Способ извлечения углеводородных соединений и устройство для извлечения углеводородов из газообразных побочных продуктов
Формула / Реферат
1. Способ извлечения углеводородных соединений из газообразных побочных продуктов, образованных в реакции синтеза Фишера-Тропша, заключающийся в том, что
абсорбируют легкие углеводородные соединения и газообразный диоксид углерода из указанных газообразных побочных продуктов с использованием абсорбирующего растворителя, включающего жидкие углеводородные соединения и абсорбент газообразного диоксида углерода;
разделяют абсорбирующий растворитель, который абсорбировал легкие углеводородные соединения и газообразный диоксид углерода, на жидкие углеводородные соединения и абсорбент для газообразного диоксида углерода;
нагревают отделенные жидкие углеводородные соединения с извлечением легких углеводородных соединений из отделенных жидких углеводородных соединений;
нагревают отделенный абсорбент газообразного диоксида углерода с десорбцией газообразного диоксида углерода из отделенного абсорбента газообразного диоксида углерода;
повторно используют газообразные побочные продукты, из которых абсорбированы легкие углеводородные соединения и газообразный диоксид углерода, в качестве газообразного сырья для реакции синтеза Фишера-Тропша.
2. Способ по п.1, где абсорбирующий растворитель содержит амины как компонент абсорбента для газообразного диоксида углерода.
3. Способ по п.1 или 2, где температура кипения жидких углеводородных соединений, содержащихся в абсорбирующем растворителе, лежит в температурном интервале от 200°С или выше до 360°С или ниже.
4. Способ по любому из пп.1-3, где отделенный абсорбент для газообразного диоксида углерода нагревают при температуре 100°С или выше и 150°С или ниже и отделенные жидкие углеводородные соединения нагревают при температуре 100°С или выше и 200°С или ниже.
5. Способ по любому из пп.1-4, где абсорбцию легких углеводородных соединений и газообразного диоксида углерода в газообразных побочных продуктах абсорбирующим растворителем осуществляют после смешивания газообразных побочных продуктов и газообразного сырья для реакции синтеза Фишера-Тропша.
6. Способ по любому из пп.1-5, где абсорбирующий растворитель, используемый для абсорбции легких углеводородных соединений и газообразного диоксида углерода, содержит абсорбент газообразного диоксида углерода, из которого десорбирован газообразный диоксид углерода при нагревании, и жидкие углеводородные соединения, из которых извлечены легкие углеводородные соединения нагреванием.
7. Установка для реализации способа по п.1, содержащая
абсорбер, который позволяет осуществить абсорбцию растворителя, включающего абсорбент для газообразного диоксида углерода и жидкие углеводородные соединения с абсорбцией газообразного диоксида углерода и легких углеводородных соединений из газообразных побочных продуктов;
сепаратор, который разделяет абсорбирующий растворитель, включающий газообразный диоксид углерода и легкие углеводородные соединения, на абсорбент для газообразного диоксида углерода и жидкие углеводородные соединения;
устройство десорбционной обработки газообразного диоксида углерода, в котором протекает десорбция газообразного диоксида углерода из отделенного абсорбента для газообразного диоксида углерода;
устройство извлечения легких углеводородов, в котором протекает извлечение легких углеводородных соединений из отделенных жидких углеводородных соединений и
линию ввода газообразных побочных продуктов, которая позволяет подавать газообразные побочные продукты, из которых абсорбированы легкие углеводородные соединения и газообразный диоксид углерода, в реактор синтеза Фишера-Тропша.
8. Установка по п.7, дополнительно включающая циркуляционную линию, которая позволяет направить на рецикл в абсорбер абсорбент для газообразного диоксида углерода, из которого десорбирован газообразный диоксид углерода, и жидкие углеводородные соединения, из которых извлечены легкие углеводородные соединения.
9. Установка по п.7 или 8, где абсорбером является поглотительная башня для газообразного диоксида углерода, в которой абсорбируется газообразный диоксид углерода из газообразного сырья, вводимого в реактор синтеза Фишера-Тропша.
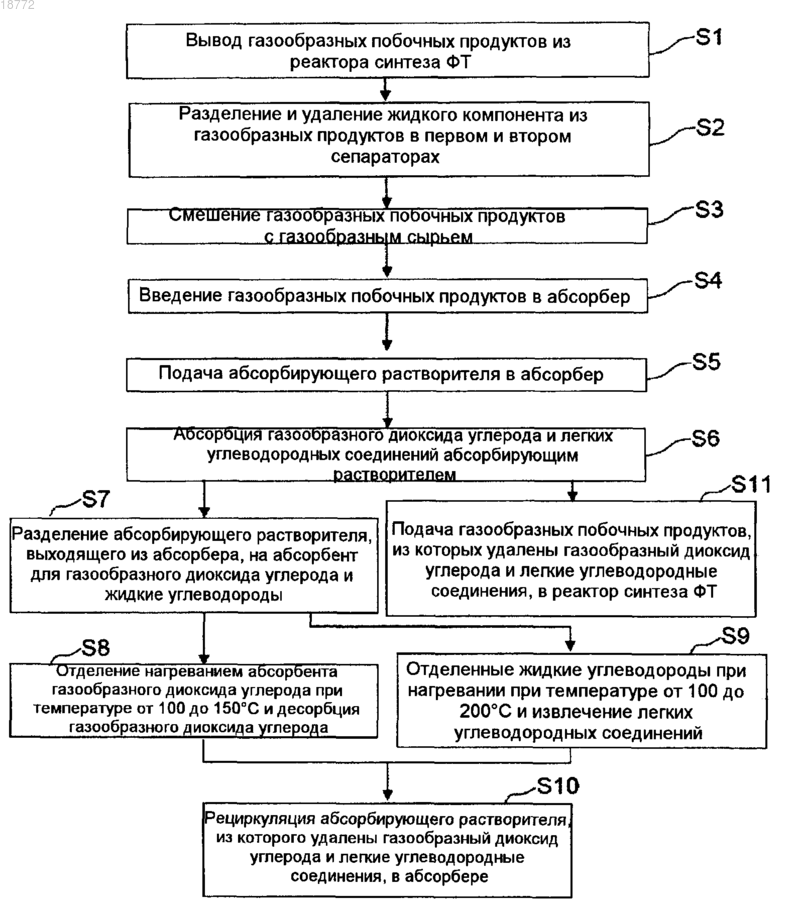
Текст
СПОСОБ ИЗВЛЕЧЕНИЯ УГЛЕВОДОРОДНЫХ СОЕДИНЕНИЙ И УСТРОЙСТВО ДЛЯ ИЗВЛЕЧЕНИЯ УГЛЕВОДОРОДОВ ИЗ ГАЗООБРАЗНЫХ ПОБОЧНЫХ ПРОДУКТОВ Предложен способ извлечения углеводородных соединений из газообразных побочных продуктов, образованных в реакции синтеза Фишера-Тропша. Способ включает абсорбцию легких углеводородных соединений и газообразного диоксида углерода из газообразных побочных продуктов с использованием абсорбирующего растворителя, включающего жидкие углеводородные соединения и абсорбент газообразного диоксида углерода, разделение абсорбирующего растворителя, который абсорбировал легкие углеводородные соединения и газообразный диоксид углерода, на жидкие углеводородные соединения и абсорбент для газообразного диоксида углерода; нагревание отделенных жидких углеводородных соединений с извлечением легких углеводородных соединений из отделенных жидких углеводородных соединений; нагревание отделенного абсорбента газообразного диоксида углерода с десорбцией газообразного диоксида углерода из отделенного абсорбента газообразного диоксида углерода и повторное использование газообразных побочных продуктов, из которых абсорбированы легкие углеводородные соединения и газообразный диоксид углерода, в качестве газообразного сырья для реакции синтеза Фишера-Тропша.(71)(73) Заявитель и патентовладелец: ДЖЭПЭН ОЙЛ, ГЭЗ ЭНД МЕТАЛЗ НЭШНЛ КОРПОРЕЙШН; ИНПЕКС КОРПОРЕЙШН; ДжейЭкс НИППОН ОЙЛ ЭНД ЭНЕРДЖИ КОРПОРЕЙШН; ДЖАПАН ПЕТРОЛЕУМ ЭКСПЛОРЕЙШН КО., ЛТД.; КОСМО ОЙЛ КО., ЛТД.; НИППОН СТИЛ ИНДЖИНИРИНГ КО., ЛТД. (JP) Область техники, к которой относится изобретение Изобретение относится к способу извлечения углеводородных соединений и к аппарату для извлечения углеводородов, который обеспечивает извлечение углеводородных соединений из газообразных побочных продуктов, образованных в процессе синтеза жидких углеводородных соединений по реакции синтеза Фишера-Тропша. Испрашивается приоритет патентной заявки Японии 2009-046151, поданной 27 февраля 2009 г.,содержание которой полностью включено в настоящий документ в качестве ссылки. Уровень техники Одним из методов синтеза жидких топлив из природного газа является недавно разработанный метод GLT (Gas To Liquids метод синтеза жидкого топлива) риформинга природного газа для получения синтез-газа, содержащего газообразный оксид углерода (СО) и газообразный водород (Н 2) в качестве основных компонентов, получение углеводородных соединений (ФТ - синтез углеводородов) с использованием данного синтез-газа в качестве газообразного сырья по реакции синтеза Фишера-Тропша (далее по тексту называемой "реакцией ФТ") и последующее гидрирование и фракционная перегонка углеводородных соединений с получением жидких топливных продуктов, таких как нафта (сырой бензин), керосин, газойль и парафин. Поскольку жидкие топливные продукты с использованием углеводородов синтеза ФТ в качестве сырья имеют высокое содержание парафинов и практически не включают серосодержащие компоненты,например, как показано в патентном документе 1, жидкие топливные продукты привлекают внимание как топлива, не загрязняющие окружающую среду. Тем не менее, в реакторе синтеза ФТ, в котором протекает реакция синтеза ФТ, тяжелые углеводороды синтеза ФТ (тяжелые углеводороды ФТ) с относительно большим числом атомов углерода вытекают в виде жидкости из нижней части реактора синтеза ФТ. Кроме того, происходит вынужденное образование легких углеводородов синтеза ФТ с относительно низким числом атомов углерода. Легкие углеводороды синтеза ФТ выходят в виде газообразных побочных продуктов наряду с непрореагировавшим газообразным сырьем из верхней части реактора синтеза ФТ. Газообразные побочные продукты включают коммерчески доступные углеводородные соединения,число атомов углерода которых составляет 3 или более (далее по тексту называемые "легкими углеводородными соединениями"), наряду с диоксидом углерода, паром, непрореагировавшим газообразным сырьем (газообразный оксид углерода и газообразный водород) и углеводородными соединениями с числом атомов углерода 2 или меньше. Таким образом, если содержание легких углеводородных соединений увеличивается в газообразных побочных продуктах, эффективность производства жидких топливных продуктов будет снижаться. Традиционно газообразные побочные продукты охлаждают до сжижения легких углеводородных соединений, а затем легкие углеводородные соединения отделяют от других газообразных компонентов в газожидкостном сепараторе. Кроме того, в следующем патентном документе 2 предложен способ извлечения легких углеводородных соединений, содержащихся в обогащенном углеводородами ФТ сбрасываемом газе, путем абсорбции в конденсате ФТ в момент охлаждения. Список цитирований. Патентный документ 1: публикация не прошедшей экспертизу патентной заявки Японии 2004323626. Патентный документ 2: опубликованный японский перевод 2008-506817 публикации международного патента РСТ. Краткое изложение сущности изобретения При этом в способе, раскрытом в патентном документе 2, диоксид углерода нельзя удалить из газообразных побочных продуктов. По этой причине, когда газообразные побочные продукты повторно используют в качестве сырья для реакции синтеза ФТ, газообразный диоксид углерода может сконцентрироваться в реакторе синтеза ФТ, и, следовательно, эффективность реакции синтеза ФТ может снизиться. С другой стороны, охлаждая газообразные побочные продукты в вышеупомянутом газожидкостном сепараторе до приблизительно 10 С, можно обеспечить сжижение значительного количества легких углеводородных соединений и отделить легкие углеводородные соединения от других газообразных компонентов. Однако необходимо обеспечить дополнительный охлаждающий теплообменник, и,следовательно, устройство производственной установки усложнится. В результате этого себестоимость жидких топливных продуктов повысится. Настоящее изобретение создано в свете вышеупомянутых обстоятельств, и задача его заключается в разработке способа извлечения углеводородных соединений и аппарата для извлечения углеводородных соединений, способного эффективно извлекать легкие углеводородные соединения из газообразных побочных продуктов, и улучшать эффективность производства жидких топливных продуктов. Чтобы решить вышеуказанную проблему и достичь данной цели, настоящее изобретение предлагает следующие способы и устройства, т.е. способ извлечения углеводородных соединений из газообразных побочных продуктов, образованных в реакции синтеза Фишера-Тропша. Способ включает абсорбцию легких углеводородных соединений и газообразного диоксида углерода из газообразных побочных продуктов при использовании абсорбционного растворителя, включающего жидкие углеводородные соединения, и абсорбента для диоксида углерода, разделение абсорбционного растворителя, который абсорбировал легкие углеводородные соединения, и газообразного диоксида углерода на жидкие углеводородные соединения и абсорбент для газообразного диоксида углерода, нагревание отделенных легких углеводородных соединений с извлечением легких углеводородных соединений из отделенных жидких углеводородных соединений, нагревание абсорбента для газообразного диоксида углерода с десорбцией газообразного диоксида углерода из отделенного абсорбента для газообразного диоксида углерода и повторное использование газообразных побочных продуктов, из которых абсорбированы легкие углеводородные соединения и газообразный диоксид углерода, в качестве сырья для реакции синтеза Фишера-Тропша. В способе извлечения углеводородных соединений по настоящему изобретению легкие углеводородные соединения и газообразный диоксид углерода, входящие в газообразные побочные продукты,могут быть абсорбированы абсорбционным растворителем, включающим жидкие углеводородные соединения, и абсорбентом для газообразного диоксида углерода. Затем после отделения абсорбирующего растворителя от жидких углеводородных соединений и абсорбента газообразного диоксида углерода отделенные жидкие углеводородные соединения и абсорбент газообразного диоксида углерода нагревают до заранее заданных температур соответственно так, что газообразный диоксид углерода может быть десорбирован из абсорбента для газообразного диоксида углерода, и легкие углеводородные соединения могут быть извлечены из жидких углеводородных соединений. Кроме того, в способе извлечения углеводородных соединений согласно настоящему изобретению оборудование узла удаления СО 2 в производственной установке синтеза газа на промышленном предприятии по производству GLT может быть использовано само по себе. В данном случае нет необходимости устанавливать новое оборудование. Следовательно, легкие углеводородные соединения могут быть эффективно извлечены из газообразных побочных продуктов без использования дополнительного узла охлаждения и т.п. Кроме того, поскольку газообразный диоксид углерода удаляют из газообразных побочных продуктов, то можно повторно использовать газообразные побочные продукты как газообразное сырье для реакции синтеза ФТ, одновременно предотвращая концентрирование газообразного диоксида углерода в реакторе синтеза ФТ. Здесь, абсорбирующий растворитель может содержать амины как компонент абсорбента для газообразного диоксида углерода. В данном случае газообразный диоксид кремния, входящий в газообразные побочные продукты,может быть эффективно поглощен абсорбционным растворителем. Кроме того, газообразный диоксид углерода может быть десорбирован при нагревании абсорбента для диоксида углерода, отделенного от абсорбционного растворителя, который уже абсорбировал диоксид углерода, и легких углеводородных соединений. Кроме того, температура кипения абсорбента для газообразного диоксида углерода может составлять 200 С или выше. Кроме того, температура кипения жидких углеводородных соединений, содержащихся в абсорбционном растворителе, может лежать в температурном интервале от 200 С или выше и 360 С или ниже. В данном случае, когда жидкие углеводородные соединения, отделенные от абсорбционного растворителя, который поглотил диоксид углерода, и легких углеводородных соединений, нагревают до температуры ниже 200 С, испарение самих жидких углеводородных соединений может быть подавлено. Таким образом, жидкие углеводородные соединения могут быть использованы повторно. Кроме того, в сравнении со случаем использования углеводородных соединений с температурой кипения выше 360 С,абсорбирующий растворитель, включающий вышеназванные жидкие углеводородные соединения, более трудно заморозить даже при относительно низкой температуре. Затем абсорбирующий растворитель может сохранять текучесть. Кроме того, отделенный абсорбент для газообразного диоксида углерода можно нагревать при температуре 100 С или выше и 150 С или ниже, и отделенные жидкие углеводородные соединения можно нагревать при температуре 100 С или выше и 200 С или ниже. В данном случае, поскольку отделенный абсорбент для газообразного диоксида кремния нагревают при температуре 100 С или выше, газообразный диоксид кремния может быть эффективно десорбирован. С другой стороны, поскольку отделенный абсорбент для газообразного диоксида углерода не нагрет до температуры, превышающей 150 С, испарение абсорбента для газообразного диоксида углерода может быть подавлено. Кроме того, поскольку отделенные жидкие углеводородные соединения нагревают при температуре 100 С или выше, легкие углеводородные соединения могут быть эффективно извлечены. С другой стороны, поскольку отделенные жидкие углеводородные соединения не нагреты до температуры, превышающей 200 С, испарение жидких углеводородных соединений может быть подавлено. Кроме того, абсорбцию легких углеводородных соединений и газообразного диоксида углерода в газообразных побочных продуктах абсорбирующим растворителем можно проводить после смешивания газообразных побочных продуктов и газообразного сырья для реакции синтеза ФТ. Газообразное сырье (смешанный газ из оксида углерода и водорода) для реакции синтеза ФишераТропша включает газообразный диоксид углерода. Поэтому газообразный диоксид углерода, входящий в газообразное сырье и входящий в газообразные побочные продукты, может быть одновременно и эффективно абсорбирован абсорбцией газообразного диоксида углерода после смешивания газообразного сырья и газообразных побочных продуктов. Кроме того, абсорбирующий растворитель, использованный при абсорбции газообразного диоксида углерода и легких углеводородных соединений, может содержать абсорбент для газообразного диоксида углерода, из которого газообразный диоксид углерода десорбирован нагреванием, и жидкие углеводородные соединения, из которых легкие углеводородные соединения извлечены нагреванием. Абсорбент для газообразного диоксида углерода, из которого газообразный диоксид углерода десорбирован, и жидкие углеводородные соединения, из которых легкие углеводородные соединения извлечены, могут вновь поглощать, соответственно, газообразный диоксид углерода и легкие углеводородные соединения. Таким образом, стоимость извлечения легких углеводородных соединений может быть снижена за счет повторного использования абсорбирующего растворителя, который регенерирован, как рассмотрено выше. Аппарат для извлечения углеводородов согласно настоящему изобретению предназначен для извлечения углеводородных соединений из газообразных побочных продуктов, выходящих из реактора синтеза Фишера-Тропша. Аппарат для извлечения углеводородов включает абсорбер, который позволяет абсорбирующему растворителю, включающему абсорбент для газообразного диоксида углерода и жидкие углеводородные соединения, поглощать газообразный диоксид углерода и легкие углеводородные соединения из газообразных побочных продуктов, сепаратор, который разделяет абсорбирующий растворитель, включающий газообразный диоксид углерода и легкие углеводородные соединения, на абсорбент для газообразного диоксида кремния и жидкие углеводородные соединения, устройство для десорбции диоксида кремния, в котором протекает десорбция газообразного диоксида кремния из отделенного абсорбента для газообразного диоксида кремния, устройство для извлечения легких углеводородов,в котором извлекаются легкие углеводородные соединения из отделенных жидких углеводородных соединений, и линия подачи газообразных побочных продуктов, которая позволяет осуществить подачу газообразных побочных продуктов, из которых абсорбированы легкие углеводородные соединения и газообразный диоксид углерода, в реактор синтеза Фишера-Тропша. Согласно аппарату для извлечения углеводородов, имеющему данную конфигурацию, газообразный диоксид углерода и легкие углеводородные соединения, входящие в газообразные побочные продукты, абсорбируются абсорбирующим растворителем. Абсорбирующий растворитель, который абсорбировал газообразный диоксид углерода и легкие углеводородные соединения, разделяют на абсорбент для газообразного диоксида углерода и жидкие углеводородные соединения. Абсорбент для газообразного диоксида кремния, отделенный в сепараторе, хранят и нагревают в устройстве для десорбции газообразного диоксида кремния с выделением газообразного диоксида углерода. Кроме того, легкие углеводородные соединения извлекают из жидких углеводородных соединений в устройстве для извлечения легких углеводородов. Таким образом, согласно настоящему изобретению газообразный диоксид кремния может быть эффективно удален из газообразных побочных продуктов, и легкие углеводородные соединения могут быть извлечены из газообразных побочных продуктов. Кроме того, газообразные побочные продукты, из которых в абсорбере удалены входящие в них легкие углеводородные соединения и газообразный диоксид углерода, могут быть направлены в реактор синтеза ФТ по линии подачи газообразных побочных продуктов. В результате, оказывается возможным повторно использовать газообразные побочные продукты, из которых удалены входящие в их состав легкие углеводородные соединения и газообразный диоксид углерода, в качестве сырья для реакции синтеза ФТ. Здесь устройство для извлечения углеводородов может дополнительно включать линию циркуляции, которая позволяет извлечь абсорбент для газообразного диоксида углерода, из которого десорбирован газообразный диоксид углерода, и жидкие углеводородные соединения, из которых извлечены легкие углеводородные соединения, и направить на рецикл в абсорбер. В данном случае, поскольку абсорбент для газообразного диоксида углерода, из которого десорбирован газообразный диоксид углерода, и жидкие углеводородные соединения, из которых извлечены легкие углеводородные соединения, могут циркулировать в абсорбере, то можно получить абсорбирующий растворитель, включающий регенерированный абсорбент для диоксида углерода, и жидкие углеводородные соединения и повторно использовать абсорбирующий растворитель в абсорбере. Кроме того, абсорбером может быть абсорбционная башня для газообразного диоксида углерода, в которой протекает абсорбция газообразного диоксида углерода, входящего в газообразное сырье, вводимое в реактор синтеза Фишера-Тропша. Газообразный диоксид углерода содержится в газообразном сырье (смешанном газе из оксида углерода и водорода), использованного для реакции синтеза ФТ, как упомянуто выше. Поэтому абсорбционная башня для газообразного диоксида углерода может быть установлена выше по потоку от реактора синтеза ФТ, чтобы удалить газообразный диоксид углерода, содержащийся в газообразном сырье. Таким образом, при использовании абсорбирующего растворителя, включающего абсорбент для газообразного диоксида углерода и жидкие углеводородные соединения в абсорбционной башне для газообразного диоксида углерода, газообразный диоксид углерода может быть удален, а легкие углеводородные соединения могут быть извлечены из газообразных побочных продуктов без установки отдельно нового оборудования. Положительные эффекты от изобретения. Согласно настоящему изобретению можно осуществить способ извлечения углеводородных соединений и аппарат для извлечения углеводородов, способные эффективно извлекать легкие углеводородные соединения из газообразных побочных продуктов и улучшать производительность получения жидких топливных продуктов. Краткое описание чертежей На фиг. 1 представлена схема общей конфигурации системы синтеза углеводородных соединений,для которой использовано устройство для извлечения углеводородов согласно варианту осуществления настоящего изобретения. На фиг. 2 дана пояснительная схема, показывающая периферию устройства для извлечения углеводородов согласно варианту осуществления настоящего изобретения. На фиг. 3 представлена схема способа извлечения углеводородов согласно варианту осуществления настоящего изобретения. На фиг. 4 дана пояснительная схема, показывающая периферию устройства для извлечения углеводородов согласно другому варианту осуществления настоящего изобретения. Описание вариантов осуществления изобретения Далее в настоящем изобретении будет рассмотрен предпочтительный вариант осуществления настоящего изобретения со ссылкой на прилагаемые чертежи. Во-первых, общая конфигурация системы синтеза жидких топлив (реакционной системы синтеза углеводородов), для которой использован аппарат для извлечения углеводородов по настоящему варианту осуществления изобретения, будет рассмотрена со ссылкой на фиг. 1. Как показано на фиг. 1, система 1 синтеза жидких топлив (реакционная система синтеза углеводородов) согласно настоящему варианту осуществления изобретения представляет промышленное предприятие, на котором осуществляют GLT процесс, где протекает конверсия углеводородного сырья, такого как природный газ, в жидкие топлива. Данная система 1 синтеза жидких топлив включает установку 3 производства синтез-газа, установку 5 синтеза ФТ и установку 7 повышения качества. В установке 3 по производству синтез-газа протекает риформинг природного газа, который является углеводородным сырьем, с получением синтез-газа (газообразного сырья), включающего газообразный оксид углерода и газообразный водород. В установке 5 синтеза ФТ протекает синтез жидких углеводородных соединений из полученного синтез-газа по реакции синтеза Фишера-Тропша (далее по тексту называемой "реакцией синтеза ФТ"). В установке 7 повышения качества протекает гидрогенизация и фракционная перегонка жидких углеводородных соединений, полученных по реакции синтеза ФТ, с получением жидких топливных продуктов (нафты, керосина, газойля, парафина и т.п.). Далее по тексту будут рассмотрены компоненты данных соответствующих установок. Установка 3 по производству синтез-газа, главным образом, включает реактор 10 обессеривания,риформинг-установку 12, бойлер 14, работающий на отработанном тепле, газожидкостные сепараторы 16 и 18, установку 20 по удалению CO2 и сепаратор 26 водорода. Реактор 10 обессеривания состоит, например, из гидродесульфуратора и обеспечивает удаление серосодержащих компонентов из природного газа, который является сырьем. В риформинг-установке 12 протекает риформинг природного газа, подаваемого из реактора 10 обессеривания, с получением синтез-газа, включающего газообразный оксид углерода (СО) и газообразный водород (Н 2) в качестве основных компонентов. В бойлере 14, работающем на отработанном тепле, протекает извлечение отработанного тепла синтез-газа, полученного в риформинг-установке 12, с образованием пара высокого давления. В газожидкостном сепараторе 16 протекает разделение воды, нагретой в результате теплообмена с синтез-газом, в бойлере 14, работающем на отработанном тепле, на газ (пар высокого давления) и жидкость. В газожидкостном сепараторе 18 происходит удаление сконденсированных компонентов из синтезгаза, охлажденного в бойлере 14, работающем на отработанном тепле, и подача газового компонента в установку 20 удаления СО 2. Установка 20 для удаления СО 2 имеет поглотительную башню 22, которая удаляет газообразный диоксид углерода за счет использования абсорбирующего растворителя из синтез-газа, поступающего из газожидкостного сепаратора 18, и регенерационной башни 24, в которой протекает десорбция газообразного диоксида углерода из абсорбирующего растворителя, содержащего газообразный диоксид углерода,и регенерация абсорбирующего растворителя. В сепараторе 26 для водорода протекает отделение части газообразного водорода, входящего в син-4 018772 тез-газ, из которого отделен газообразный диоксид углерода в установке 20 удаления CO2. Установка 5 синтеза ФТ, главным образом, включает, например, барботажный колонный реактор 30(реактор синтеза углеводородов барботажного колонного типа), газожидкостной сепаратор 34, сепаратор 36, аппарат 101 извлечения углеводородов, который составляет настоящий вариант осуществления изобретения, и первый аппарат 40 для дробной перегонки. Барботажный колонный реактор 30, который является примером реактора, в котором протекает синтез жидких углеводородных соединений из синтез-газа, действует как реактор синтеза ФТ, в котором протекает синтез жидких углеводородных соединений из синтез-газа по реакции синтеза ФТ. Барботажный колонный реактор 30 включает, например, реактор барботажного колонного типа с суспензионным слоем, в котором суспензия, имеющая частицы твердого катализатора, суспендированные в жидких углеводородных соединениях (продукте реакции синтеза ФТ), содержится внутри емкости колонного типа. В барботажном колонном реакторе 30 происходит взаимодействие газообразного оксида углерода и газообразного водорода в синтез-газе, образованном в вышеназванной установке 3 получения синтез-газа,друг с другом с получением жидких углеводородных соединений. В газожидкостном сепараторе 34 происходит разделение воды, циркулирующей и нагреваемой в трубчатом теплообменнике 32, расположенном в барботажном колонном реакторе 30, на пар (пар среднего давления) и жидкость. В сепараторе 36 происходит разделение частиц катализатора и жидких углеводородных соединений в суспензии, находящейся внутри барботажного колонного реактора 30. Аппарат 101 извлечения углеводородов соединен с верхом барботажного колонного реактора 30 и извлекает углеводородные соединения, число атомов углерода которых составляет 3 или более (далее по тексту называемые "легкими углеводородными соединениями") из отводимых газообразных побочных продуктов. В первом аппарате 40 для дробной перегонки происходит фракционирование жидких углеводородных соединений, поступающих из барботажного колонного реактора 30 через сепаратор 36 и газожидкостной сепаратор 38, на соответствующие фракции. Установка 7 повышения качества включает, например, реактор 50 гидрокрекинга парафиновой фракции, реактор 52 гидрирования среднего дистиллята, реактор 54 гидрирования фракции нафты, газожидкостные сепараторы 56, 58 и 60, второй аппарат 70 для дробной перегонки и стабилизатор 72 нафты. Реактор 50 гидрокрекинга парафиновой фракции соединен с нижней частью первого аппарата 40 для дробной перегонки и имеет газожидкостной сепаратор 56, установленный ниже по потоку. Реактор 52 гидрирования среднего дистиллята соединен со средней частью первого аппарата 40 для дробной перегонки и имеет газожидкостной сепаратор 58, установленный ниже по его потоку. Реактор 54 гидрирования фракции нафты соединен с верхом первого аппарата 40 для дробной перегонки и имеет газожидкостной сепаратор 60, установленный ниже по его потоку. Во втором аппарате 70 для дробной перегонки происходит фракционирование жидких углеводородных соединений, поступающих из газожидкостных сепараторов 56 и 58, по температурам кипения. Стабилизатор 72 нафты дополнительно перегоняет жидкие углеводородные соединения, соответствующие фракции нафты, поступающие из газожидкостного сепаратора 60 и второго аппарата 70 для дробной перегонки, с отводом легких компонентов в виде отработанного газа и отделением и извлечением тяжелого компонента в виде готовой нафты. Далее будет рассмотрен процесс (GLT процесс) синтеза жидких топлив из природного газа в системе 1 синтеза жидких топлив, скомпонованной, как показано выше. Природный газ (чьим основным компонентом является СН 4) в качестве углеводородного сырья поступает в систему 1 синтеза жидких топлив из внешнего источника природного газа (не показан), такого как месторождение природного газа или станция по доставке природного газа. В вышеназванной установке 3 по производству синтез-газа происходит риформинг данного природного газа с получением синтез-газа (смешанного газа, включающего газообразный оксид углерода и газообразный водород в качестве основных компонентов). Во-первых, вышеназванный природный газ подается в реактор 10 обессеривания наряду с газообразным водородом, отделенным в сепараторе 26 для водорода. В реакторе 10 обессеривания протекает конверсия серосодержащих компонентов, входящих в состав природного газа, в присутствии газообразного водорода в сероводород под действием катализатора гидрообессеривания и адсорбция и связывание образующегося сероводорода, например, ZnO и т.д. Обессеренный природный газ поступает в риформинг-установку 12 после того, как смешан газообразный диоксид углерода (СО 2), подаваемый из источника подачи диоксида углерода (не показан), с паром, генерируемым в бойлере 14, использующем тепло отходящих газов. В риформинг-установке 12 протекает риформинг природного газа при использовании диоксида углерода и пара с получением высокотемпературного синтез-газа, включающего газообразный оксид углерода и газообразный водород в качестве основных компонентов, методом риформинга под действием пара и газообразного диоксида углерода. Высокотемпературный синтез-газ (например, 900 С, 2,0 МПаГ), образованный в риформинг-5 018772 установке 12, поступает в бойлер 14, использующем тепло отходящих газов, и охлаждается (например,до 400 С) за счет теплообмена с водой, которая циркулирует по бойлеру 14, использующему тепло отходящих газов, в результате чего отработанное тепло извлекают. Синтез-газ, охлажденный в бойлере 14, использующем тепло отходящих газов, поступает в поглотительную башню 22 узла 20 удаления СО 2 или барботажный колонный реактор 30 после отделения сконденсированных компонентов и удаления в газожидкостном сепараторе 18. В поглотительной башне 22 происходит поглощение газообразного диоксида углерода, и газообразный диоксид углерода десорбируют в регенерационной башне 24. Кроме того, десорбированный газообразный диоксид углерода подают в риформинг-установку 12 из регенерационной башни 24 и используют повторно для вышерассмотренной реакции риформинга. Синтез-газ, образованный в установке 3, поступает в барботажный колонный реактор 30 вышеназванной установки 5 синтеза ФТ. В момент поступления синтез-газа композиционное отношение синтезгаза, подаваемого в барботажный колонный реактор 30, доводят до композиционного отношения (например, Н 2:СО=2:1) (молярное отношение, подходящего для реакции синтеза ФТ. Кроме того, в сепараторе 26 для водорода происходит отделение газообразного водорода, входящего в синтез-газ, путем адсорбции и десорбции с использованием разницы давления (PSA водорода). Данный отделенный газообразный водород непрерывно поступает, например, из газгольдера (не показан) через компрессор (не показан) в различные реакторные устройства, работающие при использовании водорода (например, реактор 10 обессеривания, реактор 50 гидрокрекинга парафиновой фракции, реактор 52 гидрирования среднего дистиллята, реактор 54 гидрирования фракции нафты и т.п.), в которых протекают заранее заданные реакции с использованием газообразного водорода внутри системы 1 синтеза жидкого топлива. Далее, в вышеназванной установке 5 синтеза ФТ происходит синтез жидких углеводородных соединений по реакции синтеза ФТ из синтез-газа, полученного в вышеуказанной установке 3 по производству синтез-газа. Синтез-газ, полученный в вышеназванной установке 3 по производству синтез-газа, протекает в нижнюю часть барботажного колонного реактора 30 и поднимается через суспензию, находящуюся в барботажном колонном реакторе 30. В этот момент внутри барботажного колонного реактора 30 газообразный оксид углерода и газообразный водород, которые входят в состав синтез-газа, взаимодействуют друг с другом по механизму вышеназванной реакции синтеза ФТ, в результате чего образуются углеводородные соединения. Жидкие углеводородные соединения, полученные в барботажном колонном реакторе 30, вводят в сепаратор 36 наряду с частицами катализатора в виде суспензии. В сепараторе 36 происходит разделение суспензии на твердый компонент, такой как частицы катализатора, и жидкий компонент, включающий жидкие углеводородные соединения. Часть отделенного твердого компонента, такого как частицы катализатора, возвращают в барботажный колонный реактор 30, а жидкий компонент подают в первый аппарат 40 для дробной перегонки. Кроме того, газообразные побочные продукты, включающие непрореагировавший синтез-газ и образованные газообразные углеводородные соединения, отводят из верхней части барботажного колонного реактора 30 и подают в аппарат 101 извлечения углеводородов по настоящему варианту осуществления изобретения. В аппарате 101 извлечения углеводородов происходит удаление газообразного диоксида углерода и извлечение легких углеводородных соединений из газообразных побочных продуктов. Кроме того, оставшийся газообразный компонент после удаления газообразного диоксида углерода и легких углеводородных соединений включает непрореагировавший синтез-газ (СО и Н 2) и углеводородные соединения с числом атомов углерода 2 или меньше в качестве основных компонентов, и часть газообразного компонента направляют вновь в нижнюю часть барботажного колонного реактора 30 и повторно используют для реакции синтеза ФТ. Помимо этого, газовый компонент, который не использован повторно для реакции синтеза ФТ, выбрасывают в виде отходящего газа и используют как топочный газ,и извлекают как топливный эквивалент LPG (Liquefied Petroleum Gas - сжиженный нефтяной газ) или повторно используют как сырье для риформинг-установки 12 узла получения синтез-газа. Затем, в первом аппарате 40 для дробной перегонки происходит фракционирование жидких углеводородных соединений, которые поступают из барботажного колонного реактора 30 через сепаратор 36 и аппарат 101 извлечения углеводородов, как рассмотрено выше, на фракцию нафты (температура кипения которой составляет ниже приблизительно 150 С), средний дистиллят, соответствующий керосину и газойлю (температура кипения которого составляет приблизительно от 150 до 350 С) и парафиновую фракцию (температура кипения которой превышает приблизительно 350 С). Жидкие углеводородные соединения в виде парафиновой фракции (главным образом С 21 или больше), отводимые из нижней части первого аппарата 40 для дробной перегонки, входят в реактор 50 гидрокрекинга парафиновой фракции, жидкие углеводородные соединения в виде среднего дистиллята (главным образом от С 11 до С 20), отводимые из средней части первого аппарата 40 для дробной перегонки,поступают в реактор 52 гидрирования среднего дистиллята, и жидкие углеводородные соединения в виде фракции нафты (главным образом от C5 до С 10), отводимые из верхней части первого аппарата 40 для дробной перегонки, поступают в реактор 54 гидрирования фракции нафты. Реактор 50 гидрокрекинга парафиновой фракции обеспечивает гидрокрекинг жидких углеводородных соединений как парафиновой фракции (приблизительно С 21 или больше), которые отведены из куба первого аппарата 40 для дробной перегонки, при использовании газообразного водорода, поступающего из вышеназванного сепаратора 26 водорода, со снижением числа атомов углерода до С 20 или меньше. В данной реакции гидрокрекинга углеводородные соединения с небольшим числом атомов углерода образуются в результате расщепления С-С связей углеводородных соединений с большим числом атомов углерода при использовании катализатора и тепла. Продукт, включающий жидкие углеводородные соединения, претерпевшие гидрокрекинг в данном реакторе 50 гидрокрекинга парафиновой фракции, разделяется на газ и жидкость в газожидкостном сепараторе 56, жидкие углеводородные соединения которого поступают во второй аппарат 70 для дробной перегонки, и газовый компонент которого (включающий газообразный водород) поступает в реактор 52 гидрирования среднего дистиллята и реактор 54 гидрирования фракции нафты. В реакторе 52 гидрирования среднего дистиллята происходит гидрирование жидких углеводородных соединений как среднего дистиллята со средним числом атомов углерода (приблизительно С 11-С 20),которые поступают из средней части первого аппарата 40 для дробной перегонки, при использовании газообразного водорода, поступающего из сепаратора 26 водорода через реактор 50 гидрокрекинга парафиновой фракции. В данном процессе гидрирования протекает гидрогенизация олефинов, которые образуются в качестве побочных продуктов в реакции синтеза ФТ, конверсия кислородсодержащих соединений, таких как спирты, которые также являются побочными продуктами в реакции синтеза ФТ, в парафины путем гидродеоксигенации, и гидроизомеризация нормальных парафинов в изопарафины. Продукт, включающий гидрированные жидкие углеводородные соединения, разделяют на газ и жидкость в газожидкостном сепараторе 58, жидкие углеводородные соединения из которого подают во второй аппарат 70 для дробной перегонки, а газовый компонент из которого (включающий газообразный водород) повторно используют для вышеназванных реакций гидрогенизации. В реакторе 54 гидрирования фракции нафты протекает гидрирование жидких углеводородных соединений как фракции нафты с низким числом атомов углерода (приблизительно С 10 или меньше), которая выведена из верхней части первого аппарата 40 для дробной перегонки, при использовании газообразного водорода, поступающего из сепаратора 26 водорода через реактор 50 гидрокрекинга парафиновой фракции. Продукт, включающий гидрированные жидкие углеводородные соединения, разделяют на газ и жидкость в газожидкостном сепараторе 60, жидкие углеводородные соединения из которого направляют в стабилизатор 72 нафты, а газовый компонент (включающий газообразный водород) из которого повторно используют для вышеназванной реакции гидрогенизации. Затем во втором аппарате 70 парциальной перегонки происходит фракционирование жидких углеводородных соединений, которые поступают из реактора 50 гидрокрекинга парафиновой фракции и реактора 52 гидрирования среднего дистиллята, как рассмотрено выше, на углеводородные соединения с числом атомов углерода С 10 или меньше (чья температура кипения составляет ниже приблизительно 150 С), керосин (температура кипения которого составляет приблизительно от 150 до 250 С), газойль(температура кипения которого составляет приблизительно от 250 до 350 С) и фракцию некрекированного парафина (температура кипения которой превышает 350 С), из реактора 56 гидрокрекинга парафиновой фракции. Некрекированная парафиновая фракция выходит из нижней части второго аппарата 70 для дробной перегонки, и ее направляют на рецикл вверх по потоку реактора 50 гидрокрекинга парафиновой фракции. Керосин и газойль выводят из средней части второго аппарата 70 для дробной перегонки. Одновременно углеводородные соединения С 10 или меньше выводят из верхней части второго аппарата 70 для дробной перегонки и подают в стабилизатор 72 для нафты. Кроме того, в стабилизаторе 72 для нафты протекает ректификация углеводородных соединений С 10 или меньше, которые поступили из вышеназванного реактора 54 гидрирования фракции нафты и второго аппарата 70 для дробной перегонки, и получение нафты (С 5-С 10) в виде готового продукта. Соответственно, нафта высокой чистоты выходит из нижней части стабилизатора 72 для нафты. Одновременно отходящий газ, отличный от целевых продуктов, включающий углеводородные соединения с числом атомов углерода, равным или меньше, чем заданное число атомов углерода, в качестве основных компонентов выводят из верхней части стабилизатора 72 для нафты. Данный отходящий газ используют как топочный газ или извлекают как топливный эквивалент LPG. Далее будет рассмотрен процесс (GLT процесс), проводимый в системе 1 синтеза жидких топлив. В рассматриваемом процессе GTL природный газ превращается в жидкие топлива, такие как нафта высокой чистоты (С 5-С 15), керосин (С 11-C15) и газойль (C16-С 20). Далее будут рассмотрены конфигурация и работа сопутствующего оборудования аппарата 101 извлечения углеводородов по настоящему варианту осуществления изобретения, со ссылкой на фиг. 2. Данный аппарат 101 извлечения углеводородов включает первый газожидкостной сепаратор 103 и второй газожидкостной сепаратор 105, которые отделяют жидкий компонент (воду и жидкие углеводородные соединения) в газообразных побочных продуктах, которые выходят из верхней части барботажного колонного реактора (реактора синтеза ФТ) 30, средства 106 перемещения, такие как компрессор,-7 018772 котрые обеспечивают перенос газообразных побочных продуктов на линию 28 подачи синтез-газа, абсорбер 112, в который поступают газообразные побочные продукты, смешанные с синтез-газом, сепаратор 115, который разделяет абсорбирующий растворитель, который поглотил газообразный диоксид углерода, и легкие углеводородные соединения в абсорбере 112, на легкие углеводородные соединения и абсорбент газообразного диоксида углерода, узел 114 десорбции газообразного диоксида углерода, который обеспечивает нагрев абсорбента газообразного диоксида углерода, отделенного в сепараторе 115, с десорбцией диоксида углерода, установку 116 извлечения легких углеводородных соединений, отделенных в сепараторе 115, с извлечением легких углеводородных соединений и линию 113 подачи газообразных побочных продуктов, по которой происходит подача газообразных побочных продуктов в барботажный колонный реактор 30 из абсорбера 112. Помимо этого, в настоящем варианте осуществления изобретения первый газожидкостной сепаратор 103 и второй газожидкостной сепаратор 105 составляют газожидкостной сепаратор 38 на фиг. 1. В настоящем варианте осуществления изобретения поглотительная колонна 22 вышеупомянутой установки 20 для удаления СО 2 используется как абсорбер 112, а регенерационная башня 24 вышеупомянутой установки 20 для удаления CO2 используется как десорбционный узел 114 газообразного диоксида углерода. Кроме того, линия 23 подачи синтез-газа, по которой синтез-газ поступает в барботажный колонный реактора 30 из поглотительной башни 22, используется как линия 113 подачи газообразных побочных продуктов. Абсорбер 112 (поглотительная башня 22) сконструирован таким образом, что абсорбирующий растворитель, состоящий из смешанной жидкости абсорбента для газообразного диоксида углерода и жидких углеводородных соединений, подается из верхней части абсорбера 112. Абсорбирующий растворитель внутри абсорбера 112 поступает в сепаратор 115 по линии и разделяется на абсорбент для газообразного диоксида углерода и жидкие углеводородные соединения в данном сепараторе 115. Отделенный абсорбент для газообразного диоксида углерода подают в десорбционную установку 114 газообразного диоксида углерода (регенерационная башня 24), и отделенные жидкие углеводородные соединения подают в установку 116 по извлечению легких углеводородных соединений. Далее будет рассмотрен способ извлечения углеводородных соединений по настоящему варианту осуществления изобретения с использованием аппарата 101 извлечения углеводородов со ссылкой на фиг. 2 и 3. Во-первых, газообразные побочные продукты выводят из верхней части барботажного колонного реактора 30 (стадия S1 вывода газообразных побочных продуктов). Газообразные побочные продукты вводят в первый газожидкостной сепаратор 103 и второй газожидкостной сепаратор 105, где жидкий компонент (вода и жидкие углеводородные соединения) в газообразных побочных продуктах отделяют (стадия S2 газожидкостного разделения). Кроме того, кулер 104 установлен между первым газожидкостным сепаратором 103 и вторым газожидкостным сепаратором 105 и сконструирован так, что углеводородные соединения в газообразных побочных продуктах, из которых отделен жидкий компонент в первом газожидкостном сепараторе 103, сжижаются и дополнительно отделяются во втором газожидкостном сепараторе 105. Кроме того, вода и жидкие углеводородные соединения, которые отделены в первом газожидкостном сепараторе 103 и втором газожидкостном сепараторе 105, извлекают по линиям 108 и 109 извлечения соответственно. Одновременно тяжелые углеводороды ФТ, вытекающие в виде жидкости из барботажного колонного реактора 30, вводят в вышеупомянутый сепаратор 36. Газообразные побочные продукты, от которых отделен жидкий компонент в первом газожидкостном сепараторе 103 и втором газожидкостном сепараторе 105, подают на линию 28 введения синтез-газа с помощью средств 106 переноса и смешивают с синтез-газом, полученным в риформинг-установке 12(стадия S3 смешения). Затем газообразные побочные продукты, смешанные с синтез-газом, вводят в абсорбер 112 (стадияS4 введения). Затем в абсорбер 112 (стадия S5 подачи абсорбирующего растворителя) подают абсорбирующий растворитель, состоящий из смешанного с жидким абсорбентом газообразного диоксида углерода и жидкими углеводородными соединениями. Таким образом, газообразный диоксид углерода в газообразных побочных продуктах и легкие углеводородные соединения в газообразных побочных продуктах поглощаются абсорбирующим растворителем (стадия S6 абсорбции). Здесь в качестве абсорбента газообразного диоксида углерода, входящего в абсорбирующий растворитель, используют водные растворы аминов и т.п., которые поглощают газообразный диоксид углерода и выделяют поглощенный газообразный диоксид углерода при нагревании при заранее определенной температуре. Амины включают аминные соединения, соответствующие следующим общим формулам (1)-(3): Здесь в формулах R1 представляет атом водорода или алкильную группу С 1-С 10; R2 представляет атом водорода или алкильную группу С 1-С 4. Кроме того, n представляет целые числа от 1 до 5. Более того, много гидроксиалкильных групп в формулах (2) и (3) будут охватывать случай, когда число атомов углерода в алкиленовых группах, которые входят в данные гидроксиалкильные группы, отличаются друг от друга. Конкретные примеры аминных соединений, которые составляют абсорбент газообразного диоксида углерода, включают алканоламины, такие как моноэтаноламин, диэтаноламин, триэтаноламин, 2(метиламино)этанол,2-(этиламино)этанол,2-(пропиламино)этанол,н-бутиламиноэтанол,2(изопропиламино)этанол, 3-(этиламино)пропанол и дипропаноламин. Кроме того, концентрацию аминов в водных растворах устанавливают 20 мас.% или больше и 80 мас.% или меньше, а более предпочтительно устанавливают 30 мас.% или больше и 50 мас.% или меньше. Одновременно в качестве жидких углеводородных соединений, входящих в абсорбирующий растворитель, используют жидкие углеводородные соединения с температурой кипения от 200 С или выше и от 360 С или ниже. Кроме того, жидкие углеводородные соединения, которые не включают ненасыщенные компоненты, являются предпочтительными. Помимо этого, вышеупомянутыми жидкими углеводородными соединениями могут быть соединения из одного компонента, и могут быть смесью нескольких компонентов или могут быть жидкими углеводородными соединениями, полученными, когда жидкие углеводородные соединения среднего дистиллята со средним числом атомов углерода, которые выходят из средней части первого аппарата 40 для дробной перегонки, гидрируют в реакторе 52 гидрирования среднего дистиллята. Затем абсорбирующий растворитель, который поглотил газообразный диоксид углерода, и легкие углеводородные соединения подают в сепаратор 115 и разделяют на абсорбент газообразного диоксида углерода (водный раствор амина) и жидкие углеводородные соединения в сепараторе 115 (стадия S7 разделения). Затем абсорбент газообразного диоксида углерода, отделенный в сепараторе 115, подают в установку 114 десорбции газообразного диоксида углерода и нагревают при температуре, например, приблизительно от 100 до 150 С внутри установки 114 десорбции газообразного диоксида углерода, где газообразный диоксид углерода десорбируют из абсорбента для газообразного диоксида углерода (стадия S8 десорбции диоксида углерода). Кроме того, жидкие углеводородные соединения, отделенные в сепараторе 115, подают в установку 116 извлечения легких углеводородных соединений и нагревают при температуре, например, приблизительно от 100 до 200 С внутри установки 116 извлечения легких углеводородных соединений, где происходит извлечение легких углеводородных соединений из жидких углеводородных соединений (стадияS9 извлечения легких углеводородных соединений). Затем абсорбент газообразного диоксида углерода, из которого отпарен газообразный диоксид углерода, и жидкие углеводородные соединения, из которых извлечены легкие углеводородные соединения, смешивают вместе и направляют на рецикл вновь в абсорбер 112 по линии 119 рециркуляции в качестве абсорбирующего растворителя (стадия S10 рециркуляции). Кроме того, газообразные побочные продукты, из которых удалены легкие углеводородные соединения и газообразный диоксид углерода, проходят через стадию S6 абсорбции наряду с синтез-газом,полученным в риформинг-установке 12, и затем подают в барботажный колонный реактор 30 по линии 113 подачи газообразных побочных продуктов (линия 23 подачи синтез-газа) (стадия S11 подачи побочных газообразных продуктов). Таким путем из газообразных побочных продуктов извлекают легкие углеводородные соединения и удаляют газообразный диоксид углерода. Затем газообразные побочные продукты повторно используют в качестве сырья для барботажного колонного реактора 30. Согласно аппарату 101 извлечения углеводородов и способу извлечения углеводородных соединений с использованием аппарата 101 для извлечения углеводородов согласно настоящему варианту осуществления изобретения введением газообразных побочных продуктов в абсорбер 112 и подачей абсорбирующего растворителя, состоящего из смешанного жидкого абсорбента для газообразного диоксида углерода и жидких углеводородных соединений, в абсорбер 112 можно поглощать легкие углеводородные соединения и газообразный диоксид углерода в газообразных побочных продуктах абсорбирующим растворителем. Затем, разделяя абсорбирующий растворитель на абсорбент для газообразного диоксида углерода и жидкие углеводородные соединения в сепараторе 115 и нагревая жидкие углеводородные соединения при заранее заданной температуре, можно извлекать легкие углеводородные соединения из газообразных побочных продуктов. Кроме того, поскольку газообразный диоксид углерода удален из газообразных побочных продуктов, концентрация газообразного диоксида углерода внутри барботажного колонного реактора 30 может быть снижена, когда газообразные побочные продукты поступают в барботажный колонный реактор 30 и повторно используются в качестве сырья. Таким образом, реакцию синтеза ФТ можно спокойно осуществить. Кроме того, поскольку газообразный диоксид углерода десорбируется из отделенного абсорбента для газообразного диоксида углерода на стадии S8 десорбции диоксида углерода, можно повторно использовать абсорбент для газообразного диоксида углерода. Кроме того, поскольку температура кипения жидких углеводородных соединений, содержащихся в абсорбирующем растворителе, лежит в температурном интервале от 200 С или выше до 360 С или ниже,когда жидкие углеводородные соединения нагреваются на стадии S9 извлечения легких углеводородных соединений, можно предупредить испарение жидких углеводородных соединений, которые составляют абсорбирующий растворитель, и повторно использовать жидкие углеводородные соединения. Помимо этого, можно сохранять текучесть абсорбирующего растворителя без замерзания даже при относительно низкой температуре. Кроме того, поскольку абсорбент для газообразного диоксида углерода нагревают при температуре 100 С или выше и 150 С или ниже на стадии S8 десорбции диоксида углерода, а жидкие углеводородные соединения нагревают при температуре 100 С или выше и 200 С или ниже на стадии S9 извлечения легких углеводородных соединений, можно предупредить испарение абсорбента для газообразного диоксида углерода и жидких углеводородных соединений, входящих в абсорбирующий растворитель, и абсорбирующий растворитель может быть повторно использован. Кроме того, поскольку поглотительная башня 22 установки 20 удаления СО 2, в которой извлекается газообразный диоксид углерода из синтез-газа, образованного в риформинг-установке 12, используется как абсорбер 112, то газообразный диоксид углерода может быть удален из газообразных побочных продуктов и легкие углеводородные соединения могут быть извлечены без установки отдельного нового оборудования. Кроме того, поскольку абсорбент для газообразного диоксида углерода, из которого десорбирован газообразный диоксид углерода на стадии S8 десорбции диоксида углерода, и жидкие углеводородные соединения, из которых извлечены легкие углеводородные соединения на стадии S9 извлечения легких углеводородных соединений, направляют на рецикл в абсорбер 112 в качестве абсорбирующего растворителя на стадию S10 циркуляции, абсорбент для газообразного диоксида углерода и жидкие углеводородные соединения могут быть повторно использованы. Следовательно, затраты на извлечение легких углеводородных соединений из газообразных побочных продуктов могут быть снижены. Хотя вариант осуществления настоящего изобретения подробно рассмотрен в настоящем документе со ссылкой на чертежи, конкретные конфигурации не ограничиваются вариантом осуществления изобретения, и изобретение также включает конструкционные изменения, которые не нарушают существа настоящего изобретения. Например, хотя показано, что поглотительная башня 22 установки 20 удаления СО 2 обеспечивает удаление газообразного диоксида углерода из синтез-газа, полученного в риформинг-установке 12, настоящее изобретение не ограничивается данным воплощением. Как показано на фиг. 4, другой абсорбер 212 может быть установлен отдельно и независимо от поглотительной башни 22 установки 20 для удаления СО 2, в которой происходит удаление газообразного диоксида углерода из синтез-газа. В данном случае абсорбер 212 используется независимо для газообразных побочных продуктов. В абсорбере 212 газообразные побочные продукты, из которых извлечены газообразный диоксид углерода и легкие углеводородные соединения, подают в реактор синтеза ФТ (например, барботажный колонный реактор 30) по линии 213 подачи газообразных побочных продуктов и повторно используются как сырье. Кроме того, абсорбент для газообразного диоксида углерода в абсорбирующем растворителе не ограничивается теми, что перечислены в варианте осуществления изобретения, и доступны любые произвольные абсорбенты, которые могут поглощать и высвобождать газообразный диоксид углерода. Более того, хотя показано, что абсорбент для газообразного диоксида углерода и жидкие углеводородные соединения подают в абсорбер в смешанном состоянии, настоящее изобретение не ограничивается этим, и могут быть применены конфигурации, в которых каждый абсорбент для газообразного диоксида углерода и жидкие углеводородные соединения подают в абсорбер по отдельности и смешивают вместе в абсорбере. Кроме того, хотя рассмотрен случай, когда использованы первый газожидкостной сепаратор и второй газожидкостной сепаратор, которые разделяют жидкий компонент и газообразные побочные продукты, настоящее изобретение не ограничивается этим, и может быть установлен один газожидкостной сепаратор, три или более газожидкостных сепараторов. Кроме того, компоновки установки 3 получения синтез-газа, установки 5 синтеза ФТ и установки 7 повышения качества не ограничиваются теми, что рассмотрены в настоящем варианте осуществления изобретения, и могут быть применены любые произвольные конфигурации, в которых газообразные побочные продукты вводят в аппарат для извлечения углеводородов. Примеры Ниже будут рассмотрены результаты подтверждающих опытов, проведенных для подтверждения эффектов настоящего изобретения. В качестве сравнительных примеров газообразные побочные продукты, выходящие из верхней части реактора синтеза ФТ, вводили в газожидкостной сепаратор и извлекали сконденсированные углеводороды ФТ. Здесь сравнительные примеры 1-3 были проведены с изменением температуры газообразных побочных продуктов в газожидкостном сепараторе. В качестве примера настоящего изобретения газообразные побочные продукты, выходящие из реактора синтеза ФТ, вводили в газожидкостной сепаратор, сконденсированные углеводороды ФТ извлекали и, как рассмотрено в варианте осуществления изобретения, в абсорбере 112 осуществляли удаление газообразного диоксида углерода, входящего в газообразные побочные продукты, и извлечение легких углеводородных соединений, входящих в газообразные побочные продукты, с использованием аппарата,как показано на фиг. 2, подавая абсорбирующий растворитель, включающий абсорбент для газообразного диоксида углерода (водный раствор диэтаноламина с концентрацией 50 мас.% и 60 об.% относительно общего количества абсорбирующего растворителя) и жидкие углеводородные соединения (фракция с температурой кипения от 200 до 360 С, полученная перегонкой выходящего из реактора 52 гидрирования среднего дистиллята и 40 об.% относительно общего количества абсорбирующего растворителя) в абсорбер 112, и обеспечивали контакт поданного абсорбирующего растворителя с газообразными побочными продуктами. И газообразный диоксид углерода, и легкие углеводородные соединения абсорбируются из газообразных побочных продуктов абсорбирующим растворителем. Затем газообразные побочные продукты, из которых удалены газообразные диоксид углерода и легкие углеводородные соединения, вновь подают в реактор 30 синтеза ФТ в качестве сырья. Одновременно, абсорбирующий растворитель, который поглотил газообразный диоксид углерода, и легкие углеводородные соединения разделяли на абсорбент для газообразного диоксида углерода и жидкие углеводородные соединения в сепараторе 115. Жидкие углеводородные соединения нагревали в установке 116 извлечения легких углеводородных соединений, где извлекали легкие углеводородные соединения. Кроме того, абсорбент для газообразного диоксида углерода, который поглотил газообразный диоксид углерода, нагревали в установке 114 для десорбции газообразного диоксида углерода, где удаляли газообразный диоксид углерода. Жидкие углеводородные соединения, из которых извлечены легкие углеводородные соединения, и абсорбент для газообразного диоксида углерода, из которого десорбирован газообразный диоксид углерода, смешивали вместе и вновь подавали в абсорбер 112. Здесь примеры 1-3 проводили установкой температур отходящих газообразных побочных продуктов в газожидкостном сепараторе до тех же значений, что и в сравнительных примерах 1-3 соответственно. Затем в соответствующих сравнительных примерах, когда общие количества (общие количества жидких углеводородных соединений, извлеченных в газожидкостном сепараторе, и тяжелых углеводородов ФТ, вытекающих в виде жидкости из реактора синтеза ФТ) углеводородов синтеза ФТ (жидких углеводородных соединений), которые получены из реактора синтеза ФТ, в единицу времени принимали за 100, измеряли общие количества (общие количества жидких углеводородных соединений, извлеченных из газожидкостного сепаратора, легких углеводородных соединений, извлеченных из установки по извлечению, и тяжелых углеводородов ФТ, вытекающих в виде жидкости из реактора синтеза ФТ) углеводородов синтеза ФТ (жидких углеводородных соединений), которые получены из реактора синтеза ФТ, в единицу времени в соответствующих примерах, как образовавшиеся количества. Результаты показаны в таблице. В соответствующих температурных условиях было подтверждено, что полученное количество углеводородов синтеза ФТ (жидких углеводородных соединений) увеличивается за счет извлечения легких углеводородных соединений в абсорбере 112. Т.е. согласно настоящему изобретению полученное количество жидких углеводородных соединений может быть увеличено без установки, например, дополнительного охлаждающего устройства, когда газообразные побочные продукты, из которых удалены газообразный диоксид углерода и легкие углеводородные соединения, повторно используют в качестве сырья для реакции синтеза ФТ. Промышленная применимость Согласно способу извлечения углеводородных соединений и аппарату для извлечения углеводородов по настоящему изобретению легкие углеводородные соединения могут быть эффективно извлечены из газообразных побочных продуктов, которые образованы как побочные продукты в реакции синтеза ФТ без использования, например, дополнительного охлаждающего устройства, газообразные побочные продукты могут быть повторно использованы в качестве сырья для реакции синтеза ФТ удалением газообразного диоксида углерода из газообразных побочных продуктов, и производительность производства жидких топливных продуктов может быть увеличена. Описание номеров ссылок. 30 - барботажный колонный реактор (реактор синтеза ФТ); 101 - устройство для извлечения углеводородных соединений; 112 - абсорбер; 114 - установка десорбции газообразного диоксида углерода; 115 - сепаратор; 116 - установка для извлечения легких углеводородных соединений. ФОРМУЛА ИЗОБРЕТЕНИЯ 1. Способ извлечения углеводородных соединений из газообразных побочных продуктов, образованных в реакции синтеза Фишера-Тропша, заключающийся в том, что абсорбируют легкие углеводородные соединения и газообразный диоксид углерода из указанных газообразных побочных продуктов с использованием абсорбирующего растворителя, включающего жидкие углеводородные соединения и абсорбент газообразного диоксида углерода; разделяют абсорбирующий растворитель, который абсорбировал легкие углеводородные соединения и газообразный диоксид углерода, на жидкие углеводородные соединения и абсорбент для газообразного диоксида углерода; нагревают отделенные жидкие углеводородные соединения с извлечением легких углеводородных соединений из отделенных жидких углеводородных соединений; нагревают отделенный абсорбент газообразного диоксида углерода с десорбцией газообразного диоксида углерода из отделенного абсорбента газообразного диоксида углерода; повторно используют газообразные побочные продукты, из которых абсорбированы легкие углеводородные соединения и газообразный диоксид углерода, в качестве газообразного сырья для реакции синтеза Фишера-Тропша. 2. Способ по п.1, где абсорбирующий растворитель содержит амины как компонент абсорбента для газообразного диоксида углерода. 3. Способ по п.1 или 2, где температура кипения жидких углеводородных соединений, содержащихся в абсорбирующем растворителе, лежит в температурном интервале от 200 С или выше до 360 С или ниже. 4. Способ по любому из пп.1-3, где отделенный абсорбент для газообразного диоксида углерода нагревают при температуре 100 С или выше и 150 С или ниже и отделенные жидкие углеводородные соединения нагревают при температуре 100 С или выше и 200 С или ниже. 5. Способ по любому из пп.1-4, где абсорбцию легких углеводородных соединений и газообразного диоксида углерода в газообразных побочных продуктах абсорбирующим растворителем осуществляют после смешивания газообразных побочных продуктов и газообразного сырья для реакции синтеза Фишера-Тропша. 6. Способ по любому из пп.1-5, где абсорбирующий растворитель, используемый для абсорбции легких углеводородных соединений и газообразного диоксида углерода, содержит абсорбент газообразного диоксида углерода, из которого десорбирован газообразный диоксид углерода при нагревании, и жидкие углеводородные соединения, из которых извлечены легкие углеводородные соединения нагреванием. 7. Установка для реализации способа по п.1, содержащая абсорбер, который позволяет осуществить абсорбцию растворителя, включающего абсорбент для газообразного диоксида углерода и жидкие углеводородные соединения с абсорбцией газообразного диоксида углерода и легких углеводородных соединений из газообразных побочных продуктов; сепаратор, который разделяет абсорбирующий растворитель, включающий газообразный диоксид углерода и легкие углеводородные соединения, на абсорбент для газообразного диоксида углерода и жидкие углеводородные соединения; устройство десорбционной обработки газообразного диоксида углерода, в котором протекает десорбция газообразного диоксида углерода из отделенного абсорбента для газообразного диоксида углерода; устройство извлечения легких углеводородов, в котором протекает извлечение легких углеводородных соединений из отделенных жидких углеводородных соединений; и линию ввода газообразных побочных продуктов, которая позволяет подавать газообразные побочные продукты, из которых абсорбированы легкие углеводородные соединения и газообразный диоксид углерода, в реактор синтеза Фишера-Тропша. 8. Установка по п.7, дополнительно включающая циркуляционную линию, которая позволяет направить на рецикл в абсорбер абсорбент для газообразного диоксида углерода, из которого десорбирован газообразный диоксид углерода, и жидкие углеводородные соединения, из которых извлечены легкие углеводородные соединения. 9. Установка по п.7 или 8, где абсорбером является поглотительная башня для газообразного диоксида углерода, в которой абсорбируется газообразный диоксид углерода из газообразного сырья, вводимого в реактор синтеза Фишера-Тропша.
МПК / Метки
МПК: C10G 2/00
Метки: продуктов, способ, углеводородных, углеводородов, газообразных, устройство, соединений, извлечения, побочных
Код ссылки
<a href="https://eas.patents.su/15-18772-sposob-izvlecheniya-uglevodorodnyh-soedinenijj-i-ustrojjstvo-dlya-izvlecheniya-uglevodorodov-iz-gazoobraznyh-pobochnyh-produktov.html" rel="bookmark" title="База патентов Евразийского Союза">Способ извлечения углеводородных соединений и устройство для извлечения углеводородов из газообразных побочных продуктов</a>
Предыдущий патент: Способ обработки продуктов из натурального каучука
Следующий патент: Водонепроницаемая и проницаемая для пара обувь