Реактор для получения цианидов
Формула / Реферат
1. Реактор для превращения метана, аммиака, кислорода и гидроксидов щелочных или щелочно-земельных металлов в цианиды щелочных или щелочно-земельных металлов посредством двухстадийной реакции, где первую стадию осуществляют над катализатором, где смешиваются реакционные газы и протекает каталитическая реакция между аммиаком, метаном и кислородом с образованием цианистого водорода, оксида/диоксида углерода и воды, и на второй стадии газы охлаждают перед абсорбцией гидроксидом щелочного или щелочно-земельного металла для получения соответствующего цианида, причем реактор включает в себя отсек с впуском (I) для газа, выполненный в виде конуса (Н), содержащий распределительную пластину (G) с отверстиями, расположенную по центру под впуском (I), обеспечивающую равномерное распределение газа, входящего в реактор через впуск (I), и катализаторную сетку (С), помещенную ниже указанной распределительной пластины (G), где катализаторная сетка (С) представлена в форме катализаторной сетки (сеток) (С), закрепленной неподвижно грузами (В) для катализатора, причем грузы (В) предпочтительно выполнены в виде одного кольца, разделенного на части с помощью зажимов, предназначенных для предохранения его от падения, отличающийся тем, что содержит дополнительные распределительные пластины с отверстиями диаметром менее 20 мм с шагом больше 1 диаметра, при этом распределительные пластины размещены на расстоянии друг от друга в направлении потока газа, причем первая распределительная пластина (Gα) в основном выполняет функцию распределения газа, тогда как последняя распределительная пластина (Gw) установлена в качестве экрана для защиты от теплового излучения и в качестве распределительной пластины перед катализаторной сеткой (С), а также сильфонный компенсатор (А), проходящий от пересечения со стенкой/фланцем реактора до катализаторной сетки (С)/грузов (В), причем грузы (В) имеют высоту, достаточную для защиты сильфонного компенсатора (А).
2. Реактор по п.1, отличающийся тем, что количество распределительных пластин составляет 2-4, предпочтительно 2-3, наиболее предпочтительно 3.
3. Реактор по п.1 или 2, отличающийся тем, что отверстия в распределительных пластинах (G) выполнены с возможностью обеспечения скорости газов в пределах от 1 до 40 м/с, предпочтительно около 15 м/с.
4. Реактор по любому из пп.1-3, отличающийся тем, что первая распределительная пластина (Gα) рядом с впуском реактора имеет форму конуса с вершиной конуса, направленной к впуску реактора.
5. Реактор по любому из предшествующих пунктов, отличающийся тем, что первая распределительная пластина (Gα) имеет диаметр, близкий к или больший чем внутренний диаметр впускной трубы для реакционных газов.
6. Реактор по любому из предшествующих пунктов, отличающийся тем, что диаметр последовательно расположенных распределительных пластин увеличивается со второй по предпоследнюю распределительную пластину, перекрывая от 40 до 90% от общего внутреннего диаметра стенки реактора.
7. Реактор по любому из предшествующих пунктов, отличающийся тем, что последняя распределительная пластина (Gw) перекрывает все поперечное сечение реактора и предпочтительно является горизонтальной.
8. Реактор по любому из предшествующих пунктов, отличающийся тем, что катализаторная сетка содержит сплав каталитических благородных металлов, включая платину, иридий, родий, осмий, золото и серебро, а также их сплавы и/или оксидные катализаторы, такие как Fe2O3/Bi2O3/MoO3/P2O5/SiO2, причем наиболее предпочтительной является тканая или плетеная Pt/Rh проволочная сетка.
9. Реактор по п.8, отличающийся тем, что катализаторная сетка (С) выполнена из проволоки из 90/10 Pt/Rh диаметром 0,076 мм и с количеством ячеек 1024.
10. Реактор по любому из предшествующих пунктов, отличающийся тем, что катализаторная сетка поддерживается при помощи устройства, такого как поддерживающая сетка, содержащая материал, выдерживающий температуру приблизительно до 1500°С, такой как металлический или керамический сетчатый материал, поддерживаемый огнеупорным слоем, который может включать кольца Рашига, кольца Палля и т.п., зафиксированные при помощи пакета, соединенного с сильфонными компенсаторами.
11. Способ получения цианида щелочного или щелочно-земельного металла с использованием реактора по любому из пп.1-10, включающий стадии, на которых осуществляют реакцию между метаном, аммиаком и кислородом с образованием цианистого водорода, воды и монооксида/диоксида углерода, после чего продукты этой реакции взаимодействуют с гидроксидом щелочного или щелочно-земельного металла с получением цианида щелочного или щелочно-земельного металла.
12. Способ по п.11, где гидроксид щелочного металла представляет собой гидроксид натрия и где реакции следуют, но не ограничиваются ими, приведенным ниже реакциям
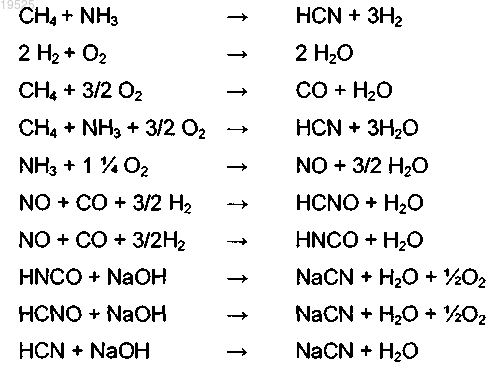
13. Способ по п.11 или 12, где давление в реакторе лежит в пределах от 1 до 30 бар.
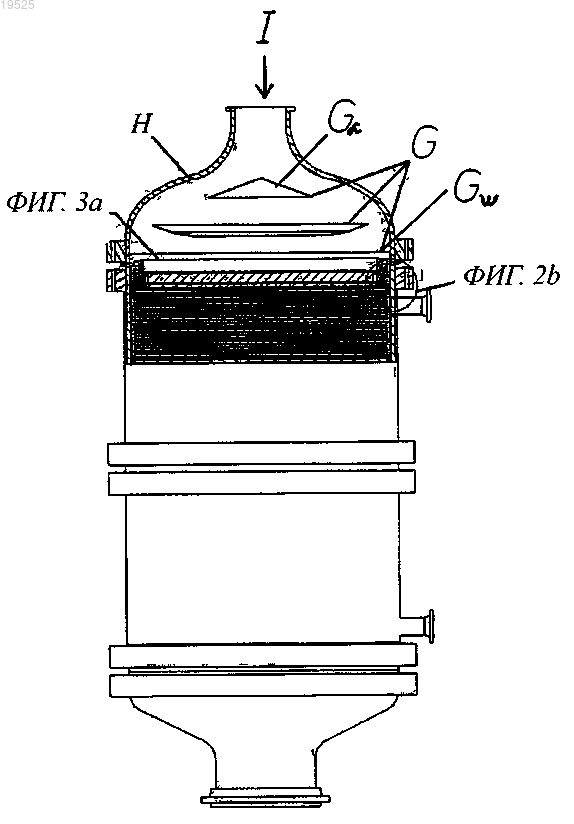
Текст
РЕАКТОР ДЛЯ ПОЛУЧЕНИЯ ЦИАНИДОВ Реактор для превращения метана, аммиака, кислорода и гидроксидов щелочных или щелочноземельных металлов в цианиды щелочных или щелочно-земельных металлов посредством двухстадийной реакции, включающий в себя первый отсек с устройством для впуска (I) газа, где первый отсек образован конусом (Н) с распределительными пластинами (G), обеспечивающими равномерное распределение газа над каталитическим материалом (С), где распределительные пластины (G) расположены между впуском (I) газа в реактор и имеют множество отверстий,при этом распределительные пластины размещены с интервалами относительно друг от друга в направлении потока газа; первая распределительная пластина (пластины) (G) в основном выполняет функцию распределения газа, тогда как последняя распределительная пластина (G) работает в качестве экрана для защиты от теплового излучения и в качестве распределительной пластины перед катализаторной сеткой (С), и где катализаторная сетка (С) представлена в форме катализаторной сетки (сеток) (С), зафиксированной при помощи грузов (В) для катализатора,и обеспечивается улучшенный способ синтеза HCN/NaCN при помощи парофазной реакции аммиака, метана и кислорода с последующей абсорбцией полученного газа гидроксидом натрия с образованием цианида натрия. Степень конверсии аммиака и метана в цианид натрия с помощью реактора согласно изобретению обычно составляет более 90%. Предшествующий уровень техники Настоящее изобретение относится к реактору для получения цианистого водорода и цианида натрия. Настоящий реактор использует способ, который является усовершенствованием известного способа Андруссова для получения цианистого водорода (HCN) и цианида натрия (NaCN). В частности, реактор согласно изобретению использует способ, который является более эффективным (далее называемый новым способом) по сравнению со способом Андруссова. Кроме того, изобретение в одном из вариантов относится к реактору для превращения метана, аммиака и кислорода, а также гидроксидов щелочных или щелочно-земельных металлов в цианиды щелочных или щелочно-земельных металлов посредством двухстадийных реакций: 1 - над катализатором, где смешиваются реакционные газы, протекает каталитическая реакция между аммиаком, метаном и кислородом, в ходе которой происходит образование цианистого водорода, оксида/диоксида углерода и воды; и 2 - газы охлаждают перед абсорбцией гидроксидом щелочного или щелочно-земельного металла для получения соответствующего цианида, при этом реактор включает в себя первый отсек с устройством для впуска газа, где первый отсек образован конусом с распределительными пластинами, обеспечивающими равномерное распределение газа над каталитическим материалом, причем распределительные пластины располагаются между впуском реактора для газов и пакетом катализатора в реакторе, расположенном ниже распределительных пластин, и имеют множество отверстий диаметром менее 20 мм с шагом больше 1 диаметра, при этом распределительные пластины размещены на расстоянии друг от друга в направлении потока газа; первая распределительная пластина (пластины) в основном выполняет функцию распределения газа, тогда как последняя распределительная пластина работает в качестве экрана для защиты от теплового излучения и в качестве распределительной пластины перед катализаторной сеткой, где катализаторная сетка закреплена неподвижно грузами для катализатора. Цианистый водород (HCN) представляет собой одно из самых маломасштабных промышленных химических веществ, которое, тем не менее, является достаточно важным для химической промышленности. В частности, HCN используют для получения цианурхлорида, метилметакрилата, адипонитрила(для найлона-6,6), цианида натрия, ферроцианидов и хелатирующих агентов. Цианид натрия в основном используют для кучного выщелачивания золота (Au) и серебра (Ag). В настоящее время практически все мировое производство HCN/NaCN осуществляется в соответствии с одним из трех способов:(1) способ Андруссова, при котором аммиак, метан и кислород реагируют в присутствии катализатора окисления с образованием HCN, СО, воды и Н 2;(2) "прямой синтез из аммиака и метана" или способ Дегусса (Degussa), при котором аммиак и метан реагируют в отсутствие воздуха в нагретых до высокой температуры трубках, содержащих платино/родиевый катализатор, с образованием HCN и водорода; и(3) способ Шавинигана (Shawinigan), при котором аммиак и пропан проходят между разнесенными электродами внутри псевдосжиженного слоя кокса. Помимо указанных выше способов получения HCN напрямую, его еще получают в качестве побочного продукта при производстве акрилонитрила по реакции пропилена и аммиака в присутствии катализатора окисления. Для получения NaCN в соответствии со всеми различными способами необходимо нейтрализоватьHCN гидроксидом натрия (NaOH). Хотя каждый из этих способов применяется в промышленном масштабе, несомненно, наиболее широко используемым является способ Андруссова. Согласно способу Андруссова парофазная смесь кислородсодержащего газа (обычно воздуха), аммиака (NH3) и метана контактирует с металлическим платиновым катализатором при температуре выше 1200C, причем часть метана сжигают для обеспечения тепла, необходимого для реакции метана с аммиаком, являющейся эндотермической. Полная реакция способа Андруссова имеет следующий вид: Полные реакции нового способа согласно настоящему изобретению, используемого в реакторе,кроме того, включают в себя В приведенных выше реакциях, используемых в реакторе, согласно настоящему изобретению в ка-1 019525 честве примера описана щелочная реакция гидроксида натрия с HCN, HNCO и HCNO, но с равным успехом может быть использован любой щелочной или щелочно-земельный металл, такой как калий, кальций, магний и т.д. Одна из особенностей способа Андруссова заключается в том, что в процессе использования катализатор становится менее активным. Хотя причина такой дезактивации в точности неизвестна, предполагается, что отчасти это обусловлено науглероживанием катализатора, что приводит к блокированию части активных зон на поверхности катализатора тонким слоем нагара. Эта дезактивация активных зон катализатора снижает конверсию аммиака и метана в среднем приблизительно до 65%. Вследствие высокой стоимости метана и аммиака важно, чтобы имеющиеся в наличии источники метана и аммиака использовались наиболее эффективным образом. Краткое описание изобретения Авторами изобретения было установлено, что в способе синтеза HCN и NaCN парофазной реакцией аммиака, метана и кислорода с последующей абсорбцией газообразного продукта гидроксидом натрия с получением цианида натрия выход HCN и NaCN может быть увеличен до получения степени конверсии аммиака и метана более 75%. Как правило, конверсия аммиака и метана в соответствии с изобретением составляет более 90%. Такое увеличение связано с усовершенствованным механическим устройством реакторной установки, как пояснено ниже. Обсуждение уровня техники Значительное количество работ посвящено поиску сырья для получения HCN. Например, патентный документ US 2006981 Andrussow (Андруссов) раскрывает замену части углеводородного сырья, необходимого для процесса, кислородсодержащими углеводородными соединениями, такими как метанол; в патентном документе Italian No. 845992, на имя Montecatini Edison, S.p.A., раскрыто дополнение метана ацетонитрилом. Каждый из этих дополнительных компонентов сырья посредством тех же ссылок также раскрыт с возможностью использования его в качестве первичного сырья для получения HCN. Помимо этого при различных способах получения HCN в реагенты добавляют инертные разбавители. Например, в патентном документе US 2688531 автор Eck упоминает о добавлении азота в реагенты при некаталитическом способе получения HCN по реакции СН 4 с NH3 при температуре выше 1425C. Аналогично, Bellringer et al. в патентных документах US 2746843 и US 3149914 раскрывают введение водяного пара или азота в реакцию метанола с NH3 и О 2 в присутствии сурьмяно-цинкового катализатора для получения HCN. Gross et al. в патентном документе US 3033658 отмечает, что при реакции СН 4 сNH3 и О 2 в присутствии катализатора, содержащего металлы платиновой группы, реагенты желательно разбавлять инертными газами, такими как N2, для снижения температуры реакции. С другой стороны,Sennewald et al. в патентном документе US 3254110 не объясняют причин выявленного ими преимущества разбавления реагентов водяным паром, СО 2 или N2 при получении HCN по реакции пропилена с NH3 и О 2 в присутствии молибденового или фосфорномолибденовокислого катализатора при температуре 300-405 С. Аналогичным образом, Brown et al. в патентном документе US 3577218 не конкретизируют своих предпочтений добавлению N2 в качестве разбавителя при способе получения HCN, согласно которому NH3 и СН 4 реагируют в отсутствие воздуха в присутствии катализатора платина-на-алюминии при температуре 1000C. Однако в патентном документе US 3667907 Rushmere добавляет водяной пар в реагенты с единственной целью улучшения конверсии NH3 по способу Андруссова. Аналогичный интерес представляет собой патентный документ DE 2421166, раскрывающий использование СО 2 в отсутствие реагентов для снижения углеродистых отложений в катализаторных трубках процесса прямого синтеза из аммиака и метана и, вследствие этого, для снижения падения давления во время проведения процесса. Подробное описание изобретения При получении HCN по способу Андруссова смесь аммиака, метана и кислородсодержащего газа подают в реактор, содержащий неподвижный слой платинового катализатора. Поскольку процесс является эндотермическим, для поддержания температуры реакции на уровне 1000-1200C следует обеспечивать достаточный избыток метана по сравнению со стехиометрическим количеством, необходимым для образования HCN. Реакционные газы преимущественно содержат HCN, N2, CO, H2, H2O, NH3 и небольшие количества СН 4, СО 2, а также, в случае, если в качестве кислородсодержащего газа использовался воздух, аргон. На многих промышленных производствах горячие реакционные газы используются для получения пара, и теплота сгорания возвращается иным образом. После охлаждения до температуры приблизительно 75C реакционные газы проходят через абсорбер, в котором происходит извлечение NH3 путем абсорбции водным раствором моноаммонийфосфата с образованием диаммонийфосфата. Диаммонийфосфат затем десорбируют паром для отделения аммиака, который рециклизуют в процесс, а моноаммонийфосфат, таким образом, регенерируют и рециклизуют в холодный абсорбер отходящих газов. Отходящий газ, не содержащий аммиака, из реактора поступает в холодный водный абсорбер, в котором из него извлекают HCN, а не содержащий HCN отходящий газ, имеющий теплотворную способность около 90 БТЕ (британских тепловых единиц (BTU - British Thermal Unit, используют в качестве топлива. Чистый HCN далее смешивают с гидроксидом натрия с получением цианида натрия. Способ Андруссова обычно проводят при температуре катализа в пределах приблизительно от 1000 до 1200C и предпочтительно в пределах от 1100 до 1200C. Соотношения реагентов СН 4, NH3 и О 2 в большинстве случаев будут близкими к стехиометрическим, насколько это возможно с точки зрения безопасности, при этом количества О 2 и СН 4 должны быть достаточными для обеспечения необходимой температуры реакции. Избыточные количества NH3 играют в основном роль разбавителя и проходят через реакционную систему непрореагировавшими. Из-за значительных затрат на обработку реакционной смеси, направленную на выделение целевой HCN и удаление таких непрореагировавших материалов,желательно, конечно, минимизировать утечку из системы непрореагировавших NH3 и СН 4. Эти проблемы уменьшаются в случае получения цианида натрия абсорбцией реакционных газов непосредственно цианидом натрия. Как было описано выше, при прямом получении NaCN (цианида натрия) обычно следуют способу Андруссова, начиная от поступления воздуха, аммиака и метана и заканчивая абсорбцией HCN (цианистоводородной кислоты) с помощью NaOH (с получением цианида натрия). Способ Андруссова также может использоваться косвенным образом, когда сначала выделяют HCN до того, как она смешана сNaOH и иногда высушена и брикетирована. Прямой путь, когда NaCN получают абсорбцией HCN с помощью NaOH, дает возможность использования нового и ранее неизвестного способа получения, а именно нового способа согласно настоящему изобретению, как показано на фиг. 1. Новый способ, используемый в реакторе, согласно настоящему изобретению подразделяется на две различающиеся технологические части. Часть, в которой метан окисляется до СО в ненасыщенных условиях, и часть, где получают NO. Для получения СО может использоваться любая горелка; он также может быть побочным продуктом силовых установок. Может использоваться любой источник СО. Получение NO может осуществляться путем окисления аммиака (NH3) в присутствии Pt/Rh катализатора (или других катализаторов, используемых для получения NO), как это имеет место на заводе по производству азотной кислоты, но может использоваться любой источник NO. После сгорания/окисления аммиака и метана реакционные газы смешивают и гасят водой путем прямого впрыскивания или путем охлаждения. Газ дополнительно охлаждают перед абсорбцией егоNaOH для получения NaCN. Протекаемые реакции могут быть описаны следующими уравнениями: Суммарная реакция При получении NaCN в соответствии со способом Андруссова аммиак и метан сжигают в воздухе с эффективностью конверсии в HCN 50-68%. Новый способ, используемый в реакторе согласно настоящему изобретению, будет давать степень конверсии 75-95%, как показано на фиг. 1. Фиг. 1 представляет собой схему технологического процесса получения NaCN в реакторе в соответствии с изобретением. Натрий на этой схеме обычно может быть заменен любым щелочным или щелочно-земельным металлом,например K, Ca или Mg. Технологические параметры процесса, изображенного на фиг. 1, следующие: давление - 1-15 бар; температура - 750-1300 С; концентрация аммиака - 10-15 об.%; катализатор окисления аммиака - Pt/Ru, Pt/Rh/Pd Fe2O3, Cr2O3; окисление метана - с использованием катализатора или без катализатора. В указанных выше реакциях согласно настоящему изобретению в качестве примера приведена щелочная реакция гидроксида натрия с HCN, HNCO и HCNO, однако с равным успехом вместо натрия может быть использован любой щелочной или щелочно-земельный металл, такой как калий, кальций, магний и т.д. Реакции, соответствующие приведенным выше уравнениям реакций согласно настоящему изобретению, могут проводиться в реакторной установке, предпочтительно сконструированной, как показано на прилагаемых чертежах 2 а, 2b и 3 а, 3b, 3 с, где: на фиг. 2 а изображены возможная конструкция и устройство реактора в соответствии с изобретением; на фиг. 2b в разрезе с фиг. 2 а, обозначенном на фиг. 2 а окружностью, показаны структура и устрой-3 019525 ство пакета катализатора, расположенного после впускного устройства и распределительных пластин реактора на фиг. 2 а; на фиг. 3 а-3 с показан пакет катализатора реактора с фиг. 2 а, на фиг. 3b выполнено сечение пакета катализатора с фиг. 3 а, а на фиг. 3 с представлено детальное изображение добавочной секции пакета катализатора с фиг. 3b соответственно. Другие преимущества нового способа, используемого в реакторе согласно настоящему изобретению, по сравнению со способом Андруссова заключаются в следующем. К достоинствам новой реакторной установки, изображенной на фиг. 2 а, b и 3 а-с, начиная от впускного устройства и заканчивая выпускным, относятся: 1) конус, допускающий более высокое давление при меньшей толщине стенок, обеспечивает меньший вес установленного металла. Предпочтительной формой является эллиптическая; 2) распределительные пластины дают равномерное распределение газа над катализаторными сетками и защищают входной конус реактора от высокого теплового излучения. Количество рядов распределительных пластин может составлять согласно предпочтительному варианту осуществления от 1 до 4,при этом оптимальным количеством является 3. Распределительные пластины размещают между устройством для впуска газа в реактор и катализатором. Пространство между пластинами и впускным устройством и катализатором составляет приблизительно 1/4 от общего расстояния, при этом самая нижняя пластина находится на 200-500 мм выше катализатора. Распределительные пластины будут иметь небольшие отверстия диаметром до 20 мм, например от 1 до 20 мм, с шагом больше 1 диаметра, при этом распределительные пластины располагаются на некотором расстоянии друг от друга в направлении потока газа. Количество отверстий будет отличаться для разных установок и будет определяться скоростью потока через отверстия. Скорость может изменяться от 1 до 40 м/с с предпочтительным значением, близким к 15 м/с. Первая пластина, ближайшая к впускному устройству реактора, может иметь форму конуса с вершиной конуса, направленной к впускному устройству реактора. В промежутках могут использоваться горизонтальные пластины либо пластины иной формы. Первая распределительная пластина имеет диаметр, близкий или больший чем внутренний диаметр впускной трубы. Вторая пластина будет иметь меньший диаметр, близкий к большему диаметру первой пластины, и самый большой диаметр, составляющий от 40 до 90% от общего диаметра внутренней части стенки реактора. Пластина может быть установлена горизонтально или вертикально и иметь любую форму, или может занимать промежуточное положение между этими двумя. Третья (последняя в рассматриваемом варианте осуществления) распределительная пластина будет перекрывать все поперечное сечение реактора и будет установлена горизонтально. Распределительные пластины образуют концентрические окружности по отношению ко второй и последующим распределительным пластинам, начиная от устройства для впуска газа, в форме кольца с наименьшим и наибольшим диаметром, где наименьший диаметр предпочтительно находится за пределами наибольшего диаметра предшествующего кольца/пластины. Согласно рассматриваемому варианту осуществления изобретения первые две распределительные пластины предназначены главным образом для распределения газа, тогда как последняя (третья) распределительная пластина действует одновременно как экран для защиты от теплового излучения и как распределительная пластина. Температура в газовом потоке перед последней пластиной близка к температуре входящего газа, в то время как последняя распределительная пластина будет обращена к горячим катализаторным сеткам и будет нагреваться за счет излучения. Эта пластина может иметь температуру на 100-300C выше, чем температура поступающего газа. Определение "близкий к" применительно к температуре означает, что температура может колебаться в пределах диапазона 50C, хотя также могут происходить и меньшие колебания, такие как 30, 20 и 10C; 3) конструкция пакета катализатора изготовлена из высоколегированного сплава металлов, такого как Inconell 600 или т.п., чтобы противостоять действию высокой температуры, при этом некоторые части могут иметь покрытие либо быть изготовлены с применением керамикоподобных материалов для удлинения срока службы. В связи с фиг. 3 отмечаем следующие детали: А) сильфонный компенсатор для высоких температур и изменений расхода. Сильфонный компенсатор может быть изготовлен как цельная деталь от пересечения со стенкой/фланцем реактора до носителя катализатора/катализаторной массы. Этот компенсатор будет принимать на себя напряжение от высокотемпературной нагрузки и потока газа. Это позволит предотвратить возникновение трещин в компенсаторе и избежать обхода реагирующими газами катализатора. Обход реагирующих газов будет вызывать реакции на более низких теплообменных устройствах реактора, что приведет к потере продукта и эрозионному изнашиванию оборудования;B) грузы катализатора для защиты сильфонного компенсатора и удержания катализаторных сеток(С) на месте. Грузы катализатора имеют по меньшей мере два основных назначения. Они заключаются в удерживании сетки на месте во время работы и в защите сильфонного компенсатора от высокотемпера-4 019525 турного излучения. Грузы могут быть сконструированы в виде одного кольца, разделенного на части с помощью зажимов, предназначенных для предохранения его от падения, и имеющего высоту, достаточную для защиты сильфонного компенсатора;C) катализаторные сетки, изготовленные из стандартного сплава или сплава нового типа, состоящие в основном из тканых или плетеных Pt/Rh проволок. Стандартный катализатор состоит из 90/10 Pt/Rh проволоки диаметром 0,076 мм с количеством ячеек 1024. Однако изобретение может использоваться для любого типа тканого или плетеного катализатора или для любой формы катализатора на носителе;D) носитель катализатора, допускающий возможность расширения и предусматривающий хорошую поддержку катализатора, что обеспечивает длительный срок службы катализатора и высокие степени конверсии. Носитель катализатора состоит из нескольких частей. Часть, близкая к катализатору, состоит из кольца, разделенного на несколько частей вдоль внутреннего диаметра пакета катализатора. Он присоединен к пакету таким образом, что он может следовать за расширением и сокращением, которые могут произойти во время работы установки такого типа. В связи с этим кольцо представляет собой гибкую поддерживающую сетку, которая будет создавать катализатору равную поддержку на протяжении всего цикла работы реактора. Поддерживающая сетка содержит материал, выдерживающий температуру приблизительно до 1500C, такой как металлический или керамический сетчатый материал. Ниже этого кольца и поддерживающей сетки расположен керамический слой (например, кольца Рашига или т.п.),который также поддерживает катализатор и в то же время действует как изолятор по отношению к более холодным поверхностям теплообменных устройств/бойлеров, находящихся ниже по потоку от катализатора. Носитель катализатора будет способствовать большей продолжительности срока службы реактора и получению более высоких скоростей конверсии, поскольку катализатор не будет разрушаться, поскольку имеется место для обхода катализатора реагирующими газами. Керамический слой поддерживается при помощи экрана и балок, которые могут охлаждаться с помощью теплообменных устройств ниже. Кроме того, на фиг. 2b, приведены следующие детали:E) охлаждаемый носитель пакета катализатора во избежание нарушения целостности и дробления носителя катализатора;F) охлаждение получаемых газов путем использования теплообменного устройства из высоколегированного сплава непосредственно под реактором. Кроме того, на фиг. 2 а указаны следующие детали:G) распределительные пластины (обозначение G относится к первой распределительной пластине,а G обозначают последнюю/крайнюю распределительную пластину перед катализаторной сеткой (С. Первая распределительная пластина (G) рядом с впускным устройством реактора предпочтительно имеет форму конуса с вершиной конуса, направленной к впускному устройству реактора, и, как альтернатива, предпочтительно имеет диаметр, близкий к или больший чем диаметр впускной трубы для реакционных газов; Н) конус реактора (предпочтительно, но необязательно, эллиптической формы, образующий распределительную камеру для газов, содержащую распределительные пластины G);I) впуск газа (обозначен как входящий аксиально по отношению к вершине конуса реактора, но он также может быть расположен неаксиально по отношению к конусу Н реактора, например, находиться в боковой стенке конуса реактора, в таком случае распределительные пластины будут расположены в направлении потока газа, входящего в конус реактора). К другим достоинствам изобретения относятся меньшее количество оборудования - меньшие капиталовложения; меньшие эксплуатационные затраты на 1 т полученного продукта за счет:c) большей продолжительности срока службы реактора;d) снижения средств на эксплуатационное обслуживание;e) уменьшения численности обслуживающего персонала;g) уменьшения выброса NH3, HCN, NO, CO, CO2 и т.д. Новизна нового способа согласно настоящему изобретению заключается в том, что HCN/NaCN получают при помощи реакции окисления аммиака и реакции окисления метана, проводимых по отдельности или одновременно. Давление в новом способе согласно настоящему изобретению не является критически важным,процесс можно проводить как при повышенном, так и при пониженном давлении, например, в пределах от 1 до 30 бар в соответствии с инженерной экономикой конкретной рассматриваемой установки. Большинство операций типа реакции Андруссова проводится при давлении немного выше атмосферного,например при 5-10 фунт/кв.дюйм (1,4-1,8 бар). На практике для нового способа в соответствии с изобретением может использоваться широкий ряд катализаторов окисления, например такие катализаторы, как указаны в патентном документе US 1934838. Безусловно, наиболее широко используемыми для этого процесса катализаторами являются катализаторы на основе благородных металлов, включая платину, иридий, родий, палладий, осмий, золото и серебро, а также их сплавы. Однако также используют и оксидные катализаторы, такие какFe2O3/Bi2O3/MoO3/P2O5/SiO2, раскрытые в патентном документе US 3516789 для Sennewald, смешанные оксиды сурьмы и олова, о которых упоминает Bellringer в патентном документе US 3149914, оксиды молибдена, такие как описаны в патентном документе US 2746843, а также редкоземельные металлы, тоже упоминавшиеся в рассмотренном выше патенте для Andrussow US Pat. No 1934838. В патентном документе US 3254110 Sennewald указывает на то, что комбинации оксидов переходных металлов являются хорошими катализаторами для получения нитрилов. Тем не менее, наиболее широко из них всех используются платина/родиевые катализаторы. Хотя, по-видимому, нет причин, почему бы не использовать изобретение для процесса, отличного от проводимого в неподвижном слое, тем не менее, способ согласно настоящему изобретению обычно проводят над неподвижным дырчатым слоем катализатора, такого как гранулы, сферы, стружка, сеть,щит или металлическая сетка. Катализатор в форме частиц обычно наносят на инертный носитель, имеющий средний размер в пределах от 0,16 до 1,0 см. Достаточно часто катализатор имеет вид нескольких слоев мелкоячеистой металлической сетки, через которую реагирующие газы проходят сверху вниз. Хотя это не является существенным для получения эффекта изобретения, экономика способа согласно изобретению улучшается в случае максимальной регенерации тепла для реакции, например, за счет использования разновидностей реакторов, описанных и заявленных в патентных документах US 2782107 для Inman и US 3215495 для Jenks. Ниже приведены два примера, относящиеся к работе реактора для получения цианида. В первом примере использованы традиционные реактор и катализатор, а во втором использован реактор согласно изобретению. Описание примеров осуществления изобретения Пример 1. Традиционный реактор не имеет распределения или защиты от излучения, а носитель катализатора является простым, не обладающим возможностью расширения. Кроме того, тепло снимают простым впрыскиванием воды в горячие реакционные газы. Действие катализатора рассчитано на 12 об.% аммиака, 13 об.% природного газа, 75 об.% воздуха, давление составляет 4 бар, удельная нагрузка катализатора- 25 тН/м 2 д, 16 катализаторных сеток состава 90/10 Pt/Rh с 1024 ячейками и диаметром проволоки 0,076 мм. Измеренная температура в катализаторе составила 1050C. Время работы реактора составило 70 дней с эффективностью 50-55% (степень конверсии аммиака вHCN). Операцию пришлось прекратить из-за возникновения трещин в катализаторе. Пример 2. Реактор сконструирован в соответствии с изобретением с распределительными и защищающими от излучения пластинами в верхней части реактора. Носитель катализатора был таким, как описан в изобретении. Реактор работал в тех же условиях, что описаны в примере 1. Время работы реактора составило 100 дней с эффективностью 70-75%, при этом отсутствовало растрескивание катализатора благодаря улучшенной механической конструкции носителя катализатора. Распределение и защита от излучения способствовали меньшим тепловым потерям и улучшенному распределению над всей поверхностью катализатора, создавая лучшие реакционные условия для реагентов. Улучшение работы реактора ясно показано в примерах, описанных выше, при этом эксплуатационные затраты сберегаются как за счет снижения расходов на катализатор, так и за счет использования меньшего количества сырьевых материалов. Кроме того, существенно снижается выброс в атмосферу газов, вызывающих парниковый эффект. Ссылки на предшествующий уровень техники. Патентные документы СШАMellor, Treatise on Inorganic and Theoretical Chemistry (Курс неорганической и теоретической химии), vol. 5, Longmans, Green, N. Y., (1924), p. 817, 818. ФОРМУЛА ИЗОБРЕТЕНИЯ 1. Реактор для превращения метана, аммиака, кислорода и гидроксидов щелочных или щелочноземельных металлов в цианиды щелочных или щелочно-земельных металлов посредством двухстадийной реакции, где первую стадию осуществляют над катализатором, где смешиваются реакционные газы и протекает каталитическая реакция между аммиаком, метаном и кислородом с образованием цианистого водорода, оксида/диоксида углерода и воды, и на второй стадии газы охлаждают перед абсорбцией гидроксидом щелочного или щелочно-земельного металла для получения соответствующего цианида, причем реактор включает в себя отсек с впуском (I) для газа, выполненный в виде конуса (Н), содержащий распределительную пластину (G) с отверстиями, расположенную по центру под впуском (I), обеспечивающую равномерное распределение газа, входящего в реактор через впуск (I), и катализаторную сетку(С), помещенную ниже указанной распределительной пластины (G), где катализаторная сетка (С) представлена в форме катализаторной сетки (сеток) (С), закрепленной неподвижно грузами (В) для катализатора, причем грузы (В) предпочтительно выполнены в виде одного кольца, разделенного на части с помощью зажимов, предназначенных для предохранения его от падения, отличающийся тем, что содержит дополнительные распределительные пластины с отверстиями диаметром менее 20 мм с шагом больше 1 диаметра, при этом распределительные пластины размещены на расстоянии друг от друга в направлении потока газа, причем первая распределительная пластина (G) в основном выполняет функцию распределения газа, тогда как последняя распределительная пластина (G) установлена в качестве экрана для защиты от теплового излучения и в качестве распределительной пластины перед катализаторной сеткой(С), а также сильфонный компенсатор (А), проходящий от пересечения со стенкой/фланцем реактора до катализаторной сетки (С)/грузов (В), причем грузы (В) имеют высоту, достаточную для защиты сильфонного компенсатора (А). 2. Реактор по п.1, отличающийся тем, что количество распределительных пластин составляет 2-4,предпочтительно 2-3, наиболее предпочтительно 3. 3. Реактор по п.1 или 2, отличающийся тем, что отверстия в распределительных пластинах (G) выполнены с возможностью обеспечения скорости газов в пределах от 1 до 40 м/с, предпочтительно около 15 м/с. 4. Реактор по любому из пп.1-3, отличающийся тем, что первая распределительная пластина (G) рядом с впуском реактора имеет форму конуса с вершиной конуса, направленной к впуску реактора. 5. Реактор по любому из предшествующих пунктов, отличающийся тем, что первая распределительная пластина (G) имеет диаметр, близкий к или больший чем внутренний диаметр впускной трубы для реакционных газов. 6. Реактор по любому из предшествующих пунктов, отличающийся тем, что диаметр последовательно расположенных распределительных пластин увеличивается со второй по предпоследнюю распределительную пластину, перекрывая от 40 до 90% от общего внутреннего диаметра стенки реактора. 7. Реактор по любому из предшествующих пунктов, отличающийся тем, что последняя распределительная пластина (G) перекрывает все поперечное сечение реактора и предпочтительно является горизонтальной. 8. Реактор по любому из предшествующих пунктов, отличающийся тем, что катализаторная сетка содержит сплав каталитических благородных металлов, включая платину, иридий, родий, осмий, золото и серебро, а также их сплавы и/или оксидные катализаторы, такие как Fe2O3/Bi2O3/MoO3/P2O5/SiO2, причем наиболее предпочтительной является тканая или плетеная Pt/Rh проволочная сетка. 9. Реактор по п.8, отличающийся тем, что катализаторная сетка (С) выполнена из проволоки из 90/10 Pt/Rh диаметром 0,076 мм и с количеством ячеек 1024. 10. Реактор по любому из предшествующих пунктов, отличающийся тем, что катализаторная сетка поддерживается при помощи устройства, такого как поддерживающая сетка, содержащая материал, выдерживающий температуру приблизительно до 1500 С, такой как металлический или керамический сетчатый материал, поддерживаемый огнеупорным слоем, который может включать кольца Рашига, кольца Палля и т.п., зафиксированные при помощи пакета, соединенного с сильфонными компенсаторами. 11. Способ получения цианида щелочного или щелочно-земельного металла с использованием реактора по любому из пп.1-10, включающий стадии, на которых осуществляют реакцию между метаном,аммиаком и кислородом с образованием цианистого водорода, воды и монооксида/диоксида углерода,после чего продукты этой реакции взаимодействуют с гидроксидом щелочного или щелочно-земельного металла с получением цианида щелочного или щелочно-земельного металла. 12. Способ по п.11, где гидроксид щелочного металла представляет собой гидроксид натрия и где реакции следуют, но не ограничиваются ими, приведенным ниже реакциям
МПК / Метки
МПК: B01J 12/00, B01J 8/02, C01C 3/02
Метки: получения, реактор, цианидов
Код ссылки
<a href="https://eas.patents.su/10-19525-reaktor-dlya-polucheniya-cianidov.html" rel="bookmark" title="База патентов Евразийского Союза">Реактор для получения цианидов</a>
Предыдущий патент: Соединения и композиции как ингибиторы киназы с-kit и pdgfr
Следующий патент: Пневматический воздухораспределитель для регулируемой подачи сжатого воздуха в тормозной цилиндр
Случайный патент: Аналоги глюкагона