен поверхностного слоя, как показано в поперечном сечении затвердевшей структуры на фиг. 2, можно утверждать, что значениебудет распределено до 35 и на глубину больше 10 мм от поверхности, которая подвергается горячей прокатке. Учитывая вышеизложенное, согласно третьему варианту осуществления настоящего изобретения в титановой плоской заготовке, отлитой с использованием электронно-лучевой плавильной печи, формируется слой толщиной 10 мм или больше, состоящий из кристаллических зерен, у которых уголнаклона С-оси гексагональной плотно упакованной структуры, представляющей собой -фазу, на виде со стороны боковой поверхности плоской заготовки, подлежащей горячей прокатке, во всех измеряемых точках находится в диапазоне от 35 до 90 от направления нормали к поверхности, подлежащей горячей прокатке (направление нормали определяется как 0). С целью более стабильного подавления дефектов поверхности после горячей прокатки в промышленности является желательным наличие поверхностного слоя, состоящего из кристаллических зерен, с диапазоном значенийот 40 до 90. Полагают, что достижение значенийв диапазоне от 40 до 90 возможно путем регулирования условий отливки, по меньшей мере, таким образом, чтобы толщина поверхностного слоя со структурой, имеющей значенияот 75 до 90, составляла 10 мм или больше. При использовании пучка электронов, который может быть сжат за счет поляризации, можно легко подвести тепло даже в узкую зону между литейной формой и расплавленным титаном, за счет чего обеспечивается надежный контроль поверхности отливки и затвердевшей структуры. Когдазадается в диапазоне от 45 до 90 с использованием электронно-лучевой плавильной печи,расплавленный титан быстро затвердевает и можно отделить титан от поверхности литейной формы за счет термического сжатия на относительно ранней стадии, так что достигается эффект улучшения свойств поверхности отливки путем устранения схватывания между литейной формой и титаном. С другой стороны, при вакуумно-плазменном плавлении (в дуге плазмы) нет возможности отклонения дуги, как в случае пучка электронов при электронном плавлении пучком, что делает затруднительным регулирование области облучения в плавильной печи и поддержание баланса количества подведенного тепла; это затрудняет получение затвердевшей структуры титановой плоской заготовки для горячей прокатки согласно настоящему изобретению. Поверхность отлитой плоской заготовки подвергают механической обработке для удаления впадин,выпуклостей и других дефектов поверхности отливки, затем осуществляют горячую прокатку заготовки до толщины приблизительно 3-6 мм, впоследствии проводят процесс очистки от окалины путем дробеструйной обработки и травления смесью азотной и фтористо-водородной кислот и визуально оценивают поверхностные дефекты. Согласно изобретению предпочтительно, чтобы толщина титановой плоской заготовки для горячей прокатки составляла от 225 до 290 мм, а отношение ширины W заготовки к толщине T заготовки (W/T) составляло от 2,5 до 8,0. Когда толщина титановой плоской заготовки превышает 290 мм или W/T8,0,нагрузка при прокатке становится большой вследствие увеличенной площади поперечного сечения плоской заготовки, и происходит схватывание между валком прокатывающих вальцов и титаном, поэтому после горячей прокатки качество поверхности может ухудшиться, а также может быть превышена допустимая предельная нагрузка на стан горячей прокатки. Кроме того, могут возникнуть осложнения при поддержании высокой скорости затвердевания и может быть затруднено получение углаот 45 до 90. Напротив, при малой толщине, меньшей 225 мм, и когда отношение W/T становится меньше 2,5, с поверхности (верхней и нижней) вблизи кромки плоской заготовки беспрепятственно происходит потеря тепла на угловые и/или боковые части литейной формы, так что иногда трудно контролировать получение углаот 45 до 90, т.е. направление затвердевания со стороны угловых участков поверхности. Кроме того, при малой толщине, меньшей 225 мм, нагрузка на затвердевшую оболочку становится большой, когда увеличивается скорость извлечения в ходе скоростной разливки, что также нежелательно с точки зрения возникновения разломов затвердевшей оболочки и других проблем. Более того, когда отношение W/T становится меньшим 2,5, возрастает боковое уширение вследствие разбухания в начале горячей прокатки и иногда развиваются краевые трещины и/или дефекты стыков. С точки зрения эффективности производства плоской заготовки для горячей прокатки с использованием электронно-лучевой плавильной печи, а также стабильности транспортировки заготовки для прокатки в рулон полосового материала с использованием стана горячей прокатки общего назначения (для стали или т.п.), предпочтительно поддерживать величину L/W, т.е. отношение длины L к ширине W титановой плоской заготовки для горячей прокатки, равной 5 или больше, а длину плоской заготовки - равной 5000 мм или больше. Титан является легким металлом, его плотность составляет 60% от плотности стали, поэтому при малом отношении L/W и короткой длине плоской заготовки силы реакции от действия транспортных валков и т.п. могут вызвать пульсацию плоской заготовки, из-за чего могут возникнуть дефекты на поверхности после горячей прокатки. Как указано выше, предпочтительно длина плоской заготовки составляет 5000 мм или больше, более предпочтительно 5600 мм, еще более предпочтительно 6000 мм или больше, причем самая предпочтительная длина составляет 7000 мм или больше. Вышеупомянутую титановую плоскую заготовку для горячей прокатки получают следующими способами. Как показано на фиг. 5, исходный расплавляемый материал для получения титановой плоской заготовки согласно настоящему изобретению загружается в подину 3, расплавляется под действием пучка 2 электронов, испускаемых электронной пушкой 1, смонтированной выше поддона, объединяется с расплавом, удерживаемым в подине 3, и выливается внутрь литейной формы 4, установленной ниже подины 3. Расплав 9, вылитый в литейную форму 4, объединяется с расплавом титана в ванне 5, сформированной внутри литейной формы 4, и нижняя часть расплава титана в ванне 5 извлекается снизу со скоростью извлечения титановой плоской заготовки 6, постепенно затвердевая с образованием титановой плоской заготовки. Указанную титановую плоскую заготовку извлекают, поддерживая ее с помощью опоры 7, смонтированной на вершине извлекающего штока 8. Следует отметить, что указанное направление извлечения представляет собой направление литья. Титановую плоскую заготовку 6 заданной длины вынимают из электронно-лучевой плавильной печи в атмосферу. Внутри электронно-лучевой плавильной печи поддерживается заданный уровень вакуума, причем расплавленный титан и нагретая до высокой температуры полученная плоская заготовка находятся в атмосфере пониженного давления и почти не подвергаются окислению. Затем передняя и боковые поверхности плоской заготовки подвергаются необходимой механической обработке для того,чтобы получить титановую плоскую заготовку для горячей прокатки. В настоящем изобретении для получения титановой плоской заготовки для горячей прокатки с использованием электронно-лучевой плавильной печи используется прямоугольная литейная форма, при этом скорость извлечения титановой плоской заготовки из литейной формы составляет 1 см/мин или больше. Когда скорость извлечения титановой заготовки становится меньшей 1,0 см/мин, расплав титана в ванне 5 становится неглубоким, поскольку замедляется скорость разливки, и влияние теплового потока между литейной формой и титановой ванной затрудняет получение углаот 45 до 90. Кроме того, иногда образуется осадок под действием испарения из расплава титана в ванне 5, который налипает на стенках литейной формы 4 выше расплава титана в ванне 5. Кроме того, когда скорость извлечения титановой заготовки становится маленькой, т.е. меньшей 1,0 см/мин, значительно растет вышеупомянутый осадок, поскольку для литья требуется больше времени. Это нежелательно, поскольку осадок может попасть между стенками расплава титана в ванне 5 и литейной формы 4 и может вовлекаться на поверхность титановой плоской заготовки 6, образовавшейся при затвердевании расплава титана в ванне 5, в результате чего ухудшается качество поверхности полученной отливки титановой плоской заготовки 6. Более предпочтительна скорость извлечения 1,5 см/мин или больше, поскольку можно стабильно получать литую структуру и поверхность отливки в подходящем состоянии. С точки зрения регулирования литой структуры и получения хорошего состояния поверхности отливки, отсутствуют основания для ограничения скорости извлечения, однако, когда скорость извлечения титановой заготовки 6 превышает 10 см/мин, может возникнуть прорыв незатвердевшего расплава вследствие извлечения титановой плоской заготовки 6 из литейной формы 4 в неполностью затвердевшем состоянии, что нежелательно. С другой стороны, при использовании стали скорость разливки плоской заготовки составляет приблизительно от 100 до 300 мм/мин, что гораздо выше, чем при использовании титана согласно настоящему изобретению, однако для титана необходим контроль над неокисляющей атмосферой для подавления окисления в ходе плавления и последующего затвердевания, вследствие чего скорость разливки(скорости извлечения) должна быть ограничена. Таким образом, согласно изобретению более предпочтительно, чтобы скорость извлечения титановой заготовки из литейной формы 4 находилась в диапазоне от 1,5 до 10 см/мин. Поскольку поверхность отлитой титановой плоской заготовки, полученной в указанных выше условиях, имеет отличное качество, достигнут результат, заключающийся в возможности значительно минимизировать механическую или другую обработку поверхности до процесса горячей прокатки. Более того,в зависимости от характеристик поверхности отливки обработка поверхности может быть исключена. В результате также может быть устранено снижение выхода продукта вследствие обработки поверхности заготовки. В настоящем изобретении в титановой плоской заготовке, полученной вышеупомянутым способом,значительно подавляется возникновение поверхностных дефектов в ходе горячей прокатки, и, поскольку указанная заготовка имеет идеальную форму для подачи в стан горячей прокатки общего назначения,можно исключить, например, традиционную операцию обжима болванки в плоскую заготовку, подходящую для горячей прокатки, а также последующий процесс рихтования. Таким образом, для титановой плоской заготовки, полученной вышеупомянутым способом, достигнут результат, заключающийся в обеспечении возможности ее подачи непосредственно в стан горячей прокатки общего назначения, используемый для стали или т.п., без прохождения через процесс предварительной обработки. Более того, титановая плоская заготовка, полученная с использованием электронно-лучевой плавильной печи, для горячей прокатки предварительно нагревается. Для снижения сопротивления деформации предпочтительно температуру нагрева задают в диапазоне от 800 до 950C. Кроме того, с целью подавления образования окалины в ходе нагревания заготовки предпочтительно температуру нагрева задают ниже точки перехода в -фазу. Следует отметить, что из титановой плоской заготовки согласно настоящему изобретению можно эффективно изготовить рулон полосового материала толщиной приблизительно от 2 до 10 мм с помощью описанной выше горячей прокатки. Таким образом, согласно настоящему изобретению титановая плоская заготовка перерабатывается соответствующим образом путем горячей прокатки и, кроме того, в титановом плоском материале, полученном путем горячей прокатки, значительно подавлены дефекты поверхности, причем, даже если впоследствии материал подвергается холодной прокатке, из него можно получить прочный лист. Изобретение подробно объясняется с использованием следующих примеров. Пример 1. 1. Исходный материал для плавления - губчатый титан. 2. Устройство для плавления - электронно-лучевая плавильная печь. 1) Мощность пучка электронов: в области подины - максимум 1000 кВт; в области литейной формы - максимум 400 кВт. 2) Литейная форма прямоугольного сечения. Размер сечения: высота - 270 мм, ширина - 1100 мм. Конструкция - стальная пластина с водяным охлаждением. 3) Скорость извлечения - от 0,2 до 11,0 см/мин. 4) Прочее. Область облучения (сканирования) пучком электронов на периферийной области литейной формы регулируется таким образом, чтобы получать поверхность отливки и затвердевшую структуру с соответствующими характеристиками. Из исходного материала с помощью вышеуказанного устройства соответствующей конструкции получают плоские заготовки технически чистого титана тип 2 по стандарту JIS различной длины: 5600,6000, 7000, 8000 и 9000 мм. Поверхность полученных титановых заготовок подвергают механической обработке, чтобы удалить с ее поверхности впадины, выпуклости и другие дефекты поверхности. Затем используют вышеописанный метод для измерения углав сечении структуры (затвердевшей). Глубину механической обработки варьируют в некоторой степени с целью регулирования толщины поверхностного слоя, имеющегоот 70 до 90. Указанные титановые плоские заготовки подвергают горячей прокатке в рулон полосового материала толщиной приблизительно 5 мм с использованием оборудования для горячей прокатки стали. После того как рулон полосового материал был подвергнут дробеструйной обработке и травлению смесью азотной и фтористо-водородной кислот, материал визуально обследуется на наличие дефектов поверхности, и решается вопрос о его приемке или отбраковке, для чего вычисляют показатель приемки путем определения распространения дефектов поверхности на отдельных участках рулона длиной 1 м. Распространение дефектов поверхности (показатель приемки) определяют путем идентификации их наличия/отсутствия на отдельных участках рулона длиной 1 м после дробеструйной обработки и травления смесью азотной и фтористо-водородной кислот. Участок, на котором отсутствуют поверхностные дефекты, считается прошедшим испытание, причем показатель приемки определяют как отношение количества участков, прошедших испытание с положительным результатом, к общему числу участков 100(%). Показатель приемки, меньший 90%, определяется как брак (Б), от 90 до 95% является хорошим(хор.), и 95% или больше - отличным (отл.). В табл. 1 показаны состояние поверхности отлитой плоской заготовки, характеристики затвердевшей структуры в продольном сечении (уголна уровне одной четверти толщины, толщина поверхностной структуры, в которой уголсоставляет от 70 до 90), и параметры распространения дефектов поверхности рулона полосового материала, полученного горячей прокаткой. Таблица 1 Показатель приемки определяют путем визуального обследования поверхностных дефектов после дробеструйной обработки и травления смесью азотной и фтористо-водородной кислот и оценивают наличие/отсутствие поверхностных дефектов на отдельных участках рулона длиной 1 м. Оценка брак (Б) ставится, когда показатель приемки меньше 90%, хорошая (хор.) оценка - от 90 до 95%, и отличная оценка (отл.) при степени приемки 95% и выше. В примерах 1-10 согласно изобретению, в которых скорость извлечения изменяется от 1,0 до 5,0 см/мин,качество поверхности отлитой титановой плоской заготовки является хорошим, причем не наблюдаются признаки выплесков расплавленного материала или других прилипаний. С другой стороны, в сравнительных примерах 1 и 2, в которых скорость извлечения составляет меньше 1 см/мин, что соответствует вышеупомянутому нижнему пределу, наблюдаются признаки выплесков или других прилипаний, образовавшихся на поверхности полученной титановой плоской заготовки из-за разбрызгивания из ванны 5 с титаном. В сравнительном примере 3, в котором была установлена самая высокая скорость извлечения 11 см/мин, температура поверхности титановой плоской заготовки 6, извлеченной из литейной формы 4,оказалась очень высокой, поэтому отливка была прекращена. В примерах 1-10 согласно изобретению, в которых скорость извлечения изменяется от 1,0 до 5,0 см/мин,уголзатвердевшей структуры плоской заготовки в продольном сечении на уровне одной четверти толщины составляет от 47 до 79, т.е. больше 45, причем показатель приемки дефектов поверхности после горячей прокатки составляет 91% или больше, т.е. дефекты поверхности подавляются. Кроме того, в примере 3 согласно изобретению и в примерах 6-10 согласно изобретению, в которых толщина поверхностной структуры, имеющейот 70 до 90, составляет 10 мм или больше, показатель приемки дефектов поверхности после горячей прокатки является стабильно высоким, 97% или больше. Следует отметить, что в примерах 2 и 3 согласно изобретению, в которых скорость извлечения составляет 1,2 см/мин, и в примерах 4-7 согласно изобретению со скоростью извлечения 1,5 см/мин варьируют глубину механической обработки поверхности полученной плоской заготовки с целью регулирования толщины поверхностного слоя, имеющего уголот 70 до 90. С другой стороны, в сравнительном примере 1 и сравнительном примере 2, в которых скорость извлечения составляет 0,2 и 0,5 см/мин, уголна уровне одной четверти толщины равен 22 и 31, соответственно, причем оба значения меньше 45, поэтому после горячей прокатки показатель приемки дефектов поверхности является весьма низким, менее 70%, причем наблюдаются грубые дефекты. В табл. 2 приведены примеры для технически чистого титана тип 1 по стандарту JIS и для титановых сплавов, имеющих состав: Ti - 1% Fe - 0,36% О (% означает мас.%) и Ti - 3% Al - 2,5% V (% означает мас.%). Исходные материалы для плавления были подготовлены таким образом, чтобы получить заданный состав в вышеупомянутых условиях производства. Для технически чистого титана тип 1 по стандарту JIS и для титановых сплавов, имеющих состав: Ti - 1% Fe - 0,36% О и Ti - 3% Al - 2,5% V, были получены результаты, аналогичные полученным для технически чистого титана тип 2 по стандарту JIS из табл. 1. Таблица 2 Показатель приемки определяют путем визуального обследования поверхностных дефектов после дробеструйной обработки и травления смесью азотной и фтористо-водородной кислот и оценивают наличие/отсутствие поверхностных дефектов на отдельных участках рулона длиной 1 м. Оценка брак (Б) ставится, когда показатель приемки меньше чем 90%, хорошая (хор.) оценка - от 90 до менее чем 95%, и отличная оценка (отл.) при степени приемки 95% или больше. В примерах 11-17 согласно изобретению, в которых скорость извлечения изменяется от 1,0 до 4,0 см/мин,качество поверхности отлитой титановой плоской заготовки является хорошим, причем не наблюдаются признаки выплесков расплавленного материала или других прилипаний. Даже для различных типов сплавов получено хорошее качество поверхности отливок при заданной скорости извлечения. С другой стороны, в сравнительных примерах 4-6, в которых скорость извлечения составляет менее 1 см/мин, что соответствует вышеупомянутому нижнему пределу, наблюдаются признаки выплесков или других прилипаний, образовавшихся на поверхности полученной титановой плоской заготовки из-за разбрызгивания из ванны 5 с титаном. В примерах 11-17 согласно изобретению, в которых скорость извлечения изменяется от 1,0 до 4,0 см/мин,уголзатвердевшей структуры плоской заготовки в продольном сечении на уровне одной четверти толщины составляет от 46 до 74, т.е. больше 45, причем показатель приемки дефектов поверхности после горячей прокатки составляет 92% или больше, т.е. дефекты поверхности подавляются. Кроме того, в примерах 12-17 согласно изобретению, в которых толщина поверхностной структуры, имеющейот 70 до 90, составляет 10 мм или больше, показатель приемки дефектов поверхности после горячей прокатки является стабильным на высоком уровне, 97% или больше. С другой стороны, в сравнительных примерах 4-6, в которых скорость извлечения является небольшой (0,5 см/мин), уголна уровне одной четверти толщины равен приблизительно 30, т.е. меньше 45, поэтому после горячей прокатки показатель приемки дефектов поверхности является весьма низким,менее 75%, причем наблюдаются грубые дефекты. Следует отметить, что в примерах 1-10 и 11-17 согласно изобретению, несмотря на то что после горячей прокатки на кромках рулона полосового материала имеются крошечные трещины, указанные материалы практически не содержат трещин, причем краевые трещины не вызывают никаких проблем даже после следующей холодной прокатки до толщины приблизительно 0,5 мм. Таким образом, в примерах 11-17, выполненных согласно настоящему изобретению, подтверждается, что возможно эффективное производство титановой плоской заготовки с отличной поверхностью отливки и титанового плоского материала с пониженным содержанием дефектов поверхности в ходе горячей прокатки. Кроме того, по указанной выше методике определяют ориентацию кристаллов -фазы титана (гексагональной плотно упакованной структуры) на уровне 10 мм вглубь от поверхности плоской заготовки по методу Лауэ, приблизительно для каждых 40 точек образца. В табл. 3 для определяемой ориентации кристаллов показан диапазон распределения угла , который определяется как наблюдаемый со стороны поверхности плоской заготовки, которая подвергается горячей прокатке, угол наклона направления С-оси-фазы титана (гексагональной плотноупакованной структуры) относительно направления нормали к поверхности плоской заготовки, подлежащей горячей прокатке (направление нормали определяется как 0). Как показано, в табл. 3, в примерах 3, 6-10 и 12-17 согласно изобретению, в которых показатель приемки поверхностных дефектов после горячей прокатки остается стабильным на высоком уровне, 97% или больше, значениенаходится в диапазоне от 35 до 90. С другой стороны, в примерах 2, 4 и 11 согласно изобретению и в сравнительных примерах 1, 2, 4, 5 и 6, в которых поставлены оценки хор. (показатель приемки от 90 до менее чем 95%) и Б (показатель приемки меньше чем 90%), значениераспределяется в диапазоне от 4 до 21 и меньше чем 35. Кроме того, можно отметить, что в сравнительных примерах 1, 2, 4, 5 и 6 значениераспределяется в еще более узком диапазоне от 4 до 7 или больше. Таблица 3 Промышленная применимость Настоящее изобретение относится к способу получения титановой плоской заготовки с использованием электронно-лучевой плавильной печи и к плоской заготовке. Согласно настоящему изобретению возможно получение титановой плоской заготовки, которая подвергается горячей прокатке в рулон полосового материала или плоский материал, в частности титановой плоской заготовки, отлитой в электронно-лучевой плавильной печи, которую можно подавать непосредственно в стан горячей прокатки общего назначения (например, для стали и т.п.) для получения рулона полосового материала без предварительного прохождения отлитой плоской заготовки через процесс обжима, такой как блюминг или процесс рихтования. Более того, в плоской заготовке согласно настоящему изобретению можно подавить появление дефектов поверхности в рулоне полосового или плоского материала. В результате можно существенно снизить потребление энергии и эксплуатационные расходы при изготовлении рулона полосового материала или плоского материала. ФОРМУЛА ИЗОБРЕТЕНИЯ 1. Титановая плоская заготовка для горячей прокатки, характеризующаяся тем, что она выполнена посредством отливки в условиях, при которых угол между направлением ее литья и направлением затвердевания находится в диапазоне от 45 до 90. 2. Титановая плоская заготовка по п.1, характеризующаяся тем, что в части ее поверхностного слоя имеется область толщиной 10 мм или больше, образованная в условиях, когда угол между направлением литья заготовки и направлением затвердевания находился в диапазоне от 70 до 90. 3. Титановая плоская заготовка для горячей прокатки, характеризующаяся тем, что она выполнена посредством отливки в электронно-лучевой плавильной печи и содержит слой толщиной 10 мм или больше из кристаллических зерен, для которых угол наклона С-оси гексагональной плотно упакованной структуры, являющейся альфа-фазой титана, относительно направления нормали к поверхности, подлежащей горячей прокатке, находится в диапазоне от 35 до 90, где направление нормали определяется как 0. 4. Титановая плоская заготовка по любому из пп.1-3, характеризующаяся тем, что ее толщина составляет от 225 до 290 мм и отношение W/T ширины W к толщине T составляет от 2,5 до 8,0. 5. Титановая плоская заготовка по любому из пп.1-3, характеризующаяся тем, что отношение L/W ее длины L к ширине W составляет 5 или больше, а длина L равна 5000 мм или больше. 6. Титановая плоская заготовка по любому из пп.1-3, характеризующаяся тем, что она изготовлена из технически чистого титана. 7. Титановая плоская заготовка по любому из пп.1-3, характеризующаяся тем, что она является титановой плоской заготовкой для горячей прокатки, отлитой в электронно-лучевой плавильной печи. 8. Способ получения титановой плоской заготовки для горячей прокатки по п.1 или 2 в электроннолучевой плавильной печи, характеризующийся тем, что скорость извлечения титановой плоской заготовки составляет не менее 1,0 см/мин, при этом угол между направлением ее литья и направлением затвердевания находится в диапазоне от 45 до 90. 9. Способ получения титановой плоской заготовки для горячей прокатки по п.3 в электроннолучевой плавильной печи, характеризующийся тем, что скорость извлечения титановой плоской заготовки составляет на менее 1,0 см/мин, при этом в титановой плоской заготовке образуется слой из кристаллических зерен, для которых угол наклона С-оси гексагональной плотно упакованной структуры, являющейся альфа-фазой титана, относительно направления нормали к поверхности, подлежащей горячей прокатке, находится в диапазоне от 35 до 90. 10. Способ прокатки титановой плоской заготовки для горячей прокатки, характеризующийся тем,что титановую плоскую заготовку для горячей прокатки по любому из пп.1-3 подают в стан горячей прокатки и подвергают горячей прокатке в рулон полосового материала.
МПК / Метки
МПК: B22D 11/041, B22D 11/20, B22D 11/00, B22D 21/06, C22B 9/22, C22B 34/12, B22D 27/02
Метки: прокатки, способ, заготовка, получения, плоская, титановая, горячей
Код ссылки
<a href="https://eas.patents.su/15-20258-titanovaya-ploskaya-zagotovka-dlya-goryachejj-prokatki-sposob-ee-polucheniya-i-sposob-ee-prokatki.html" rel="bookmark" title="База патентов Евразийского Союза">Титановая плоская заготовка для горячей прокатки, способ ее получения и способ ее прокатки</a>
Предыдущий патент: Новый конъюгат интерферона альфа с полиэтиленгликолем, представленный одним позиционным изомером пэг-nαh-ифн, и иммунобиологическое средство на его основе
Следующий патент: Соединения бензотиадиазепина, способ их получения и фармацевтические композиции, содержащие их
Случайный патент: Соединение бензазепина и его применения