Система и способ для гидравлического разрыва подземного пласта
Формула / Реферат
1. Система для формирования активированной смеси жидкостей для гидравлического разрыва подземного пласта, содержащая:
(a) источник базовой жидкости разрыва;
(b) насос базовой жидкости, соединенный по текучей среде с источником базовой жидкости разрыва и сконфигурированный для увеличения давления базовой жидкости, по меньшей мере, до давления разрыва пласта;
(c) источник сжиженного природного газа (СПГ);
(d) сборку насоса СПГ, соединенную по текучей среде с источником СПГ и включающую узел насоса, сконфигурированный для увеличения давления СПГ, по меньшей мере, до давления разрыва, и нагреватель, предназначенный для испарения сжатого СПГ до газообразной фазы;
(e) смеситель жидкости разрыва, имеющий первый вход, соединенный по текучей среде с насосом базовой жидкости, второй вход, соединенный по текучей среде со сборкой насоса СПГ, и выход для соединения с устьевым отверстием скважины и для смешивания базовой жидкости и газообразного природного газа, чтобы сформировать смесь жидкостей разрыва, предназначенную для нагнетания в устьевое отверстие скважины.
2. Система по п.1, в которой узел насоса включает по меньшей мере один центробежный криогенный насос.
3. Система по п.2, в которой узел насоса включает насос высокого давления СПГ, соединенный по текучей среде по меньшей мере с одним криогенным насосом и рассчитанный, по меньшей мере, на давление разрыва пласта.
4. Система по п.1, в которой нагреватель включает по меньшей мере один теплообменник, соединенный по текучей среде с узлом насоса, чтобы получать сжатый СПГ, и термически соединенный с источником тепла, способным нагревать сжатый СПГ, по меньшей мере, до желательной температуры применения.
5. Система по п.1, в которой нагреватель является беспламенным каталитическим нагревателем.
6. Система по п.5, в которой беспламенный каталитический нагреватель включает по меньшей мере один каталитический элемент, сообщающийся по текучей среде с топливным газом и способный к окислению топливного газа, чтобы вырабатывать тепло, и трубопровод СПГ, термически соединенный, но изолированный по текучей среде от каталитического элемента и для подачи СПГ через него.
7. Система по п.6, в которой беспламенный каталитический нагреватель содержит множество каталитических элементов, расположенных концентрически вокруг трубопровода СПГ, формирующих каталитическую связку для одного прохода СПГ через беспламенный каталитический нагреватель.
8. Система по п.1, в которой смеситель включает главную линию потока, имеющую входной конец и выходной конец, коленчатый трубопровод, соединенный по текучей среде с главной линией потока между входным концом и выходным концом, коленчатый трубопровод, отходящий под острым углом от входного конца и, в основном, проходящий по пути линейного потока через главную линию потока, входной конец, предназначенный для приема потока базовой жидкости от насоса базовой жидкости и прямоугольного коленчатого трубопровода, предназначенного для получения потока природного газа от сборки насоса СПГ.
9. Система по п.1, в которой источник СПГ включает по меньшей мере один бак СПГ, и система дополнительно включает возвратный трубопровод для газообразного природного газа, соединенный по текучей среде с нагревателем, и бак для подачи сжатого газообразного природного газа в бак для поддержания давления.
10. Система по п.9, дополнительно включающая факел, трубопроводную факельную линию, соединенную по текучей среде с факелом и предохранительным клапаном, соединяющим трубопровод факельной линии с баком, таким образом, что газообразный природный газ может быть подан из бака к факелу.
11. Система по п.9, дополнительно включающая криогенный источник инертного газа, расширитель для сжижения инертного газа, соединенный по текучей среде с источником инертного газа и имеющий всасывающий клапан, соединенный по текучей среде с баком, чтобы получать газообразный природный газ из бака, и выпускной клапан, соединенный с баком, чтобы подать СПГ в бак, узел сжижения инертного газа, обеспечивающий испарение криогенного инертного газа в нем и способный создавать достаточное охлаждение для превращения газообразного природного газа в СПГ.
12. Система по п.1, в которой источник СПГ содержит множество баков СПГ, трубопровод паровой линии между баками, соединенный по текучей среде с каждым баком, и трубопровод линии жидкости между баками, соединенный по текучей среде с каждым баком.
13. Система по п.1, в которой источник базовой жидкости разрыва включает подачу жидкости разрыва и, дополнительно, по меньшей мере одного из расклинивающего агента и химического модификатора разрыва.
14. Система по п.13, в которой источник базовой жидкости разрыва включает по меньшей мере один из расклинивающего агента и химического модификатора разрыва, и система дополнительно включает смеситель, смешивания базовой жидкости и по меньшей мере одного расклинивающего агента и химического модификатора разрыва на входе смесителя.
15. Способ для гидравлического разрыва подземного пласта, включающий использование системы по п.1, содержащий:
(a) сжатие базовой жидкости и сжатие базовой жидкости, по меньшей мере, до давления разрыва пласта;
(b) сжатие сжиженного природного газа (СПГ) и сжатие СПГ, по меньшей мере, до давления разрыва с последующим нагреванием СПГ до тех пор, пока СПГ не будет выпарен до газообразной фазы;
(c) смешивание сжатой базовой жидкости и поддержание давления газообразного природного газа, чтобы сформировать смесь жидкостей гидравлического разрыва пласта;
(d) нагнетание смеси жидкостей разрыва через устьевое отверстие скважины и в скважину до контакта с пластом;
(e) продолжение нагнетания смеси жидкостей разрыва до разрыва пласта.
16. Способ по п.15, в котором базовая жидкость разрыва включает жидкость разрыва и, дополнительно, по меньшей мере один из расклинивающего агента и химического модификатора разрыва.
17. Способ по п.16, в котором базовая жидкость разрыва включает по меньшей мере один из расклинивающего агента и химического модификатора разрыва, и способ дополнительно включает смешивание жидкости разрыва по меньшей мере с одним расклинивающим агентом и химическим модификатором разрыва до смешивания базовой жидкости с природным газом.
18. Способ по п.15, в котором активированная жидкость разрыва является пеной.
19. Способ по п.15, в котором СПГ подается по меньшей мере из одного бака СПГ, и способ дополнительно включает подачу газообразного природного газа из бака СПГ к факелу.
20. Способ по п.15, в котором СПГ подается по меньшей мере из одного бака СПГ, и способ дополнительно включает прием газообразного природного газа из бака СПГ и охлаждение газообразного природного газа до состояния СПГ, выпаривая криогенный инертный газ и вводя газообразный природный газ в контакт с испаренным инертным газом.
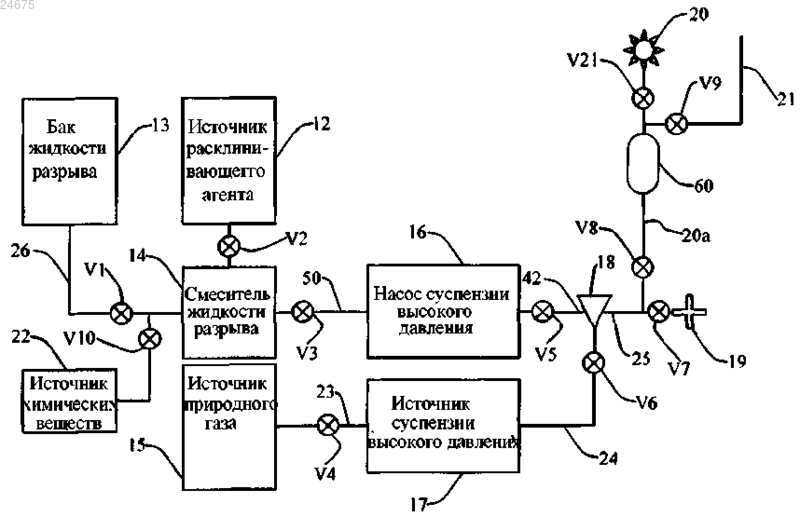
Текст
СИСТЕМА И СПОСОБ ДЛЯ ГИДРАВЛИЧЕСКОГО РАЗРЫВА ПОДЗЕМНОГО ПЛАСТА Изобретение относится к добыче углеводородов через новые и старые скважины и, в частности,к способу для разрыва подземного пласта, включающему: подготовку активированной жидкости разрыва путем смешивания газообразного природного газа и базовой жидкости разрыва в смесителе; нагнетание активированной жидкости разрыва через устьевое отверстие скважины в скважину; продолжение нагнетания активированной жидкости разрыва вплоть до разрыва пласта. Система для создания активированной жидкости разрыва, используемая для разрыва подземного пласта, включает источник базовой жидкости разрыва, источник природного газа и смеситель для приема природного газа из источника природного газа и базовой жидкости от источника базовой жидкости разрыва и смешивания природного газа и базовой жидкости разрыва, чтобы произвести активированную жидкость разрыва.(71)(73) Заявитель и патентовладелец: МИЛЛЕНИУМ СТИМЬЮЛЭЙШН СЕРВИСЕЗ ЛТД. (CA) Заявка на данное изобретение подана в пользу патентной заявки США 61433441, поданной 17 января 2011 г., и включает весь объем этой заявки в качестве ссылки. Область изобретения Настоящее изобретение в целом относится к системе способу разрыва гидравлического разрыва подземного пласта. Предпосылки создания изобретения Гидравлический разрыв пласта представляет собой известную технологию, используемую для повышения производительности существующих скважин, скважин низкого дебита, новых скважин и скважин, которые больше ничего не производят. Жидкости разрыва и расклинивающие материалы смешиваются в специальном оборудовании, затем перекачиваются через ствол скважины в подземный пласт, содержащий углеводородные материалы, которые подлежат добыче. Закачка жидкостей разрыва, которые несут расклинивающие материалы, заканчивается под высоким давлением, достаточным для разрушения подземного пласта. Жидкость разрыва вносит расклинивающие материалы в трещины породы пласта. После завершения закачки жидкости и нагнетания расклинивающего агента, давление уменьшается, и расклинивающий агент удерживает трещины открытыми. Скважина затем обрабатывается, чтобы удалить жидкость разрыва из трещин и пласта. После удаления достаточного объема жидкости разрыва добыча продукта возобновляется или начинается заново, используя улучшенные условия извлечения через созданную систему трещин. Например, в некоторых случаях, при добыче природного газа из угольных месторождений и месторождений метана, расклинивающие агенты не применяются, и простого гидравлического удара достаточно для обеспечения желательного повышения эффективности добычи. Неудачное удаление достаточного объема жидкости разрыва из пласта может заблокировать поток углеводородов и значительно уменьшить эффективность полученной системы трещин и производительность скважины. Чтобы улучшить извлечение жидкости разрыва, в операциях по гидравлическому разрыву пласта используются газы, преимущественно азот и двуокись углерода. Использование газов в процессе разрыва пласта, особенно двуокиси углерода и азота, нашло широкое применение в промышленности. При использовании этих газов объем жидкого компонента жидкости разрыва может быть уменьшен или этот компонент может не применяться. С меньшим количеством жидкости, используемой в операциях по гидроразрыву пласта и при высокой текучести и расширении газового компонента, жидкости разрыва намного легче удалить. Далее, замена жидкостей газами может обеспечить экономический эффект и экологические преимущества, снижая объем жидкости, используемой для завершения операции разрыва. В целом, составы, используемые для разрыва пласта, можно различать как чисто газовую среду (состав, состоящий почти из 100% газа включая двуокись углерода или азот), тумана (смеси, состоящей примерно из 95% газа (двуокиси углерода или азота, несущий жидкую фазу), пену или эмульсию (смесь, состоящую примерно из 50-95% газа, сформированной в сплошной в жидкой фазе), или активированную жидкость (смесь, состоящей примерно из 5-50% газа в жидкой фазе). Использование азота или двуокиси углерода с нефтью или основанной на воде жидкости разрыва было описано в технической литературе и может обеспечить определенные выгоды. Однако, несмотря на всю эту выгоду, использование азота или двуокиси углерода для разрыва пласта все еще может иметь некоторое неблагоприятное воздействие на процесс гидравлического разрыва пласта и создать проблемы во время извлечения жидкости разрыва, что увеличивает затраты и отрицательно воздействует на окружающую среду. Были предложены и другие газы, чтобы получить выгоду, связанную с добавлением газов к жидкостям разрыва, в то же время позволяющие избежать по меньшей мере некоторых трудностей, связанных с азотом и двуокисью углерода. В частности, для использования в гидравлическом разрыве пласта был предложен природный газ. Природный газ не разрушает коллекторские породы, инертным по отношению к жидкостям месторождения, извлекаемым без загрязнения газа месторождения и часто легко доступным. Однако, хотя использование природного газа для гидравлического разрыва пласта является реальным, оно потенциально опасно, и не было обеспечено подходящее и безопасное устройство и способ для гидравлического разрыва пласта, используя природный газ. Краткое описание изобретения Согласно одному варианту воплощения изобретения обеспечивается система создания активированной жидкости разрыва для гидравлического разрыва подземного пласта. Система включает: источник базовой жидкости разрыва; насос базовой жидкости соединенный по текучей среде с источником базовой жидкости разрыва и предназначенный для поддержания давления базовой жидкости, по меньшей мере равного давлению разрыва пласта; источник сжиженного газа ("LNG"); насос LNG соединенный по текучей среде с источником LNG и включающий узел насоса, предназначенный для сжатия LNG по меньшей мере до давления разрыва пласта и нагреватель, предназначенный для нагревания сжатого LNG до желательной температуры применения и смеситель жидкости разрыва. Смеситель имеет первый вход,соединенный по текучей среде с насосом базовой жидкости, второй вход, соединенный по текучей с насосом LNG и выход для соединения с устьевым отверстием скважины; смеситель используется для смешивания базовой жидкости с нагретым и сжатым природным газом, чтобы сформировать смесь жидко-1 024675 стей разрыва для нагнетания в устьевое отверстие скважины. Узел насоса может дополнительно включать по меньшей мере один центробежный криогенный насос, соединенный по текучей среде по меньшей мере с одним криогенным насосом; этот насос LNG создает давление, по меньшей мере равное давлению разрыва пласта. Нагреватель может включать по меньшей мере один теплообменник, соединенный по текучей среде с узлом насоса, чтобы получить сжатый LNG. Теплообменник также термически соединен с источником тепла и может нагреть сжатый LNG по меньшей мере до желательной температуры применения. Нагреватель может быть безрамным каталитическим нагревателем. Безрамный каталитический нагреватель может включать по меньшей мере один каталитический элемент, способный окислять топливный газ для выработки тепла, и трубопровод LNG,термически соединенный, но отделенный по текучей среде от каталитического элемента и служащий для прохода через него газа LNG Безрамный каталитический нагреватель также может включить множество каталитических элементов, расположенных концентрически вокруг трубопровода LNG, формирующего каталитическую связь для единственного прохода LNG через безрамный каталитический нагреватель. Смеситель может включать главный подающий трубопровод, имеющий входной конец и выходной конец, и коленчатый трубопровод, соединенный по текучей среде с главным подающим трубопроводом между входным концом и выходным концом. Коленчатый трубопровод проходит под острым углом от входного конца и, в основном, создает путь линейного потока через главный подающий трубопровод. Входной конец служит для приема потока базовой жидкости от основного жидкостного насоса, и коленчатый трубопровод служит для приема потока природного газа от насоса LNG Источник LNG может включать по меньшей мере один бак LNG, и система может дополнительно включать трубопровод возврата природного газа, соединенный по текучей среде с испарителем, и бак для подачи сжатого газообразного природного газа в бак для создания давления. Система может дополнительно включать факел, трубопровод факельной линии, соединенный по текучей среде с факелом и клапан сброса давления, соединенный по текучей среде с трубопроводом факельной линии к баку так, что газообразный природный газ из бака может быть подан на факел для сжигания. Система может дополнительно включать криогенный источник инертного газа, расширитель сжатого инертного газа, соединенный по текучей среде с источником инертного газа и имеющий впускной клапан, соединенный по текучей среде с баком для приема газообразного природного газа из бака, и выпускной клапан, соединенный с баком для подачи LNG в бак. Узел сжижения инертного газа позволяет криогенному инертному газу испаряться в баке с достаточным охлаждением, чтобы превратить газообразный природный газ в LNG. Источник LNG может включать несколько баков для LNG, трубопроводную линию между баками для передачи пара, соединенную по текучей среде с каждым баком, и трубопровод жидкостной линии между баками, соединенный по текучей среде с каждым баком. Источник базовой жидкости разрыва может включать узел подачи жидкости разрыва и дополнительно, по меньшей мере один из расклинивающих агентов и химический модификатор разрыва, а система может дополнительно включать смеситель для смешивания базовой жидкости по меньшей мере с одним из расклинивающих агентов и химическим модификатором разрыва на выходе смесителя. Согласно другому варианту воплощения изобретения оно обеспечивает способ разрываподземного пласта. Этот способ включает следующие стадии: обеспечение базовой жидкости и сжатие базовой жидкости по меньшей мере до давления разрыва пласта; обеспечение сжиженного газа (LNG) и сжатие LNG по меньшей мере до давления разрыва пласта, последующее нагревание LNG до желательной температуры применения; смешивание сжатый базовой жидкости и сжатого природного газа, чтобы сформировать активированную жидкость разрыва; нагнетание активированной смеси жидкостей разрыва через устьевое отверстие скважины в скважину, связанную с пластом; и продолжение нагнетания активированной жидкости разрыва вплоть до разрыва пласта. Базовая жидкость разрыва может включать жидкость разрыва и дополнительно, по меньшей мере один из расклинивающих агентов и химический модификатор разрыва. Базовая жидкость разрыва может включать по меньшей мере один расклинивающий агент и химический модификатор разрыва, и способ может дополнительно включать смешивание жидкости разрыва по меньшей мере с одним расклинивающим агентом и химическим модификатором разрыва до смешивания базовой жидкости с природным газом. Активированная жидкость разрыва может быть пеной.LNG может подаваться по меньшей мере из одного бака LNG, и способ может дополнительно включать подачу газообразного природного газа из бака LNG на факел. LNG может быть получен по меньшей мере из одного бака LNG, и способ может дополнительно включать прием газообразного природного газ из бака LNG и охлаждение газообразного природного газа до сжиженного состояния, выпаривая криогенный инертный газ и входя в контакт с испаренным инертным газом и с газообразным природным газом. Краткое описание чертежей Варианты воплощения изобретения будут теперь описаны со ссылками на приложенные чертежи. Фиг. 1 - блок-схема системы разрыва, используемой для нагнетания смеси жидкостей разрыва, состоящей из природного газа и базовой жидкости, в подземный пласт согласно по меньшей мере некоторым из вариантов воплощения. Фиг. 2 - блок-схема основных компонентов системы разрыва, показанной на фиг. 1, которая включает хранение сжатого природного газа и оборудование подачи согласно первому варианту воплощения. Фиг. 3 - блок-схема основных компонентов системы разрыва, показанной на фиг. 1, которая включает хранилище сжиженного газа (LNG) и оборудование подачи согласно второму варианту воплощения. Фиг. 4 - блок-схема основных компонентов насоса для разрыва с помощью LNG, используемого во втором варианте воплощения. Фиг. 5 - блок-схема смесителя природного газа и поток суспензии разрыва по меньшей мере для некоторых из вариантов воплощения. Фиг. 6 - блок-схема системы разрыва для нагнетания жидкости разрыва, содержащей поток чистого природного газа, в подземный пласт согласно третьему варианту воплощения. Фиг. 7 - блок-схема системы разрыва для нагнетания смеси жидкостей разрыва, содержащей природный газ и расклинивающий агент, в подземный пласт согласно четвертому варианту воплощения. Фиг. 8 - блок-схема системы разрыва для нагнетания смеси жидкостей разрыва, содержащей природный газ и базовую жидкость без расклинивающего агента, в подземный пласт согласно пятому варианту воплощения. Фиг. 9 - схема системы разрыва для нагнетания смеси жидкостей разрыва в подземный пласт, в котором система включает оборудование для выпуска природного газа и продувки оборудования согласно шестому варианту воплощения. Фиг. 10 - блок-схема хранилища LNG и оборудование регулирования пара, используемое во втором варианте воплощения. Фиг. 11 - блок-схема контроллера для управления системой гидроразрыва в некоторых вариантах воплощения. Фиг. 12 - схема примерного поверхностного оборудования по меньшей мере для некоторых вариантов воплощения системы разрыва. Фиг. 13 - вид в разрезе по линии I-I фиг. 10. Фиг. 14(а) и (b) - схема испарителя катализатора сжиженного газа, перекачиваемого насосом, в другом варианте воплощения. Фиг. 15 - схема последовательности технологических операций, иллюстрирующая способ разрыва подземного пласта смесью жидкостей разрыва, используя систему гидроразрыва, согласно по меньшей мере некоторым из вариантов воплощения. Подробное описание изобретения Введение. Последующее описание и описанные в нем варианты воплощения снабжены примерами конкретных вариантов воплощения и принципов настоящего изобретения. Эти примеры приведены в целях объяснения, а не ограничения этих принципов изобретения в его различных аспектах. В описании аналогичные части на всех фигурах обозначены одними и теми же цифровыми позициями. Фигуры не обязательно должны быть выполнены в масштабе, и в некоторых случаях соотношения, возможно, были увеличены, чтобы более ясно отобразить определенные признаки. Описанные здесь варианты воплощения предусматривают устройства, системы, и способы разрыва пласта в подземном месторождении с помощью смеси жидкостей разрыва, включающей природный газ и базовую жидкость, или с помощью природного газа разрыва. В первом варианте воплощения обеспечивается система разрыва, которая нагнетает смесь жидкостей разрыва, содержащую природный газ и базовую жидкость, в которой природный газ хранится как сжатый природный газ (CNG), и в которой базовая жидкость может включать жидкость разрыва, расклинивающий агент и загуститель. Во втором варианте воплощения обеспечивается система разрыва, которая нагнетает в скважину смесь жидкостей разрыва, включающую природный газ и базовая жидкость, в которой природный газ хранится как LNG, и в которой базовая жидкость может включать жидкость разрыва, расклинивающий агент и загуститель. В третьем варианте воплощения обеспечивается система разрыва, которая нагнетает жидкость разрыва,состоящую только из потокаприродного газа. В четвертом варианте воплощения обеспечивается система разрыва, которая нагнетает смесь жидкостей разрыва, состоящую только из потока природного газа и расклинивающего агента. В пятом варианте воплощения обеспечивается система разрыва, которая нагнетает смесь жидкостей разрыва, включающую природный газ и базовую жидкость, в которой базовая жидкость не содержит расклинивающего агента. В шестом варианте воплощения обеспечивается система разрыва, который нагнетает смесь жидкостей разрыва, включающую природный газ и базовую жидкость и которая включает оборудование для подачи природного газа и для продувки системы. Каждый из этих вариантов воплощения будет описан ниже более подробно. Термин "природный газ", как он используется здесь, означает либо только один метан (СН 4), либо смесь метана с другими газами, такими как другие газообразные углеводороды. Природный газ часто представляет собой смесь, состоящую примерно из 85-99% метана (СН 4) и 1-15% этана (С 2 Н 6) с небольшим количеством компонентов пропана (С 3 Н 8) бутана (С 4 Н 10) и пентана (С 5 Н 12) со следами более длинных цепей углеводородов. Природный газ, как он используется здесь, может также содержать инертные газы, такие как двуокись углерода и азот различных пропорциях, хотя объемы примерно выше 30% предложили бы дополнительную выгоду, полученную от его применения. CNG относится к сжатому природному газу, LNG относится к сжиженному газу. Поток природного газа для гидравлического разрыва пласта может быть обеспечен как газ при давлении с расходом, достаточном для осуществления гидравлического разрыва пласта подземного месторождения. Поток природного газа может быть смешан с базовой жидкостью, чтобы сформировать смесь жидкостей разрыва, или введен как чистый поток (т.е. без базовой жидкости), или смешан только с расклинивающим агентом. Базовая жидкость может включать жидкость разрыва, такую как обычная углеводородная жидкость для обслуживания скважины, жидкость разрыва, содержащая один несколько расклинивающих агентов и/или дополнительно загустители или модификаторы реологии, такие как смазки. Гидравлическая энергия для создания трещины в пласте подземного месторождения получена благодаря сжатию газообразного природного газа и базовой жидкой смеси на поверхности с общим расходом, достаточным для передачи необходимой энергии в подземное месторождение. После выполнения операции гидроразрыва пласта природный газ и сопутствующая жидкость, используемые для образования трещин,могут быть извлечены, и примененный активированный природный газ направляется к существующим установкам для обработки и продажи. Обеспечивается система разрыва, который включает оборудование для хранения компонентов смеси жидкостей разрыва, оборудование для нагнетания смеси природного газа и жидкости разрыва в подземное пласт, например в нефтяную скважину или газовую скважину, и оборудование для извлечения и разделения жидкостей, извлеченных из скважины. В некоторых вариантах воплощения источник природного газа - сжатый газ (CNG) в баллонах и перекачивается насосом, дополнительно сжимающим природный газ до подходящего давления разрыва пласта. В других вариантах воплощения сжатый газ хранится в герметичных емкостях под давлением выше давления разрыва пласта и просто выпускается в поток разрыва. В некоторых вариантах воплощения источник газа - емкость, содержащая сжиженный газ(LNG) и соединенная с насосом для гидроразрыва, повышающим давление LNG до давления разрыва пласта и нагревающим сжатый поток LNG. Эффективное хранение газообразного природного газа достигается при максимально возможном давлении, которое обычно не меньше 30 МПа. Сжатие природного газа до величины, необходимой для гидравлического разрыва пласта, может быть достигнуто его подачей в газообразной фазе. Были применены компрессоры газовой фазы, создающие давление около 100 МПа, которое является подходящими для сжатия природного газа до давления разрыва пласта. Потоки жидкости разрыва, содержащие природный газ, улучшают удаление жидкости разрыва из скважины и, следовательно, отдачу пласта после разрыва. Использование природного газа позволяет избежать несовместимости жидких компонентов, что часто встречается при использовании двуокиси углерода или азота как активирующей среды. После завершения операции разрыва компоненты природного газа извлекаются вместе с жидкостью разрыва и нефтью и/или газом месторождения. Введенный природный газ извлекается в существующую систему переработки нефти или газа с небольшой помехой нормальному функционированию. Это позволить отказаться от выпуска газа в отдельный трубопровод или сжигания в факеле, типичного для операции по отделению жидкости гидроразрыва пласта от коммерческого газа. Кроме того, использование природного газа в потоке жидкости разрыва позволяет использовать местный доступный газ, чтобы получить выгоду от газифицируемого потока жидкости разрыва без обширной логистики, связанной с азотом или двуокисью углерода. Фиг. 1 представляет собой общее описание основных компонентов системы разрыва согласно тем вариантам воплощения, в которых используется смесь жидкостей разрыва, включающая природный газ и базовую жидкость, которая может содержать расклинивающий агент и/или химическую добавку. Жидкость разрыва хранится в баке жидкости разрыва (13), расклинивающий агент хранится в баке расклинивающего агента (12) и химические добавки, такие как загуститель, хранятся в баке (22) химических добавок. Природный газ хранится в емкости (15) природного газа, и поток природного газа подается насосом высокого давления (17) в смеситель (18) жидкости разрыва через трубопровод (24). Природный газ, хранящийся в емкости (15), может быть сжатым природным газом или сжиженным газом. Насос высокого давления (17) природного газа является компрессором, если сжатый природный газ является источником или специальным насосом разрыва пласта сжиженного газа, если сжиженный газ является источником. Выход от насоса природного газа высокого давления (17), независимо от состояния источника газа, находится в газообразном состоянии. В смесителе (18), поток природного газа от трубопровода (24) объединяется с основным потоком жидкой фазы из трубопровода (42); эта базовая жидкость может включать жидкость разрыва, дополнительно объединенную с расклинивающим агентом и химической добавкой. Объединенная смесь разрыва пласта затем входит в скважину (19) через трубопровод (25), течет вниз по стволу скважины на пласт месторождения, создавая гидравлическую трещину, используя расход и давление смеси жидкостей разрыва. После подачи желаемых материалов разрыва пласта в скважине (19), нагнетание прекращается, и операция разрыва завершается. После операции по гидроразрыва пласта и в период, считаемый достаточным для разрыва пласта, скважина (19) открывается для потока, направляемого в трубопровод (20 а) и затем поступает в емкость разделителя (60) в котором, газы отделяются от жидкостей. Начальный поток из скважины будет состоять, в основном, из введенных материалов разрыва пласта, и емкость разделителя (60) используется, чтобы отделить введенный природный газ от извлекаемого потока, поступающего через трубопровод (20 а). Жидкости и твердые тела, выходящие из емкости разделителя (60), направляются в баки или хранилища (не показаны). Природный газ от извлекаемого потока выходит из разделителя (60) и первоначально направляется к факелу (20), пока поток не будет стабилизирован, и затем направляется в трубопровод (21) для обработки и продажи. В дальнейших вариантах воплощения предлагаются способы разрыва пласта скважины, используя природный газ или смесь природного газа и базовой жидкости. Ряд конкретных способов относится к безопасному и надежному применению природного газа в виде сжиженного газа. Способы использования LNG для местного хранения позволяют эффективно хранить значительные объемы газа под атмосферным давлением. Как криогенная жидкость, одна единица объема LNG содержит приблизительно шестьсот объемов газа при атмосферных условиях. Таким образом, требуется меньшее количество емкостей-хранилищ и очень низкое давление хранения и подачи сниженного газа по сравнению со сжатым природным газом. Точно так же, сжатый природный газ со сверхвысоким давлениям, с которыми сталкиваются при гидравлическом разрыве пласта, LNG жидкой форме является исключительно эффективным. Опять же, в жидкости объемный расход очень снижен и LNG относительно несжимаем по сравнению с сжатым природным газом, нагревание при сжатии устраняется, и размер и количество оборудования значительно сокращаются. Это значительно снижает сложность операции, удаляя многие из затрат и опасностей, которые присутствовали бы с известными методиками. Кроме того, с меньшим количеством элементов оборудования, функционирующих при низких давлениях с меньшим количеством соединений между оборудованием, использованием LNG обеспечивает необходимую простоту для частого перемещения оборудования между скважинами. Инертный криогенный газ при температуре близкой или ниже температуры сжиженного газа позволяет быстро, эффективно и безопасно предварительно охладите скважинный глубинный насос природного газа и нагреватель до рабочей температуре до ввода криогенного LNG. Это устраняет или минимизирует использование LNG для охлаждения, избегая, таким образом, ненужного сжигания в факелах и от потенциальных проблем безопасности, связанных с системой охлаждения огнеопасного сжиженного газа. Местное объединение перекачки криогенного сжиженного газа и системы нагрева наиболее эффективно, комбинируя систему перекачки и нагрева в одном агрегате. Бак-хранилище LNG функционирует под повышенными давлениями, чтобы устранить или минимизировать утечку газа во время хранения. Повышенное давление также позволяет применить бустерное нагнетание при извлечении LNG из бака-хранилища при расходах разрыва, обеспечивая, таким образом,подачу газа к насосам LNG. Как боковой поток, пары от насоса разделения LNG при необходимости направляются в бак-хранилище LNG для поддержания давления в емкости и увеличения этого давления. Энергия для нагревания LNG может быть получена многими путями, где в предпочтительном варианте воплощения используется тепло, которое вырабатывается без применения огня. Такое тепло для портативной установки может быть получено из окружающей среды, отработанного тепла из двигателя внутреннего сгорания, каталитической камеры сгорания или элемента электрического нагрева. Альтернативно, тепло может быть выработано, используя пламенный источник тепла, местный для нагревателя или отдаленный от процесса, как это диктуется требованиями техники безопасности. Следовательно, описанные здесь варианты воплощения предусматривают систему гидроразрыва и способ использования системы разрыва и смеси жидкостей разрыва, чтобы образовать трещины в подземном пласте. Природный газ, используемый в смеси жидкостей разрыва, может быть легко доступен по приемлемой стоимости, безвреден для окружающей среды и коммерчески извлекаем. Его использование в качестве газовой фазы выгодно, чтобы повысить добычу нефти и газа после разрыва пласта, и он также является подходящей заменой жидкости разрыва, снижая, таким образом, воздействие на окружающую среду и затраты на разрыв пласта. Способность извлекать газ через существующее оборудование и устройства для ведения добычи может, в основном снизить объем сжигания в факеле, сэкономить время на пуск скважины в производство и получить непосредственные доходы от газа из скважины. Кроме того, методика применима к обычным и нетрадиционным нефтяным и газовым скважинам и подходит для разрыва с помощью базовых углеводородных жидкостей, воды и других базовых жидкостей и кислот. Первый вариант воплощения: система разрыва, используя смесь жидкостей разрыва, включающую базовую жидкость и природный газ из источника сжатого природного газа. Согласно первому варианту воплощения на фиг. 2 показана система для разрыва пласта подземного месторождения, через которое проходит скважина, используя смесь жидкостей разрыва. Смесь жидкостей разрыва формируется, смешивая поток природного газа с базовой жидкостью, в которой природный газ получен от источника сжатого природного газа. Базовая жидкость включает жидкость разрыва и может дополнительно включить химический увеличитель вязкости и расклинивающий агент. Более конкретно, жидкость разрыва может быть нефтью, водой, метанолом, кислотой или их комбинациями, если это желательно. Расклинивающий агент может быть природным песком или произведенными частицами. Химические добавки будут продуктами, обычно применимыми для увеличения вязкости жидкости, снижения трения или создания желательных свойств. Основные компоненты описываемой системы включают бак для жидкости разрыва, оборудование для приготовления и подачи базовой жидкости для смешивания с потоком природного газа, емкость для природного газа, оборудование для передачи потока природного газа для смешивания с базовой жидкостью, смеситель для смешивания базовой жидкости и потока природного газа, чтобы сформировать смесь жидкостей разрыва, и оборудование для подачи смеси жидкостей разрыва к устьевому отверстию скважины. Определенные компоненты системы разрыва перечислены ниже. Бак (13) для жидкости разрыва пласта, подходящий для хранения воды или углеводородной жидкости соединен через трубопровод(26) со смесителем (14) жидкостей разрыва и с увеличителем вязкости химических веществ, добавляемых через трубопровод из емкости (22) с химическими добавками. Баки (13) для жидкости разрыва могут быть любыми емкостями, используемыми в промышленности для гидравлического разрыва пласта и могут включать более одного бака или другой подходящего устройства для хранения достаточного объема жидкости. Трубопровод (26), как и все другие трубопроводы, показанные на фиг. 2, является трубой или шлангом с достаточной пропускной способностью. Смеситель (14) получает жидкость разрыва повышенной вязкости и смешивает расклинивающий агент из емкости (12) для расклинивающего агента с жидкостью разрыва, чтобы сформировать базовую жидкость, которая находится теперь в виде суспензии. Смеситель (14) является многоцелевым устройством, которое извлекает жидкость из бака жидкости разрыва с помощью центробежного насоса (не показан), получает химические вещества из емкости (22) с химическими добавками и смешивает их с жидкостью разрыва, часто в самом центробежном насосе. Жидкость разрыва объединена с расклинивающим агентом, поступающим из емкости подачи расклинивающего агента (12) в смесительную камеру или в другой смеситель (14) и затем извлекается другим центробежным насосом, установленным на смесителе (14). Примером типичной смесительной установки является установка МР 1060 компании National Oilwell Varco, установленная на трейлере. Примером емкости для расклинивающего агента (12) являются емкость 110m3, способная выдавать 9 тонн расклинивающего агента в минуту. Созданный жидкий раствор базовой жидкости затем перекачивается через трубопровод от смесителя (14) к насосу высокого давления (16) для подачи суспензии. Насос высокого давления (16) для подачи суспензии поддерживает давление потока базовой жидкий на уровне давления разрыва пласта и соединен через трубопровод (25) со смесителем (18) жидкости разрыва. Примером насоса высокого давления для разрыва пласта является поршневой насос Quintuplex с дизельным приводом, установленный на трейлере и имеющий мощность до 1500 кВт или 2000 л.с. В качестве насоса (16) могут использоваться несколько насосов. Некоторые из упомянутых компонентов могут быть объединены, например, смеситель (14) и насос высокого давления (16) для подачи суспензии могут быть выполнены как один узел. В этом варианте воплощения источник природного газа используются одна несколько емкостей(15), содержащих сжатый природный газ (CNG). Примером емкости, применяемой для хранения и транспортировки сжатых природных газов, является установленный на трейлере бак компании LincolnComposition TITAN Tank, содержащий до 2500 см 3 (89000 scf) CNG при давлении до 25 МПа. Емкость(15) - хранилище CNG соединено с компрессорным насосом природного газа высокого давления, представленным здесь как насосы (127 а, 127b, 127 с), соединенный через трубопровод (123) с распределительным клапаном (V4) и используемым для сжатия газа до давления разрыва пласта. Сжатие может быть достигнуто любым насосом, способным к повышению давления потока газа, например, могут быть применены поршневые компрессоры, обеспечивающие высокое давление, требуемое для гидравлического разрыва пласта. Обычно компрессоры имеют постоянный коэффициент сжатия так, что для достижения давления разрыва пласта может потребоваться многоступенчатое сжатие. Точно так же, чтобы достигнуть желательного расхода, кратное число ступеней компрессора может быть применено параллельно. Компрессорный насос (127 а, 127b, 127 с) имеет три ступени сжатия, хотя может быть необходимо большее или меньшее число ступеней сжатия, чтобы достигнуть желательного давления на выходе. Потоком сжатого природного газа от емкости-хранилища (15) к компрессорным насосам природного газа высокого давления (127a, 127b, 127 с) управляют с помощью клапана (V4). Компрессорный насос (127 а,127b, 127 с) соединен со смесителем жидкости разрыва (18) через трубопровод (24) с газовым распределительным клапаном (V61). Потоком природного газа под давлением от насосов компрессора природного газа высокого давления (127 а, 127b, 127 с) к смесителю жидкости разрыва (18) управляют с помощью клапана (V61). Если давление сжатого газа в емкости выше давления разрыва пласта, поток газа можно регулировать через клапаны (V4) и (V61), непосредственно соединенных со смесителем суспензии через трубопровод (128) с обходом компрессорного насоса природного газа высокого давления (127a, 127b,127 с), используя клапан (V4). Второй вариант воплощения: система разрыва с использованием смеси жидкостей разрыва, включающей базовую жидкость и природный газ от источника сжиженного газа. Как показано на фиг. 3, 10-14 и согласно второму варианту воплощения обеспечивается система разрыва пласта, в которой используется смесь жидкостей разрыва, включающая базовую жидкость и природный газ от источника сжиженного газа. В частности, система разрыва включает хранилище LNG и подсистему управления паром для хранения LNG и подсистему управления паром для нагрева LNG до температуры применения. В этой системе природный газ смешивается с базовой жидкостью. В этом варианте воплощения LNG нагревается до температуры, при которой природный газ находится в паровой фазе, однако в других вариантах воплощения природный газ может быть нагрет до температуры, при которой природный газ остается в жидкой фазе. На фиг. 3 показана система разрыва фиг. 1 с указанным хранилищем LNG и подсистемой управления паром. В этом варианте воплощения источник (215) природного газа является одной из нескольких емкостей, содержащих сжиженный газ (LNG). Примером емкости, используемой для хранения природного газа, является установленный на салазках транспортер LNG фирмы EKIP Research and Production Company, содержащий 35,36 м 3 жидкого природного газа с давлением до 0,6 МПа. LNG обычно хранится под атмосферным давлением при температуре примерно -162 С. Емкость-хранилище LNG (215) соединена с насосом природного газа высокого давления (229), через подающий трубопровод LNG (223) с подающим клапаном (V42). Насос природного газа высокого давления (229) служит для повышения давления LNG до давления разрыва пласта с помощью узла (230), Природный газ высокого давления обеспечивается нагревом сжатого LNG с помощью нагревателя (231) насоса (229). Подающий трубопровод (223) является специальным трубопроводом для LNG, например типа 4014SS Cryogenic 50 Series, поставляемым компанией JGB Enterprises Inc. Замена жидких объемов, удаленных из емкости-хранилища LNG (215) достигается направлением потока созданного сжатого газа от нагревателя (231) через возвратный трубопровод (232) с контролем потока обратным клапаном (V11). Свежий пар регулируется, чтобы создать подходящее давление в емкости LNG (215). Передача LNG из емкости-хранилища (215) к насосу природного газа (229) поддерживается потоком возвратного пара через обратный трубопровод (232), обеспечивая достаточное давление источнике природного газа (215) для подачи потока LNG на вход природного газа высокого давления насоса (229). В одной конфигурации насос (229) природного газа разрыва объединяет сжатие и нагревание LNG в однопроцессорном узле, например в одном корпусе на автономных салазках с приводом. Однако эти стадии могут быть выполнены на отдельных узлах. Все компоненты, которые входят в контакт сLNG, должны быть подходящими для криогенного обслуживания. Потоком природного газа под давлением от насоса (229) к смесителю потока суспензии природного газа (18) управляют с помощью клапана(V6) и через подающий трубопровод природного газа 24. Как показано на фиг. 10 и 13, подсистема хранения LNG и управления паром используется для хранения и управления LNG, используемого в системе гидроразрыва. Управление хранением LNG необходимо, чтобы обеспечить безопасную рабочую зону, где хранится LNG до его использования. При хранении при температуре -162 С и атмосферном давлении LNG будет медленно нагреваться, и происходит испарение жидкости, чтобы поддерживать ее равновесное состояние. Произведенные газы затем при необходимости извлекаются из бака, чтобы избежать превышения давления. Подсистема хранения LNG и управления паром LNG включает источник LNG (215), который может быть одним или несколькими баками LNG (715). Управление давления в каждом из этих баков (715) достигается предохранительным клапаном V18 с параметрами разгрузки, устанавливаемыми на основании расчета конструкции бака. Предохранительный клапан (V18) связан с каждым резервуаром (715) через трубопровод сбора пара (62), и паропровод между баками (61), который, в свою очередь, соединен с паровой линии 63 в каждом резервуаре. В одной конфигурации предохранительный клапан (V18) соединен с трубопроводной линией, подводящей газ к факелу 20 (соединение трубопровода 720 а с факелом 20 не показано на чертежах), где отведенные пары газа безопасно сжигаются. Альтернативно, собранный пар может быть снова превращен в жидкость и закачен обратно в бакхранилище LNG (715), создавая безопасную, эффективную и безвредную для окружающей среды замкнутую систему обработки пара: трубопровод собранного пара (62) соединен с трубопроводом (53) через клапан (V17) и с установкой сжижения азота (55). Источник жидкого азота (57) подает сжиженный азот через трубопровод подачи азота (52) на установку сжижения азота (55), в которой испарение азота обеспечивает достаточное охлаждение, чтобы повторно превратить пары природного газа в жидкость LNG. Произведенный LNG затем прокачивается через возвратный трубопровод (54) в жидкостную линию загрузки емкостей LNG (715); возвратный трубопровод (54) также обеспечивает заполнение баков (715) по мере необходимости. Баки LNG (715) соединены по текучей среде через свои линии загрузки жидкости(54) и через трубопровод (56), чтобы гарантировать равномерное распределение LNG между всеми баками. Кроме того, баки LNG (715) соединены по текучей среде через свои линии подачи пара (63) и трубопровод (61). Возвратный трубопровод 232 насоса 229 природного газа разрыва, показан как трубопровод (732) на фиг. 10 и 13, и служит для возврата сжатого природного газ обратно в баки (715), чтобы создать необходимое давление в баках (715). Поток из возвратного трубопровода (732) регулируется, используя клапан (V22), который, в свою очередь, соединен с трубопроводом (61). Жидкий природный газ подается из баков в насос 229 природного газа разрыва через трубопровод 223; потоком из каждого бака управляет управляющий клапан (V42). В альтернативном варианте воплощения баки LNG (715) могут выдерживать давление 2 МПа прежде, чем потребуется сбросить давления. При загрузке этих баков (715) средой LNG в нормальных условиях -162 С повышенное разгрузочное давление задержит выпуск газа до тех пор, пока температура не достигнет уровня, близкого к -110 С. С минимальным приростом тепла, обеспечиваемым свойствами термоизоляции баков LNG и при нормальном цикле использования утечка газа фактически может быть устранена. Кроме того, повышенное разгрузочное давление в источнике LNG (55) гарантирует небольшие ошибки в поддержании давления во время перекачки насосом пара от LNG в нагреватель (31) и возможность повысить внутреннее давление баков, чтобы гарантировать надежную подачу к насосу (229) природного газа разрыва, и избежать открытия предохранительных клапанов во время процесса разрыва пласта. На фиг. 4 представлена блок-схема, иллюстрирующая основные узлы насоса (229) природного газа разрыва. LNG полается к узлу (230) насоса из подающего трубопровода (223). Узел насоса включает центробежный криогенный насос (233), насос LNG высокого давления (235) и трубопровод (234), цепь соединения криогенного центробежного насоса (233) и насос LNG (235). Соответствующее давление подачи к насосу LNG (235) высокого давления необходимо, чтобы гарантировать отсутствие блокировки пара или кавитации в цикле закачки. Могут быть применены одиночные или многостадийные центробежные криогенные насосы (233) в зависимости от требований по давлению подачи и расходу, чтобы поддерживать работу насоса LNG высокого давления (235). Примером центробежного криогенного насоса (233),обеспечивающего давление подачи и расход является бустерный насос 236 компании ACD Industries,обеспечивающий расход до 1,5 м 3/мин и высоту нагнетания LNG до 95 кПа. Насос LNG высокого давления (235) используется для поддержания давления LNG по меньшей мере до 35 МПа и при необходимости до 100 МПа, чтобы обеспечить достаточное давление разрыва пласта. Чтобы достичь таких давлений,может использоваться поршневой насос, хотя также могут быть применены другие типы насосов, создающие достаточный расход и давление. Примером такого насоса является криогенные насосы серии 5-SLS компании ACD Industries, обеспечивающие давление 124 МПа с расходами LNG до 0,5 м 3/мин. Могут быть применены одноступенчатые или многоступенчатые насосы LNG высокого давления (235),соответствующие требованиям расхода для разрыва пласта. Мощность для привода насосов (233) и (235) может быть получена от двигателя внутреннего сгорания через прямую передачу, электродвигателя или гидравлического двигателя, если желательно. Сжатый LNG, выходящий из насоса высокого давления (235) направляется в нагреватель (231) по трубопроводу (236), чтобы нагреть природный газ до температуры применения, которая в этом конкретном варианте воплощения изменяет фазу природного газа от жидкости до газа. Как правило, минимальная температура для нагрева LNG составляет примерно -77 С, и эта температура лежит в диапазоне, где многие углеродистые стали переходят от аустенитного до мартенситного кристаллического состояния с соответствующим изменением в металлургическом процессе. В одном варианте воплощения конечная температура природного газа, подводимого к трубопроводам (24) и (232) находится в диапазоне от 0 до 20 С, чтобы избежать проблем замерзания жидкости, с которой среда входит в контакт, и обеспечить гибкость уплотнений. Нагреватель (231) включает систему теплообмена, обеспечивающую передачу тепла LNG, и в этом варианте воплощения включает первый теплообменник (237), второй теплообменник(239), выходной патрубок первого теплообменника и подающий трубопровод (238) природного газа, который проходит от подающего трубопровода 236 и через эти два теплообменника 237, 239, и который соединен с подающим трубопроводом 24 и снабжен возвратным клапаном (V11). Возвратный клапан(V11), в свою очередь, соединен с возвратным трубопроводом (232). В этом варианте воплощения LNG сначала нагревается источником тепла (240), в качестве которого используется горячий воздух, продуваемый через змеевик первого теплообменника (237) вентилятором(не показан). LNG при температуре порядка -162 С может получить значительную энергию из воздуха,приводя к снижению тепловой нагрузки. Выход из первого теплообменника (237) затем направляется к змеевикам теплообменника во втором теплообменнике (239) через подающий трубопровод (238). Во втором теплообменнике (239) LNG нагревается до конечной целевой температуры другим источником тепла(241). Энергия, полученная от этого второго источника тепла (241), должна быть значительной, чтобы поддержать быстрое нагревание LNG. Источник тепла (241) может быть осуществлен без пламени и может быть в виде отработанного тепла от двигателя внутреннего сгорания, тепла из каталитической камеры сгорания или электрического элемента. Альтернативно, тепло может быть выработано, используя пламенный источник тепла, местный или удаленный от скважины, как диктуется требованиями техники безопасности. Сжатого природного газа подается через подающий трубопровод (24) с газовым распреде-8 024675 лительным клапаном (V6) к смесителю суспензии потока природного газа (18). Как только природный газ был достаточно нагрет (в этом конкретном варианте он находится в газообразном состоянии), он перекачивается по подающему трубопроводу (24) и смешивается с базовой жидкостью в смесителе (18). Давление жидкой среды, обрабатываемой в смесителе (18), может быть значительным, абразия жидкости может быть значимым фактором, и утечек нужно избежать. Для пропускной способности важным является эффективное смешивание составляющих. Хотя можно использовать различные типы смесителей, наиболее подходящий смеситель (318) для сжатого природного газа и потока суспензии разрыва показан на фиг. 5. Смеситель суспензии потока природного газа (318) служит для объединения и смешивания потока базовой жидкости от трубопровода (342) с газообразным потоком природного газа от подающего трубопровода (324) в корпусе (343) смесителя. Достижение хорошего объединения потока жидкости разрыва, расклинивающего агента и потока газообразного природного газа может способствовать созданию желательной структуры и поведения смеси жидкостей разрыва для активированной жидкости, пены или тумана. Например, создание подходящей пены требует газовой фазы, которая будет полностью рассеяна в жидкой фазе пузырьками, размер которых должен быть как можно меньше. Достаточная дисперсия может быть достигнута многими способами, один из которых представлен штуцерным устройством (344) в трубопроводе потока природного газа, который на основе уменьшения проходного сечения увеличивает скорость потока природного газа. Контакт потока природного газа с потоком жидкости разрыва с высокой скоростью обеспечивает хорошее смешивание. Для выполнения смешивания могут использоваться другие механизмы, включая внутренние диверторы, турбулизаторы и различные статические или динамические смесители. Для безопасного управления потоком разрыва, содержащим природный газ, следует принять во внимание, что содержащие газы жидкие растворы могут иметь очень высокие скорости, которые могут быстро разрушить компоненты, работающие под давлением. Объединение потока суспензии базовой жидкости с потоком природного газа с дальнейшей транспортировкой полученной смеси через трубопроводы в ствол скважины делается на основе того факта,что частицы расклинивающего агента воздействуют на изменения пути следования потока, что может привести к отказу узлов и опасной утечке огнеопасного газа. Как таковой, смеситель (18) сконструирован так, что он позволяет базовой жидкости, содержащей расклинивающий агент, проходить, в основном, по прямому пути через смеситель. Например, трубопровод (342) базовой жидкости может иметь, в основном, линейный внутренний диаметр, а трубопровод (324) может соединять трубопровод (342) под углом. Например, в одном варианте воплощения смеситель (18) включает главную линию потока, имеющую входной конец и выходной конец, при этом трубопровод с прямоугольным коленом соединен по текучей среде с главной линией потока между входным концом и выходным концом, причем трубопровод с прямоугольным коленом проходит под острым углом от входного конца и, в основном, по пути линейного потока через главную линию потока, причем входной конец получает поток от источника базовой жидкости разрыва, а трубопровод с прямоугольным коленом служит для приема потока от источника природного газа. После выхода из корпуса смесителя (343) смесь жидкостей разрыва направляется через трубопровод (325) к устьевому отверстию скважины и вниз по стволу скважины, чтобы создать гидравлический удар в пласте подземного месторождения. Показанная на фиг. 11 система разрыва может управляться дистанционно контроллером (58); конфигурация и работа контроллера (58) описаны ниже в шестом варианте воплощения. В этом втором варианте воплощения функции управления контроллером (58) выполняются с помощью беспроводной связи с управляемыми компонентами, как показано на фиг. 11. Область применения может включить управление по проводам или используя комбинацию проводной и беспроводной связи. В этом варианте воплощения предполагается контроллер (58) в автоматизированной станции управления, установленной в кабине на шасси грузового автомобиля. Системой можно управлять, чтобы разрешить прокачку только природного газа или жидкости, только жидкой суспензии или любой желательной комбинации природного газа, жидкости и жидкой суспензии. В некоторых применениях природный газ будет использоваться только для части обработки, такой как предварительная обработка или продувка. Альтернативно, будут прокачиваться только жидкость или жидкая суспензия, снова с жидкостью как предварительная подушкой, подушкой или промывка и только в жидкой суспензии на стадии обработки. После обработки оборудование отключается, клапан (V7) устьевого отверстия скважины закрывается, и делаются приготовления для переезда на новое место или для завершения другой обработки для разрыва пласта. Емкости-хранилища LNG крепятся с закрытием клапанов (V4) и открытием клапана (V18). Клапан (V5) закрыт, и клапан (V8) открыт, чтобы обеспечить удаление природного газа высокого давления из обрабатывающей линии природного газа (24), обрабатывающей линии (25) и насоса (229). Когда система высокого давления приводится к номинальному давлению, насосы (229) LNG разрыва включаются на малой мощности, чтобы удалить LNG из трубопровода (23) в насосы и через нагреватели с выгрузкой через трубопроводные линии (24), (25), через клапан (V8), разделитель (60) и факелу (20). Альтернативно, клапан (V13) может быть открыт, чтобы продуть систему высокого давления. Клапан (V8) или клапан (V13) может быть в виде дроссельного клапана для регулирования давления и расхода газа, подаваемого в разделитель и факельную систему. Одновременно из источника инертного газа (45) через трубопровод (46) подается газообразный азот по трубопроводу (23), чтобы снизить давление LNG через LNG насосы (229) жидкости разрыва на факел (20). После вытеснения всех газоконденсатных жидкостей из трубопровода низкого давления (23), клапан (V14) открывается для выпуска газа и полной очистки системы низкого давления. Соответственно, открывается клапан (V15) и газообразный азот направляется через линию (24) обработки природного газа (24), чтобы закончить очистку системы высокого давления. Во всех случаях поток передается к факелу до тех пор, пока содержание природного газа не будет значительно ниже огнеопасного предела. Содержание природного газа может быть оценено монитором содержания углеводорода в потоке газа. После полной очистки системы от природного газа обрабатывающая линия могут быть удалена от скважины (19) и начинается оценка обработки разрывом. Поток снова инициируется через открытый впускной клапан (V7) устьевого отверстия скважины с клапаном (V8) факельной линии при открытом клапане (V20) и закрытом клапане (V9) трубопровода. Поток направляется через линию(20 а) в разделитель (60) на факел (20). Разделитель (60) захватывает жидкости и твердые тела и пропускает газ к факелу. Жидкости накапливаются в разделителе (60) и вытекают из него в емкости-хранилища,не показанные на чертеже. Полученные твердые тела могут включать мелкие частицы продуктивного пласта и расклинивающего агента, которые собираются в емкости разделителя (60) и удаляются из него при необходимости непрерывной работы разделителя. После достижения стабильного потока и достаточного давления газовой фазы, чтобы направить поток в трубопровод, факел закрывается клапаном(V21), и поток направляется в трубопровод сбыта (21) через входной клапан (V9). Поток из скважины(19) продолжает направляться через разделитель (60) с газом к трубопроводу (21) до тех пор, пока обработка разрывом достаточно не откачана из скважины до получения чистой нефти и оценки скважины. Затем скважина может быть введена в эксплуатацию. На фиг. 14 показано альтернативное устройство для нагревания LNG, которое включает каталитический нагреватель для использования в насосе для гидроразрыва с помощью LNG. Каталитические элементы (66) излучают тепло, выделяемое окислением топливного газа, такого как природный газ, пропан или другое подходящее топливо с кислородом в присутствии катализатора, например платины. Топливный газ с воздухом нагнетается в каталитические элементы с выделением тепла, излучаемого к трубе теплообменника LNG (67). Это обеспечивает энергию, которая должна быть достаточной для нагреваLNG до температуры применения. На схеме фиг. 14 восемь каталитических элементов (66) расположены концентрически в вокруг трубы теплообменника LNG (67), формируя каталитическую сборку (68) для одиночного прохода через каталитическую систему нагрева. Через каждую трубу теплообмена LNG (69) проходит природный газ, и труба имеет ребра своей наружной поверхности, чтобы увеличить площадь нагреваемой поверхности и служит для передачи тепла стенке трубы теплообменника (69) для нагревания LNG Четыре сборки показаны как четыре группы из восьми каталитических элементов в каждой сборке, нагревающей трубу теплообменника LNG (67). Поток LNG выходит из соседнего подогревателя через трубопровод (238), ведущего к двум из каталитических сборок в этой конфигурации. На схеме также показано, что LNG, выходящий из одной каталитической сборки (68), направляется к другой каталитической сборке (68) для дополнительного нагревания. Конфигурация и расположение каталитических сборок и пути прохождения потока через каталитические сборки могут быть различными в зависимости от желательной цели нагревания. Каталитические элементы обычно производят 35 британских тепловых единиц/час (Btu/h) на каждый квадратный дюйм (15 кВ/м 2) площади поверхности, так, что восемь сборок элементов шириной 26" (0,67 м) и длиной 120" (3 м) производят более чем 870.000 Btu/h (255 кВт) энергии. Для показанных четырех сборок системы доступен уровень выработки тепла, приближающий к 1025 кВт энергии. Этот уровень энергии более чем достаточен, чтобы обеспечить теплоемкость (160 см 3/мин),необходимую для насоса для гидроразрыва с помощью LNG при соблюдении безопасности и компактного расположения. При каталитическом процессе, рабочая температура поверхности каталитического нагревательного элемента находится в диапазоне от 370 до 540 С, что значительно ниже температуры самовоспламенения природного газа в воздухе (580 С). Таким образом, каталитический нагреватель обеспечивает реально безопасный, беспламенный источник тепла для нагревания потенциально огнеопасногоLNG. Третий вариант воплощения: система разрыва для нагнетания жидкости разрыва, включающей поток чистого природного газа. Согласно третьему варианту воплощения и со ссылкой на фиг. 6 обеспечивается устройство для гидроразрыва пласта, в котором используется жидкость разрыва в виде потока чистого природного газа,в котором "чистый" означает отсутствие базовой жидкости или компонентов расклинивающего агента. Разрыв пласта потоком чистого природного газа может быть выгодным в ситуациях, где любая жидкость является нежелательной, и расклинивающий агент не является необходимым, чтобы поддерживать созданную систему гидроразрыва во время производства. Это часто имеет место для разлома угольного пласта, содержащего метан, или сланцевых пластов с низким давлением, где удаление жидкости может быть затруднено. В этом варианте воплощения источник природного газа (415) является одной или несколькими емкостями, содержащими либо сжатый природный газ, либо сжиженный газ. Источник природного газа (415) соединен с насосом природного газа высокого давления (417) через трубопровод (423) с клапа- 10024675 ном (V44) для контроля подачи природного газа. Насос природного газа высокого давления представляет собой компрессор, служащий для сжатия газа в случае источника CNG, и является криогенным насосом и нагревателем в случае источника LNG. Приготовленный поток природного газа прокачивается насосом высокого давления (417) через трубопровод (24) с клапаном (V74) и трубопровод (425) в устьевое отверстие скважины (19). Поток чистого газа затем идет вниз по стволу скважины, чтобы создать гидравлический разрыв пласта подземного месторождения. Четвертый вариант воплощения: система разрыва для нагнетания смеси жидкостей разрыва, включающей природный газ и расклинивающий агент, но без жидкости разрыва. Согласно четвертому варианту воплощения и со ссылкой на фиг. 7 обеспечивается устройство для гидроразрыва и конфигурация, в которой используется поток природного газа и расклинивающего агента, но без жидкости разрыва. Разрыв потоком природного газа, содержащего только расклинивающий агент, может быть выгоден в ситуациях, когда нежелательна любая жидкость, и в производственных условиях расклинивающий агент должен обслуживать созданную систему гидроразрыва. Это часто имеет место при разрыве угольного пласта, содержащего метан или разрыве сланцевого пласта с низким давлением, где удаление жидкости может оказаться трудным. В этом варианте воплощения источник природного газа (515) является одной или несколькими емкостями, содержащими либо сжатый природный газ,либо сжиженный газ. Источник природного газа (515) соединен с насосом природного газа высокого давления (517) через трубопровод (523) с клапаном (V45) для контроля подачи природного газа. Насос природного газа высокого давления (517) является компрессором, в котором применяется сжатие газа в случае источника CNG, и он является криогенным насосом и нагревателем в случае источника LNG. Поток природного газа выходит из насоса природного газа высокого давления (517) через трубопровод(524). Источник (512) расклинивающего агента с распределительным клапаном (V25) пересекает трубопровод (524). Источник (512) расклинивающего агента поддерживает давление, соответствующего давлению на выходе насоса природного газа высокого давления (517). Расклинивающий агент выходит из источника (512) под действием силы тяжести в трубопровод (524) с добавлением расклинивающего агента, управляемого клапаном (V25). Полученный жидкий раствор природного газа продолжает движение по трубопроводу (524), через клапан (V75) трубопровода (525) и в устьевое отверстие скважины (19). Поток газа и расклинивающего агента затем течет вниз по стволу скважины, чтобы создать гидравлический разрыв пласта подземного месторождения. Пятый вариант воплощения: система разрыва для нагнетания смеси жидкостей разрыва, включающей природный газ и базовую жидкость без расклинивающего агента. Согласно пятому варианту воплощения и со ссылкой на фиг. 8, обеспечивается устройство для гидроразрыва, в котором используется смесь жидкостей разрыва, включающая природный газ и базовую жидкость без расклинивающего агента. Разрыв пласта с такой смесью жидкости разрыва может быть выгоден в ситуациях, когда в созданной системе гидроразрыва желательна жидкая часть, а расклинивающий агент не является необходимым для поддержания созданной системы разрыва во время этой операции. Это часто случай для кислотного разрыва карбонатных пластов, где используется активированный природный газ или кислотная пена,создания и в системе травления трещин. В этом варианте воплощения емкость жидкости разрыва (13) содержит желательную жидкость. Трубопровод (26) используется для передачи жидкости в смеситель(614), в который также направляются химические вещества от химического источника (22), которые смешиваются с жидкостью. Выход смесителя (614) проходит через трубопровод (650) с управляющим клапаном (V36) и поступает в насос высокого давления (616). Выход жидкости из насоса высокого давления (616) направляется в смеситель жидкости разрыва (618) по трубопроводу (642) с управляющим клапаном (V56). Источник природного газа (15) является одной или несколькими емкостями, содержащими либо сжатый природный газ, либо сжиженный газ. Источник природного газа (15) соединен с насосом природного газа высокого давления (17) через трубопровод (23) с клапаном (V4) для контроля подачи природного газа. Насос природного газа высокого давления - компрессор, применяющий сжатие газа в случае источника CNG, и являющийся криогенным насосом и нагревателем в случае использования LNG. Поток природного газа выходит из насоса природного газа высокого давления (17) и подается через трубопровод (24) и клапан (V6) в смеситель (618) для потока суспензии природного газа, где она объединяется с потоком жидкости разрыва из трубопровода (42). Поток смеси природного газа и жидкости выходит из смесителя (618) и по трубопроводу (625) направляется в устьевое отверстие скважины(19). Поток смеси природного газа и жидкости затем течет вниз по стволу скважины, создавая гидравлический разрыв пласта подземного месторождения. Шестой вариант воплощения: система разрыва пласта, имеющая оборудование для отвода природного газа и продувки. Согласно шестому варианту воплощения, система разрыва на природном газе может дополнительно включать оборудование для продувки, очистки и/или отделения природного газа ("оборудование для выпуска, очистки и отделения"). Такое оборудование предпочтительно, чтобы снизить риски, связанные с природным газом, являющимся огнеопасным источником газа высокого давления. Оборудование может включать использование криогенного инертного охлажденного газа для предварительного охлаждения насоса природного газа высокого давления или охлаждения другого оборудования до использования природного газа. Это избавляет от необходимости предварительно охлаждать систему, используя огнеопасный природный газ и устраняет необходимость удаления природного газа сжиганием в факеле или иным образом. Инертный газ также может использоваться для испытания системы разрыва под давлением, чтобы обнаружить любые утечки или отказы в работе или использовать любую конфигурацию или функциональное тестирование системы. Кроме того, инертный газ может использоваться для замены любого источника природного газа, чтобы быстро очистить систему от любого остаточного природного газа, кислорода или воздуха до, во время или после операции разрыва пласта. В случае утечки или соответствующего отказа во время операции разрыва пласта, оборудование для выпуска, очистки и удаления позволяет найти компонент, который будет изолирован с тем, чтобы остальные элементы системы не были затронуты. На фиг. 9 представлен вариант воплощения системы разрыва, имеющей хранилище жидкости разрыва и оборудование питания, как показано на фиг. 1 с оборудованием для выпуска, продувки и отделения природного газа. Оборудование для выпуска, продувки и отделения включает ряд клапанов V12-V16,соединенных по текучей среде с трубопроводами (23, 24, 42, 50) для подачи природного газа и базовой жидкости в системе, источник инертного продувочного газа (45) для очистки компонентов системы (и дополнительно криогенного охлаждения таких компонентов), ряд подающих трубопроводов (46, 47) инертного газа для подачи инертный газ в природный газ и базовой жидкости через трубопроводы подачи (23, 24, 42, 50) и выпускные трубопроводы (48, 49, 51) для продувки газов из подающих трубопроводов (23, 24, 42, 50). Может также быть обеспечен контроллер (58) (см. фиг. 11) для управления операциями выпуска, продувки и отделения. Продувка выполняется до введения природного газа в систему из клапана (V4) через оборудование и трубопроводы к клапану (V7) устьевого отверстия скважины, т.е. подающий трубопровод (23), насос природного газа (17), трубопровод (24), смеситель (18) и трубопровод (25). В настоящей системе удаление газа, сопровождаемое продувкой, выполняется на всех содержащих природный газ трубопроводах и оборудовании после операции разрыва пласта и до демонтажа оборудования для транспортировки. Выпуск и продувка могут потенциально охватывать систему от клапана (V5) и далее по линии до клапана(V3), (в котором выпуск осуществляется через клапан (V16) и трубопровод (51) к факелу (20) для устранения избыточного давления в обратном направлении, и от источника выпускного клапана природного газа (V4) через оборудование и трубопроводы к клапану (V7) устьевого отверстия скважины. Дополнительно, и в случае незапланированного выпуска природного газа из-за отказа узла, поврежденный узел может быть внутренне изолирован и природный газ, остающийся в изолированных компонентах системы, извлекается продувкой. Для продувки и выпуска природного газа из части системы низкого давления, источник (45) продувочного инертного газа соединен через подающий трубопровод (46) инертного газа и клапан (V12) источника инертного газа с трубопроводом подачи природного газа (23) после выпускного клапана (V4) природного газа и перед насосом высокого давления (17). Это расположение позволяет подать инертный газ в секцию низкого давления подающего трубопровода природного газа (23). Дополнительно, выпускной трубопровод (48) вместе с выпускным трубопроводом (49) присоединен к подающему трубопроводу (23) природного газа через выпускной клапан (V14), который расположенным на выходе клапана (V4) источника выпускного природного газа и на входе насоса высокого давления (17); этот выпускной трубопровод (48) соединен с выпускным трубопроводом (49), который, в свою очередь, соединен с трубопроводом (20 а) факела (20). Это устройство позволяет направить инертный газ и природный газ из подающего трубопровода природного газа (23) на факел (20). Для продувки части высокого давления системы природного газа, источник (45) продувочного инертного газа соединен с секцией высокого давления подающего трубопровода природного газа (24)(который расположен на выходе насоса природного газа высокого давления (17 через трубопровод (47) подачи инертного газа и клапан источника инертного газа (V15). Кроме того, выпускной трубопровод(49) с трубопроводом (20 а) факельной линии соединен с трубопроводом подачи (24) природного газа на выходе насоса природного газа высокого давления (17) через выпускной клапан (V13). Это устройство позволяет с помощью инертного газа продуть трубопроводом подачи (24) природного газа и газов, подаваемых из этого трубопровода (24) на факел (20). Для продувки и выпуска части жидкости разрыва высокого давления системы из скважины, трубопровод (20 а) факельной линии через клапан (V8) соединен с трубопроводом (25) подачи жидкости разрыва на входе клапана (V7), и смесителем (18) на выходе подающего трубопровода (42) базовой жидкий и разделительных клапанов (V5) и (V6). Это устройство позволяет продуть трубопровод (25) с помощью газовой среды от источника (45) через трубопровод (47), открытый клапан (V15), смеситель (18) и трубопровод (25); при этом клапаны (V13), (V5), (V7) закрыты. Кроме того, это устройство позволяет удалить газ из трубопровода подачи (25) жидкости разрыва с подачей газа на факел (20) через клапан V8 и трубопровод (20 а) факельной линии. Кроме того, трубопровод (50) подачи базовой жидкости соединен с факелом (20) через выпускной клапан (V16) и выпускной трубопровод (51); это устройство позволяет направить газы, извлекаемые из базовой жидкости на факел (20), например в случае возникновения внутренней утечки, и природный газ входит в основное хранилище жидкости и часть подачи системы. Выпускное и продувочное Оборудование обеспечивает изоляцию, выпуск газа и продувку системы,чтобы сделать ее безопасной при любых приемлемых условиях. Например, если возникнет утечка в смесителе (18) жидкости разрыва, изолирующие клапаны (V5), (V6) и (V7) могут быть немедленно закрыты,чтобы отделить утечку от других частей системы. Питательные клапаны (V3) и (V4) закрываются и клапан (V8) открывается, чтобы направить все газы в изолированную неисправную часть системы и к факелу (20), контролируя и устраняя выход потока природного газа из мешалки суспензии (18). Как другой пример, клапан (V14) может быть открыт, чтобы продуть содержимое трубопроводов и оборудования между клапанами (V4) и насос (17) природного газа высокого давления через выпускные трубопроводы(48), (49) и трубопровод факельной линии (20 а). Точно так же клапан (13) может быть открыт, чтобы продуть содержимое участка между трубопроводом и оборудованием между насосом (17) природного газа высокого давления и клапаном (V6) через выпускные трубопроводы (49) и трубопровод (20 а) факельной линии. Продувка может быть инициирована через впускные клапаны (V12) и (V15) и направление среды для продувки из источника инертного газа (45) через трубопроводы (46) и (47) подачи инертного газа. Поток продувочного газа может быть направлен различными путями в трубопроводы природного газа и жидкости разрыва (23), (24), (25) и выпускные трубопроводы (48) и (49) и к трубопроводу факельной линии (20 а), управляя клапанами (V12), (V15), (V13), (V14), (V6), (V5), (V8) и (V16), если необходимо продуть всю систему. Источник (45) продувочного инертного газа состоит из хранилища для хранения инертной среды,подходящей для продувки с устройством, подходящим для перемещения продувочной среды через систему. В одном варианте воплощения продувочная среда является инертным газом, таким как двуокись углерода или азот, и может храниться либо как криогенная жидкость, либо как сжатый газ. Можно завершить продувку с инертной средой в газообразной фазе, но в некоторых случаях и/или в последующих процессах, таких как охлаждение системы, инертная жидкость может использоваться в жидкой фазе. В зависимости от выбора инертной среды и ее фазы, движущаяся через систему продувочная среда будет проходить по распределительному клапану, насосу или насосу с нагревателем, которые в одном варианте воплощения не показаны, но содержатся в источнике (45) продувочного инертного газа, и которые в другом варианте воплощения могут быть существующим оборудованием. Вышеописанная конфигурация оборудования выпуска и продувки и способ для выпуска и продувки при использовании такого оборудования относится конкретно к системе гидроразрыва, представленной на фиг. 1. Однако такое оборудование выпуска и продувки может быть легко приспособлено для других систем гидроразрыва, например показанных на фиг. 2, 3, 6-8. Используя LNG в качестве источника природного газа, как показано в варианте воплощения на фиг. 3, источник (45) продувочного инертного газа может быть источником жидкого азота, и насос (229) природного газа разрыва, охлажденного до криогенных температур, проверяется под давлением, используя азот. В таком варианте воплощения опасности, с которыми сталкиваются при завершении этих стадий, используя LNG, могут быть снижены или устранены. Жидкий азот извлекается из источника (45) через линию (46) к насосу (229) природного газа разрыва. Внутренние криогенные узлы насоса природного газа разрыва (229), заполняются жидким азотом, который испаряется при контакте с теплыми компонентами. Созданный пар удаляется в атмосферу через трубопровод факельной линии (20), пока внутренние части достаточно не охладятся так, что жидкий азот больше не испаряется. Как показано на фиг. 11, работа система разрыва включая оборудование для продувки и удаления газа, может управляться дистанционно контроллером (58). Этот контроллер (58) имеет память, запрограммированную для управления работой по меньшей мере некоторых компонентов системы. Контроллер (58) может связываться с компонентами в системе прямой связью или беспроводным соединением. Например, смеситель жидкостей разрыва (814), насос природного газа высокого давления (817) и насос суспензии высокого давления (816) могут управляться дистанционно. Клапаны (V1)-(V16) также могут управляться дистанционно. Дистанционное управление обеспечивает доступное и надежное управление операции из центра управления плюс позволяет управлять системой в процессе ее нормального функционирования и, в частности, в чрезвычайной ситуации, не подвергая персонал опасности. Управление узлами осуществляется оператором или системой через пользовательский интерфейс (59) или с помощью программного обеспечения, содержащего алгоритмы, хранящиеся в памяти контроллера и разработанные для управления узлами, чтобы выполнить задачу наиболее эффективным образом. Контроллером может быть любая подходящая система управления процессом и может включать управляющие входы от пультов управления оператора или компьютера. Подобная способность управления применима к другим описанным конфигурациям и другим компонентам. Например, контроллер (58) управляет операцией питательного клапана (V4) и насосом природного газа высокого давления (817), регулируя, таким образом, подачу сжатого природного газа из его источника (815) к смесителе для создания суспензии потока природного газа (18). Одновременно контроллер(58) управляет работой распределительного клапана (V1) жидкости разрыва, чтобы отрегулировать, поток из бака (813) жидкости разрыва, клапаном (V2) подачи расклинивающего агента, чтобы отрегулиро- 13024675 вать поток из источника расклинивающего агента (812), химический источник (822) и смеситель жидкостей разрыва (814) для подачи должным образом созданного раствора суспензии к насосу высокого давления (816). Другие функции управления также выполняются контроллером (58), соединенным с насосом высокого давления (816) для перекачки суспензии. Контроллер (58) также обеспечивает пропорционально смешивание природного газа и жидкости в созданном потоке суспензии, управляя относительной подачей потока природного газа разрыва пласта по сравнению с потоком жидкой суспензии, управляя насоса высокого давления (816) для перекачки суспензии и насосом природного газа высокого давления(814). Контроллер (58) соединен с клапанами (V3), (V5), (V6), (V7), (V8), (V10), (V11), (V12), (V13), (V14),(V15) и (V16) и источником (845) инертного газа для управления утечки газа, продувкой и контроля условий компонентов системы. В этом отношении память контроллера может хранить инструкции по выполнению продувки и удаления газа, как описано выше. Способ выполнения работ. Фиг. 15 - технологическая схема способа формования смеси жидкостей разрыва, которая содержит природный газ как газовую фазу в достаточном количестве, чтобы по желанию изменить характеристики операции разрыва. На стадии (80) достаточное количество природного газа сделано доступным, чтобы завершить операцию разрыва пласта. Операция разрыва пласта может быть связана с потреблением значительного количества жидкости разрыва общим объемом более 500 м 3 с нетрадиционными объемами потребления жидкости разрыва пласта порядка 4000 м 3. Применение любого приемлемого количества природного газа для операции разрыва может быть в диапазоне от 50.000 до 300.000 см 3 газа в течение периода закачки 4-6 ч. Чтобы отвечать требованиям расхода, природный газ хранится в ожидании закачки для большинства применений. Хранилище природного газа может быть завершено либо путем его хранения сжатом виде в баллонах, либо хранением сжиженного газа в криогенных емкостях. Эффективное хранилище природного газа в сжатом виде достигается при максимальном возможном давлении, которое обычно меньше 30 МПа в объеме примерно 10.000 см 3 в каждом узле. Эффективное хранилище этих количеств даже при максимальных давлениях потребовало бы нескольких герметичных емкостей с многочисленными соединениями между баками и насосным оборудованием при повышенных давлениях хранения. Альтернативно, сжиженный газ (LNG) может храниться в локальных баках LNG, которые позволяют эффективно хранить значительные объемы под атмосферным давлением. Как криогенная жидкость,одна единица объема LNG содержит примерно шестьсот объемов газа в атмосферных условиях. В одной емкости-хранилище LNG, содержащем 60 м 3 LNG, хранится эквивалент 36000 см 3. Большой объем работы потребовал бы примерно 10 баков-хранилищ LNG по сравнению с более чем 30 емкостями сжатого природного газа. Использование LNG устраняет проблемы, связанные с хранением газовой фазы; для подачи природного газа потребуется множество емкостей высокого давления и трубопроводов в очень сложной и потенциально опасной системе. Стадия (81) фиг. 15 относится к обработке достаточного количества природного газа до давления разрыва пласта. Давления разрыва часто находятся в диапазоне от 35 до 70 МПа при расходе природного газа от 400 до 1200 см 3/мин. Дополнительное сжатие сжатого природного газа до давления разрыва требует применения компрессоров газовой фазы. Альтернативно, сжимая природный газ до сверхвысоких давлений, с которыми сталкиваются при гидравлическом разрыве пласта, жидкая форма газа типа LNG является исключительно эффективной. В жидкости объемные параметры очень снижены и несжимаемы по сравнению с газообразным природным газом, нагревание при сжатии отсутствует, и размер и количество оборудования значительно сокращаются. Криогенный жидкий природный газ непосредственно сжимается до давления разрыва пласта с помощью одного насоса, и затем просто нагревается до температуры применения. Для верхнего предела давления газа разрыва LNG прокачиваться с расходом примерно 2 м 3/мин жидкости, приводя к расходу газа свыше 1500000 см 3/день через 8 узлов с расходом до 160 см 3/мин каждый. Эта небольшая и более простая конфигурация оборудования значительно снижает сложность операции и удаляет многие из затрат и опасностей, которые имели бы место при методиках сжатого газа. На стадии (82) поток природного газа объединяется с потоком базовой жидкости. Как описано выше, для объединения этих двух потоков в линии высокого давления до подачи в скважину или в устьевое отверстие скважины может использоваться смеситель (18); этот подход обеспечивает легкое манипулирование отдельными потоками без перерыва типичных операций по разрыву пласта, заканчивая задачу без модификации скважины и является простым и эффективным способом смешивания природного газа и потоков жидкости - суспензии. Это приводит к простому, эффективному и надежному способу смешивания этих компонентов. Альтернативно, поток базовой жидкости может быть объединен с потоком природного газа в процессе с низким давлением или в стволе скважины при давлении разрыва. Природный газ вводится вниз в ствол скважины по одному трубопроводу и жидкий раствор вниз по другому, и эти два потока объединяются в некоторый момент в стволе скважины. В этих случаях обеспечивается некоторый тип специализированного устьевого отверстия скважины или конфигурации ствола скважины в виде дополнитель- 14024675 ного трубчатого и общего пространства, где эти два потока могут встретиться. В одном варианте воплощения стадия (80) включает подачу сжиженного газа, хранящегося в криогенных емкостях, стадия (81) включает использование криогенного насоса, чтобы поднять давление сжиженного газа до давления разрыва пласта при подходящем расходе и использование теплообменника для нагревания жидкого природного газа до температуры применения; и стадия (82) включает объединение природного газа с базовой жидкостью в смесителе (18), чтобы получить конечную жидкость разрыва до ее прохождения к устьевому отверстию скважины. Примеры Следующие примеры предназначены только для иллюстрации реализации способа и не ограничивают объем изобретения. Пример 1. Фиг. 12 - схема варианта воплощения, показывающая конфигурацию, где компоненты системы разрыва пласта природным газом смонтированы на ряде мобильных прицепов. Мобильные прицепы транспортируют оборудование для создания и сжатия суспензии разрыва, основанной на базовой жидкости; смеситель (14) жидкостей разрыва, химический источник (22), насос высокого давления (16) плюс транспортное оборудование для хранения, поддержания давления и нагревания сжиженного газа; бакхранилище LNG (215) и насосы (229) LNG разрыва и вспомогательное оборудование; источник (45) продувочного инертного газа и контроллер (58). Конфигурация и устройство любого узла могут быть изменены, или по желанию оборудование может быть установлено временно или постоянно. Этот вариант воплощения иллюстрирует множество баков-хранилищ LNG (215), соединенных с множеством насосов (229) LNG разрыва. Предварительное испытание под давлением насоса системы накачки жидкости и расклинивающего агента, компоненты (14),(16), (22) и трубопроводы (26), (50), (42), (25) заполняются жидкостью разрыва (13) или другой подходящей жидкостью, как желательно. Подача жидкости (13), добавление расклинивающего агента (12), добавление химических веществ (22), смешивание расклинивающего агента (14) и сжатие жидкой суспензии (16) завершается в компонентах оборудования, как показано на чертеже, и передачей жидкой суспензии на линию обработки (42). Баки-хранилища LNG соединены с трубопроводом (62) для продувки к факелу (20) через факельную линию (20 а) до начала обработки, когда клапан (V18) закрыт. Трубопровод(46) соединяет источник инертного газа (45) с входным трубопроводом (23) для подачи жидкого азота к насосам LNG для криогенного охлаждения, продувки предварительной обработки и тестирования под давлением системы трубопроводов подачи LNG (23), насосного оборудования, нагревательной аппаратуры (229) и линии трубопровода природного газа (24). Источник инертного газа (45) также соединен с трубопроводом (24) природного газа, чтобы обеспечить продувку или очистку газообразным азотом системы высокого давления, если это требуется. Выкаченный или продутый природный газ может быть направлен к разделителю (60) и к факелу(20) или через выпускной трубопровод (49) с клапаном (V13) или через трубопровод (20 а) с клапаном(V8). Точно так же, трубопровод низкого давления (23) может быть продут газообразным азотом или газ может быть удален через трубопровод (46) и подан через выпускной трубопровод (48) к разделителю(60) и далее к факелу (20) через клапан (V14). Охлаждение и продувка завершаются направлением с жидкого азота через трубопроводы (46) и (23) на вход насосов (229) LNG разрыва. В свою очередь каждый из насосов (229) LNG разрыва загружают жидким азотом до его охлаждения до температуры приемаLNG без испарения. Испаренный азот выпускается из насосов (229) LNG через трубопровод природного газа (24), клапан (V6), трубопровод факельной линии (20 а) к факелу (20). После охлаждения каждого насоса LNG клапан факела (V8) закрывается, и азот, прокачанный и нагретый установками LNG, обеспечивает испытание системы с азотом под высоким давлением. Система подачи базовой жидкости изолирована в течение этого процесса закрытым клапаном (V5). После завершения испытания под давлением системы накачки природного газа открывается клапан (V8), давление сбрасывается, источник азота отключается клапаном (V12) и питательные клапаны LNG (V4) открываются, чтобы пропустить поток LNG в систему. Насосы (229) LNG разрыва вводятся в действие, чтобы вытеснить азот из системы с LNG в процессе подготовки к началу операции по гидроразрыву пласта. Выход от насосов LNG жидкости разрыва направляется через трубопровод (24) обрабатывающей линии на факельную линию (20 а) до тех пор, пока природный газ не будет виден как факел. Затем клапан (V8) закрывается, клапаны (V5), (V6) и(V7) открываются, и начинается обработка по разрыву пласта. LNG извлекается из баков (215) через трубопровод (23) в насосы (229) LNG разрыва для сжатия и нагревания с выгрузкой через трубопровод (24) обрабатывающей линии природного газа. Поток суспензии базовой жидкости из трубопровода (42) в смеси с газообразным потоком природного газа из трубопровода (24) подается в смеситель (18) жидкости разрыва и направляется на скважину (19) по трубопроводу (25) обрабатывающей линии. Пример 2. Используя устройство, например устройство фиг. 3, 9 и 11, предлагаем пример применения системы, чтобы иллюстрировать способ. Цель состоит в стимулировании газового месторождения на глубине 2500 м загрузкой 100 т расклинивающего агента, используя 75% тонкой взвеси реагента на водной основе для снижения поверхностного натяжения для разрыва пласта с природным газом. Скважина имеет перфорационный канал на глубине 2500 м с креплением скважины 114,3 мм без системы трубопроводов при статической температуре в забое 90 С. В этом примере источник природного газа выбран как сжиженный газ (LNG) и соответствующее устройство с применением конфигурация фиг. 3. Таблица 1 Гидроразрыв с использованием природного газа Оборудование доставлено к месту расположения скважины и размещено. Для данной обработки конкретное оборудование включает один из насосов высокого давления (16) мощностью 1127 кВт, семь насосов (229) LNG разрыва производительностью 1170 см 3/мин, две емкости для жидкости (13) емкостью 60 м 3 и три бака LNG (215). Источник продувки инертным газом заполнен жидким азотом. Имеется химический источник (22), содержащий две добавки. Осуществляется проверка безопасности перед проведением операции разрыва с детализацией опасности участка, местоположение аппаратуры, обеспечивающей безопасность работы, безопасные места и план эвакуации. Оборудование вводится в действие в порядке, конфигурация которого определена на фиг. 9 и 11, включая адаптацию исходных операций по гидроразрыву пласта с использованием LNG, представленную на фиг. 3. Емкости для жидкости (13) загружены 119 м 3 воды, и баки-хранилища LNG (215) содержат 168 м 3 LNG Емкость для расклинивающего агента (12) загружена 10 т просеянного песка размером ячейки сита 50/140 и 90 т просеянного песка размером ячейки сита 30/50. Химический источник (22) загружен 107 л понизителя трения и 308 л пенящимся поверхностно-активного вещества. Затем выполняется испытание системы под давлением, близком к ожидаемому давлению нагнетания порядка 57.000 кПа, и испытание компонентов высокого давления завершается при давлении 69000 кПа. Управление клапаном и работа устройств завершается под управлением контроллера (58). Тест под давлением жидкой части системы от выпускного клапана (V1) бака с жидкостью разрыва пласта до клапана управления обработки устьевого отверстия скважины (V7) заканчивается с водой из баков(13). Чтобы создать давление испытания на герметичность клапаны испытания (V1), (V3), (V6), (V7),(V8), (V10) и (V16) закрываются. Затем открывается клапан (V1), чтобы подать воду к смесителю (14) жидкостей разрыва. Смеситель жидкостей разрыва работает под давлением, обычно меньше 700 кПа и не должен иметь утечек жидкости. Клапан (V3) затем открывается для подачи питательной воды к насосу(16) для подачи суспензии высокого давления. Выпускное открытие (не показано) на обрабатывающей линии (42), перед клапаном (V5) открывается, чтобы обеспечить поток через насос высокого давления. Насос высокого давления (16) медленно вращается, чтобы захватить подачу воды и когда весь поток воды проходит через выпускное отверстие, насос полностью заполнен жидкостью, и отверстие закрывается. Весь персонал покидает участок, и к насосу высокого давления (16) подводится дополнительная мощность для увеличения давления в самом насосе плюс в трубопроводах (42) и (25) обрабатывающей линии, клапанах (V5), (V6), (V7) и (V18) и смесителе (18) для суспензии природного газа до необходимого испытательного давления 69.000 кПа. По достижении испытательного давления насос высокого давления (16) для подачи суспензии останавливается, и испытанные компоненты проверяются на соответствие нормам. Затем давление жидкостной линии сбрасывается, и тест по жидкостной системы завершен. Затем начинается подготовка и тестирование системы природного газа. Испытание под давлением заканчивается на всех компонентах от клапана (V42) до клапана (V6), включая трубопровод (32) линии подачи пара к источнику LNG (215), и для опрессовки, продувки и охлаждения системы подачи природного газа будет использован азот. Чтобы инициировать испытание под давлением, клапаны (V4), (V6),(V11), (V12), (V13), (V14) и (V15) закрываются. Затем клапан (V12) открывается, и вводится в действие источник инертного продувочного газа, чтобы закачать и выпарить азот в системе под давлением 2 МПа и завершить испытание под низким давлением. Затем работа источника инертного газа прекращается, и трубопровод (23), клапаны (V4), (V6), (V12), (V13), (V14) и (V15) проверяются на утечки. После подтверждения отсутствия утечек, давление передается от системы к факелу (V20) через трубопровод выпускной линии (48) и открытый клапан (V14). После этого закрывается клапан (V14) и источник LNG (15) вводится в действие, чтобы подать жидкий азот к насосу (229) LNG разрыва через трубопровод (46) и трубопровод (23). Насос (229) LNG разрыва, вводится в действие, и внутренние криогенные компоненты заполняются жидким азотом, который испаряется при контакте с теплыми частями. Созданный азотный пар отводится в атмосферу через трубопровод факельной линии (20) до тех пор, пока внутренние части не будут достаточно охлаждены так, что жидкий азот больше не испаряется. Работа насоса (229) LNG разрыва затем прекращается и трубопровод (23), клапаны (V42), (V14) и (V12) проверяются на утечки. Затем насос (229) LNG вводится в действие, чтобы создать давление и выпарить жидкий азот с паром,направляемым к факелу для удаления воздуха из испытательной системы. Полнота продувки может быть определена, помещая измеритель кислорода в поток продувки или прокачивая требуемый объем с запасом. После завершения продувки насос (229) LNG останавливается и клапан (V6) закрывается. Весь персонал покидает участок, и к насосу (229) LNG разрыва подводится дополнительная мощность, требуемая для испытания самого насоса плюс трубопровода (24) обрабатывающей линии и клапанов (V6), (V13) и(V15) под необходимым испытательным давлением 69.000 кПа. При этом испытательном давлении насос(229) LNG разрыва останавливается, и испытанные компоненты проверяются на утечки. В это время трубопровод (32) линии подачи пара проверяется путем открытия клапана (V11), чтобы обеспечить давление азота в трубопроводе. Клапан впуска пара (V22), соединенный с баком (15) LNG остается закрытым для испытания, чтобы избежать действия давления бака LNG с азотом. Клапаном (V11) управляют для испытания под давлением трубопровода (32) только для установки давления в баке (15) источника LNG Источник (45) продувочного инертного газа отключается от системы запорным клапаном (V12). Затем давление в жидкостной линии до факела сбрасывается, и продувка и испытание под давлением завершаются. Управляющий клапан бака (V42) источника LNG затем открывается и клапан (V6), открывается,чтобы снова пропустить поток по трубопроводу факельной линии (20). Насос (229) LNG разрыва вводится в действие с подачей LNG, чтобы вытеснить жидкий азот из трубопровода (23) через насос и трубопроводы (24) и (25) к трубопроводу факельной линии (20) с природным газом. Это гарантирует, что подача LNG была установлена в насосе LNG разрыва до начала операций. В это время проверяется система факела (20). Безопасность предварительной обработки и проведения операций затем проверяется всем персоналом. Рассматриваются все опасные места, включая местоположение аппаратуры, обеспечивающей безопасность работы, участки безопасности и план эвакуации. Обсуждаются детали процедуры обработки,обязанности по обслуживания оборудования, максимумы давления и любая другая работа, определенная для этой скважины или операции по гидроразрыву пласта. Источник природного газа (215), как правило, под атмосферным давлением предварительно испытывается под давлением 350 кПа, используя насос (229) LNG разрыва через трубопровод паровой линии(232) с открытыми клапанами (V12) и (V22), чтобы гарантировать соответствующее давление подачи во время операции по разрыву пласта. Как только система была проверена на безопасность под давлением и источник (215) LNG находится под давлением, регулируемым контроллером (58), клапан (V8) факела и клапан (V6) линии природного газа закрываются. Клапан (V5) жидкостной линии и клапан (V7) управления скважиной открываются. Теперь начинаются операции по разрыву пласта согласно примерной программе обработки, представленной в табл. 2. Работа оборудования и управление клапанами завершаются, используя контроллер(58), причем персонал обслуживания процесса не входят в опасную область высокого давления во время обработки. Управляющий клапан (V1) жидкости разрыва открывается, и смеситель жидкостей разрыва(14), работающий вместе с насосом высокого давления (16) для подачи суспензии, начинает подачу жидкости в скважину с расходом 0,5 м 3/мин, чтобы начать заполнение скважины. Химические вещества, понизитель трения и пенящееся поверхностно-активное вещество, добавляются к потоку жидкости в необходимых соотношениях под управлением контроллера (58). Свойствами созданной пены природного газа можно управлять многими способами. Изменение качества пены, пропорции природного газа к общему объему изменяет плотность и вязкость полученной смеси. Изменение силы или концентрации пенящегося поверхностно-активного вещества изменяет размер газового пузырька и полученную вязкость пены. Изменение вязкости жидкости фазы, добавляя загуститель, изменит полученную вязкость пены. Клапан(V6) открывается, и насос (229) LNG вводится в действие, чтобы начать закачку базовой жидкости и газообразного природного газа в поток. Закачка жидкости начинается и устанавливается до включения насоса потока природного газа, чтобы гарантировать, что природный газ случайно не вернется обратно в жидкостную систему. Контроллер (58) контролирует скорость подачи жидкости и скорость добавления природного газа через отдельные расходомеры или счетчики хода поршня и регулирует насос (229) LNG разрыва, чтобы поддерживать правильное соотношение 75% для качественной пены. С расходом скважины заполнения скважины, определенным в этом примере, при полном расходе пены 2,0 м 3/мин насос(229) LNG разрыва отрегулирован на расход 468 см 3/мин. Это требует расхода LNG из источника хранения (215) порядка 0,78 м 3/мин. Заполнение ствола скважины продолжается до закачки 17,8 м 3 пены. Ствол скважины от поверхности до перфораций теперь заполнен пеной природного газа. Закачка продолжается, и давление в стволе скважины повышается по мере закачки дополнительного объема до тех пор, пока не достигнуто давление разрыва пластов и не начнется растрескивание пласта. Скважина теперь заполнена, начато образование трещин и установлена скорость подачи в подземные трещины. Общий расход затем увеличивается до желательного расхода обработки 5,0 м 3/мин и начинается нагнетание пенной подушки. Расход жидкость составляет 1,25 м 3/мин и расход природного газа 1170 см 3/мин, требуя расхода LNG порядка 1.96 м 3/мин и приводя полному расходу 5,0 м 3/мин при ожидаемом давлении разрыва подземного пласта 45.189 кПа. Как сжимаемый газ, расход природного газа на поверхности основан на забойном давлении разрыва пласта и полного целевого расхода. Сжатие природного газа до 45.189 кПа при 90 С таково, что 312 см 3 природного газа должны создать один квадратный метр пространства. Когда давление разрыва пласта в забое отклоняется от ожидаемого, контроллер (58) регулирует поверхностный расход природного газа, чтобы поддерживать надлежащий расход потока в скважину для качественной 75%-ной пены. Пенная подушка природного газа продолжается до тех пор, пока в ствол скважины не будет прокачен полный объем пены 40 м 3, 10 м 3 воды с качеством 75%. Подушка служит для расширения подземной трещины в достаточной степени, чтобы в нее можно было ввести расклинивающий агент на следующей стадии обработки. Таблица 2 Программа обработки при разрыве пласта Согласно программе обработки расклинивающий агент начинает подаваться, открывая клапан (V2) подачи расклинивающего агента, поток расклинивающего агента поступает в смеситель (14) жидкостей разрыва. В данном примере используется песок с изменяющимся размером ячеек сита; однако с равным успехом может быть применен любой другой природный или искусственный расклинивающий агент. Расход потока расклинивающего агента в смеситель управляется с помощью шнеков, ремней или скользящего затвора для достижения правильной пропорции расклинивающего агента в жидком потоке. В этой программе операций по гидроразрыву пласта расход смесителя (14) жидкостей разрыва и насоса высокого давления (16) для подачи суспензии остается постоянным так, что расход воды может быть снижен за счет добавленного расклинивающего агента. Чтобы поддерживать качество пены и полную требуемую скорость закачки пены, расход природного газа регулируется. В этом случае, чтобы поддерживать расход забоя скважины, расход жидкость снижен от 1,25 до 1,22 м 3/мин, и расход природного газа уменьшен от 1170 до 1143 см 3/мин с учетом добавленного расклинивающего агента. Программа обработки продолжается с увеличивающимися концентрациями песка и с регулированием расходов воды и природного газ, пока не будет закачено достаточное количество расклинивающего агента. Если произойдет выпадение песка из жидкости разрыва, когда расклинивающий агент находится в стволе скважины или в забое, создавая мосты в трещинах скважины до такой степени, что нагнетание ограничено и увеличение давлений вне допустимого максимума, нагнетание будет остановлено и попытки повторного нагнетания не должны рассматриваться. Как только расклинивающий агент был закачан, скважина промывается, чтобы вытеснить расклинивающий агент через поверхностное оборудование вниз по стволу скважины и в подземную трещину. Скважина должна промываться заданным объемом пены 0,5 м 3, как определено для этого примера. Если давление образования трещин в забое отличается от ожидаемого, во время промывки объем природного газа, закачиваемого в поток, должен регулироваться для измененной сжимаемости, чтобы гарантировать нужный объем закачиваемого потока. При промывке скважины все оборудование выключается, клапан (V7) закрывается, мгновенное давление на устье закрытой скважины регистрируется, и все оборудование и источники материалов закрепляются. Все давление в обрабатывающем линиях, трубопроводе и насосном оборудовании сбрасывается через трубопровода факельной линии (20) и природный газ, содержащийся в оборудовании, продувается азотом. Затем оборудование для разрыва пласта природным газом демонтируется. Отметим, что качество пены 75%, представленное в этом примере, является только одним возможным значением по качеству пены и в зависимости от требований скважины, могут использоваться значения качества пены от 60 до более чем 95%. Кроме того,количество применяемого природного газа или качество пены, используемое в подушке для переноса расклинивающего агента или промывки скважины, может быть различным. Кроме того, этот проект обработки основан на поддержании постоянного расхода смесителя. Концентрация расклинивающего агента также может быть изменена, регулируя расход смесителя с компенсацией расхода природного газа,чтобы обеспечить различное качество пены, но все еще поддерживать ту же самую полную скорость закачки. Если желательно, расклинивающий агент может вообще фактически не использоваться. После демонтажа оборудования для разрыва пласта и во время, которое представляется подходящим для скважины с разрываемым пластом, скважина откачивается до получения чистой нефти и оценки. Пена природного газа рассчитана на разрыв при обратном потоке так, что природный газ и вода больше плотно не смешиваются в виде стабильной пены. Скорее вода и природный газ просто беспорядочно смешаны. Гашение пены может быть достигнуто различными способами, например, разложением или удалением пенящегося поверхностно-активного вещества. Разложение может включать диссоциацию поверхностно-активного вещества, термическую деструкцию молекул пены или разрушающее действие химических реагентов. Удаление пенящегося поверхностно-активного вещества из жидкой фазы обычно достигается сорбцией молекул на твердые тела, такие как пластовая порода, с которой пена входит в контакт. Гашение пены природного газа также может сопровождаться управляемым уменьшением вязкости жидкой фазы. Обратный поток скважины после разрыва пласта достигается, снижая давление в устьевом отверстии скважины, чтобы позволить жидкостям разрыва вытекать из скважины, созданных трещин и месторождения, открывая, таким образом, пути выхода нефти и газа из месторождения. Внутри месторождения снижение давления позволяет природному газу расширяться и форсировать извлечение жидкости разрыва из месторождения и трещин. Расширение природного газа также гарантирует, что газовая фаза существует в месторождении и в созданных трещинах. Эта газовая фаза обеспечивает проходимость к газу в ближайшей области месторождения и снижает капиллярное давление, удерживающее жидкую фазу в матрице месторождения. Дополнительная выгода заключается в растворимости природного газа в жидкой фазе, приводящей к снижению поверхностного натяжения. Этот механизм может дополнительно снизить капиллярное давление и улучшить относительную проницаемость. Внутри ствола скважины, уменьшение давления позволяет природному газу расширяться и дополнительно снижать плотность смеси природного газа и жидкости колонки в стволе скважины. Эта сниженная плотность усиливает поток природного газа и жидкости вверх по стволу скважины, снижая давление потока в забое скважины. Сниженное забойное давление обеспечивает более высокий перепад давления между месторождением и стволом скважины, разрешая более высокую депрессию на пласт и усиливает движение жидкости разрыва от месторождения в ствол скважины. Поток жидкости фазы из месторождения и созданных трещин, таким образом, увеличивается, гарантируя отсутствие блоков жидкости. Введенный природный газ и жидкость разрыва, выходящие из скважины, направляются в разделитель (60), в котором газы, жидкости и твердые тела могут быть разделены. Произведенные твердые тела могут включать расклинивающий агент разрыва и накапливаются в емкости разделителя (60) и удаляются при необходимости освобождения пространства. Жидкости собираются в разделителе (60) и дренируются в емкости-хранилища (не показаны). Во время очистки и оценки скважины, поток введенного и основанного на месторождении природного газа из емкости разделителя (60) направляется на факельную вышку (20) или предпочтительно в газопровод (21) для перепродажи. Использование природного газа как активатора газовой фазы позволяет перенаправить газопровод и очистку трещин без необходимости сжигания газа в факеле. Кроме того, использование природного газа разрешает прямую продажу введенного природного газа или газа месторождения. Как дальнейшее соображение, отметим, что в вышеупомянутом примере использовано только примерно 110 м 3 воды, тогда как использование той же самой обработки без активирования потребовало бы свыше 430 м 3 воды. Замена подобного объема воды обычной двуокисью углерода или азота потребовала бы либо значительного объема сжигаемого газа, либо очистки от произведенного газа до достижения типичного состава для продажи газа. Качество пены может быть увеличено выше 75%, чтобы дополнительно снизить расход воды. Эти меры снижают воздействие на окружающую среду и улучшают экономику. Сопоставимые способы, используя тот же самый подход, являются другими вариантами воплощения и применимы к другим типам обработки разрывом и областей применения, включая активирование и туман жидкости разрыва с расклинивающими агентами и без них; с жидкостями и без жидкостей разрыва, таких как кислоты, пресная вода, морская вода, метанол и углеводороды; и для использования во всех типах месторождений, включая труднодоступные залежи нефти и газа, метан угольных пластов, сланцевая нефть и газ, и восстановление обычных месторождений нефти и газа. Для специалистов в данной области очевидны различные модификации описанных вариантов воплощения. Настоящее изобретение не предназначено быть ограниченным, описанными здесь вариантами воплощения, но должно принято в полном объеме в соответствии с требованиями, по которым ссылка на единственный элемент не должна означать "один и только один", если это конкретно не заявлено, а ско- 20024675 рее "один или более". Все структурные и функциональные эквиваленты элементов различных вариантов воплощения описаны в процессе раскрытия, и они известны или позже становятся известными обычным специалистам и предназначены быть охваченными пунктами формулы изобретении. ФОРМУЛА ИЗОБРЕТЕНИЯ 1. Система для формирования активированной смеси жидкостей для гидравлического разрыва подземного пласта, содержащая:(a) источник базовой жидкости разрыва;(b) насос базовой жидкости, соединенный по текучей среде с источником базовой жидкости разрыва и сконфигурированный для увеличения давления базовой жидкости, по меньшей мере, до давления разрыва пласта;(c) источник сжиженного природного газа (СПГ);(d) сборку насоса СПГ, соединенную по текучей среде с источником СПГ и включающую узел насоса, сконфигурированный для увеличения давления СПГ, по меньшей мере, до давления разрыва, и нагреватель, предназначенный для испарения сжатого СПГ до газообразной фазы;(e) смеситель жидкости разрыва, имеющий первый вход, соединенный по текучей среде с насосом базовой жидкости, второй вход, соединенный по текучей среде со сборкой насоса СПГ, и выход для соединения с устьевым отверстием скважины и для смешивания базовой жидкости и газообразного природного газа, чтобы сформировать смесь жидкостей разрыва, предназначенную для нагнетания в устьевое отверстие скважины. 2. Система по п.1, в которой узел насоса включает по меньшей мере один центробежный криогенный насос. 3. Система по п.2, в которой узел насоса включает насос высокого давления СПГ, соединенный по текучей среде по меньшей мере с одним криогенным насосом и рассчитанный по меньшей мере на давления разрыва пласта. 4. Система по п.1, в которой нагреватель включает по меньшей мере один теплообменник, соединенный по текучей среде с узлом насоса, чтобы получать сжатый СПГ, и термически соединенный с источником тепла, способным нагревать сжатый СПГ по меньшей мере до желательной температуры применения. 5. Система по п.1, в которой нагреватель является беспламенным каталитическим нагревателем. 6. Система по п.5, в которой беспламенный каталитический нагреватель включает по меньшей мере один каталитический элемент, сообщающийся по текучей среде с топливным газом и способный к окислению топливного газа, чтобы вырабатывать тепло, и трубопровод СПГ, термически соединенный, но изолированный по текучей среде от каталитического элемента и для подачи СПГ через него. 7. Система по п.6, в которой беспламенный каталитический нагреватель содержит множество каталитических элементов, расположенных концентрически вокруг трубопровода СПГ, формирующих каталитическую связку для одного прохода СПГ через беспламенный каталитический нагреватель. 8. Система по п.1, в которой смеситель включает главную линию потока, имеющую входной конец и выходной конец, коленчатый трубопровод, соединенный по текучей среде с главной линией потока между входным концом и выходным концом, коленчатый трубопровод, отходящий под острым углом от входного конца и в основном проходящий по пути линейного потока через главную линию потока, входной конец, предназначенный для приема потока базовой жидкости от насоса базовой жидкости и прямоугольного коленчатого трубопровода, предназначенного для получения потока природного газа от сборки насоса СПГ. 9. Система по п.1, в которой источник СПГ включает по меньшей мере один бак СПГ, и система дополнительно включает возвратный трубопровод для газообразного природного газа, соединенный по текучей среде с нагревателем, и бак для подачи сжатого газообразного природного газа в бак для поддержания давления. 10. Система по п.9, дополнительно включающая факел, трубопроводную факельную линию, соединенную по текучей среде с факелом и предохранительным клапаном, соединяющим трубопровод факельной линии с баком, таким образом, что газообразный природный газ может быть подан из бака к факелу. 11. Система по п.9, дополнительно включающая криогенный источник инертного газа, расширитель для сжижения инертного газа, соединенный по текучей среде с источником инертного газа и имеющий всасывающий клапан, соединенный по текучей среде с баком, чтобы получать газообразный природный газ из бака, и выпускной клапан, соединенный с баком, чтобы подать СПГ в бак, узел сжижения инертного газа, обеспечивающий испарение криогенного инертного газа в нем и способный создавать достаточное охлаждение для превращения газообразного природного газа в СПГ. 12. Система по п.1, в которой источник СПГ содержит множество баков СПГ, трубопровод паровой линии между баками, соединенный по текучей среде с каждым баком, и трубопровод линии жидкости между баками, соединенный по текучей среде с каждым баком. 13. Система по п.1, в которой источник базовой жидкости разрыва включает подачу жидкости разрыва и, дополнительно, по меньшей мере одного из расклинивающего агента и химического модификатора разрыва. 14. Система по п.13, в которой источник базовой жидкости разрыва включает по меньшей мере один из расклинивающего агента и химического модификатора разрыва, и система дополнительно включает смеситель, смешивания базовой жидкости и по меньшей мере одного расклинивающего агента и химического модификатора разрыва на входе смесителя. 15. Способ для гидравлического разрыва подземного пласта, включающий использование системы по п.1, содержащий:(a) сжатие базовой жидкости и сжатие базовой жидкости, по меньшей мере, до давления разрыва пласта;(b) сжатие сжиженного природного газа (СПГ) и сжатие СПГ, по меньшей мере, до давления разрыва с последующим нагреванием СПГ до тех пор, пока СПГ не будет выпарен до газообразной фазы;(c) смешивание сжатой базовой жидкости и поддержание давления газообразного природного газа,чтобы сформировать смесь жидкостей гидравлического разрыва пласта;(d) нагнетание смеси жидкостей разрыва через устьевое отверстие скважины и в скважину до контакта с пластом;(e) продолжение нагнетания смеси жидкостей разрыва до разрыва пласта. 16. Способ по п.15, в котором базовая жидкость разрыва включает жидкость разрыва и, дополнительно, по меньшей мере один из расклинивающего агента и химического модификатора разрыва. 17. Способ по п.16, в котором базовая жидкость разрыва включает по меньшей мере один из расклинивающего агента и химического модификатора разрыва, и способ дополнительно включает смешивание жидкости разрыва по меньшей мере с одним расклинивающим агентом и химическим модификатором разрыва до смешивания базовой жидкости с природным газом. 18. Способ по п.15, в котором активированная жидкость разрыва является пеной. 19. Способ по п.15, в котором СПГ подается по меньшей мере из одного бака СПГ, и способ дополнительно включает подачу газообразного природного газа из бака СПГ к факелу. 20. Способ по п.15, в котором СПГ подается по меньшей мере из одного бака СПГ, и способ дополнительно включает прием газообразного природного газа из бака СПГ и охлаждение газообразного природного газа до состояния СПГ, выпаривая криогенный инертный газ и вводя газообразный природный газ в контакт с испаренным инертным газом.
МПК / Метки
МПК: E21B 43/24, E21B 43/26, F23C 13/00, E21B 43/267
Метки: система, способ, гидравлического, разрыва, пласта, подземного
Код ссылки
<a href="https://eas.patents.su/29-24675-sistema-i-sposob-dlya-gidravlicheskogo-razryva-podzemnogo-plasta.html" rel="bookmark" title="База патентов Евразийского Союза">Система и способ для гидравлического разрыва подземного пласта</a>
Предыдущий патент: Способ получения низших хлоридов титана
Следующий патент: Устройство и способ проведения гетерогенных каталитических реакций
Случайный патент: Замок для усиленной двери