Способ покрытия резьбового трубчатого компонента, резьбовой трубчатый компонент и результирующее соединение
Номер патента: 24642
Опубликовано: 31.10.2016
Авторы: Пинель Элит, Пети Микаель, Гуидер Мохамед, Гард Эрик
Формула / Реферат
1. Резьбовой трубчатый компонент для бурения или эксплуатации углеводородных скважин, причем указанный трубчатый компонент, имеющий на одном из своих концов (1, 2) резьбовую зону (3, 4), выполненную на его наружной или внутренней периферийной поверхности, в зависимости от того, имеет резьбовой конец наружную или внутреннюю резьбу, по меньшей мере часть конца (1, 2) покрыта по меньшей мере одной смазывающей сухой пленкой (12), содержащей по меньшей мере 65 вес.% полиарилэфиркетона, отличающийся тем, что смазывающая сухая пленка (12) имеет структуру со степенью кристалличности в пределах 10-35%.
2. Резьбовой трубчатый компонент по п.1, отличающийся тем, что полиарилэфиркетон выбран из полиэфирэфиркетона (ПЭЭК), полиэфиркетона (ПЭК) и их смесей.
3. Резьбовой трубчатый компонент по любому из предыдущих пунктов, отличающийся тем, что смазывающая сухая пленка (12) содержит также по меньшей мере один твердый смазочный материал класса 4 в соотношениях в диапазоне от 10 до 35 вес.%
4. Резьбовой трубчатый компонент по п.3, отличающийся тем, что смазывающая сухая пленка (12) содержит сополимер перфторалкоксиэтилена в соотношениях в диапазоне от 10 до 30 вес.%.
5. Резьбовой трубчатый компонент по любому из предыдущих пунктов, отличающийся тем, что смазывающая сухая пленка (12) содержит механический армирующий агент, выбранный из перечня следующих наполнителей: сажа, слюда, волластонит, наноразмерный оксид алюминия, наноразмерный оксид титана, стеклянные порошки, наноалмаз, наноразмерные WS2 или WS2-фуллерены в соотношениях в диапазоне от 1 до 15 вес.%.
6. Резьбовой трубчатый компонент по любому из предыдущих пунктов, отличающийся тем, что часть, покрытая смазывающей сухой пленкой (12), предварительно прошла этап подготовки поверхности, выбранный из группы, состоящей из пескоструйной обработки, марганцевой фосфатации, электролитического покрытия Cu или сплавами Cu-Sn-Zn и сплавами Fe и Zn, нанесенными проецированием.
7. Резьбовой трубчатый компонент по любому из пп.1-5, отличающийся тем, что часть, покрытая смазывающей сухой пленкой (12), предварительно покрыта подслоем из полиэфирэфиркетона с полукристаллической структурой и содержащим слюдяные наполнители.
8. Резьбовой трубчатый компонент по любому из предыдущих пунктов, отличающийся тем, что вся резьбовая зона (3, 4) покрыта смазывающей сухой пленкой (12).
9. Резьбовой трубчатый компонент по любому из предыдущих пунктов, отличающийся тем, что содержит поверхность уплотнения металл-металл, причем указанная поверхность уплотнения покрыта смазывающей сухой пленкой (12).
10. Резьбовое трубное соединение, содержащее резьбовой трубчатый компонент с наружной резьбой и резьбовой трубчатый компонент с внутренней резьбой, ввинченные один в другой, отличающееся тем, что по меньшей мере один из указанных резьбовых трубчатых компонентов - по одному из предыдущих пунктов.
11. Способ покрытия резьбового трубчатого компонента для бурения или эксплуатации углеводородных скважин, причем указанный трубчатый компонент, имеющий на одном из своих концов (1, 2) резьбовую зону (3, 4), выполненную на его наружной или внутренней периферийной поверхности, в зависимости от того, имеет резьбовой конец наружную или внутреннюю резьбу, отличающийся тем, что включает следующие этапы, на которых
получают смесь, содержащую полиарилэфиркетоновый порошок в суспензии в воде в соотношениях в диапазоне от 25 до 35 вес.%;
указанную смесь наносят на часть конца (1, 2) указанного резьбового трубчатого компонента;
часть конца (1, 2) с нанесенным таким образом покрытием сушат при температуре 100-150°C в течение 5-10 мин;
часть конца (1, 2) с нанесенным таким образом покрытием нагревают до температуры 350-450°C в течение 5-15 мин со скоростью повышения температуры 10-20°C/мин;
часть конца (1, 2) с нанесенным таким образом покрытием охлаждают до температуры окружающей среды со скоростью охлаждения менее 10°C/мин для получения практически кристаллической структуры.
12. Способ покрытия резьбового трубчатого компонента по п.11, отличающийся тем, что смесь также содержит коалесцирующий агент с высокой скоростью испарения с точкой кипения в пределах 100-200°C и в соотношениях в диапазоне от 2,5 до 10 вес.%.
13. Способ покрытия резьбового трубчатого компонента по п.11 или 12, отличающийся тем, что смесь содержит также неионогенный смачивающий и диспергирующий агент в соотношениях в диапазоне от 2,5 до 10 вес.%.
14. Способ покрытия резьбового трубчатого компонента по любому из пп.11-13, отличающийся тем, что смесь содержит также по меньшей мере один твердый смазочный материал класса 4 в соотношениях в диапазоне от 3 до 12 вес.%.
15. Способ покрытия резьбового трубчатого компонента по п.14, отличающийся тем, что твердый смазочный материал класса 4 является сополимером перфторалкоксиэтилена в соотношениях в диапазоне от 3 до 12 вес.%.
16. Способ покрытия резьбового трубчатого компонента по п.14, отличающийся тем, что смесь также содержит механический армирующий агент, выбранный из перечня следующих наполнителей: сажа, слюда, волластонит, наноразмерный оксид алюминия, наноразмерный оксид титана, стеклянные порошки, наноалмаз, наноразмерные WS2 или WS2-фуллерены в соотношениях в диапазоне от 0,5 до 5 вес.%.
17. Способ покрытия резьбового трубчатого компонента по п.11, отличающийся тем, что часть конца (1, 2) покрывают, используя систему пневматического распыления, причем диаметр указанной системы находится в пределах 0,7-1,8 мм, а давление воздуха находится в пределах 4-6 бар.
18. Способ покрытия резьбового трубчатого компонента по любому из пп.11-17, отличающийся тем, что перед нанесением смеси на часть конца выполняют этап подготовки поверхности, выбранный из группы, состоящей из пескоструйной обработки, марганцевой фосфатации, электролитического покрытия Cu или сплавами Cu-Sn-Zn и частицами сплавов Fe и Zn, нанесенных проецированием.
19. Способ покрытия резьбового трубчатого компонента по любому из пп.11-17, отличающийся тем, что перед нанесением смеси на часть конца выполняют этап подготовки поверхности, на котором выполняют подслой из полиэфирэфиркетона с полукристаллической структурой и содержащий слюдяные наполнители.
20. Способ покрытия резьбового трубчатого компонента для бурения или эксплуатации углеводородных скважин, причем указанный трубчатый компонент имеет на одном из своих концов (1, 2) резьбовую зону (3, 4), выполненную на его наружной или внутренней периферийной поверхности, в зависимости от того, имеет резьбовой конец наружную или внутреннюю резьбу, отличающийся тем, что включает следующие этапы, на которых
часть конца (1, 2) указанного резьбового трубчатого компонента нагревают до температуры в пределах 360-420°C, предпочтительно до температуры, близкой к 400°C;
на часть конца (1, 2) указанного резьбового трубчатого компонента наносят порошки ПЭК и/или ПЭЭК;
часть конца (1, 2) с нанесенным таким образом покрытием выдерживают при температуре в пределах 360-420°C, предпочтительно при температуре, близкой к 400°C, в течение 1-4 мин;
часть конца (1, 2) с нанесенным таким образом покрытием охлаждают до температуры окружающей среды со скоростью охлаждения менее 10°C/мин для получения практически кристаллической структуры.
21. Способ покрытия резьбового трубчатого компонента по п.20, отличающийся тем, что перед нагреванием части, на которую должно быть нанесено покрытие, выполняют этап, на котором указанную часть обезжиривают.
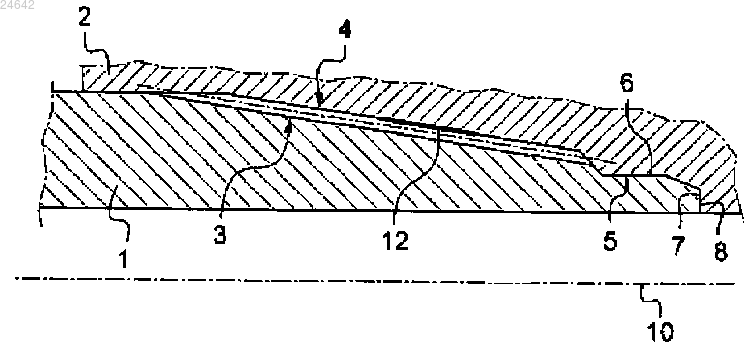
Текст
СПОСОБ ПОКРЫТИЯ РЕЗЬБОВОГО ТРУБЧАТОГО КОМПОНЕНТА, РЕЗЬБОВОЙ ТРУБЧАТЫЙ КОМПОНЕНТ И РЕЗУЛЬТИРУЮЩЕЕ СОЕДИНЕНИЕ Изобретение относится к резьбовому трубчатому компоненту для бурения или эксплуатации углеводородных скважин, причем указанный трубчатый компонент имеет на одном из своих концов (1, 2) резьбовую зону (3, 4), выполненную на его наружной или внутренней периферийной поверхности в зависимости от того, имеет резьбовой конец наружную или внутреннюю резьбу,причем, по меньшей мере, часть конца (1, 2) покрыта по меньшей мере одной смазывающей сухой пленкой (12), содержащей по меньшей мере 65 вес.% полиарилэфиркетона. Кроме того,изобретение относится к способу нанесения указанной пленки (12).(71)(73) Заявитель и патентовладелец: ВАЛЛУРЕК МАННЕСМАНН ОЙЛ ЭНД ГЕС ФРАНС (FR); НИППОН СТИЛ ЭНД СУМИТОМО МЕТАЛ КОРПОРЭЙШН (JP) Настоящее изобретение относится к трубчатому компоненту, используемому для бурения и эксплуатации углеводородных скважин, и, в частности, к резьбовому концу этого компонента, причем указанный конец имеет наружную или внутреннюю резьбу и может быть соединен с соответствующим концом другого компонента для образования соединения. Кроме того, изобретение относится к способу получения стойкой к заеданию пленки на этом трубчатом компоненте. Компонент, "используемый для бурения и эксплуатации углеводородных скважин", - это любой элемент, являющийся практически трубчатым по форме и предназначенный для соединения с еще одним элементом такого же типа или иного, чтобы в конечном итоге образовать колонну труб для бурения углеводородной скважины или райзер, предназначенный для технического обслуживания и ремонта (известные также как райзеры для ремонта) или для эксплуатации, такой как райзеры, или для обсадной колонны, или лифтовой колонны (колонны насосно-компрессорных труб), используемых при эксплуатации скважин. Кроме того, изобретение может быть применимым к компонентам, используемым в бурильной колонне, таким как бурильные трубы, утяжеленные бурильные трубы, воротники бура, и частям трубных соединений и утяжеленных труб, известных как замковые соединения или бурильные замки. Каждый трубчатый компонент содержит один конец, имеющий зону с наружной резьбой и/или один конец, имеющий зону с внутренней резьбой, каждый из которых предназначен для соединения свинчиванием с соответствующим концом другого компонента, причем полученная сборка образует соединение. Резьбовые трубчатые компоненты соединены под определенными напряжениями, чтобы обеспечить выполнение требований к затяжке и уплотнению, выдвигаемых условиями эксплуатации, притом,что в скважине может потребоваться несколько раз свинчивать и развинчивать резьбовые трубчатые компоненты. Условия использования этих резьбовых трубчатых компонентов вызывают возникновение разных типов напряжений, что обуславливает необходимость использования покрытий на чувствительных участках этих компонентов, таких, как резьбовые зоны, упоры или уплотнительные поверхности. Операции свинчивания обычно выполняют при высокой осевой нагрузке, например под весом трубы длиной несколько метров, соединяемой посредством резьбового соединения, возможно, с небольшим несовпадением оси соединяемых резьбовых элементов, что вызывает риски заедания в резьбовых зонах и уплотнительных поверхностях металл-металл. По этой причине резьбовые зоны, поверхности упоров и уплотнительные поверхности металл-металл необходимо покрывать смазками. Кроме того, резьбовые трубчатые компоненты хранят (иногда несколько лет), затем свинчивают в агрессивной среде. Примерами могут служить ситуация морского бурения с солеными брызгами или ситуация бурения на суше, когда присутствуют песок, пыль или другие загрязняющие вещества. Таким образом, на поверхностях, которые должны взаимодействовать при свинчивании (резьбовые зоны) или тугом контакте (уплотнительные поверхности металл-металл), необходимо использовать покрытия, противостоящие коррозии. Кроме того, эти поверхности необходимо обрабатывать против коррозии. Однако с экологической точки зрения оказывается, что смазки для свинчивания, отвечающие требованиям стандарта Американского института нефти (API) RP5A3, не дают длительного решения, поскольку эти смазки, содержащие тяжелые металлы, могут быть вытеснены из трубчатых компонентов и высвобождены в окружение или в скважину, приводя к закупорке, вызывающей необходимость операций по чистке. Кроме того, эти смазки не обеспечивают достаточную защиту от коррозии и должны быть применены по месту при каждой операции свинчивания. Для того чтобы решить проблемы обеспечения длительной коррозионной стойкости и противозадирных свойств и соблюсти экологические прерогативы, основные действующие лица в области резьбовых соединений активно разрабатывают сплошные сухие покрытия (т.е. не вязкие и не липкие, как смазки), которые одновременно являются смазочными материалами и защищают от коррозии, и которые можно окончательно наносить на трубчатые компоненты на заводе. В частности, разрабатывают покрытия, являющиеся инертными по отношению к окружающей среде и стойкими к износу. Настоящее изобретение основано на открытии, что использование полиарилэфиркетонов позволяет получить смазывающие сухие пленки, обладающие высокой стойкостью к износу, высокими противозадирными свойствами, имеющие высокую механическую прочность с низким коэффициентом трения и являющиеся стойкими к экстремальным условиям работы углеводородной скважины. Используемые решения можно адаптировать и к различным маркам металла для соединений для вышеупомянутых трубчатых компонентов. Использование этих полиарилэфиркетонов и их свойства в контексте резьбовых трубчатых компонентов, определенных выше, в известных технических решениях не описаны и не предложены. В частности, настоящее изобретение относится к резьбовому трубчатому компоненту для бурения или эксплуатации углеводородных скважин, причем указанный трубчатый компонент имеет на одном из своих концов резьбовую зону, выполненную на его наружной или внутренней поверхности в зависимости от того, имеет резьбовой конец наружную или внутреннюю резьбу, у которого, по меньшей мере,-1 024642 часть конца покрыта по меньшей мере одной смазывающей сухой пленкой, содержащей не менее 65 вес.% полиарилэфиркетона. Факультативные характеристики, которые являются дополнительными или заменяющими, определены ниже. Полиарилэфиркетон выбирают из полиэфирэфиркетона (ПЭЭК), полиэфиркетона (ПЭК) и их смесей. Смазывающая сухая пленка имеет структуру со степенью кристалличности в пределах 10-35%. Кроме того, смазывающая сухая пленка содержит по меньшей мере один твердый смазочный материал класса 4 в соотношениях в диапазоне от 10 до 35 вес.%. Смазывающая сухая пленка содержит сополимер перфторалкоксиэтилена в соотношениях в диапазоне от 10 до 30 вес.%. Смазывающая сухая пленка содержит механический армирующий агент, выбранный из перечня следующих наполнителей: сажа, слюда, волластонит, наноразмерный оксид алюминия, наноразмерный оксид титана, стеклянные порошки, наноалмаз, наноразмерные WS2 или WS2-фуллерены в соотношениях в диапазоне от 1 до 15 вес.%. Часть, покрытая смазывающей сухой пленкой, предварительно прошла этап подготовки поверхности, выбранный из группы, состоящей из пескоструйной обработки, марганцевой фосфатапии, электролитического покрытия Cu или сплавами Cu-Sn-Zn и сплавами Fe и Zn, нанесенными проецированием. Часть, покрытая смазывающей сухой пленкой, предварительно покрыта подслоем из полиэфирэфиркетона с полукристаллической структурой и содержащим слюдяные наполнители. Смазывающей сухой пленкой покрыта вся резьбовая зона. Резьбовой трубчатый компонент содержит поверхность уплотнения металл-металл, причем указанная поверхность уплотнения покрыта смазывающей сухой пленкой. Кроме того, настоящее изобретение относится к резьбовому трубному соединению, содержащему резьбовой трубчатый компонент с наружной резьбой и резьбовой трубчатый компонент с внутренней резьбой, свинченные один в другой, в котором по меньшей мере один из указанных резьбовых трубчатых компонентов является таким, как определено выше. Кроме того, настоящее изобретение относится к способу покрытия резьбового трубчатого компонента для бурения или эксплуатации углеводородных скважин, причем указанный трубчатый компонент имеет на одном из своих концов резьбовую зону, выполненную на его наружной или внутренней поверхности в зависимости от того, имеет резьбовой конец наружную или внутреннюю резьбу, причем способ включает следующие этапы, на которых: получают смесь, содержащую полиарилэфиркетоновый порошок в суспензии в воде в соотношениях в диапазоне от 25 до 35 вес.%; указанную смесь наносят на часть конца указанного резьбового трубчатого компонента; часть конца с нанесенным таким образом покрытием сушат при температуре 100-150C в течение 5-10 мин; часть конца, с нанесенным таким образом покрытием, нагревают до температуры 350-450C в течение 5-15 мин со скоростью повышения температуры 10-20C/мин; часть конца, с нанесенным таким образом покрытием, охлаждают до температуры окружающей среды со скоростью охлаждения менее 10C/мин для получения практически кристаллической структуры. Факультативные характеристики, которые являются дополнительными или заменяющими, определены ниже. Кроме того, смесь содержит коалесцирующий агент с высокой скоростью испарения с точкой кипения в пределах 100-200C и в соотношениях в диапазоне от 2,5 до 10 вес.% Кроме того, смесь содержит неионогенный смачивающий и диспергирующий агент в соотношениях в диапазоне от 2,5 до 10 вес.%. Кроме того, смесь содержит по меньшей мере один твердый смазочный материал класса 4 в соотношениях в диапазоне от 3 до 12 вес.%. Твердый смазочный материал класса 4 является сополимером перфторалкоксиэтилена в соотношениях в диапазоне от 3 до 12 вес.%. Кроме того, смесь содержит механический армирующий агент, выбранный из перечня следующих наполнителей: сажа, слюда, волластонит, наноразмерный оксид алюминия, наноразмерный оксид титана,стеклянные порошки, наноалмаз, наноразмерные WS2 или WS2-фуллерены в соотношениях в диапазоне от 0,5 до 5 вес.% Часть конца покрывают, используя систему пневматического распыления, причем диаметр указанной системы находится в пределах 0,7-1,8 мм, а давление воздуха - в пределах 4-6 бар. Перед нанесением смеси на часть конца выполняют этап подготовки поверхности, выбранный из группы, состоящей из пескоструйной обработки, марганцевой фосфатации, электролитического покрытия Cu или сплавами Cu-Sn-Zn и частицами сплавов Fe и Zn, нанесенными проецированием. Перед нанесением смеси на часть конца выполняют этап подготовки поверхности, на котором вы-2 024642 полняют подслой из полиэфирэфиркетона с полукристаллической структурой и содержащий слюдяные наполнители. Кроме того, настоящее изобретение относится к способу покрытия резьбового трубчатого компонента для бурения или эксплуатации углеводородных скважин, причем указанный трубчатый компонент имеет на одном из своих концов резьбовую зону, выполненную на его наружной или внутренней поверхности в зависимости от того, имеет резьбовой конец наружную или внутреннюю резьбу, причем способ включает следующие этапы, на которых: часть конца указанного резьбового трубчатого компонента нагревают до температуры в пределах 360-420C, предпочтительно до температуры, близкой к 400C; на часть конца указанного резьбового трубчатого компонента наносят порошки ПЭК и/или ПЭЭК; часть конца с нанесенным таким образом покрытием выдерживают при температуре в пределах 360-420C, предпочтительно при температуре, близкой к 400C, в течение 1-4 мин; часть конца с нанесенным таким образом покрытием охлаждают до температуры окружающей среды со скоростью охлаждения менее 10C/мин для получения практически кристаллической структуры. Преимущественно, перед нагреванием указанной части выполняют этап, на котором указанную часть обезжиривают. Отличительные признаки и преимущества изобретения более подробно описаны в последующем описании, которое подано со ссылками на прилагаемые чертежи. На фиг. 1 показан схематический вид соединения, полученного в результате соединения двух трубчатых компонентов свинчиванием. На фиг. 2 показан схематический вид графика свинчивания двух резьбовых трубчатых компонентов. На фиг. 3 показан схематический вид подслоя, покрытого смазывающей сухой пленкой. На фиг. 4 показан схематический вид испытательной установки. На фиг. 5 показан схематический вид другой испытательной установки. На фиг. 6 и 7 показаны графики результатов испытаний. Резьбовое соединение, показанное на фиг. 1, содержит первый трубчатый компонент с осью вращения 10, имеющий конец 1 с наружной резьбой, и второй трубчатый компонент с осью вращения 10, имеющий конец 2 с внутренней резьбой. Оба конца, 1 и 2, каждый из которых заканчивается в концевой поверхности, ориентированной радиально относительно оси 10 резьбового соединения, соответственно имеют резьбовые зоны 3 и 4, которые взаимодействуют для взаимного соединения этих двух компонентов свинчиванием. Резьбовые зоны 3 и 4 могут быть с резьбой трапецеидального, самозапирающегося и т.д. типа. Кроме того, на концах с наружной и внутренней резьбой рядом с резьбовыми зонами 3, 4 предусмотрены соответственно поверхности уплотнения металл-металл 5, 6, предназначенные для вхождения в уплотненный тугой контакт между собой после соединения двух резьбовых компонентов свинчиванием. Наконец, конец 1 с наружной резьбой заканчивается в концевой поверхности 7, упирающейся в соответствующую поверхность 8, предусмотренную на конце 2 с внутренней резьбой, когда эти два конца свинчены. Заявитель предусмотрел и другие конструктивные исполнения, в которых упор, образованный в данном случае двумя контактными поверхностями 7 и 8, заменено самозапирающимся затягивающимся взаимодействием резьбовых зон 3, 4 (см. документы US 4822081, US RE 30467 и US RE 34467). Как можно видеть на фиг. 1 и 3, по меньшей мере одно из резьбовых трубчатых соединений покрыто на части своего конца 1, называемой подслоем 11, смазывающей сухой пленкой 12, содержащей по меньшей мере 65 вес.% полиарилэфиркетона, причем указанная смазывающая сухая пленка 12 имеет структуру со степенью кристалличности по меньшей мере 10%. Напомним, что степень кристалличности определяют по энтальпии плавления или кристаллизации (H) полимера. Теоретическая энтальпия плавления для полностью кристаллического полиарилэфиркетона, в частности полиэфирэфиркетона(ПЭЭК), равна 122 Дж/г согласно Hay и Coll (Polymer Communications, 1984, 25, 175-178). Присутствие степени кристалличности по меньшей мере 10% обеспечивает преимущество, заключающееся в отличных механических свойствах, в частности в высоком крутящем моменте на стопоре ("крутящий момент на стопоре"). Однако чтобы сохранить характеристики пленки с точки зрения адгезии и защиты в подготовке поверхности против коррозии степень кристалличности предпочтительно поддерживать ниже 35%. Полиарилэфиркетоны, используемые в изобретении, могут быть получены из водных дисперсий полиэфирэфиркетона или из водных дисперсий полиэфиркетона. Эти водные дисперсии могут содержать органические или неорганические механические армирующие агенты, такие, как слюдяные наполнители типа мусковита и/или биотита, представленные алюмосиликатом и гидратированным калием или магнием, аморфные оксиды алюминия с гамма-кристаллической структурой и размером частиц в пределах 20-300 нм, наполнители из диоксида титана с размером частиц в пределах 10-100 нм, смолы сополимера перфторалкоксиэтилена (ПФА), аморфные черные наполнители "сажа", синтетические графитовые порошки с диаметром менее 5 мкм, наноалмазные порошки, полученные детонацией и с размером частиц в пределах 4-6 нм, стекло типа C с толщиной волокон в пределах 1-1,3 мкм с диаметром D9050 мкм, наноматериалы WS2 типа фуллерен с размером частиц в пределах 80-220 нм или ламеллярные наполнители бисульфида вольфрама WS2 с размером частиц D50=55 нм. Полиэфирэфиркетоны, аббревиатура для которых - ПЭЭК, и полиэфиркетоны, аббревиатура для которых - ПЭК, получают путем синтеза нуклеофильного замещения. Полиэтерификация дает в результате жесткие тугоплавкие поликристаллические полимеры. Они входят в категорию материалов с самыми высокими эксплуатационными характеристиками в ассортименте термопластичных материалов. Они имеют температуру стеклования 143C и за счет своей полукристаллической структуры сохраняют свои отличные механические свойства при температурах, близких к их точке плавления, которая равна 343C. Их квазилинейная и ароматическая структура обеспечивает отличную долгосрочную термостойкость ПЭЭК и ПЭК. Молекулярная структура полиэфирэфиркетонов: Имея температуру стеклования 157C и точку плавления 374C, полиэфиркетоны (ПЭК) обеспечивают лучшие эксплуатационные характеристики при высоких температурах по сравнению с полиэфирэфиркетонами (ПЭЭК), обладая всеми теми же преимуществами такими, как жесткость, прочность и химическая стойкость. Температура длительной эксплуатации равна 240C, а температура деформации под нагрузкой для армированных марок ПЭЭК и ПЭК превышает 300C по сравнению с другими полимерами. ПЭЭК обладает высокоуровневыми механическими свойствами и сохраняет свои свойства при температурах до 250C для предела прочности при растяжении и до 300C для предела прочности при изгибе. Эти механические характеристики значительно улучшаются при добавлении 10-30% твердых смазочных материалов, таких, как графит, сажа, полимеры типа фторированного ПТФЭ или смолы типа перфторалкоксиэтилена (ПФА), или стекловолокна. Полиэфиркетоны обладают почти в три раза более высокой износостойкостью по сравнению с полиэфирэфиркетонами при высоких температурах и сохраняют свои механические и физические свойства при температурах, более чем на 30C выше температур для ПЭЭК, допуская более высокие нагрузки без постоянной деформации. Полиэфирэфиркетоны и полиэфиркетоны обладают химической стойкостью, в частности против насыщенных солевых растворов, газообразного сульфида водорода при температуре 200C, а также стойкостью к гидролизу при температуре 200C при давлении 1,6 МПа с термостойкостью, сравнимой с фторированными полимерами. Табл. 1 наглядно показывает преимущественные механические свойства ПЭЭК и ПЭК по сравнению с фторированными полимерами (ПТФЭ и ПФА). Таблица 1 Для полиэфиркетонов и полиэфирэфиркетонов возможны различные реализации, но включающие преобразование плавлением при температуре в пределах 370-420C. Нанесение может быть осуществле-4 024642 но нанесением порошка в электростатическом поле, распылением водных дисперсий и термическим нанесением. В расплавленном состоянии полиэфирэфиркетоны и полиэфиркетоны не чувствительны к коррозии, но они могут быть загрязнены литьевыми пресс-формами, выполненными из сплавов, содержащих медь или хром (как в некоторых марках мартенситных нержавеющих сталей, содержащих 13% хрома, например), которые будут катализировать деструкцию и давать покрытия, менее стойкие к окислению. В целом, после преобразования плавлением полиэфиркетоны и полиэфирэфиркетоны хорошо прилипают к металлу, особенно если он хорошо не отполирован. Допускаемая шероховатость составляет 2025% общей требуемой толщины сухой пленки. Адгезию можно повысить, используя подслой в качестве промотора адгезии или используя поверхностную обработку механическим истиранием (песко- или дробеструйную очистку), протравливанием в хромовой кислоте или плазменной обработкой с окислителем воздуха, или восстановителем типа O2 или даже типа NH3. При этом следует помнить, что поверхностное окисление почти всех металлов обычно уменьшает адгезию полимера. Для того чтобы не изменить поверхностную энергию крепления оказывается необходимым нагревание металла в инертной атмосфере или индукцией. Наконец, охлаждение должно быть достаточно медленным, чтобы дать в результате хорошую рекристаллизацию и сохранить присущие свойства полимера, такие, как износостойкость и сопротивление царапанию. Быстрое охлаждение дало бы аморфное покрытие, которое по-прежнему требовалось бы повторно кристаллизовать путем отжига частей при температуре 200C в течение 30 мин. Механические свойства полимера можно повысить повышением кристалличности посредством способа регулируемого охлаждения, например со скоростью охлаждения 10C/мин с 400 до 250C с последующим этапом постоянной температуры 30 мин-1 ч при температуре 250C. На первом этапе заявитель исследовал получение полиарилэфиркетонового покрытия из водной суспензии полиэфирэфиркетона, продаваемой компанией Victrex под названием серии Vicote F800, который содержит по меньшей мере один твердый смазочный материал, предпочтительно фторированный полимер типа смолы сополимера перфторалкоксиэтилена, для повышения износостойкости и/или по меньшей мере одно неорганическое твердое соединение типа сажи для повышения сопротивления истиранию. Физико-химические характеристики различных водных суспензий серии Vicote F800 оценены в табл. 2. Таблица 2 Кроме того, заявитель точно определил состав водных суспензий порошка полиэфирэфиркетона. В частности, было установлено, что водные суспензии могут предпочтительно содержать 25-35 вес.% порошка полиэфирэфиркетона с размером частиц D90 10 мкм, продаваемого компанией Victrex под торговым наименованием Vicote 704. Водные суспензии могут также содержать частицы твердого смазочного материала по меньшей мере из одного из классов 1, 2 и 4 и предпочтительно в соотношениях в диапазоне от 3 до 12 вес.% твердого смазочного материала из класса 4 в виде фторированного порошка типа сополимера перфторалкоксиэтилена, продаваемого компанией DYNEON под торговым наименованием Hyflon PFA со средним разме-5 024642 ром частиц в пределах 20-30 мкм. Термин "твердый смазочный материал" в том значении, в каком он используется в настоящем описании, означает твердое и устойчивое тело, которое, будучи помещенным между двумя трущимися поверхностями, может уменьшить коэффициент трения и уменьшить износ и повреждение этих поверхностей. Эти тела могут разбиваться на разные категории, определяемые их функциональным механизмом и их структурой, а именно: класс 1: твердые тела, смазывающие свойства которых обусловлены их кристаллической структурой, например графит, оксид цинка (ZnO) или нитрид бора (BN); класс 2: твердые тела, смазывающие свойства которых обусловлены их кристаллической структурой, а также реакционным химическим элементом в их составе, например дисульфид молибдена MoS2,фторид графита, сульфиды олова, сульфиды висмута, дисульфид вольфрама или фторид кальция; класс 3: твердые тела, смазывающие свойства которых обусловлены их химической реакционной способностью, например некоторые химические соединения типа тиосульфата или Desilube 88, продаваемый компанией Desilube Technologies Inc; класс 4: твердые тела, смазывающие свойства которых обусловлены пластическим или вязкопластическим поведением под действием силы трения, например политетрафторэтилен (ПТФЭ) или полиамиды. Водные суспензии могут содержать механические армирующие агенты, предпочтительно в соотношениях в диапазоне от 0,5 до 1 вес.% наполнителей "сажа", продаваемых компанией Evonik под торговым наименованием Printex с удельной поверхностью по методу Брунауэра, Эммета и Теллера в пределах 25-300 м 2/г и средним размером частиц в пределах 1-5 мкм. Водные суспензии могут содержать коалесцирующий агент, предпочтительно с высокой скоростью испарения и точкой кипения в пределах 100-200C, типа этиленгликоль монобутилэфира, в соотношениях в диапазоне от 2,5 до 10 вес.% и предпочтительнее в соотношениях в диапазоне от 2,5 до 5 вес.% суспензии, чтобы обеспечить коалесценцию или образование пленки наружной пластификацией полимерных субстанций и изменить поверхностное натяжение суспензии, чтобы облегчить растекание. Водные суспензии могут содержать поверхностно-активное вещество и предпочтительно неионогенный смачивающий и диспергирующий агент типа диоктилсульфосукцината натрия (соединение серной кислоты и алифатического сложного эфира в смеси воды и этилового спирта) в соотношениях в диапазоне от 2,5 до 10 вес.%, предпочтительно в соотношениях в диапазоне от 2,5 до 5 вес.% суспензии,чтобы улучшить смачивание крепления и предотвратить осаждение порошков из раствора. Что касается способа нанесения сухой пленки на часть конца 1, 2 резьбового трубчатого компонента, заявитель установил, что порошок полиэфирэфиркетона марки Vicote 704 может быть нанесен проецированием с помощью пистолета для нанесения порошка в электростатическом поле с использованием сухого или влажного метода. В первом варианте перед нанесением порошка ПЭЭК часть конца 1, 2 предварительно нагревают до температуры 400C. Затем покрытую часть выдерживают при температуре в пределах 360-420C 2 мин и предпочтительно при начальной температуре 400C, для создания хорошего вида поверхности. Этот этап могут повторять несколько раз до получения требуемой толщины. Порошок должен проходить обезвоживание в течение не менее 2 ч при температуре 180C. Во втором варианте на часть конца 1, 2 наносят покрытие путем пневматического распыления холодной водной суспензии порошка Vicote 704, который может быть или не быть армированным. Для этого способа часть конца 1, 2 предпочтительно должна быть идеально чистой и обезжиренной растворителем, предпочтительно полярным апротонным (не принимающим и не отдающим ионы водорода) растворителем, таким, как ацетон. Нанесение может быть выполнено с помощью системы пневматического распыления с пистолетом с подачей самотеком и чашей, причем часть конца 1, 2 должна быть температуры окружающей среды. Температура смеси предпочтительно близка к температуре окружающей среды, причем указанная температура окружающей среды - это температура предпочтительно в пределах 20-30C. Диаметр распылителя пистолета - предпочтительно в пределах 0,7-1,8 мм, а минимальное давление воздуха 4 бара, предпочтительно в пределах 4-6 бар. Затем часть с нанесенным покрытием оставляют при температуре окружающей среды на 5-10 мин. Указанную часть затем помещают в печь при температуре 120C на 5-10 мин. Этот этап сушки могут выполнять индукцией (индукционным нагревом), например. Затем часть помещают в печь либо при температуре 400C, либо при более низкой температуре с последующим повышением температуры до 400C со скоростью 10-20C/мин. После достижения максимальной температуры металла часть резьбового конца 1, 2 оставляют при этой температуре на 5-15 мин, предпочтительно минимум на 10 мин, чтобы позволить сухой пленке полностью расплавиться и образовать гомогенную пленку. Затем часть резьбового конца 1, 2 вынимают из печи и дают остыть до температуры окружающей среды. Скорость охлаждения предпочтительно должна быть низкой, а именно в пределах 1-200C/мин,чтобы получить полукристаллическую структуру. Альтернативой нанесению в электростатическом поле является нанесение порошка Vicote методом сухого термического нанесения на часть резьбового конца 1, 2 с использованием термовоздуходувки. В этом способспособе часть конца 1, 2 предпочтительно должна быть идеально чистой и обезжиренной растворителем, предпочтительно полярным апротонным растворителем, таким, как ацетон. Деталь предварительно нагревают в печи при температуре 260C. На деталь газом-носителем с помощью термовоздуходувки наносят порошок Vicote, при этом мелкие частицы полиарилэфиркетона нагреваются до точки плавления, разгоняются и переносятся на субстрат. После этого этапа осуществляют быстрое охлаждение на воздухе до температуры окружающей среды. Этот этап могут повторять несколько раз до получения требуемой толщины. Толщина сухого покрытия находится в пределах 20-70 мкм, предпочтительно в пределах 30-50 мкм. Испытания заключаются в оценке ряда параметров, а именно: момента трения на поверхностях контакта при высоких контактных напряжениях по Герцу (испытание Бриджмена); силы адгезии пленки на субстрате (испытание царапанием, испытание с поперечной штриховкой); стойкости воздействию влажной среды; стойкости при погружении в воду; износостойкости при высоком давлении (испытание на машине Фалекса). Испытание Бриджмена позволяет определить трибологические характеристики наполнителей сухой пленки во время операции свинчивания, специфические для соединений класса "Премиум". В частности,моделируют и определяют крутящий момент на стопоре CSB, известный также как ToSR ("torque onshoulder resistance"). Этот момент возникает при операциях свинчивания, специфических для соединений класса "Премиум", используемых в нефтедобывающей промышленности, и представлен на фиг. 2. Кривая на фиг. 2 показывает крутящий момент при свинчивании (или зажиме) как функцию числа выполненных витков вращения. Как можно видеть, профиль крутящего момента свинчивания для соединений класса "Премиум" разбит на четыре части. В первой части P1 наружные витки резьбового элемента (или ниппеля бурильного замка) с наружной резьбой первого компонента резьбового трубчатого соединения еще не имеют радиальной затяжки с внутренними витками соответствующего резьбового элемента (или муфты бурильного замка) с внутренней резьбой второго компонента того же резьбового трубчатого соединения. Во второй части P2 геометрическое зацепление витков резьбовых элементов с наружной и внутренней резьбой создает радиальную затяжку, увеличивающуюся по мере продолжения свинчивания (создающего малый, но увеличивающийся крутящий момент свинчивания). В третьей части P3 поверхность уплотнения на наружной периферии концевой части резьбового элемента с наружной резьбой зацеплена радиально с соответствующей поверхностью уплотнения резьбового элемента с внутренней резьбой, образуя уплотнение металл-металл. В четвертой части P4 передняя торцевая поверхность резьбового элемента с наружной резьбой упирается в осевом направлении в кольцевую поверхность упора свинчивания резьбового элемента с внутренней резьбой. Эта четвертая часть P4 соответствует окончательной фазе свинчивания. Крутящий момент свинчивания CAB, соответствующий концу третьей части P3 и началу четвертой части P4, называется стопорным крутящим моментом стыковки. Крутящий момент свинчивания CP, соответствующий концу четвертой части P4, называется крутящим моментом пластификации CP. Считается, что упор наружной резьбы при свинчивании (торцевая часть элемента с наружной резьбой) и/или упор внутренней резьбы при свинчивании (зона, находящаяся за кольцеобразной упорной поверхностью элемента с внутренней резьбой) подвергается (или подвергаются) пластической деформации, которая может вызвать ухудшение показателей герметичности контакта между поверхностями уплотнения из-за пластификации указанных поверхностей уплотнения. Разница между величинами крутящего момента пластификации CP и стопорного крутящего момента стыковки CAB называется крутящим моментом на стопоре CSB (CSB=CP-САВ). В конце свинчивания резьбовое трубчатое соединение подвергается оптимальной затяжке, что служит гарантией оптимальной механической прочности резьбового соединения, например в части растягивающих усилий, равно как и в части случайного развинчивания при эксплуатации, и оптимальных характеристик уплотнения. Таким образом, разработчик резьбового соединения обязан определить для данного типа резьбового соединения значение для оптимального крутящего момента затяжки, которое для всех соединений этого типа соединения должно быть ниже крутящего момента пластификации CP (во избежание пластификации упоров и нежелательных последствий, которые из этого следуют) и выше стопорного крутящего момента стыковки CAB. Окончательное свинчивание с крутящим моментом, меньшим CAB, не может гарантировать правильное относительное расположение элементов с наружной и внутренней резьбой и,таким образом, эффективную посадку с натягом между их поверхностями уплотнения. Кроме того, существует риск развинчивания. Для одного и того же типа соединения действительное значение стопорного крутящего момента стыковки CAB значительно колеблется от одного соединения к другому, поскольку оно зависит от диаметральных и осевых допусков на механическую обработку наружной и внутренней резьбы и поверхности (поверхностей) уплотнения; оптимальный крутящий момент свинчивания должен быть значительно выше, чем стопорный крутящий момент стыковки CAB. Как следствие, чем выше значение крутящего момента на стопоре CSB, тем больше запас для определения оптимизированного крутящего момента свинчивания, и тем более стойким будет резьбовое соединение к рабочим напряжениям. Испытания трением были проведены с использованием машины типа Бриджмена. Этот тип машины описан, в частности, в статье D Kuhlmann-Wilsdorf et al, "Plastic flow between Bridgman anvils under highpressures", J. Mater. Res., vol 6, no 12, Dec 1991. Схематический и функциональный пример машины Бриджмена показан на фиг. 5. Эта машина содержит: диск DQ, который может быть приведен во вращение с выбранными частотами вращения; первый упорный конец EC1, предпочтительно конического типа, постоянно прикрепленный к первой стороне диска DQ; второй упорный конец EC2, предпочтительно конического типа,постоянно прикрепленный ко второй стороне диска DQ, противоположной его первой стороне; первыйEP1 и второй EP2 элементы давления, такие, как, например, поршни, которые могут прикладывать выбранное осевое давление P; третий упорный конец EC3, предпочтительно цилиндрического типа, постоянно прикрепленный к одной стороне первого элемента давления EP1; четвертый упорный конец EC4,предпочтительно цилиндрического типа, постоянно прикрепленный к одной стороне второго элемента давления EP2. Для испытания состава смазочного материала два образца материала, идентичного материалу, из которого выполнен резьбовой элемент, покрывают указанным составом для получения первого S1 и второго S2 образцов. Затем первый образец S1 помещают между свободными сторонами первого EC1 и третьего EC3 упорных концов, а второй образец S2 - между свободными сторонами второго EC2 и четвертого EC4 упорных концов. Затем диск DQ вращают с выбранной частотой вращения, прикладывая при этом выбранное осевое давление P (например, порядка 1 ГПа) каждым элементом давления - первым EP1 и вторым EP2, и измеряют крутящий момент свинчивания, которому подвергается каждый образец S1,S2. В испытании Бриджмена осевое давление, частоту вращения и угол вращения выбирают, чтобы имитировать давление Герца и относительную скорость поверхностей упора в конце свинчивания. С помощью этой машины можно установить несколько разных пар параметров (крутящий момент свинчивания,частота вращения) для прикладывания заданных крутящих моментов свинчивания к образцам S1 и S2 и,таким образом, проверки, точно ли следуют образцы S1 и S2 данному профилю крутящего момента свинчивания, и, в частности, могут ли они достичь числа полных оборотов до задира, которое, по меньшей мере, равно пороговому значению, выбранному в отношении крутящих моментов свинчивания. В настоящем случае выбранное контактное давление было 1 ГПа, а частота вращения составляла 1 об/мин. Образцы для испытаний были изготовлены из нержавеющей стали, содержащей 13% хрома, механически обработаны, а затем покрыты разными составами сухой пленки. Испытание царапанием, схематически показанное на фиг. 4, позволяет определять силу адгезии или адгезию пленки на поверхности или подготовленной поверхности. Этот метод, заключающийся в сдвигании и деформации пленки сферическим шариком, подвергающимся увеличивающейся нагрузке, позволяет также определять два основных трибологических параметра, а именно: коэффициент трения и критическую нагрузку, соответствующую появлению потери когезии пленки. Условия эксперимента включают использование сферического индентора, изготовленного из сплава Инконель 718 диаметром 5 мм, и металлического образца, изготовленного из углеродистой сталиXC48, обработанного цинковой или марганцевой фосфатацией, или с электролитическим покрытием сплавами Cu-Sn-Zn. Параметры были следующими: нагрузка, увеличивавшаяся с 10 до 310 Н со скоростью увеличения нагрузки 15 Н/с, или нагрузка, увеличивавшаяся с 250 до 750 Н со скоростью увеличения нагрузки 25 Н/с. Скорость смещения шарика была 2 мм/с на протяжении 20 с (длина пути 40 мм). Измеренный коэффициент трения считается низким, если он находится в пределах =0,05 для нагрузки 10 Н, и =0,09 для нагрузки 310 Н. Для нагрузки 310 Н на поверхности углеродистой сталибыл измерен равным 0,07. Следует отметить, что для испытания для каждого типа покрытия необходимо четко устанавливать нагрузку и рабочие условия. Испытание с поперечной штриховкой заключается в оценке стойкости одно- или многослойного покрытия к отрыву от подложки при нанесении на покрытие поперечной штриховки надрезами на всю толщину покрытия до указанной подложки в соответствии с разбивкой на шесть категорий. Отличная адгезия покрытия с подложкой должна соответствовать классу 0 по стандарту ISO 2409 (2007): идеально гладкие края к надрезам, отсутствие отделившихся квадратов поперечной штриховки. Для того чтобы учесть условия эксплуатации, испытание с поперечной штриховкой проводят после помещения во влажную среду (35C и относительная влажность воздуха 90%). Характеристиками хорошей влагостойкости являются отсутствие изменений внешнего вида, отсутствие образования вздутий или пузырей, отсутствие коррозии, отсутствие растрескивания, отсутствие отслаивания в соответствии с классификациями по стандарту ISO 4628 и отсутствие потери адгезии. Испытания на коррозионную стойкость заключаются в испытании с распылением нейтральной соли, проводимом в камере для климатических испытаний при следующих условиях: температура 35C с солевым раствором 50 г/л плотностью в пределах 1,029-1,036 при температуре 25C, с рН в пределах 6,5-7,2 при температуре 25C со средним расходом 1,5 мл/ч. Образцы, которые были неповрежденными, без ржавления, должны были затем после воздействия соответствовать классу ReO стандарта ISO 9227. Этот способ предусматривает средства проверки, что сравнительное качество металлического материала с коррозионностойким покрытием или без него (металлическое или органическое покрытие на металлическом материале) поддерживается. Испытания на водостойкость заключаются в проведении на образцах ускоренного испытания на коррозию в соответствии со стандартом DIN 50017, проводимого в камере для климатических испытаний. Это испытание, содержащее один цикл в сутки, заключается в осаждении водяного пара путем конденсации при следующих условиях: температура 35C, относительная влажность 90% в течение 8 ч, затем высыхание образца. После 7 циклов проверяют, не поржавела ли подложка, защищенная покрытием. Отличная водостойкость должна соответствовать классификациям по стандарту ISO 4628: отсутствие коррозии, отсутствие образования вздутий или пузырей, отсутствие растрескивания, отсутствие отслаивания хромистой или углеродистой стали, обработанной или не обработанной фосфатацией цинком(нанесение фосфата 8-20 г/м 2) или марганцем или обработанной электролитическим покрытием трехкомпонентным сплавом Cu-Sn-Zn с промежуточным слоем Ni. Испытание погружением в воду является намного более тяжелым, чем испытание на водостойкость по стандарту DIN 50017. Оно заключается в испытании водостойкости покрытий. Оно взято из стандарта Американского общества по испытанию материалов ASTM D870-09, относящегося к промышленным и автомобильным краскам. Погружение в воду может вызвать ухудшение характеристик покрытий. Для прогнозирования срока службы покрытия важно знать, как оно сопротивляется погружению в воду. Разрушение или повреждение при испытании погружением в воду может быть вызвано рядом факторов, в частности дефектностью самого покрытия, загрязнением подложки или недостаточной подготовкой поверхности. Таким образом,это испытание используют для оценки отдельных покрытий или систем покрытий в целом. Испытание заключается в полупогружении образца в деминерализованную воду на 168 ч при температуре 40C в печи. Адгезия, образование вздутий или пузырей, ржавчина или раковины, наблюдаемые визуально, указывают на чувствительность покрытия к воде. В испытании на износостойкость при высоком давлении (называемом также испытанием на машине Фалекса) используют вращающийся индентор, зажатый между двумя V-образными блоками, как показано на фиг. 6. Испытание на машине Фалекса используют, в частности, при высоких скоростях для оценки противоизносных свойств и свойств в условиях экстремальных давлений смазывающих текучих сред в соответствии со стандартами ASTM D2670 и ASTM D3233, но и используют также при низких скоростях для оценки твердых смазочных материалов по методу в соответствии со стандартом ASTMD2625. Испытание на машине Фалекса адаптировано под резьбовые соединения, используемые при эксплуатации углеводородных скважин, в том, что в нем используют полузакрытую геометрию контакта (для захвата третьего смазывающего тела); диапазон давления-частоты вращения, соответствующий таковому в соединениях; возможность проведения однонаправленного или знакопеременного испытаний для имитации операций свинчивания и развинчивания. Условия испытаний: нагрузка=785 Н; частота вращения индентера=60 об/мин; среднее давление контакта металл-металл=560 МПа; скорость скольжения индентера=20 мм/с. Цель этого испытания заключается в том, чтобы сымитировать и оценить долговечность в части противозадирных свойств для различных пленок без необходимости проведения оценки на соединениях. Это испытание означает, что характеристики различных покрытий можно сравнивать с фактическими испытаниями на соединении. Критерий задира определен по стандарту ASTM D2625-94, относящемуся к измерению нагрузочной способности пленки твердого смазочного материала, и соответствует резкому увеличению крутящего момента по сравнению с начальным состоянием порядка на 1130 Нмм или коэффициента трения порядка на 0,15 для нагрузки 785 Н. Обычно задир наблюдается, когда приложенная нагрузка уменьшается, независимо от материалов и конфигурации. Заявитель оценил характеристики, особенно трибореологические характеристики, различных пленок, полученных с использованием водных суспензий полиэфирэфиркетона, для их сравнения, в том числе, с характеристиками, наблюдаемыми у термореактивной пленки типа фторэтана или вязкопластической пленки с воскообразной термопластичной матрицей. Фторэтановая пленка состоит из водной дисперсии фторэтиленвинилэфира, отвержденной с использованием алифатического полиизоцианатного отвердителя. Воскообразная термопластическая матрица содержит по меньшей мере один полиэтиленовый воск и главным образом сверхосновный кальция сульфонат, в которых диспергированы изменяющие трение наполнители, как описано в документе WO 2008/139058. На первой стадии заявитель оценил адгезию, коэффициент трения, антикоррозионную защиту и характеристики при погружении водных суспензий полиэфирэфиркетона на различных подложках, получивших конкретную обработку по подготовке поверхности: углеродистая сталь XC48 с поверхностью после станочной обработки (XC48 AsM); нержавеющая сталь Z20C13 (13Cr); углеродистая сталь XC48 с цинковым (PhZn) или марганцевым (PhMn) фосфатированием; углеродистая сталь XC48 с электролитическим покрытием сплавом Cu-Sn-Zn (TA). В табл. 3, 4 и 5 подытожены результаты адгезии, полученные соответственно для водных суспензийVicote F804, Vicote F805 и Vicote F807Blk на образцах, прошедших различные подготовки поверхности,при испытании царапанием и испытании с поперечной штриховкой по стандарту ISO 2409. Здесь следует напомнить, что испытание царапанием характеризует силу адгезии материала с высокими характеристиками, предпочтительно термореактивного или термопластичного, как функцию увеличения прикладываемой нагрузки. Критическая нагрузка, определяющая разрушение на поверхности сопряжения и, таким образом, силу адгезии материала, выше, если материал стойкий и адгезионный. Минимальная критическая нагрузка 310 Н соответствует минимальной адгезии для давлений, которые могут достигать 1,1 ГПа, ниже которой происходит увеличение количества продукта износа в контакте,и, таким образом, противозадирные свойства являются недостаточными. Для испытания с поперечной штриховкой в соответствии со стандартом ISO 2409, который предусматривает измерение адгезии после повреждения материала процарапыванием до поверхности сопряжения, отметка 0 соответствует отличной адгезии, а отметка 5 означает очень плохую адгезию. Таблица 3 Характеристики адгезии Vicote F804 Все испытанные пленки имели недостаточные силы адгезии независимо от подготовки поверхности, выполненной на углеродистых сталях фосфатированием пинком, за исключением углеродистых сталей с марганцевым фосфатированием. Кроме того, полиэфирэфиркетоновая пленка имела низкую совместимость с поверхностной обработкой типа фосфатирования цинком. Чтобы объяснить эти результаты, заявитель оценил также степень шероховатости, получаемую без фосфатирования. Поскольку механизм адгезии для полиэфирэфиркетоновой пленки является, главным образом, физическим за счет механического заклинивания, шероховатость подложки является определяющим фактором. В то же время рекомендуется обрабатывать подложку посредством бомбардирования песком, чтобы получить шероховатость Ra (Ra - среднеарифметическое относительно средней линии амплитуды шероховатости) 20 или 25% от толщины требуемой окончательной пленки для обеспечения хорошей адгезии пленки, т.е. шероховатость Ra в пределах 4-6 мкм минимум. Шероховатость была определена с помощью ругозиметра в соответствии со стандартом ISO 1997. Таблица 6 Шероховатость образцов для испытания как функция подготовки поверхности Как видно из табл. 6, относительно высокая шероховатость, полученная марганцевым фосфатированием, обеспечивает лучшую степень адгезии. Эта таблица показывает также, что очень слабо полярные подготовки поверхности, такие как электролитическое покрытие трехкомпонентным сплавом Cu-Sn-Zn,не способствуют адгезии. В свете этих первых результатов заявитель выбрал для определения коррозионной стойкости лишь подложки с естественно низкой стойкостью к коррозии, тем самым, исключая мартенситную нержавеющую сталь, содержащую 13% хрома, для которой критическая в части сцепления нагрузка для полиэфирэфиркетоновых пленок была более 180 Н. Толщина пленок, полученных холодным пневматическим распылением, была в пределах 20-45 мкм. Степень ржавления в пределах Re0 и Re9 была определена в соответствии со стандартом ISO 4528-3. Степень образования вздутия и отделения в пределах 2S2 (низкая концентрация вздутий и малых размеров) и 5S5 (распространенное вздутие и больших размеров) была определена в соответствии со стандартом ISO 4628-2. Результаты подытожены в табл. 7 и 8. Таблица 7 Коррозионная стойкость для разных подготовок поверхности с Vicote F805 Таблица 8 Коррозионная стойкость для разных подготовок поверхности с Vicote F807Blk Коррозионная стойкость подготовок поверхности, покрытых однослойной полиэфирэфиркетоновой пленкой, была в целом недостаточной за исключением электролитического покрытия сплавом Cu-Sn-Zn,несмотря на низкую адгезию или сильную потерю когезии пленки под напряжением. Кроме того, эти результаты показывают, что полиэфирэфиркетоновая пленка Vicote F807Blk, содержащая неорганическое соединение типа сажи, имеет относительно лучшую коррозионную стойкость по сравнению с VicoteF805 независимо от подготовки поверхности. Абсолютный лучший результат был получен в случае электролитического покрытия лишь с 5 коррозионными пятнами (язвами) после 1000 ч. Наблюдалось, что добавление электропроводного армирующего наполнителя в виде сажи усиливало механизм защиты от коррозии за счет его действия в качестве расходуемого анода. Наконец, заявитель оценил средние коэффициенты трения пленки, подвергавшейся абразивному износу посредством испытания царапанием в широком диапазоне нагрузки между 10 и 750 Н. Результаты подытожены в табл. 9. Таблица 9 Средние коэффициенты трения (испытание царапанием) Коэффициенты трения полиэфирэфиркетоновых пленок были ниже 0,135 независимо от подготовки поверхности и достигали 0,075 для среднего контактного давления 500 МПа для полиэфирэфиркетона,содержавшего фторированный полимер типа перфторалкоксиэтилена. Первые результаты показывают, что однослойные полиэфирэфиркетоновые пленки обладают достаточными смазывающими свойствами и антикоррозионными характеристиками, зависящими не только от состава пленки, но и от адгезии подложки. Затем на втором этапе заявитель разработал средство для улучшения адгезионных и антикоррозионных характеристик. Заявитель хотел заменить пескоструйную обработку, когда она была невозможной из-за геометрии частей, на которые должно быть нанесено покрытие. Прежде всего, заявитель провел исследования, не изменяя состав изученных промышленных пленок. Фактически, добавление промоторов адгезии или подавляющих коррозию наполнителей в количестве более 10% повышает PCV (концентрацию наполнителей по объему) выше PCV, для которой имеется как раз достаточно связующего, чтобы покрыть порошкообразные вещества (наполнители и заполнители), и, как результат, пористость и потерю когезии пленки, полученной из имеющихся в продаже водных суспензий. Возможны и другие альтернативы с использованием полиэфирэфиркетонового порошка Vicote 704. Заявитель исследовал увеличение адгезии с подслоем типа промотора адгезии. Непосредственная адгезия между материалами редка. Поскольку непосредственная адгезия в основном, но не единственным образом связана с взаимодействиями Ван-дер-Ваальса, она происходит с очень гладкими материалами, которые крайне чисты (например, слюда или кремний), приведенными в тесный контакт, т.е. в пределах расстояний на атомной шкале (нанометрических). Таким образом, это часто невозможно осуществить, если поверхности шероховаты, но, с другой стороны, полностью подходит для пленок с низкой шероховатостью. Таким образом, заявитель, в основном, исследовал пленку, совместимую со способом получения полиэфирэфиркетоновой пленки путем плавления при температуре 400C. Подслоем вместо фосфатации цинком может быть нанесенное покрытие сплавами железа и цинка,продаваемых под торговым наименованием Dacroforge Z компанией Dacral, но способ его получения механическим нанесением, эквивалентным пескоструйной/дробеструйной обработке, ограничивает его использование в полых телах, имеющих малые диаметры и коротких по высоте. Подслоем предпочтительно является наполненный полиарилэфиркетон. Раствор, содержащий interalia слюдяные наполнители типа мусковита или биотита в соотношениях в диапазоне от 25 до 50 вес.% в органическом полиэфирэфиркетоновом связующем, продается под торговым наименованием Vicote F817 компанией-поставщиком Victrex. Способ нанесения и плавления подслоя идентичен описанному для верхнего слоя. Отличие заключается в том, что требуется высокая скорость охлаждения для получения менее кристаллической структуры, которая обладает более высокими изолирующими свойствами, чтобы задержать возникновение коррозионных язв и уменьшить плотность тока пассивации материала. Толщина подслоя может быть 30-40 мкм. Антикоррозионные и адгезионные свойства подслоя, оцененные с использованием двух способов с разной кинетикой охлаждения, подытожены в табл. 10 и 11 соответственно. Таблица 10 Коррозионная стойкость для разных подготовок поверхности с подслоем Vicote F817 Таблица 11 Адгезионные характеристики и коэффициент трения для Vicote F817 Подслой из Vicote F817 обладал достаточными защитными и адгезионными, но недостаточными смазывающими свойствами. Смазывающие свойства были обеспечены верхним слоем из полиарилэфиркетона. Антикоррозионные, адгезионные свойства и характеристики трения двойного слоя подытожены в табл. 12 и 13. Общая толщина пленки, содержавшей подслой и верхний слой (верхнее покрытие), была в пределах 40-70 мкм. Таблица 12 Коррозионная стойкость для разных двухслойных подготовок поверхности Таблица 13 Адгезионные характеристики и коэффициент трения двойного слоя Коэффициенты трения для среднего контактного давления 500 МПа были достаточного низкими,особенно для пленки из Vicote F807 Blk, у которой =0,085 независимо от подготовки поверхности, и сравнимы с коэффициентами трения для фторэтановой и эпоксидной термореактивной пленки, и должны допускать получение значения стопорного крутящего момента стыковки менее 70% оптимального крутящего момента свинчивания. В целом, коэффициент трения, адгезия и защита от коррозии полиэфирэфиркетоновой пленки значительно улучшаются, предпочтительно полиэфирэфиркетоновым нижним слоем с заполнением слюдяным наполнителем, и, в частности, верхним слоем из полиэфирэфиркетона, содержащим по меньшей мере один фторированный полимер, пластически деформируемый под напряжением, и/или механический армирующий наполнитель типа сажи. Наконец, заявитель оценил трибореологическое поведение пленки посредством испытания Бриджмена для определения значения крутящего момента на стопоре. Значение крутящего момента на стопоре, полученное для Vicote F807 Blk, было равно 85% эталонного значения смазки API RP 5A3 на углеродистой стали XC48 и нержавеющей стали Z20C13. Однако трудность подготовки образцов, связанная со способом получения пленки, и малый диаметр образцов означают, что это значение нельзя считать абсолютным эталоном. Кристаллическая структура и много потенциальных межмолекулярных взаимодействий типа Ван-дер-Ваальса в полиэфирэфиркетоне указывают на мощную когезию материала и высокий предел прочности на сдвиг и, таким образом, вероятно на значительно более высокое значение крутящего момента на стопоре. Одновременно заявитель оценил противозадирные свойства пленки посредством испытания на машине Фалекса. Конфигурация испытания применительно к соединению может содержать паруV-образных блоков с разными подготовками поверхности, покрытыми пленкой ПЭЭК в один или два слоя, и индентор из углеродистой стали XC48 с поверхностью после станочной обработки или индентор из нержавеющей стали Z20C13, содержащей 13% хрома. Условия испытания с использованием нагрузки 785 Н соответствуют среднему давлению в контакте 150 МПа, которое относительно близко к давлению в контакте, зарегистрированному при свинчивании в начале упора на витках резьбы и опорной поверхности (100-300 МПа), и значению произведения давления на скорость (PV)=11,2 МПам/с, близкому к образовывающему закономерность износа при нарезании резьбы на опорных сторонах витков резьбы с PV=5 МПа м/с. Заявитель изучил армированные полиэфирэфиркетоны Vicote F805 и F807 Blk. Фиг. 6 показывает очень хорошую долговечность двухслойной пленки Vicote F817/Vicote F807 Blk по сравнению с воскообразным термопластичным раствором, используемым в настоящее время в соединении, и несмотря на поверхностную обработку типа электролитического покрытия трехкомпонентным сплавом, считающуюся противозадирной (см. документ WO 2008/032872). Задир, согласно определению этого термина в стандарте ASTM D2625-94, так и не был получен, хотя в случае с воскообразным термопластичным раствором HMS3 он был получен через 51 мин. Относительно низкий и постоянный коэффициент трения =0,08 характеризовал очень низкий абразивный износ. Для того чтобы определить пределы противозадирных свойств пленки, ниже заявитель оценил долговечность и коэффициент трения пленки с помощью испытания на машине Фалекса при растущих нагрузках в пределах 1335-4200 Н. Скорость скольжения была 10 мм/с в отличие от 20 мм/с ранее. Результаты показаны на фиг. 7. Эти результаты показывают, что задир не происходит при средних контактных давлениях 350 МПа,и подтверждают очень высокую износостойкость предлагаемой пленки. Кроме того, при повышении давления коэффициент трения снижался и был в пределах 0,056-0,078. С целью подтвердить противозадирные свойства и коэффициент трения, наблюдавшиеся в лаборатории при использовании испытания на машине Фалекса и испытания царапанием на образцах, в частности из углеродистой стали с электролитическим покрытием сплавом Cu-Sn-Zn, заявитель выполнил свинчивания на соединениях 7 29L80 VAM TOP HT, которые очень чувствительны к задиру. Крутящий момент свинчивания был 29900 Нм. Конец 2 с внутренней резьбой из углеродистой стали был обработан посредством электролитического покрытия, а конец 1 с наружной резьбой был обработан фосфатапией цинком и покрыт УФотверждаемой акриловой смолой, описанной в патентной публикации WO 2006/104251. Двухслойная пленка ПЭЭК была нанесена на обработанную муфту со скоростью охлаждения менее 5C/мин. Результаты свинчивания подытожены в табл. 14. Таблица 14 Сравнение результатов свинчивания 7 29L80 VAM TOP HT - CW UD Полученные результаты свинчивания подтверждают замечательные противозадирные свойства полиэфирэфиркетоновой пленки и, в частности, армированной полиэфирэфиркетоновой пленки. Таблица 15 Результаты свинчиваний соединения 7 29L80 VAM TOP HERETO Таким образом, предложена смазочная пленка, обладающая очень интересными противозадирными свойствами при ее нанесении на поверхность углеродистой стали или поверхность стали, содержащей по меньшей мере 13% хрома. Кроме того, она позволяет обойтись без электролитического покрытия двухкомпонентными (Cu-Sn) или трехкомпонентными (Cu-Sn-Zn) сплавами. ФОРМУЛА ИЗОБРЕТЕНИЯ 1. Резьбовой трубчатый компонент для бурения или эксплуатации углеводородных скважин, причем указанный трубчатый компонент, имеющий на одном из своих концов (1, 2) резьбовую зону(3, 4), выполненную на его наружной или внутренней периферийной поверхности, в зависимости от того,имеет резьбовой конец наружную или внутреннюю резьбу, по меньшей мере часть конца (1, 2) покрыта по меньшей мере одной смазывающей сухой пленкой (12), содержащей по меньшей мере 65 вес.% полиарилэфиркетона, отличающийся тем, что смазывающая сухая пленка (12) имеет структуру со степенью кристалличности в пределах 10-35%. 2. Резьбовой трубчатый компонент по п.1, отличающийся тем, что полиарилэфиркетон выбран из полиэфирэфиркетона (ПЭЭК), полиэфиркетона (ПЭК) и их смесей. 3. Резьбовой трубчатый компонент по любому из предыдущих пунктов, отличающийся тем, что смазывающая сухая пленка (12) содержит также по меньшей мере один твердый смазочный материал класса 4 в соотношениях в диапазоне от 10 до 35 вес.% 4. Резьбовой трубчатый компонент по п.3, отличающийся тем, что смазывающая сухая пленка (12) содержит сополимер перфторалкоксиэтилена в соотношениях в диапазоне от 10 до 30 вес.%. 5. Резьбовой трубчатый компонент по любому из предыдущих пунктов, отличающийся тем, что смазывающая сухая пленка (12) содержит механический армирующий агент, выбранный из перечня следующих наполнителей: сажа, слюда, волластонит, наноразмерный оксид алюминия, наноразмерный оксид титана, стеклянные порошки, наноалмаз, наноразмерные WS2 или WS2-фуллерены в соотношениях в диапазоне от 1 до 15 вес.%. 6. Резьбовой трубчатый компонент по любому из предыдущих пунктов, отличающийся тем, что часть, покрытая смазывающей сухой пленкой (12), предварительно прошла этап подготовки поверхности, выбранный из группы, состоящей из пескоструйной обработки, марганцевой фосфатации, электролитического покрытия Cu или сплавами Cu-Sn-Zn и сплавами Fe и Zn, нанесенными проецированием. 7. Резьбовой трубчатый компонент по любому из пп.1-5, отличающийся тем, что часть, покрытая смазывающей сухой пленкой (12), предварительно покрыта подслоем из полиэфирэфиркетона с полукристаллической структурой и содержащим слюдяные наполнители. 8. Резьбовой трубчатый компонент по любому из предыдущих пунктов, отличающийся тем, что вся резьбовая зона (3, 4) покрыта смазывающей сухой пленкой (12). 9. Резьбовой трубчатый компонент по любому из предыдущих пунктов, отличающийся тем, что содержит поверхность уплотнения металл-металл, причем указанная поверхность уплотнения покрыта смазывающей сухой пленкой (12). 10. Резьбовое трубное соединение, содержащее резьбовой трубчатый компонент с наружной резьбой и резьбовой трубчатый компонент с внутренней резьбой, ввинченные один в другой, отличающееся тем, что по меньшей мере один из указанных резьбовых трубчатых компонентов - по одному из предыдущих пунктов. 11. Способ покрытия резьбового трубчатого компонента для бурения или эксплуатации углеводородных скважин, причем указанный трубчатый компонент, имеющий на одном из своих концов (1, 2) резьбовую зону (3, 4), выполненную на его наружной или внутренней периферийной поверхности, в зависимости от того, имеет резьбовой конец наружную или внутреннюю резьбу, отличающийся тем, что включает следующие этапы, на которых получают смесь, содержащую полиарилэфиркетоновый порошок в суспензии в воде в соотношениях в диапазоне от 25 до 35 вес.%; указанную смесь наносят на часть конца (1, 2) указанного резьбового трубчатого компонента; часть конца (1, 2) с нанесенным таким образом покрытием сушат при температуре 100-150C в течение 5-10 мин; часть конца (1, 2) с нанесенным таким образом покрытием нагревают до температуры 350-450C в течение 5-15 мин со скоростью повышения температуры 10-20C/мин; часть конца (1, 2) с нанесенным таким образом покрытием охлаждают до температуры окружающей среды со скоростью охлаждения менее 10C/мин для получения практически кристаллической структуры. 12. Способ покрытия резьбового трубчатого компонента по п.11, отличающийся тем, что смесь также содержит коалесцирующий агент с высокой скоростью испарения с точкой кипения в пределах 100-200C и в соотношениях в диапазоне от 2,5 до 10 вес.%. 13. Способ покрытия резьбового трубчатого компонента по п.11 или 12, отличающийся тем, что смесь содержит также неионогенный смачивающий и диспергирующий агент в соотношениях в диапазоне от 2,5 до 10 вес.%. 14. Способ покрытия резьбового трубчатого компонента по любому из пп.11-13, отличающийся тем, что смесь содержит также по меньшей мере один твердый смазочный материал класса 4 в соотношениях в диапазоне от 3 до 12 вес.%. 15. Способ покрытия резьбового трубчатого компонента по п.14, отличающийся тем, что твердый смазочный материал класса 4 является сополимером перфторалкоксиэтилена в соотношениях в диапазоне от 3 до 12 вес.%. 16. Способ покрытия резьбового трубчатого компонента по п.14, отличающийся тем, что смесь также содержит механический армирующий агент, выбранный из перечня следующих наполнителей: сажа, слюда, волластонит, наноразмерный оксид алюминия, наноразмерный оксид титана, стеклянные порошки, наноалмаз, наноразмерные WS2 или WS2-фуллерены в соотношениях в диапазоне от 0,5 до 5 вес.%. 17. Способ покрытия резьбового трубчатого компонента по п.11, отличающийся тем, что часть конца (1, 2) покрывают, используя систему пневматического распыления, причем диаметр указанной системы находится в пределах 0,7-1,8 мм, а давление воздуха находится в пределах 4-6 бар. 18. Способ покрытия резьбового трубчатого компонента по любому из пп.11-17, отличающийся тем, что перед нанесением смеси на часть конца выполняют этап подготовки поверхности, выбранный из группы, состоящей из пескоструйной обработки, марганцевой фосфатации, электролитического покрытия Cu или сплавами Cu-Sn-Zn и частицами сплавов Fe и Zn, нанесенных проецированием. 19. Способ покрытия резьбового трубчатого компонента по любому из пп.11-17, отличающийся тем, что перед нанесением смеси на часть конца выполняют этап подготовки поверхности, на котором выполняют подслой из полиэфирэфиркетона с полукристаллической структурой и содержащий слюдяные наполнители. 20. Способ покрытия резьбового трубчатого компонента для бурения или эксплуатации углеводородных скважин, причем указанный трубчатый компонент имеет на одном из своих концов (1, 2) резьбовую зону (3, 4), выполненную на его наружной или внутренней периферийной поверхности, в зависимости от того, имеет резьбовой конец наружную или внутреннюю резьбу, отличающийся тем, что включает следующие этапы, на которых часть конца (1, 2) указанного резьбового трубчатого компонента нагревают до температуры в пределах 360-420C, предпочтительно до температуры, близкой к 400C; на часть конца (1, 2) указанного резьбового трубчатого компонента наносят порошки ПЭК и/или ПЭЭК; часть конца (1, 2) с нанесенным таким образом покрытием выдерживают при температуре в пределах 360-420C, предпочтительно при температуре, близкой к 400C, в течение 1-4 мин; часть конца (1, 2) с нанесенным таким образом покрытием охлаждают до температуры окружающей среды со скоростью охлаждения менее 10C/мин для получения практически кристаллической структуры. 21. Способ покрытия резьбового трубчатого компонента по п.20, отличающийся тем, что перед нагреванием части, на которую должно быть нанесено покрытие, выполняют этап, на котором указанную часть обезжиривают.
МПК / Метки
МПК: C10M 107/32
Метки: компонент, резьбового, резьбовой, покрытия, соединение, способ, трубчатый, трубчатого, результирующее, компонента
Код ссылки
<a href="https://eas.patents.su/20-24642-sposob-pokrytiya-rezbovogo-trubchatogo-komponenta-rezbovojj-trubchatyjj-komponent-i-rezultiruyushhee-soedinenie.html" rel="bookmark" title="База патентов Евразийского Союза">Способ покрытия резьбового трубчатого компонента, резьбовой трубчатый компонент и результирующее соединение</a>