Способ извлечения тетрагалогенидов переходных металлов и углеводородов из потока отходов
Номер патента: 24476
Опубликовано: 30.09.2016
Авторы: Рясянен Юкка, Люлюкангас Микко, Малинен Пекка, Нюфорс Клаус
Формула / Реферат
1. Способ извлечения тетрагалогенида переходного металла из потока отходов процесса получения катализатора, включающий следующие стадии:
(a) формирование смешанного потока, содержащего тетрагалогенид переходного металла и галогеналкоксиды переходного металла;
(b) формирование стекающей жидкостной пленки из смешанного потока стадии (а) при температуре от 50 до 85°С и абсолютном давлении от 10 до 60 кПа (от 0,1 до 0,6 бар);
(c) формирование испарением из пленки стадии (b) первого потока, содержащего от 90 до 100% регенерируемых компонентов, включающих галогенид переходного металла, и второго потока, представляющего собой остаток после указанного выпаривания, содержащего примерно от 20 до 80% галогеналкоксидов переходных металлов.
2. Способ по п.1, в котором указанный первый поток содержит менее 1 мас.% галогеналкоксидов переходных металлов.
3. Способ по п.1 или 2, в котором отношение остаток/дистиллят (О/Д) составляет от 0,05 до 0,35.
4. Способ по любому из предыдущих пунктов, в котором указанный переходный металл является переходным металлом группы 4 или группы 5.
5. Способ по п.4, в котором указанный переходный металл является титаном.
6. Способ по любому из предыдущих пунктов, в котором указанный тетрагалогенид переходного металла представляет собой тетрахлорид переходного металла, а указанный галогеналкоксид представляет собой хлоралкоксид переходного металла.
7. Способ по любому из пп.1-6, в котором стадия (а) включает следующие стадии:
(а-1) проведение стадии промывки твердого компонента катализатора полимеризации олефинов, полученного из процесса получения катализатора, посредством приведения его в контакт с промывной жидкостью, для получения смеси, включающей твердый компонент катализатора и промывную жидкость;
(а-2) разделение смеси стадии (а-1) на фракцию продукта, содержащую основную часть твердого компонента катализатора, и жидкую фракцию, содержащую промывную жидкость;
(а-3) извлечение жидкой фракции; и
(а-4) получение смешанного потока, включающего тетрагалогенид переходного металла и галогеналкоксиды переходного металла из указанной жидкой фракции.
8. Способ по п.7, в котором промывную жидкость выбирают из группы, состоящей из тетрагалогенида титана, алифатических углеводородов, ароматических углеводородов и их смесей.
9. Способ по п.8, в котором промывную жидкость выбирают из группы, состоящей из алифатических углеводородов, ароматических углеводородов и их смесей.
10. Способ по п.9, дополнительно включающий следующие стадии:
(d) подачу первого потока на стадию перегонки;
(e) отбор с указанной стадии перегонки первого потока легкой фракции, включающего по меньшей мере 80% промывной жидкости; и
(f) отбор с указанной стадии перегонки первого потока кубового продукта, включающего по меньшей мере 80 мас.% тетрагалогенида переходного металла.
11. Способ по п.10, в котором первый поток легкой фракции содержит по меньшей мере 90% промывной жидкости.
12. Способ по п.10 или 11, в котором первый поток кубового продукта содержит по меньшей мере 95 мас.% тетрагалогенида переходного металла.
13. Способ по любому из пп.9-12, в котором указанную промывную жидкость выбирают из группы, состоящей из бензола, толуола, 1,2-диметилбензола, 1,3-диметилбензола, 1,4-диметилбензола, этилбензола, 1,2-диэтилбензола, 1,3-диэтилбензола и 1,4-диэтилбензола.
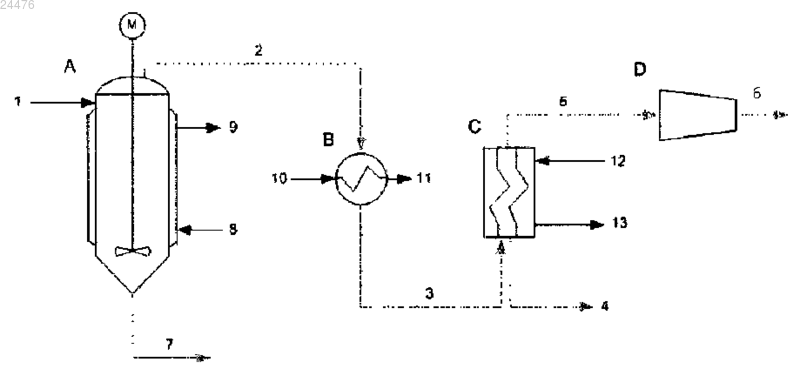
Текст
СПОСОБ ИЗВЛЕЧЕНИЯ ТЕТРАГАЛОГЕНИДОВ ПЕРЕХОДНЫХ МЕТАЛЛОВ И УГЛЕВОДОРОДОВ ИЗ ПОТОКА ОТХОДОВ Изобретение представляет способ извлечения тетрагалогенидов переходных металлов из потока отходов, поступающего с процесса получения катализатора, посредством (а) формирования смешанного потока, содержащего тетрагалогенид переходных металлов и алкоксигалогениды переходных металлов; (b) формирования стекающей жидкостной пленки из смешанного потока стадии (а) при температуре от 25 до 85 С и абсолютном давлении от 5 до 60 кПа (от 0,05 до 0,6 бар); и (с) формирования из пленки стадии (b) первого потока пара, содержащего от 90 до 100% регенерируемых компонентов, и второго потока жидкости, содержащего примерно от 10 до 80% галогеналкоксидов титана. Цель изобретения Данное изобретение относится к извлечению регенерируемых компонентов из потока отходов процесса получения катализаторов. Более конкретно, данное изобретение направлено на извлечение углеводородных материалов и тетрагалогенидов переходных металлов из потока отходов, отобранного из процесса производства катализаторов полимеризации олефинов. Данный способ направлен на извлечение и очистку углеводородных материалов и тетрагалогенидов переходных металлов до такой степени чистоты, чтобы их можно было повторно использовать в процессе производства катализаторов полимеризации олефинов. Область техники Известно применение тонкопленочного испарителя для извлечения легких компонентов из вязкой жидкости. Документ WO-A-2006056562 описывает, что такие испарители можно применять при обработке сточных вод процесса получения катализатора полимеризации олефинов при температуре более 90 С и времени пребывания менее 15 мин. Предпочтительно стадии испарения предшествовала стадия перегонки. Сущность изобретения Задача, решаемая данным изобретением В то время, как способ, предложенный в WO-A-2006056562, может хорошо подходить для некоторых типов сточных вод, авторы данного изобретения обнаружили, что особенно для жидких стоков, содержащих углеводороды, тетрахлорид титана и галогенированные алкоксиды титана, он приводит к получению очень вязкого остатка при относительно высоких отношениях остатка к дистилляту. Кроме того, при высоких температурах остаток может формировать куски, покрытые дегтем, которые могут оставаться в испарителе и нарушать процесс. После тщательных исследований авторы изобретения обнаружили, что при проведении испарения при пониженном давлении и при более низкой температуре образования кусков можно избежать и получить остаток с более низкой вязкостью. Краткое описание изобретения В данном изобретении предложен способ извлечения тетрахлорида титана из производственных стоков, включающий следующие стадии:(a) формирование смешанного потока, включающего тетрахлориды титана и алкоксихлориды титана;(b) формирование из потока стадии (а) стекающей жидкостной пленки при температуре от 25 до 85 С и абсолютном давлении от 5 до 60 кПа (от 0,05 до 0,6 бар).(c) формирование из пленки стадии (b) первого потока, содержащего от 90 до 100% регенерируемых компонентов, и второго потока, содержащего примерно от 10 до 80% галогеналкоксидов титана. Описание чертежа Фигура изображает схему типичного испарителя. Подробное описание изобретения Определения Если не оговорено другое, все величины процентного содержания в данной патентной заявке приведены относительно массы. Таким образом, цифра 70% относится к 70 мас.%. Данный текст относится к регенерируемым компонентам. Это некоторые жидкие компоненты, которые используют в процессе получения катализаторов либо в качестве реагентов, либо в качестве растворителей. Под регенерируемыми компонентами в данном описании понимают группу соединений, состоящую из тетрагалогенидов переходных металлов, алифатических углеводородов, которые предпочтительно содержат от 5 до 12 атомов углерода, ароматических углеводородов, которые предпочтительно содержат от 5 до 12 атомов углерода, и их смесей. Таким образом, в одном из примеров воплощения регенерируемые компоненты могут состоять из тетрахлорида титана. В другом примере воплощения регенерируемые компоненты могут состоять из толуола и тетрахлорида титана. В дополнительном примере воплощения регенерируемые компоненты могут состоять из толуола, гептана и тетрахлорида титана. Термины "галогеналкоксид переходного металла" и "алкоксигалогенид переходного металла" взаимозаменяемо используют в данном тексте для обозначения соединений, имеющих по меньшей мере одну алкоксигруппу и по меньшей мере одну группу галогенида, соединенные с атомом переходного металла. Они образуются, например, если галогенид переходного металла, например, тетрахлорид титана, реагирует со спиртом, например, 2-этилгексанолом, или сложным эфиром, например, ди-2-этилгексилфталатом. Обычно галогеналкоксиды, описываемые в этом тексте, представляют собой соединения, содержащие одну алкоксигруппу и три галогенидных группы, например, трихлор-2-этилгексанолят титана. Получение катализаторов Данный способ извлечения можно использовать при производстве большого количества катализаторов. Способ особенно пригоден для извлечения одного или большего количества компонентов, применяемых при производстве катализаторов полимеризации типа Циглера-Натта. Такие катализаторы можно использовать для полимеризации этилена, пропилена и других -олефинов, имеющих от 4 до 12 атомов углерода, или их смесей. Такие катализаторы описаны, среди прочих, в WO-A-87/07620, WO-A-92/21705,-1 024476WO-A-93/11165, WO-A-93/11166, WO-A-93/19100, WO-A-97/36939, WO-A-98/12234, WO-A-99/33842,WO-A-03/000756, WO-A-03/000757, WO-A-03/000754, WO-A-03/000755, WO-A-2004/029112, WO-A92/19659, WO-A-92/19653, WO-A-92/19658, US-A-4382019, US-A-4435550, US-A-4465782, US-A4473660, US-A-4560671, US-A-5539067, US-A-5618771, ЕР-А-45975, ЕР-А-45976, ЕР-А-45977, WO-A95/32994, US-A-4107414, US-A-4186107, US-A-4226963, US-A-4347160, US-A-4472524, US-A-4522930,US-A-4530912, US-A-4532313, US-A-4657882, US-А-4581342, US-A-4657882. Такие катализаторы обычно включают твердый компонент на основе переходного металла и сокатализатор. В соответствии с одним из предпочтительных примеров воплощения данное изобретение используют при получении катализаторов, где твердый компонент на основе переходного металла включает галогенид магния и соединение переходного металла. Эти соединения могут быть нанесены на носитель в виде частиц, например, на неорганические оксиды, такие как оксид кремния или оксид алюминия, или,обычно, сам галогенид магния может формировать твердый носитель. Примеры таких катализаторов описаны, среди прочего, в WO-A-87/07620, WO-A-92/21705, WO-A-93/11165, WO-A-93/11166, WO-A93/19100, WO-A-97/36939, WO-A-98/12234, WO-A-99/33842, WO-A-03/000756, WO-A-03/000757, WO-A03/000754, WO-A-2005/118655, ЕР-А-810235 и WO-A-2004/029112. В дополнительном примере воплощения твердый компонент на основе переходного металла обычно содержит, в дополнение к галогениду магния и соединению переходного металла, также донор электронов (внутренний донор электронов). Подходящими донорами электронов являются, помимо прочих,сложные эфиры карбоновых кислот, например, фталаты, цитраконаты и сукцинаты. Также можно использовать кислород- или азотсодержащие соединения кремния. Примеры подходящих соединений приведены в WO-A-92/19659, WO-A-92/19653, WO-A-92/19658, US-A-4347160, US-A-4382019, US-A4435550, US-A-4465782, US-A-4473660, US-A-4530912 и US-A-4560671. Таким образом, в одном из предпочтительных примеров воплощения активированный дихлорид магния суспендируют в инертных условиях в алифатическом углеводороде в реакторе при атмосферном давлении. Раствор охлаждают до температуры -15 С, и добавляют охлажденный тетрахлорид титана,поддерживая температуру на указанном уровне. Затем температуру суспензии медленно повышают до 20 С. При этой температуре к суспензии добавляют ди(этилгексил)фталат (DOP). После добавления фталата температуру повышают до 135 С, и суспензию выдерживают в течение некоторого периода времени. После этого катализатор отфильтровывают от жидкости. Затем добавляют другую порцию тетрахлорида титана, а температуру поддерживают при 135 С. После этого катализатор отфильтровывают от жидкости и промывают гептаном при 80 С. Затем твердый компонент катализатора фильтруют и сушат. Такие способы описаны, помимо прочего, в ЕР-А-491566, ЕР-А-591224 и ЕР-А-586390. Согласно другому предпочтительному примеру воплощения компонент катализатора получают в соответствии с WO-A-2004/029112 или WO-А-2003/106510. Согласно этому примеру воплощения твердый компонент катализатора получают с помощью процесса, включающего приготовление раствора магниевого комплекса посредством реакции алкоксидного соединения магния и донора электронов, или его предшественника, в жидкой реакционной среде, состоящей из ароматических соединений С 6-С 10; проведение реакции указанного магниевого комплекса с соединением по меньшей мере одного четырехвалентного металла IV группы, с получением эмульсии дисперсной фазы TiCl4/нерастворимое в толуоле масло, имеющей мольное отношение металла 4 группы/Mg от 0,1 до 10, в масляной дисперсионной среде, имеющей мольное отношение металл 4 группы/Mg от 10 до 100; и перемешивание эмульсии, возможно в присутствии стабилизатора эмульсии и/или агента, снижающего турбулентность до минимума. Частицы катализатора получают после отверждения указанных частиц дисперсной фазы. Смешанный поток Обычно твердый компонент катализатора подвергают одной или более стадиям декантации и промывки. На стадии декантации суспензию катализатора концентрируют путем декантации избытка жидкой фазы. Количество декантируемой жидкости зависит, помимо прочего, от исходной концентрации катализатора в суспензии. Обычно из катализатора можно удалить от 20 до 85% жидкости. Декантированная жидкая часть может, в дополнение к жидкой фазе, содержать незначительное количество катализатора. Однако количество катализатора в декантированной жидкости составляет предпочтительно менее 5% масс, более предпочтительно менее 2 мас.% и, в частности, менее 1 мас.%. Декантированная жидкость содержит реагенты, применяемые в процессе получения катализаторов, и их растворимые продукты реакции. Обычно жидкость содержит по меньшей мере тетрагалогенид переходного металла, предпочтительно тетрагалогенид переходного металла группы 4 или группы 5. На стадии промывки твердый компоненткатализатора контактирует с промывной жидкостью. Затем избыток жидкой фазы удаляют, обычно декантацией, и получают концентрированную суспензию катализатора. К этой концентрированной суспензии можно добавить другую порцию промывной жидкости, и эту процедуру можно повторять необходимое количество раз. Промывная жидкость, используемая на следующей стадии промывки, если такая стадия присутствует, может быть такой же, как промывная жидкость, используемая на предыдущей стадии промывки,или отличаться от нее. Соответственно, промывную жидкость выбирают из группы, состоящей из тетра-2 024476 галогенидов переходных металлов, алифатических углеводородов и ароматических углеводородов. Примерами тетрагалогенидов переходных металлов являются тетрагалогениды переходных металлов группы 4 или группы 5, например, тетрагалогениды титана, тетрагалогениды циркония и тетрагалогениды ванадия. Особенно предпочтительным тетрагалогенидом переходного металла является тетрахлорид переходного металла, например, тетрахлорид переходного металла группы 4 или группы 5, например, тетрахлорид титана, тетрахлорид циркония или тетрахлорид ванадия, а особенно тетрахлорид титана. Под алифатическими углеводородами в данном описании понимают углеводородные соединения с линейной, разветвленной или циклической цепью, которые не являются ароматическими и которые являются жидкими в условиях промывки. Предпочтительными алифатическими углеводородами являются алканы или циклоалканы, имеющие от 5 до 12 атомов углерода. Примерами пригодных алифатических углеводородов являются н-пентан, изопентан, н-гексан, 2-метилпентан, 3-метилпентан, циклогексан, нгептан, 2-метилгексан, 3-метилгексан, 3-этилпентан, н-октан, 2-метилгептан, 3-метилгептан, 4-метилгептан и 3-этилгексан. Под ароматическим углеводородом в данном описании понимают углеводородное соединение, которое является жидким в условиях промывки и которое содержит ароматическую группу, например, бензольное кольцо или кольцо циклопентадиенила. Ароматическая группа может содержать углеводородные заместители. Предпочтительные ароматические углеводороды представляют собой замещенные или незамещенные ароматические углеводородные соединения, имеющие от 5 до 12 атомов углерода. Примерами пригодных ароматических углеводородов являются бензол, толуол, 1,2-диметилбензол, 1,3-диметилбензол, 1,4-диметилбензол, этилбензол, 1,2-диэтилбензол, 1,3-диэтилбензол и 1,4-диэтилбензол. В качестве промывной жидкости можно также применять смеси вышеуказанных соединений. Поток жидкости, выходящий со стадии промывки, содержит промывную жидкость совместно с галогеналкоксидами переходных металлов, обычно галогеналкоксидами титана, например, хлоралкоксидами титана. Дополнительно он может содержать непрореагировавший донор электронов, непрореагировавший галогенид переходного металла, следы галогенида магния и другие соединения, применяемые при получении катализатора. Поток жидкости, выходящий с одной или более стадий декантации, или с одной или более стадий промывки, или с одной или более объединенных стадий декантации и промывки, образует смешанный поток. В альтернативном случае потоки жидкости, выходящие с одной или более стадий промывки,можно объединить с образованием смешанного потока. Смешанный поток содержит регенерируемые компоненты, например, промывную жидкость и тетрагалогенид переходного металла, которые можно использовать в процессе получения катализатора. С другой стороны, он также содержит галогеналкоксиды переходного металла, которые невозможно использовать повторно, но которые следует утилизировать. Смешанный поток можно подвергнуть процессам предварительного механического разделения, например, фильтрованию, перед тем, как подвергнуть этот поток процессу выпаривания. Стекающая жидкостная пленка Регенерируемые соединения отделяют от компонентов, подлежащих утилизации, используя способ испарения из стекающей жидкостной пленки. В таком процессе из потока образуют стекающую жидкостную пленку при температуре и давлении, при которых испаряется часть компонентов, содержащихся в потоке. Фракцию пара собирают, конденсируют и повторно используют, в то время как остаток утилизируют. Стекающую жидкостную пленку получают в испарителе, например, в тонкопленочном испарителе. Он обычно состоит из вертикального нагреваемого корпуса и вращающихся лопастей. Питающий поток,который может быть предварительно подогрет, поступает в верхнюю часть испарителя. Питающий поток пропускаютчерез распределительное кольцо, закрепленное на роторе, которое равномерно распределяет питающий поток по внутренней стенке испарителя. Вращающиеся лопасти поддерживают круговое движение стекающей жидкостной пленки в условиях турбулентного потока. Сочетание тонкой пленки и турбулентных условий создает быстрый тепло- и массоперенос. Это позволяет быстро нагревать пленку и испарять легкие компоненты. Чистые пары отбирают из верхней части испарителя, в то время как остаток отбирают из нижней части. Толщину и течение пленки регулируют находящимися внутри вращающимися лопастями. Различные лопасти, которые иногда называют системами очистки, хорошо известны в данной области. Обычно пленка имеет толщину менее 20 мм, предпочтительно не более 10 мм, а особенно - не более 5 мм. Обычно после того, как пары отобраны, их охлаждают и конденсируют. Обычно пар отбирают из верхней части испарителя, а затем конденсируют; но в меньших по размеру испарителях конденсатор может быть расположен внутри испарителя. В таком случае конденсированный дистиллят отбирают из нижней части. Такие испарители известны также как испарители с малым расстоянием от нагревателя до конденсатора. Испарители хорошо известны в данной области, и их можно приобрести, помимо прочего, у Niro,Columbia Energy, Pfaudler, Buss - SMS - Canzler GmbH, GIG Karasek и InCon. Обзор приведен, например,-3 024476Coulson and Richardson's Chemical Engineering, т. 2, пятое издание, Particle Technology and Separation Processes (Технология переработки частиц и процессы разделения), Butterworth Heinemann (2002), параграф 14.7.6, сс. 814-816. В оборудовании, соответствующем фигуре, поток жидкости, выходящий со стадий декантации и промывки, поступает в испаритель А, в качестве питающего потока 1. Испаритель имеет вращающиеся лопасти, закрепленные на валу, приводимом в движение двигателем М. Температуру внутри испарителя А регулируют посредством нагревательной рубашки, в которую горячие нефтепродукты поступают по линии 8, а выходят по линии 9. Питающий поток образует тонкую пленку, которая падает сверху вниз по стенке испарителя А. В то время как питающий поток проходит сверху вниз, летучие компоненты испаряют и собирают, в качестве дистиллята, посредством линии 2. Высококипящий остаток остается в жидкой форме, и его отбирают в качестве нижнего потока 7. После выхода из испарителя А парообразный поток 2 дистиллята конденсируют в холодильнике В,в который охлаждающий агент подают по линии 10 и отбирают по линии 11. Поток 3 конденсата отбирают из холодильника В и направляют в охлаждаемую ловушку С, откуда сконденсированный продукт отбирают в виде потока 4. Из охлаждаемой ловушки С вакуумная линия 5 ведет к вакуумному насосу D,откуда инертный газ отбирают по линии 6. Охлаждаемую ловушку С охлаждают охлаждающим маслом,поступающим по линии 12 и выходящим по линии 13. Первый поток Первый поток представляет собой поток пара, испаренного из стекающей жидкостной пленки. Этот поток пара затем отбирают и конденсируют в охладителе. Первый поток содержит регенерируемые компоненты смешанного потока. Согласно одному из предпочтительных примеров воплощения, первый поток состоит по существу из тетрагалогенида переходного металла, предпочтительно тетрагалогенида переходного металла 4 или 5 группы, в частности, тетрахлорида титана, тетрахлорида циркония или тетрахлорида ванадия. Особенно предпочтительно он является тетрахлоридом переходного металла, например, тетрахлоридом титана,тетрахлоридом циркония или тетрахлоридом ванадия, в частности, тетрахлоридом титана. В соответствии с этим примером воплощения первый поток содержит от 90 до 100%, предпочтительно от 95 до 100%, в частности от 99 до 100%, например 99,5% тетрагалогенида переходного металла. Согласно другому предпочтительному примеру воплощения, первый поток содержит указанный тетрагалогенид переходного металла и, дополнительно, углеводород или смесь углеводородов. Углеводород является тем же самым, что и описываемая выше промывная жидкость. В этом примере воплощения первый поток содержит от 5 до 70 мас.% тетрагалогенида переходного металла и от 30 до 95 мас.% углеводорода или смеси углеводородов. Обычно примерно от 50 до 95% регенерируемых компонентов извлекают в первом потоке, в то время как остальные переходят во второй поток. В то время как экономически было бы выгодно извлекать как можно больше регенерируемых компонентов, имеются практические пределы, связанные с тем,что второй поток должен быть технологичным. Как понимают специалисты, в первом потоке может также присутствовать некоторое количество алкоксигалогенидов переходных металлов. Количество таких алкоксигалогенидов предпочтительно составляет менее 2 мас.%, а более предпочтительно - менее 1 мас.% от первого потока. Дополнительная обработка первого потока Если первый поток содержит более одного регенерируемого компонента, например, галогенид переходного металла и ароматический углеводород, то предпочтительно дополнительно разделить компоненты таким образом, чтобы каждый компонент можно было по отдельности возвратить в процесс получения катализатора. Разделение компонентов может быть достигнуто с помощью хорошо известных способов разделения, например, мгновенным испарением, перегонкой, отгонкой и т.п. Предпочтительно компоненты разделяют перегонкой. В процессе перегонки углеводород обычно извлекают в виде дистиллята, а тетрагалогенид переходного металла - в виде кубового продукта. Поэтому обычно поток дистиллята содержит от 80 до 100 мас.% углеводорода или смеси углеводородов, предпочтительно от 90 до 100 мас.% и более предпочтительно от 95 до 100 мас.%. Кубовый продукт содержит от 80 до 100 мас.% тетрагалогенида переходного металла, предпочтительно от 90 до 100%, а более предпочтительно от 95 до 100%. В одном из конкретных примеров воплощения поток дистиллята содержит от 99 до 100 мас.% толуола, а поток кубового продукта - от 99 до 100 мас.% тетрахлорида титана. Второй поток Второй поток содержит остаток после выпаривания. В основном он содержит галогеналкоксиды переходных металлов. Также он содержит некоторое количество тетрагалогенида переходного металла,но также и незначительные количества твердых или высококипящих компонентов, применяемых в процессе получения катализатора, таких как дихлорид магния, донор электронов и т.п. В то время как было бы преимуществом удалить из второго потока весь тетрагалогенид переходного металла, это привело бы к тому, что второй поток стал бы слишком вязким для переработки. Таким образом, некоторое количест-4 024476 во тетрагалогенида переходного металла по необходимости остается во втором потоке. Также во втором потоке может присутствовать некоторое количество остаточного углеводорода. В качестве примера, второй поток содержит от 10 до 40 мас.% тетрагалогенида переходного металла, от 10 до 80 мас.% галогеналкоксида переходного металла, от 10 до 40 мас.% донора электронов и дихлорида магния и до 10 мас.% углеводородов. Обычно второй поток и его компоненты невозможно извлечь и повторно использовать. Вместо этого второй поток представляет собой поток отходов, и его утилизируют. Он содержит компоненты, опасные для окружающей среды. Таким образом, его следует рассматривать как проблему стока и обрабатывать соответствующим образом. Преимущества данного изобретения Данное изобретение представляет простой и экономичный способ извлечения и повторного использования компонентов, применяемых для получения катализаторов полимеризации олефинов. Этот способ является надежным в работе, и компоненты можно извлечь с высоким выходом. Примеры Способы Содержание титана и магния Был проведен элементный анализ стоков производства катализаторов путем отбора жидкого образца массой М в инертных условиях. Затем образец обрабатывали изопропанолом, перемешивали и затем подкисляли разбавленной азотной кислотой при перемешивании. Затем колбу с образцом открывали, и его переносили в платиновую чашку; колбу промывали дополнительным количеством изопропанола и разбавленной азотной кислоты. Платиновую чашку переносили на теплую песчаную баню (80) и выпаривали в течение ночи. Остаток образца разбавляли до известного объема V, растворяя его в азотной кислоте (65% HNO3, 5% от V), плавиковой кислоте (HF, 40%, 3% от V) и свежедеионизированной (ДИ) воде (5% от V). Затем раствор переносили в полипропиленовую мерную колбу, платиновую чашку ополаскивали, и образец разбавляли ДИ водой до конечного объема, V, и оставляли для стабилизации на 2 ч. Анализ проводили при комнатной температуре с использованием оптического эмиссионного спектрометра с индукционно связанной плазмой (ICP-OES) Thermo Elemental ICAP 6300, откалиброванного по холостой пробе (раствор 5% HNO3, 3% HF в деионизированной воде), и стандартов - 0,5, 1, 10, 50, 100 и 300 млн ч. Al, Mg и Ti, в растворах 5% HNO3, 3% HF в деионизированной воде. Непосредственно перед анализом проводили "перекалибровку", используя холостую пробу и стандарт 100 млн ч; для подтверждения перекалибровки пропускали образец для контроля качества (20 млн ч. Al, Mg и Ti в растворе 5% HNO3, 3% HF в деионизированной воде). Образец для контроля качества пропускали также после каждого пятого образца, а также в конце запланированного набора анализов. Содержание Mg определяли с использованием линии 285,213 нм, а содержание Ti - с использованием линии 336,121 нм. Содержание алюминия определяли по линии 167,079 нм, когда концентрация Al вICP образце составляла от 0 до 10 млн ч. (калибровку проводили только до 100 млн ч.); а при концентрациях Al выше 10 млн ч. - по линии 396,152 нм. Приведенные величины являются средним значением из трех последовательных аликвот, взятых от одного образца, и относятся к исходному катализатору, при введении в компьютерную программу расчета исходной массы образца и объема разбавления. Содержание TiCl4 Предполагали, что титан присутствует в виде TiCl4 и галогеналкоксида типа TiCl3OEHA. При расчетах концентрации этих компонентов основывались на количестве Ti (определенного методом атомноэмиссионной спектрометрии с индукционно связанной плазмой (ICP-AES и 2-этилгексанола (полученного гидролизом образца с последующим анализом методом газовой хроматографии (ГХ, откуда рассчитывали мольное количество тетрахлорида титана по уравнению где nTi, TiCl3OEHA = nEHA [мольн.]. Содержание углеводородов Определение количества углеводородов в образце проводили с использованием газовой хроматографии (газ-носитель Не, пламенно-ионизационный детектор, колонка DB-1, 30 м 0,32 мм, толщина пленки 0,25 мкм). 50-100 мг образца взвешивали в 20-мл колбе (точность взвешивания 0,1 мг). Добавляли 3-4 мл дихлорметана, а затем - известную массу нонана, в качестве внутреннего стандарта. Образец обрабатывали ультразвуком в течение 5-10 мин, в ультразвуковой ванне. Образец разбавляли соответствующим образом, и жидкий образец фильтровали с использованием фильтра 0,45 мкм в кювету пробоотборника газового хроматографа. Фаза нагревания включала выдержку при 40 С в течение 5 мин; увеличение температуры со скоростью 10 С/мин до 250 С с последующей выдержкой температуры в течение еще 4 мин. Для анализа 2-этилгексанола к раствору перед обработкой ультразвуком добавляли примерно 1 мл воды. При переносе образца в кювету пробоотборника газового хроматографа образец удаляли только из органической фазы. Затем содержание компонента х, Сх, в образце рассчитывали по уравнению: где Ах представляет собой площадь пика компонента х, F представляет собой коэффициент для компонента х, Mi представляет собой массу внутреннего стандарта (нонана) в мг, Ау представляет собой площадь пика внутреннего стандарта, Fistd представляет собой коэффициент для внутреннего стандарта, и Мобр представляет собой массу образца в мг. Результаты обычно рассчитывали автоматически с помощью компьютера, контролирующего газовый хроматограф. Предел определения для углеводородов составляет 0,01 мас.%, а для 2-этилгексанола 0,1 мас.%. Содержание алкоксигалогенидов титана Предполагали, что весь титан присутствует в виде TiCl4 и галогеналкоксида типа TiCl3OEHA. При расчетах концентрации этих компонентов основывались на количестве Ti (определенного методом ICPAES) и 2-этилгексанола (полученного гидролизом образца с последующим анализом посредством ГХ). Количество 2-этилгексанола затем брали в качестве количества алкоксигалогенида титана, то естьnTi, TiCl3OEHA = nEHA [мольн.]. Содержание MgCl2 Содержание MgCl2 в жидкой смеси определяли из анализа на Mg, как описано выше, в предположении, что весь Mg находится в форме MgCl2. Содержание ди-2-этилгексилфталата Содержание ди-2-этилгексилфталата в жидкой фазе измеряли с использованием высокоэффективной жидкостной хроматографии ВЖХ (УФ-детектор, колонка RP-8, 2504 мм). Для приготовления стандартных растворов использовали чистый ди-2-этилгексилфталат. 50-100 мг образца взвешивали в 20 мл колбе (точность взвешивания 0,1 мг). Добавляли 10 мл ацетонитрила, и суспензию образца обрабатывали в течение 5-10 мин в ультразвуковой ванне. Суспензию в ацетонитриле разбавляли соответствующим образом, и жидкий образец фильтровали с использованием фильтра 0,45 мкм в кювету пробоотборника прибора ВЖХ. При проведении ВЖХ получали высоты пиков. Процентное содержание донора в образце рассчитывали с использованием следующего уравнения: процентное содержание (%) = A1 сVА 2-1m-10,1%,гдеA1 = высота пика образца,с = концентрация стандартного раствора (мг/л),V = объем раствора образца (мл),А 2 = высота пика стандарта,m = масса образца (мг). Пример 1 Твердые компоненты катализатора Циглера-Натта подвергли стадии промывки толуолом. Стадия промывки заключалась в одной стадии декантации и одной стадии промывки. При стадии декантации из катализатора удаляли часть жидкой фазы, так, чтобы примерно 20% жидкости оставалось в катализаторе. Затем к катализатору добавляли некоторый объем толуола, соответствующий объему удаленной жидкости. После этого жидкость удаляли таким же образом, как и при стадии декантации, описанной выше. Жидкую фазу извлекали и анализировали. Было обнаружено, что она содержит 58 мас.% толуола, 26 мас.% TiCl4, 6% гептана, 8% галогеналкоксидов титана, 1,5% ди-2-этилгексилфталата и 0,5% MgCl2. Она обозначена как жидкость А. Пример 2 Повторили процедуру примера 1, за исключением того, что применяли другой способ получения катализатора. Было обнаружено, что полученная жидкая фаза содержала 65 мас.% толуола, 20 мас.%TiCl4, 6% гептана, 7% галогеналкоксидов титана, 1,5% ди-2-этилгексилфталата и 0,5% MgCl2. Она обозначена как жидкость В. Пример 3 Повторили процедуру примера 1, за исключением того, что применяли другой способ получения катализатора. Было обнаружено, что полученная жидкая фаза содержала 64 мас.% толуола, 22 мас.%TiCl4, 4% гептана, 6% галогеналкоксидов титана, 2,5% ди-2-этилгексилфталата и 1,5% MgCl2. Она обозначена как жидкость С. Приведенные ниже примеры 4 и 5 были проведены для того, чтобы продемонстрировать максимальное извлечение дистиллята. Пример 4 Жидкость С (из примера 3) перенесли в тонкопленочный испаритель, предоставленный GIG KarasekGmbH, имеющий диаметр 70 мм и длину 190 мм. Испаритель имеет цилиндрический корпус, который очищают скользящие лопасти. Он имеет нагреваемую поверхность 4 дм 2 и три лопасти, предотвращаю-6 024476 щие разбрызгивание. Испаритель работал в атмосфере аргона. Стекающая пленка жидкости С формировалась в испарителе при абсолютном давлении 20 кПа (220 мбар; 0,2 бар). Температура нагреваемых маслом стенок испарителя составляла 60 С. Скорость вращения очищающих лопастей составляла 392 оборотов в минуту. Скорость подачи жидкости С составляла 4 г/мин. В целом, 109,4 г жидкости С обрабатывали, как описано выше. Толщина пленки составляла менее 1 мм. В результате было извлечено 99 г фракции дистиллята и 10,4 г остатка. Остаток был вязким и медленно текучим в условиях проведения испытания, возможно, из-за очень высокого отношения дистиллята к остатку. Однако засорения оборудования не наблюдали. Данные и результаты приведены в таблице. Фракцию дистиллята проанализировали и обнаружили, что она содержит 73% толуола, 22% TiCl4 и 5% гептана. Также был проанализирован остаток, и было обнаружено, что он содержит 19% TiCl4, 43%TiCl3C8H16OH, 13% С 24 Н 38 О 4, 1% С 7 Н 16 и 6% MgCl2. Пример 5 Повторили процедуру примера 4, за исключением того, что давление составляло 45 кПа (450 мбар); температура масла составляла 80 С, а расход - 2,5 г/мин. Остаток был текучим в условиях проведения испытаний, и засорения оборудования не наблюдали. Другие данные и результаты приведены в таблице. Примеры 6 и 7 были проведены, чтобы продемонстрировать максимальную производительность. Пример 6 Повторили процедуру примера 4, за исключением того, что использовали жидкость В вместо жидкости С, и того, что температура масла составляла 70 С, давление - 24 кПа (240 мбар), а расход составлял 7 г/мин. Остаток был текучим в условиях проведения испытания, и засорения оборудования не наблюдали. Другие данные и результаты приведены в таблице. Пример 7 Повторили процедуру примера 6, за исключением того, что температура масла составляла 80 С,давление - 25 кПа (250 мбар), а расход - 8 г/мин. Остаток был текучим в условиях проведения испытаний, и засорения оборудования не наблюдали. Другие данные и результаты приведены в таблице. Сравнительный пример 8 Повторили процедуру примера 4, за исключением того, что вместо жидкости С использовали жидкость А. Кроме того, температура масла составляла 110 С, испытание проводили при атмосферном давлении (0,1 МПа; 1,0 бар), и расход составлял 6 г/мин. Остаток становился чрезвычайно вязким и почти не текучим, даже несмотря на то, что отношение остатка к дистилляту было несколько выше, чем в примере 4. Кроме того, в кубе испарителя образовывались куски, и их невозможно было удалить в ходе эксперимента. Дополнительные данные и результаты приведены в таблице. Пример 9 Фракцию дистиллята примера 4 проанализировали и обнаружили, что она содержит 73% толуола,22% TiCl4 и 5% гептана. Ее направили на стадию перегонки при абсолютном давлении 0,1 МПа (1 бар); полученный при этом дистиллят содержал 1% TiCl4, 93% толуола и 6% гептана. Кубовый продукт содержал 99,5% TiCl4 и 0,5% толуола. Температура в кубе колонны составляла 136 С. Данные экспериментов по испарению В испарителе образовывались куски, и масса этих кусков не включена в приведенную цифру. Таким образом, истинная масса остатка была больше измеренной. ФОРМУЛА ИЗОБРЕТЕНИЯ 1. Способ извлечения тетрагалогенида переходного металла из потока отходов процесса получения катализатора, включающий следующие стадии:(a) формирование смешанного потока, содержащего тетрагалогенид переходного металла и галогеналкоксиды переходного металла;(b) формирование стекающей жидкостной плнки из смешанного потока стадии (а) при температуре от 50 до 85 С и абсолютном давлении от 10 до 60 кПа (от 0,1 до 0,6 бар);(c) формирование испарением из пленки стадии (b) первого потока, содержащего от 90 до 100% регенерируемых компонентов, включающих галогенид переходного металла, и второго потока, представляющего собой остаток после указанного выпаривания, содержащего примерно от 20 до 80% галогеналкоксидов переходных металлов. 2. Способ по п.1, в котором указанный первый поток содержит менее 1 мас.% галогеналкоксидов переходных металлов. 3. Способ по п.1 или 2, в котором отношение остаток/дистиллят (О/Д) составляет от 0,05 до 0,35. 4. Способ по любому из предыдущих пунктов, в котором указанный переходный металл является переходным металлом группы 4 или группы 5. 5. Способ по п.4, в котором указанный переходный металл является титаном. 6. Способ по любому из предыдущих пунктов, в котором указанный тетрагалогенид переходного металла представляет собой тетрахлорид переходного металла, а указанный галогеналкоксид представляет собой хлоралкоксид переходного металла. 7. Способ по любому из пп.1-6, в котором стадия (а) включает следующие стадии:(а-1) проведение стадии промывки твердого компонента катализатора полимеризации олефинов,полученного из процесса получения катализатора, посредством приведения его в контакт с промывной жидкостью, для получения смеси, включающей твердый компонент катализатора и промывную жидкость;(а-2) разделение смеси стадии (а-1) на фракцию продукта, содержащую основную часть твердого компонента катализатора, и жидкую фракцию, содержащую промывную жидкость;(а-4) получение смешанного потока, включающего тетрагалогенид переходного металла и галогеналкоксиды переходного металла из указанной жидкой фракции. 8. Способ по п.7, в котором промывную жидкость выбирают из группы, состоящей из тетрагалогенида титана, алифатических углеводородов, ароматических углеводородов и их смесей. 9. Способ по п.8, в котором промывную жидкость выбирают из группы, состоящей из алифатических углеводородов, ароматических углеводородов и их смесей. 10. Способ по п.9, дополнительно включающий следующие стадии:(d) подачу первого потока на стадию перегонки;(e) отбор с указанной стадии перегонки первого потока легкой фракции, включающего по меньшей мере 80% промывной жидкости; и(f) отбор с указанной стадии перегонки первого потока кубового продукта, включающего по меньшей мере 80 мас.% тетрагалогенида переходного металла. 11. Способ по п.10, в котором первый поток легкой фракции содержит по меньшей мере 90% промывной жидкости. 12. Способ по п.10 или 11, в котором первый поток кубового продукта содержит по меньшей мере 95 мас.% тетрагалогенида переходного металла. 13. Способ по любому из пп.9-12, в котором указанную промывную жидкость выбирают из группы,состоящей из бензола, толуола, 1,2-диметилбензола, 1,3-диметилбензола, 1,4-диметилбензола, этилбензола, 1,2-диэтилбензола, 1,3-диэтилбензола и 1,4-диэтилбензола.
МПК / Метки
МПК: C01G 23/02, C01G 1/06, C22B 34/12, B01D 1/22
Метки: переходных, потока, тетрагалогенидов, металлов, углеводородов, извлечения, способ, отходов
Код ссылки
<a href="https://eas.patents.su/9-24476-sposob-izvlecheniya-tetragalogenidov-perehodnyh-metallov-i-uglevodorodov-iz-potoka-othodov.html" rel="bookmark" title="База патентов Евразийского Союза">Способ извлечения тетрагалогенидов переходных металлов и углеводородов из потока отходов</a>
Предыдущий патент: Композиции витамина в12 для интраназального применения
Следующий патент: Композиции и способы завершения скважин
Случайный патент: Средство защиты и способ аутентификации пользователя с помощью этого средства