Способ получения железа прямого восстановления
Формула / Реферат
1. Способ прямого восстановления железной руды, который выполняют с помощью агрегата, включающего в себя гравитационную печь (2), имеющую по меньшей мере одну зону (8) восстановления железной руды в верхней части и по меньшей мере одну зону (9) отложения углерода и одну зону охлаждения (10) восстановленного металлического продукта в нижней части, а также средств подачи смеси восстановительного газа в реактор в зону восстановления, средства для повторного использования выпуска или отходящего из реактора реакторного газа для синтез-газа и средства смешивания рециркулирующего газа с природным газом для образования восстановительной газовой смеси, отличающийся тем, что он включает следующие стадии:
a) извлечение отходящего реакторного газа из реактора (8) для повторного использования;
b) очистка отходящего реакторного газа от частиц и пыли в системе очистки (4);
c) получение обезвоженного отходящего газа на первой стадии (5) преобразования посредством смещения оксида углерода СО и водяного пара H2O, присутствующих в отходящем реакторном газе, в сторону CO2 и Н2, используя реакцию конверсии водяного газа;
d) обработка отходящего реакторного газа компрессором или средствами перекачивания (27);
e) удаление CO2 из отходящего реакторного газа на второй стадии (6) преобразования, используя средства поглощения (21) диоксида углерода CO2 и средства удаления (22), для образования синтез-газа, включающего, в основном, СО и Н2;
f) удаление азота N2 и оксида углерода СО из отходящего реакторного газа на третьей стадии (7) преобразования с использованием средств поглощения N2 и СО для образования синтез-газа, включающего, в основном, Н2;
g) разделение потока синтез-газа на первый (37) и второй (19) потоки;
h) смешивание синтез-газа первого потока (37) с природным газом, подаваемым внешним источником (38);
i) нагревание синтез-газа из стадии f) во втором потоке (19) с помощью физического тепла, полученного от процесса обезвоживания на стадии с);
j) нагревание смеси синтез-газа первого (37) потока из стадии f) и природного газа в стадии h) с помощью физического тепла от восстановленного металлического продукта, полученного в зоне охлаждения (10);
k) извлечение смеси синтез-газа и природного газа от стадии j) из зоны охлаждения (10) металлического продукта к газогенератору (3);
l) нагревание газовой смеси из стадии k) инжектированием кислорода О2 в магистраль (41) к смеси синтез-газа и природного газа и подведение смеси к газогенератору (3);
m) обработка инжектированным кислородом О2 газовой смеси со стадии l) в газогенераторе для получения восстановительной газовой смеси и подведение газовой смеси от газогенератора (3) к реактору (8);
n) смешивание синтез-газа из стадии i) второго потока (19) с потоком восстанавливаемой газовой смеси стадии m) для обеспечения восстановительной газовой смеси;
о) подача восстановительной газовой смеси, образованной на стадии n), к зоне восстановления (8) реактора.
2. Способ по п.1, характеризующийся тем, что дополнительно используют средства (24) обмена теплом для того, чтобы передать физическое тепло обезвоженного отходящего газа, образованного на стадии с), средствам (22) удаления СО2 второй стадии (6) преобразования.
3. Способ по п.1, характеризующийся тем, что восстановительный газ покидает газогенератор нагретым до температуры между 800 и 1400°С, предпочтительно до 1200°С.
4. Способ по п.1, характеризующийся тем, что восстановительный газ поступает в зону восстановления (8) реактора, имея температуру 910°С или выше.
5. Способ по п.1, характеризующийся тем, что поток газа из второй стадии (6) преобразования разделяют на первый (32) и второй (33) потоки, из которых газ первого потока (32) используют в качестве горючего остаточного газа в парогенераторе (25), генерирующем тепло для второй стадии (6) преобразования, а газ второго потока (33) подают к третьей стадии (7) преобразования.
6. Способ по п.1, характеризующийся тем, что результатом следующих друг за другом первой, второй и третьей стадий (5, 6, 7) преобразования является поток практически чистого водорода Н2.
7. Способ по п.1, характеризующийся тем, что нагревание на стадии m) достигают инжектированием предварительно определенного количества кислорода O2 и/или воздуха в смесь синтез-газа и природного газа, поступающую из зоны охлаждения (10).
8. Способ по п.1, характеризующийся тем, что азот N2 и оксид углерода, удаленные с помощью третьей стадии (7) преобразования, сжигают вместе с диоксидом углерода CO2, удаленным посредством второй стадии (6) преобразования.
9. Способ по п.1, характеризующийся тем, что в очистительную систему (4) дополнительно входит мультициклон (15) и последующий фильтр (16), через которые проходит отходящий реакторный газ.
10. Способ по п.1, характеризующийся тем, что на первой стадии (5) переработки применяют любой катализатор, известный в данном уровне техники, который пригоден для реакции конверсии водяного газа, например магнетит, любой переходный металл или оксид переходного металла, предпочтительно используемым является порода бурого железняка в форме кусков.
11. Способ по п.1, характеризующийся тем, что в третьей системе (7) преобразования используют любые физические средства разделения, такие как мембраны, или молекулярные сита, или любую соответствующую химическую систему поглощения.
12. Способ по п.11, характеризующийся тем, что третья система (7) преобразования включает молекулярное сито (34), которое включает любое соответствующее вещество, обладающее открытой структурой, такое как любой алюмосиликат, глина, активированный углерод или синтетический углерод.
13. Способ по п.1, характеризующийся тем, что обезвоженный отходящий газ из стадии с) охлаждают с помощью средств охлаждения (29) перед поступлением в компрессор или средства перекачивания (27).
14. Способ по п.1, характеризующийся тем, что устанавливают дополнительный нагреватель (43) для нагревания синтез-газа, полученного после третьей стадии (7) преобразования и перед позицией стадии h), в которой синтез-газ смешивают с природным газом.
15. Способ по п.14, характеризующийся тем, что поток отходящего газа из второй стадии (6) преобразования используют в качестве горючего газа в дополнительном нагревателе (43).
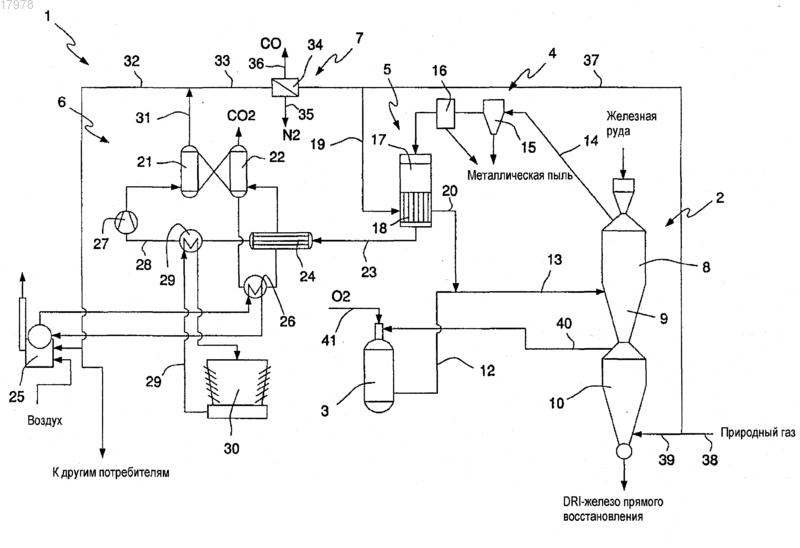
Текст
СПОСОБ ПОЛУЧЕНИЯ ЖЕЛЕЗА ПРЯМОГО ВОССТАНОВЛЕНИЯ Настоящее изобретение относится к способу прямого восстановления железной руды,выполняемому посредством агрегата, включающего гравитационную печь (2), которая имеет по меньшей мере одну зону (8) восстановления железной руды в верхней части вышеупомянутого и по меньшей мере одну зону (9) отложения углерода и одну зону (10) охлаждения восстановленного металла в нижней части вышеупомянутого и средства загрузки восстановительной газовой смеси в реактор в соответствии с зоной восстановления, средства для повторного использования выпуска или отходящего из реактора реакторного газа для синтез-газа и смешивание рециркулирующего газа с природным газом для образования восстановительной газовой смеси. В соответствии с изобретением на первой стадии (5) преобразования не вступивший в реакцию моноксид углерода СО и пар, присутствующий в отходящем реакторном газе, преобразуют в двуокись углерода и водорода в соответствии с реакцией конверсии водяного газа СО+Н 2O=СO2+Н 2,на второй стадии преобразования обезвоженный отходящий реакторный газ, включающий, в основном, диоксид углерода и водород, обрабатывают для удаления диоксида углерода, и на третьей стадии преобразования выполняют физическое разделение и азота, и оксида углерода от восстановительного синтез-газа для снижения уровней СО и любых существующих в рециркулирующем газе других газов до такого низкого уровня, насколько это возможно, чтобы рециркулирующий восстановительный газ являлся, насколько это возможно, приближенным к чистому водороду Н 2. Область техники изобретения Настоящее изобретение относится, главным образом, к способу получения железа прямого восстановления в соответствии с преамбулой п.1. Более конкретно настоящее изобретение относится к способу очистки и удаления двуокиси углерода и пара из отработанного восстановительного газа в способе прямого восстановления железа. Основы техники изобретения Способы прямого восстановления для получения металлизованного железа из окатышей оксида железа, крупнокусковой руды или подобных материалов, которые включают оксид железа, широко известны и используются в сталеплавильной промышленности. Способами прямого восстановления (DR) получают металлы из их руд удалением из руд связанного кислорода при температурах ниже температуры плавления любого из материалов, включенных в способ. Продукт, получаемый в результате способа прямого восстановления, известен как DRI или "железо прямого восстановления". В способе прямого восстановления железную руду переводят в продукт с высоким содержанием железа в виде металла. Непосредственное восстановление железной руды в реакторе прямого восстановления проводят в присутствии восстановительного газа, например природного газа, который включает восстановительные добавки водород (Н 2) и оксид углерода (СО), которые при контактировании восстанавливают железную руду до металлического железа. Альтернативно, восстановительный газ в виде оксида углерода может быть получен с помощью газогенератора в процессе сгорания, которое имеет место при реагировании углерода с кислородом, такая реакция также имеет преимущество, предоставляя тепло для соответствующих реакций газообразования в шахтной печи. Если реакции прямого восстановления проводят в печах ниже, чем примерно при 1000 С, то восстановительные добавки ограничены обычно СО и Н 2. В способе DRI-прямого восстановления железа железо восстанавливают, а диоксид углерода, полученный в реакции восстановления, удаляют вместе с восстановительным газом, широко известным как отходящий реакторный газ. Отходящий реакторный газ включает не вступивший в реакцию водород Н 2, не вступивший в реакцию оксид углерода СО, диоксид углерода СО 2 и воду в виде пара. После охлаждения отходящий реакторный газ подвергают повторной обработке для удаления диоксида углерода и повышения содержания водорода и оксида углерода перед тем, как возвратить обогащенный отходящий газ в реактор прямого восстановления в качестве эффективного восстановительного газа. Очищенный продукт, известный как синтез-газ (от англ. synthesisgas), является газовой смесью, которая содержит переменные количества оксида углерода и водорода посредством превращения отходящего реакторного газа в газообразный продукт с теплотворной способностью. Синтез-газ является по определению продуктом, содержащим, прежде всего, оксид углерода,диоксид углерода и водород. Отходящий реакторный газ содержит в значительной степени диоксид углерода и воду, которые образуются в процессе реакции. Для некоторых схем используют стадию конверсии для того, чтобы предоставить больше водорода и оксида углерода, а для некоторых схем используют стадию реакции конверсии водяного газа для совершенствования оборотного газа с тем, чтобы предоставить очищенный восстановительный газ повышенной эффективности, известный как синтез-газ. Во всех этих схемах необходимо удалять диоксид углерода из отходящего реакторного газа для того, чтобы поддерживать процесс восстановления. Прямое восстановление железной руды, т.е. оксидов железа, в основном гематита Fe2O3, выполняют восстановлением железной руды до металлического железа с помощью реакции с моноксидом углерода,водородом и/или твердым углеродом через последовательные состояния окисления. Обычно оксиды железа и углеродсодержащее вещество, например уголь, загружают в печь. Тепло поставляют в печь сжиганием топлива с воздухом для получения среди прочего моноксида углерода. По мере того как твердое вещество опускается в реакторе вниз, оно встречает поток восстановительного газа, который течет в противоположном направлении, и вещество восстанавливают до железа в виде металла и извлекают из печи. Отработанные и печные газы удаляют из печи через магистраль отработанного газа или трубопровод. В настоящее время агрегаты прямого получения железа для получения железа прямого восстановления,известного как DRI-железо прямого восстановления или горячебрикетированное железо (предварительно восстановленные вещества, используемые как исходный материал для получения железа и стали), производят эти продукты контактированием восстановительного газа, состоящего преимущественно из водорода и моноксида углерода, при эффективной температуре восстановления в интервале примерно от 750 до примерно 1050 С в слое содержащего железо дисперсного материала в виде кусков или окатышей. Потоки газа, используемые для прямого восстановления, часто подсчитываются на основании отношения между восстановительными агентами и окислительными агентами, определенными мольным отношением (Н 2+СО/Н 2 О+СО 2) газовой смеси. Эту величину обычно указывают с помощью термина "восстанавливающая способность" или величина R. Восстанавливающая способность является мерой эффективности газовой смеси, используемой в качестве восстановителя; чем выше восстанавливающая способность, тем больше эффективность. На протяжении многих лет способы прямого восстановления железа и другие способы совершенствовались в части различных схем получения для генерации синтез-газа повышенной эффективности из отработанного восстановительного газа или отходящего реакторного газа, содержащего высокие концен-1 017978 трации Н 2 и СО. В последние годы стала неотложной необходимость предоставления более эффективных, более продуктивных и менее затратных сталеплавильных процессов из-за повышения стоимости продукции (особенно энергетических затрат), а также из-за возрастания ограничений, которые накладывают на сталеплавильный цех по экологическим соображениям. Цель настоящего изобретения состоит,следовательно, в обеспечении способа получения железа прямого восстановления, в котором более простым образом совершенствуется преобразование отходящего реакторного газа для того, чтобы получить выходящий поток синтез-газа с высоким содержанием водорода и моноксида углерода. Еще одной целью является достижение существенного снижения удельного потребления ископаемого топлива, т.е. до более низкого удельного потребления первичной энергии ископаемых и значительного уменьшения удельных выбросов СО 2 на тонну полученного DRI-железа прямого восстановления. Следовательно, целью настоящего изобретения является предоставление способа прямого получения железа, с помощью которого производительность получения DRI-железа прямого восстановления может быть увеличена, и способа, который в то же самое время дает возможность снизить потребление ископаемого топлива. Дополнительно целью настоящего изобретения является получение рециркулирующего газа путем очистки и удаления двуокиси углерода и пара из обработанного восстановительного газа процесса прямого восстановления, характеризующегося тем, что рециркулирующий газ является практически чистым водородом с тем, чтобы дополнительно улучшить восстановительные свойства в реакторе. Дополнительно целью настоящего изобретения является предоставление способа, который снижает проблемы, связанные с металлическим запылением от агрегата, частицами и другими нежелательными компонентами в отходящем реакторном газе без увеличения расхода воды. Дополнительно целью настоящего изобретения является предоставление способа, который уменьшает расход воды, в частности, в качестве охлаждающей среды в процессе преобразования отходящего реакторного газа до синтез-газа. Охлаждение и повторное нагревание требует затратного теплообменного оборудования, а большой соединительный высокотемпературный трубопровод делает способ менее привлекательным. Также хорошо известно использование воды в скрубберах для удаления пыли. Другие цели изобретения будут указаны в данном описании или будут очевидны квалифицированному специалисту в данной области техники. Краткое описание изобретения Настоящее изобретение относится к способу получения DRI-железа прямого восстановления, в котором двуокись углерода СО 2 и пар Н 2 О удаляют из отработанного в процессе отходящего реакторного газа для получения восстановленной формы или выходящего синтез-газа с высоким содержанием водорода и моноксида углерода. Цель изобретения достигают, главным образом, выполнением способа, описанного в п.1. Более конкретно способ включает преобразование не вступившего в реакцию моноксида углерода СО, присутствующего в отходящем реакторном газе, в двуокись углерода СО 2 и водород в качестве первой стадии преобразования, которая сопровождается реакцией конверсии водяного газаCO+H2O=СО 2+Н 2, характеризующейся тем, что пар, присутствующий в отходящем газе, действует как реакционноспособная вода. Упомянутая первая стадия преобразования предшествует второй стадии преобразования, в которой отходящий реакторный газ обрабатывают дополнительно для удаления двуокиси углерода и повышают содержание водорода и моноксида углерода перед возвращением обогащенного отходящего газа в реактор прямого восстановления. Из ряда хорошо известных переходных металлов и оксидов переходных металлов в качестве катализатора для реакции конверсии водяного газа предпочтительно используют магнетит Fe3O4. Поскольку реакция конверсии водяного газа является экзотермической, т.е. реакцией, которая протекает с выделением тепла, отходящий газ выходит с температурой примерно 480-520 С, что примерно на 120 С выше, чем температура отходящего газа как таковая. Физическое тепло или полученную потенциальную энергию используют на стадиях последующей очистки газа. Третьей стадией преобразования является восстановление отходящего газа посредством дополнительного удаления оксида углерода и азота, чтобы обеспечить рециркулирующий газ, содержащий практически чистый водород. На второй стадии преобразования отходящий реакторный газ, который включает, главным образом,двуокись углерода и водород, обрабатывают для удаления двуокиси углерода, получая, таким образом,практически не содержащий двуокись углерода рециркулирующий поток для шахтной печи. Такой практически не содержащий двуокись углерода рециркулирующий поток нагревают и возвращают в шахтную печь, как часть общего восстановительного газа. Хорошо известно, что для того, чтобы получить восстановительный газ повышенной эффективности из реформинг-установки, в которой отходящий реакторный газ очищают до синтез-газа, содержащего высокую концентрацию Н 2 и СО, желательно поддерживать низкое содержание пара в потоке, входящем в реформинг-установку. Основной причиной для сниженного содержания пара в восстановительном газе является эффект разбавления пара при выполнении процесса конверсии. Несмотря на то, что удаление пара из реформинг-установки должно приводить к концентрированному восстановительному газу,такую стадию рассматривают как неэкономичную, поскольку потребуется охлаждать выходящий из ре-2 017978 форминг-установки продукт для конденсации воды и удаления, после чего необходимо будет повторное нагревание перед тем, как его ввести в установку восстановления железной руды. Охлаждение и повторное нагревание требуют затратного теплообменного оборудования и соединительного большого высокотемпературного трубопровода, что делает процесс непривлекательным. Кроме того, стадия конденсации воды увеличивает перепад давления и, тем самым, требует, чтобы эксплуатацию реформинг-установки выполняли при гораздо более высоком давлении, требующем повышения или температуры эксплуатации, или повышения отношения пар-углерод, или и того, и другого для того, чтобы удовлетворять требованию по остаточному метану. Действующие в настоящее время схемы для получения восстановительного газа повышенной эффективности нуждаются в совершенствовании, касающемся эффективности энергии и снижения затрат на получение. Для того чтобы усовершенствовать это, настоящее изобретение использует стадию каталитической обработки, расположенную после шахтной печи, в которой пар отходящего реакторного газа сдвигают в сторону водорода посредством не вступившего в реакцию моноксида углерода по реакции конверсии водяного газа CO+H2O=CO2+H2. В настоящем описываемом варианте воплощения используют катализатор, например магнетит или бурый железняк (лимонит). Реакция конверсии водяного газа является чувствительной к температуре и характеризуется тем, что тенденция к смещению в сторону реагирующих веществ увеличивается при более высоких температурах. Следовательно, относительно высокие температуры отходящего реакторного газа, которые в связи с этим были рассмотрены как проблема, можно использовать как преимущество. Помимо этого, тот факт, что отходящий реакторный газ из реактора DRI-прямого восстановления железа получен при низком давлении,что обычно считают недостатком, его можно использовать как преимущество. Изобретение также включает третью стадию преобразования с физическим отделением азота, и оксида углерода СО от восстанавливающего синтез-газа из вышеупомянутых стадий один и два. Цель третьей стадии преобразования состоит в том, чтобы снизить уровни СО и любого другогогаза, находящегося в рециркулирующем газе, до насколько возможно низкого уровня для того, чтобы рециркулирующий восстановительный газ был, по возможности, близким к чистому водороду Н 2. Краткое описание чертежей Элементы, цели и преимущества настоящего изобретения станут более очевидными из следующего описания предпочтительных вариантов воплощения со ссылкой на чертежи, на которых одними и теми же ссылками характеризуют указанные одни и те же или соответствующие части на нескольких видах и на которых фиг. 1 показывает схематично первый вариант воплощения настоящего изобретения, изображающий диаграмму способа и агрегаты получения DRI в соответствии с настоящим изобретением; фиг. 2 - второй вариант воплощения настоящего изобретения. Подробное описание изобретения Ниже в данном документе описывают две альтернативные схемы способа, одна из которых осуществлена с дополнительным нагревателем, а другая без дополнительного нагревателя для нагревания исходного выходящего продукта реформинг-установки, обогащенного водородом Н 2. Эти схемы показаны на фиг. 1 и 2 соответственно. Со ссылкой на фиг. 1 показан первый план расположения агрегата восстановления, обозначенного номером позиции 1, пригодного для выполнения способа, соответствующего настоящему изобретению. На плане расположения номер позиции 2 представляет, в целом, шахту прямого восстановления для получения DRI-железа прямого восстановления, 3 представляет газогенератор, поставляющий синтетический газ, известный по-другому как синтез-газ, который использует извлекаемый из реактора и очищенный газ для применения в качестве восстановительного газа в шахте восстановления, 4 представляет систему очистки от частиц для отделения частиц металла из отходящего реакторного газа, поступающих из реактора, 5, 6 и 7 представляют систему преобразования, включающую три стадии преобразования, характеризующиеся тем, что 5 представляет первую стадию преобразования пара, преобразующую моноксид углерода, присутствующий в отходящем реакторном газе, до двуокиси углерода и водорода, а 6 вторую стадию преобразования для удаления двуокиси углерода из преобразованного пара отходящего реакторного газа и 7 - третью стадию преобразования для удаления азота и оксида углерода из отходящего реакторного газа. Шахта 2 прямого восстановления сверху вниз включает зону загрузки железной руды, реакторную зону 8 прямого восстановления минералов, зону 9 науглероживания и охлаждающую емкость 10. В реакторе или шахте 8 получают горячее металлическое железо или DRI-железо прямого восстановления из оксидов в виде окатышей и/или кусков, которые из-за эффекта гравитации опускаются в зону 9 науглероживания. Охлаждающая емкость 10, расположенная ниже, в свою очередь присоединена непосредственно к устройству выгрузки. Существует, таким образом, единственный поток вещества от верхней части к нижней части или к основанию шахты или колонны. По мере того как твердое вещество продвигается вниз через реактор 8, оно встречает поток восстановительного газа, который подают в зону реакции упомянутого реактора, протекающий в противоположном направлении, причем упомянутая зона является по форме практически цилиндром, внутрь которого подают поток восстановительного газа из газогенератора 3 через трубопроводы 12, 13. Отработанный газ или "отходящий газ" извлекают из верхней части реактора 8 после того, как он прореагировал с оксидами железа и протекает по магистрали отработанного газа или трубопроводу 14 к системе 4 очистки от частиц. Температура отработанного газа зависит от той железной руды, которая загружена в реактор, но, как правило, газ покидает реактор примерно от 340 до 380 С. Поскольку в извлеченном из реактора 8 отработанном газе имеется пыль, отходящий газ, отправленный к системе очистки от частиц, проходит мультициклон 15, в котором основную часть пыли в отходящем газе отделяют,а после этого проходит фильтр 16, где из отходящего газа удаляют большое количество оставшейся пыли и мелких частиц. Большую часть металлической пыли и частиц отходящего реакторного газа можно удалить посредством этого. После соответствующей обработки, включающей компактирование металлической пыли из системы 4 очистки от частиц в брикеты или куски пригодного размера и формы, материал можно загрузить в шахтную печь. Первая стадия 5 преобразования включает передаточное устройство (шифтер) 17 преобразования паров углеводородов и в котором, таким образом, из практически чистого отходящего реакторного газа можно удалить воду путем преобразования в диоксид углерода и водород. Более конкретно передаточное устройство (шифтер) 17 предназначено для конвертирования не вступившего в реакцию моноксида углерода, присутствующего в отходящем реакторном газе, в диоксид углерода в соответствии с хорошо известной реакцией конверсии водяного газа CO+H2O=CO2+H2, где пар, присутствующий в отходящем газе, функционирует как реакционная вода. Передаточное устройство (шифтер) 17 может включать любой катализатор, известный для данного уровня техники, который пригоден для реакции конверсии водяного газа, например магнетит, или любой переходный металл, или оксиды переходного металла. В настоящем варианте воплощения в качестве катализатора используют бурый железняк в виде кусков. Реакция конверсии водяного газа очень чувствительна к температуре с тенденцией смещения в сторону вступающих в реакцию веществ при повышении температуры, характеризующаяся тем, что высокую температуру отходящего газа используют как преимущество. Поскольку реакция на первой стадии 5 преобразования является экзотермической, то обезвоженный отходящий газ выходит при температуре более высокой, чем он имел вначале, когда он поступал на стадию системы. Следовательно, температура обезвоженного газа, покидающего передаточное устройство (шифтер) 17, на всем протяжении трубопровода или магистрали, обозначенной 16, обычно составляет примерно 480-520 С. В теплообменнике 18, установленном после передаточного устройства (шифтера) 17, обезвоженный отходящий газ, в основном,включающий диоксид углерода и водород, охлаждают примерно до 300-340 С при обмене теплом с частью рециркулирующего газа, проходящего на всем протяжении магистрали 19. Более конкретно тепло от передаточного устройства (шифтера) 17 первой стадии 5 преобразования используют для того, чтобы нагреть рециркулирующий газ, содержащий высокие концентрации СО и H2, поступающий из второй стадии 6 преобразования, перед тем как рециркулирующий газ в магистрали 20 смешивают с потоком синтез-газа, который подают внешним источником, в данном случае газогенератором 3, и имеющим температуру примерно 1200 С. Приготовление рециркулирующего газа, а также синтез-газа из газогенератора 3 будет более подробно обсуждаться далее в данном документе. Вторая стадия 6 системы преобразования для удаления диоксида углерода СО 2 из обезвоженного отходящего газа включает средства 21 поглощения CO2 и средства 22 удаления CO2, которые в таком качестве известны в данном уровне техники. Из теплообменника 18 обезвоженный отходящий газ пропускают по магистрали 23 к ребойлеру 24, в который выпускают физическое тепло газа. Пар, полученный с одной стороны через ребойлер 24 под влиянием физического тепла, полученного от обезвоженного газа, проходящего через ребойлер, а с другой стороны - физического тепла, полученного от парогенератора 25 через теплообменник 26, используют в устройстве удаления СО 2 для выделения диоксида углерода из обезвоженного газа тем способом, который, как таковой, хорошо известен для данного уровня техники. Диоксид углерода высокой чистоты, удаляемый из установки удаления, предпочтительно можно собрать и реализовать другим потребителям. Перед тем как попасть в компрессор или средство перекачивания 27, которые также составляют часть второй системы 6 преобразования, обезвоженный газ,протекающий по магистрали 28, охлаждают при пропускании через водяное охлаждение 29. Подогретую воду от водяного охлаждения направляют для охлаждения через магистраль 29 к охлаждающей башне 30. Обезвоженный газ, посылаемый в магистраль 28 к компрессору или средству перекачивания 27, проходит через устройство 21 поглощения СО 2, тем самым увеличивая его восстанавливающий потенциал. После того как газ обработают в устройстве поглощения 21 СО 2, газ в магистрали 31 имеет состав, включающий, главным образом, оксид углерода, диоксид углерода и водород. Поток 14 рециркулирующего газа в магистрали 31 разделяют на два потока течения 32 и 33, из которых путь 32 используют, с одной стороны, в качестве горючего остаточного газа в парогенераторе 25, а с другой стороны, его можно собрать и распределить другим потребителям. Поскольку количество остаточного газа должно быть низким для того, чтобы его можно было использовать в качестве восстановительной среды, то N2, входящий в состав газа, необходимо удалять. Следовательно, газовый поток второго пути течения 33 пропускают через отделитель азота N2, включающий средства физического отделения, например молекулярное сито 34, или в молекулярное сито, предусмотренное для поглощения азота из газа. Физические средства отделения могут включать для этой цели любые средства, например мем-4 017978 браны, молекулярные сита или химические системы поглощения. Молекулярное сито 34 предусмотрено предпочтительно для поглощения не только азота, но также и присутствующего в газе оксида углерода СО, который удаляют из устройства 22 удаления СО 2 сгоревшим и смешанным с CO2. Молекулярное сито 34 может включать любое пригодное вещество, обладающее открытой структурой с молекулами,которые обладают абсорбционными свойствами в качестве не ограничивающего примера, например алюмосиликат, глину, активный углерод или искусственный углерод и подобное. Поток 35 указывает выведение N2, удаленного из остаточного газа, а поток 36 - удаление диоксида углерода. Поток 33 из молекулярного сита 34 разделяют на два пути течения или потока 19 и 37, из которых один путь 19, который уже упоминали выше в данном документе, направляют для прохождения через теплообменник 18 для того, чтобы получить тепло, выделенное первой системой 5 преобразования, включающей передаточное устройство (шифтер) 17, в то время как другой поток 37 направляют к охлаждающей емкости 10DRI-прямого восстановления железа шахты восстановления 2. Следует отметить, что целью стадии обработки в молекулярном сите 34 является снижение уровня СО и любых других газов, существующих в рециркулирующем газе, до настолько низкого уровня, насколько это возможно, для того, чтобы рециркулирующий газ в двух магистралях 19 и 37 являлся насколько возможно приближенным к чистому водороду Н 2. С помощью очистки водородный уровень в рециркулирующем газе не только достигает синтезгаза с более высокой восстанавливающей способностью, или R, и эффективностью, но также таких условий процесса, которые гарантирует надлежащее восстановление железных руд плохого качества. Синтез-газ, используемый в качестве восстановительной среды в настоящем способе прямого восстановления, является предварительно нагретой смесью практически чистого водорода Н 2, поступающего из магистрали 37, и природного газа, например CH4. Агрегат выгодно предоставляют вместе с устройствами регулирования, не показанными на чертеже, для управления количеством природного газа, который загружается для смешивания с рециркулирующим газом в магистраль 37, для того, чтобы оптимизировать реакции восстановления и преобразования. Холодный природный газ, подаваемый в процесс с помощью магистрали 38 и смешиваемый с рециркулирующим газом, поступающим из магистрали 36,причем смешанный газ подают в охлаждающую емкость 10 с помощью смешивания с магистралью 39 и после этого пропускают через горячее DRI-железо прямого восстановления в охлаждающей емкости 10. Соответственно, DRI-железо прямого восстановления в охлаждающей емкости охлаждают, пока в это время смесь рециркулирующего газа и природного газа нагревают перед тем, как подать к газогенератору 3 данной системы обработки. Предварительный подогрев смешанного газа вплоть до 520 С можно выполнить предпочтительно путем обмена теплом с горячим DRI-железом прямого восстановления в охлаждающей емкости 10. Управляя содержанием природного газа в восстановительном газе, поступающем в реактор 2, возможно непосредственно управлять процессом восстановления в зоне реакции 8 реактора с помощью соответствующего регулирования температуры загрузки в зоне реакции, предпочтительно между 800 и 900 С, и кинетикой реакции. Газовую смесь извлекают из охлаждающей емкости 10 DRI-прямого восстановления железа с помощью устройств для извлечения и направляют по выходящей магистрали 40 к газогенератору 3 и частично окисляют кислородом или воздухом, поступающим в газогенератор через магистраль 41. Дополнительный способ нагревания восстановительного газа предоставляют в позиции, где газовая смесь поступает в газогенератор через магистраль 40, путем инжектирования предварительно определенного количества чистого кислорода или обогащенного кислородом воздуха в упомянутый трубопровод 40 с тем, чтобы получить частичное сгорание СО и Н 2 и нагреть вводимый восстановительный газ до температуры между 850 и 1200 С. После прохождения дополнительного процесса нагревания поток восстановительного газа подают в первую магистраль 12 для восстановления и преобразования посредством второй магистрали 13. Перед поступлением в реактор с помощью трубопровода 20 полученный горячий газ из газогенератора 3 смешивают с истощенным предварительно нагретым примерно при 400 С газовым потоком, содержащим, в основном, водород Н 2. Эту смесь, которой можно управлять при температуре между 800 и 950 С с помощью средств регулирования, не показанных на чертеже, подают в реактор 1 прямого восстановления, где происходит восстановление. Следует отметить, что главным восстанавливающим компонентом в газе будет водород. Со ссылкой на фиг. 2 описывают альтернативную схему способа, имеющую дополнительный нагреватель для нагревания исходного выходящего вещества реформинг-установки с высокой концентрацией водорода Н 2. Обозначения позиций на фиг. 2 соответствуют обозначениям на фиг. 1 для того, чтобы продемонстрировать тот факт, что они относятся к таким же или подобным устройствам. Остаточный газ в магистрали 32 разделяют на два потока течения 32 и 42, из которых поток 32, как упоминалось в данном документе выше, используют как остаточный газ парогенератора 25, а другую часть 42 используют как остаточный газ в дополнительном нагревателе 43 рециркулирующего газа для нагревания рециркулирующего газа в магистрали 37 перед тем, как его смешивают с природным газом и пропускают через охладитель 10 DRI-железа прямого восстановления. Рециркулирующий газ, нагретый в подогревателе 43 рециркулирующего газа, проводят по магистрали 44. Холодный природный газ, поступающий для процесса по магистрали 38 и смешиваемый с рециркулирующим газом, поступающим из магистрали 44, где смешанный газ вводят в охлаждающую емкость 10 смешиванием магистрали 39 и пропускают через горячее DRI-железо прямого восстановления в охлаждающем сосуде 10. Соответственно, DRI-железо пря-5 017978 мого восстановления охлаждается, в то время как смесь рециркулирующего газа и природного газа нагревается перед подачей в газогенератор 3 системы обработки. Восстановительный газ, подаваемый в реактор 8, нагревают до температуры выше 910 С перед поступлением в реактор 8 через магистраль 13. Упомянутая температура является хорошим интегральным коэффициентом, который не допускает "слипания" в реакторе. Высокое содержание в газе водорода Н 2 с одной стороны и низкий молекулярный вес с другой стороны допускают небольшой размер реактора. Настоящее изобретение не ограничивают приведенным выше описанием, иллюстрированным на чертежах, но оно может быть изменено или модифицировано несколькими различными путями в рамках идеи изобретения, обозначенной в нижеследующей формуле изобретения. ФОРМУЛА ИЗОБРЕТЕНИЯ 1. Способ прямого восстановления железной руды, который выполняют с помощью агрегата, включающего в себя гравитационную печь (2), имеющую по меньшей мере одну зону (8) восстановления железной руды в верхней части и по меньшей мере одну зону (9) отложения углерода и одну зону охлаждения (10) восстановленного металлического продукта в нижней части, а также средств подачи смеси восстановительного газа в реактор в зону восстановления, средства для повторного использования выпуска или отходящего из реактора реакторного газа для синтез-газа и средства смешивания рециркулирующего газа с природным газом для образования восстановительной газовой смеси, отличающийся тем, что он включает следующие стадии:a) извлечение отходящего реакторного газа из реактора (8) для повторного использования;b) очистка отходящего реакторного газа от частиц и пыли в системе очистки (4);c) получение обезвоженного отходящего газа на первой стадии (5) преобразования посредством смещения оксида углерода СО и водяного пара H2O, присутствующих в отходящем реакторном газе, в сторону CO2 и Н 2, используя реакцию конверсии водяного газа;d) обработка отходящего реакторного газа компрессором или средствами перекачивания (27);e) удаление CO2 из отходящего реакторного газа на второй стадии (6) преобразования, используя средства поглощения (21) диоксида углерода CO2 и средства удаления (22), для образования синтез-газа,включающего, в основном, СО и Н 2;f) удаление азота N2 и оксида углерода СО из отходящего реакторного газа на третьей стадии (7) преобразования с использованием средств поглощения N2 и СО для образования синтез-газа, включающего, в основном, Н 2;h) смешивание синтез-газа первого потока (37) с природным газом, подаваемым внешним источником (38);i) нагревание синтез-газа из стадии f) во втором потоке (19) с помощью физического тепла, полученного от процесса обезвоживания на стадии с);j) нагревание смеси синтез-газа первого (37) потока из стадии f) и природного газа в стадии h) с помощью физического тепла от восстановленного металлического продукта, полученного в зоне охлаждения (10);k) извлечение смеси синтез-газа и природного газа от стадии j) из зоны охлаждения (10) металлического продукта к газогенератору (3);l) нагревание газовой смеси из стадии k) инжектированием кислорода О 2 в магистраль (41) к смеси синтез-газа и природного газа и подведение смеси к газогенератору (3);m) обработка инжектированным кислородом О 2 газовой смеси со стадии l) в газогенераторе для получения восстановительной газовой смеси и подведение газовой смеси от газогенератора (3) к реакторуn) смешивание синтез-газа из стадии i) второго потока (19) с потоком восстанавливаемой газовой смеси стадии m) для обеспечения восстановительной газовой смеси; о) подача восстановительной газовой смеси, образованной на стадии n), к зоне восстановления (8) реактора. 2. Способ по п.1, характеризующийся тем, что дополнительно используют средства (24) обмена теплом для того, чтобы передать физическое тепло обезвоженного отходящего газа, образованного на стадии с), средствам (22) удаления СО 2 второй стадии (6) преобразования. 3. Способ по п.1, характеризующийся тем, что восстановительный газ покидает газогенератор нагретым до температуры между 800 и 1400 С, предпочтительно до 1200 С. 4. Способ по п.1, характеризующийся тем, что восстановительный газ поступает в зону восстановления (8) реактора, имея температуру 910 С или выше. 5. Способ по п.1, характеризующийся тем, что поток газа из второй стадии (6) преобразования разделяют на первый (32) и второй (33) потоки, из которых газ первого потока (32) используют в качестве горючего остаточного газа в парогенераторе (25), генерирующем тепло для второй стадии (6) преобразования, а газ второго потока (33) подают к третьей стадии (7) преобразования. 6. Способ по п.1, характеризующийся тем, что результатом следующих друг за другом первой, второй и третьей стадий (5, 6, 7) преобразования является поток практически чистого водорода Н 2. 7. Способ по п.1, характеризующийся тем, что нагревание на стадии m) достигают инжектированием предварительно определенного количества кислорода O2 и/или воздуха в смесь синтез-газа и природного газа, поступающую из зоны охлаждения (10). 8. Способ по п.1, характеризующийся тем, что азот N2 и оксид углерода, удаленные с помощью третьей стадии (7) преобразования, сжигают вместе с диоксидом углерода CO2, удаленным посредством второй стадии (6) преобразования. 9. Способ по п.1, характеризующийся тем, что в очистительную систему (4) дополнительно входит мультициклон (15) и последующий фильтр (16), через которые проходит отходящий реакторный газ. 10. Способ по п.1, характеризующийся тем, что на первой стадии (5) переработки применяют любой катализатор, известный в данном уровне техники, который пригоден для реакции конверсии водяного газа, например магнетит, любой переходный металл или оксид переходного металла, предпочтительно используемым является порода бурого железняка в форме кусков. 11. Способ по п.1, характеризующийся тем, что в третьей системе (7) преобразования используют любые физические средства разделения, такие как мембраны, или молекулярные сита, или любую соответствующую химическую систему поглощения. 12. Способ по п.11, характеризующийся тем, что третья система (7) преобразования включает молекулярное сито (34), которое включает любое соответствующее вещество, обладающее открытой структурой, такое как любой алюмосиликат, глина, активированный углерод или синтетический углерод. 13. Способ по п.1, характеризующийся тем, что обезвоженный отходящий газ из стадии с) охлаждают с помощью средств охлаждения (29) перед поступлением в компрессор или средства перекачивания(27). 14. Способ по п.1, характеризующийся тем, что устанавливают дополнительный нагреватель (43) для нагревания синтез-газа, полученного после третьей стадии (7) преобразования и перед позицией стадии h), в которой синтез-газ смешивают с природным газом. 15. Способ по п.14, характеризующийся тем, что поток отходящего газа из второй стадии (6) преобразования используют в качестве горючего газа в дополнительном нагревателе (43).
МПК / Метки
МПК: C21B 13/00, C21B 13/02
Метки: способ, восстановления, получения, железа, прямого
Код ссылки
<a href="https://eas.patents.su/9-17978-sposob-polucheniya-zheleza-pryamogo-vosstanovleniya.html" rel="bookmark" title="База патентов Евразийского Союза">Способ получения железа прямого восстановления</a>
Предыдущий патент: Транспортирующее и разъединительное устройство
Следующий патент: Термопластичный эластомерный блок-сополимер, способ его получения и содержащая его эластомерная композиция
Случайный патент: Фунгицидные смеси, содержащие замещенные 1-метилпиразол-4-илкарбоксанилиды