Теплоизоляционный материал на основе минеральной ваты
Номер патента: 24394
Опубликовано: 30.09.2016
Авторы: Дус Жером, Голетто Валери, Жилль Жером, Летурми Арно
Формула / Реферат
1. Теплоизоляционный материал на основе минеральной ваты, отличающийся тем, что волокна имеют показатель микронейр ниже 10 л/мин, предпочтительно ниже 7 л/мин, в частности составляющий от 3 до 6 л/мин, причем материал содержит элементы, отражающие и/или поглощающие инфракрасное излучение, причем материал имеет коэффициент теплопроводности ниже 30 мВт/мК, при этом волокна в мате расположены плоско и, по существу, по меньшей мере 75% волокон параллельны длинным сторонам мата.
2. Теплоизоляционный материал по п.1, отличающийся тем, что он имеет плотность не более 35 кг/м3, предпочтительно от 20 до 30 кг/м3.
3. Теплоизоляционный материал по любому из предыдущих пунктов, отличающийся тем, что элементами, отражающими и/или поглощающими инфракрасное излучение, являются металлические частицы типа алюминия.
4. Теплоизоляционный материал по любому из предыдущих пунктов, отличающийся тем, что элементы, отражающие и/или поглощающие инфракрасное излучение, находятся в содержании, составляющем от 1 до 10 вес.% материала, предпочтительно от 2 до 6%.
5. Теплоизоляционный материал по любому из предыдущих пунктов, отличающийся тем, что отражающие и/или поглощающие инфракрасное излучение элементы имеют размер от 5 до 25 мкм.
6. Теплоизоляционный материал по любому из предыдущих пунктов, отличающийся тем, что он имеет толщину больше или равную 30 мм, в частности от 40 до 150 мм.
7. Теплоизоляционный материал по любому из предыдущих пунктов, отличающийся тем, что он выполнен с возможностью скатывания в рулон.
8. Теплоизоляционный материал по любому из предыдущих пунктов, отличающийся тем, что он предназначен для встраивания в систему звукоизоляции.
9. Теплоизоляционный материал по любому из предыдущих пунктов, отличающийся тем, что он основан на стекловолокнах и имеет долю неволокнистой фракции ниже 1%.
10. Теплоизоляционный материал по любому из предыдущих пунктов, отличающийся тем, что он основан на кальций-боросиликатном стекле с долей бора ниже 10 вес.% от состава стекла, предпочтительно от 4 до 7%.
11. Теплоизоляционный материал по любому из предыдущих пунктов, отличающийся тем, что он получен способом прядения путем внутреннего центрифугирования и путем осаждения на волокна отражающих и/или поглощающих инфракрасное излучение элементов.
12. Материал по любому из предыдущих пунктов, отличающийся тем, что он предназначен для обшивки стен и/или кровли здания.
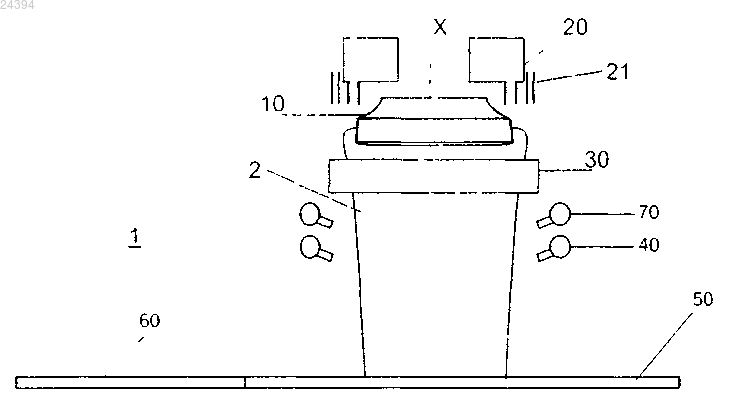
Текст
ТЕПЛОИЗОЛЯЦИОННЫЙ МАТЕРИАЛ НА ОСНОВЕ МИНЕРАЛЬНОЙ ВАТЫ Теплоизоляционный материал на основе минеральной ваты, отличающийся тем, что волокна имеют показатель микронейр ниже 10 л/мин, предпочтительно ниже 7 л/мин, в частности составляющий от 3 до 6 л/мин, тем, что материал содержит элементы, отражающие или поглощающие инфракрасное излучение, и тем, что материал имеет коэффициент теплопроводности ниже 30 мВт/мК. Изобретение относится к материалам на основе минеральной ваты, такой как стекловата, предназначенным, в частности, для введения в состав теплоизоляционных и, возможно, звукоизоляционных материалов, в частности для обшивки стен и/или кровли. На рынке изоляционных материалов поставщикам всегда хотелось бы предлагать материалы, все более и более эффективные в отношении теплоизоляции. О термических характеристиках материала обычно можно судить, зная коэффициент теплопроводности . Напомним, что коэффициент теплопроводности А материала есть способность материала пропускать тепловой поток; он выражается в Вт/мК. Чем ниже эта теплопроводность, тем более изолирующим является материал, и, следовательно, тем лучше теплоизоляция. Сегодня на рынке материалы на основе минеральных волокон, представляющие собой минеральную шерсть или стекловату, имеют теплопроводность от 0,040 до 0,035 Вт/мК, лучше даже 0,032 Вт/мК. Если не указано иное, коэффициент теплопроводности измерен обычным методом при 10 С, согласно стандарту ISO 8301. Другие решения позволяют получить коэффициент теплопроводности 0,032 Вт/мК, даже 0,031 Вт/мК, но это совсем другие материалы, например на основе особых пенополистиролов. Однако изобретение относится исключительно к области материалов на основе минеральных волокон. Материалы на основе минеральной ваты, в частности стекловаты, получают известным способом внутреннего центрифугирования в комбинации с вытягиванием газовой струей высокой температуры. Этот способ формирования волокон состоит во введении нити расплавленного стекла в центрифугу,называемую также прядильным диском, вращающуюся с высокой скоростью, по периметру которой проделано очень большое число отверстий, через которые стекло выталкивается в виде филаментов под действием центробежной силы. Затем эти филаменты подвергаются действию вытягивающего кольцевого потока, имеющего повышенную температуру и скорость, который создается форсункой и который идет вдоль поверхности центрифуги, потока, который делает их тоньше и превращает в волокна. Образованные волокна увлекаются этой вытягивающей газовой струей к приемному устройству, обычно состоящему из газопроницаемой ленты, которая соединена с аспирационным устройством. Связующее,необходимое, чтобы соединить волокна в ворсистом материале, распыляется на волокна, когда они вытягиваются к приемному устройству. Скопление волокон на приемном устройстве под действием всасывания создает слой волокон, толщина которого может меняться в зависимости от конечного материала,который нужно получить. Этот способ превращения стекла в волокна является очень сложным и требует баланса большого числа переменных параметров. В частности, давление в форсунке, а также скорость газа при вытяжке играют важную роль в оптимизации вытягивания волокон. Важным фактором является также конструкция прядильного диска. Обычно волокна, полученные внутренним центрифугированием, имеют средний диаметр 3 мкм, что соответствует показателю микронейр от 3 до 5 г, или же средний диаметр 2 мкм (микронейр от 2,8 до менее 5 г). Напомним, что тонкость волокон определяется значением их микронейра (F) ниже 5 г. Величина микронейр, называемая также "индексом тонкости", характеризует удельную поверхность, благодаря измерению потери аэродинамической нагрузки, когда к заданному количеству волокон, вытянутых из незамасленного мата, прикладывается заданное давление газа, обычно воздуха или азота. Это измерение,являющееся обычным на установках по производству минеральных волокон, осуществляется в соответствии со стандартом DIN 53941 или ASTM D 1448 и использует устройство, называемое прибором"Micronaire". Однако такое устройство имеет предел измерений, что касается определенной тонкости волокон. Для очень тонких волокон тонкость ("показатель микронейр") может быть измерена в л/мин, согласно известному методу, описанному в заявке на патент WO 2003/098209. Действительно, эта патентная заявка относится к устройству определения индекса тонкости волокон, содержащему устройство измерения индекса тонкости, причем указанное устройство измерения индекса тонкости снабжено, с одной стороны, по меньшей мере одним первым отверстием, соединенным с измерительной ячейкой, способной принимать образец, состоящий из множества волокон, а с другой стороны, вторым отверстием, соединенным с устройством измерения перепада давления от одной до другой стороны указанного образца,причем указанное устройство измерения перепада давления должно быть соединено с устройством создания течения жидкости, отличающемуся тем, что устройство измерения индекса тонкости содержит по меньшей мере один объемный расходомер для жидкости, проходящей через указанную ячейку. Это устройство дает соответствие между значениями "микронейр" и литрами в минуту (л/мин). Для сведения можно отметить, что, согласно этому документу WO 2003/098209, имеется количественная связь между значениями показателя микронейр и величиной среднего диаметра образца волокон. Обычно значение микронейр примерно 12 л/мин соответствует среднему диаметру 2,5-3,0 мкм, значение 13,5 л/мин по существу соответствует среднему диаметру 3-3,5 мкм и, наконец, 18 л/мин соответствует примерно 4-5 мкм. Для некоторых приложений были получены тонкие волокна со средним диаметром около 3 мкм. В частности, чтобы получить стеклянные оболочки толщиной несколько миллиметров для получения аэрозольных фильтров или разделителей в батареях, в документе WO 99/65835 предлагается устройство внутреннего центрифугирования, которое позволяет также получить волокна диаметром примерно 3 мкм. Устройство в этом документе содержит центрифугу, снабженную отверстиями, которые объединены в ряды, причем по меньшей мере два соседних ряда имеют отверстия разных диаметров, и высота формирования волокон центрифугой меньше или равна 35 мм. Но этот тип приложений для фильтров,использующий, кроме того, материалы очень малой толщины, слишком далек от применения теплоизоляционных материалов, и там совсем не используется понятие коэффициента теплопроводности. Для другого применения, относящегося к изоляционным материалам, из документа ЕР 1370496 известно устройство внутреннего центрифугирования, которое дает тонкие волокна, средний диаметр которых не превышает 3,5 мкм, и с наименьшим полученным средним диаметром 2,1 мкм. Для этого форсунка в этом устройстве имеет некоторые особенности в комбинации с особой конфигурацией центрифуги. Так, центрифуга содержит по меньшей мере две кольцевые зоны, число отверстий в которых на единицу поверхности отличается на значение, больше или равное 5%, причем расстояние между центрами наиболее близких отверстий в одной и той же кольцевой зоне по существу постоянно по всей этой кольцевой зоне, и это расстояние меняется от зоны к зоне по меньшей мере на 3%, уменьшаясь сверху вниз диска в позиции центрифугирования. Такое устройство, которое создает более тонкие волокна, улучшает коэффициент теплопроводности полученных материалов при плотности, эквивалентной плотности обычных материалов. Пример, приведенный в этом документе, представляет собой материал толщиной 80 мм, который при низкой плотности(9 кг/м 3) обеспечивает достаточно хорошую теплопроводность 41,2 Вт/мК. Тем не менее, всегда хотелось бы улучшить теплопроводность материала, чтобы достичь удовлетворительных изоляционных характеристик без использования слишком больших толщин. Действительно, в зависимости от коэффициента теплопроводности материала, из которого образован материал, толщину материала нужно подбирать так, чтобы получить характеристику, которая выражается как можно более высоким тепловым сопротивлением (обозначается R). Ясно, что с материалом, описанным в предшествующем документе ЕР 1370496, желание повысить термическое сопротивление привело бы к существенному увеличению толщины материала, что было бы не совместимо с некоторыми приложениями, связанными с изоляцией зданий. Поэтому задачей изобретения является создание теплоизоляционного материала на основе минеральных волокон, который имеет улучшенные теплоизоляционные свойства, чтобы он мог использоваться с разумной толщиной для строительных приложений, для которых этот материал предназначен, причем этот материал может сильно сжиматься, будучи способным возвращаться к своей номинальной толщине, и предпочтительно может находиться в виде рулона. Согласно изобретению теплоизоляционный материал, основанный на минеральной вате, отличается тем, что волокна имеют показатель микронейр ниже 10 л/мин, в частности не более 9 л/мин, предпочтительно ниже 7 л/мин, в частности составляющий от 3 до 6 л/мин, причем материал содержит элементы,отражающие и/или поглощающие инфракрасное излучение, и тем, что материал имеет коэффициент теплопроводности ниже 30 мВт/мК. Материал характеризуется также средним диаметром волокон ниже 2 мкм и даже ниже 1 мкм. Согласно изобретению оказалось, что для особого применения в теплоизоляции удалось изготовить материал, содержащий еще более тонкие волокна, чем в предшествующем уровне техники, с такой структурой, что материал характеризуется улучшенным коэффициентом теплопроводности по сравнению с уровнем техники. Элементы, отражающие и/или поглощающие инфракрасное излучение, предназначены не пропускать тепло, падающее на материал, чтобы снизить, таким образом, тепловой поток,проходящий через материал, что в таком случае снижает коэффициент теплопроводности материала. Материал по изобретению, несомненно, позволяет получать улучшенные теплоизоляционные характеристики и дает также, благодаря тонкости его волокон, более мягкий материал, приятный в обращении. Согласно одной характеристике, плотность материала не превышает 35 кг/м 3, предпочтительно составляет от 20 до 30 кг/м 3. Предпочтительно волокна являются, по существу, в частности, по меньшей мере на 75% почти параллельными большим размерам материала, имеющего чаще всего форму почти прямоугольного параллелепипеда. Под "почти параллельным" понимается параллельное расположение с точностью 30. Это параллельное расположение волокон препятствует, таким образом, передаче тепла через толщину материала (перпендикулярно указанным плоскостям). Долю волокон, ориентированных по толщине материала (перпендикулярно большим размерам), сводят к минимуму, что позволяет предотвратить процесс передачи тепла через воздушные ходы, образовавшиеся между этими волокнами в виде вентиляционных каналов. Структура является, по существу, структурой типа минеральной ваты, состоящей из волокон, в частности стекловолокон, связанных между собой связующим, и содержит элементы, отражающие и/или поглощающие инфракрасное излучение, в количестве по меньшей мере 0,5%, в частности от 1 до 10% от веса материала, в частности от 1 до 6%, предпочтительно от 2 до 6%. Ввиду назначения материала желательно добавлять обычные добавки типа масляных, чтобы улавливать пыль, типа антистатиков или типа водоотталкивающих агентов, таких как силикон. Отражающие и/или поглощающие элементы могут представлять собой, например, металлические частицы, такие как алюминиевые, при необходимости из другого металла, такого как серебро, медь, золото или металлического сплава, такого как сталь. Эти частицы могут быть выбраны из диспергируемых в воде металлических пигментов, которые имеются в продаже. Размер отражающих и/или поглощающих элементов составляет от 5 до 25 мкм. Согласно другой характеристике, толщина материала составляет по меньшей мере 30 мм, в частности от 40 до 150 мм, в зависимости от желаемого применения и желаемого термического сопротивления. Материал плотностью, не превышающей 35 кг/м 3, благоприятно находится в виде рулона. Благодаря своей низкой плотности, обеспечивающей ему соответствующую толщину, материал можно сильно сжимать, в частности для облегчения условий его перевозки, и он способен восстанавливать свою номинальную толщину, когда он готов к использованию по своему конечному назначению. Материал применяется, в частности, для обшивки стен и/или кровли в здании. Этот термоизоляционный материал может быть также встроен в систему звукоизоляции. Материал предпочтительно имеет в основе стекловолокна, причем доля неволокнистой фракции не превышает 1%, чтобы еще больше ограничить теплоперенос. Стекло предпочтительно является кальциево-боросиликатным стеклом с содержанием бора ниже 10 вес.% от состава стекла, предпочтительно с содержанием бора от 4 до 7%. Материал по изобретению чаще всего получают способом прядения волокон путем внутреннего центрифугирования, с помощью прядильной установки, параметры прядения которой настроены так,чтобы давать волокна с желаемым индексом тонкости, и путем распыления на волокна раствора, содержащего элементы, отражающие и/или поглощающие инфракрасное излучение. Согласно изобретению способ получения минеральной ваты предусматривает установку, которая включает в себя устройство внутреннего центрифугирования, содержащее центрифугу, которая может вращаться вокруг оси X, в частности вертикальной, и в боковой поверхности которой проделано множество отверстий, чтобы выдавать филаменты расплавленного материала, устройство вытягивания с помощью газовой струи высокой температуры, в виде кольцевой форсунки, которая обеспечивает вытягивание филаментов в волокна, причем способ отличается тем, что он состоит в осаждении на волокна элементов, отражающих и/или поглощающих инфракрасное излучение. Согласно одной характеристике, установка содержит кольцо, снабженное множеством отверстий,через которые разбрызгивается раствор, содержащий отражающие и/или поглощающие инфракрасное излучение элементы. Элементы, отражающие и/или поглощающие инфракрасное излучение, представляют собой, например, металлические частицы типа алюминия. Эти элементы могут распределяться отдельно или вместе со связующим, обычно наносимым на волокна. Согласно другой характеристике, способ состоит в контролировании комбинации параметров, которыми являются по меньшей мере давление в форсунке от 450 до 750 мм вод.ст. (водяного столба),вращение центрифуги со скоростью выше 2000 об/мин и количество волокон, вытягиваемое в сутки через одно отверстие центрифуги, максимум 0,5 кг, предпочтительно максимум 0,4 кг. Так, для одной и той же конструкции центрифуги по изобретению давление в форсунке составляет от 500 и до максимум 750 мм вод.ст., чтобы сформировать, например, волокна с показателем микронейр 5,5 л/мин, соответственно 3,4 л/мин. Эти значения давления не вызывают слишком сильной турбулентности и позволяют равномерную укладку пластов волокон на приемный конвейер и дают волокно, которое очень предпочтительно является немного более длинным. Согласно одной характеристике, способ по изобретению таков, что скорость подачи расплавленного материала на центрифугу ниже 18 т/сут для центрифуги с числом отверстий по меньшей мере 32000, а предпочтительно соответствует комбинации: скорость подачи не более 14 т/сут и число отверстий в центрифуге по меньшей мере 36000. Диаметр дисков составляет от 200 до 800 мм, предпочтительно равен 600 мм. Обычно диски с диаметром 600 мм имеют не более 32000 отверстий. Напротив, изобретение, увеличивая число отверстий на единицу поверхности, дает диск, число отверстий в котором существенно выше, чем согласно уровню техники. Высота перфорированной полосы диска предпочтительно не превосходит 35 мм. Центрифуга содержит две или более кольцевых зон, расположенных одна над другой, причем отверстия в центрифуге представляют от одной зоны к другой ряды отверстий разного диаметра, причем диаметр в кольцевом ряду уменьшается сверху вниз боковой поверхности диска в позиции центрифугирования. Диаметр отверстий составляет от 0,5 до 1,1 мм. Согласно другой характеристике, расстояние между центрами соседних отверстий в одной и той же кольцевой зоне является постоянным или нет во всей кольцевой зоне, и это расстояние меняется от зоны к зоне по меньшей мере на 3% или даже по меньшей мере на 10% и уменьшается сверху вниз боковой поверхности диска в позиции центрифугирования, в частности расстояние составляет от 0,8 до 2 мм. Таким образом, способ по изобретению, благодаря введению элементов, отражающих и/или поглощающих инфракрасное излучение, и благодаря регулированию, в основном, давления в форсунке, скорости вращения центрифуги и неожиданно количества расплавленного материала, вытягиваемого в сутки через одно отверстие диска центрифуги, дает материал, волокна которого являются особенно тонкими,имея показатель микронейр ниже 10 л/мин, причем более 65% волокон имеют средний диаметр ниже 1 мкм, в сочетании с коэффициентом теплопроводности ниже 30 мВт/мК, что не предлагалось в уровне техники. Кроме того, для последовательного снижения коэффициента теплопроводности способ по изобретению реализует как можно более плоское продвижение волокон, то есть согласно расположению волокон, которое параллельно большим размерам материала. Такая конфигурация получается, в частности, благодаря характеристикам, относящимся к приему и удалению волокон транспортером, продолжающим приемный конвейер. Для этого способ по изобретению состоит в установке скорости движения транспортера, стыкующегося с приемным конвейером, выше скорости движения указанного приемного конвейера, в частности выше более чем на 10%, предпочтительно по меньшей мере на 15%. Другие преимущества и характеристики изобретения будут описаны более подробно в сочетании с приложенными чертежами, на которых показано: на фиг. 1 - схематический вид в вертикальном разрезе прядильной установки согласно изобретению; на фиг. 2 - схематический вид в вертикальном разрезе прядильного устройства установки. На фиг. 1 схематически показано сечение по вертикальной плоскости установки 1 формирования матов из минеральной ваты. Установка 1 известным образом содержит сверху вниз по схеме или сверху вниз в направлении движения вытягиваемого материала в расплавленном состоянии: устройство внутреннего центрифугирования 10, которое подает филаменты растяжимого материала, устройство вытягивания 20, выпускающее газовую струю, которая превращает филаменты в волокна, падающие в виде завесы 2, кольцевой индуктор 30, находящийся под устройством центрифугирования 10, устройство подачи связующего 40, приемный конвейер 50 для волокон, на котором скапливаются волокна, чтобы образовать мат. Затем мат с помощью транспортера 60, который продолжает в той же плоскости приемный конвейер 50, направляется к сушильной камере для обжига волокон и связующего. Согласно изобретению установка содержит устройство 70 распыления элементов, отражающих и/или поглощающих инфракрасное излучение, которое имеет вид кольца, снабженного отверстиями для распыления и находящегося под устройством центрифугирования 10 и индуктором 30, до устройства подачи связующего 40. Как вариант, устройство распыления могло бы быть устройством подачи связующего, при этом связующее содержало бы отражающие и/или поглощающие инфракрасное излучение элементы. Отражающие и поглощающие инфракрасное излучение элементы находятся в виде металлических частиц типа алюминия. Частицы имеют, например, средний размер от 10 до 18 мкм. Они имеют размеры выше 2 мкм, обычно от 5 до 25 мкм. На фиг. 2 более детально показаны устройства 10, 20 и 30 прядильной установки. Устройство центрифугирования 10 содержит центрифугу 11, называемую также прядильным диском, вращающуюся с высокой скоростью, без дна в своей нижней части и с очень большим числом отверстий, проделанных на уровне ее боковой поверхности 12, через которые расплавленный материал выталкивается в виде филаментов под действием центробежной силы. Центрифуга 11 без дна закреплена зажимным средством на полом валу 13, вращающемся вокруг оси X, установленной вертикально, причем вал приводится в действие непоказанным мотором. Барабан 14 с цельным дном соединен с центрифугой, будучи размещенным внутри центрифуги так,чтобы его отверстие было расположено против свободного конца полого вала 13 и чтобы его боковая стенка 15 была существенно удалена от боковой поверхности или полосы 12. В цилиндрической стенке 15 барабана проделано небольшое число отверстий 16, относительно крупных, например диаметром порядка 3 мм. Струйка расплавленного стекла подается в центрифугу, проходя через полый вал 13, и вытекает в барабан 14. Расплавленное стекло, проходя через отверстия 16 барабана, распределяется затем в виде первичных нитей 16 а, которые направляются внутрь боковой поверхности 12, откуда они выталкиваются через отверстия 17 диска под действием центробежной силы в виде филаментов 17 а. Устройство вытягивания 20 состоит из кольцевой форсунки, которая создает газовую струю, имеющую высокую температуру и скорость, идущую вдоль боковой стенки 12 центрифуги. Эта форсунка служит дляподдержания повышенной температуры боковой стенки центрифуги и способствует умень-4 024394 шению толщины филаментов, преобразуя их в волокна. Газовая струя для вытягивания обычно канализируется с помощью холодного обволакивающего газового слоя. Этот газовый слой производится продувочной коронкой 21, окружающей кольцевую форсунку. Будучи холодной, она позволяет, кроме того, облегчить охлаждение волокон, механическая прочность которых, таким образом, улучшается в результате эффекта тепловой закалки. Кольцевой индуктор 30 нагревает устройство центрифугирования снизу, помогая в сохранении теплового равновесия диска 11. Устройство 40 подачи связующего состоит из кольца, через которое вытекает завеса волокон 2. Кольцо содержит множество сопел, опрыскивающих связующим завесу волокон. Обычно связующее,которое участвует в сцеплении волокон друг с другом, содержит противопылевые добавки типа масел и антистатики. Минеральный материал, который преобразуют в волокна, чаще всего состоит из стекла. Годится любой тип стекла, который можно преобразовать способом, называемым внутренним центрифугированием. Однако согласно изобретению предпочтительно кальциево-боросиликатное стекло, в котором содержание бора ниже 10%, в частности составляет от 2 до 9%, предпочтительно от 4 до 7%. Согласно изобретению получение тонких волокон осуществляется путем регулирования различных параметров, которыми являются, в частности давление в форсунке 20; скорость вращения диска 11; количество волокон, вытягиваемое в сутки через каждое отверстие 17 диска. Кольцевая форсунка 20 имеет стандартную конструкцию. Температура газовой струи на выходе форсунки составляет от 1350 до 1500 С, предпочтительно примерно 1400 С. Согласно изобретению давление в форсунке устанавливается на уровне от 450 до 750 мм вод.ст.(напомним, что 1 мм вод.ст. = 9,81 Па), чтобы в комбинации с другими вышеназванными параметрами образовать струю газа для вытягивания, наилучшим образом подходящую для желаемой тонкости волокон. Если, как обычно, давление форсунки составляет 500 мм вод.ст., согласно изобретению можно решиться повысить давление для утонения волокон, что, однако, требует дополнительной энергии. Нужен компромисс между указанными выше различными параметрами, чтобы получить желаемый материал, в зависимости от принимаемых в расчет экономических и энергетических факторов. Согласно изобретению скорость вращения диска выше, чем обычная скорость 1900 об/мин. Диск согласно изобретению вращается со скоростью выше 2000 об/мин, например 2200 об/мин. Согласно изобретению количество вытягиваемого волокна на одно отверстие диска составляет максимум 0,5 кг в сутки и предпочтительно не превышает 0,4 кг/сут. Количество вытянутого волокна в сутки на отверстие соответствует расходу расплавленного материала, проходящего через каждое отверстие в сутки. Эта производительность связана, разумеется, со скоростью расплавленного материала, подаваемого выше центрифуги, и с числом отверстий, проделанных в центрифуге. Согласно изобретению подача расплавленного материала не превышает 19 тонн в сутки (т/сут.), предпочтительно не превышает 14 т/сут. Для сравнения, обычная производительность печи, выдающей расплавленное стекло, составляет, как правило, порядка 23-25 т/сут. Что касается диска, он содержит по меньшей мере 32000 отверстий, предпочтительно по меньшей мере 36000 отверстий, т.е. число, превышающее число отверстий в стандартном диске, составляющее обычно 31846. Диск центрифуги имеет предпочтительный диаметр 600 мм, но он может составлять 400 или 800 мм, с коррекцией соответственно числа отверстий и количества подаваемого расплавленного материала. Диск содержит две или более кольцевые зоны, расположенные одна над другой, причем каждая зона снабжена одним или несколькими кольцевыми рядами отверстий. Облегчить получение тонких волокон могут, кроме того, некоторые особые характеристики, относящиеся к диску. Высота перфорированной полосы диска, т.е. высота, на которой располагаются отверстия, не превышает 35 мм. Отверстия диска имеют от зоны к зоне ряды отверстий разного диаметра, причем диаметр в каждом кольцевом ряду уменьшается сверху вниз боковой поверхности диска в позиции центрифугирования. Диаметр отверстий составляет от 0,5 до 1,1 мм. Расстояние между центрами соседних отверстий одной и той же кольцевой зоны является по существу постоянным или нет во всей кольцевой зоне, причем это расстояние меняется от зоны к зоне по меньшей мере на 3% или даже по меньшей мере на 10% и уменьшается сверху вниз боковой поверхности диска в позиции центрифугирования, в частности расстояние составляет от 0,8 до 2 мм. Согласно изобретению связующее, распределяемое кольцом 40, благоприятно имеет содержание ниже 8%, предпочтительно содержание не превышает 5%, чтобы получить материал, который можно сматывать в рулон. Вместе со связующим распределяется добавка, отражающая инфракрасное излучение, в виде металлических частиц, таких как алюминиевые. Частицы могут быть введены в связующее или подаваться в водной фазе, распыляемой отдельно на волокна вблизи связующего. Содержание частиц составляет от 0,5 до 2,0 вес.% в расчете на вес волокон. Такие частицы специально комбинируются с волокнами, полученными выше, чтобы обеспечить снижение коэффициента теплопроводностипри чуть повышенном диапазоне плотности материала, обычно 30 кг/м 3 или ниже. Наконец, снижение коэффициента теплопроводностиможет также быть связано с расположением волокон в мате. Большинство, более 75%, даже более 85% волокон расположено по существу параллельно большим размерам материала. Для этого скорость движения транспортера 60 согласно изобретению выше, чем скорость приемного конвейера 50, более чем на 10%, предпочтительно выше по меньшей мере на 15%. Это изменение скорости с ускорением приводит к тому, что волокна располагаются как можно более плоско в плоскости движения конвейера, ориентируясь по существу параллельно большим размерам полученного мата волокон. Ниже дается один пример материала по изобретению, полученного согласно способу по изобретению. Установка содержит прядильный диск диаметром 600 мм с 36000 отверстиями, причем расположение и диаметр отверстий такие, как описано выше. Производительность на отверстие в сутки равна 0,4 кг. Скорость вращения диска составляет 2200 об/мин. Давление в форсунке равно 500 мм вод.ст. Скорость транспортера 60 на 15% выше скорости приемного конвейера. Алюминиевые частицы со средним диаметром 12 мкм наносятся на волокна с помощью водной дисперсии, содержащей 2 вес.% алюминия в расчете на волокна. Полученный материал имеет следующие характеристики: индекс тонкости волокон 5,5 л/мин; коэффициент теплопроводности, измеренный при 10 С согласно стандарту ISO 8301, 29,6 мВт/мК; плотность 30 кг/м 3; содержание связующего 5% от веса материала; толщина 45 мм; волокна более чем на 80% почти параллельны большим размерам. Определение ориентации волокон осуществляется следующим образом: из материала отбирают несколько образцов в форме параллелепипеда (в частности, по меньшей мере 6) одинакового размера, с толщиной, идентичной толщине материала. Этот разрез проводится с помощью режущего инструмента,такого как лезвие, дающего чистый срез без захвата волокон в направлении разреза, таким образом, не искажающий расположение волокон, образующих материал, которое имелось перед резкой. Каждый образец обследуют по срезу, рассматриваемую поверхность разделяют на единичные поверхности малых размеров, волокна детектируют визуально в каждой единичной поверхности и определяют угол, составляемый направлением волокон относительно горизонтального направления, параллельного большим размерам материала, и вычисляют средний угол для каждой из поверхностей. Для этого может применяться средство ввода изображений, соединенное с программой обработки изображений. Таким образом,для каждого образца определяют долю волокон, имеющих угол ориентации, вписывающийся в заданный угловой сектор. Затем проводят усреднение данных для каждого образца, чтобы определить ориентацию волокон в материале. В этом примере было установлено, что 80% измерений углов находилось в секторе 0-30 и 150-180 (горизонтальные волокна), а 15% измерений углов находилось в секторе 30-60 и 120150 (наклонные волокна), и 5% измерений углов находилось в секторе 60-90 и 90-120 (вертикальные волокна). В отсутствие алюминиевых частиц коэффициент теплопроводности материала равен 30,2 мВт/мК. Таким образом, изобретение позволяет достичь снижения более чем на 0,5 мВт/мК. Теплопроводность можно еще больше снизить, подбирая состав стекла, в частности стекла, обогащенного бором. Материал, полученный в тех же условиях с 2 вес.% алюминия, имеет коэффициент теплопроводности 29,4 мВт/мК. Таким образом, введение отражающих и/или поглощающих инфракрасное излучение элементов в полученные волокна и конструкция прядильной установки в соответствии с несколькими особыми характеристиками, связанными главным образом с вращением прядильного диска, форсункой, количеством вытягиваемого волокна, и дополнительно связанными с приемным конвейером и продолжающим его транспортером, неожиданно позволили получить теплоизоляционный материал согласно изобретению,которого до настоящего времени не существовало. Преимуществом материала по изобретению, благодаря его очень тонким волокнам, является большая мягкость при прикосновении, что делает обращение с ним менее неудобным. Благодаря своему намного сниженному коэффициенту теплопроводности, материал обеспечивает еще более эффективную теплоизоляцию и позволяет получить оптимальный уровень термического сопротивления при разумных толщинах. Наконец, материал по изобретению, благодаря своей плотности не выше 30 кг/м 3, может находиться в виде рулона и/или может быть сжат и, таким образом, легко транспортируется и легок в обращении,чтобы легко резаться и устанавливаться на место, по желанию, напротив изолируемых стен. ФОРМУЛА ИЗОБРЕТЕНИЯ 1. Теплоизоляционный материал на основе минеральной ваты, отличающийся тем, что волокна имеют показатель микронейр ниже 10 л/мин, предпочтительно ниже 7 л/мин, в частности составляющий от 3 до 6 л/мин, причем материал содержит элементы, отражающие и/или поглощающие инфракрасное излучение, причем материал имеет коэффициент теплопроводности ниже 30 мВт/мК, при этом волокна в мате расположены плоско и, по существу, по меньшей мере 75% волокон параллельны длинным сторонам мата. 2. Теплоизоляционный материал по п.1, отличающийся тем, что он имеет плотность не более 35 кг/м 3, предпочтительно от 20 до 30 кг/м 3. 3. Теплоизоляционный материал по любому из предыдущих пунктов, отличающийся тем, что элементами, отражающими и/или поглощающими инфракрасное излучение, являются металлические частицы типа алюминия. 4. Теплоизоляционный материал по любому из предыдущих пунктов, отличающийся тем, что элементы, отражающие и/или поглощающие инфракрасное излучение, находятся в содержании, составляющем от 1 до 10 вес.% материала, предпочтительно от 2 до 6%. 5. Теплоизоляционный материал по любому из предыдущих пунктов, отличающийся тем, что отражающие и/или поглощающие инфракрасное излучение элементы имеют размер от 5 до 25 мкм. 6. Теплоизоляционный материал по любому из предыдущих пунктов, отличающийся тем, что он имеет толщину больше или равную 30 мм, в частности от 40 до 150 мм. 7. Теплоизоляционный материал по любому из предыдущих пунктов, отличающийся тем, что он выполнен с возможностью скатывания в рулон. 8. Теплоизоляционный материал по любому из предыдущих пунктов, отличающийся тем, что он предназначен для встраивания в систему звукоизоляции. 9. Теплоизоляционный материал по любому из предыдущих пунктов, отличающийся тем, что он основан на стекловолокнах и имеет долю неволокнистой фракции ниже 1%. 10. Теплоизоляционный материал по любому из предыдущих пунктов, отличающийся тем, что он основан на кальций-боросиликатном стекле с долей бора ниже 10 вес.% от состава стекла, предпочтительно от 4 до 7%. 11. Теплоизоляционный материал по любому из предыдущих пунктов, отличающийся тем, что он получен способом прядения путем внутреннего центрифугирования и путем осаждения на волокна отражающих и/или поглощающих инфракрасное излучение элементов. 12. Материал по любому из предыдущих пунктов, отличающийся тем, что он предназначен для обшивки стен и/или кровли здания.
МПК / Метки
МПК: C03B 37/10, D04H 13/00, C03C 25/10, C03B 37/04, C03C 25/14, D04H 1/42, D04H 1/74
Метки: основе, теплоизоляционный, материал, ваты, минеральной
Код ссылки
<a href="https://eas.patents.su/9-24394-teploizolyacionnyjj-material-na-osnove-mineralnojj-vaty.html" rel="bookmark" title="База патентов Евразийского Союза">Теплоизоляционный материал на основе минеральной ваты</a>
Предыдущий патент: Синергетическая гербицидная композиция
Следующий патент: Система беспроводной связи, устройство мобильной станции и устройство базовой станции
Случайный патент: Упаковка для сигарет