Газификация горючих органических материалов
Формула / Реферат
1. Способ получения горючего газа, имеющего низшую теплоту сгорания по меньшей мере 1 МДж/Нм3, в котором проводят реакцию окислительного газа, содержащего водяной пар, или кислород, или CO2, с органическим материалом в контакте с ванной расплавленного силиката, содержащегося в резервуаре, и подводят тепло в расплавленный силикат, причем указанный способ функционирует в непрерывном режиме, силикат регулярно выводят из резервуара и регулярно вводят стеклующиеся материалы для снабжения ванны силиката и для сохранения состава силиката, по существу, постоянным и ниже предела осаждения железа.
2. Способ по п.1, отличающийся тем, что силикат содержит от 40 до 80 вес.% SiO2.
3. Способ по п.2, отличающийся тем, что сумма масс СаО, Fe2O3 и щелочного оксида, содержащихся в силикате, варьируется от 5 до 60 вес.%.
4. Способ по любому одному из предыдущих пунктов, отличающийся тем, что подвод тепла осуществляют по типу погружного горения.
5. Способ по п.4, отличающийся тем, что окислитель топлива для погружного горения содержит более 80 об.% чистого кислорода.
6. Способ по п.5, отличающийся тем, что пламя погружного горения является окислительным.
7. Способ по любому одному из пп.5 или 6, отличающийся тем, что окислительный газ создают погружным горением.
8. Способ по любому одному из пп.5, 6 или 7, отличающийся тем, что погружное горение, с одной стороны, и реакцию между окислительным газом и органическим материалом, с другой стороны, реализуют в разделенных зонах, чтобы дымовые газы и горючий газ могли улавливаться через разные дымовые каналы.
9. Способ по любому одному из пп.5, 6, 7 или 8, отличающийся тем, что в качестве топлива для погружного горения частично используют горючий газ, образованный согласно самому этому способу, причем этот газ факультативно смешивают с другими горючими газами.
10. Способ по любому одному из пп.1-9, отличающийся тем, что органический материал находится в достаточном количестве, чтобы суммарная мольная доля водорода и моноксида углерода в горючем газе составляла по меньшей мере 10%.
11. Способ по любому одному из пп.1-10, отличающийся тем, что окислительный газ содержит по меньшей мере 30 об.% паров воды.
12. Способ по любому одному из пп.1-11, отличающийся тем, что силикат находится при температуре от 800 до 1700°С.
13. Способ по любому одному из пп.1-12, отличающийся тем, что тепло подводится посредством электричества.
14. Способ по любому одному из пп.1-13, отличающийся тем, что горючий газ нагревают, проводя под опущенным сводом, прежде чем вывести его через вытяжной канал.
15. Способ непрерывного промышленного производства стекла, включающий в себя стадии, на которых
непрерывно производят стекло в стекловаренной печи, содержащей топливную газовую горелку, образующую газообразные продукты горения,
указанные газообразные продукты горения используют в бойлере для непрерывного получения водяного пара,
водяной пар, полученный в бойлере, подают в стекловаренную печь для реакции с органическим материалом и получения горючего газа, причем указанный горючий газ получают согласно способу по любому из пп.1-14.
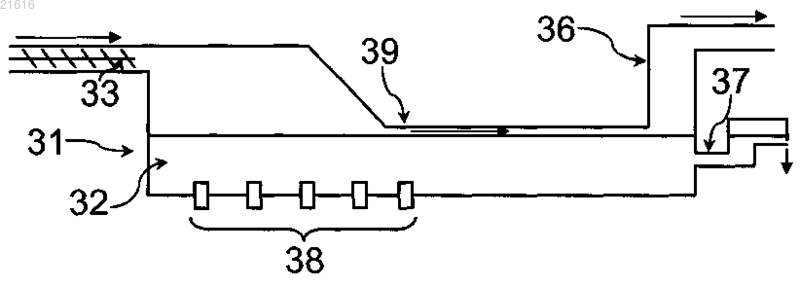
Текст
ГАЗИФИКАЦИЯ ГОРЮЧИХ ОРГАНИЧЕСКИХ МАТЕРИАЛОВ Изобретение относится к способу превращения твердого и жидкого горючего материала в горючий газ. Способ получения горючего газа, имеющего низшую теплоту сгорания по меньшей мере 1 МДж/Нм 3, включает реакцию окислительного газа, содержащего водяной пар, или кислород, илиCO2, с органическим материалом в контакте с ванной расплавленного силиката, содержащимся в резервуаре, и включающий подвод тепла в расплавленный силикат, причем указанный способ функционирует в непрерывном режиме, силикат регулярно выводится из резервуара, и регулярно вводятся стеклующиеся материалы для снабжения ванны силиката и для сохранения состава силиката, по существу, постоянным и ниже предела осаждения железа. Изобретение также относится к способу непрерывного промышленного производства стекла, в котором горючий газ получают согласно способу, описанному выше. Изобретение относится к способу и устройству для превращения твердого или жидкого горючего материала в горючий газ. Целью изобретения является получение горючего газа напрямую из твердых или жидких горючих материалов, как биомасса, и/или из таких отходов, как использованные шины, пластмасса, продукты перемалывания автомобилей, шлаки, из альтернативных топливных материалов (называемых "MCS") и даже бытовых отходов и т.д., или косвенно, исходя из этих же материалов, предварительно превращенных в масло после первого процесса пиролиза. Согласно изобретению предлагается технология, которая направлена на замену применению ископаемой энергии в промышленных процессах, на снижение эмиссии CO2 в атмосферу и на снижение стоимости энергии. Действительно, в целях снижения концентрации парниковых газов в атмосфере производственников соответствующей налоговой политикой побуждают использовать не ископаемую энергию(нефть, природный газ), так как она всегда приносит больше углерода и CO2 к поверхности земли, но возобновляемое горючее, такое как биомасса, которое при своем росте поглощает CO2 из атмосферы,который затем будет выброшен при сгорании биомассы. Однако в промышленных процессах не всегда можно использовать биомассу напрямую, в частности, это обусловлено составом этой биомассы, который обычно приводит к золе. Уже предлагалось получать горючий газ из биомассы, подвергая ее пиролизу при температуре выше 500 С, даже выше 1000 С в неподвижном или кипящем слое, содержащем керамические окатыши или шарики, через который проходит водяной пар, и/или воздух, или чистый кислород. Однако в слое накапливается зола, получаемая из биомассы, что не преминет заблокировать слой. Поэтому газификатор этого типа нужно регулярно останавливать и чистить. Статья MACCORMAC "Gasification of coal in an experimental Rummel double-shaft slag-bath gasifier"(Газификация угля в экспериментальном газификаторе Руммеля со шлаковой ванной и двумя валами),IGE Journal, vol. 5, 1 Mai 1965, рр. 385-399, раскрывает газификацию угля в шлаке. Испытывалось погружное горение в шлаке, но от него отказались из-за проблем, вызванных обильным образованием пены, а также осаждением железа. Действительно, уголь, как и также большинство органических материалов типа биомассы, содержит железо. Даже без погружного горения образуется пена, и осаждается железо, требуя прекращения работы. Металлическое железо трудно удалить, так как это требует очень высоких температур, порядка 1500 С. Теперь же был найден способ, осуществляемый в непрерывном режиме, позволяющий газифицировать органический материал в расплавленной массе, без осаждения железа. Согласно изобретению, в качестве расплавленной массы используется силикат, и указанный силикат непрерывно обновляют, выводя его и регулярно замещая в ходе работы. Это непрерывное обновление ванны силиката позволяет непрерывно выводить железо, концентрация которого остается, таким образом, ниже предела осаждения. Из-за высокого содержания кремнезема силикат вспенивается слабо или совсем не вспенивается, он хорошо растворяет железо. Низкая тенденция силиката к пенообразованию делает возможным даже обеспечить подвод тепла в расплавленный силикат путем погружного горения. Согласно изобретению газификация органического материала, приводящая к получению горючего газа, включает реакцию водяного пара, или кислорода, или CO2 с органическим материалом в контакте с расплавленным силикатом, при этом в расплавленный силикат вносится тепло. Выражение "или" в предыдущем предложении охватывает, разумеется, также выражение "и/или". Выражение "в контакте" охватывает случаи, когда органический материал может быть выше ванны силиката, всплывая в ней, или может находиться внутри ванны силиката, или присутствовать одновременно и в, и на ванне силиката. Предпочтительно окислительный газ, реагирующий с органическим материалом, содержит по меньшей мере 30 об.% воды. Он может содержать даже 100% воды. Окислительный газ может быть также кислородом, который вносится с воздухом. Таким образом, газ для реакции с органическим материалом может быть воздухом или воздухом, обогащенным кислородом. Воздух может быть влажным. Это может быть воздух, наполненный водяным паром. Таким образом, воздух может вносить одновременно кислород, воду и СО 2. Способ согласно изобретению имеет следующие преимущества: полученный газ имеет высокую PCI (низшая теплота сгорания), в частности, от 5 до 25 МДж/Нм 3,зола, которая может содержать нежелательные оксиды и тяжелые металлы, инертизована (нейтрализована) в стеклянную массу, которую можно непрерывно выводить в ходе газификации и которую можно гранулировать для захоронения (по классу 3, то есть класс инертных и неопасных отходов) или использовать в гранулах для гражданского строительства, например, как заполнитель материалов типа битума или асфальта для дорог, шоссе, или в качестве других строительных материалов,способ является компактным и требует ограниченных инвестиций, и может осуществляться в автоматизированном и непрерывном режиме. Таким образом, способ согласно изобретению является одновременно системой производства горючего газа (типа "синтез-газа", или "сингаза", содержащего СО и водород) и системой производства строительных материалов. Благодаря тому, что силикат является жидким, облегчается функционирование всей системы, так как зола органического материала увлекается течением силиката наружу из резер-1 021616 вуара. Обновление силиката в ванне таково, что он сохраняет высокое содержание кремнезема, обычно по меньшей мере 40 вес.% кремнезема. Способ согласно изобретению основан на принципе газификации в среде расплавленного силиката при высокой температуре посредством газа, являющегося окислительным по отношению к углероду. В рамках настоящей заявки "окислительным газом" можно назвать газ, реагирующий с органическим материалом. Газ является не полностью окислительным по отношению к углероду, так как речь не идет о создании избытка CO2, но, напротив, стремятся получить как можно больше газа-восстановителя, такого,как СО и Н 2. На самом деле эта реакция газификации является эндотермической, и поэтому внесение энергии (или тепла) осуществляется в систему прямо в ванну силиката. Таким образом, изобретение относится в первую очередь к способу получения горючего газа, имеющего низшую теплоту сгорания по меньшей мере 1 МДж/Нм 3, включающему в себя реакцию окислительного газа, содержащего водяной пар, или кислород, или CO2, с органическим материалом в контакте с расплавленным силикатом и включающий подвод тепла в расплавленный силикат. Температура силиката устанавливается на уровне от 800 С до 1700 С в зависимости от его химического состава. Он содержит кремнезем и по меньшей мере один оксид из следующей группы: СаО, Fe2O3,Na2O, K2O. Функцией оксида, добавленного к кремнезему, является снизить вязкость силиката, чтобы достичь достаточной текучести, облегчающей перемешивание и, таким образом, желательные реакции. Желательная вязкость варьируется обычно от 10 до 1000 пуаз, предпочтительно от 20 до 500 пуаз при рабочей температуре. В пределах объема изобретения множество силикатов охватывает, в частности, шлаки, стекло и более или менее водорастворимые силикаты, как силикаты щелочных металлов (таких, как Na, K) и/или щелочно-земельных металлов (таких, как Са, Mg), возможно в виде смешанных силикатов (несколько силикатов щелочных и/или щелочно-земельных металлов). Силикат обычно содержит от 40 до 80 вес.% SiO2. Он содержит также по меньшей мере один другой оксид для разжижения ванны, причем указанный оксид обычно может быть выбран из следующей группы: СаО, Fe2O3, Na2O, K2O. Так, силикат может, в частности, содержать 0-20 вес.% СаО,0-20 вес.% Fe2O3,0-20 вес.% щелочного оксида, как Na2O или K2O (это охватывает случай Na2O и/или K2O),причем сумма масс СаО + Fe2O3 + щелочной оксид обычно не равна нулю и предпочтительно лежит в диапазоне от 5 до 60 вес.%. Он может также содержать, в частности, MgO, Al2O3, TiO2, MgO2, Р 2 О 5, SO2, Cl. Один особенно подходящий состав силиката содержит 60-80 вес.% SiO2,10-20%. вес.% СаО,5-15 вес.% Fe2O3,2-10 вес.% щелочного оксида (как Na2O или K2O, что охватывает случай Na2O и/или K2O). Функцией оксида, добавленного к кремнезему, является снижнение вязкости силиката, чтобы достичь достаточную текучесть, облегчающую перемешивание и, таким образом, желательные реакции. Желательная вязкость варьируется обычно от 10 до 1000 пуаз, предпочтительно от 20 до 500 пуаз при рабочей температуре, то есть при температуре от 800 до 1700 С. Расплавленный силикат может содержаться, в частности, в резервуаре, снабженном огнеупорной футеровкой, с перепускной системой с сифоном (или горлом) для отведения избыточного расплавленного силиката. Силикат удерживается в расплавленном состоянии благодаря подводу тепла, которое может осуществляться посредством электричества (обычно электродами, погруженными в силикат, как электроды из молибдена, графита, железа, согласно хорошо известной практике в стекольной промышленности), или которое может получаться в результате введения окислителя топлива, который частично сжигает углерод, образованный при газификации горючих веществ, введенных в силикат, вместе с возможным подводом другого горючего газа. Этот добавленный горючий газ может быть собственно горючим газом(синтез-газ), произведенным устройством по изобретению, после возможного охлаждения, очистки,фильтрации и сжатия, или газом, не производящимся установкой, таким, как водород или ископаемый природный газ, или смесь синтез-газа с тем или другим из двух вышеназванных газов, или же жидким топливом. Очистка служит в основном для удаления воды, а фильтрация служит в основном для удаления пыли и смол. Так как реакция горения является экзотермической, подвод тепла к расплавленному силикату обычно является единственным подводом энергии. Можно также комбинировать нагрев электричеством и нагрев посредством горения. В рамках изобретения подвод тепла осуществляется внутрь силиката погружным устройством, в частности, типа погружного электрода, или погружным горением. Для случая горения в силикат вводится окислитель топлива, которым обычно является кислород, который может вноситься с воздухом. Таким образом, в качестве окислителя топлива можно использовать чистый кислород, воздух или воздух, обогащенный кислородом. Предпочтительно используют окисли-2 021616 тель топлива, содержащий более 80 об.% чистого кислорода, даже чистый кислород, так как это означает сниженный объем газа (если сравнивать, например, с воздухом), что настолько же снижает тенденцию к образованию пены. Погружное горение является предпочтительным механизмом подвода тепла, так как оно способствует перемешиванию веществ в ванне расплавленного силиката. Это перемешивание ведет к лучшей однородности расплавленного силиката в ванне, что благоприятно для отсутствия осаждения,такого, как осаждение железа. Кроме того, предпочтительно, чтобы пламя было окислительным, так как это ведет к окислению металлических частиц в суспензии, что еще больше предотвращает осаждение,например, выпадение железа. Избыток кислорода играет двойную роль в этом погружном горении: 1) он препятствует осаждению металла, и 2) лишний кислород может участвовать в реакции газификации. Газы, введенные в силикат для этого погружного горения, заставляют подниматься частицы, которые возможно образовались. Таким образом, использование для этого погружного горения окислителя топлива с высоким содержанием кислорода или чистого кислорода является отличным компромиссом, позволяющим перемешивать ванну и приводящим к почти полному отсутствию металлического железа, не вызывая излишнего пенообразования. Твердые иди жидкие горючие вещества для газификации вводятся предпочтительно внутрь расплавленного силиката (ниже уровня поверхности жидкого силиката) с помощью подходящего загрузочного устройства (шнековая или поршневая система, насос в случае жидкости и т.д.). Они могут также быть введены на поверхность расплавленного силиката. В зависимости от газа, выбранного для реакции с органическим материалом, газификация осуществляется по меньшей мере по одной из следующих реакций: причем эти реакции являются эндотермическими. При необходимости, если подвод тепла в силикат осуществляется погружным горением, реакция горения кислорода с углеродом органического материала и/или с синтез-газом имеет место согласно причем эти реакции являются экзотермическими. Таким образом, вода и CO2 могут, в частности, получаться в результате погружного горения синтезгаза или смеси синтез-газа с СН 4, и/или Н 2, и/или любым другим горючим газом, причем выгодно затем вводить их в соответствующих пропорциях в газифицируемую массу при повышенной температуре. Дополнительную воду можно также ввести в виде пара или влаги из введенных органических материалов. Получение СО или Н 2 из органического материала является эндотермическим, поэтому подводится тепло. Подвод тепла обычно ограничен до минимума, необходимого для компенсации тепловых потерь устройством и расхода тепла на эндотермическую реакцию газификации, а также, при необходимости,для нагрева входящих газов (H2O, воздух, O2, CO2) . Для случая, когда подвод тепла осуществляется путем погружного горения, его можно отделить от окружения, куда будут вводиться окислительные газы, требующиеся для газификации, в целях повышения теплоты сгорания получаемого горючего газа. В этом случае следует обеспечить непрерывный подвод тепла, создаваемого в зоне погружного горения, к зоне реакции с окислительным газом. Это может быть осуществлено циркуляцией жидкого силиката относительно неподвижных точек ввода горючих веществ, окислительного газа и окислителя топлива. Эта циркуляция может быть осуществлена, например, путем естественной конвекции, возникающей в результате разницы температур и/или глубины резервуара, или перемешивание (в частности, вращением) силиката, в частности, с помощью мешалки например, металлической, в частности из прочной стали, в частности, с переменной скоростью, в частности, магнитогидродинамического типа (или "MHD"), или приведением в движение (например, во вращение) самого резервуара, или любым другим способом. В этом случае имеется два выхода для потоков газа: 1) для горючего газа, который направляют на применение, 2) для дымовых газов от сгорания остаточного углерода (не превращенного в горючий газ) и/или от погружного горения, которые соединяются с другим контуром, как, например, контуром основных дымовых газов промышленной печи-утилизаторе. Разделение этих двух газов (произведенный горючий газ с одной стороны и газообразные продукты горения с другой стороны) обеспечивается благодаря двум раздельным вытяжным каналам, причем один находится вблизи и даже непосредственно над линией введения окислительного газа (вода, или O2, илиCO2), а другой размещается вблизи и даже непосредственно над линией введения окислителя топлива. Таким образом, изобретение относится также к способу, согласно которому погружное горение, с одной стороны, и реакция между окислительным газом и органическим материалом, с другой стороны, реализуются в достаточно разделенных зонах, чтобы дымовые газы от сгорания и горючий газ могли соби-3 021616 раться в разных вытяжных каналах. Следует отметить, что окислительный газ может создаваться, по меньшей мере, частично и даже полностью, внутри ванны расплавленного силиката в результате погружного горения, которое снабжает его теплом. Действительно, погружное горение горючих веществ с окислителем топлива образует воду иCO2, которые будут подниматься в виде пузырей в ванне силиката, чтобы затем реагировать с органическими материалами, которые в большей части находятся в верхней части ванны, более или менее всплывшими. Горючие вещества могут быть частью собственно горючего газа, образованного согласно изобретению, который повторно вводится в ванну. К этому собственно горючему газу можно добавлять другое горючее вещество, но это не является строго обязательным. Горючий газ, полученный согласно изобретению, содержит водород (Н 2) и моноксид углерода (СО). Обычно он также содержит метан (СН 4). Суммарная мольная доля водорода и моноксида углерода составляет по меньшей мере 10%, обычно даже по меньшей мере 30%, даже по меньшей мере 35%. Эта процентная доля газа-восстановителя (Н 2 и СО) достигается, когда окислительный газ встречает достаточно органического материала при своем движении. Этот горючий газ обычно имеет низшую теплоту сгорания по меньшей мере 1 МДж/Нм 3, обычно даже по меньшей мере 5 МДж/Нм 3, причем она может достигать даже по меньшей мере 10 МДж/Нм 3. Обычно она ниже 30 МДж/Нм 3. Коэффициент полезного действия есть полезная энергия (энергия полученного газа, используемого вне устройства), деленная на всю входящую энергию (горючие материалы и возможная энергия, поступающая извне). Этот КПД обычно составляет от 10 до 80%. Способ согласно изобретению может осуществляться, в частности, в непрерывном режиме: полученный газ выходит горячим (500 С-1300 С) вверх устройства и может быть направлен на промышленный процесс, в котором он будет использоваться: стекловаренная печь, электрогенератор, металлургический завод и т.д. Так как произведенный горючий газ является горячим, представляет интерес, чтобы извлечь максимальную пользу от его тепла, приблизить устройство по изобретению к установке, в которой он будет применяться, чтобы ограничить тепловые потери. Преимуществом этого является также ограничение или предотвращение конденсации смол в линии, подводящей горючий газ к установке утилизации. Можно также охладить этот горючий газ, например, преобразуя его энергию, например, в водяной пар посредством бойлера, при необходимости фильтруя его (удаление пыли), очищая (удаление воды), сжимая и храня перед проведением на установку его утилизации. В этом случае применение может быть более удаленным. В процессе, действующем в непрерывном режиме, силикат содержится в резервуаре, причем силикат регулярно удаляется из резервуара, а стеклующиеся материалы регулярно вводятся для питания ванны силиката. Некоторые твердые органические материалы, в частности, типа биомассы, могут быть преобразованы в вязкую жидкость (или масло) пиролизом при примерно 500 С под давлением (как нефть образуется естественным путем из органических материалов). Таким образом, можно до газификации в устройстве согласно изобретению, превратить эти органические материалы в масло. Этот дает преимущество существенно уменьшить объем материала, вводимого в газификатор согласно изобретению. Кроме того, это вещество, сконденсированное в виде масла, становится транспортабельным в той степени, что расходы на транспортировку становятся в этом случае приемлемыми, что не справедливо для исходной биомассы,слишком объемистой, принимая во внимание энергию, которая из нее добывается. Газификация согласно изобретению может осуществляться под давлением, что позволяет затем подавать горючий газ под давлением. Это может быть желательным, в частности, для достижения достаточных импульсов горючего газа в горелки для конечного применения. Газификацию под давлением легче реализовать, исходя из масла, так как загрузку масла можно провести с помощью насоса. Горючий газ, созданный устройством согласно изобретению, может использоваться для питания в качестве топлива горелки промышленной печи, такой как стекловаренная печь. В таком случае этот газ сжигается вторичным воздухом (причем в этом случае первичный воздух - это воздух, нагнетаемый в силикат), который мог быть подвергнут термической регенерации в регенераторе согласно принципу,хорошо известному специалисту стекольной промышленности (чередование дымовые газы/воздух в регенераторах). При необходимости горючий газ, образованный согласно изобретению, может быть нагрет перед горением при его конечной утилизации (говорят о двойной регенерации, если нагревают и окислитель топлива, и горючее). Однако не обязательно выгодно, чтобы полученный газ имел высокую теплоту сгорания и был уже достаточно горячим. Таким образом, для способа согласно изобретению выгодно, когда горючий газ используется сразу после его синтеза, так как этот газ создается горячим, что выгодно в определенных приложениях, как, в частности, горение в форсунке стекловаренной печи. Необязательно, горючий газ может выходить при относительно умеренной температуре (500 С), в частности, если он охлаждается слоями органического материала или свежим введенным углем, через который он проходит в устройстве. Так как это газ с относительно низкой PCI (если сравнивать с природным газом), предпочтительно нагреть его перед его сжиганием в печи-утилизаторе (пример: стекловаренная печь), чтобы получить достаточную температуру адиабатического пламени, в частности, при выплавке стекла. Для этого можно предусмотреть систему двойной регенерации: в первом цикле горячие дымовые газы, выходящие после горения в печи-утилизаторе (в частности, стекловаренной печи) нагревают две регенерационные камеры: одну для воздуха для горения (как в современных газовых печах), а другую для горючего газа. В следующем цикле контуры газа меняют на обратные, и теперь в этих камерах нагреваются воздух и газ, затем оба сгорают при поступлении в печь-утилизатор, с получением горячих дымовых газов и передавая свое тепло загружаемому материалу. Обе камеры, для воздуха и горючего газа, должны, разумеется, быть непроницаемы друг для друга из-за угрозы преждевременного сгорания или даже взрыва. Чтобы избежать необходимости нагрева горючего газа перед его использованием в печиутилизаторе, рекомендуется повысить температуру газа на выходе из устройства получения горючего газа (называемого "газогенератором") и его PCI, чтобы обеспечить достаточную температуру адиабатического пламени. Этот результат можно получить применением газогенератора с очень высокой температурой газификации (1000 С) и/или действующего с разделением нагнетания окислителя топлива и окислительного газа (по принципу двух вытяжных каналов с фиг. 2). Действительно, в этом случае имеется полное разложение смол и конденсатов, и максимальное увеличение отношения СО/CO2 и доли Н 2 в полученном горючем газе. Газ является довольно горячим (500 С), и его PCI достаточно велика (20 кДж/кг) для того, чтобы напрямую питать печь-утилизатор, в частности, стекловаренную печь, не проходя через регенерацию. В таком случае он сгорает после своего поступления в печь с воздухом для горения, который мог быть подвергнут классической регенерации. Это решение имеет то преимущество, что не нужно снова нагревать газ в керамическом регенераторе, который всегда трудно герметизировать: таким образом снижают риск преждевременного горения или взрыва. Получить водяной пар и/или горячую смесь воздух/О 2, необходимые для газификатора, можно с помощью бойлера или теплообменника, использующего остаточную энергию дымовых газов. Водяной пар, требующийся для способа согласно изобретению в качестве окислительного газа, может быть получен посредством бойлера. Этот бойлер может быть установлен в контур главных дымовых газов печиутилизатора (как стекловаренная печь или другой промышленный процесс) горючего газа, полученного согласно изобретению, или в контур охлаждения полученного горючего газа. Тепло этого дыма или этих газов служит для испарения воды. В частности, для случая наличия двух вытяжных каналов для сбора газов (продуктов горения с одной стороны и горючего газа с другой стороны) бойлер может быть установлен в контур дымовых газов, выходящих из устройства по изобретению. Предпочтительно, водяной пар находится при температуре от 100 до 800 С и под давлением от 1 до 100 бар. Изобретение относится также к промышленному устройству, содержащему печь-утилизатор горючего газа, который в ней сгорает и в котором тепло дымовых газов от сгорания служит для испарения воды, которая служит в качестве окислительного газа для получения горючего газа по принципам газификации согласно изобретению, причем полученный горючий газ повторно вводится в печь-утилизатор,чтобы там сгореть. Эта печь-утилизатор может быть любой системой, основанной на сгорании горючего газа, такой, как стекловаренная печь (плавление стекла, флоат-печь для преобразования плоского стекла и т.д.). В частности, печь может быть типа регенератора или рекуператора, то есть часть тепла дымовых газов могла уже быть извлечена регенератором или рекуператором перед тем, как направить их в бойлер для испарения воды. Известно, что дымовые газы выходят из таких регенераторов или рекуператоров еще с высокой температурой, обычно ниже 600 С, но, как правило, выше 300 С, и поэтому устройство согласно изобретению очень выгодно, так как эта теплота, обычно выбрасываемая в атмосферу с дымовыми газами, служит здесь с большой пользой для испарения воды в рамках системы производства энергии. Таким образом, изобретение относится также к промышленному устройству, содержащему производственную установку, содержащую топливную газовую горелку, создающую газообразные продукты горения,бойлер, производящий водяной пар (разумеется, это охватывает случай, когда может иметься несколько бойлеров),установку для получения горючего газа, включающую в себя реакцию окислительного газа, содержащего водяной пар, с органическим материалом,причем газообразные продукты горения проводятся в бойлер для испарения воды и получения водяного пара, водяной пар, произведенный бойлером, проводится на установку получения горючего газа,чтобы реагировать с органическим материалом, горючий газ проводится на производственную установку, чтобы сгореть там в качестве газообразного топлива. В этом контексте установка получения горючего газа может функционировать согласно способу по изобретению, то есть с ванной силиката, но речь может идти также об установке, работающей, в соответствие с известными принципами, с неподвижным или кипящим слоем. Таким образом, изобретение относится также к способу непрерывного промышленного производства, использующему только что описанное промышленное устройство. Этот способ включает в себя: непрерывное получение на промышленной производственной установке, содержащей топливную газовую горелку, образующую газообразные продукты горения,-5 021616 непрерывное получение водяного пара в бойлере,непрерывное получение горючего газа в установке получения горючего газа, включающее реакцию окислительного газа, содержащего водяной пар, с органическим материалом,причем газообразные продукты горения проводятся в бойлер для испарения воды и получения водяного пара, водяной пар, полученный в бойлере, проводится на установку получения горючего газа для реакции с органическим материалом, а горючий газ проводится на промышленную производственную установку, чтобы сгореть там в качестве газообразного топлива. Органические материалы, которые можно вводить в силикат, могут быть твердыми или жидкими горючими материалами, такими, как биомасса и/или отходы, такие, как отслужившие покрышки, пластмасса, продукты перемалывания автомобилей, шлаки, альтернативные топливные материалы (называемые "MCS") и даже бытовые отходы. Органические материалы могут иметь биологическую природу или быть получены из продовольственной промышленности. Это может быть животная мука. Речь может идти, в частности, о биомассе типа соломы, стеблей тростника и т.д. Это может быть также уголь, лигнит, битумные сланцы, торф и т.д. Эти вещества могут также быть древесными отходами, макулатурой с бумажной промышленности. Они могут состоят также из органических полимеров, например, полиэтилена, полипропилена, полистирола, остатков покрышек, или измельченных компонентов автомобиля. Органические материалы могут быть тщательно смешаны с неорганическими материалами, которые с пользой обогащают состав. Например, это может быть песок, загрязненный разливами нефти, причем песок будет обогащать силикат кремнеземом, а углеводород-загрязнитель является источником горючего газа. Можно также газифицировать натуральные пески, содержащие углеводороды, как битумные сланцы. Это могут быть также композитные стеклопластиковые материалы. Можно назвать многослойные стекла, например, сочетающие по меньшей мере одно стекло с по меньшей мере одним листом полимера,термопластичного или нет, типа поливинилбутираля PVB, этилен-винилацетата EVA, полиуретана PU или полиэтилентерефталата PET. Можно также назвать композитные материалы на основе полимеров,усиленных стекловолокном (или углеродным волокном, или другим типом упрочняющего волокна), использующиеся в автомобильной промышленности или, например, для судов. Можно упомянуть также композитные материалы стекло/металл (остекления, снабженные электросоединительными элементами,металлическими покрытиями). Таким образом, устройство согласно изобретению может служить для использования органических отходов в качестве вторсырья. Силикат постепенно наполняется минеральной золой, образующейся из введенного горючего материала. Его можно непрерывно удалять, в частности, посредством перепускной трубы с сифоном (чтобы избежать выхода горючего газа), соединенной с основным резервуаром. Обеспечить постоянство вязкости силиката при заданной температуре можно, анализируя его химический состав и вводя вместе с горючими материалами корректирующие оксиды (СаО, Fe2O3 и т.д.). Природа и количество корректирующих оксидов зависит, разумеется, от природы введенных материалов. Устройство согласно изобретению может быть интегрировано в промышленную установку (как стекловаренная печь), которая в таком случае способна полностью или частично обойтись без ископаемого топлива. Для случая применения газа, полученного согласно изобретению, в горелках можно снабжать этими газами от газификации лишь ограниченное число горелок, а другие горелки остаются работать на газообразном топливе или природном газе. Таким образом, можно пропорционально уменьшить подлежащую обложению налогами эмиссию CO2 и можно также снизить стоимость энергии. Устройство согласно изобретению недорого, в нем используются дешевые материалы, и имеет компактный размер по сравнению с устройствами уровня техники, в которых используются неподвижный или псевдоожиженный слой. Введенные органические материалы обычно являются холодными в сравнении с температурой ванны силиката. Если газы, образованные по способу согласно изобретению, проходят вблизи или в зоне обогащения этими материалами, то, с одной стороны, органические материалы будут нагреваться этими газами, но с другой стороны, газы охлаждаются, что может иметь недостатком образование смол, и кроме того, эта пониженная температура в известных случаях менее благоприятна для конечного применения. Вот почему выгодно заставить полученный горючий газ проходить через более горячую зону поверхности силиката, находящуюся предпочтительно ниже относительно направления течения или отвода силиката. Эта более горячая зона получается, в частности, благодаря подводу тепла, которое может иметь в основе электричество. Тепло может также быть создано в результате погружного горения части полученного горючего газа с О 2 или воздухом. Эта операция является операцией типа "обратного хода",так как газы от газификации (образованный горючий газ) движутся в направлении от холода к теплу (как в газификаторах с прямоточным кипящим слоем). Здесь газы образуются в первой камере (то есть они могут быть достаточно холодными, так как введенный органический материал является холодным), но затем они вынуждены проходить в нижнюю зону между сводом и силикатом, в результате чего они нагреваются, преимуществом является разложение смол и продолжение газификации. Таким образом, согласно изобретению горючий газ может нагреться, проходя под пониженным сводом, прежде чем выйти в вытяжной канал. Фиг. 1 показывает устройство согласно изобретению в варианте осуществления, согласно которому полученный горючий газ не отделяется от газообразных продуктов горения. Резервуар 1 содержит ванну расплавленного силиката 2 при температуре 1200 С и с вязкостью ниже 1000 пуаз, в которую посредством шнекового транспортера 3 на поверхность ванны вводят биомассу MCS. Ниже уровня поверхности ванны также вводят водяной пар при 400 С (по линии 4) и воздух при 500 С (по линии 5). Через единственный вытяжной канал 6 собирают образованный горючий газ, смешанный с газообразными продуктами горения. С помощью того же шнекового транспортера непрерывно вводят смесь стеклующихся материалов, чтобы сохранить состав силиката по существу постоянным. Температура ванны силиката поддерживается электродами. Силикат непрерывно выводят, в зависимости от изменения его состава, через горло 7. Фиг. 2 показывает устройство согласно изобретению в варианте осуществления, согласно которому образованный горючий газ отделяют от газообразных продуктов горения. Резервуар 21 содержит ванну расплавленного силиката 22 с температурой 1300 С и вязкостью ниже 1000 пуаз, в которую ниже уровня ванны вводят биомассу MCS с помощью шнекового транспортера 23. Водяной пар вводится в первую зону резервуара по линии 24, а воздух по линии 25 вводится во вторую зону резервуара, достаточно удаленную от первой зоны. Ванна 22 перемешивается ротационной мешалкой 28, чтобы теплота сгорания,образованная в первой зоне, поступала во вторую зону. Первый вытяжной канал 26, находящийся выше первой зоны, собирает полученный горючий газ, а второй вытяжной канал 27, находящийся выше второй зоны, собирает газообразные продукты горения. Эти газообразные продукты горения могут направляться в бойлер или контур сбора дымовых газов печи-утилизатора, чтобы извлечь из них тепло. С помощью того же шнека непрерывно вводят смесь стеклующихся материалов, чтобы сохранить состав силиката по существу постоянным. Силикат непрерывно выводят, в зависимости от изменения его состава, через горло 29. Фиг. 3 показывает устройство по изобретению в варианте осуществления "обратный ход", согласно которому полученный горючий газ не отделяется от газообразных продуктов горения и вынужден проходить в нижнюю зону между сводом и силикатом, чтобы разогреться. Емкость 31 содержит ванну расплавленного силиката 32 с температурой 1300 С и вязкостью 50 пуаз, в которую выше поверхности ванны вводят биомассу MCS посредством шнекового транспортера 33. Через единственный вытяжной канал 36 собирают образованный горючий газ в смеси с газообразными продуктами горения. Также с помощью шнека 33 непрерывно вводят смесь стеклующихся материалов (внося кремнезем, CaO, Fe2O3), чтобы сохранить состав силиката по существу постоянным. Силикат непрерывно выводят, в зависимости от изменения его состава, через горло 37. Ванну силиката нагревают также посредством погружных горелок 38, питаемых О 2 (окислитель топлива) и охлажденным полученным горючим газом, возможно обогащенным другими горючими газами, которые сильнее нагревают зону, принимающую массу, требующую газификации, и центральную зону ванны (находящуюся под пониженным сводом). Образованный горючий газ вынужден омывать эту более горячую зону жидкой ванны, проходя под пониженной частью 39 свода. Примечательно, что именно погружное горение О 2/горючий газ является "in situ" источником окислительного газа, содержащего воду и CO2, который сам будет реагировать с органическим материалом, находящимся выше внутри или на поверхности ванны расплавленного силиката. Не исключено добавление окислительного газа извне, но это не обязательно. Наконец, горючий газ, удаленный по вытяжному каналу 36, содержит менее 30% CO2. Фиг. 4 показывает промышленное устройство, действующее по замкнутому циклу в том, что касается использования теплоты дымовых газов. Устройство содержит печь-утилизатор 41 газа, который в ней сгорает, и дает дымовые газы, выходящие по линии 42. Эти дымовые газы проходят в бойлер 43 для испарения воды, которая проводится по линии 44 в ванну силиката 45, работающую согласно принципу изобретения, причем полученный горючий газ подводится по линии 46 в печь 41, чтобы там сгореть. Печь 41 снабжается газом, выходящим из ванны силиката, а также из другого источника 47. Дымовые газы после того, как они отработали на испарение воды, выводятся по линии 48 в основной вытяжной канал печи. Пример 1. В устройство с фиг. 1 вводят 9 т/сут древесных отходов и 1000 нм 3/ч воздуха, насыщенного 83 об.% водяного пара, чтобы обеспечить газификацию. Подвод тепла посредством электричества в ванну силиката составляет 500 кВт. Введенная древесина создает около 3 вес.% золы и выводится 300 кг/с силиката,наполненного золой. Состав (моль%) газа из биомассы был следующим: Видно, в частности, что образуется больше Н 2, чем СО. Полученный газ имел низшую теплоту сгорания 9 МДж/Нм 3. Если считать, что древесина имеет энергию 12 МДж/кг, то можно оценить, что 80% этой энергии было рекуперировано газификацией согласно изобретению. Пример 2. Действуют, как в примере 1, за исключением того, что введенный воздух не содержит воды. Состав Видно, что образуется больше СО, чем Н 2. Полученный газ имеет низшую теплоту сгорания 7 МДж/Нм 3. Подвод тепла электричеством в ванну силиката составлял 300 кВт. Если считать, что древесина имеет энергию 12 МДж/кг, то можно оценить, что 80% этой энергии было рекуперировано газификацией без водяного пара. ФОРМУЛА ИЗОБРЕТЕНИЯ 1. Способ получения горючего газа, имеющего низшую теплоту сгорания по меньшей мере 1 МДж/Нм 3,в котором проводят реакцию окислительного газа, содержащего водяной пар, или кислород, или CO2, с органическим материалом в контакте с ванной расплавленного силиката, содержащегося в резервуаре, и подводят тепло в расплавленный силикат, причем указанный способ функционирует в непрерывном режиме, силикат регулярно выводят из резервуара и регулярно вводят стеклующиеся материалы для снабжения ванны силиката и для сохранения состава силиката, по существу, постоянным и ниже предела осаждения железа. 2. Способ по п.1, отличающийся тем, что силикат содержит от 40 до 80 вес.% SiO2. 3. Способ по п.2, отличающийся тем, что сумма масс СаО, Fe2O3 и щелочного оксида, содержащихся в силикате, варьируется от 5 до 60 вес.%. 4. Способ по любому одному из предыдущих пунктов, отличающийся тем, что подвод тепла осуществляют по типу погружного горения. 5. Способ по п.4, отличающийся тем, что окислитель топлива для погружного горения содержит более 80 об.% чистого кислорода. 6. Способ по п.5, отличающийся тем, что пламя погружного горения является окислительным. 7. Способ по любому одному из пп.5 или 6, отличающийся тем, что окислительный газ создают погружным горением. 8. Способ по любому одному из пп.5, 6 или 7, отличающийся тем, что погружное горение, с одной стороны, и реакцию между окислительным газом и органическим материалом, с другой стороны, реализуют в разделенных зонах, чтобы дымовые газы и горючий газ могли улавливаться через разные дымовые каналы. 9. Способ по любому одному из пп.5, 6, 7 или 8, отличающийся тем, что в качестве топлива для погружного горения частично используют горючий газ, образованный согласно самому этому способу, причем этот газ факультативно смешивают с другими горючими газами. 10. Способ по любому одному из пп.1-9, отличающийся тем, что органический материал находится в достаточном количестве, чтобы суммарная мольная доля водорода и моноксида углерода в горючем газе составляла по меньшей мере 10%. 11. Способ по любому одному из пп.1-10, отличающийся тем, что окислительный газ содержит по меньшей мере 30 об.% паров воды. 12. Способ по любому одному из пп.1-11, отличающийся тем, что силикат находится при температуре от 800 до 1700 С. 13. Способ по любому одному из пп.1-12, отличающийся тем, что тепло подводится посредством электричества. 14. Способ по любому одному из пп.1-13, отличающийся тем, что горючий газ нагревают, проводя под опущенным сводом, прежде чем вывести его через вытяжной канал. 15. Способ непрерывного промышленного производства стекла, включающий в себя стадии, на которых непрерывно производят стекло в стекловаренной печи, содержащей топливную газовую горелку, образующую газообразные продукты горения,указанные газообразные продукты горения используют в бойлере для непрерывного получения водяного пара,водяной пар, полученный в бойлере, подают в стекловаренную печь для реакции с органическим материалом и получения горючего газа, причем указанный горючий газ получают согласно способу по любому из пп.1-14.
МПК / Метки
МПК: C10J 3/57, C10B 49/14
Метки: газификация, материалов, органических, горючих
Код ссылки
<a href="https://eas.patents.su/10-21616-gazifikaciya-goryuchih-organicheskih-materialov.html" rel="bookmark" title="База патентов Евразийского Союза">Газификация горючих органических материалов</a>
Предыдущий патент: Цельное интравагинальное кольцо, содержащее прогестерон, и способ изготовления и применения такого кольца
Следующий патент: Новые гербициды
Случайный патент: Конденсатор с электрическим двойным слоем