Способ предварительной обработки интегрированной катализаторной суспензии без подложки
Формула / Реферат
1. Способ гидроочистки тяжелых масел, где указанный способ содержит по меньшей мере одну стадию реакции гидроочистки для гидроочистки тяжелых масел и использует активную катализаторную суспензию, включающий предварительную обработку активной катализаторной суспензии водородом в блоке предварительной обработки перед ее подачей на стадию реакции для увеличения температуры и уменьшения ударной нагрузки на активную катализаторную суспензию, увеличивая таким образом конверсию тяжелых масел, причем перед предварительной обработкой активная катализаторная суспензия синтезируется в результате взаимодействия металлов групп VIII и VIB с легким углеводородом, сульфатом аммония и аммиачным газом с образованием активной катализаторной суспензии в масле.
2. Способ по п.1, в котором условия в блоке предварительной обработки включают температуру в пределах 400-1000°F (204-538°С).
3. Способ по любому из пп.1-2, в котором условия в блоке предварительной обработки включают давление в пределах 100-3000 фунтов/дюйм2 (689-20684 кПа).
4. Способ по любому из пп.1-3, в котором расход водорода в блоке предварительной обработки находится в пределах 2500-7500 станд.футов3/баррель (593339-1780017 л/м3).
5. Способ по любому из пп.1-4, в котором в блоке предварительной обработки продолжительность нахождения катализаторной суспензии составляет от 1,5 до 3 ч.
6. Способ гидроочистки тяжелых масел, включающий:
(а) взаимодействие потока исходного углеводородного продукта в условиях гидроочистки суспензии водородным потоком и потоком, содержащим катализаторную суспензию гидроочистки, в блоке гидроочистки суспензии вакуумного остатка и извлечение потока продукта, а также потока, содержащего отработанную катализаторную суспензию гидроочистки и не преобразованный исходный углеводородный продукт;
(б) прохождение потока, содержащего отработанную катализаторную суспензию гидроочистки и не преобразованный исходный углеводородный продукт, в блок обезмасливания, где он соединяется с растворителем, продуктами и газами, затем извлекаемыми;
(в) прохождение потока, содержащего отработанную катализаторную суспензию, в блок извлечения металлов, где он контактирует с аммониевым выщелачивающим раствором для извлечения сульфата аммония и соединений, содержащих металлы групп VIII и VIB;
(г) подачу соединений, содержащих металлы групп VIII и VIB, в блок синтеза катализатора, где они контактируют с аммиаком, газообразным сернистым водородом, углеводородным потоком, который не является тяжелыми маслами, водородом и небольшим количеством воды для создания активной катализаторной суспензии в масле, причем в масле, содержащем сульфат аммония;
(д) прохождение активной катализаторной суспензии в масле в блок предварительной обработки с потоком водорода для повышения температуры и сокращения ударной нагрузки на активную катализаторную суспензию, увеличивая таким образом уровень преобразования тяжелых масел, при этом выходящий поток контактирует с водородом и разлагается на сернистый водород и аммиак;
(е) прохождение выходящего потока стадии (д), содержащего активную катализаторную суспензию в масле, в хранилище или в блок гидроочистки суспензии вакуумного остатка.
7. Способ по п.6, в котором условия гидрообработки суспензии выбираются из группы, состоящей из гидрокрекинга, гидрообработки, гидрообессеривания, гидроденитрификации и гидродеметаллизации.
8. Способ по п.7, в котором способ является гидрокрекингом суспензии и в котором гидрокрекинг суспензии происходит при температуре по меньшей мере 800°F (427°C) с давлением водорода от 1500 до 3500 фунтов/дюйм2 (от 10342 до 24132 кПа).
9. Способ по п.1, в котором поток, содержащий отработанную катализаторную суспензию, подвергается последовательным стадиям экстракции растворителем и кристаллизации в блоке извлечения металлов в целях извлечения сульфата аммония, а также соединений, содержащих металлы групп VIII и VIB.
10. Способ по п.1, в котором металлом группы VIII является никель и металлом группы VIB является молибден.
11. Способ по п.1, в котором условия в блоке синтеза катализатора включают температуру в пределах 80-200°F (27-93°С) и давление в пределах 100-3000 фунтов/дюйм2изб. (689-20684 кПа).
12. Способ по п.1, в котором условия в блоке предварительной обработки включают температуру в пределах 400-1000°F (204-538°С), давление в пределах 100-3000 фунтов/дюйм2изб. (689-20684 кПа), расход водорода в пределах 2500-7500 станд.футов3/баррель (593339-1780017 л/м3) и продолжительность нахождения в блоке предварительной обработки от 1,5 до 3 ч.
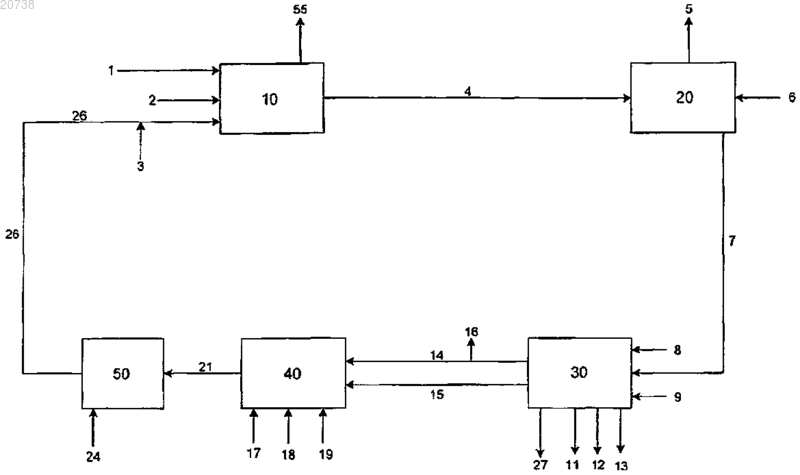
Текст
СПОСОБ ПРЕДВАРИТЕЛЬНОЙ ОБРАБОТКИ ИНТЕГРИРОВАННОЙ КАТАЛИЗАТОРНОЙ СУСПЕНЗИИ БЕЗ ПОДЛОЖКИ Способ гидроочистки суспензии, включающий в себя предварительную обработку катализаторной суспензии для улучшения активности в установке гидроочистки вакуумного остатка. Предварительная обработка катализаторной суспензии повышает ее температуру, таким образом уменьшая ударную нагрузку, получаемую катализаторной суспензией при входе в реактор. Область техники изобретения Изобретение касается способа гидроочистки суспензии, включающего предварительную подготовку катализаторной суспензии для улучшения технологического способа в блоках гидроочистки вакуумного остатка. Уровень техники Составы катализаторной суспензии, средства для их приготовления и их использование в гидроочистке тяжелых исходных продуктов известны в области техники нефтепереработки. Некоторые примеры рассматриваются ниже. Патент США 4710486 раскрывает способ приготовления диспергированного металлсульфидного катализатора соединения сульфида металла группы VIB гидроочистки масла. Стадии способа включают в себя реакцию водного раствора аммиака и соединения металла, такого как оксид молибдена или оксид вольфрама, для образования водорастворимого кислородсодержащего соединения,такого как молибденовокислый аммоний или вольфрамовокислый аммоний. Патент США 4970190 описывает способ приготовления диспергированного сульфидного катализатора металла группы VIB для использования в гидроочистке нефтяного масла. Этот катализатор активируется соединением металла группы VIII. Стадии способа включают в себя растворение соединения металла группы VIB, такого как оксид молибдена или оксид вольфрама, с аммиаком для образования водорастворимого соединения, такого как водосодержащий молибденовокислый аммоний или водосодержащий вольфрамовокислый аммоний. Способы гидроочистки суспензии часто происходят при температурах более высоких, чем те, при которых суспензии, содержащие катализаторы, синтезируются и хранятся. Например, способ гидрокрекинга суспензии в патенте США 20060054533 обычно проходит при температуре не менее 800F (не менее 427 С) с давлением водорода от приблизительно 1500 до приблизительно 3500 фунтов/дюйм 2 (от приблизительно 10342 до приблизительно 24131 кПа). Катализаторные суспензии обычно поступают в реактор (или первичный реактор, если их несколько) вакуумной установки переработки остатка при температуре приблизительно 450F (приблизительно 232 С) и давлении водорода приблизительно 400 фунтов/дюйм 2 (приблизительно 2758 кПа). Эта разница температуры и давления создает ударную нагрузку на высокоактивную катализаторную суспензию и активизирует образование кокса. Образование кокса снижает эффективность преобразования данным катализатором. Сущность изобретения Изобретение описывает способ гидроочистки суспензии, в частности гидрокрекинга суспензии, в котором катализаторная суспензия проходит предварительную обработку до поступления в реактор (реакторы) способа гидроочистки суспензии вакуумного остатка. Предварительная обработка катализаторной суспензии повышает ее температуру, таким образом уменьшая ударную нагрузку, получаемую катализаторной суспензией при поступлении в реактор. Способ согласно изобретению складывается следующим образом. Способ гидроочистки тяжелых масел, имеющий по меньшей мере одну стадию реакции, включает следующие стадии:(а) взаимодействие потока исходного углеводородного продукта в условиях гидроочистки суспензии водородным потоком и потоком, содержащим катализатор гидроочистки суспензии, в блоке гидроочистки суспензии вакуумного остатка и извлечение потока продукта, а также потока, содержащего отработанную катализаторную суспензию гидроочистки и не преобразованный углеводородный исходный продукт;(б) прохождение потока, содержащего отработанную катализаторную суспензию гидроочистки и не преобразованный углеводородный исходный продукт, в блок обезмасливания, где он соединяется с растворителем, продукты и газы затем извлекают, а также и поток, содержащий отработанную катализаторную суспензию;(в) прохождение потока, содержащего отработанную катализаторную суспензию, в блок извлечения металлов, где он контактирует с аммониевым выщелачивающим раствором для извлечения сульфата аммония и соединений, содержащих металлы групп VIII и VIB;(г) подачу соединений, содержащих металлы групп VIII и VIB, в блок синтеза катализатора, где они контактируют с аммиаком, газообразным сернистым водородом, углеводородным потоком, водородом и небольшим количеством воды, для создания активной катализаторной суспензии в масле, причем в масле, содержащем сульфат аммония;(д) прохождение выходящего потока стадии (г) в блок предварительной обработки для повышения температуры и сокращения ударной нагрузки на катализаторную суспензию, при этом выходящий поток контактирует с водородом и разлагается на сернистый водород и аммиак, потоки которых удаляются из блока предварительной обработки;(е) прохождение выходящего потока стадии (д), содержащего активную катализаторную суспензию,в масле в хранилище или в блок гидроочистки суспензии вакуумного остатка. Краткое описание чертежа На чертеже показан способ, описанный в настоящем изобретении, для гидроочистки суспензии ва-1 020738 куумного остатка с использованием предварительно обработанной катализаторной суспензии. Подробное описание изобретения Поток 1, содержащий водород, поступает в блок 10 гидроочистки суспензии вакуумного остатка(VRHU). Способы гидроочистки, которые могут применяться в настоящем изобретении, включают в себя гидрокрекинг, гидроочистку, гидрообессеривание, гидроденитрификацию и гидродеметаллизацию. Гидрокрекинг вместе с тем является предпочтительным способом. Также в блок 10 гидроочистки суспензии вакуумного остатка (VRHU) поступает поток 2 исходного продукта (вакуумный остаток является исходным продуктом), поток 3 водорода и поток 26 катализаторной суспензии (который может быть подмешан к потоку 3, содержащему воду). Способ гидрокрекинга суспензии обычно работает при температуре по меньшей мере 800F (427C) с давлением водорода от приблизительно 1500 до приблизительно 3500 фунт/дюйм 2 (от приблизительно 10342 до приблизительно 24131 кПа). Катализаторная суспензия после предварительной обработки обычно поступает в реактор (или начальный реактор, если их несколько) в блоке гидроочистки вакуумного остатка при температуре приблизительно 700F (приблизительно 371 С) и давлении водорода приблизительно 2000 фунт/дюйм 2 (приблизительно 13789 кПа). Продукты обработки выходят из блока 10 гидроочистки суспензии вакуумного остатка (VRHU) через поток 55. Поток 4 отработанной катализаторной суспензии, содержащий непреобразованное масло,поступает в блок 20 обезмасливания, где контактирует с растворителем (поток 6), таким как толуол или нафта, для удаления продуктов обработки и газов (поток 5). Обезмасливание включает в себя концентрацию твердой фазы и удаление жидкости, в которых можно использовать стадии фильтрования в перекрестном потоке, центрифугирования, сушки и квенчинга. Поток 7 содержит обезмасленную отработанную катализаторную суспензию. Поток 7 поступает в блок 30 извлечения металлов (MRU). Обогащенный воздух поступает в блок 30 извлечения металлов(MRU) через поток 8. Поток 9 является раствором, подходящим для извлечения металлов, таким как кетоксим. Путем серии стадий экстракции растворителем и кристаллизации в блоке 30 извлечения металлов (MRU) металлы из масляного потока извлекаются вместе с побочным продуктом сульфатом аммония(поток 27). Ванадий удаляется через поток 11 в виде V2O5. Отработанный растворитель извлечения металлов удаляется через поток 12 и сточная вода удаляется через поток 13. Металлом группы VIII, используемым в CASH способе, часто является никель. Никель извлекается,как поток сульфата никеля (поток 14) и пропускается в блок 40 синтеза катализатора (CSU). Часть потока сульфата никеля (поток 16) может быть отведена, чтобы контролировать количество никеля, поступающего в блок 40 синтеза катализатора (CSU). Извлеченные металлы группы VI, такие как молибден, выходят из блока извлечения металлов (MRU) в потоке 15. Если металл является молибденом, он извлекается как поток димолибдата аммония (поток 15), который проходит в блок 40 синтеза катализатора (CSU). Легкий углеводород или вакуумный газойль (VGO) (поток 17) поступает в блок 40 синтеза катализатора(CSU) с небольшим количеством воды (поток 18). Поток 19 содержит водород. В блоке 40 синтеза катализатора (CSU) условия включают в себя температуру в пределах 80-200F(2068-3447 кПа). Ингредиенты смешиваются в блоке 40 синтеза катализатора (CSU) для формирования активной катализаторной суспензии в масле. Небольшое количество сульфата аммония, образованное сульфатом никеля, и аммиачный газ, добавленный в блок 40 синтеза катализатора (CSU), также присутствуют в этом потоке. Небольшой поток воды (поток 18) служит для поддержания небольшого количества сульфата аммония в растворе. Это предотвращает образование осадка в оборудовании. Активная катализаторная суспензия в масле (поток 21) поступает в блок 50 предварительной обработки катализатора(CPU). Водород поступает в блок 50 предварительной обработки катализатора (CPU) через поток 24. Условия технологического способа блока 50 предварительной обработки катализатора (CPU) включают в себя температуру в пределах от приблизительно 400 до приблизительно 1000F (от приблизительно 204 до приблизительно 538 С), предпочтительно от приблизительно 500 до приблизительно 800F (от приблизительно 260 до приблизительно 427 С) и наиболее предпочтительно от приблизительно 600 до приблизительно 700F (от приблизительно 316 до приблизительно 371 С). Давление изменяется от приблизительно 100 до приблизительно 3000 фунт/дюйм 2 (от приблизительно 689 до приблизительно 20684 кПа), предпочтительно от 300 до приблизительно 2500 фунт/дюйм 2 (от 2068 до приблизительно 17237 кПа) и более предпочтительно от приблизительно 500 до приблизительно 2000 фунт/дюйм 2 (от приблизительно 3447 до приблизительно 13789 кПа). Уровень водорода составляет в пределах 2500-7500 станд.футов 3 газа/баррель (593339-1780017 л/м 3), предпочтительно 5000-6000 станд.футов 3 газа/баррель(118668-1424014 л/м 3). Предварительная обработка сульфата аммония в сероводород и аммиак требует приблизительно 2 ч. Продолжительность нахождения в блоке предварительной обработки катализатора(CPU) для смеси, содержащей масло, суспензию и сульфат аммония, составляет от 1,5 до 3 ч, предпочтительно приблизительно 2 ч. На каждый моль сернистого водорода, произведенного в блоке 50 предварительной обработки ката-2 020738 лизатора (CPU), производится 2 моль аммиака. Блок 50 предварительной обработки катализатора (CPU) представляет собой проточный реактор с перемешиванием (CSTR или иначе - реактор идеального смешения). Реактор данного типа применяют для предотвращения агломерирования катализатора. Исходным продуктом 2 остатка для переработки в способе согласно настоящему изобретению является углеводородное вещество с высокой температурой кипения, имеющее обычный интервал кипения,главным образом, выше 600F (выше 316 С), часто имеющее интервал точки кипения, в котором по меньшей мере 80% объема к объему подачи кипит между 600 и 1500F (между 316 и 816 С) или между 800 и 1450F (между 427 и 788 С). Исходные продукты остатка, с пользой перерабатываемые в способе согласно настоящему изобретению, могут иметь содержание асфальтенов более 500 или 1000 ч/млн и могут иметь содержание асфальтенов до 10000 ч/млн или более. Остатки исходного продукта также обычно содержат более 10 ч/млн металлов и более 0,1 мас.% серы. Считается, что металлы должны присутствовать как органометаллические соединения, но концентрация металлов, относящаяся к данному документу, рассчитывается в частях на миллион чистого металла. Загрязняющие металлы в подаче обычно включают в себя никель, ванадий и железо. Сера присутствует в виде органических серных составов, весовой процент серы рассчитывается на основе свободной серы. Типичный исходный продукт для настоящего изобретения включает в себя деасфальтированный остаток или дистиллят нефти, остатки колонны атмосферной дистилляции сырой нефти (слабо крекированная сырая нефть или остаток атмосферной колонны) или остатки колонны вакуумной дистилляции (вакуумный остаток). Пример. Типичные свойства исходного продукта вакуумного остатка приведены ниже. Типичные условия способа, используемые для обогащения тяжелого масла, перечислены ниже. Две партии потоков катализаторной суспензии, полученные, как описано выше, направлены в установку гидрокрекинга вакуумного остатка (VRHU) для использования в качестве катализатора. Первая партия посылается в установку гидрокрекинга вакуумного остатка (VRHU) напрямую из блока синтеза катализатора или из хранилища без предварительной обработки. Вторая партия была предварительно обработана в водороде, как показано на чертеже, до поступления в установку гидрокрекинга вакуумного остатка (VRHU). Наглядное сравнение показателей работы установки гидрокрекинга вакуумного остатка (VRHU) с обработанной катализаторной суспензией и необработанной катализаторной суспензией, представлены ниже: Улучшение приблизительно эквивалентно увеличению дозировки свежего катализатора в установке гидрокрекинга вакуумного остатка (VRHU) на 30%. ФОРМУЛА ИЗОБРЕТЕНИЯ 1. Способ гидроочистки тяжелых масел, где указанный способ содержит по меньшей мере одну стадию реакции гидроочистки для гидроочистки тяжелых масел и использует активную катализаторную суспензию, включающий предварительную обработку активной катализаторной суспензии водородом в блоке предварительной обработки перед ее подачей на стадию реакции для увеличения температуры и уменьшения ударной нагрузки на активную катализаторную суспензию, увеличивая таким образом конверсию тяжелых масел, причем перед предварительной обработкой активная катализаторная суспензия синтезируется в результате взаимодействия металлов групп VIII и VIB с легким углеводородом, сульфатом аммония и аммиачным газом с образованием активной катализаторной суспензии в масле. 2. Способ по п.1, в котором условия в блоке предварительной обработки включают температуру в пределах 400-1000F (204-538 С). 3. Способ по любому из пп.1-2, в котором условия в блоке предварительной обработки включают давление в пределах 100-3000 фунтов/дюйм 2 (689-20684 кПа). 4. Способ по любому из пп.1-3, в котором расход водорода в блоке предварительной обработки находится в пределах 2500-7500 станд.футов 3/баррель (593339-1780017 л/м 3). 5. Способ по любому из пп.1-4, в котором в блоке предварительной обработки продолжительность нахождения катализаторной суспензии составляет от 1,5 до 3 ч. 6. Способ гидроочистки тяжелых масел, включающий:(а) взаимодействие потока исходного углеводородного продукта в условиях гидроочистки суспензии водородным потоком и потоком, содержащим катализаторную суспензию гидроочистки, в блоке гидроочистки суспензии вакуумного остатка и извлечение потока продукта, а также потока, содержащего отработанную катализаторную суспензию гидроочистки и не преобразованный исходный углеводородный продукт;(б) прохождение потока, содержащего отработанную катализаторную суспензию гидроочистки и не преобразованный исходный углеводородный продукт, в блок обезмасливания, где он соединяется с растворителем, продуктами и газами, затем извлекаемыми;(в) прохождение потока, содержащего отработанную катализаторную суспензию, в блок извлечения металлов, где он контактирует с аммониевым выщелачивающим раствором для извлечения сульфата аммония и соединений, содержащих металлы групп VIII и VIB;(г) подачу соединений, содержащих металлы групп VIII и VIB, в блок синтеза катализатора, где они контактируют с аммиаком, газообразным сернистым водородом, углеводородным потоком, который не является тяжелыми маслами, водородом и небольшим количеством воды для создания активной катализаторной суспензии в масле, причем в масле, содержащем сульфат аммония;(д) прохождение активной катализаторной суспензии в масле в блок предварительной обработки с потоком водорода для повышения температуры и сокращения ударной нагрузки на активную катализаторную суспензию, увеличивая таким образом уровень преобразования тяжелых масел, при этом выходящий поток контактирует с водородом и разлагается на сернистый водород и аммиак;(е) прохождение выходящего потока стадии (д), содержащего активную катализаторную суспензию в масле, в хранилище или в блок гидроочистки суспензии вакуумного остатка. 7. Способ по п.6, в котором условия гидрообработки суспензии выбираются из группы, состоящей из гидрокрекинга, гидрообработки, гидрообессеривания, гидроденитрификации и гидродеметаллизации. 8. Способ по п.7, в котором способ является гидрокрекингом суспензии и в котором гидрокрекинг суспензии происходит при температуре по меньшей мере 800F (427C) с давлением водорода от 1500 до 3500 фунтов/дюйм 2 (от 10342 до 24132 кПа). 9. Способ по п.1, в котором поток, содержащий отработанную катализаторную суспензию, подвергается последовательным стадиям экстракции растворителем и кристаллизации в блоке извлечения металлов в целях извлечения сульфата аммония, а также соединений, содержащих металлы групп VIII и VIB. 10. Способ по п.1, в котором металлом группы VIII является никель и металлом группы VIB является молибден. 11. Способ по п.1, в котором условия в блоке синтеза катализатора включают температуру в пределах 80-200F (27-93 С) и давление в пределах 100-3000 фунтов/дюйм 2 изб. (689-20684 кПа). 12. Способ по п.1, в котором условия в блоке предварительной обработки включают температуру в пределах 400-1000F (204-538 С), давление в пределах 100-3000 фунтов/дюйм 2 изб. (689-20684 кПа), расход водорода в пределах 2500-7500 станд.футов 3/баррель (593339-1780017 л/м 3) и продолжительность нахождения в блоке предварительной обработки от 1,5 до 3 ч.
МПК / Метки
МПК: C10G 47/00
Метки: обработки, интегрированной, предварительной, суспензии, способ, подложки, катализаторной
Код ссылки
<a href="https://eas.patents.su/6-20738-sposob-predvaritelnojj-obrabotki-integrirovannojj-katalizatornojj-suspenzii-bez-podlozhki.html" rel="bookmark" title="База патентов Евразийского Союза">Способ предварительной обработки интегрированной катализаторной суспензии без подложки</a>
Предыдущий патент: Система и способ получения циклогексана
Следующий патент: Способы и композиции для замедления набора веса, связанного с применением атипичных антипсихотических препаратов
Случайный патент: Способ производства гранулированных комбикормов