Способ очистки газа
Номер патента: 24546
Опубликовано: 30.09.2016
Авторы: Кескинен Кари И, Петтерссон Марианне, Айттамаа Юхани, Коскинен Юкка
Формула / Реферат
1. Способ очистки газа, полученного посредством газификации сырьевого материала в форме биомассы с получением газа, содержащего основной компонент, выбранный из монооксида углерода, диоксида углерода, водорода, углеводородов и их смесей, и второстепенный компонент, выбранный из группы, состоящей из сернистого водорода, хлористого водорода, аммиака, карбонилсульфида, цианистого водорода и их смесей, который включает следующие стадии:
контакт газа с кислым водным промывочным раствором, содержащим ионы переходных металлов, способных связывать сульфид-ионы,
связывание значительной доли загрязнений в форме сернистого водорода, содержащихся в газе, с получением практически нерастворимых сульфидных соединений переходных металлов для удаления загрязнений в форме сернистого водорода из газа и
отделение полученного таким образом очищенного газа от водного раствора;
причем H2S удаляют из газа посредством промывки, осуществляемой в виде многостадийного процесса, при этом во время первой стадии поступающий на первую стадию газ контактирует с промывочной жидкостью, которая содержит меньше стехиометрического количества ионов металла относительно содержания сульфидных соединений, а во время второй стадии процесса обработанный газ контактирует с промывочной жидкостью, которая содержит избыток ионов металла относительно содержания сульфидных соединений в газе.
2. Способ по п.1, отличающийся тем, что полученный сульфид металла выпадает в осадок в водном растворе и необязательно отделяется.
3. Способ по п.1 или 2, отличающийся тем, что ионы металла, содержащиеся в промывочном растворе, представляют собой ионы переходного металла, выбранного из группы, состоящей из меди, цинка, железа, кобальта и их смесей, в частности из меди, цинка, железа и их смесей, предпочтительно ионы металла в промывочном растворе являются двухвалентными ионами металлов меди, цинка, железа и их смесей, причем предпочтительно водный промывочный раствор имеет pH в диапазоне от 1 до 6,5, в частности от 1,5 до 5,5.
4. Способ по любому из пп.1-3, отличающийся тем, что водный раствор получают посредством растворения от 1 до 10000 мас.ч., предпочтительно от 50 до 5000 мас.ч. соли металла в 1000000 мас.ч. воды.
5. Способ по любому из пп.1-4, отличающийся тем, что концентрация ионов переходного металла (или металлов) лежит в диапазоне от 0,00001 до 0,1 М, например от 0,00001 до 0,01 М, обычно от 0,00005 до 0,005 М, предпочтительно от 0,0001 до 0,001 М.
6. Способ по любому из пп.1-5, отличающийся тем, что молярное отношение иона металла к сульфидным соединениям, содержащимся в газе, подлежащем очистке, превышает 1, предпочтительно лежит в диапазоне от 1,4 до 6, в частности от 1,5 до 5,5, особо предпочтительно от 2 до 4,5.
7. Способ по любому из предыдущих пунктов, отличающийся тем, что для обеспечения контакта газа с промывочным раствором проводят распыление капелек промывочного раствора в газ, поддержание их в газовой фазе и осаждение абсорбированного серосодержащего соединения в форме твердого сульфида металла в капельках промывочного раствора, причем предпочтительно промывочный раствор вступает в контакт с газом в распылительной камере, имеющей, по существу, вертикальную центральную ось, газ подают в распылительную камеру так, что он движется вдоль центральной оси распылительной камеры, а промывочный раствор подают через распылительные сопла, расположенные в виде одной или нескольких распылительных зон вдоль центральной оси на различных высотах в распылительной камере.
8. Способ по п.7, отличающийся тем, что газ подают в распылительную камеру через газораспределители, расположенные ниже самой нижней распылительной зоны, а сульфид металла удаляют из реактора совместно с отработанной промывочной жидкостью через выпускное отверстие, расположенное в нижней части камеры.
9. Способ по любому из пп.1-8, отличающийся тем, что промывочный раствор содержит в качестве металла менее 1500 мас.ч. на миллион, предпочтительно менее 1000 мас.ч. на миллион, в частности от 10 до 450 мас.ч. на миллион соли меди, сульфата меди.
10. Способ по любому из пп.1-9, отличающийся тем, что из газа удаляют значительную долю сернистого водорода, в частности не менее 95%, предпочтительно не менее 98%, особо предпочтительно не менее 99,5 мас.% сернистого водорода удаляют из газа.
11. Способ по любому из предыдущих пунктов, отличающийся тем, что концентрация сернистого водорода в очищенном газе составляет менее 100 об.ч. на миллиард, в частности менее 50 об.ч. на миллиард.
12. Способ по любому из предыдущих пунктов, отличающийся тем, что газ контактирует с промывочным раствором при температуре, лежащей в диапазоне от 10 до 80°C, и при давлении, лежащем в диапазоне от 1 до 50 бар, причем предпочтительно стадии контакта газа с промывочным раствором предшествует по меньшей мере одна стадия очистки газа.
13. Способ по любому из пп.1-12, отличающийся тем, что удаление H2S из газа посредством промывки, осуществляемой в виде многостадийного процесса, выполняют путем противоточной промывки.
14. Способ по любому из предыдущих пунктов, отличающийся тем, что очищенный газ используют для получения водорода, синтетического природного газа (CHГ), метанола, диметилового эфира или альдегидов, необязательно посредством гидроформилирования, или очищенный газ, необязательно после дополнительных стадий обработки, используют для получения углеводородной композиции, содержащей C4-C90 углеводороды, например, очищенный газ, необязательно после дополнительных стадий обработки, используют для получения углеводородной композиции в способе Фишера-Тропша.
15. Способ по п.14, включающий следующие стадии:
газификацию сырьевого материала в форме биомассы с получением газа, содержащего в качестве основных компонентов монооксид углерода, диоксид углерода, водород и углеводороды, возможно совместно с инертными компонентами, и в качестве второстепенных компонентов - загрязнения, выбранные из сернистого водорода, хлористого водорода, аммиака, цианистого водорода, карбонилсульфида и их смесей;
подачу газа, полученного посредством газификации сырьевого материала в форме биомассы, в риформер;
риформинг газа с целью снижения содержания углеводородов в газообразном эффлюенте риформера;
получение газообразного эффлюента из выпускного отверстия риформера;
необязательное регулирование молярного отношения водорода и монооксида углерода в очищенном газе;
удаление значительной доли загрязнений из газа посредством обеспечения контакта газа с промывочным раствором, представляющим собой низкоконцентрированный раствор ионов переходных металлов в воде;
извлечение очищенного газа;
необязательное регулирование молярного отношения водорода и монооксида углерода в очищенном газе и
подача полученного таким образом газа в реакционную зону реактора Фишера-Тропша, причем промывочный раствор содержит соль меди, например сульфат меди, концентрация которой в промывочном растворе составляет 1500 мас.ч. на миллион или менее, в частности от 100 до 1200 ч. на миллион в пересчете на медь.
16. Способ по п.15, отличающийся тем, что он включает получение углеводородной композиции, являющейся твердой или полутвердой при температуре окружающей среды, и дальнейшую обработку углеводородной композиции посредством гидрообработки, например гидроизомеризации, газообразным водородом при повышенной температуре в присутствии катализатора для получения углеводородной композиции, пригодной для использования в качестве углеводородов дизельного класса или в качестве композиции, из которой могут быть получены такие углеводороды.
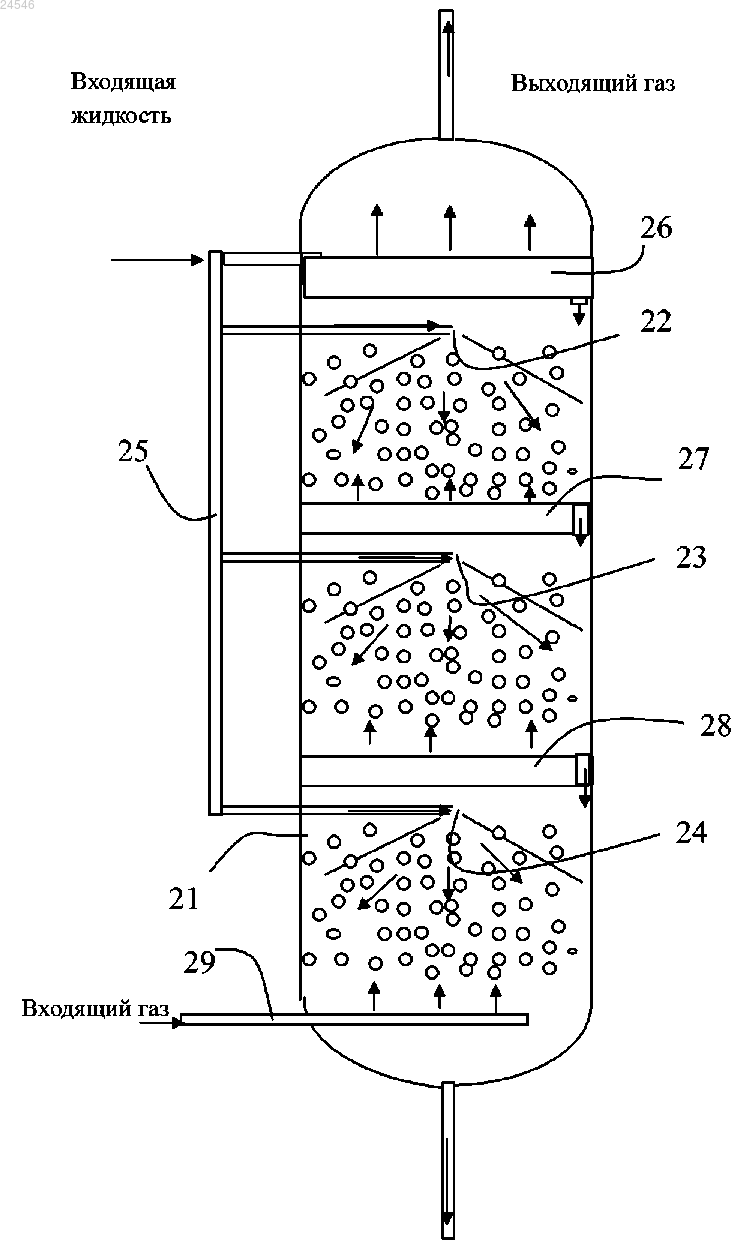
Текст
Способ очистки газа, полученного посредством газификации сырьевого материала в форме биомассы. Газ, который содержит монооксид углерода, диоксид углерода, водород, углеводороды и их смеси, можно очистить от загрязнений, таких как сернистый водород, хлористый водород,аммиак, карбонилсульфид, цианистый водород и их смеси, посредством обеспечения контакта газа с кислым водным промывочным раствором, содержащим ионы переходных металлов,способные связывать сульфид-ионы, для связывания значительной доли загрязнений в форме сернистого водорода, содержащихся в газе, с получением практически нерастворимых сульфидных соединений переходных металлов с целью удаления загрязнений в форме сернистого водорода из газа и отделения полученного таким способом очищенного газа от водного раствора. Очищенный газ можно использовать для получения углеводородных композиций, например, с использованием способа Фишера-Тропша. НЕСТЕ ОИЛ ОЙЙ (FI) Кескинен Кари И, Коскинен Юкка,Айттамаа Юхани, Петтерссон Марианне (FI) Новоселова С.В., Дощечкина В.В.,Липатова И.И., Рыбаков В.М., Хмара М.В. (RU) Область техники Настоящее изобретение относится к очистке газа. В частности, настоящее изобретение относится к способу удаления сернистого водорода и сходных серосодержащих соединений, необязательно - совместно с аммиаком и хлористым водородом, из газа, полученного посредством газификации биомассы. Предшествующий уровень техники В реакторе Фишера-Тропша (далее также сокращенно называемом ФТ-реактором) водород и монооксид углерода реагируют в присутствии катализатора на основе переходного металла, такого как кобальт или железо, с образованием композиции, содержащей широкий спектр линейных алканов, вплоть до восков. После соответствующей обработки этого продукта получают жидкую углеводородную композицию, которую можно использовать в качестве топлива для двигателей внутреннего сгорания, в частности дизельных двигателей. Многие углеродсодержащие источники использовали в качестве сырьевых материалов для получения газа, содержащего водород и монооксид углерода (также известного под названием "сингаз"), который может быть подан в способ Фишера-Тропша. Первоначально в качестве основного сырьевого материала использовали уголь, однако позже в коммерческих способах начали использовать и природный газ. Еще позже были разработаны способы, в которых биологические материалы, такие как растительные масла, растительные воски и другие растительные продукты и части растений или даже масла и воски животного происхождения, газифицировали и обрабатывали для получения подходящего исходного материала. В другом альтернативном подходе, а именно в способе переработки биомассы в жидкость (BTL,от англ. "biomass to liquid"), в качестве сырьевого материала используют биомассу, содержащую целые растения. BTL-способ обеспечивает утилизацию отходов лесного хозяйства. Обычно BTL-способ включает стадии предварительной обработки исходной биомассы, газификации биомассы, охлаждения и фильтрации сырого сингаза, очистки сырого газа, реакции конверсии для регулирования отношения H2/C, ФТ-способ и очистку продукта ФТ-способа. Для газификации биомассы можно использовать газообразный кислород (например, посредством вдувания его в газификационную зону) с целью минимизации содержания инертных веществ в сингазе. Для получения топлива в ФТ-способе предпочтительно использовать пар, или кислород, или их комбинации, вдуваемые в газификационную зону. Характерный диапазон температур от примерно 500C до примерно 900C. В этих условиях биомасса, например лигноцеллюлозные материалы, будет выделять газ, содержащий монооксид углерода, диоксид углерода, водород и водяной пар. Кроме того, газ будет содержать углеводороды и загрязнения, такие как соединения серы и следовые количества металлов. Их следует удалить. Поэтому способ также включает стадии очистки сингаза и защиты (например, для защиты катализаторов на последующих стадиях способа). На практике газ, полученный посредством газификации биомассы, который часто подвергают дополнительному риформингу, охлаждают перед реакцией Фишера-Тропша, и из газа, который необязательно подвергают риформингу, удаляют загрязнения, такие как COS, HCN, СО 2, следы соединений щелочных металлов и карбонильных соединений металлов (Ni, Fe), HCl, NH3, смолистые соединения и серосодержащие соединения. В качестве примера характерного состава: исходный газ, направляемый в способы удаления H2S, в характерном случае содержит от 100 до 400 частей на миллион H2S, от 20 до 40 об.% СО 2, от 0,5 до 6 об.% CH4, от 20 до 40 об.% H2S и от 10 до 30 об.% CO. Давление исходного газа предпочтительно лежит в диапазоне от 4 до 30 бар(а), в зависимости от рабочего давления газификатора. Температура исходного газа лежит в диапазоне от примерно 30C до примерно 100C. Для удаления загрязнений используют по меньшей мере одну стадию обработки, обычно - несколько раздельных стадий обработки. Для удаления соединений серы и диоксида углерода обычно используют промывку метанолом. Такие способы промывки коммерчески используют для эффективного удаления СО 2 при низком содержании серы. Стандартную промывку метанолом производят при температурах около -40C, и это требует значительной энергии. Смолистые соединения, такие как нафталин и бензол,обычно удаляют посредством дополнительной физической промывки, а карбонилы металлов - с использованием термической обработки или защитных слоев. Сущность изобретения Задача настоящего изобретения состоит в том, чтобы устранить по меньшей мере часть проблем,связанных с известной технологией. В частности, задача настоящего изобретения состоит в том, чтобы обеспечить способ эффективного удаления сернистого водорода и других загрязнений, таких как NH3, COS, HCN и соединения легких щелочных металлов, из синтез-газа. Настоящее изобретение основано на идее абсорбции загрязнений, например соединений серы (в частности, сульфидов, таких как H2S), содержащихся в синтез-газе, водным раствором, содержащим ионы металлов, и осаждения абсорбированных соединений серы с ионами металлов в форме твердых сульфи-1 024546 дов металлов. Из предшествующего уровня техники известно, что газ, содержащий большие объемы сернистого водорода, можно освободить от сернистого водорода, вначале пропустив поток газа через водный раствор, содержащий ионы меди в воде, для абсорбции сернистого водорода, а затем окислив полученный таким образом сульфид меди воздухом или газообразным кислородом с получением элементарной серы. В этом известном способе, описанном в публикации DE 2304497, водная абсорбционная среда содержит довольно высокие концентрации ионов меди (28,9 г Cu в 1400 мл воды), а абсорбцию сернистого водорода осуществляют посредством пропускания пузырьков газа через водную среду. Из предшествующего уровня техники (EP 0986432) известно, что серу и/или серосодержащие соединения-загрязнители можно удалить из потока газа, который также содержит СО 2, способом, который включает стадии: обеспечения контакта потока газа с предварительно выбранными ионами металла в форме водного раствора соли при pH, лежащем в диапазоне от примерно -0,05 до примерно 7,0, причем ионы металла и загрязнители реагируют друг с другом с образованием твердой соли металла и загрязнителя, которая осаждается из потока газа. Ион металла предпочтительно выбирают так, что соответствующий сульфид металла по существу нерастворим, причем металл выбран из группы, состоящей из Zn,Fe, Cu, Ag, Pb, Cd, Co, Mg, Mn, Ni и Sn. Приведены примеры использования в качестве промывочных жидкостей 1 М раствора ZnSO4 и 1 М раствора CuSO4. В контексте настоящего изобретения было обнаружено, что ионы металлов, например Cu2+ ионы,быстро реагируют с H2S в жидкости даже при очень низких концентрациях ионов металлов. Обычно концентрация соединения, содержащего ионы металла, в промывочном растворе зависит от растворимости соответствующего сульфида металла в данном растворе. Концентрация иона металла в случае меди может быть ниже примерно 1000 мас. частей на миллион или ниже примерно 100 мас. частей на миллион, в пересчете на массу абсорбционной жидкости. Это обеспечивает концепцию очень эффективного и выгодного интегрированного способа для удаления H2S и других загрязнений, указанных выше, из сингаза. Абсорбционная жидкость может быть приведена в контакт с газом, подлежащим очистке, например в колонне, такой как тарельчатая колонна или наполненная колонна, но могут быть использованы и другие устройства, обеспечивающие контакт. Абсорбционная жидкость может быть подана посредством распыления или атомизации, хотя не исключено и пропускание через нее пузырьков газа. При абсорбции серосодержащих соединений с образованием сульфидов металлов абсорбируются и кислые соединения,такие как хлористый водород. Кроме того, водный раствор, содержащий ионы металлов, может быть использован в кислой форме. В этой форме он будет способен абсорбировать аммиак (NH3) и хлористый водород (HCl), а также другие щелочные и кислые загрязнения. Более конкретно, настоящее изобретение характеризуется тем, что заявлено в отличительной части п.1 формулы изобретения. Изобретение обеспечивает существенные преимущества. Так, в новом способе согласно настоящему изобретению объединены раздельные фазы очистки. Можно включить даже стадию охлаждения газа. Загрязнения, такие как H2S, COS, NH3, HCl, некоторые органические соединения и мелкие частицы абсорбируются водным раствором. Описанный способ абсорбции для данного специфического применения также обеспечивает следующие преимущества: удаление загрязнений, описанных выше, и, в частности, почти полное удалениеH2S облегчает проведение последующего способа промывки метанолом в связи со снижением затрат на энергоресурсы благодаря удалению H2S из метанола и затрат на защитный слой для удаления H2S перед реактором Фишера-Тропша. В водном растворе сульфата меди сернистый водород осаждается в форме сульфида меди согласно формуле 1: В целом, абсорбция H2S из синтез-газа водным раствором MeSO4 (где Me обозначает металл, в частности переходный металл, такой как медь, железо, цинк или кобальт) является способом, ограниченным массопереносом. H2S должен раствориться в жидкой фазе, где быстро происходит реакция междуH2S и MeSO4. Ионы Me2+ и H2S должны присутствовать в пленке жидкости, в которой происходит реакция, и массоперенос H2S и Me2+ в пленку жидкости ограничивает реакцию. В реакции ионов Me2+ с H2S образуется MeS, который эффективно выпадает в виде мелких кристаллов из-за плохой растворимости сульфида в воде. Кристаллы формируются в соответствии с механизмами нуклеации и роста кристаллов. Скорость нуклеации и роста кристаллов зависит от перенасыщения пленки ионами Me2+ и S2-. Массоперенос может также зависеть от скорости нуклеации, которая влияет на концентрации Me2+ и S2-. Также растворяются и реагируют другие компоненты синтез-газа, такие как СО 2, NH3.pH ионной системы должен лежать в специфическом диапазоне в зависимости от используемого иона металла. Например, в случае меди, т.е. Cu2+, pH должен лежать в диапазоне от примерно 1 до примерно 5,2 для предотвращения осаждения других компонентов, отличающихся от CuS, таких как CuCO3,-2 024546Cu(OH)2 и (NH2)SO4, в зависимости от концентрации CuSO4 в водном растворе, состава синтез-газа и общего давления и температуры. Дополнительно H2S осаждается из жидкости в виде сульфидов с ионами металлов. Поскольку растворимость сульфидов металлов очень мала, можно использовать низкие концентрации ионов металлов,при этом все еще обеспечивается эффективное осаждение. Осаждение сульфидов является удобным и более выгодным способом удаления H2S, чем традиционная промывка метанолом, поскольку оно обеспечивает дополнительную движущую силу для массопереноса H2S из газа в жидкую фазу. Это обусловлено тем, что концентрации H2S, HS- и S2- в жидкой фазе поддерживаются низкими благодаря осаждению S2- в форме сульфида металла. При использовании кислого промывочного раствора из газа также можно отмыть аммиак. Способ согласно настоящему изобретению можно использовать в установке для получения углеводородных композиций, пригодных для использования в непереработанном виде в качестве дизельного топлива или для переработки в дизельное топливо. В особо предпочтительном варианте осуществления настоящего изобретения промывку производят в форме многостадийного процесса, например посредством противоточной промывки. В таком варианте осуществления настоящего изобретения можно получить водный эффлюент, который практически полностью освобожден от ионов металлов, происходящих из промывочной жидкости, и который можно направить для дальнейшей обработки в традиционную установку для очистки сточных вод. Далее настоящее изобретение будет исследовано более подробно с помощью подробного описания и со ссылками на прилагаемый рисунок промывной колонны для удаления загрязнений, таких как H2S,NH3 и COS, из синтез-газа для синтеза Фишера-Тропша. Краткое описание графических материалов Фиг. с 1 по 3 относятся к примеру 1. Фиг. 1 иллюстрирует эксперимент, включающий контакт газа с абсорбционным раствором, в данном случае - водным раствором CuSO4, связывающим H2S. На рисунке показан график зависимости отношения молярного потока H2S на выходе из промывочного резервуара к молярному потоку H2S на входе в промывочный резервуар от времени [ч:мин]; эксперимент был начат в 9:33, и последняя точка была измерена в 15:11. Фиг. 2 иллюстрирует эксперимент, сходный с описанным выше в связи с фиг. 1, включающий контакт газа с абсорбционным раствором, в данном случае -водным раствором CuSO4, связывающим H2S. На рисунке показан график зависимости отношения молярного потока H2S на выходе из промывочного резервуара к молярному потоку H2S на входе в промывочный резервуар от времени [ч:мин]; эксперимент был начат в 9:53. Фиг. 3 иллюстрирует эксперимент, сходный с описанным выше в связи с фиг. 1, включающий контакт газа с абсорбционным раствором, в данном случае водным раствором CuSO4, связывающим H2S. На рисунке показан график зависимости отношения молярного потока H2S на выходе из промывочного резервуара к молярному потоку H2S на входе в промывочный резервуар от времени [ч:мин]; эксперимент был начат в 10:43. Фиг. 4 демонстрирует различные концентрации газа из примера 2 и концентрацию S в отходящем газе как функцию стехиометрического отношения Cu/S в подаваемом газе. Фиг. 5 является блок-схемой варианта осуществления способа согласно настоящему изобретению. Фиг. 6 изображает вид сбоку конструкции распылительной камеры согласно настоящему изобретению, более подробно обсуждаемой в примере 3. Сведения, подтверждающие возможность осуществления изобретения Для порядка следует указать, что предпочтительные варианты осуществления настоящего изобретения обсуждаются со ссылкой на сульфат меди в качестве абсорбирующего соединения, являющегося солью металла. Хотя сульфат меди очень эффективен и предпочтителен во многих вариантах осуществления настоящего изобретения, в некоторых вариантах осуществления настоящего изобретения могут также быть использованы другие соли, указанные ниже. Следует отметить, что в тех случаях, когда указаны численные значения и численные диапазоны,примерные значения следует интерпретировать как включающие точные значения. Как указано выше, настоящее изобретение относится к очистке газа, полученного посредством газификации сырьевого материала, представляющего собой биомассу. В частности, настоящее изобретение обеспечивает способ очистки газификационного газа (сингаза) посредством абсорбции загрязнений, содержащихся в сингазе, жидкой абсорбционной средой, содержащей ионы металлов, способные связывать сульфид-ионы с образованием твердых сульфидов, обладающих низкой растворимостью и поэтому способных выпадать в осадок из раствора. В предпочтительном варианте осуществления настоящее изобретение осуществляют посредством обеспечения контакта газа с кислым водным промывочным раствором, содержащим ионы переходных металлов, способных связываться с сульфид-ионами, образующимися из сульфидных соединений, содержащихся в газе. Концентрация катионов переходных металлов может быть низкой, например, водный раствор может иметь концентрацию ионов переходных металлов, лежащую в диапазоне от примерно 0,00001 М до примерно 0,1 М, например от примерно 0,00001 М до примерно 0,01 М, в частности от 0,00001 до 0,1 М. Значительная доля сульфидных загрязнений, присутствующих и содержащихся в газе,может быть преобразована в форму сульфидных соединений переходных металлов. Сульфидные соединения, полученные таким образом, предпочтительно выпадают в осадок в промывочном растворе, за счет чего сульфидные загрязнения удаляются из газа. Очищенный газ, полученный таким способом, отделяют от водного раствора. Значительная доля загрязнений в форме сернистого водорода, содержащихся в газе, предпочтительно связывается с образованием практически нерастворимых (т.е. очень малорастворимых) сульфидных соединений переходных металлов. В предпочтительном варианте осуществления настоящего изобретения ионы металлов, т.е. катионы, содержащиеся в промывочном растворе, являются производными переходных металлов, выбранных из группы, состоящей из меди, цинка, железа, кобальта и их смесей, в частности из меди, цинка, железа и их смесей. Ионы металлов, содержащиеся в промывочном растворе, предпочтительно являются двухвалентными катионами металлов меди, цинка, железа и их смесями. Ионы переходных металлов получают из водорастворимых солей металлов посредством растворения этих солей в воде. В одном из вариантов осуществления настоящего изобретения водный раствор получают посредством растворения от примерно 1 до 10000 частей, предпочтительно от примерно 50 до 5000 массовых частей соли металла в 1000000 массовых частей воды. Концентрация ионов металлов в водном промывочном растворе обычно лежит в диапазоне от примерно 0,00005 до примерно 0,005 М, предпочтительно от примерно 0,0001 до примерно 0,001 М. Для приготовления подходящих промывочных растворов водорастворимые соли металлов, содержащие вышеуказанные катионы, могут содержать анион, выбранный из группы анионов, происходящих от неорганических кислот, таких как сульфат, сульфит, фосфат, фосфит, нитрат, хлорид, карбонат и их смеси. Также возможно использование анионов, происходящих от простых органических кислот (обычно содержащих не более 10 атомов углерода, например 6 и меньше атомов углерода). Примерами таких анионов являются цитрат, малонат, ацетат и их смеси. На основании вышесказанного, специфическими неограничивающими примерами анионов являются следующие: сульфат, сульфит, бисульфит, тиосульфат, хлорид, йодид, фосфат, одноосновный фосфат,двухосновный фосфат, гипофосфит, дигидропирофосфат, карбонат, бикарбонат, метасиликат, цитрат,малат, малеат, малонат, сукцинат, лактат, формиат, ацетат, бутират, пропионат, бензоат, тартрат, аскорбат и глюконат. С учетом вышесказанного, в особо предпочтительном варианте осуществления настоящего изобретения комбинации катионов металлов и анионов выбирают так, чтобы полученная соль была растворимой в воде. Соль также может быть гидратированной солью. Такие соли обычно являются кристаллогидратами солей с одной или несколькими связанными молекулами кристаллизационной воды. Раствор CuSO4 может быть приготовлен либо посредством растворения порошкообразного CuSO4 в воде, либо посредством проведения реакции порошкообразного CuO с раствором H2SO4 в воде. В первом случае образующуюся H2SO4 необходимо удалять из циркулирующей промывочной жидкости. Во втором случае образующаяся H2SO4 будет реагировать с CuO с образованием желаемых Cu2+ и SO42- ионов. Кроме того, порошок металлической Cu с водным раствором H2SO4 дает водный раствор CuSO4 и водород. В предпочтительном варианте осуществления настоящего изобретения водный промывочный раствор является кислым или слабокислым; предпочтительно он имеет pH в диапазоне примерно от 1 до 6,5,в частности примерно от 1 до 5. pH будет варьироваться в указанном диапазоне в зависимости от выбранных катионов металлов. Газ обычно контактирует с промывочным раствором при температуре от 10 до 80C и при давлении от 1 до 50 бар (абсолютное давление). Соответственно, промывку можно проводить при температуре и давлении окружающей среды (от 20 до 25C и 1 бар(а, хотя также можно использовать данную технологию при более низких температурах (от 10 до менее чем 20C) и при повышенных температурах (от более чем 25 до 80C). Давление может превышать 1 бар(а), например, оно может лежать в диапазоне от примерно 1,5 до 50 бар(а). Обычно сингаз, полученный посредством газификации, выделяют при более высокой температуре,чем указано выше. Поэтому в одном из вариантов осуществления настоящего изобретения газификационный газ охлаждают до температуры, лежащей в вышеуказанном диапазоне (от 10 до 80C), перед тем как привести его в контакт с промывочной жидкостью. Существует возможность извлечь некоторое количество тепла, содержащегося в газификационном газе, посредством контакта его с охлаждающей средой, например с охлаждающей водой, в теплообменнике. Молярное отношение катионов металлов к сульфидным соединениям, содержащимся в газе, подлежащем очистке (то есть, отношение Me2+/S2- в исходном газе), в характерном случае больше 1, предпочтительно лежит в диапазоне от примерно 1,4 до примерно 6, в частности лежит в диапазоне от примерно 1,5 до примерно 5,5, особо предпочтительно в диапазоне от примерно 2 до примерно 4,5. Существует несколько способов обеспечения контакта сингаза с промывочной жидкостью/абсорбционной средой, как будет видно из вариантов осуществления настоящего изобретения, описанных ниже. В первом предпочтительном варианте осуществления настоящего изобретения контакт сингаза с абсорбционной средой происходит при распылении или атомизации абсорбционной среды в газ. Предпочтительно, контакт сингаза с абсорбционной средой происходит на поверхности раздела между газом и капельками абсорбционной среды. Во втором предпочтительном варианте осуществления настоящего изобретения газ, подлежащий очистке, в виде пузырьков подают в резервуар с мешалкой, содержащий абсорбционный раствор. Этот вариант осуществления альтернативной концепции способа более подробно описан в примере 3. В третьем варианте осуществления настоящего изобретения можно использовать абсорбционные башни с тарелками и/или набивкой, работающие в противоточном режиме. Конкретный тип оборудования зависит от концентрации ионов металлов в растворе, количества газа и содержания в нем загрязнений. Одним из способов осуществления способа химической абсорбции является использование химической распылительной абсорбции в сочетании с ситовыми тарелками над секциями распылительной камеры, как описано и показано в примере 3 и на фиг. 6. Соответственно, в конкретном варианте осуществления настоящего изобретения, основанном на подходе с использованием распылительной камеры, промывочный раствор контактирует с газом в распылительной камере, имеющей по существу вертикальную центральную ось; газ подают в распылительную камеру снизу или сверху и получают с противоположного конца, то есть он перемещается в направлении центральной оси распылительной камеры. Промывочный раствор подают через распылительные сопла, образующие по меньшей мере две распылительные зоны, расположенные последовательно вдоль центральной оси на различных высотах в распылительной камере. В предпочтительном варианте осуществления настоящего изобретения имеется от 1 до 10 распылительных зон, например от 2 до 5 распылительных зон, в устройстве, обеспечивающем контакт. Газ подают в распылительную камеру, например в камеру вышеописанного типа, через газораспределители, расположенные ниже самой нижней распылительной зоны, а сульфид металла удаляют из абсорбера совместно с использованной промывочной жидкостью через выпускное отверстие, расположенное в нижней части камеры. После абсорбции сульфид металла отделяют и направляют для дальнейшей переработки. Следует отметить специфический пример, в котором сульфат меди используют в качестве водорастворимой соли для приготовления промывочного раствора: почти все ионы Cu2+ из промывочного блока, в котором используют CuSO4, осаждаются в виде кристаллов CuS и удаляются посредством фильтрации из промывочной жидкости, вытекающей из блока. После абсорбции сульфидов кристаллы CuS и суспензию CuS в воде отделяют от циркулирующей промывочной жидкости, их можно подать в нижнюю промывочную секцию с дополнительной водой. Часть синтез-газа подают в нижнюю промывочную колонну, где почти все ионы Cu, содержащиеся в оттекающей промывочной жидкости, осаждаются. В описанных выше вариантах осуществления промывочный раствор содержит менее 1500 мас. частей на миллион металла, например менее 500 мас. частей на миллион металла, предпочтительно от примерно 10 до примерно 450 мас. частей на миллион, например от 15 до 400 мас. частей на миллион соли меди, в частности сульфата меди. Блок для промывки с использованием ионов переходных металлов может также состоять из двух секций для водной промывки в присутствии Me2+ (пронумерованных в направлении движения потока газа), причем в первой секции используют разбавленную водную промывочную жидкость, содержащую ионы Me2+, а во второй секции используют другую водную промывочную жидкость с довольно высокой концентрацией ионов Me2+. Необходимое количество ионов Me2+ подают в форме водного раствора Me2+ во вторую промывочную секцию и обеспечивают циркуляцию раствора. Синтез-газ из первой промывочной секции подают во вторую промывочную секцию, где почти весь H2S, содержащийся в синтезгазе, удаляется посредством противоточной промывки. Этот способ проиллюстрирован на фиг. 5. Первая и вторая секции могут быть расположены вдоль вертикальной оси зоны или устройства для обеспечения контакта друг над другом. В одном из вариантов осуществления настоящего изобретения вторую секцию (или секции) размещают над первой секцией (или секциями). Необходимое количество ионов Cu2+ в форме водного раствора CuSO4 подают во вторую промывочную секцию и обеспечивают циркуляцию раствора (поток 4). Синтез-газ из первой промывочной секции подают во вторую промывочную секцию, где почти весь H2S, содержащийся в синтез-газе, удаляют посредством противоточной промывки, что также показано на фиг. 5. Таким образом, в описанном выше многостадийном способе во время первой стадии входящий газ вступает в контакт с промывочной жидкостью, которая является "бедной" в том смысле, что она содер-5 024546 жит меньше стехиометрического количества иона металла относительно количества сульфидных соединений. На последней стадии способа обрабатываемый газ вступает в контакт с промывочной жидкостью,которая содержит избыток ионов металла относительно содержания сульфидных соединений в газе. Может иметься от 2 до 30 стадий промывки, однако обычно их количество лежит в диапазоне от 2 до 10, в частности от 2 до 5. В этих вариантах осуществления настоящего изобретения промывочные растворы содержат в качестве металла, как указано выше, обычно менее 1500 мас. частей на миллион, например менее 500 мас. частей на миллион, предпочтительно от примерно 10 до примерно 450 мас. частей на миллион, соли меди, в частности сульфата меди; фактическую концентрацию определяют на основании концентрации сульфида в газе, подлежащем обработке, на различных стадиях. Как указано выше, в способе любого рода после первой стадии промывки газа можно получить водный эффлюент, из которого практически полностью удалены ионы металла, происходящие из промывочной жидкости, и который можно направить для дальнейшей обработки в стандартную установку для очистки сточных вод. Результаты очистки с использованием ионов переходных металлов в водных промывочных жидкостях являются очень хорошими. Способом согласно настоящему изобретению можно удалить значительную долю сернистого водорода из газа. По меньшей мере 95 об.%, предпочтительно по меньшей мере 98 об.%, особо предпочтительно по меньшей мере 99,5 об.% сернистого водорода удаляется из газа. В результате, в предпочтительном варианте осуществления настоящего изобретения концентрация сернистого водорода в очищенном газе составляет менее чем примерно 100 объемных частей на миллиард, в частности менее чем примерно 50 объемных частей на миллиард. Очищенный газ находит несколько применений. Его можно использовать для получения водорода,метанола, этанола, диметилового эфира или альдегидов, необязательно - посредством гидроформилирования, или непосредственно использовать в двигателях, например - для получения электроэнергии. Кроме того, его можно использовать для получения синтетического природного газа (СПГ). Очищенный газ можно также использовать для получения углеводородной композиции, содержащей C4-C90 углеводороды, необязательно после дополнительной очистки. В частности, углеводородную композицию можно получить в способе Фишера-Тропша (ФТ). Стадию очистки газа можно интегрировать в способ Фишера-Тропша; такой способ содержит стадии начальной газификации сырьевого материала, например, посредством газификации продувкой кислорода, с получением газа, содержащего в качестве основных компонентов монооксид углерода, диоксид углерода, водород и углеводороды, возможно совместно с инертными компонентами, и в качестве второстепенных компонентов - загрязнения, выбранные из сернистого водорода, хлористого водорода,аммиака, цианистого водорода, карбонилсульфида и их смесей; последующей подачи газа, полученного посредством газификации сырьевого материала, в риформер; риформинга газа с целью снижения содержания углеводородов в газообразном эффлюенте риформера и одновременного преобразования смолистых компонентов в СО, СО 2 и воду; получения газообразного эффлюента из выпускного отверстия риформера; необязательного регулирования соотношения водорода и монооксида углерода в очищенном газе; удаления значительной доли загрязнений из газа посредством обеспечения контакта газа с промывочным раствором, представляющим собой кислый низкоконцентрированный раствор ионов переходных металлов в воде; извлечения очищенного газа; необязательного регулирования соотношения водорода и монооксида углерода в очищенном газе и подачи полученного таким образом газа в реакционную зону реактора Фишера-Тропша для получения углеводородной композиции в присутствии катализатора. Предпочтительно соль меди растворяют в водном растворе для получения промывочной жидкости для вышеописанной прикладной задачи. Концентрация соли меди, например сульфата меди, в промывочном растворе предпочтительно составляет 1500 мас. частей на миллион или меньше, в частности от 100 до 1200 мас. частей на миллион, в одном из вариантов осуществления настоящего изобретения меньше 1000 мас. частей на миллион, в частности от примерно 10 до примерно 450 мас. частей на миллион. Во всех этих применениях газ, полученный посредством газификации биомассы продувкой кислорода, обычно содержит монооксид углерода, диоксид углерода, водород и углеводороды, возможно совместно с инертными компонентами. Органический сырьевой материал или исходный материал для способа предпочтительно является материалом, состоящим из биологического вещества, то есть вещества животного или растительного происхождения. В контексте настоящего изобретения термин "биомасса" использован для обозначения любого такого сырьевого материала. Типичной характеристикой исходных материалов для способа согласно настоящему изобретению является то, что они содержат углерод, в частности, в количестве, превышающем примерно 20%, пред-6 024546 почтительно в количестве, превышающем примерно 30%, более предпочтительно в количестве, превышающем примерно 40%, в пересчете на сухое вещество. Исходная биомасса предпочтительно выбрана из однолетних или многолетних растений и их частей или остатков, таких как древесина, древесная щепа и частицы древесины (опилки и т.п.), отходы лесных хозяйств и лесоматериалы, полученные при рубках ухода, сельскохозяйственные отходы, такие как солома, оливковый жмых, энергетические культуры, такие как ива, энергетическое сено, мискантус (Miscanthous) и торф. Однако можно использовать и различные отходы, такие как топливо, полученное из твердых бытовых отходов (RDF), отходы лесопильных заводов, фанерных и мебельных производств и другие механические древесные отходы, а также жидкие отходы (включая промышленные и муниципальные отходы). Кроме вышеупомянутых материалов растительного происхождения, можно использовать различные животные продукты, такие как жиры и воски. Кроме того, пиролизное масло, полученное из биомассы, и отработанные щелоки из целлюлозной промышленности также являются подходящим исходным биологическим материалом для газификации. Биомассу обычно газифицируют в реакторе с продувкой кислородом, в реакторе с псевдоожиженным слоем или в реакторе с циркулирующим псевдоожиженным слоем (CFB) при температуре в диапазоне от примерно 500C до примерно 900C. Циркулирующий псевдоожиженный слой формируют из гранулированного или зернистого материала псевдоожиженного слоя, такого как алюмосиликат (например, песок) или сходный неорганический материал. Биомассу перед газификацией предпочтительно размалывают или измельчают до частиц или гранул со средним размером менее примерно 5 мм, предпочтительно менее примерно 2 мм, в частности не более 1 мм. В реактор обычно подают биомассу с содержанием влаги менее 15 мас.%, предпочтительно до 10 мас.% и менее. Газификацию можно ускорить посредством подачи пара, воздуха или кислорода в реактор, особенно хорошие результаты получают при подаче кислорода или кислорода совместно с паром. В зависимости от вида биомассы, температуры и концентрации кислорода "конверсия углерода", то есть конверсия элементарного углерода, содержащегося в сырьевом материале, в легкие соединения, углеводороды и смолу, превышает 70%, предпочтительно превышает 75%, в частности превышает 80% от массы углерода в сырьевом материале. Посредством газификации получают газ, содержащий в качестве основных компонентов монооксид углерода, водород и диоксид углерода совместно с некоторым количеством воды или пара. Газ выделяют. Его можно использовать в способе Фишера-Тропша для получения углеводородов посредством реакции монооксида углерода с водородом в присутствии катализатора с целью конверсии по меньшей мере значительной части монооксида углерода и водорода, содержащихся в газе, в углеводородную композицию, содержащую C4-C90 углеводороды. Полученную таким образом углеводородную композицию выделяют и подвергают дальнейшей обработке. В случае восков и сходных углеводородов, которые являются твердыми или полутвердыми при температуре окружающей среды, а также в случае высокомолекулярных углеводородов, углеводородную композицию, полученную способом Фишера-Тропша, предпочтительно перерабатывают дальше посредством гидрообработки, например, посредством гидроизомеризации, с использованием газообразного водорода при повышенной температуре в присутствии катализатора для получения углеводородной композиции, пригодной для использования в качестве углеводородного топлива дизельного класса, или в качестве композиции, из которой могут быть получены такие углеводороды. Обычно гидрообработку (например, гидроизомеризацию) газообразным водородом проводят при температуре, примерно равной 300C, в реакторе с неподвижным слоем. Катализатором обычно является металлический катализатор на носителе или без носителя, например никель на углеродном носителе. В стандартном газификационном реакторе получают газообразный продукт с молярным отношением водорода к монооксиду углерода в диапазоне от 0,5 до 1,5. В частности, газификация таких сырьевых материалов, как древесина, однолетние растения или торф, в присутствии газообразного кислорода дает газообразный продукт, в котором молярное отношение водорода к монооксиду углерода лежит в диапазоне примерно от 0,8 до 1,1. На практике, молярное отношение водорода к монооксиду углерода перед реакцией Фишера-Тропша необходимо увеличить примерно до 2. По этой причине необходима отдельная стадия, во время которой это отношение увеличивают, и эту стадию осуществляют не позднее, чем непосредственно перед реакцией Фишера-Тропша, или даже одновременно с реакцией Фишера-Тропша. Стадии контакта газа с промывочным раствором предшествует по меньшей мере одна стадия очистки газа. Такой вариант осуществления настоящего изобретения может быть объединен с любым из вариантов осуществления настоящего изобретения, описанных выше. По меньшей мере одна из предшествующих стадий очистки предпочтительно выбрана из группы,состоящей из фильтрации, мембранной фильтрации, абсорбции с перепадом давления и промывки жидкостью, способной, например, абсорбировать диоксид углерода. Описание примеров осуществления изобретения Пример 1. Полунепрерывные испытания по удалению H2S посредством абсорбции с использованием водного раствора сульфата меди (CuSO4) в качестве модельного абсорбента. Материалы и методы Испытания с абсорбцией были проведены с использованием микрореакторного оборудования для реакции конверсии водяным паром (WGS). Полунепрерывные испытания по удалению H2S посредством абсорбции с использованием в качестве абсорбента водного раствора сульфата меди (CuSO4) были проведены в простой газопромывной склянке объемом 0,5 л с магнитной мешалкой, помещенной в технологическую линию микрореактора перед постоянно включенным масс-спектрометром. Испытания с абсорбцией были проведены при комнатной температуре и атмосферном давлении. Общая объемная скорость газа, подаваемого в WGS-реактор, была равна 12 дм 3/ч. Основной состав исходного газа приведен в таблице. Загрязняющие компоненты были закуплены в компании AGA в виде газовых смесей, разбавленных водородом - H2S/H2, COS/H2 и NH3/H2. В подаваемом газе концентрация H2S была равна 500 об. частям на миллион во всех экспериментах. В некоторых испытаниях в подаваемом газе также было использовано 85 частей на миллион COS и 800 частей на миллион NH3. Однако практически весь карбонилсульфид был гидролизован еще до абсорбционной склянки, поскольку невозможно было обойти каталитический реактор, где происходил гидролиз COS в качестве побочной реакции в реакции конверсии водяным паром. Полученный газ анализировали в режиме реального времени с использованием масс-спектрометра(ГХ-МС, но газохроматографическое разделение не использовали). Предел количественного определения зависит от компонента, и в данных масс-спектрометрических измерения предел количественного определения составлял примерно 1 часть на миллион. В экспериментах с абсорбцией, проведенных в лаборатории, в газопромывной пузырьковой склянке, описанной выше, была выполнена следующая программа испытаний: Концентрация CuSO4 в различных экспериментах варьировалась от разбавленного раствора с концентрацией, равной 50 частям на миллион, до 500 частей на миллион. Массоперенос в пузырьковой газопромывной склянке активировали посредством перемешивания. Скорость абсорбции H2S в водном растворе CuSO4 измеряли при различных концентрациях CuSO4. Производили идентификацию/количественное определение кристаллизованных твердых компонентов, содержащих медь, и распределение по размеру кристаллизованных частиц. Результаты Скорости подачи различных загрязняющих компонентов в синтез-газ, поступающий в WGSреактор, в экспериментах были следующими: Испытание 1 - концентрация CuSO4 - 0,01 мас.%, концентрация H2S в исходном газе - 500 об. частей на миллион,Испытание 2 - концентрация CuSO4 - 0,01 мас.%, концентрация H2S в исходном газе - 500 об. частей на миллион, NH3 - 800 об. частей на миллион, карбонилсульфид (COS) - 85 об. частей на миллион,Испытание 3 - концентрация CuSO4 - 0,0051 мас.%, концентрация H2S в исходном газе - 500 об. частей на миллион, NH3 - 800 об. частей на миллион, карбонилсульфид (COS) - 85 об. частей на миллион,Отношение молярного потока H2S на выходе из газопромывной склянки к молярному потоку H2S на входе в газопромывную склянку в различных экспериментах показано в виде функции времени на фиг. 1-3. ВыводыCuSO4 был способен полностью удалять 500 частей на миллион H2S (молярная фракция) из исходного газа в водных растворах с концентрациями 0,01 и 0,005 мас.%. Продуктом является твердый осадокCuS. Слишком высокий pH приводил к осаждению, например, гидроксидов металлов или карбонатов,при этом не происходило удаления сернистого водорода, или он удалялся в меньшем количестве. Образование карбоната также зависело от парциального давления СО 2. Слишком низкий pH приводил к отсутствию образования осадка, в этом случае не происходило удаления сернистого водорода (результаты не приведены). NH3 в исходном газе не влиял на удаление H2S сульфатом меди. Что касается результатов, приведенных на рисунках, то следует отметить, что экспериментальная установка была следующей: склянку с водным промывочным раствором сульфата меди помещали между двумя холодильниками продукта реактора и волюметрическим газовым расходомером барабанного типа. При открытии клапанов газ можно было направить к волюметрическому газовому расходомеру барабанного типа через водный раствор CuSO4, а затем к газовому хроматографу-масс-спектрометру, после чего газ направляли к волюметрическому газовому расходомеру барабанного типа для отведения. Первая точка на графике соответствует моменту времени непосредственно перед подачей газа в склянку с раствором CuSO4. В этот момент времени осаждение Cu еще не обнаруживается. Затем была взята серия из 4 образцов в течение 7 мин, после короткого перерыва была взята новая серия из 4 образцов в течение 7 мин, и т.д. Точки на графиках, в которых концентрация H2S равна 0, соответствуют точкам полного удаленияH2S из газа. Вскоре после того как вся медь была израсходована, концентрация H2S снова начала возрастать. В некоторых испытаниях в исходном газе содержался карбонилсульфид. При пропускании через конверсионный реактор он практически полностью гидролизовался, так как исходный газ также содержал воду Поэтому в газе, подававшемся на промывку с использованием CuSO4, содержание H2S было больше, чем в газе, подававшемся в систему. Этот эффект можно было видеть по результатам анализов, так как количество COS в эффлюенте составляло 0-3 об. части на миллион. Пример 2. Испытание по удалению H2S из сингаза посредством абсорбции в абсорбционной колонне с наполнителем. Испытания по удалению H2S из сингаза посредством абсорбции в абсорбционной колонне с наполнителем были проведены на полупромышленной испытательной установке. Эффективность абсорбера была испытана на установке для получения сингаза в Варкаусе, Финляндия. Технические характеристики абсорбера и справочные данные приведены ниже: Абсорбер абсорбер с наполнителем, наполнитель - металл, размер частиц металла - 2 дюйма или 50 мм, площадь поверхности - 100 м 2/м 3,высота: 9 м, диаметр: 0,1 м. Исходный газ Скорость подачи: 50-60 кг/ч,Давление: 30 бар, температура: 25C,Состав (в мол. %): СО 21, СО 2 30, Н 2 31, CH4 3, N2 15, H2S 140 частей/млн, нафталин 100 частей/млн, бензол 1200 частей/млн, следовые количества NH3 и COS. Подаваемый абсорбентCuSO4-вода, концентрация 0,15 мас.%,Скорость подачи варьировалась, эквивалентное молярное отношение Cu2+ к H2S составляло 1,5-6. Молярный % H2S в выходящем газе измеряли с помощью постоянно включенного газоанализатора сернистого водорода. Минимальная измеренная мольная доля H2S в выходящем сингазе составляла 70 частей на миллиард при эквивалентном молярном отношении Cu2+ к H2S в выходящем газе, равном 6. В результате была определена корреляция между концентрацией S в полученном газе и стехиометрическим отношением Cu/S в исходном газе. При стехиометрических отношениях в диапазоне от 1 до 5 наблюдали практически линейную зависимость, тогда как стехиометрическое отношение Cu/S, равное 1,5, приводило к менее чем 3 об. частям на миллион H2S, а отношение, равное 5, приводило к 90 об. частям на миллиард H2S в полученном газе. Пример 3. Газопромывочная абсорбционная колонна для удаления H2S. Газопромывочная абсорбционная колонна может быть сконструирована так, как показано на прилагаемой фиг. 6. Далее способ будет описан со ссылкой на вариант осуществления, изображенный на рисунке, хотя следует отметить, что конкретные детали не следует считать ограничивающими использование газопромывочной абсорбционной колонны в контексте настоящего изобретения. Газопромывочная абсорбционная колонна 21 состоит из блока 25 сетчатого каплеуловителя, за которым следует секция распылительной абсорбции и входное газораспределительное устройство 29 в нижней части распылительной камеры. Колонна может содержать сетчатые тарелки 26, 27 и 28, как показано на рисунке, и распылительные секции 22, 23 и 24, расположенные последовательно, для повышения эффективности промывки и абсорбции. Очень разбавленный водный раствор CuSO4 с концентрацией менее 500 мас. частей на миллион подают в распылительную камеру 21 на сетчатую тарелку 26, расположенную в верхней части камеры, и распыляют в распылительную камеру под сетчатой тарелкой с помощью специфической системы 22 распылительных сопел, где происходит эффективный массоперенос между распыленными капельками жидкости и газом. Серосодержащие компоненты быстро реагируют в жидкой фазе с Cu2+ при очень низких концентрациях ионов. Система распылительных сопел имеет специальную конструкцию, обеспечивающую гомогенную плотную фазу, состоящую из капелек раствора CuSO4 в воде и вступающую в эффективный контакт с входящим синтез-газом. Сопла обычно расположены последовательно на различных уровнях по высоте колонны. Синтезгаз, описанный выше, подают в реактор через газораспределители 29 из нижней части камеры. МолекулыH2S, содержащиеся в синтез-газе, эффективно контактируют с капельками распыленной жидкости, за счет чего обеспечиваются эффективный массоперенос H2S в жидкую фазу и быстрая реакция с ионамиCu2+, содержащимися в капельках, с образованием CuS и H2SO4 согласно уравнению реакции Большая часть капелек распыленной жидкости ударяется о стенку камеры и падает на ее дно. Часть мелких капелек распыленной жидкости захватывается газом и отделяется от газа на защитном поддоне, расположенном в верхней части распылительной камеры.CuS отделяют в виде кристаллического твердого вещества в блоке для выделения CuS. Сепарационный блок может быть осадительным резервуаром для CuS, гидроциклоном, центрифугой или фильтровальной установкой. Отходящий газ после абсорбции H2S содержит менее 50 об. частей на миллиард H2S, и поэтому нет необходимости в использовании дополнительных защитных слоев для дополнительного удаления H2S для синтеза Фишера-Тропша. Вместо ионов Cu можно использовать и другие металлы, образующие сульфиды с очень низкой растворимостью. Можно использовать отработанные катализаторы из способа Фишера-Тропша (Fe, Co). Преимущества использования газопромывочной абсорбционной колонны: В целом, использование газопромывочной абсорбционной колонны, в том числе использование конкретной газопромывочной абсорбционной колонны, изображенной на рисунке, обеспечивает несколько преимуществ. Так, очень низкие концентрации ионов Cu2+ быстро реагируют с H2S в жидкой фазе. Это обеспечивает очень эффективный и выгодный способ удаления H2S и других загрязнений, указанных выше, из сингаза до концентраций менее 20 об. частей на миллиард. H2S вступает в химическую реакцию с CuSO4 с образованием твердого CuS и серной кислоты. CuS легко можно отделить в виде твердого вещества для использования в качестве сырьевого материала в медной промышленности. Полученный CuS можно использовать для получения металлической меди или других соединений меди. Способ удаления H2S согласно настоящему изобретению является очень эффективным, и для синтеза Фишера-Тропша не нужны дополнительные защитные слои для удаления H2S. Распылительный блок обеспечивает эффективный массоперенос H2S в капельки и относительно малые размеры реактора. Большая часть эффективного массопереноса происходит непосредственно после распыления. ФОРМУЛА ИЗОБРЕТЕНИЯ 1. Способ очистки газа, полученного посредством газификации сырьевого материала в форме биомассы с получением газа, содержащего основной компонент, выбранный из монооксида углерода, диоксида углерода, водорода, углеводородов и их смесей, и второстепенный компонент, выбранный из группы, состоящей из сернистого водорода, хлористого водорода, аммиака, карбонилсульфида, цианистого водорода и их смесей, который включает следующие стадии: контакт газа с кислым водным промывочным раствором, содержащим ионы переходных металлов,способных связывать сульфид-ионы,связывание значительной доли загрязнений в форме сернистого водорода, содержащихся в газе, с получением практически нерастворимых сульфидных соединений переходных металлов для удаления загрязнений в форме сернистого водорода из газа и отделение полученного таким образом очищенного газа от водного раствора; причем H2S удаляют из газа посредством промывки, осуществляемой в виде многостадийного процесса, при этом во время первой стадии поступающий на первую стадию газ контактирует с промывочной жидкостью, которая содержит меньше стехиометрического количества ионов металла относительно содержания сульфидных соединений, а во время второй стадии процесса обработанный газ контактирует с промывочной жидкостью, которая содержит избыток ионов металла относительно содержания сульфидных соединений в газе. 2. Способ по п.1, отличающийся тем, что полученный сульфид металла выпадает в осадок в водном растворе и необязательно отделяется. 3. Способ по п.1 или 2, отличающийся тем, что ионы металла, содержащиеся в промывочном растворе, представляют собой ионы переходного металла, выбранного из группы, состоящей из меди, цинка,железа, кобальта и их смесей, в частности из меди, цинка, железа и их смесей, предпочтительно ионы металла в промывочном растворе являются двухвалентными ионами металлов меди, цинка, железа и их смесей, причем предпочтительно водный промывочный раствор имеет pH в диапазоне от 1 до 6,5, в частности от 1,5 до 5,5. 4. Способ по любому из пп.1-3, отличающийся тем, что водный раствор получают посредством растворения от 1 до 10000 мас.ч., предпочтительно от 50 до 5000 мас.ч. соли металла в 1000000 мас.ч. воды. 5. Способ по любому из пп.1-4, отличающийся тем, что концентрация ионов переходного металла(или металлов) лежит в диапазоне от 0,00001 до 0,1 М, например от 0,00001 до 0,01 М, обычно от 0,00005 до 0,005 М, предпочтительно от 0,0001 до 0,001 М. 6. Способ по любому из пп.1-5, отличающийся тем, что молярное отношение иона металла к сульфидным соединениям, содержащимся в газе, подлежащем очистке, превышает 1, предпочтительно лежит в диапазоне от 1,4 до 6, в частности от 1,5 до 5,5, особо предпочтительно от 2 до 4,5. 7. Способ по любому из предыдущих пунктов, отличающийся тем, что для обеспечения контакта газа с промывочным раствором проводят распыление капелек промывочного раствора в газ, поддержание их в газовой фазе и осаждение абсорбированного серосодержащего соединения в форме твердого сульфида металла в капельках промывочного раствора, причем предпочтительно промывочный раствор вступает в контакт с газом в распылительной камере, имеющей, по существу, вертикальную центральную ось, газ подают в распылительную камеру так, что он движется вдоль центральной оси распылительной камеры, а промывочный раствор подают через распылительные сопла, расположенные в виде одной или нескольких распылительных зон вдоль центральной оси на различных высотах в распылительной камере. 8. Способ по п.7, отличающийся тем, что газ подают в распылительную камеру через газораспределители, расположенные ниже самой нижней распылительной зоны, а сульфид металла удаляют из реактора совместно с отработанной промывочной жидкостью через выпускное отверстие, расположенное в нижней части камеры. 9. Способ по любому из пп.1-8, отличающийся тем, что промывочный раствор содержит в качестве металла менее 1500 мас.ч. на миллион, предпочтительно менее 1000 мас.ч. на миллион, в частности от 10 до 450 мас.ч. на миллион соли меди, сульфата меди. 10. Способ по любому из пп.1-9, отличающийся тем, что из газа удаляют значительную долю сернистого водорода, в частности не менее 95%, предпочтительно не менее 98%, особо предпочтительно не менее 99,5 мас.% сернистого водорода удаляют из газа. 11. Способ по любому из предыдущих пунктов, отличающийся тем, что концентрация сернистого водорода в очищенном газе составляет менее 100 об.ч. на миллиард, в частности менее 50 об.ч. на миллиард. 12. Способ по любому из предыдущих пунктов, отличающийся тем, что газ контактирует с промывочным раствором при температуре, лежащей в диапазоне от 10 до 80C, и при давлении, лежащем в диапазоне от 1 до 50 бар, причем предпочтительно стадии контакта газа с промывочным раствором предшествует по меньшей мере одна стадия очистки газа. 13. Способ по любому из пп.1-12, отличающийся тем, что удаление H2S из газа посредством промывки, осуществляемой в виде многостадийного процесса, выполняют путем противоточной промывки. 14. Способ по любому из предыдущих пунктов, отличающийся тем, что очищенный газ используют для получения водорода, синтетического природного газа (СПГ), метанола, диметилового эфира или альдегидов, необязательно посредством гидроформилирования, или очищенный газ, необязательно после дополнительных стадий обработки, используют для получения углеводородной композиции, содержащей C4-C90 углеводороды, например, очищенный газ, необязательно после дополнительных стадий обработки, используют для получения углеводородной композиции в способе Фишера-Тропша. 15. Способ по п.14, включающий следующие стадии: газификацию сырьевого материала в форме биомассы с получением газа, содержащего в качестве основных компонентов монооксид углерода, диоксид углерода, водород и углеводороды, возможно совместно с инертными компонентами, и в качестве второстепенных компонентов - загрязнения, выбранные из сернистого водорода, хлористого водорода, аммиака, цианистого водорода, карбонилсульфида и их смесей; подачу газа, полученного посредством газификации сырьевого материала в форме биомассы, в риформер; риформинг газа с целью снижения содержания углеводородов в газообразном эффлюенте риформера; получение газообразного эффлюента из выпускного отверстия риформера; необязательное регулирование молярного отношения водорода и монооксида углерода в очищенном газе; удаление значительной доли загрязнений из газа посредством обеспечения контакта газа с промывочным раствором, представляющим собой низкоконцентрированный раствор ионов переходных металлов в воде; извлечение очищенного газа; необязательное регулирование молярного отношения водорода и монооксида углерода в очищенном газе и подача полученного таким образом газа в реакционную зону реактора Фишера-Тропша, причем промывочный раствор содержит соль меди, например сульфат меди, концентрация которой в промывочном растворе составляет 1500 мас.ч. на миллион или менее, в частности от 100 до 1200 ч. на миллион в пересчете на медь. 16. Способ по п.15, отличающийся тем, что он включает получение углеводородной композиции,являющейся твердой или полутвердой при температуре окружающей среды, и дальнейшую обработку углеводородной композиции посредством гидрообработки, например гидроизомеризации, газообразным водородом при повышенной температуре в присутствии катализатора для получения углеводородной композиции, пригодной для использования в качестве углеводородов дизельного класса или в качестве композиции, из которой могут быть получены такие углеводороды.
МПК / Метки
МПК: C10G 2/00, B01D 53/52, B01D 53/14, C01B 17/05
Код ссылки
<a href="https://eas.patents.su/14-24546-sposob-ochistki-gaza.html" rel="bookmark" title="База патентов Евразийского Союза">Способ очистки газа</a>
Предыдущий патент: Композиция против срыгивания и/или желудочно-пищеводного рефлюкса, ее получение и применение
Следующий патент: Многофункциональный катетер
Случайный патент: Барабан машины для бережного ухода за бельем