Хромоникелевый сплав
Номер патента: 20052
Опубликовано: 29.08.2014
Авторы: Фрайхерр Фон Рихтхофен Александер, Якоби Дитлинде, Кардук Петер
Формула / Реферат
1. Хромоникелевый сплав с высокими стойкостью к окислению и науглероживанию, длительной прочностью и сопротивлением ползучести, который содержит
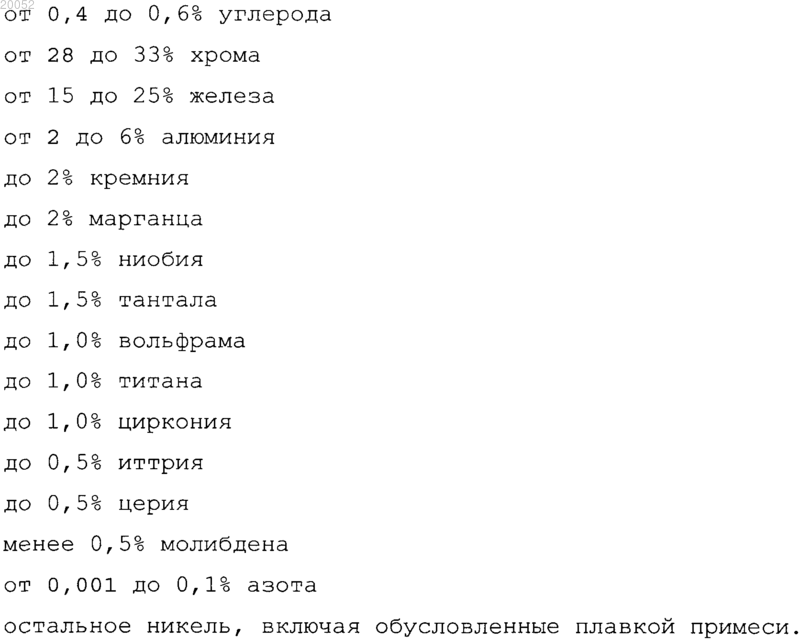
2. Сплав по п.1, который содержит
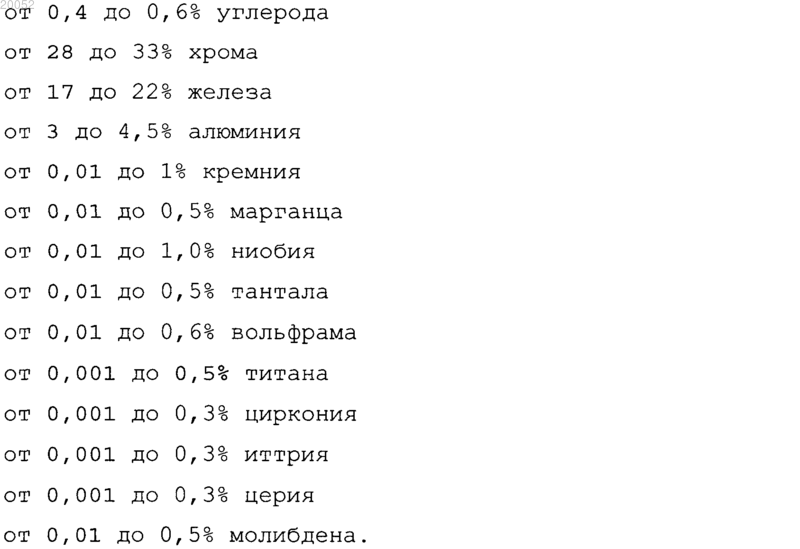
3. Способ, по меньшей мере частичного, кондиционирования объектов из сплава по п.1 или 2 в поверхностной зоне путем механического съема с давлением прижима от 10 до 40 МПа и последующего нагревания со скоростью нагрева от 10 до 100°C/ч до температуры на поверхности от 400 до 740°C при слабоокислительных условиях с предотвращением образования конденсата.
4. Способ по п.3, отличающийся тем, что давление прижима составляет от 15 до 30 МПа.
5. Способ по п.3 или 4, отличающийся тем, что нагревание проводится в атмосфере защитного газа.
6. Способ по любому из пп.3-5, отличающийся тем, что при съеме поверхностную зону подвергают холодному деформированию на глубину от 0,1 до 0,5 мм.
7. Способ по любому из пп.3-6, отличающийся заключительным отжигом, выдерживанием от 1 до 50 ч при 400-750°C, а также заключительным нагревом со скоростью от 10 до 100°C/ч до рабочей температуры.
8. Способ по п.7, отличающийся тем, что температура выдерживания составляет от 550 до 650°C.
9. Способ по любому из пп.7, 8, отличающийся тем, что атмосфера отжига состоит из слабоокислительной смеси водяного пара, водорода, углеводородов и инертных газов с парциальным давлением кислорода при 600°C ниже 10-20 бар.
10. Способ по п.9, отличающийся парциальным давлением кислорода ниже 10-30 бар.
11. Способ по любому из пп.7-10, отличающийся тем, что атмосфера отжига состоит из 0,1-10 мол.% водяного пара, 7-99,9 мол.% водорода и углеводородов, по отдельности или в комбинации, а также 0-88 мол.% инертных газов, по отдельности или в комбинации.
12. Применение сплава по любому из пп.1, 2 в качестве материала для получения отливок.
13. Применение сплава по любому из пп.1, 2 в качестве материала для нефтехимических установок.
14. Применение сплава по любому из пп.1, 2 в качестве материала для змеевиков крекинг-печей и печей риформинга, подогревателей, труб риформера, а также для установок прямого восстановления железной руды.
15. Применение сплава по любому из пп.1, 2 в качестве материала для получения деталей печей, трубчатых излучателей для нагрева печей, валков для отжигательных печей, деталей установок непрерывной разливки и полосового литья, колпаков и муфт для отжигательных печей, деталей больших дизельных двигателей и формовок для засыпки катализаторов.
Текст
Хромоникелевый сплав с 0,4-0,6% углерода, 28-33% хрома, 15-25% железа, 2-6% алюминия, до 2% кремния, до 2% марганца, до 1,5% ниобия, до 1,5% тантала, до 1,0% вольфрама, до 1,0% титана, до 1,0% циркония, до 0,5% иттрия, до 0,5% церия, до 0,5% молибдена, до 0,1% азота,остальное - никель, имеет высокие стойкость к окислению и науглероживанию, длительную прочность и сопротивление ползучести. Этот сплав подходит, в частности, в качестве материала для компонентов нефтехимических установок и деталей, например для змеевиков крекинг-печей и печей для риформинга, подогревателей и труб риформера, а также для применения для деталей установок прямого восстановления железной руды. Нефтехимия требует для высокотемпературных процессов материалы, которые были бы как термостойкими, так и коррозионно-устойчивыми и, в частности, через которые проходили бы, с одной стороны, горячие продуктовые газы, а, с другой стороны, также горячие газообразные продукты сгорания, например, установок парового крекинга. Их змеевики снаружи испытывают действие окислительных азотирующих газообразных продуктов сгорания с температурами до 1100C и выше, а внутри также испытывают температуры до примерно 900C и в известных случаях также высокое давление науглероживающей и окислительной атмосферы. Поэтому при контакте с горячими газообразными продуктами сгорания происходят, начиная от наружной поверхности трубы, азотирование материала трубы и возникновение слоя окалины. Науглероживающая углеводородная атмосфера внутри трубы связана с опасностью, что углерод будет диффундировать оттуда в материал трубы, что добавляет карбиды в материале, и из имеющегося там карбида М 23 С 9 при усилении науглероживания будет образовываться более обогащенный углеродом карбид M7C6. Следствием этого являются внутренние напряжения из-за связанного с образованием или превращением карбидов увеличения объема карбидов, а также снижение прочности и вязкости материала трубы. Кроме того, на внутренней поверхности доходит до возникновения прочно удерживающегося слоя кокса толщиной до нескольких миллиметров. Циклические температурные нагрузки, которые возникают вследствие остановки установки, приводят, кроме того, к тому, что трубы из-за разных коэффициентов теплового расширения металлической трубы и слоя кокса напрессовываются на коксовый слой. Это ведет к высоким напряжениям в трубе, что может привести к возникновению трещин на внутренней поверхности трубы. Позднее через такие трещины в материал трубы может попасть больше углеводородов. Из описания к патенту US 5306358 известен свариваемый ВИГ-сваркой никель-хром-железный сплав с содержанием до 0,5% углерода, от 8 до 22% хрома, до 36% железа, до 8% марганца, кремния и ниобия, до 6% алюминия, до 1% титана, до 0,3% циркония, до 40% кобальта, до 20% молибдена и вольфрама, а также до 0,1% иттрия, остальное никель. Далее, в описании к немецкому патенту 10302989 в качестве материала, подходящего для змеевиков крекинг-печей и печей риформинга, описан также хромоникелевый литейный сплав, содержащий до 0,8% углерода, 15-40% хрома, 0,5-13% железа, 1,5-7% алюминия, до 0,2% кремния, до 0,2% марганца,0,1-2,5% ниобия, до 11% вольфрама и молибдена, до 1,5% титана, 0,1-0,4% циркония и 0,01-0,1% иттрия,остальное никель. Этот сплав полностью оправдал себя, в частности, при применении в качестве материала для труб, хотя практика, кроме того, требует материалов для труб с увеличенным сроком службы. Поэтому изобретение направлено на хромоникелевый сплав с улучшенной стойкостью в таких условиях, какие имеются, например, при крекинге и риформинге углеводородов. Решение этой задачи состоит в хромоникелевом сплаве с 0,4-0,6% углерода, 28-33% хрома, 15-25% железа, 2-6% алюминия, до 2% каждого из кремния и марганца, до 1,5% каждого из ниобия и тантала, до 1,0% каждого из вольфрама, титана и циркония, до 0,5% каждого из иттрия и церия, до 0,5% молибдена и до 0,1% азота, остальное никель, включая обусловленные плавкой примеси. Предпочтительно этот сплав содержит, соответственно по отдельности или в комбинации, 17-22% железа, 3-4,5% алюминия, 0,01-1% кремния, до 0,5% марганца, 0,5-1,0% ниобия, до 0,5 тантала, до 0,6% вольфрама, 0,001-0,5% титана, до 0,3% циркония, до 0,3% иттрия, до 0,3% церия, 0,01-0,5% молибдена и 0,001-0,1% азота. Сплав согласно изобретению отличается, в частности, сравнительно высоким содержанием хрома и никеля, а также намеренным содержанием углерода в пределах сравнительно узкого диапазона. Из факультативных компонентов сплава кремний улучшает стойкость к окислению и науглероживанию. Марганец также положительно влияет на стойкость к окислению, а также дополнительно благоприятно влияет на свариваемость, раскисляет плавку и стабильно связывает серу. Ниобий улучшает длительную прочность, образует стабильные карбиды и карбонитриды; кроме того, он служит как отвердитель смешанных кристаллов. Титан и тантал улучшают длительную прочность. Уже при очень низком содержании образуются очень тонко распределенные карбиды и карбонитриды. При более высоких содержаниях титан и тантал действуют как отвердители смешанных кристаллов. Вольфрам улучшает длительную прочность. В частности, при высоких температурах вольфрам путем отверждения смешанных кристаллов улучшает прочность, так как карбиды при повышенных температурах частично переходят в раствор. Кобальт также улучшает длительную прочность путем твердения смешанных кристаллов, цирконий из-за образования карбидов, в частности во взаимодействии с титаном и танталом. Очевидно, что иттрий и церий улучшают не только стойкость к окислению и, в частности, адгезию,но также рост верхнего слоя Al2O3. Кроме того, иттрий и церий уже при очень низких содержаниях улучшают сопротивление ползучести, так как они стабильно связывают все еще имеющуюся свободную серу. Низкие содержания бора также улучшают длительную прочность, предотвращают ликвацию серы и замедляют старение из-за укрупнения карбидов M23C6. Молибден также улучшает длительную прочность, в частности, при высоких температурах, путем отверждения смешанных кристаллов. В частности, при очень высоких температурах карбиды частично переходят в раствор. Азот улучшает длительную прочность путем образования карбонитридов, тогда как гафний уже при низких содержаниях улучшает стойкость к окислению путем лучшей адгезии верхнего слоя и положительно влияет на длительную прочность. Фосфор, сера, цинк, свинец, мышьяк, висмут, олово и теллур относятся к примесям, поэтому их содержание должно быть как можно меньшим. В этих условиях сплав годится, в частности, в качестве литейного материала для компонентов нефтехимических установок, например, для получения змеевиков для крекинг-печей и печей риформинга,для труб риформера, а также как материал для установок прямого восстановления железной руды, а также для конструкционных элементов, испытывающих близкую нагрузку. Сюда относятся детали печей,трубные излучатели для обогрева печей, валки для отжигательной печи, детали для установок непрерывной разливки и полосового литья, колпаки и муфты для отжигательной печи, детали больших дизельных двигателей и формовки для засыпки катализатора. В целом сплав отличается высокой стойкостью к окислению и науглероживанию, а также хорошими длительной прочностью и сопротивлением ползучести. Внутренняя поверхность труб крекинг-печей или риформера отличается, кроме того, каталитически инертным, алюминийсодержащим оксидным слоем и препятствует тем самым возникновению нитей каталитического кокса, так называемых углеродных нанотрубок. Отличающие материал свойства сохраняются также при многократном выгорании кокса,неизбежно осаждающегося при крекинге на внутренних стенках труб. Особенно выгодно применение сплава для получения труб для центробежного литья, если они рассверливаются при давлении сжатия от 10 до 40 МПа, например 10-25 МПа. При таком растачивании изза давления сжатия происходит холодная деформация или наклеп материала труб в приповерхностной зоне на глубину, например, от 0,1 до 0,5 мм. При нагревании трубы холоднодеформированная зона рекристаллизуется, при этом возникает очень тонкозернистая структура. Рекристаллизационная структура улучшает диффузию оксидообразующих элементов алюминия и хрома, что облегчает образование состоящего в основном из оксида алюминия сплошного слоя с высокой плотностью и стабильностью. Образующийся при этом прочно удерживающийся алюминийсодержащий оксид образует сплошной защитный слой на внутренней стенке трубы, который, по существу, не содержит каталитически активных центров, например, из никеля или железа, и даже после длительной циклической тепловой нагрузки все еще стабилен. Этот алюминийсодержащий оксидный слой предотвращает, в отличие от других материалов труб без такого верхнего слоя, внедрение кислорода в основной материал и, тем самым,внутреннее окисление материала труб. Кроме того, верхний слой подавляет не только науглероживание материала труб, но также коррозию примесями в технологическом газе. Верхний слой состоит преимущественно из Al2O3 и смешанного оксида (Al,Cr)2 О 3 и является, по существу, инертным в отношении образования каталитического кокса. Он беден такими элементами, как железо и никель, которые катализируют образование кокса. Особенно выгодной для образования прочного оксидного защитного слоя является тепловая обработка, которую можно очень экономично провести также in situ; она служит для доводки, например,внутренней поверхности труб парового крекинга после их установки, когда рассматриваемая печь нагревается до своей рабочей температуры. Эта доводку можно провести как нагревание с включенными в промежутке изотермическими термообработками в атмосфере печи, устанавливающейся при нагревании согласно изобретению, например,в очень слабоокислительной, содержащей водяной пар атмосфере, с парциальным давлением кислорода максимум 10-20, предпочтительно максимум 10-30 бар. Особенно подходит атмосфера защитного газа, состоящая из 0,1-10 мол.% водяного пара, 7-99,9 мол.% водорода и углеводорода, по отдельности или в комбинации, а также 0-88 мол.% инертных газов. Атмосфера при доводке состоит предпочтительно из чрезвычайно слабоокислительной смеси водяного пара, водорода, углеводородов и инертных газов в таком количественно соотношении, чтобы парциальное давление кислорода в смеси при температуре 600C было меньше 10-20 бар, предпочтительно меньше 10-30 бар. Начальный нагрев внутренней части трубы после предшествующего механического снятия поверхностного слоя, т.е. отдельный нагрев образующейся при этом холоднодеформированной поверхностной зоны, происходит предпочтительно в очень слабоокислительной атмосфере защитного газа в несколько фаз, соответственно со скоростью от 10 до 100C/ч, сначала до 400-750C, предпочтительно примерно до 550C на внутренней поверхности трубы. К этой фазе нагрева примыкает выдерживание от 1 до 50 ч в упомянутом температурном диапазоне. Нагревание проводится в присутствии атмосферы водяного пара,после того как температура достигнет значения, которое исключает образование конденсированной воды. Вслед за этим выдерживанием трубу доводят затем до рабочей температуры, например до 800-900C,и, тем самым, она готова к работе. Однако в условиях крекинга температура печи постепенно повышается дальше вследствие осаждения пиролитического кокса и достигает в конце концов на внутренней поверхности примерно 1000 или же 1050C. При этой температуре внутренний слой, состоящий в основном из Al2O3 и в меньшей степени из (Al,Cr)2 О 3, превращается из переходного оксида, такого как -, - или -Al2O3, в стабильный -оксид алюминия. Тем самым, труба со своим механически снятым внутренним слоем в многостадийном способе, но предпочтительно в один проход, достигает своего рабочего состояния. Однако способ не должен непременно проводиться в одну стадию, но может начинаться также с отдельной предварительной стадии. Эта предварительная стадия охватывает начальный нагрев после снятия внутренней поверхности и до выдерживания при 400-750C. Предварительно обработанная таким образом труба может затем, например, на другом предприятии обрабатываться дальше in situ вышеописанным образом, начиная с ее холодного состояния, т.е. доводиться в собранном состоянии до рабочей температуры. Разумеется, упомянутая отдельная предварительная обработка не ограничена трубами, но подходит также для частичной или полной доводки поверхностных зон других изделий, которые затем обрабатываются, в соответствии с их свойствами и применением как способом по изобретению, так и другими способами, однако начиная с определенного исходного состояния. Далее изобретение в целях иллюстрации поясняется на пяти никелевых сплавах в сравнении с десятью традиционными никелевыми сплавами, состав которых указан в табл. I и которые отличаются от никель-хром-железного сплава согласно изобретению, в частности, содержанием в них углерода (сплавы 5 и 6), хрома (сплавы 4, 13 и 14), алюминия (сплавы 12, 13), кобальта (сплавы 1, 2) и железа (сплавы 3,12, 14, 15). Как следует из графика согласно фиг. 1, в сплаве 9 по изобретению после 25-минутного отжига при 1150C на воздухе никакого внутреннего окисления не происходит и после более 200 циклов, тогда как оба сравнительных сплава 12 и 13 уже через несколько циклов испытывают возрастающее уменьшение веса как следствие катастрофического окисления. Кроме того, сплав 9 отличается высокой стойкостью к науглероживанию, так как согласно диаграмме на фиг. 2, благодаря меньшему увеличению веса после всех трех науглероживающих обработок,он имеет самое малое увеличение веса по сравнению с обычными сплавами 12 и 13. Кроме того, графики на фиг. 3 а и 3b показывают, что длительная прочность никелевого сплава 11 согласно изобретению в основной области еще лучше, чем у обоих сравнительных сплавов 12 и 13. Исключение составляет здесь не отвечающий изобретению сплав 15 из-за слишком низкого содержания в нем железа, но который имеет худшую стойкость к окислению, науглероживанию и закоксовыванию. Наконец, из графика на фиг. 4 следует, что сопротивление ползучести сплава 11 намного лучше,чем у сравнительного сплава 12. Далее, несколько участков труб из никелевого сплава согласно изобретению использовали в лабораторной установке в серии имитации режима крекинга, чтобы провести опыты с нагреванием в разных газовых атмосферах и с разными условиями нагревания, за которыми непосредственно следовала 30 минутная фаза крекинга при температуре 900C, чтобы изучить и оценить начальную фазу образования каталитического кокса или склонность к образованию каталитического кокса. Данные и результаты этих опытов с образцами сплава 11 согласно изобретению из табл. I собраны в табл. II. Они показывают, что соответствующая газовая атмосфера в сочетании с регулированием температуры согласно изобретению приводит к существенному снижению и так уже низкого образования каталитического кокса. Примеры поверхностных свойств внутренней части печных труб из сплава 8, состав которого отвечает изобретению, выявляются из фиг. 5 и 6. Фиг. 6 (опыт 7 согласно табл. II) показывает преимущество поверхности после доводки согласно изобретению в сравнении с фиг. 5, которая относится к поверхности, не доведенной согласно изобретению (табл. II, опыт 2). На фиг. 7 (сплав 14) и 8 (изобретение) показаны поверхностные области в поперечном шлифе. Образцы нагревали до 950C и подвергали затем 10 циклам крекинга каждый 10 ч в атмосфере, состоящей из водяного пара, водорода и углеводородов. После каждого цикла испытуемые трубы выжигали для удаления отложений кокса в течение 1 ч. Кроме того, снимок структуры на фиг. 7 показывает в виде темных областей, занимающий большую площадь и, тем самым, также большой объем, результат внутреннего окисления на внутренней стороне трубы в случае обычного хромоникелевого литейного сплава,в сравнении со снимком структуры (фиг. 8) сплава 9 согласно изобретению, который не испытал практически никакого внутреннего окисления, хотя оба образца одинаковым образом подвергались многократной циклической обработке, состоящей, с одной стороны, из крекинга и, с другой стороны, удаления отложений углерода. Опыты показывают, что в образцах из традиционных сплавов происходит сильное внутреннее окисление на внутренней поверхности трубы, начиная с поверхностных дефектов. Этим обусловлено возникновение на внутренней поверхности трубы маленьких металлических центров с высоким содержанием никеля, на которых в значительной степени образуется углерод в виде углеродных нанотрубок(фиг. 11). Напротив, образец 9 из сплава согласно изобретению после тех же десяти циклов крекинга и последующей выдержки в коксующей атмосфере не содержит никаких углеродных нанотрубок, что можно объяснить, по существу, сплошным плотным каталитически инертным алюминийсодержащим оксидным слоем. Напротив, фиг. 11 относится к полученному на растровом электронном микроскопе (РЭМ) виду сверху обычного образца, показанного на фиг. 7, в виде шлифа; эта фигура показывает катастрофическое окисление из-за отсутствия верхнего слоя и соответствующее этому катастрофическое образование каталитического кокса в виде углеродных нанотрубок. Особенно наглядной, при сравнении графиков на фиг. 9 и 10, оказывается стабильность оксидного слоя на сплаве согласно изобретению, на основании изменения концентрации алюминия с глубиной краевой зоны после десяти фаз крекинга с соответствующим удалением отложений кокса путем выжигания в промежуточной фазе. Тогда как, согласно графику на фиг. 9, в приповерхностной области вследствие локальных отказов защитного верхнего слоя и возникающего из-за этого сильного внутреннего окисления алюминия материал обедняется алюминием, концентрации алюминия на графике с фиг. 10 движутся примерно в сторону исходного уровня литейного материала. Здесь четко видно значение в трубах согласно изобретению сплошного плотного и, в частности, прочно удерживающегося внутреннего алюминийсодержащего оксидного слоя. Стабильность алюминийсодержащего оксидного слоя была исследована также долговременными опытами в лабораторной установке в условиях, близких к условиям процесса. Образцы сплавов 9 и 11 согласно изобретению нагревали в водяном паре до 950C и подвергали затем трехкратному 72-часовому крекингу при этой температуре; затем их подвергали 4-часовому выжиганию при 900C. Снимок на фиг. 12 показывает сплошной алюминийсодержащий оксидный слой после трех циклов крекинга и, кроме того, показывает, что алюминийсодержащий оксидный слой материала сам покрывает карбид хрома на поверхности. Видно, что имеющиеся на поверхности карбиды хрома полностью покрыты алюминийсодержащим оксидным слоем. Даже в поврежденных зонах поверхности, в которых имеются скопления первичных карбидов основного материала и которые поэтому особенно склонны к внутреннему окислению, материал защищен равномерным алюминийсодержащим оксидным слоем, как это отчетливо показывают снимки структуры на фиг. 13. Видно, что окисленный прежний карбид МС оброс алюминийсодержащим оксидом и, тем самым, закрыт. Микрофотографии структуры приповерхностных зон согласно фиг. 14 и 15 показывают, что даже после длительных циклических испытаний не возникает никакого внутреннего окисления, что обусловлено стабильным и сплошным алюминийсодержащим оксидным слоем. В этих опытах использовались образцы 8-11 сплавов согласно изобретению. В целом, никель-хром-железный сплав согласно изобретению в качестве, например, материала для труб после съема внутренней поверхности механическим давлением и последующей многостадийной термообработки in situ для доводки внутренней поверхности отличается высокой стойкостью к окислению, коррозии и, в частности, высокой длительной прочностью и сопротивлением ползучести. Однако особенно следует подчеркнуть, прежде всего, исключительную стойкость материала к науглероживанию, которая обусловлена быстрым образованием, по существу, сплошного и стабильного оксидного слоя, или слоя Al2O3. Этот слой, прежде всего в трубах для парового крекинга и трубах риформера, по существу, подавляет возникновение каталитически активных центров, опасных образованием каталитического кокса. Эти свойства материала не теряются также после большого числа заметно более продолжительных циклов крекинга, сочетающихся с выжиганием осевшего кокса. Таблица I Это значение было определено подсчетом углеродных нитей на определенной площади трубы.После достижения рабочей температуры обработка 1 ч при 250 ppm серы (H2S) в водяном паре. ФОРМУЛА ИЗОБРЕТЕНИЯ 1. Хромоникелевый сплав с высокими стойкостью к окислению и науглероживанию, длительной прочностью и сопротивлением ползучести, который содержит 3. Способ, по меньшей мере частичного, кондиционирования объектов из сплава по п.1 или 2 в поверхностной зоне путем механического съема с давлением прижима от 10 до 40 МПа и последующего нагревания со скоростью нагрева от 10 до 100C/ч до температуры на поверхности от 400 до 740C при слабоокислительных условиях с предотвращением образования конденсата. 4. Способ по п.3, отличающийся тем, что давление прижима составляет от 15 до 30 МПа. 5. Способ по п.3 или 4, отличающийся тем, что нагревание проводится в атмосфере защитного газа. 6. Способ по любому из пп.3-5, отличающийся тем, что при съеме поверхностную зону подвергают холодному деформированию на глубину от 0,1 до 0,5 мм. 7. Способ по любому из пп.3-6, отличающийся заключительным отжигом, выдерживанием от 1 до 50 ч при 400-750C, а также заключительным нагревом со скоростью от 10 до 100C/ч до рабочей температуры. 8. Способ по п.7, отличающийся тем, что температура выдерживания составляет от 550 до 650C. 9. Способ по любому из пп.7, 8, отличающийся тем, что атмосфера отжига состоит из слабоокислительной смеси водяного пара, водорода, углеводородов и инертных газов с парциальным давлением кислорода при 600C ниже 10-20 бар. 10. Способ по п.9, отличающийся парциальным давлением кислорода ниже 10-30 бар. 11. Способ по любому из пп.7-10, отличающийся тем, что атмосфера отжига состоит из 0,1-10 мол.% водяного пара, 7-99,9 мол.% водорода и углеводородов, по отдельности или в комбинации, а также 0-88 мол.% инертных газов, по отдельности или в комбинации. 12. Применение сплава по любому из пп.1, 2 в качестве материала для получения отливок. 13. Применение сплава по любому из пп.1, 2 в качестве материала для нефтехимических установок. 14. Применение сплава по любому из пп.1, 2 в качестве материала для змеевиков крекинг-печей и печей риформинга, подогревателей, труб риформера, а также для установок прямого восстановления железной руды. 15. Применение сплава по любому из пп.1, 2 в качестве материала для получения деталей печей,трубчатых излучателей для нагрева печей, валков для отжигательных печей, деталей установок непрерывной разливки и полосового литья, колпаков и муфт для отжигательных печей, деталей больших дизельных двигателей и формовок для засыпки катализаторов.
МПК / Метки
МПК: C22C 19/05
Метки: сплав, хромоникелевый
Код ссылки
<a href="https://eas.patents.su/12-20052-hromonikelevyjj-splav.html" rel="bookmark" title="База патентов Евразийского Союза">Хромоникелевый сплав</a>
Предыдущий патент: Получение сырья для алкилирования
Следующий патент: Герметичный ступичный подшипниковый узел для сельскохозяйственных применений
Случайный патент: Датчик расхода жидкости