Криогенная система для удаления кислотных газов из потока газообразных углеводородов
Формула / Реферат
1. Система для удаления кислотных газов из потока сырьевого газа, содержащая
криогенную дистилляционную колонну, имеющую зону регулируемого замораживания, которая принимает распыляемую холодную жидкость, главным образом метан, причем колонна принимает и затем разделяет поток сырьевого газа на поток газообразного головного метанового погона и, по существу, твердый материал, состоящий из осажденного диоксида углерода;
холодильное оборудование, расположенное по потоку после криогенной дистилляционной колонны, для охлаждения потока, головного метанового погона и возвращения его части в криогенную дистилляционную колонну в качестве холодной распыляемой жидкости;
коллекторную тарелку, расположенную под зоной регулируемого замораживания, для приема, по существу, твердого материала, когда он осаждается в зоне регулируемого замораживания, и направления, по существу, твердого материала из криогенной дистилляционной колонны;
первый фильтр для приема, по существу, твердого материала и разделения, по существу, твердого материала на поток, содержащий первый фильтрационный осадок, в основном состоящий из диоксида углерода, и поток, содержащий фильтрат, содержащий нетвердый материал, представляющий собой по меньшей мере один из группы, состоящей из этана, пропана, бутана или сероводорода;
промывной резервуар для промывания первого фильтрационного осадка с использованием потока холодного диоксида углерода и получения первой твердофазно-жидкостной суспензии;
второй фильтр для приема первой твердофазно-жидкостной суспензии и разделения первой твердофазно-жидкостной суспензии на второй фильтрационный осадок, содержащий главным образом твердый диоксид углерода, и второй фильтрат, включающий нетвердый материал, представляющей собой по меньшей мере одно из группы, состоящей из этана, пропана, бутана или сероводорода; и
жидкостный возвратный трубопровод для возвращения по меньшей мере части нетвердого первого фильтрата или второго фильтрата в криогенную дистилляционную колонну.
2. Система по п.1, в которой коллекторная тарелка содержит спускную трубу, в которую падает осажденный, по существу, твердый материал.
3. Система по п.1, в которой коллекторная тарелка направляет, по существу, твердый материал из криогенной дистилляционной колонны (i) гравитационным течением, (ii) действием механического транспортного устройства, (iii) с помощью распыления части холодной распыляемой жидкости в коллекторную тарелку и, по существу, на твердый материал или (iv) их комбинацией.
4. Система по п.3, в которой коллекторная тарелка содержит спускную трубу, в которую падает осажденный, по существу, твердый материал; и механическое транспортное устройство, такое как шнек, который размещен внутри спускной трубы.
5. Система по п.1, в которой криогенная дистилляционная колонна дополнительно содержит верхнюю ректификационную зону над зоной регулируемого замораживания и нижнюю дистилляционную зону под зоной регулируемого замораживания, причем криогенная дистилляционная колонна выполнена с возможностью приема потока сырьевого газа в нижнюю дистилляционную зону.
6. Система по п.5, в которой криогенная дистилляционная колонна выполнена с возможностью выведения кубового потока из нижней дистилляционной зоны, причем кубовый поток содержит кислотные газы в жидкостной фазе; при этом по меньшей мере часть первого фильтрата возвращается в нижнюю дистилляционную зону по жидкостному возвратному трубопроводу.
7. Система по п.6, в которой кубовый сырьевой поток содержит метан, диоксид углерода, этан, пропан, бутан, сероводород, ароматические углеводороды или их комбинации, по существу, в жидкостной фазе.
8. Система по п.1, в которой первый фильтр включает (i) пористую среду, (ii) один или более фильтр-пресс, (iii) один или более ленточный фильтр, (iv) гидроциклон, (v) центробежный сепаратор или (vi) их комбинации.
9. Система по п.6, в которой коллекторная тарелка действует при температуре от около -70 до -80°F (от -56,7 до -62,2°С).
10. Система по п.1, в которой промывной резервуар содержит смеситель для перемешивания первого фильтрационного осадка, чтобы получить первую твердофазно-жидкостную суспензию.
11. Система по п.1, в которой второй фильтр содержит пористую среду.
12. Система по п.1, выполненная с возможностью объединения первого фильтрата и второго фильтрата и возвращения объединенного первого фильтрата и второго фильтрата в нижнюю дистилляционную зону в качестве жидкого материала.
13. Система по п.12, в которой первый фильтрат дополнительно содержит диоксид углерода, сероводород или их комбинации.
14. Система по п.1, дополнительно содержащая теплообменник, нагревающий, по существу, твердый материал, отобранный в основном из фильтрационного осадка конечной стадии, для получения потока в основном чистого диоксида углерода в жидкостной фазе; при этом поток холодного диоксида углерода содержит часть потока в основном чистого диоксида углерода.
15. Система по п.14, в которой фильтрационный осадок конечной стадии получен после первого фильтра на втором фильтре или третьем фильтре.
16. Система по п.5, в которой поток сырьевого газа содержит сероводород; система дополнительно содержит систему для удаления сероводорода, выполненную с возможностью удаления значительной части сероводорода из потока сырьевого газа до нагнетания потока сырьевого газа в криогенную дистилляционную колонну.
17. Система по п.1, в которой криогенная дистилляционная колонна дополнительно содержит верхнюю ректификационную зону над зоной регулируемого замораживания; при этом криогенная дистилляционная колонна выполнена с возможностью приема потока сырьевого газа в зону регулируемого замораживания.
18. Система по п.17, в которой жидкостной возвратный трубопровод объединяет по меньшей мере часть первого или второго фильтрата с потоком сырьевого газа перед нагнетанием потока сырьевого газа в криогенную дистилляционную колонну.
19. Система по п.18, дополнительно содержащая дистилляционный сепаратор, выполненный с возможностью приема второго фильтрата и для получения потока кубовой жидкости, включающей диоксид углерода, H2S или их комбинации в жидкостной фазе, и потока извлеченного метана; при этом поток извлеченного метана объединяют с потоком головного метанового погона.
20. Система по п.19, в которой каждый из первого фильтрата и потока кубовой жидкости дополнительно включает сероводород.
21. Способ удаления кислотных газов из потока обезвоженного сырьевого газа с помощью системы по п.1, согласно которому
готовят криогенную дистилляционную колонну, причем колонна имеет зону регулируемого замораживания, которая принимает холодную распыляемую жидкость, содержащую главным образом метан, и коллекторную тарелку под зоной регулируемого замораживания;
нагнетают поток сырьевого газа в криогенную дистилляционную колонну;
подвергают поток сырьевого газа глубокому охлаждению, чтобы вызвать осаждение диоксида углерода внутри потока сырьевого газа на коллекторную тарелку в виде, по существу, твердого материала, в то же время обеспечивая значительное испарение метана и выход его из криогенной дистилляционной колонны в виде потока, представляющего собой поток головного метанового погона;
пропускают поток головного метанового погона через холодильную систему, расположенную по потоку после криогенной дистилляционной колонны, причем холодильная система охлаждает поток головного метанового погона;
возвращают часть охлажденного потока головного метанового погона в криогенную дистилляционную колонну в виде жидкой флегмы, служащей в качестве холодной распыляемой жидкости;
удаляют, по существу, твердый материал из криогенной дистилляционной колонны в виде суспензии;
разделяют, по существу, твердый материал в первом фильтре на поток, содержащий первый фильтрационный осадок, состоящий из твердого материала, состоящего в основном из диоксида углерода, и поток, содержащий первый фильтрат, представляющий собой жидкий материал, содержащий один из группы, состоящей из этана, пропана, бутана или сероводорода;
промывают первый фильтрационный осадок с использованием потока холодного диоксида углерода для создания первой твердофазно-жидкостной суспензии;
разделяют первую твердофазно-жидкостную суспензию на второй фильтрационный осадок, состоящий в основном из твердой двуокиси углерода, и второй фильтрат, представляющий собой жидкий материал, содержащий по меньшей мере один из группы, состоящей из этана, пропана, бутана или сероводорода; и
возвращают по меньшей мере часть жидкого материала из первого или второго фильтратов в криогенную дистилляционную колонну.
22. Способ по п.21, согласно которому коллекторная тарелка содержит спускную трубу, в которую падает осажденный, по существу, твердый материал и механическое транспортное устройство внутри спускной трубы; при этом при удалении, по существу, твердого материала из криогенной дистилляционной колонны с помощью механического транспортного устройства перемещают, по существу, твердый материал из спускной трубы за пределы криогенной дистилляционной колонны.
23. Способ по п.21, согласно которому коллекторная тарелка содержит спускную трубу, в которую падает осажденный, по существу, твердый материал, и с помощью коллекторной тарелки направляют, по существу, твердый материал из криогенной дистилляционной колонны (i) гравитационным течением, (ii) действием механического транспортного устройства, (iii) с помощью распыления части холодной распыляемой жидкости в коллекторную тарелку и, по существу, на твердый материал или (iv) их комбинацией.
24. Способ по п.21, согласно которому криогенная дистилляционная колонна дополнительно содержит верхнюю ректификационную зону над промежуточной зоной регулируемого замораживания и нижнюю дистилляционную зону под промежуточной зоной регулируемого замораживания и поток сырьевого газа нагнетают в нижнюю дистилляционную зону.
25. Способ по п.24, согласно которому дополнительно выводят кубовый поток из нижней дистилляционной зоны, причем кубовый поток содержит кислотные газы в жидкостной фазе, и при возвращении по меньшей мере части жидкого материала в криогенную дистилляционную колонну подают жидкий материал в нижнюю дистилляционную зону.
26. Способ по п.25, согласно которому кубовый поток содержит метан, этан, пропан, бутан, сероводород, диоксид углерода или их комбинации, по существу, в жидкостной фазе.
27. Способ по п.21, согласно которому смешивают первый фильтрационный осадок с потоком холодного диоксида углерода для получения первой твердофазно-жидкостной суспензии.
28. Способ по п.21, согласно которому дополнительно объединяют первый фильтрат и второй фильтрат; при этом второй жидкий материал, который возвращают в нижнюю дистилляционную зону, содержит объединенные первый фильтрат и второй фильтрат.
29. Способ по п.21, согласно которому дополнительно нагревают, по существу, твердый материал, отобранный в основном из фильтрационного осадка конечной стадии, для получения потока, по существу, чистого диоксида углерода в жидкостной фазе; при этом поток холодного диоксида углерода содержит часть потока, по существу, чистого диоксида углерода.
30. Способ по п.29, согласно которому при нагревании пропускают, по существу, твердый материал, отобранный в основном из фильтрационного осадка конечной стадии, через такой теплообменник, в котором происходит теплообмен с потоком сырьевого газа.
31. Способ по п.21, согласно которому первый фильтр содержит пористую среду или центрифугу.
32. Способ по п.21, согласно которому поток обезвоженного сырьевого газа включает сероводород и согласно которому дополнительно удаляют значительную часть сероводорода из потока сырьевого газа до нагнетания потока сырьевого газа в криогенную дистилляционную колонну.
33. Способ по п.21, согласно которому криогенная дистилляционная колонна дополнительно содержит верхнюю ректификационную зону над промежуточной зоной регулируемого замораживания и поток сырьевого газа нагнетают в зону регулируемого замораживания.
34. Способ по п.21, согласно которому при возвращении по меньшей мере части первого фильтрата в криогенную дистилляционную колонну (i) нагнетают первый фильтрат непосредственно обратно в зону регулируемого замораживания или (ii) объединяют первый фильтрат с потоком сырьевого газа перед нагнетанием потока сырьевого газа в криогенную дистилляционную колонну.
35. Способ по п.21, согласно которому дополнительно промывают второй фильтрационный осадок с использованием потока холодного диоксида углерода; перемешивают второй фильтрационный осадок для получения твердофазно-жидкостной суспензии и подают твердофазно-жидкостную суспензию на третий фильтр, тем самым получая третий фильтрационный осадок, состоящий главным образом из твердого диоксида углерода, и третий фильтрат, содержащий метан, диоксид углерода и сероводород в жидкостной фазе.
36. Способ по п.35, согласно которому дополнительно объединяют второй фильтрат и третий фильтрат; нагнетают второй фильтрат и третий фильтрат в дистилляционный сепаратор, тем самым получая поток кубовой жидкости, состоящий главным образом из диоксида углерода в жидкостной фазе, и извлеченный поток, содержащий по меньшей мере один из группы, состоящей из этана, пропана, бутана или сероводорода.
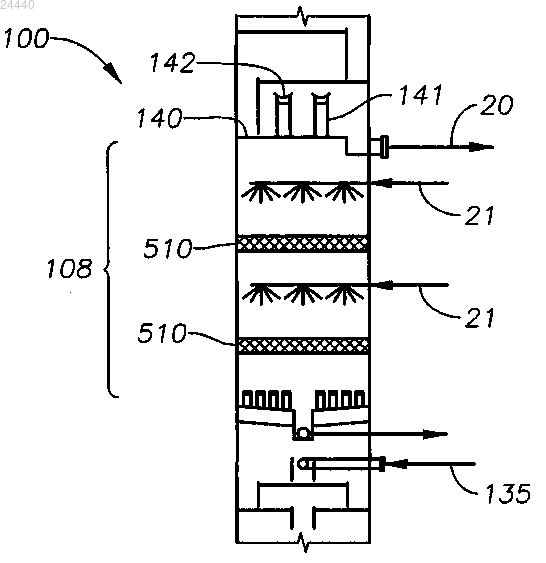
Текст
КРИОГЕННАЯ СИСТЕМА ДЛЯ УДАЛЕНИЯ КИСЛОТНЫХ ГАЗОВ ИЗ ПОТОКА ГАЗООБРАЗНЫХ УГЛЕВОДОРОДОВ Представлена система для удаления кислотных газов из потока сырьевого газа. Система содержит криогенную дистилляционную колонну. Криогенная дистилляционная колонна имеет зону регулируемого замораживания, которая принимает холодную распыляемую жидкость, состоящую главным образом из метана. Колонна принимает и затем разделяет поток сырьевого газа на поток газообразного верхнего метанового погона и, по существу, твердый материал, состоящий из диоксида углерода. Система содержит коллекторную тарелку под зоной регулируемого замораживания. Коллекторная тарелка принимает, по существу, твердый материал, когда он осаждается в зоне регулируемого замораживания. Система также имеет фильтр. Фильтр принимает,по существу, твердый материал и затем разделяет его на твердый материал, состоящий в основном из диоксида углерода, и жидкий материал, содержащий метан. Твердый материал может быть нагрет как жидкость и продан, тогда как жидкий материал возвращают в криогенную дистилляционную колонну. Каллинэйн Джон Тим, Нортроп Пол Скотт (US) Медведев В.Н. (RU)(71)(73) Заявитель и патентовладелец: ЭКСОНМОБИЛ АПСТРИМ РИСЕРЧ КОМПАНИ (US) Область техники, к которой относится изобретение Настоящее изобретение относится к области разделения компонентов. Более конкретно, настоящее изобретение относится к отделению диоксида углерода и других кислотных газов от потока газообразных углеводородов. Уровень техники Добыча углеводородов из пластового резервуара зачастую сопровождается побочным извлечением неуглеводородных газов. Такие газы включают загрязняющие примеси, такие как сероводород (H2S) и диоксид углерода (CO2). Когда H2S и CO2 извлекают как часть потока газообразных углеводородов (таких как метан или этан), газовый поток иногда называют "сернистым нефтяным газом". Сернистый нефтяной газ обычно подвергают обработке для удаления CO2, H2S и других загрязняющих примесей перед направлением его ниже по потоку для дополнительной обработки или на продажу. Процесс разделения создает такую проблему, как утилизация отделенных загрязняющих примесей. В некоторых случаях концентрированный кислотный газ (главным образом состоящий из H2S и CO2) направляют в установку регенерации серы ("SRU"). SRU преобразует H2S в доброкачественную элементарную серу. Однако в некоторых областях (таких как регион Каспийского моря) дополнительное производство элементарной серы нежелательно ввиду ограниченного рынка сбыта. Поэтому в некоторых районах мира миллионы тонн серы хранились в крупных надземных хранилищах, больше всего в Канаде и Казахстане. В то время как серу оставляют на наземное хранение, газообразный диоксид углерода чаще всего выпускают в атмосферу. Однако обыкновение выпускать CO2 в воздух иногда является нежелательным. Одно предложение для минимизации выбросов CO2 представляет способ, называемый "нагнетание кислотного газа" ("AGI"). AGI означает, что нежелательные сернистые нефтяные газы повторно закачивают в подземный пласт под давлением и связывают для более позднего потенциального применения. Альтернативно, диоксид углерода может быть использован для создания искусственного пластового давления в работах по интенсификации добычи нефти вторичным методом. Чтобы упростить проведение AGI, желательно иметь газоперерабатывающую установку, которая отделяет компоненты кислотных газов от газообразных углеводородов. Однако для "высокосернистых" потоков, т.е. потоков из эксплуатационных скважин, содержащих больше чем около 15% CO2 и/или H2S,могут быть особенно проблематичными проектирование, сооружение и эксплуатация установки, которая может экономично отделять загрязняющие примеси от желательных углеводородов. Во многих месторождениях природного газа углеводороды имеют относительно низкое процентное содержание (например, менее 40%) и высокие уровни процентного содержания кислотных газов, преимущественно диоксида углерода, но также сероводорода, карбонилсульфида, сероуглерода и разнообразных меркаптанов. В этих ситуациях может быть преимущественно использована криогенная обработка газа. Криогенная обработка газа представляет собой дистилляционный процесс, который иногда применяют для разделения газов. При криогенном разделении газов образуется поток охлажденного газообразного верхнего погона при умеренных давлениях (например, 300-600 фунтов/кв.дюйм, манометрических(psig (2,07-4,14 МПа, избыточных). В дополнение, в качестве "кубового" продукта получают сжиженный кислотный газ. Поскольку сжиженный кислотный газ имеет относительно высокую плотность, гидростатический напор можно преимущественно использовать при закачке в скважину согласно AGI для содействия процессу нагнетания. В этом отношении кислотный газ может быть извлечен в виде жидкости при давлении в колонне (например, 300-600 psia) (2,07-4,14 МПа, абсолютных). Это значит, что энергия, которая требуется на нагнетание сжиженного кислотного газа в пласт, является меньшей, чем энергия, нужная для сжатия кислотных газов, имеющих низкое давление, до уровня пластового давления. Криогенная обработка газа имеет дополнительные преимущества. Например, не требуется растворитель для поглощения диоксида углерода. В дополнение, извлечение метана может быть выполнено в одиночном резервуаре (в противоположность многокамерным системам, применяемым в процессах Райана-Холмса). Наконец, в зависимости от холодопроизводительности, могут быть соблюдены строгие технические условия на содержание H2S в продуктовом газе, например, вплоть до уровня 4 млн-1 или ниже. Существует также серьезная проблема в отношении криогенной дистилляции сернистых нефтяных газов. Когда CO2 присутствует в обрабатываемом газе с концентрациями выше чем около 5 мол.%, он будет замораживаться в стандартной установке для криогенной дистилляции с образованием твердого вещества. Преобразование CO2 в твердое вещество нарушает процесс криогенной дистилляции. Во избежание этой проблемы авторы настоящего изобретения ранее разработали разнообразные процессыControlled Freeze Zone (CFZ) ("Регулируемой Зоны Замораживания"). В технологии CFZ преимущественно используют склонность диоксида углерода к образованию твердых частиц таким образом, что создают частицам замороженного CO2 возможность формироваться внутри открытой части дистилляционной колонны и затем улавливают частицы, когда они падают на плавильную тарелку. В результате на верху колонны генерируют поток чистого метана (вместе с любым азотом или гелием, присутствующими в сырьевом газе), тогда как поток холодного жидкого CO2/H2S формируют в донной части колонны в качестве кубового продукта. Определенные аспекты CFZ - технологии и связанные с ней оборудование описаны в патентах США 4533372; 4923493; 5062270; 5120338 и 6053007. Как в основном описано в вышеуказанных патентах США, дистилляционная башня, или колонна,используемая в криогенной обработке газов, включает нижнюю дистилляционную зону и промежуточную зону регулируемого замораживания. Предпочтительно имеется также верхняя ректификационная зона. Колонна работает для создания частиц твердого CO2, для чего предусмотрена часть колонны, имеющая температуру в диапазоне ниже температуры замерзания диоксида углерода, но выше температуры кипения метана при этом давлении. Более предпочтительно, зона регулируемого замораживания действует при температуре и давлении, которые позволяют метану и другим газообразным легким углеводородам испаряться, в то же время обусловливая образование частиц замерзшего (твердого) CO2. Когда поток подводимого сырьевого газа движется вверх по колонне, частицы замерзшего CO2 выделяются из подводимого потока и под действием силы тяжести выпадают из зоны регулируемого замораживания на плавильную тарелку. Там частицы переходят в жидкое состояние. Затем поток обогащенной диоксидом углерода жидкости стекает с плавильной тарелки вниз в нижнюю дистилляционную зону у дна колонны. Нижнюю дистилляционную зону поддерживают при температуре и давлении, при которых твердый диоксид углерода практически не образуется, но выкипает растворенный метан. В одном аспекте кубовый поток кислотных газов создают в дистилляционной зоне при температуре от 30 до 40F(1,11-4,44 С). Зона регулируемого замораживания включает распыление холодной жидкости. Она представляет собой поток обогащенной метаном жидкости, известный как "флегма". Когда поток паров легких газообразных углеводородов и увлеченных кислотных газов движется вверх по колонне, поток паров сталкивается с разбрызгиваемой жидкостью. Распыляемая холодная жидкость способствует выделению частиц твердого CO2, в то же время позволяя газообразному метану испаряться и протекать вверх в ректификационную зону. В верхней ректификационной зоне метан (или верхний газовый погон) улавливают и выводят наружу по трубопроводу на продажу или для использования в качестве топлива. В одном аспекте поток верхнего метанового погона выпускают при температуре около -130F (90C). Верхний газовый погон может быть частично сжижен дополнительным охлаждением, и часть жидкости возвращают в колонну в качестве флегмы. Затем жидкую флегму нагнетают в виде факела холодного распыления в ректификационную зону и зону регулируемого замораживания. В этом отношении способ формирования холодного жидкого метана для флегмы требует оборудования, вспомогательного для CFZ-колонны. Это оборудование включает трубопроводы, форсунки, компрессоры, сепараторы, насосы и расширительные клапаны. Метан, полученный в верхней ректификационной зоне, удовлетворяет большинству технических условий для транспортировки по трубопроводам. Например, метан может соответствовать техническим условиям транспортировки по трубопроводам при содержании CO2 менее 2 мол.%, а также техническим условиям на содержание H2S на уровне 4 млн-1, если генерируют надлежащую флегму. Однако более строгие технические условия существуют для более чистого природного газа в таких вариантах применения, как извлечение гелия, криогенное выделение жидкостей из природного газа, преобразование в сжиженный природный газ (LNG, СПГ) и отделение азота. Более строгие технические требования могут быть удовлетворены повышением количества жидкой метановой флегмы. Для этого, в свою очередь, требуется более габаритное морозильное оборудование. Чем более полно оператор хочет удалить CO2, тем выше становится требования к замораживанию. Существует потребность в снижении требований к охлаждению в CFZ-процессе, в то же время попрежнему со снижением содержания CO2 до очень низких уровней. Также есть потребность в системе криогенного разделения газов и сопутствующих процессах, которые дополнены другими способами удаления CO2. Кроме того, существует потребность в способе криогенного разделения газов, который способен снижать содержание CO2 и H2S в газе до уровней, приемлемых для технических характеристик сжиженного природного газа (LNG) в процессах сжижения ниже по потоку, без повышения производительности холодильного оборудования. Сущность изобретения Представлена система для удаления кислотных газов из потока сырьевого газа. В одном варианте исполнения система включает криогенную дистилляционную колонну. Дистилляционная колонна имеет промежуточную зону регулируемого замораживания. В зону регулируемого замораживания, или распылительную секцию, направляют распыляемую холодную жидкость, главным образом состоящую из метана. Распыляемая холодная жидкость предпочтительно представляет собой жидкую флегму, образованную из контура верхнего погона ниже по потоку относительно дистилляционной колонны. Криогенную дистилляционную колонну компонуют для приема потока сырьевого газа и затем разделения потока сырьевого газа на (1) поток газообразного верхнего метанового погона и (2) по существу,твердый материал, состоящий из диоксида углерода. Система также имеет холодильное оборудование ниже по потоку относительно криогенной дистилляционной колонны. Холодильное оборудование служит для охлаждения потока верхнего метанового погона и затем возвращения части потока верхнего метанового погона в качестве флегмы в ректифика-2 024440 ционную зону криогенной дистилляционной колонны. Часть жидкой флегмы может быть распылена в зоне регулируемого замораживания, чтобы стимулировать осаждение частиц твердого диоксида углерода. Система дополнительно включает коллекторную тарелку. Коллекторную тарелку размещают ниже зоны регулируемого замораживания для приема частиц твердого CO2, когда они осаждаются в зоне регулируемого замораживания. Коллекторная тарелка предпочтительно имеет наклонное основание для направления осадка в центральную спускную трубу. В свою очередь, спускная труба необязательно может включать механическое транспортное устройство, такое как шнек, для перемещения суспензии, которая включает твердый материал CO2, из криогенной дистилляционной колонны и по направлению к установке для извлечения CO2. Установка для извлечения CO2 предпочтительно включает многочисленные фильтры. Таким образом, система включает, по меньшей мере, первый фильтр для приема суспензии. Суспензию разделяют на замерзший, или твердый, материал (называемый "фильтрационным осадком") и жидкий материал (называемый "фильтратом"). Твердый материал, по существу, состоит из диоксида углерода, тогда как жидкий материал включает метан. Жидкий материал также может содержать небольшие количества диоксида углерода, сероводорода, ртути и тяжелых углеводородов. Должно быть понятно, что как используемая здесь суспензия предполагается включающей твердый материал и жидкий материал, но может дополнительно включать газообразный материал или другой нетвердый материал. Часть суспензии, составляющая жидкий материал, может быть отделена от нее для дополнительной обработки. Обработкой нетвердого материала можно преобразовать жидкости в газы и/или твердые вещества, которые затем можно использовать для различных целей, таких как повторное нагнетание в регенерационную установку. Однако для простоты нетвердая часть суспензии, будучи однажды отделенной от суспензии, может упоминаться здесь как жидкий материал, независимо от состояния материала. Система дополнительно включает жидкостный возвратный трубопровод. По жидкостному возвратному трубопроводу возвращают по меньшей мере часть жидкого материала из установки для извлеченияCO2 в криогенную дистилляционную колонну. В ней затем может происходить дальнейшая обработка метана и любых кислотных газовых компонентов. Криогенная дистилляционная колонна предпочтительно включает верхнюю ректификационную зону над зоной регулируемого замораживания. Колонна дополнительно может включать нижнюю дистилляционную зону под зоной регулируемого замораживания. В последнем случае криогенную дистилляционную колонну предпочтительно компонуют для приема потока сырьевого газа в нижнюю дистилляционную зону. Более того, в нижнюю дистилляционную зону колонны поступает жидкий материал из жидкостного возвратного трубопровода. В нижней дистилляционной зоне происходит дополнительная обработка метана и следовых остатков кислотных газовых компонентов. В теплой нижней дистилляционной зоне метан испаряется, проходит вверх через зону регулируемого замораживания и верхнюю ректификационную зону и объединяется с потоком верхнего метанового погона. Компоненты диоксида углерода будут главным образом испаряться в нижней дистилляционной зоне, перемещаться вверх в зону регулируемого замораживания и осаждаться обратно на коллекторную тарелку. Затем CO2-компоненты транспортируются к установке для извлечения CO2 с суспензией. Когда колонна включает нижнюю дистилляционную зону, кислотные газы будут выделяться из относительно теплой нижней дистилляционной зоны в виде потока кубовой жидкости. Поток кубовой жидкости может включать этан, пропан, бутан, сероводород или их комбинации, главным образом в жидкостной фазе. Может также присутствовать диоксид углерода. В одном варианте компоновки криогенная дистилляционная колонна не включает нижнюю дистилляционную зону. В этой ситуации поток сырьевого газа нагнетают в дистилляционную колонну в зоне регулируемого замораживания. В дополнение, в жидкостном возвратном трубопроводе по меньшей мере часть жидкого материала объединяют с потоком сырьевого газа перед тем, как поток сырьевого газа поступит в криогенную дистилляционную колонну, или одновременно с этим. Дистилляционная колонна не будет иметь кубового потока для улавливания сероводорода; вместо этого сероводород и следовые количества метана и диоксида углерода улавливаются внутри установки для извлечения CO2 через второй и, необязательно, третий и четвертый фильтры. Сероводород и следовые количества метана и диоксида углерода проходят через фильтры в виде холодного жидкого фильтрата. Фильтрат затем подвергают обработке в дистилляционной колонне так, чтобы отделить поток извлеченного метана от кислотных газов. Поток извлеченного метана объединяют с потоком верхнего метанового погона на продажу в качестве коммерческого продукта. В каждом варианте исполнения на выходе установки для извлечения CO2 необязательно предусматривают теплообменник. Теплообменник предназначен для нагревания, по существу, твердого материала,отобранного, по меньшей мере частично, из фильтрационного осадка конечной стадии, для получения потока в основном чистого диоксида углерода в жидкостной фазе. По существу, твердый материал нагревают с использованием, например, потока сырьевого газа в качестве источника тепла. Здесь также представлен способ удаления кислотных газов из потока сырьевого газа с использованием системы для удаления кислотных газов. Поток сырьевого газа включает метан, диоксид углерода и,-3 024440 наиболее вероятно, другие компоненты, такие как этан и сероводород. В одном варианте исполнения способ, прежде всего, включает стадию, в которой готовят криогенную дистилляционную колонну. Колонна имеет зону регулируемого замораживания, в которую поступает распыляемая холодная жидкость, главным образом состоящая из метана. Колонна дополнительно имеет коллекторную тарелку ниже зоны регулируемого замораживания. Способ также включает стадию, в которой нагнетают поток сырьевого газа в криогенную дистилляционную колонну. В одном варианте компоновки поток сырьевого газа нагнетают в дистилляционную колонну в нижней дистилляционной зоне, ниже зоны регулируемого замораживания. В еще одном варианте компоновки поток сырьевого газа нагнетают в дистилляционную колонну в самую зону регулируемого замораживания. Предпочтительно, чтобы поток сырьевого газа был в значительной мере обезвожен перед его нагнетанием в дистилляционную колонну. Способ дополнительно включает стадию, в которой поток сырьевого газа подвергают глубокому охлаждению. Глубокое охлаждение потока сырьевого газа обусловливает осаждение диоксида углерода внутри потока сырьевого газа на коллекторную тарелку в виде, по существу, твердого материала и образование на ней суспензии. В то же время давление в дистилляционной колонне является более низким,чем давление подводимого сырьевого потока, что приводит к взрывному испарению метана внутри потока сырьевого газа. Метан проходит через ректификационную зону выше зоны регулируемого замораживания и выходит из криогенной дистилляционной колонны в виде потока верхнего метанового погона. Способ также включает стадию, в которой пропускают поток верхнего метанового погона через холодильную систему ниже по потоку относительно криогенной дистилляционной колонны. Холодильная система охлаждает по меньшей мере часть потока верхнего метанового погона с образованием жидкости. Способ дополнительно включает стадию, в которой возвращают часть поток охлажденного верхнего метанового погона в криогенную дистилляционную колонну в качестве жидкой флегмы. Часть жидкой флегмы, в свою очередь, может служить в качестве холодной распыляемой жидкости. Также в качестве части способа, по существу, твердый материал удаляют из криогенной дистилляционной колонны. В одном аспекте удаление, по существу, твердого материала выполняют с использованием механического транспортного устройства, такого как винтовой конвейер или шнек. Шнек может находиться внутри спускной трубы коллекторной тарелки, как указано выше. Шнек сгребает, по существу, твердый материал, или суспензию, выводит ее из дистилляционной колонны и направляет в оборудование для обработки твердого CO2. Предпочтительно, чтобы коллекторная тарелка действовала при температуре, например, от около -70 до -80F (от -56,7 до -62,2 С). Это находится на уровне или слегка ниже уровня температуры замерзания CO2-компонента. Способ дополнительно включает стадию, в которой разделяют, по существу, твердый материал, по существу, на твердый фильтрационный осадок и, по существу, жидкий фильтрат. Фильтрационный осадок в основном состоит из диоксида углерода, тогда как фильтрат включает метан и остаточный диоксид углерода. Фильтрат может включать другие компоненты, такие как тяжелые углеводороды и даже легкие ароматические соединения. Стадия, на которой проводят разделение, может быть проведена тем, что пропускают, по существу,твердый материал или суспензию через первый фильтр. Этим образуют первый фильтрационный осадок,в основном состоящий из твердого диоксида углерода, и первый фильтрат, включающий метан и диоксид углерода в жидкостной фазе. Первый фильтр может представлять собой, например, пористую среду или центрифугу. Стадия, на которой проводят разделение, может дополнительно включать стадии, на которых промывают первый фильтрационный осадок с использованием потока холодного диоксида углерода, перемешивают первый фильтрационный осадок с образованием первой твердофазно-жидкостной суспензии,и подают первую твердофазно-жидкостную суспензию на второй фильтр. На втором фильтре получают второй фильтрационный осадок, в основном состоящий из твердого диоксида углерода, и второй фильтрат, включающий метан и диоксид углерода, опять же в жидкостной фазе. В то время как для многих вариантов применения может быть достаточным одностадийное разделение, может быть предпринято дополнительное удаление CO2. Например, стадия, в которой проводят разделение, может включать стадии, на которых промывают второй фильтрационный осадок с использованием потока холодного диоксида углерода, перемешивают второй фильтрационный осадок для получения твердофазно-жидкостной суспензии и подают твердофазно-жидкостную суспензию еще и на третий фильтр. Этим получают третий фильтрационный осадок, главным образом состоящий из твердого диоксида углерода, и третий фильтрат, включающий еще меньшее количество метана и диоксид углерода, опять же в жидкостной фазе. Способ также включает стадию, в которой возвращают по меньшей мере часть второго жидкого материала в криогенную дистилляционную колонну. В одном аспекте второй жидкий материал направляют обратно в нижнюю дистилляционную зону. В еще одном аспекте второй жидкий материал объединяют с потоком сырьевого газа и повторно нагнетают в колонну в зоне регулируемого замораживания. В одном варианте исполнения способа объединяют первый фильтрат и второй фильтрат. Объединенная текучая среда из фильтратов образует жидкий фильтрат, который возвращают в криогенную дистилляционную колонну. В этом случае объединенный жидкий фильтрат предпочтительно нагнетают в нижнюю дистилляционную зону. В еще одном варианте исполнения способа только первый фильтрат возвращают в дистилляционную колонну в качестве жидкого фильтрата. В этом случае первый фильтрат может быть возвращен обратно в зону регулируемого замораживания. Дистилляционная колонна предпочтительно не будет иметь нижнюю дистилляционную зону. Второй и, необязательно, третий (или последующий) фильтраты направляют в отдельную дистилляционную колонну ниже по потоку, где проводят окончательное отделение остаточных кислотных газов от метана. В этом случае получают поток извлеченного метана, который объединяют с потоком верхнего метанового погона криогенной дистилляционной колонны на продажу. Краткое описание чертежей Для того чтобы настоящие изобретения можно было лучше понять, к ним прилагаются определенные иллюстрации, схемы и/или блок-схемы. Однако следует отметить, что чертежи иллюстрируют только избранные варианты осуществления изобретений и поэтому не должны рассматриваться как ограничивающие область в том плане, что изобретения могут допускать прочие равным образом эффективные варианты осуществления и применения. Фиг. 1 представляет вид сбоку иллюстративной дистилляционной CFZ-колонны в одном варианте исполнения. Как видно, поток глубоко охлажденного сырьевого газа нагнетают в промежуточную зону регулируемого замораживания колонны. Фиг. 2 А представляет вид сверху плавильной тарелки в одном варианте исполнения. Плавильная тарелка находится внутри колонны ниже зоны регулируемого замораживания. Фиг. 2 В представляет вид в разрезе плавильной тарелки из фиг. 2 А, проведенном по линии В-В. Фиг. 2 С представляет вид в разрезе плавильной тарелки из фиг. 2 А, проведенном по линии С-С. Фиг. 3 представляет увеличенный вид сбоку отпарных тарелок в нижней дистилляционной зоне дистилляционной колонны в одном варианте исполнения. Фиг. 4 А представляет перспективный вид струйной тарелки, какая может быть использована либо в нижней дистилляционной зоне, либо в верхней ректификационной зоне дистилляционной колонны, в одном варианте исполнения. Фиг. 4 В представляет вид сбоку одного из отверстий в струйной тарелке из фиг. 4 А. Фиг. 5 представляет вид сбоку промежуточной зоны регулируемого замораживания дистилляционной колонны из фиг. 1. В этом изображении в промежуточную зону регулируемого замораживания были добавлены две иллюстративных перегородки. Фиг. 6 А представляет вид сверху коллекторной тарелки в одном варианте исполнения. В одном варианте компоновки газоперерабатывающей установки коллекторную тарелку размещают внутри колонны ниже зоны регулируемого замораживания. Фиг. 6 В представляет вид в разрезе коллекторной тарелки из фиг. 6 А, проведенном по линии В-В. Фиг. 6 С представляет вид в разрезе коллекторной тарелки из фиг. 6 А, проведенном по линии С-С. Фиг. 6 В представляет вид в разрезе коллекторной тарелки из фиг. 6 А в альтернативном варианте исполнения. Изображение опять же представляет разрез, проведенный по линии В-В. Фиг. 7 представляет схематическую диаграмму, показывающую газоперерабатывающую установку для удаления кислотных газов из потока сырьевого газа, в одном варианте осуществления соответственно настоящему изобретению. Используют коллекторную тарелку из фиг. 6 А или 6D. Фиг. 8 представляет схематическую диаграмму, показывающую газоперерабатывающую установку для удаления кислотных газов из потока сырьевого газа, в альтернативном варианте осуществления соответственно настоящему изобретению. Опять применяют коллекторную тарелку из фиг. 6 А или 6D. Фиг. 9 представляет блок-схему способа удаления кислотных газов из газового потока в одном варианте осуществления соответственно настоящему изобретению. Подробное описание определенных вариантов исполнения определения Как используемый здесь, термин "углеводород" имеет отношение к органическому соединению, которое главным образом, если не исключительно, включает элементы водород и углерод. Углеводороды в основном подразделяются на два класса: алифатические, или линейно-цепочечные углеводороды, и циклические, или углеводороды с замкнутым кольцом, включающие циклические терпены. Примеры углеводородсодержащих материалов включают любую форму природного газа, нефти, угля и битума, которые могут быть использованы в качестве топлива или модифицированы в топливо. Как применяемый здесь, термин "углеводородные текучие среды" имеет отношение к углеводородам или смесям углеводородов, которые являются газами или жидкостями. Например, углеводородные текучие среды могут включать углеводород или смеси углеводородов, которые представляют собой газы или жидкости в условиях пласта, при технологических условиях или в условиях окружающей среды(температура 15 С и давление 1 атм (0,1013 МПа. Углеводородные текучие среды могут включать, например, нефть, природный газ, метан угольных пластов, сланцевое масло, пиролизное топливо, пиролиз-5 024440 ный газ, продукт пиролиза угля и другие углеводороды, которые находятся в газообразном или жидком состоянии. Термин "массопередающее устройство" относится к любому объекту, который принимает контактирующие текучие среды и пересылает эти текучие среды к другим объектам, например, посредством гравитационного течения. Одним неограничивающим примером является тарелка для отпаривания определенных текучих сред. Еще один пример представляет сетчатая насадка. Как используемый здесь, термин "текучая среда" имеет отношение к газам, жидкостям и комбинациям газов и жидкостей, а также к комбинациям газов и твердых веществ и комбинациям жидкостей и твердых веществ. Как применяемый здесь, термин "конденсируемые углеводороды" означает такие углеводороды,которые конденсируются при температуре около 15 С и абсолютном давлении на уровне одной атмосферы (0,1013 МПа). Конденсируемые углеводороды могут включать, например, смесь углеводородов,имеющих число атомов углерода свыше 4. Как используемый здесь, термин "система охлаждения замкнутого цикла" означает любую систему охлаждения, в которой в качестве хладагента используют наружную рабочую текучую среду, такую как пропан или этилен, для глубокого охлаждения потока верхнего метанового погона. Это отличается от"системы охлаждения открытого цикла", в которой в качестве рабочей текучей среды применяют часть самого потока верхнего метанового погона. Как применяемый здесь, термин "подповерхностный" имеет отношение к геологическому пласту,находящемуся ниже поверхности земли. Описание конкретных вариантов исполнения Фиг. 1 представляет схематический вид криогенной дистилляционной колонны 100, которая может быть использована в связи с настоящими изобретениями, в одном варианте исполнения. Криогенная дистилляционная колонна 100 может быть взаимозаменяемо названа здесь как "криогенная дистилляционная башня", "колонна", "CFZ-колонна" или "разделительная башня". Криогенная дистилляционная колонна 100 на фиг. 1 принимает поток 10 исходной текучей среды. Поток 10 текучей среды главным образом состоит из газов, добытых из пласта. Как правило, поток текучей среды представляет собой поток высушенного газа из устья скважины (не показано) и содержит от около 65 до около 95% метана. Однако поток 10 текучей среды может содержать метан с более низкой процентной концентрацией, такой как от около 30 до 65% или даже от 20 до 40%. Метан может присутствовать вместе со следовыми количествами других газообразных углеводородов, таких как этан. В дополнение, могут присутствовать следовые количества гелия и азота. В настоящем описании поток 10 текучей среды также будет включать определенные загрязняющие примеси. Они включают кислотные газы, такие как CO2 и H2S. Поток 10 исходной текучей среды может иметь давление, как после добычи, приблизительно 600 фунтов/кв.дюйм (psi) (4,14 МПа) или ниже. В некоторых случаях давление потока 10 исходной текучей среды может составлять вплоть до 750 psi (5,17 МПа) или даже 1000 psi (6,89 МПа). Поток 10 текучей среды перед поступлением в дистилляционную колонну 100 обычно подвергают глубокому охлаждению. Для потока 10 исходной текучей среды предусматривают теплообменник 150,такой как кожухотрубный теплообменник. Холодильная установка (не показана) поставляет хладагент(такой как жидкий пропан) в теплообменник 150 для доведения температуры потока 10 исходной текучей среды до уровня от около -30 до -40F (от -34,4 до -40 С). Затем подвергнутый глубокому охлаждению поток текучей среды может проходить через расширительное устройство 152. Расширительное устройство 152 может представлять собой, например, клапан Джоуля-Томсона ("J-T"). Расширительное устройство 152 служит в качестве детандера для достижения дополнительного охлаждения потока 10 текучей среды. При этом также предпочтительно обеспечивают частичное сжижение потока 10 текучей среды. Клапан Джоуля-Томсона (или "J-T") является предпочтительным для сырьевых газовых потоков, которые склонны к образованию твердых веществ. Расширительное устройство 152 предпочтительно устанавливают вблизи криогенной дистилляционной колонны 100, чтобы свести к минимуму потери тепла в питающем трубопроводе. В качестве альтернативы J-T-клапану расширительное устройство 152 может представлять собой турбодетандер. Турбодетандер обеспечивает более глубокое охлаждение и создает источник мощности на валу для процессов типа вышеупомянутой холодильной установки. Холодильная установка составляет часть теплообменника 150. Этим путем оператор может сводить к минимуму общие потребности в энергии для дистилляционного процесса. Однако турбодетандер может быть не в состоянии обрабатывать частицы замерзшего вещества так же хорошо, как J-Т-клапан. В любом случае теплообменник 150 и расширительное устройство 152 преобразуют поток 10 исходной текучей среды в поток 12 глубоко охлажденной текучей среды. Температура потока 12 глубоко охлажденной текучей среды предпочтительно составляет от около -40 до -70F (от -40 до -56,7 С). В одном аспекте криогенная дистилляционная колонна 100 работает при давлении около 550 psi (3,8 МПа), и поток 12 глубоко охлажденной текучей среды имеет температуру приблизительно -62F (52,2C). В этих условиях поток 12 глубоко охлажденной текучей среды находится главным образом в жидкостной фазе,-6 024440 хотя потоком 12 глубоко охлажденной текучей среды неизбежно может быть увлечена некоторая паровая фаза. Скорее всего, от присутствующего CO2 не будет происходить никакого формирования твердых веществ. Криогенную дистилляционную колонну 100 разделяют на три первичных секции. Они представляют собой нижнюю дистилляционную зону 106, промежуточную зону 108 регулируемого замораживания,или "распылительную секцию", и верхнюю дистилляционную, или "ректификационную", зону 110. В конструкции колонны согласно фиг. 1 поток 12 глубоко охлажденной текучей среды вводят в дистилляционную колонну 100 в зоне 108 регулируемого замораживания. Однако поток 12 глубоко охлажденной текучей среды альтернативно может быть введен вблизи верха нижней дистилляционной зоны 106. В компоновке согласно фиг. 1 отмечено, что нижняя дистилляционная зона 106, промежуточная распылительная секция 108, верхняя ректификационная зона 110 и все компоненты заключены внутри единичного резервуара. Однако для вариантов применения на морских промыслах, в которых может оказаться необходимым учитывать высоту колонны 100 и возможности ее перемещения, или для отдаленных мест, в которых ограничения на перевозки создают проблемы, дистилляционная колонна 100 необязательно может быть разделена на два отдельных, работающих под давлением резервуара (не показано). Например, нижняя дистилляционная зона 106 и зона 108 регулируемого замораживания могут быть размещены в одном резервуаре, тогда как верхнюю ректификационную зону 110 располагают в еще одном резервуаре. Тогда для взаимного соединения двух резервуаров могли бы быть использованы наружные трубопроводы. В любом варианте исполнения температура нижней дистилляционной зоны 106 является более высокой, чем температура подводимого потока 12 глубоко охлажденной текучей среды. Температуру нижней дистилляционной зоны 106 проектируют значительно выше температуры кипения метана в потоке 12 глубоко охлажденной текучей среды при эксплуатационном давлении колонны 100. Этим путем предпочтительно отпаривают метан из составляющих смесь более тяжелых углеводородов и сжиженных кислотных газов. Конечно, специалисту с обычной квалификацией в этой области технологии будет понятно, что жидкость внутри дистилляционной колонны 100 представляет собой смесь, чем подразумевается, что жидкость будет "кипеть" при некоторой промежуточной температуре между температурами кипения чистого метана и чистого CO2. Кроме того, в ситуации, что в смеси присутствуют более тяжелые углеводороды (такие как этан или пропан), это будет повышать температуру кипения смеси. Эти факторы становятся параметрами проектирования для рабочих температур внутри дистилляционной колонны 100. В нижней дистилляционной зоне 106 CO2 и любые другие жидкофазные текучие среды под действием силы тяжести падают в сторону дна криогенной дистилляционной колонны 100. В то же время метан и другие парофазные текучие среды отделяются и поднимаются вверх в сторону верха колонны 100. Это разделение главным образом обеспечивается разницей в плотностях между газовой и жидкостной фазами. Однако процесс разделения необязательно стимулируют внутренними компонентами внутри дистилляционной колонны 100. Как описано ниже, сюда входят плавильная тарелка 130, многочисленные надлежащим образом скомпонованные массопередающие устройства 126 и, необязательно, нагревательный трубопровод 25. Более того, к нижней дистилляционной зоне 106 могут быть подключены вспомогательные кипятильники (не показаны), чтобы содействовать удалению CO2 и теплопереносу. С привлечением опять фиг. 1, поток 12 глубоко охлажденной текучей среды может быть введен в колонну 100 вблизи верха нижней дистилляционной зоны 106. Альтернативно, может быть желательным введение сырьевого потока 12 в промежуточную распылительную зону, или зону 108 регулируемого замораживания, выше плавильной тарелки 130. Место введения потока 12 глубоко охлажденной текучей среды является параметром проектирования, который главным образом определяется составом потока 12 исходной текучей среды. Может быть предпочтительным нагнетание потока 12 глубоко охлажденной текучей среды непосредственно в нижнюю дистилляционную зону 106 через устройство 124 типа двухфазного испарителя мгновенного вскипания (или парораспределителя) в колонне 100. Применение испарителя 124 мгновенного вскипания служит для частичного отделения двухфазной парожидкостной смеси в потоке 12 глубоко охлажденной текучей среды. Испаритель 124 мгновенного вскипания может быть разрезным, чтобы двухфазная текучая среда сталкивалась с перегородками в испарителе 124 мгновенного вскипания. Если предполагаются значительные скопления жидкости или частые нарушения процесса, может оказаться необходимым частичное разделение потока 12 глубоко охлажденной текучей среды в резервуаре 173 до подачи в колонну 100. В этом случае поток 12 глубоко охлажденной текучей среды может быть разделен в двухфазном резервуаре 173. Пары выходят из двухфазного резервуара 173 через всасывающий трубопровод 11 резервуара, где они поступают в колонну 100 через впускной распределитель 121. Затем газ проходит вверх через колонну 100. Жидкость 13 выпускают из двухфазного резервуара 173. Жидкость 13 направляют в колонну 100 через распределитель 124. Жидкость 13 может быть подведена в колонну 100 гравитационным путем или с помощью насоса 175. В любом варианте компоновки, т.е. при наличии двухфазного резервуара 173 или без него, поток 12(или 11) глубоко охлажденной текучей среды поступает в колонну 100. Жидкий компонент выходит из испарителя 124 мгновенного вскипания и проходит вниз к серии отпарных тарелок 126 внутри нижней дистилляционной зоны 106. Отпарные тарелки 126 включают серию спускных труб 129 и переливных устройств 128. Они более подробно описаны ниже с привлечением фиг. 3. Отпарные тарелки 126, в сочетании с более высокой температурой в нижней дистилляционной зоне 106, обусловливают выделение метана из раствора. Образовавшийся пар уносит метан и любые увлеченные молекулы диоксида углерода, которые выкипели. Пар далее проходит вверх через газопропускные патрубки 131 плавильной тарелки 130 (видимой на фиг. 2 В) и поступают в зону 108 замораживания. Стояки 131 плавильной тарелки действуют как парораспределитель для равномерного распределения в пределах зоны 108 замораживания. Затем пар будет контактировать с холодной жидкостью из магистралей 120 с соплами для "замораживания" CO2. Иначе говоря, CO2 будет замерзать и затем осаждаться, или "осыпаться снегом", обратно на плавильную тарелку 130. Твердый CO2 затем расплавляется и под действием силы тяжести стекает в жидкой форме вниз с плавильной тарелки 130 и через нижнюю дистилляционную зону 106. Как будет более полно обсуждено ниже, распылительная секция 108 представляет собой промежуточную зону замораживания в криогенной дистилляционной колонне 100. При альтернативной конструкции, в которой поток 12 глубоко охлажденной текучей среды разделяют в резервуаре 173 до поступления в колонну 100, часть отделенной жидкостно-твердофазной суспензии 13 вводят в колонну 100 непосредственно над плавильной тарелкой 130. Таким образом, жидкостно-твердофазная смесь сернистого нефтяного газа и более тяжелых углеводородных компонентов будет вытекать из распределителя 121,причем твердые вещества и жидкости падают вниз на плавильную тарелку 130. Плавильная тарелка 130 предназначена для гравитационного приема жидких и твердых материалов,главным образом CO2 и H2S, из промежуточной распылительной секции 108. Плавильная тарелка 130 служит для нагревания жидких и твердых материалов и направления их вниз через нижнюю дистилляционную зону 106 в жидкой форме для дополнительной очистки. Плавильная тарелка 130 собирает и нагревает твердофазно-жидкостную смесь из зоны 108 регулируемого замораживания, с образованием слоя жидкости. Плавильная тарелка 130 предназначена для высвобождения потока пара обратно в зону 108 регулируемого замораживания, чтобы обеспечивать надлежащий теплоперенос для расплавления твердого CO2,и для облегчения стекания жидкостной суспензии на нижнюю дистилляцию или в нижнюю дистилляционную зону 106 колонны 100 под плавильной тарелкой 130. Фиг. 2 А представляет вид сверху плавильной тарелки 130 в одном варианте исполнения. Фиг. 2 В показывает вид в разрезе плавильной тарелки 130, проведенном по линии В-В на фиг. 2 А. Фиг. 2 С показывает вид в разрезе плавильной тарелки 130, проведенном по линии С-С. Плавильная тарелка 130 будет описана с привлечением этих трех чертежей в совокупности. Во-первых, плавильная тарелка 130 включает основание 134. Основание 134 может представлять собой, по существу, плоскую деталь. Однако в предпочтительном варианте исполнения, показанном на фиг. 2 А-2 С, для основания 134 используют главным образом неплоский профиль. Неплоская компоновка создает увеличенную площадь поверхности для контактирования жидкостей и твердых веществ, опускающихся на плавильную тарелку 130 из промежуточной зоны 108 регулируемого замораживания. Это служит для усиления теплопереноса от паров, проходящих вверх из нижней дистилляционной зоны 106 колонны 100, к жидкостям и плавящимся твердым веществам. В одном аспекте основание 134 является гофрированным. В еще одном аспекте основание 134 является главным образом синусоидальным. Этот аспект конструкции тарелки показан на фиг. 2 В. Понятно, что для увеличения площади теплопередачи плавильной тарелки 130 альтернативно могут быть использованы другие неплоские геометрические формы. Основание 134 плавильной тарелки предпочтительно является наклонным. Наклон продемонстрирован в виде сбоку фиг. 2 С. Хотя должна расплавляться большая часть твердых веществ, наклон служит для обеспечения того, что любые нерасплавленные твердые вещества в жидкостной смеси будут стекать с плавильной тарелки 130 и отправляться вниз в нижнюю дистилляционную зону 106. В изображении фиг. 2 С сток, или "спускная труба" 138 видна размещенной по центру плавильной тарелки 130. Основание 134 плавильной тарелки наклонено внутрь в сторону спускнойтрубы 138 для подачи твердофазно-жидкостной смеси. Основание 134 может быть наклонено любым способом для облегчения гравитационного стока жидкости. Как описано в патенте США 4533372, плавильная тарелка была названа как "полуглухая тарелка". Это название обусловлено наличием одиночного патрубка для прохода газа. Газопропускной патрубок оснащен отверстием, через которое пары могут проходить вверх через полуглухую тарелку. Однако присутствие одиночного газопропускного патрубка означает, что все газы, проходящие вверх через полуглухую тарелку, должны были выходить через единственное отверстие. С другой стороны, в плавильной тарелке 130 согласно фиг. 2 А-2 С предусмотрены многочисленные газопропускные патрубки 131(или "стояки для восходящего потока"). Применение многочисленных газопропускных патрубков 131 обеспечивает улучшенное распределение паров. Это содействует лучшему тепло/массопереносу в промежуточной зоне 108 регулируемого замораживания. Газопропускные патрубки 131 могут иметь любой профиль. Например, газопропускные патрубки 131 могут быть круглыми, прямоугольными или любой иной формы, которая позволяет пару проходить через плавильную тарелку 130. Газопропускные патрубки 131 также могут быть узкими и протяженными вверх в промежуточную распылительную секцию 108. Это позволяет обеспечить благоприятный перепад давления для равномерного распределения пара по мере его подъема в CFZ-зону 108 регулируемого замораживания. Газопропускные патрубки 131 предпочтительно размещают на вершинах гофрированного основания 134 для создания дополнительной площади теплопереноса. Верхние отверстия газопропускных патрубков 131 предпочтительно накрывают шляпками или крышками 132. Этим сводят к минимуму вероятность того, что твердые вещества, падающие из зоны 108 регулируемого замораживания, смогут избежать падения на плавильную тарелку 130. На фиг. 2 А-2 С крышки 132 видны над каждым из газопропускных патрубков 131. Плавильную тарелку 130 также оснащают барботажными колпачками. Барботажные колпачки определяют выпуклые зубцы в основании 134, возвышающиеся из-под плавильной тарелки 130. Барботажные колпачки дополнительно увеличивают площадь поверхности в плавильной тарелке 130 для обеспечения дополнительного теплопереноса к обогащенной диоксидом углерода (CO2) жидкости. С такой компоновкой, как с увеличенным углом наклона, должно быть достигнуто надлежащее выведение жидкости, чтобы гарантировать то, что жидкость направляется вниз на отпарные тарелки 126. Опять с привлечением фиг. 1, плавильная тарелка 130 может быть оснащена системой внешнего переноса жидкости. Система переноса служит для обеспечения того, чтобы вся жидкость, по существу, не содержала твердых веществ, и чтобы была достигнута достаточная теплопередача. Система переноса,прежде всего, включает вытяжное сопло 136. В одном варианте исполнения вытяжное сопло 136 размещают внутри вытяжного стока, или спускной трубы 138 (см. на фиг. 2 С). Текучие среды, собранные в спускной трубе 138, направляют в транспортный трубопровод 135. Течение по транспортному трубопроводу 135 можно регулировать с помощью регулирующего клапана 137 и регулятора "LC" уровня (смотри на фиг. 1). Текучие среды возвращают в нижнюю дистилляционную зону 106 через транспортный трубопровод 135. Если уровень жидкости является слишком высоким, регулирующий клапан 137 открывается; если же уровень слишком низок, регулирующий клапан 137 закрывается. Если оператор выбирает режим без использования системы переноса в нижней дистилляционной зоне 106, то регулирующий клапан 137 закрывают и текучие среды направляют непосредственно в массопередающие устройства, или "отпарные тарелки" 126, ниже плавильной тарелки 130 для выпаривания через переливную спускную трубу 139. Используют или нет систему внешнего переноса, твердый CO2 нагревают на плавильной тарелке 130 и преобразуют в CO2-обогащенную жидкость. Плавильную тарелку 130 нагревают снизу парами из нижней дистилляционной зоны 106. Необязательно может быть подведено дополнительное тепло к плавильной тарелке 130 или непосредственно над основанием 134 плавильной тарелки разнообразными путями, такими как нагревательный трубопровод 25. В нагревательном трубопроводе 25 используют тепловую энергию, уже доступную из донного кипятильника 160, для облегчения расплавления твердых веществ.CO2-обогащенную жидкость выводят с плавильной тарелки 130 при регулировании уровня жидкости, и под действием силы тяжести вводят в нижнюю дистилляционную зону 106. Как отмечено, в нижней дистилляционной зоне 106 ниже плавильной тарелки 130 находятся многочисленные отпарные тарелки 126. Отпарные тарелки 126 предпочтительно располагаются, по существу, параллельно друг другу,одна над другой. Каждая из отпарных тарелок 126 необязательно может быть позиционирована с очень слабым наклоном, с таким переливным устройством, чтобы на тарелке поддерживался уровень жидкости. Текучие среды под действием силы тяжести стекают вдоль каждой тарелки через переливные устройства и затем стекают вниз на следующую тарелку через спускную трубу. Отпарные тарелки 126 могут иметь разнообразные компоновки. Отпарные тарелки 126 могут быть размещены главным образом в горизонтальном положении с образованием синусоидального каскадного потока жидкости. Однако предпочтительно, чтобы отпарные тарелки 126 были скомпонованы для создания каскадного потока жидкости, который подразделяется отдельными отпарными тарелками главным образом вдоль одной и той же горизонтальной плоскости. Это показано в варианте компоновки фиг. 3,где поток жидкости разделяют по меньшей мере один раз так, что жидкость падает в две противолежащих спускных трубы 129. Фиг. 3 представляет вид сбоку сборного узла отпарных тарелок 126 в одном варианте исполнения. Каждая из отпарных тарелок 126 получает сверху и накапливает текучие среды. Каждая отпарная тарелка 126 предпочтительно имеет переливное устройство 128, которое служит в качестве порога, чтобы обеспечить накопление небольшого слоя текучей среды на каждой из отпарных тарелок 126. Выступ порога может составлять от 1/2 до 1 дюйма (12,7-25,4 мм), хотя может быть использована любая высота. Переливными устройствами 128 создают эффект водопада, когда текучая среда падает с тарелки 126 на тарелку 126. В одном аспекте отпарным тарелкам 126 не придают никакого наклона, но эффект водопада создают с помощью конфигурации более высокого переливного устройства 128. Текучая среда контактирует с поступающим паром, обогащенным легкими углеводородами, которые выпаривают метан из жидкости, стекающей в режиме противотока, в этой "контактной области" тарелок 126. Переливные устройства 128 служат для динамического закупоривания спускных труб 129, чтобы содействовать предотвращению обходного течения пара через спускные трубы 129, и чтобы дополнительно облегчить выделение газообразных углеводородов. Процентная доля метана в жидкости становится все меньшей по мере перемещения жидкости вниз через нижнюю дистилляционную зону 106. Эффективность дистилляции зависит от числа тарелок 126 в нижней дистилляционной зоне 106. В верхней части нижней дистилляционной зоны 106 содержание метана в жидкости может доходить до 25 мол.%, тогда как на нижней отпарной тарелке содержание метана может быть снижено до уровня 0,04 мольного процента. Содержание метана быстро падает вдоль ряда отпарных тарелок 126 (или прочих массопередающих устройств). Число массопередающих устройств,используемых в нижней дистилляционной зоне 106, представляет собой проектный параметр, который выбирают на основе состава потока 10 сырьевого газа. Однако для удаления метана до желательного содержания в сжиженном кислотном газе, например, в 1% или менее обычно нужно применять лишь немного уровней отпарных тарелок 126. Могут быть использованы разнообразные индивидуальные компоновки отпарных тарелок 126, которые облегчают выделение метана. Отпарная тарелка 126 может представлять собой просто панель с ситчатыми отверстиями или барботажными колпачками. Однако для обеспечения дополнительного теплопереноса на текучую среду и для предотвращения нежелательного закупоривания твердыми веществами ниже плавильной тарелки могут быть применены так называемые "струйные тарелки". Вместо тарелок также может быть использована беспорядочная или структурированная насадка. Фиг. 4 А представляет вид сверху иллюстративной струйной тарелки 426 в одном варианте исполнения. Фиг. 4 В представляет вид в разрезе струйного лепестка 422, выступающего из струйной тарелки 426. Как показано, каждая струйная тарелка 426 имеет корпус 424 с многочисленными струйными лепестками 422, сформированными внутри корпуса 424. Каждый струйный лепесток 422 включает наклонный элемент 422 лепестка, накрывающий отверстие 425. Таким образом, струйная тарелка 426 имеет многочисленные мелкие отверстия 425. При работе одна или более струйных тарелок 426 могут быть размещены в отпарной 106 и/или ректификационной 110 секциях колонны 100. Тарелки 426 могут быть скомпонованы с многочисленными протоками, такими как картина отпарных тарелок 126 на фиг. 3. Однако может быть использована любая компоновка из тарелок или насадок, которая облегчает отделение газообразного метана. Текучая среда каскадом стекает вниз на каждую струйную тарелку 426. Затем текучие среды протекают вдоль корпуса 424. Ориентацию лепестков 422 оптимизируют так, чтобы быстро и эффективно направлять движение текучей среды по тарелке 426. Необязательно может быть предусмотрена примыкающая спускная труба(не показана), чтобы перемещать жидкость на последующую тарелку 426. Отверстия 425 также позволяют газообразным парам, высвобождающимся во время процесса перемещения текучей среды в нижнюю дистилляционную зону 106, более эффективно проходить вверх к плавильной тарелке 130 и через газопропускные патрубки 131. В одном аспекте тарелки (такие как тарелки 126 или 426) могут быть изготовлены из устойчивых к загрязнению материалов, т.е. материалов, которые препятствуют накоплению твердых веществ. Устойчивые к загрязнению материалы применяют в некотором технологическом оборудовании, чтобы предотвратить накопление частиц продуктов коррозии металлов, полимеров, солей, гидратов, тонкодисперсных катализаторов или прочих твердых химических соединений. В случае криогенной дистилляционной колонны 100 устойчивые к загрязнению материалы могут быть использованы в тарелках 126 или 426, чтобы ограничить налипание твердого CO2. Например, на поверхность тарелок 126 или 426 может быть нанесено покрытие из материала Teflon. Альтернативно, для обеспечения того, что CO2 не станет накапливаться в твердой форме вдоль внутреннего диаметра дистилляционной колонны 100, может быть предусмотрена физическая компоновка. В этом отношении струйные лепестки 422 могут быть ориентированы так, чтобы выталкивать жидкость вдоль стенки колонны 100, тем самым препятствуя накоплению твердых веществ вдоль стенки колонны 100 и обеспечивая хороший контакт паров и жидкости. В любой из конструкций тарелок, когда стекающая вниз жидкость наталкивается на отпарные тарелки 126, происходит разделение материалов. Газообразный метан выделяется из раствора и движется вверх в форме пара. Однако CO2 является достаточно холодным и имеет достаточно высокую концентрацию, чтобы оставаться в своей жидкой форме и перемещаться вниз ко дну нижней дистилляционной зоны 106. Затем жидкость выходит из криогенной дистилляционной колонны 100 в выходной трубопровод в виде кубового потока 22 текучей среды. По выходе из дистилляционной колонны 100 кубовый поток 22 текучей среды поступает в кипятильник 160. В фиг. 1 кипятильник 160 представляет собой резервуар типа котла, который поставляет выкипевший пар к донной части отпарных тарелок. Трубопровод для пара из кипятильника показан кодовым номером 27 позиции. В дополнение, выкипевший пар может быть доставлен по нагревательному трубопроводу 25 для подведения дополнительного тепла к плавильной тарелке 130. Количество дополнительного тепла регулируют с помощью клапана 165 и регулятора ТС температуры. Альтернативно,чтобы сэкономить энергию, для потока 10 исходной текучей среды может быть использован теплооб- 10024440 менник, такой как термосифонный теплообменник (не показан). В этом отношении жидкости, поступающие в кипятильник 160, остаются при относительно низкой температуре, например от около 30 до 40F (1,11-4,44 С). Отбором теплоты от потока 10 исходной текучей среды оператор может нагревать холодный кубовый поток 22 текучей среды из дистилляционной колонны 100, в то же время проводя предварительное охлаждение добытого из эксплуатационной скважины потока 10 текучей среды. Для этого случая текучая среда, подводящая дополнительное тепло по трубопроводу 25, представляет собой смешанную фазу, возвращаемую из кипятильника 160. Предусматривается, что в некоторых условиях плавильная тарелка 130 может работать без нагревательного трубопровода 25. В этих случаях плавильная тарелка 130 может быть скомпонована с внутренним нагревательным устройством, таким как электрический нагреватель. Однако предпочтительно, чтобы была привлечена нагревательная система, в которой используют тепловую энергию, отбираемую из кубового потока 22 текучей среды. В одном аспекте теплые текучие среды в нагревательном трубопроводе 25 выходят с температурой от 30 до 40F (1,11-4,44 С), так что они содержат относительно много тепловой энергии. Таким образом, на фиг. 1 поток 25 пара показан направляемым к плавильной тарелке 130 через нагревательный змеевик (не показан) на плавильной тарелке 130. Альтернативно, поток 25 пара может быть связан с транспортным трубопроводом 135. При работе большую часть потока пара из кипятильника вводят в донную часть колонны по трубопроводу 27, выше уровня жидкости на дне и на уровне или ниже последней отпарной тарелки 126. Когда пар из кипятильника проходит вверх через каждую тарелку 126, остаточный метан выпаривается из жидкости. Этот пар охлаждается по мере перемещения его вверх по колонне. К моменту времени, когда поток пара из трубопровода 27 достигает гофрированной плавильной тарелки 130, температура может снизиться до уровня от около -20 до 0F (от -28,9 до -17,8 С). Однако он остается довольно теплым по сравнению с плавлением твердого вещества на плавильной тарелке 130, которое может происходить при температуре от около -50 до -70F (от -45,6 до -56,7 С). Пар все еще имеет достаточно высокое теплосодержание для расплавления твердого CO2 по мере его вступления в контакт с плавильной тарелкой 130. Со ссылкой опять на кипятильник 160, текучие среды в кубовом потоке 24, который выходит из кипятильника 160 в жидкой форме, необязательно могут быть пропущены через расширительный клапан 162. Расширительный клапан 162 снижает давление кубового жидкого продукта, эффективно обеспечивая охлаждающее действие. Таким образом, получают глубоко охлажденный кубовый поток 26. Тем самым также создают гидростатический напор. В этом отношении CO2-обогащенная жидкость, выходящая из кипятильника 160, может быть закачана в забой скважины через одну или более AGI-скважин (для нагнетания кислотного газа) (схематически показанных на фиг. 1 кодовым номером 250 позиции). В некоторых ситуациях жидкий CO2 может быть закачан в частично разработанный нефтеносный пласт как часть процесса интенсификации добычи нефти вторичным методом. Таким образом, CO2 мог бы представлять собой смешивающуюся нагнетаемую текучую среду. В качестве альтернативы, CO2 может быть использован в качестве смешивающегося агента для нагнетания в пласт при интенсификации добычи нефти вторичным методом. Со ссылкой опять на нижнюю дистилляционную зону 106 дистилляционной колонны 100 газ движется вверх через нижнюю дистилляционную зону 106, через газопропускные патрубки 131 в плавильной тарелке 130 и поступает в зону 108 регулируемого замораживания. Зона 108 регулируемого замораживания формирует открытую камеру, имеющую многочисленные распылительные сопла 122. Когда пар движется вверх через зону 108 регулируемого замораживания, температура пара становится гораздо более низкой. Пар контактирует с жидким метаном, поступающим из распылительных сопел 122. Этот жидкий метан является гораздо более холодным, чем движущийся вверх пар, который был подвергнут глубокому охлаждению с использованием наружной холодильной установки 170. В одном варианте компоновки жидкий метан выходит из распылительных сопел 122 при температуре приблизительно от-120 до -130F (от -84,4 до -90 С). Однако при испарении жидкого метана он поглощает теплоту из своего окружения, тем самым снижая температуру движущегося вверх пара. Испаренный метан также протекает вверх благодаря его уменьшенной плотности (относительно жидкого метана) и градиента давления внутри колонны 100. Когда пары метана движутся далее вверх по криогенной дистилляционной колонне 100, они покидают зону 108 регулируемого замораживания и поступают в верхнюю ректификационную зону 110. Пары продолжают двигаться вверх вместе с другими легкими газами, выделившимися из потока 12 глубоко охлажденной исходной текучей среды. Объединенные углеводородные пары выходят из верха криогенной дистилляционной колонны 100, образуя поток 14 верхнего метанового погона. Газообразные углеводороды в потоке 14 верхнего метанового погона направляют в наружную холодильную установку 170. В одном аспекте в холодильной установке 170 используют этиленовый хладагент или другое охлаждающее средство, способное глубоко охлаждать поток 14 верхнего метанового погона до температуры от около -135 до -145F (от -92,8 до -98,3 С). Это служит, по меньшей мере частично, для сжижения потока 14 верхнего метанового погона. Затем поток 14 охлажденного метана движется к дефлегматору или разделительной камере 172. Разделительную камеру 172 применяют для отделения газа 16 от жидкой флегмы 18. Газ 16 представляет собой более легкие углеводороды, главным образом метан, из потока 10 исходного сырьевого газа. Также могут присутствовать азот и гелий. Газообразный метан 16, конечно, представляет собой"продукт", который в конечном итоге стараются уловить и реализовать на рынке, вместе с любым этаном. Часть потока 14 верхнего метанового погона, выходящего из холодильной установки 170, остается сконденсированной. Эта часть составляет жидкую флегму 18, которую отделяют в разделительной камере 172 и возвращают в колонну 100. Для перемещения жидкой флегмы 18 обратно в колонну 100 может быть применен насос 19. Альтернативно, разделительную камеру 172 сооружают выше колонны 100 для обеспечения гравитационной подачи жидкой флегмы 18. Жидкая флегма 18 будет включать любой диоксид углерода, который улетучивается из верхней ректификационной зоны 110. Однако большую часть жидкой флегмы 18 составляет метан, обычно 95% или более, с азотом (если он присутствует в потоке 10 исходной текучей среды) и следами сероводорода (если он также присутствует в потоке 10 исходной текучей среды). В одном варианте компоновки охлаждения поток 14 верхнего метанового погона отбирают с помощью системы охлаждения открытого цикла. В этой компоновке поток 14 верхнего метанового погона проводят через теплообменник с перекрестным током для глубокого охлаждения возвращаемой части потока верхнего метанового погона, используемого в качестве жидкой флегмы 18. После этого поток 14 верхнего метанового погона сжимают до давления от около 1000 до 1400 psi (6,9-9,6 МПа) и затем охлаждают с использованием окружающего воздуха и, возможно, внешнего пропанового хладагента. Затем поток сжатого и глубоко охлажденного газа направляют через детандер для дополнительного охлаждения. Может быть применен турбодетандер для извлечения еще большего количества жидкости, а также некоторой мощности на валу. Патент США 6053007, озаглавленный "Способ разделения многокомпонентного газового потока, содержащего по меньшей мере один замораживаемый компонент", описывает охлаждение потока верхнего метанового погона, и включен здесь ссылкой во всей своей полноте. Здесь понятно, что настоящие изобретения не ограничиваются способом охлаждения для потока 14 верхнего метанового погона. Также понятно, что степень охлаждения между холодильной установкой 170 и начальной холодильной установкой 150 может варьировать. В некоторых случаях может быть желательным, чтобы холодильная установка 150 работала при более высокой температуре, но затем было более резкое охлаждение потока 14 верхнего метанового погона в холодильной установке 170. Опять же,настоящие изобретения не ограничиваются этими типами вариантов конструкции. Возвращаясь опять к фиг. 1, жидкую флегму 18 возвращают в верхнюю дистилляционную, или ректификационную, зону 110. Затем жидкую флегму 18 гравитационным путем переносят через одно или более массопередающих устройств 116 в верхнюю ректификационную зону 110. В одном варианте исполнения массопередающие устройства 116 представляют собой ректификационные тарелки, которые создают каскадные серии переливных устройств 118 и спускных труб 119, подобно описанным выше тарелкам 126. Вместо тарелок также может быть применена беспорядочная или структурированная насадка. Когда текучие среды из потока 18 жидкой флегмы движутся вниз по ректификационным тарелкам 116, из верхней ректификационной зоны 110 испаряется дополнительный метан. Газообразный метан вновь объединяется с потоком 14 верхнего метанового погона, чтобы образовать часть потока 16 газообразного продукта. Однако остальная жидкостная фаза жидкой флегмы 18 падает на коллекторную тарелку 140. Когда это происходит, поток 18 жидкой флегмы неизбежно будет захватывать небольшую процентную долю углеводорода и остаточные кислотные газы, движущиеся вверх из зоны 108 регулируемого замораживания. Жидкая смесь метана и диоксида углерода собирается на коллекторной тарелке 140. Коллекторная тарелка 140 предпочтительно представляет собой главным образом плоскую деталь для сбора жидкостей. Однако, как и для плавильной тарелки 130, коллекторная тарелка 140 также имеет один, и предпочтительно многочисленные, газопропускный патрубок для проведения газов, поступающих снизу вверх из зоны 108 регулируемого замораживания. Может быть использована компоновка "газопропускной патрубок-и-колпачок", такая же, как представленная деталями 131 и 132 на фиг. 2 В и 2 С. Газопропускные патрубки 141 и колпачки 142 для коллекторной тарелки 140 показаны в увеличенном виде на фиг. 5, дополнительно обсуждаемой ниже. Здесь следует отметить, что в верхней ректификационной зоне 110 любой присутствующий H2S более предпочтительно растворяется в жидкости, нежели остается в газе при рабочей температуре. В этом отношении H2S имеет сравнительно низкую относительную летучесть. Посредством контакта остаточного пара с большим количеством жидкости криогенная дистилляционная колонна 100 обусловливает снижение концентрации H2S до уровня желательного предела в частях на миллион (ppm, млн-1), такого как соответственно техническим условиям для 10 или даже 4 млн-1. Когда текучая среда движется через массопередающие устройства 116 в верхней ректификационной зоне 110, H2S контактирует с жидким метаном и вытягивается из паровой фазы и становится частью жидкостного потока 20. Отсюда H2S движется в жидкой форме вниз через нижнюю дистилляционную зону 106 и в конечном итоге выходит из криогенной дистилляционной колонны 100 как часть кубового потока 22 сжиженных кислотных газов. В криогенной дистилляционной колонне 100 жидкость, собравшаяся на коллекторной тарелке 140,выводится из верхней ректификационной зоны 110 в виде жидкостного потока 20. Жидкостный поток 20 главным образом состоит из метана. В одном аспекте жидкостный поток 20 состоит примерно из 93 мол.% метана, 3% CO2, 0,5% H2S и 3,5% N2. В этот момент жидкостный поток 20 имеет температуру от около -125 до -130F (от -87,2 до -90 С). Он является лишь слегка более теплым, чем флегмовая текучая среда 18. Жидкостный поток 20 направляют в сборный барабан 174 для магистралей с соплами. Назначение сборного барабана 174 для магистралей с соплами состоит в обеспечении емкости для нагнетания насосом 176. При выходе из сборного барабана 174 для магистралей с соплами образуется распыляемый поток 21. Распыляемый поток 21 сжимается насосом 176 для второго повторного введения в криогенную дистилляционную колонну 100. В этом случае распыляемый поток 21 нагнетают в промежуточную зону 108 регулируемого замораживания и выпускают через сопла 122. Некоторая часть распыляемого потока 21, в особенности метан, испаряется и улетучивается при выходе из сопел 122. После этого метан поднимается через промежуточную зону 108 регулируемого замораживания, через газопропускные патрубки в коллекторной тарелке 140 и через массопередающие устройства 116 в верхней ректификационной зоне 110. Метан покидает дистилляционную колонну 100 как поток 14 верхнего метанового погона и в конечном итоге становится частью коммерческого продукта в газовом потоке 16. Поток 21, распыляемый из сопел 122, также обусловливает десублимацию диоксида углерода из газовой фазы. В этом отношении некоторая часть CO2 моментально переходит в газовую фазу и движется вверх вместе с метаном. Однако вследствие очень низкой температуры внутри зоны 108 регулируемого замораживания газообразный диоксид углерода быстро переходит в твердую фазу и начинает выпадать в виде "снега". Это явление называют десублимацией. Этим путем некоторое количество CO2 никогда не переходит вновь в жидкостную фазу, пока не дойдет до плавильной тарелки 130. Этот "снег" диоксида углерода оседает на плавильную тарелку 130 и плавится, переходя в жидкостную фазу. ОтсюдаCO2-обогащенная жидкость каскадом стекает вниз через массопередающие устройства или тарелки 126 в нижнюю дистилляционную зону 106 вместе с жидким CO2 из потока 12 глубоко охлажденного сырьевого газа, как описано выше. В этот момент любой остаточный метан из потока 21, распыляемого из сопел 122, должен быстро переходить в пар. Эти пары движутся вверх в криогенной дистилляционной колонне 100 и вновь поступают в верхнюю ректификационную зону 110. Желательно иметь глубоко охлажденную жидкость, в такой мере контактирующую с газом, который движется вверх по колонне 100, насколько это возможно. Если бы пар обходил стороной распыляемый поток 21, выбрасываемый из сопел 122, то до верхней ректификационной зоны 110 колонны 100 могли бы доходить увеличенные количества CO2. Для повышения эффективности газо-жидкостного контакта в зоне 108 регулируемого замораживания могут быть использованы многочисленные сопла 122,имеющие специально приспособленную конструкцию. Таким образом, вместо того, чтобы применять одиночный источник распыления на одном или более уровнях в потоке 21 флегмовой текучей среды,скорее можно использовать несколько магистралей 120 с соплами, необязательно оснащенных многочисленными распылительными соплами 122. Таким образом, конструкция распылительных сопел 122 влияет на массоперенос, который происходит внутри зоны 108 регулируемого замораживания. Авторы настоящего изобретения ранее предлагали разнообразные компоновки сопел в находящейся одновременно на рассмотрении патентной публикации WO 2008/091316, имеющей дату международной подачи 20 ноября 2007 г Эта заявка и фиг. 6 А и 6 В в ней включены здесь ссылкой для разъяснений относительно конструкций сопел. Стремятся к тому, чтобы сопла обеспечивали 360-градусный охват внутри зоны 108 регулируемого замораживания и создавали хороший контакт пара и жидкости и тепло/массоперенос. Этим, в свою очередь, достигают более эффективного глубокого охлаждения любого газообразного диоксида углерода, движущегося вверх через криогенную дистилляционную колонну 100. Применение многочисленных магистралей 120 и соответствующих перекрывающихся компоновок сопел 122 для полного охвата также сводит к минимуму противоточное смешение. В этом отношении полный охват предотвращает обратное перемещение тонкодисперсных частиц CO2 с малой массой обратно в колонну и поступление их в верхнюю ректификационную зону 110. В противном случае эти частицы повторно смешивались бы с метаном и поступали в поток 14 верхнего метанового погона, который пришлось бы опять вовлекать в рециркуляцию. Можно видеть, что процесс циркуляции паров через криогенную дистилляционную колонну 100 в конечном итоге приводит к газу, включающему коммерческий метановый продукт 16. Продуктовый газ 16 отправляют по трубопроводу на продажу. Продуктовый газ 16 предпочтительно соответствует техническим условиям на эксплуатацию трубопровода в отношении содержания CO2 на уровне от 1 до 4 мол.%, а также техническим условиям на содержание H2S на уровне 4 млн-1 или менее, при условии,что генерируют достаточное количество флегмы. В то же время кислотные газы и, если присутствуют,тяжелые углеводороды, удаляются с кубовым потоком 22 текучей среды. Было обнаружено, что имеет место изначальная неэффективность замораживания кислотных газовых компонентов с образованием твердого вещества в зоне 108 регулируемого замораживания, затем расплавления их с образованием жидкостного кубового потока 22 в нижней дистилляционной зоне 106 и затем выделения CO2 из любых подводимых природных газов с использованием донного кипятильника 160. В связи с замораживанием CO2 расходуется значительное количество энергии. Эта энергия, по меньшей мере частично, теряется, когда твердые компоненты в зоне 108 регулируемого замораживания расплавляют и затем повторно смешивают в нижней дистилляционной зоне 106 с любым H2S и прочими тяжелыми углеводородами в жидкостной фазе. Поскольку более желательно использование относительно чистого CO2 для нагнетания или утилизации кислотных газов, для отделения замороженного CO2 является желательным процесс обогащения кислотными газами или другой способ очистки. Это разделение должно происходить в нижней части зоны 108 регулируемого замораживания или в верхней части нижней дистилляционной зоны 106. Таким образом, вместо расплавления CO2 (и повторного смешения с любым жидким H2S и компонентами тяжелых углеводородов) и гравитационного падения жидкофазных компонентов через нижнюю дистилляционную зону 106 здесь предлагается заменить плавильную тарелку 130 коллекторной тарелкой. Коллекторная тарелка будет принимать осадки из зоны 108 регулируемого замораживания в форме твердофазно-жидкостной суспензии. Твердофазно-жидкостную суспензию будут собирать на коллекторной тарелке и удалять из криогенной дистилляционной колонны для отдельной переработки. Фиг. 6 А представляет вид сверху коллекторной тарелки 610 в одном варианте исполнения. Фиг. 6 В представляет вид в разрезе коллекторной тарелки 610, проведенном по линии В-В на фиг. 6 А. Фиг. 6 С представляет вид в разрезе коллекторной тарелки 610, проведенном по линии С-С. Коллекторная тарелка 610 будет описана с привлечением этих трех чертежей вместе. Во-первых, коллекторная тарелка 610 включает основание 620. Основание 620 может представлять собой главным образом плоскую деталь, или может иметь волнистости для увеличения площади поверхности. В любом отношении основание 620 предпочтительно делают наклонным внутрь вдоль противолежащих сторон, чтобы текучие среды, оседающие на основание 620, под действием силы тяжести стекали в сторону центральной спускной трубы 630. Что касается фиг. 6 С, сточная, или "спускная труба" 630 более четко видна посередине коллекторной тарелки 130. Основание 620 коллекторной тарелки наклонено внутрь в сторону спускной трубы 630 для подачи твердофазно-жидкостной суспензии. Основание 620 может быть наклонено любым способом,чтобы облегчить гравитационное выведение твердого вещества и жидкости. Так же, как для плавильной тарелки 130 из фиг. 2 А, коллекторная тарелка 610 на фиг. 6 А, 6 В и 6 С имеет многочисленные газопропускные патрубки 622, 624 (или "стояки для восходящего потока"). Газопропускные патрубки 622, 624 обеспечивают улучшенное распределение пара, позволяя текучим средам в газовой фазе проходить вверх из нижней дистилляционной зоны 106 и поступать в промежуточную зону 108 регулируемого замораживания. Это также содействует лучшему тепло/массопереносу в зоне 108 регулируемого замораживания. Газопропускные патрубки 622, 62 4 могут иметь любой профиль. Например, газопропускные патрубки 622, 624 могут быть круглыми, прямоугольными или любой иной формы, которая позволяет пару проходить через коллекторную тарелку 610. Газопропускные патрубки 622, 624 также могут быть узкими и протяженными вверх в зону 108 регулируемого замораживания. Это позволяет обеспечить благоприятный перепад давления для равномерного распределения пара по мере его подъема в зону 108 замораживания. Верхние отверстия газопропускных патрубков 622, 624 предпочтительно накрывают шляпками или колпачками 626. Колпачки 626 сводят к минимуму вероятность того, что твердые вещества, падающие из зоны 108 регулируемого замораживания, будут миновать коллекторную тарелку 610 и проходить в нижнюю дистилляционную зону 706. Вместе с основанием 620 спускная труба 630 предпочтительно является наклонной. Наклонная компоновка для спускной трубы 630' продемонстрирована в виде сбоку на фиг. 6D. Фиг. 6D представляет вид в разрезе коллекторной тарелки 610 из фиг. 6 А в альтернативном варианте исполнения. Вид показывает разрез, проведенный по линии В-В на фиг. 6 А. Коллекторную тарелку 610 компонуют введенной в криогенную дистилляционную колонну как часть системы для удаления кислотных газов из потока сырьевого газа. Коллекторная тарелка 610 предназначена для приема частиц твердых веществ и жидкостей, падающих из зоны регулируемого замораживания криогенной дистилляционной колонны. Коллекторная тарелка 610 дополнительно предназначена для транспортирования суспензии, образованной частицами твердого вещества и жидкости, из колонны и в установку для извлечения CO2. Фиг. 7 представляет схематическую диаграмму, показывающую газоперерабатывающую установку 700 для удаления кислотных газов из потока газообразных углеводородов в одном варианте осуществления согласно настоящему изобретению. Поток газообразных углеводородов получают при работах по добыче углеводородов, которые проводят в районе разработки месторождения, или "промысле". Промысел может представлять собой любое место, где добывают сжимаемые углеводороды. Промысел может быть на суше, вблизи побережья или на море. Промысел может действовать с использованием естественного пластового давления или может применять процедуры интенсификации добычи нефти вторичным методом. Заявленные здесь системы и способы не ограничиваются типом месторождения, которое нахо- 14024440 дится в стадии разработки, в такой мере, насколько обеспечивается добыча сжимаемых углеводородов,загрязненных компонентами кислотных газов. В газоперерабатывающей установке700 применяют коллекторную тарелку, такую как коллекторная тарелка 610 на фиг. 6 А. На фиг. 7 можно видеть, что коллекторную тарелку 610 встраивают в криогенную дистилляционную колонну 705. Дистилляционная колонна 705 имеет промежуточную зону 708 регулируемого замораживания. Зона 708 регулируемого замораживания, или распылительная секция, принимает распыляемую холодную жидкость, главным образом состоящую из метана. Распыляемая холодная жидкость предпочтительно представляет собой жидкую флегму, образованную из контура 714 верхнего погона ниже по потоку относительно дистилляционной колонны 705. Контур 714 верхнего погона включает холодильное оборудование внутри теплообменника 170, который служит для охлаждения потока 14 верхнего метанового погона и затем возвращения части потока 14 верхнего метанового погона в криогенную дистилляционную колонну 705 в качестве жидкой флегмы 18. Жидкую флегму 18 распыляют внутри зоны 708 регулируемого замораживания через магистрали 120 с соплами, чтобы обеспечить осаждение частиц твердого диоксида углерода. Как иллюстрировано на фиг. 7, жидкую флегму 18 подают в верхнюю ректификационную секцию 710, которая дополнительно будет обсуждена ниже, перед ее распылением через магистрали 120 с соплами. В других вариантах исполнения часть или вся жидкая флегма 18 может быть выведена непосредственно в магистрали 120 с соплами или в сборный барабан 174 для магистралей с соплами. Как и в случае колонны 100 на фиг. 1, криогенная дистилляционная колонна 705 предназначена для приема потока 10 исходной текучей среды, включающей кислотные газы. Поток 10 исходной текучей среды содержит метан, диоксид углерода и, возможно, следовые количества этана, азота, гелия и сероводорода. Поток 10 исходной текучей среды предпочтительно подвергают обезвоживанию до некоторой степени перед нагнетанием в дистилляционную колонну 705. Обезвоживание может быть выполнено пропусканием потока исходной текучей среды через процесс гликолевой дегидратации. (Система обезвоживания не показана на фиг. 7). В дополнение, поток 10 исходной текучей среды предпочтительно подвергают глубокому охлаждению перед поступлением его в дистилляционную колонну 705. Для глубокого охлаждения потока 10 исходной текучей среды предусмотрен теплообменник 150, такой как кожухотрубный теплообменник. Холодильная установка (не показана) поставляет хладагент (такой как жидкий пропан) в теплообменник 150 для доведения температуры потока 10 исходной текучей среды до уровня от около -30 до -40F (от-34,4 до -40 С). Затем поток 10 текучей среды может проходить через расширительное устройство 152,такое как клапан Джоуля-Томсона ("J-T"). В результате получают поток 712 глубоко охлажденного сырьевого газа. Температура потока 712 глубоко охлажденного сырьевого газа предпочтительно варьирует от -40 до -70F (от -40 до -56,7 С). Следует отметить, что в газоперерабатывающей установке 700 поток 712 сырьевого газа направляют в дистилляционную колонну 705 ниже зоны 708 регулируемого замораживания. Более конкретно,поток 712 сырьевого газа нагнетают в нижнюю дистилляционную зону 706 ниже зоны 708 регулируемого замораживания. Однако понятно, что поток 712 сырьевого газа может быть направлен через двухфазный резервуар, такой как резервуар 173, показанный на фиг. 1. Этим достигают разделения на поток,включающий главным образом пары метана (нагнетаемые в зону 708 регулируемого замораживания), и жидкие кислотные газы и, возможно, тяжелые углеводороды (нагнетаемые в нижнюю дистилляционную зону 706). Двухфазный резервуар 173 сводит к минимуму возможность закупоривания твердыми веществами впускного трубопровода и внутренних деталей дистилляционной колонны 705. В одном аспекте криогенная дистилляционная колонна 712 работает при давлении около 550 psi(3,8 МПа) в зоне 708 регулируемого замораживания, и температура потока 712 глубоко охлажденного сырьевого газа составляет приблизительно -62F (52,2 С). В этих условиях поток 712 сырьевого газа находится главным образом в жидкостной фазе, хотя потоком 712 глубоко охлажденного газа неизбежно может быть увлечена некоторая паровая фаза. Скорее всего, от присутствующего CO2 не будет происходить никакого формирования твердых веществ. Криогенная дистилляционная колонна 705 также включает верхнюю ректификационную зону 710. Верхняя ректификационная зона 710 находится над зоной 708 регулируемого замораживания. Как обсуждалось выше в связи с криогенной дистилляционной колонной 100 на фиг. 1, дистилляционная зона 710 служит для дополнительного отделения паров метана от молекул любого увлеченного диоксида углерода. Из дистилляционной зоны 710 выпускают поток 14 верхнего метанового погона. Она также выводит часть текучей среды в поток 20 жидкости, который пропускают через сборный барабан 174 для магистралей с соплами, затем в бустерный компрессор 176 и затем нагнетают обратно в колонну 705 через магистрали 120 с соплами. Как отмечено, газоперерабатывающая установка 700 дополнительно включает коллекторную тарелку 610. Коллекторную тарелку 610 размещают ниже зоны 708 регулируемого замораживания для приема,по существу, твердого материала, когда он осаждается из зоны 708 регулируемого замораживания. Предпочтительно, чтобы коллекторная тарелка 610 работала при температуре, например, от около -70 до-80F (от -56,7 до -62,2 С). Это находится на уровне или слегка ниже уровня температуры замерзанияCO2-компонента. Таким образом, на коллекторной тарелке 610 образуется суспензия. Коллекторная тарелка 610 предпочтительно имеет наклонное основание (показанное кодовым номером 620 позиции на фиг. 6 С) для направления суспензии в центральную спускную трубу (показанную кодовым номером 630 позиции на фиг. 6 С). Спускная труба 630, в свою очередь, необязательно может включать механическое транспортное устройство, такое как шнек (показанный кодовым номером 640 позиции на фиг. 6 В), внутри спускной трубы. Шнек 640 служит для механического перемещения суспензии, которая включает твердый CO2-материал, из криогенной дистилляционной колонны 705 и в сторону установки 740 для извлечения CO2. В газоперерабатывающей установке 700 предусмотрен выходной трубопровод 741 для суспензии. По выходному трубопроводу 741 для суспензии перемещают суспензию из дистилляционной колонны 705 в установку 740 для извлечения CO2. Этим путем диоксид углерода в значительной степени удаляют из дистилляционной колонны 705, прежде чем он будет падать в нижнюю дистилляционную зону 706. Суспензия может перемещаться под действием силы тяжести. Альтернативно или в дополнение, суспензию можно транспортировать с помощью шнека 640. В дополнительном альтернативном варианте, часть холодной жидкой флегмы 18 может быть направлена от боковой стенки дистилляционной колонны 705 в коллекторную тарелку 610 для вытеснения суспензии с коллекторной тарелки и из дистилляционной колонны 705. Есть несколько потенциальных преимуществ извлечения CO2 в твердом состоянии, не допуская расплавления твердого вещества и вывода в виде части кубового потока 722 текучей среды. Во-первых,когда действуют при надлежащих температуре и давлении, процесс кристаллизации диоксида углерода в твердое состояние обычно приводит, по существу, к чистому твердому материалу. В то время как некоторые следовые количества метана, сероводорода и тяжелых углеводородов могут быть увлечены твердыми веществами в виде части суспензии, отделение твердого CO2 позволяет получить, по существу,чистый CO2-продукт. Необходимость выпаривания легких продуктов, таких как метан, или других кислотных продуктов, таких как H2S, не является обязательной, поскольку такие продукты будут попадать в виде жидкостей в кубовый поток 722 текучей среды. Кроме того, поскольку значительную часть CO2 внутри потока 712 сырьевого газа извлекают в виде чистого твердого вещества, количество CO2 в кубовом потоке текучей среды будет сокращаться. Это, в свою очередь, снижает потребности в процессах обработки ниже по потоку, таких как установки для обогащения кислотных газов и извлечения серы (не показаны). В дополнение, ценные тяжелые углеводороды, такие как этан или пропан, могут быть с большей легкостью извлечены из кубового потока 722 текучей среды, поскольку содержание CO2 является значительно сниженным. В дополнение, удаление значительной части CO2 внутри потока 712 сырьевого газа в виде боковой фракции (по выходному трубопроводу 741 для суспензии) может снизить нагрузку на дистилляционную колонну 705, обусловленную паром и жидкостью. Это, в свою очередь, позволяет уменьшить рабочие нагрузки на кипятильник 160 и конденсатор, т.е. разделительную камеру 172, и снизить требования к охлаждению. Более важно то, что извлечение твердого CO2 может обеспечить возможность уменьшения диаметра колонны 705 при эквивалентной пропускной способности сырьевого материала. Сокращение размеров в основном является пропорциональным количеству твердого CO2, извлекаемого из колонны 705. С обращением опять к фиг. 7, суспензию на основе диоксида углерода транспортируют по выходному трубопроводу 741 для суспензии в установку 740 для извлечения CO2. Установка 740 для извлечения CO2 включает первый фильтр 742. Первый фильтр 742 предпочтительно представляет собой пористую среду, которая задерживает значительную часть твердого материала из суспензии. Первый фильтр 742 может представлять собой, например, проволочную сетку. Альтернативно, фильтр 742 может быть пористым материалом из сложного полиэфира или другого синтетического материала. Альтернативно,фильтр 742 может представлять собой центробежный сепаратор, гидроциклон, один или многие ленточные фильтры, один или многие фильтр-прессы или их комбинации. Жидкостная часть суспензии известна как "фильтрат". Фильтрат проходит через первый фильтр 742 и поступает в жидкостный трубопровод 744. Фильтрат включает главным образом СН 4, но также может содержать CO2 и H2S. Жидкостный трубопровод 744 подает фильтрат в жидкостный возвратный трубопровод 760. Жидкостный возвратный трубопровод 760 возвращает фильтрат в нижнюю дистилляционную зону 706 криогенной дистилляционной колонны 705. СН 4 испаряется и становится частью потока 14 верхнего метанового погона. H2S и любые компоненты тяжелых углеводородов выводятся из колонны 705 в виде жидкостей в кубовом потоке 722 текучей среды. Следует отметить, что жидкостный трубопровод 744 также может содержать тяжелые углеводороды, в частности, измеримые количества таких компонентов, как этан и пропан. Эти компоненты могут быть извлечены направлением фильтрата 744 в процесс, подобный традиционной технологической линии для сжижения природного газа ("NGL") (не показано). Первый фильтр 742 задерживает твердую часть суспензии, известную как "фильтрационный осадок". Фильтрационный осадок главным образом включает диоксид углерода. Твердый фильтрационный осадок направляют по первому трубопроводу 746 для твердого материала. Фильтрационный осадок может быть выведен с первого фильтра 742 по первому трубопроводу 746 для твердого материала с помощью шнекового транспортера, экстракторов Гильдебрандта или другими средствами, известными в технологии. После этого фильтрационный осадок может быть нагрет до перехода в жидкостную фазу. В одном аспекте твердый диоксид углерода из первого трубопровода 746 для твердого материала нагревают в теплообменнике 772. В теплообменнике 772 для расплавления диоксида углерода может быть использовано, например, тепло от потока 10 исходной текучей среды. В то же время нагретый жидкий CO2 направляют как в основном чистый сжиженный диоксид углерода по трубопроводу 786 для CO2-текучей среды. Вместо подачи замороженного диоксида углерода (или фильтрационного осадка) по трубопроводу 746 для твердого материала непосредственно в теплообменник 772, оператор может выбрать обработку замороженного диоксида углерода в стадии, в которой проводят дополнительное фильтрование. В газоперерабатывающей установке 700 установка 740 для извлечения CO2 может включать промывной резервуар 748. В промывном резервуаре 748 холодный жидкий CO2 распыляют на замороженный диоксид углерода. Это приводит к созданию новой суспензии, причем любые остаточные метан и сероводород вымываются из твердого фильтрационного осадка в виде жидкости. Холодный диоксид углерода, используемый в качестве промывного средства, направляют по питающему трубопроводу 784 для CO2. Холодный CO2, используемый в качестве промывного средства,предпочтительно отбирают из выпускного канала 778 для теплообменника 772. Трубопровод для холодного CO2 показан кодовым номером 780. С обращением опять к промывному резервуару 748, суспензию предпочтительно перемешивают в промывном резервуаре 748. В промывном резервуаре 748 может быть предусмотрено перемешивающее устройство 747. Перемешивающее устройство 747 может представлять собой, например, набор лопаток,которые вращаются внутри твердого материала для создания открытой поверхности. Созданная открытая поверхность обнажает твердый материал для воздействия холодного жидкого CO2 из питающего трубопровода 784. Это, в свою очередь, содействует вымыванию остаточных метана и сероводорода из твердого вещества. Новую суспензию выводят из промывного резервуара 748 по трубопроводу 750 для суспензии. Новую суспензию подают на второй фильтр, отмеченный на фиг. 7 кодовым номером 752 позиции. Второй фильтр 752 задерживает твердофазную часть новой суспензии. Твердофазная часть опять включает главным образом диоксид углерода. Твердофазная часть представляет собой второй фильтрационный осадок,и ее подают по второму трубопроводу 756 для твердого материала. После этого второй фильтрационный осадок может быть нагрет до перехода в жидкостную фазу. Следует отметить, что стадии, на которых проводят промывание и фильтрование, показаны как проводимые в отдельных резервуарах, например, промывном резервуаре 748 и фильтрационном резервуаре 752. Однако оператор может выбрать объединение промывания и фильтрования твердого материала в одиночном резервуаре. Жидкая часть новой суспензии, известная как второй фильтрат, проходит через второй фильтр 752 и направляется в жидкостный трубопровод 754. Второй фильтрат включает СН 4 и, возможно, H2S и тяжелые углеводороды. Жидкостный трубопровод 754 подает жидкую часть суспензии в жидкостный возвратный трубопровод 760. Таким образом, жидкость, представляющую собой второй фильтрат 754, объединяют с жидкостью, представляющей собой первый фильтрат 754, перед нагнетанием в дистилляционную колонну 705 по жидкостному возвратному трубопроводу 760. СН 4 испаряется и становится частью потока 14 верхнего метанового погона. H2S и С 2+-соединения выводятся из колонны 705 в виде жидкостей в кубовом потоке 722 текучей среды. Если либо в первом фильтрате 744, либо во втором фильтрате 754 может содержаться любой расплавленный CO2, то расплавленный CO2 будет испаряться в зоне 708 регулируемого замораживания и в конечном итоге осаждаться обратно на коллекторную тарелку 610 в виде замороженного материала. Необязательно, первый 744 и/или второй 754 фильтрат может быть выведен через жидкостный возвратный трубопровод 760 в малую периферийную дистилляционную колонну (не показана) для дополнительной очистки. Оператор может выбрать выведение в основном чистого твердого CO2 по трубопроводу 756 непосредственно в теплообменник 772. Альтернативно, может быть проведено дополнительное отделение загрязняющих примесей. Блок 770 на фиг. 7 изображает одну или более дополнительных стадий, в которых проводят промывание и фильтрование для твердого CO2 в трубопроводе 756. Число стадий промывания и фильтрования зависит от желательной чистоты CO2-продукта. Трубопровод 782 показан подводящим холодный CO2 в качестве промывного средства. Из дополнительных стадий промывания и фильтрования получают третий (и последующие) фильтрат 774. Третий (и последующий) твердый CO2 (или фильтрационный осадок) подают по трубопроводу 776 в теплообменник 772. Трубопровод для конечногоCO2-продукта виден как трубопровод 786. Жидкий CO2-продукт может быть использован для нагнетания кислотных газов, или может быть направлен на продажу в виде высокочистого продукта. Потребитель может, например, использовать жидкий CO2-продукт для интенсификации добычи нефти вторичным методом или на другие цели. Газоперерабатывающая установка 700 на фиг. 7 идеально подходит для применения в условиях, где поток 712 глубоко охлажденного сырьевого газа имеет высокое содержание CO2, такое как более высокое, чем приблизительно 30%. При этом условии для замораживания всего CO2 из потока 712 сырьевого газа может понадобиться значительное охлаждение. Поэтому представляется, что более энергетически выгодным является нагнетание потока 712 сырьевого газа в нижнюю дистилляционную зону 706 под зоной 808 регулируемого замораживания и под коллекторной тарелкой 610. Любой CO2, который остается в жидком состоянии и выводится из дистилляционной колонны 705 с кубовым сырьевым потоком 722,будет извлечен с помощью кипятильника 160 и повторно введен в нижнюю дистилляционную зону 706. В иллюстративной газоперерабатывающей системе 700 коллекторную тарелку 610 и соответствующий выходной трубопровод 741 для суспензии размещают значительно выше места введения сырьевого газа. Оператор может выбрать более высокую точку, в которой поток 12 сырьевого газа поступает в криогенную дистилляционную колонну 705. Представляется, что размещение места введения на большей высоте будет увеличивать количество текучей среды из потока 712 сырьевого газа, которое извлекается на коллекторной тарелке 610 в виде твердого вещества. Это является более преимущественным, где поток 712 сырьевого газа имеет более низкое содержание CO2, такое как от около 10 до 30 мол.%. В одном моделировании, проведенном Заявителем, коллекторную тарелку 610 и соответствующий выходной трубопровод 741 для суспензии размещали в месте введения сырьевого газа или слегка выше него. Поток 712 сырьевого газа моделировали имеющим состав из 70 мол.% CO2 и 30 мол.% СН 4. Температура исходного газа была принята на уровне 40 С, с величиной расхода нагнетаемого потока приблизительно 10000 стандартных м 3/ч. Криогенную дистилляционную колонну 705 моделировали действующей при давлении 450 psia (3,1 МПа, абсолютных). В этом моделировании приблизительно 93% сырьевого CO2 выходили из криогенной дистилляционной колонны в виде твердого вещества. Очень малое количество текучей среды оставалось для движения вниз по дистилляционной колонне в форме жидкости. Конечно, тем самым получалось значительное сокращение объема для кубового потока 722 текучей среды, и характеристики нагрузки для кипятильника 160 снижались примерно на 89%. Недостаток этого подхода состоит в том, что требуется усиленное охлаждение в теплообменнике 150 выше по потоку относительно дистилляционной колонны 705 для глубокого охлаждения потока 10 исходной текучей среды. Это отчасти компенсируется небольшим снижением степени охлаждения, необходимой в теплообменнике 170 ниже по потоку относительно дистилляционной колонны 705. Фиг. 8 представляет схематическую диаграмму, показывающую газоперерабатывающую установку 800 для удаления кислотных газов из газового потока в альтернативном варианте осуществления согласно настоящему изобретению. Газоперерабатывающая установка 800 в основном подобна газоперерабатывающей установке 700. В этом отношении в газоперерабатывающей установке 800 также используют коллекторную тарелку, такую же, как коллекторная тарелка 610 на фиг. 6 А. Коллекторную тарелку 610 встраивают в криогенную дистилляционную колонну 805. Дистилляционная колонна 805 опять же имеет промежуточную зону 808 регулируемого замораживания. Зона 808 регулируемого замораживания, или распылительная секция, принимает распыляемую холодную жидкость, включающую главным образом метан. Как и в случае колонны 705 на фиг. 1, криогенная дистилляционная колонна 805 предназначена для приема потока 10 исходной текучей среды, включающей углеводород и кислотные газы. Поток 10 исходной текучей среды предпочтительно подвергают обезвоживанию до некоторой степени перед нагнетанием в дистилляционную колонну 805. В дополнение, поток 10 исходной текучей среды предпочтительно подвергают глубокому охлаждению перед поступлением его в дистилляционную колонну 805. Для глубокого охлаждения потока 10 исходной текучей среды предусмотрен теплообменник 150, такой как кожухотрубный теплообменник. Холодильная установка (не показана) поставляет хладагент (такой как жидкий пропан) в теплообменник 150 для доведения температуры потока 10 исходной текучей среды до уровня от около -60 до -80F (от -51,1 до -62,2 С). Затем поток 10 исходной текучей среды может проходить через расширительное устройство 152, такое как клапан Джоуля-Томсона ("J-T"). В результате получают поток 812 глубоко охлажденного сырьевого газа. Как отмечено выше, в газоперерабатывающей установке 700 поток 712 сырьевого газа поступает ниже зоны 708 регулируемого замораживания. Более конкретно, поток 712 сырьевого газа нагнетают в нижнюю дистилляционную зону 706. Однако в криогенной дистилляционной колонне 805 дистилляционная зона (706 на фиг. 7) устранена, и коллекторная тарелка 610 теперь находится в зоне 808 регулируемого замораживания. В дополнение, поток 812 сырьевого газа нагнетают в зону 808 регулируемого замораживания над коллекторной тарелкой 610. Это согласуется с вышеописанным моделированием. Цель перемещения места нагнетания для потока 812 глубоко охлажденного сырьевого газа вверх в зону 808 регулируемого замораживания заключается в достижении более высокой степени извлечения твердого CO2. Для исполнения этого температуру потока 812 глубоко охлажденного сырьевого газа доводят до уровня от около -60 до -80F (от -51,1 до -62,2 С). Это представляет собой диапазон более низ- 18024440 ких температур, чем температуры, которые были сообщены потоку 712 сырьевого газа на фиг. 7. Когда поток 812 сырьевого газа поступает в колонну 805, он мгновенно испаряется и охлаждается, вызывая осаждение CO2 в зоне 808 регулируемого замораживания. Любой парообразный CO2 будет охлаждаться жидкой флегмой из СН 4, падающей вниз из магистралей 120 с соплами. Этим формируется твердое вещество, которое осаждается на коллекторной тарелке 610 с образованием суспензии. Как и в случае газоперерабатывающей установки 700, суспензия перемещается в газоперерабатывающей установке 800 из криогенной дистилляционной колонны 805, через выходной трубопровод 741 для суспензии, и в систему 840 для извлечения CO2. Система 840 для извлечения CO2 может быть такой же, как система 740 для извлечения CO2 на фиг. 7. В этом отношении суспензия, главным образом состоящая из диоксида углерода, проходит через первый фильтр 742, и затем, необязательно, проходит через одну, две или три стадии, на которых проводят промывание и фильтрование, пока не будет получен в основном чистый твердый CO2. Твердый CO2 предпочтительно нагревают с помощью теплообменника 7 72 и затем выводят через выпускной канал 778 в виде жидкости. Жидкий CO2 выпускают как продукт по трубопроводу 786. В системе 840 для извлечения CO2 фиг. 8 первый фильтрат 744 из первого фильтра 742 возвращают в криогенную дистилляционную колонну 805. Это согласуется с работой системы 740 для извлеченияCO2 фиг. 7. Однако вместо возвращения обогащенного метаном первого фильтрата 744 через жидкостный возвратный трубопровод 760 и направления в колонну 805 первый фильтрат 744 объединяют с потоком 10 исходной текучей среды. Этим путем обогащенный метаном первый фильтрат 744 может быть подвергнут повторному глубокому охлаждению перед нагнетанием в зону 808 регулируемого замораживания. В системе 840 для извлечения CO2 второй фильтрат 754 и последующий(ие) фильтрат(ы) 874 не объединяют в жидкостном возвратном трубопроводе 760; скорее второй фильтрат 754 и последующий(ие) фильтрат(ы) 874 объединяют друг с другом и направляют в находящуюся ниже по потоку дистилляционную колонну 892. Второй фильтрат 754 и последующий(ие) фильтрат(ы) 874 главным образом состоят из сероводорода, но могут содержать следовые количества метана и диоксида углерода. В кипятильнике 892 метан высвобождается как поток 894 извлеченного метана. Поток 894 извлеченного метана объединяют с метановым продуктом 16 для продажи и поставляют на рынок как продукт 898 для продажи. Из кипятильника 892 также выходит жидкость 896. Жидкость 896 главным образом включает сероводород со следовыми количествами диоксида углерода. Обогащенную сероводородом (H2S) жидкость 896 отправляют на утилизацию или проводят через установку для извлечения серы (не показана). В качестве альтернативы, второй фильтрат 754 и последующий(ие) фильтрат(ы) 874 могут быть утилизированы или направлены в установку для извлечения серы без проведения через кипятильник 892. Это в особенности применимо, если уровень содержания СН 4 не гарантирует извлечения или требует разделения. Как можно видеть на фиг. 7 и 8, могут быть использованы различные технологические схемы. Оптимальная компоновка будет зависеть от ряда переменных факторов. Эти переменные факторы включают доступность (или производительность) охлаждения, создаваемого внутри теплообменника верхнего погона, такого как теплообменник 170, желательную чистоту CO2-продукта 786 и, что наиболее важно,состава потока 10 исходной текучей среды. Независимо от выбранной схемы потоков, будет использован базовый принцип дистилляции в сочетании с удалением и очисткой твердого вещества. В некоторых ситуациях поток 10 исходной текучей среды может иметь высокую концентрацию сероводорода, такую как более высокую, чем от около 5 до 10 процентов. В некоторых вариантах исполнения, таких, в которых желательно извлечение твердого CO2, может быть нежелательным проведение потока сырьевого газа, имеющего высокую концентрацию H2S, через криогенную дистилляционную колонну, поскольку представляется, что высокие уровни содержания H2S могут приводить к растворениюCO2, тем самым препятствуя образованию твердого вещества в зоне регулируемого замораживания. В этой ситуации природные газы с высоким отношением H2S к CO2 могут быть поданы в колонну предварительной обработки (не показана) для селективного удаления H2S до введения в основную дистилляционную колонну 705 или 805. Отделение может быть достигнуто с использованием таких процессов отделения H2S, как селективное поглощение аминами, окислительно-восстановительные процессы или адсорбция. После этого газовый поток может быть обезвожен и охлажден в соответствии с вышеописанными иллюстративными технологическими установками 700 или 800. Дополнительно или альтернативно, другие варианты исполнения могут быть нечувствительными к состоянию извлеченногоCO2-продукта, и H2S может быть оставлен в потоке исходной текучей среды. Дополнительное преимущество удаления сернистых соединений выше по потоку относительно дистилляционной колонны состоит в том, что удаление серы может позволить получение CO2-продукта 786 высокой чистоты из системы 740 или 840 извлечения. В дополнение, из кубового потока 722 текучей среды могут быть извлечены высокочистые С 2+-продукты. Конечно, можно допустить, чтобы небольшие количества H2S просочились в криогенную дистилляционную колонну 705, 805 при условии, что фазовое поведение внутри колонны 705, 805 обеспечит возможность формирования твердого CO2. Такие малые количества H2S будут выведены с кубовым потоком 22 текучей среды. Здесь также представлен способ удаления кислотных газов из потока сырьевого газа. Фиг. 9 представляет блок-схему, которая показывает способ 900 удаления кислотных газов из потока сырьевого газа с использованием системы для удаления кислотных газов в одном варианте осуществления согласно настоящим изобретениям. Поток сырьевого газа включает метан, диоксид углерода и, наиболее вероятно,другие компоненты, такие как этан и сероводород. Способ 900 прежде всего включает стадию, в которой готовят криогенную дистилляционную колонну. Эта стадия показана Блоком 905. Колонна имеет зону регулируемого замораживания, которая принимает распыляемую холодную жидкость, главным образом состоящую из метана. Колонна дополнительно имеет коллекторную тарелку ниже зоны регулируемого замораживания. Способ 900 также включает стадию, в которой нагнетают поток сырьевого газа в криогенную дистилляционную колонну. Это продемонстрировано в блоке 910. В одном варианте компоновки поток сырьевого газа нагнетают в дистилляционную колонну в нижней дистилляционной зоне под зоной регулируемого замораживания. В еще одном варианте компоновки поток сырьевого газа нагнетают в дистилляционную колонну в самую зону регулируемого замораживания. Поток сырьевого газа предпочтительно был подвергнут обезвоживанию перед нагнетанием его в дистилляционную колонну. Способ 900 дополнительно включает стадию, в которой проводят глубокое охлаждение потока сырьевого газа. Это обозначено в блоке 915 фиг. 9. Глубокое охлаждение потока сырьевого газа вызывает осаждение диоксида углерода внутри потока сырьевого газа на коллекторную тарелку в виде, по существу, твердого материала. В то же время давление в дистилляционной колонне является более низким, чем давление подводимого потока, что обусловливает почти полное испарение метана внутри потока сырьевого газа. Метан проходит через верхнюю ректификационную зону над зоной регулируемого замораживания и затем выходит из криогенной дистилляционной колонны как поток верхнего метанового погона. Способ 900 также включает стадию, в которой пропускают поток верхнего метанового погона через холодильную систему ниже по потоку относительно криогенной дистилляционной колонны. Это представлено в блоке 920. Холодильная система охлаждает по меньшей мере часть потока верхнего метанового погона до сжижения. Способ 900 дополнительно включает стадию, в которой возвращают часть охлажденного потока верхнего метанового погона в криогенную дистилляционную колонну в качестве жидкой флегмы. Жидкая флегма, в свою очередь, служит для распыления холодной жидкости. Это представлено в блоке 925. Также в качестве части способа 900, из криогенной дистилляционной колонны в основном удаляют твердый материал. Это показано в блоке 930. Удаление, по существу, твердого материала предпочтительно проводят путем гравитационного течения. Альтернативно, может быть предусмотрено механическое транспортное устройство, такое как винтовой транспортер или шнек. Шнек может находиться внутри спускной трубы коллекторной тарелки, как продемонстрировано на фиг. 6 А-6D. Альтернативно, шнек может быть размещен снаружи дистилляционной колонны для направления, по существу, твердого материала в систему извлечения CO2. В любом случае шнек срезает, по существу, твердый материал, выводит его в виде суспензии из дистилляционной колонны и направляет в систему извлечения CO2. Способ 900 дополнительно включает стадию, в которой разделяют суспензию диоксида углерода на твердый материал и жидкий материал. Это показано в блоке 935. Первый твердый материал главным образом состоит из диоксида углерода, тогда как жидкий материал включает метан и остаточный диоксид углерода. Жидкий материал может включать другие компоненты, такие как сероводород, тяжелые углеводороды и даже легкие ароматические соединения. Стадия блока 935, в которой проводят разделение, может быть проведена пропусканием суспензии через первый фильтр. Этим получают первый фильтрационный осадок, главным образом состоящий из твердого диоксида углерода, и первый фильтрат, включающий метан и диоксид углерода в жидкостной фазе. Первый фильтр может представлять собой, например, пористую среду или центрифугу. Стадия блока 935, в которой проводят разделение, может дополнительно включать стадии, на которых выполняют промывание первого фильтрационного осадка потоком холодного диоксида углерода,перемешивают первый фильтрационный осадок для получения первой твердофазно-жидкостной суспензии и подают первую твердофазно-жидкостную суспензию на второй фильтр. Второй фильтр образует второй фильтрационный осадок, главным образом состоящий из твердого диоксида углерода, и второй фильтрат, включающий главным образом метан, но также диоксид углерода и сероводород, опять же в жидкостной фазе. Может быть предпринято дополнительное удаление CO2. Например, стадия блока 935, в которой проводят разделение, может дополнительно включать стадии, на которых проводят промывание второго фильтрационного осадка с использованием потока холодного диоксида углерода, перемешивают второй фильтрационный осадок для получения твердофазно-жидкостной суспензии и направляют твердофазножидкостную суспензию еще и на третий фильтр. Этим получают третий фильтрационный осадок, главным образом состоящий из твердого диоксида углерода, и третий фильтрат, включающий метан, сероводород и диоксид углерода, опять же в жидкостной фазе. Способ 900 также включает стадию, в которой возвращают по меньшей мере часть второго жидкого материала в криогенную дистилляционную колонну. Это показано в блоке 940. В одном аспекте второй жидкий материал направляют обратно в нижнюю дистилляционную зону. В еще одном аспекте второй жидкий материал объединяют с потоком сырьевого газа и нагнетают в колонну в зоне регулируемого замораживания. В одном варианте исполнения способа 900 объединяют первый фильтрат и второй фильтрат. Объединенная текучая среда из фильтратов образует жидкий материал, который возвращают в криогенную дистилляционную колонну. В этом случае жидкий материал предпочтительно нагнетают в нижнюю дистилляционную зону. В еще одном варианте исполнения способа 900 в дистилляционную колонну возвращают только первый фильтрат. В этом случае первый фильтрат может быть возвращен обратно в зону регулируемого замораживания. Дистилляционная колонна предпочтительно не будет иметь нижнюю дистилляционную зону; вместо этого второй и, необязательно, третий фильтраты направляют в отдельную, находящуюся ниже по потоку дистилляционную колонну, где остаточные газы окончательно отделяют от метана. В этом случае получают поток извлеченного метана, который объединяют с потоком верхнего метанового погона криогенной дистилляционной колонны для продажи. В еще одном дополнительном варианте исполнения способа 900 нагревают конечный фильтрационный осадок. Это выполняют независимо от того, имеются ли одна, две, три или более стадий фильтрования. Конечный фильтрационный осадок представляет собой фильтрационный осадок последней стадии, отобранный с конечного фильтра, каким бы он ни был. Конечно, сюда будет входить по меньшей мере часть первого твердого материала. Эта стадия, в которой проводят нагревание, показана в блоке 945 фиг. 9. Стадия, в которой проводят нагревание, может быть выполнена, например, теплообменом твердого диоксида углерода, составляющего фильтрационный осадок, с потоком сырьевого газа. В результате получают холодную жидкость из чистого диоксида углерода. Чистый диоксид углерода может быть продан на рынке или использован в работах для интенсификации добычи нефти вторичным методом. В дополнение, часть потока холодного диоксида углерода может быть применена в качестве промывного средства для создания твердофазно-жидкостной суспензии, как описано выше. В то время как будет очевидно, что описанные здесь изобретения хорошо рассчитаны на достижение вышеизложенных выгод и преимуществ, будет понятно, что изобретения восприимчивы к модификации, вариации и изменению без выхода за пределы их смысла. Представлены усовершенствования для функционирования процесса удаления кислотных газов с использованием зоны регулируемого замораживания. Усовершенствования представляют конструкцию для удаления CO2 до очень низких уровней содержания в продуктовом газе. Изобретения здесь также могут снизить требования, предъявляемые к охлаждению в криогенных дистилляционных колоннах, в то же время с соблюдением технических условий для сжиженного природного газа (LNG) в отношении максимально допустимого содержания CO2. ФОРМУЛА ИЗОБРЕТЕНИЯ 1. Система для удаления кислотных газов из потока сырьевого газа, содержащая криогенную дистилляционную колонну, имеющую зону регулируемого замораживания, которая принимает распыляемую холодную жидкость, главным образом метан, причем колонна принимает и затем разделяет поток сырьевого газа на поток газообразного головного метанового погона и, по существу,твердый материал, состоящий из осажденного диоксида углерода; холодильное оборудование, расположенное по потоку после криогенной дистилляционной колонны, для охлаждения потока, головного метанового погона и возвращения его части в криогенную дистилляционную колонну в качестве холодной распыляемой жидкости; коллекторную тарелку, расположенную под зоной регулируемого замораживания, для приема, по существу, твердого материала, когда он осаждается в зоне регулируемого замораживания, и направления, по существу, твердого материала из криогенной дистилляционной колонны; первый фильтр для приема, по существу, твердого материала и разделения, по существу, твердого материала на поток, содержащий первый фильтрационный осадок, в основном состоящий из диоксида углерода, и поток, содержащий фильтрат, содержащий нетвердый материал, представляющий собой по меньшей мере один из группы, состоящей из этана, пропана, бутана или сероводорода; промывной резервуар для промывания первого фильтрационного осадка с использованием потока холодного диоксида углерода и получения первой твердофазно-жидкостной суспензии; второй фильтр для приема первой твердофазно-жидкостной суспензии и разделения первой твердофазно-жидкостной суспензии на второй фильтрационный осадок, содержащий главным образом твердый диоксид углерода, и второй фильтрат, включающий нетвердый материал, представляющей собой по меньшей мере одно из группы, состоящей из этана, пропана, бутана или сероводорода; и жидкостный возвратный трубопровод для возвращения по меньшей мере части нетвердого первого фильтрата или второго фильтрата в криогенную дистилляционную колонну. 2. Система по п.1, в которой коллекторная тарелка содержит спускную трубу, в которую падает осажденный, по существу, твердый материал. 3. Система по п.1, в которой коллекторная тарелка направляет, по существу, твердый материал из криогенной дистилляционной колонны (i) гравитационным течением, (ii) действием механического транспортного устройства, (iii) с помощью распыления части холодной распыляемой жидкости в коллекторную тарелку и, по существу, на твердый материал или (iv) их комбинацией. 4. Система по п.3, в которой коллекторная тарелка содержит спускную трубу, в которую падает осажденный, по существу, твердый материал; и механическое транспортное устройство, такое как шнек,который размещен внутри спускной трубы. 5. Система по п.1, в которой криогенная дистилляционная колонна дополнительно содержит верхнюю ректификационную зону над зоной регулируемого замораживания и нижнюю дистилляционную зону под зоной регулируемого замораживания, причем криогенная дистилляционная колонна выполнена с возможностью приема потока сырьевого газа в нижнюю дистилляционную зону. 6. Система по п.5, в которой криогенная дистилляционная колонна выполнена с возможностью выведения кубового потока из нижней дистилляционной зоны, причем кубовый поток содержит кислотные газы в жидкостной фазе; при этом по меньшей мере часть первого фильтрата возвращается в нижнюю дистилляционную зону по жидкостному возвратному трубопроводу. 7. Система по п.6, в которой кубовый сырьевой поток содержит метан, диоксид углерода, этан, пропан, бутан, сероводород, ароматические углеводороды или их комбинации, по существу, в жидкостной фазе. 8. Система по п.1, в которой первый фильтр включает (i) пористую среду, (ii) один или более фильтр-пресс, (iii) один или более ленточный фильтр, (iv) гидроциклон, (v) центробежный сепаратор или(vi) их комбинации. 9. Система по п.6, в которой коллекторная тарелка действует при температуре от около -70 до -80F(от -56,7 до -62,2 С). 10. Система по п.1, в которой промывной резервуар содержит смеситель для перемешивания первого фильтрационного осадка, чтобы получить первую твердофазно-жидкостную суспензию. 11. Система по п.1, в которой второй фильтр содержит пористую среду. 12. Система по п.1, выполненная с возможностью объединения первого фильтрата и второго фильтрата и возвращения объединенного первого фильтрата и второго фильтрата в нижнюю дистилляционную зону в качестве жидкого материала. 13. Система по п.12, в которой первый фильтрат дополнительно содержит диоксид углерода, сероводород или их комбинации. 14. Система по п.1, дополнительно содержащая теплообменник, нагревающий, по существу, твердый материал, отобранный в основном из фильтрационного осадка конечной стадии, для получения потока в основном чистого диоксида углерода в жидкостной фазе; при этом поток холодного диоксида углерода содержит часть потока в основном чистого диоксида углерода. 15. Система по п.14, в которой фильтрационный осадок конечной стадии получен после первого фильтра на втором фильтре или третьем фильтре. 16. Система по п.5, в которой поток сырьевого газа содержит сероводород; система дополнительно содержит систему для удаления сероводорода, выполненную с возможностью удаления значительной части сероводорода из потока сырьевого газа до нагнетания потока сырьевого газа в криогенную дистилляционную колонну. 17. Система по п.1, в которой криогенная дистилляционная колонна дополнительно содержит верхнюю ректификационную зону над зоной регулируемого замораживания; при этом криогенная дистилляционная колонна выполнена с возможностью приема потока сырьевого газа в зону регулируемого замораживания. 18. Система по п.17, в которой жидкостной возвратный трубопровод объединяет по меньшей мере часть первого или второго фильтрата с потоком сырьевого газа перед нагнетанием потока сырьевого газа в криогенную дистилляционную колонну. 19. Система по п.18, дополнительно содержащая дистилляционный сепаратор, выполненный с возможностью приема второго фильтрата и для получения потока кубовой жидкости, включающей диоксид углерода, H2S или их комбинации в жидкостной фазе, и потока извлеченного метана; при этом поток извлеченного метана объединяют с потоком головного метанового погона. 20. Система по п.19, в которой каждый из первого фильтрата и потока кубовой жидкости дополнительно включает сероводород. 21. Способ удаления кислотных газов из потока обезвоженного сырьевого газа с помощью системы по п.1, согласно которому готовят криогенную дистилляционную колонну, причем колонна имеет зону регулируемого замораживания, которая принимает холодную распыляемую жидкость, содержащую главным образом метан,и коллекторную тарелку под зоной регулируемого замораживания; нагнетают поток сырьевого газа в криогенную дистилляционную колонну; подвергают поток сырьевого газа глубокому охлаждению, чтобы вызвать осаждение диоксида углерода внутри потока сырьевого газа на коллекторную тарелку в виде, по существу, твердого материала, в то же время обеспечивая значительное испарение метана и выход его из криогенной дистилляционной колонны в виде потока, представляющего собой поток головного метанового погона; пропускают поток головного метанового погона через холодильную систему, расположенную по потоку после криогенной дистилляционной колонны, причем холодильная система охлаждает поток головного метанового погона; возвращают часть охлажденного потока головного метанового погона в криогенную дистилляционную колонну в виде жидкой флегмы, служащей в качестве холодной распыляемой жидкости; удаляют, по существу, твердый материал из криогенной дистилляционной колонны в виде суспензии; разделяют, по существу, твердый материал в первом фильтре на поток, содержащий первый фильтрационный осадок, состоящий из твердого материала, состоящего в основном из диоксида углерода, и поток, содержащий первый фильтрат, представляющий собой жидкий материал, содержащий один из группы, состоящей из этана, пропана, бутана или сероводорода; промывают первый фильтрационный осадок с использованием потока холодного диоксида углерода для создания первой твердофазно-жидкостной суспензии; разделяют первую твердофазно-жидкостную суспензию на второй фильтрационный осадок, состоящий в основном из твердой двуокиси углерода, и второй фильтрат, представляющий собой жидкий материал, содержащий по меньшей мере один из группы, состоящей из этана, пропана, бутана или сероводорода; и возвращают по меньшей мере часть жидкого материала из первого или второго фильтратов в криогенную дистилляционную колонну. 22. Способ по п.21, согласно которому коллекторная тарелка содержит спускную трубу, в которую падает осажденный, по существу, твердый материал и механическое транспортное устройство внутри спускной трубы; при этом при удалении, по существу, твердого материала из криогенной дистилляционной колонны с помощью механического транспортного устройства перемещают, по существу, твердый материал из спускной трубы за пределы криогенной дистилляционной колонны. 23. Способ по п.21, согласно которому коллекторная тарелка содержит спускную трубу, в которую падает осажденный, по существу, твердый материал, и с помощью коллекторной тарелки направляют, по существу, твердый материал из криогенной дистилляционной колонны (i) гравитационным течением, (ii) действием механического транспортного устройства, (iii) с помощью распыления части холодной распыляемой жидкости в коллекторную тарелку и, по существу, на твердый материал или (iv) их комбинацией. 24. Способ по п.21, согласно которому криогенная дистилляционная колонна дополнительно содержит верхнюю ректификационную зону над промежуточной зоной регулируемого замораживания и нижнюю дистилляционную зону под промежуточной зоной регулируемого замораживания и поток сырьевого газа нагнетают в нижнюю дистилляционную зону. 25. Способ по п.24, согласно которому дополнительно выводят кубовый поток из нижней дистилляционной зоны, причем кубовый поток содержит кислотные газы в жидкостной фазе, и при возвращении по меньшей мере части жидкого материала в криогенную дистилляционную колонну подают жидкий материал в нижнюю дистилляционную зону. 26. Способ по п.25, согласно которому кубовый поток содержит метан, этан, пропан, бутан, сероводород, диоксид углерода или их комбинации, по существу, в жидкостной фазе. 27. Способ по п.21, согласно которому смешивают первый фильтрационный осадок с потоком холодного диоксида углерода для получения первой твердофазно-жидкостной суспензии. 28. Способ по п.21, согласно которому дополнительно объединяют первый фильтрат и второй фильтрат; при этом второй жидкий материал, который возвращают в нижнюю дистилляционную зону,содержит объединенные первый фильтрат и второй фильтрат. 29. Способ по п.21, согласно которому дополнительно нагревают, по существу, твердый материал,отобранный в основном из фильтрационного осадка конечной стадии, для получения потока, по существу, чистого диоксида углерода в жидкостной фазе; при этом поток холодного диоксида углерода содержит часть потока, по существу, чистого диоксида углерода. 30. Способ по п.29, согласно которому при нагревании пропускают, по существу, твердый материал, отобранный в основном из фильтрационного осадка конечной стадии, через такой теплообменник, в котором происходит теплообмен с потоком сырьевого газа. 31. Способ по п.21, согласно которому первый фильтр содержит пористую среду или центрифугу. 32. Способ по п.21, согласно которому поток обезвоженного сырьевого газа включает сероводород и согласно которому дополнительно удаляют значительную часть сероводорода из потока сырьевого газа до нагнетания потока сырьевого газа в криогенную дистилляционную колонну. 33. Способ по п.21, согласно которому криогенная дистилляционная колонна дополнительно содержит верхнюю ректификационную зону над промежуточной зоной регулируемого замораживания и поток сырьевого газа нагнетают в зону регулируемого замораживания. 34. Способ по п.21, согласно которому при возвращении по меньшей мере части первого фильтрата в криогенную дистилляционную колонну (i) нагнетают первый фильтрат непосредственно обратно в зону регулируемого замораживания или (ii) объединяют первый фильтрат с потоком сырьевого газа перед нагнетанием потока сырьевого газа в криогенную дистилляционную колонну. 35. Способ по п.21, согласно которому дополнительно промывают второй фильтрационный осадок с использованием потока холодного диоксида углерода; перемешивают второй фильтрационный осадок для получения твердофазно-жидкостной суспензии и подают твердофазно-жидкостную суспензию на третий фильтр, тем самым получая третий фильтрационный осадок, состоящий главным образом из твердого диоксида углерода, и третий фильтрат, содержащий метан, диоксид углерода и сероводород в жидкостной фазе. 36. Способ по п.35, согласно которому дополнительно объединяют второй фильтрат и третий фильтрат; нагнетают второй фильтрат и третий фильтрат в дистилляционный сепаратор, тем самым получая поток кубовой жидкости, состоящий главным образом из диоксида углерода в жидкостной фазе, и извлеченный поток, содержащий по меньшей мере один из группы, состоящей из этана, пропана, бутана или сероводорода.
МПК / Метки
МПК: F25J 3/00
Метки: потока, газов, углеводородов, газообразных, кислотных, криогенная, система, удаления
Код ссылки
<a href="https://eas.patents.su/28-24440-kriogennaya-sistema-dlya-udaleniya-kislotnyh-gazov-iz-potoka-gazoobraznyh-uglevodorodov.html" rel="bookmark" title="База патентов Евразийского Союза">Криогенная система для удаления кислотных газов из потока газообразных углеводородов</a>
Предыдущий патент: Способ получения бензола из метана
Следующий патент: Слитый белок bche-альбумин для лечения злоупотребления кокаином