Способ получения равномерно кристаллизованных гранулятов из поликонденсата
Номер патента: 16775
Опубликовано: 30.07.2012
Авторы: Локер Петер, Эусебио Фернандо, Кристель Андреас, Кулберт Брент Аллан
Формула / Реферат
1. Способ непрерывного получения частично кристаллического гранулята из поликонденсата, включающий в себя следующие стадии:
получение расплава поликонденсата,
формование гранул из поликонденсата и отверждение расплава поликонденсата в жидкой охлаждающей среде, при этом формование гранул может проводиться до или после отверждения,
отделение гранул от жидкой охлаждающей среды после их охлаждения до средней температуры, лежащей в диапазоне температур кристаллизации,
кристаллизация гранул в камере обработки (12),
при этом в камере обработки обрабатывающий газ движется противоточно гранулам из поликонденсата,
отличающийся тем, что скорость потока обрабатывающего газа поддерживают выше точки псевдоожижения гранулята из поликонденсата и что минимальное время выдержки по меньшей мере 95% гранулята из поликонденсата в камере обработки (12) составляет более 20% от среднего времени выдержки.
2. Способ по п.1, отличающийся тем, что обрабатывающий газ подают при температуре, которая превышает среднюю температуру гранул из поликонденсата на входе в камеру обработки (12).
3. Способ по п.1 или 2, отличающийся тем, что жидкая охлаждающая среда, по меньшей мере, частично циркулирует в контуре и нагревается.
4. Способ по любому из предыдущих пунктов, отличающийся тем, что в качестве поликонденсата используют полиамид, поликарбонат, полигидроксиалканоат, полилактид или сложный полиэфир и их сополимеры и/или их смеси.
5. Способ по п.4, отличающийся тем, что в качестве сложного полиэфира используют полиэтилентерефталат, полибутилентерефталат или полиэтиленнафталат.
6. Способ по любому из предыдущих пунктов, отличающийся тем, что скорость оседания гранул из поликонденсата в камере обработки (12) составляет более 0,05 м/мин.
7. Способ по любому из предыдущих пунктов, отличающийся тем, что скорость оседания гранул из поликонденсата в камере обработки (12) составляет более 0,15 м/мин.
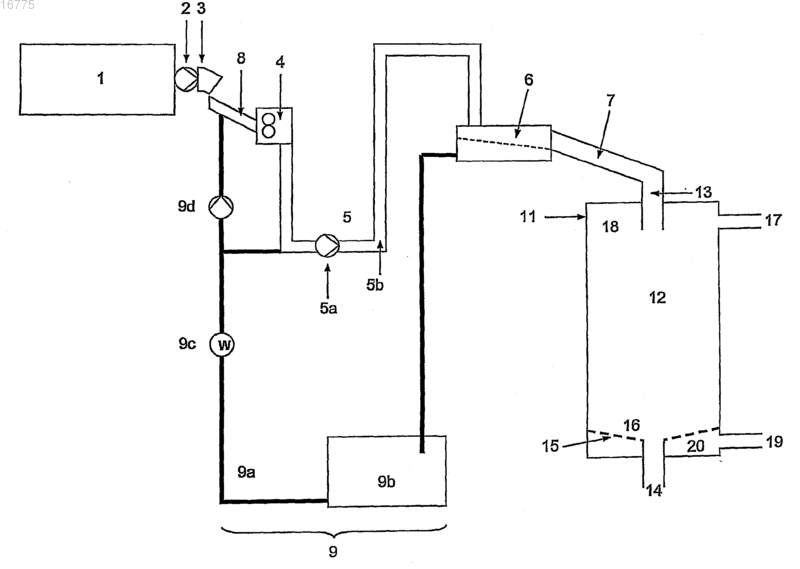
Текст
СПОСОБ ПОЛУЧЕНИЯ РАВНОМЕРНО КРИСТАЛЛИЗОВАННЫХ ГРАНУЛЯТОВ ИЗ ПОЛИКОНДЕНСАТА Изобретение относится к способу непрерывного получения частично кристаллического гранулята из поликонденсата, включающему в себя следующие стадии: получение расплава поликонденсата,формование гранул из поликонденсата и отверждение расплава поликонденсата в жидкой охлаждающей среде, при этом формование гранул может проводиться до или после отверждения,отделение гранул от жидкой охлаждающей среды после их охлаждения до средней температуры,лежащей в диапазоне температур кристаллизации поликонденсата, и кристаллизация гранул в камере обработки, причм в камере обработки обрабатывающий газ движется противоточно гранулам из поликонденсата, скорость потока обрабатывающего газа превышает точку псевдоожижения гранулята из поликонденсата, и гранулы из поликонденсата характеризуются узким диапазоном времени выдержки в камере обработки. 016775 Область техники, к которой относится изобретение Изобретение относится к способу непрерывного получения частично кристаллизованного гранулята из поликонденсата согласно ограничительной части п.1 формулы изобретения. Сведения о предшествующем уровне техники Из уровня техники известны способы получения частично кристаллических гранулятов из расплавленных кристаллизуемых поликонденсатов путм охлаждения, резки и термообработки. Обычно поликонденсат охлаждают до температуры ниже температуры стеклования и снова нагревают с целью кристаллизации. В качестве альтернативы охлаждение может проводиться и до соответствующей температуры кристаллизации, в результате чего возможно обеспечить последующую кристаллизацию без необходимости подвода тепла извне (DE 10349016, Bruckmann; DE 102004015515, Otto и др.). Однако этим способам присущ недостаток, проявляющийся в том, что они не способны обеспечить соблюдение требований, предъявляемых к обеспечению гибкорегулируемого и одинакового качества продукта на выходе в отношении температуры и степени кристаллизации. Также недостатком является частое образование агломератов на начальном участке зоны кристаллизации, которые не всегда распадаются. Более эффективный контроль за температурой достигается в том случае, когда кристаллизация вс ещ горячих гранул проводится при дополнительной подаче горячего обрабатывающего газа в кипящий слой, как это описано в US 3544525 (Balint и др.) или WO 01/12698 (Borer и др.). Однако контроль и равномерность кристаллизации остаются по-прежнему не удовлетворительными. В источнике WO 01/12698 (Borer и др.) предложено использовать также комбинацию из фонтанирующего и кипящего слов, благодаря чему достигается более эффективный контроль и равномерность кристаллизации. Однако в этом случае присутствует недостаток, при котором приходится применять в больших количествах обрабатывающий газ для обеспечения завихрения гранул из поликонденсата на протяжнном участке обработки. Сущность изобретения Задачей настоящего изобретения является создание способа, с помощью которого могут быть получены просто и энергетически эффективно равномерно кристаллизованные гранулы из поликонденсата с контролируемой температурой и без образования агломерата. Эта задача решается посредством п.1 формулы изобретения, согласно которому получают расплав поликонденсата, из которого в жидкой охлаждающей среде формируют гранулы и охлаждают их, после чего гранулы подают в жидкой охлаждающей среде в разделительное устройство и отделяют от жидкой охлаждающей среды. После этого гранулы обрабатывают в кристаллизационном устройстве при соблюдении узкого диапазона времени выдержки в противотоке обрабатывающего газа, проходящего через гранулы со скоростью свыше скорости их псевдоожижения. Согласно предпочтительному варианту осуществления температура обрабатывающего газа превышает среднюю температуру гранулята, благодаря чему достигается преимущество, при котором гранулы из поликонденсата обладают на выходе постоянной заданной температурой. Пригодными к применению поликонденсатами являются кристаллизуемые термопластичные поликонденсаты, как, например, полиамиды, сложные полиэфиры, поликарбонаты, полигидроксиалканоаты,полилактиды или их сополимеры, образуемые реакцией поликонденсации при отщеплении низкомолекулярного продукта реакции. При этом поликонденсация может протекать либо непосредственно между мономерами, либо через промежуточную стадию, переходящую затем в переэтерификацию, причм переэтерификация может также сопровождаться отщеплением низкомолекулярного продукта реакции или же полимеризацией с раскрытием кольца. Полученный при этом поликонденсат является, по существу,линейным, причм в данном случае может образоваться незначительное количество ответвлений. Полиамид представляет собой полимер, получаемый поликонденсацией из его мономеров либо из компонентов - диамина и дикарбоновой кислоты, либо из бифункционального мономера с концевой аминогруппой или кислотной карбоксильной группой. Сложным полиэфиром служит при этом полимер, получаемый поликонденсацией из его мономеров, из компонентов - диола и дикарбоновой кислоты. Применяются разные, в большинстве свом линейные или циклические диолы. Также могут применяться разные, в большинстве свом ароматические дикарбоновые кислоты. Вместо дикарбоновой кислоты может также применяться е соответствующий диметиловый сложный эфир. Типичными примерами сложных полиэфиров могут служить полиэтилентерефталат, полибутилентерефталат и полиэтиленнафталат, которые используются в качестве либо гомополимеров, либо сополимеров. Политерефталат получают из его мономеров, из компонентов - диола и дикарбоновой кислоты, при этом диол в качестве основного мономера состоит из этиленгликоля (1,2-этандиола), а дикарбоновая кислота в качестве основного мономера - из терефталевой кислоты. В качестве сомономеров применяются дополнительные линейные, циклические или ароматические соединения диола и дикарбоновой кислоты. Типичными сомономерами являются диэтиленгликоль, изофталевая кислота или 1,4-бис-гидроксиметилциклогексан. Полигидроксиалканоаты представляют собой полимеры, образуемые поликонденсацией из их мо-1 016775 номеров общей формулы HO-CH(R)-(CH2)n-COOH, при этом R означает обычно алифатический углеводород с 1-15 атомами углерода, n = 1-10, обычно 1-3. Типичным примером служит полигидроксибутират,в котором R = СН 3 и n = 1. Полилактиды (известные как полимеры молочной кислоты) представляют собой полимеры, которые могут быть непосредственно получены из молочной кислоты отщеплением воды или же поликонденсаций с раскрытием кольца из их циклических димеров (лактидов). Поликонденсат может представлять собой новый или же повторно используемый материал. В качестве повторно используемых материалов имеются в виду полимеры, повторно извлечнные во время процессов изготовления и обработки(постпромышленные), или же полимеры, собранные и повторно обработанные (постбытовые). В полимеры могут вводиться добавки. В качестве последних пригодны, например, катализаторы,красители и пигменты, ультрафиолетовые защитные средства, вспомогательные вещества для обработки,стабилизаторы, модификаторы ударной вязкости, вспениватели химического или физического происхождения, наполнители, средства облучения, противовоспламенители, пластификаторы, улучшающие барьерные или механические свойства частицы, армирующие тела, такие как шарики или волокна, реактивные вещества, как, например, поглотители кислорода, поглотители ацетальдегида или вещества, увеличивающие молекулярный вес, и пр. Приготовление расплава полимера проводится с применением известных из уровня техники аппаратов и реакторов. В принципе могут применяться реакторы для полимеризации, в которых полимеры приготавливаются в виде жидкой фазы, как, например, котлы с мешалкой, клеточные реакторы или дисковые реакторы, или же аппаратура, в которой предварительно приготовленные полимеры подвергаются плавлению, например экструдеры или пластикаторы. Приготовление полимера может проводиться непрерывно или периодически. Однако при последующей обработке предпочтительно применять непрерывные процессы. В выпускном устройстве, в частности в сопле или сопловой пластине, из расплава поликонденсата формируются отдельные поликонденсатные жгуты. Для получения гранулятов из поликонденсатных жгутов могут применяться известные в уровне техники примы грануляции, такие как непрерывная грануляция, водокольцевая грануляция, подводная грануляция или головная грануляция. При этом выходящие из подводящих расплав каналов поликонденсатные жгуты отверждаются и разделяются на множество отдельных гранул, причм разделение может происходить до или после отверждения. Несмотря на использование понятия вода при обозначении гранулирующих устройств могут также применяться и другие виды жидких сред. Разделение происходит, например, в результате самостоятельного каплеобразования, применения жидкого средства для сдвига или путм механического отделения, в частности резанием. Если самостоятельное или вызванное средой для сдвига каплеобразование происходит на выходе из сопла, то резание может проводиться как непосредственно на выходе из сопла, так и после прохождения некоторого обрабатывающего участка. Отверждение расплава поликонденсата достигается охлаждением посредством одной или нескольких охлаждающих жидкостей, причм речь может идти о газообразных(например, воздух, азот, СО 2) или жидких (например, вода или этиленгликоль) охлаждающих средах или же об их комбинации. Согласно изобретению применяется по меньшей мере одна охлаждающая среда. Поликонденсат, в частности, в виде поликонденсатных жгутов или каплей, до поступления в жидкую охлаждающую среду, может, например, перемещаться по участку, содержащему обрабатывающий газ, в частности воздух или водяной туман. Средний размер гранул должен составлять от 0,1 до 10 мм, предпочтительно от 0,5 до 3 мм, в частности от 0,85 до 2,5 мм. Гранулы должны иметь предпочтительно определнную форму, например цилиндрическую, шаровую, капельную, шарообразную, или же форму, предложенную, например, в ЕР 0541674 (Yau). Охлаждение гранул из поликонденсата может проводиться до средней температуры, лежащей ниже диапазона температур кристаллизации поликонденсата. Однако предпочтительно охлаждение гранул из поликонденсата проводится до средней температуры, лежащей в диапазоне температур кристаллизации поликонденсата. Для этого можно поднять температуру охлаждающей среды и/или соответственно сократить время выдержки в ней. Одновременно с охлаждением гранулы из поликонденсата могут подаваться на последующую технологическую операцию. Необходимый диапазон температур кристаллизации становится наглядным, если полупериод кристаллизации (t1/2) записать в виде температурной функции. Этот диапазон ограничивается вверх и вниз температурой, при которой полупериод кристаллизации достигает величины, превышающей приблизительно в десять раз минимальный полупериод кристаллизации. Поскольку очень короткие полупериоды кристаллизации (t1/2) определяемы лишь с большим трудом, то пользуются минимальным значением t1/2 = 1 мин. Для полиэтилентерефталата температурный диапазон составляет от 110 до 220 С. При этом полупериод кристаллизации определяют изотермической кристаллизацией с помощью дифференциальной сканирующей калориметрии, причм полупериод кристаллизации t1/2 соответствует времени, которое необходимо при данной температуре по истечении времени индукции для достижения 50% возможной кристалличности.-2 016775 После охлаждения охлаждающую среду отделяют от гранул. При необходимости может проводиться дополнительная обработка (кондиционирование) гранул в жидкой среде, для чего может применяться непосредственно охлаждающая среда или какая-либо другая жидкость. Отделение гранул от жидкой охлаждающей среды производится с помощью известных из уровня техники разделительных устройств. При этом могут применяться лишь пассивные разделительные устройства, как, например, сита или рештки, через которые может проходить охлаждающая среда, но не могут проходить гранулы. Однако обычно используют активные разделительные устройства, по меньшей мере, для частичного разделения, при этом разделение происходит, например, под действием пропускания газа, центробежной силы или соударений. Такие устройства известны, например, в виде отсасывающих устройств, отражательных или центробежных сушилок. Также частичное разделение может производиться с помощью ненасыщенного, при желании подогретого газового потока путм испарения охлаждающей среды. После отделения поликонденсатных гранул от жидкой охлаждающей среды последние могут непосредственно подаваться в последующую камеру обработки на кристаллизацию. Однако, при необходимости, поликонденсатные гранулы могут также направляться по транспортному участку, причм между отдельными гранулами должно обеспечиваться постоянное относительное движение. Это относительное движение достигается, например, большой скоростью течения по трубопроводу (свыше 0,3 м/мин, в частности свыше 1 м/мин), омыванием транспортирующим газом, механическим движением, сообщаемым,например, мешалкой или транспортирующим шнеком, или созданием колебаний или вибрации. Согласно изобретению гранулы из поликонденсата поступают в камеру обработки для кристаллизации, по существу, сверху вниз, в то время как сама камера омывается обрабатывающим газом снизу вверх. При этом обрабатывающий газ имеет скорость движения в пустой трубе, которая превышает точку псвевдоожижения гранул из поликонденсата в камере обработки. Гранулы из поликонденсата перемещаются через камеру обработки при узком диапазоне времени выдержки. Для обеспечения узкого диапазона времени выдержки в данных условиях необходимо исключить,по меньшей мере, на отдельных участках камеры обработки интенсивное завихрение. Это достигается в результате того, что в камере обработки предупреждается образование пузырей за счт применения слов из подпорных элементов, как это предложено делать в заявке фирмы Bler AG на Устройство и способ термической обработки сыпучих материалов (дата подачи 8.12.2006), или же в результате того, что при одновременно высокой скорости оседания гранул из поликонденсата скорость обрабатывающего газа задатся лишь незначительно превышающей точку псевдоожижения этих гранул. Камера обработки для проведения кристаллизации охвачена корпусом. Горизонтальное сечение камеры обработки может иметь любую форму, однако предпочтительно оно является круглым или прямоугольным. Камера обработки расположена, по существу, вертикально, вследствие чего гранулят может перемещаться в устройстве сверху вниз. Важно при этом, чтобы обеспечивался равномерный поток продукта. Камера обработки ограничена с боков оболочкой. Оболочковая стенка может состоять при этом из цилиндрических, конических сегментов или из комбинации этих сегментов, что позволяет воздействовать на распределение скорости газа по высоте устройства. Расширение в зоне потолка позволяет уменьшить скорость газа, что исключает унос гранул. Сужение в зоне потолка позволяет повысить скорость газа, что способствует более интенсивному завихрению, благодаря чему предупреждается возможное слипание. Отдельным вариантом осуществления предусмотрена, по меньшей мере, приблизительно вращательно-симметричная оболочка корпуса, гарантирующая технологические преимущества, а также преимущества, обеспечивающие равномерность потока продукта. Внутри камеры обработки может располагаться вытеснительное тело, через которое гранулы не перемещаются, и, следовательно, оно уменьшает размер камеры обработки. Такие вытеснительные тела могут применяться, например, для ввода обрабатывающего газа, адаптации свободной поверхности поперечного сечения или для улучшения потока гранул. По меньшей мере одно загрузочное отверстие выполнено в зоне потолка камеры обработки, которое позволяет вводить обрабатываемый гранулят в эту камеру. Загрузочное отверстие может представлять собой, например, отверстие в корпусе или выходное отверстие трубы, заведнной в корпус. Загрузочное отверстие может быть разделено на несколько сегментов, что позволяет распределять гранулы внутри камеры обработки. По меньшей мере одно разгрузочное отверстие выполнено в нижней части камеры обработки, через которое может выпускаться обработанный гранулят из этой камеры. В качестве разгрузочного отверстия может служить, например, отверстие в корпусе или входное отверстие трубы, выведенной наружу из корпуса. Обычно гранулят податся через конический участок разгрузочного отверстия. Угол выпускного конуса к горизонту составляет предпочтительно 50-80 в том случае, когда гранулят в выпускном конусе не подвержен ожижению или вибрации, и 15-60, в частности 30-50, в том случае, когда гранулят в выпускном конусе ожижается или подвержен вибрации.-3 016775 В качестве альтернативы гранулят может подаваться в разгрузочное отверстие с помощью механического разгрузочного устройства, такого, например, как шнек. Под разгрузочным отверстием может располагаться запорный элемент, например шлюзовый затвор, горизонтально расположенный разгрузочный валок или автоматическая задвижка, с помощью которой регулируется подача гранулята из камеры обработки. В качестве регулирующего параметра может выступать при этом, например, уровень заполнения камеры обработки гранулятом или же вес гранул в устройстве. В донной части камеры обработки расположено по меньшей мере одно устройство для подачи обрабатывающего газа. Это подающее устройство содержит по меньшей мере одно входное отверстие, через которое обрабатывающий газ устремляется внутрь камеры обработки. Устройство для подачи обрабатывающего газа может содержать приспособления, такие, например,как открытые снизу конусы или ряды крышеобразных элементов, а также трубопроводы или металлические листы с выпускными отверстиями, если требуется достаточно равномерное распределение обрабатывающего газа. Отдельным вариантом осуществления предусмотрено, чтобы камера обработки ограничивалась вниз, по крайней мере, частично проницаемым для газа запорным устройством, в частности металлическим листом с множеством впускных отверстий, через которые может проходить, по крайней мере, на отдельных участках обрабатывающий газ и не могут проходить гранулы. Для этого отверстия выполнены с диаметром, который меньше диаметра гранул. Поверхность пропускания составляет предпочтительно от 1 до 30%. Предпочтительными являются отверстия, составляющие 20-90%, в частности 30-80% от диаметра гранул. Количество, размер и расположение отверстий могут быть выбраны ровными или не ровными. Запорное устройство расположено горизонтально или в виде конуса. Под запорным устройством может располагаться распределительная камера, по которой обрабатывающий газ поступает в запорное устройство. В этой распределительной камере выполнено по меньшей мере одно отверстие для подачи обрабатывающего газа. Кроме того, могут быть расположены приспособления для распределения обрабатывающего газа, такие как подпорные металлические листы, клапаны или задвижки, а также раздельные каналы для отдельной подачи обрабатывающего газа. В качестве альтернативы камера обработки может быть ограничена книзу газонепроницаемым запорным устройством. В этом случае, по меньшей мере, в качестве одного устройства для подачи обрабатывающего газа может применяться отверстие в корпусе, выходное отверстие одной или нескольких труб, заведнных в корпус, или же крышеобразный элемент или серия этих элементов, которые либо снабжены отверстиями, либо являются открытыми снизу. При этом возможно применение вытеснительного тела для подачи газа. Согласно отдельному варианту осуществления настоящего изобретения предусмотрено, чтобы дополнительно по меньшей мере к одному устройству для подачи обрабатывающего газа в донной части камеры обработки было выполнено по меньшей мере одно дополнительное устройство для подачи обрабатывающего газа, благодаря чему обеспечивался бы многоступенчатый подвод тепла, а также многоступенчатый профиль скорости газа. В зоне потолка камеры обработки располагается по меньшей мере одно устройство для отвода обрабатывающего газа. Это устройство может представлять собой, например, отверстие в корпусе или входное отверстие в трубе, выведенной наружу из корпуса. Отводящее устройство может располагаться в оболочке или потолке камеры обработки. В отводящем устройстве или под ним могут находиться устройства, которые пропускают обрабатывающий газ, но препятствуют прохождению гранул. Это может достигаться, например, с помощью изогнутого или разврнутого в противоположное направление проточного канала или зигзагообразного отделителя. Между отводящим устройством и устройством подачи обрабатывающего газа может располагаться замкнутый или частично замкнутый контур. Предпочтительно обрабатывающий газ поступает в камеру обработки при температуре, которая превышает среднюю температуру гранулята из поликонденсата на входе в камеру обработки. Для этого обрабатывающий газ, по меньшей мере, частично податся по контуру, причм соответственно подводится или отводится незначительное количество обменного газа. Внутри контура могут располагаться дополнительные устройства, как, например, устройства сжатия (например, вентиляторы, воздуходувки или компрессоры), теплообменники или очистительные устройства (например, фильтры, циклоны,скрубберы или каталитические сжигающие устройства). Поскольку значительная часть энергии сжатия в виде тепла переходит в газовый поток, то повышенная температура обработки может поддерживаться также при использовании меньшей дополнительной мощности нагревателя. Если же входная температура гранул из поликонденсата изменяется, то это может быть компенсировано дополнительной мощностью нагревателя. Большая скорость оседания гранул из поликонденсата в камере обработки препятствует образованию канала, по которому может проходить большое количество обрабатывающего газа через сыпучую массу гранулята при низком теплообмене между газом и гранулятом. Достаточными скоростями оседания являются скорости свыше 0,05 м/мин, в частности свыше 0,15 м/мин. Обычно скорость оседания должна составлять менее 5 м/мин, в частности менее 2 м/мин, так как в противном случае потребуется очень короткое время обработки или же очень большие камеры обработки.-4 016775 Достаточно узкий диапазон времени выдержки достигается в том случае, когда такой диапазон обладает начальной характеристикой, которая превосходит такую же характеристику каскада из трх или более, в частности из четырх или более, котлов с мешалками. При этом начальная характеристика описывает диапазон от нулевого момента времени до среднего времени выдержки. Этим гарантируется положение, при котором минимальное время выдержки, по меньшей мере 95%, в частности по меньшей мере 97% гранулята из поликонденсата в камере обработки составляет более 20% от среднего времени выдержки. Среднее время выдержки определяется расходом гранулята и объмом камеры обработки. Минимальное среднее время выдержки достигается в том случае, когда при проведении процесса образуется агломерат. Максимальное время выдержки зависит от максимально допустимой высоты камеры обработки, причм она определяется подачей обрабатывающего газа. Оптимальными являются средние показатели выдержки от 0,2 до 60 мин, при этом, например, для обработки полиэтилентерефталата с содержанием сомономера менее 6 мол.% достаточными являются средние показатели выдержки от 1 до 15 мин, в частности от 2 до 8 мин. Точкой псевдоожижения считается скорость потока, при которой сыпучая масса находится в наиболее рыхлом состоянии. Определение точки псевдоожижения путм измерения кривой потери давления описано в VDI Wrmeatlas (Тепловом атласе Общества немецких инженеров), 5-е изд., 1988, гл. Lf, рис. 4. Приблизительный расчт может быть заимствован из Wrme und Stoffbertragung in der Wirbelschicht"(Тепло и массопередача в кипящем слое), Н. Martin, Chem. Ing. Tech 52 (1980),3, стр. 199-209. Для определения пористости (Р) пользуются расчтом, применяемым для геометрии частиц, причм действительно для Р: (l/14/Os)(1/3) и Os: поверхность шара одинакового объма/поверхность частицы. Для частиц сыпучего материала, не имеющих форму шара, может применяться диаметр шара одинакового объма. В качестве альтернативы пористость может также рассчитываться по насыпному весу в точке псевдоожижения и плотности продукта: Р = 1 - плотность засыпки/плотность продукта. Если при обеих методиках расчта обнаруживаются существенные расхождения между показателями пористости, то на всякий случай необходимо провести измерение. При среднем диаметре гранул от 1,4 до 5 мм и их температуре от 0 до 300 С точка псевдоожижения достигается при скорости в пустой трубе от около 0,8 до 2 м/с. Средний диаметр гранул соответствует при этом среднему диаметру шариков гранулята равного объма. При этом скорость в пустой трубе соответствует скорости газа в незаполненной камере обработки и рассчитывается по количеству газа в единицу времени, делнному на площадь сечения камеры обработки. Другие преимущества, признаки и возможности применения изобретения приводятся ниже в описании двух вариантов осуществления изобретения со ссылкой на чертежи, на которых фиг. 1 - первый вариант осуществления изобретения; фиг. 2 - второй вариант осуществления изобретения. На фиг. 1 представлен первый вариант осуществления изобретения, при этом поликонденсатный материал податся из плавильного реактора с помощью насоса (2) для расплава и, при необходимости,фильтра для расплава (не показан) и посредством сопла (3) прессуется в виде жгута. Поликонденсатные жгуты охлаждают в охлаждающем устройстве (8) и режут с помощью гранулятора (4) на гранулы. После гранулятора (4) гранулы перемещаются по транспортному участку (5) в их сушилку (6). В транспортном трубопроводе (5b) могут быть, при необходимости, установлены насос (5 а), разветвители, такие как трубные переводы, отделители агломерата или дозаторы для альтернативных видов охлаждающих и/или транспортирующих сред. Отделнная охлаждающая среда поступает в систему циркуляции (9), которая в данном случае состоит из трубопроводов (9 а), по меньшей мере одного резервуара (9b), по меньшей мере одного теплообменника (9 с) и по меньшей мере одного насоса (9d), в результате чего достигается целенаправленное воздействие охлаждающей среды с равномерной температурой на поликонденсатные жгуты. После отделения охлаждающей среды гранулы поступают по другому транспортному участку (7) и через загрузочное отверстие (13) в зоне потолка (18) в камеру обработки (12). Здесь в противотоке гранулы обрабатываются газом, причм обрабатывающий газ поступает через отверстие (19) в распределительную камеру (20) и затем податся через устройство (15) для подачи обрабатывающего газа, в данном случае через отверстие в металлическом листе, в донную часть (16) камеры обработки (12) и снова отводится отводящим устройством (17) в зоне потолка (18) из камеры обработки (12). Путм регулировки количества газа с помощью точки псевдоожижения сыпучего гранулята последний перемещается в камере обработки (12), по существу, с образованием стержневого потока в виде рыхлого устойчивого слоя и выходит из камеры обработки (12) через разгрузочное отверстие (14), при этом выгружаемое количество задатся запорным устройством (не показано), таким как шлюзовой затвор или пневматическая задвижка. На фиг. 2 показан другой вариант осуществления изобретения, отличающийся тем, что вместо жгутовой грануляции применяется подводная грануляция, причм поликонденсатные жгуты режутся непо-5 016775 средственно на выходе из сопла устройством (4) для подводной резки. Другим отличием является наличие двух отверстий (13) для загрузки гранулята в камеру обработки (12). С одной стороны, обрабатывающий газ податся через загрузочное отверстие (19) в устройство (15) для подачи обрабатывающего газа, в данном случае через множество впускных каналов в донной части камеры обработки (16). С другой стороны, обрабатывающий газ податся через другое загрузочное отверстие (21) в другое устройство(22) для подачи обрабатывающего газа, в данном случае через открытый снизу обратный конус, на расположенный выше донной части (16) участок камеры обработки (12). Таким образом, камера обработки (12) оказывается разделнной на две зоны, при этом количество газа в обеих зонах превышает точку псевдоожижения сыпучего гранулята. Однако в верхней зоне возникает сильное завихрение и происходит обратное перемешивание, что ведт к быстрому выравниванию температур гранулята и обрабатывающего газа. Тогда в нижней части снова образуется зона обработки с узким диапазоном времени выдержки. Возможность осуществления изобретения Преимущества процесса согласно изобретению иллюстрируются на примере применения, при этом продолжительность выдержки при получении однородных, свободных от агломерата гранулятов составляет менее той же продолжительности при традиционных процессах. Пример. Обрабатывали сополимер полиэтилентерефталата, модифицированный изофталевой кислотой 2 мол.%, с показателем внутренней вязкости (IV) 0,6 дл/г в опытной установке (фиг. 2), причм расплав приготовили в двухвалковом экструдере без применения насоса (5 а). Производительность составила 200 кг/ч, температура расплава на выходе из сопла - 290 С. При подводной грануляции вес гранулы составил 18 мг. В качестве охлаждающей среды использовали воду с температурой 90 С. На входе в камеру обработки средняя температура гранулята составила ок. 140 С. Камера обработки была разделена на две зоны посредством двух устройств для впуска газа, при этом в нижнюю зону воздух поступал при температуре 170 С, вследствие чего скорость газа (скорость в пустой трубе) составила ок. 1 м/с, а в верхнюю зону подавалось дополнительное количество воздуха при температуре 180 С, в результате чего скорость газа составила ок. 2 м/с. В верхней зоне было отмечено сильное завихрение над слоем высотой 30 см при времени выдержки ок. 2 мин. В нижней зоне образовался подвижный устойчивый слой, характеризовавшийся скоростью оседания 90 мм/мин над слоем высотой 100 см при времени выдержки ок. 90 мин. После добавки цветных гранул из полиэтилентерефталата диапазон выдержки составил от 4 до 25 мин, причм не выгружались гранулы с продолжительностью выдержки менее 4 мин. Температура гранул при выгрузке составила 175 С. Гранулы имели совершенно белый цвет, при этом отсутствовали аморфные(прозрачные) гранулы. Теплота плавления при дифференциальной сканирующей калориметрии составила 41,8 Дж/г, что соответствует 36% кристалличности. При этом не образовывались комки или агломераты. Перечень позиций 1 - реактор,2 - устройство для подачи поликонденсатного расплава,3 - сопло,4 - режущее устройство (гранулятор),5 - устройство для транспортировки гранул из поликонденсата в жидкой охлаждающей среде,6 - устройство для отделения гранул из поликонденсата от жидкой охлаждающей среды,7 - устройство для подачи гранулята из поликонденсата,8 - устройство для охлаждения поликонденсатных жгутов,9 - система возврата жидкой охлаждающей среды,11 - оболочка корпуса,12 - камера обработки,13 - отверстие для загрузки гранулята,14 - отверстие для выгрузки гранулята,15 - устройство для подачи обрабатывающего газа,16 - донная часть камеры обработки,17 - устройство для отвода обрабатывающего газа,18 - зона потолка камеры обработки,19 - отверстие для подачи обрабатывающего газа,20 - распределительная камера для впуска газа,21 - дополнительное впускное отверстие,22 - дополнительное устройство для подачи обрабатывающего газа. ФОРМУЛА ИЗОБРЕТЕНИЯ 1. Способ непрерывного получения частично кристаллического гранулята из поликонденсата,включающий в себя следующие стадии: получение расплава поликонденсата,-6 016775 формование гранул из поликонденсата и отверждение расплава поликонденсата в жидкой охлаждающей среде, при этом формование гранул может проводиться до или после отверждения,отделение гранул от жидкой охлаждающей среды после их охлаждения до средней температуры,лежащей в диапазоне температур кристаллизации,кристаллизация гранул в камере обработки (12),при этом в камере обработки обрабатывающий газ движется противоточно гранулам из поликонденсата,отличающийся тем, что скорость потока обрабатывающего газа поддерживают выше точки псевдоожижения гранулята из поликонденсата и что минимальное время выдержки по меньшей мере 95% гранулята из поликонденсата в камере обработки (12) составляет более 20% от среднего времени выдержки. 2. Способ по п.1, отличающийся тем, что обрабатывающий газ подают при температуре, которая превышает среднюю температуру гранул из поликонденсата на входе в камеру обработки (12). 3. Способ по п.1 или 2, отличающийся тем, что жидкая охлаждающая среда, по меньшей мере, частично циркулирует в контуре и нагревается. 4. Способ по любому из предыдущих пунктов, отличающийся тем, что в качестве поликонденсата используют полиамид, поликарбонат, полигидроксиалканоат, полилактид или сложный полиэфир и их сополимеры и/или их смеси. 5. Способ по п.4, отличающийся тем, что в качестве сложного полиэфира используют полиэтилентерефталат, полибутилентерефталат или полиэтиленнафталат. 6. Способ по любому из предыдущих пунктов, отличающийся тем, что скорость оседания гранул из поликонденсата в камере обработки (12) составляет более 0,05 м/мин. 7. Способ по любому из предыдущих пунктов, отличающийся тем, что скорость оседания гранул из поликонденсата в камере обработки (12) составляет более 0,15 м/мин.
МПК / Метки
МПК: B29B 13/02, B29B 13/06, B29B 9/16
Метки: гранулятов, получения, равномерно, способ, кристаллизованных, поликонденсата
Код ссылки
<a href="https://eas.patents.su/9-16775-sposob-polucheniya-ravnomerno-kristallizovannyh-granulyatov-iz-polikondensata.html" rel="bookmark" title="База патентов Евразийского Союза">Способ получения равномерно кристаллизованных гранулятов из поликонденсата</a>
Предыдущий патент: Капустоуборочный комбайн
Следующий патент: Неадгезивные эластичные желатиновые матрицы
Случайный патент: Проходной изолятор