Катализатор для получения параксилола путем совместной конверсии метанола и/или диметилового эфира и сжиженного газа c4, способ приготовления этого продукта и способ его использования
Формула / Реферат
1. Катализатор для получения параксилола путем совместной конверсии метанола и/или диметилового эфира и сжиженного газа С4, отличающийся тем, что указанный катализатор представляет собой ароматизирующий катализатор с молекулярным ситом с конфигурационно-селективной функцией, совместно модифицированный биметаллом и силоксановым соединением, где биметаллом является цинк и галлий, а силоксановое соединение имеет структурную формулу I
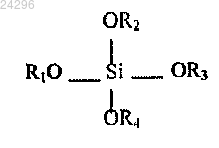
где R1, R2, R3 и R4 независимо выбирают из алкильной группы C1-С10.
2. Катализатор по п.1, отличающийся тем, что указанное силоксановое соединение представляет собой тетраэтоксисилан.
3. Катализатор по п.1, отличающийся тем, что молекулярное сито в указанном ароматизирующем катализаторе с конфигурационно-селективной функцией представляет собой молекулярное сито цеолита HZSM-5 и/или HZSM-11.
4. Катализатор по п.1, отличающийся тем, что объем загрузки цинка составляет 0,5-8 мас.% от общей массы катализатора; объем загрузки галлия составляет 0,5-8 мас.% от общей массы катализатора и объем загрузки силоксанового соединения составляет 0,5-10 мас.% от общей массы катализатора.
5. Способ получения любого из указанных катализаторов по п.1-4, включающий следующие стадии:
(a) молекулярное сито импрегнируют раствором, содержащим по меньшей мере одну растворимую соль одного из элементов - цинка и галлия, затем фильтруют, сушат и прокаливают с получением модифицированного металлом молекулярного сита;
(b) указанное модифицированное металлом молекулярное сито, полученное на стадии (а), импрегнируют раствором, содержащим по меньшей мере одну растворимую соль другого из элементов - цинка и галлия, затем фильтруют, сушат и прокаливают с получением модифицированного биметаллом молекулярного сита;
(с) указанное модифицированное биметаллом молекулярное сито, полученное на стадии (b), импрегнируют силоксановым соединением, затем фильтруют, сушат и прокаливают с получением указанного ароматизирующего катализатора с молекулярным ситом, совместно модифицированного биметаллом и силоксановым соединением.
6. Способ получения параксилола путем совместной конверсии метанола и/или диметилового эфира и сжиженного газа С4, включающий следующие стадии: газовую смесь, содержащую метанол и/или диметиловый эфир и сжиженный газ С4, пропускают через реактор для получения параксилола с помощью реакции ароматизации;
отличающийся тем, что в указанный реактор загружают любой из указанных катализаторов по пп.1-4;
отличающийся тем, что указанная реакция ароматизации выполняется при температуре 350-550°С, давлении от атмосферного давления до 5 МПа и среднечасовой скорости подачи указанной газовой смеси от 0,1 до 20 ч-1.
7. Способ по п.6, отличающийся тем, что выполняется в реакторе с неподвижным слоем или с псевдоожиженным слоем.
Текст
КАТАЛИЗАТОР ДЛЯ ПОЛУЧЕНИЯ ПАРАКСИЛОЛА ПУТЕМ СОВМЕСТНОЙ КОНВЕРСИИ МЕТАНОЛА И/ИЛИ ДИМЕТИЛОВОГО ЭФИРА И СЖИЖЕННОГО ГАЗА C4, СПОСОБ ПРИГОТОВЛЕНИЯ ЭТОГО ПРОДУКТА И СПОСОБ ЕГО ИСПОЛЬЗОВАНИЯ Предлагается катализатор для получения параксилола путем совместной конверсии метанола и/или диметилового эфира и сжиженного газа С 4, a также его приготовление и применение. Катализатор представляет собой ароматизирующий катализатор с молекулярным ситом с конфигурационноселективной функцией, совместно модифицированный биметаллом и силоксановым соединением. Метанол и/или диметиловый эфир и сжиженный газ С 4 подают в реактор вместе, где реакция ароматизации протекает на катализаторе с модифицированным конфигурационно-селективным молекулярным ситом. Выход ароматических углеводородов эффективно повышается, причем параксилол является основным продуктом. В продуктах, полученных путем совместной конверсии метанола и/или диметилового эфира и сжиженного газа С 4, выход ароматических углеводородов более 70 мас.%, содержание параксилола в ароматических углеводородах более 80 мас.% и селективность параксилола в ксилоле более 99 мас.%.(71)(73) Заявитель и патентовладелец: ДАЛЯНЬ ИНСТИТЬЮТ ОФ КЕМИКАЛ ФИЗИКС, ЧАЙНИЗ АКАДЕМИ ОФ САЙЭНС (CN) Область технического применения Настоящее изобретение относится к способу получения параксилола путем совместной конверсии метанола и/или диметилового эфира и сжиженного газа С 4. Конкретнее, настоящее изобретение относится к высокоселективному катализатору для получения параксилола путем совместной конверсии метанола и/или диметилового эфира и сжиженного газа С 4. Кроме того, настоящее описание изобретения относится к способу приготовления и применения указанного катализатора. Предпосылки создания изобретения Параксилол является основным сырьевым материалом для получения полиэфира. В настоящее время параксилол в основном получают путем диспропорционирования, изомеризации, адсорбционного разделения или криогенного разделения сырьевого материала, содержащего толуол, ароматические углеводороды С 9 и смешанный ксилол из продуктов каталитического риформинга сырой нефти. По этому способу соотношение целевого параксилола-продукта в смешанных ароматических углеводородах C8 составляет всего лишь около 20% из-за того, что реакция получения параксилола регулируется термодинамикой. Оборудование для него огромное при высоких эксплуатационных расходах из-за большого количества вторичного материала, а также требуется дорогостоящая система адсорбционного разделения,поскольку параксилол-продукт высокой чистоты нельзя получить путем обычной ректификации. В связи с ростом дефицита нефтяных ресурсов многие отечественные и зарубежные научноисследовательские институты начали активно разрабатывать новые методы получения ароматических углеводородов, например получение ароматических углеводородов из метанола или из сжиженного газа и т.д. Технология преобразования метанола в ароматические углеводороды предоставляет новый путь получения ароматических углеводородов из угля или природного газа, при которой углеводороды можно непосредственно получать путем реакции ароматизации метанола или диметилового эфира на композитном катализаторе, содержащем металл и цеолит. В 1977 году в работе Mobil's Chang et al. (Journal of Catalysis, 1977, 47, 249) сообщалось о способе получения ароматических углеводородов и других углеводородов на цеолитных катализаторах ZSM-5 из метанола или других оксигенатов. Было показано, что алканы и олефины можно конвертировать в ароматические углеводороды в определенных условиях под воздействием металлических компонентов. Таким образом, основным направлением исследований стало то, что цеолитные катализаторы ZSM-5 модифицируются металлическим компонентом с целью получения большего количества ароматических углеводородов путем конверсии метанола. В настоящее время модификация цеолитных катализаторов ZSM-5 в основном направлена на использование Zn и Ga, между тем, сообщалось об использовании других металлов, например Ag, Cu. Авторы Ono et al. (J Chem. Soc., Faraday Trans. 1, 1988, 84 (4), 1091; Microporous Materials, 1995, 4, 379) исследовали каталитическую производительность способа преобразования метанола в ароматические углеводороды (МТА) на цеолитных катализаторах ZSM-5, которые были модифицированы с помощью Zn иAg с использованием ионообменного метода. Было установлено, что выход ароматических углеводородов в продуктах увеличился примерно до 67,4% (С%) после модификации цеолита ZSM-5 с помощью Zn и увеличился примерно до 80% после модификации цеолита ZSM-5 с помощью Ag. В патенте CN 101244969 описана установка с псевдоожиженным слоем, содержащая реактор ароматизации углеводорода С 1-С 2 или метанола и систему регенерации катализатора. Путем регулирования состояния коксования катализатора в реакторе ароматизации осуществляется непрерывная эффективная конверсия углеводородов С 1-С 2 или метанола в ароматические углеводороды с высокой селективностью. В патенте CN 1880288 описан способ с высокой общей селективностью по ароматическим углеводородам, и который может работать гибко. В качестве основного продукта получают ароматические углеводороды в результате конверсии метанола на модифицированных цеолитных катализаторах ZSM-5. В патенте US 4615995 описан цеолитный катализатор ZSM-5, загруженный Zn и Mn. Катализатор используется для конверсии метанола в олефин и ароматические углеводороды. В продуктах соотношение низкоуглеродистых олефинов к ароматическим углеводородам можно контролировать путем регулирования содержания Zn и Mn, загруженных в катализатор. Эффективным способом расширения источников ароматических углеводородов является способ ароматизации сжиженного нефтяного газа (СНГ) из побочных продуктов нефтепереработки. В процессе ароматизации СНГ в ароматические углеводороды можно одновременно получать бензин высокого качества и ароматические углеводороды, например бензол, толуол и ксилол (БТК). В патенте США 4642402 описан способ конверсии легких углеводородов в ароматические углеводороды, разработанный фирмойUOP, превращающий С 3 и С 4 в ароматические углеводороды ВТХ с помощью реакции ароматизации на цеолитном катализаторе ZSM-5, модифицированном Ga, в котором выход ароматических углеводородов составляет примерно 60%. В патенте CN 1023633C описан цеолитный катализатор HZSM-5, модифицированный галлием,цинком и платиной, при использовании для реакции ароматизации низкоуглеродного алкана. Катализатор применим для ароматизации алкана C5-C8, главным образом, олефинов в смешанные ароматические углеводороды, содержащие бензол, толуол и ксилол. Общий выход ароматических углеводородов составляет около 50 мас.%. В патенте CN 1660724 А описан способ с псевдоожиженным слоем, который используется для ароматизации сжиженного газа в бензол, толуол и ксилол на катализаторе DLC-2, общий выход бензола,толуола и ксилола составляет около 65 мас.%. Указанные способы конверсии метанола или сжиженного газа в ароматические углеводороды, в которых во всех используется один сырьевой материал для получения целевых смешанных ароматических углеводородов: бензола, толуола и ксилола (БТК), имеют низкую рыночную стоимость и, таким образом,низкую экономическую прибыль. Раскрытие В настоящей заявке представлен катализатор для получения ароматических углеводородов с высоким выходом путем совместной конверсии метанола и/или диметилового эфира и сжиженного газа С 4; способ приготовления указанного катализатора и применение указанного катализатора. И более конкретно, в настоящей заявке представлен высокопродуктивный способ получения ароматических углеводородов с использованием указанного катализатора. При объединении метанола из угля и сжиженного газа С 4 из побочных продуктов нефтепереработки в качестве сырьевого материала с помощью указанного способа ароматические углеводороды можно получать в больших количествах. При этом выход ароматических углеводородов можно эффективно повысить путем объединения ароматизации метанола и ароматизации сжиженного газа. В настоящей заявке также представлен способ получения параксилола с высоким выходом путем совместной конверсии метанола и/или диметилового эфира и сжиженного газа С 4. Метанол и/или диметиловый эфир и сжиженный газ С 4 подвергаются совместной конверсии в параксилол с помощью реакции ароматизации и реакции конфигурационно-селективного алкилирования на катализаторе с молекулярным ситом с конфигурационно-селективной функцией, совместно модифицированном биметаллом и силоксановым соединением. В настоящей заявке представлен катализатор для получения параксилола путем совместной конверсии метанола и/или диметилового эфира и сжиженного газа С 4. Указанный катализатор представляет собой ароматизирующий катализатор с молекулярным ситом с конфигурационно-селективной функцией,совместно модифицированный биметаллом и силоксановым соединением, в котором указанным биметаллом являются цинк и галлий, в котором силоксановое соединение имеет структурную формулу в виде формулы I(формула I),где R1, R2, R3 и R4 независимо выбирают из алкильной группы C1-С 10. В предпочтительном варианте осуществления указанное силоксановое соединение представляет собой тетраэтоксисилан. В предпочтительном варианте осуществления способ модификации молекулярного сита при взаимодействии биметаллом и силоксановым соединением включает следующие стадии: (а) молекулярное сито импрегнируют раствором, содержащим по меньшей мере одну растворимую соль одного из элементов - цинка и галлия, затем фильтруют, сушат и прокаливают с получением модифицированного металлом молекулярного сита; (b) указанное модифицированное металлом молекулярное сито, полученное на стадии (а), импрегнируют раствором, содержащим по меньшей мере одну растворимую соль другого из элементов - цинка и галлия, затем фильтруют, сушат и прокаливают с получением модифицированного биметаллом молекулярного сита; (с) указанное модифицированное биметаллом молекулярное сито, полученное на стадии (b), импрегнируют силоксановым соединением, затем фильтруют, сушат и прокаливают с получением указанного ароматизирующего катализатора с молекулярным ситом, совместно модифицированного биметаллом и силоксановым соединением. В предпочтительном варианте осуществления молекулярное сито, используемое в указанном ароматизирующем катализаторе с молекулярным ситом с конфигурационно-селективной функцией, представляет собой молекулярное сито цеолита HZSM-5 и/или HZSM-11. В предпочтительном варианте осуществления объем загрузки указанного цинка составляет 0,5-8 мас.% от общей массы указанного катализатора; и объем загрузки указанного галлия составляет 0,5-8 мас.% от общей массы указанного катализатора; и объем загрузки указанного силоксанового соединения на основе окиси кремния составляет 0,5-10 мас.% от общей массы указанного катализатора. В другом аспекте в настоящей заявке представлен способ получения любого из указанных катализаторов, включающий следующие стадии:(a) молекулярное сито цеолита импрегнируют раствором, содержащим по меньшей мере одну растворимую соль одного из элементов - цинка и галлия, затем фильтруют, сушат и прокаливают с получением модифицированного металлом молекулярного сита;(b) указанное модифицированное металлом молекулярное сито, полученное на стадии (а), импрег-2 024296 нируют раствором, содержащим по меньшей мере одну растворимую соль другого из элементов - цинка и галлия, затем фильтруют, сушат и прокаливают с получением модифицированного биметаллом молекулярного сита;(с) указанное модифицированное биметаллом молекулярное сито, полученное на стадии (b), импрегнируют силоксановым соединением, затем фильтруют, сушат и прокаливают с получением указанного ароматизирующего катализатора с молекулярным ситом, совместно модифицированного биметаллом и силоксановым соединением. В другом аспекте в настоящей заявке представлен способ получения параксилола путем совместной конверсии метанола и/или диметилового эфира и сжиженного газа С 4, включающий следующие стадии: газовую смесь, содержащую метанол и/или диметиловый эфир и сжиженный газ С 4, пропускают через реактор для получения параксилола с помощью реакции ароматизации; в котором в указанный реактор загружают любой из указанных катализаторов по пункту 1-4; в котором указанная реакция ароматизации выполняется при температуре 350-550 С, давлении от атмосферного давления до 5 МПа и среднечасовой скорости подачи указанной газовой смеси от 0,1 до 20 ч-1. В настоящей заявке выход ароматических углеводородов составляет более 70 мас.% в неводных продуктах в результате ароматизации метанола и/или диметилового эфира и сжиженного газа С 4; и селективность параксилола в ароматических углеводородах составляет более 80 мас.% и селективность параксилола в изомерах ксилола составляет более 99 мас.%. В предпочтительном варианте осуществления указанный способ выполняется в реакторе с неподвижном слоем или с псевдоожиженным слоем. Подробное описание вариантов осуществления В частности, в настоящей заявке представлен катализатор для получения параксилола путем совместной конверсии метанола и/или диметилового эфира и сжиженного газа С 4. Указанный катализатор представляет собой ароматизирующий катализатор с молекулярным ситом с конфигурационноселективной функцией, совместно модифицированный биметаллом и силоксановым соединением, в котором указанный биметалл представляет собой цинк и галлий. В настоящей заявке указанный ароматизирующий катализатор с молекулярным ситом, совместно модифицированный биметаллом и силоксановым соединением, получают с помощью следующих стадий:(а) сырьевой порошок цеолитного молекулярного сита, содержащий матричный агент, подвергают ионному обмену NH4+, затем прокаливают с получением кислотного цеолитного молекулярного сита;(b) указанное кислотное цеолитное молекулярное сито, полученное на стадии (а), импрегнируют раствором, содержащим одну растворимую соль, затем фильтруют, сушат и прокаливают с получением модифицированного металлом молекулярного сита;(с) указанное модифицированное металлом молекулярное сито, полученное на стадии (b), импрегнируют раствором, содержащим другую растворимую соль, затем фильтруют, сушат и прокаливают с получением модифицированного биметаллом молекулярного сита;(d) указанное модифицированное биметаллом молекулярное сито, полученное на стадии (с), модифицируют путем импрегнирования силоксановым соединением, регулируя кислотность и структуру пор наружной поверхности с получением указанного катализатора, совместно модифицированного биметаллом и силоксановым соединением; и(e) указанный катализатор, совместно модифицированный биметаллом и силоксановым соединением, полученный на стадии (d), формуют с помощью технологии прессования или распылительной сушки. Указанный биметалл представляет собой цинк и галлий. В настоящей заявке способ модификации с использованием силоксанового соединения также известен как модификация путем силанизации. Стадию (1) можно пропустить, когда цеолитное молекулярное сито представляет собой молекулярное сито Н-цеолита. И модификацию путем силанизации можно осуществлять до выполнения модификации биметаллом. В котором указанное силоксановое соединение имеет структурную формулу в виде формулы I(формула I) где R1, R2, R3 и R4 независимо выбирают из алкильной группы C1-С 10. В котором указанная алкильная группа C1-С 10 содержит метил, этил, н-пропил, изопропил, н-бутил,изобутил, третичный бутил, пентил, гексил, гептил, нонил и децил. Указанная алкильная группа содержит все изомеры, когда изомеры имеются. Например, пропильная группа содержит н-пропил и изопропил, а бутил содержит н-бутил, изобутил и третичный бутил. В предпочтительном варианте осуществления указанное силоксановое соединение представляет со-3 024296 бой жидкость при комнатной температуре. Если указанное силоксановое соединение в твердом состоянии при комнатной температуре, его следует нагреть до состояния жидкости перед использованием для импрегнирования. В указанном катализаторе, модифицированном биметаллом и силоксановым соединением, объем загрузки каждого металла составляет 0,5-8 мас.% от общей массы указанного катализатора; а объем загрузки указанного силоксанового соединения на основе окиси кремния составляет 0,5-10 мас.% от общей массы указанного катализатора. В предпочтительном варианте осуществления молекулярное сито, используемое в указанном катализаторе, представляет собой молекулярное сито цеолита HZSM-5 и/или HZSM-11. В еще одном предпочтительном варианте осуществления молекулярное сито, используемое в указанном катализаторе,представляет собой молекулярное сито цеолита HZSM-5. В предпочтительном варианте осуществления указанное силоксановое соединение представляет собой тетраэтоксисилан (каждый из элементов R1, R2,R3 и R4 является этилом). В настоящей заявке в качестве сырьевого материала используется смесь метанола и/или диметилового эфира и сжиженного газа С 4, в которой указанный метанол - это чистый метанол или водный раствор метанола, а массовая процентная концентрация метанола в водном растворе составляет 50-100%. Указанный сырьевой материал может смешиваться с метанолом и/или диметиловым эфиром и сжиженным газом С 4 в любой пропорции. Хотя метанол, диметиловый эфир или сжиженный газ С 4 могут использоваться независимо друг от друга в качестве сырьевого материала, более высокий выход ароматических углеводородов достигается, когда сырьевой материал представляет собой смесь метанола и/или диметилового эфира и сжиженного газа С 4. В предпочтительном варианте осуществления массовое соотношение метанола и/или диметилового эфира к сжиженному газу С 4 в сырьевом материале составляет(10-90):(90-10). В еще одном предпочтительном варианте осуществления массовое соотношение метанола и/или диметилового эфира к сжиженному газу С 4 в сырьевом материале составляет (30-70):(70-30). В настоящей заявке способ получения параксилола путем совместной конверсии метанола и/или диметилового эфира и сжиженного газа С 4 выполняется в реакторе с неподвижным слоем или с псевдоожиженным слоем. Реакция осуществляется при температуре 350-550 С, предпочтительно при температуре 400-500 С. Реакция осуществляется при давлении от атмосферного давления до 5 МПа, предпочтительно при давлении от атмосферного давления до 2 МПа. Реакция осуществляется при среднечасовой скорости подачи указанной газовой смеси от 0,1 до 20 ч-1, предпочтительно при среднечасовой скорости подачи указанной газовой смеси от 1 до 10 ч-1. Подробное описание варианта осуществления Настоящая заявка подробно описана со ссылкой на следующие примеры, но не ограничивается этими примерами. В следующих примерах все реагенты и сырьевые материалы приобретены путем коммерческой покупки, и мас.% означает процентное отношение по массе, если не указано иначе. В настоящей заявке, в частности, все процентные отношения и объемы основаны на массе, если не указано иначе. Пример 1. Получение катализатора, используемого в неподвижном слое 1) 500 г сырьевого порошка, содержащего матричный агент внутри молекулярного сита цеолитаZSM-5 (производства Катализаторного завода при Нанькайском университете, мольное отношениеSiO2/Al2O3=50), прокалили при 550 С для удаления матричного агента, а затем подвергли ионному обмену четыре раза раствором нитрата аммония 0,5 моль/л при температуре водяного термостата 80 С, а затем высушили в воздухе при 120 С и после этого прокалили при 550 С в течение 3 ч. После этого получили молекулярное сито цеолита HZSM-5. 2) 20 г молекулярного сита цеолита HZSM-5, полученного на стадии 1), импрегнировали раствором нитрата цинка [Zn(NO3)2] с массовой процентной концентрацией 5% при комнатной температуре в течение 4 ч, а затем высушили при 120 С после декантирования надосадочной жидкости и после этого прокалили в воздухе при 550 С в течение 6 ч с получением модифицированного цинком молекулярного сита цеолита HZSM-5. 3) Модифицированное цинком молекулярное сито цеолита HZSM-5, полученное на стадии 2), импрегнировали раствором нитрата галлия [Ga(NO3)2] с массовой процентной концентрацией 8% при комнатной температуре в течение 4 ч а затем высушили при 120 С после декантирования надосадочной жидкости и после этого прокалили в воздухе при 550 С в течение 6 ч с получением модифицированного галлием и цинком молекулярного сита цеолита HZSM-5. 4) Модифицированное галлием и цинком молекулярное сито цеолита HZSM-5, полученное на стадии 3), импрегнировали тетраэтоксисиланом (TEOS) при комнатной температуре в течение 24 ч, а затем высушили при 120 С после декантирования надосадочной жидкости и после этого прокалили в воздухе при 550 С в течение 6 ч с получением молекулярного сита цеолита HZSM-5, совместно модифицированного галлием и цинком и силоксановым соединением, которое получило название СРХ-01. Пример 2. Получение катализатора, используемого в неподвижном слое 1) 20 г молекулярного сита цеолита HZSM-5, полученного на стадии 1) примера 1, импрегнировали раствором нитрата галлия [Ga(NO3)2] с массовой процентной концентрацией 10% при комнатной темпе-4 024296 ратуре в течение 4 ч, а затем высушили при 120 С после декантирования надосадочной жидкости и после этого прокалили в воздухе при 550 С в течение 6 ч с получением молекулярного сита цеолита HZSM-5,модифицированного галлием. 2) Модифицированное галлием молекулярное сито цеолита HZSM-5, полученное на стадии 1), импрегнировали раствором нитрата цинка [Zn(NO3)2] с массовой процентной концентрацией 8% при комнатной температуре в течение 4 ч, а затем высушили при 120 С после декантирования надосадочной жидкости и после этого прокалили в воздухе при 550 С в течение 6 ч с получением модифицированного галлием и цинком молекулярного сита цеолита HZSM-5. 3) Модифицированное галлием и цинком молекулярное сито цеолита HZSM-5, полученное на стадии 2), импрегнировали тетраэтоксисиланом (TEOS) при комнатной температуре в течение 24 ч, а затем высушили при 120 С после декантирования надосадочной жидкости и после этого прокалили в воздухе при 550 С в течение 6 ч с получением молекулярного сита цеолита HZSM-5, совместно модифицированного галлием и цинком и силоксановым соединением, которое получило название СРХ-02. Пример 3. Получение катализатора, используемого в псевдоожиженном слое 1) 200 г молекулярного сита цеолита HZSM-5, полученного на стадии 1) примера 1, импрегнировали раствором нитрата цинка [Zn(NO3)2] с массовой процентной концентрацией 10% при комнатной температуре в течение 4 ч, а затем высушили при 120 С после декантирования надосадочной жидкости и после этого прокалили в воздухе при 550 С в течение 6 ч с получением модифицированного цинком молекулярного сита цеолита HZSM-5. 2) Модифицированное цинком молекулярное сито цеолита HZSM-5, полученное на стадии 1), импрегнировали раствором нитрата галлия [Ga(NO3)2] с массовой процентной концентрацией 15% при комнатной температуре в течение 4 ч, а затем высушили при 120 С после декантирования надосадочной жидкости и после этого прокалили в воздухе при 550 С в течение 6 ч с получением модифицированного биметаллом из галлия и цинка молекулярного сита цеолита HZSM-5. 3) Модифицированное галлием и цинком молекулярное сито цеолита HZSM-5, полученное на стадии 2), импрегнировали тетраэтоксисиланом (TEOS) при комнатной температуре в течение 24 ч, а затем высушили при 120 С после декантирования надосадочной жидкости и после этого прокалили в воздухе при 550 С в течение 6 ч с получением молекулярного сита цеолита HZSM-5, совместно модифицированного биметаллом из галлия и цинка и силоксановым соединением. 4) Молекулярное сито цеолита HZSM-5, совместно модифицированное биметаллом из галлия и цинка и силоксановым соединением, полученное на стадии 3), смешали с каолином, золем кремнистой кислоты, золем оксида алюминия и деионизированной водой до состояния суспензии. Массовое соотношение цеолитного молекулярного сита:каолин:сухая масса золя кремнистой кислоты:сухая масса золя оксида алюминия составила 30:32:26:12. Содержание твердого вещества в суспензии составило около 35 мас.%. Затем суспензию выдержали при комнатной температуре в течение 5 ч, а затем сформовали путем распылительной сушки после измельчения коллоидной мельницей до получения микросфер катализатора с размером частиц 20-100 M. Элементный анализ показал, что в расчете на общую массу катализатора катализатор содержал 2,3 мас.% цинка, 3,1 мас.% галлия и 5,3 мас.% силоксанового соединения, при рассчете по окиси кремния. Катализатор получил название СРХ-03. Пример 4. Оценка катализатора в реакторе с неподвижным слоем В качестве катализаторов в реакции использовали СРХ-01 из примера 1 и СРХ-02 из примера 2. 5 г катализатора загрузили в реактор с неподвижным слоем, а затем обработали в воздухе при 550 С в течение 1 часа с последующим охлаждением в азоте до достижения температуры реакции 450 С, 0,15 МПа. Метанол и сжиженный газ С 4 закачали в испаритель, примешали к сырьевым материалам при температуре 200 С, а затем провели контактирование с катализатором в реакторе. Сырьевые материалы с метанолом и сжиженным газом С 4 в соотношении 50:50 ввели в реактор с общей среднечасовой скоростью подачи 2 ч-1. Распределение сырьевого материала и безводных продуктов показано в табл. 1. На катализаторе СРХ-01 и катализаторе СРХ-02 выход ароматических углеводородов в безводных продуктах составил 71,31 и 73,03 мас.%, а содержание параксилола в ароматических углеводородах составило 87,17 и 86,67 мас.%, селективность параксилола в изомерах ксилола составила 99,41 и 99,32 мас.% соответственно. Таблица 1. Распределение сырьевых материалов и безводных продуктов С 5+: углеводороды с углеродным числом не менее пяти; С 9+: углеводороды с углеродным числом не менее девяти. Пример 5. Оценка катализатора в неподвижном слое В качестве катализаторов в реакции использовали СРХ-01 из примера 1 и СРХ-02 из примера 2. 5 г катализатора загрузили в реактор с неподвижным слоем, а затем обработали в воздухе при 550 С в течение 1 ч с последующим охлаждением в азоте до достижения температуры реакции 450 С, 0,1 МПа. Метанол и сжиженный газ С 4 закачали в испаритель, примешали к сырьевым материалам при температуре 200 С, а затем провели контактирование с катализатором в реакторе. Сырьевые материалы с метанолом и сжиженным газом С 4 в соотношении 30:70 ввели в реактор с общей среднечасовой скоростью подачи 2 ч-1. Распределение сырьевого материала и безводных продуктов показано в табл. 2. На катализаторе СРХ-01 и катализаторе СРХ-02 выход ароматических углеводородов в безводных продуктах составил 75,21 и 79,01 мас.%, содержание параксилола в ароматических углеводородах составило 85,88 и 85,74 мас.%, а селективность параксилола в изомерах ксилола составила 99,21 и 99,19 мас.% соответственно. Таблица 2. Распределение сырьевых материалов и продуктов С 5+: углеводороды с углеродным числом не менее пяти; С 9+: углеводороды с углеродным числом не менее девяти. Пример 6. Оценка катализатора в псевдоожиженном слое В качестве катализаторов в реакции использовали СРХ-03 из примера 3. 10 г катализатора загрузили в реактор с псевдоожиженным слоем, а затем обработали в воздухе при 550 С в течение 1 ч с последующим охлаждением в азоте до достижения температуры реакции 450 С, 0,1 МПа. Метанол и сжиженный газ С 4 закачали в испаритель, примешали к сырьевым материалам при температуре 200 С, а затем провели контактирование с катализатором в реакторе. Два сырьевых материала с метанолом и сжиженным газом С 4 в соотношении 50:50 и 30:70 ввели в реактор с общей среднечасовой скоростью подачи 2 ч 1 соответственно. Распределение сырьевых материалов и безводных продуктов показано в табл. 2. Выход ароматических углеводородов в безводных продуктах составил 70,12 и 72,87 мас.%, содержание параксилола в ароматических углеводородах составило 84,47 и 85,21 мас.%, а селективность параксилола в изомерах ксилола составила 99,04 и 99,08 мас.% соответственно. Таблица 3. Распределение сырьевых материалов и продуктов С 5+: углеводороды с углеродным числом не менее пяти; С 9+: углеводороды с углеродным числом не менее девяти. ФОРМУЛА ИЗОБРЕТЕНИЯ 1. Катализатор для получения параксилола путем совместной конверсии метанола и/или диметилового эфира и сжиженного газа С 4, отличающийся тем, что указанный катализатор представляет собой ароматизирующий катализатор с молекулярным ситом с конфигурационно-селективной функцией, совместно модифицированный биметаллом и силоксановым соединением, где биметаллом является цинк и галлий, а силоксановое соединение имеет структурную формулу I где R1, R2, R3 и R4 независимо выбирают из алкильной группы C1-С 10. 2. Катализатор по п.1, отличающийся тем, что указанное силоксановое соединение представляет собой тетраэтоксисилан. 3. Катализатор по п.1, отличающийся тем, что молекулярное сито в указанном ароматизирующем катализаторе с конфигурационно-селективной функцией представляет собой молекулярное сито цеолитаHZSM-5 и/или HZSM-11. 4. Катализатор по п.1, отличающийся тем, что объем загрузки цинка составляет 0,5-8 мас.% от общей массы катализатора; объем загрузки галлия составляет 0,5-8 мас.% от общей массы катализатора и объем загрузки силоксанового соединения составляет 0,5-10 мас.% от общей массы катализатора. 5. Способ получения любого из указанных катализаторов по п.1-4, включающий следующие стадии:(a) молекулярное сито импрегнируют раствором, содержащим по меньшей мере одну растворимую соль одного из элементов - цинка и галлия, затем фильтруют, сушат и прокаливают с получением модифицированного металлом молекулярного сита;(b) указанное модифицированное металлом молекулярное сито, полученное на стадии (а), импрегнируют раствором, содержащим по меньшей мере одну растворимую соль другого из элементов - цинка и галлия, затем фильтруют, сушат и прокаливают с получением модифицированного биметаллом молекулярного сита;(с) указанное модифицированное биметаллом молекулярное сито, полученное на стадии (b), импрегнируют силоксановым соединением, затем фильтруют, сушат и прокаливают с получением указанного ароматизирующего катализатора с молекулярным ситом, совместно модифицированного биметаллом и силоксановым соединением. 6. Способ получения параксилола путем совместной конверсии метанола и/или диметилового эфира и сжиженного газа С 4, включающий следующие стадии: газовую смесь, содержащую метанол и/или диметиловый эфир и сжиженный газ С 4, пропускают через реактор для получения параксилола с помощью реакции ароматизации; отличающийся тем, что в указанный реактор загружают любой из указанных катализаторов по пп.14; отличающийся тем, что указанная реакция ароматизации выполняется при температуре 350-550 С,давлении от атмосферного давления до 5 МПа и среднечасовой скорости подачи указанной газовой смеси от 0,1 до 20 ч-1. 7. Способ по п.6, отличающийся тем, что выполняется в реакторе с неподвижным слоем или с псевдоожиженным слоем.
МПК / Метки
МПК: B01J 29/04, B01J 29/00, B01J 29/40
Метки: параксилола, катализатор, метанола, путем, продукта, получения, эфира, сжиженного, приготовления, способ, этого, совместной, диметилового, конверсии, использования, газа
Код ссылки
<a href="https://eas.patents.su/9-24296-katalizator-dlya-polucheniya-paraksilola-putem-sovmestnojj-konversii-metanola-i-ili-dimetilovogo-efira-i-szhizhennogo-gaza-c4-sposob-prigotovleniya-etogo-produkta-i-sposob-ego-ispo.html" rel="bookmark" title="База патентов Евразийского Союза">Катализатор для получения параксилола путем совместной конверсии метанола и/или диметилового эфира и сжиженного газа c4, способ приготовления этого продукта и способ его использования</a>
Предыдущий патент: N-[4-(1h-пиразоло[3,4-b]пиразин-6-ил)фенил]сульфонамиды и их применение в качестве лекарственных средств
Следующий патент: 2′,4′-дифтор-2′-метилзамещенные нуклеозидные производные в качестве ингибиторов репликации рнк вируса гепатита с
Случайный патент: Синергические гербицидные средства, которые хорошо переносятся культурными растениями и содержат гербициды из группы бензоилпиразолов