Стали для кислых сред
Номер патента: 18884
Опубликовано: 29.11.2013
Авторы: Туркони Густаво Лопес, Фукуи Росихико, Гарсия Альфонсо Искьердо
Формула / Реферат
1. Сталь, содержащая углерод (С) от 0,2 до 0,3 вес.%; марганец (Mn) от 0,1 до 1 вес.%; кремний (Si) от 0 до 0,5 вес.%; хром (Cr) от 0,4 до 1,5 вес.%; молибден (Mo) от 0,1 до 1 вес.%; ниобий (Nb) от 0 до 0,1 вес.%; алюминий (Al) от 0 до 0,1 вес.%; кальций (Ca) от 0 до 0,01 вес.%; бор (В) менее 100 ч./млн; титан (Ti) от 0 до 0,05 вес.%; вольфрам (W) от 0,1 до 1,5 вес.%; ванадий (V) менее 0,05 вес.%; медь (Cu) от 0 до не более чем 0,15 вес.%; кислород (О) менее 200 ч./млн; азот (N) менее 0,01 вес.%; сера (S) менее 0,003 вес.% и фосфор (Р) менее 0,015 вес.%; где количественное содержание элементов дано в вес.%, исходя из общего веса композиции стали.
2. Сталь по п.1, в которой значение выражения Mo/10 + Cr/12 + W/25 + Nb/3 + 25*В составляет от 0,05 до 0,39 вес.%.
3. Сталь по любому из пп.1 или 2, которая характеризуется пределом текучести от 120 до 140 тыс. фунтов/кв.дюйм.
4. Сталь по любому из пп.1-3, которая характеризуется стойкостью к коррозионному растрескиванию под напряжением в сульфидсодержащей среде, составляющей около 720 ч, согласно испытанию по методике A NACE TM0177, при напряжении около 85% SMYS (минимальный предел прочности материала) для полноразмерных образцов.
5. Сталь по любому из пп.1-4, содержащая углерод (С) от 0,2 до 0,3 вес.%; марганец (Mn) от 0,2 до 0,5 вес.%; кремний (Si) от 0,15 до 0,4 вес.%; хром (Cr) от 0,4 до 1 вес.%; молибден (Mo) от 0,3 до 0,8 вес.%; ниобий (Nb) от 0,02 до 0,06 вес.%; алюминий (Al) от 0,02 до 0,07 вес.%; кальций (Ca) от 0 до 0,01 вес.%; бор (В) от 10 до 30 ч./млн; титан (Ti) от 0,1 до 0,03 вес.%; вольфрам (W) от 0,2 до 0,6 вес.%; ванадий (V) менее 0,05 вес.%; медь (Cu) от 0 до не более чем 0,08 вес.%; кислород (О) менее 200 ч./млн; азот (N) менее 0,01 вес.%; сера (S) менее 0,002 вес.% и фосфор (Р) менее 0,010 вес.%.
6. Сталь по любому из пп.1-5, предназначенная для изготовления труб.
7. Сталь, содержащая углерод (С), молибден (Mo), хром (Cr), вольфрам (W), ниобий (Nb), бор (В) и ванадий в количестве менее 0,05 вес.%, в которой количественное содержание элементов, приведенное в вес.% от общего веса состава стали, таково, что значение выражения Mo/10 + Cr/12 + W/25 + Nb/3 + 25*В составляет от 0,05 до 0,39 вес.%.
8. Сталь по п.7, в которой значение выражения Mo/10 + Cr/12 + W/25 + Nb/3 + 25*В составляет от 0,10 до 0,26 вес.%.
9. Сталь по любому из пп.7 и 8, которая характеризуется линейной зависимостью между стойкостью к коррозионному растрескиванию под напряжением в сульфидсодержащей среде (KISSC) в режиме I и пределом текучести.
10. Сталь по любому из пп.7-9, которая характеризуется средним размером пакетов dpacket, составляющим менее 3 мкм.
11. Сталь по любому из пп.7-10, которая содержит выделившуюся фазу с диаметром частиц, dp, составляющим более 70 нм, и средний коэффициент формы ≥0,62, где коэффициент формы вычисляется по формуле 4Ap/Р2, где А - это площадь проекции частицы, а Р - периметр проекции частицы.
12. Сталь по любому из пп.7-11, микроструктура которой содержит более 95 об.% мартенсита и менее 5 об.% бейнита, исходя из общего объема композиции стали.
13. Сталь по п.7, содержащая углерод (С) от 0,2 до 0,3 вес.%; хром (Cr) от 0,4 до 1,5 вес.%; молибден (Mo) от 0,1 до 1 вес.%; ниобий (Nb) от 0 до 0,1 вес.%; бор (В) менее 100 ч./млн; вольфрам (W) от 0,1 до 1,5 вес.%; исходя из общего веса композиции стали.
14. Сталь по п.13, содержащая марганец (Mn) от 0,1 до 1 вес.%; кремний (Si) от 0 до 0,5 вес.%; алюминий (Al) от 0 до 0,1 вес.%; кальций (Ca) от 0 до 0,01 вес.%; титан (Ti) от 0 до 0,05 вес.%; ванадий (V) менее 0,05 вес.%; медь (Cu) от 0 до не более чем 0,15 вес.%; кислород (О) менее 200 ч./млн; азот (N) менее 0,01 вес.%; сера (S) менее 0,003 вес.% и фосфор (Р) менее 0,015 вес.%.
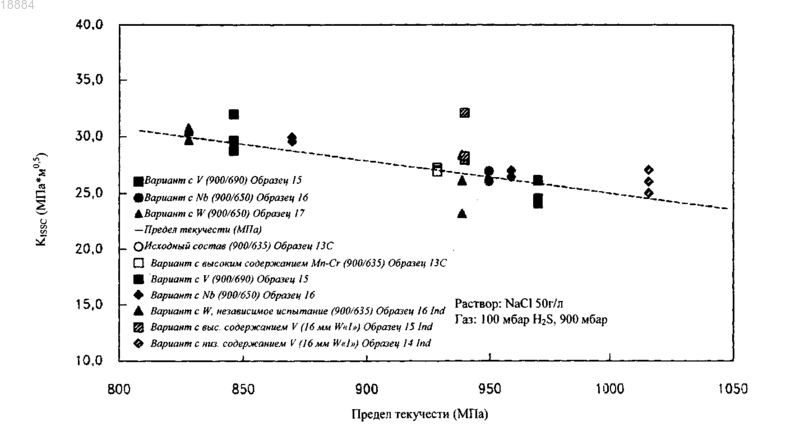
Текст
СТАЛИ ДЛЯ КИСЛЫХ СРЕД Настоящее изобретение относится к составам стали, обеспечивающим улучшенные свойства в коррозионной среде. Варианты воплощения изобретения также относятся к поверхностной защите стали путем уменьшения проникновения водорода. Кроме того, обеспечивается хороший контроль процесса в отношении рабочего времени термической обработки и устойчивости к поверхностному окислению при температуре прокатки. Туркони Густаво Лопес (AR), Фукуи Росихико (JP), Гарсия Альфонсо Искьердо (MX) Дощечкина В.В., Липатова И.И.,Рыбаков В.М., Новоселова С.В.,Хмара М.В. (RU)(71)(73) Заявитель и патентовладелец: ТЕНАРИС КОННЕКШНС ЛИМИТЕД (VC) Область техники, к которой относится изобретение Положения описанного изобретения относятся к составам стали, обеспечивающим высокую прочность в коррозионной среде. Варианты воплощения изобретения также относятся к поверхностной защите стали путем уменьшения проникновения водорода. Кроме того, обеспечивается хороший контроль технологического процесса в отношении рабочего времени термической обработки и устойчивости к поверхностному окислению при температуре прокатки. Предшествующий уровень техники Проникновение водорода в металлы широко исследовалось в связи с проблемой накопления энергии, так же как и деградация переходных металлов, например расслоение, водородная хрупкость, растрескивание и коррозия. На концентрацию водорода в металлах, таких как сталь, может влиять скорость коррозии стали, степень защиты антикоррозионной пленки, образующейся на стали, а также коэффициент диффузии водорода в стали. Также на подвижность водорода в стали влияет микроструктура, включая тип и количество выделений, текстуру металла и плотность дислокаций. Таким образом, количество абсорбированного водорода зависит не только от взаимодействия микроструктуры с водородом, но также от образуемых антикоррозионных веществ. Абсорбция водорода может также быть улучшена в присутствии абсорбированных каталитических ядов, таких как сероводород (H2S). Несмотря на то, что этот феномен еще недостаточно изучен, он имеет огромное значение для высокопрочных низколегированных сталей (HSLA), используемых в нефтедобыче. Комбинация высокой прочности сталей и большого количества водорода в сероводородной среде может привести к катастрофическим последствиям для этих сталей. Таким образом, имеется потребность в сталях, обеспечивающих улучшенную коррозионную стойкость в агрессивных средах, таких как сероводородная среда. Сущность изобретения Варианты воплощения данного изобретения относятся к составам стали, обеспечивающим улучшенные свойства в коррозионной среде. Варианты воплощения изобретения также относятся к поверхностной защите стали путем уменьшения проникновения водорода. Кроме того, обеспечивается хороший контроль технологического процесса в отношении рабочего времени термической обработки и устойчивости к поверхностному окислению при температуре прокатки. В одном из вариантов воплощения данного изобретения описывается состав стали, содержащий углерод (С) от 0,2 до 0,3 вес.%; марганец (Mn) от 0,1 до 1 вес.%; кремний (Si) от 0 до 0,5 вес.%; хром (Cr) от 0,4 до 1,5 вес.%; молибден (Mo) от 0,1 до 1 вес.%; ниобий (Nb) от 0 до 0,1 вес.%; алюминий (Al) от 0 до 0,1 вес.%; кальций (Ca) от 0 до 0,01 вес.%; бор (В) менее 100 ч./млн; титан (Ti) от 0 до 0,05 вес.%; вольфрам (W) от 0,1 до 1,5 вес.%; ванадий (V) от 0 до не более 0,05 вес.%; медь (Cu) от 0 до не более 0,15 вес.%; кислород (О) менее 200 ч./млн; азот (N) менее 0,01 вес.%; сера (S) менее 0,003 вес.% и фосфор (Р) менее 0,015 вес.%; где количественное содержание элементов дано в вес.%, исходя из общего веса состава стали. Учитывается, что в другом варианте воплощения изобретения не все из перечисленных элементов должны присутствовать в составе стали, и предполагается использование других составов для применения в кислой среде. В одном из вариантов воплощения изобретения такая сталь может иметь следующий состав: углерод (С) от 0,2 до 0,3 вес.%; марганец (Mn) от 0,1 до 1 вес.%; хром (Cr) от 0,4 до 1,5 вес.%; кремний (Si) от 0,15 до 0,5 вес.%; молибден (Mo) от 0,1 до 1 вес.%; вольфрам (W) от 0,1 до 1,5 вес.%; ниобий (Nb) от 0 до 0,1 вес.%; бор (В) менее 100 ч./млн; где количественное содержание элементов дано в вес.%, исходя из общего веса композиции. В другом варианте воплощения изобретения состав стали включает углерод (С), молибден (Mo),хром (Cr), вольфрам (W), ниобий (Nb) и бор (В). Указано количественное содержание каждого элемента в вес.% от общего состава стали, исходя из чего состав стали соответствует формуле Mo/10 + Cr/12 +W/25 + Nb/3 + 25 В от 0,05 до 0,39 вес.%. В других вариантах воплощения изобретения представлен способ получения состава стали. Способ охватывает получение хотя бы одного из следующих элементов: углерод (С), молибден (Mo), хром (Cr),вольфрам (W), ниобий (Nb), бор (В) и их комбинаций. Также способ включает выбор количественного содержания каждого из полученных элементов, исходя из чего, состав стали соответствует формуле Мо/10 + Cr/12 + W/25 + Nb/3 + 25 В от 0,05 до 0,39 вес.%, где количественное содержание элементов дано в вес.%, исходя из общего веса состава стали. В другом варианте воплощения изобретения стойкость состава к коррозионному растрескиванию под напряжением в сульфидсодержащей среде составляет около 720 ч согласно испытанию в соответствии с NACE TM0177, по методу испытания А, при напряжении около 85% минимального предела прочности материала (SMYS) для полноразмерных образцов. В другом варианте воплощения изобретения состав стали демонстрирует главным образом линейное отношение между стойкостью к коррозионному растрескиванию под напряжением в сульфидсодержащей среде (KISSC) в режиме I и пределом текучести. Другие варианты воплощения изобретения предполагают изготовление труб из составов стали. Перечень чертежей На фиг. 1 отображены значения стойкости к коррозионному растрескиванию под напряжением в сульфидсодержащей среде (KISSC) в режиме I в зависимости от предела текучести для вариантов воплощения описанных составов сталей; на фиг. 2 - стандартизованные значения 50% FATT (температура, при которой поверхность разрушения образца по Шарпи демонстрирует 50% вязкой и 50% хрупкой зоны) в зависимости от размера пластин для вариантов воплощения описанных составов стали, иллюстрируя улучшение стандартизованной жесткости при уменьшении размера пластин; на фиг. 3 - стандартизованное значение KISSC в зависимости от размера пластин для вариантов воплощения описанных составов стали и на фиг. 4 - измерение предела текучести в зависимости от температуры отпуска для вариантов воплощения описанных составов. Сведения, подтверждающие возможность осуществления изобретения Варианты воплощения описанного изобретения предусматривают составы стали для применения в кислой среде. Свойства, представляющие интерес, включают, но не ограничиваются следующими: прокаливаемость, микроструктура, геометрия выделений, твердость, предел текучести, жесткость, коррозионная стойкость, стойкость к коррозионному растрескиванию под напряжением в сульфидсодержащей среде, образование защитных слоев от проникновения водорода, а также стойкость к окислению при высокой температуре. В конкретных вариантах воплощения изобретения также раскрывается главным образом линейное отношение между стойкостью к коррозионному растрескиванию под напряжением в сульфидсодержащей среде (KISSC) в режиме I и пределом текучести (YS) для вариантов воплощения композиции с выбором микроструктурных параметров. Эти микроструктурные параметры могут включать, но не ограничиваются следующими: уменьшение размера зерна, размер пластин мартенсита, а также форма и распределение выделений. В других вариантах воплощения изобретения также раскрывается, что существует определенная связь между следующими микроструктурными параметрами, которая приводит к этому соотношению: средний размер пакета, dpacket, менее 3 мкм; выделения, имеющие диаметр частиц dp, более 70 нм и коэффициент формы 0,62, как будет обсуждаться ниже; мартенситные микроструктуры в объемной фракции более 95 об.%, исходя из общего объема композиции стали, т.е. микроструктура стали содержит более 95 об.% мартенсита и менее 5 об.% байнита,исходя из общего объема композиции стали. Также было обнаружено, что варианты воплощения композиций стали, имеющей микроструктурные параметры в пределах выбранного диапазона, могут также обеспечивать дополнительные преимущества. Например, композиции стали могут демонстрировать улучшенную коррозионную стойкость в кислой среде, а также улучшенный контроль технологического процесса. В конкретных вариантах воплощения изобретения эти улучшения обеспечиваются путем добавления или ограничения выбранных элементов следующим образом: добавление вольфрама (W) уменьшает окисление стали при нагревании в атмосферах, обычно создающихся в пламенных печах, используемых для горячей прокатки; ограничение максимального содержания меди (Cu) предотвращает проникновение водорода в сталь путем образования защитного антикоррозионного слоя; кислород (О) предотвращает образование крупных вкраплений в стали, обеспечивая отдельные вкрапления частиц размером менее 50 мкм. Такое предотвращение образования вкраплений также препятствует образованию очагов парообразования для водородного растрескивания; низкое содержание ванадия (V) уменьшает крутизну кривой отпуска (предел текучести в сравнении с температурой отпуска), что улучшает возможность контроля технологического процесса. В конкретных вариантах воплощения изобретения также раскрываются составы стали, содержащие вольфрам, имеющие низкое содержание меди и низкое содержание ванадия, а также демонстрирующие микроструктуру, размер пластин и форму осадка, указанные выше. Эти составы перечислены ниже в табл. 1, исходя из вес.% всего состава, если не указано иное. Учитывается, что не каждый нижеуказанный элемент должен быть включен в состав стали, и поэтому рассматриваются варианты, включающие некоторые, но не все перечисленные элементы. Углерод (С). Углерод - это элемент, улучающий закаливаемость стали и способствующий повышению уровня прочности после закалки и отпуска. В одном из вариантов воплощения изобретения, если количественное содержание углерода меньше 0,15 вес.%, закаливаемость стали значительно снижается,и прочность стали не может повыситься до желаемого уровня. С другой стороны, если содержание углерода превышает 0,40%, возможно образование закалочных трещин и длительное разрушение, что осложняет производство бесшовных стальных труб. Поэтому в одном из вариантов воплощения изобретения диапазон содержания углерода составляет 0,200,30 вес.%. Марганец (Mn). Добавление марганца в состав стали способствует дезоксидации и десульфуризации. В одном из вариантов воплощения изобретения марганец может добавляться в количестве не менее 0,1 вес.% для достижения такого положительного эффекта. Более того, добавление марганца также улучшает закаливаемость и прочность. Однако высокие концентрации марганца способствуют выделению фосфора, серы и других загрязняющих элементов, которые ухудшают стойкость к коррозионному растрескиванию под напряжением в сульфидсодержащей среде. Таким образом, в одном из вариантов воплощения изобретения диапазон содержания марганца составляет от 0,20 до 0,50 вес.%. Хром (Cr). Добавление хрома в сталь повышает прочность и стойкость при закаливании, поскольку хром улучшает закаливаемость во время охлаждения и образует карбиды во время отпуска термообработкой. Для этого в одном из вариантов воплощения изобретения добавляется более 0,4 вес.% хрома. Однако в конкретных вариантах воплощения изобретения наличие хрома в концентрации выше 1,5 вес.% приводит к нейтрализации его действия и ухудшению стойкости к коррозионному растрескиванию под напряжением. Таким образом, в одном из вариантов воплощения изобретения хром представлен в концентрации от 0,40 до 1,5 вес.%. В предпочтительном варианте воплощения изобретения хром представлен в концентрации от 0,40 до 1,0 вес.%. Кремний (Si). Кремний - это элемент, содержащийся в стали и способствующий дезоксидации. Поскольку кремний повышает стойкость стали к размягчению при отпуске, добавление кремния также повышает стойкость стали к коррозионному растрескиванию под напряжением. Примечательно, что значительно более высокие концентрации кремния могут ухудшать прочность и стойкость стали к коррозионному растрескиванию под напряжением, а также способствовать образованию клейких отложений. В одном из вариантов воплощения изобретения кремний может добавляться в количестве от 0 до 0,5 вес.%. В другом варианте воплощения изобретения концентрация кремния может варьироваться от 0,15 до 0,40 вес.%. Молибден (Mo). Как и в случае с хромом, молибден повышает закаливаемость стали и значительно улучшает стойкость стали к размягчению при отпуске и стойкость к коррозионному растрескиванию под напряжением. Кроме того, молибден предотвращает выделение фосфора (Р) на межзеренных границах. В одном из вариантов воплощения изобретения содержание молибдена в количестве менее 0,2 вес.% не оказывает значительного эффекта. В других вариантах воплощения изобретения, если концентрация молибдена превышает 1,5 вес.%, усиливается влияние молибдена на закаливаемость и реакцию на отпуск, а также ухудшается стойкость к коррозионному растрескиванию под напряжением. В этих случаях избыточный молибден осаждается в виде мелких игольчатых частиц, на месте которых начинается образование трещин. Следовательно, в одном из вариантов воплощения изобретения содержание молибдена варьируется от 0,10 до 1,0 вес.%. В других вариантах воплощения изобретения содержание молибдена варьируется от 0,3 до 0,8 вес.%. Вольфрам (W). Добавление вольфрама повышает прочность стали, поскольку он оказывает положительный эффект на закаливаемость и способствует повышению стойкости стали к размягчению при отпуске. Эти положи-3 018884 тельные эффекты способствуют повышению стойкости стали к коррозионному растрескиванию под напряжением с указанным уровнем прочности. Кроме того, вольфрам способствует значительному повышению стойкости к окислению при высокой температуре. Более того, если снижение прочности стали в результате высокого отпуска предполагается компенсировать лишь добавлением молибдена, стойкость стали к коррозионному растрескиванию под напряжением в сульфидсодержащей среде может ухудшиться в результате осаждения крупных игольчатых карбидов молибдена. Вольфрам может оказывать схожий с молибденом эффект на стойкость стали к размягчению при отпуске, но имеет преимущество в том, что крупные карбиды вольфрама образуются сложнее вследствие более медленной скорости диффузии. Этот эффект возникает вследствие того, что атомная масса вольфрама почти в два раза больше атомной массы молибдена. При высоком содержании вольфрама его эффект становится более выраженным, а выделение приводит к ухудшению стойкости закаленных и отпущенных сталей к коррозионному растрескиванию под напряжением. Более того, эффект добавления вольфрама может быть незначительным при содержании вольфрама в количестве от 0,1 до 1,5 вес.%. В другом варианте воплощения изобретения содержание вольфрама варьируется от 0,2 до 0,6 вес.%. Бор (В). Добавление небольшого количества бора значительно повышает прокаливаемость стали. Кроме того, за счет добавления бора повышается стойкость толстостенных труб из отпущенной стали к коррозионному растрескиванию под напряжением. В одном из вариантов воплощения изобретения бор добавляется в количестве не более 100 ч./млн для улучшения закаливаемости и устранения неблагоприятного эффекта. В другом варианте воплощения изобретения бор присутствует в составе стали в количестве 1030 ч./млн. Алюминий (Al). Алюминий способствует дезоксидации, повышению жесткости и улучшению стойкости стали к коррозионному растрескиванию под напряжением в сульфидсодержащей среде. Алюминий реагирует с азотом (N) с образованием выделений фазы AIN, которая препятствует росту аустенитного зерна во время термической обработки, и способствует образованию мелкого аустенитного зерна. В конкретных вариантах воплощения изобретения эффекты дезоксидации и измельчения зерен могут быть незначительными при содержании алюминия в количестве менее 0,005 вес.%. Более того, при избыточном содержании алюминия может возрастать концентрация неметаллических вкраплений, что приводит к повышению частоты возникновения дефектов и снижению жесткости. В одном из вариантов воплощения изобретения содержание алюминия варьируется в диапазоне от 0 до 0,10 вес.%. В других вариантах воплощения изобретения содержание алюминия варьируется от 0,02 до 0,07 вес.%. Титан (Ti). Титан может добавляться в количестве, которого достаточно для формирования азота в виде нитрида титана TiN. К счастью, в сталях, содержащих бор, можно избежать образования нитрида бора BN. Это позволяет бору присутствовать в стали в виде растворенного вещества, что обеспечивает повышение закаливаемости стали. Титан, растворенный в стали, равно как и титан, присутствующий в избытке и образующий нитрид титана TiN, усиливает неспособность стали к рекристаллизации при высоких температурах деформации. В сталях, претерпевших закалку с цементационного нагрева, растворенный титан осаждается мелкими частицами во время отпуска и повышает стойкость стали к размягчению при отпуске. Поскольку сродство азота и титана в стали довольно высоко, если все содержащееся количество азота переходит в нитрид титана, содержание азота и титана должно соответствовать уравнению 1, где количество элементов дано в вес.%, исходя из общего веса состава сталиTi вес.%(48/14)N вес.% (уравнение 1). В одном из вариантов воплощения изобретения содержание титана варьируется от 0,005 до 0,05 вес.%. В других вариантах воплощения изобретения содержание титана варьируется от 0,01 до 0,03 вес.%. Примечательно, что в одном из вариантов воплощения изобретения превышение содержания титана в 0,05 вес.% ухудшает жесткость стали. Ниобий (Nb). Растворенный ниобий подобно растворенному титану осаждается в виде очень мелких частиц карбонитридов при отпуске (карбонитриды ниобия) и повышает стойкость стали к размягчению при отпуске. Это свойство позволяет производить отпуск стали при высоких температурах. Карбонитриды ниобия, которые растворяются в стали во время нагревания при высокой температуре перед пробиванием отверстий, практически не осаждаются во время прокатки. Однако карбонитриды ниобия осаждаются в виде мелких частиц во время охлаждения трубы при свободной конвекции. Поскольку число мелких частиц карбонитридов ниобия достаточно высокое, они препятствуют укрупнению зерна и предотвращают чрезмерный рост зерен во время аустенизации перед закалкой. Если содержание ниобия менее 0,1 вес.%, в значительной степени возникают различные эффекты,описанные выше, когда содержание ниобия превышает 0,1 вес.%, ухудшается пластичность в горячем состоянии и жесткость стали. Следовательно, в одном из вариантов воплощения изобретения содержание ниобия варьируется от 0 до 0,10 вес.%. В других вариантах воплощения изобретения содержание ниобия варьируется от 0,02 до 0,06 вес.%. Ванадий (V). Когда в стали присутствует ванадий, он осаждается в виде очень мелких частиц во время отпуска,что повышает стойкость к размягчению стали при отпуске. Благодаря этому ванадий можно добавлять для облегчения достижения высоких уровней прочности стали в бесшовных трубах даже при температурах отпуска выше 650C. Такие высокие уровни прочности необходимы для повышения стойкости стальных труб сверхвысокой прочности к коррозионному растрескиванию под напряжением в сульфидсодержащей среде. У сталей, содержащих ванадий в количестве выше 0,1 вес.%, отмечается очень крутая кривая отпуска, что позволяет ослабить контроль за процессом производства труб. Для увеличения рабочего времени/улучшения контроля за процессом производства стали содержание ванадия ограничивают до 0,05 вес.%. Азот (N). По мере сокращения содержания азота в стали повышается жесткость и стойкость к коррозионному растрескиванию под напряжением в сульфидсодержащей среде. В одном из вариантов воплощения изобретения содержание азота ограничивается не более чем 0,01 вес.%. Фосфор (Р) и сера (S). Концентрация фосфора и серы в стали поддерживается на низких уровнях, поскольку фосфор и сера вызывают коррозионное растрескивание под напряжением в сульфидсодержащей среде. Фосфор - это элемент, обычно присутствующий в стали, он ухудшает жесткость и стойкость стали к коррозионному растрескиванию под напряжением, поскольку выделяется на межзеренных границах. Таким образом, в одном из вариантов воплощения изобретения содержание фосфора ограничивается количеством не более 0,025 вес.%. В другом варианте воплощения изобретения содержание фосфора ограничивается количеством не более 0,015 вес.%. С целью повышения стойкости к коррозионному растрескиванию под напряжением, особенно в случаях со сталью, претерпевшей закалку с цементационного нагрева, содержание фосфора должно быть 0,010 вес.%. В одном из вариантов воплощения изобретения содержание серы ограничивается 0,005 вес.% или более низким уровнем во избежание образования вкраплений, ухудшающих жесткость стали и стойкость к коррозионному растрескиванию под напряжением в сульфидсодержащей среде. В частности, в одном из вариантов воплощения изобретения для повышения стойкости к коррозионному растрескиванию под напряжением в сульфидсодержащей среде закаленных и отпущенных сталей, произведенных путем закалки с цементационного нагрева, содержание серы ограничивается количеством не более 0,005 вес.%, а содержание фосфора ограничивается количеством не более 0,010 вес.%. Кальций (Ca). Кальций объединяется с серой с образованием сульфидов и закругляет форму вкраплений, что приводит к повышению стойкости сталей к коррозионному растрескиванию под напряжением в сульфидсодержащей среде. Однако при недостаточной дезоксидации стали стойкость к коррозионному растрескиванию под напряжением в сульфидсодержащей среде может ухудшаться. Если содержание кальция менее 0,001 вес.%, его эффект будет незначительным. С другой стороны, избыточное содержание кальция может привести к повреждениям поверхности изделий, произведенных из стали, а также снижению жесткости и коррозионной стойкости стали. В одном из вариантов воплощения изобретения при добавлении кальция к стали его содержание варьируется от 0,001 до 0,01 вес.%. В других вариантах воплощения изобретения содержание кальция составляет менее 0,005 вес.%. Кислород (О). Кислород обычно присутствует в стали в виде загрязняющей примеси и может ухудшить жесткость и стойкость отпущенных сталей к коррозионному растрескиванию под напряжением в сульфидсодержащей среде. В одном из вариантов воплощения изобретения содержание кислорода составляет менее 200 ч./млн. Медь (Cu). Уменьшение количественного содержания меди в стали препятствует проникновению водорода в сталь за счет образования клейкого антикоррозионного слоя. В одном из вариантов воплощения изобретения содержание меди составляет менее 0,15 вес.%. В других вариантах воплощения изобретения содержание меди составляет менее 0,08 вес.%. Примеры Базовая формула. Эмпирическая формула выведена для разработки вариантов воплощения композиции стали для применения в кислой среде. Составы сталей могут быть определены из уравнения 2 с целью оценки конкретного преимущества для одного или нескольких вышеописанных свойств. Более того, составы сталей могут быть определены из уравнения 2 с пределом текучести в диапазоне около 120-140 тыс. фунтов/кв.дюйм (приблизительно 827-965 МПа) МинМо/10 + Cr/12 + W/25 + Nb/3 + 25 ВМакс (уравнение 2) где количественное содержание элементов дано в вес.%, исходя из общего веса композиции. Для определения состава, который получен в соответствии с уравнением 2, количественное содержание различных элементов композиции вводится в уравнение 2 в вес.% и производится вычисление по уравнению 2. Композиции, по которым результат уравнения 2 входит в максимальный или минимальный диапазон, соответствуют уравнению 2. В одном из вариантов воплощения изобретения минимальные и максимальные значения уравнения 2 варьируются от 0,05 до 0,39 вес.% соответственно. В другом варианте воплощения изобретения минимальные и максимальные значения уравнения 2 варьируются от 0,10 до 0,26 вес.% соответственно. Образцы композиций стали в соответствии с уравнением 2 были приготовлены с использованием лабораторных и промышленных весов для изучения влияния различных элементов и характеристик каждого химического состава стали в умеренно кислой среде с целью достичь предела текучести от 120 до 140 тыс. фунтов/кв.дюйм. Как будет обсуждаться в примерах ниже, правильный выбор химического состава и условий термической обработки позволяет достичь высокой прочности сталей и высокой стойкости к коррозионному растрескиванию под напряжением. Комбинации Мо, В, Cr и W используются для обеспечения высокой жесткости стали. Более того,комбинации Mo, Cr, Nb и W используются для достижения стойкости к размягчению при отпуске и достижения нужной микроструктуры, а также характеристик выделяемой фазы, которые повышают стойкость к коррозионному растрескиванию под напряжением при сохранении высокой прочности. Нужно понимать, что эти примеры представлены для дальнейшей иллюстрации вариантов воплощения описанных композиций и ни в коем случае не ограничивают варианты воплощения изобретения в данном описании. В табл. 2 представлены три композиции, приготовленные в соответствии с уравнением 2, вариант с низким содержанием Mn-Cr, вариант V, вариант с высоким содержанием Nb (более подробно обсуждается ниже в примере 3 в качестве образцов 14, 15 и 16). Количественное содержание элементов дано в вес.%, исходя из общего веса композиции, если не указано иное. Таблица 2 Композиции сталей в соответствии с уравнением 2 Для сравнения жесткости отпущенных сталей с различными уровнями прочности стандартизованное значение 50% FATT (температура перехода от вязкого разрушения к хрупкому), относящееся к выбранному значению предела текучести, вычислялось по уравнению 3. Уравнение 3 эмпирически получено из экспериментальных данных FATT в сравнении с пределом текучести. Говоря кратко, предел текучести и 50% FATT измерялись для каждого образца и уравнение 3 применялось для стандартизации значений 50% FATT до выбранного значения предела текучести в одном из вариантов воплощения изобретения около 122 тыс. фунтов/кв.дюйм. Эта стандартизация позволяет устранить вариации свойств благодаря пределу текучести, что позволяет проводить анализ других факторов,влияющих на результаты. Подобным образом для сравнения измеренных значений KISSC с различными уровнями предела текучести стандартизованные значения KISSC вычислялись по уравнению 4, эмпирически полученному с помощью экспериментальных данных KISSC в сравнении с YS/ В одном из вариантов воплощения изобретения значения KISSC были стандартизованы до 122 тыс. фунтов/кв.дюйм. Стандартизованные значения 50% FATT и стандартизованные значения KISSC вариантов воплощения составов обратно пропорциональны квадратному корню размера пластин, как показано на фиг. 2 и 3 соответственно. Эти результаты показывают, что жесткость, измеренная 50% FATT, и стойкость к коррозионному растрескиванию под напряжением, измеренному KISSC, улучшаются при уменьшении размера пластин. Для сравнения структуры осадка отпущенных и закаленных сталей коэффициент формы измерялся в соответствии с уравнением 5 где А и Р - это зона частицы и периметр частицы соответственно, спроектированные на плоскость. В одном из вариантов воплощения изобретения периметр может измеряться с помощью просвечивающего электронного микроскопа (ТЭМ), оснащенного функцией автоматического анализа изображения. Коэффициент формы равен примерно 1 для круглых частиц и менее 1 для продолговатых частиц. Стойкость к коррозии под напряжением. Стойкость к коррозии под напряжением исследовалась по методу испытания А NACE ТМ 0177-96(постоянная нагрузка). Результаты проиллюстрированы ниже в табл. 3. Повышение стойкости к коррозионному растрескиванию под напряжением наблюдалось, когда размер частиц выделяющейся фазы превышал 70 нм, например, у карбида железа, имеющего коэффициент формы 0,62. Таблица 3 Стойкость к коррозионному растрескиванию под напряжением и коэффициент формы составов сталей с частицами выделившейся фазы dp 70 нм Аустенизация и температуры отпуска, соответственно, указаны в скобках.около 85% минимального предела прочности материала. На основе этих данных и результатов последующей оптической микроскопии, сканирующей электронной микроскопии (СЭМ), просвечивающей электронной микроскопии (ТЭМ), ориентационной микроскопии изображений (ОМИ) и комбинаций этих методов было обнаружено положительное действие нижеописанной микроструктуры и параметров осадка. Средний размер пакетов стали, dpacket, менее 3 мкм. Выделенная фаза с диаметром частиц, dp, более 70 нм, имеющих коэффициент формы 0,62. Контроль термической обработки. Легкость контроля термической обработки (контроль технологического процесса) определялась путем оценки крутизны кривой предела текучести в зависимости от температуры отпуска. Репрезентативные измерения представлены в табл. 4 и на фиг. 4. Таблица 4 Крутизна кривой предела текучести в зависимости от температуры отпуска Согласно табл. 4 содержание ванадия приводит к увеличению крутизны кривой предела текучести/температуры, что свидетельствует о том, что тяжело достичь хорошего контроля технологического процесса в составах сталей, содержащих ванадий. Состав стали с низким содержанием V (вариант Mn-Cr) обеспечивает менее крутую кривую, чем другие изученные составы, что обозначает улучшенную возможность контроля процесса при достиже-7 018884 нии высокого предела текучести. Пример 1. Влияние содержания меди на образование слоя, защищающего от проникновения водорода. а) Материалы. Химические составы некоторых вариантов воплощения композиции стали представлены в табл. 5. Были изучены четыре типа среднеуглеродистой стали (около 0,22-0,26 вес.%) с содержанием Ti, Nb и V,а также добавок. Составы отличались добавлением меди и молибдена, количество элементов дано в вес.%, исходя из общего веса композиции, если не указано иное. Таблица 5 Композиции, рассмотренные в примере 1 Образец 1: 0,2 Cu - 0,45 Мо; низкое содержание Cu, высокое содержание Мо. Образец 2: 0,14 Cu - 0,48 Мо; высокое содержание Cu, низкое содержание Мо. Образец 3: 0,04 Cu - 0,70 Мо; низкое содержание Cu, высокое содержание Мо. Образец 4: 0,16 Cu - 0,68 Мо; высокое содержание Cu, высокое содержание Мо. б) Микроструктура и характеристика продукта коррозии. Микроструктура образцов 1-4 изучалась путем сканирующей электронной микроскопии (СЭМ) и рентгеновской дифракции при различных уровнях рН. Результаты этих наблюдений описаны выше. рН 2,7, наблюдение путем СЭМ. В целом изучались два слоя продуктов коррозии. Один слой изучался вблизи стальной поверхности и обозначен как внутренний слой, а другой слой изучался на поверхности внутреннего слоя и обозначен как внешний слой. Во внутреннем слое в большом количестве присутствовали легирующие элементы, а также он включал нестехиометрически сплавленные сульфиды железа FeS [(Fe, Mo, Cr, Mn, Cu, Ni, Na)z(S, O)x]. Внешний слой содержал кристаллы сульфида с полигональной морфологией; Fe+S или Fe+S+O. Далее наблюдалось, что чем выше содержание Cu в стали, тем ниже соотношение S:O и тем ниже клейкость коррозионных продуктов. Образующиеся сульфидные соединения не обладали высокой степенью защиты. рН 2,7, рентгеновское наблюдение. Внутренний слой определялся рентгеновским анализом как макинавит (тетрагональный сульфид железа). При приближении стальной поверхности наблюдалось более высокое число вкраплений тетрагонального сульфида железа. Чем ниже соотношение S:O, которое присутствует в коррозионном продукте сульфида, тем выше содержание Cu в стали и тем больше вкраплений кубического FeS. Кубический FeS связан с более высокой степенью коррозии. рН 4,3, рентгеновское наблюдение. Наблюдался только клейкий слой макинавита. Внешние кубические кристаллы сульфида не наблюдались. в) Проникновение водорода. Поскольку концентрация Cu в стали увеличилась, соотношение S:O в слое макинавита сократилось,что сделало слой более пористым. В результате этого подповерхностная концентрация водорода также увеличилась. г) Потеря веса. Потеря веса наблюдалась в сталях приблизительно при рН 2,7 и 4,3. д) Предварительные заключения. Образовались внутренние и внешние коррозионные продукты макинавита и кубического FeS соответственно. Внутренний слой макинавита сначала образовывался в процессе твердотельной реакции в результате наличия легирующих элементов в этом слое.(Fe(II переносилось через слой макинавита и заново осаждалось в виде тетрагонального и кубического FeS. Более высокие концентрации Cu стали результатом большей проницаемости слоя макинавита, что привело к большему поглощению Н. Таким образом, было определено, что существует как минимум два фактора, которые приводят к увеличению наблюдаемой коррозии при увеличении содержания Cu (меньшее S:O): (а) низкая клейкость коррозионного продукта, что приводит к относительно слабому антикоррозионному слою, и (б) повышение пористости макинавита, что способствует повышению концентрации подповерхностного Н. е) Механическая характеристика - стойкость к коррозионному растрескиванию под напряжением в сульфидсодержащей среде. При указанном пределе текучести и микроструктуре стали с низким содержанием Cu продемонстрировали более высокую стойкость к коррозионному растрескиванию под напряжением в сульфидсодержащей среде благодаря образованию клейкого слоя коррозионного продукта, который снижает концентрацию подповерхностного водорода. Пример 2. Влияние содержания W на устойчивость к окислению при высокой температуре. Рост зерен, стойкость к отпуску, коэффициент формы карбида железа, устойчивость к окислению, а также коррозионная стойкость, исследованные в образцах 6 С-9, представленных в табл. 6 ниже, где количественное содержание элементов дано в вес.%, исходя из общего веса состава стали, если не указано иное. а) Материалы. Таблица 6 Композиции, рассмотренные в примере 2 Образец 6 С: Исходный состав. Образец 7: Исходный состав с низким содержанием Мо. Образец 8: Исходный состав с 0,2 вес.% W, замещающего Мо. Образец 9: Исходный состав с 0,4 вес.% W, замещающего Мо. б) Рост зерен (СЭМ). В основном, не было обнаружено различий в размере зерен после аустенизации в диапазоне температуры от 920 до 1050C, это означает, что размер зерен в целом не зависит от содержания W. в) Стойкость при отпуске. В основном, не наблюдалось воздействие на стойкость при отпуске, измеряемое в понятиях увеличения жесткости в виде функции кривой отпуска. г) Коэффициент формы цементита. В основном, не наблюдалось эффекта на коэффициент формы цементита или других выделенных фаз, который повлиял бы на стойкость к коррозионному растрескиванию под напряжением. д) Стойкость к окислению. Повышение стойкости к окислению в атмосферах 9% СО 2 + 18% Н 2 О + 3% О 2 и 9% СО 2 + 18% Н 2 О+6% О 2 в диапазоне температуры от 1200 до 1340C наблюдалось в композициях, содержащих W. Каждый из образцов 8 и 9 продемонстрировал меньшее увеличение веса и поэтому меньшую степень окисления в отличие от исходного образца 6 С. Добавление W приводит к уменьшению количества фаялита при равновесных условиях и, следовательно, снижает динамику окисления. Предполагается, что добавление W к сталям облегчает процесс удаления окалины, что замедляет образование фаялита. е) Стойкость к коррозии. Добавление W обеспечивает стойкость к коррозии. Образцы 8 и 9 продемонстрировали улучшенную стойкость к питтинговой коррозии по сравнению с образцом 6 С. Пример 3. Микроструктура и механические характеристики других композиций стали для работы в кислой среде. Изучение микроструктуры (СЭМ), твердости, предела текучести, жесткости в зависимости от размера пакетов, выделенной фазы и KISSC проводилось на образцах 13 С-16, результаты которого представлены в табл. 7, где количество элементов дано в вес.%, исходя из общего веса композиции, если не указано иное. Образец 13 С: Исходный состав. Образец 14: Композиция включает в себя уменьшенное количество Mn и Cr. Образец 15: Композиция включает в себя V для стимулирования отверждения выделенной фазы. Образец 16: Композиция включает в себя высокое содержание Nb для стимулирования отверждения выделенной фазы. Образец 17: Композиция включает в себя W. В конкретных вариантах воплощения изобретения образцы не претерпевали горячую прокатку для моделирования промышленной обработки. б) Микроскопия. Ориентационная микроскопия изображений проводилась для исследования микроструктуры закаленных сталей. Подобный размер пакетов может достигаться в других химических композициях путем изменения процесса термической обработки. После закалки составов внутри каждого аустенитного зерна образуется мартенсит. Внутри каждого мартенсита пакеты могут быть определены по ориентации мартенсита (подобно формированию субзерна). Когда близлежащие пакеты имеют различную ориентацию, они ведут себя подобно межзеренной границе, что затрудняет возникновение растрескивания. Таким образом, эти образцы демонстрируют более высокие значения KISSC и более низкие температуры перехода по Шарпи. в) Жесткость. Высокие температуры отпуска требовались для достижения указанной жесткости в композиции,содержащей V (образец 15), благодаря отверждению выделенной фазы. Однако крутая кривая отпуска для этой композиции осложняет процесс контроля (см. табл. 5). г) Предел текучести. Стали проходили термическую обработку для достижения "высокого" и "низкого" предела текучести. Ограниченное содержание V имело существенное значение, поскольку было определено, что V делает сталь очень чувствительной к температуре проката. д) Твердость в зависимости от размера пакетов. Значение 50% FATT увеличивается вместе с размером пакетов. Значение KISSC улучшается по мере рафинирования размера пакетов линейным образом (фиг. 3). е) Выделенная фаза (образцы 13 С, 15, 16). Средний размер выделений для исходной композиции (13 С) был сравнимым с композицией с Nb(образец 16), для которой он приблизительно вполовину меньше, чем в составе с V (образец 15), что объясняет стойкость к отпуску и наклон кривой отпуска. Более высокие значения коэффициента формы, измеренные в образцах 15 и 16, сравнивались с образцом 13 С. ж) Стойкость к коррозионному растрескиванию под напряжением в сульфидсодержащей среде. Значения KISSC, измеренные в образцах 13 С, 14, 15 и 16, изображались в зависимости от предела текучести (фиг. 1) для изучения отношения между этими свойствами. Хорошая корреляция наблюдалась между значениями KISSC и пределом текучести. Чем выше предел текучести, тем ниже KISSC. Полагается, что это не имеет никакого статистического значения при стойкости к коррозионному растрескиванию под напряжением в сульфидсодержащей среде для указанного предела текучести с изменением состава стали. Это наблюдение связано со сходствами конечной микроструктуры (уменьшение размера зерна, размер пакетов, форма и распределение выделенной фазы). Когда образцы с пределом текучести от 122 до 127 тыс. фунтов/кв.дюйм (приблизительно от 841 до 876 МПа) нагружались до уровня нагрузки около 85% SMYS, составы с V и Nb выдержали без повреждений около 720 ч. Пример 4. Влияние микроструктуры на диффузию водорода. Кривые отпуска, измеренные для получения значений предела текучести и твердости в виде функции температуры отпуска, изученные на образцах 10 С-12, представлены в табл. 8 ниже, где количество элементов дано в вес.%, исходя из общего веса состава стали, если не указано иное. Далее изучалось концентрация в ч./млн Образец 10 С: Исходный состав. Образец 11: Состав с высоким содержанием V. Образец 12: Состав с высоким содержанием Cr. б) Кривая отпуска (образцы 10, 11). Материал с высоким содержанием V (образец 11) продемонстрировал очень крутую кривую отпуска (измерение в виде предела текучести и жесткости в зависимости от температуры). Ограничение содержания V улучшило контроль процесса термической обработки. в) Проникновение водорода (образцы 9, 10, 11). Для указанного предела текучести способность захватывания Н была сопоставимой у трех видов сталей. Аналогичным образом для указанного предела текучести способность возврата Н была сопоставимой у трех видов сталей. Хотя вышеприведенное описание показывает, описывает и выделяет фундаментальные новые характеристики представленных идей изобретения, предполагается, что различные упущения, замены и изменения в отдельных элементах используемого оборудования и вариантах использования могут быть сделаны специалистами в данной области техники без отступления от объема настоящего изобретения. Следовательно, сущность данного изобретения не ограничивается вышеприведенным описанием, но определяется формулой изобретения. ФОРМУЛА ИЗОБРЕТЕНИЯ 1. Сталь, содержащая углерод (С) от 0,2 до 0,3 вес.%; марганец (Mn) от 0,1 до 1 вес.%; кремний (Si) от 0 до 0,5 вес.%; хром (Cr) от 0,4 до 1,5 вес.%; молибден (Mo) от 0,1 до 1 вес.%; ниобий (Nb) от 0 до 0,1 вес.%; алюминий (Al) от 0 до 0,1 вес.%; кальций (Ca) от 0 до 0,01 вес.%; бор (В) менее 100 ч./млн; титан(Ti) от 0 до 0,05 вес.%; вольфрам (W) от 0,1 до 1,5 вес.%; ванадий (V) менее 0,05 вес.%; медь (Cu) от 0 до не более чем 0,15 вес.%; кислород (О) менее 200 ч./млн; азот (N) менее 0,01 вес.%; сера (S) менее 0,003 вес.% и фосфор (Р) менее 0,015 вес.%; где количественное содержание элементов дано в вес.%, исходя из общего веса композиции стали. 2. Сталь по п.1, в которой значение выражения Mo/10 + Cr/12 + W/25 + Nb/3 + 25 В составляет от 0,05 до 0,39 вес.%. 3. Сталь по любому из пп.1 или 2, которая характеризуется пределом текучести от 120 до 140 тыс. фунтов/кв.дюйм. 4. Сталь по любому из пп.1-3, которая характеризуется стойкостью к коррозионному растрескиванию под напряжением в сульфидсодержащей среде, составляющей около 720 ч, согласно испытанию по методике A NACE TM0177, при напряжении около 85% SMYS (минимальный предел прочности материала) для полноразмерных образцов. 5. Сталь по любому из пп.1-4, содержащая углерод (С) от 0,2 до 0,3 вес.%; марганец (Mn) от 0,2 до 0,5 вес.%; кремний (Si) от 0,15 до 0,4 вес.%; хром (Cr) от 0,4 до 1 вес.%; молибден (Mo) от 0,3 до 0,8 вес.%; ниобий (Nb) от 0,02 до 0,06 вес.%; алюминий (Al) от 0,02 до 0,07 вес.%; кальций (Ca) от 0 до 0,01 вес.%; бор (В) от 10 до 30 ч./млн; титан (Ti) от 0,1 до 0,03 вес.%; вольфрам (W) от 0,2 до 0,6 вес.%; ванадий (V) менее 0,05 вес.%; медь (Cu) от 0 до не более чем 0,08 вес.%; кислород (О) менее 200 ч./млн; азот(N) менее 0,01 вес.%; сера (S) менее 0,002 вес.% и фосфор (Р) менее 0,010 вес.%. 6. Сталь по любому из пп.1-5, предназначенная для изготовления труб. 7. Сталь, содержащая углерод (С), молибден (Mo), хром (Cr), вольфрам (W), ниобий (Nb), бор (В) и ванадий в количестве менее 0,05 вес.%, в которой количественное содержание элементов, приведенное в вес.% от общего веса состава стали, таково, что значение выражения Mo/10 + Cr/12 + W/25 + Nb/3 + 25 В составляет от 0,05 до 0,39 вес.%. 8. Сталь по п.7, в которой значение выражения Mo/10 + Cr/12 + W/25 + Nb/3 + 25 В составляет от 0,10 до 0,26 вес.%. 9. Сталь по любому из пп.7 и 8, которая характеризуется линейной зависимостью между стойко- 11018884 стью к коррозионному растрескиванию под напряжением в сульфидсодержащей среде (KISSC) в режиме I и пределом текучести. 10. Сталь по любому из пп.7-9, которая характеризуется средним размером пакетов dpacket, составляющим менее 3 мкм. 11. Сталь по любому из пп.7-10, которая содержит выделившуюся фазу с диаметром частиц, dp, составляющим более 70 нм, и средний коэффициент формы 0,62, где коэффициент формы вычисляется по формуле 4A/Р 2, где А - это площадь проекции частицы, а Р - периметр проекции частицы. 12. Сталь по любому из пп.7-11, микроструктура которой содержит более 95 об.% мартенсита и менее 5 об.% бейнита, исходя из общего объема композиции стали. 13. Сталь по п.7, содержащая углерод (С) от 0,2 до 0,3 вес.%; хром (Cr) от 0,4 до 1,5 вес.%; молибден (Mo) от 0,1 до 1 вес.%; ниобий (Nb) от 0 до 0,1 вес.%; бор (В) менее 100 ч./млн; вольфрам (W) от 0,1 до 1,5 вес.%; исходя из общего веса композиции стали. 14. Сталь по п.13, содержащая марганец (Mn) от 0,1 до 1 вес.%; кремний (Si) от 0 до 0,5 вес.%; алюминий (Al) от 0 до 0,1 вес.%; кальций (Ca) от 0 до 0,01 вес.%; титан (Ti) от 0 до 0,05 вес.%; ванадий(V) менее 0,05 вес.%; медь (Cu) от 0 до не более чем 0,15 вес.%; кислород (О) менее 200 ч./млн; азот (N) менее 0,01 вес.%; сера (S) менее 0,003 вес.% и фосфор (Р) менее 0,015 вес.%.
МПК / Метки
МПК: C22C 38/22
Код ссылки
<a href="https://eas.patents.su/14-18884-stali-dlya-kislyh-sred.html" rel="bookmark" title="База патентов Евразийского Союза">Стали для кислых сред</a>
Предыдущий патент: Компактная крышка с визуальной идентификацией вскрытия
Следующий патент: Фармацевтическая композиция контролируемого высвобождения, содержащая толперизона гидрохлорид
Случайный патент: Гербицидный состав