Усовершенствования в области топливных элементов
Формула / Реферат
1. Способ снабжения топливом среднетемпературного твердооксидного топливного элемента, включающий стадии подведения топлива, обогащенного монооксидом углерода, в анодную область (5d) топливного элемента, после того как топливо вступит в контакт с катализатором (10b1, 10b2) реакции конверсии водяного газа в области анода таким образом, что реакция конверсии водяного газа протекает благодаря присутствию в топливе остаточной воды и/или водяного пара, образованного на аноде, где топливо содержит количество воды, недостаточное для полного каталитического превращения топлива в диоксид углерода, и водород под действием катализатора конверсии водяного газа (WGS).
2. Способ по п.1, где указанный среднетемпературный твердооксидный топливный элемент является частью батареи среднетемпературных твердооксидных топливных элементов, включающей анодную область (5d), катод (5f), отделенный от анода, газонепроницаемый электролит (5е) между анодом и катодом, первое приспособление (1b) для подачи окислителя к катоду, второе приспособление (2) для подачи топлива к аноду, где второе приспособление включает катализатор (10b1, 10b2) реакции конверсии водяного газа, размещенный вблизи анода, для реализации в условиях эксплуатации катализа реакции конверсии водяного газа между монооксидом углерода в топливе и водой/водяным паром, которые присутствуют как остаточные в топливе или образованные путем реакции на аноде.
3. Способ по п.2, по которому топливо подают к аноду через камеру (11b), имеющую стенку (10с) с пористым участком, рядом с которым, снаружи камеры, размещен анод, причем топливо проходит через пористый участок для контактирования с анодом, и катализатор реакции конверсии водяного газа размещен в камере вблизи пористого участка, но отдельно от него.
4. Способ по п.2 или 3, по которому топливо подают к аноду через камеру (11b), имеющую стенку (10с) с пористым участком, рядом с которым, снаружи камеры, размещен анод, причем топливо проходит через пористый участок для контактирования с анодом, где катализатор реакции конверсии водяного газа расположен на стенке в камере между порами пористого участка так, что поры открыты для прохождения топлива.
5. Способ по п.3, по которому катализатор реакции конверсии водяного газа размещают на носителе, размещенном на стороне, противоположной пористому участку стенки, но на небольшом расстоянии от него.
6. Способ по п.4, по которому носитель сформирован внутренней поверхностью второй стенки камеры, причем вторая стенка несет на себе катализатор реакции конверсии водяного газа и расположена параллельно пористому участку стенки, но на небольшом расстоянии от него.
7. Способ по п.4, по которому носитель сформирован вставкой, закрепленной на внутренней поверхности второй стенки камеры, причем вставка несет на себе катализатор реакции конверсии водяного газа и расположена параллельно пористому участку стенки, но на небольшом расстоянии от него.
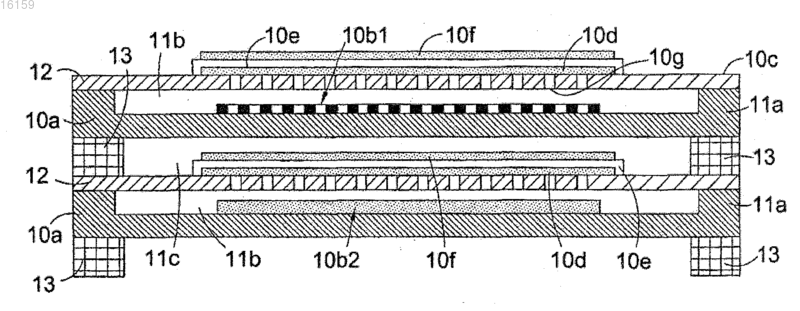
Текст
Способ снабжения топливом среднетемпературного твердооксидного топливного элемента,включающий стадии подведения (11b) топлива, обогащенного монооксидом углерода, в анодную область (10d) топливного элемента, после того как топливо вступит в контакт с катализатором(10b1), (10b2) реакции конверсии водяного газа в области анода таким образом, что реакция конверсии водяного газа протекает благодаря присутствию в топливе остаточной воды и/или водяного пара, образованного на аноде, и также батарея топливных элементов, реализующая способ, включающая анод (10d), катод (10f), отделенный от анода, газонепроницаемый электролит(10 е) между анодом и катодом, первое приспособление для подачи окислителя к катоду (11 е), второе приспособление (11b) для подачи топлива к аноду, в которой второе приспособление включает катализатор (10b1), (10b2) реакции конверсии водяного газа, размещенный вблизи анода, для катализирования реакции конверсии водяного газа между монооксидом углерода в топливе и водой/ водяным паром, которые присутствуют как остаточные в топливе или образованные из реакции на аноде. Представлен также способ нанесения катализатора на металлическую подложку методом струйной печати.(71)(73) Заявитель и патентовладелец: СЕРЕС ИНТЕЛЛЕКЧУАЛ ПРОПЕРТИ КОМПАНИ ЛИМИТЕД 016159 Уровень техники Хорошо известно преобразование углеводородного топлива, такого как пропан, в синтез-газ, содержащий водород, монооксид углерода и азот, окислением углеводорода субстехиометрическим количеством воздуха, таким как при использовании установки для риформинга с частичным каталитическим окислением (СРОХ). В маломасштабных вариантах применения СРОХ предпочтительно проводят на катализаторе из драгоценного металла для обеспечения того, что образование газообразных продуктов будет преобладать над формированием углерода. Полученный синтез-газ может быть использован в качестве топлива для твердооксидного топливного элемента. Монооксид углерода в синтез-газе может быть либо преобразован взаимодействием с водяным паром в диоксид углерода и водород в условиях реакции сдвига (конверсии) водяного газа (WGS), либо может быть непосредственно электрохимически окислен до диоксида углерода на аноде топливного элемента. Все топливные элементы работают на водороде, и некоторые технологии топливных элементов, такие как твердооксидные топливные элементы (SOFC), могут также действовать с использованием монооксида углерода или смеси водорода с монооксидом углерода. Однако большинство топливных элементов более эффективно работает на водороде, нежели с использованием монооксида углерода. Известные твердооксидные топливные элементы и батареи топливных элементов обычно работают в диапазоне температур 700-1000 С. В этих условиях внутреннее потребление монооксида углерода может быть реализовано в результате как реакции конверсии водяного газа, катализируемой анодом топливного элемента, так и прямого электрохимического окисления. В этих технологиях внутренний риформинг внутри анода топливного элемента происходит при температурах, которые близки к температурам, типичным для топливного элемента, например, около 800 С, и часто анод топливного элемента представляет собой толстую пленку с толщиной свыше 100 микрон (100 мкм). В US 2002/0031695 в разделе [193] представлена ссылка на применение катализаторов риформинга метанола в поле течения анодного отсека для обеспечения внутреннего риформинга (т.е. в топливном элементе), и которая имеет отношение к топливным элементам с жидким/пастообразным электролитом,работающим при низкой температуре. Хотя это прямо не указано, это должно быть связано с подачей воды/водяного пара для реализации полноценного внутреннего риформинга, со всеми сопутствующими недостатками, такими как необходимость в подведении воды, насосе, системе контроля, и обусловленными этим расходами. Известный уровень техники также указывает предпочтение либо внутреннего, либо внешнего риформинга для систем на основе топливных элементов с использованием неочищенных водородных топлив. Внешний риформинг имеет место, когда топливо подвергают риформингу в синтез-газ снаружи батареи. Внутренний риформинг происходит, когда топливо подвергают риформингу внутри батареи, зачастую на аноде топливного элемента или вблизи такового. Каждому способу присущи свои преимущества и недостатки, с общим доводом в пользу внутреннего риформинга как более простого, составляющего систему с меньшим числом деталей и имеющего более высокую эффективность. Специалисты в этой области техники знают, что полный внутренний риформинг требует значительной энергии, расходуемой в процессе риформинга, и что имеет место компромисс между химической и тепловой энергией,чтобы соблюсти условия действия контрольной системы и обеспечить возможность эффективного применения внутреннего риформинга. Внутренний риформинг создает проблемы подбора материалов топливного элемента, компоновки и организации системы управления в режимах пуска, работы при динамической нагрузке и отключения. Прочие известные источники включают патенты US 5340664, GB 2405028, US 4374184, US 4454207 и US 2001/0010873. Применение устройства для внешнего риформинга с частичным каталитическим окислением(СРОХ) не свободно от своих ограничений. Полученный поток продуктов риформинга не только становится более разбавленным в присутствии азота, поступающего из воздуха, который подают в устройство для риформинга, но и всегда существует опасность осаждения углерода ниже по потоку относительно устройства для риформинга, когда температура падает ниже 700 С, например, внутри батареи среднетемпературных топливных элементов. Подобным образом применение реактора для конверсии водяного газа (WGS), как следует из его названия, требует подведения воды в реакционную зону, чтобы монооксид углерода и вода могли взаимодействовать со сдвигом равновесия реакции в сторону образования диоксида углерода и водорода. Настоящее изобретение относится к среднетемпературным твердооксидным топливным элементам(SOFC), в которые топливо, обогащенное монооксидом углерода, подают либо из подходящего непосредственного источника, например сети потребительского (бытового) газа, либо опосредованно из источника углеводородов, подвергаемых риформингу снаружи топливного элемента. Изобретение в одном из своих аспектов представляет способ снабжения топливом среднетемпературного твердооксидного топливного элемента, включающий стадии подведения топлива, обогащенного монооксидом углерода, в анодную область топливного элемента после того, как топливо вступит в контакт с катализатором реакции конверсии водяного газа в области анода таким образом, что реакция кон-1 016159 версии водяного газа протекает благодаря присутствию в топливе остаточной воды и/или водяного пара,образованного на аноде. Будет понятно, что способ действует без необходимости внешнего снабжения водой или водяным паром, поскольку большие количества воды не нужны, так как топливо представляет собой либо напрямую поставляемое топливо, обогащенное монооксидом углерода (например, бытовой газ), либо углеводородное топливо, которое уже было по существу подвергнуто преобразованию с использованием риформинга с частичным каталитическим окислением (СРОХ). Таким образом, имеет место некоторая конверсия водяного газа (WGS) внутри элемента, но это не согласуется с высокотемпературными твердооксидными топливными элементами (SOFC), где, как известно, полный риформинг внутри элемента проводят с необходимым внешним снабжением водой/водяным паром, как отмечено выше. Реакция конверсии водяного газа (WGS) по термическим параметрам непосредственно соответствует условиям реакции в топливном элементе в диапазоне 450-650 С, предпочтительно 500-650 С. Реакция конверсии водяного газа (WGS) в аноде или элементе как таковом (анод/электролит/катод) по существу не протекает. Таким образом, способ предпочтительно не включает стадию обеспечения отдельного подведения воды (в форме водяного пара или в ином виде) к катализатору конверсии водяного газа (WGS). Предпочтительно топливо, подводимое в анодную область топливного элемента, не обогащено водой. Предпочтительно топливо, подводимое в анодную область топливного элемента, содержит количество воды, недостаточное для полного каталитического превращения топлива в диоксид углерода и водород в результате действия катализатора конверсии водяного газа (WGS). Предпочтительно топливо, подаваемое в анодную область топливного элемента, имеет соотношение водяной пар : углерод 1. Более предпочтительно соотношение водяной пар : углерод составляет 0,75. Более предпочтительно соотношение водяной пар : углерод составляет 0,5. Более предпочтительно соотношение водяной пар : углерод составляет 0,25. Более предпочтительно соотношение водяной пар : углерод составляет 0,20. Более предпочтительно соотношение водяной пар : углерод составляет 0,15. Более предпочтительно соотношение водяной пар : углерод составляет 0,10. Более предпочтительно соотношение водяной пар : углерод составляет 0,05. Поэтому на самом деле способ обеспечивает возможность извлечения дополнительной энергии в топливном элементе с помощью реакции конверсии водяного газа (WGS) с использованием только присутствующих воды/водяного пара, т.е. остаточных в топливе или образуемых на аноде. В такой ситуации среднетемпературный топливный элемент может обеспечить эффективное использование химической энергии монооксида углерода в продукте риформинга, который в противном случае прошел бы через элемент практически непрореагировавшим. Во втором аспекте изобретение представляет батарею топливных элементов, включающую анод,катод, отделенный от анода, газонепроницаемый электролит между анодом и катодом, первое приспособление для подачи окислителя к катоду, второе приспособление для подачи топлива к аноду, где второе приспособление включает катализатор реакции конверсии водяного газа, размещенный вблизи анода,для катализирования реакции конверсии водяного газа между монооксидом углерода в топливе и водой/водяным паром, которые присутствуют как остаточные в топливе или образованные из реакции на аноде. Предпочтительно топливо подают к аноду через камеру, имеющую стенку с пористым участком, по соседству с которым снаружи камеры размещен анод, причем топливо проходит через пористый участок для контакта с анодом, и названный катализатор реакции конверсии водяного газа размещен в камере близко к названному пористому участку, но отдельно от него. Дополнительно или альтернативно катализатор может быть расположен на стенке в камере между порами пористого участка так, что поры открыты для прохождения топлива. Желательно, катализатор размещен на носителе, размещенном на стороне, противоположной пористому участку стенки, но на небольшом расстоянии от него. Носитель предпочтительно создается внутренней поверхностью второй стенки камеры, причем вторая стенка несет на себе катализатор реакции конверсии водяного газа и расположена параллельно пористому участку стенки, но на небольшом расстоянии от него. Носитель может быть сформирован вставкой, закрепленной на внутренней поверхности второй стенки камеры, причем вставка несет на себе катализатор реакции конверсии водяного газа и расположена параллельно пористому участку стенки, но на небольшом расстоянии от него. Изобретение в третьем аспекте представляет способ размещения катализатора конверсии водяного газа на металлической подложке для использования в топливном элементе, включающий нанесение катализатора на подложку методом струйной печати. Предпочтительно способ включает стадии:(i) предварительного окисления чистой сухой подложки обжигом в воздушной среде при температуре до 1000 С с получением на металле слоя с улучшенным сцеплением;(ii) осаждения предшественника катализатора с заданной конфигурацией размещения с использованием маски или по заданному маршруту осаждения;(iii) обжига слоя предшественника при температуре до 700 С;(iv) осаждения катализатора с использованием устройства для струйной печати и(v) обжига катализатора при температуре 300-600 С. Альтернативно, способ включает стадии:(i) предварительного окисления чистой сухой подложки обжигом в воздушной среде при температуре до 1000 С с получением на металле слоя с улучшенным сцеплением;(ii) осаждения предшественника катализатора с катализатором, осажденным на его поверхности, с заданной конфигурацией размещения с использованием маски или по заданному маршруту осаждения, с использованием устройства для струйной печати; и(iii) обжига слоя предшественника при температуре до 700 С. Будет очевидно, что согласно изобретению комбинирование обогащенного монооксидом углерода(СО) потока топлива с катализатором конверсии водяного газа (WGS), который размещен вблизи определенных областей анодной стороны топливного элемента в среднетемпературном твердооксидном топливном элементе, работающем при температурах 450-650 С, обеспечивает возможность высокоэффективной работы системы с коротким временем срабатывания, приводя к уменьшению сложности системы топливного элемента и снижению стоимости системы. Предпочтительно катализатор реакции конверсии водяного газа представляет собой катализатор парового риформинга на основе драгоценного металла, желательно катализатор, оптимизированный для низкой активности метанирования. Однако может быть использован ряд прочих каталитических структур, включая каталитическую структуру для высокотемпературной конверсии водяного газа (WGS) на основе драгоценного металла. Желательно катализатор размещают на пластинчатой или решетчатой детали батареи элементов, и он может быть помещен в элемент несколькими путями, в том числе мокрым осаждением (нанесением грунтовочного покрытия, трафаретной печатью, набрызгиванием в условиях струйной печати, нанесением в виде краски) поверх некоторой части или всей пластины (предпочтительно из нержавеющей стали),мокрым осаждением на оборотной стороне подложки из нержавеющей стали в топливном элементе, осаждением в поры пористой металлической подложки, нанесением покрытия на сетку из нержавеющей стали или керамический монолитный блок или керамические гранулы, который(е) затем вставляют в топливный канал анода. Несколько элементов согласно изобретению могут быть собраны в батарею топливных элементов. Вариант осуществления изобретения теперь будет описан только в качестве примера и с привлечением сопроводительных чертежей, на которых фиг. 1 а схематически представляет вид батареи твердооксидных топливных элементов (SOFC) и системы снабжения ее топливом и выведения отходящих газов согласно изобретению; фиг. 1b представляет подробный схематический вид батареи топливных элементов типа, используемого в изобретении, и как показано на фиг. 1 а; фиг. 2 представляет график, показывающий прогнозированный профиль концентраций вдоль поперечного сечения анодного отсека в среднетемпературных твердооксидных топливных элементах (ITSOFC) на металлической подложке, при работе с полной мощностью; фиг. 3 представляет схематический вид в разобранном состоянии части батареи твердооксидных топливных элементов на металлической подложке, включающей топливные элементы согласно изобретению; и фиг. 4 представляет таблицу типов топлива, которые могут быть подвергнуты риформингу с использованием частичного каталитического окисления (СРОХ), автотермического риформинга (ATR) и частичного каталитического окисления (СРОХ) с конверсией водяного газа (WGS.). Фиг. 1 а показывает структурную компоновку системы среднетемпературного твердооксидного топливного элемента с устройством для риформинга с частичным каталитическим окислением (СРОХ). В этой компоновке устройство для риформинга с частичным каталитическим окислением (СРОХ) является внешним для батареи и работает при температурах около 650-850 С с образованием потока топлива, обогащенного монооксидом углерода (СО). Ассортимент материалов и конструкцию трубопровода, передающего поток продуктов риформинга от устройства для риформинга к батарее топливных элементов,тщательно подбирают так, чтобы сократить или предотвратить осаждение углерода на примыкающих поверхностях при таких относительно низких температурах. Последнего можно в значительной степени избежать применением очень коротких трубных соединений и тщательным подбором материала труб,например, употреблением хромоникелевых (NiCr) сплавов, таких как 601, для подведения продуктов риформинга в батарею топливных элементов. Таким образом, в батарее элементов, действующей при температурах 450-650 С, имеет место тесное согласование термических характеристик между работой среднетемпературного твердооксидного топливного элемента при температуре 450-650 С и реакцией конверсии водяного газа (WGS) при температуре 400-600 С, которое является преимущественным для проектирования термических параметров батареи и условий эксплуатационного контроля. Это именно то тесное согласование рабочих температур,которое обеспечивает возможность применения конверсии водяного газа (WGS) для желательной работы топливного элемента в этом температурном диапазоне согласно изобретению, и делает его непригодным-3 016159 для технологий высокотемпературных твердооксидных топливных элементов (SOFC) или низкотемпературных топливных элементов. Как показано на фиг. 1 а, воздух подают в систему с использованием компрессора (1), с разделением воздушного потока на два потока, причем основной поток (1b) направляют в батарею (5) топливных элементов к катоду после предварительного нагревания до температуры около 450 С в агрегате (7) для предварительного нагревания воздуха путем теплообмена с потоком отходящего газа, затем дополнительно нагреваемого в результате охлаждения продуктов риформинга из устройства (3) для риформинга перед введением в батарею при температуре около 500 С, причем вспомогательный поток (1 а) подают в устройство (3) для риформинга с частичным каталитическим окислением (СРОХ). Предусмотрен ряд приспособлений (не показаны) для контроля массового расхода потока (1 а), чтобы поддерживать желательное соотношение кислород/углерод в устройстве для риформинга. В устройство для риформинга также подают углеводородное топливо (2), реагирующее с воздухом с образованием газообразных продуктов риформинга, главным образом состоящих из водорода, монооксида углерода и азота. Продукты риформинга затем пропускают через теплообменник, где они охлаждаются от температуры 700-800 С до температуры около 500 С потоком воздуха, подводимого к батарее. Охлажденные продукты риформинга затем подают в батарею (5) топливных элементов к анодной стороне. Для ясности на фиг. 1 а батарея изображена в виде только одного элемента, но на самом деле батарея составлена штабелем из элементов,два из которых показаны на фиг. 1b. Повторяющийся слой батареи состоит из межкомпонентных соединительных пластин (5 а) из нержавеющей стали, на анодной стороне одной из них или вблизи таковой осажден или размещен слой (5b) катализатора, который способствует потреблению монооксида углерода, катализируя реакцию конверсии водяного газа (WGS). Сам топливный элемент состоит из пористой подложки (5 с) из нержавеющей стали, на которую осажден анод (5d). Анод покрыт газонепроницаемым электролитом (5 е) , поверх которого осажден катод (5f) . Водород в продуктах риформинга потребляется в аноде топливного элемента в результате электрохимической реакции с кислородом, образуя водяной пар. Этот водяной пар вместе с любыми остаточными водой/водяным паром в топливе, затем образует реактант, с участием которого монооксид углерода в продуктах риформинга может быть преобразован в водород каталитической реакцией конверсии водяного газа (WGS). Истощенный поток топлива, состоящий главным образом из диоксида углерода, водяного пара и азота, с некоторым количеством остаточного водорода и, возможно, некоторым остаточным монооксидом углерода (СО), направляют в горелку (б) для сжигания остаточного газа. Здесь остаточное топливо расходуется в результате реакции с газом, выделяющимся с катода батареи. Горячий отходящий газ из горелки для сжигания остаточного газа затем направляют в теплообменник (7) для предварительного нагревания воздуха, где он охлаждается путем теплообмена с поступающим воздушным потоком (1b). Подаваемый на катод воздух (1b), нагретый с помощью устройства (7) для предварительного нагревания воздуха, и при охлаждении продуктов риформинга перед подачей в батарею при температуре около 500 С, поставляет окислитель для реакции в топливном элементе, но вместе с тем представляет собой средство, с помощью которого рассеивается существенная доля тепла, генерированной протекающей в элементе реакцией. Горячий газ, исходящий от катода в батарее, затем направляют в горелку для сжигания остаточного газа. Фиг. 1b показывает один полный элемент и часть еще одного из пары топливных элементов, формирующих батарею. Каждый элемент содержит межкомпонентную соединительную пластину 10 а,имеющую приподнятые края 11 а для формирования топливного канала 11b при перекрывании стальной подложкой, состоящей из пластины 10 с из нержавеющей стали, перфорированной в центральной области 10 д таковой. Стальная пластина 10 с приварена к приподнятым краям 11 а с формированием газонепроницаемых соединений в областях 12, и каждая стальная пластина отделена от межкомпонентной соединительной пластины следующего элемента прокладкой 13. Анод 10d осажден поверх верхней стороны перфорированной области каждой стальной пластины 10 с так, что анод через перфорации в стальных пластинах 10 с способен контактировать с топливом, подводимым в топливные каналы 11b. Верхнюю поверхность анода 10d полностью перекрывает газонепроницаемый электролит 10 е, и поверх него осажден катод 10f. Пространство над катодом между каждой стальной пластиной 10 с и расположенной над нею межкомпонентной соединительной пластиной 10 а, и ограниченное прокладками 13, создает канал 11 с для окислителя (воздуха) для катода. Вышеизложенное описывает известную компоновку батареи топливных элементов, но изобретение предусматривает катализатор 10b1 и 10b2 конверсии водяного газа (WGS), размещенный на соответствующей межкомпонентной соединительной пластине, отдаленной от соответственной стальной пластины 10 с, чтобы оставить зазор для топлива, контактирующего с анодом 10d. На фиг. 1b показаны два варианта расположения катализатора, позицией 10b1 показан катализатор, осажденный на вставке, закрепленной на стенке межкомпонентной соединительной пластины 11 а, параллельно пористой перфорированной стальной пластине 10 с, и позиция 10b2 изображает слой катализатора, осажденный на пористой перфорированной стальной пластине 10 с. В воздухе, подводимом к устройству для риформинга (если только он не подается из источника сухого воздуха), всегда будет присутствовать небольшая процентная доля водяных паров, и в общем преобразование углеводородных топлив также создает немного водяного пара. Таким образом, поток про-4 016159 дуктов риформинга уже содержит некоторое количество воды, приходя в контакт с катализатором конверсии водяного газа (WGS). Кроме того, в потоке продуктов риформинга присутствует водород с определенной концентрацией, который будет реагировать на аноде топливного элемента, образуя водяные пары, которые, в свою очередь, также поступают в зону реакции конверсии водяного газа (WGS). Поэтому при такой компоновке можно исключить необходимость применения либо внешней системы снабжения водой в какой-то форме, либо системы извлечения воды конденсацией отходящего газа топливного элемента и снабжения водой/водяным паром устройства для риформинга, либо рециркуляции отходящего анодного газа. В дополнение, для экономии расходов на катализатор конверсии водяного газа (WGS) есть только одно условие, состоящее в создании достаточной концентрации каталитического материала или площади поверхности катализатора конверсии водяного газа (WGS) для обеспечения конверсии монооксида углерода (СО) в диоксид углерода (CO2). Таким образом, для реализации этого конструктивного признака может быть привлечен процесс нанесения покрытия на вставку с катализатором конверсии водяного газа(WGS), или процесс осаждения катализатора конверсии водяного газа (WGS), основываясь на типе топлива и типе рабочей среды. Например, катализатор конверсии водяного газа (WGS) мог бы быть осажден на предшественник катализатора с использованием набрызгивания методом струйной печати, где плотность осаждаемых капелек в струе варьирует вдоль линии предполагаемого течения газообразного реактанта. Картина распределения плотности осаждения капелек может быть спроектирована с учетом концентрации монооксида углерода (СО), подвергаемого конверсии, водорода, достигающего остального анодного объема, температуры в окружении катализатора конверсии водяного газа (WGS) и количества воды, доступной для реакции конверсии водяного газа (WGS). Так, зона осаждения катализатора может быть расположена в области после поступления газообразного реактанта в содержащую анод зону, и осаждение может быть проведено в одной или более зонах, пока большая часть монооксида углерода(СО) не будет преобразована в водород (Н 2) и диоксид углерода (СО 2) так, что любая дальнейшая конверсия уже не влияла бы на эффективность работы системы, даже при дополнительных затратах на привлечение добавочного каталитического материала. Примерами получения покрытия из катализатора конверсии водяного газа на металлическом межкомпонентном соединении являются следующие: А) 1. Формуют лист металла (толщиной от 50 до 1000 мкм), такой как межкомпонентная соединительная пластина, из таких металлов, как ферритная нержавеющая сталь Crofer 22 APU, или 1.4509 по номенклатуре EU. 2. Очищают и высушивают сформованный лист или пластину. 3. Лист или пластину подвергают предварительному окислению путем обжига в воздушной среде при температуре до 1000 С для создания на стали слоя с улучшенным сцеплением. 4. Осаждают предшественник катализатора классическими способами, такими как нанесение грунтовочного покрытия или набрызгивание. Предшественник может представлять собой, например, оксид алюминия или оксид церия. Осаждение выполняют соответственно заданной конфигурации с использованием маски или по заданному маршруту осаждения. 5. Прокаливают слой предшественника, например, при температуре до 700 С. 6. Осаждают катализатор, такой как находящийся в водном растворе соли, в контролируемом режиме с использованием классических способов, таких как нанесение грунтовочного покрытия или набрызгивание или метод струйной печати. 7. Подвергают катализатор обжигу при температуре 300-600 С. В) Альтернативный способ включает осаждение предшественника в виде предварительно покрытого предшественника, т.е. уже имеющего металлический катализатор, осажденный на поверхности предшественника. В этом случае вышеуказанные стадии 6 и 7 не требуются. Предпочтительный способ включает нанесение покрытия на вставку, которая располагалась бы между межкомпонентным соединением и подложкой. Этот способ имеет несколько преимуществ перед покрытием межкомпонентного соединения в том, что он сокращает число термических обработок, каковым подвергаются слои батареи топливных элементов, и, поскольку он может быть исполнен независимо, также позволяет быстро разместить и соединить детали при сборке батареи топливных элементов. Такие покрытые вставки включают покрытые сетки, покрытые тканые материалы, формованные пластины или пористый керамический лист. Эти вставки также обеспечивают увеличенную площадь поверхности для нанесения каталитического покрытия, и если вставка покрыта погружением, меньшее количество отходов катализатора во время процесса приготовления, например, если вставка представляет собой грубую тканую сетку из проволоки с диаметром, к примеру, 5-30 мкм, с плотностью плетения, которая определяется предполагаемой каталитической активностью во время работы топливного элемента. Дополнительное преимущество этого способа состоит в том, что во время работы топливного элемента тепловое расширение покрытой сетки происходит независимо от теплового расширения топливного элемента,и тем самым повышается долговечность. Каталитическое покрытие на сетках и тканых материалах хорошо известно специалистам в этой области техники, и есть много компаний, которые предлагают свой опыт и продукцию в этой области.-5 016159 В случае употребления покрытой вставки слой батареи топливных элементов сооружают помещением покрытой вставки в места установки на межкомпонентной соединительной пластине, размещением топливного элемента на металлической подложке на межкомпонентной соединительной пластине и привариванием с использованием, например, лазерной сварки, непористой части топливного элемента к краям межкомпонентной соединительной пластины. Этим путем затем формируют основу слоя батареи топливных элементов. Чтобы изготовить батарею, на верхнюю часть топливного элемента помещают неэлектропроводную разделительную прокладку, такую как прокладка из материала Thermiculite 866 фирмы Flexitallic. Затем на верхнюю поверхность по меньшей мере одной части прокладки помещают катодный токосборник. Эта структура представляет собой повторный слой батареи топливных элементов на металлической подложке, и слой может быть размещен на верхней части еще одного слоя до достижения требуемой выходной мощности батареи или батарейного модуля. Чтобы сократить возможность осаждения углерода в области топливного элемента как результата реакции разложения монооксида углерода (СО) в топливном элементе, предпочтительно отделять точку начала реакции конверсии водяного газа (WGS), пока имеется в распоряжении водяной пар в потоке продуктов риформинга. Тем самым начало катализатора конверсии водяного газа (WGS) может быть в достаточной мере отделено от точки, в которой поток продуктов риформинга впервые сталкивается с анодом топливного элемента - например, начало катализатора конверсии водяного газа (WGS) и анод могут быть разделены промежутком в 0,2-2 см в топливном элементе, имеющем длину 12 см. Требуемое разделение можно рассчитать по скорости течения продуктов риформинга в анодной области и рядом с ней и также по времени реакции, которое затрачивается на то, чтобы водяной пар покинул анодную область и контактировал с областью, где размещена зона конверсии водяного газа (WGS). Осаждение углерода можно также подавить применением носителя из оксида церия для катализатора конверсии водяного газа(WGS) и также использованием катализатора на основе драгоценного металла в качестве катализатора конверсии водяного газа (WGS). Эффект внутренней конверсии водяного газа (WGS) иллюстрирован на фиг. 2, которая показывает прогнозированный профиль концентраций вдоль поперечного сечения анодного отсека в среднетемпературном твердооксидном топливном элементе (IT-SOFC) на металлической подложке при работе с полной мощностью. Следует отметить что фракция, выраженная в мольных долях, монооксида углерода двигается вдоль анодного отсека и заменяется эквивалентной долей диоксида углерода, что демонстрирует действие реакции конверсии водяного газа (WGS). Однако также заслуживает упоминания то, что мольная доля водорода никогда не превышает примерно 30%, что неизбежно ведет к уменьшенной удельной мощности топливного элемента, если сравнивать с питанием от парового риформинга, которое может содержать водород с мольной долей до 60%. Фиг. 3 показывает вид в разобранном состоянии части батареи твердооксидных топливных элементов на металлической подложке, с указанием областей, где могли бы быть размещены покрытая сетка или вставки для конверсии водяного газа (WGS). Фиг. 4 показывает таблицу типов топлива, которые могут быть подвергнуты риформингу с использованием частичного каталитического окисления (СРОХ), аутотермического риформинга (ATR) и частичного каталитического окисления (СРОХ) с конверсией водяного газа (WGS) Для систем, где низкая стоимость и простота являются более важными, нежели производительность, риформинг с частичным каталитическим окислением (СРОХ) предоставляет ряд преимуществ, в частности, когда это связано с батареей твердооксидных топливных элементов, которая может работать на потоке топлива, обогащенного монооксидом углерода. Батареи среднетемпературных твердооксидных топливных элементов (SOFC) имеют преимущества перед известными батареями высокотемпературных твердооксидных топливных элементов (SOFC), которые были описаны в других публикациях. Однако один недостаток заключается в том, что их более низкая рабочая температура снижает их способность эффективно действовать на монооксиде углерода как газообразном топливе, хотя, в отличие от низкотемпературных типов топливных элементов, они устойчивы к высоким концентрациям монооксида углерода (СО). Настоящее изобретение позволяет эффективно использовать батареи среднетемпературных твердооксидных топливных элементов (SOFC) с потоками обогащенного монооксидом углерода (СО) топлива,и таким образом использовать также устройства для риформинга с частичным каталитическим окислением (СРОХ), благодаря этому сочетая достоинства обеих технологий. Для применения в средне- и маломасштабном производстве энергии (50 кВт (электрических,kWe устройство для риформинга с частичным каталитическим окислением (СРОХ) представляет собой версию устройства для риформинга быстрого запуска, представляющую вариант простого недорогого риформинга топлива. Недостаток состоит в том, что вследствие потребления воздуха для риформинга в реакции с частичным каталитическим окислением (СРОХ) полученный поток топлива является более разбавленным, чем другие формы продуктов риформинга. Таким образом, при использовании конверсии водяного газа (WGS) для преобразования монооксида углерода (СО) в диоксид углерода (CO2) и водород этот эффект разбавления может быть частично компенсирован. Реакция конверсии водяного газа (WGS) протекает при температуре около 450-600 С, и преимущественно это близко к рабочей температуре-6 016159 среднетемпературного твердооксидного топливного элемента, и поскольку реакция конверсии водяного газа (WGS) является умеренно экзотермической, в ситуации с батареей среднетемпературных твердооксидных топливных элементов (IT-SOFC) она будет подвергаться очень малым температурным колебаниям, во время активной конверсии потока топлива из продуктов риформинга. В дополнение, катализатор конверсии водяного газа (WGS) может обеспечивать паровой риформинг любого проскока углеводорода,который мог бы произойти из основного устройства для риформинга, тем самым увеличивая срок службы системы топливных элементов. Использование в изобретении специализированного катализатора внутри топливного канала батареи среднетемпературных твердооксидных топливных элементов также применимо к внутреннему паровому риформингу углеводородов и улучшению утилизации монооксида углерода (СО) в потоке продуктов риформинга после парового риформинга и/или аутотермического риформинга. Применение устройства для риформинга с частичным каталитическим окислением (СРОХ) в системе топливных элементов может означать слегка увеличенную термическую эффективность, чем компоновка на основе устройства для парового риформинга, и это может быть преимущественным там, где акцент делается на уровень теплоотдачи, например, в случае применения в комбинированных системах тепло- и энергоснабжения (СНР). Эта компоновка применима к многим типам углеводородного топлива, например, бутан, пропан,сжиженный нефтяной газ (LPG), природный газ, бытовой газ, газифицированный уголь, метан, автогаз. Изобретение несомненно может быть использовано с прямой подачей обогащенного монооксидом углерода (СО) топлива, в этом случае исключается риформинг с частичным каталитическим окислением(СРОХ). Следует отметить, что изобретение непригодно для использования в топливных элементах, работающих на топливах, которые не содержат по меньшей мере небольшого количества воды или водородного компонента, так как существует необходимость в присутствии по меньшей мере некоторой доли водяных паров в потоке топлива для протекания реакции конверсии водяного газа (WGS). Это добавление воды можно было бы выполнять впрыскиванием водяного пара или пропусканием некоторого количества водорода в поток топлива, который мог бы даже поступать из контура рециркуляции отходящего газа от еще одной батареи твердооксидных топливных элементов. Процедура пуска: инициируют процесс частичного каталитического окисления (СРОХ); разогревают батарею топливных элементов с использованием блока горелок и потока горячих продуктов риформинга; анодная реакция в батарее топливных элементов будет активирована при температуре около 400500 С; этот момент батарея переходит в рабочий режим, и подача топлива в горелки может быть сокращена или отключена. Выключение: топливный элемент, устойчивый к циклическим изменениям окислительно-восстановительного потенциала,отключают подачу топлива на устройство для риформинга и тем самым батарею топливных элементов; пропускают поток воздуха через катодную сторону батареи топливных элементов, если требуется; топливный элемент, неустойчивый к циклическим изменениям окислительно-восстановительного потенциала,стравливают топливо в устройство для риформинга и тем самым в батарею топливных элементов; продолжают продувать воздух через катодную сторону; температура батареи будет падать, при температуре батареи топливных элементов около 300 С(ниже точки редокс-потенциала для катализатора в аноде) подачу топлива можно прекратить и оставить батарею остывать естественным образом; продувают воздух через катодную сторону, если требуется. Варианты применения для этого типа компоновки топливных элементов с устройством для риформинга включают употребление, где ключевым критерием является не общая эффективность системы, а, к примеру, способность работать без потребности в воде. Такие варианты применения могут включать системы дистанционного контроля или коммуникаций, или варианты применения в холодном климате,где есть опасность замерзания запасов воды. Другие варианты применения включают источники мощности для транспортных средств, например, для автомобилей или морского транспорта, где есть потребность в снабжении электрической энергией независимо от основного силового агрегата - в так называемой вспомогательной силовой установке (APU). Предпочтительная компоновка включает нанесение покрытия на вставку, которую можно было бы разместить между межкомпонентным соединением и подложкой. Это имеет ряд преимуществ перед нанесением покрытия на межкомпонентное соединение, которые состоят в том, что этим сокращается число тепловых обработок, испытываемых слоями батареи топливных элементов, и поскольку это может-7 016159 быть выполнено независимо, также позволяет быстро разместить и соединить детали при сборке батареи топливных элементов. Такие покрытые вставки включают покрытые сетки, покрытые тканые материалы,формованные пластины или пористый керамический лист. Эти вставки также обеспечивают увеличенную площадь поверхности для нанесения каталитического покрытия, и если вставка покрыта погружением, меньшее количество отходов катализатора во время процесса приготовления, например, если вставка представляет собой грубую тканую сетку из проволоки с диаметром, к примеру, 5-30 мкм, с плотностью плетения, которая определяется предполагаемой каталитической активностью во время работы топливного элемента. Дополнительное преимущество этого способа состоит в том, что во время работы топливного элемента тепловое расширение покрытой сетки происходит отдельно от теплового расширения топливного элемента, и тем самым повышается долговечность. Специалистам в этой области техники будет без труда понятно, что простые модификации способов и узлов согласно изобретению могут быть осуществлены без выхода за пределы области изобретения. Список позиций на чертежах 1 - компрессор; 1 а - вспомогательный поток; 1b - основной поток (подача входящего потока воздуха/катодного воздуха); 2 - углеводородное топливо; 3 - устройство для риформинга с частичным каталитическим окислением (СРОХ); 5 - батарея топливных элементов; 5 а - межкомпонентные соединительные пластины из нержавеющей стали; 5b - слой катализатора; 5 с - пористая подложка из нержавеющей стали; 5d - анод; 5 е - газонепроницаемый электролит; 5f -катод; 6 - горелка для сжигания остаточного газа; 7 - устройство для предварительного нагревания воздуха; 7 - теплообменник устройства для предварительного нагревания воздуха; 10 а - межкомпонентная соединительная пластина; 10b1 - катализатор конверсии водяного газа (WGS); 10b2 - катализатор конверсии водяного газа (WGS); 10 с - пластина из нержавеющей стали; 10d - анод; 10 е - газонепроницаемый электролит; 10f - катод; 10g - центральная область; 11 а - приподнятые края; 11b - топливный канал; 11 с - канал для окислителя (воздуха); 12 - области, в которых стальную пластину 10 с сваривают с приподнятыми краями 11 а с образованием газонепроницаемого соединения; 13 - прокладка. ФОРМУЛА ИЗОБРЕТЕНИЯ 1. Способ снабжения топливом среднетемпературного твердооксидного топливного элемента,включающий стадии подведения топлива, обогащенного монооксидом углерода, в анодную область (5d) топливного элемента, после того как топливо вступит в контакт с катализатором (10b1, 10b2) реакции конверсии водяного газа в области анода таким образом, что реакция конверсии водяного газа протекает благодаря присутствию в топливе остаточной воды и/или водяного пара, образованного на аноде, где топливо содержит количество воды, недостаточное для полного каталитического превращения топлива в диоксид углерода, и водород под действием катализатора конверсии водяного газа (WGS). 2. Способ по п.1, где указанный среднетемпературный твердооксидный топливный элемент является частью батареи среднетемпературных твердооксидных топливных элементов, включающей анодную область (5d), катод (5f), отделенный от анода, газонепроницаемый электролит (5 е) между анодом и катодом, первое приспособление (1b) для подачи окислителя к катоду, второе приспособление (2) для подачи топлива к аноду, где второе приспособление включает катализатор (10b1, 10b2) реакции конверсии водяного газа, размещенный вблизи анода, для реализации в условиях эксплуатации катализа реакции конверсии водяного газа между монооксидом углерода в топливе и водой/водяным паром, которые присутствуют как остаточные в топливе или образованные путем реакции на аноде. 3. Способ по п.2, по которому топливо подают к аноду через камеру (11b), имеющую стенку (10 с) с пористым участком, рядом с которым, снаружи камеры, размещен анод, причем топливо проходит через-8 016159 пористый участок для контактирования с анодом, и катализатор реакции конверсии водяного газа размещен в камере вблизи пористого участка, но отдельно от него. 4. Способ по п.2 или 3, по которому топливо подают к аноду через камеру (11b), имеющую стенку(10 с) с пористым участком, рядом с которым, снаружи камеры, размещен анод, причем топливо проходит через пористый участок для контактирования с анодом, где катализатор реакции конверсии водяного газа расположен на стенке в камере между порами пористого участка так, что поры открыты для прохождения топлива. 5. Способ по п.3, по которому катализатор реакции конверсии водяного газа размещают на носителе, размещенном на стороне, противоположной пористому участку стенки, но на небольшом расстоянии от него. 6. Способ по п.4, по которому носитель сформирован внутренней поверхностью второй стенки камеры, причем вторая стенка несет на себе катализатор реакции конверсии водяного газа и расположена параллельно пористому участку стенки, но на небольшом расстоянии от него. 7. Способ по п.4, по которому носитель сформирован вставкой, закрепленной на внутренней поверхности второй стенки камеры, причем вставка несет на себе катализатор реакции конверсии водяного газа и расположена параллельно пористому участку стенки, но на небольшом расстоянии от него.
МПК / Метки
МПК: B01J 37/02, H01M 4/86, C01B 3/12, H01M 8/12, C01B 3/02, H01M 8/02, C01B 3/16
Метки: топливных, усовершенствования, элементов, области
Код ссылки
<a href="https://eas.patents.su/11-16159-usovershenstvovaniya-v-oblasti-toplivnyh-elementov.html" rel="bookmark" title="База патентов Евразийского Союза">Усовершенствования в области топливных элементов</a>