Способ удаления загрязняющих примесей из газообразного сырьевого потока на основе циклического адсорбционного процесса
Номер патента: 24199
Опубликовано: 31.08.2016
Авторы: Джонсон Роберт А., Декман Гарри В., Келли Брюс Т., Равикович Питер И., Андерсон Томас Н.
Формула / Реферат
1. Способ удаления загрязняющих примесей из газообразного сырьевого потока на основе циклического адсорбционного процесса, причем способ включает стадии, на которых:
a) пропускают газообразный сырьевой поток при давлении подачи через адсорбентный слой в течение интервала времени адсорбции более 1 и менее 60 с для отделения одной или более загрязняющих примесей от газообразного сырьевого потока с образованием потока продукта;
b) прерывают течение газообразного сырьевого потока;
c) выполняют многочисленные стадии сбрасывания давления, причем на каждой стадии сбрасывания давления снижают давление внутри адсорбентного слоя от начального давления сброса давления до конечного давления сброса давления;
d) пропускают продувочный поток в адсорбентный слой для удаления углеводородов из адсорбентного слоя;
e) подвергают продутый адсорбентный слой обработке на одной или более стадиях выдувания, где на каждой стадии выдувания снижают давление внутри адсорбентного слоя от начального давления выдувания до конечного давления выдувания;
f) выполняют многочисленные стадии восстановления давления, где на каждой стадии восстановления давления увеличивают давление внутри резервуара для циклической адсорбции от начального давления восстановления давления до конечного давления восстановления давления; и
g) повторяют стадии (a)-(f) в течение по меньшей мере одного дополнительного цикла.
2. Способ по п.1, в котором сырьевой поток представляет собой углеводородсодержащий поток, имеющий >1 об.% углеводородов в расчете на общий объем сырьевого потока.
3. Способ по любому из пп.1, 2, в котором сырьевой поток включает углеводороды и СО2, причем содержание СО2 варьирует в диапазоне 1-80 мол.% и углеводородов - в диапазоне 20-99 мол.%.
4. Способ по любому из пп.1-3, в котором адсорбентный слой включает адсорбентный материал, содержащий мезопористый наполнитель, который сокращает невымываемое поровое пространство между частицами адсорбента до менее чем 30 об.% в порах с диаметрами свыше 20 ангстрем (2 нм) и менее 1 мкм.
5. Способ по любому из пп.1-3, в котором адсорбентный слой включает адсорбентный материал, содержащий мезопористый наполнитель, который сокращает невымываемое поровое пространство между частицами адсорбента менее чем до 20 об.% в порах с диаметрами свыше 20 ангстрем (2 нм) и менее 1 мкм.
6. Способ по любому из пп.1-3, в котором адсорбентный слой включает адсорбентный материал, содержащий мезопористый наполнитель, который сокращает невымываемое поровое пространство между частицами адсорбента менее чем до 10 об.% в порах с диаметрами свыше 20 ангстрем (2 нм) и менее 1 мкм.
7. Способ по любому из пп.1-4, в котором адсорбционный слой включает первый адсорбентный материал, селективный к СО2, и второй адсорбентный материал, селективный к H2S.
8. Способ по любому из пп.1-7, в котором интервал времени адсорбции составляет более 2 и менее 50 с.
9. Способ по любому из пп.1-7, в котором интервал времени адсорбции составляет более 2 и менее 10 с.
10. Способ по любому из пп.1-9, в котором продувочный поток включает менее 40 мол.% метана.
11. Способ по любому из пп.1-10, в котором адсорбентный слой включает адсорбентный материал, имеющий отношение коэффициентов однокомпонентной диффузии СО2 и метана более 10.
12. Способ по любому из пп.1-10, в котором адсорбентный слой включает адсорбентный материал, имеющий отношение коэффициентов однокомпонентной диффузии CO2 и метана более 100.
13. Способ по любому из пп.1-10, в котором адсорбентный слой включает структурированный контактор, имеющий многочисленные каналы через структурированный контактор.
14. Способ по любому из пп.1-13, в котором давление подачи составляет более 350 psig (2413 кПа, манометрических).
15. Способ по любому из пп.1-13, в котором давление подачи составляет более 500 psig (3447 кПа, манометрических).
16. Способ на основе циклического адсорбционного процесса по любому из пп.1-15, причем этим способом извлекают более 90% желательного продукта, исходя из отношения, полученного делением количества желательного продукта в потоке продукта на количество желательного продукта в газообразном сырьевом потоке.
17. Способ по любому из пп.1-15, причем этим способом извлекают более 95% желательного продукта, исходя из отношения, полученного делением количества желательного продукта в потоке продукта на количество желательного продукта в газообразном сырьевом потоке.
18. Способ по любому из пп.1-15, причем этим способом извлекают более 97% желательного продукта, исходя из отношения, полученного делением количества желательного продукта в потоке продукта на количество желательного продукта в газообразном сырьевом потоке.
19. Способ по любому из пп.1-18, в котором каждая из стадий сбрасывания давления включает стадии, на которых пропускают часть сырьевого потока в адсорбентном слое в уравнительный резервуар, и затем во время одной из стадий восстановления давления пропускают по меньшей мере долю этой части в адсорбентный слой из уравнительного резервуара.
20. Способ по любому из пп.1-15, дополнительно включающий стадию, на которой пропускают вторую продувку через адсорбентный слой после одной или более стадий выдувания и перед повторением стадий (a)-(f).
21. Способ по любому из пп.1-20, в котором газообразный сырьевой поток включает одну или более загрязняющих примесей сверх порогового уровня загрязнения, причем одна или более загрязняющих примесей составляет одно или более из 1-80 мол.% СО2, менее 1 мол.% H2S или любой их комбинации, причем пороговый уровень загрязнения включает одно или более из менее 10 ч./млн H2S, менее 4 мол.% СО2 и любой их комбинации; и поток продукта имеет загрязняющие примеси менее порогового уровня загрязнения.
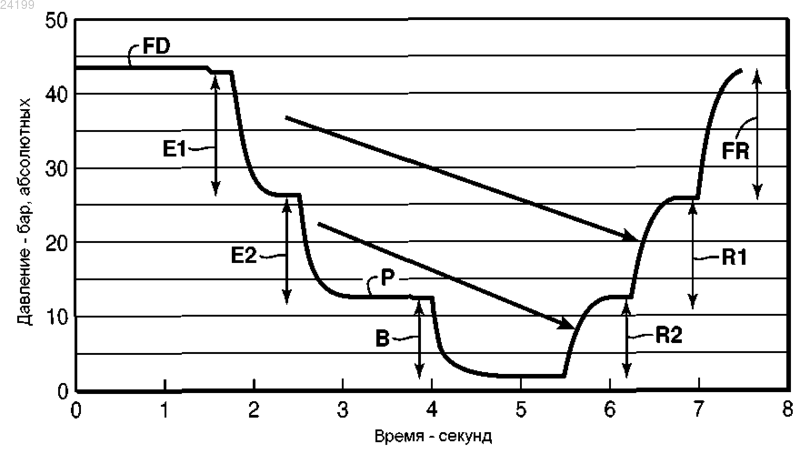
Текст
СПОСОБ УДАЛЕНИЯ ЗАГРЯЗНЯЮЩИХ ПРИМЕСЕЙ ИЗ ГАЗООБРАЗНОГО СЫРЬЕВОГО ПОТОКА НА ОСНОВЕ ЦИКЛИЧЕСКОГО АДСОРБЦИОННОГО ПРОЦЕССА Способ удаления CO2 из потоков природного газа на основе циклической адсорбции при переменном давлении с помощью комбинации селективного адсорбентного материала,содержащего эффективное количество неадсорбирующего наполнителя, конструкции адсорбентного контактора и схемы адсорбционного цикла. Удаление загрязняющих примесей из газовых потоков, предпочтительно потоков природного газа, с использованием короткоцикловых циклических адсорбционных процессов, таких как короткоцикловая адсорбция при переменном давлении (RC-PSA). Разделение при высоком давлении с высокой степенью извлечения продукта и/или высокой чистотой продукта обеспечиваются комбинацией рациональных выборов адсорбентного материала, газотвердофазного контактора, конфигурации системы и схемы цикла. Например, схемы циклов, которые включают стадии продувки и ступенчатого выдувания, а также включение мезопористого наполнителя в адсорбентный материал, значительно повышают степень извлечения продукта (например, метана). RC-PSA-продукт с содержанием менее 10 млн-1 H2S может быть получен из сырьевого потока природного газа, который содержит менее 1 мол.% H2S.(71)(73) Заявитель и патентовладелец: ЭКСОНМОБИЛ АПСТРИМ РИСЕРЧ КОМПАНИ (US) Перекрестная ссылка на родственные заявки Заявка на данное изобретение утверждает преимущество патентной заявки США 61/448121, озаглавленной "Способы удаления загрязняющих примесей из потока углеводородов в циклическом адсорбционном процессе, и связанные с этим устройства и системы ", поданной 1 марта 2011 г., полное содержание которой включено в описание ссылкой. Заявка на данное изобретение относится к патентной заявке США 61/448117, озаглавленной"Устройства и системы, имеющие контактор с заключенным в нем адсорбентом, и связанные с этим циклические адсорбционные процессы", поданной 1 марта 2011 г.; к патентной заявке США 61/448120,озаглавленной "Устройства и системы, имеющие сборный узел тарельчатого возвратно-поступательного клапана, и связанные с этим циклические адсорбционные процессы", поданной 1 марта 2011 г.; к патентной заявке США 61/448123, озаглавленной "Устройства и системы, имеющие сборный узел поворотного клапана, и связанные с этим циклические адсорбционные процессы", поданной 1 марта 2011 г.; к патентной заявке США 61/448125, озаглавленной "Устройства и системы, имеющие многочисленные слои с компактной конфигурацией для циклических адсорбционных процессов, и связанные с этим способы", поданной 1 марта 2011 г.; и к патентной заявке США 61/594,824, озаглавленной "Способы удаления загрязняющих примесей из потока углеводородов в циклическом адсорбционном процессе, и связанные с этим устройства и системы", поданной 3 февраля 2012 г., каждая из которых включена в описание ссылкой во всей своей полноте. Область техники, к которой относится изобретение Настоящее изобретение относится к циклическому адсорбционному процессу для удаления загрязняющих примесей, например CO2 и H2S, из потоков углеводородов с помощью комбинации характерных признаков, таких как конфигурации системы, структуры и материалы адсорбентов, и/или стадии циклического режима. Уровень техники Разделение газов является важным во многих отраслях промышленности и может быть выполнено пропусканием смеси газов над адсорбентным материалом, который предпочтительно поглощает более легко адсорбируемый компонент сравнительно с менее легко адсорбируемым компонентом смеси. Одним из важнейших типов технологии разделения газов является циклический адсорбционный процесс,такой как адсорбция при переменном давлении (PSA). Процессы PSA основываются на том факте, что под давлением газы проявляют тенденцию адсорбироваться внутри пористой структуры микропористого адсорбентного материала или внутри свободного объема полимерного материала. Чем выше давление,тем больше количество целевого газового компонента, который адсорбируется. Когда давление снижается, адсорбированный целевой компонент высвобождается, или десорбируется. Процессы PSA могут быть использованы для разделения газов внутри газовой смеси, поскольку различные газы склонны заполнять микропоры или свободный объем адсорбента в различной степени. Если газовую смесь, такую как природный газ, пропускают под давлением через резервуар, содержащий полимерный или микропористый адсорбент, который является более селективным по отношению, например, к диоксиду углерода, чем к метану, то по меньшей мере часть диоксида углерода избирательно поглощается адсорбентом, и газ, выходящий из резервуара, обогащается метаном. Когда слой достигает предела своей способности адсорбировать диоксид углерода, его регенерируют снижением давления, тем самым высвобождая поглощенный диоксид углерода. Затем, как правило, его продувают и восстанавливают давление, после чего он готов к еще одному циклу адсорбции. В то время как в технологии имеются разнообразные инструктивные указания относительно новых адсорбентных материалов, новых и усовершенствованных контакторов с параллельными каналами, и усовершенствованного оборудования для короткоцикловой PSA (RC-PSA), ни одно из них до сих пор не представляет надежного решения проблемы достижения хорошего извлечения метана, когда подводимый сырьевой газ находится под высоким давлением. Это является критически важной проблемой, поскольку природный газ часто добывают при высоких давлениях (30-700 бар (3-70 МПа, и является предпочтительной работа разделительных систем под высоким давлением, чтобы избежать дополнительного сжатия перед транспортированием на рынок сбыта. Одна проблема в распространении технологии PSA на условия высокого давления, в особенности в отношении таких потоков, которые содержат большие количества СО 2, состоит в том, что в конце адсорбционной стадии могут присутствовать значительные количества газообразного продукта в проточных каналах и поровых пространствах. Это может вести к плохому извлечению желательного продукта, а также к потокам продукта с низкой чистотой. Достижение высокой степени извлечения и высокой чистоты в процессах разделения при высоких давлениях является в особенности выгодным в операциях обработки природного газа. Многие месторождения природного газа имеют значительные уровни содержания СО 2, а также других загрязняющих примесей, таких как H2S, N2, Н 2 О, меркаптаны, и/или тяжелые углеводороды, которые должны быть удалены до различной степени, прежде чем газ может быть транспортирован на рынок сбыта. Предпочтительно, чтобы как можно больше кислотного газа (например, H2S и CO2) было удалено из природного газа, и некоторые варианты применения требуют высокочистого газообразного продукта с уровнями содержания загрязняющих примесей порядка частей на миллион, соответствующими условиям безопасно-1 024199 сти или эксплуатационным спецификациям. Во всех операциях разделения природного газа метан представляет собой ценный компонент и действует как легкий компонент в циклических адсорбционных процессах. Небольшие увеличения степени извлечения этого легкого компонента могут иметь результатом значительные улучшения экономических показателей процесса, а также служат для предотвращения нежелательной потери ресурсов. Традиционные промышленные практические подходы к удалению кислотных газов из природного газа являются ограниченными в достижении высокой степени извлечения и высокой чистоты, в частности, когда концентрации кислотных газов превышают 30%, поскольку эти процессы включают значительное потребление энергии на охлаждение, и они часто требуют применения крупногабаритного оборудования. Например, традиционные способы удаления в ситуациях с содержанием от 20 до 30 мол.% кислотных газов из потоков природного газа предусматривают физические и химические растворители. Эти способы требуют проведения погрузочно-разгрузочных работ и хранения на складе растворителя, а также значительного расходования энергии на регенерацию растворителя. В случае более высоких концентраций кислотных газов в некоторых вариантах применения используют объемное фракционирование в сочетании с технологией типа Selexol с системой физического растворителя, которая нуждается в охлаждении и может обусловливать значительную потерю тяжелых углеводородов с потоком кислотных газов. Как правило, простые PSA-циклы могут не обеспечивать преимущества в отношении кинетических характеристик адсорбции, поскольку продолжительности циклов являются длительными, и общеупотребительные PSA-системы обычно приводят к значительной потере метана с потоком кислотных газов. Относительно низкая степень извлечения продукта наряду с крупными габаритами и стоимостью традиционных PSA-систем обычно препятствует их применению в ситуациях крупномасштабной обработки природного газа. В то время как были предложены разнообразные концепции для повышения производительности PSA-систем, ни одна из них не обеспечивала разделения при высоком давлении, которое давало бы чистоту продукта и степень извлечения, необходимые для обработки природного газа. Поэтому в технологии существует потребность в усовершенствованных способах удаления загрязняющих примесей из сырьевых потоков, таких как потоки природного газа, при высоком давлении с высокой чистотой продукта и степенью извлечения продукта. Сущность изобретения В соответствии с настоящим изобретением представлен способ удаления загрязняющих примесей,например СО 2, из потоков углеводородов, таких как потоки природного газа, в условиях циклического адсорбционного процесса, причем способ включает стадии, на которых: а) подвергают поток природного газа, включающий метан и СО 2, обработке в адсорбционной стадии введением его во впускной сырьевой конец адсорбентного слоя, состоящего из адсорбентного материала, селективного в адсорбировании СО 2, причем адсорбентный слой имеет сырьевой впускной конец и продуктовый выпускной конец, и причем адсорбентный слой действует при первом давлении и первой температуре, в котором по меньшей мере часть указанного СО 2 адсорбируется адсорбентным слоем и в котором газообразный продукт, обогащенный метаном и обедненный диоксидом углерода (CO2), выходит из продуктового выпускного конца указанного адсорбентного слоя, причем указанный адсорбентный материал является пористым и содержит эффективное количество неадсорбирующего материала мезопористого наполнителя, причем адсорбционную стадию проводят в течение периода времени менее 10 с;b) прекращают введение указанного потока природного газа в указанный адсорбентный слой перед проскоком указанного целевого вещества из продуктового выпускного конца указанного адсорбентного слоя; с) подвергают указанный адсорбентный слой воздействию в последовательных от 1 до 10 уравнительных стадиях, в которых давление в указанном слое снижают на предварительно заданную величину в каждой последующей стадии;d) проводят обогащенный диоксидом углерода (СО 2) высоконапорный газовый поток через указанный адсорбентный слой для удаления углеводородов из слоя; е) подвергают продутый адсорбентный слой обработке в многочисленных последовательных стадиях выдувания, в которых давление в слое снижают на предварительно заданную величину в каждой последующей стадии выдувания;f) подвергают указанный адсорбентный слой воздействию в последовательных от 1 до 10 уравнительных стадиях, в которых давление в указанном слое повышают на предварительно заданную величину в каждой последующей стадии; иg) восстанавливают давление в указанном адсорбентном слое путем создания давления с использованием подводимого сырья. Краткое описание чертежей Фиг. 1 представляет изображение одного варианта исполнения адсорбентного контактора с параллельными каналами, который может быть использован в настоящем изобретении. Этот контактор имеет монолитную форму, которая непосредственно сформирована из микропористого адсорбента и содержит многочисленные параллельные газовые каналы. Фиг. 2 представляет изображение в разрезе, проведенном вдоль продольной оси контактора из приведенной здесь фиг. 1. Фиг. 3 представляет увеличенное изображение секции вида в разрезе монолита из фиг. 2, подробно показывающее структуру адсорбентного слоя, наряду с блокатором, занимающим некоторые из мезопор и макропор. Фиг. 4 представляет увеличенный вид небольшого участка поперечного сечения контактора из фиг. 1, показывающий стенки каналов, покрытые слоем адсорбента. Фиг. 5 представляет изображение адсорбентного контактора со спиральной намоткой для применения в настоящем изобретении. Фиг. 6 представляет изображение еще одной конфигурации адсорбентного контактора согласно настоящему изобретению, который состоит из пучка пустотелых трубок. Фиг. 7 представляет блок-схему одного примерного варианта осуществления настоящего изобретения, показывающую последовательность выдувания для одного адсорбентного слоя. Фиг. 8 представляет технологическую блок-схему одного примерного варианта исполнения повторно-цикловой RC-PSA-системы, в котором может достигаться высокая чистота и степень извлечения продукта. Фиг. 9 представляет технологическую блок-схему одной примерной вакуумной RC-PSA-системы, в которой может достигаться высокая чистота и степень извлечения продукта. Фиг. 10 представляет график, показывающий давление в адсорбентном слое одного варианта осуществления настоящего изобретения, в котором сборные узлы из четырнадцати адсорбентных слоев использованы для выполнения адсорбционного цикла с двумя уравниваниями давления. Фиг. 11 А и 11B представляют схемы, показывающие расположение стадий для сборных узлов из четырнадцати адсорбентных слоев в адсорбционном RC-PSA-цикле с двумя уравниваниями давления. Фиг. 12 А и 12B представляют схемы, показывающие расположение стадий для сборных узлов из шестнадцати адсорбентных слоев в адсорбционном RC-PSA-цикле с тремя уравниваниями давления. Фиг. 13 А и 13B представляют схематические изображения адсорбентных структур и слоя. Фиг. 14 А и 14B показывают взаимозависимость между давлением и временем для примерных циклов в RC-PSA-циклах, описанных на фиг. 8. Фиг. 15 А и 15B показывают один примерный график цикла для базовой RC-PSA-системы из фиг. 8. Фиг. 16 показывает один примерный график цикла для повторно-цикловой RC-PSA-системы из фиг. 8. Фиг. 17 показывает один примерный график цикла для базовой RC-PSA-системы, в которой используются уравнительные резервуары. Фиг. 18 показывает один примерный график цикла для повторно-цикловой RC-PSA-системы, в которой используются уравнительные резервуары. Фиг. 19 показывает взаимозависимость между давлением и временем для одного примерного вакуумного RC-PSA-цикла, описанного на фиг. 9. Фиг. 20 показывает один примерный график цикла для вакуумной RC-PSA-системы, описанной на фиг. 9. Фиг. 21 представляет иллюстрацию вида сбоку одной примерной установки для обработки углеводородов, состоящей из циклической адсорбционной системы со сборными узлами из четырнадцати адсорбентных слоев, размещенных в двух уровнях из семи слоев, равномерно распределенных вокруг центрального клапанного сборного узла для распределения потока. Фиг. 22 представляет иллюстрацию вида сверху одной примерной установки для обработки углеводородов, состоящей из циклической адсорбционной системы со сборными узлами из четырнадцати адсорбентных слоев, размещенных в двух уровнях из семи слоев, равномерно распределенных вокруг центрального клапанного сборного узла для распределения потока. Фиг. 23 представляет трехмерное изображение еще одной примерной установки для обработки углеводородов, состоящей из циклической адсорбционной системы с семью сборными узлами адсорбентных слоев, размещенными в два ряда. Фиг. 24 А-24 С представляют виды сверху, сбоку и снизу, соответственно, отдельного сборного узла адсорбентного слоя из примерной установки для обработки углеводородов из фиг. 23. Фиг. 25 представляет трехмерное изображение опорных конструкций для отдельных адсорбентных слоев, присоединенных к основанию стеллажа примерной установки для обработки углеводородов согласно фиг. 23. Фиг. 26 А-26 С представляют виды сверху, сбоку и снизу, соответственно, пары отдельных сборных узлов адсорбентного слоя с соединительными трубопроводами и опорными конструкциями слоя для примерной установки для обработки углеводородов согласно фиг. 23. Фиг. 27 представляет трехмерное изображение сети клапанов и трубопроводов для семи взаимосвязанных адсорбентных слоев примерной установки для обработки углеводородов согласно фиг. 23. Подробное описание изобретения Все численные значения в пределах подробного описания и пунктов патентной формулы здесь модифицированы терминами "около" или "приблизительно" соответственно указанным значениям и учитывают погрешности экспериментов и отклонения, которые следовало бы ожидать специалисту, имеющему обычную квалификацию в этой области технологии. Кроме того, составы газов представлены как уровни содержания в мольных процентах, если не оговорено нечто иное. Если не оговорено иное, все используемые здесь технические и научные термины имеют такое же значение, как обычно понимаемое специалистом с обычной квалификацией в этой области технологии, к которой имеет отношение настоящее изобретение. Термины единственного числа включают упоминаемые объекты во множественном числе, если контекст определенно не оговаривает иного. Подобным образом, слово "или" предполагает включение понятия "и", если контекст определенно не оговаривает иного. Термин "включает" означает "содержит". Все упомянутые здесь патенты и публикации включены ссылкой во всей своей полноте, если не оговорено иное. В случае противоречия в значении термина или выражения, будет преобладать настоящее описание, включающее разъяснения терминов. Обозначающие направление термины, такие как "верхний", "нижний", "верх", "низ", "передняя часть", "задняя часть","вертикальный" и "горизонтальный", использованы здесь для выражения и прояснения взаимосвязи между разнообразными элементами. Должно быть понятно, что такие термины не указывают абсолютной ориентации (например, "вертикальный" компонент может становиться горизонтальным при повороте устройства). Перечисленные здесь материалы, способы и примеры являются только иллюстративными и не предполагаются быть ограничивающими. Настоящее изобретение относится к удалению загрязняющих примесей из газовых потоков, предпочтительно потеков природного газа, с использованием процессов короткоцикловой адсорбции, таких как короткоцикловая адсорбция при переменном давлении (RC-PSA). Разделения при высоком давлении с высокой степенью извлечения продукта и/или высокой чистотой продукта обеспечены комбинацией рационального выбора адсорбентного материала, газотвердофазного контактора, конфигурации системы и проектных схем циклов. Например, проектные схемы циклов, которые предусматривают стадии продувки и ступенчатого выдувания, а также включение мезопористого наполнителя в адсорбентный материал, значительно улучшают степень извлечения продукта (например, метана). При сравнении с общеупотребительной технологией адсорбции при переменном давлении для удаления кислотного газа (например, СО 2 и H2S) из потоков природного газа, например, преимущества определенных вариантов осуществления настоящего изобретения включают более низкие потери углеводородов с потоком кислотных газов, более низкое общее потребление энергии, и меньшие занимаемую оборудованием площадь и его вес. В других комбинациях описываемых здесь признаков представлены RC-PSA-системы, которые создают потоки высокочистого продукта из находящегося под высоким давлением природного газа, в то же время с извлечением свыше 99% углеводородов. Например, в одном варианте исполнения RC-PSAсистемы продукт с содержанием менее 10 млн-1 H2S может быть получен из сырьевого потока природного газа, который содержит менее 1 мольного процента H2S. Другие заявки в этой области техники включают патентные заявки США 61/447806, 61/447812,61/447824, 61/447848, 61/447869, 61/447835 и 61/447877, каждая из которых включена здесь ссылкой во всей своей полноте. Способность удалять загрязняющие примеси из подводимого сырьевого потока, такого как поток метана, при высоком давлении с высокой степенью извлечения, является весьма выгодным в обработке природного газа. В качестве одного примера газовые месторождения содержат метан и также могут иметь значительные уровни содержания Н 2 О, H2S, СО 2, N2, меркаптанов и/или тяжелых углеводородов,которые должны быть удалены до различной степени, прежде чем газ может быть транспортирован на рынок сбыта. Природный газ зачастую добывают при высоких давлениях (30-700 бар (3-70 МПа) абс.). Может оказаться предпочтительной работа разделительных систем под высоким давлением, чтобы избежать дополнительного сжатия перед транспортированием на рынок сбыта. То есть, обработка может быть более экономичной в плане потребления энергии, так как не предусматривает дополнительного сжатия. В дополнение, обработка при высоких давлениях повышает работоспособность адсорбента и сводит к минимуму габариты оборудования. В операциях разделения природного газа метан является ценным компонентом и действует как легкий компонент в циклических адсорбционных процессах. Небольшие увеличения степени извлечения этого легкого компонента могут иметь результатом значительные улучшения экономических показателей процесса, а также служат для предотвращения нежелательной потери ресурсов (например, потери метана или другого целевого продукта). В процессе удаления загрязняющих примесей является желательным извлечение более 90%, предпочтительно более 95% метана, более 97% метана или более 99% метана. Степень извлечения определяется как отношение, полученное делением числа молей желательного или целевого газа в потоке продукта на число молей того же желательного или целевого газа в потоке подводимого сырья. Традиционные PSA-процессы не способны выполнять обработку высоконапорных газов (с давлением выше, чем около 30 бар (3 МПа), абс.), в то же время по-прежнему обеспечивая высокую степень извлечения метана (например, 90, 95 или 97%). Как правило, в этих процессах метан теряется с кислотным газом по двум механизмам. Во-первых, метан из подводимого сырьевого потока остается в поровых пространствах между гранулами и/или частицами адсорбента после адсорбционной стадии (например, внутри пор контактора). Поровые объемы в традиционных PSA-процессах могут быть довольно значительными, поскольку они обычно действуют в режимах долговременных циклов, порядка минут или часов, и поэтому объемы адсорбента и оборудования оказываются крупными. Даже для меньших традиционных короткоцикловых PSA-процессоров поровое пространство должным образом не регулируется, и по-прежнему может составлять большую часть общего объема системы. Во-вторых, метан адсорбируется на адсорбентном материале, поскольку в традиционных PSA-системах используются материалы с относительно низкой селективностью, и адсорбционно-десорбционная способность является такой, что эффективное отношение молекул CO2 к молекулам метана, поступающих в абсорбентный материал и выходящих из него, составляет около 5-10. Вследствие этих обоих механизмов значительные количества метана могут оставаться в PSA-системе после адсорбционной стадии и теряются с кислотным газом в регенеративных стадиях цикла. Ввиду низкой степени извлечения метана традиционныеPSA-системы не нашли широкого применения для крупномасштабного удаления кислотных газов из природного газа. В дополнение к высокой степени извлечения, в некоторых вариантах применения для обработки природного газа требуется получение потока высокочистого продукта при высоком давлении. Для получения газа, который может быть в конечном итоге продан на рынках сбыта топлива для жилого сектора и промышленности, такие загрязняющие примеси, как N2, Hg, меркаптаны и кислотные газы (например,CO2 и H2S), должны быть удалены до приемлемых уровней содержания. Чаще всего H2S должен быть удален до низких уровней содержания в предлагаемом для продажи продукте по соображениям охраны здоровья и безопасности, при концентрациях H2S в продукте менее 16 млн-1, менее 10 млн-1, менее 4 млн-1 или даже менее чем 1 млн-1. При продаже для транспортировки по трубопроводам, чтобы удовлетворять требованиям в отношении воспламеняемости и соответствия горелкам, может быть предпочтительным, чтобы содержание N2 и CO2 в продукте было менее 5 мол.%, менее 2 мол.% или предпочтительно менее 1,5 мол.%. Кроме того, когда очищенный продукт преобразуют в сжиженный природный газ (LNG), может быть предпочтительным, чтобы содержание СО 2 было менее 100 млн-1, менее 75 млн-1,или предпочтительно менее 50 млн-1, для предотвращения засорения криогенного теплообменника твердым CO2. Чистота продукта определяется как отношение, полученное делением числа молей желательных газов в потоке продукта на общее число молей газа в потоке продукта. Традиционные PSA-процессы не способны удалять загрязняющие примеси, такие как H2S, из находящихся под высоким давлением потоков подводимого сырья, такого как природный газ, до уровней порядка частей на миллион, в то же время обеспечивая высокую степень извлечения. Например, авторамKikkinides и др. удалось моделировать PSA-процесс, в котором очищался природный газ под давлением около 30 бар (3 МПа, абс.), содержащий 1000 млн-1 H2S и 5% СО 2, и получался поток продукта, содержащий 1 млн-1 H2S и 3% СО 2, в то же время с достижением степени извлечения свыше 95%. См.E.S. Kikkinides, V.I. Sikavitsas, и R.T. Yang, "Natural Gas Desulfurization by Adsorption: Feasibility and Multiplicity of Cyclic Steady States" ("Обессеривание природного газа путем адсорбции: реализуемость и сложность циклических установившихся режимов"), Ind. Eng. Chem. Res. 1995, vol. 34 (1), p. 255-262. Вакуумная регенерация при давлениях около 0,1 бар (0,01 МПа, абс.) требовалась для получения низких уровней содержания H2S в продукте. Еще одна традиционная PSA-система была продемонстрирована в промышленном масштабе для удаления СО 2 и H2S до низких уровней содержания в системе, спроектированной для удаления азота из природного газа при давлениях менее чем около 8 бар (0,8 МПа, абс.). См. каталоги продуктов от фирмы Guild Associates на веб-сайте http://www.moleculargate.com/landfill-gaspurification/MolecularGate Introduction.pdf. Также требуется вакуумная регенерация, и сообщается степень извлечения метана 93%. В то время как оба из этих способов демонстрируют высокую степень извлечения и высокую чистоту, производительность не может поддерживаться при высоких давлениях, как это необходимо для большинства крупномасштабных установок для переработки природного газа. Как степень извлечения, так и чистота продукта снижаются, когда традиционные процессы действуют при более высоком давлении подводимых сырьевых потоков. В дополнение, эти традиционные PSA-процессы не могут работать в короткоцикловых режимах, тем самым значительно ограничивая производительностьPSA-систем, что проявляется в более крупногабаритном и более дорогостоящем разделительном оборудовании. Многие факторы ограничивают способность сокращать продолжительность циклов в традиционных PSA-процессах, и в результате ограничиваются достижимые степень извлечения и чистота продукта. Например, высокие скорости пропускания подводимого сырьевого газа через адсорбентный слой или контактор в короткоцикловых процессах негативно влияют на производительность традиционныхPSA-процессов, как отмечено выше авторами Kikkinides et al., где концентрация H2S в продукте возрастает в 100 раз, когда скорость газа повышается на 25%. Настоящее изобретение создает возможность проведения PSA-процессов для высоконапорных потоков подводимого сырья, такого как природный газ, что обеспечивает высокую степень извлечения продукта и/или высокую чистоту продукта с использованием комбинаций разнообразных признаков,имеющих отношение к А) стадиям цикла (например, стадиям адсорбционного цикла, распределению интервалов времени, и уровням давления); В) структурам и материалам адсорбента и С) конфигурациям адсорбционной системы. Описываемая здесь уникальная комбинация признаков обусловливает производительность, ранее недостижимую PSA-процессами, и в результате настоящего изобретения может быть использована для экономичной обработки высоконапорного природного газа в крупном масштабе. Для начала, стадии цикла могут включать одну или более стадий адсорбционного цикла, распределение интервалов времени и уровни давления, которые описаны выше как признак А. Эти стадии цикла могут включать А 1) продолжительности короткоцикловой адсорбции; А 2) продувку выхлопным потоком (называемую рекуперативной продувкой); A3) продувку продуктом; А 4) вакуумную регенерацию; А 5) выбор надлежащих давлений продувки и А 6) многочисленные стадии выдувания. При работеPSA-систем с продолжительностями цикла порядка скорее секунд, нежели минут или часов, как в традиционных PSA-системах, количество адсорбента и общие габариты системы могут быть значительно сокращены. То есть, вес, стоимость и занимаемая производственная площадь короткоцикловыхPSA-систем являются значительно меньшими, чем в традиционных PSA-процессах. В дополнение, малый объем адсорбента и резервуаров в RC-PSA-системе позволяет проводить разнообразные продувки,которые повышают степень извлечения и/или чистоту продукта. Например, часть обогащенного загрязняющими примесями выхлопного потока из стадии сбрасывания давления в одном адсорбентном слое может быть использована для продувки еще одного адсорбентного слоя, чтобы вытеснить метан, захваченный в поровых пространствах между частицами адсорбента, или метан, остающийся в каналах адсорбентных контакторов. Метан, вытесненный во время стадии рекуперативной продувки, может быть вовлечен в рециркуляцию и уловлен, тем самым повышая степень извлечения метана RC-PSA-системы. Для более высокой чистоты продукта адсорбентный слой может быть продут с использованием части газообразного продукта, который подвергает адсорбентный слой воздействию среды с низким парциальным давлением загрязняющей примеси (например, H2S) и обеспечивает дополнительную десорбцию H2S из адсорбентного слоя. В результате этого во время последующей адсорбционной стадии может быть получен высокочистый метан. В альтернативном варианте, парциальное давление H2S в адсорбентном слое может быть снижено в стадии, в которой установку подвергают воздействию вакуума во время регенеративных стадий, чтобы дополнительно десорбировать H2S из адсорбентного слоя. Опять же, в последующей адсорбционной стадии может быть получен высокочистый метан. Для стадии продувки любого типа в адсорбционном цикле уровни давления должны быть выбраны для сокращения необходимого объема газового потока, вместе с любыми требованиями к сжатию, в то же время с сохранением желательного результата стадии продувки. Наконец, может быть выполнено сбрасывание давления в адсорбентном слое для десорбции загрязняющих примесей с использованием нескольких стадий выдувания при уровнях давления, выбранных в соответствии с входными давлениями присоединенного компрессорного оборудования, чтобы сократить число необходимых стадий и связанное с этим потребление энергии. Кроме того, разнообразные стадии в цикле могут включать начальное давление и конечное давление, как только стадия завершается. Например, сырьевой поток может быть подведен при давлении подачи, тогда как стадии сбрасывания давления могут снижать давление внутри адсорбентного слоя от начального давления при сбросе до конечного давления при сбросе. Подобным образом, каждая из стадий выдувания также может снижать давление внутри адсорбентного слоя от начального давления выдувания до конечного давления выдувания. Для восстановления давления в адсорбентном слое стадии восстановления давления могут увеличивать давление внутри резервуара для выполнения циклического адсорбционного процесса от начального давления повторной прессуризации до конечного давления повторной прессуризации. Дополнительные признаки могут включать структуры и материалы адсорбента, которые описаны выше как признак В. Эти признаки структуры и материала адсорбента включают В 1) выбор адсорбентного материала; В 2) структурированные адсорбентные контакторы; В 3) расположение адсорбентного материала внутри контактора и В 4) использование мезопористого наполнителя для уменьшения макропор и мезопор внутри контактора. Адсорбентный материал должен иметь высокую селективность в отношении компонента или компонентов, которые должны быть удалены, сравнительно с целевым продуктом. Кроме того, короткоцикловые процессы обеспечивают возможность кинетического разделения, в котором селективность усиливается в результате использования различий в скоростях диффузии для загрязняющих примесей относительно целевого продукта, который может представлять собой метан. В результате может быть достигнута высокая степень извлечения, поскольку адсорбируется только малая доля целевого продукта (например, метана для потока подводимого сырьевого природного газа), и теряется с загрязняющими примесями (например, кислотным газом для потока подводимого сырьевого природного газа). Для удаления H2S выбирают материалы, которые являются селективными для H2S, чтобы уменьшить адсорбцию как СО 2, так и метана. В RC-PSA-процессах скорости газа внутри адсорбентных слоев также могут быть довольно высокими благодаря большому объему потока и короткой продолжительности стадии. Поэтому структурированные адсорбентные контакторы с многочисленными, по существу, параллельными каналами, облицованными адсорбентным материалом, используются для минимизации падения давления. Кроме того, преимущество также обеспечивается расположением адсорбентного материала внутри адсорбентного контактора. Например, как H2S, так и СО 2 могут быть удалены до низких уровней содержания созданием контактора с первой секцией, содержащей материал, селективный для удаления H2S, и второй секцией, содержащей адсорбентный материал, селективный для удаления СО 2 (например, композитный адсорбентный слой). Во время регенерации композитного адсорбентного слоя СО 2, десорбированный из второй секции, протекает через первую секцию и производит продувку для удаления H2S из первой секции адсорбентного слоя, которая может включать, по существу, весь адсорбированный H2S. В результате на последующей адсорбционной стадии из RC-PSA-системы может быть получен метановый продукт с содержанием менее 4 млн-1, или менее 10 млн-1 H2S и менее 1,5% CO2. Более того, поровые пространства между частицами адсорбента внутри структурированного адсорбентного контактора могут быть заполнены наполнителем с использованием материалов разнообразных типов, которые обеспечивают возможность диффузии в частицы адсорбента и из них, но, по существу,сокращают объем порового пространства во всей системе в целом. В результате применения мезопористого наполнителя меньшее количество метана остается захваченным в адсорбентном слое контактора после адсорбционной стадии, и поэтому меньшее количество метана теряется с кислотным газом, приводя к более высокой совокупной степени извлечения метана. Еще другие дополнительные признаки включают признаки конфигурации адсорбционной системы,которые описаны выше как признак С. Эти признаки включают одно или более из С 1) последовательного расположения RC-PSA и С 2) уравнительных резервуаров, специально предназначенных для каждой уравнительной стадии. В дополнение к описанным выше определенным признакам или в качестве альтернативы им, многочисленные RC-PSA-системы могут быть использованы в последовательном расположении для повышения степени извлечения. Первая RC-PSA-система обрабатывает подводимый сырьевой поток (например, природный газ) для получения высокочистого продукта, и выхлопной поток из первой RC-PSA-системы направляется во вторую RC-PSA-систему для удаления продукта из потока кислотного газа, чтобы сократить потерю продукта с потоком кислотного газа и повысить совокупную степень извлечения продукта. Кроме того, дополнительное усовершенствование может включать применение в RC-PSA-системе уравнительных резервуаров. Например, каждый адсорбентный слой в RC-PSAсистеме может включать уравнительный резервуар для каждой уравнительной стадии, чтобы более эффективно управлять регенерацией в процессе. То есть, уравнительные резервуары могут быть использованы для сокращения времени, связанного со сбрасыванием давления и восстановлением давления в адсорбентном слое во время цикла. В результате может быть сокращена продолжительность цикла, тем самым улучшая производительность RC-PSA-системы и уменьшая ее габариты. Описанные выше признаки могут быть скомбинированы в различных конфигурациях для повышения производительности RC-PSA-системы для разделений при высоких давлениях. Например, PSAсистема с высокой степенью извлечения может быть достигнута комбинацией таких признаков, как продолжительности короткоцикловой адсорбции; продувка выхлопным потоком; выбор адсорбентного материала; структурированные адсорбентные контакторы; и использование мезопористого наполнителя для сокращения макропор и мезопор внутри контактора. Производительность могла бы быть дополнительно повышена добавлением таких признаков, как выбор правильных давлений продувки; многочисленные стадии выдувания и уравнительные резервуары. В качестве еще одного примера, PSA-система высокой чистоты может быть сконструирована сочетанием таких признаков, как продолжительности короткоцикловой адсорбции и продувка продуктом; вакуумная регенерация; выбор адсорбентного материала; структурированные адсорбентные контакторы; и расположение материала внутри контактора. Производительность могла бы быть дополнительно увеличена добавлением таких признаков, как многочисленные стадии выдувания и уравнительные резервуары. В качестве еще одного примера, как высокая степень извлечения, так и высокая чистота могли бы быть достигнуты сочетанием таких признаков, как продолжительности короткоцикловой адсорбции; продувка выхлопным потоком; продувка продуктом; выбор адсорбентного материала; структурированные адсорбентные контакторы; расположение материала внутри контактора и использование мезопористого наполнителя для сокращения макропор и мезопор внутри контактора. Производительность могла бы быть дополнительно увеличена добавлением таких факторов, как многочисленные стадии выдувания, и/или последовательное расположение RC-PSA-системы, и/или уравнительные резервуары, специально предназначенные для каждой уравнительной стадии. В качестве еще одного примера как высокая степень извлечения, так и высокая чистота могли бы быть достигнуты комбинированием таких факторов, как продолжительности короткоцикловой адсорбции; продувка выхлопным потоком; вакуумная регенерация; Выбор адсорбентного материала; структурированные адсорбентные контакторы; расположение материала внутри контактора и использование мезопористого на-7 024199 полнителя для сокращения макропор и мезопор внутри контактора. Производительность могла бы быть дополнительно увеличена добавлением таких факторов, как многочисленные стадии выдувания, и/или последовательное расположение RC-PSA-системы, и/или уравнительные резервуары, специально предназначенные для каждой уравнительной стадии Дополнительные подробности конкретных признаков представлены в фигурах и в последующих абзацах. В частности, дополнительные подробности относительно признаков стадий цикла представлены на фиг. 1-6 и связанных с ними абзацах. Циклические адсорбционные процессы согласно настоящему изобретению являются предпочтительными для выполнения с продолжительностями короткоцикловой адсорбции или в режиме, названном выше как признак А 1. Традиционные системы адсорбции при переменном давлении являются дорогостоящими в эксплуатации и требуют большой производственной площади, чтобы быть способными удалять значительные количества СО 2 из потоков природного газа. Кроме того, традиционные установки адсорбции при переменном давлении имеют продолжительности циклов,превышающие одну минуту, типично более, чем от двух до четырех минут. Напротив, общие продолжительности цикла для RC-PSA-систем типично составляют менее 90 с, предпочтительно менее 30 с, менее 20 с, более предпочтительно менее 15 с и еще более предпочтительно менее 10 с. Одно преимуществоRC-PSA-технологии состоит в значительно более эффективном использовании адсорбентного материала. Количество адсорбента, необходимое для RC-PSA-технологии, может составлять лишь часть от того, что требуется для традиционной PSA-технологии, чтобы достигнуть такой же производительности разделения. В результате этого занимаемая производственная площадь, капиталовложения и количество активного адсорбента, необходимого для RC-PSA, обычно являются значительно меньшими, чем таковые для традиционной PSA-системы, обрабатывающей эквивалентное количество газа. Например, RC-PSAустановка с 3-секундным интервалом продолжительности адсорбции для цикла может использовать только 5 вес.% адсорбента, применяемого в традиционной PSA с одноминутным интервалом продолжительности адсорбции для цикла. Патенты США 6406523; 6451095; 6488747; 6533846 и 6565635 описывают разнообразные аспекты RC-PSA-технологии. Меньшие объемы оборудования, связанного с RC-PSA-технологией, улучшают эксплуатационную гибкость, что может быть использовано для дополнительной интенсификации процесса. Например, для повышения производительности системы в RC-PSA-системе могут быть использованы стадии продувки. Стадия продувки может включать применение выхлопного газа, который отмечен выше как признак А 2,для повышения степени извлечения метана для RC-PSA-системы. В этой стадии, называемой рекуперативной продувкой, газообразный поток с низкими концентрациями газообразных продуктов может быть использован для продувки адсорбентного слоя после адсорбционной и уравнительной стадий цикла. Этот обогащенный загрязняющими примесями продувочный поток вытесняет метан из проточных каналов и поровых пространств между частицами адсорбента и/или в структуре контактора таким образом,что метан может быть вовлечен в рециркуляцию или уловлен, и обработан иным путем, тем самым сокращая потерю газообразных продуктов с выхлопным потоком. Эта стадия продувки значительно повышает степень извлечения газообразных продуктов. Кроме того, также может быть оптимизировано давление продувки, что отмечено выше как признак А 5, таким образом, что давление является достаточно низким для снижения величины расхода потока продувки, подаваемого для эффективного вытеснения из каналов, но достаточно высоким, чтобы предотвращать десорбцию загрязняющих примесей из адсорбентного слоя в продувочный поток. Предпочтительным источником для рекуперативной продувки является отведение части выхлопного потока из стадий выдувания, который -затем подвергают сжатию до давления, необходимого для стадии продувки. Также могут быть предусмотрены альтернативные источники для продувки, такие как N2 или другие газы, по существу, не содержащие метана, которые могут быть получены из других технологических установок. Примерные давления продувки могут составлять от 50 бар (5 МПа, абс.) до 1 бар (0,1 МПа, абс.),что может зависеть от разнообразных факторов. Продувка еще одного типа, которая может быть использована в RC-PSA-системах для повышения чистоты продукта, представляет собой продувку продуктом, которая отмечена выше как признак A3, в которой чистый газ, по существу, не содержащий загрязняющих примесей (например, СО 2 и H2S), используют для очистки адсорбентного слоя во время: регенерации. Сниженное парциальное давление загрязняющих примесей в проточных каналах адсорбентного слоя создает движущую силу, которая содействует десорбции загрязняющих примесей, позволяя счистить адсорбентный материал до большей степени, чем это возможно при простом колебании давления до атмосферного давления. В результате этого сокращается проникновение загрязняющих примесей в поток продукта во время последующего адсорбционного цикла и получается более чистый продукт. Неограничивающие примеры таких газов (т.е. "чистого газа") включают метан и азот, течение которых поддерживают через параллельные каналы по направлению противотока относительно направления подачи сырья во время по меньшей мере части стадий десорбции в процессе. Предпочтительным источником чистого газа является применение части потока продукта, давление которого снижают до уровня, приемлемого для использования при продувке. Давление продувки выбирают, как правило, на уровне самого низкого давления при сбросе, хотя может быть использован любой уровень давления между наинизшим давлением при сбросе и давлением подачи сырья. Давление продувки главным образом выбирают для сокращения величины расхода потока, требуемого для продувки. Еще один способ повышения чистоты продукта из RC-PSA-системы состоит в применении вакуумной регенерации (как отмеченной выше признаком: А 4). В некоторых вариантах исполнения адсорбентный слой может быть подвергнут воздействию вакуума при давлении, большем или равном 0,1 бар(0,01 МПа, абс.), большем или равном 0,25 бар (0,025 МПа, абс.) или большем или равном 0,5 бар(0,05 МПа, абс.), во время стадии выдувания, для дополнительного снижения парциального давления загрязняющих примесей в проточных каналах. Этим создается увеличенная движущая сила, которая содействует десорбции загрязняющих примесей, дополнительно уменьшая концентрацию загрязняющих примесей в адсорбентном слое в конце стадии выдувания. В результате этого во время последующего адсорбционного цикла получается высокочистый газообразный продукт. Если загрязненный выхлопной поток из RC-PSA-системы должен быть подвергнут сжатию перед последующим использованием или утилизацией, то во время регенерации может быть предпочтительным применение многочисленных стадий выдувания, отмеченных выше как признак А 6. В одном варианте исполнения сбрасывание давления в адсорбентном слое проводят в многочисленных стадиях выдувания, где каждая стадия снижает давление в адсорбентном слое от начального давления до конечного давления. Уровни давления для стадий выдувания выбирают, чтобы снизить расход энергии на сжатие выхлопного потока, в то же время по-прежнему снижая давление до минимального давления в системе,чтобы обеспечить возможность максимальной десорбции загрязняющих примесей. Например, в RC-PSAсистеме с минимальным давлением выдувания в 1 бар (0,1 МПа, абс.) конечные давления выдувания могут быть выбраны около 1 бар (0,1 МПа, абс.), 3 бар (0,3 МПа, абс.) и 9 бар (0,9 МПа, абс.), поскольку типичные CO2-компрессоры работают со степенями повышения давления около 3. При такой конфигурации общее потребление энергии для сжатия потоков выдувания является гораздо меньшим, чем мощность, требуемая для сжатия всего потока от давления 1 бар (0,1 МПа, абс.). В других вариантах исполнения, которые включают стадию вакуумного выдувания для получения высокочистого продукта, применение многочисленных стадий выдувания сокращает размеры вакуумной системы, поскольку большая часть загрязняющих примесей уходит в выхлопной поток при давлениях выше атмосферного давления(1 бар (0,1 МПа, абс Например, в RC-PSA-системе с минимальным давлением 0,5 бар (0,05 МПа, абс.) большая часть загрязняющих примесей выводится посредством стадий выдувания при давлениях 1,5 бар(0,015 МПа, абс.) и 4,5 бар (0,045 МПа, абс.) так, что общий расход энергии на сжатие сводится к минимуму и становятся минимальными габариты вакуумной системы для выхлопного потока с давлением 0,5 бар (0,05 МПа, абс.). В качестве дополнительного усовершенствования стадий выдувания в адсорбционном цикле сбрасывание давления в стадиях выдувания может быть выполнено как с сырьевой, так и с продуктовой сторон адсорбентного слоя. По сравнению со сбрасыванием давления только с одного конца адсорбентного слоя, этим сокращается время, необходимое для стадий выдувания. В результате этого сокращается общая продолжительность цикла, что повышает производительность RC-PSA-системы. В альтернативном варианте, для фиксированной продолжительности выдувания сбрасывание давления с использованием обоих концов адсорбентного слоя позволяет достигнуть более низких уровней давления, что дополнительно очищает слой и создает более чистый продукт на последующей адсорбционной стадии. Сбрасывание давления из обоих концов также повышает степень извлечения и чистоту продукта,когда в адсорбционной системе используют композитный адсорбентный слой. В одном примере стадия выдувания может быть выполнена из обеих сырьевой и продуктовой сторон композитного адсорбентного слоя, содержащего первый участок слоя, имеющий аминофункционализированный адсорбентный материал для удаления H2S, и второй участок слоя, имеющий адсорбентный слой из цеолита типа DDR для удаления СО 2 из природного газа. Во время адсорбционной стадии газ из подводимого сырьевого потока,который может быть назван сырьевым газом, сначала контактирует с аминофункционализированным адсорбентным слоем, и поглощение H2S происходит раньше, чем сырьевой газ будет контактировать сDDR-адсорбентным слоем, где происходит внедрение СО 2. Во время стадии выдувания выдувной поток из продуктового конца адсорбентного слоя, по существу, не содержит H2S и может быть использован для стадии рекуперативной продувки, чтобы повысить степень извлечения желательного продукта без повторного введения H2S в систему, что также позволяет получать метан во время последующей адсорбционной стадии, который, по существу, не содержит H2S. В дополнение, поскольку продуктовая сторона адсорбентного слоя, по существу, не содержит H2S, поток продукта во время последующей адсорбционной стадии может быть, по существу, свободным от H2S. Выдувной поток из сырьевого конца адсорбентного слоя содержит значительные количества адсорбированного H2S и может образовывать выхлопной поток. В дополнение к признакам стадий цикла, для интенсификации процесса могут быть использованы разнообразные признаки структуры и материала адсорбента. Например, выбор надлежащего адсорбентного материала для RC-PSA-системы, который отмечен выше как признак В 1, является одним из важнейших факторов в получении системы с высокой степенью извлечения, высокой чистотой продукта или ими обеими. Для достижения, по существу, полного удаления загрязняющих примесей, таких как кислотный газ, из потоков природного газа выбирают адсорбентный материал, который является селективным для удаляемых загрязняющих примесей, но имеет низкую способность поглощать продукт. Например, адсорбентный материал может быть селективным к одному или более компонентам кислотных газов, но имеет низкую способность поглощать как метан, так и более тяжелые углеводороды (например,углеводороды с числом содержащихся атомов углерода, равным двум или выше чем около двух). Предпочтительные адсорбенты для удаления кислотных газов выбирают из группы, состоящей из мезопористых или микропористых материалов, имеющих или не имеющих функциональные группы для химических реакций с кислотными газами. Примеры материалов без функциональных групп включают катионные цеолиты и станносиликаты. Функционализированные материалы, которые химически реагируют с H2S и СО 2, проявляют значительно повышенную селективность в отношении H2S и СО 2 сравнительно с углеводородами. Кроме того, эти материалы не катализируют нежелательные реакции с углеводородами, которые происходят на кислотных цеолитах. Соответственно этому, могут быть предпочтительными функционализированные мезопористые адсорбенты, в которых их сродство к углеводородам дополнительно снижено по сравнению с нефункционализированными материалами с мелкими порами,такими как цеолиты. В альтернативном варианте, адсорбция тяжелых углеводородов может быть подавлена кинетически с использованием мелкопористых функционализированных адсорбентных материалов,в которых диффузия тяжелых углеводородов является медленной по сравнению с H2S и СО 2. Неограничивающие примеры функциональных групп, пригодных для применения здесь, включают первичные,вторичные, третичные и другие непротоногенные основные группы, такие как амидины, гуанидины и бигуаниды. Кроме того, эти материалы могут быть функционализированы функциональными группами двух или более типов. Другие неограничивающие примеры предпочтительных селективных адсорбентных материалов для применения в приведенных здесь вариантах исполнения включают микропористые материалы, такие как цеолиты, AlPO (алюмофосфатные цеолиты), SAPO (кремнеалюмофосфатные молекулярные сита), MOF(металлоорганические каркасы), ZIF (цеолитные имидазолятные каркасы, такие как ZIF-7, ZIF-9, ZIF-8,ZIF-11, и т.д.) и углероды, а также мезопористые материалы, такие как аминофункционализированные МСМ-материалы, материалы типа S3A, KIT. Для кислотных газов, таких как H2S и CO2, которые обычно находятся в потоках природного газа, также предпочтительны такие адсорбенты, как катионные цеолиты, аминофункционализированные мезопористые материалы, станносиликаты, углероды. В качестве одного примера для удаления СО 2 из природного газа в определенных вариантах исполнения может быть составлен адсорбент со специфическим классом цеолитных материалов с 8-членными кольцами, который имеет кинетическую селективность в отношении СО 2 сравнительно с метаном. Кинетическая селективность цеолитных материалов с 8-членными кольцами этого класса позволяет СО 2 быстро проникать (диффундировать) в кристаллы цеолита, в то же время затрудняя транспорт метана таким образом, что можно избирательно отделять СО 2 от смеси СО 2 и метана. Для удаления СО 2 из природного газа цеолитные материалы с 8-членными кольцами этого специфического класса имеют соотношение"Si/Al" от около 2 до около 1000, предпочтительно от около 10 до около 500 и более предпочтительно от около 50 до около 300. Следует отметить, что термин "Si/Al", как используемый здесь, определяется как молярное отношение оксида кремния к оксиду алюминия в структуре цеолита. Предпочтительный класс цеолитов с 8-членными кольцами, которые пригодны для применения здесь, позволяют СО 2 входить во внутреннюю пористую структуру через 8-членные окна таким образом, что отношение коэффициентов однокомпонентной диффузии CO2 и метана (т.е. DCO2/DCH4) составляет более 10, предпочтительно более чем около 50, более предпочтительно больше чем около 100 и еще более предпочтительно свыше 200. Предпочтительным адсорбентным материалом является Deca-Dodecasil 3R (DDR), который представляет собой цеолит. В контролируемых равновесием циклических адсорбционных процессах селективность по большей части обеспечивается характеристиками равновесной адсорбции адсорбентом, и изотерма конкурентной адсорбции легкого продукта (такого как метан) в микропорах или свободном объеме адсорбента не является преимущественной. В кинетически контролируемых циклических адсорбционных процессах селективность по большей части обусловливается диффузионными характеристиками адсорбента, и коэффициент диффузионного транспорта в микропоры и в свободный объем адсорбента для легких частиц является меньшим, чем для более тяжелых частиц (таких как СО 2 или H2S). Кроме того, в кинетически контролируемых циклических адсорбционных процессах с микропористыми адсорбентами диффузионная селективность может возникать вследствие различий диффузии в микропоры адсорбента, или из селективного диффузионного поверхностного сопротивления в кристаллах или частицах, которые составляют адсорбент. Когда используют кинетически селективный адсорбент, то предпочтительно формировать адсорбентный слой из частиц адсорбента в основном с однородными размерами. В одном предпочтительном варианте исполнения частицы имеют гранулометрический состав, как определяемый с помощью сканирующего электронного микроскопа так, что среднеквадратичное отклонение характеристической величины составляет менее 90% от среднего размера. В одном более предпочтительном варианте исполнения среднеквадратичное отклонение может быть менее 50% от среднего размера и наиболее предпочтительно менее 25% от среднего размера. Кроме того, когда адсорбент является кинетически селективным, для охарактеризования производительности адсорбента может быть использована характеристическая константа времени диффузии. Для целей настоящего изобретения выбирают следующую константу времени:tau(i) для L2/D(i), чтобы охарактеризовать кинетическое поведение адсорбента, где L представляет характеристический размер (м) каждой адсорбентной частицы или кристалла и D(i) (м 2/с) представляет коэффициент диффузии каждой молекулярной частицы (i) в адсорбенте. Предпочтительно, чтобы значениеtau для целевого газа (такого как СО 2) составляло менее чем 1/20 от значения tau для основных компонентов в сырьевом потоке, от которого его отделяют. Более предпочтительно значение tau может быть менее 1/50 от значения для основных компонентов в сырьевом потоке, от которого его отделяют. Наиболее предпочтительно значение tau составляет менее 1/50 от значения для основных компонентов в сырьевом потоке, от которого его отделяют. Когда адсорбент имеет кинетическую селективность, также является предпочтительным, чтобы характеристические размеры частиц адсорбента выбирались таким образом, что значение tau составляет менее 1/4 продолжительности адсорбционной стадии и более 1/40000 продолжительности адсорбционной стадии. Более предпочтительно значение tau составляет менее 1/10 продолжительности адсорбционной стадии и более 1/4000 продолжительности адсорбционной стадии. Еще один признак структуры и материала адсорбента может включать адсорбентный слой, представляющий собой структурированный адсорбентный контактор, который отмечен выше как признак В 2. Структурированный адсорбентный контактор может быть использован для создания большой площади поверхности для массопереноса между газами в разнообразных потоках и адсорбентным материалом, в то же время со снижением сопротивления потоку текучей среды, чтобы уменьшить падение давления в пределах адсорбентного слоя при высоких скоростях течения текучей среды, имеющих место во время быстрых стадий адсорбционного цикла. В практической реализации настоящего изобретения могут быть применены адсорбентные структуры нескольких неограничивающих типов, включающие монолитную структуру, спиральную намотку и полое волокно. Примерные варианты исполнения контакторов приведены на фиг. 1-6. Эти структуры преимущественно могут быть сформированы непосредственно из матрицы, смешанной из адсорбента, мезопористого наполнителя и термальной кассы, с использованием такого конструкционного материала, как керамика, стекло или металл, который покрыт матрицей из адсорбента и мезопористого наполнителя. Для некоторых определенных вариантов применения мезопористый наполнитель и термальная масса могут не понадобиться. Монолитные структуры типично формируют экструзией материалов через фильеры с образованием микроканалов, хотя возможны другие методы,такие как диффузионное связывание протравленных металлических пластин. Методы формирования могли бы включать экструзию смешанной матрицы из адсорбента, мезопористого наполнителя и термальной массы, или экструзию конструкционного материала, такого как керамика, металл или пластик, с последующим нанесением тонкого покрытия из матрицы, смешанной из материалов адсорбента и мезопористого наполнителя, на внутреннюю сторону микроканалов в монолите. Дополнительно, монолитная структура могла бы быть сформирована диффузионным связыванием пакета металлических пластин, в которых перед связыванием были протравлены проточные каналы, и затем на внутренность проточных каналов нанесено тонкое покрытие матрицы из адсорбента и мезопористого наполнителя. В одном предпочтительном варианте исполнения адсорбент внедряют в контактор с параллельными каналами. "Контакторы с параллельными каналами" определяются здесь как подгруппа адсорбентных контакторов, включающая структурированные (сконструированные) контакторы, в которых в структуре сформированы, по существу, параллельные проточные каналы. Параллельные проточные каналы подробно описаны в патентных публикациях Соединенных Штатов 2008/0282892 и 2008/0282886, обе из которых включены здесь ссылкой. Эти проточные каналы могут быть сформированы разнообразными путями, и, в дополнение к адсорбентному материалу, структура может содержать такие компоненты, как материалы подложки, теплоотводящие материалы, и компоненты для сокращения пустот. Самые многообразные монолитные формы могут быть образованы непосредственно с помощью экструзионных процессов. Один пример цилиндрического монолита схематически показан здесь на фиг. 1. Цилиндрический монолит 1 содержит многочисленные параллельные проточные каналы 3, которые проходят по всей длине монолита. Эти проточные каналы 3 могут иметь диаметры (просветы каналов) от около 5 до около 1000 мкм, предпочтительно от около 50 до около 250 мкм, пока все каналы в данном контакторе имеют, по существу, одинаковый размер просвета канала. Каналы могли бы иметь разнообразные формы, включающие, но не ограничивающиеся таковыми, круглые, квадратные, треугольные и шестиугольные.Пространство между каналами занято адсорбентом 5. Как показано на фиг. 1, каналы 3 занимают около 25% объема монолита и адсорбент 5 занимает около 75% объема монолита. Адсорбент 5 может занимать от около 50 до около 98% объема монолита. Эффективная толщина адсорбента может быть определена из объемных долей, занимаемых адсорбентом 5 и структурой каналов, как: Эффективная толщина адсорбента = 1/2 диаметра канала(объемная доля адсорбента/объемная доля каналов). Фиг. 2 здесь представляет вид в разрезе, проведенном вдоль продольной оси проточных каналов 3,протяженных по длине монолита, со стенками проточных каналов, сформированными полностью из адсорбента 5 плюс связующее средство, мезопористый наполнитель и теплоотводящий материал. Схематическое увеличенное изображение маленького участка поперечного сечения адсорбентного слоя 5 показано здесь на фиг. 3. Адсорбентный слой 5 состоит из микропористого адсорбента или полимерных частиц 7; твердых частиц (термальная масса) 9; которые действуют как теплоотводы, блокатора 13 и открытых мезопор и макропор 11. Как показано, микропористый адсорбент или полимерные частицы 7 занимают около 60% объема адсорбентного слоя и частицы термальной массы 9 занимают около 5% объема. При таком составе общий объем пустот (проточных каналов) составляет около 55% объема,занимаемого микропористым адсорбентом или полимерными частицами. Объем микропористого адсорбента 5 или полимерных частиц 7 может варьировать от около 25 до около 98% объема адсорбентного слоя. На практике объемная доля твердых частиц 9, используемых для поглощения тепловой энергии и ограничения повышений температуры, варьирует от около 0 до около 75%, предпочтительно от около 5 до около 75% и более предпочтительно от около 10 до около 60% объема адсорбентного слоя. Мезопористый неадсорбирующий наполнитель, или блокатор 13, заполняет желательную часть пространства или полостей, оставленных между частицами, таким образом, что объемная доля открытых мезопор и макропор 11 в адсорбентном слое 5 составляет менее чем около 30 об.%, или менее чем около 20 об.%, или менее 10 об.%. Когда монолитный контактор используют в процессе разделения газов, который основывается на кинетическом разделении (преимущественно контролируемом диффузией), то предпочтительно, чтобы частицы 7 микропористого адсорбента, или полимера, имели, по существу, одинаковые размеры. Предпочтительно, чтобы среднеквадратичное отклонение объема отдельных частиц 7 микропористого адсорбента, или полимера, было менее 100% от среднего объема частиц для кинетически контролируемых процессов. В одном более предпочтительном варианте исполнения среднеквадратичное отклонение объема отдельных частиц 7 микропористого адсорбента, или полимера, составляет менее 50% от среднего объема частиц, или еще более предпочтительно, менее 25% от среднего объема частиц. Гранулометрический состав для цеолитных адсорбентов может регулироваться методом, применяемым для: синтеза этих частиц. Также возможно разделение предварительно синтезированных частиц микропористого адсорбента по размеру с использованием таких методов, как колонна для гравитационного осаждения. Фиг. 4 здесь показывает увеличенный вид поперечного сечения небольшого участка контактора с параллельными каналами. Эта фигура показывает адсорбентный материал адсорбентного слоя 5, покрывающий внутренность структуры 9 адсорбентного слоя с образованием проточных газовых каналов 3. Адсорбентный слой 5 может содержать или может не содержать мезопористый наполнитель и другие материалы. Фиг. 5 здесь показывает адсорбентный контактор в форме спиральной намотки, пригодный для применения в настоящем изобретении. Структуры со спиральной намоткой обычно изготавливают наматыванием единственного плоского листа в сборный узел. Предпочтительно, чтобы сквозь лист не проходили никакие протоки. Промежутки между слоями спирально намотанного листа могут быть сформированы любым подходящим способом. Могут быть использованы следующие неограничивающие способы: применение продольных распорных проволок; создание углублений, или гофрирование, листа; и наклеивание частиц однородного размера на лист. Неограничивающие способы формирования включают стадии, на которых проводят спиральную намотку единственного листа, изготовленного из матрицы, смешанной из адсорбента, мезопористого наполнителя и термальной массы; наносят тонкое покрытие из матрицы, смешанной из адсорбента и мезопористого наполнителя, на тонкий металлический лист, и затем выполняют спиральную намотку листа; проводят спиральную намотку тонкого металлического листа или сетки, и затем наносят тонкое покрытие из матрицы, смешанной из адсорбента и мезопористого наполнителя, на полученный спиральной намоткой сборный узел. Фиг. 6 здесь показывает адсорбентный контактор, составленный из полых волокон. Структуры из полых волокон могут быть выполнены объединением в пучок многочисленных пустотелых трубок, подобно пучку трубок в кожухотрубном теплообменнике, для создания сборного узла. Полые волокна могут быть заделаны на одном конце в заливочный материал, такой как эпоксидная смола, который совместим с материалом полых волокон. Поток газа может проходить либо внутри, либо снаружи полых волокон, но в любом случае параллельно продольной оси сборного узла. Предпочтительно, чтобы газ не протекал сквозь стенки полых волокон. Один предпочтительный способ получения адсорбентной структуры из полых волокон состоит из стадий, на которых сначала изготавливают полые волокна из матрицы, смешанной из адсорбента,мезопористого наполнителя и термальной массы, после чего объединяют полые волокна в пучок, затем заполняют пространство вокруг наружной стороны волокон заливочным материалом так, что газ может протекать только через внутренность волокон. Еще один способ может включать стадии, на которых сначала изготавливают полые волокна из матрицы, смешанной из адсорбента, мезопористого наполнителя и термальной массы, затем объединяют полые волокна в пучок и заделывают оба конца волокон в заливочный материал таким образом, что газ протекает как внутри, так и снаружи волокон. Еще один дополнительный способ получения структур из полых волокон состоит из стадий, в которых наносят тонкое покрытие из матрицы, смешанной из адсорбента и мезопористого наполнителя, на внутренность пустотелых трубок малого диаметра, выполненных из неограничивающего материала, выбранного из группы, состоящей из металла (например, гиподермических игл), керамики, пластика и т.д.,затем заполняют пространство вокруг наружной стороны волокон заливочным материалом, чтобы газ мог протекать только внутри волокон. И еще один дополнительный способ получения структуры состоит из стадий, на которых изготавливают сборный узел из мелких пустотелых трубок, выполненных из материала, выбранного из металла,керамики, пластика, и т.д., и затем заделывают оба конца в заливочный материал, или соединяют сваркой, затем наносят тонкое покрытие внутри трубок из матрицы, смешанной из адсорбента и мезопористого наполнителя. Кроме того, еще один способ состоит из стадий, в которых изготавливают сборный узел тем же путем, как отмечено в предыдущем способе, но с тем исключением, что матрицу, смешанную из адсорбента и мезопористого наполнителя, наносят в виде тонкого покрытия как на внутреннюю, так и на наружную стороны полых волокон. Эти структурированные контакторы могут быть использованы для формирования единственного адсорбентного слоя для RC-PSA-системы разнообразными путями. В одном способе адсорбентный слой состоит из единственного структурированного адсорбентного контактора, который изготовлен по длине адсорбентного слоя. В еще одном способе адсорбентный слой может состоять из многочисленных более коротких сегментов структурированных контакторов, которые собраны в пакет друг с другом для образования полной длины адсорбентного слоя. В этом способе сегменты структурированных контакторов могут быть смонтированы с зазором или без зазоров между смежными сегментами. Создание маленького зазора между смежными сегментами, предпочтительно менее 1000 мкм или предпочтительно менее 500 мкм и еще более предпочтительно меньше 200 мкм, позволяет перераспределять газ среди сегментов,что может ослабить любой эффект неравномерного распределения внутри проточных каналов структурированных контакторов. Для вариантов исполнения, в которых используют более чем один адсорбентный материал, расположение различных адсорбентных материалов внутри структурированного адсорбентного слоя, которое отмечено выше как признак В 3, может влиять на производительность RC-PSA-системы. В этих вариантах исполнения композитный адсорбентный слой может быть использован с двумя или более адсорбентами, каждый из которых преимущественно адсорбирует различные загрязняющие примеси из сырьевого потока. Композитный адсорбентный слой может быть сформирован несколькими различными путями,такими как применение сегментных структурированных контакторов, каждый с иными нанесенными на них адсорбентными материалами. В качестве одного примера, для удаления СО 2 и H2S из природного газа может быть использован композитный адсорбентный слой, где первый сегмент слоя содержит аминофункционализированный адсорбент на носителе из KIT-6 (мезопористого кремнезема) для удаленияH2S, и остальные сегменты, которые составляют адсорбентный слой, содержат DDR-адсорбент для удаления СО 2. В этом варианте исполнения H2S удаляется из сырьевого потока, когда он проходит через первый сегмент, и затем CO2 удаляется из сырьевого потока, когда он проходит через остальные сегменты адсорбентного слоя. Преимущество применения композитных слоев в этом эксплуатационном режиме состоит в том, что десорбированная загрязняющая примесь из одного сегмента адсорбентного слоя может создавать парциальное давление продувки для других сегментов адсорбентного слоя, чтобы стимулировать удаление других загрязняющих примесей из соответствующих адсорбентных слоев. В отношении предшествующего примера, во время стадии выдувания десорбированный из содержащих DDR сегментов слоя CO2 может протекать в противоточном режиме через первый сегмент, содержащий аминофункционализированный адсорбент, для создания парциального давления продувки, которая, по существу, не содержит H2S, для десорбирования H2S из первого сегмента композитного адсорбентного слоя. Этим путем первый сегмент композитного слоя может быть очищен до низких уровней содержания H2S,и в результате этого во время последующих адсорбционных стадий может быть получен поток высокочистого продукта с уровнями содержания H2S порядка частей на миллион. Следует отметить, что эта эффективная продувка адсорбирующего H2S сегмента композитного слоя может быть более эффективной, если сероводороду (H2S) не позволяют проникать в DDR-сегменты слоя во время адсорбционной стадии, чтобы CO2 в DDR-сегментах слоя, по существу, не содержал H2S. Два адсорбентных материала внутри адсорбентного слоя также могут быть размещены, будучи равномерно диспергированными по всем адсорбентным слоям, при условии, что количество одного адсорбентного материала является значительно большим, чем количество другого адсорбентного материала. Например, для удаления H2S и CO2 из природного газа, как описано выше, требуется примерно в десять раз больше DDR, чем аминофункционализированного материала. В одном предпочтительном варианте исполнения количество селективного к H2S абсорбента является меньшим, чем пятикратное количество селективного в отношении СО 2 абсорбента. Если эти материалы однородно смешаны и распределены вдоль адсорбентного контактора, то достигается такой же результат, в котором СО 2 создает парциальное давление продувки аминофункционализированного материала, распределенного в адсорбентном слое, и,по существу, вычищает H2S, обеспечивая возможность получения высокочистого метана на последующей адсорбционной стадии. Степень извлечения продукта RC-PSA-системой также может быть повышена применением мезопористого наполнителя, как отмечено выше в признаке В 4, который может быть использован для сокращения порового пространства в адсорбентном слое. В результате этого сокращается количество газообразных продуктов, захваченных в поровом пространстве, так что меньшее количество газообразного продукта теряется с загрязняющими примесями во время регенерации, тем самым улучшая степень извлечения газообразных продуктов. Применение мезопористого наполнителя описано в Публикациях патентных заявок США 2008/0282892, 2008/0282885 и 2008/028286, каждая из которых включена здесь ссылкой во всей своей полноте. Невымываемое поровое пространство, присутствующее внутри стенки канала в адсорбенте, может определяться общим объемом, занимаемым мезопорами и макропорами. Мезопоры определяются правилами ИЮПАК как поры с размерами в диапазоне величин от 20 до 500 ангстрем (2-50 нм). Макропоры определяются здесь как поры с размерами свыше 500 ангстрем(50 нм) и менее 1 мкм. Поскольку проточные каналы являются более крупными, чем 1 мкм по величине,они не рассматриваются как часть макропорового объема. Невымываемое поровое пространство определяется здесь как открытый поровый объем, занятый порами в адсорбенте, которые имеют диаметр между 20 ангстремами (2 нм) и 10000 ангстремами (1 мкм), деленный на общий объем контактора, который занят адсорбентным материалом, включая связанные мезопоры и макропоры в адсорбентном материале. Невымываемое поровое пространство, далее совокупно называемое мезопорами, может быть сокращено заполнением мезопор между частицами для уменьшения открытого объема, в то же время обеспечивая быстрый транспорт газа через адсорбентный слой. Это заполнение невымываемого порового пространства желательно для снижения до приемлемых уровней количества потерь желательного продукта во время стадии быстрой десорбции, а также; для обеспечения высокой степени чистоты адсорбентного слоя после десорбции. Такое заполнение мезопор может быть выполнено разнообразными путями. Например,может быть использован полимерный наполнитель с быстрой диффузией H2S и СО 2, такой как силиконовый каучук или полимер с собственной пористостью. В альтернативном варианте, для заполнения порового пространства может быть применен пиролитический углерод, имеющий мезопористость и/или микропористость. Еще один дополнительный способ состоит в заполнении порового пространства инертными твердыми материалами с более мелкими размерами, или заполнением порового пространства пополняемой жидкостью, через которую быстро диффундируют желательные газы (такой как вода, растворители или масло). Поровое пространство внутри стенки адсорбента предпочтительно сокращают до величины менее чем около 40 об.%, предпочтительно до менее чем 30 об.%, более предпочтительно до менее чем 20 об.%, еще более предпочтительно до менее чем 10 об.% и наиболее предпочтительно до менее чем около 5 об.% открытого порового объема. В дополнение к признакам структуры и материала адсорбента, разнообразные признаки конфигурации адсорбционной системы могут быть применены в дополнение к другим признакам, или как альтернативное усовершенствование процесса. Один такой вариант исполнения может включать последовательное расположение RC-PSA-установок для повышения степени извлечения из RC-PSA-системы, как отмечено выше в качестве признака C1. В порядке одного примера, последовательное расположениеRC-PSA-установок может быть использовано для повышения степени извлечения и чистоты целевого газа или продукта, пропусканием непродуктового потока из первой RC-PSA-установки во вторуюRC-PSA-установку для удаления продукта из непродуктового потока от первой RC-PSA-установки. В качестве одного примера, кислотный газ может быть удален из потока природного газа для получения потока высокочистого метана в первой RC-PSA-установке этой системы. Кислотный газ из первойRC-PSA-установки может содержать долю метана, который может быть удален с использованием второйRC-PSA-установки. Метановый продукт из второй RC-PSA-установки может быть вовлечен в рециркуляцию или использован где-нибудь еще в установке, и кислотный газ может быть выведен из второйRC-PSA-установки или направлен наружу для утилизации. При улавливании метана с использованием второй RC-PSA-установки вся RC-PSA-система в целом достигает высокой степени извлечения продукта и высокой чистоты продукта даже для природного газа под высоким давлением. Кроме того, в качестве еще одного признака для повышения продуктивности любой RC-PSAсистемы могут быть применены уравнительные резервуары или баки, как отмечено выше для признака С 2, и для сокращения всей необходимой продолжительности цикла. Как описано в патентной заявке США номер 61/594824, которая включена здесь ссылкой, один или более независимых резервуаров под давлением могут быть предусмотрены для каждой уравнительной стадии для каждого адсорбентного слоя в RC-PSA-системе. То есть, непосредственно к одному из адсорбентных слоев присоединены специализированные резервуары под давлением, называемые уравнительными резервуарами или баками. Газы, выводимые из адсорбентного слоя во время стадии сбрасывания давления, временно хранятся в уравнительном резервуаре и затем используются позже в цикле для восстановления давления в том же адсорбентном слое. Поскольку с помощью специализированных уравнительных резервуаров сокращают- 14024199 ся расстояния для трубопроводов и клапанов, временной интервал для уравнительных стадий между адсорбентным слоем и уравнительным резервуаром обычно является более коротким, чем время, необходимое для уравнивания между двумя адсорбентными слоями, и поэтому может быть сокращена общая продолжительность цикла. В результате этого уменьшается количество адсорбентного материала, используемого внутри адсорбентного слоя, и могут быть сокращены общие габариты и вес циклической адсорбционной системы, тогда как может быть повышена производительность (например, меньшие величины расхода потека продувки, меньшее сжатие в рециркуляции и т.д.). Кроме того, уменьшается количество трубопроводов и клапанов для RC-PSA-системы, поскольку для уравнительных стадий не требуются соединения слоя со слоем. Описанные выше признаки могут быть включены в PSA-системы для повышения производительности обработки высоконапорного природного газа, чтобы обеспечить разделения с высокой степенью извлечения, высокой чистотой, или как высокой степенью извлечения, так и высокой чистотой. Фиг. 7-9 представляют диаграммы примерных PSA-систем, иллюстрирующие, как описываемые здесь признаки могут быть скомбинированы для разделений. На фиг. 7 высокая степень извлечения метана обеспечивается работой PSA-системы 700 в коротких циклах (признак А 1) с рекуперативной продувкой (признак А 2) при надлежащем промежуточном давлении (признак А 5) и с использованием многочисленных стадий выдувания (признак А 6). Используют структурированный контактор (признак В 2), покрытый цеолитом с кинетической селективностью для СО 2 (признак B1), и поровое пространство сокращают применением мезопористого наполнителя (признак В 4). Примерные варианты исполнения RC-PSA-системы 700 дополнительно описаны в примерах 1 и 2 для обработки природного газа при давлении 55 бар (5,5 МПа) с 30% кислотного газа для достижения 97%-ной степени извлечения метана. В еще одном варианте исполнения, показанном на фиг. 8, как высокая степень извлечения метана,так и высокая чистота продукта достигаются с использованием серии из двух PSA-установок в системе 800. PSA-установки 801 и 821 реализуют описанные здесь признаки, включающие короткие циклы (признак А 1), рекуперативную продувку (признак А 2), продувку продуктом (признак A3), выбор давлений продувки (признак A5), структурированные адсорбентные контакторы (признак B2) с отдельными материалами для кинетического отделения СО 2 и равновесной адсорбции H2S (признак B1), размещенными в контакторе в двух отдельных сегментах (признак В 3), и введение мезопористого наполнителя для сокращения порового объема (признак В 4) и повышения степени извлечения. Степень извлечения метана повышается применением двух PSA-установок в последовательном соединении (признак С 1) для улавливания метана, теряемого в поток кислотного газа из первой PSA-установки 801, с использованием второйPSA-установки 821. PSA-система также может использовать уравнительные резервуары (признак С 2) для сокращения продолжительности цикла и повышения продуктивности. Технические характеристики и подробности RC-PSA-системы 800 описаны в примерах 3 и 4 для обработки природного газа с 12% CO2 и 0,01-0,1% H2S с получением метана менее чем с 1,5% CO2 и менее 4 млн-1 H2S, в то же время с достижением 99%-ной степени извлечения. В еще одном дополнительном варианте исполнения, показанном на фиг. 9, как высокая степень извлечения метана, так и высокая чистота продукта достигаются в единственной PSA-установке 900. ЭтаPSA-установка работает в короткоцикловом режиме (признак А 1) с рекуперативной продувкой (признак А 2) при надлежащем промежуточном давлении (признак А 5), с последующим выдуванием до вакуумметрического давления (признак А 4) для достижения высокой чистоты продукта. Структурированный адсорбентный контактор (признак В 2) используют с двумя специфическими материалами для кинетического отделения CO2 и равновесной адсорбции H2S (признак В 1), размещенными в контакторе в двух отдельных сегментах (признак В 3), и введением мезопористого наполнителя для сокращения порового объема (признак В 4) и повышения степени извлечения. Уравнительные резервуары (признак С 2) также могут быть использованы для сокращения требуемой продолжительности цикла и тем самым повышения продуктивности системы. Технические характеристики и подробности RC-PSA-системы 900 описаны в примере 5 для обработки природного газа с 12% СО 2 и 0,01-0,1% H2S, с получением метана менее чем с 1,5% СО 2 и менее 4 млн-1 H2S, в то же время с достижением 99%-ной степени извлечения. Настоящее изобретение может быть лучше понято с привлечением нижеследующих примеров, которые представлены для целей иллюстрации и не должны восприниматься как ограничивающие изобретение. Пример 1. Этот пример иллюстрирует удаление СО 2 и H2S из природного газа при высоком давлении с использованием RC-PSA-системы 700 из фиг. 7, для которой в результате моделирования прогнозируется 98%-ная степень извлечения. Со ссылкой на упрощенную технологическую блок-схему на фиг. 7,RC-PSA-установку 701 используют наряду с разнообразными компрессорами 710 а-710 е для удаления загрязняющих примесей из сырьевого потока. RC-PSA-установка 701 включает многочисленные адсорбентные слои, соединенные через клапаны и трубопроводы, как более подробно описано ниже. Для работы сырьевой поток пропускают в RC-PSA-установку 701 по трубопроводу 702 и 704. Сырьевой поток предпочтительно содержит природный газ, который может быть смешан с рециркуляционным потоком из выпускного трубопровода 703 для рекуперативной продувки, связанного с компрессором 710 а. Поток очищенного продукта, обогащенный метаном, выходит из RC-PSA-установки 701 по трубопроводу 706 при давлении, слегка пониженном вследствие падения давления в пределах адсорбентных слоев, клапанов и трубопроводов, находящихся внутри RC-PSA-установки 701. В этом примере сырьевой газ, поступающий через трубопровод 702, содержит 30% кислотного газа (СО 2+H2S) и 70% СН 4. Давление сырьевого потока и рециркуляционного потока составляет около 55 бар (5,5 МПа, абс.). Поток продукта, выходящий через трубопровод 706, содержит около 6% кислотного газа и 94% CH4, и давление составляет около 54 бар (5,4 МПа, абс.). Поток рекуперативной продувки может быть пропущен в RC-PSA-установку 701 по трубопроводу 708. Этот продувочный поток обогащен кислотным газом (СО 2 и/или H2S) и может состоять из выходного потока из стадий выдувания в RC-PSA-цикле, более подробно описанном ниже. Назначение потока рекуперативной продувки состоит в вымывании метана и других углеводородов из каналов адсорбентного контактора и поровых пространств в адсорбентном слое. Выходной поток из этой продувки сжимают в компрессоре 710 а и вовлекают в рециркуляцию обратно для подачи в RC-PSA-установку по трубопроводу 703. Этим путем метан улавливается, вместо того, чтобы быть потерянным с кислотным газом, и поэтому степень извлечения в RC-PSA-системе повышается. Кислотный газ, десорбированный из RC-PSA-установки 701, выходит при трех различных уровнях давления для сведения к минимуму потребления энергии, необходимой для сжатия кислотного газа, отправляемого на утилизацию. Минимальное давление устанавливают примерно на 1 бар (0,1 МПа, абс.) для стимулирования десорбции загрязняющих примесей и достижения повышенной чистоты продукта в последующих адсорбционных стадиях. Уровни давления для остальных двух стадий выдувания были выбраны для оптимизации согласования с кислотным компрессором и меньшего расходования энергии. Типичные компрессоры для кислотных газов работают при коэффициентах повышения давления около 3, и поэтому уровни давления при выдувании составляют 3 бар (0,3 МПа, абс.) и 9 бар (0,9 МПа, абс.). Коэффициент повышения давления представляет собой выходное давление, деленное на давление всасывания. Как показано на фиг. 7, малонапорный выхлопной поток при давлении 1 бар (0,1 МПа, абс.) сжимают в компрессоре 710b и объединяют с выхлопным потоком с промежуточным давлением около 3 бар(0,3 МПа, абс.), который подвергают сжатию в компрессоре 710 с. Выходной поток из компрессора 710 с объединяют с высоконапорным выхлопным потоком при давлении около 9 бар (0,9 МПа, абс.) и сжимают в компрессоре 710d. Выходной поток из компрессора 710d может быть под давлением около 19 бар(1,9 МПа, абс.), который может иметь часть, пропускаемую по трубопроводу 708 в качестве продувочного потока, и в компрессор 710 е для дополнительного сжатия перед дальнейшей обработкой (например,кислотного газа для нагнетания в утилизационные буровые скважины, трубопроводы и/или т.п.). Каждая RC-PSA-установка 701 состоит из четырнадцати адсорбентных слоев, каждый из которых состоит из структурированного контактора с многочисленными проточными газовыми каналами. Гидравлические диаметры проточных газовых каналов варьируют от 20 до 1000 мкм, предпочтительно от 25 до 400 мкм и еще более предпочтительно от 40 до 125 мкм. Общая длина проточных газовых каналов через контактор варьирует от 0,2 до 3 м, предпочтительно от 0,5 до 1,5 м и наиболее предпочтительно варьирует от 0,75 до 1,25 м. Структурированный контактор может быть сегментирован вдоль своей длины таким образом, что каждый сегмент имеет многочисленные проточные каналы, и газ протекает последовательно из проточных каналов в одном сегменте в проточные каналы в отдельном сегменте. Вдоль длины контактора могут присутствовать от 1 до 10 сегментов. Физическая скорость течения газа через проточные каналы на впускной стороне адсорбентного слоя варьирует в диапазоне от 1 до 10 м/с, предпочтительно в диапазоне от 2 до 5 м/с. Сопротивление потоку газа при течении через проточные каналы вызывает падение давления во время адсорбционной стадии менее чем на 8 бар (0,8 МПа, абс.), предпочтительно менее чем на 4 бар (0,4 МПа, абс.) и более предпочтительно менее чем на 2 бар (0,2 МПа, абс.),как рассчитано по комбинации давления подачи, вязкости подводимого сырья, гидравлического диаметра канала и общей длины канала и входной скорости сырьевого потока. Проточные газовые каналы в структурированном адсорбентном контакторе сформированы из слоя,содержащего адсорбентный материал, селективный в отношении СО 2 и H2S, который может быть на всем или на части по меньшей мере одного участка стенок структурированного контактора. Слой также может содержать материал мезопористого наполнителя, который сокращает поровое пространство в слое до менее чем 30 об.%, или более предпочтительно 20 об.%, или еще более предпочтительно 10 об.%, или наиболее предпочтительно до менее чем 4 об.%. Средняя толщина слоя может быть в диапазоне от 25 до 450 мкм, предпочтительно в диапазоне от 30 до 200 мкм и наиболее предпочтительно от 50 до 125 мкм. В одном предпочтительном варианте исполнения адсорбентный материал представляет собой цеолит и имеет коэффициент кинетической селективности для CO2 свыше 50, предпочтительно более 100, и еще более предпочтительно свыше 200. Коэффициент кинетической селективности представляет собой скорость диффузии загрязняющей примеси, такой как СО 2, деленную на скорость диффузии продукта, такого как метан. Во время адсорбционной стадии изменение среднего содержания СО 2 и H2S в адсорбенте вдоль длины каналов предпочтительно составляет более 0,2 ммоль/г, более предпочтительно более 0,5 ммоль/г и наиболее предпочтительно свыше 1 ммоль/г, где среднее содержание представлено как число миллимолей загрязняющей примеси на 1 г адсорбента.RC-PSA-установка 701 работает в короткоцикловом режиме на протяжении серии стадий, которые включают адсорбцию, за которой следуют многочисленные стадии регенерации адсорбентного слоя перед адсорбционной стадией в последующем цикле. Каждый адсорбентный слой непрерывно выполняет одну и ту же серию стадий, и распределение во времени цикла для каждого слоя может быть синхронизировано с другими слоями, чтобы обеспечить непрерывное течение сырьевого потока, продукта и продувочных потоков. Выбор точного распределения времени стадий и цикла зависит от состава газа в сырьевом потоке, спецификаций продукта, характера загрязняющих примесей, и общей степени извлечения углеводородов. Для RC-PSA-установки 701 в этом примере требуются четырнадцать адсорбентных слоев, чтобы выполнить цикл для непрерывной поточной обработки. Стадии цикла для единственного адсорбентного слоя иллюстрированы с использованием зависимости давления в адсорбентном слое от времени, что показано на фиг. 10. Во время адсорбционной стадии,которая обозначена как FD (для сырьевого потока), кислотный газ адсорбируется в адсорбентном слое и получается очищенный метановый продукт. Течение сырьевого потока останавливают до появления значительного проскока кислотного газа в поток продукта и в слое сбрасывают давление в двух уравнительных стадиях, обозначенных как Е 1 и Е 2. Значительный проскок кислотного газа в поток продукта происходит, когда адсорбентный слой загружен более чем на 50%, предпочтительно более чем на 75%. После каждой стадии предусмотрено короткое выдерживание, которое не показано. После уравнительных стадий выполняют стадию рекуперативной продувки, которая обозначена как Р, для извлечения метана, оставшегося в проточных каналах и поровом пространстве в адсорбентном слое. Затем в адсорбентном слое сбрасывают давление в трех стадия выдувания для снижения давления, чтобы десорбировать кислотный газ из адсорбентного слоя, что обозначено как BD. После десорбирования кислотного газа до возможной степени проводят восстановление давления в адсорбентном слое в стадиях, которые обозначены как R1 и R2, и в стадии восстановления давления, которая обозначена как FR. Источник газа для двух стадий R1 и R2 восстановления давления представляет собой газ из еще одного адсорбентного слоя,подвергнутого обработке в стадиях сбрасывания давления Е 1 и Е 2 в то же время. Газ для подачи в стадию восстановления давления получают из сырьевого потока в RC-PSA-установку через трубопровод 704 на фиг. 7. Распределение времени для каждого из четырнадцати адсорбентных слоев синхронизируют таким образом, чтобы потоки сырья, продукта и продувки были непрерывными. График цикла для всех четырнадцати адсорбентных слоев показан на фиг. 11 а и 11b. Кодовые буквенные обозначения на фиг. 11 а и 11b являются одинаковыми с теми, которые обозначены на фиг. 10, с добавлением стадии выдерживания,которая обозначена как Н. На фиг. 11 а и 11b две группы адсорбентных слоев 1101 и 1102 показаны с адсорбентными слоями в первой группе 1101, маркированными от 1 до 7 в верхней части графика последовательности, и адсорбентными слоями во второй группе 1102, маркированными от 8 до 14 в нижней части графика последовательности. Фиг. 11 а представляет часть последовательности, которая продолжается на фиг. 11b, как обозначено кодовым буквенным обозначением А. Во время работы в установившемся режиме два адсорбентных слоя подвергаются обработке в адсорбционной стадии, на которой кислотный газ удаляется из сырьевого потока для образования очищенного метанового продукта. График времени цикла для каждого адсорбентного слоя распределен на этапы таким образом, что достигается непрерывное течение сырья и продукта. Например, слой 2 на фиг. 11 а начинает адсорбционную стадию (обозначенную FD) немедленного после того, как слой 1 завершает адсорбционную стадию, и т.д. Подобным образом непрерывное течение создается для стадии продувки и потоков выдувания в компрессоры для кислотных газов. Временной график циклов между адсорбентными слоями также синхронизируют таким образом, что первая уравнительная стадия Е 1 для одного слоя совпадает со стадией R1 восстановления давления для еще одного слоя так, что газ, выведенный во время стадии сбрасывания давления, используется для восстановления давления: в еще одном слое. Например, адсорбентный слой 7 на фиг. 11 а подвергают обработке в уравнительной стадии Е 1 в то же самое время, когда адсорбентный слой 2 подвергают обработке в стадии R1 восстановления давления. Ниже дополнительно описаны уровни давления, направления течения и продолжительности для каждой из стадий в цикле. В нижеследующих описаниях циклов термин "прямоточный" имеет отношение к течению газа от сырьевой стороны слоя к продуктовой стороне, и "противоточный" обозначает течение в противоположном направлении. Нижеизложенным представлен один предпочтительный цикл,в котором:FD: Адсорбция СО 2 и получение очищенного метана под давлением 55 бар (5,5 МПа, абс.) (прямоточное течение) из первого адсорбентного слоя; Е 1: Сбрасывание давления в первом адсорбентном слое от около 55 бар (5,5 МПа, абс.) до около 35,5 бар (3,55 МПа, абс.) с направлением газа в еще один адсорбентный слой для повышения давления от около 19 бар (1,9 МПа, абс.) до около 35,5 бар (3,55 МПа, абс.) (прямоточное течение); Е 2: Сбрасывание давления в первом адсорбентном слое от около 35,5 бар (3,55 МПа, абс.) до около 19 бар (1,9 МПа, абс.) с направлением газа в еще один адсорбентный слой для повышения давления от около 1,2 бар (0,12 МПа, абс.) до около 19 бар (1,9 МПа, абс.) (прямоточное течение); Р: Продувка первого адсорбентного слоя при давлении около 19 бар (1,9 МПа, абс.) частью газа из стадии BD1 при давлении около 9 бар (0,9 МПа, абс.), который подвергнут сжатию до давления продувки. Газ, вытесненный из адсорбентного слоя во время стадии продувки, сжимают до давления 55 бар(5,5 МПа, абс.) и вовлекают в рециркуляцию в трубопровод для подачи сырья (прямоточное течение);BD1: Выдувание, или сбрасывание давления, первого адсорбентного слоя от около 19 бар (1,9 МПа,абс.) до около 9 бар (0,9 МПа, абс.). Десорбированный газ выводится в третью ступень компрессора для кислотных газов (противоточное течение);BD2: Выдувание, или сбрасывание давления, первого адсорбентного слоя от около 9 бар (0,9 МПа,абс.) до около 3 бар (0,3 МПа, абс.). Десорбированный газ выводится во вторую ступень компрессора для кислотных газов (противоточное течение);BD3: Выдувание, или сбрасывание давления, первого адсорбентного слоя от около 3 бар (0,3 МПа,абс.) до около 1,2 бар (0,12 МПа, абс.). Десорбированный газ выводится в первую ступень компрессора для кислотных газов (противоточное течение);R2: Восстановление давления в первом адсорбентном слое от около 1,2 бар (0,12 МПа, абс.) до около 19 бар (1,9 МПа, абс.) с использованием газа, выведенного из еще одного дополнительного адсорбентного слоя, который подвергается обработке на стадии Е 2 (противоточное течение);R1: Восстановление давления в первом адсорбентном слое от коло 19 бар (1,9 МПа, абс.) до около 35,5 бар (3,55 МПа, абс.) с использованием газа, выведенного из еще одного дополнительного адсорбентного слоя, который подвергается обработке на стадии Е 1 (противоточное течение); и FR: Восстановление давления в первом адсорбентном слое от около 35,5 бар (3,55 МПа, абс.) до около 55 бар (5,5 МПа,абс.) газом из сырьевого трубопровода (прямоточное течение). Продолжительность каждой стадии в цикле является следующей: В целом для выполнения обсужденных выше стадий цикла требуются 10,5 с. В этом примере продолжительность адсорбционной стадии обусловливается скоростями диффузии СО 2 и метана, причем короткая продолжительность адсорбционной стадии позволяет более быстро диффундирующим молекулам СО 2 достигнуть равновесных адсорбционных емкостей внутри адсорбентного материала, прежде чем медленнее диффундирующий метан сможет в значительной мере диффундировать в адсорбентный материал. Предпочтительно снижать давление в адсорбентном слое настолько быстро, насколько возможно,после адсорбционной стадии, чтобы сократить любую дополнительную диффузию метана в частицу адсорбента, чтобы уменьшить потери метана. Кроме того, предпочтительно, чтобы общая продолжительность стадий регенерации была по возможности более короткой, для максимизации продуктивности адсорбентного слоя. Общий временной интервал для всех уравнительных стадий является меньшим в десять раз, предпочтительно меньшим в пять раз, чем для адсорбционной стадии. Наиболее предпочтительно, чтобы общая продолжительность всех уравнительных стадий была меньше, чем продолжительность адсорбционной стадии. Также предпочтительно, чтобы общая продолжительность всех стадий восстановления давления была в десять раз меньше, предпочтительно в пять раз меньше, чем продолжительность адсорбционной стадии. Наиболее предпочтительно, чтобы общая продолжительность всех стадий восстановления давления была меньшей, чем продолжительность адсорбционной стадии. Результирующая производительность RC-PSA-системы, описанной в этом примере, была прогнозирована на основе моделирования цикла с использованием обсужденных выше параметров. ЕдинственнаяRC-PSA-установка с четырнадцатью адсорбентными слоями может обрабатывать 150 MSCFD(177000 ст.м 3/ч) сырьевого газа с 30% кислотного газа и 70% метана для получения 108 MSCFD(127440 ст.м 3/ч) газообразного продукта с около 5,4% кислотного газа и остальным количеством, приходящимся на метан. В RC-PSA-системе достигается примерно 98%-ная степень извлечения метана. Также образуется выхлопной поток примерно с 94% кислотного газа на утилизацию. Традиционные PSAсистемы не обеспечивают высокой степени извлечения, которая продемонстрирована в этой RC-PSAсистеме для обработки природного газа при этих условиях с таким составом. Кроме того, система сокра- 18024199 щает потерю тяжелых углеводородов, по сравнению с традиционными технологиями разделения. Пример 2. Этот пример описывает модифицированный цикл для RC-PSA-системы в примере 1. В этом примере RC-PSA-система 700 согласно фиг. 7 использована для обработки такого же сырьевого газа, как описано в примере 1. Конфигурация каждого адсорбентного слоя является такой же, как в примере 1, включая размеры проточных каналов, длину адсорбентных слоев, адсорбентный материал, мезопористый наполнитель и т.д. Однако число адсорбентных слоев увеличено от четырнадцати до шестнадцати для приспособления к модифицированному циклу, в котором используют три уравнительные стадии вместо двух уравнительных стадий, как в примере 1. График цикла для шестнадцати адсорбентных слоев в этом примере показан на фиг. 12 а и 12b. Обозначение конкретных стадий является таким же, как на фиг. 10 и 11, описанных в примере 1. На фиг. 12 а и 12b показаны две группы адсорбентных слоев, с адсорбентными слоями в первой группе, маркированными от 1 до 8 в верхней части графика последовательности, и адсорбентными слоями во второй группе,маркированными от 9 до 16 в нижней части графика последовательности. Фиг. 12 а представляет часть последовательности, которая продолжается на фиг. 12b, как обозначено кодовым буквенным обозначением В. Как в примере 1, непрерывные течения предусмотрены для потоков подводимого сырья, продукта, продувки и выдувания. Кроме того, временной график циклов для каждого адсорбентного слоя синхронизирован таким образом, что уравнивания от слоя к слою могут быть выполнены, как в примере 1. С тремя уравнительными стадиями в цикле индивидуальный адсорбентный слой может быть подвергнут сбрасыванию давления до более низкого давления продувки, чем это достижимо только с двумя уравнительными стадиями. Например, стадия продувки в примере 1 выполняется при давлении 19 бар(1,9 МПа, абс.) после двух уравнительных стадий, тогда как стадию продувки в этом примере выполняют при давлении 12,5 бар (1,25 МПа, абс.) после трех уравнительных стадий. В результате этого общий расход потока, необходимый для стадии продувки, является меньшим, поскольку требуется такая же скорость, но нужен меньший массовый расход потока благодаря меньшему давлению. Как более низкое давление, так и меньший расход потока сокращают габариты и потребление энергии в приданных компрессорах для продувочного потока. Давление и направление течения для каждой из стадий в цикле являются следующими:FD: Адсорбция СО 2 и получение очищенного метана под давлением 55 бар (5,5 МПа, абс.) (прямоточное течение) из первого адсорбентного слоя; Е 1: Сбрасывание давления в первом адсорбентном слое от около 55 бар (5,5 МПа, абс.) до около 39 бар (3,9 МПа, абс.) с направлением газа в еще один адсорбентный слой для повышения давления от около 26 бар (2,6 МПа, абс.) до около 39 бар (3,9 МПа, абс.) (прямоточное течение); Е 2: Сбрасывание давления в первом адсорбентном слое от около 39 бар (3,9 МПа, абс.) до около 26 бар (2,6 МПа, абс.) с направлением газа в еще один адсорбентный слой для повышения давления от около 12,5 бар (1,25 МПа, абс.) до около 26 бар (2,6 МПа, абс.) (прямоточное течение); Е 3: Сбрасывание давления в первом адсорбентном слое от около 26 бар (2,6 МПа, абс.) до около 12,5 бар (1,25 МПа, абс.) с направлением газа в еще один адсорбентный слой для повышения давления от около 1 бар (0,1 МПа, абс.) до около 12,5 бар (1,25 МПа, абс.) (прямоточное течение); Р: Продувка первого адсорбентного слоя при давлении около 12,5 бар (1,25 МПа, абс.) частью газа из стадии BD1 при давлении около 9 бар (0,9 МПа, абс.), который подвергнут сжатию до давления продувки. Газ, вытесненный из адсорбентного слоя во время стадии продувки, сжимают до давления 55 бар(5,5 МПа, абс.) и вовлекают в рециркуляцию в трубопровод для подачи сырья (прямоточное течение);BD1: Выдувание, или сбрасывание давления, первого адсорбентного слоя от около 12,5 бар(1,25 МПа, абс.) до около 9 бар (0,9 МПа, абс.). Десорбированный газ выводится в третью ступень компрессора для кислотных газов (противоточное течение);BD2: Выдувание, или сбрасывание давления, первого адсорбентного слоя от около 9 бар (0,9 МПа,абс.) до около 3 бар (0,3 МПа, абс.). Десорбированный газ выводится во вторую ступень компрессора для кислотных газов (противоточное течение);BD3: Выдувание, или сбрасывание давления, первого адсорбентного слоя от около 3 бар (0,3 МПа,абс.) до около 1 бар (0,1 МПа, абс.). Десорбированный газ выводится в первую ступень компрессора для кислотных газов (противоточное течение);R3: Восстановление давления в первом адсорбентном слое от около 1 бар (0,1 МПа, абс.) до около 12,5 бар (1,25 МПа, абс.) с использованием газа, выведенного из еще одного дополнительного адсорбентного слоя, который подвергается обработке на стадии Е 3 (противоточное течение);R2: Восстановление давления в первом адсорбентном слое от около 12,5 бар (1,25 МПа, абс.) до около 26 бар (2,6 МПа, абс.) с использованием газа, выведенного из еще одного дополнительного адсорбентного слоя, который подвергается обработке на стадии Е 2 (противоточное течение);R1: Восстановление давления в первом адсорбентном слое от около 26 бар (2,6 МПа, абс.) до около 39 бар (3,9 МПа, абс.) с использованием газа, выведенного из еще одного дополнительного адсорбентного слоя, который подвергается обработке на стадии Е 1 (противоточное течение); иFR: Восстановление давления в первом адсорбентном слое от около 39 бар (3,9 МПа, абс.) до около 55 бар (5,5 МПа, абс.) газом из сырьевого трубопровода (прямоточное течение). Продолжительность каждой стадии в цикле является следующей: Дополнительные уравнительные стадии и стадии восстановления давления, наряду со связанными с ними стадиями выдерживания, увеличивают общую продолжительность цикла до 12 с. Продолжительность адсорбционной стадии остается такой же, как в примере 1, будучи основанной на кинетических характеристиках адсорбентного материала. Стадии регенерации для этого цикла требуют слегка большей продолжительности вследствие дополнительных уравнительных стадий и стадий восстановления давления. Как в примере 1, предпочтительно, чтобы общий временной интервал для всех уравнительных стадий был меньшим в десять раз, предпочтительно меньшим в пять раз, чем для адсорбционной стадии. Наиболее предпочтительно, чтобы общая продолжительность всех уравнительных стадий была меньше,чем продолжительность адсорбционной стадии. Также предпочтительно, чтобы общая продолжительность всех стадий восстановления давления была в десять раз меньше, предпочтительно в пять раз меньше, чем продолжительность адсорбционной стадии. Наиболее предпочтительно, чтобы общая продолжительность всех стадий восстановления давления была меньшей, чем продолжительность адсорбционной стадии. Хотя число адсорбентных слоев в этом примере было увеличено от четырнадцати до шестнадцати,производительность единственной RC-PSA-установки повысилась пропорционально от 150 MSCFDMSCFD (141600 ст.м 3/ч) очищенного метанового продукта, содержащего примерно 5,4% кислотного газа, и степень извлечения метана повысилась до около 98,6% для этого примера. Выгода от применения трех уравнительных стадий в этом примере очевидна по величине расхода продувочного потока, которая снизилась от 20,6 MSCFD (24308 ст.м 3/ч) в примере 1 до 14,3 MSCFD (16874 ст.м 3/ч) в этом примере. Уменьшенный расход потока, наряду с пониженным давлением для продувки, приводит к значительному сокращению потребления энергии и габаритов связанного с этим компрессорного оборудования. Пример 3. Этот пример иллюстрирует удаление CO2 и H2S из природного газа при высоком давлении с использованием RC-PSA-системы 800 из фиг. 8, в котором прогнозирована более чем 99%-ная степень извлечения метана, и получается поток высокочистого продукта с менее чем 1,5% СО 2 и менее чем 4 млн-1H2S. Co ссылкой на упрощенную технологическую блок-схему на фиг. 8, для удаления загрязняющих примесей из сырьевого потока использованы две RC-PSA-установки 801 и 821 наряду с разнообразными компрессорами 806 и 814. В этом примере две RC-PSA-системы размещены в последовательном соединении, где первая RC-PSA-установка 801 производит газообразный продукт с требуемой чистотой, и вторая RC-PSA-установка 821 получает метан из выдувного потока установки 801 для повышения общей степени извлечения продукта для системы 800, Каждая из двух RC-PSA-установок 801 и 821 включает один или более адсорбционных слоев, соединенных через клапаны и трубопроводы. Сырьевой поток природного газа, содержащий СО 2 и H2S, поступает в первую RC-PSA-установку 801 по трубопроводу 802, и поток очищенного продукта, обогащенный метаном, выходит через трубопровод 803 при давлении, слегка пониженном вследствие падения давления в пределах адсорбентных слоев, клапанов и трубопроводов, находящихся внутри RC-PSA-установки 801. Кислотный газ, удален- 20024199 ный из сырьевого потока, десорбируется при низком давлении, и выхлопной поток газа выходит из установки по трубопроводу 807. Для получения продукта с высокой чистотой в RC-PSA-установке 801 часть потока продукта отводят через трубопровод 804 и снижают его давление, чтобы использовать для продувки продуктом в адсорбентных слоях 801. Низкое парциальное давление кислотного газа в потоке продукта создает движущую силу, которая содействует десорбции кислотного газа из адсорбентных слоев, чтобы повысить чистоту продукта во время последующей адсорбционной стадии. Выходной поток из стадии продувки продуктом выходит через трубопровод 806 и объединяется с выхлопным потоком в трубопроводе 807 для обработки во второй RC-PSA-установке 821. В этом примере сырьевой газ, поступающий через трубопровод 802, содержит 12% СО 2 и 100 млн-1 H2S и находится под давлением 44 бар(4,4 МПа, абс.). Газообразный продукт, выходящий через трубопровод 803, содержит 1,3% СО 2 и около 4 млн-1 H2S. Кислотный газ в трубопроводе 806 и 807 находится под давлением около 1,4 бар (0,14 МПа,абс.). Для повышения степени извлечения продукта в RC-PSA-системе 800 метан и другие углеводороды,содержащиеся в выхлопном потоке из первой RC-PSA-установки 801, удаляются во второй RC-PSAустановке 821. Кислотный газ и метан, отделенные в первой RC-PSA-установке 801, поступают во вторую RC-PSA-установку 821 по трубопроводу 809 после сжатия в компрессоре 808. Кислотный газ адсорбируется из сырьевого потока в RC-PSA-установке 821, и поток продукта, обогащенный метаном, выходит через трубопровод 810, имея слегка пониженное давление вследствие падения давления в пределах адсорбентных слоев, клапанов и трубопроводов, находящихся внутри RC-PSA-установки 821. Кислотный газ выводится при низком давлении через трубопровод 811. Часть кислотного газа отводят через трубопровод 812 и сжимают в компрессоре 814 для использования в рекуперативной продувке, поток для которой поступает в RC-PSA-установку 821 по трубопроводу 815. Этот поток обогащен кислотным газом, и используется для вымывания метана из проточных каналов и поровых пространств в адсорбентном слое для повышения степени извлечения в системе. Выходной поток из этой стадии продувки выходит из RC-PSA-установки 821 по трубопроводу 816 и объединяется с продуктом из трубопровода 810, и объединенный поток в трубопроводе 817 содержит извлеченные углеводороды, используемые в качестве топливного газа или для других целей внутри предприятия. Остальную часть кислотного газа выводят через трубопровод 813 путем вентиляции, или сжатия и повторного нагнетания. В этом примере сырьевой поток, поступающий во вторую RC-PSA-установку 821, имеет давление 45 бар (4,5 МПа, абс.) и содержит около 65% кислотного газа и 35% метана. Газообразный продукт содержит около 92% метана и 8% кислотного газа. Выхлопной поток кислотного газа покидает установку под давлением около 1,4 бар(0,14 МПа, абс.), и стадию рекуперативной продувки выполняют при давлении около 11 бар (1,1 МПа,абс.). Каждая RC-PSA-установка 801 состоит из десяти адсорбентных слоев, каждый из которых состоит из структурированного контактора с многочисленными проточными газовыми каналами. В этом примере проточные газовые каналы являются, по существу, квадратными, как показано на фиг. 13 а, с высотой 1301 225 мкм и шириной 225 мкм. Общая длина проточных газовых каналов составляет 1,1 м, и общий диаметр каждого адсорбентного слоя составляет 1,2 м. Структурированный контактор может быть сегментирован вдоль его длины таким образом, что каждый сегмент имеет многочисленные проточные каналы, и газ проходит последовательно из проточных каналов в одном сегменте в проточные каналы в отдельном сегменте. Вдоль длины контактора могут присутствовать от 1 до 10 сегментов. Общее падение давления по длине адсорбентного слоя во время адсорбционной стадии составляет около 1 бар(0,1 МПа). Проточные газовые каналы в структурированном адсорбентном контакторе сформированы из слоя,содержащего адсорбентный материал, который может быть на всем или на части по меньшей мере одного участка стенок структурированного контактора. Слой также может содержать материал мезопористого наполнителя, который сокращает поровое пространство в слое до менее, чем около 20%. Средняя толщина слоя составляет 150 мкм, размер 1302 на фиг. 13 а. В этом примере два различных адсорбентных материала используют в композитном слое для обеспечения почти полного удаления H2S, чтобы получить высокочистый метановый продукт. В первом сегменте адсорбентного слоя, имеющем длину 0,10 м,используют аминофункционализированный адсорбент, который селективно адсорбирует H2S. В остальных сегментах адсорбентного слоя, имеющих длину 1 м, используют цеолит, такой как DDR, для поглощения СО 2. Фиг. 13b представляет схематическое изображение композитного слоя 1310, показывая первый сегмент 1311 с функционализированным адсорбентом, и вторые сегменты 1312 с DDR. Впускные и выпускные трубопроводы показаны схематически под кодовыми номерами 1314 и 1316 позиций соответственно. Вторая RC-PSA-установка 821 состоит из десяти адсорбентных слоев, которые идентичны описанным выше адсорбентным слоям, за исключением общего диаметра, который составляет 0,7 м. Все прочие размеры и материалы являются такими же, как в адсорбентных слоях установки 801. Однако в альтернативных вариантах исполнения адсорбентный материал может быть смешан между собой или мог бы быть в форме двух отдельных адсорбентных слоев в одном и том же резервуаре. Адсорбция загрязняющих примесей и последующая регенерация адсорбентного слоя достигаются посредством серии стадий в быстром непрерывном цикле. Выбор точного распределения времени стадий и цикла зависит от нескольких факторов, включающих состав подводимого сырья, спецификации продукта, характер загрязняющих примесей и общую степень извлечения углеводородов. Для первойRC-PSA-установки 801 стадии цикла для единственного адсорбентного слоя иллюстрированы с использованием графика давления в адсорбентном слое в зависимости от времени, показанного на фиг. 14 а. В дополнение к адсорбционной стадии (FD), после пяти уравнительных стадий (Е 1-Е 5) следует единственная стадия (В) выдувания, стадия (Р) продувки продуктом и пять стадий (R1-R5) восстановления давления, наряду со стадий (FR) восстановления давления путем подачи сырья. Индивидуальные стадии цикла на фиг. 14 а более подробно описаны следующим образом.FD: Адсорбционная стадия, предусматривающая подачу природного газа под давлением 44 бар(4,4 МПа, абс.) и получение очищенного метана (прямоточное течение) в первом адсорбентном слое; Е 1: Сбрасывание давления в первом адсорбентном слое от 4 4 бар (4,4 МПа, абс.) до около 35,9 бар(3,59 МПа, абс.) с направлением газа в еще один адсорбентный слой для повышения давления в нем от около 28,7 бар (2,87 МПа, абс.) до около 35,9 бар (3,59 МПа, абс.) (прямоточное течение); Е 2: Сбрасывание давления в первом адсорбентном слое от около 35,9 бар (3,59 МПа, абс.) до около 28,7 бар (2,87 МПа, абс.) с направлением газа в еще один адсорбентный слой для повышения давления в нем от около 22 бар (2,2 МПа, абс.) до около 28,7 бар (2,87 МПа, абс.) (прямоточное течение); Е 3: Сбрасывание давления в первом адсорбентном слое от около 2 8,7 бар (2,87 МПа, абс.) до около 22 бар (2,2 МПа, абс.) с направлением газа в еще один адсорбентный слой для повышения давления в нем от около 15,24 бар (1,524 МПа, абс.) до около 22 бар (2,2 МПа, абс.) (прямоточное течение); Е 4: Сбрасывание давления в первом адсорбентном слое от около 22 бар (2,2 МПа, абс.) до около 15,24 бар (1,524 МПа, абс.) с направлением газа в еще один адсорбентный слой для повышения давления в нем от около 8,05 бар (0,805 МПа, абс.) до около 15,24 бар (1,524 МПа, абс.) (прямоточное течение); Е 5: Сбрасывание давления в первом адсорбентном слое от около 15,24 бар (1,524 МПа, абс.) до около 8,05 бар (0,805 МПа, абс.) с направлением газа в еще один адсорбентный слой для повышения давления от около 1,4 бар (0,14 МПа, абс.) до около 8,05 бар (0,805 МПа, абс.) (прямоточное течение);BD1: Выдувание, или сбрасывание давления, первого адсорбентного слоя от около 8,05 бар(0,805 МПа, абс.) до около 1,4 бар (0,14 МПа, абс.). Выхлопной поток газа направляют в компрессор, такой как компрессор 908 на фиг. 9, который питает вторую RC-PSA-установку (противоточное течение); Р: Продувка первого адсорбентного слоя при давлении около 1,4 бар (0,14 МПа, абс.) частью газообразного продукта под давлением 2,5 бар (0,25 МПа, абс.). Выходной поток из продувки объединяют с выхлопным потоком газа из стадии выдувания и сжимают до давления 45 бар (4,5 МПа, абс.) для подачи во вторую RC-PSA-установку;R5: Восстановление давления в первом адсорбентном слое от около 1,4 бар (0,14 МПа, абс.) до около 8,1 бар (0,81 МПа, абс.) газом из стадии Е 5 еще одного дополнительного адсорбентного слоя (противоточное течение);R4: Восстановление давления в первом адсорбентном слое от около 8,1 бар (0,81 МПа, абс.) до около 15,2 бар (1,52 МПа, абс.) газом из стадии Е 4 еще одного дополнительного адсорбентного слоя (противоточное течение);R3: Восстановление давления в первом адсорбентном слое от около 15,2 бар (1,52 МПа, абс.) до около 22 бар (2,2 МПа, абс.) газом из стадии ЕЗ еще одного дополнительного адсорбентного слоя (противоточное течение);R2: Восстановление давления в первом адсорбентном слое от около 22 бар (2,2 МПа, абс.) до около 28,7 бар (2,87 МПа, абс.) газом из стадии Е 2 еще одного дополнительного адсорбентного слоя (противоточное течение);R1: Восстановление давления в первом адсорбентном слое от около 28,7 бар (2,87 МПа, абс.) до около 35,9 бар (3,59 МПа, абс.) газом из стадии Е 1 еще одного дополнительного адсорбентного слояFR: Восстановление давления в первом адсорбентном слое от около 35,9 бар (3,59 МПа, абс.) до около 44 бар (4,4 МПа, абс.) сырьевым газом (прямоточное течение). Типичный график для цикла первой RC-PSA-установки 801 является следующим: Общая продолжительность цикла для вышеописанных стадий составляет 15 с для первой RC-PSAустановки 801. Продолжительность времени адсорбции для первой RC-PSA-установки 801 в этом примере была увеличена до 3 с, по сравнению с 1,5 с для предыдущих примеров, вследствие того, что в этом примере были предусмотрены кристаллы адсорбента с более крупными размерами. В результате этого диффузия метана и СО 2 в кристаллы цеолита является более медленной, и высокая кинетическая селективность для СО 2 сравнительно с метаном по-прежнему достигается в пределах 3 с. Для второй RC-PSA-установки 821 использован иной цикл, как показано на фиг. 14b, которая представляет график давления со временем для одного адсорбентного слоя в цикле. В этом цикле после адсорбционной стадии (FD) следуют две уравнительные стадии (Е 1-Е 2), стадия (Р) рекуперативной продувки, единственная стадия (В) выдувания, две стадии (R1-R2) сбрасывания давления и стадия (FR) сбрасывания давления путем подачи сырья. Дополнительные подробности стадий цикла и фиг. 14b описаны следующим образом.FD: Адсорбционная стадия, предусматривающая подачу сжатого выхлопного потока газа из первойRC-PSA-системы (прямоточное течение) для получения обогащенного метаном потока; Е 1: Сбрасывание давления в первом адсорбентном слое от 4 5 бар (4,5 МПа, абс.) до около 26,1 бар(2,61 МПа, абс.) с направлением газа в еще один адсорбентный слой для повышения давления в нем от около 12,7 бар (1,27 МПа, абс.) до около 26,1 бар (2,61 МПа, абс.) (прямоточное течение); Е 2: Сбрасывание давления в первом адсорбентном слое от околэ 26,1 бар (2,61 МПа, абс.) до около 12,7 бар (1,27 МПа, абс.) с направлением газа в еще один адсорбентный слой для повышения давления в нем от около 1,4 бар (0,14 МПа, абс.) до около 12,7 бар (1,27 МПа, абс.) (прямоточное течение); Р: Продувка первого адсорбентного слоя при давлении около 11,7 бар (1,17 МПа, абс.) газом из стадии BD1 из еще одного адсорбентного слоя, который подвергнут сжатию до давления 12,7 барBD1: Выдувание, или сбрасывание давления, первого адсорбентного слоя от около 11,7 бар(1,17 МПа, абс.) до около 1,4 бар (0,14 МПа, абс.) (противоточное течение). Десорбированный газ направляют в установку для утилизации (например, вентиляцией или сжатием для нагнетания);R2: Восстановление давления в первом адсорбентном слое от около 1,4 бар (0,14 МПа, абс.) до око- 23024199 ло 12,7 бар (1,27 МПа, абс.) газом из стадии Е 2 еще одного дополнительного адсорбентного слоя (противоточное течение);R1: Восстановление давления в первом, адсорбентном слое от около 12,7 бар (1,27 МПа, абс.) до около 26,1 бар (2,61 МПа, абс.) газом из стадии Е 1 еще одного дополнительного адсорбентного слояFR: Восстановление давления в первом адсорбентном слое от около 26,1 бар (2,61 МПа, абс.) до около 45 бар (4,5 МПа, абс.) сырьевым газом (прямоточное течение). Типичный график для цикла второй RC-PSA-установки 821 является следующим. Общая продолжительность цикла для вышеописанных стадий составляет 7,5 с для второйRC-PSA-установки 821. Продолжительность времени адсорбции для этой установки составляет 1,5 с, как в предшествующих примерах. Для обеих RC-PSA-установок 801 и 821 распределение времени для каждого из адсорбентных слоев синхронизируют таким образом, что течение потоков сырья, продукта, выдувания и продувки является непрерывным. График цикла для всех 10 адсорбентных слоев в первой RC-PSA-установке 8 91 показан на фиг. 15 а и 15b. Обозначения для конкретных стадий являются такими же, как на фиг. 14 а, с добавлением стадии выдерживания, обозначенной как Н. На фиг. 15 а и 15b две группы адсорбентных слоев показаны с адсорбентными слоями в первой группе, маркированными от 1 до 5 в верхней части графика последовательности, и с адсорбентными слоями во второй группе, маркированными от 6 до 10 в нижней части графика последовательности. Фиг. 15 а является частью последовательности, которая продолжается на фиг. 15b, как показано кодовым буквенным обозначением С. В любое данное время два адсорбентных слоя выполняют адсорбционную стадию, на которой кислотный газ удаляется из сырьевого потока для получения очищенного метанового продукта. Распределение времени цикла для каждого адсорбентного слоя разделено на этапы таким образом, что достигается непрерывное течение сырья и продукта. Например, слой 2 на фиг. 15 а начинает адсорбционную стадию (отмеченную FD) немедленно после того, как слой 1 завершает адсорбционную стадию, и так далее. В подобном режиме непрерывное течение предусмотрено для стадии продувки и потоков выдувания в компрессоры для кислотных газов. Распределение времени циклов между адсорбентными слоями также синхронизируют таким образом, что первая уравнительная стадия Е.1 для одного слоя совпадают со стадий R1 восстановления давления для еще одного слоя, чтобы газ, выведенный во время стадии сбрасывания давления, использовался для восстановления давления в еще одном слое. Например, адсорбентный слой 7 на фиг. 15 а подвергают обработке в уравнительной стадии Е 1 в то же время, когда адсорбентный слой 2 выполняет стадию R1 восстановления давления. График цикла для второй RC-PSA-установки 821 показан на фиг. 16, и имеет такие же признаки,как описанные выше на фиг. 15 а и 15b, включая непрерывное течение потоков сырья, продукта, выдувания и продувки. Обозначения стадий являются такими же, как описано для фиг. 14b, с добавлением стадии выдерживания, отмеченной как Н на фиг. 16. Производительность RC-PSA-системы, описанной в этом примере, была прогнозирована на основе моделирования цикла с использованием обсужденных выше параметров. Результаты обобщены ниже в табл. 1. Комбинация признаков, описанных в этом варианте исполнения, таких как последовательнаяPSA-конфигурация, мезопористый наполнитель и рекуперативная продувка, имеет результатом высокую степень извлечения продукта на уровне 99,4%. Кроме того, высокая чистота продукта менее чем с 1,5% СО 2 и 4 млн-1 H2S обеспечивается отчасти благодаря комбинации таких признаков, как композитный слой с селективным к H2S адсорбентом и кинетически селективным к CO2 адсорбентом и включением Следует отметить, что чистота, достигаемая этой RC-PSA-системой, является неожиданной, поскольку СО 2 и H2S удаляются в процессе в двух совершенно различных масштабах. СО 2 удаляется от 12 до 1,5%, т.е. со снижением в восемь раз. H2S удаляется от 100 до 2 4 млн-1, т.е. с сокращением в 25 раз. Этот результат достигается благодаря применению композитного слоя с правильным выбором стадий цикла и направлений течения. H2S из потока сырьевого газа абсорбируется в первом сегменте композитного слоя, тогда как адсорбирование СО 2 в первом сегменте является пренебрежимо малым, но адсорбция его становится сильной во втором сегменте композитного слоя. Во время стадии десорбции СО 2 из второго сегмента протекает в режиме противоточного течения через первый сегмент композитного слоя. Поскольку, по существу, никакой H2S не присутствует в СО 2, десорбированном во втором сегменте, этот газовый поток обеспечивает парциальное давление продувки в первом сегменте, приводя к очень малому количеству H2S в первом сегменте адсорбентного слоя, что позволяет получить высокочистый газообразный продукт, по существу, не содержащий H2S, в последующей адсорбционной стадии. Этот результат также может быть достигнут, если селективный к H2S адсорбент равномерно диспергирован вCO2-адсорбенте вдоль всей длины слоя. Пример 4. Этот пример описывает такую же RC-PSA-систему, как в примере 3, с двумя модификациями: 1) используют уравнительные резервуары вместо уравниваний от слоя к слою и 2) были применены адсорбентные слои с более крупными диаметрами. В результате этих модификаций повышается продуктивность и производительностьRC-PSA-системы. Применение уравнительных резервуаров сокращает время, требуемое для каждой уравнительной стадии, тем самым уменьшая общую продолжительность цикла. Для каждой из пяти уравнительных стадий для каждого адсорбентного слоя в системе предусмотрен один независимый резервуар под давлением. Эти уравнительные резервуары присоединены непосредственно к одному из адсорбентных слоев. Газы, выведенные из адсорбентного слоя во время стадии сбрасывания давления, временно хранятся в уравнительном резервуаре и затем позже используются в цикле для восстановления давления в том же адсорбентном слое. Поскольку посредством специализированных уравнительных резервуаров сокращаются дистанции для трубопроводов и клапанов, временные интервалы для уравнительных стадий между адсорбентным слоем и уравнительным резервуаром обычно являются более короткими, чем время, необходимое для уравнивания между двумя адсорбентными слоями, и поэтому может быть сокращена общая продолжительность цикла, повышая продуктивность. Также сокращаются габариты и весRC-PSA-системы. Адсорбентные слои в этом примере идентичны тем, которые описаны в примере 3, в том числе в отношении размеров адсорбентных слоев и проточных газовых каналов, адсорбентных материалов и композитного слоя. Одним исключением является только диаметр адсорбентного слоя во второйRC-PSA-установке 821, который увеличен до 1,16 м. В каждой RC-PSA-установке используют такие же последовательности стадий цикла, как в примере 3. Однако более короткие продолжительности цикла, обусловленные применением уравнительных резервуаров, предусматривают различное число адсорбентных слоев для каждой RC-PSA-установки. Для первой RC-PSA-установки 801 требуются шестнадцать адсорбентных слоев, тогда как для второйRC-PSA-установки 821 нужны пять адсорбентных слоев. График цикла для первой RC-PSA-установки 801 показан на фиг. 17, и график цикла для второй RC-PSA-установки 821 показан на фиг. 18. Как и в предшествующих примерах, предусмотрено непрерывное течение потоков сырья и продукта. Однако требования к синхронизации между адсорбентными слоями снижены, поскольку перенос газа между адсорбентными резервуарами устранен вследствие применения уравнительных резервуаров. Таким образом, первая RC-PSA-установка может работать с четырьмя сериями слоев, причем каждая серия исполняет один и тот же график цикла, как показано на фиг. 17. Временные интервалы стадий цикла для первой RC-PSA-установки 801 показаны в табл. 2. Общая продолжительность цикла для первой RC-PSA-установки 801 составляет 10,3 с. Общая продолжительность цикла для второй RC-PSA-установки 821 составляет 6,7 с, как показано в табл. 3 с временными интервалами стадий цикла. Таблица 3 Производительность RC-PSA-системы, описываемой в этом примере, была прогнозирована на основе моделирования цикла с использованием обсуждаемых выше параметров. Результаты обобщены в табл. 4. Комбинация признаков, описанных в этом варианте исполнения, таких как последовательнаяPSA-конфигурация, мезопористый наполнитель и рекуперативная продувка, имеет результатом высокую степень извлечения продукта на уровне 99,4%. Кроме того, высокая чистота продукта менее чем с 1,5% СО 2 и 4 млн-1 H2S обеспечивается отчасти благодаря комбинации таких признаков, как композитный слой с селективным к H2S адсорбентом и кинетически селективным к CO2 адсорбентом, и включением стадии продувки продуктом. Результирующая производительность RC-PSA-системы в этом примере обобщена в табл. 4. Как и в предыдущих примерах, была достигнута степень извлечения метана свыше 99%, тогда как получался высокочистый газообразный продукт с 1,5% СО 2 и около 1 млн-1 H2S. Пропускная способностьRC-PSA-системы для этого примера составляет 170 MSCFD (200600 ст.м 3/ч), что более чем вдвое превышает пропускную способность подобной системы в примере 3. Повышенная продуктивность для этого примера обусловливается применением уравнительных резервуаров. Для крупномасштабного предприятия для переработки газа усовершенствования в этом примере могут иметь результатом значительные сокращения стоимости и габаритов оборудования для удаления кислотных газов. Пример 5. Сырьевой поток природного газа, описанный в примерах 3 и 4, может быть обработанRC-PSA-системами, в которых используются различные комбинации признаков, описываемых в настоящем изобретении. В этом примере описан один возможный вариант исполнения, в котором используют единственную RC-PSA-установку для получения высокочистого метана менее чем с 1,5% СО 2, и менее чем 4 млн-1 H2S, в то же время с достижением высокой степени извлечения метана. Высокая чистота продукта и высокая степень извлечения метана достигаются с использованием вакуумной регенерации в сочетании с прочими факторами, такими как рекуперативная продувка, композитный слой, мезопористый наполнитель и двойные адсорбентные материалы. Фиг. 9 представляет упрощенную технологическую блок-схему для RC-PSA-системы 900, в которой RC-PSA-установка 910 сообщается по текучей среде с разнообразными трубопроводами 901-905 и связанными с ними компрессорами 906 а-906b. Система 900 сблокирована для управления течением текучих сред через систему для выполнения разнообразных стадий цикла, которые описаны ниже. В этом примере сырьевой потек направляют в RC-PSA-систему 900 по трубопроводу 903, содержащему природный газ из трубопровода 901, который может быть объединен с рециркуляционным потоком из трубопровода 902. Поток очищенного продукта, обогащенного метаном, выходит изRC-PSA-системы 910 через трубопровод 904 при давлении, слегка пониженном вследствие падения давления в пределах адсорбентных слоев, клапанов и трубопроводов, находящихся внутриRC-PSA-установки 910. Подводимый сырьевой газ во впускном трубопроводе 901 содержит 12% СО 2 и 100 млн-1 H2S и имеет давление около 85 бар (8,5 МПа). Поток продукта в трубопроводе 904 очищен вRC-PSA-установке 910 до содержания 1,5% СО 2 и менее 1 млн-1 H2S. Кислотный газ десорбируется из адсорбентных слоев и выходит из RC-PSA-установки 910 через трубопровод, соединенный с компрессором 906 а, который создает вакуумметрическое давление на стороне всасывания компрессора около 0,5 бар (0,05 МПа, абс.). Кислотный газ подвергают сжатию в компрессоре 906 а до давления около 20 бар (2 МПа, абс.) и часть потока отводят через трубопровод 905 для использования в рекуперативной продувке в RC-PSA-системе 910. Этот поток обогащен кислотным газом и используется для вымывания метана из проточных каналов и поровых пространств в слое адсорбента адсорбентных слоев, тем самым повышая степень извлечения продукта в RC-PSA-системе. Выходной поток из этой продувки собирают и подвергают сжатию в компрессоре 906b. Выходной продувочный поток обогащен метаном и может быть использован для разнообразных целей, таких как газообразное топливо. В этом примере по меньшей мере часть может быть вовлечена в рециркуляцию обратно во впускной трубопровод RC-PSA-установки 910 через трубопровод 902, и остальная часть используется где-нибудь еще на предприятии. Часть потока кислотного газа, не использованную для рекуперативной продувки, подвергают дополнительному сжатию и направляют на утилизацию путем повторного нагнетания или другими способами.RC-PSA-установка 910 состоит из двенадцати адсорбентных слоев, каждый из которых состоит из структурированного контактора с многочисленными проточными газовыми каналами. В этом примере проточные газовые каналы являются, по существу, квадратными, как показано на фиг. 13 а, с высотой 1301 225 мкм и шириной 225 мкм. Общая длина проточных газовых каналов составляет 1,1 м, и общий диаметр каждого адсорбентного слоя составляет 1,2 м. Структурированный контактор может быть сегментирован вдоль его длины таким образом, что каждый сегмент имеет многочисленные проточные каналы, и газ проходит последовательно из проточных каналов в одном сегменте в проточные каналы в отдельном сегменте. Вдоль длины контактора могут присутствовать от 1 до 10 сегментов. Общее падение давления по длине адсорбентного слоя во время адсорбционной стадии составляет около 1 бар(0,1 МПа). Проточные газовые каналы в структурированном адсорбентном контакторе сформированы из слоя,содержащего адсорбентный материал, который может быть на всем или на части по меньшей мере одного участка стенок структурированного контактора. Слой также может содержать материал мезопористого наполнителя, который сокращает поровое пространство в слое до менее чем около 20%. Средняя толщина слоя составляет 150 мкм, размер 1302 на фиг. 13 а. В этом примере два различных адсорбентных материала используют в композитном слое для обеспечения почти полного удаления H2S, чтобы получить высокочистый метановый продукт. В первом сегменте адсорбентного слоя, имеющем длину 0,10 м,используют аминофункционализированный адсорбент, который селективно адсорбирует H2S. В остальных сегментах адсорбентного слоя, имеющих длину 1 м, используют цеолит, такой как DDR, для поглощения СО 2. Фиг. 13b представляет схематическое изображение композитного слоя 1310, показывая первый сегмент 1311 с функционализированным адсорбентом и вторые сегменты 1312 с DDR. Впускные и выпускные трубопроводы показаны схематически под кодовыми номерами 1314 и 1316 позиций соответственно. Адсорбирование загрязняющих примесей и последующая регенерация адсорбентного слоя достигаются посредством серии стадий в быстром непрерывном цикле. Выбор точного распределения времени стадий и цикла зависит от нескольких факторов, включающих состав подводимого сырья, спецификации продукта, характер загрязняющих примесей и общую степень извлечения углеводородов. Для RC-PSA-установки 910 стадии цикла для единственного адсорбентного слоя иллюстрированы с использованием графика давления в адсорбентном слое в зависимости от времени, показанного на фиг. 19. В дополнение к адсорбционной стадии (FD), после пяти уравнительных стадий (Е 1-Е 5) следует стадия(Р) рекуперативной продувки, единственная стадия (В) выдувания, пять стадий (R1R5) восстановления давления и стадия (FR) восстановления давления путем подачи сырья. Индивидуальные стадии цикла на фиг. 19 более подробно описаны следующим образом.FD: Адсорбция кислотного газа из природного газа под давлением 85 бар (8,5 МПа, абс.) и получение очищенного метана (прямоточное течение) из первого адсорбентного слоя; Е 1: Сбрасывание давления в адсорбентном слое от 85 бар (8,5 МПа, абс.) до около 73 бар (7,3 МПа,абс.) с направлением газа в уравнительный резервуар M1; Е 2: Сбрасывание давления в адсорбентном слое от около 7 3 бар (7,3 МПа, абс.) до 59 бар (5,9 МПа,абс.) с направлением газа в уравнительный резервуар М 2; Е 3: Сбрасывание давления в адсорбентном слое от около 5 9 бар (5,9 МПа, абс.) до около 45 бар(4,5 МПа, абс.) с направлением газа в уравнительный резервуар М 3; Е 4: Сбрасывание давления в адсорбентном слое от около 4 5 бар (4,5 МПа, абс.) до около 36 бар(3,6 МПа, абс.) с направлением газа в уравнительный резервуар М 4; Е 5: Сбрасывание давления в адсорбентном слое от около 3 6 бар (3,6 МПа, абс.) до около 20 бар(2,0 МПа, абс.) с направлением газа в уравнительный резервуар М 5; Р: Продувка адсорбентного слоя при давлении около 20 бар (2,0 МПа, абс.) газом из стадии BD1 под давлением 1,4 бар (0,14 МПа, абс.), который сжимают до давления 21 бар (2,1 МПа, абс.). Газ, вытесненный из адсорбентного слоя в этой стадии, собирают и подвергают сжатию для разнообразных вариантов применения, включающих газообразное топливо, или вовлекают в рециркуляцию для подачи вBD1: Выдувание, или сбрасывание давления, адсорбентного слоя от около 20 бар (2,0 МПа, абс.) до около 0,5 бар (0,05 МПа, абс.). Выходящий поток газа направляют в первую ступень компрессора. Часть потока используют для необходимой продувки после подвергания сжатию до давления около 21 барR5: Восстановление давления в первом адсорбентном слое от около 0,5 бар (0,05 МПа, абс.) до около 20 бар (2,0 МПа, абс.) газом из М 5;R4: Восстановление давления в первом адсорбентном слое от около 20 бар (2,0 МПа, абс.) до около 36 бар (3,6 МПа, абс.) газом из М 4;R3: Восстановление давления в первом адсорбентном слое от около 36 бар (3,6 МПа, абс.) до около 45 бар (4,5 МПа, абс.) газом из МЗ;R2: Восстановление давления в первом адсорбентном слое от около 45 бар (4,5 МПа, абс.) до около 59 бар (5,9 МПа, абс.) газом из М 2;R1: Восстановление давления в первом адсорбентном слое от около 59 бар (5,9 МПа, абс.) до около 73 бар (7,3 МПа, абс.) газом из M1;FR: Восстановление давления в первом адсорбентном слое от около 73 бар (7,3 МПа, абс.) до около 85 бар (8,5 МПа, абс.) сырьевым газом. Типичный график для цикла в этом примере является следующим. Общая продолжительность цикла для вышеописанных стадий составляет 9 с. При использовании уравнительных резервуаров продолжительность стадий сокращается по сравнению с предыдущими примерами и поэтому уменьшается общая продолжительность цикла. В результате этого повышается продуктивность адсорбентных слоев, поскольку на адсорбцию затрачивается большая часть общего времени цикла. Поэтому для непрерывного течения потоков сырья и продукта требуется меньшее количество адсорбентных слоев. В этом примере для непрерывного течения требуются только три адсорбентных слоя,поскольку каждый слой находится в состоянии адсорбции в течение 1/3 времени. Вся RC-PSA-установка 910 может работать с четырьмя сериями из трех слоев, действующих по одному и тому же графику цикла, как показано на фиг. 20. Соображения в отношении стадий являются такими же, как описано на фиг. 19, с добавлением стадии выдерживания, отмеченной на фиг. 16 как Н. При такой конфигурации четыре адсорбентных слоя находятся в адсорбционной стадии в любое данное время. Поскольку используются уравнительные резервуары, каждый адсорбентный слой действует независимо, и распределение времени циклов для различных адсорбентных слоев не синхронизированы для обеспечения уравнивания между адсорбентными слоями. Синхронизация адсорбентных слоев необходима только для обеспечения непрерывного течения потоков сырья и продукта. Производительность описанной в этом примере RC-PSA-системы прогнозирована на основе моделирования с использованием обсужденных выше параметров. Результаты показаны в табл. 5. Комбинация признаков в этом варианте исполнения обеспечивает получение потока высокочистого продукта с 1,5% СО 2 и менее 1 млн-1 H2S, в то же время с достижением высокой степени извлечения свыше 99%. Сочетанием вакуумной регенерации с другими признаками, такими как рекуперативная продувка,мезопористый наполнитель и уравнительные резервуары, RC-PSA-система, описанная в этом примере,достигает чистоты и степени извлечения, подобных RC-PSA-системам, описанным в примерах 3 и 4, но продуктивность повышена до 193 MSCFD (227740 ст.м 3/ч), и число адсорбентных слоев значительно сокращено. В результате этого стоимость и габариты оборудования для удаления кислотных газов являются значительно меньшими, чем в традиционной PSA или другой технологии с такой чистотой продукта.
МПК / Метки
МПК: B01D 53/26, B01D 53/047
Метки: удаления, сырьевого, примесей, газообразного, процесса, адсорбционного, циклического, загрязняющих, основе, способ, потока
Код ссылки
<a href="https://eas.patents.su/30-24199-sposob-udaleniya-zagryaznyayushhih-primesejj-iz-gazoobraznogo-syrevogo-potoka-na-osnove-ciklicheskogo-adsorbcionnogo-processa.html" rel="bookmark" title="База патентов Евразийского Союза">Способ удаления загрязняющих примесей из газообразного сырьевого потока на основе циклического адсорбционного процесса</a>
Предыдущий патент: Способ короткоцикловой адсорбции при переменном давлении и температуре для отделения тяжелых углеводородов от потоков природного газа
Следующий патент: Способ и устройство восстановления первоначальной формы насосно-компрессорной трубы
Случайный патент: Вакцинная композиция против папилломавируса человека и способы ее получения и применения