Многослойный материал повышенной коррозионной стойкости (варианты) и способы его получения
Номер патента: 16878
Опубликовано: 30.08.2012
Авторы: Перелыгин Юрий Петрович, Первухина Ольга Леонидовна, Лось Ирина Сергеевна, Кирий Геннадий Владимирович, Абрамов Павел Иванович, Гордополов Юрий Александрович, Розен Андрей Андреевич, Розен Андрей Евгеньевич, Денисов Игорь Владимирович, Крюков Дмитрий Борисович, Усатый Сергей Геннадьевич, Первухин Леонид Борисович
Формула / Реферат
1. Многослойный материал повышенной коррозионной стойкости в средах, где водные растворы щелочей, солей кислот или кислот, анионы которых не являются окислителями, содержащий соединенные с помощью сплошного неразъемного соединения, чередующиеся нечетные и четные слои, при этом
нечетные наружные и внутренние слои выполнены из металлов или сплавов, характеризующихся в условиях контакта с указанной рабочей средой стационарным электрохимическим потенциалом в диапазоне от электрохимического потенциала полной пассивации до электрохимического потенциала перепассивации;
четные внутренние слои, являющиеся протекторными, выполнены из металлов или сплавов, характеризующихся в условиях контакта с указанной рабочей средой стационарным электрохимическим потенциалом, меньшим, чем стационарный электрохимический потенциал соседних нечетных слоев в тех же условиях.
2. Многослойный материал повышенной коррозионной стойкости в средах, где водные растворы щелочей, солей кислот или кислот, анионы которых являются окислителями, содержащий соединенные с помощью сплошного неразъемного соединения, чередующиеся нечетные и четные слои, при этом
нечетные наружные и внутренние слои выполнены из металлов или сплавов, характеризующихся в условиях контакта с указанной рабочей средой стационарным электрохимическим потенциалом в диапазоне от электрохимического потенциала полной пассивации до электрохимического потенциала перепассивации;
четные внутренние протекторные слои, являющиеся протекторными, выполнены из металлов или сплавов, характеризующихся в условиях контакта с указанной рабочей средой стационарным электрохимическим потенциалом, превышающим электрохимический потенциал металла или сплава наружного слоя в таких же условиях и имеющим величину в диапазоне от электрохимического потенциала полной пассивации материала наружного слоя до электрохимического потенциала перепассивации материала наружного слоя, и при этом обладающих меньшим водородным перенапряжением, чем материалы нечетных слоев.
3. Многослойный материал повышенной коррозионной стойкости, содержащий чередующиеся нечетные и четные слои, соединенные с помощью сплошного неразъемного соединения, при этом
первый, один из наружных, слой и ближайший к нему внутренний слой выполнены из металлов или сплавов, характеризующихся в условиях контакта с рабочей средой, содержащей водные растворы щелочей, солей кислот или кислот, анионы которых не являются окислителями, стационарным электрохимическим потенциалом в диапазоне от электрохимического потенциала полной пассивации до электрохимического потенциала перепассивации;
четный внутренний слой, прилегающий к первому наружному слою, выполнен из металлов или сплавов, характеризующихся в условиях контакта с рабочей средой, содержащей водные растворы щелочей, солей кислот или кислот, анионы которых не являются окислителями, стационарным электрохимическим потенциалом, меньшим, чем стационарный электрохимический потенциал соседних нечетных слоев в тех же условиях;
второй нечетный наружный слой и ближайший к нему нечетный внутренний слой выполнены из металлов или сплавов, характеризующихся в условиях контакта с рабочей средой, содержащей водные растворы щелочей, солей кислот или кислот, анионы которых являются окислителями, стационарным электрохимическим потенциалом в диапазоне от электрохимического потенциала полной пассивации до электрохимического потенциала перепассивации;
четный внутренний слой, прилегающий ко второму нечетному наружному слою, и другие четные слои, прилегающие к нечетным внутренним слоям, выполнены из металлов или сплавов, характеризующихся в условиях контакта с рабочей средой, содержащей водные растворы щелочей, солей кислот или кислот, анионы которых являются окислителями, стационарным электрохимическим потенциалом, превышающим электрохимический потенциал металла или сплава второго наружного слоя в таких же условиях и имеющим величину в диапазоне от электрохимического потенциала полной пассивации материала второго наружного слоя до электрохимического потенциала перепассивации материала второго наружного слоя, и при этом обладающих меньшим водородным перенапряжением, чем материалы соседних нечетных слоев.
4. Материал по любому из пп.1, или 2, или 3, отличающийся тем, что на наружном слое дополнительно содержится плакирующий слой оксидированного алюминия.
5. Материал по любому из пп.1, или 2, или 3, отличающийся тем, что материал выполнен в форме листов, пластин, лент, полос, уголков, швеллеров, двутавров, дисков, стержней различного профиля, труб различного профиля, колец; изделий конструктивной формы открытого профиля или замкнутого сплошного профиля или полого профиля проектных очертаний.
6. Способ получения многослойного материала повышенной коррозионной стойкости, включающий формирование сплошного неразъемного соединения слоев, выполненных из металлов и/или их сплавов и размещенных один слой на другом, при этом
в качестве материала нечетных слоев используют металлы или сплавы, характеризующиеся в условиях контакта с рабочей средой, содержащей водные растворы щелочей, солей кислот или кислот, анионы которых не являются окислителями, стационарным электрохимическим потенциалом в диапазоне от электрохимического потенциала полной пассивации до электрохимического потенциала перепассивации;
в качестве материала четных слоев используют металлы или сплавы, характеризующиеся в условиях контакта с указанной рабочей средой стационарным электрохимическим потенциалом, меньшим, чем стационарный электрохимический потенциал соседних нечетных слоев в таких же условиях.
7. Способ получения многослойного материала повышенной коррозионной стойкости, включающий формирование сплошного неразъемного соединения слоев, выполненных из металлов и/или их сплавов и размещенных один слой на другом, при этом
в качестве материала нечетных наружного и внутренних слоев используют металлы или сплавы, характеризующиеся в условиях контакта с рабочей средой, содержащей водные растворы щелочей, солей кислот или кислот, анионы которых являются окислителями, стационарным электрохимическим потенциалом в диапазоне от электрохимического потенциала полной пассивации до электрохимического потенциала перепассивации;
в качестве материала четных внутренних слоев используют металлы или сплавы, характеризующиеся в условиях контакта с рабочей средой, содержащей водные растворы щелочей, солей кислот или кислот, анионы которых являются окислителями, стационарным электрохимическим потенциалом, превышающим электрохимический потенциал металла или сплава наружного слоя в таких же условиях и имеющим величину в диапазоне от электрохимического потенциала полной пассивации материала наружного слоя до электрохимического потенциала перепассивации материала наружного слоя, и при этом обладающие меньшим водородным перенапряжением, чем материалы нечетных слоев.
8. Способ получения многослойного материала повышенной коррозионной стойкости, включающий формирование сплошного неразъемного соединения слоев, выполненных из металлов и/или их сплавов и размещенных один слой на другом, при этом
в качестве материала первого наружного слоя используют металлы или сплавы, характеризующиеся в условиях контакта с рабочей средой, содержащей водные растворы щелочей, солей кислот или кислот, анионы которых не являются окислителями, стационарным электрохимическим потенциалом в диапазоне от электрохимического потенциала полной пассивации до электрохимического потенциала перепассивации;
в качестве материала четного внутреннего слоя, прилегающего к первому наружному слою, используют металлы или сплавы, характеризующиеся в условиях контакта с рабочей средой, содержащей водные растворы щелочей, солей кислот или кислот, анионы которых не являются окислителями, стационарным электрохимическим потенциалом, меньшим, чем величина стационарного электрохимического потенциала соседних нечетных слоев в тех же условиях;
в качестве материала второго наружного слоя используют металлы или сплавы, характеризующиеся в условиях контакта с рабочей средой, содержащей водные растворы щелочей, солей кислот или кислот, анионы которых являются окислителями, стационарным электрохимическим потенциалом в диапазоне от электрохимического потенциала полной пассивации до электрохимического потенциала перепассивации;
в качестве материала четного внутреннего слоя, прилегающего ко второму наружному слою, и материала четных слоев, прилегающих к нечетным внутренним слоям, используют металлы или сплавы, характеризующиеся в условиях контакта с рабочей средой, содержащей водные растворы щелочей, солей кислот или кислот, анионы которых являются окислителями, стационарным электрохимическим потенциалом, превышающим электрохимический потенциал металла или сплава второго наружного слоя в таких же условиях и имеющим величину в диапазоне от электрохимического потенциала полной пассивации материала второго наружного слоя до электрохимического потенциала перепассивации материала второго наружного слоя, и при этом обладающие меньшим водородным перенапряжением, чем материалы соседних нечетных слоев.
9. Способ по п.8, отличающийся тем, что сплошное неразъемное соединение материалов слоев формируют путем соединения одного из наружных слоев первого многослойного материала, приспособленного для работы в условиях двухстороннего контакта с первой рабочей средой, содержащей водные растворы щелочей, солей кислот или кислот, анионы которых не являются окислителями, с одним из наружных слоев второго многослойного материала, приспособленного для работы в условиях двухстороннего контакта со второй рабочей средой, содержащей водные растворы щелочей, солей кислот или кислот, анионы которых являются окислителями.
10. Способ по любому из пп.6, или 7, или 8, отличающийся тем, что в качестве материалов четных слоев используют металлы или сплавы, дополнительно характеризующиеся в условиях контакта с рабочей средой образованием продуктов коррозии, имеющих объем больше, чем объем металла или сплава в слое до коррозии.
11. Способ по любому из пп.6, или 7, или 8, отличающийся тем, что указанное сплошное неразъемное соединение указанных четных и нечетных слоев формируют с помощью сварки взрывом и/или диффузионной сварки в вакууме, в инертных газах или в восстановительных газах; и/или высокочастотной сварки; и/или сварки прокаткой; и/или ручной дуговой наплавки; и/или механизированной наплавки плавящимся электродом сплошной или порошковой проволокой в среде инертных газов и смесях; и/или автоматической аргонодуговой наплавки; и/или автоматической наплавки ленточным электродом под флюсом; и/или автоматической наплавки проволочным электродом под флюсом; и/или автоматической наплавки порошковой проволокой в среде активных или инертных газов и в их смесях; и/или автоматической наплавки самозащитной порошковой проволокой или лентой; и/или электрошлаковой наплавки; и/или плазменной наплавки проволокой сплошного сечения или порошком; и/или газовой наплавки; и/или наплавки с индукционным нагревом.
12. Способ по любому из пп.6, или 7, или 8, отличающийся тем, что дополнительно наружный слой полученного многослойного материала плакируют алюминием предпочтительно с помощью взрывного плакирования и производят последующее оксидирование полученного плакирующего слоя предпочтительно с помощью микродугового оксидирования.
13. Способ по любому из пп.6, или 7, или 8, отличающийся тем, что формирование многослойных материалов осуществляют в форме листов, пластин, лент, полос, уголков, швеллеров, двутавров, дисков, стержней различного профиля, труб различного профиля, колец; изделий конструктивной формы открытого профиля или замкнутого сплошного профиля или полого профиля проектных очертаний.
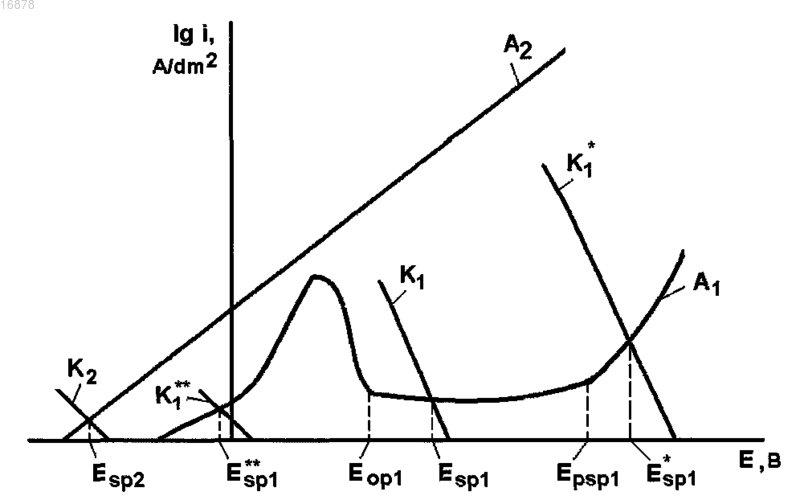
Текст
МНОГОСЛОЙНЫЙ МАТЕРИАЛ ПОВЫШЕННОЙ КОРРОЗИОННОЙ СТОЙКОСТИ Настоящее изобретение касается разработки вариантов конструкционных многослойных материалов повышенной коррозионной стойкости, содержащих последовательно соединенные наружные основные слои, непосредственно контактирующие с рабочими агрессивными средами с одной или двух сторон многослойного материала, и размещенные между ними чередующиеся внутренние основные и внутренние протекторные слои. При этом основные слои выполняют из металлических материалов, характеризующихся в течение длительного времени состоянием пассивности с последующим развитием в них коррозии питтингового типа, а внутренние протекторные слои, контактирующие с рабочей агрессивной средой по мере развития глубоких очагов питтинговой коррозии в предыдущих наружных и внутренних основных слоях,характеризуются развитием общей коррозии и оказывают протекторное действие в отношении наружных и внутренних основных слоев. Предложены способы получения таких материалов. Лось Ирина Сергеевна, Первухин Леонид Борисович, Перелыгин Юрий Петрович, Гордополов Юрий Александрович, Первухина Ольга Леонидовна (RU), Кирий Геннадий Владимирович (умер),Абрамов Павел Иванович, Усатый Сергей Геннадьевич, Крюков Дмитрий Борисович, Денисов Игорь Владимирович, Розен Андрей Андреевич, Розен Андрей Евгеньевич(71)(73) Заявитель и патентовладелец: РОЗЕН АНДРЕЙ ЕВГЕНЬЕВИЧ (RU) 016878 Область техники Изобретение относится к области электрохимии, материаловедения и металлургии, а именно - к конструкционным материалам, обладающим высокой коррозионной стойкостью и высокими механическими свойствами, в частности к металлическим многослойным конструкционным материалам и способам их получения. Предшествующий уровень техники До настоящего времени решение задачи повышения коррозионной стойкости металлических конструкционных материалов было основано на разработке дорогостоящих однослойных конструкционных материалов или многослойных материалов с использованием в качестве слоев, составляющих этот материал, металлов и их сплавов, обладающих высокой коррозионной стойкостью в агрессивных средах. При этом в качестве рабочей среды рассматривали абстрактную агрессивную среду без учета степени ее агрессивности и состава, а не конкретную среду, в которой этот материал будет использован при одностороннем или двухстороннем контакте. Однако учет свойств среды при выборе составляющих многослойного материала позволяет проводить оптимизацию выбора составляющих многослойного материала. Известен способ получения многослойного материала и многослойный материал, изготовленный сваркой взрывом по меньшей мере двух плакирующих слоев, промежуточного и заднего слоев(US 5323955 A1). Два плакирующих слоя выбирают из группы материалов с высокой коррозионной стойкостью, включающей Mo, W, Re, Ru, Pa, Pt, Au, Ag и их сплавы. Промежуточный слой изготавливают из материала, выбранного из группы, включающей медь, серебро, тантал и сплавы никеля. Задний слой изготавливают из материала, выбранного из группы, включающей низколегированную сталь, нержавеющую сталь, никель, медь, алюминий, титан и их сплавы. Также известен трехслойный металлический материал, полученный сваркой взрывом трех слоев: первого слоя из стали, второго слоя из никеля и меди, включающего медь от 65 до 75% и никель от 35% до 25%, и слоя титана, прилегающего к слою из никеля и меди (US 5190831 A1). Также известен многослойный материал (US 4839242 A1), который включает основной слой из стали, слой из никеля или никелевого сплава, который приварен к основному слою, слой из низкоуглеродистого сплава на основе железа, который содержит не более 0,01% углерода по весу и приварен к никелевому слою, и плакирующий слой из материала на основе титана, который приварен к слою из низкоуглеродистого сплава на основе железа. Также известны материалы из интерметаллических соединений, включающие опорный слой из нержавеющей мартенситной стали, имеющей твердость по Виккерсу 400 МПа или 400 HV и более, плакированный, например, слоем из титана или слоем из сплава титана через промежуточный слой, который выполнен, например, из материала, выбранного из группы, включающей никель, железо, сплавы меди с никелем, и способ получения этих материалов (US 6194088 A1). При этом на опорный слой может быть нанесена плакировка в виде жесткой пленки, верхняя поверхность которой является наружным слоем интерметаллического соединения, состоящего из соединений, выбранных из группы, включающей Ti-Ni интерметаллическое соединение, Ti-Fe интерметаллическое соединение, смесь Ti-Ni интерметаллического соединения и Ti-Cu интерметаллического соединения. Кроме того, плакировка может состоять из нескольких слоев. Например, плакировка может иметь внутренний слой из TiFe2 и внешний слой из TiFe,или иметь внутренний слой из TiC, а внешний - из TiFe, или иметь нижний слой из TiNi и внешний слой из TiNi3, или иметь нижний слой из TiNi и внешний слой - из TiCu. При этом осуществляют упрочнение указанного материала закалкой до твердости нержавеющей стали и при этом формируют жесткую пленку, выполненную из интерметаллического соединения титана. Процедура закаливания включает нагревание композиции до температуры от 900 до 1150C в течение от 30 с до 5 мин с последующим охлаждением со скоростью 1C/с или более. Также известен способ производства трехслойных полос, преимущественно в рулонах, с основным слоем из углеродистой стали и двусторонней плакировкой основного слоя коррозионно-стойкими сплавами из сталей аустенитного класса (SU 1447612 A1). При этом наплавкой или сваркой взрывом получают трехслойную заготовку, а затем осуществляют горячую прокатку этой заготовки при температуре 910-950C с последующим ее охлаждением со скоростью 10-100C/с. Наиболее близким к предлагаемому изобретению является материал, полученный соединением холодной прокаткой листов из ферритной нержавеющей стали или аустенитной нержавеющей стали на листе из низкоуглеродистой стали (JP 6293978 B). При этом поверхностный слой нержавеющей стали покрывают слоем олова или сплавом олова со свинцом толщиной 0,1-10,0 мкм. Возникающая в процессе эксплуатации в атмосфере солевой среды питтинговая коррозия нержавеющей стали подавляется и задерживается электрохимической коррозией наружных протекторов за счет электрической емкости олова или сплава олова и свинца. Протекторные слои указанного состава технологически не могут быть использованы для защиты других металлических материалов и сплавов, например никелевых или титановых сплавов, что обусловлено низкой адгезией к ним олова и свинца.-1 016878 Однако указанные выше технические решения разработаны без учета свойств рабочих сред, в контакте с которыми эксплуатируется полученный многослойный материал, что не позволяет оптимально использовать свойства материалов слоев, составляющих многослойный материал, например, для уменьшения его толщины, стоимости. Раскрытие изобретения Целью изобретения является создание конструкционного материала повышенной коррозионной стойкости, приспособленного для работы в условиях одностороннего или двухстороннего контакта с агрессивными средами одинаковой или различной активности. При создании изобретения была поставлена задача разработки материала повышенной коррозионной стойкости, имеющего многослойную структуру, содержащую последовательно соединенные наружные основные слои и размещенные между ними чередующиеся внутренние основные и внутренние протекторные слои, в котором наружные основные слои, непосредственно контактирующие с агрессивной средой с одной или двух сторон материала, и внутренние основные слои находились бы длительное время в состоянии пассивности, а развивающаяся в них коррозия была бы коррозией питтингового типа, а внутренние протекторные слои, контактирующие с рабочей агрессивной средой по мере развития глубоких очагов питтинговой коррозии в предыдущих наружных и внутренних основных слоях, находились бы длительное время в состоянии общей коррозии и при этом оказывали протекторное действие в отношении наружных и внутренних основных слоев. Также была поставлена задача разработки способов получения таких материалов. Поставленная задача была решена разработкой варианта многослойного материала повышенной коррозионной стойкости согласно изобретению, содержащего размещенные один на другом и соединенные с помощью сплошного неразъемного соединения чередующиеся нечетные и четные слои, отличающегося тем, что материал приспособлен для работы в условиях одностороннего или двустороннего контакта с рабочей средой, содержащей водные растворы щелочей, солей кислот или кислот, анионы которых не являются окислителями, и при этом имеет нечетные слои, являющиеся основными, и четные слои, являющиеся протекторными, и при этом содержит нечетные наружные и внутренние слои, выполненные из металлов или сплавов, характеризующихся в условиях контакта с указанной рабочей средой стационарным электрохимическим потенциалом в диапазоне от электрохимического потенциала полной пассивации до электрохимического потенциала перепассивации; четные внутренние слои, выполненные из металлов или сплавов, характеризующихся в условиях контакта с указанной рабочей средой стационарным электрохимическим потенциалом, меньшим, чем стационарный электрохимический потенциал соседних нечетных слоев в тех же условиях. Кроме того, поставленная задача была решена разработкой варианта многослойного материала повышенной коррозионной стойкости согласно изобретению, содержащего размещенные один на другом и соединенные с помощью сплошного неразъемного соединения чередующиеся нечетные и четные слои,отличающегося тем, что материал приспособлен для работы в условиях одностороннего или двустороннего контакта с рабочей средой, содержащей водные растворы щелочей, солей кислот или кислот, анионы которых являются окислителями, и при этом имеет нечетные слои, являющиеся основными, и четные слои, являющиеся протекторными, и при этом содержит нечетные наружные и внутренние слои, выполненные из металлов или сплавов, характеризующихся в условиях контакта с указанной рабочей средой стационарным электрохимическим потенциалом в диапазоне от электрохимического потенциала полной пассивации до электрохимического потенциала перепассивации; четные внутренние протекторные слои, выполненные из металлов или сплавов, характеризующихся в условиях контакта с указанной рабочей средой стационарным электрохимическим потенциалом, превышающим электрохимический потенциал металла или сплава наружного слоя в таких же условиях и имеющим величину в диапазоне от электрохимического потенциала полной пассивации материала наружного слоя до электрохимического потенциала перепассивации материала наружного слоя, и при этом обладающих меньшим водородным перенапряжением, чем материалы соседних нечетных слоев. Кроме того, поставленная задача была решена разработкой варианта многослойного материала повышенной коррозионной стойкости согласно изобретению, содержащего чередующиеся нечетные и четные слои, соединенные с помощью сплошного неразъемного соединения, отличающегося тем, что материал приспособлен для работы в условиях одновременного контакта первого нечетного наружного слоя с первой рабочей средой, содержащей водные растворы щелочей, солей кислот или кислот, анионы которых не являются окислителями, и контакта второго нечетного наружного слоя со второй рабочей средой,содержащей водные растворы щелочей, солей кислот или кислот, анионы которых являются окислителями, и при этом имеет нечетные слои, являющиеся основными, и четные слои, являющиеся протекторными, и при этом содержит первый нечетный наружный слой и ближайший к нему нечетный внутренний слой, выполненные из металлов или сплавов, характеризующихся в условиях контакта с предполагаемой первой рабочей средой стационарным электрохимическим потенциалом в диапазоне от электрохимического потенциала-2 016878 полной пассивации до электрохимического потенциала перепассивации; четный внутренний слой, прилегающий к первому нечетному наружному слою, выполненный из металлов или сплавов, характеризующихся в условиях контакта с первой предполагаемой рабочей средой стационарным электрохимическим потенциалом, меньшим, чем стационарный электрохимический потенциал соседних нечетных слоев в тех же условиях; второй нечетный наружный слой и ближайший к нему нечетный внутренний слой, выполненные из металлов или сплавов, характеризующихся в условиях контакта с предполагаемой второй рабочей средой стационарным электрохимическим потенциалом в диапазоне от электрохимического потенциала полной пассивации до электрохимического потенциала перепассивации; четный внутренний слой, прилегающий ко второму нечетному наружному слою, и других четные слои, прилегающие к нечетным внутренним слоям, выполненные из металлов или сплавов, характеризующихся в условиях контакта со второй предполагаемой рабочей средой стационарным электрохимическим потенциалом, превышающим электрохимический потенциал металла или сплава второго наружного слоя в таких же условиях и имеющим величину в диапазоне от электрохимического потенциала полной пассивации материала второго наружного слоя до электрохимического потенциала перепассивации материала второго наружного слоя, и при этом обладающих меньшим водородным перенапряжением,чем материалы соседних нечетных слоев. При этом согласно изобретению возможно, чтобы многослойные материалы на наружном слое дополнительно содержали плакирующий слой оксидированного алюминия. При этом согласно изобретению возможно, чтобы многослойные материалы согласно изобретению были изготовлены в форме листов, пластин, лент, полос, уголков, швеллеров, двутавров, дисков, стержней различного профиля, труб различного профиля, колец; изделий конструктивной формы открытого профиля или замкнутого сплошного профиля или полого профиля проектных очертаний. Поставленная задача была решена также разработкой способа получения многослойного материала повышенной коррозионной стойкости согласно изобретению, включающего формирование сплошного неразъемного соединения слоев, выполненных из металлов и/или их сплавов и размещенных один слой на другом, отличающегося тем, что способ приспособлен для получения многослойного материала, обладающего повышенной коррозионной стойкостью в условиях одностороннего или двустороннего контакта с рабочей средой, содержащей водные растворы щелочей, солей кислот или кислот, анионы которых не являются окислителями, при этом в качестве материала нечетных слоев используют металлы или сплавы, характеризующиеся в условиях контакта с предполагаемой рабочей средой стационарным электрохимическим потенциалом в диапазоне от электрохимического потенциала полной пассивации до электрохимического потенциала перепассивации; в качестве материала четных слоев используют металлы или сплавы, характеризующиеся в условиях контакта с указанной рабочей средой стационарным электрохимическим потенциалом, меньшим, чем стационарный электрохимический потенциал соседних нечетных слоев в таких же условиях. Кроме того, поставленная задача была решена созданием способа получения многослойного материала повышенной коррозионной стойкости согласно изобретению, включающего формирование сплошного неразъемного соединения слоев, выполненных из металлов и/или их сплавов и размещенных один слой на другом, отличающегося тем, что способ приспособлен для получения многослойного материала, обладающего повышенной коррозионной стойкостью в условиях одностороннего или двустороннего контакта с рабочей средой, содержащей водные растворы щелочей, солей кислот или кислот, анионы которых являются окислителями, и при этом в качестве материала нечетных наружного и внутренних слоев используют металлы или сплавы,характеризующиеся в условиях контакта с предполагаемой рабочей средой стационарным электрохимическим потенциалом в диапазоне от электрохимического потенциала полной пассивации до электрохимического потенциала перепассивации; в качестве материала четных внутренних слоев используют металлы или сплавы, характеризующиеся в условиях контакта с указанной рабочей средой стационарным электрохимическим потенциалом,превышающим электрохимический потенциал металла или сплава наружного слоя в таких же условиях и имеющим величину в диапазоне от электрохимического потенциала полной пассивации материала наружного слоя до электрохимического потенциала перепассивации материала наружного слоя, и при этом обладающие меньшим водородным перенапряжением, чем материалы нечетных слоев. Кроме того, поставленная задача была решена созданием способа получения многослойного материала повышенной коррозионной стойкости согласно изобретению, включающего формирование сплошного неразъемного соединения слоев, выполненных из металлов и/или их сплавов и размещенных один слой на другом, отличающегося тем, что способ приспособлен для получения многослойного материала, обладающего повышенной коррозионной стойкостью в условиях одновременного контакта первого наружного слоя с первой рабочей средой, содержащей водные растворы щелочей, солей кислот или кислот, анионы которых не являются окислителями, и контакта второго наружного слоя со второй рабочей средой, содержащей водные растворы щелочей, солей кислот или кислот, анионы которых являются окислителями; и в котором-3 016878 формируют сплошное неразъемное соединение материалов, по меньшей мере, пяти слоев, и при этом в качестве материала первого наружного слоя используют металлы или сплавы, характеризующиеся в условиях контакта с первой предполагаемой рабочей средой стационарным электрохимическим потенциалом в диапазоне от электрохимического потенциала полной пассивации до электрохимического потенциала перепассивации; в качестве материала четного внутреннего слоя, прилегающего к первому наружному слою, используют металлы или сплавы, характеризующиеся в условиях контакта с предполагаемой первой рабочей средой стационарным электрохимическим потенциалом, меньшим, чем величина стационарного электрохимического потенциала соседних нечетных слоев в тех же условиях; в качестве материала второго наружного слоя используют металлы или сплавы, характеризующиеся в условиях контакта с предполагаемой второй рабочей средой стационарным электрохимическим потенциалом в диапазоне от электрохимического потенциала полной пассивации до электрохимического потенциала перепассивации; в качестве материала четного внутреннего слоя, прилегающего ко второму наружному слою, и материала четных слоев, прилегающих к нечетным внутренним слоям, используют металлы или сплавы,характеризующиеся в условиях контакта с предполагаемой второй рабочей средой стационарным электрохимическим потенциалом, превышающим электрохимический потенциал металла или сплава второго наружного слоя в таких же условиях и имеющим величину в диапазоне от электрохимического потенциала полной пассивации материала второго наружного слоя до электрохимического потенциала перепассивации материала второго наружного слоя, и при этом обладающие меньшим водородным перенапряжением, чем материалы соседних нечетных слоев. При этом согласно изобретению целесообразно в качестве материалов четных слоев использовать металлы или сплавы, дополнительно характеризующиеся в условиях контакта с предполагаемой рабочей средой образованием продуктов коррозии, имеющих объем больше, чем объем металла или сплава в слое до коррозии. При этом согласно изобретению при получении многослойного материала для работы в условиях одновременного двухстороннего контакта с первой и второй рабочими средами возможно формировать сплошное неразъемное соединение материалов слоев путем соединения одного из наружных слоев первого многослойного материала, приспособленного для работы в условиях двухстороннего контакта с первой рабочей средой, с одним из наружных слоев второго многослойного материала, приспособленного для работы в условиях двухстороннего контакта со второй рабочей средой. При этом согласно изобретению возможно формировать указанное сплошное неразъемное соединение указанных четных и нечетных слоев с помощью сварки взрывом и/или диффузионной сварки в вакууме, в инертных газах или в восстановительных газах; и/или высокочастотной сварки; и/или сварки прокаткой; и/или ручной дуговой наплавки; и/или механизированной наплавки плавящимся электродом сплошной или порошковой проволокой в среде инертных газов и смесях; и/или автоматической аргонодуговой наплавки; и/или автоматической наплавки ленточным электродом под флюсом; и/или автоматической наплавки проволочным электродом под флюсом; и/или автоматической наплавки порошковой проволокой в среде активных или инертных газов и в их смесях; и/или автоматической наплавки самозащитной порошковой проволокой или лентой; и/или электрошлаковой наплавки; и/или плазменной наплавки проволокой сплошного сечения или порошком; и/или газовой наплавки; и/или наплавки с индукционным нагревом. При этом согласно изобретению возможно дополнительно наружный слой полученного многослойного материала плакировать алюминием предпочтительно с помощью взрывного плакирования и производить последующее оксидирование полученного плакирующего слоя предпочтительно с помощью микродугового оксидирования. При этом согласно изобретению возможно формирование многослойных материалов осуществлять в форме листов, пластин, лент, полос, уголков, швеллеров, двутавров, дисков, стержней различного профиля, труб различного профиля, колец; изделий конструктивной формы открытого профиля или замкнутого сплошного профиля или полого профиля проектных очертаний. Краткое описание чертежей В дальнейшем изобретение поясняется описанием вариантов многослойных материалов повышенной коррозионной стойкости согласно изобретению, примеров осуществления способа получения многослойных материалов согласно изобретению и прилагаемыми чертежами, на которых показаны: фиг. 1 - схематичные анодные и катодные поляризационные кривые наружного основного слоя многослойного материала согласно изобретению для варианта наружного слоя, контактирующего с агрессивной рабочей средой, которая содержит водные растворы щелочей, солей кислот или кислоты,анионы которых не являются окислителями, и соседнего с ним внутреннего протекторного слоя; фиг. 2 - схематичные анодные и катодные поляризационные кривые наружного основного слоя многослойного материала согласно изобретению для варианта наружного слоя, контактирующего с агрессивной рабочей средой, которая содержит водные растворы щелочей, солей кислот или кислот, анионы которых являются окислителями, и соседнего с ним внутреннего протекторного слоя.-4 016878 При этом приведенные ниже примеры не ограничивают возможностей осуществления изобретения и не выходят за рамки пунктов формулы изобретения. Наилучшие варианты осуществления изобретения Многослойный материал повышенной коррозионной стойкости согласно изобретению может быть получен способом согласно изобретению, в котором формируют последовательно сплошное неразъемное соединение основных и протекторных слоев, выполненных из металлов и/или их сплавов, имеющих определенные свойства в условиях контакта с рабочими средами и размещенных один слой на другом. Такие соединения могут быть получены с помощью известных технологических приемов, например согласно изобретению с помощью сварки взрывом и/или диффузионной сварки в вакууме, в инертных газах или в восстановительных газах; и/или высокочастотной сварки; и/или сварки прокаткой; и/или ручной дуговой наплавки; и/или механизированной наплавки плавящимся электродом сплошной или порошковой проволокой в среде инертных газов и смесях; и/или автоматической аргонодуговой наплавки; и/или автоматической наплавки ленточным электродом под флюсом; и/или автоматической наплавки проволочным электродом под флюсом; и/или автоматической наплавки порошковой проволокой в среде активных или инертных газов и в их смесях; и/или автоматической наплавки самозащитной порошковой проволокой или лентой; и/или электрошлаковой наплавки; и/или плазменной наплавки проволокой сплошного сечения или порошком; и/или газовой наплавки; и/или наплавки с индукционным нагревом. При этом согласно изобретению многослойный материал может быть сформирован в форме готового изделия, например трубы, диска, изделий сложной пространственной конфигурации, изделий различного профиля, сплошных или полых. При необходимости сформированное изделие из многослойного материала, например пластина, полоса, лист, труба, может быть подвергнуто холодной или горячей прокатке для получения желаемых параметров. Кроме того, согласно изобретению возможно дополнительно наружный слой полученного многослойного материала плакировать алюминием, предпочтительно с помощью взрывного плакирования, и производить последующее оксидирование полученного плакирующего слоя предпочтительно с помощью микродугового оксидирования. В способе получения многослойных материалов повышенной коррозионной стойкости согласно изобретению используют материалы или сплавы, имеющие согласно изобретению определенные характеристики их электрохимического взаимодействия с предполагаемой рабочей средой при контакте с ней,обусловливающие пассивное или активное состояние материалов слоев многослойного материала. При этом в зависимости от химической и электрохимической активности рабочей среды в условиях одностороннего или двухстороннего контакта с наружными поверхностями основных слоев и с внутренними протекторными и основными слоями, в том числе в пограничных зонах между слоями, для изготовления слоев многослойных материалов используют различные материалы или сплавы. Известно, что в различных материалах процесс коррозии протекает по-разному. В коррозионностойких материалах или сплавах коррозия начинается в основном с образованием очагов питтинговой коррозии. Однако возникновение даже незначительного количества локализованных поверхностных очагов питтинга приводит к нарушению сплошности поверхности конструкционного материала, к образованию каналов, открытых для проникновения в них рабочей среды, что приводит к развитию глубоких очагов коррозии и потере прочности материала. В материалах, обладающих низкой коррозионной стойкостью, развивается, как правило, коррозия общего типа, с разрушением массива материала и образованием различных продуктов коррозии. На фиг. 1 и 2 представлены схематичные анодная A1 и катодная поляризационные кривые K1 одного коррозионно-стойкого металлического материала 1 (металла или сплава) и анодная A2 и катодная K2 поляризационные кривые другого металлического материала 2 (металла или сплава), обладающего низкой коррозионной стойкостью, при их контакте с рабочей средой, которая содержит водные растворы щелочей, солей кислот или кислоты, анионы которых не являются окислителями (фиг. 1), и с рабочей средой, которая содержит водные растворы щелочей, солей кислот или кислот, анионы которых являются окислителями (фиг. 2). При этом показаны зависимости электрохимического потенциала материалов 1 и 2 от плотности поляризационного тока i. Из анодной поляризационной кривой A1 (фиг. 1) видно, что в процессе длительного контакта с указанной средой материал 1 изменяет свое состояние, и, соответственно, изменяется его химическая и электрохимическая активность, характеризуемая электрохимическим потенциалом E в данной среде. При постепенном увеличении анодного потенциала материала 1, связанном с образованием оксидных соединений, плотность анодного тока i снижается. Электрохимический потенциал материала 1 смещается в положительную сторону от значения электрохимического стационарного потенциала (electrochemical stationary potential) материала 1 ESP1 до ESP1. Таким образом, образованные соединения формируют защитную пленку, препятствующую коррозии материала 1. Во время образования оксидных соединений плотность анодного поляризационного тока падает, электрохимический потенциал материала 1 постепенно растет, достигая величины электрохимического потенциала полной пассивности EOP1 (electrochemical overall potential). В дальнейшем при практически неизменной плотности поляризационного тока электрохимический потенциал материала 1 растет по величине в диапазоне от электрохимического-5 016878 потенциала полной пассивности EOP1 до электрохимического потенциала перепассивации EPRP1 (electrochemical potential of repassivation). В указанном диапазоне состояние материала 1 характеризуется как пассивное. Чем больше диапазон между EOP1 и EPRP1 и чем меньше при этом величина плотности поляризационного тока, тем большей коррозионной стойкостью обладает материал 1 в рабочей среде. При дальнейшем взаимодействии коррозионно-стойкого материала 1 с рабочей средой в материале начинается коррозия с образованием очагов питтинговой коррозии, например, вследствие неоднородности сформировавшейся защитной оксидной пленки или поверхностной неоднородности материала 1, и при этом электрохимический потенциал материала 1 увеличивается более EPRP1. Состояние материала 1 в точке пересечения анодной A1 и катодной K1 поляризационных кривых оценивается как стационарное в отношении процессов растворения материала в качестве анода и в качестве катода, на котором протекают реакции восстановления, и характеризуется величиной стационарного электрохимического потенциала ESP1 в рабочей среде и соответствующей ему величиной минимально возможного тока коррозии. При величинах EESP1 в коррозионно-стойком материале 1 начинают постепенно превалировать процессы растворения материала в очагах питтинга, а при величинах ЕESP1 превалируют процессы восстановления кислорода или водорода на материале 1. Таким образом, в зависимости от эффекта, который необходимо получить при эксплуатации материала 1 в указанных рабочих средах,для повышения коррозионной стойкости основных конструкционных слоев материала необходимо обеспечить гарантированное воздействие на него других протекторных слоев, обеспечивающих поддержание материала 1 в состоянии, близком к пассивному (фиг. 2), предпочтительно, к стационарному состоянию,характеризуемому величиной электрохимического стационарного потенциала ESP1, или в состоянии катода, на котором будут протекать реакции восстановления иона водорода или молекулы кислорода(фиг. 1). Характер анодных A2 и катодных K2 поляризационных кривых материала 2 (фиг. 1), обладающего невысокой коррозионной стойкостью, показывает, что материал 2 при взаимодействии с указанными средами не способен к пассивации, и превалирующими процессами являются процессы растворения материала 2, при этом при значительном градиенте поляризационного тока электрохимический потенциал материала 2 меняется медленнее. Характер анодных A2 и катодных K2 поляризационных кривых материала 2 (фиг. 2), обладающего коррозионной стойкостью выше материала 1, показывает, что материал 2 находится в неизменном состоянии, а материал 1 находится в пассивном состоянии и характеризуется потенциалом, величина которого является точкой пересечения катодной кривой K2 и анодной кривой A1 (ESP12). В процессе электрохимического взаимодействия материалов 1 и 2 с рабочей средой в зависимости от состава среды в приповерхностном слое происходит выделение водорода или восстановление кислорода. В присутствии восстановленного кислорода ток коррозии может быть обусловлен растворением материала 1 или 2 или пассивации материала за счет образования трудно растворимых химически инертных соединений, в присутствии атомарного водорода будут происходить процессы замедления коррозии за счет образования оксидных упрочняющих пленок, снижающих электрохимический потенциал материала в указанных рабочих средах. Согласно изобретению решена проблема поддержания конструкционных коррозионно-стойких материалов в течение длительного периода в состоянии слабо развивающейся питтинговой коррозии путем создания многослойных материалов, содержащих основные слои из материалов, характеризующихся равновесным состоянием при общем состоянии пассивности материала, поддерживаемым с помощью воздействия на материалы основных слоев продуктов растворения протекторных слоев и обеспечения протекания тока коррозии в определенном заданном направлении. На фиг. 1 и 2 проиллюстрированы процессы влияния протекторных слоев из материала 2 на материалы 1 основных конструкционных слоев. При этом в зависимости от того, содержит ли рабочая среда анионы, являющиеся окислителями, основные слои многослойного материала согласно изобретению выполнены из разных материалов, коррозионная стойкость которых в виде отдельного материала не является очень высокой, но в сочетании с электрохимической активностью внутренних соседних протекторных слоев позволяет поддерживать основные слои в состоянии заданной степени пассивности. Так, согласно изобретению, материал наружного основного слоя, контактирующего с рабочей средой, выбирают таким образом, чтобы в условиях взаимодействия этого материала с рабочей средой стационарный потенциал материала ESP1 этого слоя лежал в области пассивности этого материала, т.е. стационарный потенциал материала 1 ESP1 удовлетворял неравенству EOP1ESP1EPRP1. В качестве материала 2 для многослойного материала согласно изобретению, приспособленного для эксплуатации в условиях взаимодействия с рабочей средой, содержащей анионы, не являющиеся окислителями, выбран материал, характеризующийся меньшим, чем у материала 1, стационарным потенциаломESP2ESP1 (кривые A2 и K2 на фиг. 1). Под воздействием процессов, протекающих в материале 2, электрохимический потенциал материала 2 остается более высоким, чем потенциал материала 1, что в области контакта материалов 1 и 2 в каналах питтинга обеспечивает направление тока коррозии к материалу 2,защищая при этом материал 1. Внутренний протекторный слой становится анодом и начинает растворяться, а соседние основные слои становятся катодами.-6 016878 При достижении рабочей средой пограничной поверхности соседнего с ним внутреннего протекторного слоя начинается коррозия материала 2 по общему типу, с растворением материала 2 и восстановлением кислорода на пограничной поверхности материала 1. При этом в пограничных поверхностях материала 1 образуется пленка из окисных соединений, замедляющая процесс питтингообразования в материале 1 основного слоя, снижается скорость поступления рабочей среды через питтинговые каналы и процесс растворения материала 2 замедляется. Реакция может протекать вплоть до полного растворения материала внутреннего протекторного слоя. Катодная поляризационная кривая K1 материала 1 смещается сначала до положения кривой K1 с образованием области равновесных процессов при наличии слабо развивающихся очагов питтинга (область ESP1), а затем по мере усиления защитной оксидной пленки смещается в положение кривой K1, что фактически замедляет процессы химического взаимодействия материала 1 с рабочей средой, что также приводит к повышению коррозионной стойкости. Согласно изобретению в случае использования в качестве основных слоев материала, продукты коррозии которого имеют больший объем, чем объем материала в очаге коррозии, происходит постепенное зашлаковывание питтинговых каналов, и процесс питтинговой коррозии замедляется. Этот прием недостаточен для значительного повышения коррозионной стойкости, однако согласно изобретению может служить дополнительным приемом для повышения коррозионной стойкости многослойного материала. В качестве слоев многослойного материала согласно изобретению, приспособленного для эксплуатации в условиях взаимодействия с рабочей средой, содержащей анионы, являющиеся окислителями,используют разные материалы. Так же, как и в предыдущем случае, материал 1 наружного основного слоя выбирают из материалов, в которых при взаимодействии с выбранной агрессивной средой образуется защитная оксидная пленка, и стационарный потенциал материала 1 лежит в области пассивности этого материала, т.е. стационарный потенциал материала 1 удовлетворяет неравенству EOP1ESP1EPRP1. Материал 2 выбирают таким образом, чтобы величина его стационарного электрохимического потенциалаESP2 в условиях контакта с предполагаемой рабочей средой находилась в интервале значений от электрохимического потенциала полной пассивации материала 1 до электрохимического потенциала перепассивации материала 1: EOP1ESP2EPRP1, при этом стационарный электрохимический потенциал ESP2 был более высоким, чем у материала 1: ESP2ESP1. Кроме того, материал 2 протекторного четного слоя должен обладать водородным перенапряжением, меньшим, чем материал 1. В этом случае весь материал 1 основного слоя становится анодом, а материал 2 внутреннего протекторного слоя становится катодом. Происходит растворение материала 1. Реакции, протекающие на 2-м слое, характеризует кривая K2, которая пересекает анодную поляризационную кривую A1 в точке, соответствующей стационарному электрохимическому потенциалу ESP12 системы материалов 1 и 2 в материале 2 в зоне контакта с каналом питтинга материала 1. Это значение должно находиться в диапазоне значений EOP1-EPRP1 материала 1-го слоя, в этом случае материал 1 возвращается в пассивное состояние. В качестве материалов третьего и последующих нечетных основных слоев можно использовать материалы, идентичные материалу 1. Третий слой будет взаимодействовать с рабочей средой лишь в случае, когда область общей коррозии предыдущего протекторного слоя достигнет значительного размера. Тогда третий слой становится вторым анодом и в соответствии с поляризационной диаграммой, представленной на фиг. 2, и будет находиться в пассивном состоянии. Скорость реакции будет мала, т.к. процесс лимитируется химической стадией растворения пассивной пленки. На третьем слое протекают те же самые реакции, что и на первом. При образовании сквозных каналов питтинга в третьем слое начинается процесс коррозии четвертого слоя. Этот процесс аналогичен процессу коррозии второго протекторного слоя, т.е. четвертый слой является протектором как для третьего, так и для пятого слоев. Процесс коррозии в последующих слоях также аналогичен процессу в первых трех слоях. В случае использования многослойного материала в условиях одновременного контакта с рабочей средой, содержащей водные растворы щелочей, солей кислот или кислот, анионы которых не являются окислителями, с одной стороны материала и контакта с рабочей средой, содержащей водные растворы солей кислот или кислот, анионы которых являются окислителями, с другой стороны материала, согласно изобретению формируют многослойный материал путем сплошного неразъемного соединения многослойного материала, приспособленного для работы в условиях одностороннего или двустороннего контакта с рабочей средой, содержащей водные растворы щелочей, солей кислот или кислот, анионы которых не являются окислителями, с многослойным материалом, приспособленным для работы в условиях одностороннего или двустороннего контакта с рабочей средой, содержащей водные растворы щелочей,солей кислот или кислот, анионы которых являются окислителями. В этом случае оценивают время коррозионного процесса до достижения очагом коррозии центральной части многослойного материала с каждой стороны материала. При равенстве оценочного времени коррозии с каждой стороны осуществляют сплошное неразъемное соединение между одним из поверхностных слоев многослойного материала, приспособленного для работы в условиях контакта с рабочей средой, содержащей водные растворы щелочей, солей кислот или кислот, анионы которых не являются окислителями, и одним из поверхностных слоев многослойного материала согласно изобретению, приспособленного для работы в условиях контакта с рабочей средой, содержащей водные растворы щело-7 016878 чей, солей кислот или кислот, анионы которых являются окислителями. При этом процессы, происходящие в материале с одной его стороны, аналогичны процессам, рассмотренным в первом случае, а с другой стороны - аналогичны процессам, рассмотренным во втором случае. При времени распространения коррозионного процесса, меньшем со стороны среды, содержащей водные растворы щелочей, солей кислот или кислот, анионы которых не являются окислителями, между слоями, которые должны соединяться, устанавливают промежуточный слой, аналогичный четному слою,описанному в первом случае, а если время распространения коррозионного процесса со стороны этой среды больше, чем с противоположной стороны, в качестве протекторного слоя используют промежуточный слой, аналогичный четному слою, рассмотренному во втором случае. При этом согласно изобретению многослойный материал может быть сформирован в форме готового изделия, например трубы, диска, изделий сложной пространственной конфигурации, изделий различного профиля, сплошных или полых. При необходимости сформированное изделие из многослойного материала, например пластина, полоса, лист, труба, может быть подвергнута холодной или горячей прокатке для получения желаемых параметров. Кроме того, согласно изобретению возможно дополнительно наружный слой полученного многослойного материала плакировать алюминием предпочтительно с помощью взрывного плакирования и производить последующее оксидирование полученного плакирующего слоя предпочтительно с помощью микродугового оксидирования. Ниже приведены примеры, иллюстрирующие проведенные испытания различных вариантов многослойного материала повышенной коррозионной стойкости согласно изобретению, полученных способами получения многослойных материалов согласно изобретению. Элементный состав используемых материалов слоев приведен в табл. 1-6. Таблица 1 Многослойные материалы согласно изобретению подвергали длительному воздействию рабочих сред. Коррозионную стойкость C многослойного материала согласно изобретению оценивали по длительности периода до возникновения очагов коррозии, наличию, характеру и скорости развития коррозионных очагов в каждом из слоев, в сравнении с коррозионной стойкостью Ci материала наружного основного слоя в условиях контакта с такой же рабочей средой. Для контроля за процессом развития коррозии можно использовать бесконтактные методы контроля, например голографическую интерферометрию или ультразвуковую дефектоскопию. Пример 1. Многослойный материал согласно изобретению был изготовлен для эксплуатации в условиях одностороннего контакта с рабочей средой, содержащей 1%-ный водный раствор хлорида натрия, при этом в качестве материала первого наружного основного слоя, контактирующего с рабочей средой, и третьего наружного основного слоя, контактирующего с обычной окружающей средой, была выбрана коррозионно-стойкая сталь А, элементный состав которой приведен в табл. 1, имеющая в указанной рабочей среде электрохимический стационарный потенциал ESPA=+0,2 В. При этом значение ESPA находится в диапазоне между электрохимическим потенциалом полной пассивации EOPA=+0,05 В и электрохимическим потенциалом перепассивации EPRPA=+0,4 В. В качестве материала внутреннего протекторного слоя была выбрана углеродистая конструкционная качественная сталь В, имеющая в указанной рабочей среде стационарный потенциал ESPB=-0,44 В меньше ESPA=+0,2 В. Трехслойные заготовки состава A-B-A размерами 10015006000 мм с толщиной слоя коррозионно-стойкой стали A по 10 мм с каждой стороны и углеродистой стали В толщиной 80 мм согласно изобретению были получены сваркой взрывом. Заготовки сваривали в две технологические операции, наваривая за прием один слой коррозионно-стойкой стали A с одной из сторон слоя углеродистой стали В. Сварку производили при величине зазора между листами 3-7 мм со скоростью детонации взрывчатого вещества 2500-2900 м/с и массовой скоростью 350-440 м/с. В полученном трехслойном материале слои прочно соединены, наличия зон промежуточного состава и отслоений не обнаружено. Образцы в форме пластин, выполненные из листов изготовленного трехслойного материала, были подвергнуты испытаниям в условиях контакта наружного слоя с указанной средой - 1%-ным водным раствором хлорида натрия в течение длительного периода времени - 4350 ч. При этом проводили мониторинг состояния материалов A первого наружного слоя, контактирующего с рабочей средой, второго внутреннего слоя B и третьего наружного слоя A, обращенного в обычную окружающую среду. В том числе, исследовали очаги коррозии и образующиеся продукты коррозии материалов A и внутренних пограничных поверхностей слоев материалов A и B при различных температурах рабочей среды в диапазоне от 5 до 220C. В результате исследований было установлено, что при продолжительном контакте с рабочей средой в первом наружном слое A трехслойного материала возникают очаги коррозии питтингового типа, количество, глубина и площадь которых увеличиваются очень медленно. В процессе развития и углубления очагов питтинга в первом слое A рабочая среда проникает внутрь каналов очагов питтинга. Согласно изобретению в случае использования в качестве основного слоя материала, продукты коррозии которого имеют больший объем, чем объем материала в очаге коррозии, происходит постепенное зашлаковывание питтинговых каналов, и процесс питтинговой коррозии замедляется.-9 016878 При достижении рабочей средой пограничной поверхности внутреннего протекторного слоя B начинается коррозия материала В по общему типу, с растворением материала B и восстановлением кислорода на пограничной поверхности слоя A. При этом в пограничных поверхностях слоя материала A, соседних с пограничными поверхностями материала B, образуется пленка из окисных соединений, замедляющая процесс питтингообразования в материале первого наружного основного слоя A и процесс разрушения материала B внутреннего протекторного слоя. Третий наружный основной слой не подвергается коррозии. Коррозионная стойкость трехслойного материала в указанной среде по сравнению с коррозионной стойкостью аналогичного однослойного материала A такой же толщины выше в 3,0-5,5 раз в зависимости от температуры рабочей среды. Большие значения увеличения коррозионной стойкости соответствуют более высокой температуре среды. Пример 2. Многослойный материал согласно изобретению был изготовлен для эксплуатации в условиях одностороннего контакта с рабочей средой, содержащей 5%-ный водный раствор сульфата калия при температуре от 5 до 220C, выполнен трехслойным, при этом наружные основные слои были выполнены из материала D и соединены с внутренним протекторным слоем C из низколегированной стали с помощью механизированной наплавки плавящимся электродом в среде инертных газов и смесях. Состав наплавленных наружных основных слоев соответствует составу плавящегося электрода, применяемого при наплавке - материалу D. Стационарный потенциал коррозионно-стойкой стали D в указанной рабочей среде ESPD=+0,22 В. Указанное значение находится в интервале между значениями электрохимического потенциала полной пассивации EOPD=+0,06 В и электрохимического потенциала перепассивации EPRPD=+0,45 В. Стационарный потенциал стали C внутреннего протекторного слоя составляет ESPC=-0,4 В. Наплавку наружных основных слоев D осуществляли в нижнем пространственном положении электродом диаметром 2,0 мм в два приема, с кантовкой заготовки на 180, в следующем режиме: величина тока наплавки 280-320 A; величина напряжения наплавки 26-32 В; вылет электрода 12-16 мм; объем расхода защитного газа (аргона) 14-18 л/мин. Перед наплавкой проводили местный подогрев внутреннего протекторного слоя C газовой горелкой до температуры 550+50C. Толщина каждого из наплавленных слоев D после дополнительного отделочного фрезерования с удалением припуска 2,0 мм составляла 5,0 мм при толщине 20,0 мм протекторного слоя стали C. Габаритные размеры полученных пластин трехслойного материала D-C-D - 304001000 мм. Исследования показали, что по мере развития питтинговой коррозии в наружном основном слое D рабочая среда через питтинговые каналы достигает внутреннего протекторного слоя, начинается коррозия общего типа с растворением стали C и с выделением кислорода на пограничной поверхности слоя стали D. Скорость общей коррозии трехслойного материала D-C-D в рабочей среде в зависимости от температуры рабочей среды снижается в 1,9-2,5 раза по сравнению со скоростью коррозии аналогичного однослойного материала D такой же толщины. Большие значения увеличения коррозионной стойкости соответствуют более высокой температуре среды. Пример 3. Материал согласно изобретению был изготовлен для эксплуатации в условиях одностороннего контакта с рабочей средой, содержащей 5%-ный водный раствор серной кислоты при температуре от 5 до 80C, выполнен трехслойным, при этом наружные основные слои были выполнены из материала P и соединены с внутренним протекторным слоем из углеродистой конструкционной стали обычного качестваF. В рабочей среде стационарный потенциал первого слоя P составляет ESPP=+0,35 В и находится в диапазоне от электрохимического потенциала полной пассивации EOPP=-0,1 В до электрохимического потенциала перепассивации EPRPP=+0,9 В. Стационарный потенциал стали F в рабочей среде ESPF=-0,5 В. Многослойный материал получали способом ручной дуговой наплавки прутков из материала P диаметром 5,0 мм на поверхность листа из стали F размерами 1015003000 мм. Наплавку выполняли с двух сторон в нижнем положении с кантовкой заготовки на 180 при следующих режимах: величина тока наплавки 60-80 A; величина напряжения наплавки 22-24 В. Толщина слоя P наплавки 3,0 мм с каждой стороны. В процессе развития коррозии в слое P при достижении рабочей средой внутреннего протекторного слоя происходит растворение конструкционной углеродистой стали F с выделением водорода на пограничной поверхности слоя P. Коррозионная стойкость трехслойного материала P-F-P в указанной рабочей среде по сравнению с коррозионной стойкостью однослойного материала P аналогичной толщины выше в 2,0-2,3 раза в зависимости от температуры рабочей среды. Большие значения увеличения коррозионной стойкости соответствуют более высокой температуре среды. При этом полученный трехслойный материал P-F-P обладает также существенно более высокой механической прочностью по сравнению с однослойным материалом- 10016878 Пример 4. Многослойный материал согласно изобретению был изготовлен для эксплуатации в условиях одностороннего контакта с рабочей средой, содержащей 5%-ный водный раствор соляной кислоты при температуре от 5 до 150C в присутствии кислорода воздуха, выполнен трехслойным, при этом оба наружных основных слоя были выполнены из материала Q и соединены с внутренним протекторным слоем из меди T. В рабочей среде стационарный потенциал первого наружного слоя Q составляет ESPQ=+0,05 В и находится в диапазоне от электрохимического потенциала полной пассивации EOPQ=-0,05 В до электрохимического потенциала перепассивации EPRPQ=+0,4 В. Стационарный потенциал материла T в рабочей среде ESPF=+0,1 В. Многослойный материал изготавливали по следующей технологической схеме. Сначала проводили сварку взрывом по режиму: скорость детонации взрывчатого вещества 2500-2900 м/с, величина зазора между листами 2,0-4,0 мм, массовая скорость 320-360 м/с. Так были изготовлены биметаллические заготовки Q-T из листов с размерами 310002000 мм с толщиной 1,0 мм слоя Q. Затем полученные биметаллические заготовки нагревали до температуры 500-540C, располагали оба биметаллических листа из материала Q-T медным слоем T внутрь и совместно прокатывали с обжатием 100%. В процессе развития коррозии при достижении рабочей средой внутреннего протекторного слоя T происходило восстановление кислорода с образованием гидроксид-иона, образующего с растворившимся металлом первого слоя Q пассивную пленку, что значительно снижает питтинговую коррозию основного слоя Q. Коррозионная стойкость трехслойного материала Q-T-Q в указанной рабочей среде по сравнению с коррозионной стойкостью однослойного материала Q толщиной 3,0 мм выше в 7,0-9,5 раз в зависимости от температуры рабочей среды. Большие значения увеличения коррозионной стойкости соответствуют более высокой температуре среды. Пример 5. Многослойный материал согласно изобретению был изготовлен для эксплуатации в условиях двухстороннего контакта с рабочей средой, содержащей 20% раствор нитрата калия при температуре от 5 до 150C, выполнен пятислойным, при этом нечетные основные слои были выполнены из материала G, четные протекторные слои были выполнены из латуни S. В рабочей среде стационарный потенциал материла G нечетного слоя составляет ESPG=-0,23 В и находится в диапазоне от электрохимического потенциала полной пассивации EOPG=-0,75 В до электрохимического потенциала перепассивации EPRPG=-0,04 В. Стационарный потенциал материла S в рабочей среде ESPS=-0,3 В. Способ получения многослойного материала включал ручную аргонодуговую наплавку неплавящимся электродом и диффузионную сварку в вакууме. Ручную аргонодуговую наплавку неплавящимся электродом из латуни S выполняли на сплаве G. При этом формировали слой латуни S толщиной 1,2 мм на каждом слое сплава G; затем производили последующую шлифовку латунного слоя на глубину 0,2 мм. После шлифования толщина каждого слоя сплава S составляла 1,0 мм. На третий слой из сплава G наплавляли латунь S с обеих сторон. Наплавку осуществляли в нижнем пространственном положении на постоянном токе прямой полярности неплавящимся вольфрамовым электродом диаметром 3 мм с присадкой оксида лантана, с присадочной проволокой диаметром 1,6 мм из материала S в режиме: величина тока наплавки 120-160 А; величина напряжения наплавки 18-22 В; вылет электрода 5-7 мм; объем расхода защитного газа (аргона) 12-16 л/мин. Наплавленные слои латуни S соединялись между собой при помощи диффузионной сварки в вакууме со следующими параметрами: температура 650+20C, контактное давление 1,0-1,2 МПа, остаточное давление 1,010-4 мм рт.ст., время сварки 1,5-2 ч. Окончательные габаритные размеры полученных заготовок составляли 7200600 мм. В процессе развития коррозии при достижении рабочей средой внутреннего протекторного слоя с любой из сторон происходит восстановление кислорода на латуни S с образованием гидроксид-иона,который образует с растворившимся металлом G нечетных основных слоев пассивную пленку, что значительно снижает питтинговую коррозию этих слоев. Коррозионная стойкость многослойного материалаG-S-G-S-G в рабочей среде выше от 7,0 до 15,0 раз по сравнению с материалом G толщиной 7,0 мм. Таким образом, производство пятислойных материалов состава G-S-G-S-G способом согласно изобретению обеспечивает получение в указанном материале высокой коррозионной стойкости. Пример 6. Многослойный материал согласно изобретению был изготовлен для эксплуатации в условиях двухстороннего контакта с рабочей средой, содержащей 50% раствор азотной кислоты при температуре от 5 до 110C, выполнен трехслойным, при этом нечетные основные слои были выполнены из коррозионностойкой стали H, четный протекторный слой были выполнены из алюминия R. В рабочей среде стационарный потенциал материала H нечетного слоя составляет Esph=+0,2 В и на- 11016878 ходится в диапазоне от электрохимического потенциала полной пассивации EOPH=+0,1 В до электрохимического потенциала перепассивации EPRPH=+0,35 В. Стационарный потенциал материла R в рабочей среде ESPR=+0,25 В. Две биметаллические заготовки H-R размерами 210002000 мм с толщиной 1,0 мм слоя R на слое коррозионно-стойкой стали H были получены аргонодуговой наплавкой при следующих параметрах: диаметр сварочной проволоки 1,6 мм, величина тока наплавки 180-260 А, величина напряжения наплавки 24-28 В, объем расхода защитного газа 15-20 л/мин. Биметаллические заготовки были размещены алюминиевым слоем внутрь и совместно прокатаны с обжатием 100%. В процессе развития коррозии при достижении рабочей средой протекторного четного слоя происходит растворение алюминия R через стадию образования пассивной оксидной пленки и выделение водорода на слое стали H. Способ получения трехслойных материалов H-R-H согласно изобретению обеспечивает получение материала, обладающего высокой коррозионной стойкостью, высокими механическими характеристиками за счет малой величины зоны термического влияния при наплавке и высокой прочности и однородностью структуры четного слоя. Коррозионная стойкость многослойного материала в рабочей среде по сравнению со сплавом состава H аналогичной толщины увеличивается в 5,0-7,0 раз в зависимости от температуры рабочей среды. Большие значения увеличения коррозионной стойкости соответствуют более высокой температуре среды. Пример 7. Материал согласно изобретению, выполненный пятислойным, предназначен для эксплуатации в условиях контакта с 50%-ным раствором азотной кислоты с одной стороны (среда содержит анионы, являющиеся окислителями) и 1%-ным водным раствора хлорида натрия с другой стороны (среда не содержит анионов, являющихся окислителями). Нечетные основные первый слой, контактирующий с рабочей средой - 50%-ным раствором азотной кислоты, и третий слой многослойного материала выполнены из коррозионно-стойкой стали М, имеющей в указанной среде стационарный потенциал ESPM1=+0,15 В. Указанное значение находится в диапазоне от электрохимического потенциала полной пассивации EOPM=+0,1 В и электрохимического потенциала перепассивации EPRPM=+0,3 В. В качестве материала четного (второго) протекторного слоя со стороны азотной кислоты был выбран алюминиевый сплав R, имеющий стационарный потенциал в данной среде ESPR=+0,2 В. Наружный пятый слой, контактирующий с 1%-ным водным раствором хлорида натрия, по составу аналогичен нечетным первому и третьему слою. В среде 1%-ного водного раствора хлорида натрия стационарный потенциал коррозионно-стойкой стали М ESPM=+0,18 В. Указанное значение находится в интервале между значениями электрохимического потенциала полной пассивации EOPM=+0,04 В и электрохимического потенциала перепассивации EPRPM=+0,35 В. Четвертый слой, расположенный со стороны раствора хлорида натрия, выполнен из углеродистой конструкционной стали N. Материал четвертого слоя из стали N в среде указанного раствора хлорида натрия имеет стационарный потенциал ESPN=-0,42 В. Способ получения многослойного материала включал аргонодуговую наплавку слоя R на коррозионно-стойкую сталь M первого и третьего слоя, сварку взрывом коррозионно-стойкой стали M и стали N между третьим, четвертым и пятыми слоями, прокатку с обжатием 100%. Заготовки для третьего, четвертого и пятого слоев состава M-N-M размерами 10015006000 мм с толщиной слоя коррозионно-стойкой стали M по 10 мм с каждой стороны были получены сваркой взрывом. Заготовки сваривали в две технологические операции, наваривая за прием один слой коррозионностойкой стали M с одной из сторон слоя углеродистой стали N. Примерный режим сварки взрывом слоя коррозионно-стойкой стали M со слоем стали N был следующим: скорость детонации взрывчатого вещества 2600-2800 м/с, величина зазора между листами 4-8 мм, массовая скорость 360-420 м/с. На свободную поверхность третьего слоя и одну из поверхностей первого слоя из стали М наплавляли материал второго слоя R толщиной по 2,0 мм на каждую сторону. Примерный режим аргонодуговой наплавки слоя R с коррозионно-стойкой сталью был следующим: диаметр сварочной проволоки 1,6 мм, величина тока наплавки 180-260 А, величина напряжения наплавки 24-28 В, объем расхода защитного газа 15-20 л/мин. На заключительной стадии биметаллические заготовки были размещены слоем наплавленного алюминиевого сплава внутрь и совместно прокатаны с обжатием 100%. В процессе развития коррозии при достижении рабочими средами внутреннего протекторного слоя со стороны контакта с азотной кислотой происходит растворение сплава R и выделение водорода на слое сплава M. При достижении рабочей средой четвертого слоя, расположенного со стороны контакта с раствором хлорида натрия, происходит растворение сплава N и выделение водорода или восстановление кислорода с образованием пассивной пленки на сплаве M. Получение пятислойных материалов состава M-R-M-N-M способом согласно изобретению, обеспечивающим сплошное неразъемное соединение слоев определенных материалов, обладающих желаемой- 12016878 химической и электрохимической активностью обеспечивает высокую коррозионную стойкость, высокие механические характеристики, малую величину зоны термического влияния при наплавке алюминия и однородности его структуры. Коррозионная стойкость многослойного материала в заданной среде по сравнению с материалом М аналогичной толщины в тех же условиях увеличивается в 15,0-20,0 раз. Результаты проведенных испытаний полученных многослойных материалов, описанных в примерах 1-7, представлены в табл. 7. Таблица 7 Как видно из табл.7, многослойные материалы согласно изобретению, полученные способами согласно изобретению для эксплуатации в условиях одностороннего или двустороннего контакта с определенными рабочими средами, в процессе эксплуатационных испытаний характеризуются коррозионной стойкостью, значительно превышающей коррозионную стойкость однослойных материалов такой же толщины, выполненных из одного материала. Таким образом, изготовление многослойных материалов согласно изобретению, с применением в качестве слоев материалов, обеспечивающих в условиях контакта с определенной рабочей средой заданную электрохимическую и химическую активность, позволяет формировать конструкционные материалы, имеющие высокую коррозионную стойкость при сравнительно малых толщинах слоев и материала в целом, с использованием экономически целесообразных сочетаний материалов основных и протекторных слоев. При этом в способ получения многослойного материала повышенной коррозионной стойкости,приспособленного для работы в условиях одностороннего или двустороннего контакта с рабочей средой и в многослойный материал, изготовленный способом согласно изобретению, могут быть внесены усовершенствования и улучшения, не выходящие за рамки изобретения. Например, специалистам, работающим в области электрохимии и металлургии, должно быть ясно, что в зависимости от условий, в которых используют многослойный материал, возможно между основными слоями использовать несколько протекторных слоев, например, для снижения стоимости материала без снижения его коррозионной стойкости. Промышленная применимость Многослойные материалы повышенной коррозионной стойкости согласно изобретению могут быть получены способами согласно изобретению с использованием широко известных технологий и оборудования, при этом в зависимости от требований к свойствам материалов слоев конструкций, изготовленных для эксплуатации в определенной агрессивной среде, многослойные материалы могут иметь различный состав слоев с их различным чередованием. При этом немаловажным является стоимость материала,обеспечивающего заданную коррозионную стойкость. Многослойные материалы согласно изобретению могут быть применены в различных отраслях промышленности. ФОРМУЛА ИЗОБРЕТЕНИЯ 1. Многослойный материал повышенной коррозионной стойкости в средах, где водные растворы щелочей, солей кислот или кислот, анионы которых не являются окислителями, содержащий соединенные с помощью сплошного неразъемного соединения, чередующиеся нечетные и четные слои, при этом нечетные наружные и внутренние слои выполнены из металлов или сплавов, характеризующихся в условиях контакта с указанной рабочей средой стационарным электрохимическим потенциалом в диапазоне от электрохимического потенциала полной пассивации до электрохимического потенциала перепассивации; четные внутренние слои, являющиеся протекторными, выполнены из металлов или сплавов, характеризующихся в условиях контакта с указанной рабочей средой стационарным электрохимическим потенциалом, меньшим, чем стационарный электрохимический потенциал соседних нечетных слоев в тех же условиях. 2. Многослойный материал повышенной коррозионной стойкости в средах, где водные растворы щелочей, солей кислот или кислот, анионы которых являются окислителями, содержащий соединенные с помощью сплошного неразъемного соединения, чередующиеся нечетные и четные слои, при этом нечетные наружные и внутренние слои выполнены из металлов или сплавов, характеризующихся в- 14016878 условиях контакта с указанной рабочей средой стационарным электрохимическим потенциалом в диапазоне от электрохимического потенциала полной пассивации до электрохимического потенциала перепассивации; четные внутренние протекторные слои, являющиеся протекторными, выполнены из металлов или сплавов, характеризующихся в условиях контакта с указанной рабочей средой стационарным электрохимическим потенциалом, превышающим электрохимический потенциал металла или сплава наружного слоя в таких же условиях и имеющим величину в диапазоне от электрохимического потенциала полной пассивации материала наружного слоя до электрохимического потенциала перепассивации материала наружного слоя, и при этом обладающих меньшим водородным перенапряжением, чем материалы нечетных слоев. 3. Многослойный материал повышенной коррозионной стойкости, содержащий чередующиеся нечетные и четные слои, соединенные с помощью сплошного неразъемного соединения, при этом первый, один из наружных, слой и ближайший к нему внутренний слой выполнены из металлов или сплавов, характеризующихся в условиях контакта с рабочей средой, содержащей водные растворы щелочей, солей кислот или кислот, анионы которых не являются окислителями, стационарным электрохимическим потенциалом в диапазоне от электрохимического потенциала полной пассивации до электрохимического потенциала перепассивации; четный внутренний слой, прилегающий к первому наружному слою, выполнен из металлов или сплавов, характеризующихся в условиях контакта с рабочей средой, содержащей водные растворы щелочей, солей кислот или кислот, анионы которых не являются окислителями, стационарным электрохимическим потенциалом, меньшим, чем стационарный электрохимический потенциал соседних нечетных слоев в тех же условиях; второй нечетный наружный слой и ближайший к нему нечетный внутренний слой выполнены из металлов или сплавов, характеризующихся в условиях контакта с рабочей средой, содержащей водные растворы щелочей, солей кислот или кислот, анионы которых являются окислителями, стационарным электрохимическим потенциалом в диапазоне от электрохимического потенциала полной пассивации до электрохимического потенциала перепассивации; четный внутренний слой, прилегающий ко второму нечетному наружному слою, и другие четные слои, прилегающие к нечетным внутренним слоям, выполнены из металлов или сплавов, характеризующихся в условиях контакта с рабочей средой, содержащей водные растворы щелочей, солей кислот или кислот, анионы которых являются окислителями, стационарным электрохимическим потенциалом, превышающим электрохимический потенциал металла или сплава второго наружного слоя в таких же условиях и имеющим величину в диапазоне от электрохимического потенциала полной пассивации материала второго наружного слоя до электрохимического потенциала перепассивации материала второго наружного слоя, и при этом обладающих меньшим водородным перенапряжением, чем материалы соседних нечетных слоев. 4. Материал по любому из пп.1, или 2, или 3, отличающийся тем, что на наружном слое дополнительно содержится плакирующий слой оксидированного алюминия. 5. Материал по любому из пп.1, или 2, или 3, отличающийся тем, что материал выполнен в форме листов, пластин, лент, полос, уголков, швеллеров, двутавров, дисков, стержней различного профиля,труб различного профиля, колец; изделий конструктивной формы открытого профиля или замкнутого сплошного профиля или полого профиля проектных очертаний. 6. Способ получения многослойного материала повышенной коррозионной стойкости, включающий формирование сплошного неразъемного соединения слоев, выполненных из металлов и/или их сплавов и размещенных один слой на другом, при этом в качестве материала нечетных слоев используют металлы или сплавы, характеризующиеся в условиях контакта с рабочей средой, содержащей водные растворы щелочей, солей кислот или кислот, анионы которых не являются окислителями, стационарным электрохимическим потенциалом в диапазоне от электрохимического потенциала полной пассивации до электрохимического потенциала перепассивации; в качестве материала четных слоев используют металлы или сплавы, характеризующиеся в условиях контакта с указанной рабочей средой стационарным электрохимическим потенциалом, меньшим, чем стационарный электрохимический потенциал соседних нечетных слоев в таких же условиях. 7. Способ получения многослойного материала повышенной коррозионной стойкости, включающий формирование сплошного неразъемного соединения слоев, выполненных из металлов и/или их сплавов и размещенных один слой на другом, при этом в качестве материала нечетных наружного и внутренних слоев используют металлы или сплавы,характеризующиеся в условиях контакта с рабочей средой, содержащей водные растворы щелочей, солей кислот или кислот, анионы которых являются окислителями, стационарным электрохимическим потенциалом в диапазоне от электрохимического потенциала полной пассивации до электрохимического потенциала перепассивации; в качестве материала четных внутренних слоев используют металлы или сплавы, характеризующиеся в условиях контакта с рабочей средой, содержащей водные растворы щелочей, солей кислот или- 15016878 кислот, анионы которых являются окислителями, стационарным электрохимическим потенциалом, превышающим электрохимический потенциал металла или сплава наружного слоя в таких же условиях и имеющим величину в диапазоне от электрохимического потенциала полной пассивации материала наружного слоя до электрохимического потенциала перепассивации материала наружного слоя, и при этом обладающие меньшим водородным перенапряжением, чем материалы нечетных слоев. 8. Способ получения многослойного материала повышенной коррозионной стойкости, включающий формирование сплошного неразъемного соединения слоев, выполненных из металлов и/или их сплавов и размещенных один слой на другом, при этом в качестве материала первого наружного слоя используют металлы или сплавы, характеризующиеся в условиях контакта с рабочей средой, содержащей водные растворы щелочей, солей кислот или кислот,анионы которых не являются окислителями, стационарным электрохимическим потенциалом в диапазоне от электрохимического потенциала полной пассивации до электрохимического потенциала перепассивации; в качестве материала четного внутреннего слоя, прилегающего к первому наружному слою, используют металлы или сплавы, характеризующиеся в условиях контакта с рабочей средой, содержащей водные растворы щелочей, солей кислот или кислот, анионы которых не являются окислителями, стационарным электрохимическим потенциалом, меньшим, чем величина стационарного электрохимического потенциала соседних нечетных слоев в тех же условиях; в качестве материала второго наружного слоя используют металлы или сплавы, характеризующиеся в условиях контакта с рабочей средой, содержащей водные растворы щелочей, солей кислот или кислот,анионы которых являются окислителями, стационарным электрохимическим потенциалом в диапазоне от электрохимического потенциала полной пассивации до электрохимического потенциала перепассивации; в качестве материала четного внутреннего слоя, прилегающего ко второму наружному слою, и материала четных слоев, прилегающих к нечетным внутренним слоям, используют металлы или сплавы,характеризующиеся в условиях контакта с рабочей средой, содержащей водные растворы щелочей, солей кислот или кислот, анионы которых являются окислителями, стационарным электрохимическим потенциалом, превышающим электрохимический потенциал металла или сплава второго наружного слоя в таких же условиях и имеющим величину в диапазоне от электрохимического потенциала полной пассивации материала второго наружного слоя до электрохимического потенциала перепассивации материала второго наружного слоя, и при этом обладающие меньшим водородным перенапряжением, чем материалы соседних нечетных слоев. 9. Способ по п.8, отличающийся тем, что сплошное неразъемное соединение материалов слоев формируют путем соединения одного из наружных слоев первого многослойного материала, приспособленного для работы в условиях двухстороннего контакта с первой рабочей средой, содержащей водные растворы щелочей, солей кислот или кислот, анионы которых не являются окислителями, с одним из наружных слоев второго многослойного материала, приспособленного для работы в условиях двухстороннего контакта со второй рабочей средой, содержащей водные растворы щелочей, солей кислот или кислот, анионы которых являются окислителями. 10. Способ по любому из пп.6, или 7, или 8, отличающийся тем, что в качестве материалов четных слоев используют металлы или сплавы, дополнительно характеризующиеся в условиях контакта с рабочей средой образованием продуктов коррозии, имеющих объем больше, чем объем металла или сплава в слое до коррозии. 11. Способ по любому из пп.6, или 7, или 8, отличающийся тем, что указанное сплошное неразъемное соединение указанных четных и нечетных слоев формируют с помощью сварки взрывом и/или диффузионной сварки в вакууме, в инертных газах или в восстановительных газах; и/или высокочастотной сварки; и/или сварки прокаткой; и/или ручной дуговой наплавки; и/или механизированной наплавки плавящимся электродом сплошной или порошковой проволокой в среде инертных газов и смесях; и/или автоматической аргонодуговой наплавки; и/или автоматической наплавки ленточным электродом под флюсом; и/или автоматической наплавки проволочным электродом под флюсом; и/или автоматической наплавки порошковой проволокой в среде активных или инертных газов и в их смесях; и/или автоматической наплавки самозащитной порошковой проволокой или лентой; и/или электрошлаковой наплавки; и/или плазменной наплавки проволокой сплошного сечения или порошком; и/или газовой наплавки; и/или наплавки с индукционным нагревом. 12. Способ по любому из пп.6, или 7, или 8, отличающийся тем, что дополнительно наружный слой полученного многослойного материала плакируют алюминием предпочтительно с помощью взрывного плакирования и производят последующее оксидирование полученного плакирующего слоя предпочтительно с помощью микродугового оксидирования. 13. Способ по любому из пп.6, или 7, или 8, отличающийся тем, что формирование многослойных материалов осуществляют в форме листов, пластин, лент, полос, уголков, швеллеров, двутавров, дисков,стержней различного профиля, труб различного профиля, колец; изделий конструктивной формы открытого профиля или замкнутого сплошного профиля или полого профиля проектных очертаний.
МПК / Метки
МПК: B32B 7/02, C23F 13/00
Метки: варианты, получения, материал, стойкости, способы, многослойный, повышенной, коррозионной
Код ссылки
<a href="https://eas.patents.su/18-16878-mnogoslojjnyjj-material-povyshennojj-korrozionnojj-stojjkosti-varianty-i-sposoby-ego-polucheniya.html" rel="bookmark" title="База патентов Евразийского Союза">Многослойный материал повышенной коррозионной стойкости (варианты) и способы его получения</a>
Предыдущий патент: Способ удаления неполярных соединений из воды
Следующий патент: Амортизатор транспортного средства
Случайный патент: Препараты эстрамустинфосфата для парентерального применения