Способ производства композитных элементов
Номер патента: 25188
Опубликовано: 30.11.2016
Авторы: Хензик Райнер, Граальманн Онно, Грамлих Зимон, Шмит Ансгар
Формула / Реферат
1. Способ производства композитных элементов, состоящих по меньшей мере из одного покровного слоя a), усилителя c) сцепления и прочно соединенного с ними слоя b), при котором непрерывно передвигают покровный слой a) и последовательно наносимые усилитель c) сцепления и слой b) или его исходные материалы, причем в качестве усилителя c) сцепления используют вступающую в реакцию одно- или многокомпонентную систему на основе полиуретанов, полученных в результате реакции полиизоцианатов с соединениями, содержащими два изоцианатреактивных атома водорода, при этом нанесение усилителя c) сцепления осуществляют посредством вращающегося диска, кромка которого выполнена завышенной и снабжена от 10 до 100 зубцами, которые размещены в плоскости, параллельной основанию так, что при подаче усилителя c) сцепления на диск на зубцах формируются струйки жидкости с контролируемым разделением на капли, причем форма диска выбрана из группы, изображенной на фиг. 1, 3, 4, и диск, в случае круга, имеет диаметр от 0,05 до 0,4 м.
2. Способ по п.1, отличающийся тем, что диск располагают на высоте от 0,02 до 0,2 м от покровного слоя a).
3. Устройство для производства композитных элементов, состоящих по меньшей мере из одного покровного слоя a), прочно соединенного с ним слоя b) и расположенного между покровным слоем a) и слоем b) усилителя c) сцепления по п.1 или 2, которое выполнено в виде, по меньшей мере, установленного с возможностью вращения диска, кромка которого выполнена завышенной и снабжена от 10 до 100 зубцами, которые размещены в плоскости, параллельной основанию, и причем форма диска выбрана из группы, изображенной на фиг. 1, 3, 4, и диск, в случае круга, имеет диаметр от 0,05 до 0,4 м.
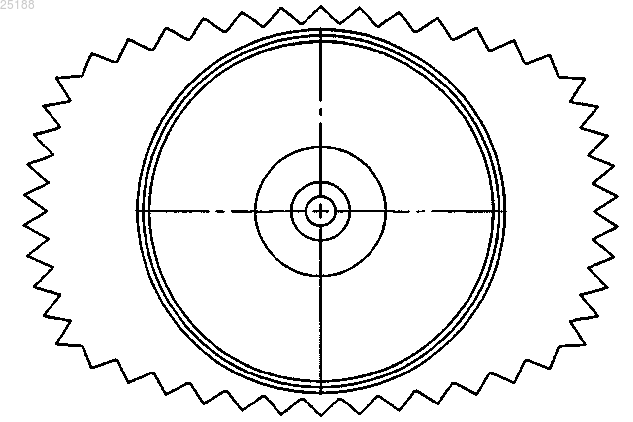
Текст
СПОСОБ ПРОИЗВОДСТВА КОМПОЗИТНЫХ ЭЛЕМЕНТОВ Изобретение касается способа производства композитных элементов, состоящих по меньшей мере из одного покровного слоя a) и прочно соединенного с ним слоя b), при этом между покровным слоем a) и прочно соединенным с ним слоем b) наносят усилитель c) сцепления, при этом покровный слой a) находится в непрерывном движении, и усилитель c) сцепления и прочно соединенный с ним слой b) или его исходные материалы наносят последовательно на покровный слой a), при этом нанесение усилителя c) сцепления осуществляют посредством вращающегося диска, который расположен по горизонтали или в незначительном отклонении от горизонтали до 15, отличающегося тем, что вращающийся диск по кромке снабжен зубцами. Предметом изобретения является способ производства композитных элементов. В качестве композитных элементов в смысле настоящего изобретения выступают плоские элементы, состоящие по меньшей мере из одного покровного слоя и прочно соединенного с ним слоя. Примером подобных композитных элементов являются панели с сердцевиной из пенополиуретана или пенополиизоцианурата и покровного слоя из металла, как, например, описано в EP 1516720. Эти композитные элементы часто называют сэндвич-элементами. Другим примером композитных элементов являются элементы, состоящие по меньшей мере из одного покровного слоя и предварительно изготовленной сердцевины из теплоизоляционного материала, например, минеральной ваты или органического изоляционного материала, такого как пенопласт, например, пенополиуретан или пенополистирол, как,например, описано в WO 2006/120234. Еще одним примером являются так называемые легкие строительные плиты, состоящие из двух покровных слоев, преимущественно из древесины, фанеры, древесностружечных плит, металла или пластика и слоя сердцевины преимущественно с сотовой, гофрированной или стековой структурой, преимущественно из картона, как описано, например, в WO 2007/093538. В широком смысле композитные элементы и компактные плиты, такие как древесные или древесностружечные плиты, покрыты покровными слоями из пластика, шпона или металла. При изготовлении композитных элементов необходимо обеспечить прочное соединение между материалом сердцевины и покровными слоями. При производстве композитных элементов с предварительно изготовленной сердцевиной это обеспечивается обычно посредством клея. При производстве сэндвичэлементов в основном происходит прочное сцепление между пеной и покровным слоем. Тем не менее,поверхностные дефекты пены могут приводить к ее отслоению от покровного слоя. Поэтому предпочтительно наносить усилитель сцепления между покровными слоями и сердцевиной, как описано в EP 1516720. Для нанесения клея или усилителя сцепления существуют различные возможности. Особенно подходящим способом является нанесение с использованием вращающегося диска. При таком способе нанесения можно обеспечить равномерность нанесения без образования аэрозолей. В WO 2006/29786 описывается способ производства сэндвич-элементов, при котором усилитель сцепления наносят при помощи вращающегося диска. Диск может быть плоским и преимущественно овальным или в форме звезды. В другом варианте диск может быть ступенчатым и содержать отверстия для выпуска усилителя сцепления. В EP 1593438 описывается устройство для производства сэндвич-элементов, в котором усилитель сцепления наносят на покровный слой с помощью вращающейся тарелки, снабженной, по меньшей мере,одним отверстием. В WO 2006/120234 описывается способ производства композитных элементов, при котором сердцевину приклеивают к покровному слою. Клей наносят также посредством вращающегося диска, как описано в патенте EP 1516720.WO 2007/0936538 описывает способ производства легких строительных плит, при котором клей наносят также посредством вращающегося диска, как и было описано в патенте WO 2006/29786. Описанные диски имеют, тем не менее, свои недостатки. Установлено, что усилитель сцепления или клей должны быстро застывать, чтобы их действие было оптимальным. Вследствие быстрой реакции материалов на диске скапливался быстро прореагировавший материал. Это оказывает отрицательное влияние на свойства известных дисков. Таким образом, уже спустя короткое время отверстия в диске закупоривались, и материал бесконтрольно сбрасывался через кромку диска. Вследствие этого распределение материала было неравномерным, прежде всего, больше материала было выброшено в краевую зону. В таком случае каплеобразование происходит не только по принципу распада ламинарных струй жидкости, а также вследствие отделения капель или даже разрушения ламелей. Оба вышеупомянутых механизма распада приводят к значительно более широким спектрам величины капель. Поэтому размеры капель больше не определяли. Чтобы обеспечить оптимальную работу диска, необходимо менять его в зависимости от быстроты действия усилителя сцепления уже через 20 мин. Это приводит к останове оборудования. Кроме того, с имеющимися в настоящее время дисками было едва возможным использование клея либо усилителя сцепления, которые содержат твердые наполнители. Задачей данного изобретения была разработка вращающихся дисков для нанесения клея или усилителя сцепления, на покровные слои/нижние поверхности, которые обеспечивали бы равномерное нанесение в течение продолжительного времени, далее обозначаемого как срок службы, и с помощью которых можно было бы наносить клей с твердыми наполнителями. Неожиданно, задача может быть решена путем применения диска, снабженного зубцами по кромке. Предметом изобретения, таким образом, является способ производства композитных элементов, состоящих по меньшей мере из одного покровного слоя a) и прочно соединенного с ним слоя b), при этом между покровным слоем a) и прочно соединенным с ним слоем b) наносят клей c), далее обозначаемый как усилитель сцепления, при этом вращающийся диск по кромке снабжен зубцами. Предметом изобретения является устройство для производства композитных элементов, состоящих по меньшей мере из одного покровного слоя a) и прочно соединенного с ним слоя b), при этом между покровным слоем a) и прочно соединенным с ним слоем b) наносят усилитель c) сцепления, при этом покровный слой a) находится в непрерывном движении, и усилитель c) сцепления вместе с прочно соединенным слоем b) либо его исходным материалом последовательно наносят на покровный слой a), нанесение усилителя сцепления осуществляется при помощи вращающегося диска, который по кромке снабжен зубцами. В предпочтительноу варианте выполнения изобретения диск имеет завышенную кромку. На этой кромке размещены зубцы. Ширина, количество и угол заострения зубцов так подобраны друг к другу, чтобы обеспечить максимально равномерное, четко распределенное нанесение клея на нижерасположенный покровный слой/нижнюю поверхность. Зубцы могут быть треугольными или четырехугольными и иметь ширину от 0,5 до 40 мм и длину от 0,1 до 50 мм. Зубцы могут иметь как одинаковую геометрию, так и различную геометрию и размеры. Зубцы могут быть горизонтальными или направленными вниз или вверх под углом до 90. В предпочтительном варианте выполнения изобретения зубцы являются остроконечными. Также возможно, что зубцы имеют скругленные концы. В другом варианте выполнения изобретения зубцам придана прямоугольная или трапециевидная форма. При этом важно, чтобы при подаче жидкости на зубцах формировались струйки жидкости, разделение которых на капли было бы контролируемым и приводило к узко распределенным спектрам по размеру капель. Завышенная кромка может быть расположена под углом от больше 0 до 150 к диску. При этом предпочтительным является наклон от 80 до 100. Кромка предназначена для выравнивания пленочного течения на диске. Переход к возвышенной кромке может быть угловым или скругленным. Количество зубцов зависит от желаемого распределения жидкости на покровном слое и от особенностей состава клея, таких как плотность, вязкость и поверхностное напряжение. Преимущественно, на диске расположено по меньшей мере от 4 до самое большее 600 зубцов, предпочтительно от 20 до 80,особенно предпочтительно от 40 до 60 зубцов. Основной формой диска предпочтительно является круглая форма. Возможно также выполнять диск в форме овала или в форме звезды. Также может быть использована геометрическая форма, которая описывает четыре внутренние линии трех пересекающихся окружностей, которые расположены следующим образом. Центр внутренней окружности находится на оси вращения. У двух других окружностей с большими диаметрами центры расположены на прямой, которая проходит через ось вращения и их радиус больше расстояния между центром окружности и осью вращения, и максимум настолько большое, что еще пока срезается самая маленькая окружность. Кромка у завышенного участка выброса имеет круглую форму и служит выравниванию потока. Диаметр этой окружности должен быть таким большим, насколько это возможно. Такой диск представлен на фиг. 1-3. На фиг. 4 представлены другие геометрические характеристики диска согласно изобретению. Могут найти применение диски S-образной формы выполнения (фиг. 4 а), диски с вогнутой (фиг. 4b) или плоской (фиг. 4 с) основной формой. Стрелка, обозначенная символомна фигуре, указывает возможное направление вращения диска. Важно при этом, чтобы контур не сильно отклонялся от окружности, так как иначе усилитель c) сцепления особенно на кромке линий контура не будет образовывать струю через зубец, а несколько струй сольются в одну, что далее приведет к неточному нанесению клея.S-образная форма выполнения обеспечивает сравнительно большую вогнутость (отклонение от круглой формы), так как критические участки, где может происходить слияние струй, округлены. Эта форма выполнения, тем не менее, на основании этого может быть использована только в одном направлении вращения. Еще одной формой выполнения может быть форма колокола, при которой материал подают по нижней стороне аппарата вдоль распылительной кромки. Нижеследующие формы выполнения применимы как к дискам, так и к колоколам. Соотношение длины диаметра диска к длине завышенной кромки находится в диапазоне от 5:1 до 100:1, преимущественно приблизительно 20:1. Диск в зависимости от ширины покровного слоя обозначается как ширина полосы, имеет диаметр от 0,05 до 0,4 м, предпочтительно от 0,1 до 0,3 м, особенно предпочтительно от 0,12 до 0,25 м, у овальных дисков относительно длинной стороны овальной формы. Соотношение диаметра диска к ширине полосы составляет от 0,05 до 0,35. Диск расположен преимущественно на высоте от 0,01 до 0,3 м, предпочтительно от 0,03 до 0,18 м,особенно предпочтительно от 0,03 до 0,15 м над смачиваемым покровным слоем. Вращающийся диск расположен по горизонтали или в незначительном отклонении от горизонтали до 15 относительно покровного слоя. Радиус смачивания усилителем сцепления на нижнем покровном слое находится преимущественно в диапазоне от 0,05 до 1,5 м, предпочтительно от 0,35 до 1,20 м. При более широких покровных слоях есть возможность использования двух или большего количества дисков, которые могут быть установле-2 025188 ны рядом либо со смещением. Число оборотов диска составляет преимущественно от 200 до 2500 мин-1, особенно предпочтительно от 200 до 2000 мин-1 и в особенности от 600 до 1200 мин-1. Есть возможность выровнять нанесение путем изменения числа оборотов. Число оборотов периодически, кратковременно уменьшают и снова увеличивают до начального уровня. Благодаря кратковременному ограничению уменьшается дальность распределения, что способствует выравниванию наносимого материала. Снижение оборотов может составлять до 10% от первоначального числа оборотов, главным образом от 50 до 80%. Распределяемый поток материала находится в диапазоне от 10 г/мин до 5 кг/мин, предпочтительно от 200 г/мин до 2 кг/мин, особенно предпочтительно от 400 г/мин до 1,8 кг/мин. В особом варианте выполнения изобретения по меньшей мере два, максимум пять дисков, особенно предпочтительно два диска, расположены друг над другом. При этом диаметр верхнего диска преимущественно больше диаметра нижнего диска, преимущественно в соотношении верхнего к нижнему диску от 1:8 до 1:10, предпочтительно 3:5. По меньшей мере верхний диск, но преимущественно все диски снабжены зубцами. При этом могут комбинироваться все вышеуказанные формы. Может также использоваться элемент, состоящий из верхней стороны в форме диска и нижней стороны в форме колокола. Преимуществом использования нескольких дисков является более равномерное распределение. При расположенных друг над другом дисках клей наносят предпочтительно на каждый диск по отдельности. При этом у верхнего диска необходимо предусмотреть концентрическую щель в виде отверстия для подачи клея на нижние диски. Внутренний радиус щелей соответствует диаметру вала. Соотношение внешнего радиуса щелей и внешнего радиуса соответствующего диска составляет максимум 0,98, предпочтительно от 0,2 до 0,5. Может наполняться также только один диск, а распределение на другие диски может осуществляться посредством приспособлений в виде отверстий или проводящих каналов. Количество отверстий либо проводящих каналов составляет от 4 до 12, предпочтительно от 4 до 8, особенно предпочтительно 4. Отверстия имеют площадь сечения, равную от 25 до 900 мм 2, предпочтительно от 100 до 650 мм 2, особенно предпочтительно от 100 до 400 мм 2. При применении колокола материал наносят на верхнюю сторону и подают на нижнюю сторону при помощи вышеуказанных проводящих каналов. Диск можно изготавливать из любых материалов, которые по отношению к усилителю сцепления ведут себя инертно. Предпочтительно использование металла или пластика. Главным образом, диски изготавливают из пластмасс. При этом особое предпочтение отдается термопластичным пластмассам,таким как полиолефины, полистирол, полиамид, тефлон или полиацеталь, как полиоксиметилен (ПОМ). В качестве покровного слоя a) можно использовать древесные плиты, гипсокартон, плитку из стекла, алюминиевую фольгу, алюминиевые, медные или стальные листы, предпочтительно, алюминиевую фольгу, алюминиевые или стальные листы, особенно предпочтительны стальные листы. Стальные листы могут быть с покрытием или без него. Они, главным образом, не подвергаются коронной обработке. При изготовлении легких строительных плит в качестве покровного слоя a) можно использовать древесные или древесностружечные плиты и в качестве слоев b) материалы с сотовой структурой, например, из древесины или картона. В качестве прочно соединенных с покровным слоем a) слоев b) при производстве изоляционных плит используют такие изоляционные материалы, как минеральная вата, вспененный полистирол или жесткая пена на основе изоцианата, называемая также жесткая полиуретановая пена. Жесткая пена на основе изоцианата может быть модифицирована изоциануратными группами. При использовании жесткой пены на основе изоцианата в качестве слоя b) изготовление композитных элементов производится преимущественно непрерывно. При этом жидкие исходные компоненты жесткой пены наносят на покровный слой a), где их отверждают до пены. Металлические листы или фольгу при использовании в качестве покровного слоя разматывают постепенно из рулона, фасонируют, разогревают, при необходимости, подвергают коронной обработке,чтобы повысить степень вспениваемости полиуретана, вспенивают исходный материал для жесткого пенопласта на основе изоцианата b), часто также обозначаемого как ПУР- или ПИР-системы, отверждают в двух лентах и в заключение разрезают по необходимой длине. Покровный слой движется с постоянной скоростью от 2 до 25 м/мин, особенно предпочтительно от 2 до 15 м/мин и в особенности от 3 до 12 м/мин, особенно предпочтительно от 3 до 9 м/мин. При этом покровный слой с момента нанесения ПУР-системы b), преимущественно в течение всего периода с момента нанесения усилителя сцепления находится в горизонтальном положении. Усилитель сцепления может наноситься и в то время, когда покровный слой во время движения слегка наклонен, то есть не находится в горизонтальном положении. В качестве клея при производстве легких строительных плит или изоляционных плит на основе минеральной ваты или полистирола могут использоваться общепринятые одно- и двухкомпонентные клеи. При непрерывном изготовлении композитных элементов на основе жесткой пены на основе изоцианата используют преимущественно усилители сцепления c) на основе полиуретанов, в особенности,двухкомпонентные системы. Нанесение усилителя c) сцепления при этом, в принципе, можно производить в любой момент процесса между раскручиванием из рулонов покровного слоя и нанесением ПУР-3 025188 или ПИР-систем. При этом выгодным является, когда интервал между нанесением усилителя c) сцепления и нанесением ПУР- или ПИР-систем был небольшим. При этом отходы, которые образуются в начале процесса и в конце, а также вследствие непредвиденных остановок, будут минимальными. Усилитель c) сцепления в случае использования двухкомпонентной системы перед нанесением на вращающийся диск механически перемешивают, при этом могут быть задействованы смесители высокого и низкого давления, преимущественно смесители низкого давления, и далее с помощью устройства подачи, например, включающегося миксера, подают на диск. После того как диск с помощью приводного механизма приводят во вращение, производят плоское распределение усилителя сцепления c) на расположенный под диском, находящийся в постоянном движении, покровный слой. Для перемешивания и нанесения усилителя c) сцепления на диск можно использовать, например, мешалку из пластика. Количество подаваемого усилителя c) сцепления согласовано со скоростью постоянно работающего двойного конвейера, чтобы можно было получить необходимый расход наносимого состава на м 2 металла. После осуществления нанесения усилителя c) сцепления на покровный слой производят нанесение исходного материала для жесткой пены б) на основе изоцианата. Реактивность c) усилителя сцепления установлена таким образом, чтобы системы b) и c) вместе вступили в реакцию (открытое время усилителя сцепления c) к моменту нанесения слоя b) еще не превышено), и через некоторое время отвердели. При применении усилителя c) сцепления температура двойной ленты может быть снижена до 55C. В качестве усилителя c) сцепления могут применяться известные в уровне техники усилителя сцепления, на основе полиуретана. Их получают в результате реакции полиизоцианатов с соединениями, содержащими два изоцианат-реактивных атома водорода, при этом условия реакции выбраны такие, чтобы в реакционной смеси соотношение количества изоцианатных групп к количеству изоцианат-реактивных групп составляло от 0,8 до 1,8:1, преимущественно от 1 до 1,6:1. Для применения в качестве полиизоцианатов подходят обычные алифатические, циклоалифатические и особенно ароматические ди- и/или полиизоцианаты. Предпочтительными являются толуилендиизоцианат (ТДИ), дифенилметандиизоцианат (МДИ) и особенно смеси из дифенилметандиизоцианата и полифениленполиметиленполиизоцианатов (сырой МДИ). Предпочтительно используют изоцианаты фирмы BASF SE Lupranat M 50, Lupranat M 70 undLupranat M 200. В предпочтительной форме исполнения изоцианаты, которые используют при получении жесткой пены на основе изоцианатов b), а также усилители c) сцепления идентичны. В предпочтительной форме исполнения используют Lupranat M 70, в особенно предпочтительной форме исполнения используют Lupranat M 200. В качестве соединений по меньшей мере с двумя изоцианат-реактивными атомами водорода принимают во внимание в общем случае такие, которые содержат в молекуле две или более реактивных групп, выбранных из OH-групп, SH-групп, NH-групп, NH2-групп и CH-кислотных групп, как, например,-дикетогруппы. Используют, главным образом, полиэфирполиолы и/или сложные полиэфирполиолы, особенно предпочтительны полиэфирполиолы. Гидроксильное число используемых полиэфирполиолов и/или сложных полиэфирполиолов составляет преимущественно от 25 до 800 мг KOH/г, молекулярные массы в общем больше, чем 400. Полиуретаны можно получать с или без средств удлинения цепи и/или средств,образующих поперечные связи. В качестве средств удлинения цепи и/или средств, образующих поперечные связи, можно использовать двух- или трехфункциональные амины и спирты, предпочтительно диолы и/или триолы с молекулярными массами меньше 400, преимущественно от 60 до 300. Полиольный компонент усилителя c) сцепления показывает при этом вязкость от 100 до 1000 мПас, преимущественно от 100 до 800 мПас, особенно предпочтительно от 150 до 400 мПас (25C). В усилителе сцепления c) могут содержаться при необходимости дополнительные или реактивные огнезащитные средства. Огнезащитные средства такого рода используют, в общем, в количестве от 0,1 до 30 мас.% из расчета на общую массу полиольного компонента. Реакцию полиизоцианатов с полиолами осуществляют преимущественно без добавления физических пенообразователей. Используемые полиолы могут, тем не менее, еще содержать остатки воды, которая действует как пенообразователь. Полученные в результате полиуретановые усилители сцеплении,которые преимущественно применяются при использовании жесткого пенопласта на основе изоцианата в качестве слоя b), показывают при этом плотность от 200 до 1200 г/л, предпочтительно от 400 до 1000 г/л,особенно предпочтительно от 450 до 900 г/л. Используемый в данном способе согласно изобретению жесткий пенопласт b) на основе изоцианатов получают общепринятым и известным методом реакцией полиизоцианатов с соединениями, содержащими по меньшей мере два изоцианат-реактивных атома водорода в присутствии пенообразователей,катализаторов и прочих вспомогательных и/или дополнительных веществ. В отношении исходных материалов, в частности, следует сказать следующее. В качестве органических полиизоцианатов пригодны предпочтительно ароматические многоатомные изоцианаты. В частности, необходимо назвать, например, 2,4- и 2,6-толуилендиизоцианат (ТДИ) и соответствующие смеси изомеров, 4,4'-, 2,4'- и 2,2'-дифенилметандиизоцианат (МДИ) и соответствующие смеси изомеров, смеси из 4,4'- и 2,4'-дифенилметандиизоцианатов, полифенил-полиметилен-полиизоцианаты,смеси из 4,4'-, 2,4'- и 2,2'-дифенилметандиизоцианатов и полифенил-полиметилен-полиизоцианатов (сырой МДИ) и смеси из сырого МДИ и толуилендиизоцианатов. Органические ди- и полиизоцианаты могут быть использованы по отдельности либо в виде смесей. Часто используют также так называемые модифицированные многоатомные изоцианаты, т.е. продукты, получаемые в результате химической реакции органических ди- и полиизоцианатов. Для примера следует назвать ди-и/или полиизоцианураты, содержащие изоциануратные и/или уретановые группы. Модифицированные полиизоцианаты можно смешать между собой либо с немодифицированными органическими полиизоцианатами, такими как 2,4'-, 4,4'-дифенилметандиизоцианат, сырой МДИ, 2,4- и/или 2,6-толуилендиизоцианат. Кроме того, свое применение могут найти продукты реакции многоатомных изоцианатов с многоатомными полиолами, а также их смеси с другими ди- и полиизоцианатами. Особенно зарекомендовал себя в качестве органического полиизоцианата сырой МДИ с содержанием NCO от 29 до 33 мас.% и вязкостью в диапазоне от 150 до 1000 мПас при 25C. В качестве соединений, по меньшей мере, с двумя изоцианат-реактивными атомами водорода используют предпочтительно полиэфирные спирты с OH-числами в диапазоне от 25 до 800 мг KOH/г. Применяемые полиэфирные спирты получают путем конденсации многофункциональных спиртов,преимущественно диолов с 2-12 атомами углерода, преимущественно, 2-6 атомами углерода, с многофункциональными карбоновыми кислотами с 2-12 атомами углерода, например, янтарной кислотой, глутаровой кислотой, адипиновой кислотой, пробковой кислотой, азелаиновой кислотой, себациновой кислотой, декандикарбоновой кислотой, малеиновой кислотой, фумаровой кислотой и, предпочтительно фталевой кислотой, изофталевой кислотой, терефталевой кислотой и изомерными нафталендикарбоновыми кислотами. Применяемые полиэфиры преимущественно имеют функциональность 1,5-4. В особенности используют полиэфирполиолы, которые получают известными способами, например, посредством анионной полимеризации алкиленоксидов H-функциональными исходными веществами в присутствии катализаторов, преимущественно гидроксиды щелочных металлов. В качестве алкиленоксидов используют преимущественно этиленоксид и/или пропиленоксид, предпочтительно чистый 1,2-пропиленоксид. В качестве исходных веществ используют преимущественно соединения по меньшей мере с 3,предпочтительно с 4-8 гидроксильными группами или по меньшей мере с двумя первичными аминогруппами в молекуле. В качестве исходных веществ по меньшей мере с 3, предпочтительно с 4-8 гидроксильными группами в молекуле используют триметилопропан, глицерин, пентаэритрит, соединения сахаров, такие как,например, глюкоза, сорбит, маннит и сахароза, многоатомные фенолы, резолы, как, например, олигомерные продукты конденсации из фенола и формальдегида и конденсаты Манниха из фенола, формальдегида и диалканоламинов, а также меламин. В качестве исходных веществ по меньшей мере с двумя первичными аминогруппами в молекуле используют предпочтительно ароматические ди-и/или полиамины, например, фенилендиамины, 2,3-,2,4-, 3,4- и 2,6-толуилендиамин и 4,4'-, 2,4'- и 2,2'-диаминодифенилметан, а также алифатические ди- и полиамины, такие как, например, этилендиамин. Полиэфирполиолы имеют функциональность предпочтительно от 3 до 8 и гидроксильные числа предпочтительно от 25 до 800 мг KOH/г и в особенности от 240 до 570 мг KOH/г. К соединениям по меньшей мере с двумя изоцианат-реактивными атомами водорода относятся также используемые, при необходимости, средства удлинения цепи и средства, образующие поперечные связи. Для модификации механических свойств можно использовать дифункциональные средства удлинения цепи, три- и высокофункциональные средства, образующие поперечные связи или, при необходимости, также их смеси. В качестве средств удлинения цепи и/или средств, образующих поперечные связи, используют предпочтительно алканоламины и, в частности, диолы и/или триолы с молекулярными массами менее 400, преимущественно от 60 до 300. Средства удлинения цепи, средства, образующие поперечные связи или их смеси целесообразно используют в количестве от 1 до 20 мас.%, предпочтительно от 2 до 5 мас.% из расчета на полиольный компонент. Получение жесткой пены происходит обычно в присутствии пенообразователей, катализаторов, огнезащитных средств и стабилизаторов ячеек, а также при необходимости с использованием прочих вспомогательных средств и добавок. В качестве пенообразователей может быть использована вода, которая реагирует с изоцианатными группами с выделением диоксида углерода. В сочетании с водой или предпочтительно вместо воды могут быть использованы так называемые физические пенообразователи. При этом речь идет об инертных по отношению к используемым компонентам соединениях, которые остаются жидкими при комнатной температуре и в условиях уретановой реакции испаряются. Точка кипения этих соединений находится предпочтительно ниже 50C. К физическим пенообразователям относятся также соединения, которые при комнатной температуре находятся в газообразной форме и при давлении вводятся в составляющие компоненты или растворяются в них, например, диоксид углерода, кипящие при низких температурах алканы и фторалканы. Соединения обычно выбирают из группы, содержащей алканы и/или циклоалканы, по меньшей мере с 4 атомами углерода, диалкиловый эфир, эфир, кетоны, ацетали, фторалканы с 1-8 атомами углерода и тетраалкилсиланы с 1-3 атомами углерода в алкильной цепи, особенно тетраметилсилан. В качестве примера следует назвать пропан, н-бутан, изо- и циклобутан, н-, изо- и циклопентан,циклогексан, диметиловый эфир, метилэтиловый эфир, метилбутиловый эфир, метиловый эфир муравьиной кислоты, ацетон, а также фторалканы, которые могут разлагаться в тропосфере, и поэтому они безопасны для озонового слоя, такие как трифторметан, дифторметан, 1,1,1,3,3-пентафторбутан, 1,1,1,3,3 пентафторпропан, 1,1,1,2-тетрафторэтан, дифторэтан и гептафторпропан. Упомянутые физические пенообразователи могут быть применены по отдельности либо в любых сочетаниях между собой. Полиуретановый или полиизоциануратный пенопласты содержат обычно огнезащитные средства. Предпочтительно используют огнезащитные средства без брома. Особенно предпочтительными являются огнезащитные средства, содержащие атомы фосфора, в частности, используют трихлоризопропилфосфат, диэтилэтанфосфонат, триэтилфосфат и/или дифенилкрезилфосфат. В качестве катализаторов используются соединения, которые сильно ускоряют реакцию изоцианатных групп с группами, реактивными по отношению к изоцианатным группам. Такими катализаторами являются сильноосновные амины, как, например, вторичные алифатические амины, имидазолы, амидины, а также алканоламины и/или металлоорганические соединения, предпочтительно на основе цинка. Для включения в состав жесткого пенопласта изоциануратных групп нужны специальные катализаторы. В качестве изоцианурат-катализаторов используют обычно металлкарбоксилаты, предпочтительно ацетат калия и его растворы. Катализаторы можно использовать, по необходимости, отдельно либо в любых их комбинациях между собой. В качестве вспомогательных средств и/или добавок используют известные для этой цели вещества,например, поверхностно-активные вещества, стабилизаторы пены, регуляторы ячеек, наполнители, пигменты, красители, защитные средства против гидролиза, антистатики, фунгистатические и бактериостатические средства. Подробные сведения по применяемым при осуществлении способа согласно изобретению основным исходным материалам, пенообразователям, катализаторам, а также вспомогательным и/или дополнительным материалам можно найти, например, в Kunststoffhandbuch, Band 7, "Polyurethane" Carl-HanserVerlag Mnchen, 1. Auflage, 1966, 2. Auflage, 1983 und 3. Auflage, 1993. ("Справочник пластмасс, том 7,Полиуретаны", издательство Карл Ханзер, Мюнхен, 1-е издание, 1966, 2-е издание, 1983 и 3-е издание,1993). Для получения жестких пенопластов на основе изоцианата полиизоцианаты и соединения, по меньшей мере, с двумя реактивными к изоцианатным группам атомами водорода вступают в реакцию в таких количествах, чтобы изоцианатный индекс в случае полиуретановых пен находился в диапазоне между 100 и 220, преимущественно между 115 и 180. Полиуретановые жесткие пенопласты могут производиться прерывно или непрерывно с помощью известных смешивающих устройств. При получении пенополиизоциануратов можно работать с индексом 180, преимущественно от 200 до 500, особенно предпочтительно от 250 до 500. Перемешивание исходных компонентов может производиться при помощи известных смешивающих устройств. Обычно жесткий ПУР-пенопласт согласно изобретению получают двухкомпонентным способом. При этом способе соединения, по меньшей мере, с двумя реактивными к изоцианатным группам атомами водорода смешивают с пенообразователями, катализаторами, а также прочими вспомогательными средствами и/или добавками в так называемый полиольный компонент, и который вступает в реакцию с полиизоцианатами или смесями полиизоцианатов и, при необходимости, с пенообразователями, также обозначаемыми как изоцианатный компонент. Исходные компоненты в большинстве случаев смешивают при температуре от 15 до 35C, преимущественно от 20 до 30C. Реакционную смесь можно перемешивать с помощью дозирующих машин высокого и низкого давления. Плотность используемого здесь жесткого пенопласта составляет преимущественно от 10 до 400 кг/м 3, преимущественно от 20 до 200, особенно предпочтительно от 30 до 100 кг/м 3. Толщина композитных элементов находится в диапазоне от 5 до 250 мм. Благодаря геометрическим характеристикам диска согласно изобретению можно существенно увеличить срок его службы, вне зависимости от накопления прореагировавшего клея на диске. Поразительным образом распределение клея на покровном слое, несмотря на накопление материала на диске, и размеры капель остались неизменными. Поразительным образом траектория полета капель, отделяющихся с диска, в основном не меняется. Другим преимуществом является то, что при геометрических характери-6 025188 стиках дисков согласно изобретению четко может быть отделена граница обрабатываемой поверхности на покровном слое. На фиг. 2 представлен диск с завышенной кромкой в разрезе. Фиг. 3 показывает диск с завышенной кромкой. ФОРМУЛА ИЗОБРЕТЕНИЯ 1. Способ производства композитных элементов, состоящих по меньшей мере из одного покровного слоя a), усилителя c) сцепления и прочно соединенного с ними слоя b), при котором непрерывно передвигают покровный слой a) и последовательно наносимые усилитель c) сцепления и слой b) или его исходные материалы, причем в качестве усилителя c) сцепления используют вступающую в реакцию одноили многокомпонентную систему на основе полиуретанов, полученных в результате реакции полиизоцианатов с соединениями, содержащими два изоцианатреактивных атома водорода, при этом нанесение усилителя c) сцепления осуществляют посредством вращающегося диска, кромка которого выполнена завышенной и снабжена от 10 до 100 зубцами, которые размещены в плоскости, параллельной основанию так, что при подаче усилителя c) сцепления на диск на зубцах формируются струйки жидкости с контролируемым разделением на капли, причем форма диска выбрана из группы, изображенной на фиг. 1, 3, 4, и диск, в случае круга, имеет диаметр от 0,05 до 0,4 м. 2. Способ по п.1, отличающийся тем, что диск располагают на высоте от 0,02 до 0,2 м от покровного слоя a). 3. Устройство для производства композитных элементов, состоящих по меньшей мере из одного покровного слоя a), прочно соединенного с ним слоя b) и расположенного между покровным слоем a) и слоем b) усилителя c) сцепления по п.1 или 2, которое выполнено в виде, по меньшей мере, установленного с возможностью вращения диска, кромка которого выполнена завышенной и снабжена от 10 до 100 зубцами, которые размещены в плоскости, параллельной основанию, и причем форма диска выбрана из группы, изображенной на фиг. 1, 3, 4, и диск, в случае круга, имеет диаметр от 0,05 до 0,4 м.
МПК / Метки
МПК: B32B 37/12
Метки: композитных, элементов, способ, производства
Код ссылки
<a href="https://eas.patents.su/8-25188-sposob-proizvodstva-kompozitnyh-elementov.html" rel="bookmark" title="База патентов Евразийского Союза">Способ производства композитных элементов</a>
Предыдущий патент: Производное дитиокарбамата 2-((4-(4-метилпиперазин-1-ил)фенил)амино)-2-оксоетил4-этилпиперазин-1-карбодитиоат, обладающее антифунгальной активностью
Следующий патент: Бромсодержащий полифенилен-1,3,4-оксадиазол, способ его получения и волокна с повышенной огне- и термостойкостью на его основе
Случайный патент: Липополисахарид бактерий e. coli штамма dsm 6601 и способ его получения