Устройство и способ обработки отходов
Формула / Реферат
1. Устройство для обработки материала твердых отходов, содержащее
вращающийся резервуар (30) с впускным каналом (32) для вводимых отходов, расположенный так, что при вращении резервуара (30) в его внутренней части образуется первая зона, главным образом заполненная материалом отходов, и вторая зона, по существу, не содержащая материала отходов;
выпускной канал (33) для обработанных отходов;
множество паровых сопел (38) для селективного введения водяного пара во внутреннюю часть резервуара (30), причем каждое паровое сопло (38) расположено в резервуаре (30);
привод, предназначенный для вращения резервуара (30) и, таким образом, для перемещения паровых сопел (38) между первой зоной и второй зоной так, что только часть из паровых сопел (38) может одновременно находиться в указанной первой зоне; и
устройство (36) для регулирования подачи водяного пара, предназначенное для подведения водяного пара только к паровым соплам, находящимся в текущий момент в первой зоне.
2. Устройство по п.1, дополнительно включающее нагревательное средство для нагревания и/или поддержания внутренней части резервуара (30) при температуре 150-200°С.
3. Устройство по п.2, в котором нагревательное средство выбирают из группы, состоящей из средства нагрева воздухом наружной паровой рубашки и нагревательного элемента.
4. Устройство по п.2, в котором нагревательное средство включает только нагревательную рубашку, нагреваемую водяным паром.
5. Устройство по любому из предшествующих пунктов, в котором устройство (36) для регулирования подачи водяного пара содержит распределительный вентиль (36) для направления водяного пара от парогенератора к паровому соплу, содержащий корпус вентиля, имеющий впускное отверстие (52), сообщающееся по текучей среде с парогенератором, и множество выпускных отверстий (54), сообщающихся по текучей среде с паровым соплом, при этом вентиль (36) выполнен так, что в любое время по меньшей мере одно из выпускных отверстий (54) является разобщенным по текучей среде с впускным отверстием (52).
6. Способ обработки материала отходов в устройстве по любому из пп.1-5, включающий стадии:
a) введения измельченного материала отходов в резервуар (30);
b) обработки измельченного материала отходов водяным паром, при этом водяной пар вводят только в измельченный материал отходов.
7. Способ по п.6, в котором водяной пар находится при температуре 150-200°С.
8. Способ по п.6 или 7, в котором резервуар (30) находится при атмосферном давлении.
9. Способ по п.6, который представляет собой непрерывно осуществляемый способ, причем материал отходов вводят во впускной канал (32) резервуара (30) и обработанный материал отходов выводят из выпускного канала (33) резервуара (30).
10. Способ по любому из пп.6-9, в котором обработанный материал отходов включает биомассу из целлюлозы, пластмассы, черные металлы и цветные металлы.
11. Способ по любому из пп.6-10, в котором внутреннюю часть резервуара нагревают до температуры 150-200°С.
12. Способ по любому из пп.6-11, в котором внутренняя часть резервуара (30) находится под давлением ниже 2 бар (0,2 МПа).
13. Способ по любому из пп.6-12, в котором внутренняя часть резервуара (30) находится, по существу, под давлением окружающей среды.
14. Способ по любому из пп.6-13, в котором устройство предназначено для обработки материала отходов в непрерывном режиме.
15. Способ по любому из пп.6-14, в котором обработанный материал отходов включает биомассу из целлюлозного материала, содержащую менее 1% серы.
16. Способ по любому из пп.6-15, в котором выпускной канал (33) соединяют с сортировочной камерой, где обработанный материал отходов разделяют на пластмассы, черные металлы, цветные металлы и биомассу из целлюлозного материала.
17. Способ по п.15 или 16, в котором биомассу транспортируют в гипербарическое устройство или топливный элемент или в установку для химического превращения для преобразования биомассы в биодизельное топливо или органический спирт, такой как биоэтанол или биобутанол, или авиационное топливо.
18. Способ по п.17, в котором биодизельное топливо или органический спирт используют для питания электрических генераторов, дополнительно содержащихся в устройстве.
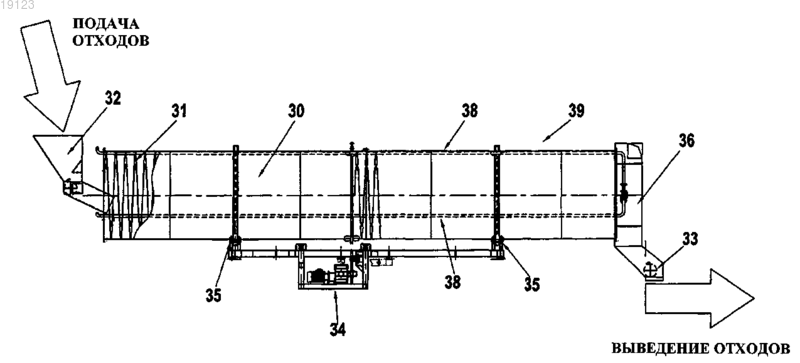
Текст
В изобретении способ и устройство для повторного использования городских бытовых отходов включают подвергание отходов обработке водяным паром при температуре 150-200 С. После паровой обработки полученный материал разделяют на составные части и биомассу и/или пластмассы подвергают дополнительной обработке. Дополнительная обработка предпочтительно дает биоэтанол из биомассы и дизельное топливо из пластмасс. В качестве альтернативы часть биомассы или вся биомасса может быть подвергнута газификации, чтобы получать водород,который, в свою очередь, может быть подан в топливный элемент для производства электрической энергии. Биодизельное топливо или биоспирт могут быть также использованы для получения электроэнергии.(71)(73) Заявитель и патентовладелец: ВИДАБЛЮПИ ВЕЙСТ ПРОУСЕССИНГ ЛИМИТЕД (GB) Настоящее изобретение относится к повторному использованию материала отходов и более конкретно к повторному использованию городских бытовых отходов. Существует ряд путей переработки городских бытовых отходов, иначе известных как городские твердые отходы, но двумя наиболее распространенными способами являются либо закапывание отходов,либо сжигание. Этим обоим способам присущи связанные с ними специфические проблемы. При утилизации закапыванием отходов отходы зарывают без сортировки. Это занимает дорогостоящие земельные участки и делает землю непригодной к использованию на многие годы. Кроме того, в землю могут проникать ядовитые стоки. Дополнительно, становится все более затруднительным отыскивать подходящие места для закапывания отходов. Что касается сжигания, то для этого обычно необходимо сортировать отходы на горючие и негорючие отходы, причем негорючие отходы отправляют к месту для закапывания, а горючие отходы сжигают. Однако сжигание отходов обычно создает сернистые выбросы и требует сооружения высоких уродливых дымовых труб. Кроме того, мусоросжигательные печи неэкономичны, поскольку они нуждаются в подведении больших количеств энергии. Впоследствии было предложено утилизировать городские отходы с использованием автоклава, в который загружают обрабатываемый материал отходов и подают водяной пар из парового аккумулятора. Пример такого решения раскрыт в патенте US-A-5190226, где твердые отходы обрабатывают при давлении 4 бар (0,4 МПа). Хотя эти предложения представляют собой более экологически благоприятное решение, чем описанные выше два ранее общеупотребительных способа, они неэффективны, так как являются процессами периодического действия. Непрерывный процесс был разработан, например, в патентеUS-A-6752337, но было предложено специальное оборудование, чтобы обслуживать технологическую установку с водяным паром высокого давления, которая является как дорогостоящей, так и опасной в обращении. В настоящем изобретении предпринята попытка предложить решение для утилизации городских бытовых отходов, которое является как энергетически эффективным, так и экологически благоприятным. Производственная установка имеет модульную конструкцию и будет принимать нерассортированные отходы и подвергать их термической обработке с использованием непрерывного парового процесса. Предпочтительно система также разрешает проблему запаха, создаваемого установкой. Согласно настоящему изобретению представлено устройство для обработки материала твердых отходов, содержащее резервуар с впускным каналом для подводимых отходов и выпускным каналом для обработанных отходов, где внутренняя часть резервуара имеет первую зону и вторую зону, устройство далее включает множество паровых сопел, чтобы целенаправленно вводить водяной пар во внутреннюю часть резервуара, привод, предназначенный для обеспечения относительного перемещения между паровыми соплами и первой зоной таким образом, что только некоторые из паровых сопел находятся в указанной первой зоне в любое время, и устройство для регулирования подачи водяного пара, предназначенное для подведения водяного пара только к паровым соплам в первой зоне. Это устройство преимущественно направляет водяной пар в материал отходов для подведения энергии, необходимой для обеспечения процесса разложения, в частности, органических материалов, содержащихся в отходах, для эффективной обработки отходов. Для проведения процесса переработки отходов преимущественным является непрерывный режим,который достигается более просто, когда резервуар представляет собой удлиненный сосуд с впускным каналом на одном конце и выпускным каналом на другом конце. Привод предназначен для вращения резервуара и таким путем перемещения материала вдоль резервуара, в то же время также с перемешиванием материала отходов для обеспечения полноценной обработки. Преимущественно паровые сопла размещены в паропроводах. Паровые сопла могут быть зафиксированы относительно внутренней части резервуара. Паровые сопла предназначены для введения водяного пара с температурой 150-200 С и таким образом подведения большого количества кинетической и тепловой энергии непосредственно к материалу отходов. Обычно для нагревания и/или поддержания внутренности при температуре 150-200 С предусмотрены средства нагревания, поскольку это представляет собой простой путь доведения материала отходов до температуры, при которой достигается процесс разложения в пределах приемлемого промежутка времени. Средства нагревания обычно выбирают из группы, состоящей из нагретого воздуха, наружной паровой рубашки и нагревательного элемента. Предпочтительным средством нагревания является только рубашка, нагреваемая водяным паром. Это является в особенности преимущественным способом, так как позволяет очень просто сделать нагревание регулируемым, избежать локальных перегревов в резервуаре и экономить топливо. В этом случае резервуар может быть подразделен на последовательные секции. Подведение теплоты в каждую секцию можно контролировать индивидуально, например таким образом,что материал в каждой зоне можно довести до желательной температуры или поддерживать при такой температуре. Например, усиленное подведение теплоты потребуется вблизи впускного канала для отходов, так как нужно довести относительно холодные отходы до технологической температуры настолько быстро, насколько возможно. Зону, ближайшую к выпускному каналу, можно регулировать для частичного высушивания материала отходов. Способ имеет то преимущество, что давление не требуется, и тем самым внутри резервуара поддерживается давление менее 2 бар (0,2 МПа), обычно менее 1,25 бар (0,125 МПа) или даже, по существу,давление окружающей среды. Это обеспечивает значительную экономию затрат и повышает безопасность по сравнению с системами, работающими под давлением. Обработанный материал отходов предпочтительно включает биомассу, содержащую целлюлозный материал и содержащую менее 1% серы. Биомасса находит множество вариантов применения, и это обеспечивает ключевые преимущества представляемой системы. Обычно предусмотрена сортировочная камера, где обработанный материал отходов разделяют на пластмассы, черные металлы, цветные металлы и биомассу из целлюлозного материала. После этого биомассу транспортируют в гипербарическое устройство или топливный элемент или в установку для химического превращения, для преобразования биомассы в биодизельное топливо, органический спирт,такой как биоэтанол или биобутанол, или авиационное топливо. Биотопливо может быть использовано для питания генератора или генераторов для производства электрической энергии или может быть применено для питания других двигателей (например, авиационных двигателей) или других генераторов. Согласно второму аспекту настоящего изобретения представлен распределительный вентиль для направления водяного пара от парогенератора или парового котла к паровому соплу, который содержит корпус вентиля, имеющий впускное отверстие, которое может сообщаться с парогенератором для подачи текучей среды, и множество выпускных отверстий, которые могут сообщаться с паровым соплом для подведения текучей среды, причем вентиль выполнен так, что в любое время по меньшей мере одно из выпускных отверстий перестает сообщаться по текучей среде с впускным отверстием. Этот компонент позволяет направлять водяной пар в желательный канал паропровода простым и надежным образом. Обычно впускное отверстие скомпоновано так, чтобы сообщаться по текучей среде только с одним выпускным отверстием в то время, когда обычно только один паропровод будет находиться внутри материала отходов в этот момент. Разумеется, это может варьировать в зависимости от компоновки оборудования. Распределительный вентиль может иметь впускное отверстие, сообщающееся по текучей среде с одним концом трубчатого вентильного элемента, заключенного в корпусе вентиля, где выпускные отверстия расположены по окружности корпуса вентиля так, чтобы индивидуально сообщаться по текучей среде с вентильным элементом при его вращении в корпусе вентиля. Распределительный вентиль тем самым обеспечивает превосходный путь реализации устройства для регулирования подачи водяного пара согласно первому варианту осуществления изобретения. Распределительный вентиль согласно предпочтительному варианту исполнения преимущественно может иметь впускное отверстие во впускном коллекторе с сообщением по текучей среде, проходящим в осевом направлении через поворотную вентильную камеру до корпуса вентиля. Предпочтительно поворотная вентильная камера имеет питающий паровой канал для подведения пара в нагревательную рубашку и возвратный проток для конденсата, чтобы принимать конденсат из нагревательной рубашки, и питающий паровой канал сообщается по текучей среде с паропроводом во впускном коллекторе, а возвратный проток для конденсата сообщается по текучей среде с возвратным трубопроводом во впускном коллекторе. Этим создается простой вариант соединения для подачи водяного пара во вращающуюся нагревательную рубашку с помощью поворотной вентильной камеры, вращающейся вместе с резервуаром, в то время как остальная часть вентиля остается неподвижной. Согласно третьему варианту осуществления настоящего изобретения представлен способ обработки материала отходов, включающий стадии:a) введения измельченного материала отходов в резервуар иb) обработки измельченного материала отходов водяным паром при температуре 150-200 С, при этом резервуар находится при давлении окружающей среды, и/или водяной пар вводят только в измельченный материал отходов. Этим путем материал отходов разлагается на многочисленные полезные продукты эффективным в промышленном отношении и экологически благоприятным образом. Способ обычно будет представлять собой непрерывный способ, причем материал отходов вводят через впускной канал резервуара, и обработанный материал отходов выводят через выпускной канал резервуара. Разумеется, способ предпочтительно осуществляют с использованием устройства согласно первому и второму вариантам осуществления изобретения. Обработанный материал отходов преимущественно будет включать биомассу из целлюлозы, пластмассы, черные металлы и цветные металлы. Сформированная в этом способе биомасса является в особенности преимущественной, поскольку она пригодна для дальнейшей обработки с образованием биодизельного топлива, топлива для топливного элемента, биоспирта, например биоэтанола, заменителя ископаемого топлива или авиационного топлива, по возможности смешанного с биоспиртом. Чтобы сделать настоящее изобретение более понятным, теперь будут описаны его варианты осуществления с помощью примеров со ссылкой на сопроводительные чертежи, на которых: фиг. 1 показывает схематическое изображение производственной установки согласно настоящему изобретению; фиг. 2 представляет блок-схему базового процесса, используемого в настоящем изобретении; фиг. 3 представляет схематический чертеж первого устройства для паровой обработки, используемого в первом варианте осуществления настоящего изобретения; фиг. 4 представляет схематический чертеж, изображающий производство этанола из системы согласно настоящему изобретению; фиг. 5 представляет схематический чертеж, изображающий производство биодизельного топлива из системы согласно настоящему изобретению; фиг. 6 представляет изображение распределительного вентиля согласно первому варианту осуществления настоящего изобретения; фиг. 7 представляет схематический чертеж устройства для паровой обработки, используемого в настоящем изобретении; и фиг. 8 показывает второй распределительный вентиль второго предпочтительного варианта осуществления настоящего изобретения на виде сверху (фиг. 8 А) и в перспективном изображении (фиг. 8 В). На фиг. 1 схематически показана предпочтительная производственная установка согласно настоящему изобретению. Мусоровозы доставляют городские бытовые отходы на перевалочную площадку А,где необработанные отходы, без сортировки, непрерывно подаются через механическое измельчительное устройство В в устройство С для паровой обработки. На фиг. 1 представлены два устройства для паровой обработки, действующие параллельно, каждое со своим собственным бункером для хранения измельченных отходов перед подачей их в устройство. Термин "необработанный" означает, что никакой дополнительный материал, такой как химикаты и/или вода, не добавляют в отходы перед подачей в устройство(а) для паровой обработки. Устройство С для паровой обработки действует так, что отходы обрабатывают приблизительно в течение 45-60 мин и обработанные отходы затем разделяют на стадии Е сортировки на различные категории, такие как необработанная биомасса или целлюлоза, пластмассы, черные металлы, цветные металлы, текстильные материалы и прочие остатки и материалы. Способы и варианты разделения смешанного продукта, выходящего из устройства С для паровой обработки, хорошо известны специалистам в этой области техники. При использовании этих способов реально отправляются для закапывания менее 10% объема первоначальных отходов, и другие отсортированные отходы могут быть использованы повторно. Объем отходов сокращается на величину до 60%. Необработанную биомассу и пластмассы подвергают дополнительной обработке, указанной блоками G и Н, и/или могут быть направлены на хранение, высушены и затем поданы в блок конверсии газа (газогенератор - не показан) либо обработаны для введения в топливный элемент (не показан), который может быть использован для получения электроэнергии. Биомасса может быть также обработана с образованием топлива для гипербарического устройства (не показано) или направлена в устройство N для использования в производстве биотоплива, например биоэтанола, биобутанола или биодизеля, как более подробно описано ниже. Если желательно, биотопливо может быть использовано в качестве топлива для электрического генератора. Если все топливо, полученное в работающей на полную мощность установке, как показана на фиг. 1, используется этим последним способом, то генератор должен производить от 6 до 20 МВт электроэнергии. Фиг. 4 и 5 показывают альтернативную обработку целлюлозного материала или его части. Другие отсортированные материалы сохраняются, как указано позицией F. Пластические материалы, отсортированные из блока Р, могут быть направлены в блок J для утилизации пластмасс. По своей исконной природе материал отходов будет источать неприятные запахи как на входе в устройство С для паровой обработки, так и на выходе из него. По этой причине предлагается выводить воздух из устройства для паровой обработки и обрабатывать его с использованием способа удаления запаха, как указано позицией D в фиг. 1, таким образом, как описано в Международной заявкеPCT/GB 2006/000888, где воздух обрабатывается озоном, генерируемым с использованием ультрафиолетового излучения. Особенность этого способа состоит в том, что, если генерировать достаточное количество озона и поддерживать его в контакте с обрабатываемым воздухом в течение достаточного периода времени, то достигается значительное снижение уровней запаха. Однако для этого требуется, чтобы было создано дополнительное ультрафиолетовое излучение с длиной волны, иной, нежели используется для формирования озона, чтобы гарантировать, что никакой активный озон, присутствующий в воздухе, не будет выпущен в атмосферу из процесса. Устройство С для паровой обработки не является герметизированным для поддержания давления, но обычно будут предусмотрены экраны или завесы, чтобы обеспечить возможность выхода газов и водяного пара из устройства С для паровой обработки по необходимым маршрутам. Как показано на фиг. 2, водяной пар генерируют в кипятильном устройстве 10, которое генерирует водяной пар с повышенным давлением, обычно 12-15 бар (1,2-1,5 МПа), и в иллюстрируемом варианте осуществления, 14 бар (1,4 МПа), и имеющим предпочтительную температуру 190-200 С, который подают в секцию 12 для паровой обработки, которая может включать один или более отдельных блоков,действующих параллельно. Отходы из зоны приемки и подачи, представленной блоком В, направляют в установку для паровой обработки при температуре и давлении, указанных ниже. Обработанные отходы затем транспортируют в сортировальное устройство Е. Дополнительно, любой водяной пар, выходящий из устройства для паровой обработки, улавливают в системе 16 трубопроводов и подают в дезодорирующий блок 17, где его обрабатывают, как обсуждается выше, перед выпуском в атмосферу. На фиг. 3 более подробно показана одна форма устройства С для паровой обработки в установке. Она включает удлиненный резервуар 30, который оснащен конвейерным устройством 31 для перемещения материала отходов от впускного канала 32 к выпускному каналу 33. Впускной канал 32 показан на фиг. 3 как устройство бункерного типа, хотя мог бы быть также использован вибрационный конвейер,как показано на фиг. 7, или иное устройство. В предпочтительной компоновке резервуара 30 предусмотрено сделать его в виде вращающегося конвейера барабанного типа, внутренняя поверхность которого оснащена одним или несколькими сплошными спиральными ребрами. Разумеется, время, в течение которого обрабатывается материал отходов, является функцией скорости вращения конвейера и длины конвейера, и эти величины регулируют так, чтобы отходы обрабатывались в течение приблизительно 45-60 мин. Внутренность резервуара поддерживают при температуре 150-200 С, предпочтительно при наинизшей температуре 160 С и независимо наивысшей температуре 180 С. При температурах ниже 150 С скорость конверсии для разложения материала отходов очень низка, и было бы необходимым держать отходы в резервуаре 30 в течение периода времени, который является неприемлемым из производственных соображений. При температуре 200 С может начинаться разложение пластических материалов в отходах, например, в результате пиролиза, который генерирует ядовитые газы и другие токсичные соединения, которые было бы весьма затруднительно обрабатывать, и тем самым важно избегать образования такого токсичного материала или сводить его к минимуму. Отходы обрабатывают с использованием водяного пара, вводимого в резервуар 30 с помощью трубопроводов 35. Вводимый водяной пар предпочтительно имеет температуру 150-180 С, но может быть при температуре до 200 С. Водяной пар вводят в материал отходов в камере 30 при давлении в диапазоне от 5 до 12 бар (0,5-1,2 МПа), предпочтительно 10 бар (1,0 МПа). Хотя водяной пар может быть введен во всем объеме камеры, предпочтительно вводить водяной пар, направляя его исключительно в материал отходов. При давлениях и температурах, используемых в способе, водяной пар вносит относительно большое количество кинетической энергии, которая эффективно передается в материал отходов, когда водяной пар вводят в него. Введенный водяной пар тем самым эффективно разлагает материалы отходов. В особенности эффективно введенный водяной пар воздействует на органические материалы в отходах так, что преобразует их в биомассу из целлюлозного материала, содержащего мало серы или вообще не содержащего ее. В дополнение к впускному каналу и выпускному каналу 32, 33 камера 30 или барабан может быть также оснащена донным бункером для сбора и удаления любого донного материала, образованного при паровой обработке. Кроме того, газоотводная труба может быть предусмотрена для удаления газов, полученных в процессе. Эти газы могут быть очищены и разделены так, что полезные углеводороды могут быть использованы в других частях установки и/или имеют любую тепловую энергию, извлекаемую из них и возвращаемую в процесс. Когда всю производственную установку применяют для обработки общих отходов, может быть необходимой предварительная обработка отходов, чтобы сделать их более однородными по размеру с помощью процесса измельчения перед подачей их во впускной канал установки. Этим будет обеспечиваться то, что впускной канал в блоке обработки не будет засоряться и будет получаться более плотный продукт. Однако для изобретения необходимо, чтобы материал был в виде кусочков, то есть в форме частиц. Теперь с привлечением фиг. 3 будет более подробно описана конструкция устройства С для паровой обработки (фиг. 1). Устройство С для паровой обработки включает вращающийся барабан 30, смонтированный горизонтально на катках 35 и приводимый в движение цепью (не показана) от двигателя 34. Барабан 30 имеет одинаковую площадь поперечного сечения по всей своей длине и на своей внутренней поверхности оснащен несколькими отстоящими друг от друга ребрами. Ребра могут быть сформированы из одиночного сплошного спирального элемента или нескольких частично спиральных пластин, протяженных в спиральной конфигурации, по существу, вдоль длины барабана 30. При необходимости между поворотами спиральных секций могут быть размещены осевые ребра, чтобы способствовать поднятию и переворачиванию материала, загруженного в резервуар. Водяной пар вводят в резервуар 30 через многочисленные трубопроводы 38, протяженные вдоль длины резервуара, в этом случае они размещены на внутренних поверхностях резервуара 30 и имеют отверстия, сосредоточенные в центре каждого шага спирали. Один конец каждого трубопровода 38 закрыт, и другой конец присоединен к распределительному вентилю 36. Распределительный вентиль 36 размещен на центральной оси резервуара. Вентиль 36 сообщается по текучей среде с питающим трубопроводом от источника водяного пара. Распределительный вентиль 36 подробно показан на фиг. 6. Распределительный вентиль 36 включает впускной канал 52 вентиля, размещенный на корпусе 50 вентиля,через который от парогенератора 10 поступает водяной пар. Корпус 50 вентиля также имеет 3 вентильных выпускных канала 54, каждый из которых соединен с соответствующим паропроводом 38. Распределительный вентиль 36 может быть без труда соединен с каждым из паропроводов 38 для подачи текучей среды. Однако предпочтительно вентиль 36 подает водяной пар в каждый паропровод 38 по очереди,-4 019123 когда резервуар 30 вращается. Как более подробно разъясняется ниже, в резервуар 30 подают отходы с заданной скоростью так, что отходы заполняют резервуар только до известного уровня. Этот уровень разделяет резервуар 30 на две зоны, причем первая зона главным образом заполнена материалом отходов, тогда как вторая зона, по существу, не содержит отходов. Каждый паропровод 38 закреплен на резервуаре 30 и тем самым перемещается между двумя зонами по мере вращения резервуара 30. Вентиль 36 имеет внутренние каналы внутри корпуса 50, каждый из которых индивидуально сообщается по текучей среде с паровыми выпускными каналами 54 так, что только паропровод(ды) 38 в первой зоне соединен с источником водяного пара в любой данный момент времени. Этим путем водяной пар вводят только в материал отходов. Конец резервуара расположен внутри бандажа, который служит для удержания водяного пара внутри резервуара, и также действует как выпускной канал для обработанных отходов. Когда резервуар 30 вращается в эксплуатационных условиях со скоростью 1-2 об/мин, водяной пар вводят в материал, когда он покрывает один из трубопроводов 38, как более подробно описано выше. Внутренность резервуара 30 обычно нагревают с помощью нагревательного средства до температуры 150-200 С, предпочтительно с нижним значением 160 С и независимо с верхним значением 180 С. Нагревательное средство может представлять собой воздух, который может быть нагрет, и горячий воздух вдувают в камеру. Предпочтительно может быть применен нагревательный элемент, размещенный в резервуаре или обернутый вокруг резервуара 30. Предпочтительно резервуар 30 может иметь охватывающую его паровую рубашку, в данном случае рубашка может быть сформирована между слоями материала, из которого изготовлен резервуар. Могут быть использованы те же парогенераторы 10 или, альтернативно, может быть применен отдельный источник водяного пара. Водяной пар, подаваемый в паровую рубашку, будет иметь температуру и давление, требуемые для достижения желательной температуры в резервуаре. Фиг. 7 показывает предпочтительный вариант исполнения устройства С для паровой обработки в установке. Устройство С для паровой обработки в целом подобно устройству С для паровой обработки,показанному на фиг. 3, и одинаковые ссылочные позиции использованы для обозначения деталей устройства, которые являются одинаковыми. Отходы подают в резервуар 130 через вибрационный конвейер 132. Конвейер вибрирует для предотвращения комкования материала отходов. Материал отходов подают на вибрационный конвейер со стандартного конвейера 133. Материал отходов перемещают к выпускному каналу 33 с помощью конвейерного устройства 31 в резервуаре 130. Внутренность резервуара 130 является такой же, как внутренность резервуара 30, с ребрами, предназначенными для перемещения материала отходов, когда резервуар вращается. Принципиальное различие между резервуаром 30 и резервуаром 130 состоит в том, что водяной пар не подают в резервуар 130, чтобы нагревать камеру и материал отходов до рабочей температуры, хотя водяной пар по-прежнему используют для обработки материала отходов через трубопроводы 38. Камеру и материал отходов теперь нагревают с использованием нагревательной рубашки 140, окружающей весь резервуар 130 и более подробно описанной ниже. Резервуар 130 имеет нагревательную рубашку 140, охватывающую резервуар 130. Нагревательная рубашка 140 включает сеть трубопроводов, которые снабжаются водяным паром от вентиля 136. Для быстрого нагревания резервуара 130 и материала отходов до желательной рабочей температуры 150200 С нагревательную рубашку подразделяют на четыре секции 140a-d, протяженные от впускной секции 140 а через первую технологическую секцию 140b, вторую технологическую секцию 140 с до выпускной секции 140d. Наибольшее потребление теплоты имеет место во впускной секции 140 а, где материал отходов должен быть доведен от температуры окружающей среды до рабочей температуры за минимальное время, и типично во впускной секции 140 а требуются 40-60% энергии. Когда отходы перемещаются по резервуару 130, отходы сохраняют большую часть тепловой энергии, и тем самым меньше энергии требуется для поддержания материала отходов при надлежащей рабочей температуре. Например, в технологических секциях 140b, 140 с потребляются примерно 55-30% энергии. В конечной выпускной секции 140d материал отходов также частично высушивается до типичного влагосодержания от 20 до 40%. Теплоту подводят к нагревательной рубашке в форме водяного пара от того же парогенератора, который используют для подачи водяного пара, вводимого в материал отходов. Эффективным путем соединения нагревательной рубашки 140 с паровым котлом для подачи текучей среды является применение усовершенствованной конструкции распределительного вентиля 136, как показано на фиг. 8. Распределительный вентиль 136, показанный на фиг. 8, в общем, подобен распределительному вентилю 36, показанному на фиг. 6, и одинаковые ссылочные позиции использованы для обозначения деталей устройства, которые являются одинаковыми. Распределительный вентиль 136 включает паровое сопло 152, размещенное на впускном коллекторе 158. Сообщение по текучей среде проходит по внутренности вентильной камеры 156 до корпуса 50 вентиля. Вентильная камера 156 может вращаться вокруг центральной оси резервуара 130, но впускной коллектор 158 и корпус 50 вентиля являются неподвижными. Вентильная камера 156 имеет питающий паро-5 019123 вой канал 160 для подведения пара в нагревательную рубашку 140, и возвратный проток 162 для конденсата, чтобы возвращать конденсат из нагревательной рубашки 140. Вращение от резервуара 130 согласовано с вентильной камерой 156 через питающий паровой канал 160 и возвратный проток 162 для конденсата. Впускной коллектор 158 также включает паропровод 164, сообщающийся по текучей среде с питающим паровым каналом 160, и возвратный трубопровод 166 сообщается по текучей среде с возвратным протоком 162 для конденсата. Внутри вентильная камера разделена на первое кольцевое пространство, соединяющее питающий паровой канал 160 с паропроводом 164 через кольцевой зазор во впускном коллекторе 158, и второе кольцевое пространство, соединяющее возвратный трубопровод 166 с возвратным протоком 162 для конденсата через еще один кольцевой зазор во впускном коллекторе 158. Все кольцевые пространства окружают соединение по текучей среде между паровым впускным каналом 152 и корпусом 50 вентиля. Первое и второе кольцевые пространства отделены друг от друга по текучей среде. Разумеется, конкретная внутренняя конфигурация вентиля может варьировать. Для обеспечения эффективного удаления конденсата каждая секция 140a-d будет включать по меньшей мере один конденсационный горшок. Конденсационный горшок предназначен для предотвращения вовлечения острого пара в конденсат, возвращаемый в паровой котел. Конденсационный горшок,в свою очередь, должен быть соединен со сборником конденсата. Типично он должен включать трубопровод большого диаметра, который должен быть расположен вокруг периметра барабана. Конденсат должен стекать в сборник в разнообразных местах вокруг периметра по мере вращения конденсата вместе с барабаном, пока есть возможность стока в выводящий трубопровод, когда выпускной канал достигает нижней точки в цикле вращения. Базовый процесс показан на фиг. 2. Процесс создает большой объем биомассы, главным образом включающей целлюлозный материал. Преимущественно можно утилизировать биомассу в виде топлива для самой производственной установки или в виде отдельного продукта, такого как биоэтанол, биобутанол или другой производный продукт, как более подробно описано ниже. Целлюлозное волокно, содержащееся в биомассе, которая выходит из устройства для паровой обработки, имеет высшую теплотворную способность 11 МДж/кг, что обеспечивает 3 кВт энергии. При высушивании высшая теплотворная способность целлюлозного материала повышается до 17-18 МДж/кг. Эта биомасса практически не содержит серы и тем самым при сожжении является гораздо более чистой, чем ископаемое топливо, и поэтому используется как заменитель ископаемого топлива. Целлюлозное волокно может быть продано как товарный продукт или оно может быть направлено в установку для газификации биомассы, которая производит газообразное топливо из этой целлюлозной биомассы, как более подробно описано ниже. Это газообразное топливо затем может быть дополнительно обработано, чтобы получить водород, подаваемый в топливный элемент для получения постоянного электрического тока. Альтернативно, целлюлозный материал может быть дополнительно обработан, как показано на фиг. 4 и 5, для получения биоэтанола, биобутанола, биодизельного топлива и авиационного топлива, до того как любой твердый остаток будет обработан, как описано выше. На фиг. 4 и 5 далее показано, как биомасса и/или пластмассы, полученные из материала, выходящего после паровой обработки, могут быть переработаны для получения биоэтанола/биодизельного топлива, что показано на фиг. 1 как блоки N и J соответственно. Если сначала рассматривать целлюлозный материал, то, как показано на фиг. 4, биомасса из устройства для паровой обработки на фиг. 1 была обработана для обеззараживания материала, по существу,прекращением нежелательных анаэробных процессов, и чтобы сделать ее более подверженной гидролизу, как, в общем, показано в стадии 1 на фиг. 4. В стадии 2, показанной на фиг. 4, биомассу выдерживают в бункере 50 а для биомассы в течение около 8 ч. Затем биомассу подают в резервуар 51 а для кислотной обработки и затем обрабатывают серной кислотой из кислотной цистерны 50b, чтобы подвергнуть кислотному гидролизу в течение около 8 ч. Воду подают из водяного бака 50 с. Затем продукт фильтруют и удаляют твердые вещества (лигнин), которые могут быть использованы в качестве топлива для парового котла установки для паровой обработки. Из бункера 50d для хранения извести добавляют известь для нейтрализации жидкого продукта в нейтрализационном резервуаре 51b для удаления кислоты и дополнительно очищают и фильтруют. Гидролиз применяют для разложения твердой биомассы до целлюлозы и гемицеллюлозы, поскольку они являются основными сахаристыми веществами, содержащимися в биомассе. В процессе также преимущественно удаляют тяжелые металлы. Как упомянуто выше, кислотный гидролиз также действует для снабжения топливом парового котла в форме лигнина, который формирует основную часть негидролизуемых остатков. В альтернативной стадии 1, не показанной, вместо проведения кислотного гидролиза биомассу загружают в бак, где ее разлагают добавлением фермента, такого как фермент грибов рода Aspergillus, или применением целлулолитических микроорганизмов и питательного вещества. Дополнительно может быть добавлена вода. На этой стадии в бак может быть также введен активный озон из генератора. Полученную массу оставляют стоять в течение периода времени и затем сливают жидкость, которая будет содержать растворимые сахара. В любом случае жидкость затем подают в ферментационные резервуары 52, где происходит сбраживание при добавлении к жидкости дрожжей из бункера 53 для хранения дрожжей. Дрожжи обычно представляют собой сахаромицеты штамма Saccharomyces cerevisiae, которые могут быть использованы повторно, как показано. Сбраживание обычно занимает около 72 ч. В результате получают жидкость,содержащую этанол и другие продукты, и эту жидкость затем подают в стадию 4, включающую дистилляционную колонну 54, чтобы отогнать этанол и собрать его в баке 55 для хранения этанола. Для дистилляции берут ферментированную смесь, которая будет включать 12-14% этанольный раствор, и концентрируют смесь до содержания этанола около 99% или выше. Это достигается в две стадии, причем первая представляет собой традиционную дистилляцию, которая имеет результатом раствор с содержанием этанола около 94%, и остаточную воду удаляют с помощью молекулярных сит. Процесс, иллюстрированный на фиг. 4, часто реализуют в серии параллельных установок так, что процесс может протекать непрерывно. Этанол или другое биотопливо, полученные с использованием способа и устройства согласно настоящему изобретению, при желании могут быть использованы обычным порядком. Преимущественно топливо может быть применено для непосредственного питания генераторов, как показано на фиг. 2,размещенных на месте производства, чтобы избежать любых потерь, связанных с перевозкой или т.п. Показанные генераторы, которые обычно включают несколько машин с мощностью 1,5-3 МВт, могут быть приобретены у основного изготовителя двигателей, такого как Cummins, Perkin, Caterpillar и General Electric. Они могут быть без труда модифицированы для работы на биотопливе. Работающая на полную мощность установка, как показанная на фиг. 1, должна производить достаточно топлива для генерирования от около 6 до 15 МВт электроэнергии. Выходная мощность и генератор могут варьировать в зависимости от конкретной компоновки. Если теперь рассматривать пластические материалы, утилизируемые после паровой обработки, как показано на фиг. 5, то их подают в бак 60, куда добавляют растворитель, и полученную смесь оставляют стоять в испарительном резервуаре 61. После надлежащего промежутка времени полученные пары пропускают через цеолитный катализатор 62 и затем подвергают дистилляции в дистилляционной колонне 63 для сбора дизельного топлива. При желании в резервуар 60 может быть введен также озон. Озон, введенный в резервуары 51 и 60, может быть генерирован таким же образом, как это применялось для удаления запаха воздуха вблизи устройства для паровой обработки и генератора. Озон может быть подведен из отдельного генератора или генераторов. Дополнительно, если необходимо, воздух вблизи установки для получения этанола может быть подвергнут обработке озона для удаления любого избытка активного озона, остающегося в резервуарах 51 и 60. Настоящее изобретение предполагает переработку городских твердых отходов и разнообразных прочих органических материалов, требующих повторного использования и утилизации. Эти материалы имеют высокое содержание биомассы и склонны к заражению микроорганизмами, присутствующими в естественной окружающей среде, что может приводить к нежелательным реакциям сбраживания и разложения. Важно контролировать эти организмы, чтобы свести к минимуму заражение сырьевого материала, поступающего в последующие стадии конверсии биомассы, в особенности, если они основываются на ферментации. Также предпочтительно покрывать внутренности некоторых или всех резервуаров 51, 52, 60, 61 антимикробным средством. Предпочтительно средство является таким, которое не вымывается, не испаряется и не потребляется микроорганизмами. В особенности подходящими средствами являются такие,которые пригодны для нанесения на поверхности в виде покрытия. Пригодными антимикробными составами являются такие, которые включают в качестве активного ингредиента четвертичную аммониевую соль, предпочтительно хлоридную или бромидную соль. Атом азота в соли предпочтительно замещен силановой группой, предпочтительно триалкилоксисилановой группой, наиболее предпочтительно триметилоксисилановой группой. Наиболее предпочтительно силановая группа присоединена к атому азота соли через пропильную группу. Атом азота в соли предпочтительно также замещен тремя другими алкильными группами, по меньшей мере одна из которых предпочтительно представляет собой метил и по меньшей мере одна из которых предпочтительно представляет собой С 8-С 20-алкил. Так, предпочтительные соединения имеют следующую общую структуру:R2 представляет собой метил или С 8-С 20-алкил, предпочтительно метил;R3 представляет собой С 8-С 20-алкил, предпочтительно тетрадецил или октадецил;X представляет собой хлор, бром, предпочтительно хлор. Один пример применимого антимикробного средства включает хлорид 3(триметоксисилил)пропилдиметилоктадециламмония в качестве активного ингредиента. Еще один пример пригодного антимикробного реагента включает в качестве активного ингредиента хлорид 3(триметоксисилил)пропилдиметилтетрадециламмония. Настоящее изобретение предпочтительно имеет микробиоцидную функцию, введенную как часть полимерной пленки, нанесенной на внутренние поверхности оборудования. Полимерную пленку формируют in situ с использованием органосиланового прекурсора, который диспергирован с использованием уникальной смеси полимерных смачивающих средств и может быть повторно нанесен или пополнен без разборки оборудования. Эксперименты и измерения показали, что такие нанесенные антимикробные пленки являются прочными, долговечными и обеспечивают продолжительное во времени антимикробное действие. Отчасти полимерная пленка уничтожает микробы благодаря поверхностной структуре покрытия. Преобразования биомассы. Биомасса, полученная в данном процессе, имеет ряд вариантов применения, как обрисовано выше. Биомасса, полученная в реакционной камере С (фиг. 1), преимущественно была обеззаражена и сокращена в объеме. Важно то, что паровая обработка разрушает структуру органических материалов так, что целлюлоза и другие составные части высвобождаются и становятся более легкодоступными для последующей обработки. Биомасса, по существу, представляет собой источник целлюлозы, который был обработан так, чтобы целлюлоза была легкодоступна для дальнейшей переработки, такой как получение биотоплива, биоспиртов или т.п. Ферментация биомассы до топливных спиртов. Получение спиртов сбраживанием биомассы представляет собой один из старейших биотехнологических способов. В течение длительного времени было также известно применение полученного сбраживанием этанола как источника энергии, но в прошлом не использовалось в промышленном масштабе ввиду более высокой стоимости сравнительно с добычей нефти. Возможное использование биоэтанола как источника энергии стало вновь актуальным по мере истощения нефтяных ресурсов и возрастания их стоимости. Разработка возобновляемых биотоплив приобретает международный приоритет, обусловленный как экономическими, так и экологическими проблемами, в том числе сокращением выбросов парниковых газов, совершенствованием снабжения топливом внутри страны и поддержкой сельского хозяйства. Применение микробов для получения биотопливных материалов представляет собой в особенности привлекательный путь для производства биотоплива, в особенности, когда микробы делают это путем утилизации отходов, возникающих в других процессах. Газификация биомассы. Первоначально было разработано получение синтетического газа ("синтез-газа") как основного побочного продукта газификации угля и углеродсодержащих материалов, таких как сельскохозяйственные культуры и растительные остатки. В отличие от сжигания, которое главным образом создает диоксид углерода и воду, газификацию проводят при высоком значении отношения топлива к кислороду, и получают в основном газообразный водород (Н 2) и монооксид углерода (СО). Таким образом, синтез-газ главным образом состоит из H2 и СО, наряду с небольшими количествами СО 2 и прочих газов. Синтезгаз может быть непосредственно использован как низкосортное топливо или как топливо, подаваемое в топливные элементы. Альтернативно, он может быть применен в каталитических процессах для получения широкого ассортимента многообразных полезных химических продуктов, таких как метан, метанол и формальдегид. Биомасса согласно настоящему изобретению в высшей степени пригодна в качестве сырьевого материала для генерирования синтез-газа. Анаэробные микроорганизмы, такие как ацетогенные бактерии, предоставляют продуктивный путь для преобразования синтез-газа в полезные продукты, в частности в жидкие биотоплива, такие как биоэтанол и биодизель. Такие бактерии катализируют конверсию синтез-газа с высокой специфичностью,высокими выходами и более низкими энергозатратами, чем может быть достигнуто с использованием химических способов. Были идентифицированы некоторые микроорганизмы, способные производить биотоплива из отходящих газов и других субстратов. Например, были описаны три штамма ацетогенов для применения в производстве жидких топлив из синтез-газа: Butyribacterium methylotrophicum (Grethlein et al., 1990; Jain et al., 1994b); Clostridiumautoethanogenum (Abrini et al., 1994); Clostridium ljungdahlii (Arora et al., 1995; Barik et al., 1988; Barik et al. 1990 и Tanner et al., 1993). Штаммы Clostridium ljungdahlii и Clostridium autoethanogenum известны в преобразовании монооксида углерода в этанол. Патентная заявка US2007/275447 описывает бактерииClostridium carboxidivorans, штамм АТСС ВАА-624, "Р 7", способные синтезировать из отходящих газов продукты, которые пригодны в качестве биотоплива, в частности Р 7 может преобразовывать монооксид углерода в этанол. Кислотный гидролиз биомассы для получения спиртов. Биомасса типично содержит два базовых компонента, углеводы и лигнин. Содержащиеся в биомассе углеводы составлены целлюлозой или гемицеллюлозой, причем обе представляют собой полисахариды. Как целлюлоза, так и гемицеллюлоза могут быть преобразованы в простые сахара, в частности гексозные (в том числе глюкозу, фруктозу, маннозу и галактозу) и пентозные (в том числе ксилозу и арабинозу) сахара. Гексозные сахара традиционно сбраживают с образованием этанола, и пентозные сахара теперь способны к ферментации с использованием многообразных коммерчески доступных штаммовNRRL Y-2460, дрожжи Candida tropicalis, штамм АТСС 1369, штаммы грибов Fursarium, разработанные в организации Argonne National Laboratory, и Bacillus Macerans, разработанные в Калифорнийском Университете в Беркли и в Национальной лаборатории имени Лоуренса в Беркли. Типичными продуктами являются этанол, бутанол, 2,3-бутандиол. Все они представляют собой практичные и универсальные спирты для использования в транспортных средствах, поскольку они могут быть примешаны к бензину до высоких значений процентного содержания без существенных модификаций двигателей, и они оказывают сравнительно низкое коррозионное воздействие на топливные системы транспортных средств. Топливные спирты могут быть получены из биомассы, содержащей углеводы и лигнин, с генерированием чистой энергии. То есть спирт может быть получен из биомассы без подведения энергии от любого внешнего источника, введенная биомасса сама предоставляет сырьевой материал для этанола и энергию для всех производственных стадий. Фактически, в зависимости от конкретных технологических стадий и параметров, может быть получено большее количество энергии, чем это необходимо для всех технологических стадий, и может быть продано как в виде водяного пара, так и в форме электрической энергии. Таким образом, спирт может быть получен из биомассы, содержащей углеводы и лигнин, путем измельчения и суспендирования биомассы и затем последовательного подвергания биомассы кислотному гидролизу. Кислотный гидролиз выполняют при условиях температуры, концентрации кислоты и времени пребывания, достаточных для эффективного гидролиза гемицеллюлозы в биомассе с эффективным отделением от нее пентозных и гексозных сахаров в гидролизате, который не содержит фурфурол в количестве, достаточном для существенного ингибирования роста сбраживающих микроорганизмов, в то же время без значительного гидролиза целлюлозы в биомассе. Затем проводят сбраживание пентозных и гексозных сахаров в гидролизате, например, путем воздействия на них при надлежащих условиях окружающей среды дрожжей Pachysolen tannophilus, штамма NRRL Y-2460, штаммов грибов Fursarium и Bacillus Macerans, или т.п., и затем из ферментированных пентозных и гексозных сахаров получают спирт в ходе обычной обработки (например, дистилляции). При определенных обстоятельствах может быть желательным непосредственный гидролиз для разложения гемицеллюлозы, в то же время не обусловливая гидролиза целлюлозы, чтобы свести к минимуму образование фурфурола. Это может быть преимущественным в том смысле, что сводится к минимуму потребление энергии в процессе, и оставшаяся биомасса (включающая лигнин и целлюлозу), полученная после кислотного гидролиза гемицеллюлозы, может быть сожжена для получения энергии для всех производственных стадий, а также дополнительной энергии для прочих целей. Необходимо сводить к минимуму образование ингибиторов, таких как фурфурол, поскольку небольшие концентрации некоторых ингибиторов могут оказывать вредное воздействие на скорость роста сбраживающих микроорганизмов или убивать их. Как правило, кислотный гидролиз предпочтительно выполняют при концентрации кислоты от около 2 до 70 об.% (предпочтительно серной кислоты) и температура гидролиза составляет около 120 С или менее. Время пребывания при обработке в условиях кислотного гидролиза составляет от около 1 до 3 ч, и обработанная суспензия биомассы имеет отношение твердых веществ биомассы к жидкости от около 20/100 до 40/100 в расчете на объем. Размер частиц в биомассе составляет от 1-4 мм. Альтернативно, способ обработки биомассы, имеющей сбраживаемый материал, включает следующие стадии: суспендированную биомассу закачивают в вертикальный резервуар для кислотного гидролиза, причем биомасса предпочтительно имеет средний размер частиц 1-4 мм. Кислотный гидролиз биомассы непрерывно проводят в резервуаре при температуре около 120 С или менее для получения гидролизата. Первую часть гидролизата пропускают до конечного пункта процесса для его сбраживания и вторую часть гидролизата пропускают в суспензионный трубопровод для эффективного суспендирования биомассы. Биомассу в резервуаре после ее кислотного гидролиза промывают введением потока горячей воды в верхнюю часть резервуара. Гидролизованную и промытую биомассу выводят из верхней части резервуара и обезвоживают. Воду от обезвоживания биомассы направляют в поток промывной воды,вводимой в резервуар. Гидролизат предпочтительно обрабатывают путем нейтрализации его известью, осветляют его и затем пропускают его в традиционный ферментатор. После сбраживания "бражку" направляют в стадию отделения дрожжей и затем в конечном итоге в общеупотребительные дистилляционные колонны, где получают этанол, бутанол, 2,3-бутандиол и/или другие спирты. После обезвоживания биомассу направляют в печь вместе с продуктами отделения дрожжей для получения водяного пара. Объем полученного водяного пара является достаточным для подачи пара, необходимого для дистилляционных колонн, для пропаривания биомассы в промежуточном бункере, для нагревания промывной воды и для работы всех необходимых насосов, смесителей и т.п. Дополнительно, должно оставаться достаточное количество энергии, чтобы вся установка действовала как производитель чистой энергии, генерируя водяной пар или электроэнергию в дополнение к спирту, без подведения энергии от внешнего источника (кроме как из самой биомассы). Биомасса может быть преобразована в спирт с использованием ультразвуковой энергии. Патентная заявка US2008/044891 (FC STONE CARBON LLC) "Конверсия биомассы в спирт с использованием ультразвуковой энергии" описывает способ, включающий приложение ультразвуковой энергии к биомассе в процессе получения спирта, таком как процесс производства этанола. В способе используют ультразвуковую энергию только как средство предварительной обработки или дополнительно применяют предварительную обработку гидролизом концентрированной кислотой или гидротермическую либо химическую предварительную обработку с последующей стадией ферментативного гидролиза или ферментативного гидролиза одновременно со стадией осахаривания. Микроволновая каталитическая обработка биомассы. Китайская патентная публикация CN 100999676 (Технологический Университет Аньхой) описывает способ микроволнового каталитического крекинга биомассы для получения биологического масла с высоким содержанием гидроксиацетона с использованием карбоната натрия в качестве катализатора, карбида кремния в качестве среды, поглощающей микроволновое излучение, микроволнового источника как нагревательного средства для расщепления биомассы и смеси льда с водой для охлаждения летучих компонентов для получения биологического масла с высоким содержанием гидроксиацетона. Благодаря уникальному температурному воздействию микроволнового излучения на частицы биомассы и уникальному каталитическому эффекту карбоната натрия в расщеплении биомассы в способе реализовано образование гидроксиацетона с высокой эффективностью. Получение бутанола. Ферментативное получение бутанола также хорошо известно. Международная патентная публикация WO 2008/025522 (фирма Bayer Technology Services GmbH) относится к способу получения биоспирта, в частности этанола или бутанола, из биомассы, в котором биомассу измельчают, полученную биомассу подают на ферментацию и получают спирт из продукта сбраживания, причем нерастворимые компоненты и/или неферментированные сахара отделяют от биомассы до сбраживания и/или дрожжи и бактерии отделяют после сбраживания. Применение биомассы в топливных элементах. Электроэнергетическая промышленность, в общем, предусматривала использование топливных элементов в относительно крупных масштабах для получения электроэнергии. Получение электроэнергии топливными элементами предоставляет преимущества высокой эффективности и низких уровней выбросов в окружающую среду. Таким образом, топливные элементы могут представлять собой более экономически выгодное средство генерирования электроэнергии, чем другие существующие технологии производства электроэнергии. Топливные элементы с расплавленным карбонатом и твердооксидные топливные элементы весьма пригодны для потребления нагретых газовых потоков и тем самым являются многообещающими в плане промышленного производства электроэнергии. Газификаторы биомассы могут быть использованы как источники сырья, пригодного для применения в этих топливных элементах. Как описано выше, газы,необходимые в качестве сырья для топливных элементов, могут быть без труда получены путем газификации биомассы согласно настоящему изобретению. Более высокая эффективность общеупотребительных топливных элементов может быть достигнута в сочетании с газификаторами биомассы, например, в объединенной системе газогенератора и топливного элемента, в которой поток газа проходит из газогенератора через внешний отделитель диоксида углерода. Патентная заявка US2002/194782 (Paisley) описывает интегрированную систему газификации биомассы и топливного элемента, в которой электрохимическая реакция в топливном элементе проводится при подведении газообразных реактантов из газогенератора. Газообразное топливо из газогенератора направляют на анод топливного элемента и по меньшей мере часть отходящего газа с анода направляют в камеру сгорания. Часть отходящего газа с анода затем сжигают для извлечения остаточной энергии, чтобы повысить общую эффективность интегрированной системы газификации биомассы и топливного элемента. Кроме того, газообразный окислитель из камеры сгорания может быть направлен на катод топливного элемента. Патент US 5736026 (Energy Res. Corp.), озаглавленный "Устройство и способ совместного генерирования электроэнергии из биомассы и топливного элемента", описывает производство этанола сбраживанием биомассы с интегрированным электрическим генератором на основе топливного элемента для получения электрической и тепловой энергии, причем совместное генерирование включает применение топливного элемента, работающего на спирте, и диоксида углерода из ферментации, который повышает генерирование энергии, и применение спирта для производства теплоты и электрической энергии из топливного элемента, чем повышается эффективность получения топлива. В вышеописанном описании показано, что биомасса, полученная согласно настоящему изобретению, может быть использована многообразными путями. Обычно конкретная установка будет сосредоточена на конкретном одном из этих процессов ниже по потоку, например на генерировании электроэнергии из топливного элемента или получении биотоплив и биоспиртов. Квалифицированный специалист может реализовать это, используя один из способов, описанных или цитированных, или других способов, известных в технологии, или тех, которые могут быть разработаны. Краткие выводы. В этом документе термин "давление окружающей среды" используют для обозначения давления в резервуаре 30, когда резервуар не герметизирован для течения газов. Давление в резервуаре тем самым обычно будет равным атмосферному давлению или несколько превышающим давление вокруг установки. Давление внутри резервуара может быть слегка более высоким, чем давление вокруг установки,вследствие введения водяного пара, даже без герметизации резервуара. Термин "температура окружающей среды" используют в этом документе для обозначения температуры среды, окружающей установку,которая может варьировать в зависимости от местоположения, времени года и общих погодных условий. Целлюлозный материал, в общем, обозначает целлюлозу и гемицеллюлозу, если контекст недвусмысленно не оговаривает нечто иное. В общем, настоящее изобретение относится к способу и устройству для повторного использования городских бытовых отходов, включающим подвергание отходов воздействию водяным паром при температуре 150-200 С. После паровой обработки полученный материал разделяют на составные части и биомассу и/или пластмассы подвергают дополнительной обработке. Паровая обработка преимущественно обеззараживает обработанный материал и значительно сокращает его объем. Важно то, что паровая обработка расщепляет целлюлозу и прочие органические материалы так, что волокна обнажаются, обеспечивая возможность более легкого преобразования обработанной паром биомассы в биотопливо, биоспирты и т.д. Дополнительная обработка предпочтительно дает биоэтанол из биомассы и дизельное топливо из пластмасс. В качестве альтернативы часть биомассы или вся таковая может быть подвергнута газификации, чтобы получать водород, который, в свою очередь, может быть подан в топливный элемент для получения электрической энергии. ФОРМУЛА ИЗОБРЕТЕНИЯ 1. Устройство для обработки материала твердых отходов, содержащее вращающийся резервуар (30) с впускным каналом (32) для вводимых отходов, расположенный так,что при вращении резервуара (30) в его внутренней части образуется первая зона, главным образом заполненная материалом отходов, и вторая зона, по существу, не содержащая материала отходов; выпускной канал (33) для обработанных отходов; множество паровых сопел (38) для селективного введения водяного пара во внутреннюю часть резервуара (30), причем каждое паровое сопло (38) расположено в резервуаре (30); привод, предназначенный для вращения резервуара (30) и, таким образом, для перемещения паровых сопел (38) между первой зоной и второй зоной так, что только часть из паровых сопел (38) может одновременно находиться в указанной первой зоне; и устройство (36) для регулирования подачи водяного пара, предназначенное для подведения водяного пара только к паровым соплам, находящимся в текущий момент в первой зоне. 2. Устройство по п.1, дополнительно включающее нагревательное средство для нагревания и/или поддержания внутренней части резервуара (30) при температуре 150-200 С. 3. Устройство по п.2, в котором нагревательное средство выбирают из группы, состоящей из средства нагрева воздухом наружной паровой рубашки и нагревательного элемента. 4. Устройство по п.2, в котором нагревательное средство включает только нагревательную рубашку, нагреваемую водяным паром. 5. Устройство по любому из предшествующих пунктов, в котором устройство (36) для регулирования подачи водяного пара содержит распределительный вентиль (36) для направления водяного пара от парогенератора к паровому соплу, содержащий корпус вентиля, имеющий впускное отверстие (52), сообщающееся по текучей среде с парогенератором, и множество выпускных отверстий (54), сообщающихся по текучей среде с паровым соплом, при этом вентиль (36) выполнен так, что в любое время по меньшей мере одно из выпускных отверстий (54) является разобщенным по текучей среде с впускным отверстием (52). 6. Способ обработки материала отходов в устройстве по любому из пп.1-5, включающий стадии:a) введения измельченного материала отходов в резервуар (30);b) обработки измельченного материала отходов водяным паром, при этом водяной пар вводят только в измельченный материал отходов. 7. Способ по п.6, в котором водяной пар находится при температуре 150-200 С. 8. Способ по п.6 или 7, в котором резервуар (30) находится при атмосферном давлении. 9. Способ по п.6, который представляет собой непрерывно осуществляемый способ, причем материал отходов вводят во впускной канал (32) резервуара (30) и обработанный материал отходов выводят из выпускного канала (33) резервуара (30). 10. Способ по любому из пп.6-9, в котором обработанный материал отходов включает биомассу из целлюлозы, пластмассы, черные металлы и цветные металлы. 11. Способ по любому из пп.6-10, в котором внутреннюю часть резервуара нагревают до температуры 150-200 С. 12. Способ по любому из пп.6-11, в котором внутренняя часть резервуара (30) находится под давлением ниже 2 бар (0,2 МПа). 13. Способ по любому из пп.6-12, в котором внутренняя часть резервуара (30) находится, по существу, под давлением окружающей среды. 14. Способ по любому из пп.6-13, в котором устройство предназначено для обработки материала отходов в непрерывном режиме. 15. Способ по любому из пп.6-14, в котором обработанный материал отходов включает биомассу из целлюлозного материала, содержащую менее 1% серы. 16. Способ по любому из пп.6-15, в котором выпускной канал (33) соединяют с сортировочной камерой, где обработанный материал отходов разделяют на пластмассы, черные металлы, цветные металлы и биомассу из целлюлозного материала. 17. Способ по п.15 или 16, в котором биомассу транспортируют в гипербарическое устройство или топливный элемент или в установку для химического превращения для преобразования биомассы в биодизельное топливо или органический спирт, такой как биоэтанол или биобутанол, или авиационное топливо. 18. Способ по п.17, в котором биодизельное топливо или органический спирт используют для питания электрических генераторов, дополнительно содержащихся в устройстве.
МПК / Метки
МПК: C12P 7/08, B02C 17/00, B09B 3/00, F16K 11/00, C02F 11/10, A61L 11/00, B03B 9/06
Метки: способ, обработки, устройство, отходов
Код ссылки
<a href="https://eas.patents.su/16-19123-ustrojjstvo-i-sposob-obrabotki-othodov.html" rel="bookmark" title="База патентов Евразийского Союза">Устройство и способ обработки отходов</a>
Предыдущий патент: Производные 6-гетероциклоимидазо[1,2-а]пиридин-2-карбоксамидов, их получение и их применение в терапии
Следующий патент: Способ переработки для повторного использования изделий на основе армированного волокном полимера
Случайный патент: Прохладительный напиток