Способ запуска фракционирующей колонны
Формула / Реферат
1. Способ запуска фракционирующей колонны, которая фракционно перегоняет синтезированные углеводороды, получаемые реакцией синтеза Фишера-Тропша, включающий стадии, на которых
выводят из реактора Фишера-Тропша во внешнюю часть легкие синтезированные углеводороды, которые находятся в газообразном состоянии в реакторе, осуществляющем реакцию синтеза Фишера-Тропша;
охлаждают лёгкие синтезированные углеводороды, выгружаемые из указанного реактора для ожижения;
подают сжиженные легкие синтезированные углеводороды во фракционирующую колонну и
нагревают легкие синтезированные углеводороды и осуществляют циркулирование легких нагретых углеводородов во фракционирующей колонне.
2. Способ запуска фракционирующей колонны по п.1, в котором выгрузку легких синтезированных углеводородов из реактора Фишера-Тропша начинают перед извлечением тяжелых синтезированных углеводородов, которые находятся в жидком состоянии в указанном реакторе.
3. Способ запуска фракционирующей колонны по п.2, в котором уровень поверхности суспензии в указанном реакторе во время запуска устанавливают более низким, чем уровень поверхности суспензии в реакторе в течение нормального режима работы.
4. Способ запуска фракционирующей колонны по любому из пп.1-3, в котором непрореагировавший исходный газ, смешанный с синтезированными углеводородами, которые находятся в газообразном состоянии в указанном реакторе, выгружают из реактора и непрореагировавший исходный газ направляют назад в реактор.
5. Способ запуска фракционирующей колонны по любому из пп.1-4, далее включающий выделение воды, содержащейся в легких синтезированных углеводородах.
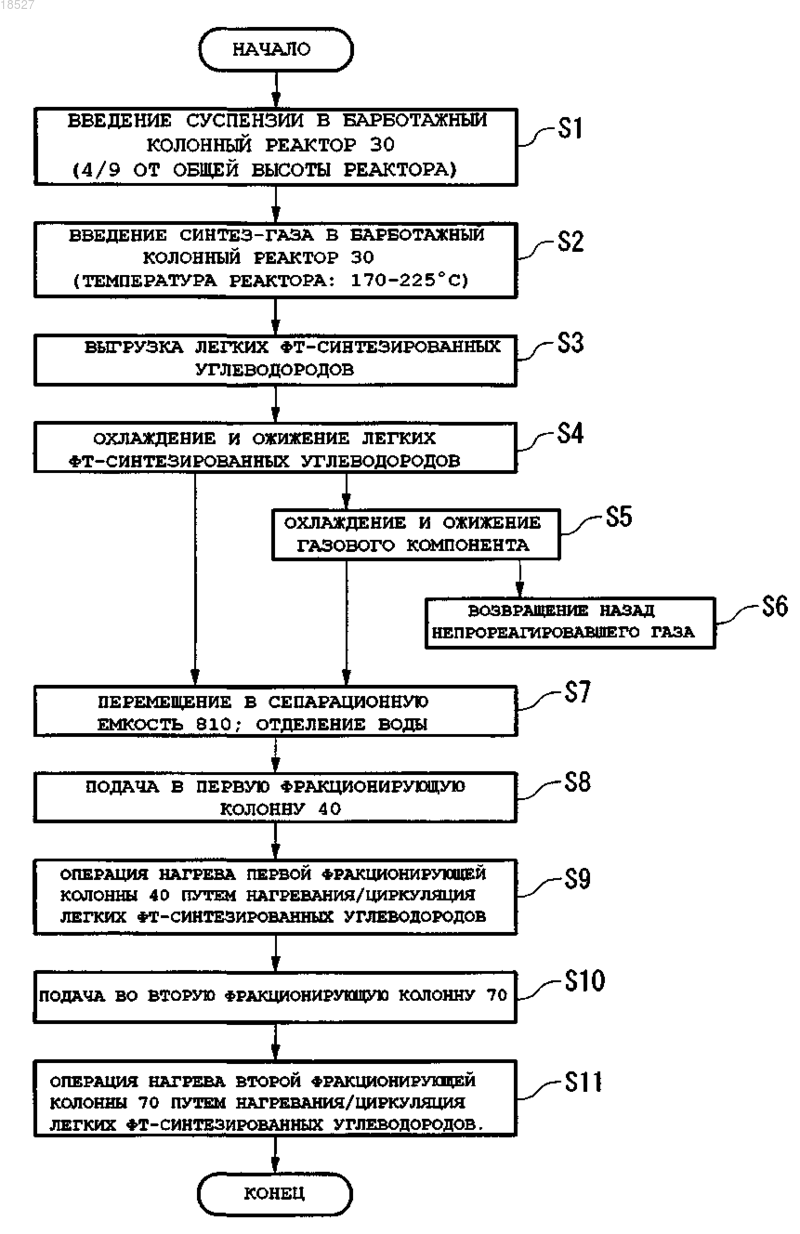
Текст
СПОСОБ ЗАПУСКА ФРАКЦИОНИРУЮЩЕЙ КОЛОННЫ Способ запуска ректификационной колонны для ректификации углеводородов, синтезированных по методу Фишера-Тропша, получаемых ФТ-синтезом. Способ включает этап, на котором легкие ФТ-синтезированные углеводороды, присутствующие в виде газа в ФТ-реакторе, где проводят синтез Фишера-Тропша, выводят из ФТ-реактора; этап, на котором легкие ФТсинтезированные углеводороды, выводимые из ФТ-реактора, охлаждают для того, чтобы ожижать углеводороды; этап, на котором сжиженные легкие ФТ-синтезированные углеводороды, подают в ректификационную колонну, и этап, на котором легкие ФТ-синтезированные углеводороды нагревают и циркулируют в ректификационной колонне.(71)(73) Заявитель и патентовладелец: ДжейЭкс НИППОН ОЙЛ ЭНД ЭНЕРДЖИ КОРПОРЕЙШН; ДЖЭПЭН ОЙЛ, ГЭЗ ЭНД МЕТАЛЗ НЭШНЛ КОРПОРЕЙШН; ИНПЕКС КОРПОРЕЙШН; ДЖАПАН ПЕТРОЛЕУМ ЭКСПЛОРЕЙШН КО., ЛТД.; КОСМО ОЙЛ КО., ЛТД.; НИППОН СТИЛ ИНДЖИНИРИНГ КО., ЛТД. (JP) Область техники Настоящее изобретение относится к способу запуска фракционирующей колонны, которая фракционно перегоняет ФТ-синтезированные углеводороды, получаемые реакцией синтеза Фишера-Тропша. Испрашивается приоритет по японской патентной заявке 2008-254221, поданной 30 сентября 2008 г., содержание которой включается сюда посредством ссылки. Уровень техники Недавно была развита в качестве одного из способов синтеза жидких топлив из природного газаGTL (синтез жидкого топлива "газ-в-жидкость") технология конверсии природного газа для получения синтез-газа, содержащего в качестве главных компонентов газообразный (СО) монооксид углерода и газообразный (Н 2) водород, синтеза углеводородов с использованием этого синтез-газа в качестве источника газа, посредством реакции синтеза Фишера-Тропша (в дальнейшем, в некоторых случаях, именуемой как "реакция ФТ-синтеза"), и далее гидрогенизацию и очистку углеводородов для получения жидких топливных продуктов, таких как нафта (сырой бензин), керосин, газойль, парафин. Здесь, поскольку жидкие топливные продукты, получаемые из ФТ-синтезированных углеводородов, получаемых реакцией ФТ-синтеза, в качестве исходного сырья, имеют высокое содержание парафинов и почти не содержат какие-либо серосодержащие компоненты, как показано, например, в патентном документе 1, то к ним привлечено внимание как к топливам, которые совместимы с окружающей средой. Далее ФТ-синтезированные углеводороды, подаваемые во фракционирующую колонну, например,как показано в патентном документе 2, фракционно перегоняют соответственно точкам кипения, и подвергнутые фракционной перегонке углеводороды затем получают из разгрузочных отверстий, соответствующим образом установленных в верхней части, средней части и нижней части фракционирующей колонны. Перечень ссылок Патентный документ Патентный документ 1. Нерассмотренная патентная публикация Японии 2004-323626. Патентный документ 2. Нерассмотренная патентная публикация Японии S61-167402. Сущность изобретения Проблемы, которые изобретение должно решать Между тем, в вышеописанной фракционирующей колонне, когда углеводороды с высокими точками плавления подают в состоянии, когда температура низкая, то тяжелые углеводороды затвердевают и теряется их текучесть. В результате, фракционную перегонку будет невозможно осуществить. По этой причине во время запуска фракционирующей колонны внутреннюю часть фракционирующей колонны заполняют легкими углеводородами, эквивалентными газойлю (число атомов углерода примерно 11-20),и углеводороды нагревают посредством теплообменнника, устанавливаемого вне фракционирующей колонны, и циркулируют внутри фракционирующей колонны для осуществления операции нагрева, таким образом, чтобы внутренняя часть фракционирующей колонны нагревалась до определенной температуры. Таким образом, когда такие углеводороды, эквивалентные газойлю, загружают, то во время запуска необходимо обеспечить резервуар или подобное для углеводородов, эквивалентных газойлю. Далее, поскольку углеводороды, которые в основном получаются содержащими серу (S), по меньшей мере, на уровне частей на миллион (ч/млн), то существует вероятность, что катализатор в реакторе очистки, который очищает подвергнутые фракционной перегонке ФТ-синтезированные углеводороды, может становиться зашлакованным. Более того, поскольку сера (S) будет смешиваться с продуктами, когда углеводороды, эквивалентные газойлю, перемешиваются с продуктами, то необходимо бесперебойно сливать углеводороды. Настоящее изобретение было сделано с учетом вышеупомянутой ситуации и его целью является обеспечение способа запуска фракционирующей колонны, который может нагревать фракционирующую колонну для работы без применения углеводородов, эквивалентных газойлю, получаемых из внешнего источника, и может получать высококачественные жидкие топлива, не беспокоясь о содержащейся сере(S), когда осуществляется операция нагрева фракционирующей колонны, которая фракционно перегоняет ФТ-синтезированные углеводороды, получаемые реакцией ФТ-синтеза. Средства решения проблемы Для того чтобы решить вышеупомянутые проблемы и достичь такой цели, настоящее изобретение предлагает следующие средства. Способ запуска фракционирующей колонны согласно настоящему изобретению является способом запуска фракционирующей колонны, которая фракционно перегоняет ФТ-синтезированные углеводороды, получаемые реакцией ФТ-синтеза. Способ включает выгрузку из ФТ-реактора во внешнюю часть легких ФТ-синтезированных углеводородов, которые находятся в газообразном состоянии в ФТреакторе, осуществляющем реакцию синтеза Фишера-Тропша; охлаждение легких ФТ-синтезированных углеводородов, выгруженных из ФТ-реактора для ожижения; подачу сжиженных легких ФТсинтезированных углеводородов во фракционирующую колонну и нагревание легких ФТсинтезированных углеводородов и циркуляцию легких ФТ-синтезированных углеводородов во фракцио-1 018527 нирующей колонне. Согласно способу запуска фракционирующей колонны, имеющему вышеуказанную конфигурацию,легкие ФТ-синтезированные углеводороды, которые находятся в газообразном состоянии, выгружают,охлаждают и ожижают, загружают во фракционирующую колонну и легкие ФТ-синтезированные углеводороды циркулируют, будучи нагретыми. Таким образом, операция нагрева фракционирующей колонны может осуществляться без использования жидких углеводородов, эквивалентных газойлю, получаемых из внешнего источника. Следовательно, не является необходимым обеспечивать резервуар или подобное для углеводородов, эквивалентных газойлю. Далее поскольку легкие ФТ-синтезированные углеводороды, полученные ФТ-синтезом, вряд ли включают любые серосодержащие соединения, то не существует вероятности, что катализатор в реакторе очистки, который очищает ректифицированные ФТсинтезированные углеводороды, отравится, и, таким образом, могут эффективно получаться жидкие топлива, такие как нафта, газойль и керосин. Более того, поскольку легкие ФТ-синтезированные углеводороды, которые являются первоначально сырьем, подаваемым в реактор гидроочистки, не имеют проблем при гидроочистке, даже если являются смешанными с продуктом, то не является необходимым отделять и сливать легкие ФТ-синтезированные углеводороды. Выгрузка легких ФТ-синтезированных углеводородов из ФТ-реактора может начинаться перед извлечением тяжелых ФТ-синтезированных углеводородов, которые находятся в жидком состоянии в ФТреакторе. В этом случае, после того как легкие синтезированные углеводороды выгружают из ФТ-реактора и осуществляют операцию нагрева фракционирующей колонны, тяжелые ФТ-синтезированные углеводороды подают во фракционирующую колонну. В результате фракционная перегонка во фракционирующей колонне может быть надежно и эффективно осуществляемой. Далее тяжелые ФТ-синтезированные углеводороды с большим числом атомов углерода могут предохраняться от перемешивания с легкими ФТ-синтезированными углеводородами, и может быть обеспечена текучесть легких ФТ-синтезированых углеводородов. Далее уровень поверхности в ФТ-реакторе во время запуска может устанавливаться ниже, чем уровень поверхности в ФТ-реакторе в течение нормального режима работы. В этом случае путем установления уровня поверхности в ФТ-реакторе более низкого, чем он же в течение нормального режима работы, извлечение тяжелых ФТ-синтезированных углеводородов не начинается до тех пор, пока тяжелые ФТ-синтезированные углеводороды не достигнут уровня поверхности ФТ-реактора в течение нормального режима работы, даже если получаются тяжелые ФТсинтезированные углеводороды. Однако легкие ФТ-синтезированные углеводороды, которые находятся в газообразном состоянии, выгружают из разгрузочного отверстия в верхней части ФТ-реактора с начальной стадии ФТ-реакции. То есть может быть сделана разновременность между началом выгрузки легких ФТ-синтезированных углеводородов из ФТ-реактора и началом извлечения тяжелых ФТсинтезированных углеводородов. В дополнение, предпочтительно, чтобы уровень поверхности во время запуска был бы пониженным, принимая во внимание требуемое, подаваемое во фракционирующую колонну, количество легких ФТ-синтезированных углеводородов. Например, предпочтительно устанавливать уровень поверхности во время запуска около 60-70% от уровня в течение нормального режима работы. Более того, непрореагировавший исходный газ, смешанный с легкими ФТ-синтезированными углеводородами, которые находятся в газообразном состоянии в ФТ-реакторе, может выгружаться из ФТреактора, и непрореагировавший исходный газ может возвращаться назад в ФТ-реактор. Внутри ФТ-реактора непрореагировавший исходный газ (синтез-газ из монооксида углерода и водорода) смешивают с легкими ФТ-синтезированными углеводородами, которые находятся в газообразном состоянии в пределах ФТ-реактора. Посредством возвращения этого исходного газа в ФТ-реактор может быть улучшена производительность углеводородов реакцией ФТ-синтеза. Далее способ может в дальнейшем включать выделение воды, содержащейся в легких ФТсинтезированных углеводородах. Поскольку вода (пар) получается в качестве побочного продукта в ФТ-реакторе, то пар также содержится в легких ФТ-синтезированных углеводородах, которые находятся в газообразном состоянии в ФТ-реакторе. Следовательно, примешивание воды во фракционирующей колонне может предотвращаться путем установки устройства выделения воды. Преимущество изобретения Согласно настоящему изобретению, когда осуществляют операцию нагрева фракционирующей колонны, которая фракционно перегоняет ФТ-синтезированные углеводороды, получаемые реакцией ФТсинтеза, возможно обеспечить способ запуска фракционирующей колонны, который может нагревать фракционирующую колонну для работы без использования углеводородов, эквивалентных газойлю, получаемых из внешнего источника, и может получать высококачественные жидкие топлива, не беспокоясь о включении любых серосодержащих (S) компонентов. Краткое описание чертежей Фиг. 1 - принципиальная схема, показывающая общую конфигурацию системы синтеза жидкого топлива, включающую фракционирующие колонны (первую фракционирующую колонну, вторую фракционирующую колонну) согласно варианту осуществления настоящего изобретения. Фиг. 2 - детальный пояснительный вид вокруг фракционирующих колонн (первой фракционирующей колонны, второй фракционирующей колонны) согласно варианту осуществления настоящего изобретения. Фиг. 3 - блок-схема, показывающая способ запуска фракционирующих колонн (первой фракционирующей колонны или второй фракционирующей колонны) согласно варианту осуществления настоящего изобретения. Фиг. 4 - детальный пояснительный вид вокруг фракционирующих колонн (первой фракционирующей колонны, второй фракционирующей колонны) согласно другому варианту осуществления настоящего изобретения. Описание вариантов осуществления В дальнейшем предпочтительные варианты осуществления настоящего изобретения будут описаны со ссылкой на прилагаемые чертежи. Первой со ссылкой на фиг. 1 будет описана общая конфигурация и процесс системы синтеза жидкого топлива (реакционная система углеводородного синтеза), где применяется способ запуска фракционирующей колонны, который является вариантом осуществления настоящего изобретения. Как показано на фиг. 1, система синтеза жидкого топлива (реакционная система углеводородного синтеза) 1 согласно варианту осуществления является промышленным устройством для осуществленияGTL-процесса, который превращает углеводородное сырье, такое как природный газ и подобное в жидкие топлива. Систему синтеза жидкого топлива 1 конструируют с установкой получения синтез-газа 3,установкой ФТ-синтеза, установкой повышения качества продукта 7. В установке получения синтез-газа 3 природный газ, который является углеводородным сырьем,облагораживают для получения синтез-газа, содержащего газообразный монооксид углерода и газообразный водород. В установке ФТ-синтеза 5 полученный синтез-газ подвергают реакции ФТ-синтеза для получения жидких углеводородов (ФТ-синтезированных углеводородов). В установке повышения качества продукта 7 жидкие углеводороды (ФТ-синтезированные углеводороды), полученные реакцией ФТ-синтеза, подвергают гидропереработке и фракционной перегонке,чтобы получить жидкотопливные продукты (нафту, керосин, газойль, парафин и подобное). Компоненты, которые составляют каждую установку, будут описываться ниже. Установка получения синтез-газа 3 в основном включает, например, реактор обессеривания 10, установку риформинга 12, котел-утилизатор 14, парожидкостные сепараторы 16 и 18 и установку выделения СО 2 20, и водородный сепаратор 26. Реактор обессеривания 10 состоит из установки гидрообессеривания и т.д., и выделяет серосодержащие компоненты из природного газа как сырья. Установка риформинга 12 улучшает качество природного газа, подаваемого из реактора обессеривания 10 для получения синтез-газа, содержащего в качестве главных компонентов газообразный (СО) монооксид углерода и газообразный (Н 2) водород. Котел-утилизатор 14 рекуперирует отходящее тепло синтез-газа, получаемого в установке риформинга 12 для получения пара высокого давления. Парожидкостной сепаратор 16 разделяет воду, нагреваемую посредством теплообмена с синтез-газом в котле-утилизаторе 14, на пар(пар высокого давления) и жидкость. Парожидкостной сепаратор 18 отделяет конденсат от синтез-газа,охлажденного в котле-утилизаторе 14, и подает газовый компонент в установку выделения СО 2 20. Установка выделения СО 2 20 имеет абсорбционную башню 22, которая выделяет из синтез-газа диоксид углерода путем использования абсорбента, подаваемого из парожидкостного сепаратора 18, и регенерационную башню 24, которая десорбирует диоксидуглеродный газ и регенерирует абсорбент, содержащий диоксидуглеродный газ. Водородный сепаратор 26 отделяет часть газообразного водорода, содержащуюся в синтез-газе, диоксидуглеродном газе, который был отделен установкой выделения СО 2 20. Здесь необходимо отметить, что вышеуказанную установку выделения СО 2 20 необязательно устанавливают в зависимости от условий. Установка ФТ-синтеза 5 состоит из, например, барботажного колонного реактора (барботажный колонный реактор углеводородного синтеза) 30, парожидкостного сепаратора 34, сепаратора 36, парожидкостного сепаратора 38 и первой фракционирующей колонны 40. Барботажный колонный реактор 30 является примером реактора, который синтезирует жидкие углеводороды (ФТ-синтезированные углеводороды) из синез-газа и работает как реактор ФТ-синтеза, который синтезирует жидкие углеводороды (ФТ-синтезированные углеводороды) из синтез-газа посредством реакции ФТ-синтеза. Барботажный колонный реактор 30 конструируют как, например, барботажный реактор с суспендированным слоем, в котором содержится суспензия, возникшая путем суспендирования твердых частиц катализатора в жидких углеводородах (ФТ-синтезированных углеводородах). Барботажный колонный реактор 30 подвергает синтез-газ (газообразный монооксид углерода и газообразный водород), получаемый установкой получения синтез-газа, реакции синтеза жидких углеводородов (ФТ-синтезированные углеводороды). Парожидкостной сепаратор 34 отделяет пар (пар среднего давления) и жидкость от воды, циркулируемой и нагреваемой в теплообменной трубе 32, установленной внутри барботажного колонного реактора 30. Сепаратор 36 отделяет частицы катализатора и жидкие углеводороды (ФТ-синтезированные углеводороды) от суспензии, содержащейся в барботажном колонном реакторе 30. Парожидкостной сепаратор 38 присоединяют к вершине барботажного колонного реактора 30 и охлаждают непрореагировавший синтез-газ и газовый компонент ФТ-синтезированных углеводородов. Первая фракционирующая колонна 40 перегоняет жидкие углеводороды (ФТ-синтезированные углеводороды), подаваемые из барботажного колонного реактора 30, через сепаратор 36 и парожидкостной сепаратор 38 и фракционирует жидкие углеводороды (ФТ-синтезированые углеводороды) на каждую фракцию согласно точкам кипения. Установка повышения качества продукта 7 состоит из, например, реактора гидрокрекинга парафиновой фракции 50, реактора гидроочистки среднего дистиллята 52, реактора гидроочистки фракции нафты 54, парожидкостных сепараторов 56, 58 и 60, второй фракционирующей колонны 70 и колонны стабилизации нафты 72. Реактор гидроочистки парафиновой фракции 50 присоединяют к кубовой части первой фракционирующей колонны 40, а парожидкостной сепаратор 56 располагают ниже по потоку от реактора. В реакторе гидрокрекинга парафиновой фракции 50 для промотирования реакции используют катализатор. Реактор гидроочистки среднего дистиллята 52 присоединяют к средней части первой фракционирующей колонны 40, а парожидкостной сепаратор 58 располагают ниже по потоку от реактора. В реакторе гидроочистки среднего дистиллята 52 для промотирования реакции используют катализатор. Реактор гидроочистки фракции нафты 54 присоединяют к верхней части первой фракционирующей колонны 40, а парожидкостной сепаратор 60 располагают ниже по потоку от реактора. В реакторе гидроочистки фракции нафты 54 для промотирования реакции используют катализатор. Вторая фракционирующая колонна 70 фракционно перегоняет жидкие углеводороды (ФТсинтезированные углеводороды), подаваемые из парожидкостных сепараторов 56 и 58 согласно точкам кипения. Колонна стабилизации нафты 72 фракционирует жидкие углеводороды (ФТ-синтезированные углеводороды) фракций нафты, подаваемых из парожидкостного сепаратора 60 и второй фракционирующей колонны 70, выгружает бутан и компоненты более легкие, чем бутан в качестве сжигаемого газа (выхлопного газа), и отделяет и удаляет компоненты, имеющие 5 атомов углерода или более в качестве продукта - нафты. Далее будет описываться процесс (GTL-процесс) синтеза жидких топлив из природного газа посредством системы синтеза жидкого топлива 1, сконструированной как указано выше. Природный газ (чьим главным компонентом является СН 4) в качестве углеводородного сырья подают в систему синтеза жидкого топлива 1 из внешнего источника природного газа (не показано), такого как газовое месторождение или завод по производству природного газа. Вышеупомянутая установка получения природного газа 3 облагораживает этот природный газ для получения синтез-газа (смешанного газа, содержащего газообразный монооксид углерода и газообразный водород в качестве главных компонентов). Во-первых, вышеуказанный природный газ подают в реактор обессеривания 10 вместе с газообразным водородом, отделенным водородным сепаратором 26. Реактор обессеривания 10 гидрогенирует и обессеривает серосодержащие компоненты, содержащиеся в природном газе, используя газообразный водород с катализатором, например ZnO. Заблаговременно обессеривая природный газ этим способом,возможно предотвратить деактивацию серосодержащими компонентами катализатора, используемого в установке риформинга 12, барботажном колонном реакторе 30 и т.д. Природный газ, обессеренный этим способом, подают в установку риформинга 12 после того, как перемешиваются газообразный (СО 2) диоксид углерода, подаваемый из источника диоксида углерода (не показано), и пар, генерируемый в котле-утилизаторе 14. Установка риформинга 12 облагораживает природный газ при использовании диоксида углерода и пара для получения высокотемпературного синтезгаза, содержащего газообразный монооксид углерода и газообразный водород, в качестве главных компонентов, посредством способа парового и диоксидуглеродного газового риформинга. Высокотемпературный синтез-газ (например, 900 С, 2,0 МПаГ), полученный в установке риформинга 12 этим путем, подают в котел-утилизатор 14 и охлаждают путем теплообмена с водой, которая протекает через котел-утилизатор 14 (например, 400 С), таким образом выделяют отходящее тепло. В это время воду, нагретую синтез-газом в котле-утилизаторе 14, подают в парожидкостной сепаратор 16. Из парожидкостного сепаратора 16 газовый компонент подают в установку риформинга 12 или другое внешнее оборудование, в качестве пара высокого давления (например, от 3,4 до 10,0 МПаГ), а воду в качестве жидкого компонента возвращают в котел-утилизатор 14. Тем временем синтез-газ, охлажденный в котле-утилизаторе 14, подают в абсорбционную башню 22 установки выделения СО 2 20 или барботажный колонный реактор 30, затем конденсат сепарируют и отделяют от синтез-газа в парожидкостном сепараторе 18. Абсорбционная башня 22 абсорбирует диоксидуглеродный газ, содержащийся в синтез-газе, в оставшийся абсорбент, чтобы отделить диоксидуглеродный газ от синтез-газа. Абсорбент, содержащий диоксидуглеродный газ, внутри этой абсорбционной башни 22 вводят в регенерационную башню 24, абсорбент, содержащий диоксидуглеродный газ, нагревают и подвергают отпаривающей обработке, например, паром, и полученный десорбированный диоксидуглеродный газ рециркулируют в установку риформинга 12 из регенерационной башни 24 и повторно используют для вышеуказанной реакции риформинга. Синтез-газ, полученный в установке получения синтез-газа 3 в этом способе, подают в барботажный колонный реактор 30 вышеуказанной установки ФТ-синтеза 5. В это время соотношение состава синтез-газа, подаваемого в барботажный колонный реактор, регулируют до соотношения состава (например, Н 2:СО (молярное соотношение, подходящее для реакции ФТ-синтеза. Часть синтез-газа, диоксидуглеродный газ которого отделили вышеуказанной установкой выделения СО 2 20, также подают в водородный сепаратор 26. Водородный сепаратор 26 отделяет газообразный водород, содержащийся в синтез-газе, абсорбцией и десорбцией (водородная PSA), используя разницу давления. Этот отделенный водород непрерывно подают из газгольдера (не показано) и т.д. посредством компрессора (не показано) в различное водородиспользующее реакционное оборудование (например,реактор обессеривания 10, реактор гидрокрекинга парафиновой фракции 50, реактор гидроочистки среднего дистиллята 52, реактор гидроочистки фракции нафты 54 и т.д.), которое осуществляет определенные реакции, использующие водород в пределах системы синтеза жидкого топлива 1. Далее вышеуказанная установка ФТ-синтеза 5 синтезирует жидкие углеводороды (ФТсинтезированные углеводороды) реакцией ФТ-синтеза из синтез-газа, получаемого вышеуказанной установкой получения синтез-газа 3. Синтез-газ, полученный в устройстве получения синтез-газа 3, перетекает из кубовой части барботажного колонного реактора 30 и поднимается в катализаторной суспензии, содержащейся в барботажном колонном реакторе 30. В это время внутри барботажного колонного реактора 30 газообразный монооксид углерода и газообразный водород, которые содержатся в синтез-газе, реагируют друг с другом по реакции ФТ-синтеза, таким образом, получая жидкие углеводороды (ФТ-синтезированные углеводороды). Более того путем протекания воды через теплообменную трубу 32 барботажного колонного реактора 30 во время этой реакции синтеза реакционное тепло реакции ФТ-синтеза выделяют, и воду, нагретую этим теплообменом, испаряют в пар. Что касается этого пара, то воду, сжиженную в парожидкостном сепараторе 34, возвращают в теплообменную трубу 32, а газовый компонент подают во внешнее оборудование в качестве пара среднего давления (например, от 1,0 до 2,5 МПаГ). Жидкие углеводороды (ФТ-синтезированные углеводороды), синтезированные в барботажном колонном реакторе 30, вводят в сепаратор 36 в качестве суспензии с частицами катализатора. Сепаратор 36 выделяет из суспензии твердые компоненты, такие как частицы катализатора и подобное, и жидкие компоненты, содержащие жидкие углеводороды (ФТ-синтезированные углеводороды). Часть отделенного катализатора подают в барботажный колонный реактор 30, а жидкий компонент подают в первую фракционирующую колонну 40. С верхней части барботажного колонного реактора 30 непрореагировавший синтез-газ и газовый компонент ФТ-синтезированных углеводородов вводят в парожидкостной сепаратор 38. Парожидкостной сепаратор 38 охлаждает эти газы для отделения части сконденсированных жидких углеводородов (ФТ-синтезированных углеводородов), чтобы вводить их в первую фракционирующую колонну 40. Между тем, что касается газового компонента, отделенного в парожидкостном сепараторе, то непрореагировавший синтез-газ (СО и Н 2) возвращают в кубовую часть барботажного колонного реактора 30 и повторно используют для реакции ФТ-синтеза. Далее отходящий газ (сжигаемый газ) кроме целевых продуктов, содержащий в качестве главного компонента углеводородный газ, имеющий небольшое число атомов углерода (С 4 или меньше), вводят во внешнее сжигающее оборудование (не показано), сжигают здесь и затем выбрасывают в атмосферу. Далее первая фракционирующая колонна 40 нагревает ФТ-синтезированные углеводороды (число атомов углерода которых различное), подаваемые через сепаратор 36 и парожидкостной сепаратор 38 из барботажного колонного реактора 30, как описывалось выше, чтобы фракционно перегонять ФТсинтезированные углеводороды, используя разницу в точках кипения. Таким образом, первая фракционирующая колонна 40 разделяет и очищает ФТ-синтезированные углеводороды на фракцию нафты (чья точка кипения ниже чем примерно 150 С), средний дистиллят (соответствующий керосиновой и газойлевой фракциям, чья точка кипения равна примерно от 150 до 350 С) и парафиновую фракцию (чья точка кипения выше чем примерно 350 С). ФТ-синтезированные углеводороды (в основном C21 или более) в качестве парафиновой фракции,отбираемые из кубовой части первой фракционирующей колонны 40, подают в реактор гидрокрекинга парафиновой фракции 50, ФТ-синтезированные углеводороды (в основном от С 11 до С 20) в качестве среднего дистиллята, отбираемые из средней части первой фракционирующей колонны 40, подают в реактор гидроочистки среднего дистиллята 52, и ФТ-синтезированные углеводороды (в основном от C5 до С 10), в качестве фракции нафты, отбираемые из верхней части первой фракционирующей колонны 40,-5 018527 подают в реактор гидроочистки фракции нафты 54. Реактор гидрокрекинга парафиновой фракции 50 подвергает гидрокрекингу ФТ-синтезированные углеводороды, такие как парафиновая фракция с большим числом атомов углерода (примерно от С 21 и более), которую подали из кубовой части первой фракционирующей колонны 40, путем использования газообразного водорода, подаваемого из вышеуказанного водородного сепаратора 2 6, для уменьшения числа атомов углерода до С 20 или меньше. В этой реакции гидрокрекинга углеводороды с небольшим числом атомов углерода и с низким молекулярным весом получают расщеплением С-С-связей углеводородов с большим числом атомов углерода, используя катализатор и тепло. Продукт, содержащий жидкие углеводороды, подвергнутые гидрокрекингу в этом реакторе гидрокрекинга парафиновой фракции 50,разделяют на газ и жидкость в парожидкостном сепараторе 56, жидкие углеводороды которого подают во вторую фракционирующую колонну 70, а газовый компонент (содержащий газообразный водород) которого подают в реактор гидроочистки среднего дистиллята 52 и реактор гидроочистки фракции нафты 54. Реактор гидроочистки среднего дистиллята 52 подвергает гидроочистке ФТ-синтезированные углеводороды (примерно от С 11 до С 20), такие как средний дистиллят, имеющий в основном среднее число атомов углерода, который подали из средней части первой фракционирующей колонны 40, путем использования газообразного водорода, подаваемого через реактор гидрокрекинга парафиновой фракции 50 из водородного сепаратора 26. В этой реакции гидроочистки для того, чтобы получить главным образом насыщенные углеводороды разветвленной цепи, жидкие углеводороды изомеризуются, и водород добавляют для насыщения связей вышеуказанных жидких углеводородов, чтобы насыщать жидкие углеводороды. В результате продукт, содержащий гидроочищенные жидкие углеводороды, разделяют на газ и жидкость в парожидкостном сепараторе 58, жидкие углеводороды которого подают во вторую фракционирующую колонну 70, а газовый компонент (содержащий газообразный водород) которого повторно используют для вышеуказанной реакции гидрогенизации. Реактор гидроочистки фракции нафты 54 подвергает гидроочистке ФТ-синтезированные углеводороды (примерно С 10 или меньше), такие как фракция нафты с небольшим числом атомов углерода, которую подали из верхней части первой фракционирующей колонны 40, путем использования газообразного водорода, подаваемого через реактор гидрокрекинга парафиновой фракции 50 из водородного сепаратора 26. В результате продукт (гидрогенизированная нафта), содержащий гидроочищенные жидкие углеводороды, разделяют на газ и жидкость в парожидкостном сепараторе 60, жидкие углеводороды которого перемещают в колонну стабилизации нафты 72, а газовый компонент (содержащий газообразный водород) которого повторно используют для вышеуказанной реакции гидрогенизации. Далее вторая фракционирующая колонна 70 перегоняет ФТ-синтезированные углеводороды, подаваемые из реактора гидрокрекинга парафиновой фракции 50 и реактора гидроочистки среднего дистиллята 52, как описывалось выше, чтобы фракционировать их на углеводороды (чьи точки кипения ниже чем примерно 150 С) с количеством атомов углерода С 10 или меньше, керосин (чья точка кипения равна примерно от 150 до 250 С), газойль (чья точка кипения равна примерно от 250 до 350 С) и некрекированную парафиновую фракцию из реактора гидрокрекинга парафиновой фракции 50 (чья точка кипения выше чем примерно 350 С). Некрекированную парафиновую фракцию получают из кубовой части второй фракционирующей колонны 70 и возвращают выше по потоку от реактора гидрокрекинга парафиновой фракции 50. Газойль отбирают из нижней части второй фракционирующей колонны 70, а керосин отбирают из ее средней части. Тем временем углеводородный газ с количеством атомов углерода С 10 или меньше отбирают из верхней части второй фракционирующей колонны 70 и подают в колонну стабилизации нафты 72. Более того, колонна стабилизации нафты 72 перегоняет углеводороды с количеством атомов углерода С 10 или меньше, которые подали из вышеуказанного реактора гидроочистки фракции нафты 54 и второй фракционирующей колонны 70, чтобы отделить нафту (С 5-С 10) в качестве продукта. Соответственно высокочистую нафту отбирают из нижней части колонны стабилизации нафты 72. В то же время выхлопной газ (сжигаемый газ) кроме продукта, содержащий в качестве главного компонента углеводороды с определенным числом атомов углерода или меньше (С 4 или меньше), выводят из верхней части колонны стабилизации нафты 72. Выхлопной газ (сжигаемый газ) вводят во внешнее сжигающее оборудование (не показано на чертежах) и сжигают, таким образом выбрасывают в атмосферу. Процесс (GTL-процесс) системы синтеза жидкого топлива 1 описывался выше. Посредством рассматриваемого GTL-процесса природный газ превращают в топлива, такие как высокочистая нафта (С 5 С 10: неочищенный бензин), керосин (С 11-С 15) и газойль (C18-C20: дизельное топливо). Далее барботажный колонный реактор 30, осуществляющий ФТ-синтез, первая фракционирующая колонна 40 и вторая фракционирующая колонна 70 будут описаны со ссылкой на фиг. 2 и 3. Верхнюю часть барботажного колонного реактора 30, описанного выше, снабжают разгрузочной линией 801, которая выгружает газовый компонент в барботажном колонном реакторе 30. Далее извлекающую линию 901, которая извлекает жидкие углеводороды (ФТ-синтезированные углеводороды) в барботажном колонном реакторе 30, устанавливают в средней части барботажного колонного реактора 30 (положение напримерно 2/3 общей высоты барботажного колонного реактора 30, как показано на фиг. 2 в настоящем варианте осуществления). Извлекающую линию 901 присоединяют к сепаратору 36 через парожидкостной сепаратор 902. Жидкие углеводороды (ФТ-синтезированные углеводороды), отделенные сепаратором 36, подают в первую фракционирующую колонну 40 посредством питающей линии 903. Разгрузочную линию 801 присоединяют к первичному резервуару 803 через теплообменник 802. Верхнюю часть первичного резервуара снабжают соединяющей линией 804, а соединяющую линию присоединяют к вторичному резервуару 806 через теплообменник 805. Верхнюю часть вторичного резервуара 806 снабжают возвратной линией 807, которая позволяет газовому компоненту во вторичном резервуаре 806 перетекать назад в кубовую часть барботажного колонного реактора 30. В дополнение теплообменник 802, первичный резервуар 803, соединяющая линия 804, теплообменник 805 и вторичный резервуар образуют парожидкостной сепаратор 38 на фиг. 1. Первичный резервуар 803 и вторичный резервуар 806 присоединяют к сепарационной емкости 810 через трубопровод 808. Сепарационную емкость 810 присоединяют к питающей линии 903, которую присоединяют к сепаратору 36 и первой фракционирующей колонне 40. Первую фракционирующую колонну 40 снабжают первой циркуляционной линией 813, которая позволяет жидкости, собирающейся в первой фракционирующей колонне 40, посредством этого циркулировать, первым насосом 814, который закачивает жидкость в циркуляционную линию 813, и теплообменником 815, который нагревает жидкость, протекающую внутри циркуляционной линии 813. Далее циркуляционную линию 813 снабжают отводной линией 816, и отводную линию 816 присоединяют ко второй фракционирующей колонне 70. Вторую фракционирующую колонну 70 снабжают второй циркуляционной линией 823, которая позволяет жидкости, собирающейся в первой фракционирующей колонне 40, посредством этого циркулировать, вторым насосом 824, который закачивает жидкость в циркуляционную линию 823, и теплообменником 825, который нагревает жидкость, протекающую внутри циркуляционной линии 823. Далее будет описываться способ запуска первой фракционирующей колонны 40 и второй фракционирующей колонны 70, имеющей вышеуказанную конструкцию. Во-первых, суспензию, получаемую смешиванием жидких углеводородов и частиц катализатора,вводят внутрь барботажного колонного реактора 30, который осуществляет ФТ-синтез (S1). В это время несмотря на то, что суспензию загружают на высоту, превышающую высоту извлекающей линии 901(около 2/3 общей высоты барботажного колонного реактора 30), в течение нормального режима работы,но во время запуска суспензию загружают на примерно 4/9 от общей высоты барботажного колонного реактора 30. То есть во время запуска уровень поверхности (уровень суспензии) в барботажном колонном реакторе 30 устанавливают ниже, чем во время нормального режима работы. Синтез-газ вводят в барботажный колонный реактор 30, чтобы генерировать углеводороды (ФТсинтезированные углеводороды) (S2). Дополнительно предварительно устанавливаемую температуру в барботажном колонном реакторе 30 в это время устанавливают ниже, чем в течение нормального режима работы (210-240 С), в особенности 170-225 С и более предпочтительно 170-210 С. Легкие ФТ-синтезированные углеводороды, которые находятся в газообразном состоянии в барботажном колонном реакторе 30, выгружают во внешнюю часть барботажного колонного реактора 30 через разгрузочную линию 801 при вышеуказанных температурных условиях (S3). В это же время, поскольку тяжелые ФТ-синтезированные углеводороды, которые находятся в жидком состоянии в барботажном колонном реакторе 30, располагаются ниже по высоте от извлекающей линии 901, то углеводороды не выделяются во внешнюю часть. В дополнение, в настоящем варианте осуществления легкие ФТ-синтезированные углеводороды являются примерно С 5-С 20, a тяжелые ФТ-синтезированные углеводороды являются примерно C15-С 100. Легкие ФТ-синтезированные углеводороды, выгружаемые через разгрузочную линию 801, охлаждают до, например, приблизительно 110 С посредством теплообменника 802 и ожижают, затем хранят в первичном резервуаре 803 (S4). Газовый компонент, который находится в газообразном состоянии при вышеуказанных температурных условиях среди легких ФТ-синтезированных углеводородов, хранящихся в первичном резервуаре 803, охлаждают до примерно 45 С теплообменником 805, установленным в соединяющей линии 804, и сжижают, затем хранят во вторичном резервуаре 806 (S5). Поскольку исходный газ (синтез-газ из монооксида углерода и водорода), который не прореагировал внутри барботажного колонного реактора 30, смешивают с газовым компонентом во вторичном резервуаре 806, то непрореагировавший исходный газ возвращают назад в барботажный колонный реактор 30 через возвратную линию 807 (S6). Далее выхлопной газ (сжигаемый газ) кроме целевых продуктов,содержащий в качестве главного компонента углеводородный газ, имеющий небольшое число атомов углерода (С 4 или меньше), вводят во внешнее сжигающее оборудование (не показано), сжигают здесь и затем выбрасывают в атмосферу. Далее в первичном резервуаре 803 и вторичном резервуаре 806 может устанавливаться сливная сис-7 018527 тема для отделения и удаления воды, смешанной со сжиженными легкими ФТ-синтезированными углеводородами, и легкие ФТ-синтезированные углеводороды вводят в сепарационную емкость 810, где далее отделяют и удаляют оставшуюся воду (S7). Здесь поскольку жидкие легкие ФТ-синтезированные углеводороды и вода находятся по-отдельности внутри сепарационной емкости 810, то только вода может быть извлечена из сливного устройства 811, установленного в нижней части сепарационной емкости 810. Легкие ФТ-синтезированные углеводороды, из которых в сепарационной емкости 810 была удалена вода, подают в первую фракционирующую колонну 40 через питающую линию 903 (S8). В это время,поскольку тяжелые ФТ-синтезированные углеводороды не извлекают из извлекающей линии 901, то только легкие ФТ-синтезированные углеводороды подают в первую фракционирующую колонну 40 из питающей линии 903. Затем легкие ФТ-синтезированные углеводороды циркулируют через внутреннюю часть первой циркуляционной линии 813 при помощи первого насоса 814, и легкие ФТ-синтезированные углеводороды нагревают до 150-200 С теплообменником 815 (S9). Таким образом, осуществляют операцию нагрева для первой фракционирующей колонны 40 до определенной температуры (примерно 320 С). Далее часть легких ФТ-синтезированных углеводородов, которые циркулируют через первую циркуляционную линию 813, подают во вторую фракционирующую колонну 70 через отводную линию 816(S10). Затем легкие ФТ-синтезированные углеводороды циркулируют через внутреннюю часть второй циркуляционной линии 823 при помощи второго насоса 824, и легкие ФТ-синтезированные углеводороды нагревают до 150-200 С теплообменником 825 (S11). Таким образом, осуществляют операцию нагрева второй фракционирующей колонны 70 и внутреннюю часть второй фракционирующей колонны 70 нагревают до определенной температуры (около 310 С). После того как первую фракционирующую колонну 40 и вторую фракционирующую колонну 70 нагревают этим способом до их определенной температуры, уровень поверхности тяжелых ФТсинтезированнных углеводородов в барботажном колонном реакторе 30 возрастает, и суспензия извлекается из извлекающей линии 901. Затем тяжелые ФТ-синтезированные углеводороды, от которых в сепараторе 36 отделены частицы катализатора, подают в первую фракционирующую колонну 40 через питающую линию 903 и начинают фракционную перегонку в первой фракционирующей колонне 40 и фракционную перегонку во второй фракционирующей колонне 70. Согласно способу запуска фракционирующей колонны (первой фракционирующей колонны 40 или второй фракционирующей колонны 70) согласно настоящему варианту осуществления, сконструированному, как описано выше, легкие ФТ-синтезированные углеводороды, которые находятся в газообразном виде в барботажном колонном реакторе 30, выгружают из разгрузочной линии 801, охлаждают и сжижают посредством теплообменников 802 и 805, и вводят в первую фракционирующую колонну 40 и вторую фракционирующую колонну 70, и легкие ФТ-синтезированные углеводороды затем циркулируют, поскольку являются нагретыми теплообменниками 815 и 825. Таким образом, может осуществляться операция нагрева первой фракционирующей колонны 40 и второй фракционирующей колонны 70, для их нагревания до их определенной температуры без использования жидких углеводородов, эквивалентных газойлю, получаемых из внешнего источника. Далее, поскольку легкие ФТ-синтезированные углеводороды, полученные ФТ-синтезом, едва ли содержат серосодержащие компоненты, то не существует возможности отравления катализатора, используемого в реакторе гидрокрекинга парафиновой фракции 50, реакторе гидроочистки среднего дистиллята 52 и реакторе гидроочистки фракции нафты 54, которые очищают ФТ-синтезированные углеводороды, подвергнутые фракционной перегонке в первой фракционирующей колонне 40. Следовательно,могут быть эффективно получены жидкие топлива, такие как нафта, газойль и керосин. Более того, поскольку легкие ФТ-синтезированные углеводороды не вызывают проблем, даже будучи смешанными с продуктом, то не является необходимым отделять и удалять легкие ФТсинтезированные углеводороды. Более того, в настоящем варианте осуществления уровень поверхности (уровень суспензии) в барботажном колонном реакторе 30 во время запуска устанавливают ниже (около 4/9 общей высоты барботажного колонного реактора 30), чем она же в течение нормального режима работы (около 2/3 общей высоты барботажного колонного реактора). Таким образом, хотя тяжелые ФТ-синтезированные углеводороды не извлекают во внешнюю часть, до тех пор, пока они не достигнут высоты извлекающей линии 901 барботажного колонного реактора 30, но легкие ФТ-синтезированные углеводороды, которые находятся в газообразном состоянии, выгружают из разгрузочной линии 801 барботажного колонного реактора 30 с начальной стадии ФТ-реакции. То есть может быть сделана разновременность между началом разгрузки ФТ-синтезированных углеводородов из барботажного колонного реактора 30 и началом извлечения тяжелых ФТ-синтезированных углеводородов. Таким образом, после того как легкие ФТ-синтезированные углеводороды выгружают из барботажного колонного реактора 30 и осуществляют операцию нагрева первой фракционирующей колонны 40 и второй фракционирующей колонны 70, тяжелые ФТ-синтезированные углеводороды подают в первую фракционирующую колонну 40 и вторую фракционирующую колонну 70. В результате может быть надежно и эффективно осуществлена фракционная перегонка в первой фракционирующей колонне и второй фракционирующей колонне. Далее тяжелые ФТ-синтезированные углеводороды с большим числом атомов углерода могут удерживаться от смешивания с легкими ФТ-синтезироввнными углеводородами,и может быть обеспечена текучесть легких ФТ-синтезированных углеводородов. Далее поскольку суспензию, получаемую смешиванием жидких углеводородов и частиц катализатора, получаемых из внешних источников, загружают в барботажный колонный реактор 30 во время запуска барботажного колонного реактора 30, то количество жидких углеводородов, требуемых, чтобы получить суспензию, может быть также уменьшено. Далее в настоящем варианте осуществления предварительно устанавливаемую температуру в барботажном колонном реакторе устанавливают равной 170-225 С и более предпочтительно 170-210 С, и устанавливают более низкой, чем предварительно устанавливаемая температура в течение нормального режима работы (210-240 С). Таким образом, точку кипения легких ФТ-синтезированных углеводородов,которые находятся в газообразном состоянии в барботажном колонном реакторе 30, снижают, и получают легкие ФТ-синтезированные углеводороды с небольшим число атомов углерода. Соответственно текучесть легких ФТ-синтезированных углеводородов может быть улучшена, и может быть хорошо осуществлена операция нагрева первой фракционирующей колонны 40 и второй фракционирующей колонны 70. Далее в настоящем варианте осуществления вторичный резервуар 806 снабжают возвратной линией 807, которая выделяет непрореагировавший исходный газ из легких ФТ-синтезированных углеводородов и позволяет непрореагировавшему исходному газу течь назад в барботажный колонный реактор 30. Таким образом, исходный газ (синтез-газ из монооксида углерода и водорода), который не прореагировал внутри барботажного колонного реактора 30, может вынуждаться вновь реагировать внутри барботажного колонного реактора 30, и производительность углеводородов посредством ФТ-синтеза может быть улучшена. Более того, в настоящем варианте осуществления обеспечивают сепарационную емкость 810, которая выделяет воду, содержащуюся в ФТ-синтезированных углеводородах. Таким образом, вода (пар),побочный продукт в барботажном колонном реакторе 30, может быть удалена из ФТ-синтезированных углеводородов, и может быть предотвращено смешивание воды в первой фракционирующей колонне 40 и второй фракционирующей колонне 70. Несмотря на то, что варианты осуществления настоящего изобретения были описаны до настоящего времени детально со ссылкой на чертежи, конкретные конфигурации не ограничиваются вариантами осуществления, и настоящее изобретение также включает изменения конструкций, которые не выходят за пределы сущности настоящего изобретения. Например, несмотря на то, что описана конфигурация, в которой первую циркуляционную линию 813 первой фракционирующей колонны 40 снабжают отводной линией 816, и легкие ФТсинтезированные углеводороды подают во вторую фракционирующую установку 70, но настоящее изобретение не ограничивается этим, как показано на фиг. 4, может быть внедрена конфигурация, в которой легкие ФТ-синтезированные углеводороды подают во вторую фракционирующую колонну 70 прямо из сепарационной емкости 810. Далее может быть внедрена конфигурация, в которой только одну из первой фракционирующей колонны 40 и второй фракционирующей колонны 70 нагревают легкими ФТ-синтезированными углеводородами. Далее в настоящем варианте осуществления конфигурация, в которой разновременность обеспечивают между выгрузкой легких ФТ-синтезированных углеводородов и извлечением тяжелых ФТсинтезированных углеводородов, делая уровень поверхности (поверхность суспензии) в барботажном колонном реакторе 30 во время запуска ниже, чем уровень в течение нормального режима работы. Однако настоящее изобретение не ограничивается этим. Например, резервуар для хранения может быть расположен на извлекающей линии 901 для суспензии, и разновременность может быть обеспечена между выгрузкой легких ФТ-синтезированных углеводородов и извлечением тяжелых ФТ-синтезированных углеводородов. Далее, несмотря на то, что описание было сделано о том, что легкие ФТ-синтезированные углеводороды, выгружаемые из разгрузочной линии 801, охлаждают на двух этапах двумя теплообменниками 802 и 805, но настоящее изобретение не ограничено этим, и легкие ФТ-синтезированные углеводороды могут охлаждаться теплообменником. Более того, хотя описание было сделано о том, что устанавливается сепарационная емкость 810, но сепарационная емкость 810 может не устанавливаться. Однако, поскольку вода может удаляться посредством установления сепарационной емкости 810, и загрязнение во фракционирующей колонне (первой фракционирующей колонне 40 или второй фракционирующей колонне 70) может быть предотвращено,то предпочтительно установить сепарационную емкость 810. Более того, температурный диапазон не ограничивается примерами настоящего варианта осуществления и предпочтительно, чтобы температурный диапазон мог быть установлен подходящим с учетом режима эксплуатации. Однако в циркуляционной линии (первой циркуляционной линии 813 и второй циркуляционной линии 823) необходимо нагревать легкие ФТ-синтезированные углеводороды, чтобы циркулировать до температуры, при которой легкие ФТ-синтезированные углеводороды не затвердевают. Промышленная применимость Согласно способу запуска фракционирующей колонны настоящего изобретения, когда осуществляют операцию нагрева фракционирующей колонны, которая фракционно перегоняет ФТсинтезированные углеводороды, полученные реакцией ФТ-синтеза, фракционирующая установка может быть нагрета без использования углеводородов, эквивалентных газойлю, получаемых из внешнего источника, и высококачественные жидкие топлива могут быть получены, не беспокоясь о включениях серосодержащих (S) соединений. Описание ссылочных номеров 1 - система синтеза жидкого топлива (реакционная система углеводородного синтеза) 30 - барботажный колонный реактор (ФТ-реактор) 40 - первая фракционирующая колонна (фракционирующая колонна) 70 - вторая фракционирующая колонна (фракционирующая колонна) ФОРМУЛА ИЗОБРЕТЕНИЯ 1. Способ запуска фракционирующей колонны, которая фракционно перегоняет синтезированные углеводороды, получаемые реакцией синтеза Фишера-Тропша, включающий стадии, на которых выводят из реактора Фишера-Тропша во внешнюю часть легкие синтезированные углеводороды,которые находятся в газообразном состоянии в реакторе, осуществляющем реакцию синтеза ФишераТропша; охлаждают лгкие синтезированные углеводороды, выгружаемые из указанного реактора для ожижения; подают сжиженные легкие синтезированные углеводороды во фракционирующую колонну и нагревают легкие синтезированные углеводороды и осуществляют циркулирование легких нагретых углеводородов во фракционирующей колонне. 2. Способ запуска фракционирующей колонны по п.1, в котором выгрузку легких синтезированных углеводородов из реактора Фишера-Тропша начинают перед извлечением тяжелых синтезированных углеводородов, которые находятся в жидком состоянии в указанном реакторе. 3. Способ запуска фракционирующей колонны по п.2, в котором уровень поверхности суспензии в указанном реакторе во время запуска устанавливают более низким, чем уровень поверхности суспензии в реакторе в течение нормального режима работы. 4. Способ запуска фракционирующей колонны по любому из пп.1-3, в котором непрореагировавший исходный газ, смешанный с синтезированными углеводородами, которые находятся в газообразном состоянии в указанном реакторе, выгружают из реактора и непрореагировавший исходный газ направляют назад в реактор. 5. Способ запуска фракционирующей колонны по любому из пп.1-4, далее включающий выделение воды, содержащейся в легких синтезированных углеводородах.
МПК / Метки
Метки: способ, колонны, фракционирующей, запуска
Код ссылки
<a href="https://eas.patents.su/13-18527-sposob-zapuska-frakcioniruyushhejj-kolonny.html" rel="bookmark" title="База патентов Евразийского Союза">Способ запуска фракционирующей колонны</a>