Термообработанный стальной материал, способ его получения и базовый стальной материал для него
Формула / Реферат
1. Сталь, имеющая химический состав, включающий, мас.%: С - 0,05-0,35, Si - не более 0,5, Mn - 0,5-2,5, Р - не более 0,03, S - не более 0,01, растворимый Al - не более 0,1, N - не более 0,01, В - 0-0,005, Ti - 0-0,1, Cr - 0-0,5, Nb - 0-0,1, Ni - 0-1,0 и Mo - 0-0,5%, и которая имеет структуру, содержащую карбиды, причем степень сфероидизации карбидов составляет 0,60-0,90, а численная плотность карбидов составляет по меньшей мере 0,50 карбида на 1 мкм2.
2. Сталь по п.1, в которой численная доля крупнозернистых карбидов, имеющих диаметр частиц по меньшей мере 0,5 мкм, в карбидах составляет не более 0,15.
3. Сталь по любому из пп.1, 2, в которой химический состав содержит по меньшей мере один элемент, выбранный из группы, состоящей из В - 0,0001-0,005%, Ti - 0,01-0,1%, Cr - 0,18-0,5%, Nb - 0,03-0,1%, Ni - 0,18-1,0% и Mo - 0,03-0,5%.
4. Сталь по любому из пп.1-3, имеющая слой покрытия на основе цинка по меньшей мере на части ее поверхности.
5. Термообработанная сталь, полученная из стали по любому из пп.1-4, которая была подвергнута обработке горячей штамповкой.
6. Термообработанная сталь, полученная из стали по любому из пп.1-4, которая была подвергнута горячей трехмерной гибке и прямой закалке.
7. Способ получения термообработанной стали, включающий стадию обработки горячей штамповкой стали по любому из пп.1-4.
8. Способ получения термообработанной стали, включающий стадию горячей трехмерной гибки и прямой закалки стали по любому из пп.1-4.
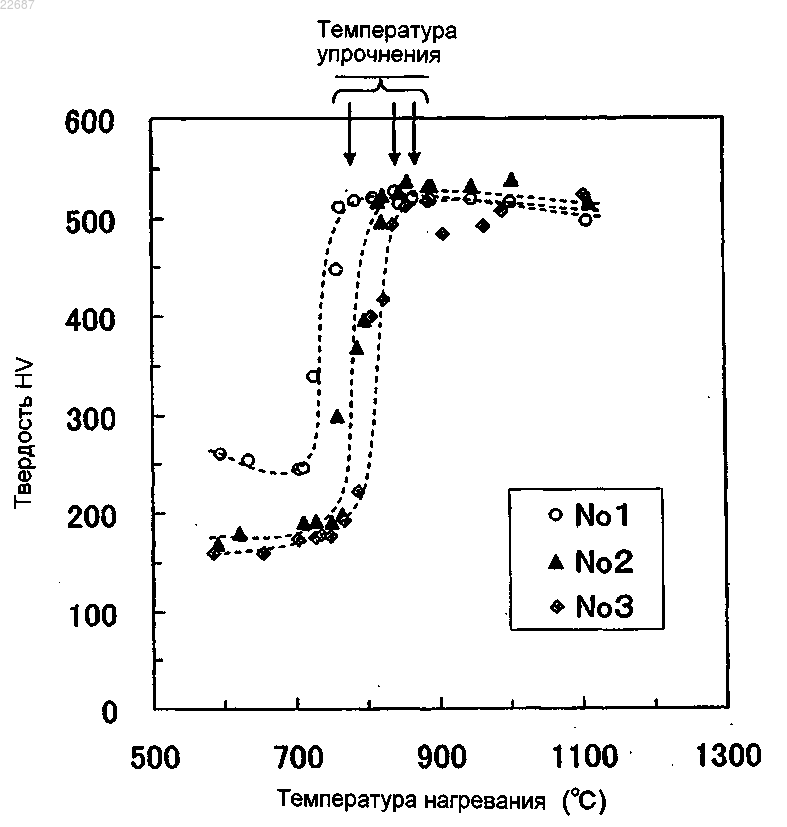
Текст
ТЕРМООБРАБОТАННЫЙ СТАЛЬНОЙ МАТЕРИАЛ, СПОСОБ ЕГО ПОЛУЧЕНИЯ И БАЗОВЫЙ СТАЛЬНОЙ МАТЕРИАЛ ДЛЯ НЕГО В изобретении представлен стальной материал, который пригоден для обработки горячей штамповкой или горячей трехмерной гибкой и прямой закалкой и который может быть использован для изготовления высокопрочного формованного изделия с достаточным закалочным упрочнением даже при кратковременном нагревании при низкой температуре, имеет химический состав,включающий, мас.%: С - 0,05-0,35, Si - не более 0,5, Mn - 0,5-2,5, Р - не более 0,03, S - не более 0,01, растворимый Al - не более 0,1, N - не более 0,01, и необязательно по меньшей мере один элемент, выбранный из группы, состоящей из В - 0,0001-0,005%, Ti - 0,01-0,1%, Cr - 0,18-0,5%,Nb - 0,03-0,1%, Ni - 0,18-1,0% и Mo - 0,03-0,5%, и имеет структуру стали, в которой степень сфероидизации карбидов составляет 0,60-0,90. Область техники, к которой относится изобретение Настоящее изобретение относится к стальному материалу для термической обработки, термообработанному стальному материалу, полученному проведением термической обработки стального материала, и способу получения термообработанного стального материала. Стальной материал согласно настоящему изобретению пригоден для вариантов применения, в которых после кратковременного нагревания проводят закалочное упрочнение, и в особенности пригоден в качестве материала для так называемой горячей трехмерной гибки и прямой закалки, или обработки горячей штамповкой. Термообработанный стальной материал согласно настоящему изобретению имеет равномерно высокую прочность, хорошую усталостную прочность и ударную вязкость, даже когда он получен термической обработкой, в которой закалочное упрочнение проводят после кратковременного нагревания. Уровень техники В последние годы возникла потребность в сокращении толщины и повышении прочности конструкционных деталей для автомобилей по соображениям глобальных экологических проблем и безопасности при столкновениях. Чтобы удовлетворить эту потребность, для конструкционных деталей автомобилей во все возрастающем объеме используют лист из высокопрочной стали в качестве основного материала. Однако когда конструкционные детали автомобилей изготавливают штамповкой листа из высокопрочной стали, используемого в качестве базового материала, легко возникают дефекты формования в виде складок и упругого последействия. Поэтому изготовление конструкционных деталей для автомобилей штамповкой листов из высокопрочной стали является непростой задачей. В качестве метода разрешения таких проблем известна так называемая горячая штамповка, причем горячая штамповка представляет собой способ изготовления высокопрочных формованных изделий путем штамповки стального листа, который был нагрет до высокой температуры в диапазоне выше 700 С,и затем подвергнут закалочному упрочнению либо внутри, либо снаружи прессующих штампов. При горячей штамповке, поскольку формование проводят в высокотемпературном диапазоне, в котором прочность стального листа снижается, могут быть подавлены вышеописанные дефекты формования. Кроме того, можно сообщить формованному изделию высокую прочность проведением закалочного упрочнения после формования. Соответственно этому горячей штамповкой можно изготавливать такие формованные изделия, как конструкционные детали для автомобилей, имеющие высокую прочность,например, такую как 1500 МПа или выше. В отношении горячей штамповки, например, патентный документ 1 представляет стальной лист для горячей штамповки, который предназначен для того, чтобы сделать возможным проведение успешного формования без возникновения разрывов или трещин во время формования путем горячей штамповки. Недавно были предложены новые способы, которые обеспечивают возможность изготовления высокопрочных формованных изделий иными методами, нежели горячая штамповка. Например, патентный документ 2 раскрывает способ гибки металлического материала по технологии "push-through" ("проталкиванием"). В этом способе, в то время как нагревательное устройство и охлаждающее устройство являются подвижными относительно металлического материала, металлический материал локально нагревают нагревательным устройством, и в месте, где сопротивление деформации было значительно снижено вследствие нагревания, прилагают изгибающий момент так, чтобы выполнить гибку до желательной формы, которая представляет собой двумерную или трехмерную гибку. Затем выполняют закалочное упрочнение охлаждением с помощью охлаждающего устройства (в настоящем описании данный способ будет обозначаться как горячая трехмерная гибка и прямая закалка). Способом горячей трехмерной гибки и прямой закалки можно эффективно изготавливать высокопрочное формованное изделие с высокой точностью гибки. Соответственно этому способом горячей трехмерной гибки и прямой закалки можно получать формованные изделия, такие как конструкционные детали для автомобилей, имеющие высокую прочность на уровне, например, 900 МПа или выше. Документы предшествующего уровня техники Патентные документы Патентный документ 1: JP 200 6-283064 А. Патентный документ 2: JP 2007-83304 А. Сущность изобретения Чтобы обеспечить коррозионную стойкость в условиях среды применения, конструкционные детали для автомобилей часто делают из оцинкованных стальных материалов, имеющих плакирование или покрытие на основе цинка (в частности, отожженные и оцинкованные стальные материалы), которые являются благоприятными с точки зрения стоимости. Поэтому, когда конструкционные детали для автомобилей изготавливают горячей штамповкой или горячей трехмерной гибкой и прямой закалкой, часто является необходимым применение оцинкованного стального материала в качестве обрабатываемого материала. Однако существуют проблемы, которые необходимо разрешить, чтобы использовать оцинкованный стальной материал для горячей штамповки или горячей трехмерной гибки и прямой закалки. А именно, когда оцинкованный стальной материал используют в качестве материала, обрабатывае-1 022687 мого горячей штамповкой или горячей трехмерной гибкой и прямой закалкой, оцинкованный стальной материал нагревают на воздухе до температуры по меньшей мере 700 С и обычно до высокотемпературного диапазона до точки Ac1 или выше, или даже точки Ас 3 или выше. Давление паров цинка по мере повышения температуры быстро возрастает, что подтверждается тем фактом, что оно составляет 200 мм рт. ст. при температуре 788 С и 400 мм рт. ст. при температуре 844 С. Поэтому, если оцинкованный стальной материал нагревают до вышеописанного высокотемпературного диапазона, существует возможность того, что большая часть плакирования или покрытия на основе цинка испарится и потеряется. В дополнение, поскольку нагревание происходит на воздухе, во время нагревания заметно увеличивается окисление цинка и противокоррозионное действие покрытия на основе цинка может быть утрачено. Кроме того, если нагревание выполняют до температуры по меньшей мере 600 С и в особенности до температуры, превышающей 660 С, при которой разлагается Г-фаза(Fe3Z10), происходит заметное растворение Zn в ферритной фазе, которая составляет базовую стальную основу оцинкованного стального материала. Поэтому существует возможность потери большей части плакирования или покрытия на основе цинка в результате не только испарения, но и растворения в стальной основе с образованием твердого раствора. Таким образом, когда оцинкованный стальной материал используют в качестве материала для горячей штамповки или горячей трехмерной гибки и прямой закалки, стальной материал, полученный горячей штамповкой или горячей трехмерной гибкой и прямой закалкой (ниже этот материал будет называться "термообработанным стальным материалом", чтобы отличать его от предназначенного для обработки материала, который будет называться "стальным материалом"), покрытие на основе цинка недостаточно сохраняется на поверхности, или даже если покрытие на основе цинка сохраняется, оно утрачивает свою антикоррозионную функцию. Поэтому для покрытия на основе цинка надлежащее проявление его антикоррозионного действия может оказаться невозможным. Соответственно этому, желательно, чтобы оцинкованный стальной материал, который подвергают обработке горячей штамповкой или горячей трехмерной гибкой и прямой закалкой, имел достаточную способность к закалочному упрочнению для изготовления высокопрочного формованного изделия, даже когда применяют кратковременное нагревание так, что слой покрытия на основе цинка может сохраняться настолько полно, насколько возможно, на поверхности термообработанного стального материала после того, как он был подвергнут горячей штамповке или горячей трехмерной гибке и прямой закалке. Такая способность не ограничивается оцинкованными стальными материалами, и она также желательна для неплакированных/непокрытых стальных материалов, которые не имеют плакирования или покрытия на основе цинка. Это обусловлено тем, что, если неплакированный или непокрытый стальной материал используют для обработки горячей штамповкой или горячей трехмерной гибкой и прямой закалкой, на поверхности стального материала во время нагревания и охлаждения образуется окалина. Поэтому на последующем этапе необходимо удалять окалину дробеструйной обработкой или травлением. Если не имеющий металлического покрытия стальной материал может быть подвергнут закалочному упрочнению, достаточному для изготовления формованного изделия, имеющего высокую прочность,кратковременным нагреванием при низкой температуре, то можно эффективно подавить образование вышеописанной окалины и могут быть сокращены расходы, требуемые для удаления окалины. Соответственно этому также желательно, чтобы не имеющий металлического покрытия стальной материал, подвергаемый обработке горячей штамповкой или горячей трехмерной гибкой и прямой закалкой, был способен к закалочному упрочнению, достаточному для изготовления формованного изделия, имеющего высокую прочность, путем кратковременного нагревания при низкой температуре, чтобы сократить образование окалины на поверхности термообработанного стального материала, которая наблюдается после проведения горячей штамповки или горячей трехмерной гибки и прямой закалки. Настоящее изобретение предназначено для разрешения указанных выше проблем предшествующего уровня техники, и его цель состоит в создании стального материала, имеющего способность к закалочному упрочнению, достаточному для изготовления формованного изделия, имеющего высокую прочность, кратковременным нагреванием при низкой температуре, тем самым делая его пригодным для применения в качестве материала, обрабатываемого горячей штамповкой или горячей трехмерной гибкой и прямой закалкой. Еще одна цель настоящего изобретения заключается в создании термообработанного стального материала с использованием этого стального материала и способа его получения. В результате проведенных авторами настоящего изобретения подробных исследований, нацеленных на разрешение вышеописанных проблем и касающихся способности к закаливанию кратковременным нагреванием, обнаружились следующие новые проблемы. А именно, в результате упрочнения термообработанного стального материала, способного к упрочнению карбидами, которые не в надлежащей степени растворяются с образованием твердого раствора во время стадии нагревания и присутствуют в нерастворенном состоянии, несмотря на то, что растворение карбидов во время стадии нагревания является недостаточным, термообработанный стальной материал иногда проявляет максимальную твердость. В этом случае было найдено, что, даже если используют температуру нагревания, которая обеспечивает максимальную твердость, растворение карбидов во время стадии нагревания становится недостаточным, и иногда возникают разнообразные проблемы вследствие ненадлежащего растворения карбидов. Например, в случае обработки горячей штамповкой, в которой закалочное упрочнение происходит внутри прессующих штампов, скорость охлаждения является относительно низкой. Поэтому относительно легко достигнуть хорошей ударной вязкости с использованием эффекта самоотпуска. Однако,даже если термообработанную сталь, имеющую высокую прочность, получают с использованием температуры нагревания, которая обеспечивает максимальную твердость, усталостная прочность ухудшается карбидами, которые присутствуют в нерастворенном состоянии, и иногда невозможно получить хорошую усталостную прочность, которая соответствует высокой прочности. В дополнение, даже если пытаются получить высокопрочный термообработанный стальной материал с использованием температуры нагревания, которая приводит к максимальной твердости, то вследствие растворения карбидов с образованием твердого раствора, происходящего недостаточно во время стадии нагревания, фактическая прокаливаемость иногда является низкой. В этом случае, поскольку на прочность после закалочного упрочнения легко влияет скорость охлаждения, и вследствие разницы в скоростях охлаждения в различных местах одного и того же стального материала, обусловленной формой стального материала или состоянием контакта между стальным материалом и штампами во время охлаждения, прочность может заметно варьировать от одного места к другому внутри одного и того же термообработанного стального материала. При горячей трехмерной гибке и прямой закалке скорость охлаждения является относительно высокой благодаря применению, например, охлаждения водой. Поэтому, даже если от одного места к другому в одном и том же стальном материале возникают различия в скорости охлаждения, скорость охлаждения в каждом месте является достаточно высокой, и тенденция к заметным колебаниям прочности от одного места к другому внутри одного и того же термообработанного стального материала не проявляется. Однако, поскольку при использовании эффекта самоотпуска становится затруднительным достижение хорошей ударной вязкости, на ударную вязкость, которая проявляется после закалочного упрочнения, легко влияет неоднородность структуры стали. Поэтому существует большая разница между температурой нагревания, необходимой для получения высокой прочности, и температурой нагревания, требуемой для получения хорошей ударной вязкости. В результате этого, даже если высокопрочный термообработанный стальной материал получают с использованием температуры нагревания, пригодной для получения максимальной твердости, ударная вязкость становится плохой вследствие карбидов, присутствующих в нерастворенном состоянии, и иногда получить хорошую ударную вязкость невозможно. Таким образом, в материалах для горячей штамповки с относительно низкой скоростью охлаждения во время закалочного упрочнения желательно получение хорошей усталостной прочности на уровне,который согласуется с их высокой прочностью, и подавление колебаний прочности от одного места к другому внутри одного и того же термообработанного стального материала, даже когда возникают различия в скорости охлаждения от одного места к другому внутри одного и того же стального материала. В материале для горячей трехмерной гибки и прямой закалки, обеспечивающей относительно высокую скорость охлаждения во время закалочного упрочнения, является желательным сокращение разности между температурой нагревания, необходимой для получения высокой прочности, и температурой нагревания, требуемой для получения хорошей ударной вязкости. Авторы настоящего изобретения провели дополнительные подробные исследования с целью разрешения этих новых проблем. В это время они рассмотрели ситуации, в которых на стальном материале проводят предварительное формование перед подверганием его обработке горячей штамповкой или горячей трехмерной гибкой и прямой закалкой. Они также исследовали, как улучшить формуемость стального материала до закалочного упрочнения. В результате они сосредоточились на форме карбидов в структуре стали, и они обнаружили новый технический принцип, который совершенно не был изучен в предшествующем уровне техники. Этот принцип состоит в том, что имеется подходящая степень сфероидизации, чтобы обеспечить быстрое растворение карбидов с образованием твердого раствора, даже когда кратковременное нагревание проводят при низкой температуре, в то же время с достижением хорошей формуемости перед закалочным упрочнением. В предшествующем уровне техники сфероидизирующая обработка карбидов, которую проводят для улучшения формуемости стального материала перед закалочным упрочнением, нацелена на достижение полной сфероидизации карбидов (со степенью сфероидизации 100%). Настоящее изобретение основано на вышеописанном техническом принципе и на следующих вновь обнаруженных фактах. А именно, стальной материал, который подвергают закалочному упрочнению, обычно содержит легирующие элементы, такие как Mn, который способен улучшать прокаливаемость стали. Легирующие элементы, образующие растворы замещения, такие как Mn, склонны легко концентрироваться в сфероидизированных карбидах. Карбиды, в которых концентрируются образующие растворы замещения легирующие элементы, такие как Mn, проявляют медленное растворение для образования твердого раствора во время стадии нагревания в ходе закалочного упрочнения, тем самым растворение карбидов становится ненадлежащим, когда кратковременное нагревание выполняют при низкой температуре. В результате,-3 022687 поскольку остаются нерастворенные карбиды, структура стали не достигает надлежащей степени однородности, и фактическая прокаливаемость иногда снижается. Если степень сфероидизации карбидов ориентирована на верхний предел, то это стимулирует растворение карбидов с образованием твердого раствора во время стадии нагревания в ходе закалочного упрочнения. В результате растворение карбидов быстро прогрессирует, даже когда кратковременное нагревание проводят при низкой температуре, и можно повысить фактическую прокаливаемость. С другой стороны, если степень сфероидизации карбидов установлена на нижний предел, то можно получить хорошую формуемость стального материала перед закалочным упрочнением. Как указано ниже, в настоящем изобретении стальной материал иногда содержит бор (В), который имеет эффект повышения ударной вязкости и прокаливаемости стального материала. Стимулирование растворения карбидов с образованием твердого раствора во время стадии нагревания в ходе закалочного упрочнения также является очень эффективным, чтобы обеспечить надлежащее проявление вышеописанного действия бора (В). Это обусловлено тем, что вышеописанное действие бора (В) проявляется,когда бор (В) присутствует в стали в твердом растворе, но бор (В) легко образует карбиды и склонен присутствовать в карбидах. Соответственно этому содействием растворению карбидов с образованием твердого раствора во время стадии нагревания в ходе закалочного упрочнения повышают долю бора (В),присутствующего в стали в форме твердого раствора, и вышеописанное действие бора (В) проявляется в надлежащей мере. Настоящее изобретение представляет стальной материал, который имеет химический состав, включающий, мас.%: С - 0,05-0,35%, Si - самое большее 0,5%, Mn - 0,5-2,5%, Р - самое большее 0,03%, S - самое большее 0,01%, Al растворимый - самое большее 0,1%, N - самое большее 0,01%, В - 0-0,005%, Ti 0-0,01%, Cr - 0-0,5%, Nb - 0-0,1%, Ni - 0-1,0% и Mo - 0-0,5%, и который имеет структуру стали, которая содержит карбиды, причем степень сфероидизации карбидов составляет 0,60-0,90. Степень сфероидизации карбидов означает долю карбидов, имеющих соотношение геометрических размеров не более 3. Более конкретно, она определяется как отношение числа карбидов, имеющих соотношение геометрических размеров не более 3, к числу карбидов, для которых их соотношение геометрических размеров было определено описанным ниже методом. По описанным ниже соображениям соотношение геометрических размеров определяют для карбидов, имеющих диаметр частиц по меньшей мере 0,2 мкм. Предпочтительные варианты осуществления настоящего изобретения включают: вышеописанный химический состав содержит по меньшей мере один элемент, выбранный из группы, состоящей из В - 0,0001-0,005%, Ti - 0,01-0,1%, Cr - 0,18-0,5%, Nb - 0,03-0,1%, Ni - 0,18-1,0% и Mo 0,03-0,5%; численная плотность карбидов составляет по меньшей мере 0,50 карбида на 1 мкм 2; численная доля крупнозернистых карбидов, имеющих диаметр частиц по меньшей мере 0,5 мкм, в карбидах составляет не более 0,15; по меньшей мере часть поверхности стального материала имеет сформированное на нем металлическое покрытие или покрытие на основе цинка. Настоящее изобретение также относится к термообработанному стальному материалу, полученному из вышеописанного стального материала, который был подвергнут обработке горячей штамповкой или горячей трехмерной гибкой и прямой закалкой, и к способу получения термообработанного стального материала, включающему стадию, в которой вышеописанный стальной материал подвергают обработке горячей штамповкой или горячей трехмерной гибкой и прямой закалкой. Стальной материал согласно настоящему изобретению (материал перед термической обработкой) имеет такие свойства, что он может быть подвергнут закалочному упрочнению, достаточному для изготовления формованного изделия с высокой прочностью, кратковременным нагреванием при низкой температуре, и тем самым пригоден в качестве материала для проведения горячей штамповки или горячей трехмерной гибки и прямой закалки. Когда стальной материал представляет собой оцинкованный стальной материал, то во время изготовления термообработанного стального материала горячей штамповкой или горячей трехмерной гибкой и прямой закалкой можно обеспечить присутствие большего количества основанного на цинке плакирования или покрытия на поверхности полученного термообработанного стального материала, чем в предшествующем уровне техники. В результате можно изготовить термообработанный стальной материал,имеющий высокую устойчивость к коррозии. Когда стальной материал представляет собой не имеющий металлического покрытия стальной материал, образование окалины, которая возникает на поверхности термообработанного стального материала, полученного горячей штамповкой или горячей трехмерной гибкой и прямой закалкой, может быть ограниченным до низкого уровня, так что можно снизить затраты, необходимые для удаления окалины на последующем этапе. В случае автомобильных деталей подходящие места, в которых применяется термообработанный стальной материал согласно настоящему изобретению, предпочтительно представляют собой такие места, где снижение веса транспортного средства может быть достигнуто повышением прочности материа-4 022687 ла, например, такие как стойки, балки дверей, крыши и усилители бамперов. Краткое разъяснение чертежей Фиг. 1 представляет график, показывающий взаимосвязь между твердостью в поперечном сечении и температурой нагревания для стальных листов из образцов 1-3 в примере; фиг. 2 показывает форму образца для испытания усталостных характеристик; фиг. 3 показывает S-N-кривую для термообработанного стального материала, который был подвергнут горячей штамповке с сэндвичеобразным размещением стальных листов образцов 1-3 в примере между парой плоских штампов; фиг. 4 схематически показывает горячую штамповку с использованием разъемных штампов; фиг. 5 представляет график, показывающий твердость в поперечном сечении для термообработанного стального материала, который был подвергнут горячей штамповке с сэндвичеобразным размещением стальных листов образцов 1 и 3 в примере в разъемных штампах; фиг. 6 представляет график, показывающий для образцов 1 и 3 в примере взаимосвязь между температурой нагревания с твердостью в поперечном сечении (на фигуре показаны соответственно и) и с поглощенной энергией в испытании на удар (на фигуре соответственно показаны и ). Варианты осуществления изобретения Далее будут разъяснены химический состав и структура стали стального материала согласно настоящему изобретению. В нижеследующем разъяснении процент в отношении химического состава стали означает процент по массе.(1) Химический состав. С: 0,05-0,35%. Углерод (С) представляет собой важный элемент, который определяет прочность стального материала после закалочного упрочнения. Если содержание С составляет менее 0,05%, достаточная прочность после закалочного упрочнения не обеспечивается. Соответственно этому содержание С выдерживают на уровне по меньшей мере 0,05%. Предпочтительно оно составляет по меньшей мере 0,1% и более предпочтительно по меньшей мере 0,15%. Если содержание С превышает 0,35%, проявляется заметное ухудшение ударной вязкости и устойчивости к замедленному разрушению стального материала после закалочного упрочнения. В дополнение, проявляется заметное ухудшение формуемости стального материала перед закалочным упрочнением, которое нежелательно, когда проводят предварительное формование стального материала до обработки горячей штамповкой или горячей трехмерной гибкой и прямой закалкой. Соответственно этому содержание С выдерживают на уровне самое большее 0,35%. Предпочтительно оно составляет самое большее 0,30%.Si: не более 0,5%. Кремний (Si) в основном содержится как загрязняющая примесь, но он проявляет эффект повышения прокаливаемости стального материала, так что он может быть добавлен преднамеренно. Однако,если содержание Si превышает 0,5%, имеет место заметное повышение точки Ас 3 стали, и становится затруднительным снизить температуру нагревания во время закалочного упрочнения. Кроме того, заметно ухудшается способность стального материала подвергаться химической конверсионной обработке и пригодность к нанесению металлического покрытия, когда изготавливают оцинкованный стальной материал. Соответственно этому содержание Si выдерживают не выше 0,5%. Предпочтительно оно составляет не более 0,3%. Чтобы получить более выраженное вышеописанное действие Si, содержание Si предпочтительно составляет по меньшей мере 0,1%.Mn: 0,5-2,5%. Марганец (Mn) проявляет эффект снижения точки Ас 3 и повышения прокаливаемости стального материала. Если содержание Mn составляет менее 0,5%, то получить вышеуказанный эффект затруднительно. Соответственно этому содержание Mn должно составлять по меньшей мере 0,5%. Предпочтительно оно составляет по меньшей мере 1,0%. Если содержание Mn превышает 2,5%, проявляется заметное ухудшение формуемости стального материала перед закалочным упрочнением, которое нежелательно, когда стальной материал подвергают предварительному формованию до обработки горячей штамповкой или горячей трехмерной гибкой и прямой закалкой. Кроме того, становится более легким развитие полосчатой структуры вследствие сегрегации Mn, приводящее к заметному снижению ударной вязкости стального материала. Соответственно этому содержание Mn выдерживают на уровне не более 2,5%. Предпочтительно оно составляет не более 2,0%. Р: не более 0,03%. Фосфор (Р) содержится как загрязняющая примесь. Фосфор (Р) действует так, что ухудшается формуемость стального материала перед закалочным упрочнением, и имеет место ухудшение ударной вязкости стального материала после закалочного упрочнения. Соответственно этому содержание Р предпочтительно является настолько низким, насколько возможно, и должно составлять не более 0,03% в настоящем изобретении. Предпочтительно оно составляет не более 0,015%.S: не более 0, 01%. Сера (S) содержится как загрязняющая примесь. Сера (S) действует так, что ухудшается формуемость стального материала перед закалочным упрочнением и происходит ухудшение ударной вязкости стального материала после закалочного упрочнения. Соответственно этому содержание S предпочтительно является настолько низким, насколько возможно, и должно составлять не более 0,01% в настоящем изобретении. Предпочтительно оно составляет не более 0,005%. Растворимый Al: не более 0,1%. Алюминий (Al) в основном содержится как загрязняющая примесь, но он проявляет эффект повышения прочности стального материала вследствие раскисления, так что он может содержаться преднамеренно. Однако, если содержание растворимого Al превышает 0,1%, проявляется заметное повышение точки Ас 3 стали и становится затруднительным снизить температуру нагревания во время закалочного упрочнения. Соответственно этому содержание растворимого Al выдерживают не выше 0,1%. Предпочтительно оно составляет не более 0,05%. Чтобы получить более выраженное вышеописанное действиеAl, содержание растворимого Al предпочтительно выдерживают на уровне по меньшей мере 0,005%.N: не более 0,01%. Азот (N), который содержится как загрязняющая примесь, проявляет эффект ухудшения формуемости стального материала перед закалочным упрочнением. Соответственно этому содержание N предпочтительно является настолько низким, насколько возможно, и в настоящем изобретении должно составлять не более 0,01%. Предпочтительно оно составляет не более 0,005%. Следующие элементы являются необязательными элементами, которые могут содержаться в стальном материале согласно настоящему изобретению в зависимости от ситуации. В: 0-0,005%, Ti: 0-0,1%, Cr: 0-0,5%, Nb: 0-0,1%, Ni: 0-1,0% и Mo: 0-0,5%. В, Ti, Cr, Nb, Ni и Мо представляют собой необязательные элементы. Каждый из них проявляет действие, состоящее в повышении ударной вязкости и прокаливаемости стального материала. Соответственно этому в стальном материале согласно настоящему изобретению могут содержаться один или более элементов, выбранных из этой группы элементов. Однако, если содержание бора (В) превышает 0,005%, вышеописанный эффект насыщается и такое содержание В является неблагоприятным по соображениям стоимости. Соответственно этому, когда бор(В) присутствует, его содержание должно составлять не более 0,005%. Для достижения более явного вышеописанного действия бора (В) содержание В предпочтительно составляет по меньшей мере 0,0001%. Когда содержание Ti превышает 0,1%, он связывается с углеродом (С) в стали и образует большое количество TiC. В результате количество С, который содействует повышению прочности стального материала при закалочном упрочнении, сокращается, и иногда получить высокую прочность стального материала после закалочного упрочнения невозможно. Соответственно этому, когда Ti присутствует, его содержание должно составлять не более 0,1%. Для достижения более достоверного вышеописанного действия Ti содержание Ti предпочтительно составляет по меньшей мере 0,01%. При связывании с растворенным азотом (N) в стали с образованием TiN Ti действует так, что снижает количество растворенного N в стали и повышает формуемость стального материала перед закалочным упрочнением. В дополнение, по сравнению с бором (В) Ti предпочтительно связывается с растворенным N в стали, чем подавляет снижение количества растворенного бора (В), обусловленное образованием BN, так что вышеописанные эффекты бора (В) могут проявляться с большей определенностью. Соответственно этому Ti и В предпочтительно содержатся совместно. Когда содержание Cr превышает 0,5%, проявляется заметное ухудшение формуемости стального материала перед закалочным упрочнением, которое нежелательно, когда проводят предварительное формование стального материала перед горячей штамповкой или горячей трехмерной гибкой и прямой закалкой. Соответственно этому, когда Cr присутствует, его содержание должно составлять не более 0,5%. Для достижения более надежного вышеописанного действия содержание Cr предпочтительно составляет по меньшей мере 0,18%. Если содержание Nb превышает 0,1%, имеет место заметное ухудшение формуемости стального материала перед закалочным упрочнением, которое нежелательно, когда проводят предварительное формование стального материала перед горячей штамповкой или горячей трехмерной гибкой и прямой закалкой. Соответственно этому, когда Nb присутствует, его содержание должно составлять не более 0,1%. Для достижения более надежного вышеописанного действия содержание Nb предпочтительно составляет по меньшей мере 0,03%. Если содержание Ni превышает 1,0%, происходит заметное ухудшение формуемости стального материала перед закалочным упрочнением, которое нежелательно, когда стальной материал подвергают предварительному формованию перед горячей штамповкой или горячей трехмерной гибкой и прямой закалкой. Соответственно этому, когда Ni присутствует, его содержание должно составлять не более 1,0%. Для достижения более надежного вышеописанного действия содержание Ni предпочтительно составляет по меньшей мере 0,18%. Если содержание Мо превышает 0,5%, имеет место заметное ухудшение формуемости стального материала перед закалочным упрочнением, которое нежелательно, когда проводят предварительное формование стального материала перед горячей штамповкой или горячей трехмерной гибкой и прямой закалкой. Соответственно этому, когда Мо присутствует, его содержание должно составлять не более 0,5%. Для достижения более достоверного вышеописанного действия содержание Мо предпочтительно составляет по меньшей мере 0,03%.(2) Структура стали. Стальной материал согласно настоящему изобретению имеет структуру стали, в которой степень сфероидизации карбидов составляет 0,60-0,90. Численная плотность карбидов предпочтительно составляет по меньшей мере 0,50 карбида на 1 мкм 2 и численная доля (фракция) крупнозернистых карбидов с диаметром частиц по меньшей мере 0,5 мкм среди общего числа карбидов предпочтительно составляет не более 0,15. Здесь диаметр частиц, применяемый в этом контексте для определения формы карбидов, означает диаметр эквивалентной окружности, определенной по площади карбида, измеренной наблюдением поперечного шлифа стального материала. Карбидами, которые представляют интерес в настоящем изобретении, являются карбиды, имеющие диаметр частиц по меньшей мере 0,2 мкм. Такие карбиды включают карбиды, имеющие высокую долю металлических элементов, такие как цементит или М 23 С 6. Карбиды включают карбонитриды. Карбиды в стали наблюдаются при обследовании поперечного шлифа стального материала, который был подвергнут травлению пикралем (5%-ный раствор пикриновой кислоты в этаноле). Это обусловлено тем, что, по существу, все частицы, имеющие диаметр частиц по меньшей мере 0,2 мкм, которые выявляются при травлении пикралем, могут рассматриваться как карбиды. Карбиды, которые рассматриваются в настоящем изобретении, представляют собой карбиды, имеющие диаметр частиц по меньшей мере 0,2 мкм, чтобы надлежащим образом оценивать диаметр частиц,степень сфероидизации, численную плотность карбидов в стали и долю крупнозернистых карбидов в карбидах. Это обусловлено тем, что, если увеличение при наблюдении карбидов слишком мало, будут оцениваться только крупнозернистые карбиды, и невозможно правильно оценить число тонкодисперсных карбидов, которые быстро растворяются с образованием твердого раствора в стадии нагревания, и тем самым содействуют прокаливаемости стального материала. С другой стороны, если увеличение при наблюдении карбидов является слишком высоким, поле зрения сокращается, и оценивается только локальное состояние карбидов, тем самым делая невозможным надлежащую оценку действия карбидов на прокаливаемость всего стального материала. Соответственно этому при наблюдении карбидов пригодным является увеличение в 2000 раз, и при таких условиях нижний предел размера частиц карбидов, которые могут быть измерены с достаточной точностью, составляет 0,2 мкм. Поэтому объектом измерения сделаны карбиды с диаметром частиц по меньшей мере 0,2 мкм. Измерение диаметра частиц карбидов может быть проведено наблюдением поперечного шлифа стального материала с помощью сканирующего электронного микроскопа. Подходящее место наблюдения находится в точке посередине между поверхностью и центром стального материала, причем срединная точка имеет усредненные характеристики полученной термической обработки. А именно, если стальной материал представляет собой стальной лист, то предпочтительно наблюдать поперечный шлиф в положении на 1/4 толщины листа от поверхности в поперечном сечении стального листа. Степень сфероидизации, которая показывает форму карбидов, означает отношение числа карбидов,имеющих соотношение геометрических размеров не более 3, к числу карбидов, для которых было рассчитано соотношение геометрических размеров. Соотношение геометрических размеров карбидов рассчитывают для карбидов, которые наблюдались для измерения вышеописанного диаметра частиц. Соотношение геометрических размеров представляет собой отношение длины самой длинной оси, которая может быть получена в поперечном сечении наблюдаемого карбида, к длине оси, которая перпендикулярна самой длинной оси. Степень сфероидизации определяют наблюдением поперечного шлифа стального материала с помощью электронного микроскопа при 2000-кратном увеличении, и рассчитывают соотношение геометрических размеров карбидов. Число полей наблюдения предпочтительно составляет по меньшей мере 2. С позиции формуемости стального материала перед закалочным упрочнением остальная часть структуры стали иная, нежели карбиды, предпочтительно представляет собой главным образом феррит. Перлит, бейнит и мартенсит отпуска представляют собой структуры, составленные из карбидов и феррита. Поэтому структура стали, состоящая из карбидов и феррита, включает случай, в котором присутствует любая из этих структур. Структура стали также содержит включения, такие как MnS и TiN, которые неизбежно образуются в случае вышеописанного химического состава. Степень сфероидизации карбидов: 0,60-0,90. Как указано выше, легирующие элементы, образующие растворы замещения, такие как Mn, склонны легко концентрироваться в сфероидизированных карбидах. Карбиды, в которых сконцентрированы такие легирующие элементы, такие как Mn, проявляют замедленное растворение с образованием твердого раствора в стадии нагревания во время закалочного упрочнения, и если кратковременное нагревание проводят при низкой температуре, растворение карбидов с образованием твердого раствора становится недостаточным, и легко возникает проблема ненадлежащего закалочного упрочнения. Соответственно этому верхний предел степени сфероидизации карбидов устанавливают так, чтобы карбиды быстро растворялись с образованием твердого раствора, даже когда кратковременное нагревание проводят при низкой температуре, и стальной материал будет, несомненно, подвергнут достаточному закалочному упроч-7 022687 нению. В результате этого может быть стимулировано растворение карбидов с образованием твердого раствора в стадии нагревания во время закалочного упрочнения. Более конкретно, если степень сфероидизации карбидов превышает 0,90, растворение карбидов с образованием твердого раствора путем кратковременного нагревания при низкой температуре может стать недостаточным, и закалочное упрочнение может быть ненадлежащим. Соответственно этому степень сфероидизации карбидов поддерживают на уровне не более 0,90. Предпочтительно она составляет не более 0,87 и более предпочтительно не более 0,85. Как можно понять из того факта, что сфероидизацию (отжиг для сфероидизации) стального материала выдерживанием его в предварительно заданных высокотемпературных диапазонах традиционно проводили для сфероидизации карбидов и тем самым смягчения стального материала перед закалочным упрочнением, необходимо повышать степень сфероидизации карбидов до определенного уровня, чтобы улучшить формуемость стального материала перед закалочным упрочнением. Если степень сфероидизации карбидов составляет менее 0,60, то имеет место заметное ухудшение формуемости стального материала перед закалочным упрочнением, которое нежелательно, когда стальной материал подвергают обработке горячей штамповкой или горячей трехмерной гибкой и прямой закалкой. Соответственно этому степень сфероидизации карбидов должна составлять по меньшей мере 0,60. Предпочтительно она составляет по меньшей мере 0,63 и более предпочтительно она составляет по меньшей мере 0,65. Численная плотность карбидов: по меньшей мере 0,50 карбида на 1 мкм 2. Поведение структуры стали во время стадии нагревания в ходе закалочного упрочнения является следующим. Сначала развиваются зародыши аустенита, происходящие из карбидов, и затем зародыши аустенита растут до достижения полной аустенизации. Соответственно этому, если численная плотность карбидов, которые служат в качестве исходных точек для зародышей аустенита, возрастает, то дистанция роста аустенита, необходимая для завершения аустенизации, сокращается, и полная аустенизация может быть достигнута при более низкой температуре в течение более короткого промежутка времени. А именно, закалочное упрочнение происходит с большей надежностью, даже когда кратковременное нагревание выполняют при низкой температуре. При выдерживании численной плотности карбидов (тех, которые имеют диаметр частиц по меньшей мере 0,2 мкм) на уровне по меньшей мере 0,50 карбида на 1 мкм 2 может быть эффективно стимулирована полная аустенизация в стадии нагревания во время закалочного упрочнения. Соответственно этому численная плотность карбидов предпочтительно должна составлять по меньшей мере 0,50 карбида на 1 мкм 2. Численная плотность карбидов более предпочтительно составляет по меньшей мере 0,60 карбида на 1 мкм 2 и наиболее предпочтительно составляет по меньшей мере 0,70 карбида на 1 мкм 2. Численная доля в карбидах крупнозернистых карбидов, имеющих диаметр частиц по меньшей мере 0,5 мкм: не более 0,15. По сравнению с тонкодисперсными карбидами, крупнозернистые карбиды медленнее растворяются с образованием твердого раствора в стадии нагревания во время закалочного упрочнения. Соответственно этому, если численная доля крупнозернистых карбидов в карбидах снижается, стимулируется растворение карбидов с образованием твердого раствора во время стадии нагревания в ходе закалочного упрочнения, и закалочное упрочнение проводится с большей достоверностью даже кратковременным нагреванием при низкой температуре. Когда численная доля в карбидах крупнозернистых карбидов, имеющих диаметр частиц по меньшей мере 0,50 мкм, относительно общего числа карбидов (имеющих диаметр частиц по меньшей мере 0,2 мкм) составляет не более 0,15, можно эффективно стимулировать растворение карбидов с образованием твердого раствора в стадии нагревания во время закалочного упрочнения. Соответственно этому численная доля крупнозернистых карбидов, имеющих диаметр частиц по меньшей мере 0,5 мкм, в карбидах предпочтительно составляет не более 0,15. Эта численная доля крупнозернистых карбидов более предпочтительно составляет не более 0,14 и наиболее предпочтительно не более 0,13. Регулирование формы карбидов, как описано выше, может быть достигнуто экспериментальным определением условий горячей прокатки и условий отжига для получения желательной формы карбидов и корректированием этих условий. Например, в отношении условий горячей прокатки известно, что, если повышать температуру при намотке в рулон, то это способствует сфероидизации карбидов, снижает численную плотность карбидов и повышает численную долю крупнозернистых карбидов. На основе этих качественных тенденций можно экспериментально определить условия горячей прокатки для получения желательной формы карбидов. Что касается условий отжига, то известно, что, если снижать скорость охлаждения, то это содействует сфероидизации карбидов, снижает численную плотность карбидов и повышает численную долю крупнозернистых карбидов. Основываясь на этих качественных тенденциях,можно экспериментально определить условия отжига для получения желательной формы карбидов.(3) Условия изготовления. Нет необходимости как-то особенно ограничивать условия изготовления стального материала согласно настоящему изобретению (материала перед закалочным упрочнением) в такой мере, насколько удовлетворяются вышеописанные химический состав и структура стали. Ниже будут разъяснены предпочтительные условия изготовления для ситуации, в которой стальной материал согласно настоящему изобретению представляет собой стальной лист. Сталь, имеющую вышеописанный химический состав, плавят традиционным путем, затем формируют в сляб непрерывным литьем или в биллет литьем и последующей прокаткой на блюминге. С позиции производительности предпочтительным является применение метода непрерывного литья. Когда используют метод непрерывного литья, предпочтительна скорость литья менее 2,0 м/мин,поскольку этим эффективно подавляется центральная сегрегация, или V-сегрегация Mn. Скорость литья предпочтительно составляет по меньшей мере 1,2 м/мин, поскольку можно поддерживать хорошую чистоту поверхности отливки наряду с хорошей производительностью. Затем полученный сляб или биллет подвергают горячей прокатке. Из соображений более равномерного формирования карбидов условия горячей прокатки предпочтительно включают начало горячей прокатки в температурном диапазоне по меньшей мере 1000 и не более 1300 С, с температурой при завершении горячей прокатки по меньшей мере 850 С. С позиции формуемости температуру при намотке в рулон предпочтительно поддерживают на верхнем пределе диапазона, но если она является слишком высокой, снижается предел текучести вследствие образования окалины. Предпочтительная температура намотки рулона составляет по меньшей мере 500 и не более 650 С. Горячекатаный стальной лист, полученный горячей прокаткой, подвергают обработке для удаления окалины травлением или тому подобным. Стальной материал согласно настоящему изобретению может представлять собой горячекатаный стальной лист, который не был подвергнут отжигу, горячекатаный отожженный стальной лист, который был подвергнут отжигу, холоднокатаный стальной лист, полученный в состоянии после холодной прокатки выполнением холодной прокатки вышеописанного горячекатаного листа или горячекатаного отожженного стального листа, или холоднокатаный отожженный стальной лист, полученный отжигом вышеописанного холоднокатаного стального листа. Способ может быть надлежащим образом выбран в соответствии с требуемой точностью толщины листового продукта или тому подобным. Соответственно этому горячекатаный стальной лист, который был подвергнут обработке для удаления окалины, при необходимости может быть подвергнут отжигу для получения горячекатаного отожженного стального листа. Горячекатаный стальной лист или горячекатаный отожженный стальной лист при необходимости может быть подвергнут холодной прокатке для получения холоднокатаного стального листа. Холоднокатаный стальной лист при необходимости может быть подвергнут отжигу для получения холоднокатаного отожженного стального листа. Когда стальной материал, подвергаемый холодной прокатке, является твердым, перед холодной прокаткой предпочтительно проводят отжиг для повышения формуемости стального материала, подвергаемого холодной прокатке. Карбиды являются твердыми, и их форма не претерпевает изменения во время холодной прокатки. Соответственно этому форма карбидов (диаметр частиц, степень сфероидизации, численная плотность,численная доля крупнозернистых карбидов или тому подобные) в холоднокатаном стальном листе в состоянии сразу после прокатки, по существу, является такой же, как форма карбидов в стальном листе,предназначенном для выполнения холодной прокатки. Таким образом, регулирование формы карбидов в холоднокатаном стальном листе в состоянии сразу после холодной прокатки может быть проведено путем регулирования формы карбидов, присутствующих в стальном листе, который должен быть подвергнут холодной прокатке. А именно, когда холодную прокатку проводят на горячекатаном стальном листе,который не был подвергнут отжигу, можно регулировать форму карбидов в холоднокатаном стальном листе регулированием условий горячей прокатки для контроля формы карбидов, присутствующих в горячекатаном стальном листе. Когда холодную прокатку проводят на горячекатаном стальном листе, который был подвергнут отжигу, можно регулировать форму карбидов в холоднокатаном стальном листе регулированием формы карбидов, присутствующих в горячекатаном отожженном стальном листе, путем регулирования условий отжига, или же как условий горячей прокатки, так и условий отжига. Холодная прокатка может быть проведена традиционным путем. Из соображений обеспечения хорошей плоскостности листа сокращение толщины за проход прокатки предпочтительно составляет по меньшей мере 30%. Во избежание чрезмерной нагрузки сокращение толщины за проход прокатки предпочтительно составляет не более 80%. Когда проводят отжиг горячекатаного стального листа или холоднокатаного стального листа, отжиг выполняют после такой обработки, как обезжиривание, которое проводят, если необходимо, традиционным путем. В это время предпочтительно проводят томление (изотермическое нагревание) при температуре в области одиночной аустенитной фазы. Путем нагревания в таком режиме подавляют образование полосчатой структуры, и структура листа может быть сделана более однородной, приводя к дополнительному повышению прокаливаемости стального листа. После томления средняя скорость охлаждения от точки Ar3 до температуры на 200 С выше Ms-точки (Ms-точка + 200 С) предпочтительно составляет по меньшей мере 20 С в 1 с. Путем охлаждения в таком режиме подавляют образование неоднородной структуры стали во время охлаждения после томления, и может быть дополнительно повышена прокаливаемость стального листа. Из соображений получения однородной структуры стали и с позиции производительности отжиг предпочтительно выполняют на линии непрерывного отжига. В этом случае отжиг предпочтительно проводят путем томления в температурном диапазоне, по меньшей мере, от точки Ас 3 до температуры не выше (точка Ас 3 + 100 С) в течение периода времени по меньшей мере от 1 с до не более 1000 с, с последующим выдерживанием в температурном диапазоне от по меньшей мере 250 до не более 550 С в течение от по меньшей мере 1 до не более 30 мин. Как очевидно квалифицированному специалисту в этой области технологии, условия горячей прокатки и условия отжига для получения структуры стали, которая удовлетворяет требованиям в отношении формы карбидов согласно настоящему изобретению, варьируют в зависимости от химического состава стального материала. Как указано выше, они могут быть определены экспериментальным путем. Когда поверхность стального листа подвергают цинкованию (нанесению металлического покрытия на основе цинка), то из соображений производительности предпочтительно проведение погружного горячего цинкования с использованием производственной линии непрерывного погружного горячего цинкования. В этом случае отжиг может быть проведен в производственной линии непрерывного погружного горячего цинкования перед погружным горячим цинкованием, или томление может быть настроено на низкий уровень температуры, и сразу может быть проведено цинкование без выполнения отжига. Также возможно проведение термической обработки для легирования после погружного горячего цинкования для получения отожженного и оцинкованного стального листа. Цинкование также может быть проведено нанесением электролитического покрытия. Некоторыми примерами цинкования являются погружное горячее цинкование, гальванизационный отжиг, нанесение электролитического цинкового покрытия, погружное горячее покрытие цинкалюминиевым сплавом, электрогальванизация никель-цинковым сплавом и электрогальванизация железо-цинковым сплавом. На удельный вес покрытия нет особенного ограничения, и он может иметь общеупотребительное значение. Цинкование может быть проведено по меньшей мере на части поверхности стального материала, но в случае стального листа его обычно проводят полностью на одной или обеих поверхностях листа. Стальной лист в настоящем изобретении, который изготовлен, как описано выше, имеет высокую прокаливаемость, и он может быть достаточно упрочнен для обеспечения высокой прочности путем закалочного упрочнения при кратковременном нагревании и/или при низкой температуре. Соответственно этому (i) при необходимости он может быть разделен на мелкие куски и подвергнут горячей штамповке для получения формованных изделий или (ii) он может быть подвергнут надлежащей обработке для получения материала для горячей трехмерной гибки и прямой закалки, и горячая трехмерная гибка и прямая закалка могут быть проведены для получения формованного изделия. В альтернативном варианте он может быть просто подвергнут закалочному упрочнению без переработки. Обработка горячей штамповкой и горячей трехмерной гибкой и прямой закалкой может быть проведена известными способами. Для достижения эффектов настоящего изобретения стадию нагревания предпочтительно проводят в течение короткого периода времени. Поэтому для быстрого нагревания предпочтительно применяют высокочастотный нагрев или резистивный нагрев. Приведенное выше разъяснение рассчитано на ситуацию, в которой стальной материал перед закалочным упрочнением представляет собой стальной лист. Однако стальной материал не ограничивается стальным листом, и может представлять собой трубу, пруток, профиль или тому подобное. Это может быть удлиненная заготовка или это может быть отрезок материала, который был отрезан от удлиненной заготовки и, необязательно, подвергнут предварительному формованию. Пример 1. После непрерывного литья каждый сляб из сталей A-I, имеющих химические составы, показанные в табл. 1, загрузили в нагревательную печь, нагрели в ней, и после извлечения из нагревательной печи каждый из них был подвергнут горячей прокатке с начальной температурой 1150 С и конечной температурой 870 С, охлажден со средней скоростью охлаждения 20-1000 С в 1 с и намотан в рулон при температуре 450-600 С для получения горячекатаных стальных листов, имеющих толщину 3,6 мм. Полученные горячекатаные стальные листы были обработаны для удаления окалины травлением. Стальные листы,полученные этим путем, будут называться горячекатаными материалами. Часть горячекатаных стальных листов после удаления окалины подвергли холодной прокатке с сокращением толщины за проход прокатки на 50% для получения холоднокатаных стальных листов. Эти стальные листы будут называться полностью упрочненными материалами. Часть полученных холоднокатаных стальных листов выдержали в течение 20 ч при температуре 650 С в нагревательной печи и затем охладили на воздухе до комнатной температуры. Эти стальные листы будут называться нагретыми в термической печи материалами. Отдельную часть холоднокатаных стальных листов подвергли термической обработке с использованием симулятора непрерывного отжига, в котором они могли быть выдержаны для томления в течение 1 мин при температуре 750-900 С, затем охлаждены до диапазона от 650 до 450 С со средней скоростью охлаждения 10-200 С в 1 с, затем выдержаны в течение 4 мин при температуре 420 С и охлаждены до комнатной температуры. Эти стальные листы будут называться непрерывно отожженными материалами. Подчеркнутые цифры выходят за пределы определенного здесь диапазона. Стальные листы образцов 1-22, показанные в табл. 2 (толщина листа 1,8 мм), были изготовлены вышеописанным способом. Для одного и того же типа стали среди образцов варьировали условия горячей прокатки и условия отжига (в случае непрерывно отожженных материалов). Горячекатаные материалы были подвергнуты шлифованию обеих поверхностей горячекатаных стальных листов для уменьшения их толщины от 3,6 до 1,8 мм, чтобы иметь такую же толщину листа, как у прочих образцов. Стальные листы образцов 1-22 были подвергнуты погружному горячему цинкованию с последующей легирующей обработкой в температурном диапазоне не выше точки A1, чтобы не изменилась бы форма карбидов, для получения отожженных и оцинкованных стальных листов образцов 1-22. Структуру поперечного шлифа стальных листов образцов 1-22, которые были получены вышеописанным путем, наблюдали на четырех полях наблюдения для каждого листа при 2000-кратном увеличении с использованием сканирующего электронного микроскопа, для определения степени сфероидизации, численной плотности карбидов и численной доли крупнозернистых карбидов. Поле наблюдения находилось на глубине 0,45 мм от поверхности стального листа, эта величина соответствовала 1/4 толщины листа, составляющей 1,8 мм. Частицы карбидов наблюдались после травления пикралем (5%-ный раствор пикриновой кислоты в этаноле). Общее число карбидов, наблюдаемых в каждом поле наблюдения, составляло 300-3000. Что касается перлита, каждый цементит, содержащийся в перлитных ламелях,считали как один карбид. С использованием симулятора закалочного упрочнения каждый стальной лист образцов 1-22 подвергли закалочному упрочнению нагреванием до температур в диапазоне 600-1100 С со скоростью нагревания 500 С в 1 с, и немедленно после того, как была достигнута предварительно заданная температура, выполнили охлаждение водой. После закалочного упрочнения измерили твердость по Виккерсу(Hv). Как показано на фиг. 1, измерили самую низшую температуру, которая давала максимальную твердость (наиболее низкая температура закалочного упрочнения). Каждый из отожженных и оцинкованных стальных листов образцов 1-22 подвергли закалочному упрочнению нагреванием до наиболее низкой температуры закалочного упрочнения со скоростью нагревания 500 С в 1 с, с последующим охлаждением водой после того, как была достигнута наиболее низкая температура закалочного упрочнения. На основании того явления, что окисление цинка сопровождается образованием оксида цинка, который имеет белый цвет, визуально наблюдали степень белизны поверхности отожженного и оцинкованного стального материала для оценки уровня, до которого сохранялось цинковое покрытие. Качество покрытия оценивали согласно следующему стандарту: А) почти полная сохранность; В) приемлемый уровень; С) сохранение малого количества;D) почти ничего не сохранилось. Отдельно, с использованием симулятора закалочного упрочнения, каждый стальной лист образцов 1-22 нагрели со скоростью нагревания 500 С в 1 с до вышеописанной наиболее низкой температуры закалочного упрочнения, выдержали при этой температуре в течение 3 с и затем охладили водой. Измерили толщину окалины, которая образовалась на поверхности стальных листов. В дополнение, каждый из стальных листов образцов 1-22 подвергли формованию путем горячей штамповки с выдерживанием в течение 4 мин при температуре 900 С и последующим сэндвичеобразным размещением между парой плоских штампов. Провели испытание на разрыв с использованием образцаJIS5 (согласно Японскому Промышленному Стандарту) для испытания на разрыв, взятого из каждого стального листа, подвергнутого формованию путем горячей штамповки, для определения предела прочности на разрыв. В дополнение, провели усталостное испытание с плоским изгибом (R=-1) на образце для испытаний на усталость, как показано на фиг. 2, который был взят из каждого стального листа, подвергнутого формованию путем горячей штамповки, и построили S-N-кривую, как показано на фиг. 3, для определения предела усталости. Рассчитали предельный коэффициент усталости (отношение предела усталости к пределу прочности при растяжении). Отдельно из стальных листов образцов 1-22 были отобраны испытательные образцы с размерами 200 мм длиной и 50 мм шириной, и они были подвергнуты обработке горячей штамповкой с выдерживанием в течение 1,5 мин при температуре 900 С и последующим сэндвичеобразным размещением между разъемными штампами, как показано на фиг. 4. В это время габарит штампа сделали равным 70 мм, и верхний и нижний зазоры составляли 0,2 мм каждый. Доведение до нижней мертвой точки провели за 60 с с прижимающей нагрузкой 49 кН. Как показано на фиг. 5, измерили твердость (Hv) в поперечном сечении стальных листов, которые были получены этой обработкой горячей штамповкой, и определили отношение наименьшей твердости в центре габарита штампа к средней твердости на участках плотного контакта, иных, нежели в зазорах (отношение твердостей при испытании в габарите штампа). С использованием симулятора закалочного упрочнения каждый стальной лист образцов 1-22 подвергли закалочному упрочнению нагреванием до температур в диапазоне 600-1100 С со скоростью нагревания 500 С в 1 с, и после того, как они достигли предварительно заданной температуры, выполнили охлаждение водой. Как показано на фиг. 6, определили наиболее низкую температуру достижения максимальной твердости (наиболее низкая температур закалочного упрочнения) и температуру достижения максимальной поглощенной энергии и определили разность Т между температурой достижения наивысшей поглощенной энергии и наиболее низкой температурой достижения наибольшей твердости(показано символом Т для образца 3 на фиг. 6). Поглощенную энергию определяли шлифованием испытательных образцов, полученных из стальных листов, до толщины 1,4 мм, наслоением трех испытательных образцов друг поверх друга и проведением теста Шарпи с V-образным 2-мм надрезом на наслоенных испытательных образцах при комнатной температуре. Чем меньше Т, тем более предпочтительно. Это обусловлено тем, что меньшее значение Т показывает, что достаточно высокая ударная вязкость может быть получена закалочным упрочнением при более низкой температуре, которая является более близкой к наиболее низкой температуре закалочного упрочнения. Результаты вышеуказанных измерений показаны в табл. 2. Таблица 2 Подчеркнутые цифры выходят за пределы определенного здесь диапазона. Как показано в табл. 1 и 2 и на фиг. 1, 3, 5 и 6, стальные листы соответствующих изобретению примеров имеют наиболее низкую температуру закалочного упрочнения, которая является более низкой, чем температура стальных листов сравнительных примеров для тех же типов стали, показывая, что высокая твердость может быть получена даже кратковременным нагреванием при низкой температуре. В дополнение, для оцинкованных стальных листов, даже если нагревание проводят при наиболее низкой температуре закалочного упрочнения, может быть сохранено значительное количество покровного слоя. Для не имеющих металлического покрытия стальных листов, даже если нагревание проводят при наиболее низкой температуре закалочного упрочнения, может быть получено низкое значение толщины окалины не более 5 мкм. Предельный коэффициент усталости в обработке горячей штамповкой имеет высокое значение по меньшей мере 0,35 и отношение твердостей при испытании в габарите штампа также имеет высокое значение по меньшей мере 0,65. Т имеет низкое значение на уровне 35 С или менее. ФОРМУЛА ИЗОБРЕТЕНИЯ 1. Сталь, имеющая химический состав, включающий, мас.%: С - 0,05-0,35, Si - не более 0,5, Mn 0,5-2,5, Р - не более 0,03, S - не более 0,01, растворимый Al - не более 0,1, N - не более 0,01, В - 0-0,005,Ti - 0-0,1, Cr - 0-0,5, Nb - 0-0,1, Ni - 0-1,0 и Mo - 0-0,5%, и которая имеет структуру, содержащую карбиды, причем степень сфероидизации карбидов составляет 0,60-0,90, а численная плотность карбидов составляет по меньшей мере 0,50 карбида на 1 мкм 2. 2. Сталь по п.1, в которой численная доля крупнозернистых карбидов, имеющих диаметр частиц по меньшей мере 0,5 мкм, в карбидах составляет не более 0,15. 3. Сталь по любому из пп.1, 2, в которой химический состав содержит по меньшей мере один элемент, выбранный из группы, состоящей из В - 0,0001-0,005%, Ti - 0,01-0,1%, Cr - 0,18-0,5%, Nb - 0,030,1%, Ni - 0,18-1,0% и Mo - 0,03-0,5%. 4. Сталь по любому из пп.1-3, имеющая слой покрытия на основе цинка по меньшей мере на части ее поверхности. 5. Термообработанная сталь, полученная из стали по любому из пп.1-4, которая была подвергнута обработке горячей штамповкой. 6. Термообработанная сталь, полученная из стали по любому из пп.1-4, которая была подвергнута горячей трехмерной гибке и прямой закалке. 7. Способ получения термообработанной стали, включающий стадию обработки горячей штамповкой стали по любому из пп.1-4. 8. Способ получения термообработанной стали, включающий стадию горячей трехмерной гибки и прямой закалки стали по любому из пп.1-4.
МПК / Метки
МПК: C22C 38/00, C22C 38/58
Метки: него, получения, базовый, термообработанный, материал, стальной, способ
Код ссылки
<a href="https://eas.patents.su/15-22687-termoobrabotannyjj-stalnojj-material-sposob-ego-polucheniya-i-bazovyjj-stalnojj-material-dlya-nego.html" rel="bookmark" title="База патентов Евразийского Союза">Термообработанный стальной материал, способ его получения и базовый стальной материал для него</a>
Предыдущий патент: Зонд для определения границ между веществами
Следующий патент: Газовый клапан для двухконтурной горелки
Случайный патент: Преобразовательное устройство, предназначенное для использования при каротаже