Оконное стекло для транспортного средства и способ его получения
Номер патента: 22966
Опубликовано: 31.03.2016
Авторы: Циглер Штефан, Ратейчак Митя, Шларб Андреас, Ройль Бернхард
Формула / Реферат
1. Оконное стекло для транспортного средства, содержащее
подложку из стекла (1) с первым коэффициентом теплового расширения;
электропроводящую структуру (2) с толщиной слоя от 5 до 40 мкм, расположенную на участке подложки (1);
соединительный элемент (3) для подключения электропитания, содержащий по меньшей мере от 50 до 60 вес.% железа, от 25 до 35 вес.% никеля, от 15 до 20 вес.% кобальта, от 0 до 0,5 вес.% кремния, от 0 до 0,1 вес.% углерода или от 0 до 0,5 вес.% марганца и имеющий второй коэффициент теплового расширения, при этом разность между первым и вторым коэффициентами теплового расширения менее 5×10-6/°С; и
слой бессвинцового припойного материала (4), который электрически соединяет соединительный элемент (3) с подобластями электропроводящей структуры (2).
2. Оконное стекло по п.1, в котором максимальное расстояние b между наружными кромками соединительного элемента и местом, покрытым слоем припоя с толщиной менее 50 мкм, составляет менее 1 мм.
3. Оконное стекло по п.2, в котором максимальное расстояние b вытекания предпочтительно меньше чем 0,5 мм, в частности приблизительно равно 0 мм.
4. Оконное стекло по любому из пп.2 или 3, в котором боковая поверхность припоя имеет форму вогнутого мениска.
5. Оконное стекло по одному из пп.1-4, в котором электропроводящая структура (2) обладает толщиной слоя от 8 до 15 мкм.
6. Оконное стекло по одному из пп.1-5, в котором электропроводящая структура (2) содержит серебро.
7. Оконное стекло по одному из пп.1-6, в котором толщина слоя припоя (4) менее 3,0×10-4 м.
8. Оконное стекло по одному из пп.1-7, в котором припойный материал (4) содержит олово и висмут, индий, цинк, медь, серебро или их смеси.
9. Оконное стекло по п.8, в котором пропорция олова в припойном составе (4) равна от 3 до 99,5 вес.%.
10. Оконное стекло по п.8 или 9, в котором пропорция висмута, индия, цинка, меди, серебра или их смесей в припойном составе (4) равна от 0,5 до 97 вес.%.
11. Оконное стекло по одному из пп.1-10, в котором соединительный элемент (3) покрыт никелем, оловом, медью и/или серебром.
12. Оконное стекло по п.11, в котором соединительный элемент (3) покрыт слоем никеля толщиной от 0,1 до 0,3 мкм и/или слоем серебра толщиной от 3 до 10 мкм.
13. Оконное стекло по одному из пп.1-12, в котором электропроводящая структура предпочтительно является нагревательными проводниками и/или антенными проводниками.
14. Способ изготовления оконного стекла по любому из пп.1-13, в котором:
a) бессвинцовый припойный материал (4) в виде пластинки с постоянной толщиной слоя, объемом и формой размещают на соединительном элементе (3), содержащем по меньшей мере от 50 до 60 вес.% железа, от 25 до 35 вес.% никеля, от 15 до 20 вес.% кобальта, от 0 до 0,5 вес.% кремния, от 0 до 0,1 вес.% углерода или от 0 до 0,5 вес.% марганца, причем разность между коэффициентами теплового расширения подложки из стекла и соединительного элемента менее 5×10-6/°С;
b) электропроводящую структуру (2) толщиной от 5 до 40 мкм накладывают на подложку (1) из стекла;
c) соединительный элемент (3) с припойным материалом (4) размещают на электропроводящей структуре (2); и
d) соединительный элемент (3) припаивают к электропроводящей структуре (2).
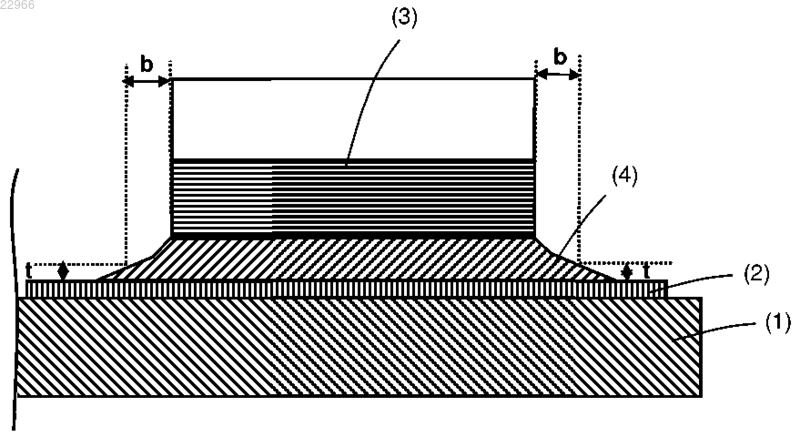
Текст
ОКОННОЕ СТЕКЛО ДЛЯ ТРАНСПОРТНОГО СРЕДСТВА И СПОСОБ ЕГО ПОЛУЧЕНИЯ Настоящее изобретение относится к оконному стеклу для транспортного средства, содержащему подложку из стекла (1) с первым коэффициентом теплового расширения, электропроводящую структуру (2) толщиной слоя от 5 до 40 мкм, расположенную на участке подложки (1),соединительный элемент (3) для подключения электропитания, содержащий по меньшей мере от 50 до 60 вес.% железа, от 25 до 35 вес.% никеля, от 15 до 20 вес.% кобальта, от 0 до 0,5 вес.% кремния, от 0 до 0,1 вес.% углерода или от 0 до 0,5 вес.% марганца и имеющий второй коэффициент теплового расширения, при этом разность между первым и вторым коэффициентами теплового расширения менее 510-6/С, и слой бессвинцового припойного материала (4),который электрически соединяет соединительный элемент (3) с подобластями электропроводящей структуры (2). Изобретение также относится к способу изготовления указанного оконного стекла,в котором бессвинцовый припойный материал (4) в виде пластинки с постоянной толщиной слоя,объемом и формой размещают на указанном соединительном элементе (3), электропроводящую структуру (2) толщиной от 5 до 40 мкм накладывают на подложку (1) из стекла, соединительный элемент (3) с припойным материалом (4) размещают на электропроводящей структуре (2) и соединительный элемент (3) припаивают к электропроводящей структуре (2). Изобретение обеспечивает экономичный и экологически щадящий способ изготовления оконного стекла,посредством чего можно избежать критичных механических напряжений в стекле. Изобретение относится к оконному стеклу для транспортного средства и экономичному и экологически щадящему способу его изготовления. Изобретение дополнительно относится к оконному стеклу с электрическим соединительным элементом для автотранспортных средств с электропроводящими структурами, например с нагревательными проводниками или антенными проводниками. Электропроводящие структуры обычно соединяются с бортовыми электрическими системами посредством припаянных к ним электрических соединительных элементов. Из-за различных коэффициентов теплового расширения использующихся материалов возникают механические напряжения, которые деформируют оконные стекла и могут привести к повреждению оконного стекла в течение изготовления и эксплуатации. Содержащие свинец припои имеют высокую пластичность, которая может компенсировать механические напряжения, возникающие между электрическим соединительным элементом и оконным стеклом за счет пластической деформации. Однако согласно директиве End of Life Vehicles Directive (директива о транспортных средствах достигших конца срока эксплуатации) 2000/53/ЕС, припои, содержащие свинец,должны быть заменены бессвинцовыми припоями, удовлетворяющими ЕС. К директиве часто дают ссылку аббревиатурой ELV (End of Life Vehicles). Задачей является исключение чрезвычайно проблематичных компонентов из продуктов, полученных в результате массового использования разовой электроники. Затрагиваемыми веществами являются свинец, ртуть, кадмий и хром. Среди прочего это относится к использованию бессвинцовых материалов для пайки в электротехнических применениях в оконных стеклах и к внедрению соответствующих заменяющих продуктов. ЕР 1942703 А 2 раскрывает электрический соединительный элемент на оконных стеклах автотранспортных средств, причем разница в коэффициенте теплового расширения оконного стекла и электрического соединительного элемента составляет 510-6/С. Для того чтобы обеспечить надежную механическую стабильность и пригодность для обработки, было предложено использовать избыточное количество припойного материала. Избытки припойного материала вытекают из промежуточного пространства между соединительным элементом и электропроводящей структурой. Избытки припойного материала вызывают высокие механические напряжения в оконном стекле. Механические напряжения в конечном счете приводят к повреждению оконного стекла. Задача настоящего изобретения - обеспечить оконное стекло электрическим соединительным элементом и предоставить экономичный и экологически щадящий способ для его изготовления, посредством чего можно избежать критичных механических напряжений в стекле. Задача настоящего изобретения решается посредством оконного стекла для транспортного средства, содержащего подложку из стекла (1) с первым коэффициентом теплового расширения; электропроводящую структуру (2) толщиной слоя от 5 до 40 мкм, расположенную на участке подложки (1); соединительный элемент (3) для подключения электропитания, содержащий по меньшей мере от 50 до 60 вес.% железа, от 25 до 35 вес.% никеля, от 15 до 20 вес.% кобальта, от 0 до 0,5 вес.% кремния, от 0 до 0,1 вес.% углерода или от 0 до 0,5 вес.% марганца и имеющий второй коэффициент теплового расширения, при этом разность между первым и вторым коэффициентами теплового расширения менее 510-6/С; и слой бессвинцового припойного материала (4), который электрически соединяет соединительный элемент (3) с подобластями электропроводящей структуры (2). Электропроводящая структура нанесена на оконное стекло. Электрический соединительный элемент электрически соединяется припойным материалом на подобластях электропроводящей структуры. Припойный материал вытекает на расстояние вытекания 1 мм из промежуточного пространства между соединительным элементом и электропроводящей структурой. В предпочтительном варианте осуществления максимальное расстояние вытекания предпочтительно составляет меньше 0,5 мм, и в особенности, приблизительно 0 мм. Максимальное расстояние вытекания определено как расстояние между внешними краями соединительного элемента и точкой области, покрытой припойным материалом, в которой толщина слоя припойного материала составляет менее 50 мкм. Максимальное расстояние вытекания измеряется для затвердевшего припойного материала после процесса припаивания. Требуемое максимальное расстояние вытекания получают посредством подобающего выбора припойного материала и вертикального расстояния между соединительным элементом и электропроводящей структурой, которое может быть определено простыми экспериментами. Вертикальное расстояние между соединительным элементом и электропроводящей структурой может быть заранее задано подходящим технологическим устройством, например дистанционирующим устройством. Максимальное расстояние вытекания может быть отрицательным, т.е. уходить назад в промежуточное пространство, образованное электрическим соединительным элементом и электрически проводящей структурой, предпочтительно при вогнутом мениске. Вогнутый мениск создается, например, за счет увеличения вертикального расстояния между дистанционирующим устройством и проводящей структу-1 022966 рой в процессе пайки, пока припой все еще является текучей средой. Преимущество состоит в уменьшении механических нагрузок на оконное стекло, в особенности в критической области с большим количеством припойного материала. Первый коэффициент теплового расширения предпочтительно составляет от 810-6/С до 910-6/С. Подложка предпочтительно является стеклом, которое предпочтительно имеет коэффициент теплового расширения от 8,310-6/С до 910-6/С в температурном диапазоне от 0 до 300 С. Второй коэффициент теплового расширения предпочтительно составляет от 810-6/С до 910-6/С,особенно предпочтительно от 8,310-6/С до 910-6/С в температурном диапазоне от 0 до 300 С. Коэффициент теплового расширения соединительного элемента может составлять 410-6/С. Электропроводящая структура согласно изобретению предпочтительно имеет толщину слоя от 8 до 15 мкм, особенно предпочтительно от 10 до 12 мкм. Электропроводящая структура согласно изобретению предпочтительно содержит серебро, особенно предпочтительно частицы серебра и стеклофритту. Толщина слоя припоя согласно изобретению составляет 3,010-4 м. Припойный материал согласно изобретению предпочтительно содержит олово и висмут, индий, цинк, медь, серебро или их смеси. Пропорция олова в припойном составе согласно изобретению равна от 3 до 99,5 вес.%, предпочтительно от 10 до 95,5 вес.%, особенно предпочтительно от 15 до 60 вес.%. Пропорция висмута, индия, цинка, меди,серебра или их смесей в припойном составе согласно изобретению равна от 0,5 до 97 вес.%, предпочтительно от 10 до 67%, при этом пропорция висмута, индия, цинка, меди или серебра может составлять 0 вес.%. Припойный состав согласно изобретению может содержать никель, германий, алюминий или фосфор в пропорции от 0 до 5 вес.%. Припойный состав согласно изобретению в особенности предпочтительно содержит Bi40Sn57Ag3, Sn40Bi57Ag3, Bi59Sn40Ag1, Bi57Sn42Ag1, In97Ag3, Sn95.5Ag3.8Cu0.7,Bi67In33, Bi33In50Sn17, Sn77.2In20Ag2.8, Sn95Ag4Cu1, SN99Cu1, Sn96.5Ag3.5 или их смеси. Соединительный элемент согласно изобретению предпочтительно содержит по меньшей мере от 50 до 75 вес.% железа, от 25 до 50 вес.% никеля, от 0 до 20 вес.% кобальта, от 0 до 1,5 вес.% магния, от 0 до 1 вес.% кремния, от 0 до 1 вес.% углерода или от 0 до 1 вес.% марганца. Соединительный элемент согласно изобретению предпочтительно содержит по меньшей мере от 55 до 70 вес.% железа, от 30 до 45 вес.% никеля, от 0 до 5 вес.% кобальта, от 0 до 1 вес.% магния, от 0 до 1 вес.% кремния или от 0 до 1 вес.% углерода. Дополнительно, соединительный элемент согласно изобретению предпочтительно содержит по меньшей мере от 50 до 60 вес.% железа, от 25 до 35 вес.% никеля, от 15 до 20 вес.% кобальта, от 0 до 0,5 вес.% кремния, от 0 до 0,1 вес.% углерода или от 0 до 0,5 вес.% марганца. Соединительный элемент согласно изобретению в особенности предпочтительно покрыт никелем,оловом, медью и/или серебром. Соединительный элемент согласно изобретению в особенности предпочтительно покрыт слоем толщиной от 0,1 до 0,3 мкм никеля и/или от 3 до 10 мкм серебра. Соединительный элемент может быть покрыт никелем, оловом, медью и/или серебром. Ni и Ag улучшают пропускную способность по току и коррозийную стойкость соединительного элемента и смачивание припойным материалом. Соединительный элемент согласно изобретению предпочтительно содержит ковар (FeCoNi) и/или инвар (FeNi) с коэффициентом теплового расширения инвара от 0,110-6/С до 410-6/С или с максимальным отличием ковара 510-6/С от коэффициента расширения оконного стекла. Ковар является железоникелькобальтовым сплавом, который имеет коэффициент теплового расширения по большей части приблизительно 510-6/С, который, таким образом, меньше, чем коэффициент типичных металлов. Состав содержит, например, 54 вес.% железа, 29 вес.% никеля и 17 вес.% кобальта. Поэтому, в области микроэлектронной и микропроцессорной технологии ковар используется в качестве материала корпуса или в качестве прослойки. Согласно принципу размещения между слоями прослойка лежит между фактическим материалом подложки и материалом по большей части, со значительно более высоким коэффициентом расширения. Таким образом, ковар служит в качестве компенсирующего элемента, который поглощает и уменьшает тепло-механические напряжения, вызванные различными коэффициентами теплового расширения других материалов. Подобным образом ковар используется для металлостеклянных реализаций электронных компонентов, переходов материалов в вакуумных камерах. Инвар является железоникелевым сплавом с долей никеля (FeNi36) 36 вес.%. Существует группа сплавов и соединений, которые имеют свойство чрезвычайно небольших или иногда отрицательных коэффициентов теплового расширения в конкретных температурных диапазонах. Инвар Fe65Ni35 содержит 65 вес.% железа и 35 вес.% никеля. Обычно легируется магнием, кремнием и углеродом до 1 вес.% для изменения механических свойств. При легировании кобальтом 5 вес.%, коэффициент теплового расширения может быть дополнительно уменьшен. Наименование одного такого сплава - Inovco,FeNi33Co4.5 с коэффициентом теплового расширения (от 20 до 100 С) 0,5510-6/С. Если используется сплав такой, как инвар с очень низким абсолютным коэффициентом теплового расширения 410-6/С, возникает избыточная компенсация механических напряжений при некритичных напряжениях в стекле или при некритичных растягивающих напряжениях в сплаве. Благодаря избыточной компенсации сплава, расстояние вытекания из промежуточного пространства между соединитель-2 022966 ным элементом и электропроводящей структурой является незначительным. Ковар и/или инвар может быть приварен, запрессован или приклеен в качестве компенсационной пластинки на соединительный элемент, выполненный, например, из стали, алюминия, титана, меди. Благодаря биметаллу может быть получено подходящее поведение при расширении соединительного элемента относительно расширения стекла. Компенсационная пластина предпочтительно является шляпкообразной. Электрический соединительный элемент на поверхности, обращенной к припойному материалу,имеет покрытие, которое содержит медь, цинк, олово, серебро, золото или их сочетание, предпочтительно серебро. Это предотвращает распространение припойного материала за границы покрытия и ограничивает расстояние вытекания. Электрический соединительный элемент может быть сконструирован в форме моста по меньшей мере с двумя контактными поверхностями, но также в форме соединительного элемента с одной контактной поверхностью. Соединительные элементы на виде сверху, например, обладают длиной и шириной от 1 до 50 мм,предпочтительно длиной и шириной от 3 до 30 мм, и в особенности предпочтительно шириной от 2 до 4 мм и длиной от 12 до 24 мм. Форма электрического соединительного элемента может образовывать хранилище для припоя в промежуточном пространстве соединительного элемента и электропроводящей структуры. Хранилища для припоя и смачивающие свойства припоя на соединительном элементе предотвращают вытекание припойного материала из промежуточного пространства. Хранилища для припоя могут иметь прямоугольную, округлую или многоугольную конструкцию. Распределение тепла при пайке и, таким образом, распределение припойного материала в течение процесса пайки может быть определено формой соединительного элемента. Припойный материал течет к наиболее горячей точке. Например, мост может иметь форму в виде одной или двух шляпок для того,чтобы эффективно распределить тепло в соединительном элементе в течение процесса пайки. Приложение энергии в процессе электрического связывания электрического соединения и электропроводящей структуры предпочтительно осуществляется посредством штампов, термодов, поршневой пайкой, предпочтительно лазерной пайкой, пайкой нагретым воздухом, индукционной пайкой, пайкой сопротивлением и/или с помощью ультразвука. Задача изобретения дополнительно решается способом изготовления оконного стекла с соединительным элементом, в котором:a) припойный материал размещается и накладывается на соединительный элемент в виде пластинки с постоянной толщиной слоя, объемом, формой и компоновкой;b) электропроводящая структура накладывается на подложку;c) соединительный элемент с припойным материалом размещается на электропроводящей структуре; иd) соединительный элемент припаивается к электропроводящей структуре. Припойный материал предпочтительно заранее накладывается на соединительные элементы предпочтительно в виде пластинки с постоянной толщиной слоя, объемом, формой и компоновкой на соединительном элементе. Соединительный элемент приваривается или прессуется к листу, плетеному проводу, сетке (не показаны), изготовленным, например, из меди и соединенным с бортовой электрической системой (также не показана). Соединительный элемент предпочтительно используется в нагреваемых оконных стеклах или в стеклах с антеннами для строений, в частности для автомобилей, поездов, самолетов или судов. Соединительный элемент служит для соединения проводящих структур оконного стекла с электрическими системами, которые размещаются вне оконного стекла. Электрические системы являются усилителями,блоками управления и источниками напряжения. Изобретение подробно разъясняется со ссылкой на чертежи и примерные варианты осуществления. Они отображают: фиг. 1 - вид в перспективе первого варианта осуществления оконного стекла согласно изобретению; фиг. 2 - разрез по лини А-А оконного стекла фиг. 1; фиг. 3 - разрез для альтернативного оконного стекла согласно изобретению; фиг. 4 - разрез для другого альтернативного оконного стекла согласно изобретению; фиг. 5 - разрез для другого альтернативного оконного стекла согласно изобретению; фиг. 6 - вид в перспективе альтернативного варианта осуществления оконного стекла согласно изобретению; фиг. 7 - разрез по линии В-В оконного стекла фиг. 6; и фиг. 8 - подробная блок-схема последовательности операций способа согласно изобретению. На фиг. 1 и 2 в каждом случае показан местный вид оконного стекла 1 с подогревом согласно изобретению в области электрического соединительного элемента 3. Оконное стекло 1 было предварительно термически напряженным одинарным безопасным стеклом 3-мм толщины, изготовленным из натрий-3 022966 кальциевого стекла. Оконное стекло 1 имело ширину 150 см и высоту 80 см. Электропроводящая структура 2 в виде структуры 2 нагревательного проводника была напечатана на оконном стекле 1. Электропроводящая структура 2 содержала частицы серебра и стеклофритту. В области края оконного стекла 1 электропроводящая структура 2 была расширена до 10 мм и образовала контактную поверхность для электрического соединительного элемента 3. В области края оконного стекла 1 также присутствовал покрывающий сериграф (не показан). В области контактной поверхности между электрическим соединительным элементом 3 и электропроводящей структурой 2 был наложен припойный материал 4, который выполнял надежное электрическое и механическое соединение между электрическим соединительным элементом 3 и электропроводящей структурой 2. Припойный материал 4 состоял из 57 вес.% висмута, 40 вес.% олова и 3 вес.% серебра. Припойный материал 4 между электрическим соединительным элементом 3 и электропроводящей структурой 2 повсеместно имел заданный объем и форму. Припойный материал 4 обладал толщиной 250 мкм. Максимальное наблюдаемое вытекание припойного материала 4 из промежуточного пространства между электрическим соединительным элементом 3 и электропроводящей структурой 2, толщина t слоя которого превышала 50 мкм, составлял b=0,5 мм. Электрический соединительный элемент 3 был сплавом, который содержал 54 вес.% железа, 29 вес.% никеля и 17 вес.% кобальта. Электрический соединительный элемент 3 был сконструирован в форме моста и имел ширину 4 мм и длину 24 мм. Толщина материала соединительного элемента 3 составляла 0,8 мм. Контактная поверхность соединительного элемента 3 имела ширину 4 мм и длину 4 мм. В оконном стекле 1 не наблюдалось никаких механических напряжений, вызванных компоновкой припойного материала 4, заранее заданным соединительным элементом 3 и электропроводящей структурой 2. Соединение оконного стекла 1 с электрическим соединительным элементом 3 посредством электропроводящей структуры 2 имело долговременную стабильность. Продолжая примерный вариант осуществления фиг. 1 и 2, на фиг. 3 отображен альтернативный вариант осуществления соединительного элемента 3 согласно изобретению. Электрический соединительный элемент 3 на поверхности, обращенной к припойному материалу 4, был снабжен покрытием 5, содержащим серебро. Это предотвращало растекание припойного материала за покрытие 5 и ограничивало расстояние b вытекания. Расстояние b вытекания припойного материала было меньше, чем 1 мм. В оконном стекле 1 не наблюдалось никаких механических напряжений, вызванных компоновкой припойного материала 4. Соединение оконного стекла 1 с электрическим соединительным элементом 3 посредством электропроводящей структуры 2 имело долговременную стабильность. Продолжая примерный вариант осуществления фиг. 1 и 2, на фиг. 4 отображен другой альтернативный вариант осуществления соединительного элемента 3 согласно изобретению. Электрический соединительный элемент 3 на поверхности, обращенной к припойному материалу 4, содержал выемку глубиной 250 мкм, которая образовывала хранилище припоя для припойного материала 4. Было возможно полностью предотвратить выход припойного материала 4 из промежуточного пространства. Термические напряжения в оконном стекле 1 не были критическими, а между соединительным элементом 3 и оконным стеклом 1 посредством электропроводящей структуры 2 было обеспечено надежное электрическое и механическое соединение. Продолжая примерный вариант осуществления фиг. 1 и 2, на фиг. 5 отображен другой альтернативный вариант осуществления соединительного элемента 3 согласно изобретению. Электрический соединительный элемент 3 был изогнут вверх в краевых областях. Высота изгиба вверх в краевой области оконного стекла 1 составляла максимум 400 мкм. Это образовывало пространство для припойного материала 4. Заранее заданный припойный материал 4 образовывал вогнутый мениск между электрическим соединительным элементом 3 и электропроводящей структурой 2. Было возможно полностью предотвратить вытекание припойного материала 4 из промежуточного пространства. Расстояние b вытекания, составлявшие приблизительно 0, было меньше 0 из-за образованного мениска. Термические напряжения в оконном стекле 1 не были критическими, а между соединительным элементом 3 и оконным стеклом 1 посредством электропроводящей структуры 2 было обеспечено надежное электрическое и механическое соединение. На фиг. 6 и 7 отображен другой вариант осуществления оконного стекла 1 согласно изобретению с соединительным элементом 3 в форме моста. Соединительный элемент 3 содержал железосодержащий сплав с коэффициентом теплового расширения 810-6/С. Толщина материала составляла 2 мм. В области контактной поверхности соединительного элемента 3 с оконным стеклом 1 были применены шляпкообразные компенсирующие элементы 6 с железоникелькобальтовым сплавом. Максимальная толщина слоя шляпкообразных компенсирующих элементов 6 составляла 4 мм. Посредством компенсирующих элементов было возможно адаптировать коэффициент теплового расширения соединительного элемента 3 к требованиям оконного стекла 1 и припойного материала 4. Шляпкообразные компенсирующие элементы 6 приводили к образованию улучшенного теплового потока в процессе выполнения припойного соединения 4. Нагрев первично возникал в центре контактной поверхности. Было возможно дополнительно уменьшить расстояние b вытекания припойного материала 4. Благодаря небольшому расстоянию b вытекания 1 мм и адаптированному коэффициенту расширения было возможно дополнительно уменьшить термические напряжения в оконном стекле 1. Термические напряжения в оконном стекле 1 не были кри-4 022966 тическими, а между соединительным элементом 3 и оконным стеклом 1 посредством электропроводящей структуры 2 было обеспечено надежное электрическое и механическое соединение. На фиг. 8 подробно показан способ изготовления оконного стекла 1 с электрическим соединительным элементом 3 согласно изобретению. Пример способа согласно изобретению для изготовления оконного стекла 1 с электрическим соединительным элементом представлен ниже. В качестве первого этапа было необходимо выделить часть припойного материала 4 согласно форме и объему. Выделенная часть припойного материала 4 была размещена на электрическом соединительном элементе 3. Электрический соединительный элемент 3 с припойным материалом был размещен на электропроводящей структуре 2. Прочное соединение электрического соединительного элемента 3 с электропроводящей структурой 2 и,таким образом, с оконным стеклом 1 возникало посредством подвода энергии. Пример. Испытуемые образцы были произведены с использованием оконного стекла 1 (толщина 3 мм, ширина 150 см и высота 80 см), электропроводящей структуры 2 в форме структуры нагревательного проводника, электрического соединительного элемента 3, слоя серебра на контактных поверхностях соединительного элемента 3 и припойного материала 4. Припойный материал 4 был наложен на контактную поверхность соединительного элемента 3 заранее в виде пластинки с постоянной толщиной слоя, объемом и формой. Соединительный элемент 3 с наложенным припойным материалом был наложен на электропроводящую структуру 2. Соединительный элемент был припаян к электропроводящей структуре 2 при температуре 200 С и при времени обработки, равном 2 с. Наблюдаемое максимальное расстояние вытекания припойного материала 4 из промежуточного пространства между электрическим соединительным элементом 3 и электропроводящей структурой 2, толщина t слоя которого превышала 50 мкм,составляло лишь b=0,5 мм. Размеры и состав электропроводящей структуры 2, электрического соединительного элемента 3, слоя серебра на контактных поверхностях соединительного элемента 3 и припойного материала 4 находятся в табл. 1, на фиг. 1 и 2 и на описаниях фигур. При перепаде температур от +80 до -30 С на всех образцах возможно было наблюдать, что стеклянная подложка 1 не была повреждена и не появилось дефектов. Было продемонстрировано, что непосредственно после пайки эти оконные стекла 1 с припаянным соединительным элементом 3 были устойчивы к внезапному понижению температуры. Сравнительный пример 1. Сравнительный пример 1 был выполнен так же, как пример со следующими отличиями. Размеры и компоненты электропроводящей структуры 2, электрического соединительного элемента 3, металлического слоя на контактных поверхностях соединительного элемента 3 и припойного материала 4 находятся в табл. 2. Припойный материал 4 в соответствии с предшествующим уровнем техники не был заранее наложен в виде пластинки на контактную поверхность соединительного элемента 3. Соединительный элемент 3 был припаян к электропроводящей структуре 2 в соответствии с традиционным способом. При вытекании припойного материала 4 из промежуточного пространства между электрическим соединительным элементом 3 и электропроводящей структурой 2, толщина t слоя которого превосходила 50 мкм,была получено среднее расстояние вытекания b = от 2 до 3 мм. При внезапном перепаде температур от +80 до -30 С наблюдалось, что стеклянная подложка 1 имела серьезное повреждение непосредственно после пайки. Сравнительный пример 2. Сравнительный пример 2 был выполнен так же, как пример со следующими отличиями. Размеры и компоненты электропроводящей структуры 2, электрического соединительного элемента 3, металлического слоя на контактных поверхностях соединительного элемента 3 и припойного материала 4 находятся в табл. 3. Припойный материал 4 в соответствии с предшествующим уровнем техники не был заранее наложен в виде пластинки на контактную поверхность соединительного элемента 3. Соединительный элемент 3 был припаян к электропроводящей структуре 2 в соответствии с традиционным способом. При вытекании припойного материала 4 из промежуточного пространства между электрическим соединительным элементом 3 и электропроводящей структурой 2, толщина t слоя которого превосходила 50 мкм,была получено среднее расстояние вытекания b= от 1 мм до 1,5 мм. При внезапном перепаде температур от +80 до -30 С наблюдалось, что стеклянная подложка 1 имела серьезное повреждение непосредственно после пайки. Было продемонстрировано, что оконные стекла согласно изобретению со стеклянными подложками 1 и электрическим соединительным элементом 3 согласно изобретению имели большую устойчивость к внезапным перепадам температур. Такой результат не был ожидаемым и вызвал удивление для специалистов в данной области техники. Список ссылочных позиций:b - максимальное расстояние вытекания припойного материала;t - ограничивающая толщина припойного материала; А-А' - линия разреза; В-В' - линия разреза. ФОРМУЛА ИЗОБРЕТЕНИЯ 1. Оконное стекло для транспортного средства, содержащее подложку из стекла (1) с первым коэффициентом теплового расширения; электропроводящую структуру (2) с толщиной слоя от 5 до 40 мкм, расположенную на участке подложки (1); соединительный элемент (3) для подключения электропитания, содержащий по меньшей мере от 50 до 60 вес.% железа, от 25 до 35 вес.% никеля, от 15 до 20 вес.% кобальта, от 0 до 0,5 вес.% кремния, от 0 до 0,1 вес.% углерода или от 0 до 0,5 вес.% марганца и имеющий второй коэффициент теплового расширения, при этом разность между первым и вторым коэффициентами теплового расширения менее 5106/С; и слой бессвинцового припойного материала (4), который электрически соединяет соединительный элемент (3) с подобластями электропроводящей структуры (2). 2. Оконное стекло по п.1, в котором максимальное расстояние b между наружными кромками соединительного элемента и местом, покрытым слоем припоя с толщиной менее 50 мкм, составляет менее 1 мм. 3. Оконное стекло по п.2, в котором максимальное расстояние b вытекания предпочтительно меньше чем 0,5 мм, в частности приблизительно равно 0 мм. 4. Оконное стекло по любому из пп.2 или 3, в котором боковая поверхность припоя имеет форму вогнутого мениска. 5. Оконное стекло по одному из пп.1-4, в котором электропроводящая структура (2) обладает толщиной слоя от 8 до 15 мкм. 6. Оконное стекло по одному из пп.1-5, в котором электропроводящая структура (2) содержит серебро. 7. Оконное стекло по одному из пп.1-6, в котором толщина слоя припоя (4) менее 3,010-4 м. 8. Оконное стекло по одному из пп.1-7, в котором припойный материал (4) содержит олово и висмут, индий, цинк, медь, серебро или их смеси. 9. Оконное стекло по п.8, в котором пропорция олова в припойном составе (4) равна от 3 до 99,5 вес.%. 10. Оконное стекло по п.8 или 9, в котором пропорция висмута, индия, цинка, меди, серебра или их смесей в припойном составе (4) равна от 0,5 до 97 вес.%. 11. Оконное стекло по одному из пп.1-10, в котором соединительный элемент (3) покрыт никелем,оловом, медью и/или серебром. 12. Оконное стекло по п.11, в котором соединительный элемент (3) покрыт слоем никеля толщиной от 0,1 до 0,3 мкм и/или слоем серебра толщиной от 3 до 10 мкм. 13. Оконное стекло по одному из пп.1-12, в котором электропроводящая структура предпочтительно является нагревательными проводниками и/или антенными проводниками. 14. Способ изготовления оконного стекла по любому из пп.1-13, в котором:a) бессвинцовый припойный материал (4) в виде пластинки с постоянной толщиной слоя, объемом и формой размещают на соединительном элементе (3), содержащем по меньшей мере от 50 до 60 вес.% железа, от 25 до 35 вес.% никеля, от 15 до 20 вес.% кобальта, от 0 до 0,5 вес.% кремния, от 0 до 0,1 вес.% углерода или от 0 до 0,5 вес.% марганца, причем разность между коэффициентами теплового расширения подложки из стекла и соединительного элемента менее 510-6/С;b) электропроводящую структуру (2) толщиной от 5 до 40 мкм накладывают на подложку (1) из стекла;c) соединительный элемент (3) с припойным материалом (4) размещают на электропроводящей структуре (2); и
МПК / Метки
МПК: H05B 3/84
Метки: оконное, транспортного, стекло, способ, получения, средства
Код ссылки
<a href="https://eas.patents.su/12-22966-okonnoe-steklo-dlya-transportnogo-sredstva-i-sposob-ego-polucheniya.html" rel="bookmark" title="База патентов Евразийского Союза">Оконное стекло для транспортного средства и способ его получения</a>
Предыдущий патент: Способ нагревания листов стекла с покрытием в печи
Следующий патент: Фармацевтическая композиция для местного применения, содержащая суспендированный мометазона фуроат
Случайный патент: Тяговый запирающий механизм с манипуляционным соединительным элементом