Дуплексная нержавеющая сталь
Формула / Реферат
1. Дуплексная ферритно-аустенитная нержавеющая сталь, содержащая менее 0,04 мас.% углерода, менее 0,7 мас.% кремния, менее 2,5 мас.% марганца, 18,5-22,5 мас.% хрома, 0,8-4,5 мас.% никеля, 0,6-1,4 мас.% молибдена, менее 1 мас.% меди, 0,10-0,24 мас.% азота, остальное представляет собой железо и неизбежные примеси, встречающиеся в нержавеющих сталях, соотношение компонентов которой соответствует следующим условиям: 19,14-0,39(Cu+Mo)<(Si+Cr)<22,45-0,39(Cu+Mo) и 0,1<(C+N)<0,78-0,06(Mn+Ni).
2. Дуплексная ферритно-аустенитная нержавеющая сталь по п.1, отличающаяся тем, что после термической обработки при температуре 900-1200°С, предпочтительно 950-1150°С доля аустенитной фазы составляет 45-75 об.%, предпочтительно 55-65 об.%, при этом остальное составляет феррит.
3. Дуплексная ферритно-аустенитная нержавеющая сталь по п.1 или 2, отличающаяся тем, что эквивалент стойкости к точечной коррозии PRE составляет 27-29,5.
4. Дуплексная ферритно-аустенитная нержавеющая сталь по любому из пп.1-3, отличающаяся тем, что измеренная температура Md30 находится в диапазоне 0-90°С, предпочтительно 10-70°С.
5. Дуплексная ферритно-аустенитная нержавеющая сталь по любому из предшествующих пунктов, отличающаяся тем, что содержание хрома составляет предпочтительно 19,0-22 мас.%, наиболее предпочтительно 19,5-21 мас.%.
6. Дуплексная ферритно-аустенитная нержавеющая сталь по любому из пп.1-5, отличающаяся тем, что содержание никеля составляет предпочтительно 1,5-3,5 мас.%, более предпочтительно 2,0-3,5 мас.%, еще более предпочтительно 2,7-3,5 мас.%.
7. Дуплексная ферритно-аустенитная нержавеющая сталь по любому из пп.1-6, отличающаяся тем, что содержание марганца предпочтительно составляет менее 2,0 мас.%.
8. Дуплексная ферритно-аустенитная нержавеющая сталь по любому из пп.1-7, отличающаяся тем, что содержание меди предпочтительно составляет вплоть до 0,7 мас.%, более предпочтительно вплоть до 0,5 мас.%.
9. Дуплексная ферритно-аустенитная нержавеющая сталь по любому из пп.1-8, отличающаяся тем, что содержание молибдена предпочтительно составляет 1,0-1,4 мас.%.
10. Дуплексная ферритно-аустенитная нержавеющая сталь по любому из пп.1-9, отличающаяся тем, что содержание азота предпочтительно составляет 0,16-0,21 мас.%.
11. Дуплексная ферритно-аустенитная нержавеющая сталь по любому из пп.1-10, отличающаяся тем, что возможно содержит один или более дополнительных элементов: менее 0,04 мас.% Al, предпочтительно менее 0,03 мас.% Al, менее 0,003 мас.% В, менее 0,003 мас.% Са, менее 0,1 мас.% Се, вплоть до 1 мас.% Со, вплоть до 0,5 мас.% W, вплоть до 0,1 мас.% Nb, вплоть до 0,1 мас.% Ti, вплоть до 0,2 мас.% V.
12. Дуплексная ферритно-аустенитная нержавеющая сталь по любому из пп.1-11, отличающаяся тем, что содержит в качестве неизбежных примесей менее 0,010 мас.%, предпочтительно менее 0,005 мас.% S, менее 0,040 мас.% Р, при этом сумма (S+P) составляет менее 0,04 мас.% и общее содержание кислорода составляет менее 100 ppm.
13. Дуплексная ферритно-аустенитная нержавеющая сталь по п.1, отличающаяся тем, что критическая температура точечной коррозии (СРТ) составляет 20-33°С, предпочтительно 23-31°С.
14. Дуплексная ферритно-аустенитная нержавеющая сталь по п.1, отличающаяся тем, что диапазон химических составов, лежащих внутри области, ограниченной а', b', с', d' и е' на фиг. 1, определен следующими координатами, мас.%:
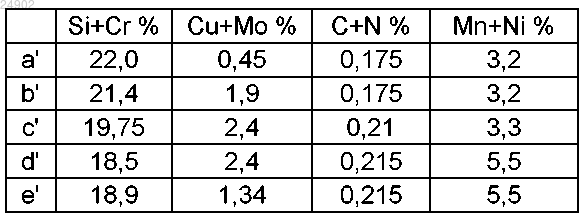
15. Дуплексная ферритно-аустенитная нержавеющая сталь по п.1, отличающаяся тем, что диапазон химических составов, лежащих внутри области, ограниченной р', q', r', s' t' и u' на фиг. 3, определен следующими координатами, мас.%:
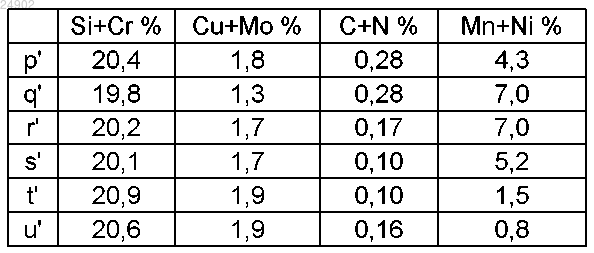
16. Дуплексная ферритно-аустенитная нержавеющая сталь по п.1, отличающаяся тем, что ее изготавливают в виде слитков, слябов, блюмов, биллетов, толстого листового проката, тонкого листового проката, полос, рулонов, прутка, катанки, проволоки, прокатного профиля, фасонного проката, бесшовных и сварных трубок и/или труб, металлического порошка и фасонных изделий.
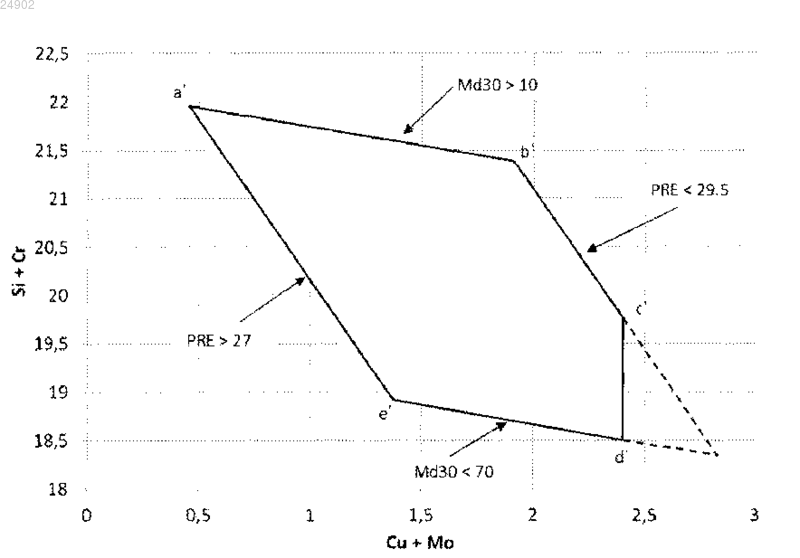
Текст
Изобретение относится к дуплексной ферритно-аустенитной нержавеющей стали, обладающей высокой деформируемостью, связанной с TRIP-эффектом, и высокой стойкостью к коррозии со сбалансированным эквивалентом стойкости к точечной коррозии. Дуплексная нержавеющая сталь содержит менее 0,04 мас.% углерода, менее 0,7 мас.% кремния, менее 2,5 мас.% марганца, 18,5-22,5 мас.% хрома, 0,8-4,5 мас.% никеля, 0,6-1,4 мас.% молибдена, менее 1 мас.% меди, 0,10-0,24 мас.% азота, остальное представляет собой железо и неизбежные примеси, встречающиеся в нержавеющих сталях. Изобретение относится к дуплексной ферритно-аустенитной нержавеющей стали, которая обладает высокой деформируемостью, связанной с TRIP-эффектом (TRIP - пластичность, обусловленная мартенситным превращением), и высокой стойкостью к коррозии с оптимизированным эквивалентом стойкости к точечной коррозии (PRE). Эффект пластичности, обусловленной мартенситным превращением (TRIP), относится к превращению метастабильного остаточного аустенита в мартенсит во время пластической деформации в результате приложенного усилия или напряжения. Это свойство придает нержавеющим сталям, обладающимTRIP-эффектом, высокую деформируемость при сохранении отличной прочности. В FI 20100178 описан способ изготовления ферритно-аустенитной нержавеющей стали, имеющей хорошую деформируемость/пластичность и высокое относительное удлинение при растяжении; такая сталь содержит менее 0,05 мас.% С; 0,2-0,7 мас.%; Si; 2-5 мас.% Mn; 19-20,5 мас.% Cr; 0,8-1,35 мас.% Ni; менее 0,6 мас.% Мо; менее 1 мас.% Cu; 0,16-0,24 мас.% N; остальное представляет собой железо и неизбежные примеси. Нержавеющую сталь по FI 20100178 подвергают термической обработке таким образом, что микроструктура нержавеющей стали содержит 45-75% аустенита в состоянии после термической обработки, при этом остальная часть микроструктуры представляет собой феррит. Далее, измеренную температуру Md30 нержавеющей стали устанавливают в диапазоне от 0 до 50 С, чтобы использовать пластичность, обусловленную мартенситным превращением (TRIP), для улучшения деформируемости нержавеющей стали. Температура Md30, которая является мерой стабильности аустенита, представляет собой температуру, при которой 0,3 истинной деформации вызывает 50%-ный переход аустенита в мартенсит. Целью настоящего изобретении является улучшение свойств дуплексной нержавеющей стали, описанной в FI 20100178, и получение новой дуплексной ферритно-аустенитной нержавеющей стали с использованием TRIP-эффекта, имеющей новый химический состав, в котором изменено, по меньшей мере, содержание никеля, а также молибдена и марганца. Существенные признаки изобретения раскрыты в прилагаемой формуле изобретения. Согласно изобретению дуплексная ферритно-аустенитная нержавеющая сталь содержит менее 0,04 мас.% С, менее 0,7 мас.% Si, менее 2,5 мас.% Mn, 18,5-22,5 мас.% Cr, 0,8-4,5 мас.% Ni, 0,6-1,4 мас.% Мо,менее 1 мас.% Cu, 0,10-0,24 мас.% N, остальное представляет собой железо и неизбежные примеси,встречающиеся в нержавеющих сталях. Содержание серы составляет менее 0,010 мас.%, а предпочтительно менее 0,005 мас.%; содержание фосфора составляет менее 0,040 мас.%, при этом суммарное количество серы и фосфора (S+P) составляет менее 0,04 мас.%, а общее содержание кислорода составляет менее 100 частей на млн (ppm). Дуплексная нержавеющая сталь по изобретению может содержать один или более дополнительных элементов, среди которых представлен алюминий, при максимальном содержании менее 0,04 мас.%,предпочтительно максимум составляет менее 0,03 мас.%. Кроме того, в небольшом количестве могут быть добавлены бор, кальций и церий; предпочтительное содержание бора и кальция составляет менее 0,003 мас.%, а церия - менее 0,1 мас.%. Кроме того, может быть добавлен кобальт в количестве вплоть до 1 мас.% в качестве частичной замены никеля и вольфрам в количестве вплоть до 0,5 мас.% в качестве частичной замены молибдена. Также в дуплексную нержавеющую сталь по изобретению может быть добавлен один или более элементов из группы, содержащей ниобий, титан и ванадий, при этом содержание ниобия и титана составляет вплоть до 0,1 мас.% , а содержание ванадия составляет вплоть до 0,2 мас.%. Для нержавеющей стали по изобретению эквивалент стойкости к точечной коррозии (PRE) был оптимизирован, чтобы обеспечить хорошую коррозийную стойкость, в пределах 27-29,5. Критическая температура точечной коррозии (СРТ) составляет 20-33 С, предпочтительно 23-31 С. Эффект TRIP (пластичность, обусловленная мартенситным превращением) в аустенитной фазе поддерживают в соответствии с измеренной температурой Md30 в диапазоне 0-90 С, предпочтительно в диапазоне 10-70 С в целях гарантированного получения хорошей деформируемости. Доля аустенитной фазы в микроструктуре дуплексной нержавеющей стали по изобретению в состоянии после термической обработки составляет 45-75 об.%, предпочтительно 55-65 об.%, причем остальное составляет феррит, чтобы создать благоприятные условия для TRIP-эффекта. Термическую обработку можно проводить с использованием различных способов термической обработки, таких как аустенизирующий отжиг, отжиг с высокочастотным индукционным нагревом или локальный отжиг, при температуре от 900 до 1200 С, предпочтительно от 950 до 1150 С. Ниже описано влияние различных элементов на микроструктуру, при этом содержание элементов приведено в мас.%. Углерод (С) вносит вклад в выделение аустенитной фазы и оказывает сильное влияние на стабильность аустенита. Углерод можно добавлять в количестве вплоть до 0,04%; но его большее количество оказывает отрицательное влияние на коррозионную стойкость. Азот (N) является важным стабилизатором аустенита в дуплексных нержавеющих сталях, и, подобно углероду, он повышает стойкость относительно мартенсита. Азот также улучшает прочность, деформационное упрочнение и коррозионную стойкость. Общие эмпирические выражения относительно тем-1 024902 пературы Md30 указывают на то, что азот и углерод оказывают одинаково сильное влияние на стабильность аустенита. Поскольку азот можно добавлять в нержавеющие стали в большем количестве, чем углерод, без отрицательного влияния на коррозийную стойкость, содержание азота от 0,10 до 0,24% является эффективным для нержавеющих сталей по изобретению. Для оптимального сочетания свойств предпочтительным является содержание азота от 0,16 до 0,21%. Кремний (Si) обычно добавляют в нержавеющие стали в целях раскисления при плавке, и его содержание не должно быть ниже 0,2%. Кремний стабилизирует ферритную фазу в дуплексных нержавеющих сталях, но оказывает более сильное стабилизирующее влияние на стойкость аустенита относительно образования мартенсита, чем показано в существующих выражениях. По этой причине максимальное содержание кремния составляет 0,7%, предпочтительно 0,5%. Марганец (Mn) является важной добавкой для стабилизации аустенитной фазы и повышения растворимости азота в нержавеющей стали. Марганец может частично заменить дорогостоящий никель и способствовать правильному соотношению фаз в стали. Слишком высокое его содержание снижает коррозионную стойкость. Марганец оказывает более сильное стабилизирующее влияние на стойкость аустенита относительно образования мартенсита, поэтому содержание марганца должно быть тщательно выверено. Содержания марганца должно быть менее 2,5%, предпочтительно менее 2,0% Хром (Cr) является главной добавкой для придания стали стойкости к коррозии. Будучи стабилизатором феррита, хром также является основной добавкой для обеспечения правильного соотношения между аустенитной фазой и ферритной фазой. Чтобы обеспечить эти функции, содержание хрома должно составлять по меньшей мере 18,5%, а чтобы ограничить ферритную фазу до количества, соответствующего текущей цели, максимальное содержание хрома должно составлять 22,5%. Предпочтительное содержание хрома составляет 19,0-22%, наиболее предпочтительно 19,5-21%. Никель (Ni) является существенным легирующим элементом для стабилизации аустенитной фазы и обеспечения хорошей пластичности; его необходимо добавлять в сталь по меньшей мере в количестве 0,8%, предпочтительно по меньшей мере 1,5%. Обладая большим влиянием на стойкость аустенита относительно образования мартенсита, никель должен присутствовать в сплаве в узком диапазоне. Кроме того, поскольку никель является дорогостоящим материалом, и учитывая колебание цен, содержание никеля в нержавеющих сталях по изобретению максимально должно составлять 4,5%, предпочтительно 3,5%, а более предпочтительно 2,0-3,5%. Еще более предпочтительно содержание никеля составляет 2,73,5%. Медь (Cu), как правило, присутствует в большинстве нержавеющих сталей в качестве примеси, составляющей 0,1-0,5%, когда значительное количество сырьевых материалов поступает в виде лома, содержащего этот элемент. Медь является слабым стабилизатором аустенитной фазы, но она сильно влияет на сопротивление образованию мартенсита, и ее необходимо учитывать при оценке деформируемости нержавеющих сталей по изобретению. Ее можно намерено вводить водить в количестве вплоть до 1,0%,но предпочтительное содержание меди составляет вплоть до 0,7%, более предпочтительно вплоть до 0,5%. Молибден (Мо) является стабилизатором феррита; его можно добавлять для повышения коррозийной стойкости, и поэтому содержание молибдена должно составлять более 0,6%. Кроме того, молибден повышает сопротивление образованию мартенсита и с учетом других добавок содержание молибдена должно составлять не более 1,4%. Предпочтительное содержание молибдена составляет 1,0-1,4%. Бор (В), кальций (Са) и церий (Се) добавляют в дуплексные стали в небольшом количестве для улучшения обрабатываемости в горячем состоянии, и их содержание не должно быть слишком высоким,поскольку это может ухудшить другие свойства. Предпочтительное содержание бора и кальция составляет менее 0,003 мас.%, церия - менее 0,1 мас.%. Сера (S) в дуплексных сталях ухудшает обрабатываемость в горячем состоянии и может образовывать сульфидные включения, которые отрицательно влияют на стойкость к точечной коррозии. Поэтому содержание серы следует ограничивать до менее 0,010 мас.%, а предпочтительно до менее 0,005 мас.%. Фосфор (Р) ухудшает обрабатываемость в горячем состоянии и может образовывать фосфидные частицы или пленки, которые отрицательно влияют на коррозионную стойкость. Поэтому содержание фосфора следует ограничивать до менее 0,040 мас.%, и чтобы при этом суммарное содержание серы и фосфора (S+P) составляло менее 0,04 мас.%. Кислород (О) вместе с другими примесными элементами неблагоприятно воздействует на пластичность в горячем состоянии. По этой причине важно поддерживать его содержание на низком уровне, в особенности в высоколегированных дуплексных сортах, которые подвержены растрескиванию. Наличие оксидных включений может снижать коррозионную стойкость (к точечной коррозии) в зависимости от типа включения. Высокое содержание кислорода также снижает ударную вязкость. Подобно сере кислород улучшает проплавление шва при сварке, изменяя поверхностную энергию сварочной зоны. Для настоящего изобретения рекомендуемое максимальное количество кислорода составляет менее 100 ppm. Для металлического порошка максимальное содержание кислорода может составлять вплоть до 250 ppm. В дуплексной нержавеющей стали с высоким содержанием азота по изобретению содержание алюминия (Al) должно быть низким, поскольку эти два элемента могут взаимодействовать с образованием нитридов алюминия, которые ухудшают ударную вязкость. Содержание алюминия ограничивают до менее 0,04 мас.%, а предпочтительно менее 0,03 мас.%. Вольфрам (W) имеет свойства, подобные свойствам молибдена, и может иногда замещать молибден, однако вольфрам может способствовать выделению сигма-фазы, так что содержание вольфрама должно составлять вплоть до 0,5 мас.%. Кобальт (Со) имеет металлургические свойства, схожие со свойствами родственного ему элемента никеля, и в производстве стали и сплавов кобальт во многом можно использовать подобным образом. Кобальт замедляет рост зерен при повышенных температурах и существенно улучшает способность сохранения твердости и жаропрочности. Кобальт улучшает стойкость к кавитационной эрозии и деформационное упрочнение. Кобальт снижает риск образования сигма-фазы в супердуплексных нержавеющих сталях. Содержание кобальта составляет вплоть до 1,0 мас.%."Микролегирующие" элементы титан (Ti), ванадий (V) и ниобий (Nb) относятся к группе добавок,названных так из-за того, что они существенно изменяют свойства сталей при низких концентрациях,часто оказывая благоприятный эффект в случае углеродистой стали, но в случае дуплексных нержавеющих сталей они часто вносят вклад в нежелательные изменения свойств, такие как снижение ударной вязкости, большее количество поверхностных дефектов, снижение пластичности стали при литье и горячей прокатке. В случае современных дуплексных нержавеющих сталей, многие из этих эффектов обусловлены сильным химическим сродством к углероду этих элементов и в особенности к азоту. В настоящем изобретении содержание ниобия и титана максимально должно составлять 0,1%, тогда как влияние ванадия менее негативно, и его содержание должно составлять менее 0,2%. Далее настоящее изобретение описано более подробно со ссылками на чертежи, где на фиг. 1 показана зависимость минимальной и максимальной температуры Md30 и значений PRE от содержания элементов Si+Cr и Cu+Мо в испытательных сплавах по изобретению; на фиг. 2 показан пример с постоянными значениями содержания C+N и Mn+Ni для зависимости минимальной и максимальной температуры Md30 и значений PRE от содержания элементов Si+Cr иCu+Мо в испытательных сплавах по изобретению согласно фиг. 1; на фиг. 3 показана зависимость минимальной и максимальной температуры Md30 и значений PRE от содержания элементов C+N и Mn+Ni в испытательных сплавах по изобретению, и на фиг. 4 показан пример с постоянными величинами Si+Cr и Cu+Мо для зависимости минимальной и максимальной температуры Md30 и значений PRE от содержания элементов C+N и Mn+Ni в испытательных сплавах по изобретению согласно фиг. 3. Исходя из влияния элементов представлена дуплексная ферритно-аустенитная нержавеющая сталь по изобретению с различным химическим составом A-G, как указано в табл. 1. Табл. 1 также содержит данные о химическом составе сравнительной дуплексной нержавеющей стали, известной из FI 20100178; она обозначена Н. Все значения представлены в табл. 1 в мас.%. Таблица 1 Сплавы A-F были изготовлены в вакуумной индукционной печи в лабораторном масштабе в количестве 60 кг в виде небольших слябов, которые были обработаны горячей прокаткой и холодной прокаткой с получением толщины 1,5 мм. Сплав G был произведен в промышленном масштабе в количестве 100 т, прошел последующую обработку горячей прокаткой и холодной прокаткой с получением рулонов с различными конечными размерами. Как видно из табл. 1, содержание углерода, азота, марганца, никеля и молибдена в дуплексных нержавеющих сталях по изобретению существенно отличается от соответствующих значений для сравнительной нержавеющей стали Н. Для сплавов различного химического состава, указанных в табл. 1, определяли значения температуры Md30, критической температуры точечной коррозии (СРТ) и PRE; результаты представлены в нижеследующей табл. 2. Для расчета прогнозируемой температуры Md30 (Md30 Нохара) аустенитной фазы, представленной в табл. 2, использовали выражение (1) Нохара, установленное для аустенитных нержавеющих сталей при температуре отжига 1050 С. Действительные температуры Md30 (Md30 изм.), указанные в табл. 2, были установлены посредством деформации образцов для испытания на растяжение на величину 0,3 истинной деформации при различ-3 024902 ных температурах и посредством измерения доли превращенного мартенсита с помощью оборудованияSatmagan. Satmagan представляет собой магнитные весы, на которых долю ферромагнитной фазы определяют путем помещения образца в насыщающее магнитное поле и сравнения магнитной и гравитационной сил, вызываемых образцом. Расчетные температуры Md30 (Md30 расч.), указанные в табл. 2, получены в соответствии с математическим ограничением оптимизации, которое также использовали для выведения выражений (3) и (4). Критическая температура точечной коррозии (СРТ) измерена в 1 М растворе хлористого натрия(NaCl) согласно стандартному методу ASTM G150; ниже этой критической температуры точечной коррозии (СРТ) невозможна точечная коррозия и наблюдается только пассивное состояние сплава. Эквивалент стойкости к точечной коррозии (PRE) рассчитывали с использованием формулы (2) Для сплавов из табл. 1 также рассчитывали суммарное содержание элементов C+N, Cr+Si, Cu+Mo иMn+Ni в мас.%, которое приведено в табл. 2. Суммы C+N и Mn+Ni представляют собой стабилизаторы аустенита; сумма элементов Si+Cr представляет собой стабилизатор феррита, а сумма элементов Cu+Мо обладает сопротивлением к образованию мартенсита. Таблица 2 Как видно из табл. 2, значения PRE в диапазоне 27-29,5 намного выше, чем значение PRE для сравнительной дуплексной нержавеющей стали Н, что свидетельствует о более высокой коррозийной стойкости сплавов A-G. Значения критической температуры точечной коррозии СРТ находятся в диапазоне 21-32 С, что намного выше, чем СРТ для аустенитных нержавеющих сталей, таких как EN 1.4401 и подобные сорта. Приведенные в табл. 2 прогнозируемые температуры, рассчитанные по выражению (1) Нохара, существенно отличаются от измеренных температур Md30 для сплавов. Кроме того, из табл. 2 видно, что расчетные температуры Md30 хорошо согласуются с измеренными температурами Md30, и таким образом,математическое ограничение оптимизации, использованное для вычисления, очень подходит для дуплексных нержавеющих сталей по изобретению. Суммарное содержание элементов C+N, Si+Cr, Mn+Ni и Cu+Mo в мас.% для дуплексных нержавеющих сталей по изобретению использовали при математическом ограничении оптимизации для установления зависимости, с одной стороны, между C+N и Mn+Ni и, с другой стороны, между Si+Cr иCu+Mo. Согласно этому математическому ограничению оптимизации суммы Cu+Mo и Si+Cr, а также суммы Mn+Ni и C+N соответственно образуют координатные оси х и у графиков, показанных на фиг. 14, где определены линейные зависимости для минимума и максимума значений PRE (27PRE29,5) и для минимума и максимума значений температуры Md30 (10Md3070). Как показано на фиг. 1, установлен диапазон химических составов для Si+Cr и Cu+Мо с предпочтительными диапазонами 0,175-0,215 для C+N и 3,2-5,5 для Mn+Ni, когда дуплексную нержавеющую сталь по изобретению подвергали отжигу при температуре 1050 С. На фиг. 1 также показано ограничениеCu+Мо 2,4, обусловленное наличием максимальных диапазонов содержания меди и молибдена. Диапазон химических составов, лежащих внутри области, ограниченной а', b', с', d' и е' на фиг. 1,определяется координатами, указанными ниже в табл.3. Таблица 3 На фиг. 2 показан один пример диапазона химических составов согласно фиг. 1, где во всех точках используют постоянные значения 0,195 для C+N и 4,1 для Mn+Ni вместо диапазонов для C+N и Mn+Ni согласно фиг. 1. Диапазон химических составов, лежащих внутри области, ограниченной а, b, с и d, на фиг. 2, определяют координатами, указанными ниже в табл. 4. На фиг. 3 показан диапазон химических составов для C+N и Mn+Ni с предпочтительными диапазонами составов 19,7-21,45 для Cr+Si и 1,3-1,9 для Cu+Мо, когда дуплексную нержавеющую сталь подвергали отжигу при температуре 1050 С. Дополнительно, в соответствии с изобретением для суммы C+N введено ограничение 0,1C+N0,28 и для суммы Mn+Ni введено ограничение 0,8Mn+Ni7,0. Диапазон химических составов, лежащих внутри области, ограниченной р', q', r', s', t' и u' на фиг. 3, определяется координатами, указанными ниже в табл. 5. Таблица 5 Влияние ограничения C+N и Mn+Ni предпочтительными диапазонами содержания элементов по изобретению выражается в том, что диапазон химических составов на фиг. 3 частично ограничен максимальным и минимальным значениями PRE и частично ограничен диапазонами содержания C+N иMn+Ni. На фиг. 4 показан один пример диапазона химических составов согласно фиг. 3 с постоянными значениями 20,5 для Cr+Si и 1,6 для Cu+Mn и с дополнительным ограничением 0,1C+N. Диапазон химических составов, лежащий внутри области, ограниченной р, q, r, s, t и и на фиг. 4, определяется координатами, указанными ниже в табл. 6. Таблица 6 При использовании значений, приведенных в табл.2, и значений согласно фиг. 1-4 установлены следующие выражения для значений минимальной и максимальной температуры Md30: если дуплексную нержавеющую сталь по изобретению подвергнуть отжигу при температуре 9501150 С. Для сплавов по настоящему изобретению, так же как и для вышеуказанного сравнительного материала Н, дополнительно определяли пределы текучести Rp0,2 и Rp1,0 и предел прочности Rm при растяжении, а также величины относительного удлинения А 50, А 5 и Ag как в продольном направлении (продол.)(сплавы А-С, G-H), так и в поперечном направлении (попереч.) (все сплавы А-Н). В табл. 7 представлены результаты испытаний для сплавов А-G по изобретению, так же как и соответствующие величины для сравнительной дуплексной нержавеющей стали Н. Таблица 7 Результаты, представленные в табл. 7, показывают, что значения Rp0,2 и Rp1,0 пределов текучести для сплавов A-G намного выше, чем соответствующие значения для сравнительной дуплексной нержавею-5 024902 щей стали Н, а значения предела прочности при растяжении Rm схожи с этим значением для сравнительной дуплексной нержавеющей стали Н. Величины удлинения А 50, A5 и Ag для сплавов A-G ниже, чем соответствующие величины для сравнительной нержавеющей стали. Дуплексную ферритно-аустенитную нержавеющую сталь по настоящему изобретению можно изготавливать в виде слитков, слябов, блюмов, биллетов и листового проката, такого как толстый листовой прокат, тонкий листовой прокат, полосы, рулоны; в виде длинномерного проката, такого как пруток, катанка, проволока, прокатный профиль, фасонный прокат, бесшовные и сварные трубки и/или трубы. Также можно производить дополнительную продукцию, такую как металлический порошок, фасонные изделия. ФОРМУЛА ИЗОБРЕТЕНИЯ 1. Дуплексная ферритно-аустенитная нержавеющая сталь, содержащая менее 0,04 мас.% углерода,менее 0,7 мас.% кремния, менее 2,5 мас.% марганца, 18,5-22,5 мас.% хрома, 0,8-4,5 мас.% никеля, 0,6-1,4 мас.% молибдена, менее 1 мас.% меди, 0,10-0,24 мас.% азота, остальное представляет собой железо и неизбежные примеси, встречающиеся в нержавеющих сталях, соотношение компонентов которой соответствует следующим условиям: 19,14-0,39(Cu+Mo)(Si+Cr)22,45-0,39(Cu+Mo) и 0,1(C+N)0,780,06(Mn+Ni). 2. Дуплексная ферритно-аустенитная нержавеющая сталь по п.1, отличающаяся тем, что после термической обработки при температуре 900-1200 С, предпочтительно 950-1150 С доля аустенитной фазы составляет 45-75 об.%, предпочтительно 55-65 об.%, при этом остальное составляет феррит. 3. Дуплексная ферритно-аустенитная нержавеющая сталь по п.1 или 2, отличающаяся тем, что эквивалент стойкости к точечной коррозии PRE составляет 27-29,5. 4. Дуплексная ферритно-аустенитная нержавеющая сталь по любому из пп.1-3, отличающаяся тем,что измеренная температура Md30 находится в диапазоне 0-90 С, предпочтительно 10-70 С. 5. Дуплексная ферритно-аустенитная нержавеющая сталь по любому из предшествующих пунктов,отличающаяся тем, что содержание хрома составляет предпочтительно 19,0-22 мас.%, наиболее предпочтительно 19,5-21 мас.%. 6. Дуплексная ферритно-аустенитная нержавеющая сталь по любому из пп.1-5, отличающаяся тем,что содержание никеля составляет предпочтительно 1,5-3,5 мас.%, более предпочтительно 2,0-3,5 мас.%,еще более предпочтительно 2,7-3,5 мас.%. 7. Дуплексная ферритно-аустенитная нержавеющая сталь по любому из пп.1-6, отличающаяся тем,что содержание марганца предпочтительно составляет менее 2,0 мас.%. 8. Дуплексная ферритно-аустенитная нержавеющая сталь по любому из пп.1-7, отличающаяся тем,что содержание меди предпочтительно составляет вплоть до 0,7 мас.%, более предпочтительно вплоть до 0,5 мас.%. 9. Дуплексная ферритно-аустенитная нержавеющая сталь по любому из пп.1-8, отличающаяся тем,что содержание молибдена предпочтительно составляет 1,0-1,4 мас.%. 10. Дуплексная ферритно-аустенитная нержавеющая сталь по любому из пп.1-9, отличающаяся тем,что содержание азота предпочтительно составляет 0,16-0,21 мас.%. 11. Дуплексная ферритно-аустенитная нержавеющая сталь по любому из пп.1-10, отличающаяся тем, что возможно содержит один или более дополнительных элементов: менее 0,04 мас.% Al, предпочтительно менее 0,03 мас.% Al, менее 0,003 мас.% В, менее 0,003 мас.% Са, менее 0,1 мас.% Се, вплоть до 1 мас.% Со, вплоть до 0,5 мас.% W, вплоть до 0,1 мас.% Nb, вплоть до 0,1 мас.% Ti, вплоть до 0,2 мас.%V. 12. Дуплексная ферритно-аустенитная нержавеющая сталь по любому из пп.1-11, отличающаяся тем, что содержит в качестве неизбежных примесей менее 0,010 мас.%, предпочтительно менее 0,005 мас.% S, менее 0,040 мас.% Р, при этом сумма (S+P) составляет менее 0,04 мас.% и общее содержание кислорода составляет менее 100 ppm. 13. Дуплексная ферритно-аустенитная нержавеющая сталь по п.1, отличающаяся тем, что критическая температура точечной коррозии (СРТ) составляет 20-33 С, предпочтительно 23-31 С. 14. Дуплексная ферритно-аустенитная нержавеющая сталь по п.1, отличающаяся тем, что диапазон химических составов, лежащих внутри области, ограниченной а', b', с', d' и е' на фиг. 1, определен следующими координатами, мас.%: 15. Дуплексная ферритно-аустенитная нержавеющая сталь по п.1, отличающаяся тем, что диапазон химических составов, лежащих внутри области, ограниченной р', q', r', s' t' и u' на фиг. 3, определен следующими координатами, мас.%: 16. Дуплексная ферритно-аустенитная нержавеющая сталь по п.1, отличающаяся тем, что ее изготавливают в виде слитков, слябов, блюмов, биллетов, толстого листового проката, тонкого листового проката, полос, рулонов, прутка, катанки, проволоки, прокатного профиля, фасонного проката, бесшовных и сварных трубок и/или труб, металлического порошка и фасонных изделий.
МПК / Метки
МПК: C22C 38/58, C22C 38/44, C22C 38/02, C22C 38/42
Метки: дуплексная, нержавеющая, сталь
Код ссылки
<a href="https://eas.patents.su/9-24902-dupleksnaya-nerzhaveyushhaya-stal.html" rel="bookmark" title="База патентов Евразийского Союза">Дуплексная нержавеющая сталь</a>
Предыдущий патент: Состав и способ получения керамического расклинивающего агента
Следующий патент: Способ производства циклических ундекапептидов
Случайный патент: Магнезиальные цементы