Устройство и способ охлаждения фрагментов расплава
Номер патента: 22298
Опубликовано: 30.12.2015
Авторы: Дорн Константин, Абдула Валерий, Францки Рената, Шумахер Эдгар
Формула / Реферат
1. Устройство охлаждения фрагментов расплава металла или сплава, полученных пропусканием расплава через фильеру, расположенную в днище тигля, включающее устанавливаемую между днищем тигля и расположенной под тиглем ванной по меньшей мере одну форсунку для подачи в подтигельное пространство охлаждающей воздушно-капельной смеси, отличающееся тем, что форсунка размещена с возможностью подачи воздушно-капельной смеси в пространство под тиглем ниспадающим потоком.
2. Устройство охлаждения фрагментов расплава по п.1, отличающееся тем, что оно содержит несколько форсунок, установленных фронтально по отношению к стенке тигля на уровне, равном половине расстояния от днища тигля до уровня охлаждающей жидкости в ванне, а расстояние В от сопла форсунки до вертикальной плоскости, совпадающей со стенкой тигля, и угол β между горизонтальной плоскостью и осью форсунки выбраны таким образом, чтобы экстремум верхней ветви параболической траектории потока охлаждающей воздушно-капельной смеси из форсунки совпадал с точкой пересечения днища тигля и его стенки.
3. Устройство охлаждения фрагментов расплава по п.2, отличающееся тем, что расстояние А между фронтально установленными по длине тигля форсунками в горизонтальной плоскости определяется из соотношения
A=2×B×tg(a/2),
где α - угол раскрытия факела форсунки;
В - расстояние от форсунки до вертикальной плоскости, совпадающей со стенкой тигля.
4. Способ охлаждения фрагментов расплава металла или сплава, полученных пропусканием расплава через фильеру, расположенную в днище тигля, посредством устанавливаемой между днищем тигля и расположенной под тиглем ванной по меньшей мере одной форсунки для подачи в подтигельное пространство охлаждающей воздушно-капельной смеси, отличающийся тем, что подачу воздушно-капельной смеси в пространство под тиглем осуществляют ниспадающим потоком.
5. Способ охлаждения фрагментов расплава по п.4, отличающийся тем, что используют несколько форсунок, установленных фронтально по отношению к стенке тигля на уровне, равном половине расстояния от днища тигля до уровня охлаждающей жидкости в ванне, а расстояние В от сопла форсунки до вертикальной плоскости, совпадающей со стенкой тигля, и угол β между горизонтальной плоскостью и осью форсунки выбирают таким образом, чтобы экстремум верхней ветви параболической траектории потока охлаждающей воздушно-капельной смеси из форсунки совпадал с точкой пересечения днища тигля и его стенки.
6. Способ охлаждения фрагментов расплава по п.5, отличающийся тем, что расстояние А между фронтально установленными по длине тигля форсунками в горизонтальной плоскости определяют из соотношения
A=2×B×tg(a/2),
где α - угол раскрытия факела форсунки;
В - расстояние от форсунки до вертикальной плоскости, совпадающей со стенкой тигля.
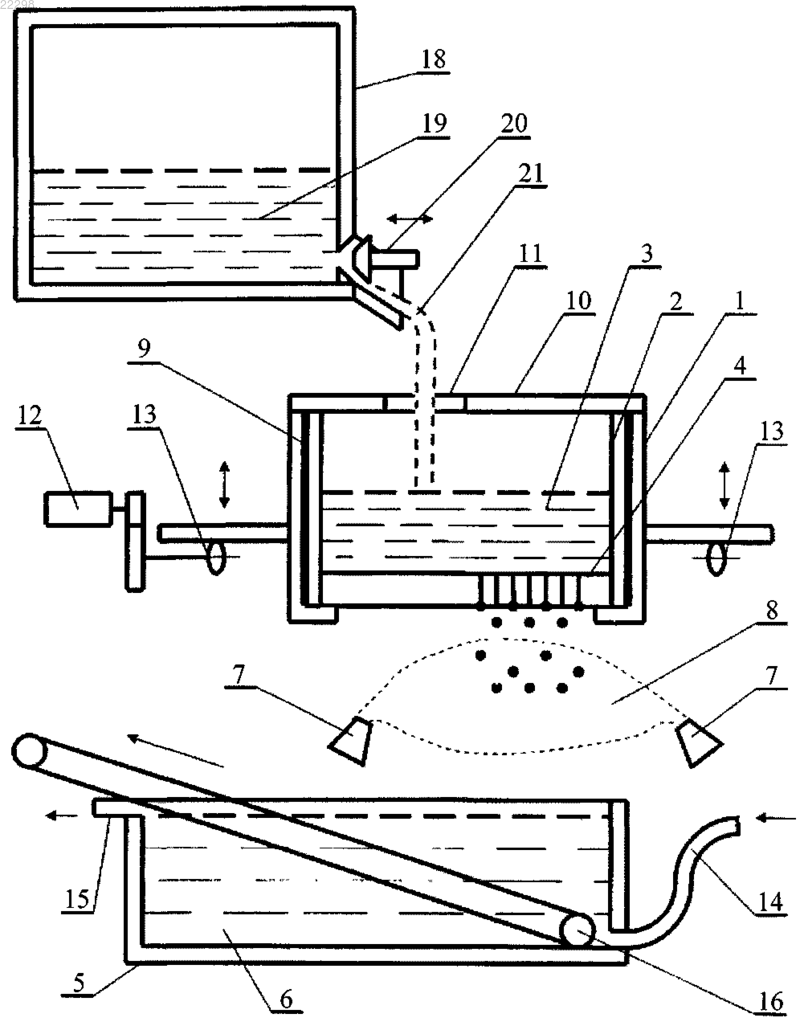
Текст
УСТРОЙСТВО И СПОСОБ ОХЛАЖДЕНИЯ ФРАГМЕНТОВ РАСПЛАВА Изобретение относится к металлургии, в частности к производству металлической дроби из расплава металла или сплава методом литья. Заявляемое устройство охлаждения фрагментов расплава металла или сплава, полученных пропусканием расплава через фильеру, включает одну или несколько форсунок для подачи в подтигельное пространство распыленной охлаждающей воздушно-капельной смеси ниспадающим потоком. Еще одним аспектом настоящего изобретения является способ охлаждения фрагментов расплава, реализуемый посредством указанного устройства. Техническим результатом заявляемого изобретения является получение дроби с высокой степенью сферичности и заданного фракционного состава. Изобретение относится к металлургии, в частности к производству металлической дроби методом литья. Дробь из различных металлов и сплавов находит широкое применение в металлургических технологиях, например в литейном производстве, используется для дробемтной и дробеструйной очистки изделий, поверхностного упрочнения деталей и т.п. При производстве дроби методом литья большое значение имеют такие характеристики процесса,как производительность, приемлемые материальные затраты, стабильность фракционного состава получаемой дроби, правильная геометрия дроби. Например, при инжекции дроби в расплав с целью легирования или раскисления от фракционного состава и формы дроби в значительной степени зависит глубина ее проникновения в объм расплава, а значит, и эффективность использования присаживаемого таким способом материала. Решаемые конкретные технологические задачи - раскисление, легирование, рафинирование и др., и размер используемой для этого дроби определяют параметры инжекции: давление транспортного газа,интенсивность подачи материала, скорость дроби в потоке, диаметр материалопровода. Данные параметры определяют эффективность использования материала и стабильность получаемого результата. Если используемая дробь содержит фрагменты разных классов крупности, установить оптимальные параметры для эффективной инжекции невозможно, снижается коэффициент использования материала. Коэффициент использования материала тем меньше, чем более разнородна дробь по классам крупности. Также на способность проникновения дроби в объм расплава оказывает ее форма. Если имеются отклонения от сферической формы, уменьшается глубина проникновения дроби в расплав, возрастает вероятность рикошета, т.е. дробь при взаимодействии с поверхностью расплава не проникает в объм расплава, а отскакивает от его поверхности. Форма дроби имеет значение и для газовой транспортировки, особенно в отношении крупных классов. Материал, состоящий из фрагментов сферической формы,меньше изнашивает трубопроводы, способствует снижению эффекта "закупоривания" материалопровода. Известны различные способы получения металлической дроби, такие как распыление струи металла воздухом, паром, водой; раздробление струи металла при падении на наклонную поверхность, смоченную водой; заливка металла в воду "дождевыми" литниками; разливка через водяные сита. Также известен метод центробежного гранулирования, основанный на дроблении расплава центробежной силой. Последний метод может быть реализован посредством вращающегося перфорированного стакана,распыления с кромки вращающегося диска или чаши, распыления оплавленного слоя вращающейся заготовки. Существует также электроконтактный способ получения дроби или металлического порошка,заключающийся в воздействии кромки вращающегося токопроводящего диска на металл, например, в виде полосы или стружки, расплавляемый за счт энергии электрического тока. Вышеперечисленные способы наряду с преимуществами имеют ряд недостатков. Так, они позволяют получать дробь из различных металлов в достаточно больших количествах при относительно низких затратах и удовлетворительной геометрии. Однако при реализации всех вышеперечисленных способов при разделении расплава какого-либо металла или сплава на отдельные фрагменты не обеспечивается точное дозирование по массе, а соответственно, получаемая дробь имеет нестабильный фракционный состав по крупности. Как следствие, невозможно подобрать оптимальный режим охлаждения, обеспечивающий получение дроби с высоким показателем сферичности одновременно для всех получающихся классов крупности. Поскольку полученная этими способами дробь имеет разную крупность, перед использованием необходимо еерассеивать и, зачастую, искать применение для некондиционных классов крупности или же возвращать ее в начало технологического процесса. Кроме того, если в дробь перерабатывается металл или сплав с повышенным сродством к кислороду, мелкие фракции в большей степени подвержены процессам окисления при контакте с атмосферой, чем крупные, что приводит к дополнительным потерям конечного продукта. Наиболее предпочтительным способом получения дроби сферической формы представляется способ, основанный на пропускании расплава металла или сплава через фильеру и последующем охлаждении получаемых при пропускании фрагментов расплава. Авторское свидетельство СССР 1222417 (опубл. 07.04.1986; МПК B22F 9/08) описывает способ получения металлических гранул из расплава, при котором расплавленный металл пропускается через отверстия в дне тигля диаметром от 1 до 8 мм и далее охлаждается в жидкости. При этом в камере под расплавом создается избыточное давление 0,01-1 атм с использованием инертного газа. Размеры гранул регулируют, изменяя диаметр отверстий, давление газа под тиглем, температуру металла и высоту его столба в тигле. Уровень сплава в тигле поддерживается постоянным. Патент РФ 2117553 (опубл. 20.08.1998; МПК B22F 9/06) раскрывает способ получения сферических гранул металла, включающий диспергирование расплавленного металла при получении его через отверстия за счет перепада давления при наложении на металл постоянного магнитного поля и пропускания через него переменного электрического тока с последующим охлаждением гранул в атмосфере воздуха, причем выходящий из отверстий металл пропускают через слой инертного газа. Обретение каплями сферической формы происходит в основном в среде инертного газа. Из заявки на патент Японии 4259312 (опубл. 14.09.1992; МПК B22F 9/08, В 23K 35/40) известен способ получения гранул металла с низкой температурой плавления, включающий пропускание жидкого металла через сопло с множеством отверстий, расстояние между которыми составляет не менее трехкратной величины диаметра отверстий. Сопло подвергается вибрации для образования отдельных капель расплавленного металла. Сферическая форма каплям придается в процессе их падения, а солидификация сферических гранул происходит в охлаждаемой зоне. В качестве наиболее близкого аналога может быть выбрано техническое решение, описанное в заявке на патент Японии 62253705 (опубл. 05.11.1987; МПК B22F 9/08). Из заявки известны устройство и способ получения металлической дроби с использованием тигля с отверстиями, установленного на виброустройстве. Частота вибраций составляет от 40 до 100 Гц, амплитуда 0,2-1,5 мм. Расплавленный металл проходит через отверстия и под действием вибрации разбивается на капли. Частичная солидификация образовавшихся капель происходит в процессе падения в атмосфере между фильерой и охлаждающей жидкостью, а окончательная солидификация капель и обретение ими сферической формы - в охлаждающей жидкости (воде). Настоящее изобретение призвано устранить недостатки известных из уровня техники способов и устройств охлаждения фрагментов расплава в процессе получения дроби и позволяет получать сферическую дробь со стабильными геометрическими параметрами и физическими свойствами. Заявляемый технический результат достигается тем, что устройство охлаждения фрагментов расплава металла или сплава, полученных пропусканием расплава через фильеру, расположенную в днище тигля, включает в себя устанавливаемую под днищем тигля по меньшей мере одну форсунку для подачи в подтигельное пространство распыленной охлаждающей воздушно-капельной смеси, причем форсунка размещена с возможностью подачи воздушно-капельной смеси в пространство под тиглем ниспадающим потоком. Устройство охлаждения фрагментов расплава может включать несколько форсунок, установленных фронтально по отношению к стенке тигля на уровне, равном половине расстояния от днища тигля до уровня охлаждающей жидкости в расположенной под тиглем ванны. Предпочтительно, если расстояние от сопла форсунки до вертикальной плоскости, совпадающей со стенкой тигля, и угол между горизонтальной плоскостью и осью форсунки будут выбраны таким образом, чтобы экстремум верхней ветви параболической траектории потока охлаждающей воздушно-капельной смеси из форсунки совпадал с точкой пересечения днища тигля и его стенки. Также предпочтительно, если расстояние между фронтально установленными по длине тигля форсунками в горизонтальной плоскости равно двукратному произведению расстояния от форсунки до вертикальной плоскости, совпадающей со стенкой тигля, и тангенсу половины угла раскрытия факела форсунки. Далее изобретение более подробно раскрывается со ссылками на фигуры и примеры реализации изобретения. На фиг. 1 представлен общий вид устройства для получения дроби из расплава. На фиг. 2 представлен вид сбоку на устройство охлаждения фрагментов расплава металла или сплава. На фиг. 3 представлен вид сверху на устройство охлаждения фрагментов расплава металла или сплава. Общий вид устройства для получения дроби из расплава металла или сплава представлен на фиг. 1. Устройство для получения дроби включает тигель (1), в корпусе которого установлен стакан (2) для размещения в нем расплава (3) металла или сплава, фильеру (4), которая установлена в днище тигля (1), и ванну (5) с охлаждающей жидкостью (6), расположенную под тиглем (1). Между тиглем (1) и ванной (5) установлено заявляемое устройство (7) охлаждения фрагментов расплава, формирующее охлаждающий поток (8) воздушно-капельной смеси. Между корпусом тигля (1) и стаканом (2) предпочтительно размещен теплоизолирующий слой (9). Корпус тигля (1) выполнен, например, из нержавеющей стали, а теплоизолирующий слой (9) представляет собой слой огнеупорной массы, которая является одновременно и футеровкой, и теплоизолятором. Кроме того, для лучшей теплоизоляции и обеспечения равномерной температуры расплава (3) на тигле(1) может быть установлена крышка (10) тигля с заливочным устройством (11). В предпочтительном варианте исполнения днище тигля (1) имеет прямоугольную форму. При этом желательно, чтобы ширина тигля (1) не превышала расстояния В от устройства (7) охлаждения фрагментов расплава до вертикальной плоскости, совпадающей со стенкой тигля (1) (расстояние В показано на фиг. 2, 3). Тигель (1) может быть соединен с механизмом (12) качания через привод (13) механизма качания для обеспечения возвратно-поступательного движения тигля (1) в вертикальном направлении. Предпочтительно, если частота колебаний лежит в диапазоне от 0,5 до 15 Гц. Колебания могут иметь разную форму, например пилообразную. Устройство (7) охлаждения фрагментов расплава может представлять собой форсунку или ряд форсунок, расположенных фронтально по отношению к стенке тигля (1). Является предпочтительным, если форсунки располагаются на уровне С, равном половине расстояния В от тигля (1) до уровня охлаждаю-2 022298 щей жидкости (6) в ванне (5). Также предпочтительно, если расстояние В от форсунки до вертикальной плоскости, совпадающей со стенкой тигля (1), и уголмежду горизонтальной плоскостью и осью форсунки выбираются таким образом, чтобы экстремум верхней ветви параболической траектории охлаждающего потока (8) воздушно-капельной смеси из форсунки совпадал с точкой пересечения днища тигля(1) и его стенки, как это показано на фиг. 2. Расстояние А между фронтально установленными по длине тигля (1) форсунками в горизонтальной плоскости (см. фиг. 3) предпочтительно определяется из соотношения где- угол раскрытия факела форсунки; В - расстояние от форсунки до вертикальной плоскости, совпадающей со стенкой тигля. Ванна (5) имеет заливное отверстие (14) и переливное отверстие (15). В ванне (3) может быть установлен транспортер (16). Расстояние от днища тигля (1) до уровня охлаждающей жидкости (6) в ванне(5) зависит металла или сплава, используемого для получения дроби, и может составлять от 65 до 250 мм. В фильере (4) выполнены каналы (17) (фиг. 2, 3), при прохождении через которые расплав (3) металла или сплава разделяется на фрагменты. Получение дроби посредством заявляемого устройства (7) охлаждения фрагментов расплава работает следующим образом. Из плавильной печи (18) находящийся в ней исходный материал (19) при открытии стопорного устройства (20) подается струей (21) в стакан (2) тигля через заливочное устройство (11). Расплав (3) в тигле проходит через каналы (17) фильеры (4), посредством которых разделяется на фрагменты. Предпочтительно, если при пропускании расплава (3) через фильеру поддерживают постоянный уровень расплава в тигле (1). Далее фрагменты попадают в область охлаждающего потока воздушно-капельной смеси (8), формируемого посредством устройства (7) охлаждения фрагментов расплава. Полному охлаждению фрагменты расплава подвергаются в охлаждающей жидкости (6) ванны (5),откуда полученная дробь может быть извлечена, например, посредством транспортера (16). Температуру верхнего слоя охлаждающей жидкости (6) желательно поддерживать в интервале от 45 до 80 С, например, за счт постоянного притока охлаждающей жидкости (6) в нижний горизонт ванны (5) через заливное отверстие (14), и этом обеспечивать свободное переливание излишков охлаждающей жидкости (6) через переливное отверстие (15) в верхней части ванны (5). В качестве охлаждающей жидкости (6) можно использовать воду или растворы на ее основе. При испытании заявляемого способа в качестве исходного материала был использован алюминиевый лом, который загружали и расплавляли в плавильной печи (18). После расплавления и нагрева до заданной температуры, расплав заливали в тигель (1) через заливочное устройство (11) в крышке (10). При этом температура алюминия в тигле составляла 700-750 С, уровень металла от внутренней поверхности дна составлял 70-90 мм. Уровень контролировался визуально через кварцевое окно и регулировался скоростью подачи металла из плавильной печи. Одновременно с подачей жидкого алюминия в тигель (1) в период прогрева тигля и фильеры запускали привод (13) механизма качания с частотой от 0,5 до 2,0 Гц, при которой обеспечивается минимальный выход расплава (3) через каналы (17) фильеры (4) с целью сокращения технологических отходов перед выходом на рабочий режим. После прогрева тигля (1) фильеры (4) и охлаждающей жидкости (6) в ванне (5) в течение полутора минут установку выводили на рабочий режим, задавая оптимальные значения амплитуды и частоты колебаний тигля (1), что обеспечивало точное дозирование расплава (3) на фрагменты, которые отделялись от нижнего среза канала (17) фильеры (4) в момент изменения направления движения тигля (1) с "вниз" на "вверх". За время нахождения в канале (17) фильеры (4) фрагменты под действием сил поверхностного натяжения принимали сферическую форму и далее охлаждались в две стадии. Фрагменты расплава в виде сформировавшихся сфер попадали в зону первичного охлаждения охлаждающим потоком (8) воздушно-капельной смеси, который формировался таким образом, чтобы воздушно-капельная смесь поступала в пространство под тиглем (1) по навесной траектории, как показано на фиг. 2, не создавая турбулентности и соответственно не нарушая геометрии сферических фрагментов. В результате охлаждающего воздействия происходила кристаллизация фрагментов, их поверхность обретала начальную жсткость, и они не деформировались в результате контакта с поверхностью охлаждающей жидкости (6) в ванне (5), расположенной на расстоянии D от днища тигля (1), равном 175 мм. Расположение форсунок первой стадии охлаждения соответствовало показанному на фиг. 2 и 3. Охлаждающая жидкость (6) в ванне (5) после примерно полутора минут от момента запуска установки разогревалась до температуры 65-85 С, ее температура контролировалась с помощью термодатчика. После достижения заданной температуры через врезанный в днище ванны патрубок заливного отверстия (14) в нижний уровень ванны (1) подавали охлаждающую жидкость с более низкой температурой,обеспечивая тем самым постоянство е температуры в поверхностном слое. Для определения качественных показателей брали дробь, полученную после выхода установки на рабочий режим. Полученная дробь имела следующие характеристики: степень сферичности не менее 97%, отклонение от номинальной массы для дроби в диапазоне заданных размеров от 4 до 8 мм не более 1,0% в весовом отношении. В известных из уровня техники способах для исключения образования жесткой оксидной пленки на поверхностифрагмента алюминиевого расплава и облегчения процесса "втягивания хвостика" в подтигельное пространство податся инертный газ. Этот подход не позволяет решить задачу полностью, поскольку поток защитного газа оказывает динамическое и охлаждающее воздействие на поверхность фрагмента, что препятствует формированию сферы. Кроме того, такой подход привносит дополнительные технические сложности, которые отсутствуют в решении, предлагаемом в заявляемом изобретении. Техническим результатом заявляемого изобретения является получение дроби с высокой степенью сферичности и фракционного состава. ФОРМУЛА ИЗОБРЕТЕНИЯ 1. Устройство охлаждения фрагментов расплава металла или сплава, полученных пропусканием расплава через фильеру, расположенную в днище тигля, включающее устанавливаемую между днищем тигля и расположенной под тиглем ванной по меньшей мере одну форсунку для подачи в подтигельное пространство охлаждающей воздушно-капельной смеси, отличающееся тем, что форсунка размещена с возможностью подачи воздушно-капельной смеси в пространство под тиглем ниспадающим потоком. 2. Устройство охлаждения фрагментов расплава по п.1, отличающееся тем, что оно содержит несколько форсунок, установленных фронтально по отношению к стенке тигля на уровне, равном половине расстояния от днища тигля до уровня охлаждающей жидкости в ванне, а расстояние В от сопла форсунки до вертикальной плоскости, совпадающей со стенкой тигля, и уголмежду горизонтальной плоскостью и осью форсунки выбраны таким образом, чтобы экстремум верхней ветви параболической траектории потока охлаждающей воздушно-капельной смеси из форсунки совпадал с точкой пересечения днища тигля и его стенки. 3. Устройство охлаждения фрагментов расплава по п.2, отличающееся тем, что расстояние А между фронтально установленными по длине тигля форсунками в горизонтальной плоскости определяется из соотношения где- угол раскрытия факела форсунки; В - расстояние от форсунки до вертикальной плоскости, совпадающей со стенкой тигля. 4. Способ охлаждения фрагментов расплава металла или сплава, полученных пропусканием расплава через фильеру, расположенную в днище тигля, посредством устанавливаемой между днищем тигля и расположенной под тиглем ванной по меньшей мере одной форсунки для подачи в подтигельное пространство охлаждающей воздушно-капельной смеси, отличающийся тем, что подачу воздушнокапельной смеси в пространство под тиглем осуществляют ниспадающим потоком. 5. Способ охлаждения фрагментов расплава по п.4, отличающийся тем, что используют несколько форсунок, установленных фронтально по отношению к стенке тигля на уровне, равном половине расстояния от днища тигля до уровня охлаждающей жидкости в ванне, а расстояние В от сопла форсунки до вертикальной плоскости, совпадающей со стенкой тигля, и уголмежду горизонтальной плоскостью и осью форсунки выбирают таким образом, чтобы экстремум верхней ветви параболической траектории потока охлаждающей воздушно-капельной смеси из форсунки совпадал с точкой пересечения днища тигля и его стенки. 6. Способ охлаждения фрагментов расплава по п.5, отличающийся тем, что расстояние А между фронтально установленными по длине тигля форсунками в горизонтальной плоскости определяют из соотношения где- угол раскрытия факела форсунки; В - расстояние от форсунки до вертикальной плоскости, совпадающей со стенкой тигля.
МПК / Метки
Метки: охлаждения, фрагментов, способ, устройство, расплава
Код ссылки
<a href="https://eas.patents.su/7-22298-ustrojjstvo-i-sposob-ohlazhdeniya-fragmentov-rasplava.html" rel="bookmark" title="База патентов Евразийского Союза">Устройство и способ охлаждения фрагментов расплава</a>
Предыдущий патент: Способ и устройство термической обработки рельсов
Следующий патент: Пирролидиноны в качестве ингибиторов metap-2
Случайный патент: Способ форматирования данных для их передачи