Способ изготовления токопроводящего рельса, используемого при электролизе, и токопроводящий рельс
Формула / Реферат
1. Способ формирования поверхности токопроводящего рельса (1, 1'), используемого в электролизе, содержащего элемент (6а, 6b, 6с, 6') для передачи электрического тока, изготовленный из серебра или сплава на основе серебра, и имеющего контактную поверхность, обладающую хорошей электропроводностью, причем токопроводящий рельс выполнен с возможностью приведения в электрический контакт с несущим стержнем (13, 13'), используемым в электролитической ванне, через элемент (6а, 6b, 6с, 6') для передачи электрического тока, отличающийся тем, что верхняя поверхность токопроводящего рельса (1, 1') содержит посадочные канавки (4) между зубьями (16) или снабжена посадочными отверстиями (19') для установки несущих стержней (13, 13'), и тем, что включает стадии, в соответствии с которыми:
(а) в качестве материала токопроводящего рельса (1, 1') выбирают сплав на основе алюминия или алюминий;
(б) поверхность (2) указанного токопроводящего рельса (1, 1') с алюминиевой поверхностью нагревают, на нагретую поверхность наносят припой (7) на основе цинка, содержащий вещество, обладающее высоким сродством к кислороду при достижении температуры алюминиевой поверхности, превышающей температуру плавления припоя, припой (7) в расплавленном состоянии распределяют по области требуемого размера алюминиевой поверхности с образованием на этой поверхности припоя в жидком состоянии;
(в) слой оксида алюминия, образовавшийся между алюминием и расплавленным припоем, разрушают посредством механической обработки таким образом, что из слоя оксида алюминия высвобождается кислород, который взаимодействует с веществом в составе припоя (7), обладающим высоким сродством к кислороду, с образованием оксидного слоя на поверхности расплавленного припоя;
(г) на верхней поверхности припоя (7), нанесенного на указанную область поверхности, формируют элемент (6а, 6b, 6с, 6') для передачи электрического тока, изготовленный из серебра или сплава на основе серебра, припой отверждают и таким образом обеспечивают прикрепление элемента для передачи электрического тока в необходимом месте в отвержденном припое.
2. Способ по п.1, отличающийся тем, что используют припой (7) на основе цинка с содержанием цинка от 85 до 98 мас.% и содержанием алюминия от 1 до 10 мас.%.
3. Способ по п.1, отличающийся тем, что используют припой (7) на основе цинка с содержанием цинка от 80 до 98 мас.%, содержанием алюминия от 1 до 20 мас.% и содержанием меди от 0,1 до 6 мас.%.
4. Способ по любому из пп.1-3, отличающийся тем, что используют припой (7), в котором веществом, обладающим высоким сродством к кислороду, является магний.
5. Способ по любому из пп.1-4, отличающийся тем, что используемый припой (7) содержит марганец.
6. Способ по любому из пп.1-5, отличающийся тем, что на стадии (б) поверхность токопроводящего рельса (1, 1'), содержащего алюминиевую поверхность, нагревают до температуры 370-550°С.
7. Способ по п.1, отличающийся тем, что разрушение оксидного слоя, образующегося между алюминием и припоем (7), осуществляют посредством зачистки.
8. Способ по п.1, отличающийся тем, что на стадии (г) элемент (6а, 6b, 6с, 6') для передачи электрического тока помещают на поверхность, обработанную припоем (7), когда припой находится в расплавленном состоянии.
9. Способ по п.8, отличающийся тем, что в качестве элемента (6а, 6b, 6с, 6') для передачи электрического тока используют элемент из серебра или сплава на основе серебра толщиной от 0,4 до 2,2 мм.
10. Способ по любому из пп.1-7, отличающийся тем, что элемент для передачи электрического тока наносят на область поверхности, обработанную припоем (7), посредством термического напыления.
11. Токопроводящий рельс (1, 1'), используемый в электролизе и содержащий элемент (6а, 6b, 6с, 6') для передачи электрического тока, изготовленный из серебра или сплава на основе серебра, имеющий контактную поверхность, обладающую хорошей электропроводностью, выполненный с возможностью приведения в электрический контакт с несущим стержнем (13, 13'), используемым в электролитической ванне, через элемент для передачи электрического тока, отличающийся тем, что верхняя поверхность токопроводящего рельса (1, 1') содержит посадочные канавки (4) между зубьями (16) или снабжена посадочными отверстиями (19') для установки несущих стержней (13, 13'), и тем, что токопроводящий рельс (1, 1') изготовлен из алюминия или сплава на основе алюминия, а между элементом (6а, 6b, 6с, 6') для передачи электрического тока и поверхностью токопроводящего рельса (1, 1') находится припой на основе цинка, обеспечивающий прикрепление элемента (6а, 6b, 6с, 6') для передачи электрического тока к токопроводящему рельсу.
12. Токопроводящий рельс по п.11, отличающийся тем, что содержание цинка в припое составляет от 80 до 98 мас.%, а содержание алюминия - от 1 до 20 мас.%.
13. Токопроводящий рельс по п.12, отличающийся тем, что припой содержит магний.
14. Токопроводящий рельс по п.11, отличающийся тем, что элемент (6а, 6b, 6с, 6') для передачи электрического тока представляет собой элемент из серебра или сплава на основе серебра толщиной от 0,4 до 2,2 мм.
15. Токопроводящий рельс по п.11, отличающийся тем, что токопроводящий рельс (1, 1') содержит приемники (21') электрического тока, изготовленные из серебра или сплава на основе серебра и имеющие контактную поверхность, обладающую хорошей электропроводностью, для обеспечения электрического контакта с устройством, предназначенным для передачи электрического тока в токопроводящий рельс.
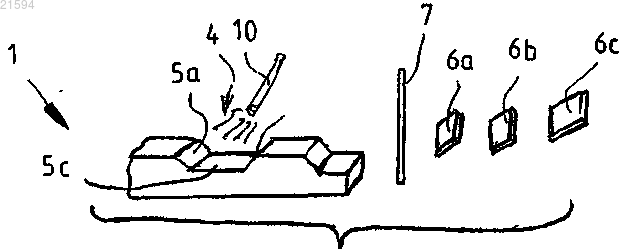
Текст
СПОСОБ ИЗГОТОВЛЕНИЯ ТОКОПРОВОДЯЩЕГО РЕЛЬСА, ИСПОЛЬЗУЕМОГО ПРИ ЭЛЕКТРОЛИЗЕ, И ТОКОПРОВОДЯЩИЙ РЕЛЬС Изобретение относится к способу получения алюминиевого токопроводящего рельса (1),используемого в электролизе и содержащего серебряный элемент (6 а, 6b, 6 с) для передачи электрического тока, имеющего контактную поверхность, обладающую хорошей электропроводностью. Для обеспечения экономичности, простоты и быстроты изготовления токопроводящего рельса (1) и элемента (6 а, 6b, 6 с) для передачи электрического тока: (а) в качестве материала токопроводящего рельса (1) выбирают сплав на основе алюминия; (б) поверхность указанного токопроводящего рельса (1) с алюминиевой поверхностью нагревают,на нагретую поверхность наносят припой на основе цинка, содержащий вещество, обладающее высоким сродством к кислороду при достижении температуры алюминиевой поверхности,превышающей температуру плавления припоя, припой в расплавленном состоянии распределяют по области требуемого размера алюминиевой поверхности с образованием на поверхности припоя в жидком состоянии; (в) слой оксида алюминия, образовавшийся между алюминием и расплавленным припоем, разрушают посредством механической обработки, что приводит к высвобождению кислорода из слоя оксида алюминия и взаимодействию кислорода с веществом в составе припоя, обладающим высоким сродством к кислороду, и образованию оксидного слоя на поверхности расплавленного припоя; (г) элемент (6 а, 6b или 6 с) для передачи электрического тока, изготовленный из серебра или сплава на основе серебра, формируют на верхней поверхности припоя, нанесенного на указанную поверхность, после чего припой отверждают и таким образом обеспечивают прикрепление элемента для передачи электрического тока с отвержденным припоем в необходимом месте. Изобретение относится также к токопроводящему рельсу (1). Область техники Настоящее изобретение относится к способу формирования поверхности токопроводящего рельса,используемого при электролизе, содержащего элемент для передачи электрического тока, изготовленный из серебра или сплава на основе серебра, и имеющего поверхность контакта, хорошо проводящую электрический ток, при этом подразумевается, что токопроводящий рельс приводится в электрический контакт с несущим стержнем, используемым в электролитической ванне, через элемент для передачи электрического тока. Настоящее изобретение также относится к токопроводящему рельсу, используемому при электролизе и содержащему элемент для передачи электрического тока, изготовленный из серебра или сплава на основе серебра, и имеющему поверхность контакта, хорошо проводящую электрический ток, при этом подразумевается, что токопроводящий рельс приводится в электрический контакт с несущим стержнем,используемым в электролитической ванне, через элемент для передачи электрического тока. Токопроводящие рельсы, называемые также погружными рельсами (шинами), используют в электролитических ваннах для подвода электрического тока к несущим стержням. Два токопроводящих рельса обычно поддерживают большое число несущих стержней, представляющих из себя компоненты, расположенные отдельно от токопроводящих рельсов. Электрический контакт между несущими стержнями и токопроводящим рельсом устанавливается при размещении несущих стержней на токопроводящих рельсах и удерживаемых на токопроводящих рельсах за счет собственного веса. В местах контакта необходима хорошая электропроводность. Кроме того, токопроводящие рельсы и несущие стержни должны хорошо проводить электрический ток во избежание избыточных затрат энергии. Токопроводящие рельсы обычно изготавливают из меди, поскольку медь обладает отличной электропроводностью. Поскольку токопроводящие рельсы могут достигать нескольких метров в длину, они обладают большой массой и, соответственно, очень высокой стоимостью. Известен способ повышения электропроводности в местах контакта, через которые токопроводящий рельс передает электрический ток на несущие стержни, основанный на использовании токопроводящих рельсов, содержащих в местах контакта слой серебра, легко припаиваемый к медному токопроводящему рельсу. В патентном документе FI 114926 предлагается способ, согласно которому приемник электрического тока, сделанный из серебра или сплава на его основе, формируют на конце несущего стержня посредством термического напыления покрытия. Приемник электрического тока образует металлургическую связь с алюминием. Для формирования покрытия методом термического напыления необходима очень высокая квалификация осуществляющего данную операцию персонала. Более того, достигаемые в конечном итоге электропроводность и надежность могут быть недостаточно высокими, поскольку на практике обеспечить хорошую металлургическую связь между алюминием и серебром с хорошей электропроводностью очень сложно. Перед нанесением покрытия покрываемые им материалы должны быть очищены от оксидных слоев с использованием таких способов, как, например, пескоструйная обработка или обработка проволочной щеткой, поскольку в противном случае не удается обеспечить хороший контакт/соединение с покрытием. Работа по очистке занимает много времени и не всегда приносит хорошие результаты. После нанесения покрытия для усиления соединения может проводиться кратковременная термообработка, которая, естественно, повышает трудоемкость данной технологической операции. В патентном документе FI 114926 указано также, что на алюминиевые стержни сначала может быть нанесено покрытие из меди, после чего на него наносят конечное покрытие из серебра или сплава на его основе. Указанная завершающая стадия является довольно сложной. В публикации WO 2006/117425 описан способ присоединения серебряного элемента к концу несущего алюминиевого стержня для формирования приемника электрического тока. Целью данного способа является обеспечение протекания эвтектической реакции между серебряным элементом и алюминием. Присоединить серебряный элемент к нижележащей поверхности алюминия затруднительно. Алюминиевый стержень необходимо постепенно нагреть, и после нагревания оксидный слой необходимо удалить с поверхности алюминия перед нанесением серебряного элемента. Удаление оксидного слоя, например посредством очистки, осуществляется с использованием таких способов, как, например, истирание. Для регулирования окислительных процессов рекомендуется проводить нагревание в восстановительной атмосфере, для создания которой необходимо использование специальных устройств, что осложняет процесс по сравнению с его осуществлением в атмосфере воздуха. Несущие стержни не обладают высокой термостойкостью, чем обусловлена необходимость осуществления нагревания с большой точностью и осторожностью. Кроме того, для обеспечения соединения серебряный элемент должен быть подвергнут давлению, прижимающему его к поверхности алюминия. Указанное давление рекомендуется прикладывать точечным образом с циклическим повторением. В целом описываемый процесс формирования контакта требует высокой точности исполнения и занимает длительное время. Краткое описание изобретения Задачей настоящего изобретения является обеспечение недорогого, легкого и быстрого способа, который позволяет изготовить токопроводящий стержень и предназначенный для него элемент для передачи электрического тока. Способ в соответствии с настоящим изобретением характеризуется следующими стадиями, в соответствии с которыми:(а) в качестве материала токопроводящего рельса выбирают сплав на основе алюминия или алюминий;(б) поверхность указанного токопроводящего рельса с алюминиевой поверхностью нагревают, после чего на нагретую поверхность наносят припой на основе цинка, содержащий вещество, обладающее высоким сродством к кислороду при достижении температуры алюминиевой поверхности, превышающей температуру плавления припоя, причем припой в расплавленном состоянии распределяют по области требуемого размера алюминиевой поверхности с образованием на этой поверхности припоя в жидком состоянии;(в) слой оксида алюминия, образовавшейся между алюминием и расплавленным припоем, разрушают посредством механической обработки таким образом, что из слоя оксида алюминия высвобождается кислород, который взаимодействует с веществом в составе припоя, обладающим высоким сродством к кислороду, с образованием оксидного слоя на поверхности расплавленного припоя;(г) на верхней поверхности припоя, нанесенного на указанную область поверхности, формируют элемент для передачи электрического тока, изготовленный из серебра или сплава на его основе, припой отверждают и таким образом обеспечивают прикрепление элемента для передачи электрического тока в необходимом месте в отвержденном припое. Вещество, обладающее высоким сродством к кислороду, т.е. способностью к взаимодействию с кислородом, должно иметь более высокое сродство к кислороду по сравнению с алюминием. Предпочтительный материал припоя содержит цинк в количестве от 85 до 98 мас.% и алюминий в количестве от 1 до 10 мас.%. Рекомендуемое содержание меди в припое составляет от 0,1 до 6 мас.%. Возможна замена меди на серебро. В качестве вещества с высоким сродством к кислороду предпочтительно использовать магний, поскольку при его взаимодействии с кислородом выделяется большое количество тепла, обеспечивающего расплавление алюминия, в результате чего между припоем и алюминием образуется плотная и прочная связь, обладающая хорошей электропроводностью. Образованный оксид магния всплывает на поверхность припоя. Предпочтительные варианты осуществления способа в соответствии с настоящим изобретением представлены в зависимых пунктах формулы изобретения 2-10. Наиболее существенным преимуществом изобретения является легкое и быстрое формирование контактной поверхности с хорошей электропроводностью и приемника электрического тока на токопроводящем рельсе, изготавливаемом из недорогого материала (алюминия или сплава на его основе). Предлагаемый способ является простым, легким в использовании и может применяться практически любым персоналом, не обладающим особыми навыками. Способ отличается также высокой экономичностью реализации. Токопроводящий рельс в соответствии с настоящим изобретением отличается тем, что его изготавливают из сплава на основе алюминия или алюминия, при этом между элементом для передачи электрического тока и токопроводящим рельсом формируют припой на основе цинка таким образом, чтобы обеспечить присоединение элемента для передачи электрического тока к токопроводящему рельсу. Предпочтительным является вплавление припоя в алюминий. В качестве элемента для передачи электрического тока предпочтительно использовать слой серебра или сплава на его основе толщиной от 0,4 до 2,2 мм. Предпочтительные варианты токопроводящего рельса в соответствии с настоящим изобретением приведены в зависимых пунктах формулы изобретения 12-15. Наиболее существенным преимуществом токопроводящего рельса в соответствии с настоящим изобретением является значительно более низкая стоимость его производства по сравнению со стоимостью производства традиционных токопроводящих рельсов. Кроме того, он отличается очень хорошими электропроводностью и долговечностью в соответствующей его эксплуатации окружающей среде. Элемент для передачи электрического тока и его контактные поверхности изнашиваются в процессе эксплуатации, однако элемент для передачи электрического тока может быть при необходимости легко заменен: старый элемент для передачи электрического тока отделяют от токопроводящего рельса и на его месте устанавливают новый с использованием предлагаемого в настоящем изобретении способа без необходимости расплавления самого токопроводящего рельса. Краткое описание графических материалов Далее настоящее изобретение изложено более подробно со ссылкой на пример и сопроводительные графические материалы, в частности на фиг. 1 представлен вид сверху электролитической ванны; на фиг. 2 представлено сечение фиг. 1 по линии II-II; на фиг. 3 представлено сечение фиг. 1 по линии III-III; на фиг. 4 представлен вид сверху структуры, изображенной на фиг. 3; на фиг. 5 представлен вид сбоку несущего стержня в держателе токопроводящего рельса на основании сочетания фиг. 3 и 4; на фиг. 6 представлено сечение фиг. 5 по линии VI-VI; на фиг. 7 и 8 представлены виды соответственно сбоку и сверху второго варианта токопроводящего рельса в соответствии с настоящим изобретением; на фиг. 9 представлен вид сбоку несущего стержня, используемого в сочетании с токопроводящим рельсом, представленным на фиг. 7 и 8; на фиг. 10 представлен вид снизу несущего стержня, представленного на фиг. 9; на фиг. 11 представлено сечение фиг. 9 по линии XI-XI; на фиг. 12 представлено более детальное изображение структуры токопроводящего рельса в соответствии с настоящим изобретением; на фиг. 13-15 представлен способ изготовления токопроводящего рельса в соответствии с фиг. 12 с элементом для передачи электрического тока; на фиг. 16 представлен альтернативный способ изготовления токопроводящего рельса с приемником электрического тока. Подробное описание изобретения На фиг. 1 представлен вид сверху цинковой электролитической ванны с двумя токопроводящими рельсами 1, расположенными на краях электролитической ванны 15. Сверху токопроводящих рельсов 1 находятся девять несущих стержней 13, расположенных на токопроводящих рельсах. Количество несущих стержней 13 может варьировать. К несущим стержням 13 присоединены подвешенные алюминиевые катоды 14, изображенные на фиг. 2, где представлено сечение фиг. 1 по линии II-II. На фиг. 3 и 4 представлены соответственно виды сбоку и сверху токопроводящего рельса 1. Токопроводящий рельс 1 изготовлен из алюминиевого сплава или алюминия. Рекомендуемая высота токопроводящего рельса составляет от 40 до 120 мм. Сверху токопроводящего рельса 1 расположены несущие стержни 13, которые на фиг. 3 изображены на заднем плане. Как показано на фигуре, на верхней поверхности токопроводящего рельса расположены зубья 16, при этом несущий стержень 13 установлен в углублении 4 между зубьями. Поскольку зубья 16 содержат наклонные поверхности, несущий стержень при помещении в углублении токопроводящего рельса 1 фиксируется в месте требуемого положения контакта. Высота зубьев 16 составляет, например, 20 мм. Длина горизонтального нижнего уровня углубления 4 составляет, например, 20 мм. Ширина токопроводящего рельса может составлять, например, 30 мм, а его длина - 4 м. Длина токопроводящего рельса может сильно варьировать в зависимости от типа электролитической ванны и находиться в пределах от 2 до 6 м. На фиг. 5 представлен вид сбоку несущего стержня 13, расположенного на токопроводящем рельсе 1 в соответствии с фиг. 3 и 4. Углубление 17, аналогичное углублению в токопроводящем рельсе, изображено на конце несущего стержня 13. Рекомендуемым материалом несущего стержня 13 является сплав на основе алюминия или алюминий, а углубление 17 покрывают покрытием из серебра, которое образует элемент для передачи электрического тока для токопроводящего рельса 1. Ширина несущего стержня 13 немного превышает ширину нижнего уровня углубления 4 в токопроводящем рельсе. Ширина несущего стержня 13 составляет, например, 16 мм при длине нижнего уровня углубления 4 токопроводящего рельса, составляющей 20 мм. При помещении несущего стержня 13 на токопроводящем рельсе 1 несущий стержень 13 располагается напротив краев нижнего уровня углубления 4 токопроводящего рельса вдоль двух линий, расположенных на наклонных поверхностях углубления 17. На фиг. 5 токопроводящий рельс изображен пунктирными линиями. На фиг. 6 представлено сечение фиг. 5 по линии VI-VI, при этом показана вторая наклонная поверхность 18. На фиг. 7 и 8 представлены соответственно виды сбоку и сверху второго варианта токопроводящего рельса 1'. Токопроводящий рельс 1' содержит ряд отверстий 19'. Диаметр отверстий 19' составляет, например, 40 мм. Рекомендуемая глубина отверстий 19' приблизительно равна их диаметру. На фиг. 9 и 10 представлены соответственно вид сбоку и снизу несущего стержня 13', расположенного на токопроводящем рельсе 1'. Полная структура/конструкция несущих стержней 13' отличается от структуры/конструкции несущих стержней, представленных на фиг. 5 и 6. Как показано на фиг. 9 и 10,на концах несущих стержней 13' находятся конические выступы 20' в форме зубьев. Диаметр зубьев на свободном конце зубьев 20' меньше диаметра отверстия 19' токопроводящего рельса 1'. Благодаря этому несущий стержень 13' устанавливается в месте требуемого контакта за счет собственного веса при помещении стержня в углубление токопроводящего рельса 1'. Конец зубьев 20' с большим диаметром по сво-3 021594 ему диаметру превышает диаметр отверстия 19'. При помещении несущего стержня 13' в отверстие 19' токопроводящего рельса 1' он располагается по линии напротив верхнего конца отверстия, образуя таким образом круговой контакт. На фиг. 11 представлено сечение фиг. 9 по линии XI-XI. Зубья 20' несущего стержня изготовлены из меди и присоединены к алюминиевой основе несущего стержня 13', например при помощи сварки трением. На фиг. 12 представлена часть представленного на фиг. 3 и 4 токопроводящего рельса 1, в которой находится область, через которую осуществляется передача электрического тока на несущий стержень. Место расположения указанной области, которое может быть названо элементом для передачи электрического тока, обозначено общим номером 2. На указанных фигурах показано, что на поверхность углубления 4 между зубьями 16 нанесены серебряные пластины 6 а, 6b, 6 с. Серебряные пластины 6 а, 6b, 6 с образуют элемент 2 для передачи электрического тока и обеспечивают возможность эффективного переноса электрического тока с токопроводящего рельса на несущий стержень, располагаемый на токопроводящем рельсе. На фиг. 13-15 изображен процесс изготовления токопроводящего стержня 1, представленного на фиг. 3, 4 и 6, или, точнее, формирования на нем элемента 2 для передачи электрического тока. На фиг. 13 представлен алюминиевый токопроводящий стержень 1, который может рассматриваться как заготовка ввиду отсутствия элемента для передачи электрического тока, т.е. серебряных пластин 6 а, 6b, 6 с, представленных на фиг. 12. Заготовка токопроводящего рельса 1 может представлять собой экструдированный алюминий с выполненным в нем некоторым числом углублений 4, на фиг. 13 представлено лишь одно из них, расположенное ближе всего к концу токопроводящего рельса. Элемент для передачи электрического тока формируют в углублении 4 путем присоединения небольших серебряных пластин 6 а, 6b, 6 с с высокой электропроводностью либо небольших пластин из сплава на основе серебра на обе наклонные поверхности 5 а, 5b углубления и на нижнюю поверхность 5 с углубления. Пластины 6 а,6b, 6 с могут также называться элементами или плитками. На фиг. 13 серебряные пластины 6 а, 6b, 6 с показаны отдельно от токопроводящего рельса 1, однако на фиг. 12 они показаны присоединенными к нему в соответствующем месте. Предпочтительная толщина пластин 6 а, 6b, 6 с составляет от 0,4 до 2,2 мм, при этом более предпочтительной является их толщина от 0,5 до 2 мм. На фиг. 13 под номером 7 изображен проволочный припой, применение которого рассмотрено ниже. Проволочный припой 7 представляет собой сплав на основе цинка с содержанием цинка от 85 до 89 мас.%, содержанием алюминия от 1 до 10 мас.% и содержанием меди от 0,1 до 6 мас.%. Припой содержит также небольшие количества марганца и магния. В качестве указанного припоя могут использоваться припои, производимые компаниями Techno Weld ltd., Aston Works, West End, Aston, Oxfordshire OX18 2NP, Великобритания. Припой припаивают в форме электродов (называемых электродами Techno Weld). Предполагается возможность замены содержащегося в электроде серебра на медь. Альтернативой продукции компании Techno Weld является продукция в форме нити, производимая и реализуемая компанией New Technology Products, 1330 Post Oak Blvd., Suite 1600 Houston, Texas 77056-3017, США, под торговым названием HTS-2000, инструкции по использованию которого приведены ниже. Содержание цинка в проволоке этого типа составляет около 80 мас.%, содержание алюминия - около 16 мас.%, а содержание меди - около 3 мас.%. Проволока содержит также небольшое количество магния, которое составляет,например, около 0,2 мас.%. Рекомендуемое содержание цинка предположительно находится в пределах от 80 до 98 мас.%, а содержание алюминия - от 1 до 20 мас.%. Пластины 6 а, 6b и 6 с присоединяют к поверхности углубления 4 путем нагревания токопроводящего рельса 1 (показанного на фиг. 13 в качестве заготовки) в месте углубления до температуры около 450 С (см. фиг. 13). Поскольку токопроводящий рельс изготовлен из алюминия, который легко взаимодействует с кислородом окружающего воздуха, на поверхности токопроводящего рельса, включая место углубления 4, находится оксид алюминия. Хорошо известно, что присоединение других металлов к поверхности оксида алюминия затруднительно. Тем не менее, в соответствии со способом, предлагаемым в настоящем изобретении, очистка токопроводящего рельса 1 от оксидов не обязательна. Температура нагрева не является критическим параметром и составляет предпочтительно от 370 до 550 С, однако может также находиться в пределах от 300 до 600 С. Если температура выходит за пределы от 260 до 620 С,можно ожидать, что желаемый результат не будет достигнут. Нагревание до очень высокой температуры связано также с риском расплавления алюминиевого рельса (температура плавления алюминия составляет 660 С). Предпочтительным является контроль температуры нагрева посредством измерения температуры поверхности углубления 4. Однако измерение температуры не является незаменимым или даже необходимым в случае, если известен характер поведения проволочного припоя 7 на поверхности токопроводящего рельса 1 при контакте проволочного припоя с поверхностью углубления. Предпочтительным способом нагревания является использование пламени газовой горелки (горения пропана, бутана или ацетилена), в случае которого сварочное сопло и насадка 10 находятся в движении для предотвращения избыточного локального перегрева. Возможно также использование нагрева посредством электрической индукции или электрического сопротивления. Однако недостатком индукционного нагрева является быстрое плавление алюминия, а нагрев с использованием электрического сопротивления является медленным. Тем не менее, индукционный и резистивный нагрев могут использоваться для базового нагрева. Задачей базового нагрева является обеспечение предварительного прогрева, который ускоряет изготовление токопроводящих рельсов в случае крупномасштабного производства за счет того, что нагрев токопроводящего рельса до рабочей температуры осуществляется с использованием электричества, а нагрев с использованием газовой горелки осуществляют в течение непродолжительного времени. После присоединения элемента для передачи электрического тока к очередному токопроводящему рельсу следующий токопроводящий рельс уже будет прогрет с использованием электричества и готов к присоединению элемента для передачи электрического тока. Проволочный припой 7 периодически прикладывают к нагретой поверхности для проверки возможности его присоединения к нижележащему материалу. Когда температура возрастает до уровня, достаточного для плавления проволочного припоя 7 при контакте с нижележащим материалом, припой наносят на поверхности 5 а, 5b и 5 с посредством перемещения проволочного припоя по указанным поверхностям и нанесения на них расплавленного припоя. Следует отметить, что проволочный припой 7 должен расплавляться за счет нагрева, вызываемого нижележащим материалом, не должен нагреваться со стороны сварочного сопла и насадки 10. Затем поверхность расплавленного металла зачищают щеткой из нержавеющей стали или латуни. Указанная обработка является очень быстрой и легкой операцией, обычно осуществляемой в течение 2 или 3 с, чего достаточно для разрушения слоя оксида алюминия под припоем с образованием алюминия и кислорода. Марганец, содержащийся в припое, может вносить вклад в разрушение слоя оксида алюминия. Освобождающийся при зачистке кислород реагирует с содержащимся в припое магнием, который характеризуется высокой способностью к взаимодействию с кислородом. Магний взаимодействует с кислородом более интенсивно, чем алюминий, благодаря чему можно сказать, что магний отбирает кислород у алюминия. Это имеет большое значение, поскольку позволяет удалить кислород с алюминия. При взаимодействии магния с кислородом происходит экзотермическая реакция с выделением теплоты. Вследствие выделения теплоты происходит локальное повышение температуры до уровня, превышающего температуру плавления алюминия, благодаря чему припой очень хорошо присоединяется к нижележащей поверхности алюминия. Оксид магния обладает очень низкой плотностью по сравнению с припоем, вследствие чего он всплывает на поверхность припоя, что обеспечивает образование очень хорошего соединения между припоем и нижележащим алюминием. Предпочтительное содержание магния в припое составляет по меньшей мере 0,01 мас.%, например находится в пределах от 0,05 до 0,3 мас.%. Вместо магния возможно использование других веществ, обладающих более высоким сродством к кислороду по сравнению с алюминием и образующих при взаимодействии с кислородом оксиды, имеющие более низкую плотность по сравнению с припоем и соответственно всплывающие на поверхность припоя. Вместо описанной выше зачистки могут использоваться и другие способы механической обработки, такие как выскабливание поверхности. Во время пребывания припоя в расплавленном состоянии серебряные пластины 6 а, 6b и 6 с помещают на него, вследствие чего серебряные пластины мгновенно прилипают к расплавленному припою и прочно соединяются с ним при отвердевании припоя, как показано на фиг. 12, где серебряные пластины изображены на своих местах. При отвердевании припоя образуется прочное соединение, хорошо проводящее электрический ток. Возможно предварительное нанесение припоя на поверхность серебряных пластин 6 а, 6b, 6 с перед их нанесением на припой, находящийся на поверхности алюминия. Если для получения элемента для передачи электрического тока используют пластины, которые вместо серебра изготовлены из сплава на основе серебра, предпочтительным является выбор сплава на основе серебра, содержащего небольшое количество меди. Содержание меди может составлять, например, 5 мас.% и варьировать в пределах от 1 до 10 мас.%. Благодаря присутствию меди механическая прочность пластин 6 а, 6b и 6 с превышает прочность пластин, изготавливаемых из чистого серебра. Однако присутствие серебра в пластинах 6 а, 6b и 6 с несколько снижает коррозионную стойкость и электропроводность поверхности контакта и элемента для передачи электрического тока. В токопроводящем рельсе, представленном на фиг. 3 и 4, может быть сформирована контактная поверхность из серебра или сплава на его основе с использованием способа, отличного от способа, представленного на фиг. 13, 14. Соответственно, использование элементов из серебра или сплава на его основе не является обязательным, и вместо этого возможно формирование элемента для передачи электрического тока термическим способом посредством напыления серебра или сплава на его основе на поверхность припоя после его отвердевания. Процесс напыления изображен на фиг. 16. В этом случае элемент для передачи электрического тока, полученный путем напыления без использования пластин из серебра или сплава на его основе, представляет собой верхний слой. Термическое напыление может осуществляться с использованием, например, процесса, основанного на сжигании газа. В процессе High Velocity Oxy-Fuel материал покрытия (серебро или слав на его основе) наносят в виде порошка с помощью газа-носителя и распылительного пистолета 9. В камере сгорания распылительного пистолета материал покрытия расплавляется и расплавленное покрытие направляют на поверхность покрываемого объекта. При использовании обычного пламенного распыления смесь горючего газа и кислорода сгорает и расплавляет материал покрытия, который в исходном состоянии может находиться в виде порошка или нитей. Расплавленный материал покрытия выдувают и направляют на покрываемый объект при помощи сжатого воздуха. Более подробное описание термического напыления не приводится, поскольку данный способ хорошо известен специалистам в соответствующей области. Недостаток термического напыления в сравнении с использованием готовых пластин из серебра или сплава на его основе заключается в том, что достижение хорошего результата с использованием данного процесса довольно затруднительно. Преимуществом термического напыления является возможность использования данного принципа для формирования покрытия на поверхности объектов любой геометрической формы. Следовательно, термическое распыление предпочтительно использовать для получения токопроводящего рельса 1', изображенного на фиг. 7 и 8, с элементом для передачи электрического тока 6'. Альтернативным вариантом является формирование элемента для передачи электрического тока с использованием принципа, описанного в отношении фиг. 1315, т.е. с использованием пластин из серебра или сплава на его основе, помещаемых в отверстия в заготовке алюминиевого токопроводящего рельса. В конструкции токопроводящего рельса 1 содержится также приемник электрического тока в месте подачи электрического тока на токопроводящий рельс. Приемник электрического тока может быть размещен, например, на втором конце 3 токопроводящего рельса 1. Токопроводящий рельс 1', представленный на фиг. 8, также содержит приемники 21' электрического тока. Приемники 21' электрического тока получают в соответствии с описанным выше способом. В отношении описанного выше изобретения и примеров его осуществления следует отметить, что настоящее изобретение может быть выполнено разнообразными способами в рамках прилагаемой формулы изобретения. Соответственно, элемент для передачи электрического тока на токопроводящем стержне 1, изображенном на фиг. 12, может состоять, например, из одного серебряного элемента 6 с, соответствующего по длине дну углубления 4 в случае, если ширина несущего стержня меньше по сравнению с длиной дна углубления 4. В этом случае серебряные элементы не располагают на диагонально ориентированных поверхностях. Если ширина несущего стержня больше по сравнению с длиной дна углубления, несущий стержень расположен на наклонных поверхностях углубления 4, на которых должны располагаться серебряные элементы 6 а, 6b. В последнем случае размещение серебряного элемента 6 с на дне углубления 4 не требуется. ФОРМУЛА ИЗОБРЕТЕНИЯ 1. Способ формирования поверхности токопроводящего рельса (1, 1'), используемого в электролизе,содержащего элемент (6 а, 6b, 6 с, 6') для передачи электрического тока, изготовленный из серебра или сплава на основе серебра, и имеющего контактную поверхность, обладающую хорошей электропроводностью, причем токопроводящий рельс выполнен с возможностью приведения в электрический контакт с несущим стержнем (13, 13'), используемым в электролитической ванне, через элемент (6 а, 6b, 6 с, 6') для передачи электрического тока, отличающийся тем, что верхняя поверхность токопроводящего рельса (1,1') содержит посадочные канавки (4) между зубьями (16) или снабжена посадочными отверстиями (19') для установки несущих стержней (13, 13'), и тем, что включает стадии, в соответствии с которыми:(а) в качестве материала токопроводящего рельса (1, 1') выбирают сплав на основе алюминия или алюминий;(б) поверхность (2) указанного токопроводящего рельса (1, 1') с алюминиевой поверхностью нагревают, на нагретую поверхность наносят припой (7) на основе цинка, содержащий вещество, обладающее высоким сродством к кислороду при достижении температуры алюминиевой поверхности, превышающей температуру плавления припоя, припой (7) в расплавленном состоянии распределяют по области требуемого размера алюминиевой поверхности с образованием на этой поверхности припоя в жидком состоянии;(в) слой оксида алюминия, образовавшийся между алюминием и расплавленным припоем, разрушают посредством механической обработки таким образом, что из слоя оксида алюминия высвобождается кислород, который взаимодействует с веществом в составе припоя (7), обладающим высоким сродством к кислороду, с образованием оксидного слоя на поверхности расплавленного припоя;(г) на верхней поверхности припоя (7), нанесенного на указанную область поверхности, формируют элемент (6 а, 6b, 6 с, 6') для передачи электрического тока, изготовленный из серебра или сплава на основе серебра, припой отверждают и таким образом обеспечивают прикрепление элемента для передачи электрического тока в необходимом месте в отвержденном припое. 2. Способ по п.1, отличающийся тем, что используют припой (7) на основе цинка с содержанием цинка от 85 до 98 мас.% и содержанием алюминия от 1 до 10 мас.%. 3. Способ по п.1, отличающийся тем, что используют припой (7) на основе цинка с содержанием цинка от 80 до 98 мас.%, содержанием алюминия от 1 до 20 мас.% и содержанием меди от 0,1 до 6 мас.%. 4. Способ по любому из пп.1-3, отличающийся тем, что используют припой (7), в котором вещест-6 021594 вом, обладающим высоким сродством к кислороду, является магний. 5. Способ по любому из пп.1-4, отличающийся тем, что используемый припой (7) содержит марганец. 6. Способ по любому из пп.1-5, отличающийся тем, что на стадии (б) поверхность токопроводящего рельса (1, 1'), содержащего алюминиевую поверхность, нагревают до температуры 370-550 С. 7. Способ по п.1, отличающийся тем, что разрушение оксидного слоя, образующегося между алюминием и припоем (7), осуществляют посредством зачистки. 8. Способ по п.1, отличающийся тем, что на стадии (г) элемент (6 а, 6b, 6 с, 6') для передачи электрического тока помещают на поверхность, обработанную припоем (7), когда припой находится в расплавленном состоянии. 9. Способ по п.8, отличающийся тем, что в качестве элемента (6 а, 6b, 6 с, 6') для передачи электрического тока используют элемент из серебра или сплава на основе серебра толщиной от 0,4 до 2,2 мм. 10. Способ по любому из пп.1-7, отличающийся тем, что элемент для передачи электрического тока наносят на область поверхности, обработанную припоем (7), посредством термического напыления. 11. Токопроводящий рельс (1, 1'), используемый в электролизе и содержащий элемент (6 а, 6b, 6 с, 6') для передачи электрического тока, изготовленный из серебра или сплава на основе серебра, имеющий контактную поверхность, обладающую хорошей электропроводностью, выполненный с возможностью приведения в электрический контакт с несущим стержнем (13, 13'), используемым в электролитической ванне, через элемент для передачи электрического тока, отличающийся тем, что верхняя поверхность токопроводящего рельса (1, 1') содержит посадочные канавки (4) между зубьями (16) или снабжена посадочными отверстиями (19') для установки несущих стержней (13, 13'), и тем, что токопроводящий рельс(1, 1') изготовлен из алюминия или сплава на основе алюминия, а между элементом (6 а, 6b, 6 с, 6') для передачи электрического тока и поверхностью токопроводящего рельса (1, 1') находится припой на основе цинка, обеспечивающий прикрепление элемента (6 а, 6b, 6 с, 6') для передачи электрического тока к токопроводящему рельсу. 12. Токопроводящий рельс по п.11, отличающийся тем, что содержание цинка в припое составляет от 80 до 98 мас.%, а содержание алюминия - от 1 до 20 мас.%. 13. Токопроводящий рельс по п.12, отличающийся тем, что припой содержит магний. 14. Токопроводящий рельс по п.11, отличающийся тем, что элемент (6 а, 6b, 6 с, 6') для передачи электрического тока представляет собой элемент из серебра или сплава на основе серебра толщиной от 0,4 до 2,2 мм. 15. Токопроводящий рельс по п.11, отличающийся тем, что токопроводящий рельс (1, 1') содержит приемники (21') электрического тока, изготовленные из серебра или сплава на основе серебра и имеющие контактную поверхность, обладающую хорошей электропроводностью, для обеспечения электрического контакта с устройством, предназначенным для передачи электрического тока в токопроводящий рельс.
МПК / Метки
МПК: B23K 1/00, B23K 1/19, C25C 7/02
Метки: электролизе, рельса, токопроводящего, рельс, изготовления, используемого, способ, токопроводящий
Код ссылки
<a href="https://eas.patents.su/10-21594-sposob-izgotovleniya-tokoprovodyashhego-relsa-ispolzuemogo-pri-elektrolize-i-tokoprovodyashhijj-rels.html" rel="bookmark" title="База патентов Евразийского Союза">Способ изготовления токопроводящего рельса, используемого при электролизе, и токопроводящий рельс</a>
Предыдущий патент: Детектор рентгеновского изображения, способ изготовления фоточувствительного элемента и способ изготовления детектора
Следующий патент: Пиримидиноны в качестве ингибиторов pi3k
Случайный патент: Вводимые перорально кортикостероидные композиции